摘要
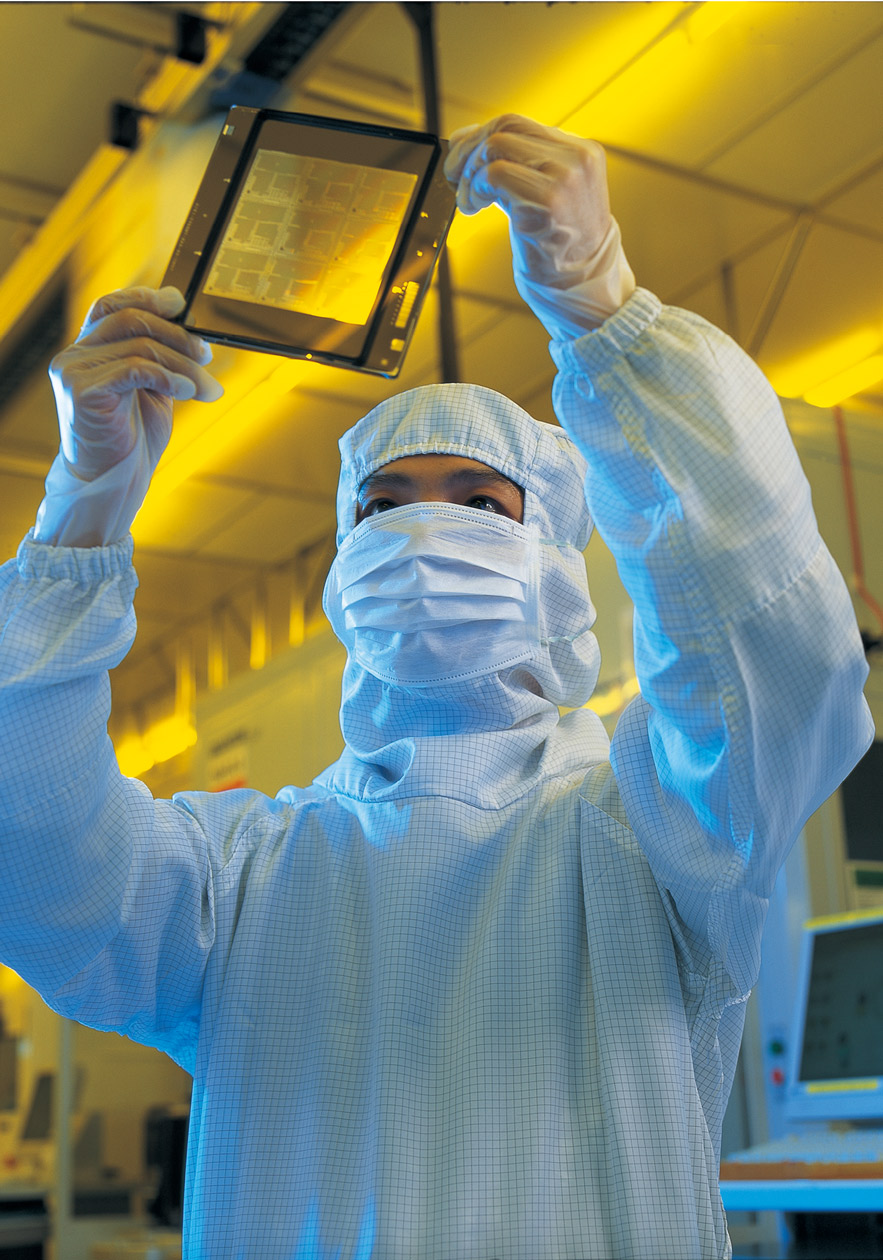
奈米粒子捕捉技術介紹
A new nanoparticle detecting and tracking system has been proposed to measure nanoparticle contamination and localize the source of the contaminant simultaneously in the cleanroom. The nanoparticle tracking and localizing system consists of minimized nanoparticle sensors and an ad-hoc network is suitable for most advanced semiconductor factories. Experimental results indicate that the system has higher counting accuracy and controlled deviation in nanoparticle’s diameter measurement.
Introduction
The geometry of semiconductor fabrication continues to shrink, particles’ diameter larger than about ¼ of the line-width may cause fatal device defects. The challenge for ultra clean particle free facilities in the fabrication of semiconductors has been well recognized since the line-width shrink dramatically. The main target of particle contamination control in semiconductor manufacturing fab is loss prevention and yield enhancement, a nanoparticle detecting device and tracking system is urging and needed for this concern.
