摘要
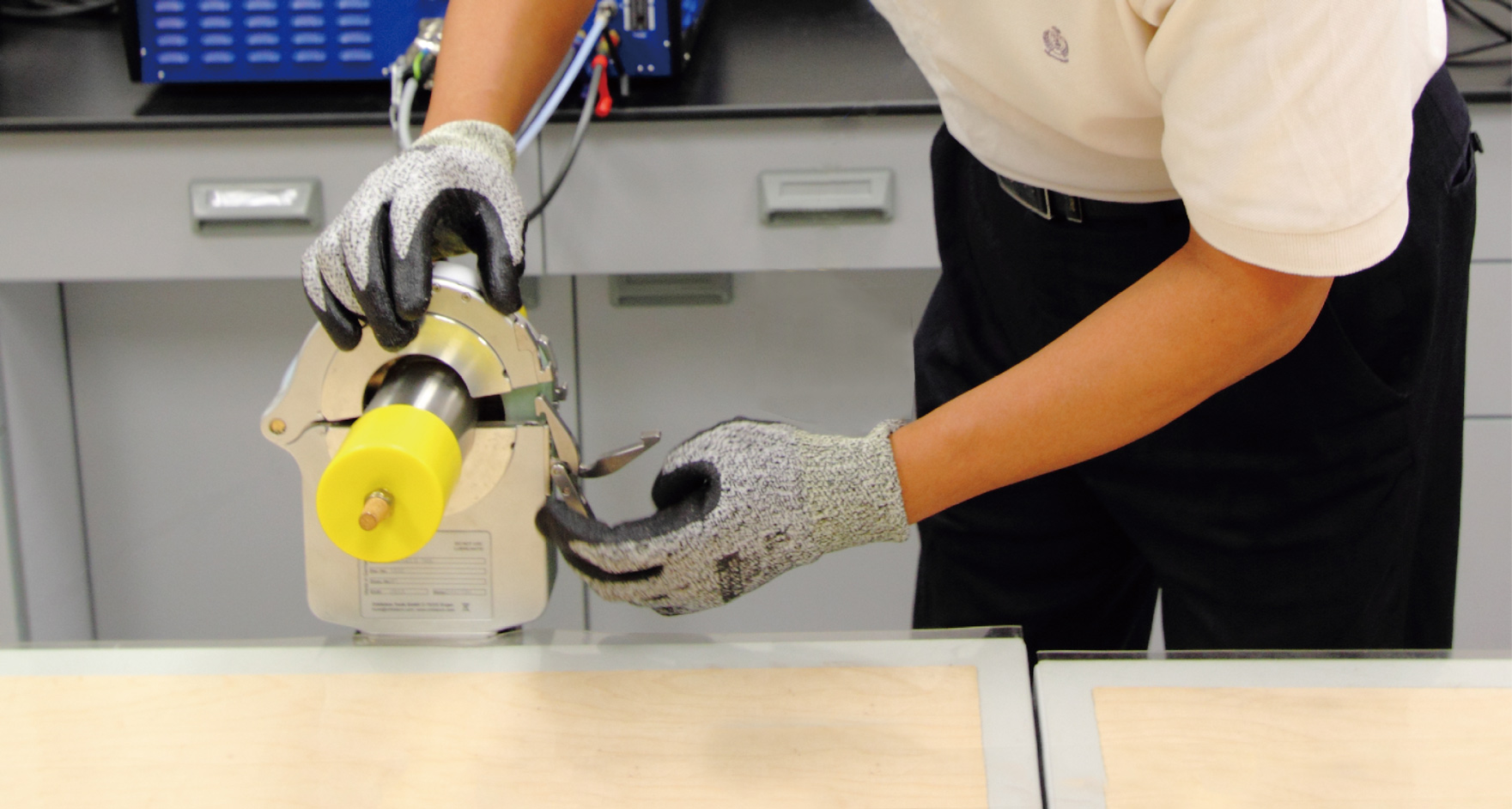
金屬管線氬銲自動銲接實務與銲道規範
Keywords / Gas Pipelines Welding,Gas Tungsten Arc Welding,Automatic Welding
半導體產業之高潔淨金屬管線銲接,主要以氬銲(GTAW)為主,並已廣泛用於製程氣體管線銲接。本文針對金屬管線自動銲接原理、氬銲自動銲接種類、銲接實務與操作參數、銲接品質管理實務及銲道品質檢查等進行探討。
前言
金屬板材及管件銲接,廣泛應用於半導體業、石化工業、建築鋼構、金屬加工及製造業等之銲接工作。其中半導體業的廠房鋼構、廠務設施及氣體供應系統等之金屬銲接則以電弧銲(Arc Welding)工法為主。
半導體產業常用之金屬材料銲接方式:
- 遮護金屬電弧銲接(Shielded Metal Arc Welding, SMAW),俗稱電銲,銲接效率低,常用於鋼筋補強銲接及碳鋼支撐架銲接。
- 氣體遮護金屬電弧銲接(Gas Metal Arc Welding, GMAW),俗稱半自動銲,搭配銲料自動傳送系統,銲接效率高且銲道穩定,常用於結構物鋼構銲接及碳鋼桶槽銲接。
- 惰氣遮護鎢極電弧銲接(Gas Tungsten Arc Welding, GTAW),俗稱氬銲,可用於手動銲或自動銲接,此種銲接銲道表面光滑,不必剃除銲渣且品質優良,常用於高潔淨製程金屬管銲接,例如特殊氣體(specialty gas)管路銲接。
金屬電弧銲接工法中,以氬銲(GTAW)銲接之銲道潔淨度及品質最佳,尤其適合小管徑、無背襯、無法從背面銲接又須全滲透的銲道,因此半導體業之高潔淨製程金屬管皆使用氬銲銲接。
氬銲銲接原理與特性
氬銲即惰氣遮護鎢極電弧銲接(GTAW),利用鎢或鎢合金為非消耗性銲接電極,因鎢的耐磨性強且熔點高(3410°C),同時使用惰性氣體為保護氣體來進行銲接,一般以氬氣為保護氣體(Shielding gas),故俗稱氬銲,亦稱TIG (Tungsten Inert Gas)。如 圖一所示,在鎢棒電極和工件間產生電弧,鎢棒電極做為負極,工件做為正極。此時,電弧會從負極鎢棒流向正極工件,電弧熱源將銲接金屬銜接處熔化形成熔池,當熔池冷卻後即形成銲道。
