摘要
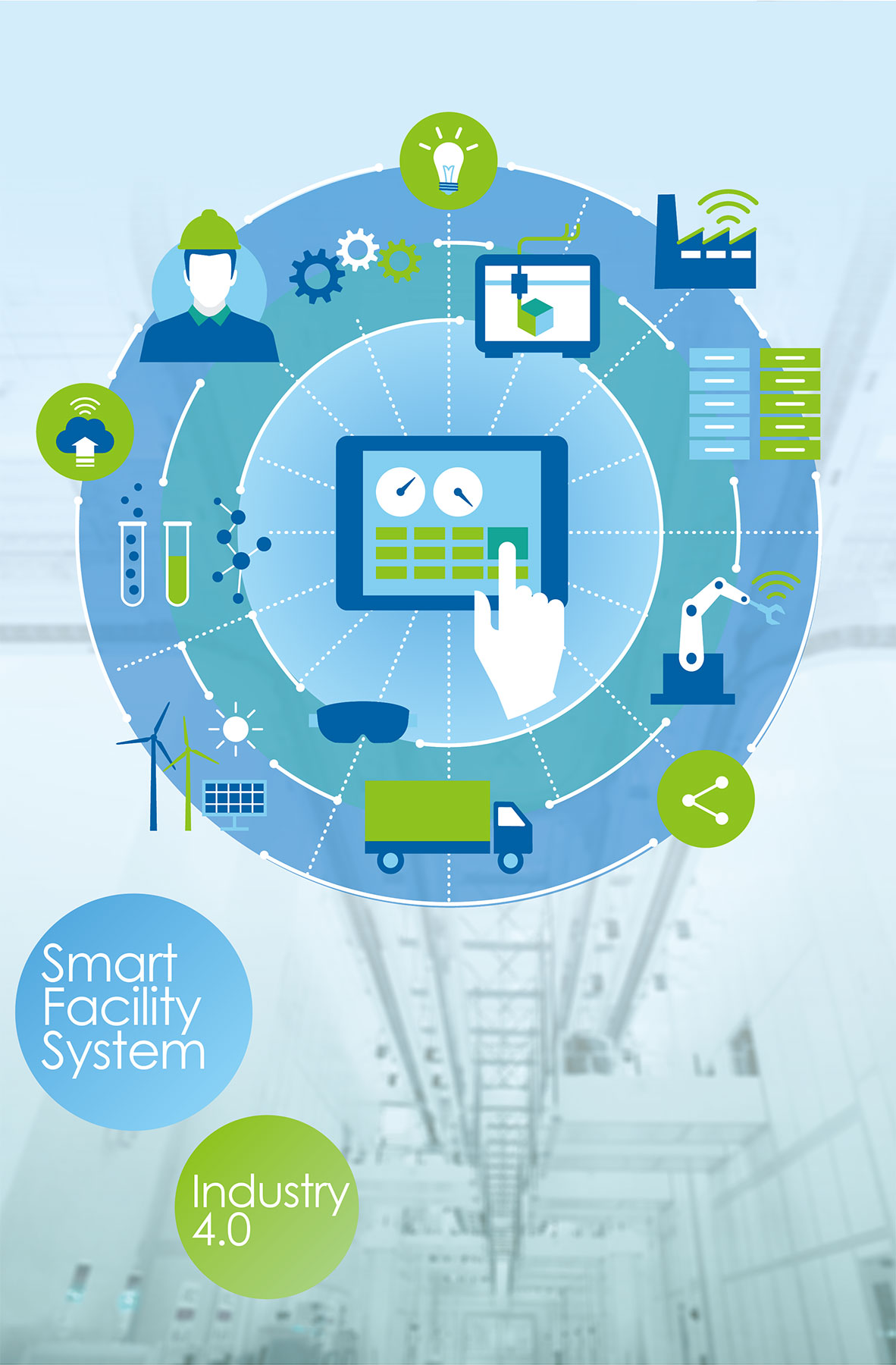
廠務系統智慧化的發展展望
近期由德國提出的工業4.0掀起極大的回響,一時之間智能化、智慧化、物聯網及大數據佔據大幅的報導及演講版面。本公司十二吋廠務部在自動化管理其實著墨已久,無論是自動化控制或是運轉資訊收集,均建立了良好基礎。本文將從介紹工業4.0的觀念切入,進而呈現目前本公司廠務系統智慧化的發展現況,並勾勒出未來可能的趨勢。
前言
工業4.0並不是以機器人取代人力,而是運用人機協同走向智慧生產。在未來的智慧工廠中,製造端上的每個機器都能夠透過物聯網(Internet of Things)相互對話,甚至能和上游的供應原料單位資料連結,讓工廠能夠輕鬆了解原物料供應狀況並即時因應。
簡單的說,就是大量運用自動化機械、感測器物聯網及大數據分析,以人機協作方式提升全製造價值鏈之生產力及品質。工業4.0的精神是連結與優化,連結製造相關元素,進行優化,透過優化後的結果,可以減少大量人力成本或許是產能提升,以增進企業競爭力與獲利。
然而在工業4.0高漲的潮流中,廠務能有什麼不一樣的改變嗎?例如以節能的觀點來看,可以應用大數據的蒐集與分析方法,找到用電量較大的設備或奇異點,進一步分析並降低不需要的用電量,達到省電省錢的功效;以智能化的觀點來說,大量的現場儀表數值,自動將數值回傳中控室,再透過智能化運算分析用水量、用電量、壓力、溫度,減少現場抄錶與手動計算等人力,再將關鍵係數給工程師做進一步的應用。
工業4.0的目標不是創造新的工業技術,而是統合所有工業相關的技術、銷售與產品體驗,是建立具有適應性、資源效率及人因工程學的智慧工廠(Smart Factory),結合自動化生產、物聯網等工業 4.0 概念,使廠務也能有效提高工作效率、減少人力應用、增加產能與減少資源浪費,藉此提升本公司在全球晶圓製造的競爭舞台。
工業4.0發展與沿革
