摘要
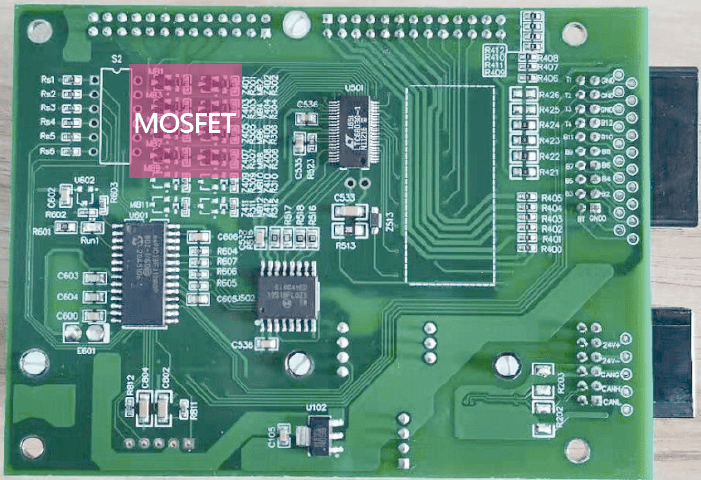
The process of wafer semiconductor will continue to be advance by Moore's Law. The power supply quality of equipment is becoming more and more rigorous standards, and the number of high-power uninterruptible power systems(UPS) has also increased. Presently, the traditionally configured lead-acid battery of UPS has no effective management mechanism for a single battery or a cell. There is a potential risk of leakage and explosion. Multiple problems make replace of lead-acid battery with LPF. The LPF with BMS is be safety monitored and managed. Through a balanced control circuit adjust the battery voltage level, and BMS returns abnormal messages to SCADA. According to the above functions of BMS, it not only improve efficiency but extend life of the battery.
前言
1.1 鋰鐵電池導入
基於安全、環保、使用年限及維護議題,鋰鐵電池漸漸取代鉛酸電池於市場的地位,其特性表現都優於鉛酸電池。各區廠務不斷電系統(UPS)紛紛開始安排導入或汰換,鋰鐵電池相較鉛酸電池除了較為安全優勢外,使用壽命也較長久,相對降低人力維護成本,如 表1。
項目 | 鉛酸電池 | 鋰鐵電池 |
---|---|---|
安全 | 漏液、爆炸等熱失控疑慮 | 鋰鐵材料無爆炸、熱失控等風險 |