Particle Contamination Control Network
In the cold-war period, scientists worked on the project of protecting people from the threat of biochemical weapon’s attack. The research not only interested in targeting the source of biochemical assault but also has to establish the accurate boundary of danger. There were many successful application examples of hazardous gas detecting system on the protection from biochemical terrorism attack and accurate boundary setting for preventing human exposure in the dangerous area. Such works had solid results and we can facilitate the same technique to control cleanroom contamination.
The particle contamination is far different from the AMC, for the AMC is sorted by the material’s compound property. But even the same compound, particle form of contaminant may show up in different diameter and thus results in different behavior. The great variability in cleanroom ambient aerosol characteristics results in a demand for fast response system. We cannot use the traditional way to detect contaminant dispersing in the surroundings by dog tracking, seeking the odor sources in the cleanroom. But the contaminants always have the nature of diffusion and will spread up in the environment, thus leave the clue of concentration gradient to localize the source of contaminant. We have been using Scanning Mobility Particle Sizer(SMPS) on particle detection for quite a long period of time before minimized particle sensors were invented. Is it possible to drive a SMPS to explore the particle contamination and localize the source of particle contamination in a vast area of cleanroom? X. Cui et al., set up a multiple detecting robot system [1], using moving robot equipped with contaminant sensor to perform extend area exploration task. The moving robots formed an ad-hoc network, by data exchanging between the robots, the system could dynamically respond the concentration gradient and direct the source of contaminant.
The swarm-based FLC algorithm is deployed to search for the source of hazardous gas in X. Cui ‘s research. Every single robot is equipped with a sensor and plays as a node in the ad-hoc network system Figure 1. They assume the sensor is always influenced by the random noise, thus can not offer absolutely correct data. Each robot could communicate with others, but in a limited range. The area of the surveying environment is adapted to orthogonal gridded map, and the swarm behavior is used here to control robot’s movement in case of the existence of overlapping unexplored cell and lost contact with adjacent robot. Moving the robot to a target cell without other robot’s support will cease the network communications. Implement a swarm behavior topology controller to plan the target cell to measure the aerosol concentration Figure 2.
Figure 1. The environment grid map and expansion cells
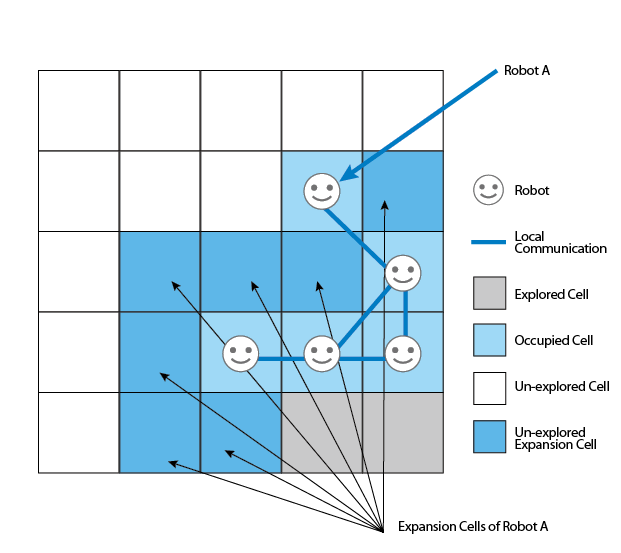
Figure 2. Block diagram of the swarm-base FLC system
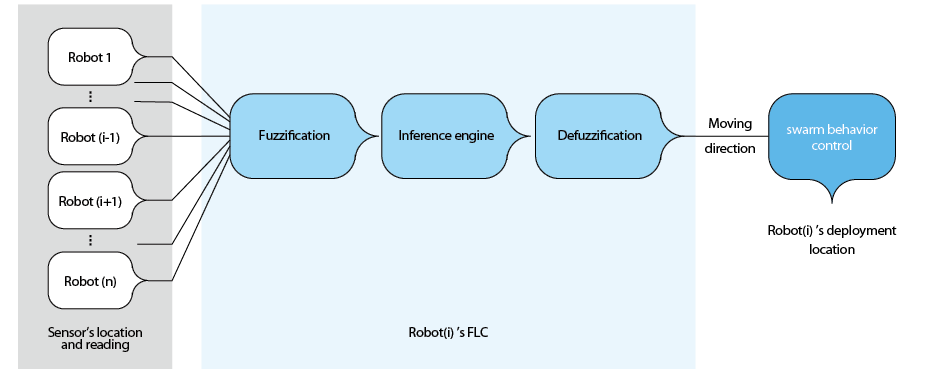
Design of the Particle Detecting Sensor
Accompanying with the progress of minimizing the wire width results in a demand for fast response system that provides information on particle diameter and concentration of monitor system for the particle contamination control. But current particle monitoring methods are not sensitive enough to measure a semiconductor cleanroom ambient, working offline and require extra personnel to collect and analyze the particle diameter distribution and concentration records in periods of time, which makes difficulties to response on the moment of the particle contamination.
