摘要
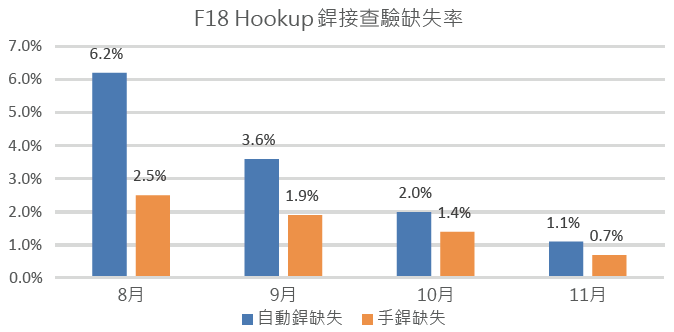
金屬銲接進化論之銲接品質提升
前言
金屬板材及管件銲接,廣泛應用於半導體業、石化工業、建築鋼構、金屬加工及製造業等之銲接工作。其中半導體業的廠房鋼構、廠務設施及氣體供應系統等之金屬銲接則以電弧銲(Arc Welding)工法為主。
半導體產業常用之金屬材料銲接方式 :
- 遮護金屬電弧銲接(Shielded Metal Arc Welding, SMAW),俗稱電銲(圖1),銲接效率低,常用於鋼筋補強銲接及碳鋼支撐架(support)銲接。
圖1、電銲
- 氣體遮護金屬電弧銲接(Gas Metal Arc Welding, GMAW),俗稱半自動銲(圖2),搭配銲料自動傳送系統,銲接效率高且銲道穩定,常用於結構物鋼構銲接及碳鋼桶槽(Tank)銲接。
圖2、半自動銲
- 惰氣遮護鎢極電弧銲接(Gas Tungsten Arc Welding, GTAW)俗稱氬銲(圖3),可用於手動銲或自動銲接,此種銲接銲道表面光滑不必剃除銲渣且品質優良,常用於高潔淨製程金屬管銲接,例如特殊氣體(specialty gas)管路銲接。
圖3、氬銲
金屬電弧銲接工法中,以氬銲(GTAW)銲接之銲道潔淨度及品質最佳,尤其適合小管徑、無背襯、無法從背面銲接又須全滲透的銲道,因此半導體業之高潔淨製程金屬管皆使用氬銲銲接。
早期銲接品質良率參差不齊,常會導致系統運轉經過一段時間後發生問題,造成運轉成本增加,因此如何確保銲接品質是刻不容緩的事。本文將以金屬管線銲接法規標準為根本,搭配銲工認證方式與訓練,呈現目前工區如何進行金屬管線銲接的管理,藉由原理認知及訓練認證,提昇銲接品質,進而達成使建廠過程更順利、更安全的目標,並可推廣至成廠區,達到3贏的局面。
文獻探討
2.1銲接發展之先期技術探討[1]