人類歷史有三次工業革命如 圖1,工業1.0(第一次工業革命,18世紀至19世紀中期)時,運用水力及蒸汽的動力源,讓工廠開始機械生產;工業2.0(第二次工業革命,19世紀後半期至20世紀初)時,廣泛使用電力於大量生產;工業3.0 (第三次工業革命,20世紀後半期)時,則利用電子及資訊技術(IT)系統,讓工業製造自動化。而工業4.0可能帶來的第四次工業革命,則是透過物聯網互聯的溝通,達成資料的交換與統整,並透過雲端與大數據的分析,進而控制與改善實體工廠生產過程的產業價值鏈。
圖1、工業革命歷史[1]

工業4.0雖是德國最新提出的,但資源整合並非唯獨是德國工業4.0的目標。事實上,許多國家都發表了類似的綱領性文件如 圖2,只不過各有不同的提法,如美國的「先進製造業國家戰略計畫」、日本的「科技工業聯盟」、英國的「工業2050戰略」和中國的「智能製造」等等。誰能早日實現這一戰略,誰就在國際上獲得了「先發制人」的先機,擁有了標準制定者的地位。
圖2、各國對工業4.0 政策與技術重點[2]
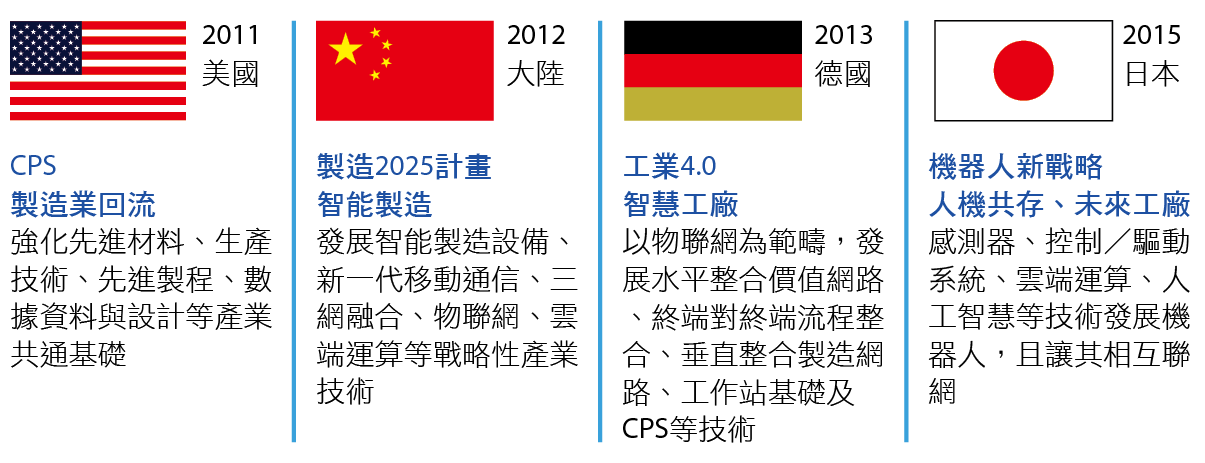
廠務智慧化發展的過去與現在
本公司廠務對於自動控制、資料蒐集與分析均具備優良模式和基礎,像是控制自動化、資料數位化及報表電子化,並透過日積月累的數據收集,叢集龐大的資源,透過運算剖析適時的提供部門決策分析,某種層面來說,亦為一種小型化大數據(big data),對於智慧工廠也已經鋪好一條平穩的道路。
自動控制系統
控制自動化:廠務在自動控制使用分散式控制系統(Distributed Control System, DCS)、可程式化邏輯控制器(Programmable Logic Controller, PLC)等系統架構如 圖3所示,搭配監控系統做到完整地自動控制系統。正常運轉情況,工程師只需處理異常事件,系統控制均為自動化處理。
圖3、DCS 自動控制架構
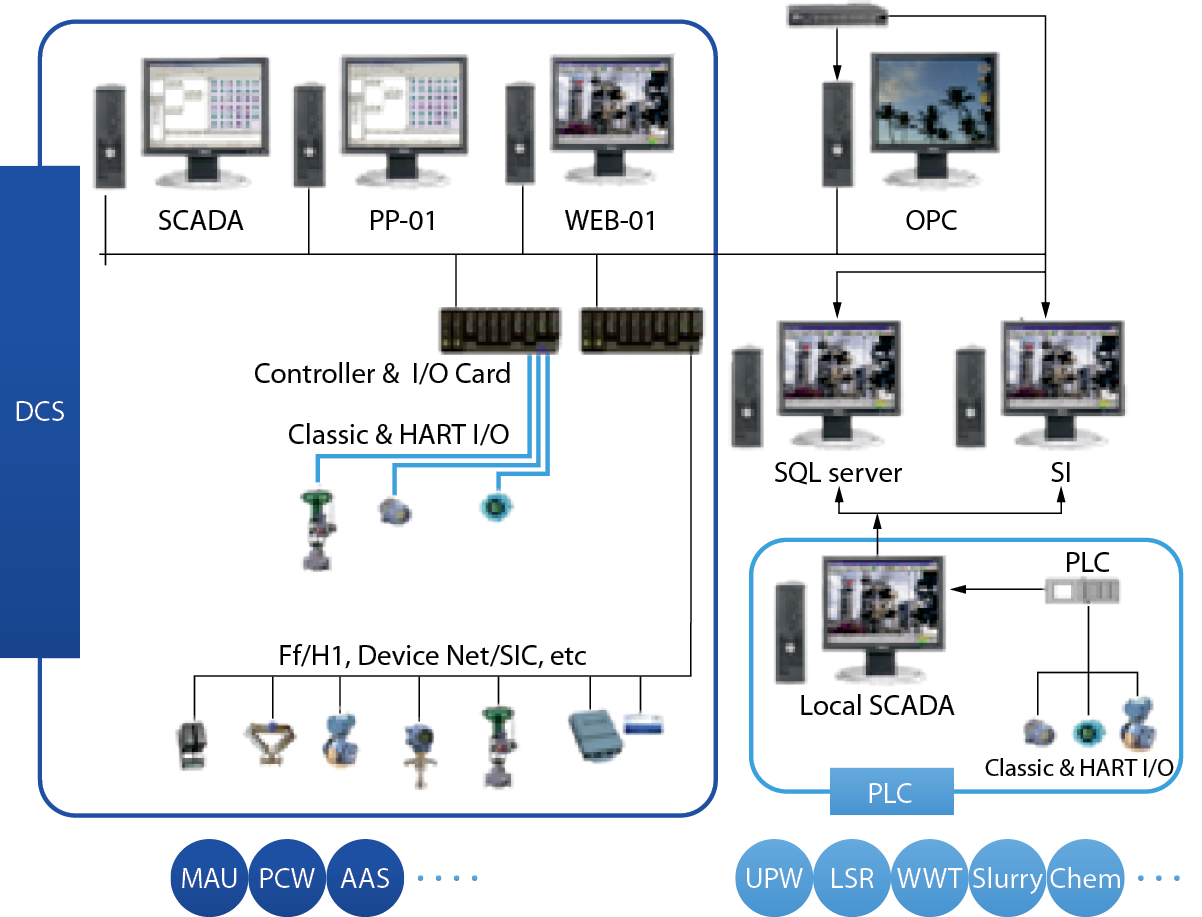
資料蒐集
儀表數值數位化:由現場儀表透過DCS/PLC回傳至SCADA並存放於廠務終端伺服器如 表1所示。早期數值須人員現場抄表、巡檢來確保系統穩定,而今透過不同的通訊協定將資料用數位的方式回傳並儲存,有利於降低人員工作量,亦鋪好日後分析的道路。
System |
Item |
Tag Name |
