摘要
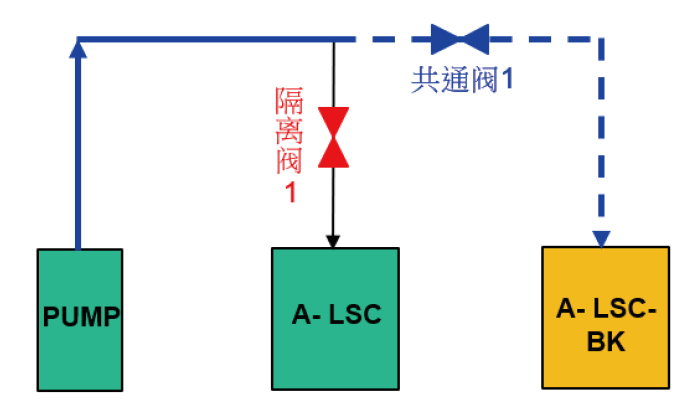
Pumping-line 全自動清管器的開發與應用
Keywords / Process exhaust pumping-line,Viscous special gas,Powder clean,An integrated auto-clean machine
「製程排氣管路」(Pumping-line)作為「生產機臺附屬系統的一環,一方面承載著提供製程chamber高真空度環境的作用,另一方面也是製程排氣輸送至「現址式廢氣處理洗滌塔」(Local scrubber, LSC)的重要管路。本文所討論的主體為廠務製程排氣管路Pumping-line(Dry pump至LSC之間的管路)。其內部流動的為高濃度、高危險性的製程特殊氣體,其中黏滯性氣體經化學反應后會產生「粉塵」(Powder)附著于管路內進而造成管路堵塞,這就需要定期停機拆卸管路手動進行Powder clean作業。
本研究著眼于Pumping-line Powder clean的自動化技術,成功開發出全自動清管器,取代「人工手動清潔管路」現行保養模式,可廣泛應用于不同製程的Pumping-line。此作法可有效提高清潔效果,減少保養人力成本支出,更可減少由於長時間停機保養造成的Dry pump內部管路冷凝堵塞故障維修成本,增加Tool有效生產的時間。
As a part of the accessory system of the Fab's manufacturing tool. On the one hand, it plays the role of providing a high vacuum environment for the process chamber, on the other hand, it is also an important pipeline for delivering the process exhaust to the Local Scrubber. The Pumping line(the pipe between Dry pump and Local Scrubber) discussed in this study is facility process exhaust pipe. The internal flow is special gas with high concentration and high risk, in which the viscous gas will produce "powder" after chemical reaction. As a result, it condensed and clogged in the pumping-line. This need to turn off tool and dismantle the pumping-line for Powder clean manually by routine maintenance.
