摘要
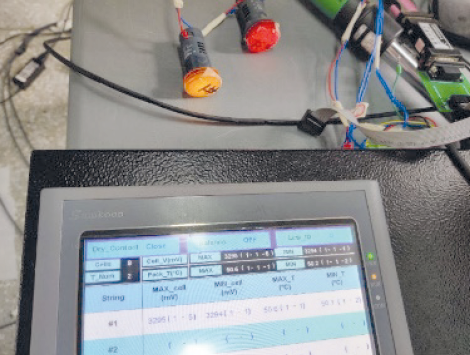
既設廠區UPS鉛酸汰換鋰鐵電池問題探討及改善對策
Keywords / Uninterruptible Power System(UPS)2,Lithium-Iron Phosphate Battery(LFP),Battery Management System(BMS)
For achieving green manufacturing mission. Lithium-iron Phosphate(LFP) batteries with batteries management system (BMS) adopted in UPS year by year in TSMC. Different form new plants, UPS modified by battery bank refit, add BMS and update UPS battery software setting in regular plants. The purpose is to provide improvement suggestions and follow-up engineering management methods for UPS equipped with LFP batteries in regular plants. This article also put forward issue discussions of current capacitance of discharge cable and wire connector were not meet discharge test criteria in PMO.I., self-discharge of LFP, accuracy of built-in thermometer. Finally, sharing evaluation method and engineering management method as a reference, to those who prepare to refit LFP batteries into UPS in regular fabs and achieve the goal of intelligent management.
前言
晶圓製造廠,對於供電品質要求甚高,為了供電穩定與電力品質,安裝不斷電系統(UPS),當市電壓降或是停電,UPS切換模式改由電池放電供應下游負載,已確保生產不中斷。
自啟用不斷電系統以來,除改善電池環境溫度、進行活化以延長鉛酸電池壽命外,公司亦評估鋰鐵電池導入的可能性。經過廠內驗證後,計劃逐步將鋰鐵電池導入新建廠區的不斷電系統,同時汰換既有廠區系統的鉛酸電池,以達到綠色製造、環境永續的承諾。
電池使用於UPS運轉多年可能因老化進入設備周期的磨損期,導致開路失效電池箱故障,進而使UPS失去備援供電能力[1]。
不同於新建廠電池櫃已導入鋰鐵電池,既設廠區需進行電池箱修改、新增電池管理系統(Battery Management System, BMS)、UPS電池電壓/充電電流等軟體設定等變更。因廠區正於鋰鐵電池導入初期,汰換工程後可能遇到電池溫度測試如何測、電池上線後因電池電壓不平衡使BMS警報觸發等問題。
本文提出一個針對既設廠區導入鋰鐵電池的管理方法流程,包含汰換前電池劣化評估方式以及導入鋰鐵電池工程之建議事項,以避免耗費人力在排除已知的疑慮。既有廠區汰換電池前,需針對電池進行放電測試,依電池健康狀態(State of Health, SOH),由最差至最好進行汰換之優先順序,以確保穩定運轉;針對導入鋰鐵電池工程從新增警報點、電池近料時間至上線啟用、增設警報硬體線、箱體改櫃、主機設定值設定、完工驗收及警報測試皆完整管理掌握,以提供即將導入的既設廠區作為參考。