A perfect particle detecting sensor should be inexpensive, small and robust providing particle contamination warning. These concepts may come true in the immediate future. For this reason, it’s an urgent need to have real time data of characterization of particle contamination in semiconductor cleanroom ambient. In the recent past, Bukowiecki et al, 2002, developed a real time characterization system of ultra fine particle on highways [2].
Thus we propose the application of a miniaturized device matrix of such instruments to form a particle detection and alarm system, which may be established by the formation of condensation particle counter (CPC) and the diffusion charging sensor (DC). The device should have high time resolution and cover very low concentration range and ultrafine particle diameters. Standard scanning mobility particle sizer(SMPS) has relatively slow response time and high installation cost so makes it difficult to use in the vast territory and changing environment in the cleanroom.
The Diffusion Charging Sensor (DC)
The DC signal is controlled by Brownian diffusion, and the current sensor measures the direct diffusion charging by the surface area of the particles. Usually keep the charging level as low as possible to prevent ions repulsion. In other words, DC measures the quantity of “active” surface of atom or ion attachment[3].
Where SA : Active surface
k : Boltzmann constant
T : Temperature
m : Mass
n : concentration of atoms
After the surface concentration and the total number concentration N of the particles are measured , we can assume the aerosol has the same surface area concentration and calculate the hypothetical mono-disperse aerosol.
Where DAve,S : Diameter of a hypo-thetical mono-disperse aerosol
Major type of aerosol in cleanroom is nuclei mode. The nuclei mode particle size < 100nm can pass through the high-efficiency particulate air (HEPA) filter in the fan filter units (FFU). The larger particles exceeding 100 nm for example coarse particle mode will be removed in the makeup air unit (MAU) and fan filter units filters. If the size distribution and surface activity of the particles do not change severely, the change in the total particle number concentration won’t influence the numerical value of DAVE,S. But it should be mentioned that on the calculation base, a shift of the characteristic diameter of the particles towards larger diameter, it will represent an increase in DAVE,S value.
N. Bukkowiecki et al.,’s research shows good correlation between DAVE,S(A) and DAVE,S(SMPS) in the particle diameters range from 20nm to 60nm since the measurement of the diffusion charging sensor active surface and number of particle counter (CPC) are separately independent, thus the value of DAVE,S could be a reliable index of the diameter of the particle shown as Figure 3.
Figure 3. Comparison of DAVE,S(A) and DAVE,S(SMPS)
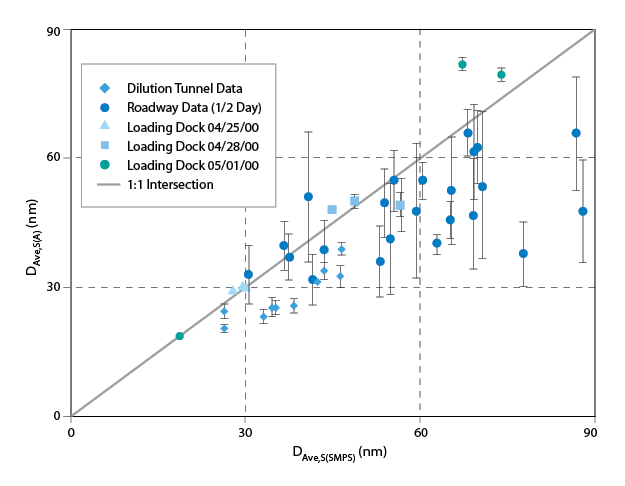
Diffusion size classifier
M. Fierz et al. designed and calibrated a miniature diffusion size classifier for field use, they shrunk the size down to 4x9x18cm,which stores data to a secure digital memory card (SD-card) and powered by built in rechargeable battery[4]. The key components of this instrument are unipolar corona charger and the electrometer. Unipolar corona charger is characterized by an estimate ion concentration of Nit=7.5x1012m-3 with a maximal corona voltage of ~5.5kV. The actual charging efficiency is measured by empirical calibration experiments, which shows high degree of statistic correlation, in spite of a noticeable charger loss down to about 20nm, which will make the instrument to underestimate the particle numbers smaller than this size.
