摘要
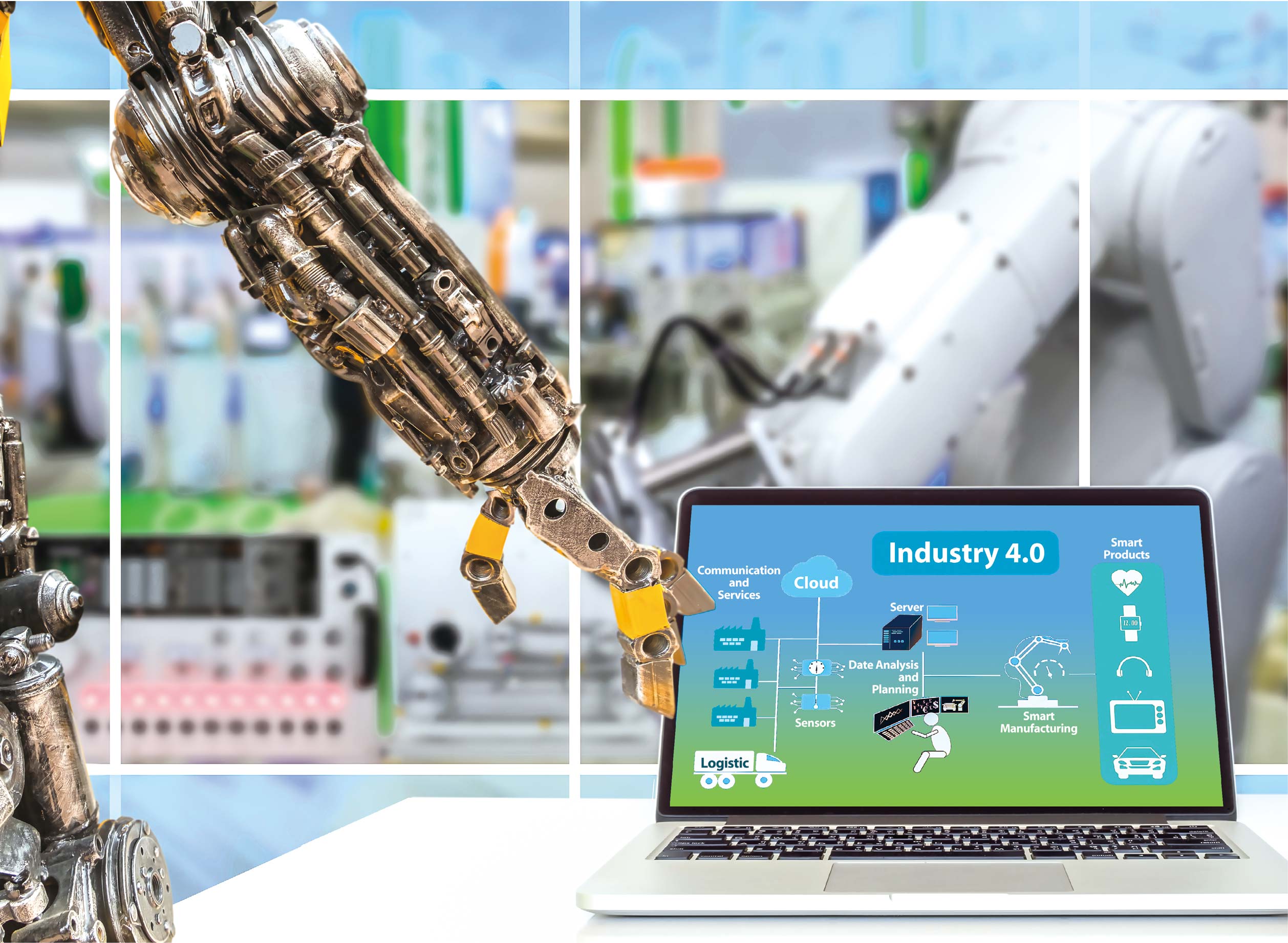
智慧工廠監控與製造業訊息管理概念
Keywords / Smart Factory,Industry 4.04,Overall Equipment Effectiveness (OEE)
隨著製造業發展與工業4.0概念的提出,工廠智慧化與製造資訊整合成為製造企業發展的關鍵。因此,在即時製造與彈性生產過程中,需要生產過程監控、產品品質管控、物流倉儲管理、生產能耗分析、廠務設備監控等系統,以實現智慧工廠的全面透明化管控,有效提供生產決策、降低管理成本。
前言
自2013 年德國提出「工業4.0」發展策略後,以智慧製造為主導的第四次工業革命開始在全球快速推進[1]。該策略旨在透過充分利用資訊通訊技術和網路空間虛擬系統—資訊物理系統 (Cyber-Physical System) 相結合的手段推動製造業朝向智能化轉型。
對此,各國工業電腦及控制器供應商不斷致力於研發工廠智慧化與生產資訊化應用,提供生產資料擷取、生產異常維護、設備全域管理、生產過程追溯,產線倉儲物流,廠務設施監控,生產能耗分析等系統的完整解決方案,內容涵蓋製造生產執行監控系統整合應用(Manufacturing Execution System,MES)看板管理、生產設備管理、網路設備管理、環境監控、設備遠端雲服務等的生產程序控制與資訊系統。