環保 | 高重金屬汙染 | 材料可分解回收,無重金屬汙染 |
壽命 | 充放電循環次數低,更換電 池頻率高 | 充放電循環次數高,降低電池更 換頻率 |
維護 | 每年需進行電池放電測試、內阻量測,人力費用/維護 成本高 | 每三年進行電池放電測試,確認電池狀況節省花費成本 |
管理 | 無法即時偵測電池狀況(電 壓/溫度等) | 主動平衡電池芯電壓,線上偵測 電池狀態,讀取即時相關參數 |
效能 | 充電時間長、自放電率高, 放電容量低 | 充電時間短、自放電率低,放電 容量高 |
空間 | 低能量密度,佔用空間大 | 高能量密度,空間利用率高 |
由於電池在製造時,無法百分之百確保各電池內容物之化學特性及容量一致,長期使用下也無法確保每顆電池芯內阻及容量衰減程度相同,數顆電池串聯長期充放電時,將導致電池容量高之電芯會先達到充電截止電壓(Over Charge),電池容量低之電芯會先到達放電截止電壓(Over Discharge)問題。為避免電池串中任何一電芯有過充或過放情況,BMS將會使該串電池停止充放電,因此該串部分電芯容量將有未充飽或未放盡之情況,如 圖1。長期運轉將造成電池容量下降、壽命減短等問題產生,因此如何進行電芯電壓管理是一重要的課題,透過BMS的加入顯得格外重要。
圖1、(a)電池芯充電平衡/不平衡(過壓) (b)電池芯放電平衡/不平衡(低壓)
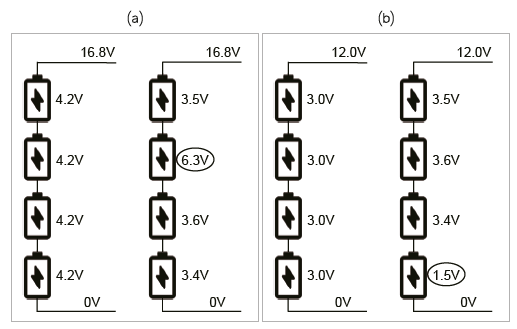
1.2 廠內鋰鐵電池運轉現況
BMS主要用來監控與管理電池模組,並提供預警保護的功能。透過均衡控制電路平衡電池芯之間電壓壓差,經系統內部通訊將電池芯電壓資訊、電池組充電和放電電流及溫度完整記錄,基於這些資訊的收集,不僅可以使電池安全運行,而且可以進行電池電量狀態(State of Charge, SOC)和健康狀態(State of Health, SOH)計算,對電池的容量與性能皆有參考價值。統計廠區易造成BMS告警為過壓告警,最常發生於 ①UPS新裝機時,因電池在組裝過程中沒有充電,電池本身自放電將會造成電壓分佈不均 ②因每顆電池容量製造無法完美一致,電池經放電測試後,將導致電壓分佈不均。綜合上述狀況當UPS充電機開啟對電池進行充電時,原先電池芯較高電壓透過BMS均衡電路調整電池電芯電壓,若電池異常過壓則UPS充電機立即停止充電,確保電池組及系統安全,將異常事件紀錄並回傳SCADA告警,使系統建立一個安全有效率的管理方式。[1]