文獻探討
2.1 鉛酸電池
是蓄電池的一種,電極主要由鉛製成,電解液是硫酸溶液的一種蓄電池。一般分為開口型電池及閥控型電池兩種。前者需要定期注酸維護,後者為免維護型蓄電池。俗稱的電瓶主要指的是鉛酸蓄電池。1859年法國物理學家普蘭特發明。其結構一般由正極板(二氧化鉛)、負極板(鉛)、隔板、電池槽、電解液和接線端子等部分組成。原理是通過將化學能和直流電能相互轉化,在放電後經充電後能復原,從而達到重複使用效果[2]。鉛蓄電池的電壓為2的倍數。
放電化學反應式 :
PbO2(s)+Pb(s)+2H2SO4(aq)→2PbSO4(s)+2H2O1 ..........(1)
充電化學反應式 :
2PbSO4(s)+2H2O1→PbO2(s)+Pb(s)+ 2H2SO4(aq) ..........(2)
2.2 鋰離子電池
是一種充電電池,它主要依靠鋰離子在正極和負極之間移動來工作。鋰離子電池使用一個嵌入的鋰化合物作為一個電極材料。目前用作鋰離子電池的正極材料主要常見的有:鋰鈷氧化物(LiCoO2)、錳酸鋰(LiMn2O4)、鎳酸鋰(LiNiO2)及磷酸鋰鐵(LiFePO4),這些鋰離子電池與其發展產品是在消費電子領域常見的。它們是可攜式電子設備中可充電電池最普遍的類型之一,具有高能量密度,無記憶效應,在不使用時只有緩慢電荷損失。除了消費類電子產品,越來越進步的鋰離子電池也越來越普及,可用於軍事,純電動汽車和航空航天應用[3]。例如,磷酸鋰鐵電池正在成為鉛酸蓄電池的一種常見的替代蓄電池,在歷史上鉛酸蓄電池用於車輛、不斷電系統等,但這種高效的新型電池已經能夠突破舊有鋰電池與鉛酸電池的各種缺點,達成全面替代的目標。鋰離子電池也由三個部分組成 : 正極、負極和電解質[4]。
正極半反應式 :
Li1-xCoO2+xLi++xe-↔LiCoO2 ..........(3)
負極半反應式 :
xLiC6↔xLi++xe-+xC6 ..........(4)
2.3 電池管理系統
電池管理系統(Battery Management System, BMS)是對電池進行管理的系統,通常具有量測電池電壓的功能,防止或避免電池過放電、過充電、過溫度等異常狀況出現。隨著技術發展,已經逐漸增加許多功能。[5]對象通常是可再次充電的二次電池,近年來大多搭配鋰離子電池組同時出現。
以下列出目前已知的常見功能,包含電壓量測(必備)、通訊、SoC(State of Charge)估算、SoH估算、異常告警、異常保護、均衡(被動均衡或主動均衡)、其他管控電路(如電池迴路繼電器控制)、溫度量測、電流測量、診斷、搭配充電器提供對應充電策略[6]。
2.4 電池健康狀態
電池的健康狀態(State of Health, SOH)的想法是把電池的新品當做100%健康的狀態,隨著電池循環充放電的使用,電池的容量與性能會逐漸的劣化,所以SOH的預估值就會由100%逐漸下降,最終到SOH=0%代表完全無法使用。但一般電動車不會等到電池完全無法放電時才更換電池,因此一種SOH的指示方式是當SOH低於一個門檻值(一般設定為60%),則警示使用者需儘早更換電池[7]。
造成電池健康劣化的因素,並非同樣的充放電參數(如充電電壓、充電電流等)都適用所有電芯。每種電芯都應有一套屬於自己的最佳充放電參數,及其對應的操作電壓、充放電速率,與過充或過放電之電壓區間範圍。
2.5 電池評估方法
2.5.1 廠牌放電曲線差異性
電池製造商[8][9]提供新品電池的放電曲線(測試條件 : 1C,終止條件 : 截止電壓達10.8V)如 圖1(a) 圖1(b),發現同樣放電時間下,不同電池型號截止電壓結果不同。汰換時需考量廠牌間放電截止電壓差異性。本文將電池新品1C放電曲線回歸成電池健康度曲線如 圖2(a) 圖2(b),以電池健康度對應電池電壓,以消除電池型號的差異性。