圖一、惰氣遮護鎢極電弧銲接GTAW
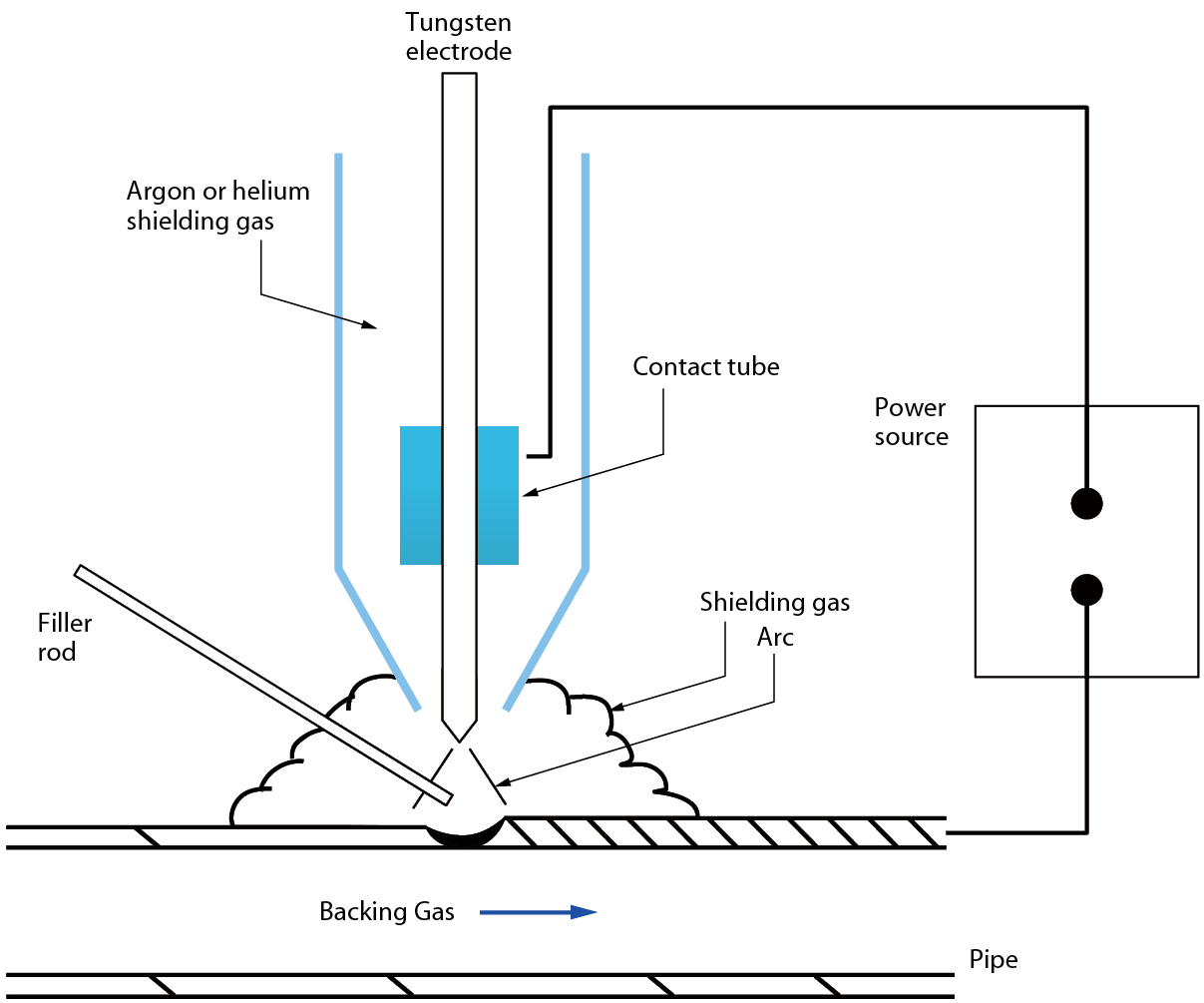
氬銲銲接時在銲把內通入惰性氣體作為保護氣體(Shielding gas),確保銲接工件熔池及鎢棒處於無活性氣體環境中,防止銲道及鎢棒接觸到活性氣體(如氧氣)而快速氧化,因氬氣具備良好起弧特性和電弧穩定性,通常以氬氣作為保護氣體。另外為避免管線內部銲道氧化,銲接時會在管線內部通入背吹氣體(Backing gases),防止管件內部的熱金屬與空氣中的氧氣接觸,一般使用氬氣或氮氣為背吹氣體。
銲接入熱量決定金屬銲接熔池大小及銲道的滲透深度。銲接入熱量與銲接電壓及電流成正比,與銲接速度成反比,可由下列公式來計算。
Q:入熱量(kJ/mm)
V:銲接電壓(V)
I :銲接電流(A)
S:銲接速度(mm/min)
Efficiency:銲接效率係數
其中銲接效率係數(Efficiency)因不同銲接方法而有所不同,鎢極氣體保護電弧銲(GTAW)為0.8,遮蔽電弧銲(SMAW,俗稱電銲)為0.75。因此銲接電壓、電流及銲接速度為銲接機調整的重要參數。
金屬管路銲接會受地心引力(重力)影響,當金屬熔池(Pool)未凝固前,熔池中的鐵水受重力產生下沉現象,而影響銲道品質,如 圖二。因此必須隨著管路銲接位置(Welding Position)不同而調整銲接電壓及電流等參數,藉以完成均勻圓周銲道。
圖二、銲道受重力影響

氬銲自動銲接分類
氬銲自動銲接為鎢棒電極圍繞管件旋轉,完成管件加熱銲接,為軌道式銲接(Orbital welding)工法,可達到高潔淨與高品質銲道的要求。與手工銲接相比,軌道式自動銲接可以提高銲接速度,排除手工銲接的不確定因素,具有高重覆性及銲接參數可追朔等優點。氬銲自動銲接一般分為兩類:開放式自動銲接及密閉式自動銲接。
開放式自動銲接機(管壁厚T≧3.0mm,填料銲接)