1.3 廠內鋰鐵電池管理面臨之問題
鋰鐵電池在運轉管理上重要任務之一就是電池芯充放電管理,初期管理設計當電池芯電壓超過均衡電壓時啟動「均衡控制電路」,方法就是把高準位電芯電壓透過平衡電阻放電。長時間下雖然全數電池芯電壓符合告警範圍內,但電池芯電壓準位分佈不均,電池組內部電壓差異性大,於大功率放電易造成電池壽命減短與損壞。
1.4 鋰鐵電池強化管理之方式
導入BMS電池智能均衡管理模式,有效改善上述問題與強化電池使用年限。電池芯高準位電壓透過平衡電阻強制放電,使電壓準位向下調整。若偵測到低準位電壓將啟動充電機對低電壓電芯進行充電。經過反覆的充放電運作,將大大提高電池芯電壓一致性,詳細內容將會於第三節進行介紹。
文獻探討
2.1 鋰鐵電池介紹
全世界儲能系統種類繁多,大至抽蓄水力電廠、儲能貨櫃和超級電容等,小至生活周遭處處可見的電池。以目前電池發展而言,鋰電池最具有成長性,眾多的電池種類需因材適用,而鋰電池最大優勢就是能量密度高,製造成本隨著市場的需求效應而不斷下降,是目前應用最多的電池種類,也是未來最具有發展性電池之一,許多不斷電系統設備更紛紛導入使用。
2.2 電池管理系統介紹
達維德-安德烈亞(Davide Andrea)著作的「Battery Management Systems for Large Lithium-Ion Battery Packs」[2]提到,BMS主要的功能是讓所有電池組的電池芯確保在其安全工作區域(State of Aging, SOA)中。BMS功能沒有絕對的定義,廣義上的需求為電池保護量測(Measurement)、電量估算(Analysis)、電池性能最佳化管理(Management)、外部設備通訊(Communications)與電池監視(Logging&Telemetry)等技術,其基礎架構如 圖2所示。
圖2、BMS功能架構
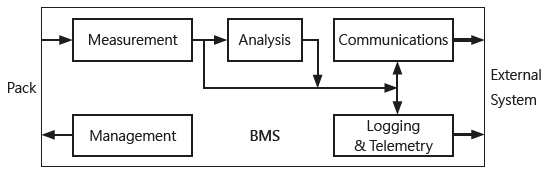
- Measurement
電池電壓、電池電流、電池溫度。 - Management
State of aging(SOA)、電池芯電壓平衡、電池溫度。 - Analysis