Another key component is the electrometer, which measures current in a very low level of the charged nanoparticles. Thus it is very sensitive and vulnerable to the zero offset and noises. The main inaccuracies coming from zero offset error is the temperature fluctuation. In cleanroom ambient measurement, we may get rid of it. With regard to noise, it can be counted as the standard deviation of the measurement.
The diffusion size classifier comparison experiment is performed with of condensation particle counter (TSI model 3775) and scanning mobility particle sizer (UGZ), shown as Figure 6 and Figure 7, diffusion size classifier has less accuracy compared to the traditional instrument, but gets satisfying result to show the capability to detecting particles whose diameter less than 100nm.
Figure 4. Calculated penetration of particles through the unipolar corona charger
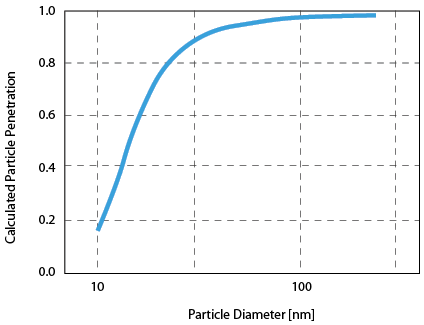
Figure 5. Experimentally determined charging efficiency
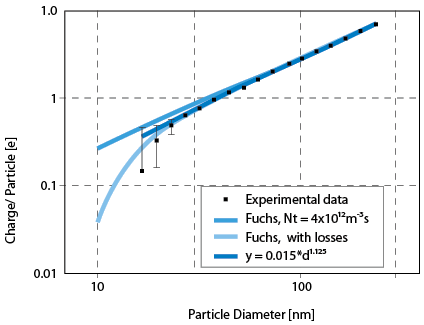
Figure 6. Compared with of condensation particle counter (CPC)
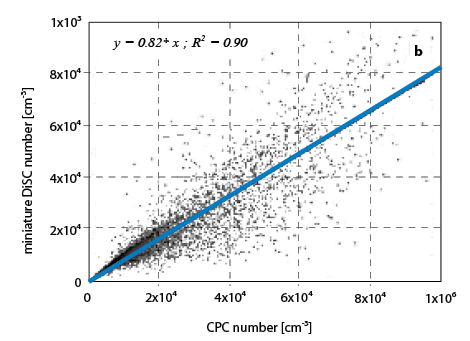
Figure 7. Compared with of condensation particle counter (CPC)
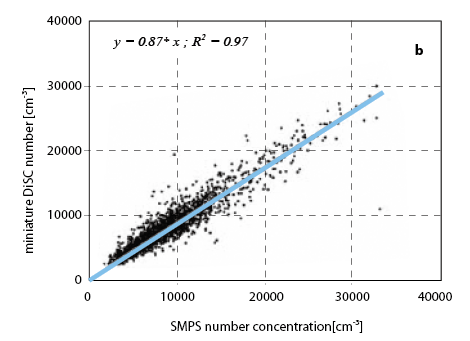
The diffusion charging sensor is a simple instrument based on unipolar charging, and the particle is charged approximately proportional to its diameter. Excess ions are removed in ion trap after the corona charger. The particle then goes through the diffusion stage, which consists of an electrical insulated stack of stainless screens. First, particles are captured and generate a diffusion current. Second, the rest of the particles then are arrested in the high-efficiency particulate air (HEPA) filter stage and also the filter current is measured. Because smaller particles are dominated by the Brownian motion and larger particles belong to inertia effected motion. The ratio of filter current and diffusion current can be a measurement of the average particle size.
R = Ifilter / Idiffusion
The diffusion charging senor in Figure 9 and Figure 10 should undergo instrument calibration from ccorresponding curve fitting before physical application Figure 8. The particle number can be calculated from the total current.