開放式自動銲接用於管壁厚≧ 3.0mm填料銲接,如 圖三。此銲接法鎢棒電極是屬於開放空間,銲條可配合自動送線機進行添料,以加速銲接速度。
圖三、開放式氬銲自動銲
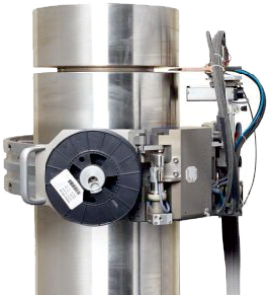
由於管壁較厚(T≧3.0mm),此類管路銲接前必須在管端開槽(Groove),同時採用多道填料多層銲接工法,管件銲道才能達到完全滲透。銲接主機需具備AVC(電弧電壓上下控制)及OSC(銲槍擺弧左右控制)功能,以提昇銲接效率與銲道品質,如 圖四所示。
圖四、多層多道填料之銲接銲道
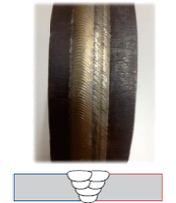
密閉式自動銲接(管壁厚T<3.0mm,不填料銲接)
密閉式自動銲接設備,如 圖五,是專為薄管(T<3.0mm)且不填料銲接所設計,銲把與管件可緊密接觸,銲接過程在密閉空間內完成,銲道可達到高品質要求,管件銲接前需緊密接合採不填料銲接,可銲接出單層高品質的銲道。
圖五、密閉式自動銲接
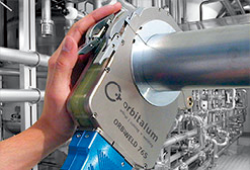
氬銲自動銲接機與銲接實務
目前半導體廠氣體供應系統之高潔淨(Ultra High Purity, UHP)金屬管線皆採用密閉式銲接,因此本文針對密閉式自動銲機進行進一步討論。
密閉式自動銲接機
密閉式自動銲接機主要由電源主機及銲把兩項元件組成,銲接主機可搭配不同管徑之銲把,且適用於6吋以下管徑之自動銲接,如 圖六。
圖六、軌道式自動銲接機
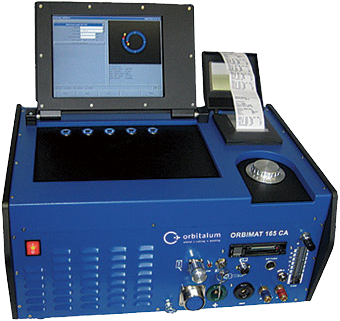
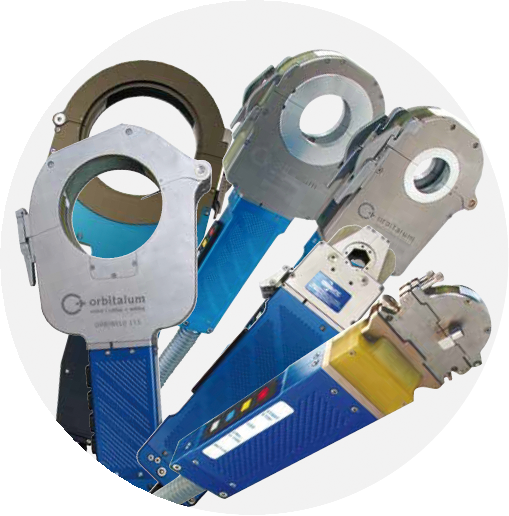
自動銲接機銲把由馬達轉動齒輪,再帶動C型傳動齒輪上之鎢棒進行圓周銲接,且銲把內部具多孔性作為保護氣體導入孔,使氬氣平均且快速充滿銲接空間,防止銲道及鎢棒接觸到空氣而快速氧化,如 圖七所示。
圖七、軌道式自動銲把構造
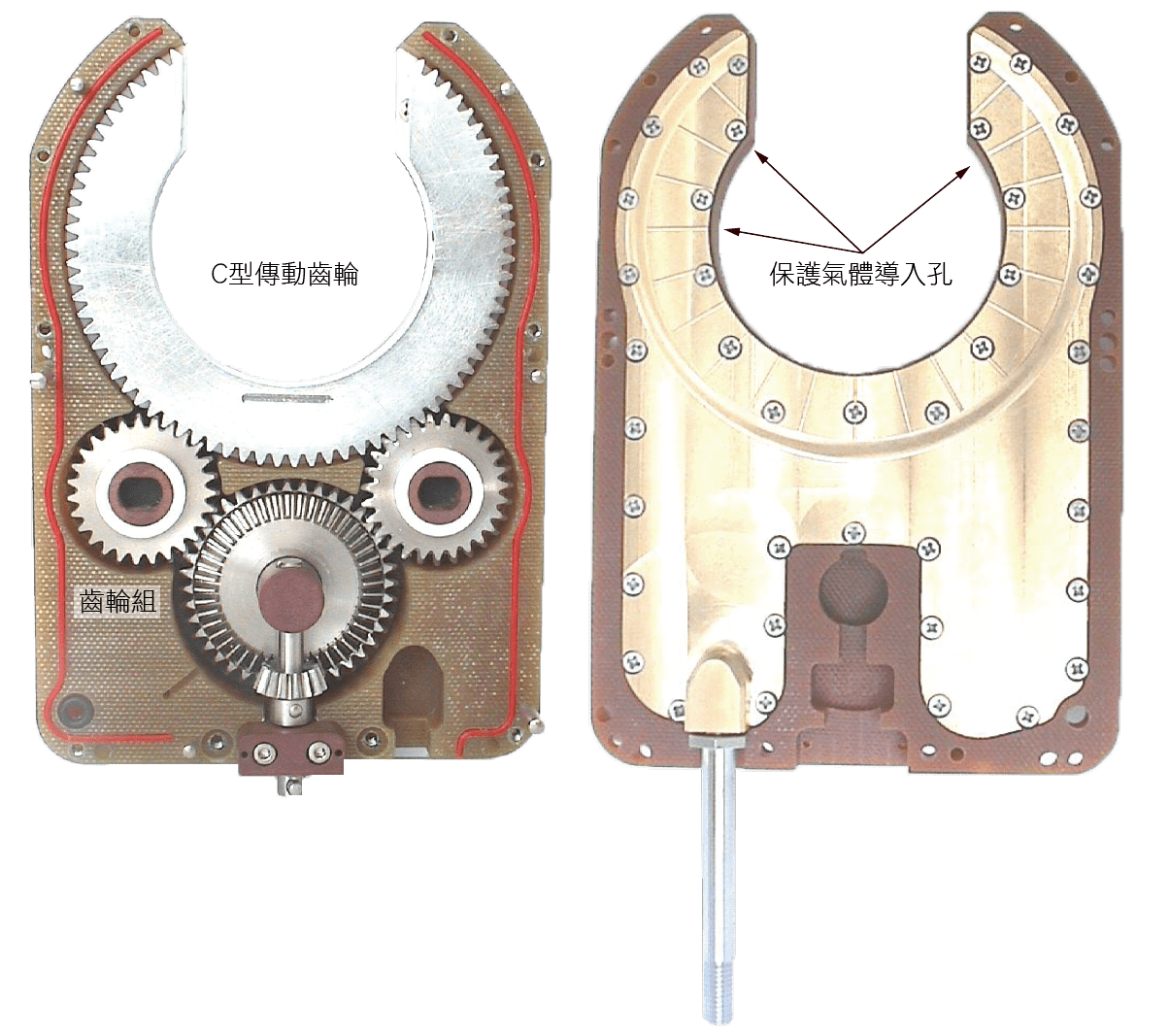