State of charge(SOC)、Depth of discharge(DOD)、State of health(SOH)、電池容量、電池內阻。 - Communications
典型的BMS通訊架構,使用CAN bus溝通內部資訊,並透過通訊模組將結果傳送至外部SCADA,如 圖3 BMS通訊架構。圖3、BMS通訊架構
- Logging & Telemetry
記錄電池各項資訊、健康狀態、錯誤訊息及告警。
目前未有明確的標準規範來訂定BMS的產品安全設計,大多參考通用的電子設備功能安全標準,例如 : 國際電工委員會(International Electrotechnical Commission, IEC)及美國保險商實驗室(Underwriters Laboratories Inc., UL)的IEC/UL60730-1準則。內容主要評估規範電子控制裝置的安全,為BMS安全設計提供了一個生命周期的理念,涵蓋功能性及安全方面開發設計、製造驗證及實際應用整體過程,目的為保障鋰鐵電池及BMS的安全與強健性[3][4]。
至於如何設計出一套對電池最佳化的控制技術,則是各家電池製造商參考此規範標準下,集眾知識研發的重要關鍵。
2.3 電芯電壓均衡原理
當充電機對一整串電池進行充電如 圖4(a),可觀察到最高電池芯電壓為4.1V,此時充電機將持續充電,當該顆最高電芯電壓為4.2V時,BMS判斷電芯過壓,將使充電機關閉如圖4(b),待該顆電芯透過平衡電阻放電,電壓低於過充電壓設定值時,充電機再開啟對該串電池進行充電如 圖4(c),待下次有電芯過壓時又重覆此步驟如 圖4(d)、圖4(e),最終達到每顆電芯電壓一致性如 圖4(f)。
圖4、BMS對電池均衡動作原理
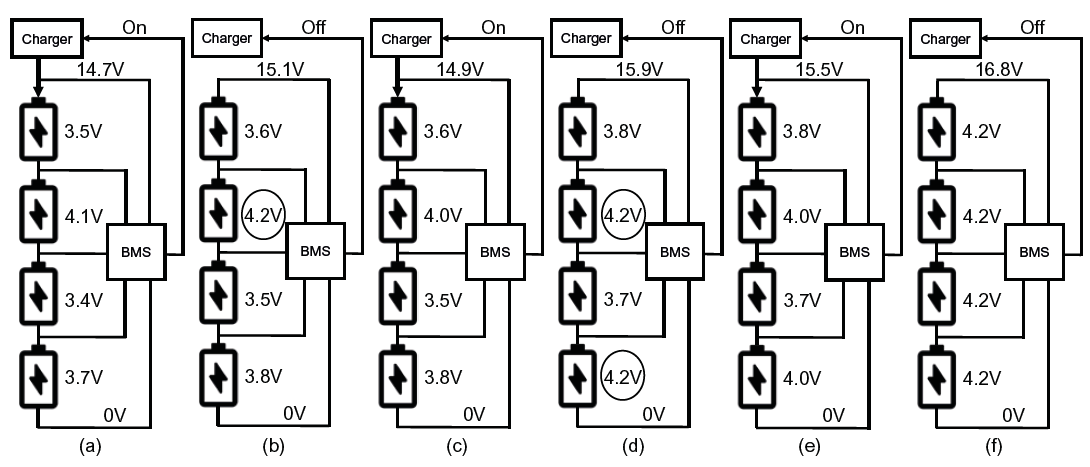
研究方法
3.1 廠區電池管理運轉架構
F15B廠區UPS配置鋰鐵電池運轉,由四大部分構成,如 圖5所示 ①UPS主機 ②鋰鐵電池 ③BMS電池管理系統 ④SCADA監控系統。其中BMS電池管理系統架構簡述,於BMS中的電池控制單元(Battery Control Unit, BCU)與電池中的電池管理單元BMU(Battery Management Unit, BMU)透過CAN Bus溝通,為主從式(Master-Slave)的架構。BCU是BMS的大腦核心,負責進行電池組運轉管理,透過RS485通訊傳輸訊號至HMI與SCADA供使用者監視與分析。電池模組內的每顆電池芯則是透過BMU來偵測其電壓與電池極柱溫度,再經由CAN Bus對BCU來傳遞該串數顆電池資訊[5]。