Figure 8. Calibration setup for the miniature diffusion size classifier (DiSC)
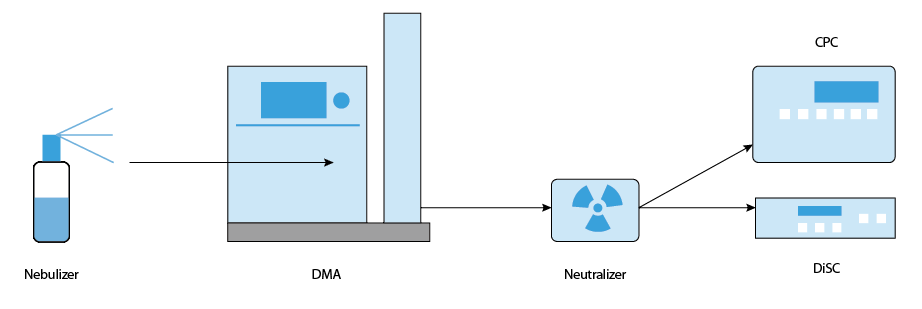
Figure 9. Schematic overview of the diffusion charging sensor[4]
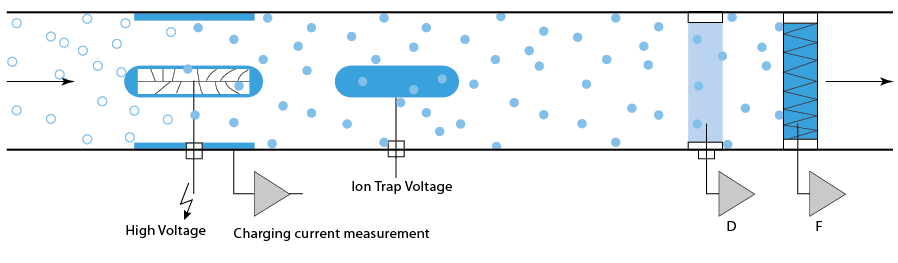
Figure 10. The miniature DiSC, measures 4x9x18cm,weighs 670grams[4]
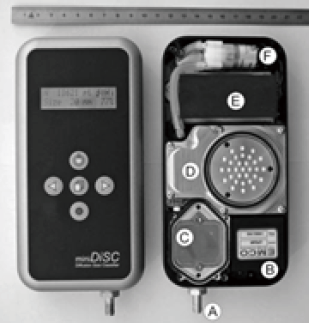
Itotal = Ifilter + Idiffusion
Where q : average charge
d : particle diameter
c : constant determined from the instrument calibration
x : 1.1 for the charger setup
Where N : particle number concen-tration
Φ : flow rate
This instrument has a limitation on the diameter of maximum penetration dMP about 500nmn and the standard calibration setup has a range from 20 to 240 nm by quasi-monodisperse NaCl aerosol.
Relevant Commercial Applications in Detecting Network and Miniature Particle Sensor
The Feral Robots project is an open source robotics project in 2005 [5], providing resources and support for upgrading the raison d’etre of commercially available robotic dog toys and equipped the robots with sensors figure 11. The robot dogs could follow concentration gradients of the contaminants and facilitates public participation in environmental monitoring and remediation[6].
Figure 11. Robot dog equipped with sensor to facilitates environment monitoring[6]
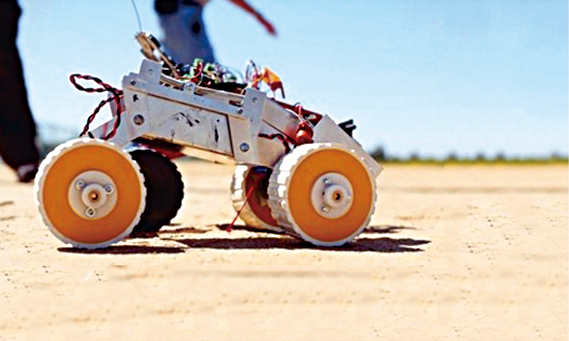
The 2009 R&D 100 winner, figure 12, NASA Mini-Classifier , which is a complete, self-contained differential mobility analyzer (DMA) that directly measures the particle size distribution of sub-micrometer particles(<100nm). The device design is based on the theory of unipolar field charging and integrated with computer for data logging and analysis, which is much more cost effective and offer better mobility to traditional scanning mobility particle sizer (SMPS)[8].