1960年Roderick G. Rohrberg發明自動氬銲機→1980年代自動氬銲機進階(ARC 107)-機械轉盤輸入式。但每次銲接需要重新設定參數→1990年代自動氬銲機發展神速 (ARC 207)-以按鍵為輸入式且銲機設有參數儲存功能→至今新一代自動氬銲機(ARC 217)-觸動式銀幕。銲接參數已設定在銲機内,更為方便省時!如 圖4自動銲接機的進化及 表1銲機技術演進及銲工銲接時間。
圖4、自動銲接機的進化
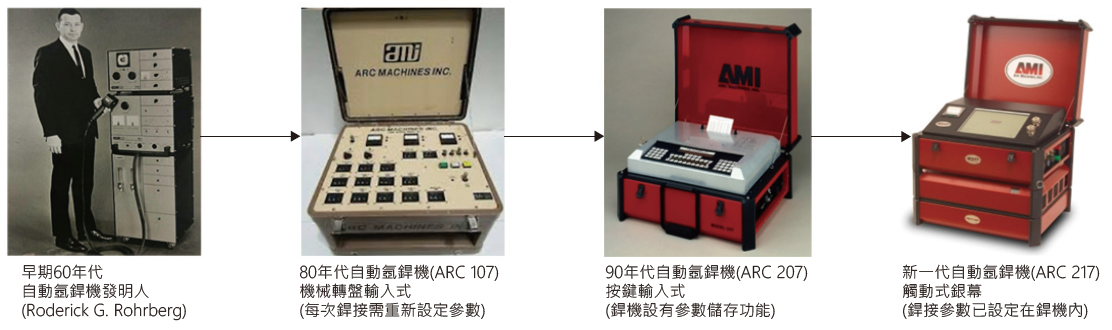
年代 |
1960 |
1980-1999 |
1990-2016 |
2013-至今 |
---|---|---|---|---|
機型 |
NA |
ARC 107 |
ARC 207 |
ARC 217 |
操作介面 |
機械轉盤輸入式(電流選項是固定的) |
機械轉盤輸入式(電流可自行調整) |
按鍵為輸入式 |
觸動式銀幕 |
參數設定 |
每次銲接重新設定 |
每次銲接重新設定 |
有儲存功能 |
參數已設定在銲機 |
平均銲一口(1")時間(銲工1-2年經驗) |
NA |
4-5小時 |
3-4小時 |
2-3小時 |
平均銲一口(1")時間(銲工3-5年經驗) |
NA |
3-4小時 |
2-3小時 |
1-1.5小時 |
備註 : 銲出試片時間是以環境(在室內),電流和氣體內壓/流量穩定的狀況下做判斷 |
2.2金屬管線銲接法規主要參考規範如下
- ASME B31.3–Process Piping,主要包含化學、製藥、紡織、造紙、半導體工廠的製程管路銲接要求。[2]
- ASME BPVC–Boiler and Pressure Vessel Code,提供ASME鍋爐壓力容器合規性檢驗及到場稽核、標準化測試、確保證書有效性的監督稽核。
- ASME IX–Welding & Brazing Qualifications,要求涉及銲工,銲接操作員的資格以及銲接使用的程序。