圖1(a)、新品電池放電曲線(CSB GPL 121000)

圖1(b)、新品電池放電曲線(YUASA NPA125)
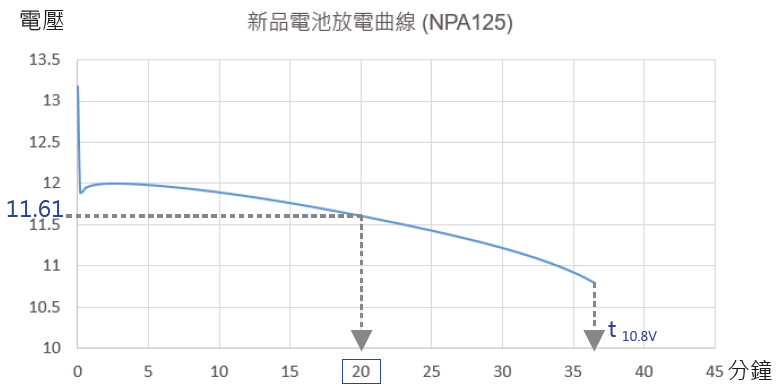
圖2(a)、電池健康狀態對應廠牌電壓值(CSB GPL121000)
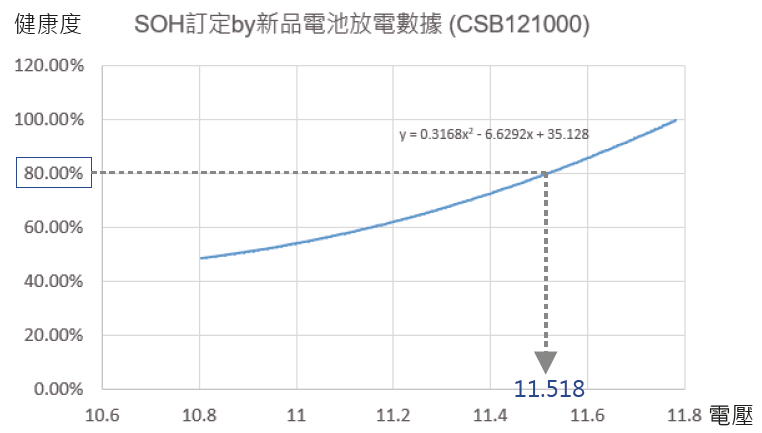
圖2(b)、電池健康狀態對應廠牌電壓值(YUASA NPA125)
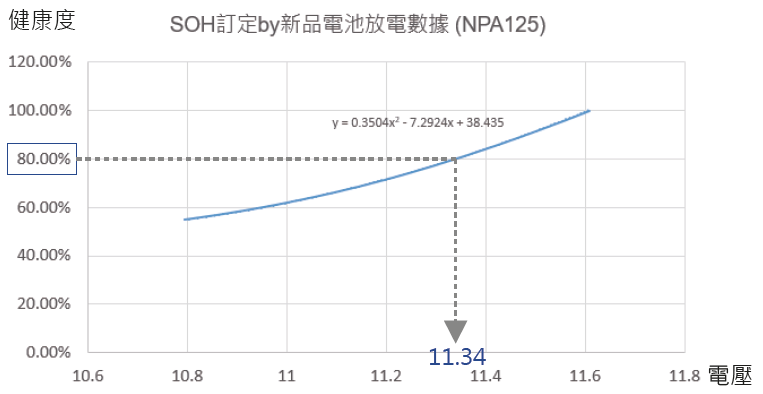
2.5.2 數據分析模式
文獻[10]利用大數據管理概念,使用數據母體取得放電前後電壓差分布趨勢,用以判斷電池健康度。並於結果說明電池充電狀況影響此手法的準確性,即放電保養前,飽電與否會影響初始電壓與截止電壓的量測值。本文使用去年放電紀錄之數據,建立電池汰換模型,用以推估電池健康度,作為UPS汰換鋰鐵電池之優先排序的依據。
2.6 精實思維的概念
2.6.1 精實生產
豐田汽車建立一套豐田生產模式(Toyata Production System, TPS),強調持續不斷的改善,生產及裝備製程的即時化(Just in Time, JIT)[11],在製造過程中就把產品做的最好的自動化方法,豐田透過此方法,來達到品質管控以及成本的下降。TPS的核心精神為精實生產(Lean production),主要是透過創新的思維與方法,結合需求來消除浪費並持續改善,以滿足需求並創造企業的價值,達到永續經營。
2.6.2 精實思維的演進
實行精實除了生產方法外,還補充了管理手法,將原本僅用於生產,擴充到整體企業的生產經營活動,使其更全面。精實製造、精實企業體、精實整合、精實文化、精實組織等。因此,精實體系越趨完善,此精實思維不僅用於製造業,其系統化變為一種管理模式,導入精實生產的各種管理方式、改善品質的流程精進手法[12]。
2.7 精實六標準差與DMAIC
2.7.1 精實六標準差
六標準差即品質管理概念[13],而精實目標為生產作業管理,整合兩者,圖3即為精實六標準差(Lean six sigma)。能用來有效解決與處理浪費、無附加價值工作時間,去除流程中的浪費,提高作業效率。
圖3、精實目標與六標準差目標
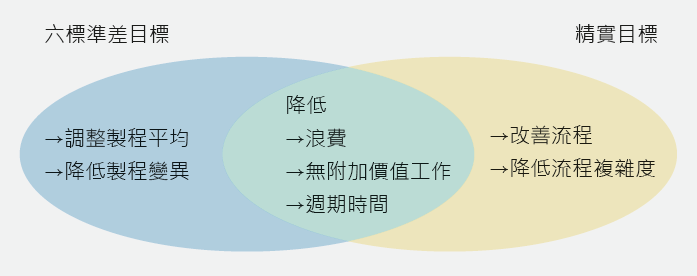
2.7.2 DMAIC模型
六標準差方法,改善手法模型定義為下列五步驟[14] :
- 界定(Define) : 制定目標,界定具體活動問題描述與專案範圍,於範圍裡釐清關鍵品質指標並進行改善活動。
- 衡量(Measure) : 採取評量方法,依照不同需求設定目標,對流程進行品管水準的衡量。
- 分析(Analysis) : 了解錯誤發生的真因,可用因果圖、FMEA等方法分析真正的原因。
- 改善(Improve) : 透過改善方案,去除或修正流程錯誤,評估個方案的成效,建構最佳的流程運作模式。
- 控制(Control) : 目的在落實改善後的新流程,管制策略。使流程的錯誤不再發生或降至最少,並實施標準化及建立標準作業程序。
計畫/研究方法
進行電池汰換前,其關鍵第一步為評估電池健康狀態,用以作為依據找出需被汰換的目標電池櫃;接著運用上述精實管理手法及模型,找出可調整或移除程序,改善後將其作業流程標準化。我們可以利用原先鉛酸電池更換程序,再納入鋰鐵電池需新增的工項,利用DMAIC模型由工程範圍界定、衡量施作流程水準、分析錯誤原因、評估成效改善流程、管理改善後流程建立標準程序等五項目,找出錯誤流程及影響汰換作業的關鍵因子,落實管理策略,維持工程品質。
除了超前佈署淘汰即將異常的電池,同時達到鋰鐵電池帶來的綠色製造及智能管理的效益。