重要銲接參數
鎢棒規格
鎢棒材質規格、研磨方式及安裝間距,都會直接影響銲接銲道品質。
- 鎢棒直徑:直徑選用與銲接管徑及電流大小成正比。
- 鎢棒角度(Angle)與研磨:一般鎢棒角度為20~35°。鎢棒需縱向研磨以維持電弧寬度,如 圖八。
圖八、鎢棒研磨方向
- 尖端直徑(Tip Diameter):電極鎢棒尖端修平可使電弧較平滑,增加電弧的起弧次數及延長電極壽命。
- 電弧間隙(Arc Gap):為鎢棒與管外壁之距離,其間隙與管壁厚度成正比,壁厚小於1.0mm電弧間隙為0.8mm;壁厚1.0~2.1mm則電弧間隙為1.5mm。
脈波電流(Pulsed Current)
軌道式自動銲接以脈波電流(Pulsed Current)來控制銲接金屬熔融量,一個銲接脈波週期包含高電流及低電流,當高電流時銲接熔池的體積增加到最大,而低電流時使銲接熔池冷卻形成銲道。
銲接速度
銲接中鎢棒電極會以線性行程速度圍繞管件旋轉,標準線性行程速度介於50~200mm/min之間。銲接速度會影響銲道魚鱗紋之覆蓋率,銲接速度越慢銲道魚鱗紋之覆蓋率則越高,如 圖九所示。依照SEMI F81規範,管路外銲道之魚鱗紋覆蓋率必須大於80%。
圖九、銲接速度對銲道之影響
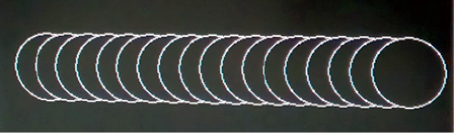

內吹氣體
內吹氣體會影響內銲道的氧化狀況, 圖十為不同氧濃度下造成內銲道的顏色變化,氧氣濃度越高內銲道褪色越明顯。依據規範SEMI F78之規定,內吹氣體的純度應為99.9997%或總不純物(水分及氧氣)必須小於3ppm,因此內焊道氧化等級需同圖中No. 1。
圖十、氧含量對銲道氧化之影響
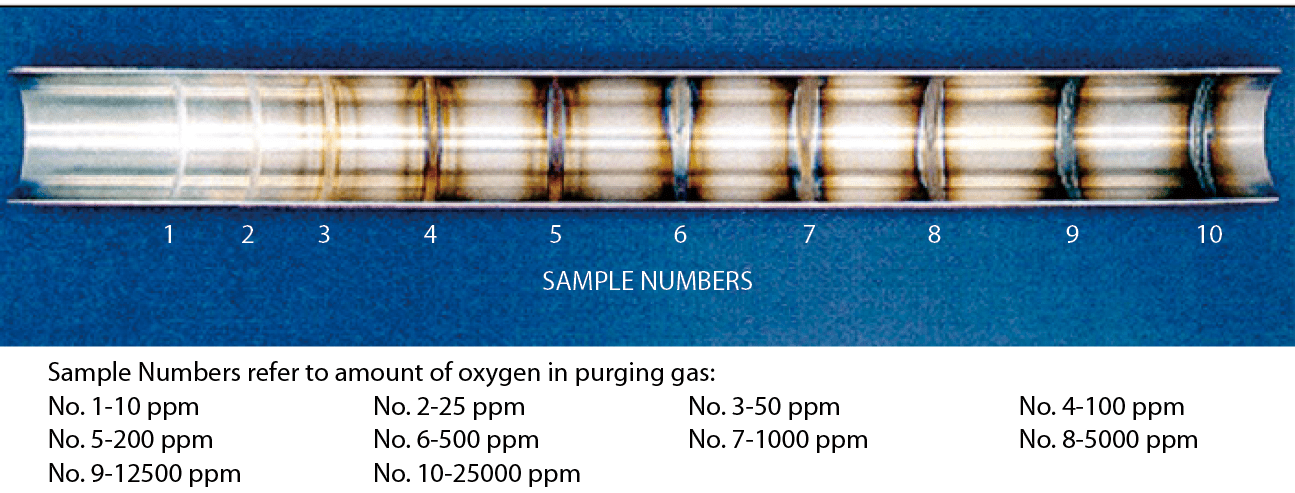
銲接象限編程
管路圓周銲接因受重力影響,銲接位置可分為四大區塊,即銲接象限,而銲接參數須依銲接象限變化調整。以 圖十一說明,S1象限為平銲(Flat Weld)位置,受重力影響管內壁容易產生銲道內凸現象;S2象限為立銲(Vertical Weld)向下位置;S3象限為仰銲(Overhead Weld)位置,管內壁銲道容易產生內凹現象;S4象限為立銲向上。因此銲接時必須隨著各象限不同而調整參數,藉以完成均一的圓周銲道。