- SEMI F81–Specification for Visual Inspection and Acceptance of Gas Tungsten Arc Welding in Fluid Distribu-tion Systems in Semiconductor Manufacturing Applications,針對半導體管線,提供鎢極氬弧銲(GTAW)的外觀檢查和驗收規範[3]。
- SEMI F78–Practice for Gas Tungsten Arc Welding in Fluid Distribution Systems in Semiconductor Manufacturing Applications,針對半導體管線,提供鎢極氬弧銲操作規程[4]。
2.3氬銲銲接機制
自動銲接最早是在1960年代使用,當時宇航工業需要對航空液壓管路採用卓越的連接技術,便開發了一種銲接機制,其中來自銲接接頭用鎢電極的旋轉電弧圍繞管圓周。電弧銲電流由控制系統調節,從而使整個過程自動化。 結果是比其替代的手工銲接方法更精確,更可靠。氬銲–自動銲接在1980年代初期對許多行業變得很實用,當時開發了組合電源/控制系統,該系統可在110VAC的電壓下作業,並且銲機結構小巧,可以在多個現場銲接中從一個地方搬到另一個地方。現代自動銲接系統提供計算機控制,可以將各種應用的銲接參數存儲在內存中,並在特定應用需要時調用。因此,可產生大量相同的銲縫(圖5),並且大大減少了錯誤或缺陷的餘地。
圖5、典型的自動銲道

2.4氬銲銲接系統
自動銲接過程中,將銲把固定在適當的管道位置,然後軌道銲頭圍繞銲縫旋轉電極和電弧,以進行所需的銲接。自動銲接系統由電源和軌道銲頭組成。電源 : 電源/控制系統(圖6)根據創建或從內存中調用的特定銲接程序來提供和控制銲接參數。電源提供控制參數,電弧銲電流,驅動銲頭中的電動機的功率,並根據需要打開/關閉保護氣。銲把 : 自動銲接頭通常是封閉式的。原因是在銲接過程中需要提供保護氣體達到外銲道的穩定性,通常都會用惰性氣體。標準的封閉式自動銲把適用於尺寸從1/16英寸(1.6mm)到6英寸(152mm)的銲管,壁厚可達154英寸(3.9mm)。較大的直徑和壁厚可使用開放式的銲把。