Focusing on the automation technology of Pumping line Powder clean, this study has successfully developed an integrated auto-clean machine, replacing the current maintenance mode of "manual pipeline cleaning", which can be widely used in pumping line of different processes. This machine could effectively improve the cleaning effect and reduce the maintenance labor cost. Even, it could reduce the maintenance cost of the condensate blockage fault in the dry pump internal pipeline caused by the long-down maintenance, and increase the effective production time of the tool.
1. 前言
1.1 製程排氣管路穩定運轉的重要性
制程排氣系統作為生產機台日常運轉的重要環節,承擔著空汙防制重要責任。該系統由制程排氣管路Pumping-line、Dry pump、現址式廢氣處理洗滌塔Local scrubber、制程排氣管路Exhaust duct、中央洗滌塔Central scrubber組成。
Pumping-line由兩部分組成,第一部分為Tool至Dry pump之間的管路,稱為Fore-line段,具有高真空度環境;第二部分為Dry pump至LSC之間的管路,無真空度需求,僅為微負壓環境(通常介於-0.9Kpa~0Kpa之間)(圖1)。其中制程排氣管路Pumping-line作為Dry pump之後的微負壓管路,內部輸送的黏滯性氣體會產生化學反應或是冷凝形成粉塵附著於管路內,雖然Pumping-line外部有包覆加熱帶以推遲粉塵形成的速度,但是隨著生產機台運轉時數的增加,粉塵累積的量會增多,進而會堵塞管路,造成Dry pump的背壓升高,存在Dry pump宕機或是制程排氣回灌Tool chamber的風險,最終造成產品的缺陷。
圖1、製程排氣處理系統介紹
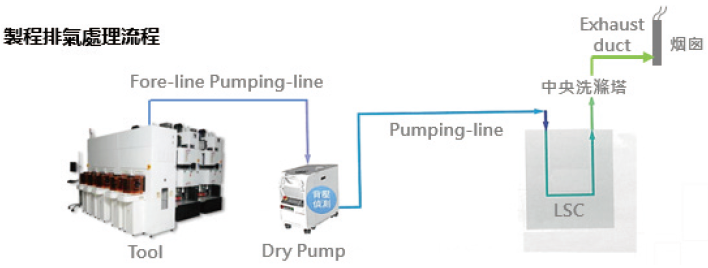
1.2 製程排氣管路(Pumping-line)運轉宿疾
在實際運轉過程中Pumping-line,通常會產生諸多持續困擾廠務工程師的問題。第一個問題就是「塞管」,不同制程所用特殊氣體不盡相同,管路內積聚的Powder成分也不同,所表現的特性也不同,清潔難度各不相同:部分制程Powder質地鬆軟、有孔隙,便於清潔;一些制程Powder質地堅硬,很難清刷;還有一些制程Powder包括易燃發火性組分,清管過程則屬於高風險作業(圖2)。依據清管時間區分清潔難度,共分5個層級,以下列舉幾項易塞制程說明(表1)。