3.1 電池更換現況
3.1.1 電池健康狀態評估
電池更換前的前置作業極為重要,即電池劣化程度評估,本文利用數據分析及消除廠牌差異後的電池健康度,來決定更換對象及優先排序。
3.1.2 鉛酸電池更換作業
鉛酸電池更換作業依序為,電池劣化評估、選定對象及優先排序、電池進料、施工前現場預置、斷電後電池拆卸、新電池上架、訊號及電源結線、定磅後畫線、電壓量測、開關復歸及環境整潔等步驟。
上述作業,鉛酸電池更換示意圖如 圖4所示,整櫃汰換或年度保養中電池放電結果不符合鉛酸電池放電保養之PMO.I.規範[15],即鉛酸電池以2C/5分鐘或1C/20分鐘放電基準,放電後截止電壓<10.8V時,皆會進行此更換作業,工程師與廠商執行上可說是相當熟悉。
圖4、鉛酸電池更換示意圖
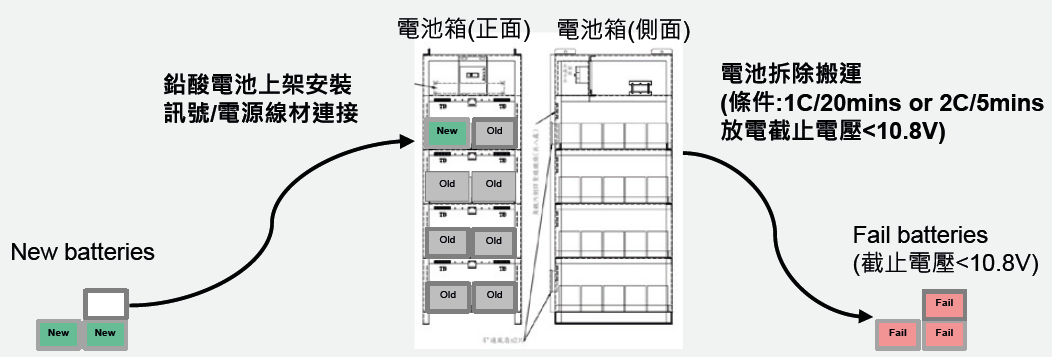
3.1.3 鉛酸電池汰換鋰鐵電池新增作業
圖5為鉛酸汰換鋰鐵電池示意圖,既設廠區欲進行鉛酸汰換鋰鐵電池作業,除原本電池更換作業項目外,需安排以下作業,包含BMS定位及固定、新增BMS、新增硬體通訊線至BMS、增加CT及防震固定架料等工項,及盤體修改之外的前置SCADA新增警報、修改UPS軟體設定。
圖5、鉛酸汰換鋰鐵電池示意圖
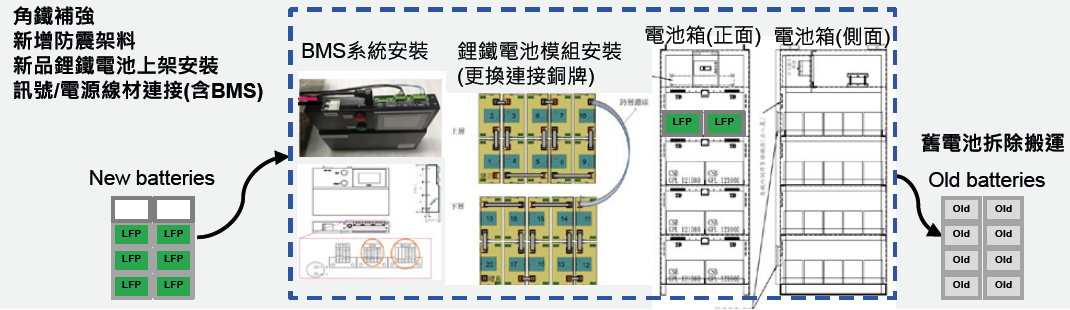
施作完成送電後,工程師需執行以下兩項目,BMS警報測試及UPS充電機啟動進行電池充電。以上施作完畢後,鋰鐵電池正式上線。
上述作業,自2019年開始陸續有廠區進行鉛酸電池汰換鋰鐵電池工程,於鋰鐵電池導入初期,現場施作工法的確認及作業流程未建立完整,既設廠區初期可能會花費大量時間在討論及現場問題解決上,過程中發現問題於下章節探討。
3.2 DMAIC架構應用
本研究目標在於改善汰換績效,即施工效率,重點著重於UPS鋰鐵電池汰換流程,運用精實六標準差的DMAIC步驟搭配各項方法,找出關鍵影響因子,即關鍵程序輸入變數(Key Process input Variable, KPIV)。以「系統穩定」、「工程師管理」為出發點,找出影響此滿意程度的關鍵品質特性(Critical to Quality, CTQ),訂定此專案的關鍵績效指標(Key Performance Variable, KPI),即關鍵程序輸出變數(Key Process output Variable, KPIV),模型架構如 圖6。
圖6、電池汰換流程架構應用

3.2.1 界定(Define)
本案例績效目標(KPI)為汰換作業效率的提升。圖7為鉛酸汰換鋰鐵電池作業流程圖,扣除評估階段,共有5個階段,其中三個階段為UPS升級鋰鐵電池的新增流程,分別為新電池安裝、UPS上電後設定、電池櫃投入確認,皆有時間浪費的可能性,而施作錯誤則可能在任何一個階段發生,皆會影響施作效率。其中施作錯誤不一定會發生,但發生必定嚴重影響效率。作業效率表示如下 :
圖7、由鉛酸汰換鋰鐵電池作業花費時間階段定義
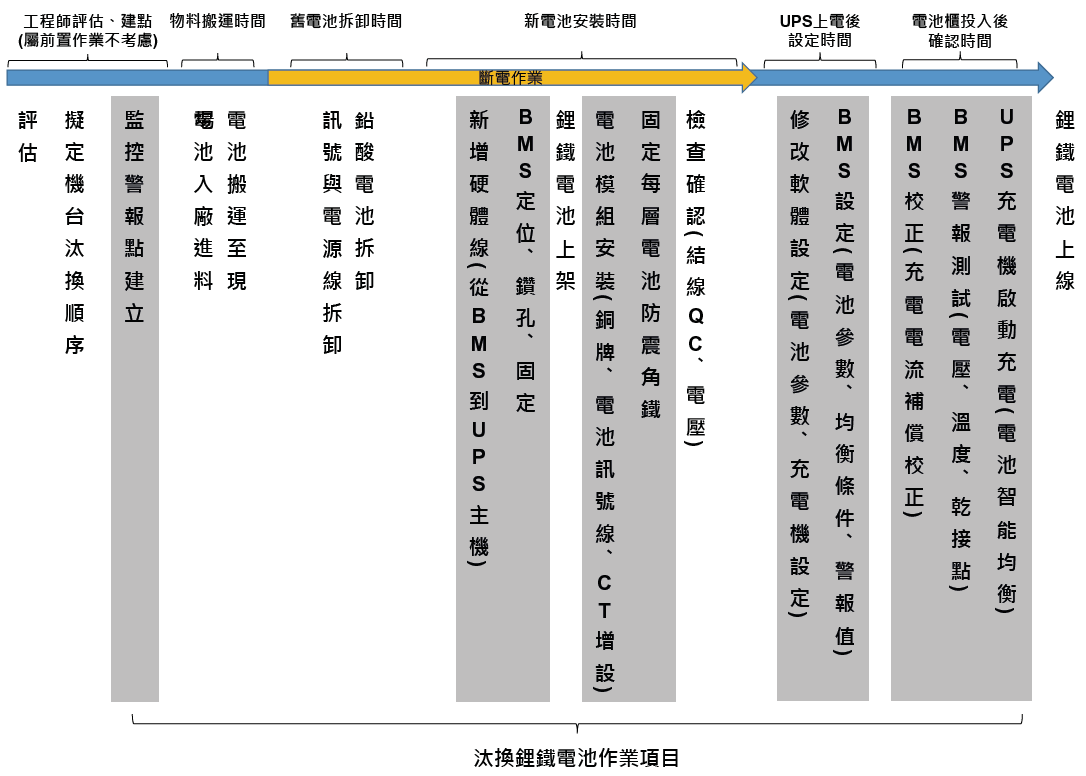
..........(5)
其中,TStandard標準作業時間;TActual實際作業時間;Terror施作錯誤時間。
3.2.2 衡量(Measure)
透過量測流程效率的方式,從 圖8得知,取前10次汰換鋰鐵電池實例,看出施作效率不穩定性,且有三台UPS施作效率低於85%,分別為82%、71%及74%,皆因Terror即施作錯誤時間發生,使總施作時間增加造成時間浪費。如 表1透過流程展開圖(Process Mapping)的方式,找出評量汰換作業耗時影響關鍵輸入因子(X΄s),篩選出真正影響的關鍵因素,縮小研究範圍。廠商群菱於施作流程中,占了四個時間階段,分別為電池搬運、拆卸電池、電池箱改櫃及鋰鐵電池安裝。本文由此範圍(T1~T4)著手。