Unit |
Value |
1 |
2 |
---|---|---|---|---|---|---|
UPW |
No.1 UF UNIT OUTLET FLOW METER |
P6UPWA_FIQUPW2031_TOTAL |
M3 |
SUM |
4249 |
4202 |
UPW |
No.1 POINT OF USE RETURN FLOW METER |
P6UPWA_FIQUPW2032_TOTAL |
M3 |
SUM |
1315 |
1317 |
UPW |
No.2 UF UNIT OUTLET FLOW METER |
P6UPWA_FIQUPW2131_TOTAL |
M3 |
SUM |
3425 |
3419 |
UPW |
No.2 POINT OF USE RETURN FLOW METER |
P6UPWA_FIQUPW2132_TOTAL |
M3 |
SUM |
1045 |
1045 |
UPW |
No.3 UF UNIT OUTLET FLOW METER |
P6UPWB_FIQUPW2231_TOTAL |
M3 |
SUM |
4628 |
4730 |
UPW |
No.3 POINT OF USE RETURN FLOW METER |
P6UPWB_FIQUPW2232_TOTAL |
M3 |
SUM |
1441 |
1437 |
UPW |
No.4 UF UNIT OUTLET FLOW METER |
P6UPWB_FIQUPW2331_TOTAL |
M3 |
SUM |
2291 |
2285 |
UPW |
No.4 POINT OF USE RETURN FLOW METER |
P6UPWB_FIQUPW2332_TOTAL |
M3 |
SUM |
1526 |
1526 |
UPW |
UPW Loop1 to tool |
C3-C4 |
M3 |
SUM |
2934 |
2885 |
UPW |
UPW Loop2 to tool |
C5-C6 |
M3 |
SUM |
2380 |
2374 |
UPW |
