摘要
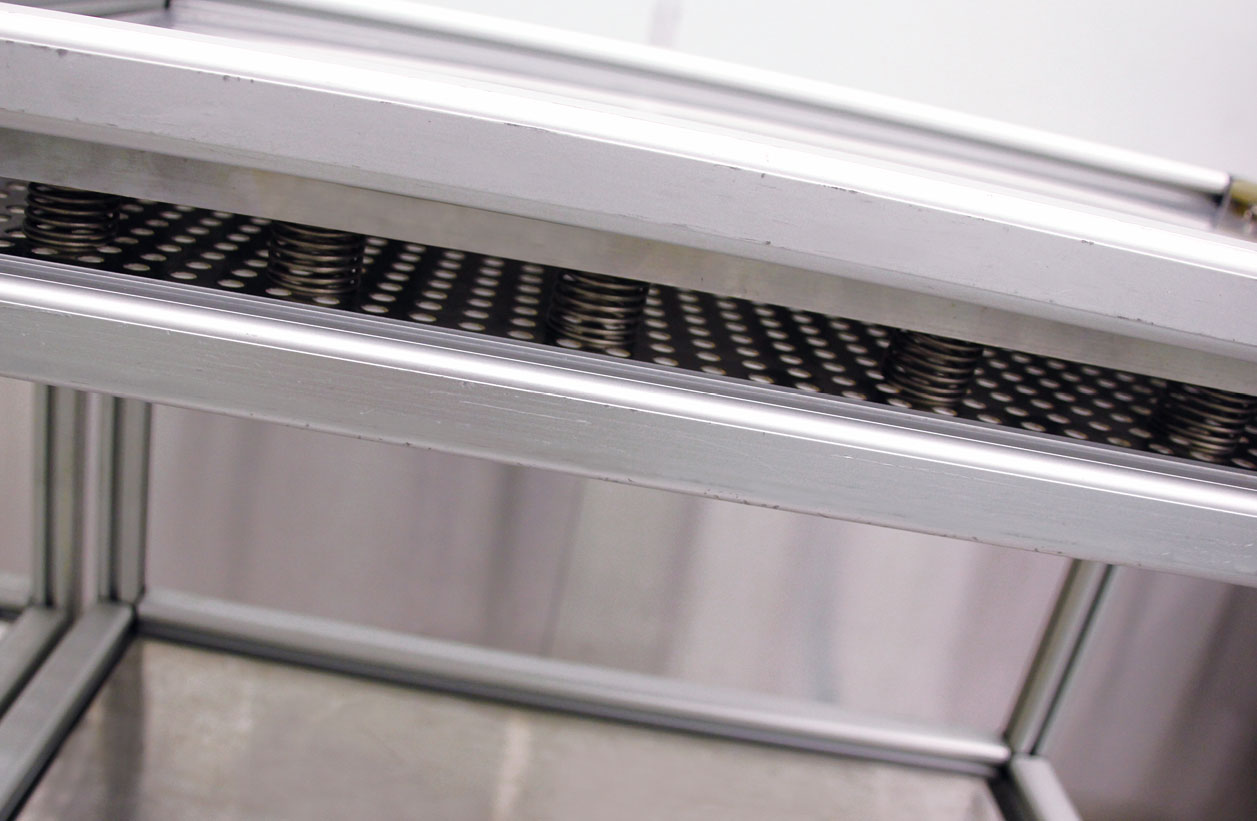
創新型微震彈簧推車研發設計及震動改善
Keywords / Wafer Vibration,Anti-Vibration Cart,Vibration Spring
針對本廠既有推車做不同類型參數實驗,包括孔洞板、實心地板、軟硬彈簧等震動試驗,以研究在各種不同的參數實驗下,推車於運送POD過程中分析Wafer震動及Wafer Notch旋轉偏移等問題做深入之探討。本研究分成實驗量測方法、使用專業量測Wafer震動精準儀器Wafersense AVS (Automatic Vibration System) 量測震動,進而提出彈簧設計理論基礎,並利用簡諧運動數學方程式推導之數值計算,建立一套完整的研究方法,以探討本研究創新設計之晶片微震彈簧對Wafer減震效果。研究結果顯示,其改善效果不僅無任何震動異音且Wafer notch無偏移現象,此外晶片盒不會過度搖晃,亦解決晶片盒內Particle揚起而遭受塵埃微粒污染Wafer問題,不僅提高晶圓良率並大量節省成本支出。
前言 Foreword
晶圓製造對製程規格之要求嚴謹,機台須具備該加工步驟所需之製程規格方可進行加工。此外,為了確保產品良率,同一批晶圓需要相同製程規格之不同步驟須使用相同機台進行加工,Wafer之示意如圖1所示。然而工作人員使用推車運送Wafer時,施加正向推力於車體上,推車運送過程中發生震動,Wafer因受到震動影響不但造成notch旋轉偏移,如圖2所示為Wafer受到震動影響前後之notch旋轉偏移情形,亦使得晶片盒內Particle揚起而汙染Wafer。此外當Wafer notch旋轉偏移,致使DIF爐管高溫Holder影響Wafer中的AM(Align Mark)變形,造成LIT製程曝光顯影時會偏移而導致Wafer Scrap問題,如圖3所示。
圖1 Wafer Notch 轉向定位不一,會重覆對焦影響 yield
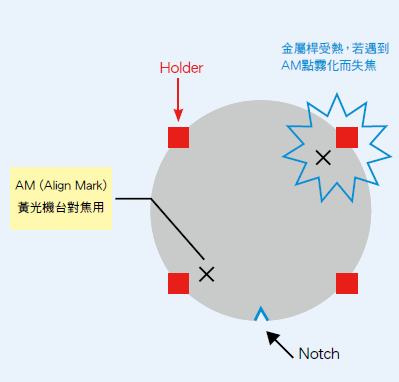
圖2 Wafer受到震動影響前後之notch旋轉偏移情形
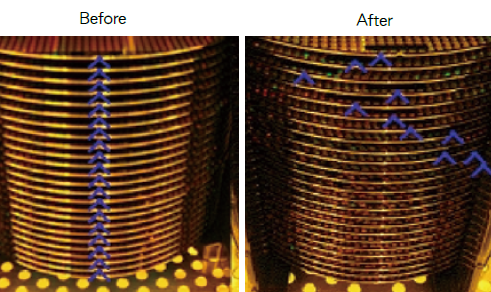
圖3 Wafer notch旋轉偏移使得爐管高溫AM變形,造成LIT 製程曝光顯影偏移
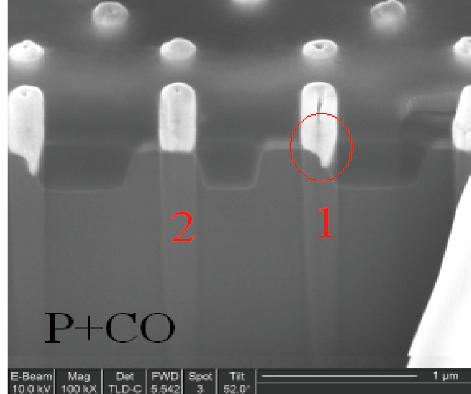
參考國內外技術報告、設備製造廠商與相關文章,發現針對推車震動對晶圓影響等相關文獻甚少,且對於此問題之解決模式也大多受限於假設條件。其問題解決方法,一般多是仰賴現場工程師的經驗判斷,於推車輪胎上加裝避震器來緩衝震動能量,其改善成效不彰且不易落實推行於真實的晶圓製造廠,以致於現階段尚無法解決推車震動對晶圓不良影響之困境。