圖8、改善前-第1~10台UPS汰換鋰鐵電池施作效率
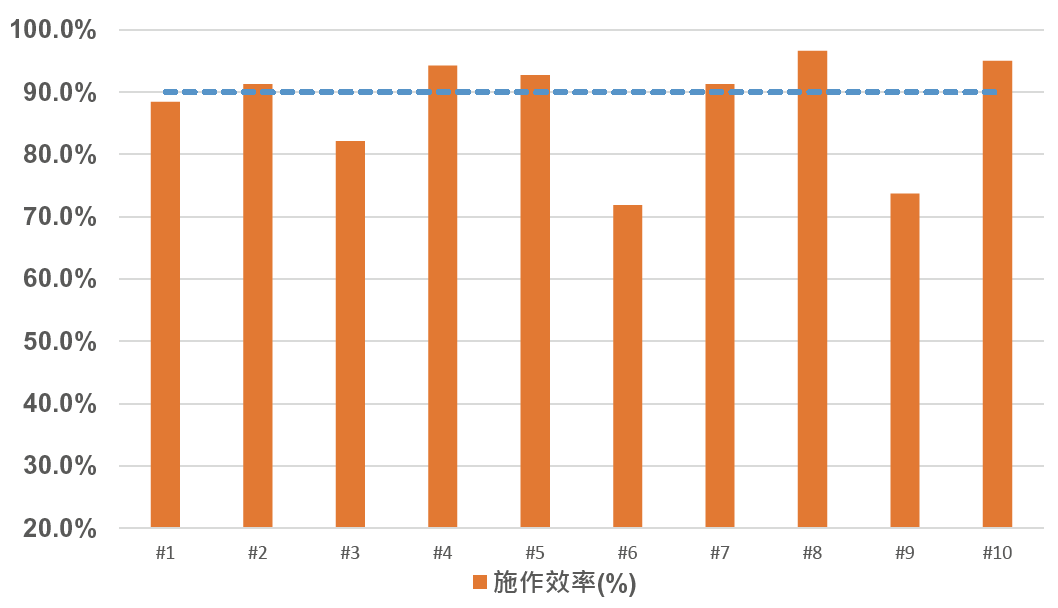
Vendor | Input | Process Step | Output |
---|---|---|---|
群菱 | 鋰鐵電池、油壓板車 | 電池入料、搬運 | T1 |
群菱 | 絕緣工具 | 電池拆卸、訊號電源線拆卸 | T2 |
群菱 | 洗孔器、軍刀、 Fuse、BMS、線材 | 電池箱改櫃、BMS增設 | T3 |
群菱 | 絕緣工具、鋰鐵電池霍爾環(CT)、線材、 電池銅牌 | 電池安裝、訊號電源線安裝 | T4 |
伊頓 儲盈 |
UPS軟體參數、 BMS參數 |
UPS設定、BMS設定 | T5 |
儲盈 | BMS參數 | BMS校正、警報測試 電池智能均衡 | T6 |
3.2.3 分析(Analysis)
此階段,目的要了解造成問題的關鍵因素,分析汰換效率降低的變異來源。首先拆解汰換流程各占耗時,如 圖9。本案例以2020年F15A施作Eaton 450kVA(人力為群菱4名、伊頓1名、儲盈1名)鉛酸汰換鋰鐵電池作業首次施作為例。由各工項耗時T1~T6中,從X΄s初步獲得範圍縮小至T1~T4,即為電池搬運(T1)、電池拆卸(T2)、BMS安裝(T3)及電池安裝(T4),分析各階段耗時變異量(ΔT1~ΔT4)。
圖9、改善前-各工項時間耗費時程圖

以 圖10,前10次汰換鋰鐵電池工程時間為例,發生Terror的3個施作案例(#3、#6、#9),皆有工程耗時變異量明顯上升,其中ΔT1~ΔT4最大差值分別為0.2、0.8、1.65、1.2小時。首先,檢視Terror發生原因為首要改善目標,其中原因有洗孔器頭斷裂、線材銅牌備料不足、Day one電池櫃凹陷導致電池安裝工法變更(①擺放位置與結線改變②新增線材);再來為針對耗時差值較大的項目,電池拆卸(ΔT2=0.8hours)、BMS安裝(ΔT3=1.65hours)及電池安裝(ΔT4=1.2hours),其中ΔT2影響因子為電池櫃靠牆面、電池櫃走道窄小;ΔT3影響因子為UPS主機不鄰靠電池櫃、電池櫃位置分散;ΔT4影響因子與ΔT2相同,為施作走道空間窄小、電池櫃靠牆面導致施作時間拉長。如 圖9發現,BMS安裝(T3)與電池安裝(T4)可以同步施作,亦為可改善的目標之一。
圖10、改善前-第1~10台UPS各工項時間耗時

3.2.4 改善(Improve)
已知Terror發生的原因後,便要採取行動策略,如備妥手工具的備品、前一周將銅牌線材於廠內備齊並清點等。由拆解工項耗時的可能範圍ΔT2~ΔT4,分析原因得知電池櫃靠牆(僅正面可進行拆裝電池)、走道窄小(改由手推車搬運電池)、櫃體位置分散(BMS訊號線加線走線槽入櫃體及櫃體開孔)等,這幾點為既設盤體及位置現況,透過前一日現勘施作UPS主機位置及電池櫃環境,先行準備材料及提早掌握即將發生的工項,減少工程不確定性。改善的面向著重於工作流程的合理性及明確細分。BMS安裝(T3)與電池安裝(T4)兩工項經審視流程合理性,妥善配置後可同時施作。
改善後,各時間階段的工項耗費時程圖,如 圖11。過去因分工較不明確,再銜接流程時易產生缺失,新的做法將步驟確認與各廠商討論後,得以使施作人員快速正確的執行工作流程。
圖11、改善後-各工項時間耗費時程圖

針對上述輸入目標進行改善,這邊將現場施工內容程序化,如 表2鋰鐵電池更換作業程序檢查表,明定各階段工作區間,該階段包含之廠商執行工作細項與規範。依檢查表單順序施作。
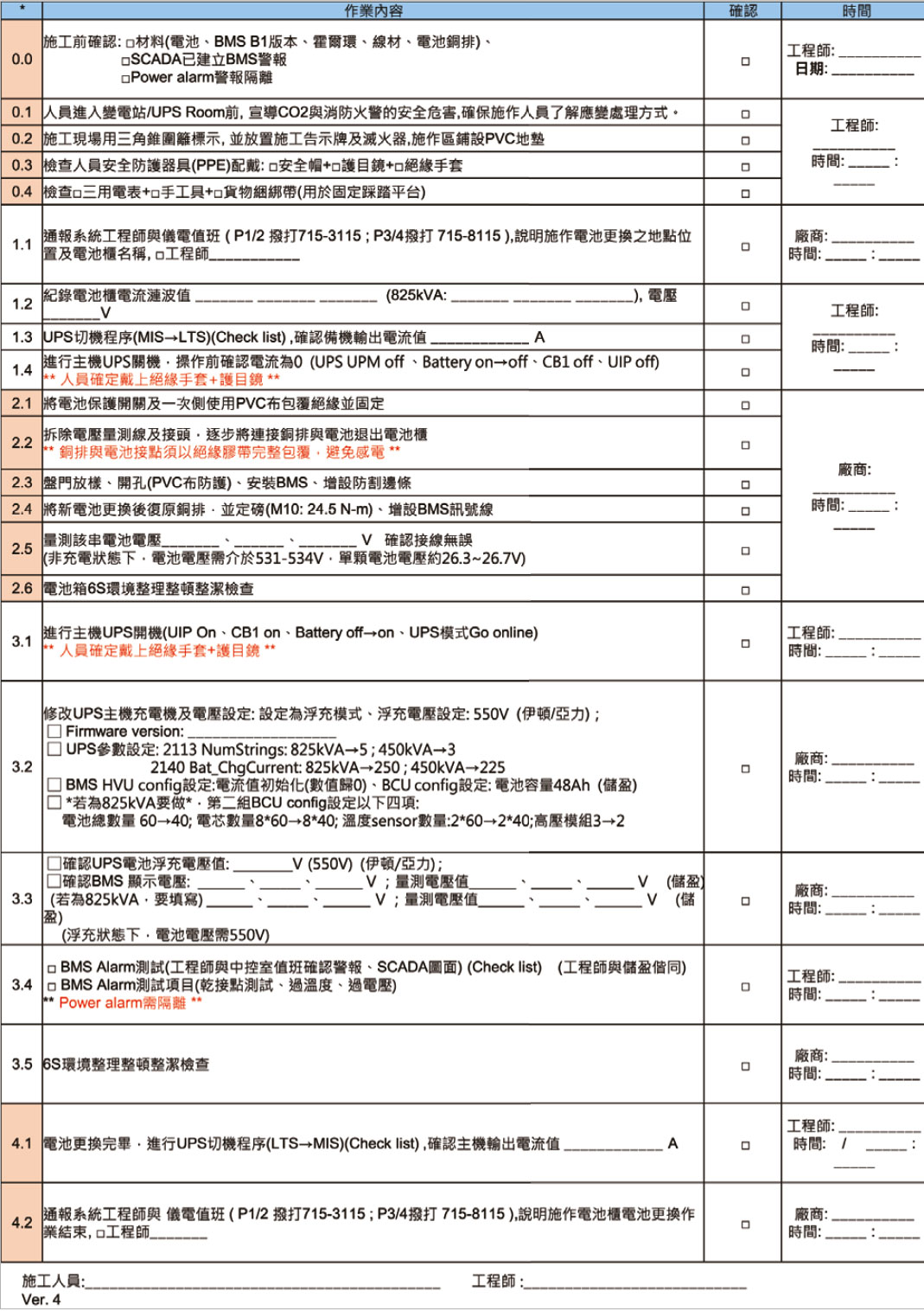
3.2.5 控制(Control)