UPW Loop3 to tool |
C7-C8 |
M3 |
SUM |
3187 |
3293 |
UPW |
UPW Loop4 to tool |
C9-C10 |
M3 |
SUM |
765 |
759 |
UPW |
UPW loop to tool Comsumption |
SUM |
M3 |
SUM |
9266 |
9311 |
自動報表
報表電子化:將現場儀表回傳之數值,透過資料庫做簡單的加減乘除運算以水課報表為例,即可算出當月或當天管路瞬時流量最大值、最小值及平均值,減少工程師手動計算時間,也能利用進階運算產出當天用水量,有助工程師透過自動報表達到分析決策效果。如 圖4所示。
圖4、數位上傳資料流
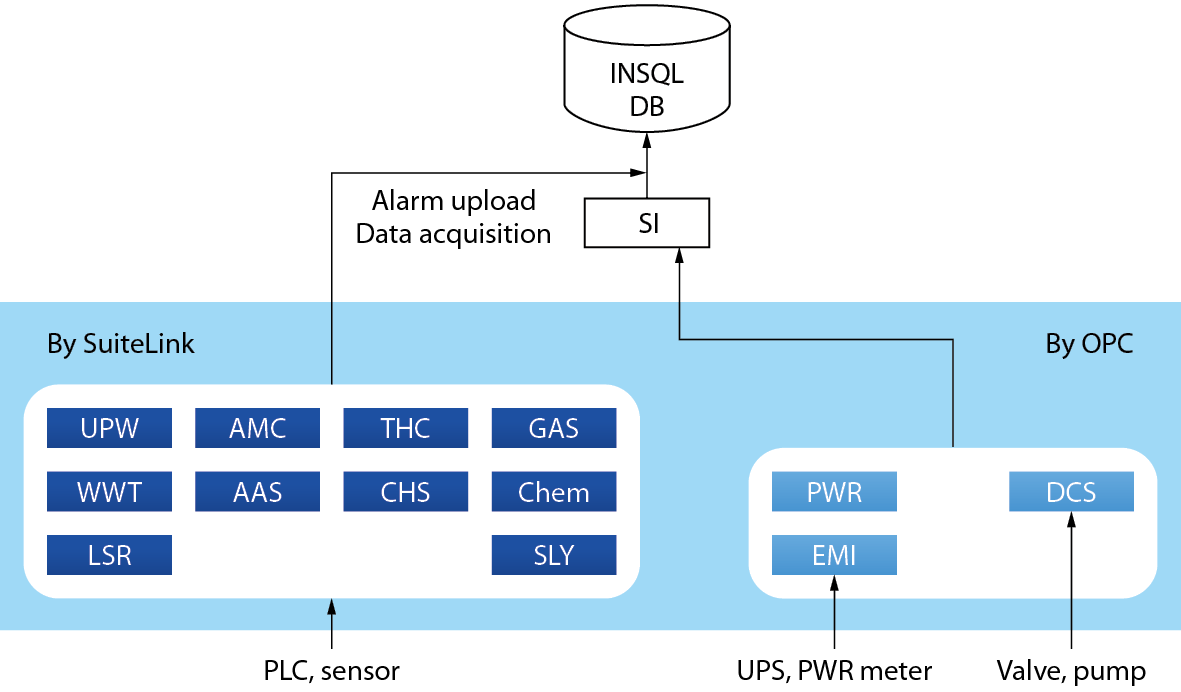
大量資料的蒐集可應用報表外,資料庫亦可透過大量數據分析,設計系統相對應的邏輯,即可自動判別系統的健康程度,若系統不健康,及時反應在平台上,告知單位主管與系統工程師,如 圖5所示。除了數值上的展現,也可看更直觀的趨勢圖(trend chart),主管與工程師可透過趨勢圖,準確看到系統的輸出情況,時間軸拉長,可看到整體趨勢是否變差或持平;時間軸拉短,可查詢異常當下輸出的變化,藉此提早預防系統問題與瞭解系統狀況如 圖6所示。
圖5、系統健康狀況平台(DIP)
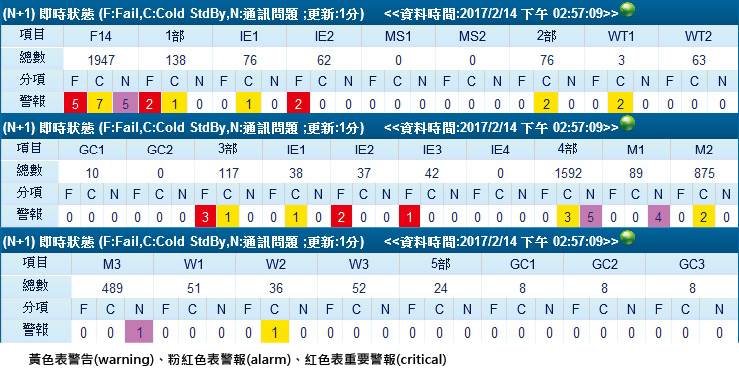
圖6、趨勢圖(auto trend chart)
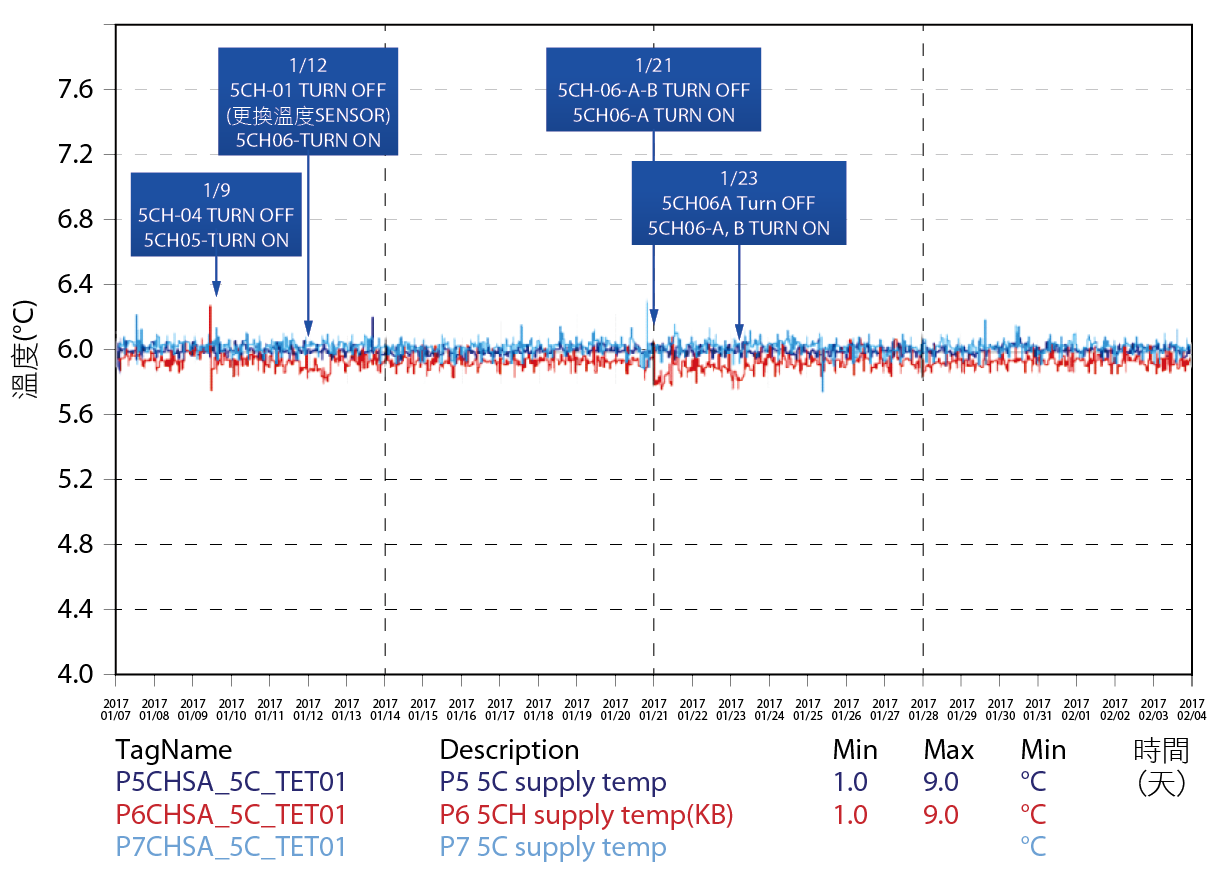
然而隨著節能議題高漲,善盡企業責任,降低能耗節省成本則是工廠內首當其衝的議題。舉例來說,用電方面,架設電錶在所有設備端,第一時間取得所有設備用電狀況,並將既有傳統電錶,改由智慧型電錶,不僅改善傳統僅能巡檢抄表的困境外,更能隨時藉由網路回傳用電度數,快速分析,藉由資料蒐集分析用電大戶的合理性、分布性,再藉此找出機會點,達到節能。如 圖7所示,重新設置一套全面性系統,來達到廠務節能智能化目標,也是現階段著墨的重點之一。
圖7、能源管理架構圖範例