Figure 12. 2009 R&D 100 Winner, NASA Mini-Classifier[8]
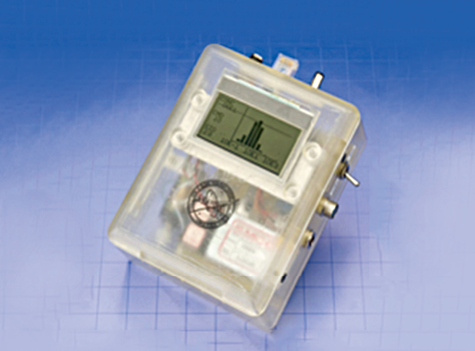
More recently in 2012, the scientists in Europe fitted chemical sensors on a robot fish to detect pollutant in the ocean.The robot fish shown in figure 13 are designed to swim independently but co-ordinate with the other robot fish to form a network monitorring water quality. Robot fish know how to return to base when their eight–hour battery life is running low and to communicate with each other and map where they are[7].
Figure 13. Pollution hunting robot fish take to the sea[7]
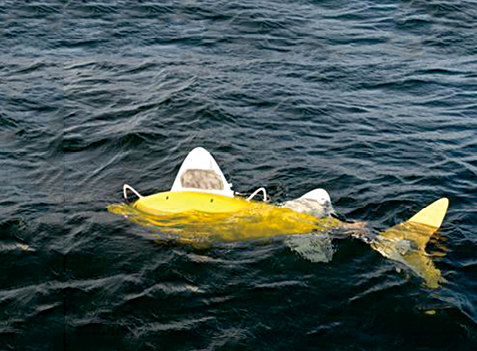
Result and discussion
In the constrained condition of limited quantity of scanning mobility particle sizer (SMPS) in a vast area, it’s not easy to localize the source of hazardous contamination with gradient seeking method. Exerting the advantage of scanning mobility particle sizer’s (SMPS) mobility, as compared to gradient seeking method, a dynamic ad-hoc network could perform cooperative exploration and sharing the measurement data to get information correctly and efficiently with much lesser sensors. Besides, the swarm-base fuzzy logic controller (FLC) approach could extract out the incorrect data and strain away the noises between the communications of the nodes.
Particle contamination in semiconductor fab may occur from the air supply of the fan filter units (FFU), the front opening unified pod (FOUP) gasket, wafer transfer robot joint or even from the metallization processed wafer surface. The source of the particle contaminant is variant and the behavior of contaminant propagation is dynamic, thus it needs a real time sampling system tracking particle from the moving robot and the sliding hatch gasket. Sometimes the consecutive action of process will accumulate heat and cause thermal desorption, static sampling may lead to a wrong direction to reduce particle contamination. Thus we could coordinate a few of scanning mobility particle sizers to form a flock based on a swarm behavior network to detect and localize the source of particle contamination. And the new miniature prototypes of particle detectors provide a low cost solution to make the particle contaminant tracking system to be feasible. Performance of the prototypes was compared in the laboratory with differential mobility analyzer (DMA) classified aerosol or scanning mobility particle sizer (SMPS) and condensation particle counter (CPC), the result is satisfied from the aspect of size and cost. We believe that the nanoparticle real time concentration detecting and source locating system will be put into practice in cleanroom in the immediate future.
參考文獻
- X. Cui, T. Hardin, R. K. Ragade, and A. S. Elmaghraby. A Swarm-based Fuzzy Logic Control Mobile Sensor Network for Hazardous Contaminants Localization. 2004 IEEE International Conference on Mobile Ad-hoc and Sensor Systems.
- N. Bukowieckia, D.B. Kittelsonb, W.F. Wattsb, H. Burtscherc, E. Weingartnera, U. Baltenspergera. Real-time characterization of ultrafine and accumulation mode particles in ambient combustion aerosols. Journal of aerosol science 33 (2002) 1139–1154.
- Siegmann, K., & Siegmann, H. C. (2000). Fast and reliable “in situ” evaluation of particles and their surfaces with special reference to diesel exhaust. SAE Technical Paper Series No. 2000-01-1995.
- M. Fierz a , C. Houle a , P. Steigmeier a & H. Burtscher. Design, Calibration, and Field Performance of a Miniature Diffusion Size Classifier. Aerosol Science and Technology. 45:1–10, 2011.
- http://www.nyu.edu/projects/xdesign/feralrobots/
- http://www.i-cherubini.it/mauro/blog/2008/03/17/feral-robots-and-environmental-health-clinic/
- http://www.reuters.com/article/2012/05/22/us-robot-fish-pollution-idUSBRE84L05U20120522
- http://www.rdmag.com/award-winners/2009/07/aerosol-analysis-compact-package
留言(0)