背景
面對智慧工廠及智慧製造強勁的市場需求,無論是軟體或硬體層面,不少台灣企業已邁向工業4.0的新趨勢發展,其發展面涵蓋自動化控制器、遠端I/O、人機界面、工業網路通訊、工業閘道、SCADA 及Web-Server 展示軟體,其已廣泛使用於全球各地的生產製造執行系統與廠務設施管理中。
工業4.0的實踐分為三個階段,第一階段是針對設備領域,做到全面的設備感知與聯網,以達到資料透明化及生產資訊視覺化,第二階段是做設備資料與生產訊息的整合及資訊分析,以提供第三階段智慧設備與大資料分析所形成的智慧服務[2]。並透過智慧設備與資訊整合,助力智慧製造進一步發展,並提出工業4.0六大範疇 [3](如 圖1所示)—設備自動化、設備監診與效益優化、機台監診與預防保養、MES整合及生產履歷、廠務能源管理、廠務環境監控—以整合的自動化系統與雲端創新技術邁向工業4.0。
圖1、工業4. 0 的六大範疇[3]
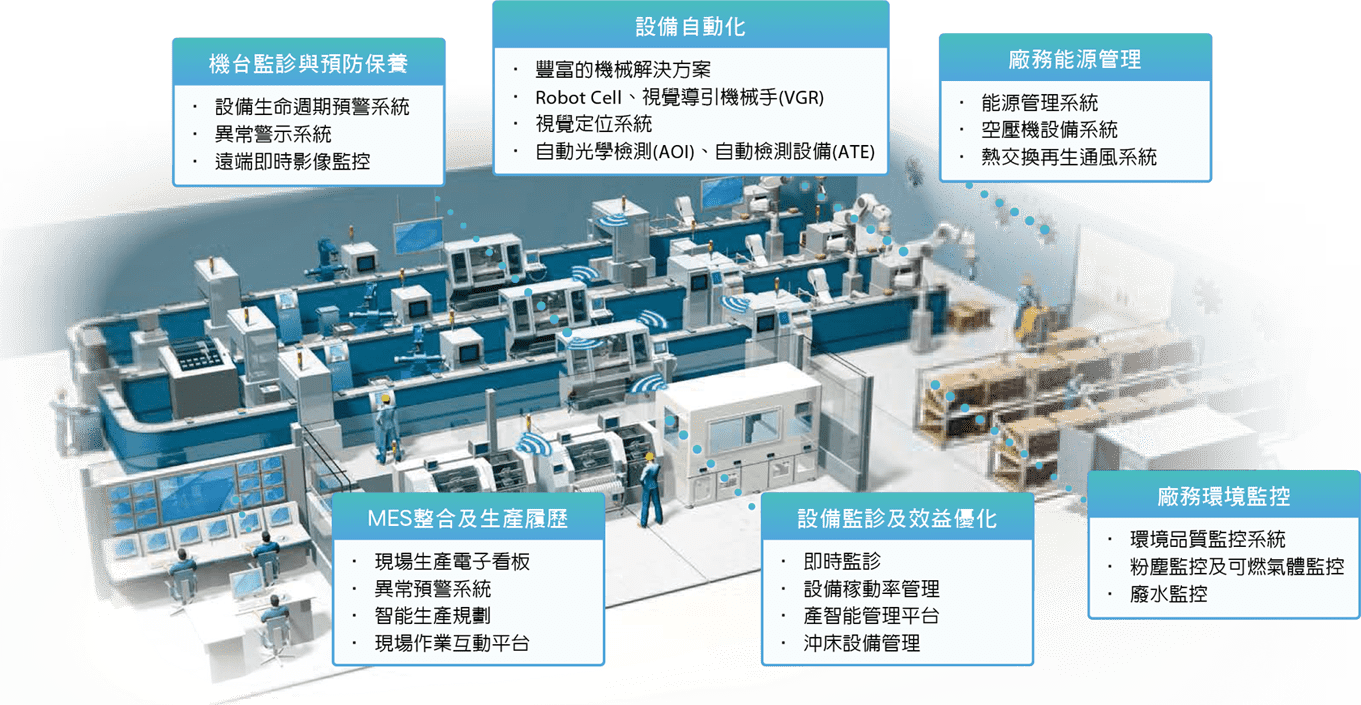
整體設備效益管理