圖十一、圓周銲接象限圖
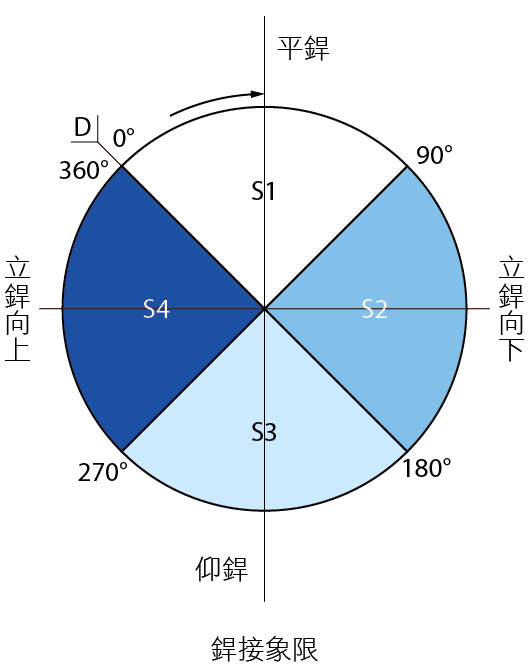
銲接實例
管線密閉式軌道自動銲接流程,如 圖十二,銲接前先進行銲把的前吹,接著起弧預熱後依序進行第一象限至第四象限的圓周銲接,最後進行銲接的收尾,銲接完成後須再進行銲把的後吹程序。前吹主要將密閉銲把完全充滿氬氣,並有吹淨除濕的功能;而後吹則是讓鎢棒在氬氣之環境下降溫。
圖十二、自動銲接電流變化圖
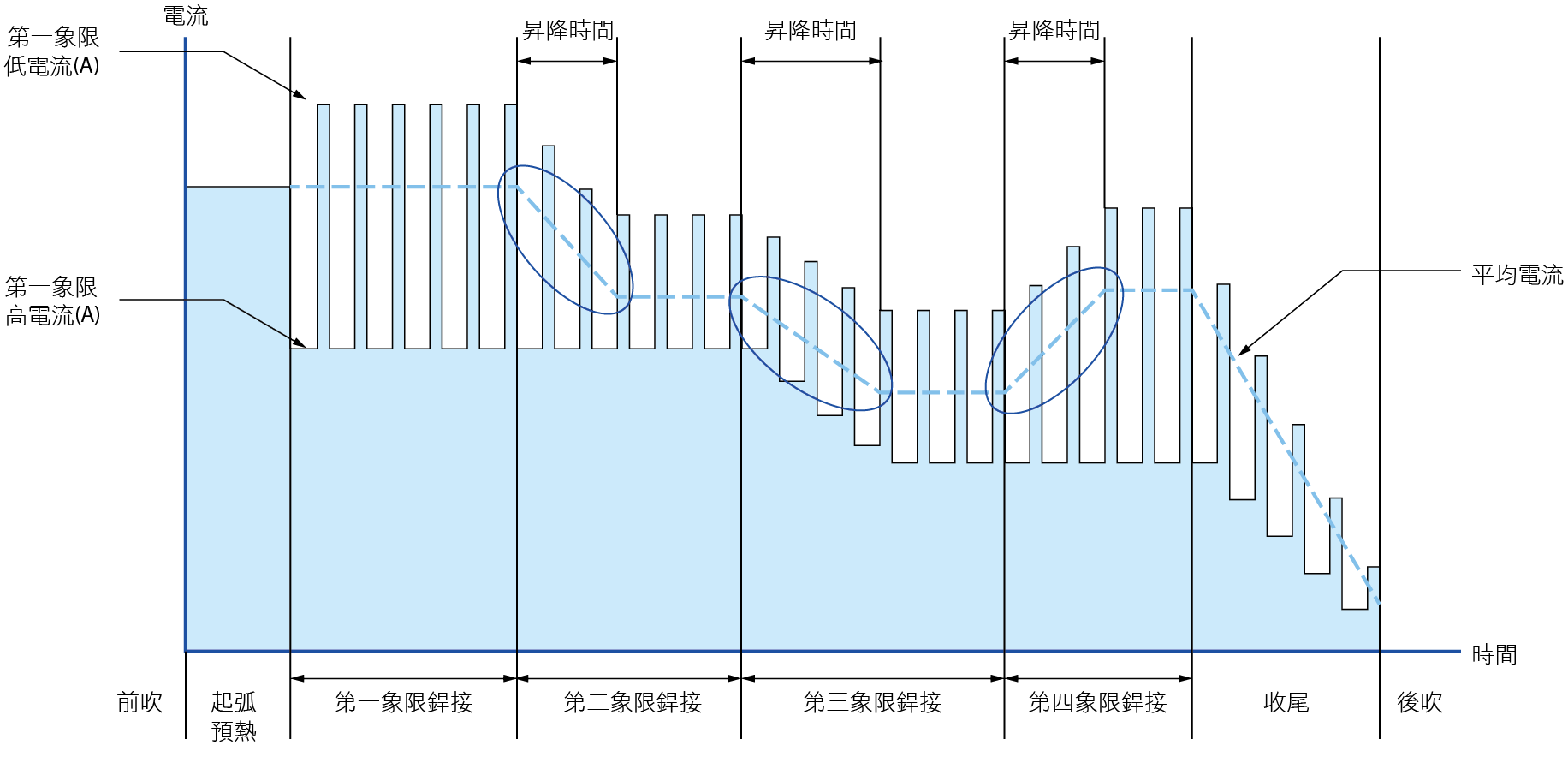
以25A外徑33.4mm 316L的管線銲接為例,銲接參數如 表一,將銲接分為四個象限,以管線剖面九點鐘位置為銲接起始點,第一象限為起銲後立銲向上且銲池受重力影響與銲接方向相反,因此電流設定較高;第二象限為平銲,銲道較易滲透因此電流略降;第三象限為立銲向下,銲池受重力影響熱量不易累積,因此將電流增加;第四象限銲為仰銲及立銲向上,因管路受前三象限所傳導的熱量累積,所以不須相對高的熱量。每批管路均需將銲接試片結果,依據SEMI F81判斷後,微調銲接參數,使得銲道品質符合規範標準。
象限 |
Sector |
單位 |
S1 |
S2 |
S3 |
S4 |
---|---|---|---|---|---|---|
起始角度 |
Start angle |
。 |
1 |
45 |
135 |
240 |
終止角度 |
Final angle |
。 |
45 |
135 |
240 |
370 |
象限銲接時間 |
Sector time |
sec |
9.4 |
18.8 |
22.0 |
27.2 |
參數緩升降時間 |
Slope time |
% |
0.0 |
20.0 |
20.0 |
20.0 |
高電流 |
HP current |
A |
56.0 |
53.8 |
57.1 |
54.9 |