透過排除異常及施工流程的改善,必須經由改善前後的比較分析,了解方法是否有效。目的在落實改善後新流程及管制策略。使流程的錯誤不再發生或降至最少,並實施標準化及建立標準作業程序,提升汰換作業效率。
精實六標準差(Lean six sigma)關鍵在於降低工程程序變異及消除無附加價值的工項,使績效指標即汰換作業效率趨於穩定。
改善後進行UPS鉛酸汰換鋰鐵電池工程共16台,蒐集資料後與改善前經驗做比較。如 表3,改善目標BMS安裝(T3)與電池安裝(T4)平均耗時改善率分別為32.7%、35.8%,表示改善成效顯著。
電池搬運 | 電池拆卸 | BMS安裝 | 電池安裝 | 軟體、BMS設定 | BMS校正 | |
---|---|---|---|---|---|---|
改善前 | 0.53 | 1.51 | 1.80 | 1.72 | 0.58 | 0.57 |
改善後 | 0.52 | 1.30 | 1.35 | 1.26 | 0.51 | 0.50 |
差異 | 0.01 | 0.21 | 0.44 | 0.45 | 0.07 | 0.07 |
改善率 | 1.8% | 15.8% | 32.7% | 35.8% | 13.2% | 14.7% |
標準差亦為工程耗時的指標之一,用以評估施作耗時的穩定性,越低表示同項目施作耗時變動偏移越小,如 表4所示,BMS安裝(T3)與電池安裝(T4)耗時標準差,從0.465、0.368降低至0.096、0.113,表示施作耗時偏移量降低。
電池搬運 | 電池拆卸 | BMS安裝 | 電池安裝 | 軟體、BMS設定 | BMS校正 | |
---|---|---|---|---|---|---|
改善前 | 0.072 | 0.244 | 0.465 | 0.368 | 0.127 | 0.114 |
改善後 | 0.063 | 0.168 | 0.096 | 0.113 | 0.05 | 0.046 |
本次例績效目標(KPI)為汰換作業效率,改善後成果如 圖12,其16台施作效率皆高於92%,其原因有二,第一為盡可能排除Terror、第二為標準化程序後各工項耗時變量降低,使得施作鉛酸汰換鋰鐵電池工程穩定性提高。
圖12、改善後-第11~26台UPS汰換鋰鐵電池施作效率
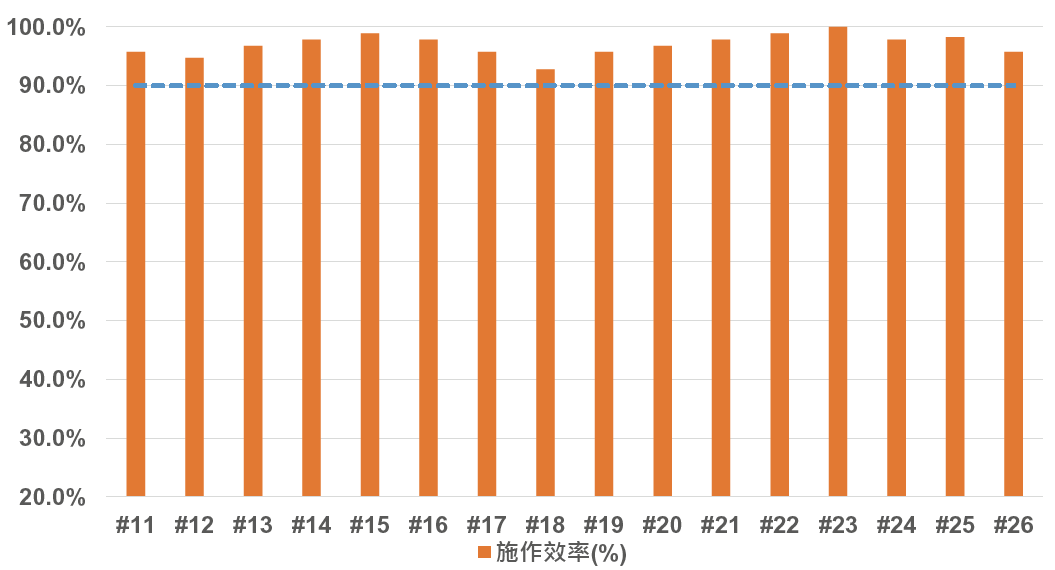
智能均衡充電若因為電池放置過久,會導致工程師需頻繁至現場操作充電機啟動,造成額外人力付出,進行Eaton機種韌體更新,可解決此問題。
結果與分析
4.1 效益
利用DMAIC模型,依步驟拆解並找出關鍵因子,完成標準化程序使工項更加清晰透明之外,亦可降低因不熟悉造成的現場的施作變因。如上章節呈現,使本次績效指標即汰換效率提高且趨於穩定,提升工程管理的品質。
如 表5,考量人力配置、施作UPS容量等條件,進行作業程序的優化評估使用,各工項耗時供大家參考。
人力 | UPS容量 | 搬運 | 電池拆卸 | BMS安裝 | 電池安裝 | 軟體、BMS設定 | 校正 |
---|---|---|---|---|---|---|---|
4 | 450 | 0.5hr | 1~1.5hr | 1.5hr | 1~2hr | 0.5hr | 0.5hr |
4 | 825 | 1hrs | 2~2.5hr | 2~2.5hr | 2~3hr | 0.5hr | 0.5hr |
4 | 450(CR) | 1.5~2hr | 1~1.5hr | 1.5hr | 1~2hr | 0.5hr | 0.5hr |
4 | 825(CR) | 2~3hr | 2~2.5hr | 2~2.5hr | 2~3hr | 0.5hr | 0.5hr |
6 | 450 | 0.5hr | 0.5~1hr | 1hr | 1~1.5hr | 0.5hr | 0.5hr |