實現智慧製造除了自動化更要做到智能化,除了大數據採集的基礎建置之外,對於產線設備穩定性所衍生的預知預防與各系統間之整合應用,以及節能減碳之相關議題更是邁向智能製造不可或缺的要素。以下舉出四個方案,分別為整體設備效益管理、廠務監控、廠務能源管理、生產與廠務自動化綜合管理[4]。講述設備自我健診及告警,其監控畫面以圖示化顯示設備及廠務系統運作狀況,有助於使工廠邁向智能製造之路。
通常生產線需面對龐大繁雜的設備及多樣化的生產過程, 而設備在生產過程中存在設備異常停機、維修等待時間、不能滿負荷運行、加工品質波動等問題,經常因故障原因不明確、維護不即時,缺少對設備維護保養精益管理依據和手法。整體設備效益管理(Overall Equipment Effectiveness, OEE)逐漸成為企業生產維護管理的重要手段,其通過即時採集生產現場設備運行資料,全面監視設備運行情況(如 圖2所示),實現企業、產線、設備等多級別OEE的精確計算,幫助企業分析設備績效落下的真正原因,以提升生產能力,優化生產流程。
圖2、智能設備整合分析[1]
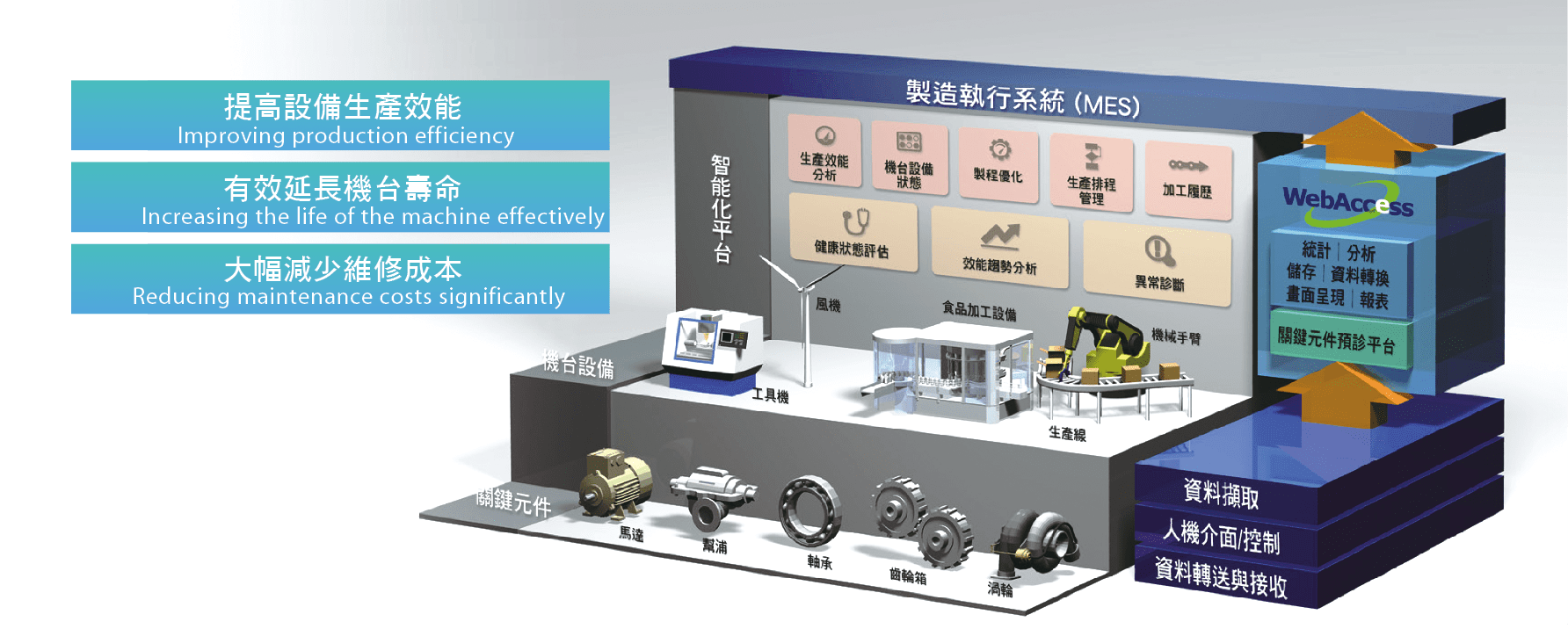
自動數據採集系統