圖5、廠區BMS系統運轉架構
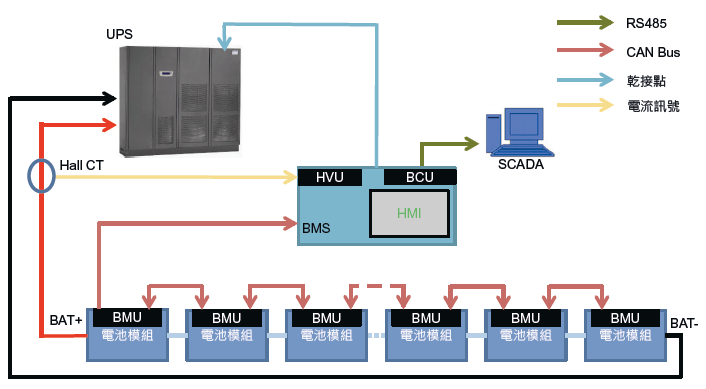
BMS偵測電池本體電芯電壓 ①當偵測值高於上限設定值,電芯電壓將透過平衡電阻進行放電程序或觸發BMS內部繼電器乾接點訊號關閉充電機 ②當偵測值低於下限設定值,BMS判斷電芯電壓異常,同樣迫使UPS關閉充電機,停止對電池充電。上述功能除了保護電池本體,也可提高系統安全性。
3.2 BMS傳統均衡電路
目前廠內UPS充電機對電池組充電電壓為550V,對每串20顆電池共160個電池芯(1顆電池內有8個電池芯)進行充電,理想上每個電芯電壓應為550/160=3437.5mV,但由於每顆電芯特性些許不一,電芯電壓會高於或低於理想值。
每顆電池組內部皆有嵌入一BMU均衡電路如 圖6,其中每顆電池內有8顆電芯,每個電芯將分別與1個平衡電阻並聯,其平衡電阻規格為5W 8Ω。
圖6、電池BMU平衡電阻
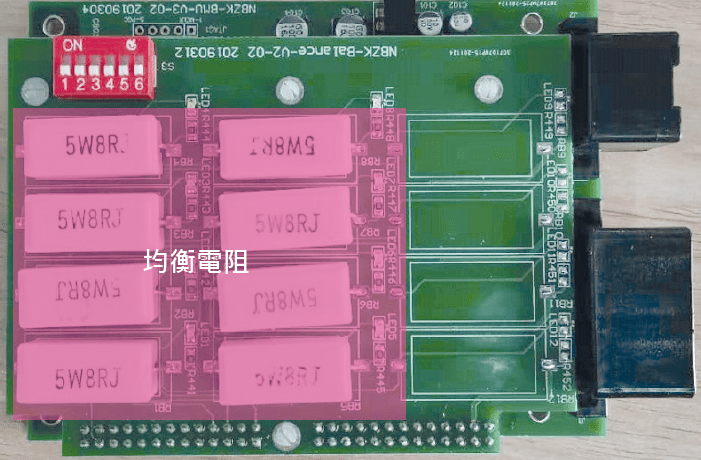
表2為均衡電路動作相關設定值,BMS設定當偵測電芯電壓高於傳統均衡電壓設定值3443mV時,將透過BMU觸發安裝於均衡電路板MOSFET開關導通如 圖7,使電芯並聯平衡電阻進行放電,達到抑制過壓效果。
項目 | 內容 | 描述 | 電壓(mV) |
---|---|---|---|
1 | 傳統均衡電壓 | 電芯電壓高於此電壓時,將進行電芯放電 | 3443 |
2 | 充電截止電壓 | 電芯電壓高於此電壓時,UPS將關閉充電機 | 3750 |
3 | 過充回復電壓 | 電芯電壓低於此電壓時,UPS將開啟充電機 | 3443 |
4 | 放電截止電壓 | 電芯電壓低於此電壓時,UPS將關閉充電 | 2000 |
圖7、電池BMU MOSFET電路
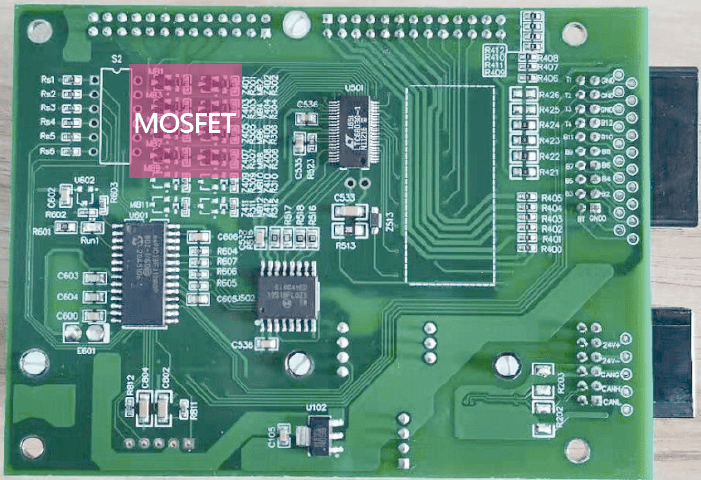