6 | 825 | 1hr | 1~1.5hr | 1.5~2hr | 1.5~2.5hr | 0.5hr | 0.5hr |
6 | 450(CR) | 1~2hr | 0.5~1hr | 1hr | 1~1.5hr | 0.5hr | 0.5hr |
6 | 825(CR) | 1~2hr | 1~1.5hr | 1.5~2hr | 1.5~2.5hr | 0.5hr | 0.5hr |
4.2 標準化流程管理圖(含考慮因素)
以F15A為案例,利用DMAIC模型,既設廠區鉛酸汰換鋰鐵電池標準化流程如 圖13所示。
圖13、由鉛酸汰換鋰鐵電池流程圖
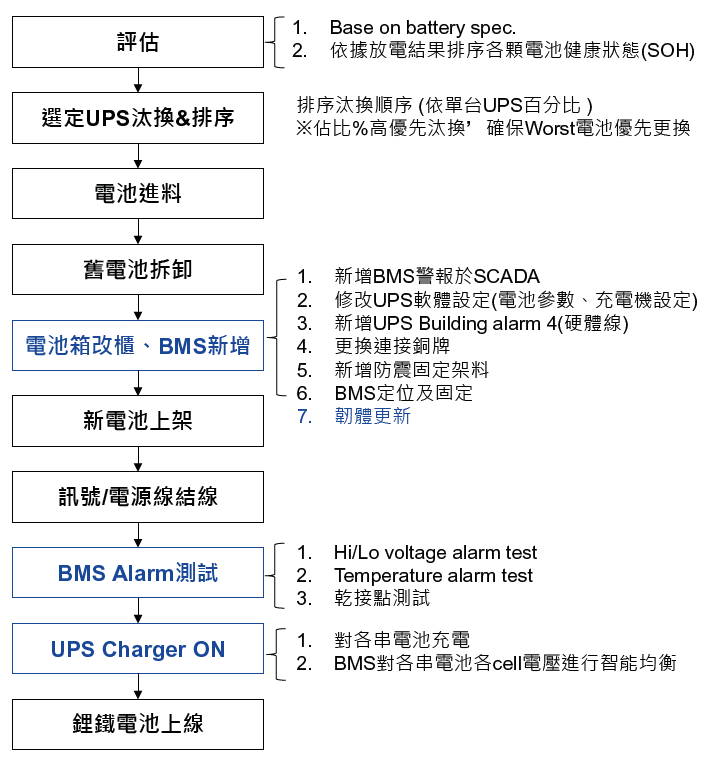
4.3 問題點改善與建議
鉛酸電池汰換鋰鐵工程中發現問題點與建議如下 :
4.3.1 電池內溫度計未測試過精度
請廠商儲盈進行電池溫昇實驗,取一鋰鐵電池模組(型號TW-BP-2450A)於高溫烘箱、烘箱由常溫升溫至80°C,當超過70°C告警溫度,確認BMS乾接點狀態轉為常開(Close→Open),其中電池內溫測器拉出裸露於,與溫度槍溫度進行比較,如 圖14~圖16。
圖14、溫度槍量測

圖15、電池內溫測器溫度顯示

圖16、乾接點狀態確認
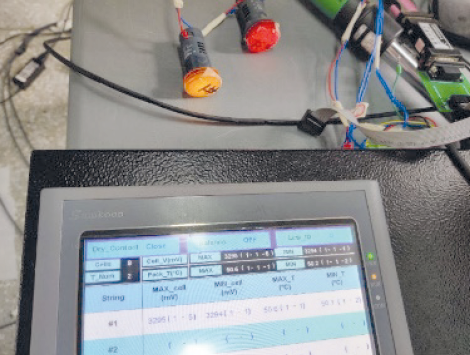
如 圖17,電池溫昇實驗曲線結果顯示,可看出電池內溫測器與溫度槍的溫度讀值有一致性,電池內溫測器精準度完成驗證。
圖17、電池溫昇曲線
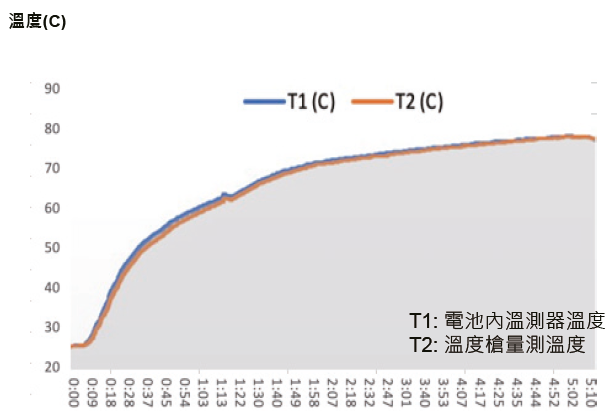
4.3.2 鋰鐵電池上線後因電池電壓不平衡使BMS警報觸發
電池上線前會經過靜置時間,BMS會進行智能均衡的功能進行電池均壓。上線後會因電壓不平衡導致告警發出,待告警解除後須手動啟動充電。
實驗為靜置六周的單串共20顆電池(共160個cells),剛上線狀態,電芯電壓平衡狀態及電芯電壓分布如 圖18 圖19,可看出電壓未平衡(3.3612V~3.4409V)且電壓值分布發散。此情況就容易造成單顆電芯電壓高觸發BMS警報,充電機被關閉。
圖18、電芯電壓平衡狀態(充電第一天-電壓不平衡)
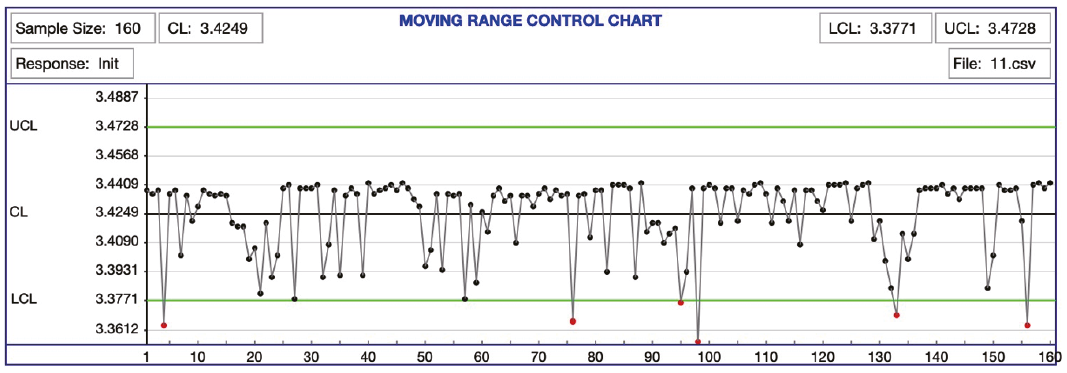
圖19、電芯電壓分布(充電第一天-電壓不平衡)

經過三天智能充電後,如 圖20 圖21所示,電壓均衡(3.4320V~3.4331V)且電壓分布集中。
圖20、電芯電壓平衡狀態(充電第三天-電芯電壓均衡)
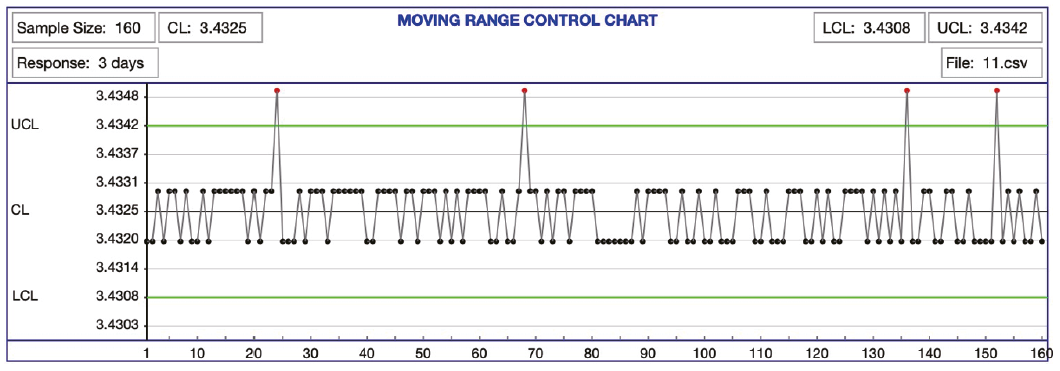
圖21、電芯電壓分布(充電第三天-電芯電壓均衡)
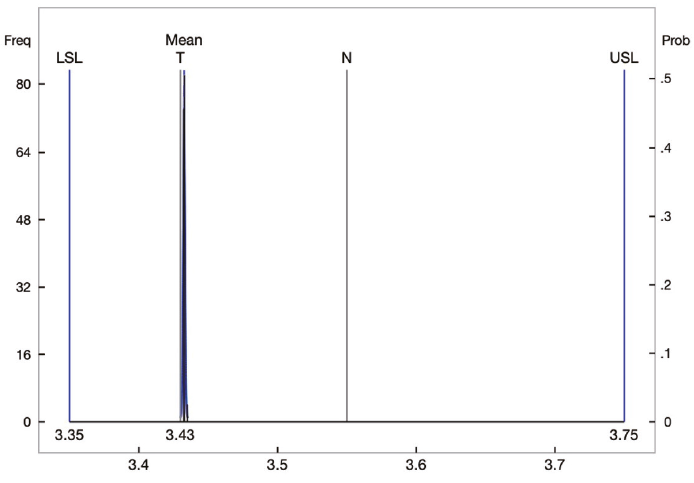
建議如下 :
- 選用出廠批號相近之電池,避免新舊電池混搭造成充電電流不平均
- 電池入廠後一個月內上線→降低電池電壓不平衡發生(減少至現場Charger ON次數)
- 若為Eaton 9395 UPS,可進行韌體更新(3.06.100)以後之版本,已通過FRC及伊頓廠驗,具備BMS告警解除自動Charger ON的功能
4.3.3 部分廠區放電線耐電流無法滿足PMOI鋰鐵電池放電規格(6C/5分鐘,即300A/5分鐘)
經調查部分廠區電池櫃放電線為UPS放電線為海巴龍38mm2(耐電流210A),無法滿足現行使用之鋰鐵電池(50AH)之PMOI放電規格6C/5分鐘(即300A/5分鐘)。
建議更換為海巴隆100mm2(耐電流350A,滿足6C放電 : 300A)。
4.3.4 825kVA未移除第六櫃電池櫃警報導致發出close battery switchgear與漣波電流異常警報
Eaton 9395 UPS容量825kVA進行鋰鐵電池更新時,由6櫃改5櫃,屆時亞力/伊頓人員需要將此兩警報從第六櫃移除,避免誤告警發出。