圖2、不同制程產出Powder形態分析
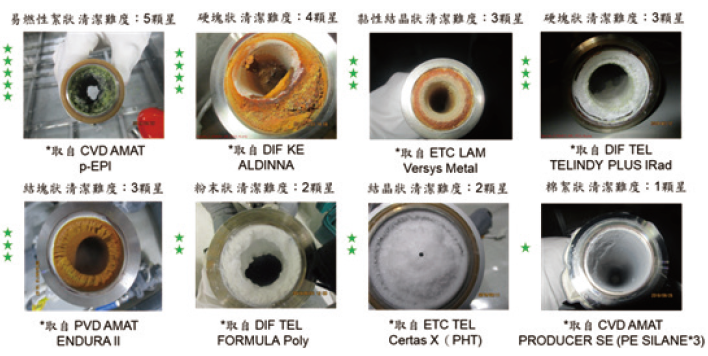
製程 | 單臺清潔時間(hr) | 清潔難度 |
---|---|---|
薄膜SiN | 1 | ★ |
蝕刻Oxide | 2.5 | ★★ |
蝕刻Metal | 3 | ★★★ |
爐管TiN | 4 | ★★★★ |
薄膜P-EPI | 6 | ★★★★★ |
Pumping-line運轉的第二大問題是「氣體洩漏」,經由運轉統計資料分析,2018/3~2021/10期間,共發生氣體洩漏10次,其中3次氣體洩漏發生原因為管路拆裝清潔保養後重新組裝氣密不佳。通過加強保養人員Pumping-line拆裝訓練,雖然可以在一定程度減少人為拆裝失誤,但是仍不可杜絕裝配失誤導致的氣體洩漏事件。
其三,Pumping-line管路拆裝清潔保養增大加熱帶損壞率。加熱帶作為推遲管路Powder堵塞的附屬裝置,在清管前,需先行拆卸下來,待保養完成後再重新安裝。此過程,分段式加熱帶接頭由於多次插拔會導致鬆動,引發加熱帶溫度監視信號中斷,甚至接頭接觸不良導致加熱帶不加熱的情況發生。據統計,人為拆裝加熱帶導致的故障發生率為31%(以2020年度南京廠加熱帶警報統計資料分析(圖3),人為原因導致的故障發生58起,總計警報184起),也是運轉過程中一大負擔。
圖3、2020年度南京廠加熱帶ALARM統計分析
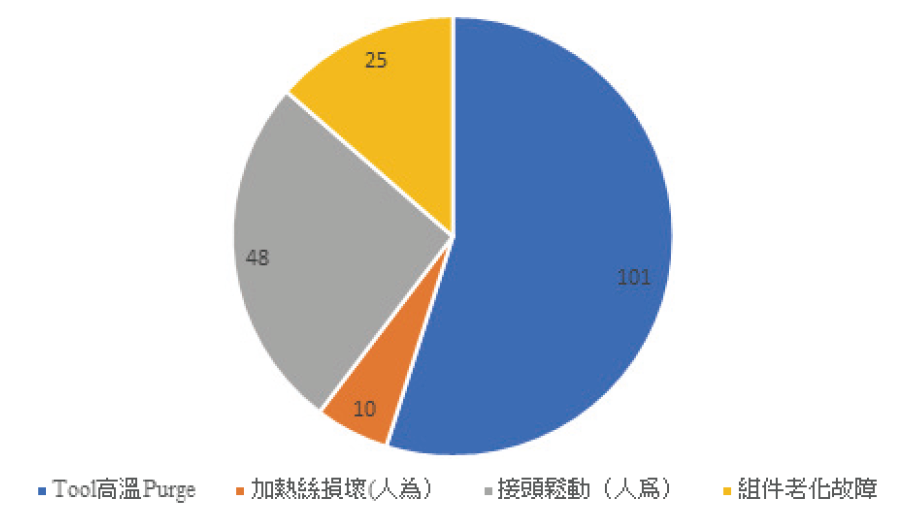
1.3 製程排氣管路保養模式智慧化變革的意義
Pumping-line現行保養模式為人員手動拆卸-清潔-組裝每段管路,依南京廠運轉經驗來看,全年消耗4500hr工時數,約占LSC system PM loading 20%(表2)。
PM項目 | 全年數量 | 單台人力 | 單人單台工時(hr) | 全年總工時(hr) |
---|---|---|---|---|
Pumping line PM | 500 | 3 | 3 | 4500 |
除卻Pumping-line清潔保養時間長之外,現行的保養工具也是非常簡易,保養人員主要憑藉「一字起和鋼刷」進行管路內壁的Powder清潔,當遇到長管和彎管的時候,這兩項工具就顯得比較乏力,無法做到有效清潔。
以上所述表明,現行Pumping-line保養模式消耗較多的人力資源成本、ESH安全成本和附屬設備維修成本。現如今在智慧化工廠改革的背景下,研發並運用自動化技術變革現行Pumping-line保養模式,就顯得很有必要且有意義。
南京廠經過腦力激蕩,發想開發出一款管路清潔裝置,以達到自動清潔效果。
2. 文獻探討
2.1 半導體行業製程排氣管路配置演變