當電芯電壓未達充電截止電壓設定值3750mV時,UPS充電機依然對整串電池充電,此時若UPS對電芯充電速率大於平衡電阻對電芯放電速率時,電芯電壓將高於3750mV,BMS將會觸發內部繼電器乾接點訊號斷開並發出過壓告警,使UPS關閉充電機不再對電池充電,電芯進而持續透過平衡電阻持續放電至低於過充回復電壓設定值3443mV時,繼電器乾接點訊號閉合,UPS開啟充電機重新對電池充電。
其上述電芯均衡流程如 圖8所示,雖然進行反覆充放電過程,但最終還是將會發生電芯電壓不均情況。
圖8、單一電池芯過壓均衡流程
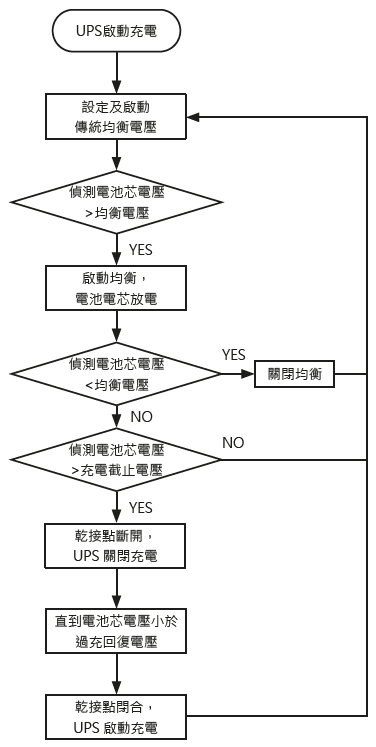
當充電機若正常對電芯充電時,若電芯電壓低於放電截止電壓設定值2000mV時,BMS也會觸發內部繼電器乾接點訊號斷開,使UPS關閉充電機不再對電池充電,此時將需檢查電池電芯狀況,其流程如 圖9所示。
圖9、單一電池芯低壓判斷流程
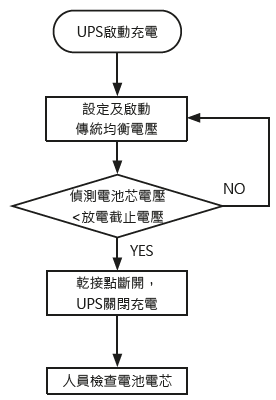
3.3 BMS智能均衡電路
3.2節所討論為BMS對電芯過壓管理問題,以及若電芯電壓低於放電截止電壓設定值2000mV異常狀況。其中BMS於電芯過壓管理上存在一問題,當電芯電壓未高於均衡電壓設定值3443mV,於該串電池之電芯即會停止均衡,但此時會存在某些電池芯電壓偏低,造成整串電芯電壓不均現象,因此智能均衡概念被提出解決此問題。
表3為智能均衡電路動作相關設定值,其概念為當有電芯電壓低於智能均衡啟動電壓時,但尚未低於放電截止電壓設定值,將透過降低電芯均衡電壓10mV,使原本傳統均衡電壓設定值3443mV將低至3433mV,此時將有更多電芯電壓因高於此電芯均衡電壓設定值,進而開始進行放電。較低電壓的電芯將會透過充電進而提升電壓,改善傳統均衡電路只針對高電壓電芯進行管理,而無法解決電壓電芯過低問題,其智能均衡流程如 圖10所示。
項目 | 內容 | 描述 | 電壓(mV) |
---|---|---|---|
1 | 智能均衡啟動電壓 | 電芯電壓低於此電壓時,將啟動智能均衡 | 3350 |
2 | 下修均衡電壓值 | 智能均衡啟動後,將下修原均衡電壓 | 10 |
圖10、單一電池芯電壓智能均衡流程
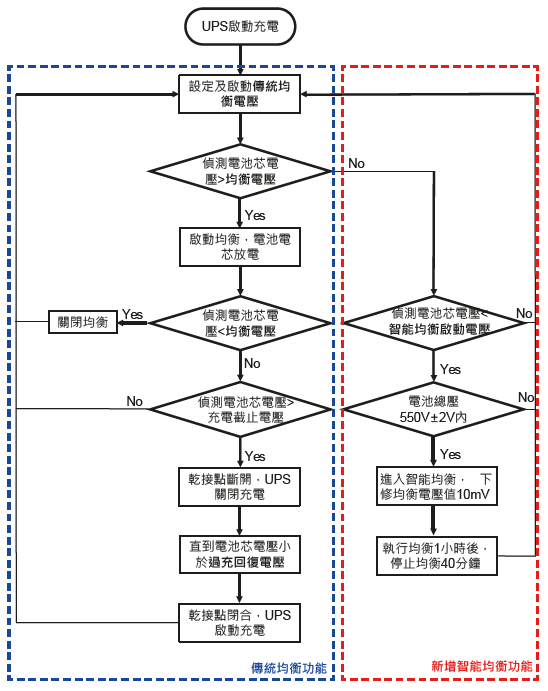
結果與分析
4.1 BMS傳統均衡對電池平衡分析