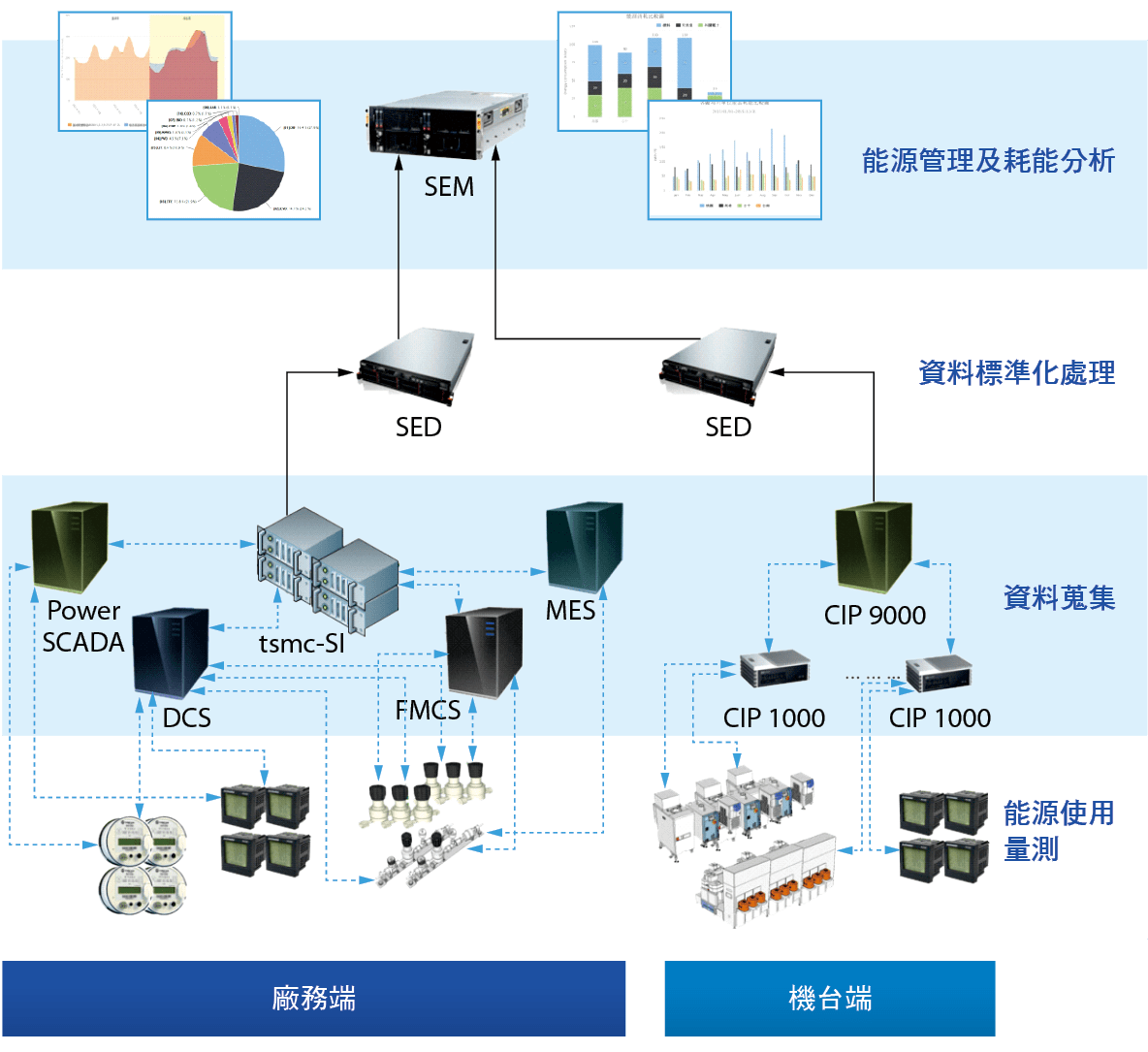
根據上述的介紹,可以看出雖然在自動控制、資料蒐集與分析已許多著墨,依舊需要靠人做最後的思考與決策,而我們知道快速分析複雜程度已經超越了依靠人腦去分析和優化的能力,因此,需要依靠智慧化技術去代替人的智慧進行複雜流程的管理,龐大資料的運算,決策過程的優化和行動的快速執行。因此未來廠務若能使系統向人一樣去思考和協同工作;意旨將資料蒐集分析後的結果,透過系統智慧化自動提出相關決策,由系統工程師確認決策內容,在由系統自動控制調整,不只全程智慧化亦將決策時間大大縮短,成為廠務智慧化往前的一大步。
廠務智能工廠願景
與其順著潮流,不如創造潮流,這就是領頭羊的概念。如何藉助大數據分析,以快速提升奈米製程良率,已成為國際半導體大廠的競爭策略,事實上,早在2003年開始,本公司已與清華大學簡禎富教授有密切的產學合作研究,希望透過挖礦(Data Mining)與大數據分析技術,協助台積電提升良率和智慧製造,針對低良率的晶圓進行分類,再挖掘造成低良率的製程、產品類別、設備、時間等可能的原因,發展分析模式,並結合演算法、資訊科技與圖形使用者介面,成為「良率提升系統」台積電以大數據提升製造智慧(Yield Enhancement System, YES)的核心。
此研究效益對本公司有卓越的貢獻,由於製程、機台裝戴的感應器約有500~1,000個,每分每秒製造的資料量以百萬筆記,此龐大的資料量需要用專業的大數據分析技術才可以辦到。反觀廠務的資料量雖沒如此龐大,但觀點是一樣的,在重要的設備上配戴感測器並透過數據回傳分析,不管是耗能分析、品質分析或是健康分析,若能在資料中,找到關鍵因子的固定行為模式,即可提前預測、預防,甚至突破!
以下將未來智能廠務分為三大類,再搭配應用範例介紹。
大數據分析管理
廠務的大數據分析,我們在乎的並不是數據的「量」,而是數據的「全」,即面對應用要求具有盡可能全面的使用樣本,以覆蓋廠務作業過程中的各類變化條件,保證從資料中能夠提取出反應對象真實狀態的全面性資訊,分析出的結果越能靠近實際狀況,此數據注重的是背後的物理意義以及特徵之間的關聯性,以防止分析出錯誤的決策,導致工廠造成無法彌補的傷害。