半導體產業離不開真空技術。生產半導體元件:①要在矽片上摻入相應的其他元素 ; ②在生產積體電路時要形成複雜的金屬薄膜和絕緣膜 ; ③要進行表面的刻蝕處理等複雜的工序。如果生產過程中的真空度不夠,矽片表面上沾了灰塵會導致內流動的電子無法通過而出現短路導致報廢。
制程真空則由通過真空泵和真空管路提供,真空管路同時也是排氣管路,其內部輸送半導體特種氣體,包括易燃性、毒性、腐蝕性等[1]。真空技術的零另一應用體現在此,真空造成的壓力差可以吸著氣體,遠距離傳輸氣體至廢氣處理系統。[2]同時氣體物質在低氣壓環境內蒸汽壓較低容易保持氣態,氣體活性較低,氣體碰撞機率較小。因而保障Fore-line高真空段易燃腐蝕性氣體不會引發火災、洩漏和附著管路等問題。
較早時,油式真空泵是半導體行業中常用的真空泵種類,最主要的特點是真空度高,能滿足新型行業的特殊工藝要求,其中又以旋片式真空泵和往復式真空泵為主要代表。因不能抽水蒸氣和可凝性氣體及易腐蝕性氣體等受限,但隨著真空泵的研發生產技術提升,轉而採用清潔、安全、耐磨、造價低、維修方便、性能穩定、振動小、噪音低等優勢的幹式真空泵,就滿足半導體行業工藝要求[3]。
幹式真空泵後端的排氣管路僅作氣體輸送用,無需真空環境,微負壓即可。但由此也帶來特種氣體沉積附著管路和氣體洩漏的問題。為此管路則設計成小段通過快接件連接,便於停機時清潔維護。同時管路閑使用「O型密封圈」O-RING進行氣密防護(圖4),高溫制程和使用腐蝕性氣體制程排氣管路還需使用耐高溫、耐腐蝕的全氟O-RING進行強化防護,避免連接段腐蝕洩漏,引發安全事故。
圖4、Pumping-line管路連接方式
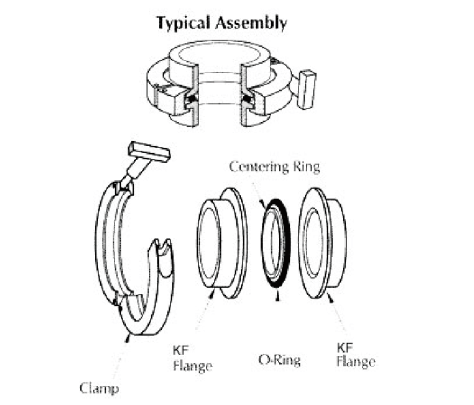
2.2 歷年關於製程排氣管路的保養模式的研究
為減少排氣管路内氣體沉積物的附著,半導體從業者一直在研究。其中主要從「源頭端減少沉積物生成」和「沉積物處理方法」兩個方向展開。大致可分以下幾類:
- 提高排氣管路内氣流溫度以確保内部氣體冷凝附著,一是包覆加熱帶[4],多數製程維持管路在120℃,少數極易塞製程維持180℃;二是管路内施以高溫N2氣體,使用熱風槍原理維持氣流溫度在250℃。兩者適用場景不同,HOT N2適用于難以包袱加熱帶的複雜管路或是管壁厚實的特殊管路,比如彎管和球閥段,加熱效果佳。但是其運行費用要高於加熱帶,體現在功率較大和N2氣體費用。三是注入特殊腐蝕性氣體清潔管路内壁[5],目前僅在fore-line段使用dry-clean技術,由於特氣費用以及對管路的傷害性沒有全面推廣。
- 管路沉積物去除方式包括在chamber出口段安裝cool trap或是濾網箱抓取粉塵[6]。Cool trap,利用一密閉容器於內部置一循環冰水管接觸片狀,或網狀物,因廢氣冷凝效應會有粉層吸附於片狀或網狀物上,只要定期更換或清洗,即可低降低粉層塞管的現象。但是需要頻繁停機,導致產能減少。
現行各廠區采取管路包覆加熱帶、加裝Hot N2以及定期拆卸排氣管路清潔的保養模式。FOR-LINE段由於高真空,氣體沉積率較低,保養周期較長,一般為3~5年;乾式真空泵後端管路為微負壓,特殊氣體易于沉積,保養周期較短,短則3個月,長則1年。