以一套建置完成的UPS供電系統而言,UPS充電機電壓550V對鋰鐵電池充電,將依 圖8傳統均衡流程進行電芯電壓平衡,由 圖11觀察到因電池已進入CV模式,雖部分電芯電壓落在3443mV水平下,但還是有一部分電芯電壓較低,但也無法進行充電,將造成電池內部壓差變大,於電池放電時將有容量不均問題,長時間影響下將造成電池壽命減短。
圖11、傳統均衡電路對電芯電壓關係

運轉經驗中最常造成電池過壓告警的2個案例為 ①UPS新裝機時,因電池在組裝過程中沒有充電,電池本身自放電將會造成電壓分佈不均。當充電機對電池開始充電時,原高電壓電芯將觸發過壓告警,如 圖12所示 ②因每顆電池容量製造無法完美一致,電池經放電測試後,將導致電壓分佈不均。電芯回充時,易造成原高電壓電芯觸發過壓告警,如 圖13所示。
圖12、新裝機電芯電壓分佈
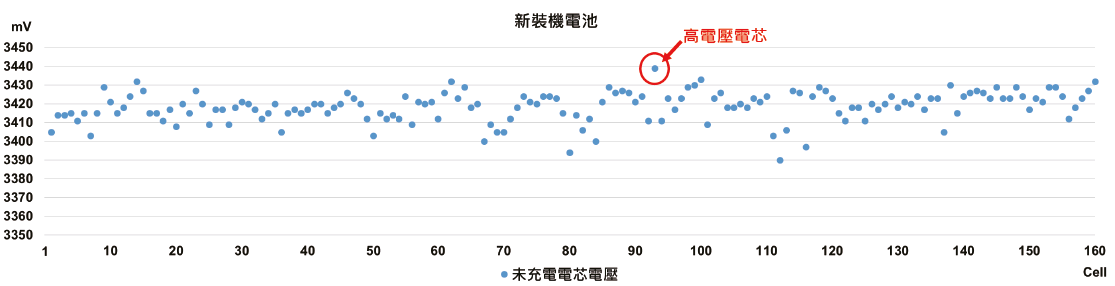
圖13、放電驗收電芯電壓分佈
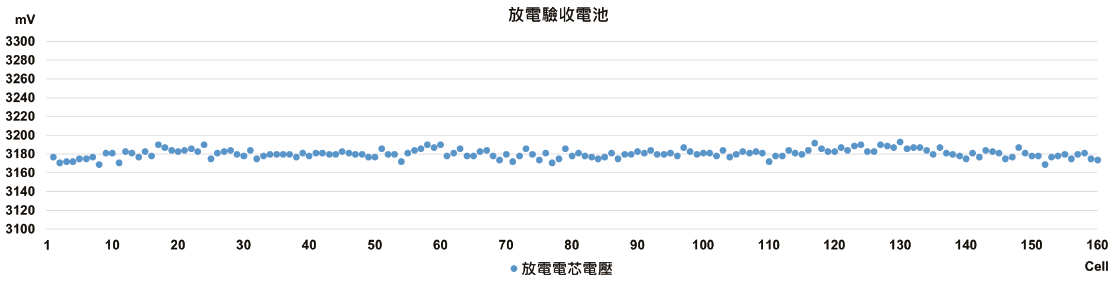
4.2 BMS智能均衡對電池平衡分析
智能均衡的特點為當有低電壓電芯觸發智能均衡啟動電壓3350mV,將啟動智能均衡功能,使原均衡電壓3443mV下修10mV至3433mV,此時若高於3433mV之電芯,BMU觸發均衡電路板上MOSFET開關導通,使電芯開始對平衡電阻放電。此時UPS充電機對該串電池充電,部分電壓較低之電芯,反覆透過此智能均衡方式,最後達到各電芯電壓一致。
由 圖14可觀察出,時間6/5 12:34起初在進行電池充電時,均衡電壓設定值為3443mV,部分電芯電壓落在3443mV下,但因尚未啟動智能均衡功能,而有部分電芯電壓將有明顯偏低離群,最低電壓為3355mV。
圖14、初期智能均衡之電池電芯平衡
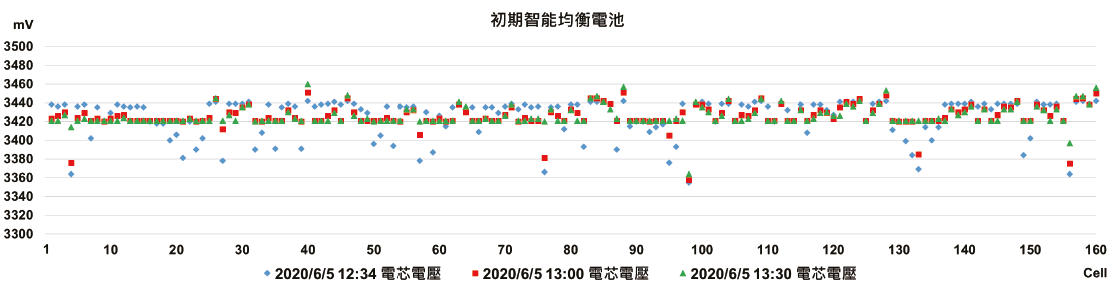
於12:34至13:00間,因有電芯電壓低於3350mV並啟動智能均衡,在13:00、13:30明顯看出因智能均衡啟動,使原均衡電壓設定值為3443mV下修10mV改為3433mV,原大部分電芯電壓高於3433mV者,將透過平衡電阻放電,低電壓電芯獲得充電,使大部分電芯電壓若在3420mV~3460mV間,只有少部分落在3420mV以下。而原離群低壓電芯將有明顯獲得改善,因透過高壓電芯放電,UPS充電機提供充電電流對該串電池進行充電,進而將電芯電壓提高。