針對生產過程中的加工、檢測、包裝、物流設備的日常管理,提供數據採集功能,通過分散式網路架構、多樣化的傳感、採集與通訊產品直接設置在現場各個加工設備旁,各種協定的透明傳輸可將設備的開停機、異常故障及代碼、模具調試、等料時間、設備維護、正常生產有效時間,以及加工參數等數據即時上傳至管理系統。藉此有效避免人為錯誤干預,保障資料真實性。
全面保全維護
基於自動化的資料採集建立軟體管理與看板提示系統,提升事後維修、設備點檢、預防維護、計畫保養效率,並透過全員參與培訓,提高維護意識與維護技能。
績效管理目標
透過建立OEE 系統對設備稼動率、人員績效、物料品質做綜合分析,並透過圖表和資料找出人員出現的問題和影響設備綜合效率與生產效率的原因,並量化分析,進而改善並提高產線的整體產能(如 圖3所示),提升設備維護保養管理水準。
圖3、智能產線可視化[4]
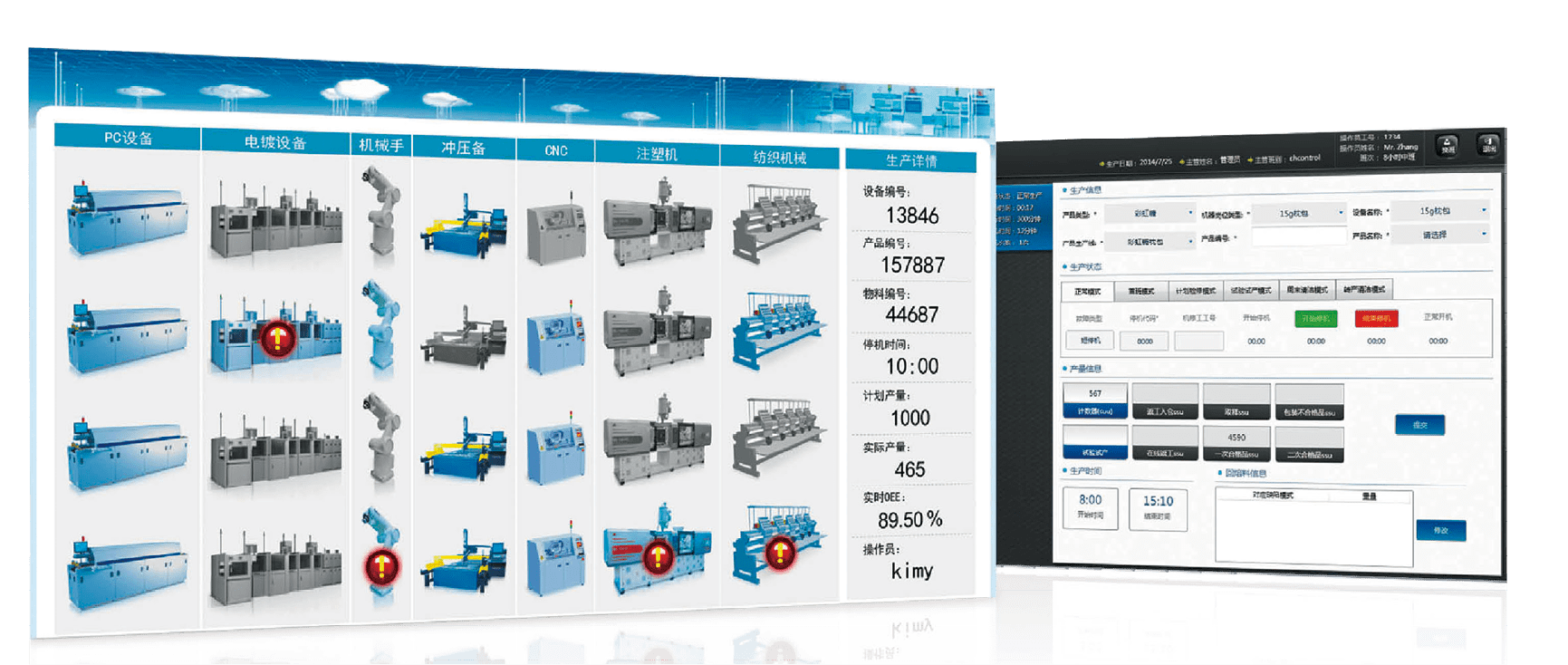
廠務監控
廠務監控系統(Facility Monitoring Control System,FMCS)是對各種工業設施的運行狀態進行集中監視及遠端控制的自動化管理系統,主要包含Room 無塵室系統、CW制程冷卻水系統、AAS 廢氣減量系統、UPW 超純水系統、WWT 汙水處理系統、Gas氣體供應系統、Chemical 