針對可能高風險製程目前係以禁止使用推車而改由MFG人員用雙手運送之暫時對策或防堵措施,以減少推車運送過程中所產生之震動,避免造成Notch旋轉偏移,如圖4所示。
圖4 高風險製程禁止使用推車而改由人員用雙手運送Wafer
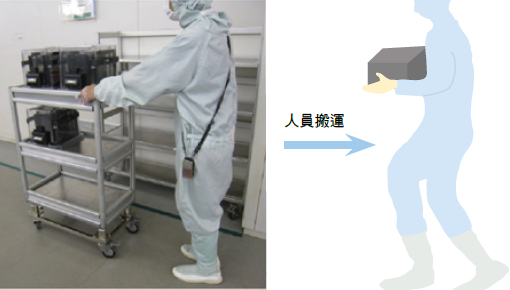
創新型微震彈簧推車研發設計
實驗方法及步驟
針對本廠既有推車做不同類型參數實驗,以研究在各種不同的參數實驗下,推車於移動過程中產生震動導致Wafer旋轉偏移影響做深入之探討。
推車實驗設計及規劃流程如圖5所示,實驗項目包括:
圖5 晶片推車實驗設計及規劃流程示意圖

(1)不同地板型式之孔洞地板、實心地板之比較差異,如圖6、圖7所示。
圖6 實心地板示意圖
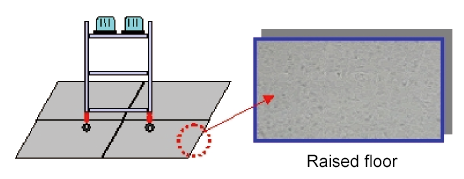
圖7 孔洞地板示意圖
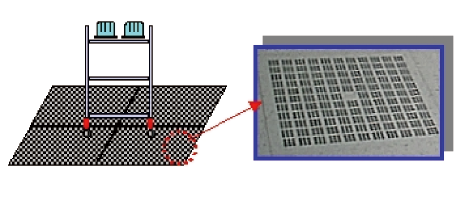
(2)推車輪胎尺寸大小之比較差異,如圖8、圖9所示。
圖8 推車硬性彈簧4吋輪胎示意圖
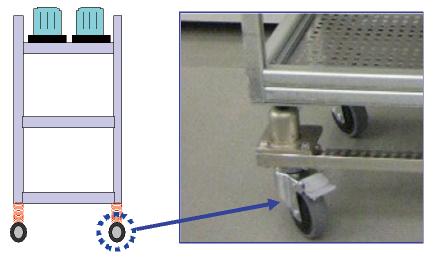
圖9 推車硬性彈簧6吋輪胎示意圖
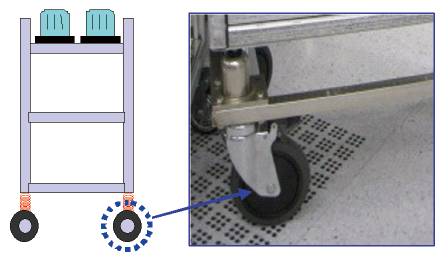
(3)推車輪胎無避震彈簧及加裝硬性彈簧之比較差異,如圖10、圖11所示。
圖10 推車無避震彈簧示意圖
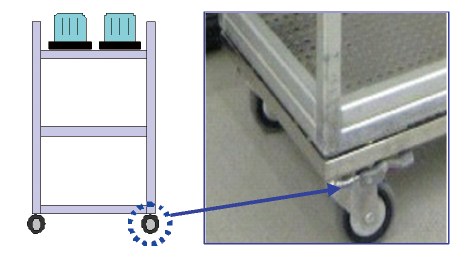
圖11 推車硬性避震彈簧示意圖
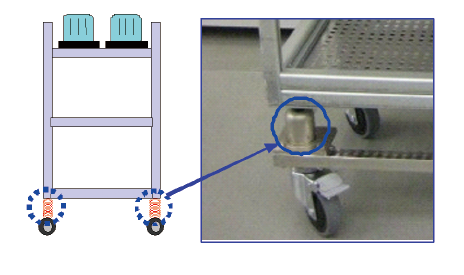
(4)推車硬性避震彈簧之平置放板與斜置放板比較,如圖12、圖13所示。
圖12 推車硬性避震彈簧之平置放板示意圖
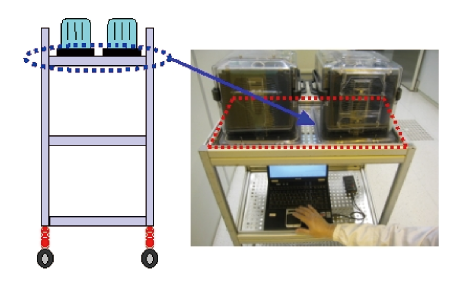
圖13 推車硬性避震彈簧之斜置放板示意圖
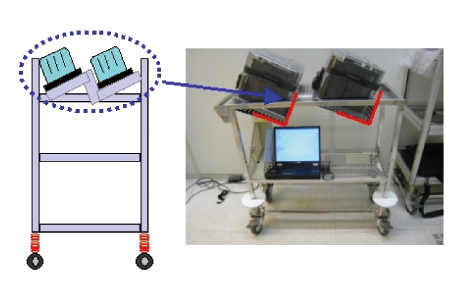
(5)推車軟性彈簧A、B型式之比較差異,如圖14、圖15所示。
圖14 推車軟性避震彈簧A示意圖
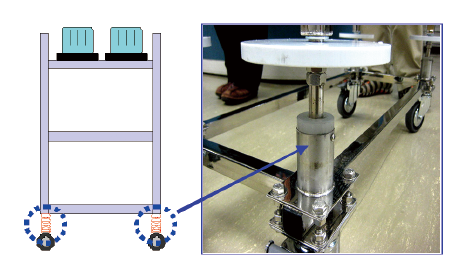
圖15 推車軟性避震彈簧B示意圖
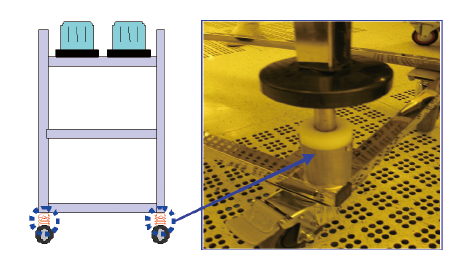
(6)晶片盒微震彈簧設計及試驗,如圖16所示。
圖16 晶片盒微震彈簧
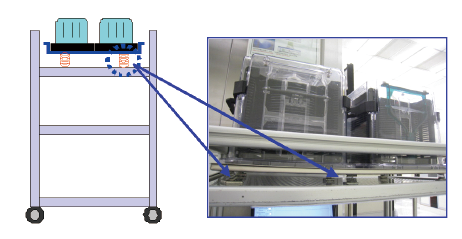
(7)圖17為推車改裝各種避震彈簧型式。
圖17 各種避震彈簧
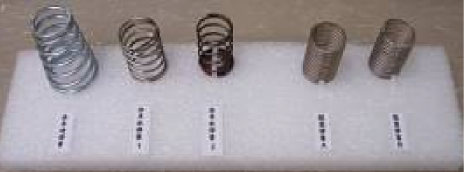