2.3 製程排氣現行保養模式存在的弊端分析
頻繁拆裝每段排氣管路,需確保復歸后管路的氣密,通常采用N2保壓或O2測量兩種測漏方法。實際運轉過程中,難免存在測漏失效的情況。同時人爲手動清潔難以清理彎管和長管内粉塵,導致管路堵塞的風險依然存在。有研究統計,某半導體廠內,2006~2010年所發生之異常事件,針對區域洗滌設備之異常事件進行統計與探討,氣體洩漏事故佔百分比62%,而氣體洩漏事故之原因,所占比例最多者為管路阻塞,約為41%[7];因而現行保養模式存在較大的氣體泄漏風險。
其次每次清管都需要DRY PUMP停機,DRY PUMP停機后溫度降低,内部管路殘留的粘滯性氣體則會沉積在管路内,停機時間越長,管路堵塞的程度越加劇,很多情況下,停機1hr DRY PUMP便無法開啓,需返廠維修,而清管時常通常大於1hr。另一方面,DRY PUMP停機也意味著無法生產,現階段全球晶片產能吃緊,頻繁清管也消耗了一部分產能。
在現有的製程排氣管路架構模式下,管路儘管包覆加熱帶以及施以HOT N2,管路内仍存在沉積粉塵需通過定期拆卸每段管路清潔,此保養模式的弊端是容易發生氣體泄漏和DRY PUMP卡死。
3. 研究方法
3.1 清管方式變革的發想
現行保養模式主要依靠自主保養人員手動拆裝每段管路,工作Loading繁重,通常保養一臺廠務側Pumping-line平均需要3人耗時3小時完成。隨著南京廠區自主保養範圍的擴大,自主保養人員朝多面手發展,人力成爲短缺的資源。
鑒於此情況,南京廠發想通過一款自動清管器實現以下三大目標(圖5):①減少拆管口數;②一次性清潔到底,從dry pump出口到LSC入口;③有效清潔管路内的粉塵,清潔程度高於人力手動清刷效果。
圖5、Pumping-line清管方式變革發想
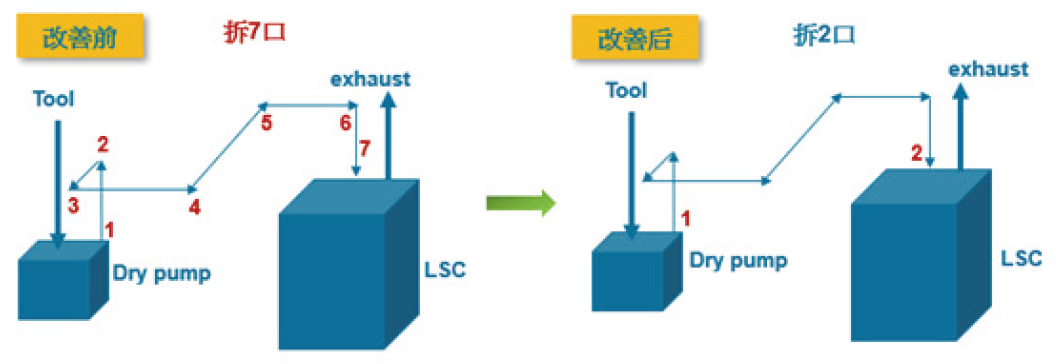
3.2 市售產品的選擇與測試
市售常見管道清潔設備包括馬桶用管道疏通器(簡稱市售A款)和貫通式管道清理機(簡稱市售B款)(圖6),兩款產品各有優缺(表3),但是均無法在廠務側Pumping-line管道内應用。
圖6、市售A款(左)和B款(右)測試
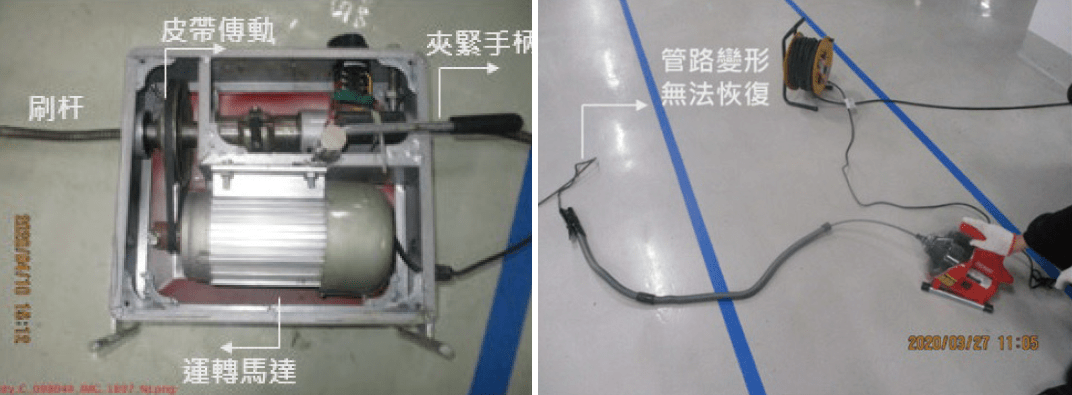
市售A款 | 市售B款 | |
---|---|---|
優點 | 内置刷杆收納空間,方便使用。旋轉速度可調節。 |
尺寸較小,便於現場使用。 刷杆强度高,清潔效果好。 |
缺點 |
刷杆為彈簧,强度不夠,難以克服阻力,手動前進困難。 刷杆容易形變,無法再次使用。 無刷頭,清潔效果有限。 |
旋轉功能為手動,需搭配夾緊手柄使用。 刷杆無法自動前進, 無刷頭,清潔效果有限。 |
3.3 清管器自主開發過程
市售產品無法實現發想的三個目標,後續自主DIY的組合配置「手電鉆+延長杆+刷頭」也僅能單段管路清潔,無法清潔到底。强烈的需求迫使南京廠繼續開發,最終開發適用的全自動Pumping line管道清潔設備。