低電流 |
LP current |
A |
25.2 |
24.2 |
25.7 |
24.7 |
高電流停留時間 |
HP time |
sec |
0.16 |
0.16 |
0.16 |
0.16 |
低電流停留時間 |
LP time |
sec |
0.16 |
0.16 |
0.16 |
0.16 |
高電流移動速度 |
HP travel speed |
mm/min |
85.0 |
85.0 |
85.0 |
85.0 |
低電流移動速度 |
LP travel speed |
mm/min |
85.0 |
85.0 |
85.0 |
85.0 |
不同批號管材的銲接參數都有差異,因為管材含硫量影響熔融金屬的表面張力,造成銲接時滲透深度的差異,高含硫量的銲道銲接面為窄且深,而低含硫量銲道為寬且淺低滲透的銲接面,因此低硫含量的管件須更大熱量方可滲透銲接,且其外銲道較寬。
銲接品質管理實務與規範
目前台積電新建廠之氣體金屬管線銲接品質管理,皆依照國際標準規範(如ASME,AWS)要求,執行銲接管理與銲道品質檢驗。以下就管理機制與規範說明。
銲接品質管理
銲接程序管理
每種銲接工法必須訂定銲接程序書(WPS, Welding Procedure Specifi-cations),並且通過銲接程序認證(PQR, Procedure Qualification Records ),銲接施工需依照銲接程序書(WPS)進行施作。
銲工認證與管理
銲工上線工作前,需通過第三公證單位之銲接認證或審核,並對銲接缺失需進行紀錄與統計。
每日試片管理
每日銲接工作前必須調整銲機參數,銲出符合規範試片且通過第三公證單位審核,再依照此參數開始銲接工作,當管規格改變時必須重新調整銲機製作試片。
銲道查驗
銲道檢查必須由具備「檢驗師」資格(VT Level II 或CWI Certified Welding Inspector)之QA/QC人員或第三公證單位執行,當查驗缺失率大於50%時,則進行加倍取樣檢查或複驗,若缺失率仍大於50%,則應進行全數檢查並紀錄。