圖5為推車實驗設計及規劃流程示意圖,將本廠既有晶片推車行走於孔洞高架地板及實心地板,以量測在x, y, z三軸不同的震動值及Wafer旋轉偏移角度之大小。此外嘗試將推車改裝不同型式大小的輪徑(4、6吋輪胎)及不同的避震彈簧材質(無彈簧、硬性彈簧、軟性彈簧)做為推車震動改善,然其改善效果有限。
因此將推車機械結構做為設計改善,依簡諧運動方程式計算出該晶片推車最佳彈簧剛性係數及最佳彈簧撓曲度,開發設計「晶片盒微震彈簧推車」最佳化模組尺寸規格,並委請專業廠商依自行設計之圖面尺寸規格開模訂製“晶片盒微震彈簧推車原型機”。目前已完成2台晶片盒微震彈簧推車並請MFG、TE人員協助,於線上使用並驗證其改善成效。
實驗量測儀器
WaferSense AVS Sensor
本研究以實驗量測方法及使用專業量測Wafer震動精準儀器Wafersense AVS (Automatic Vibration System) 量測震動數據,如圖18所示,作為震動改善之參考值。震動實驗data之擷取係由通訊連結模組收集及儲存,與電腦連線傳輸距離100m範圍內,如圖19所示。透過個人電腦的軟體程式VibeView,可即時監測震動data值;此外,振動data並可與過去的data進行比對分析。
圖18 WaferSense AVS(Automatic Vibration System)

圖19 通訊連結模組擷取器
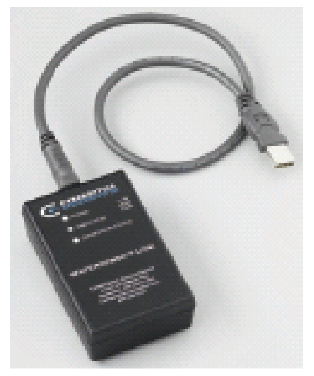
WaferSense AVS是一種無線傳輸的類晶圓加速度感測計,支援200 mm或300 mm晶圓,可直接放入POD中,如圖20所示。經半導體製程設備和自動化處理系統,其包括帶匣盒、SMIF和FOUP來觀察及監測x、y、z三軸的加速度(g = 9.8 m/s2)振動情況,準確量測Wafer在POD中震動狀況。測量範圍為±2g,能測量晶圓滑動、位移、撞擊、擦痕等相關震動狀況。
圖20 WaferSense AVS Sensor
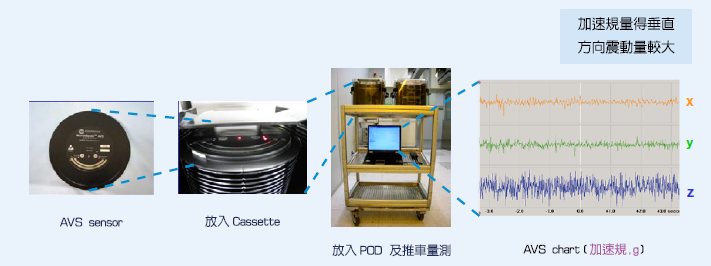
本實驗採用震動加速規(AVS)如圖20所示,此乃由於震動源係來自一外力,依據牛頓第二定律(F=ma)以量得的加速度來判別震動外力來源,若採速度規則無法觀察震動源之差異及方向。
實驗設計及震動量測手法
彈簧剛性係數計算
避震彈簧具有支稱推車重量並可緩衝路上之凹凸不平所導致車輪的上下震動,防止震動直接傳至推車並抑制車輪震動。因此本研究之避震彈簧係裝在推車底部與車輪之間,當車輪在通過路面不平處後,會有上下跳動現象之基本運動,以緩和推車所受之衝擊並迅速減弱其震動,所以施加荷重予避震彈簧後而發生撓曲,當負載解除後回復原狀態。此外,避震彈簧之功能亦保持輪胎與地面接觸,吸收車輪之跳動而不會傳至車身。