圖6、自動銲接系統
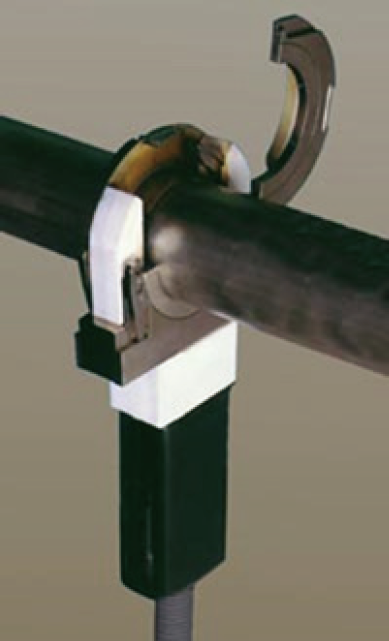
2.5依SEMI F81金屬管線銲接規範中常見缺失有下列3種 (如 圖7~圖9)
圖7、銲道咬邊
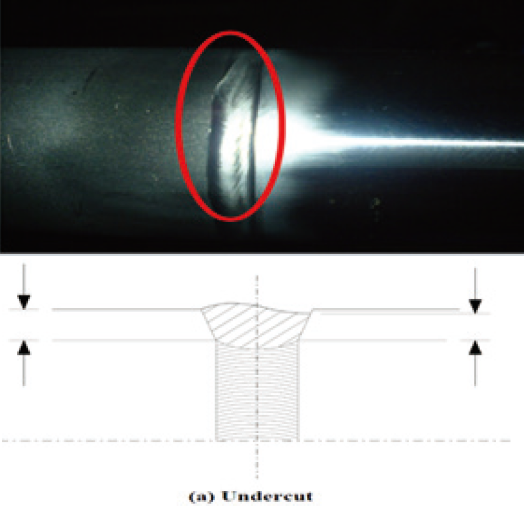
圖8、銲道下陷-外銲道不得超過管壁厚度(T)的10%-管徑<1″內外銲道不可凹陷
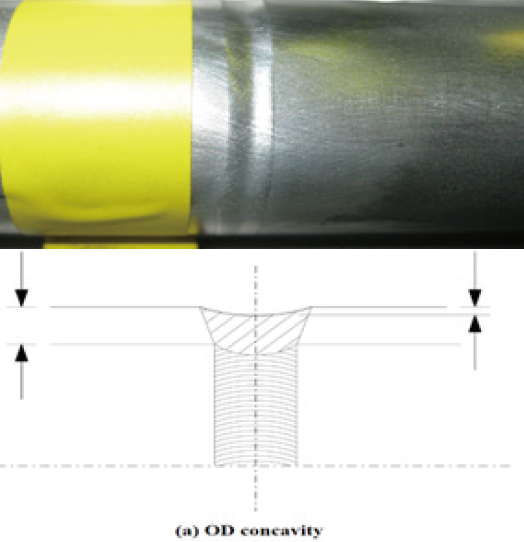
圖9、銲道飄移-內外銲道彎曲度≤35%管壁厚度
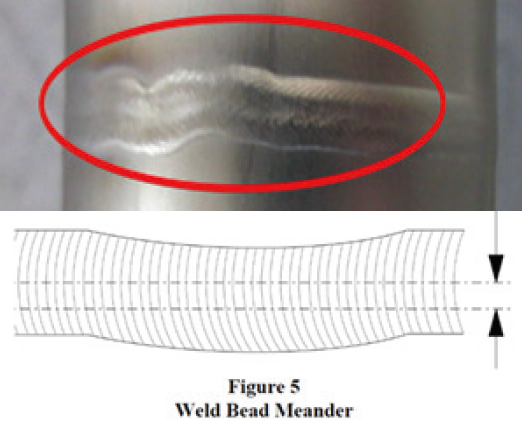
2.5.1 銲道咬邊 :
是指由於銲接參數選擇不當,或操作方法不正確,沿銲趾的母材部位產生的溝槽或凹陷。咬邊將減少母材的有效截面積、在咬邊處可能引起應力集中、特別是低合金高強鋼的銲接,咬邊的邊緣組織被淬硬,易引起裂紋。
2.5.2 銲道下陷 :
是指在銲接時電流過高,內吹氣體太小,內壓流量不足。
2.5.3 銲道飄移 :
銲點數量太多太集中,環境影響造成。
研究方法
3.1銲工認證流程
由於銲道缺失皆是人為造成居多,為確保銲接品質,我們必須針對銲工進行認證,而金屬銲接人員認證(Welding Performance Qualifications)目前大多依據ASME BPVE- Section IX來執行,方式及流程如 圖10 :
圖10、銲工培訓認證流程
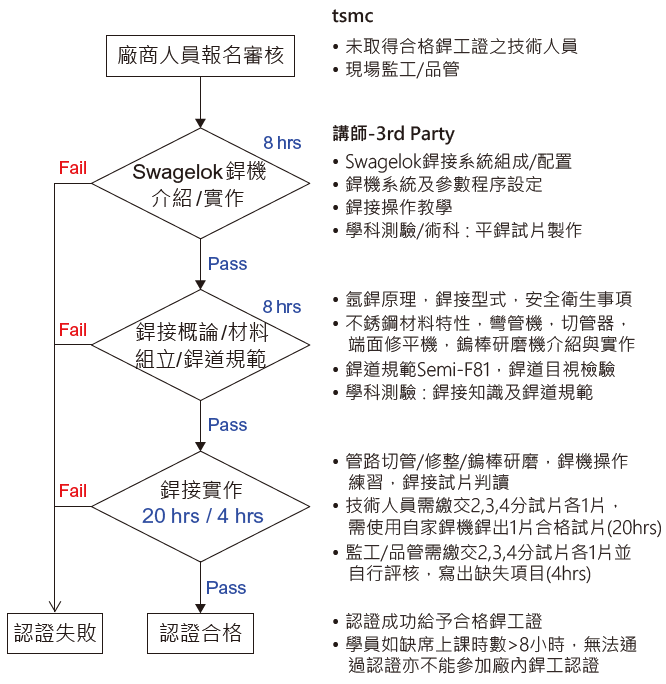
- 銲工必須確實遵守UHP(Ultra High Purity)安裝流程,確保所有銲接過程,品質和安裝系統的工法都依法規和業主的要求。
- 銲工需要至少1年在半導體領域的經歷,以確保銲接和質量的高標準。
- 銲工將進行面試,以確定他們有半導體領域的銲接經驗才同意讓他們參加認證。包含學科-教育訓練-考試,術科-銲工認證。認證將會以尺寸和管壁厚度為主。基本會分成3組級別 : 第1組–1/4″-15A,第2組–25A-80A,第3組–100A或以上(會以管壁厚度為認證考量)。