第三公證單位(3rd Party)
由第三公證單位人員執行銲道三級品質檢驗,並將查驗缺失開立稽核單進行追蹤及覆驗。
銲道品質標準
半導體業高潔淨管線銲接完成後之銲道檢查,依據規範SEMI F81進行目視檢查,此檢查標準只適用於6inch (150mm)以下金屬管氬銲無添料自動銲銲接工法,包含高純度HP (High Purity)和超高純度UHP (Ultra High Purity)的系統。
銲道應完全滲透圍繞整個內表面,滲透及銲道寬度應均勻分布整個銲道,依據SEMI F81銲道查驗標準,符合下述銲道外觀缺陷者,都必須切除重新銲接,如 表二銲道缺陷與範例圖示。
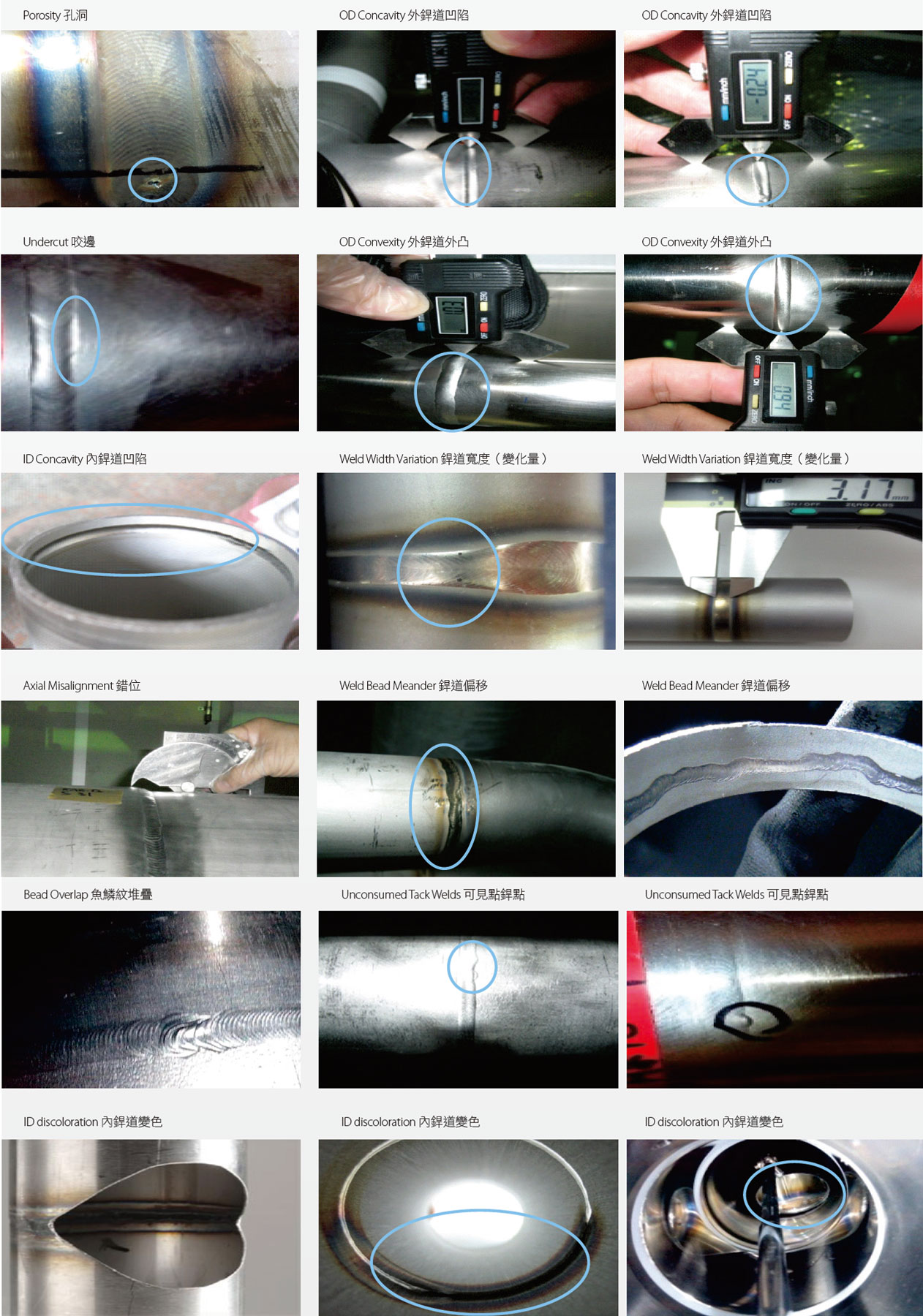
- Cracks(銲道表面裂紋),Porosity(氣孔),Inclusions(夾雜物)。
- ID Concavity:管內徑(ID)銲道凹陷(Concavity)低於管壁面。
- Undercut:銲道咬邊。
- Unconsumed Weld Tack:銲道表面有銲點(Weld Tack)痕跡為缺陷。
- ID Discoloration:管內銲道有變色(Discoloration)狀態為缺陷。
- OD Concavity:外徑(OD)銲道凹度(Concavity)>10%管壁厚度(T)為缺陷;當管徑小於1inch則不容許銲道凹度。
- OD Convexity:外徑(OD)銲道凸度(Convexity)>10%管壁厚度(T)為缺陷。
- Weld Width Variation:
內徑(ID)銲道寬度應介於1.0-2.5倍管壁厚(T),且最大銲道寬度≦1.25倍的最小銲道寬度,否則為缺陷。
外徑(OD)銲道寬度最少應為管壁厚(T)的兩倍,否則為缺陷。 - Weld Bead Meander:銲道中心線的變化距離>35%管壁厚(T)為缺陷。
- Bead Overlap:外銲道魚鱗紋重疊率<80%,內銲道魚鱗紋重疊率<70%,皆為缺陷。
- Axial Misalignment:對接管路之軸向段差量>10%管壁厚(T)為缺陷。