避震彈簧之上下端的荷重方向互為平行,當荷重方向正好與彈簧中心線成一致時其撓曲度 δ (Deflection)可寫成
撓曲度 [δ]
彈簧剛性係數(K)可由(2-1)得
彈簧剛性係數(K)
由方程式(2-1)與(2-2)可知荷重P與撓曲度 δ 變化位移成正比關係,亦即當彈簧受物質重量所施加最大荷重後壓縮而發生撓曲之變化位移求得彈簧剛性係數k值。
經由推車彈簧系統實驗量測與震動精準儀器分析結果,以各種可能影響Wafer notch shift之條件量測震動值之差異,並以不同k值之彈簧改善推車震動。壓縮彈簧之設計數據如圖21所示,除彈簧尺寸外,更需要計算出最大負荷及變位尺寸之負荷,以k表示,當彈簧被壓縮時,每增加1mm行程之負荷(kgf/mm)。
圖21 壓縮彈簧設計之示意圖
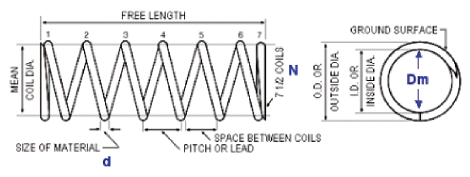
本廠既有推車硬性彈簧剛性係數總k值計算說明:
本廠既有推車軟性彈簧剛性係數總k值計算說明:
簡諧運動方程式
簡諧運動方程式之定義:當質量為M受到彈簧及阻尼的支配而運動時,這種運動即稱為簡單諧和運動(SHM),簡稱為簡諧運動,其簡諧運動方程式如(2-3)所示。
推車減震彈簧設計
針對本廠既有原型推車設計減震彈簧,如圖22所示,考量推車及POD總質量M較大(M=推車重量+POD重量=50kg),需剛性K值較大之硬性彈簧,具良好支撐性但減震效果差。而剛性K值較小之軟性彈簧,雖可改善Wafer震動及異音問題,卻另外衍生出推車明顯晃動或傾斜之其他問題。
圖22 推車減震彈簧之示意圖
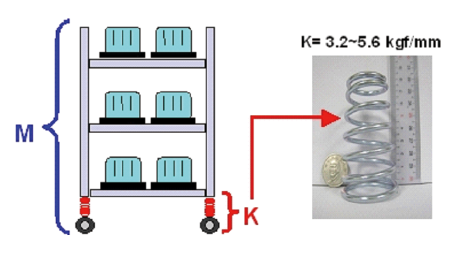
此外,本研究嘗試以阻尼C材質做震動改善,然而考量無塵室particle影響,微型阻尼特殊材質開發設計將增加開發設計與實驗成本費用而不符經濟效益。
晶片微震彈簧設計
推車減震彈簧設計僅具備整體推車總質量之良好支撐性但減震效果不佳。本研究之創新設計係將剛性係數k值小之晶片微震彈簧裝於平置放板,僅針對POD承載總質量m較小(m= POD重量=10kg),利用簡諧運動方程式計算出最佳剛性係數k值之晶片微震彈簧,不僅成功解決POD震動問題(包括Wafer notch旋轉偏移及particle汙染),並保留推車支撐性不致過度搖晃或傾斜,晶片微震彈簧設計如圖23所示。
圖23 晶片微震彈簧設計示意圖
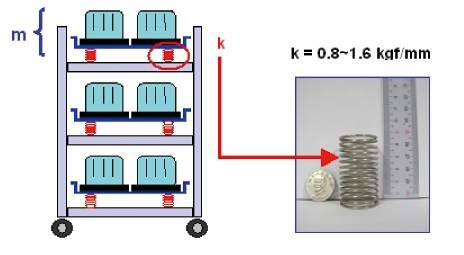
晶片微震彈簧之簡諧運動方程式可由(2-3)寫成