- 銲工需要在指定的時間完成認證。目前會以4小時為基準。未合格者需經2週才可再做認證。
- 銲工認證過程需要交2個合格試片;1個平銲,1個對銲(對銲需要送去第三方實驗室做破壞測試for WPS(銲接程序書)/PQR(銲接程序檢定紀錄))。
- 合格試片必須寫上管子爐號尺寸、等級、日期、姓名、工號與填寫認證合格表。認證合格銲工會發合格證,資料會上傳系統做管理與統計。
- 目前工區銲工須每廠認證(RFP要求),舊銲工只做試樣銲接後並須通過3rd party目視檢驗即可,不外送實驗室,除非是新銲工才會送實驗室做試樣試驗。Section IX同意只要銲接人員不中斷銲接工作時間超過6個月以上時或發生重大銲接品質瑕疵時,基本上是不需要一直銲工評定。
當然所謂的銲工認證查驗人員也必須具備下列相關證照(圖11)才有資格進行銲道檢查。
圖11、美國銲接協會銲接認證執照(左) 台灣非破壞檢測協會檢驗師(中) 台灣銲接協會檢驗師(右)
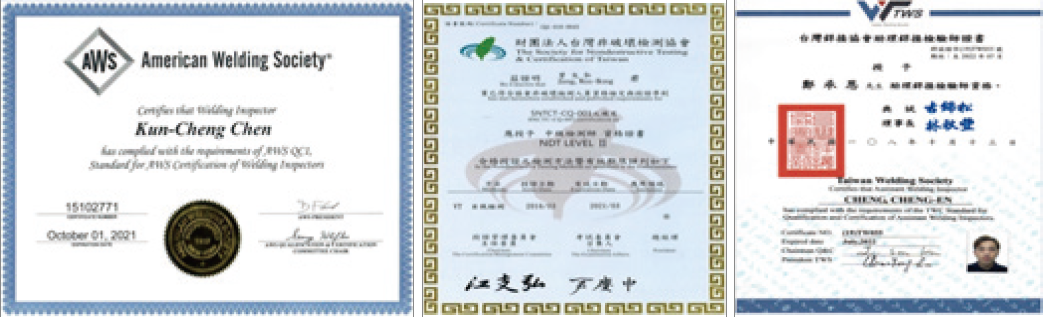
目前銲接技能訓練機構主要有下列幾個地點 :
- 中華職業技能發展學會 : 主要致力於職業安全衛生教育訓練之推廣,提供銲工擁有專業技術與知識,提升產業競爭力。
- 中華銲接技術社 : 提供各式金屬銲接加工及一般手工電銲、氬氣鎢極電銲、CO2半自動電銲,技術訓練。
- 台灣銲接有限公司 : 提供一般手工電銲、氬氣鎢極電銲、半自動電銲、電銲、氬銲、CO2銲、證照考試訓練。
而台積為提升工程師素質,在Y2013年於F8成立銲接教室進行實作訓練,接著於Y2017年轉至F15訓練中心持續幫工程師精進學習。另外為加速建廠及hookup效率及品質,也特別於台南F18成立技能訓練中心進行銲接技能把關。訓練中心規劃每班10人、訓練36小時。完成訓練並通過認證者授予tsmc銲工合格證。認證人員取得合格證後登錄於PCM系統,並配合現場工作趕上及提升工進。