範例一:智慧警報系統
在擁有大量資料庫與人員經歷後的廠區,若能將此經驗灌入資料庫,透過工程師匯入的相關資訊,並由電腦自行判斷,發展出電腦的人工智慧,即可做到當有警報觸發後,即可在圖控軟體顯示可能造成警報之原因,並可選擇相對應處理方法,讓值班工程師有更精確的判斷。
範例二:品質預測系統
廠務有很多極為重要且會直接影響產能的條件(量測點),例如無塵室溫溼度、純水壓力等,然而會影響此條件的因素不少,往往品質異常時都已無法救貨。若能透過大數據的資料分析,預先發現影響條件的因素已出問題,則可當作預先指標,使廠務工程師提前修復或是提前預警設備端停機,防止問題擴大,保護公司資源,如 圖8所示為品質預測示意圖。
圖8、品質預測示意圖
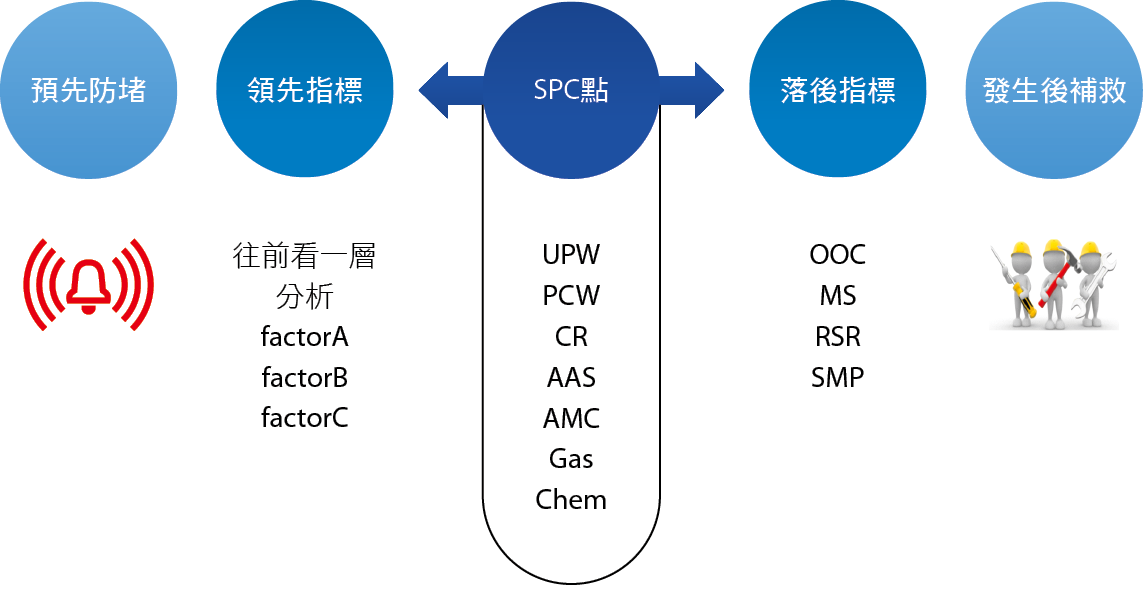
感測器物聯網應用
在工廠內,影響生產的大多是未見因素,比如設備性能衰退、精度的缺失、資源的浪費等。而可見的影響因素往往是未見因素累積到一定程度所引起,比如設備衰退導致停機、精度缺失造成品質偏差。因此對這些未見因素進行預測和管理是避免可見因素的關鍵。
範例一:轉動設備監診技術
我們知道機械設備內含許多轉動設備,若能將轉動設備安裝震動檢測儀表,透過整合平台評估設備健康狀況,建構有效的動態預防保養策略,降低機台故障異常的機率。根據經濟部能源局,更換高效率馬達最高可節省29%工業用電!若能使用高效率馬達,透過市面開發I/O模組以無線傳輸回傳至中控室電流監控,分析耗能馬達並有效規劃更換為高效率馬達以達節能效果,如 圖9所示。
圖9、轉動設備監診示意圖

自動化機械、廠務設備智慧化
現行的設備雖大多已自動控制化,設備本身卻沒有任何思想,只是接受命令,完成指令,意旨若命令錯誤,完成的指令亦錯;若能在自動化機械與設備加上人工智慧,自行判斷指令對錯,即可減少錯誤發生,也可避免蓄意行為。
範例一:智能照明節能技術
視覺化各區照明用電曲線,配合人員活動時間調配照明,遠端控制照明開啟時段;節能時段可運用微波、紅外線等感應元件,自動點滅局部照明,達到節能功效,並將用電曲線回傳,得知工廠各區域照明用電需求,藉此針對用電較低區域進行改善,如 圖10所示。