將晶片微震彈簧裝於平置放板以支稱POD穩定度,致使高度變高,考量推車每層容許高度範圍,在不影響人員運送推車之視野內,容許高度為50mm,扣除彈簧壓縮至底部所剩餘高度僅約1/2,經實驗量測觀察振幅及經驗公式得知彈簧最佳撓曲度範圍為50%,依簡諧運動方程式(2-4)針對POD重量僅10 kg,帶入方程式(2-2)以求得晶片微震彈簧A剛性係數總k值0.8,將其平均擺設於推車平置放板需16顆晶片微震彈簧以增加POD穩定度,因此單一晶片微震彈簧A剛性係數k值0.05帶入公式(2-2)求得線徑d=1.8。
(1)微震彈簧A剛性係數總k值計算說明:
(2)單一微震彈簧A線徑計算說明:
依設計圖面規格委廠商訂製線徑d=1.8之微震彈簧A及線徑d=2.1之微震彈簧B,經公式反推計算求得晶片微震彈簧B剛性係數k值0.1,其晶片微震彈簧B剛性係數總k值1.6,計算說明如下所示。
(3)單一微震彈簧B剛性係數計算說明:
結果
高架地板震動影響比較
以本廠既有推車配合震動精準儀器Wafersense AVS測量推車震動chart,經測量結果發現震動在z軸最為明顯,x、y軸影響較小,因此推車受z軸方向震動為關鍵真因。
圖24為實心板震動chart,圖面之橫座標為經過時間(單位Second),縱座標為震動波幅(單位g = 9.8 m/s2),可知在時間0 second之z軸震動值為1.07 g,然而本研究分析方法係以z軸穩定震動波幅Trend chart而非震動瞬時值,如圖示之紅線框範圍。因此實心板與孔洞板z軸震動波幅分別為± 0.89 g及± 0.97 g,無明顯差異,如圖24、25所示。
圖24 實心板推車震動 chart
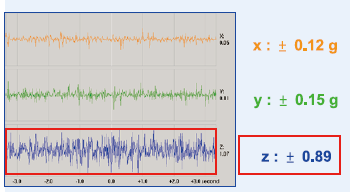
圖25 孔洞板推車震動 chart
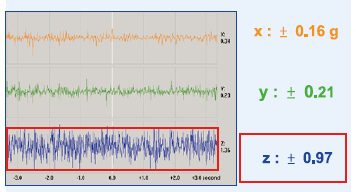
推車使用不同輪胎大小之震動比較
針對本廠既有原型推車係為無避震彈簧,將其推車震動chart做為Baseline data,其z軸震動波幅Trend chart震動值±1.1 g。當推車運送過程中,推車受到地面的震動及衝擊影響,其中一部份可藉由輪胎吸收。因此針對本廠既有4寸輪胎改裝為加大輪徑至6寸輪胎做實驗比較,然而經實驗分析結果發現,4寸輪胎z軸震動值為±0.97 g,Wafer有明顯震動及異音,其震動改善12%,Wafer notch偏移角度40°。
6寸輪胎z軸震動值±0.90 g,Wafer有明顯震動及異音,其震動改善僅18%,Wafer notch偏移角度35°,6寸輪胎之震動改善效果不明顯。
推車使用不同剛性係數彈簧之震動比較
推車輪胎雖然可吸收部分震動影響,但絕大部分仍需依靠輪胎與推車之間的懸吊裝置來吸收,因此本研究嘗試以各種不同剛性係數彈簧做實驗測試及歸納分析之減震設計,比較硬性與軟性減震彈簧之震動差異性。