銲機訓練課程為Swagelok原廠授課,銲工及品管人員受訓內容及時數如 表2,銲接參數設定如 圖12。
項目 |
名稱 |
內容 |
銲工 |
品管 |
---|---|---|---|---|
1 |
銲接概論 |
氬銲原理,銲接型式,安全衛生事項 |
1 |
1 |
2 |
材料組立 |
不銹鋼材特性,彎管機介紹,切管/ 端面修整/鎢棒研磨介紹與實作 |
3 |
3 |
3 |
銲機訓練 |
CAJON銲機介紹/銲接實作/銲接測驗 |
8 |
8 |
4 |
銲接實作 |
管路切管/修整/鎢棒研磨,銲機操作練習 |
20 |
4 |
5 |
銲道檢驗 |
銲道規範(Semi-F81),銲道目視檢驗 |
4 |
4 |
總時數 |
36 |
20 |
圖12、銲接參數設定及試燒
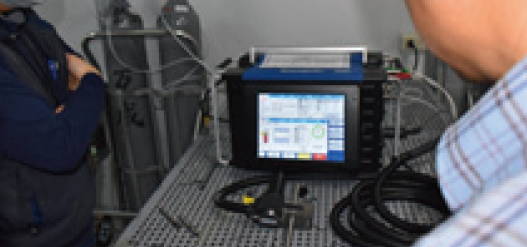
銲接實作內容如 圖13,分為夾具檢查及校正,銲機調整及試燒,彎管器及檢查儀器操作。
圖13、銲接實作
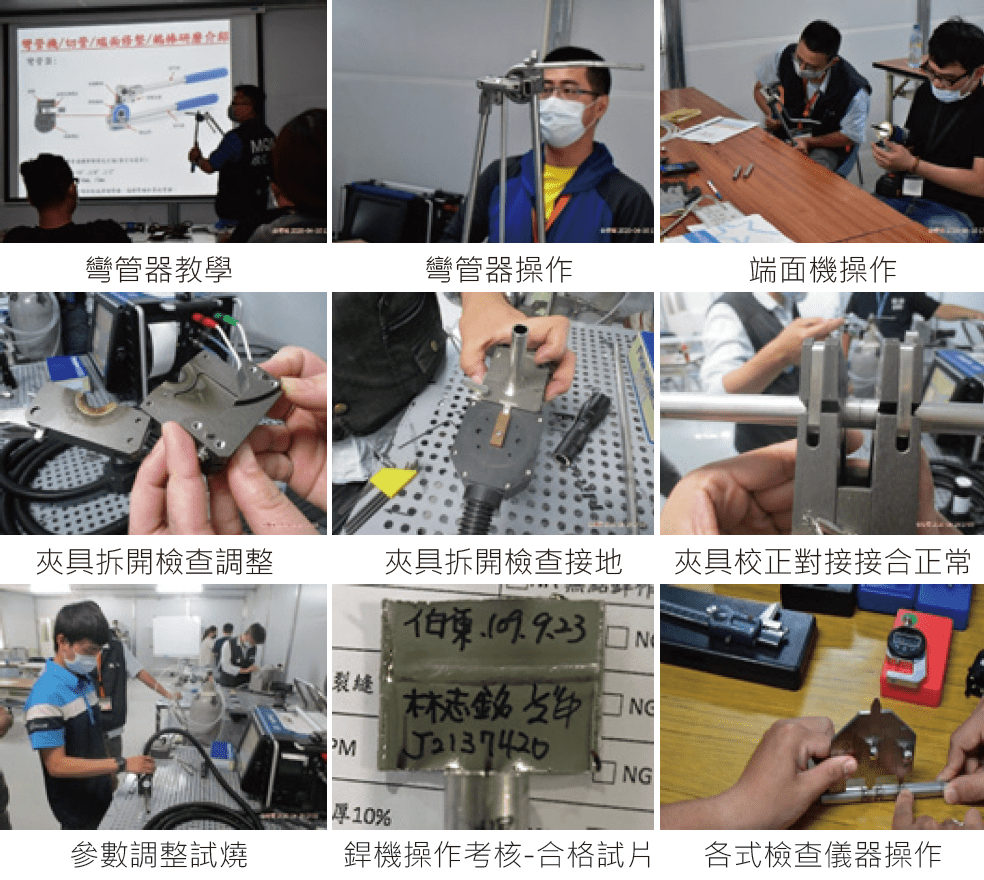
認證合格銲工則會發給識別證(圖14)及背牌(圖15),並於施工現場配掛以供查驗。
圖14、銲工識別證
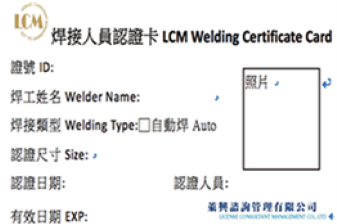
圖15、銲工背牌
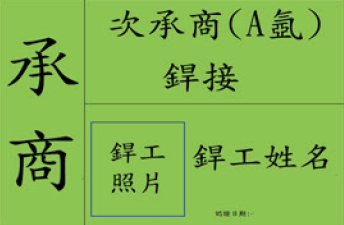
結果與分析
4.1金屬管線銲接考核有3大優點 : 提升銲工素質、降低缺失率、降低氣體/液體洩漏率。
為確保銲接品質,我們也啟動third party進行品管並統計缺失率(如 圖16)及異常照片(如 圖17)。平時定期於每週品管會議中進行檢討,圖16為F18 Hookup銲接查驗缺失率請廠商自主提報查驗數量及缺失率,初期缺失率偏高,經約談該主承商品質主管,檢討改善措施,並對Hookup人員訓練及強化正確施工品質認識,整體缺失率逐月下降。