圖10、智能照明示意圖
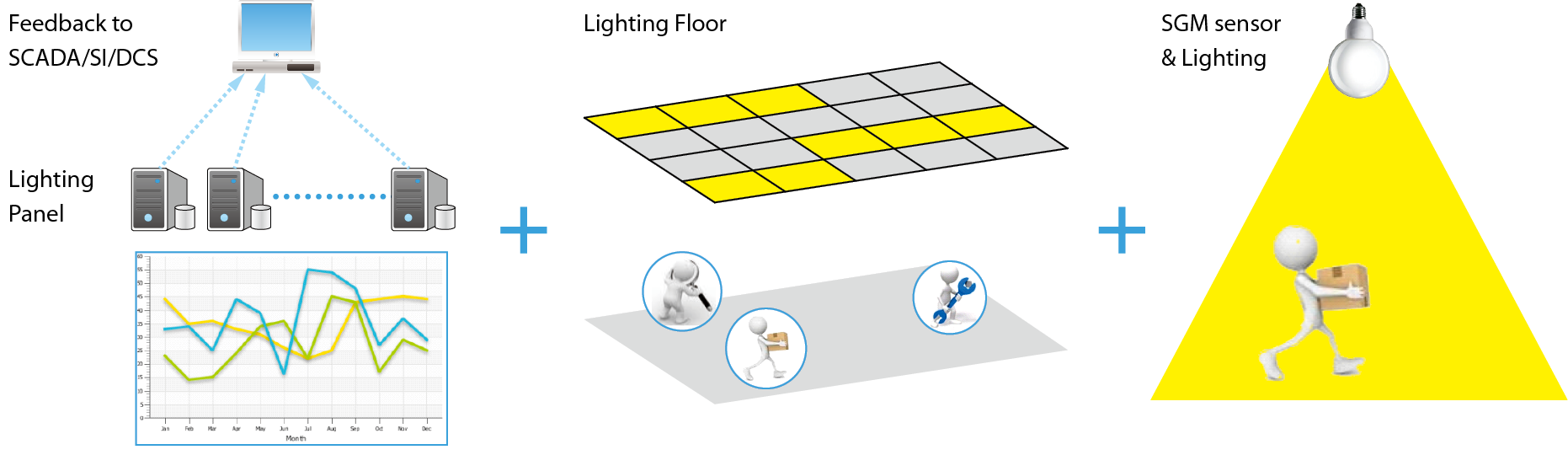
範例二:機器人應用
Pepper機器人正夯,在廠務裡亦可發展此相關應用,像是若能在自動遊走機器人上安裝照度、分貝等設備,在機器人大腦設定好巡檢路徑,即可在路線上自動量測並回傳數值,值班人員可透過數值知道現場狀況;或是在機器人頭上安裝攝影機,搭配圖像辨識功能,可以代替工程師到現場巡檢,並記錄所在位置。如 表2所示
項目 |
監工巡檢機器人 |
監測機器人 |
---|---|---|
Solution |
高風險監工: 從現有無人載具搭配麥克風矩陣、攝影機… ![]() |
現有無人載具搭配照度、分貝等設備+自建地圖/路線記憶 ![]() |
機器人 服務內容 |
圖像辨識(異象、禁入區) 警報即時回傳 地圖定位、自定義地圖 遠端廣播/對話 |
於定義路線上自動量測 資料/警報(OOC、OOS)回傳 |
導入效益 |
高風險作業違規即時回傳 緊急應變加速 落實高風險作業監視 |
可建立各種指標trend chart 可定時/連續量測 節省人力 |
範例三:虛擬實境技術導入
在實務上,廠務建廠時期,可以透過虛擬實境(Virtual Reality, VR),將工廠管線圖、規劃圖匯入VR系統,使用者只須配戴設備,即可進入虛擬的世界,彷彿看到建廠後之工廠模樣,了解動線、查看管路等功用;亦或是成廠後應用在新人訓練,配戴設備的工程師,只需在座位上就如同現場操作般,系統切換造成的視覺畫面均顯示在眼前與螢幕上,藉此了解系統實務,作為主管審核工程師是否具備專業能力的工具之一,如 圖11所示。
圖11、虛擬實境示意圖
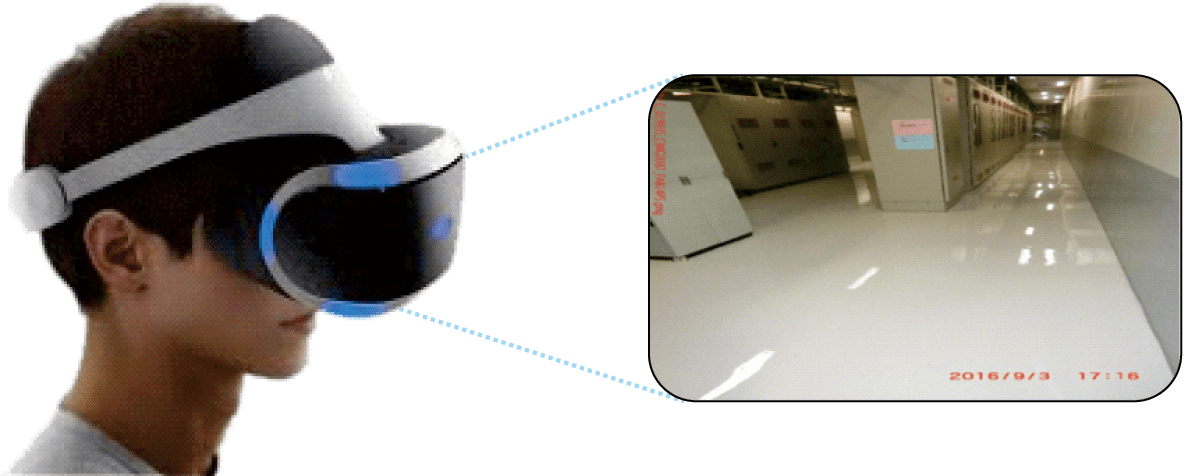
範例四:廠務智慧手機應用程式(FAC Mobile phone APP)