硬彈簧剛性係數K=5.6有較佳之推車支撐性、車身不易搖晃等優點,然而Wafer有明顯震動及異音,震動chart為±0.97g,其震動改善12%,Wafer notch偏移角度40°。軟彈簧A剛性係數K=4.2係為剛性K值較小之軟性彈簧,對Wafer震動及異音雖可略為改善,其震動chart為±0.68g,震動改善38%,Wafer notch偏移角度20°,但卻衍生出推車明顯晃動或傾斜之其他問題,此乃由於軟性彈簧之剛性K值較小,無法承載推車與POD重量支撐力,導致車身會有明顯晃動或傾斜。
軟彈簧B剛性係數K=3.2係為剛性K值較小之軟性彈簧,對Wafer震動及異音雖有不錯之改善,其震動chart為±0.52g,震動改善僅53%,Wafer notch偏移角度17°,但卻導致推車晃動、傾斜愈加嚴重,推車及POD恐有翻覆之風險。
推車使用硬性避震彈簧之平置放板與斜置放板震動比較
為改善受z軸震動影響,推車經由改裝置放板傾斜,使其POD擺放傾斜23°,然而經實驗結果發現其Wafer震動異音略為改善,z軸震動chart為±0.77g,震動改善29%,且Wafer notch偏移角度為20°,震動改善效果有限。
晶片微震彈簧設計
考量推車及POD總質量較大,需剛性K值較大之避震彈簧,具良好支撐性但減震效果差;本研究之創新晶片減震設計“晶片盒微震彈簧”,將剛性係數k值小之避震彈簧,裝於置放層以達到減震效果並保留推車支撐性不致過度搖晃或傾斜。
推車使用晶片微震數彈簧之震動比較
晶片盒微震彈簧A剛性係數k=0.8,Wafer無任何震動異音、notch無偏移現象,z軸震動chart為±0.08g,震動改善高達92%,且Wafer notch偏移角度為0°,然而晶片盒卻有明顯晃動現象,此乃由於微震彈簧A剛性係數過小,無法承載POD重量支撐力,導致POD有明顯晃動。
晶片盒微震彈簧A剛性係數k=0.8雖具有最佳改善效果(震動改善高達92%、Wafer notch偏移角度為0°),具軸向支稱力,然而徑向支稱力不足,致使晶片盒有明顯晃動現象,因此嘗試以晶片盒微震彈簧B剛性係數k=1.6試驗。經實驗結果發現,Wafer無任何震動異音、notch無偏移現象及晶片盒不會過度晃動,z軸震動chart為±0.1g,其與晶片盒微震彈簧A震動量差異不大(±0.08g),震動改善高達90%,且Wafer notch偏移角度為0°。推車減震彈簧及微震彈簧設計之震動實驗改善如圖26所示。
圖26 推車減震彈簧及微震彈簧設計之震動實驗改善
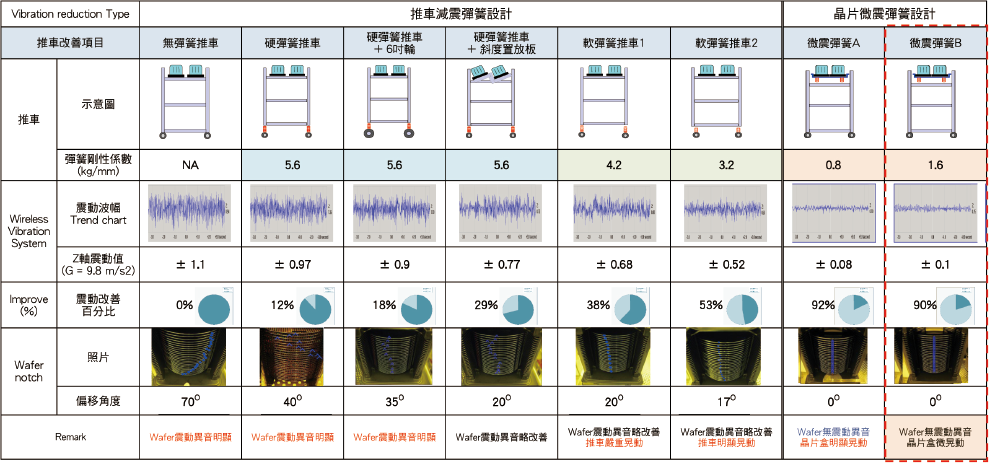
晶片盒微震彈簧推車承載測試