它的特點包括 : ①特制的導向頭和刷頭,可過彎管,一刷到底,清刷速度可調節;②配置PM-Q内視鏡,有效檢視清刷效果;③管路末端配置集塵盒,防止Powder逸散。
全自動清管器的機械傳動機構為兩顆不同功率的馬達,其一承擔刷杆的旋轉功能,其二承擔刷杆的前後移動功能。旋轉功能通過皮帶進行傳動,前後移動的原理類似於機械手臂,通過抓緊刷杆前後位移。該兩顆馬達為變頻設計,匹配不同堵塞程度管路的清刷速度,以達到節能效果。
刷杆的前端配置球形導向頭,便於刷杆通過管路的彎頭部分。刷頭的設計便於清刷,刷杆的位移操作集成於「人機交互介面」(Human machine interface, HMI)之上。
3.4 實際應用的難點與挑戰
在上機使用的過程中,遇到的第一個難點便是如何與管路銜接。經過多次嘗試,最終確定長bellow+clamp的連接方式,同時在清管器出口預留法蘭面介面,確保氣密。
第二個難點便是如何通過三通T型管和球閥(圖7)。三通T管本體的構造存在兩顆出口,黨刷杆進入三通T管往往會通往備管方向,進入路徑死角;球閥的難點在於球心縮小變徑,刷杆無法通過。採用「拆卸T管+手閥,以短bellow替換銜接」的方法(圖8),刷杆便可順利通過。不過需要注意,Pumping line備管段(共同閥通往LSC備機的部分管路)則需排定於LSC備機PM時同步清潔。
圖7、全自動清管器上機連接T管和手閥的阻礙
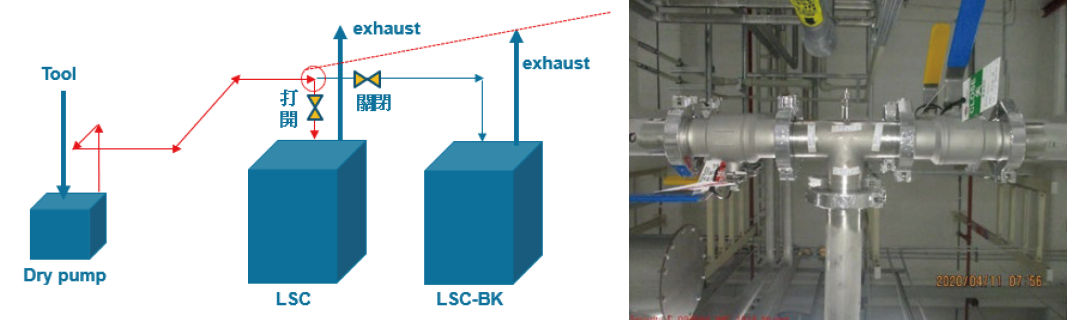
圖8、Bellow管替換T管和手閥
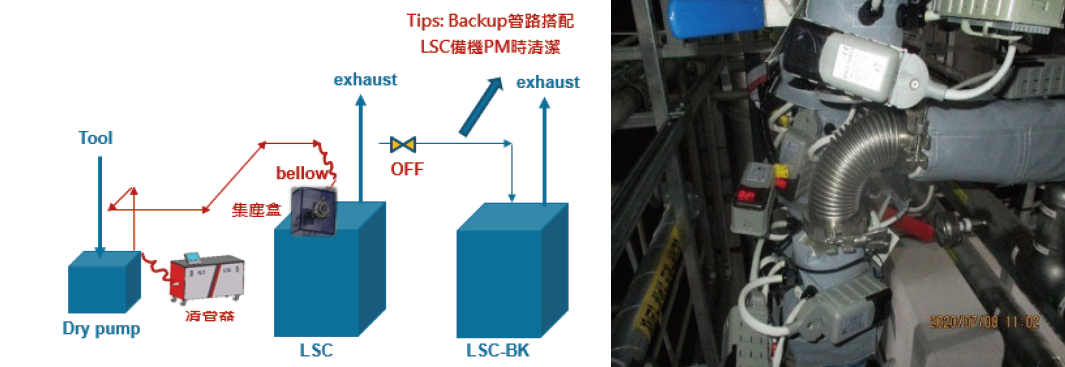
實際LSC配置場景存在不同備機模式(表4),清管器使用方法均可簡化為一主一備場景下「主機清主管;備機清備管」兩次清潔模式(圖9~圖12)。具體方法為:使用Bellow替換隔離閥與三通T管,第一次清潔主管路段pumping line;第二次搭配LSC備機清潔共通閥之後的備管段pumping line。
備機模式 | 共管 Dry pump 數量 | 主機清管範圍 | 備機清管範圍 | 注意事項 |
---|---|---|---|---|
一主一備 | 1 | 實線部分 | 虛線部分 | |
一主一備 | 2 | 實線部分 | 虛線部分 | Pump1的備管須在 Pump2停機工況下進行 |
二主一備 | 1 | 實線部分 | 虛線部分 | 同一主一備 |
二主一備 | 2 | 實線部分 | 虛線部分 | 備管範圍包含2段 |
三主一備 | 1 | 實線部分 | 虛線部分 | 同一主一備 |
三主一備 | 3 | 實線部分 | 虛線部分 | 備管範圍包含3段 |
四主一備 | 1 | 實線部分 | 虛線部分 | 同一主一備 |
圖9、LSC一主一備配置模式(1顆PUMP共管)
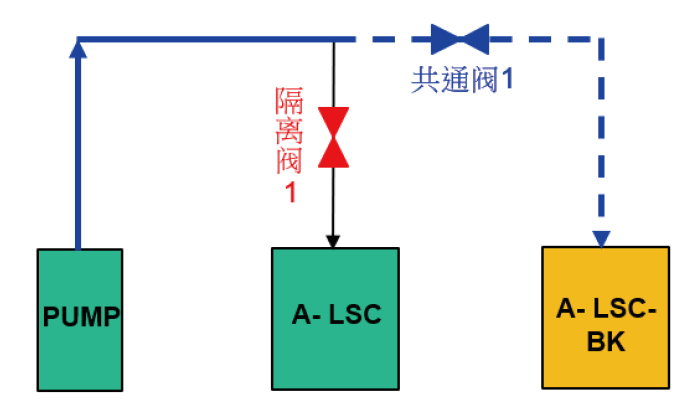
圖10、LSC一主一備配置模式(2顆PUMP共管)
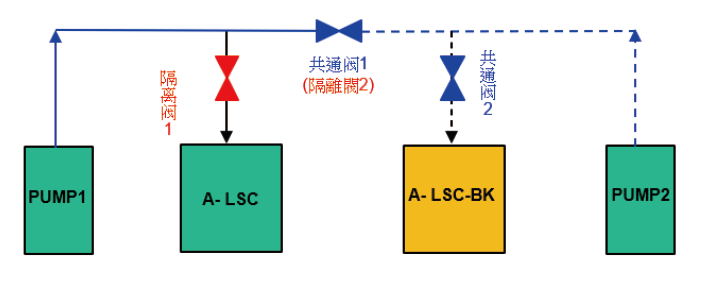