現行廠務手機已換成智慧型手機,其實廠內亦有許多應用程式可與線上連接,類似的功能也可應用於廠務,舉例來說,現今系統操作均需在圖控軟體施作,是否有機會應用手機直接操作圖控軟體,讓工程師在突發狀況時亦能用手機進行簡單的控制,並加入權限鎖定防止誤操作;或是平時工程師需看得報表與趨勢圖,是否可以直接透過手機查看,直接給予系統健康判斷,達到更智慧的工廠。
結論
工業4.0的核心並不在於進一步提高設備的效率和精度,而是如何更加合理化和智慧化地使用設備,透過智慧運算實現價值最大化。以廠務大數據來說,收集的資料是否完整,資料的物理關聯性是否有意義且被解讀,並搭配具有一定邏輯的資料流程分析手段,將資料轉換為有用的資訊,機會點可能是減少不必要的浪費,或許是系統異常前的徵兆提醒,均是未來可以著墨的地方。在廠務設備智慧化來說,感測器的精度下降、控制器的效能異常、機械轉動設備的磨損等均為現行未見因素累積引發;因為無法察覺,只能狀況發生後再解決,此為落後指標。若能將設備未見因素透過更多的資料蒐集、設備自我檢測功能及有效壽命預測等,推導成可見因素,形成先前指標,在未來的廠務將會是更大的助益,達到更穩定的運轉!
未來期許不僅電錶能夠透過網際網路建立連線,其餘微小設備也都能逐步更新達到"Internet of every-thing",不僅能更精準掌握全廠設施使用狀況,能源損耗等,讓工廠不僅智慧化更是智能化,並朝向U化(ubiquitous)邁進,讓網路智能無所不在。
參考文獻
- http://3smarket-info.blogspot.tw/2016/ 03/40_25.html
- http://www.ceu.org.tw/proArticle_content.asp?ano=1586
- http://topic.cw.com.tw/2016Industry4.0/article.html
- http://edm.ares.com.tw/dm/newsletter-2015-05-Industry4.0/focus.html
- http://www.srido.org.tw/masterblog/10
- https://scitechvista.nat.gov.tw/zh-tw/Feature/C/0/15/10/1/2432.htm
- 工業大數據-李傑著
留言(0)