經實驗比較各種減震效果、晶片旋轉偏移及晶片盒晃動等因素,選擇適當剛性係數之晶片盒微震彈簧B(k=1.6 kgf/mm)為最佳改善設計,並將其研究成果驗證於新式晶片盒微震彈簧推車原型機,如圖27所示。各種承載負荷POD數量由輕載至滿載(1~6 POD),其中黃色POD為無線傳輸之類晶圓加速度感測計sensor,經實驗測試結果顯示,無論承載負荷之POD數量由輕載至滿載(1~6 POD),亦或類晶圓加速度感測計sensor擺設於推車各平置放層(上、中、下層),其震動改善成效均高達90%以上,Wafer notch改善效果100%無旋轉偏移及震動異音。此外晶片盒不會過度搖晃,亦解決晶片盒內Particle揚起而遭受塵埃微粒污染Wafer問題,不僅提高晶圓良率並大量節省成本支出,有效解決改善Wafer Scrap問題。
圖27 晶片盒微震彈簧推車原型機各種承載測試震動改善
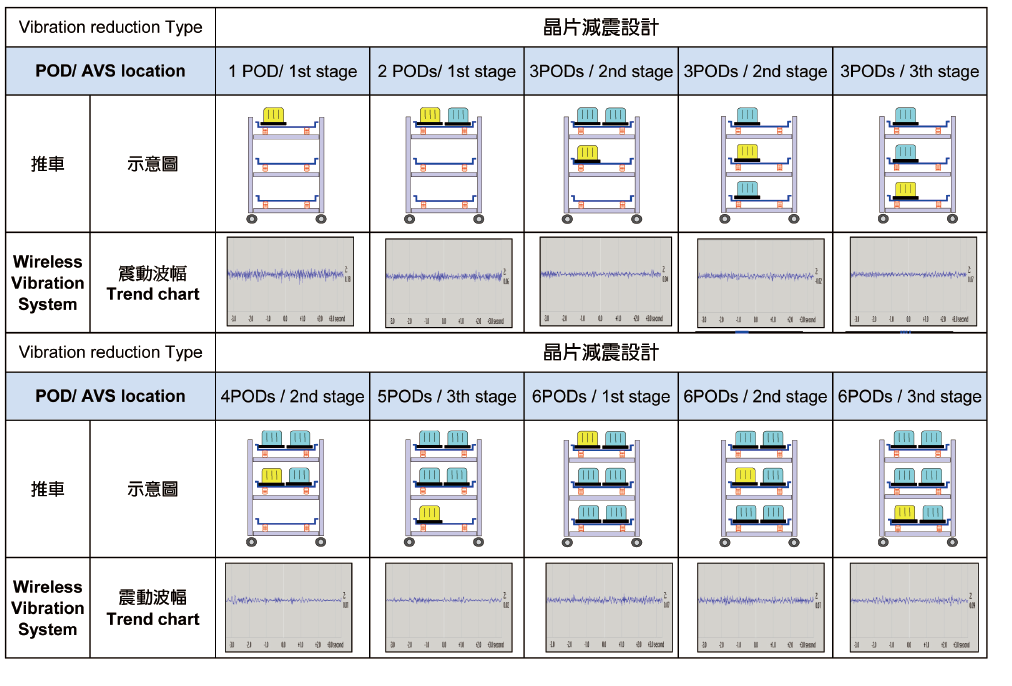
結論與建議 Conclusion
推車受到地面的震動及衝擊影響,其中一部份可藉由輪胎吸收,經實驗結果發現6寸較4寸輪胎之震動改善效果不明顯。推車輪胎雖然可吸收部分震動影響,但絕大部分仍需依靠輪胎與推車之間的懸吊裝置來吸收,因此本研究嘗試以各種不同剛性係數之彈簧做試驗,經分析結果發現彈簧的剛性k值越小,對Wafer震動影響越小。然而當彈簧剛性k值過小時,由於無法承受推車與Pod重量,導致彈簧被壓縮至底部而無避震效果。因此推車輪胎避震彈簧雖能改善對Wafer震動影響,然其改善效果有限。
本研究之創新晶片減震設計“晶片盒微震彈簧”,係將剛性係數k值小之避震彈簧,裝於置放層以達到減震效果並保留推車支撐性不致過度搖晃或傾斜。經由實驗比較各種減震效果、晶片旋轉偏移及晶片盒晃動等因素,選擇晶片盒微震彈簧B(k=1.6 kgf/mm)為最佳改善設計,並將其研究成果驗證於新式減震原型推車,各種承載負荷從1 POD至6 POD滿載,其震動改善成效均高達90%以上,改善效果不僅無任何震動異音且Wafer notch無偏移現象,此外晶片盒不會過度搖晃。
研究成果及實質效益
- 藉由本研究成果,震動改善成效高達90%以上,Wafer notch改善效果100%無旋轉偏移及震動異音。亦改善晶片盒內Particle揚起而遭受塵埃微粒污染Wafer問題,不僅提高晶圓良率並大量節省成本支出。
- 晶片微震彈簧裝置可以運用至其他承載減震設計,包括150 mm、200 mm及300 mm晶圓,如圖28所示。
圖28 晶片微震彈簧運用於其他承載減震設計
- 新開發設計之「晶片盒微震彈簧推車」最佳化模組尺寸規格,委請專業廠商依自行設計之圖面尺寸規格開模訂製“晶片盒微震彈簧推車原型機”。目前已完成2台晶片盒微震彈簧推車並請MFG、TE小組協助於線上使用,經長時間使用及測試後成效卓越,並有效解決舊有推車震動所帶來的不便及影響,深獲MFG、TE人員推崇及肯定。
- “晶片盒微震彈簧推車原型機”已通過專利,期許將此成功創新設計之晶片盒微震彈簧推車案例推廣至其他各廠區,並有效保護公司智慧財產權,以防止同業、製造廠商 (仿冒、COPY、OEM)等專利侵權問題。