圖11、LSC二主一備配置模式(2顆PUMP共管)
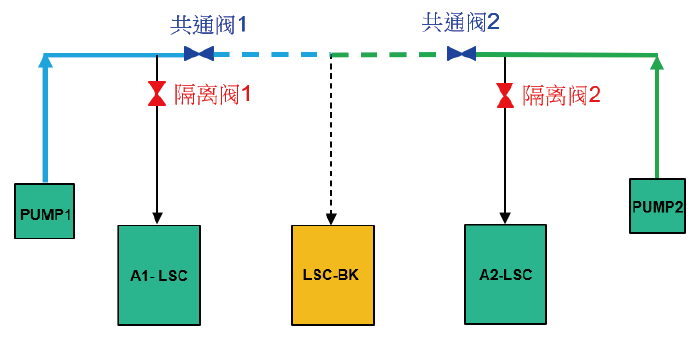
圖12、LSC三主一備配置模式(3顆PUMP共管)
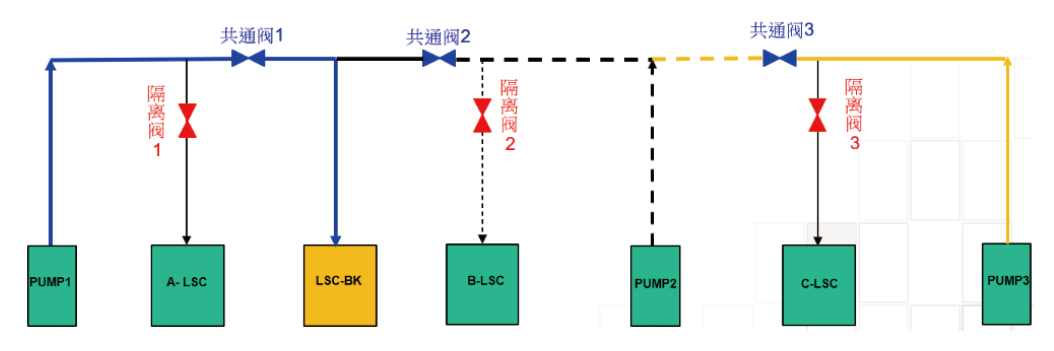
第三個難點是如何確保清刷出來的粉塵不逸散於環境中,透明PVC收集盒的配置可氣密收集粉塵。粉塵收集盒為方形設計,前後端分別預留3"和2"「法蘭介面,分別適用於不同尺寸的管路。透明設計則可以便於觀察粉塵是否妥善收集於集塵盒內。為確保集塵盒為微負壓環境,集塵盒上方預留CV介面。
在前期測試環節,自動清管器原型機體型較大,導致某些現場DRY PUMP擺放緊密的位置無法使用。後續通過優化導杆收納空間和電機擺放空間,二代機成功縮減體積近1倍(圖13),尺寸從長1250mm*寬650mm*高700mm縮減至長920mm*寬300mm*高530mm,可成功進入現場最小作業空間450mm(圖14)。
圖13、全自動清管器初代機(左)與二代機結構對比
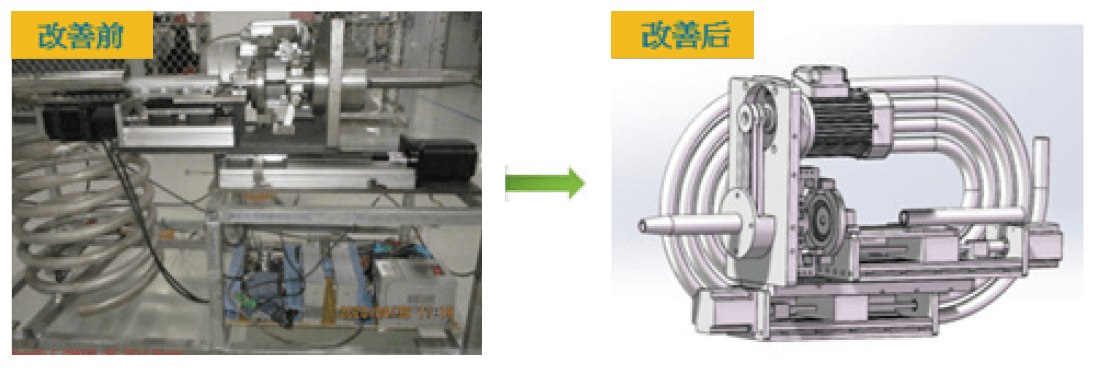
圖14、全自動清管器初代機(左)與二代機尺寸對比
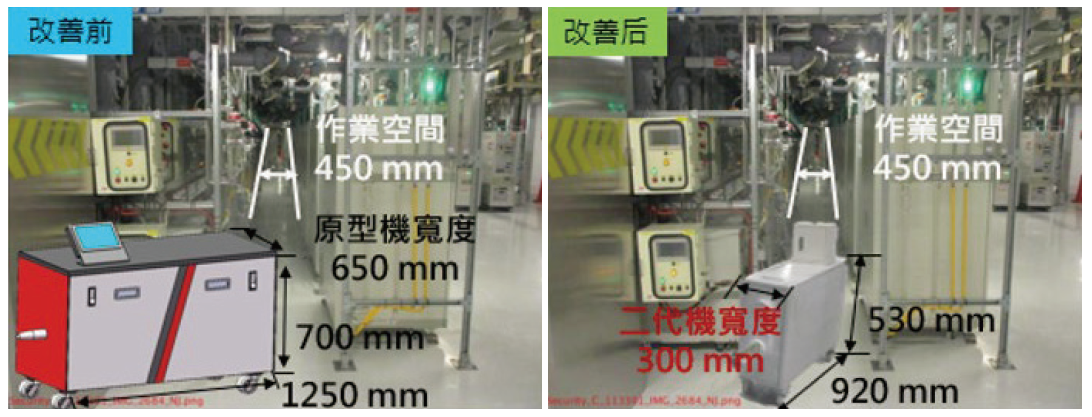
4. 結果探討
4.1 不同製程排氣管路沉積物去除效果
南京廠N1X制程排氣管路沉積Powder依據現行人力拆管清潔時間區分為五類清潔難度,Pumping-line全自動清管器從易到難測試清刷效果(圖15),最終成績為3顆星及以下難度可有效清潔(表5),Furnace和EPI制程Powder不適用清潔,在於Furnace Powder堵塞嚴重,且質地堅硬,刷頭無法有效清刷。EPI制程Powder組分包括GEH4和PH3屬易燃發火特性,現行保養需採取漸氧工法,清管器無法適配。
圖15、全自動清管器適用製程
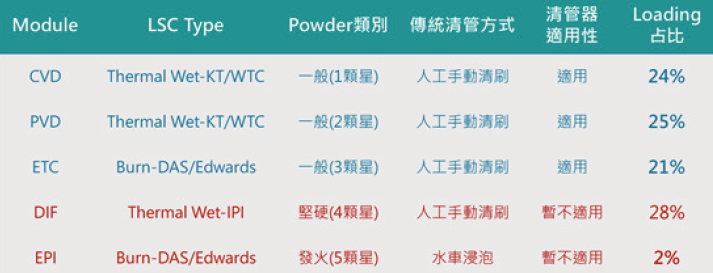
項次 | 制程 | 清管前 | 清管後 |
---|---|---|---|
1 | ETC | ![]() |
![]() |
2 | CVD | ![]() |
![]() |
3 | PVD | ![]() |
![]() |
4.2 製程排氣管路保養時間減少對生產效率提升的幫助
Pumping line保養須在dry pump停機工況下完成,減少的保養時間可以轉化為生產時間。同時,dry pump停機時間過久內部轉子容易被冷凝形成的沉積物卡住,無法啟動,這就會增加額外的維修成本和時間。據統計,每年度ETC制程每年可減少因清管造成DRY PUMP維修15次。
4.3 全自動清管器應用模式下保養費用節省分析
相較現行保養模式,應用全自動清管器可提升效率4.5倍,單支管路清潔可節省人力1名,工時減少2hr,按照全年清管500支管路計算,南京廠全年可節省工時3000hr,可節省1.36M NTD。實際使用過程中,Furnace和EPI制程不適用,因此每年最終可節省0.9M NTD(圖16)。