4.3.5 若BMS兩台以上Alarm NC接點並接導致無法發出任何告警
若UPS升級鋰鐵電池工程,鋰鐵電池超過60顆,則使用到兩台BMS,必須將Battery Alarm為NC接點進UPS Building Alarm,且需要串接,如 圖22(a) 圖22(b)。若並接會無法收到任何告警。
圖22(a)、Battery Alarm NC接點串接(BMS)
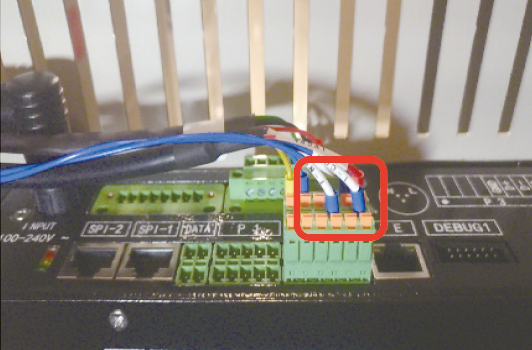
圖22(a)、Battery Alarm NC接點串接(BMS)
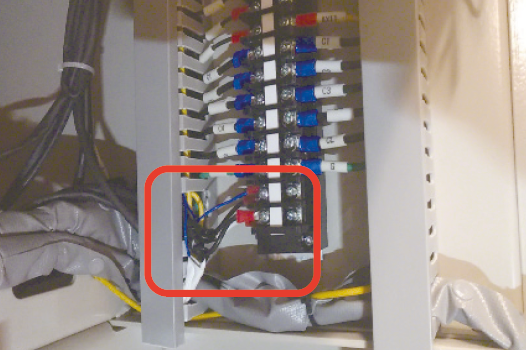
未來展望與結論
5.1 過程發現及印證
透過DMAIC模型逐步拆解作業程序,確實有效的降低鋰鐵電池汰換作業耗時。依此成效可更有效預估2021年汰換作業的時程及評估。
同時過程中完成了電池溫度計驗證的問題、施工品質的控管改善、解決放電線不符規格等問題。
而自動充電韌體更新之前,建議電池入廠後一個月內完成汰換,降低電池空置的時間,降低工程師置現場啟動充電機的人力損耗。
5.2 建議
流程優化除了要考量作業耗時外,亦可再考慮 ①施工環境 ②一周廠商人員工作量分配 ③計畫排程以及 ④工程師人力成本。本文提供方法供大家參考,透過模型拆解細項,可應用於各廠區不同的條件施工條件、環境及廠商派工人力等。
5.3 未來目標
本文應用於既設廠區鉛酸汰換鋰鐵電池作業中,其方法與廠區常用之專案管理手法PDCA相同,是一個持續改善的過程,期望透過提出DMIAC方法,不局限於作業程序優化上,可用於其他專案及應用上,增加廠務系統管理的工具。
參考文獻
- 昭松科技股份有限公司,UPS未做定期維護保養案例。
- 黃俊誠、陳藹然,高瞻自然科學教學資源平台,鉛蓄電池(Lead-acid Battery)。
- Ballon, Massie Santos. Electrovaya, Tata Motors to make electric Indica. cleantech.com. 14 October 2008.
- Lithium Ion technical handbook, Gold Peak Industries Ltd. November 2003.
- Yevgen Barsukov, Jinrong Qian, Battery Power Management for Portable Devices, 2017.
- 許家興,車輛測試中心ARTC,電動車成敗的關鍵技術-電池管理系統,2011。
- 孫建中、許盈晧、周俊宏、林炳明,工研院材化所,電池健康狀態估測技術簡介,工業材料雜誌340期,2015。
- CSB Energy Technology Co, https://www.csb-battery.com/
- Taiwan Yuasa Battery Co. ,http://www.yuasa.com.tw/
- 嚴逸帆,不斷電系統電池異常即早維修保養判斷方法,tsmc廠務季刊Vol.34, 第86-94頁,2019。
- 陳元愷,豐田模式應用於高爾夫球具產業之研究,國立中山大學管理學院高階經營碩士學程在職專班碩士論文。
- James P. Womack, Daniel T. Jones, Lean Thinking, 1996.
- 楊舜龍,成功推動精實六標準差創造高績效營運個案研究,國立交通大學高階主管管理學程碩士班碩士論文。
- Peter Pande, Robert Neuman, Roland Cavanagh, The Six Sigma Way, 2000.
- 台灣積體電路製造股份有限公司,F-CEC-02-03-008 300MM FAC UPS P.M.O.I.
留言(0)