- 三廠每年可減少百片的單片Scrap,全台積各廠可達千片以上,其經濟效益至少五千萬元台幣,目前已積極推廣至FAB2&5 MFG製造部使用。
- Fab3 EE&FAC Workshop成果發表會,榮獲最優案例頒發“貢獻獎”,並藉成果展現以擴大經驗交流及分享。
研發人力姓名 |
服務部門 |
職稱 |
參與計劃及工作項目之主要內容 |
---|---|---|---|
張智能 |
廠務部 |
部經理 |
統籌指導計劃進行、整體研究規劃、跨部門合作計劃協調、進度控制 |
徐岳聖 |
廠務部 |
副理 |
計劃管理、會議討論主持、實務規劃與製作技術指導、彈簧機構設計指導、協調小組成員 |
林嘉祺 |
廠務部 |
課長 |
實驗規劃、理論分析、實驗量測、功能測試技術指導、報告撰寫 |
黃俊銘 |
廠務部 |
課長 |
實驗規劃、推車原型機組裝技術指導、原型機功能測試 |
張家銘 |
製造部 |
課長 |
品質信賴性試驗、認證準備 |
蕭博戎 |
廠務部 |
工程師 |
文獻資料蒐集、實驗量測、理論分析、數據建檔及分析、報告撰寫 |
唐炳順 |
廠務部 |
工程師 |
文獻資料蒐集、實驗量測、推車原型機組裝 |
朱良堃 |
廠務部 |
工程師 |
實驗量測、推車原型機組裝、數據建檔及分析、報告撰寫 |
參考文獻
- 王文鴻,2001,可調式避震器設計分析與控制之研究,國立成功大學,碩士論文。
- 許自男,2005,汽車操控行為下之避震器阻尼分析,國立雲林科技大學,碩士論文。
- 張記函,2003,汽車懸吊避震器於規則路面之舒適性分析,國立雲林科技大學,碩士論文。
- 翁瑞侑,2008,彈簧及避震器對汽車乘坐振動之影響,南台科技大學,碩士論文。
- 汪國禎、許良明,2004,汽車學Ⅱ(底盤篇),復文書局。
- 張超群、張中明,2005,汽車乘坐振動之研究,第十三屆中華民國振動與噪音工程學術研討會。
- 賴耿陽,1995,汽車懸吊裝置總覽,復漢出版社。
- J. C. Dixon, 2007, The Shock Absorber Handbook, 2nd ed., Wiley.
- J. C. Dixon, 1996, Tires, Suspension and Handling, 2nd ed., SAE International.
- J. Reimpell, H. Stoll and J. W. Betzler, 2001, The Automotive Chassis: Engineering Principles, 2nd ed., SAE International.
- Philip M. Morse, 1981, Vibration & Sound, American Institute of Physics, New York.
留言(0)