圖16、全自動清管器使用模式與現行保養模式花費比對
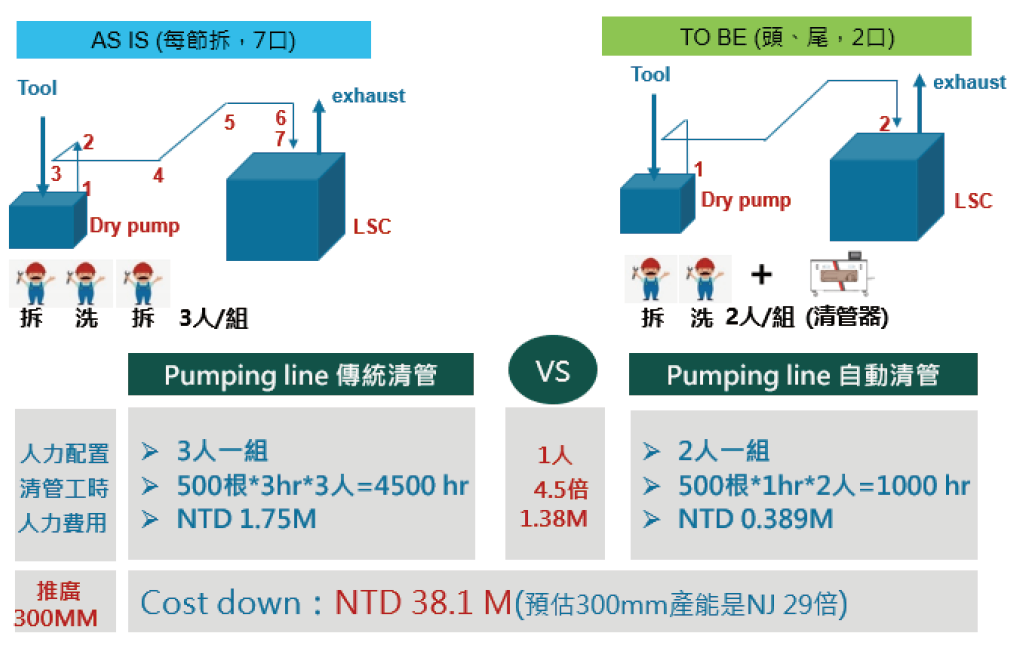
4.4 全自動清管器配置模式及保養內容
4.4.1 配置模式
以南京廠為例,P1A Pumping line易塞管LSC類型包括電熱水洗式和燃燒水洗式,共計377台。年清管次數約為500次,平均1天2支。此清管頻次下南京廠日常配置2台(一用一備)即可滿足清管需求。後續廠區如配置清管器,可參照此標準進行計算。
4.4.2 保養內容
清管器日常使用需對直接接觸Powder的元件進行定期清潔,包括導頭、刷頭和導杆,以及導杆收納管前濾網、集塵盒。此外也需對動力單元和安全裝置進行定期檢查(表6)。
項次 | 檢視或保養項目 | 1/2M | 1M | 3M | REMARK |
---|---|---|---|---|---|
1-1 | 刷頭清潔 | V | 建議2M更換刷頭 | ||
1-2 | 導頭清潔 | V | |||
1-3 | 刷杆及收納管濾網清潔 | V | |||
1-4 | 集塵盒清潔 | V | |||
2-1 | 限位器檢查 | V | |||
2-2 | 皮帶輪檢查 | V | |||
2-3 | 軸承對心檢查 | V |
5. 結論與建議
較傳統清管模式,配置全自動清管器效率可提高至4.5倍,NJ 20K產能下,全年可節省新臺幣0.97M,ROI值為0.82。推廣至300mm,估算全年可節省新臺幣38.1M。
全自動清管器目前無法于Furnace制程使用,究其原因在於Powder組分多為NH3結晶,且累積速度較快。可以嘗試的方式為增加保養頻次,於Powder初期累積的羸弱時期將其清除,同時考慮DRY PUMP停機卡死的影響,每次保養時間控制於1hr以內。其二是加裝水噴淋和烘乾系統,NH3可以溶解于水中,加水配合清刷則可清除Powder,清刷完再配合熱空氣烘乾,可保證管路正常運轉工況。
參考文獻
- Kumagai, Y H . Hazardous gas handling in semiconductor processing 《Journal of Vacuum Science & Technology A Vacuum Surface s and Films》1990.
- 蘇青森。真空技術的發展與應用《化工技術》2005.Jan。
- 張慎周。各類真空幫浦的特性與比較《化工技術》2005.Jan。
- 德易力科技股份有限公司,https://www.directlytek.com/article-about.html
- 徐偉翔。加熱用於特殊氣體管路附著去除效應-以某半導體廠為例《國立交通大學碩士論文》2012.August。
- 徐偉翔。加熱用於特殊氣體管路附著去除效應-以某半導體廠為例《國立交通大學碩士論文》2012.August。
- 陳威儒。區域洗滌設備異常事件失誤模式探討-以某半導體廠為例《國立交通大學碩士論文》2012.March。
留言(0)