結論
氬銲自動銲接因為銲道表面光滑、不必剃除銲渣、且銲道品質優良,目前已廣泛應用在半導體產業之高潔淨金屬管線銲接。台積電新建廠之金屬管線銲接管理,亦遵循國際銲接相關規範(如ASME、AWS、SEMI)標準,建立並執行管路銲接管理機制,透過人、機、料、法等多方面進行認證與管理,銲接人員須通過銲工考試完成認證、銲接設備亦須完成年度例行保養校正、銲接材料及銲接氣體必須符合標準、銲道須達到規範之標準。金屬管線氬銲自動銲接技術與管理必須隨著半導體製程之精進達到管路銲接高品質及高潔淨度的宗旨。
參考文獻
- The Orbital Welding Handbook, POLY-SOUDE
- The Orbital Welding Manual, Orbitalum.
- ASME B31.3_Process Piping, ASME.
- ASME BPVC_Boiler and Pressure Vessel Code, ASME.
- AWS A2.4_Standard Symbols for Welding, AWS.
- SEMI F81_ Specification for Visual Inspection and Acceptance of Gas Tungsten Arc Welds in Fluid Distribution Systems in Semiconductor Manufacturing Applications, SEMI.
- SEMI F78_Practice for Gas Tungsten Arc Welding of Fluid Distribution Systems in Semiconductor Manufacturing Applications, SEMI.
- SEMI E49.6_Guide for subsystem assemble and testing procedures- stainless steel systems, SEMI.
留言(0)