圖16、F18 Hookup銲接查驗缺失率
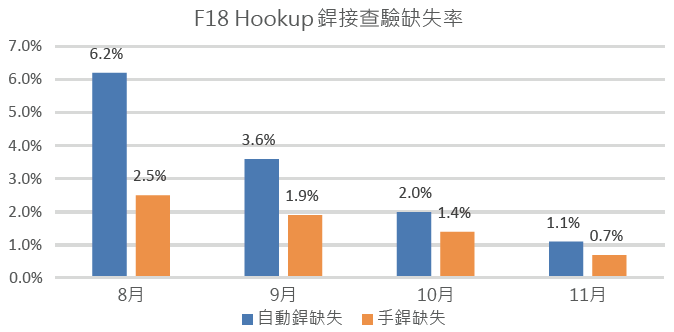
圖17、廠商銲接異常照片
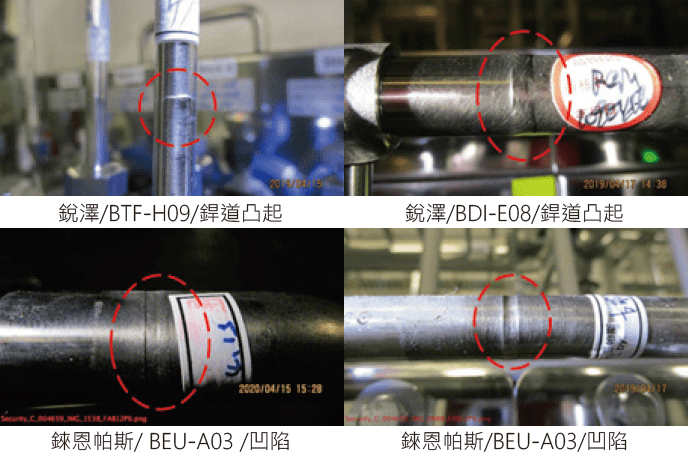
廠商銲接異常照片範例如 圖17,皆會列為改善檢討重點及案例宣導。
4.2保證銲接品質則依靠五大控制環節
人、機、料、法、環,銲前依據銲接試驗和銲接工藝評定,制訂的銲接工藝規程是「法規」,也是保證銲接品質的重要因素。
- 人 : 銲工的操作技能和經驗
- 機 : 銲接設備的高性能和穩定性
- 料 : 銲接材料的高品質
- 法 : 正確的銲接工藝規程及標準化作業
- 環 : 良好的銲接作業環境
結論
經由管路銲接的技術演進及管理機制,以及自動銲接透過人、機、料、法多方面進行認證管理,相關銲接人員須通過銲工考試完成認證、銲接設備亦須完成年度例行保養校正、銲接材料及銲接氣體必須符合標準、銲道須達到規範之標準,才能真正落實銲接品質之提升。最後金屬管線氬銲自動銲接技術與管理則必須隨著半導體製程與之精進以達到管路銲接高品質及高潔淨度的要求。
參考文獻
- The Orbital Welding Handbook, POLYSOUDE.
- ASME B31.3_Process Piping, ASME.
- SEMI F81–Specification for Visual Inspection and Accep tance of Gas Tungsten Arc Welding in Fluid Distribution Systems in Semiconductor Manufacturing Applications.
- SEMI F78–Practice for Gas Tungsten Arc Welding in Fluid Distribution Systems in Semiconductor Manufacturing Applications.
留言(0)