經過數日均衡後,由 圖15可觀察出時間6/8 11:12最低電芯電壓高於3350mV,所以智能均衡功能停止,全數電芯皆落在於3432mV~3435mV間,如此一來除了確保電芯電壓皆接近理想值,也使各電芯容量一致。
圖15、後期智能均衡之電池電芯平衡
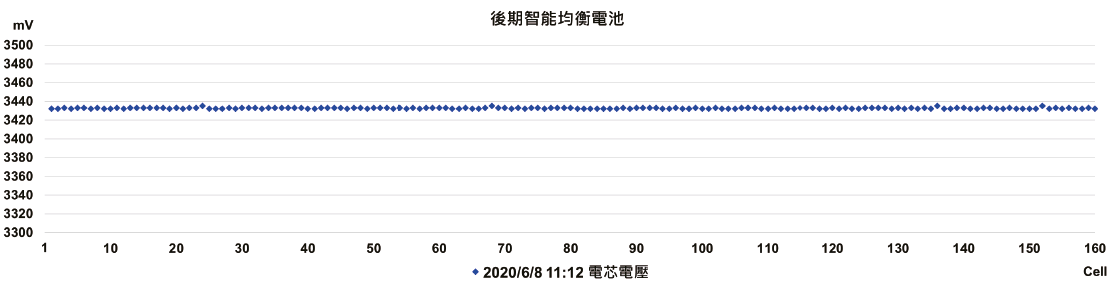
4.3 比較BMS智能均衡與傳統均衡差異
由4.1及4.2節可以了解傳統均衡僅對於電芯高電壓有抑制的功能,但對於低壓電芯無法有效的管理,進而無法達到整體電池電芯一致性。透過 圖10智能均衡的加入,當低電壓電芯觸發智能均衡啟動電壓設定值時,透過下修均衡電壓來使高電壓電芯強制放電,進而提升低電壓電芯,於電池長時間充放電運用時,能達到理想的管理。
結論
鋰鐵電池因安全性佳、能量密度大、充放電循環次數高及環保材質等優點,逐漸取代傳統鉛酸電池的應用,搭配BMS系統能夠清楚掌握每一顆電池電芯的參數及特徵。電池芯在BMS智能均衡控制加入下,也大幅改善部分電芯電壓偏低問題,避免大功率放電造成電池壽命減短損壞。
未來可以透過鋰鐵電池能運轉在環境溫度較高之特性,配合BMS監控功能來調整廠內電氣室空調溫度,改善不必要的電力耗損,已達到節能減碳之效益。
參考文獻
- 許家興、涂家政,具主動式平衡之電動車輛電池管理系統設計,財團法人車輛研究測試中心,2011。
- Davide Andrea, Battery Management Systems for Large Lithium-Ion Battery Packs, 2010.
- International Electrotechnical Commission. IEC 60730-1 Automatic Electrical Controls – Part1: General requirements, 2015.
- Weijie ZHU, Youjie SHI, Bo LEI, Functional safety analysis and design of BMS for lithium-ion battery energy storage system, Energy Storage Science and Technology, 2020.
- 謝芳吉,儲盈BMS系統介紹,TRUEWIN,2020。
留言(0)