化學品供應系統、HVAC 中央空調系統、Calamity 逃生消防系統、PV 制程真空系統、CV 潔淨真空系統、CDA 壓縮機乾燥空氣供應系統、Power電力監控系統、Door Alarm 門禁監控系統與鍋爐供熱等系統(如 圖4所示)。其主要特徵是採用可編程自動化控制器和資料擷取模組與通訊管理電腦將各個工業設施的子系統的運行資料連接至中央監控室或者管理人員電腦,形成一個網路化監控系統,管理中心通過對各個子系統的獨立維護,全面管理,綜合分析實現對工廠設施的全面體檢。
圖4、圖控化功能介面[1]
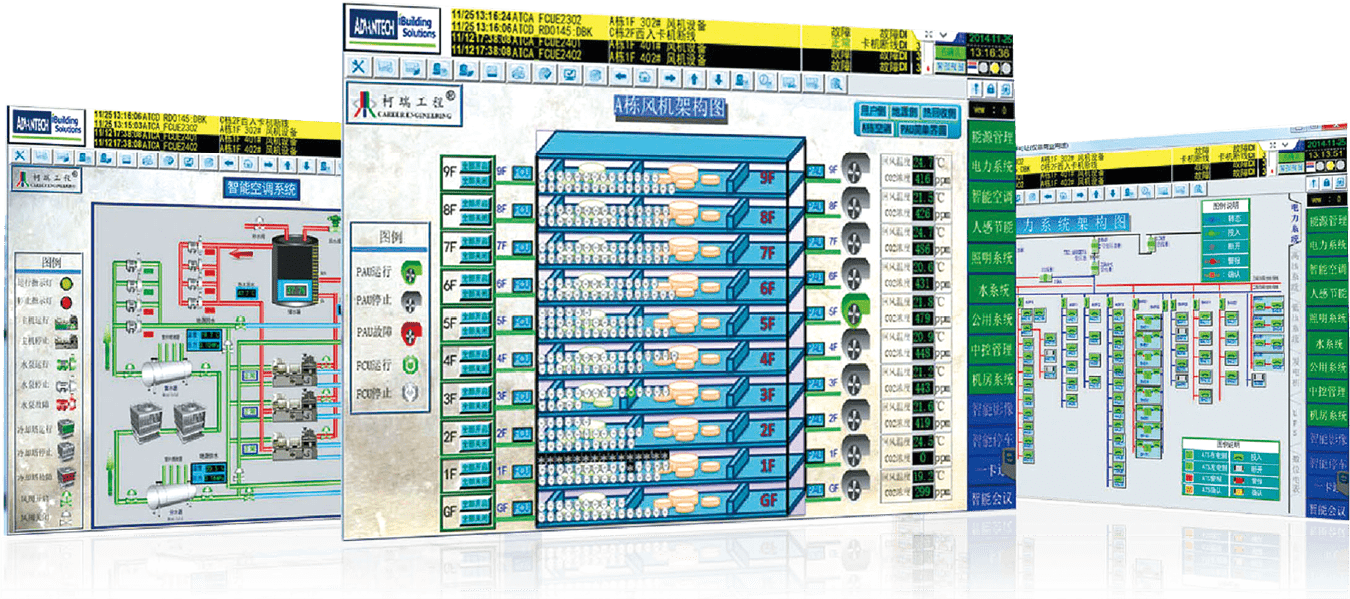
FMCS 系統按控制策略採用分散式結構的監控系統,依照控制級別可分為四層:
現場設備層
包括各類感測器、變送器、探測器、閥門執行機構、變速設備、馬達電機、限位元開關及其他相關工程設備及裝置,實現對現場資料的上傳和控制器命令的執行的功能。
控制層
包括可完成單元層操作的軟體和硬體。例如單回路控制器和可程式設計的自動化控理器等設備,實現對底層設備的資料採集,下發控制命令,監視現場控制情況的功能。
通訊傳輸層
現場設備層至現場控制器層,有兩種資料傳輸途徑。一種是控制電纜,應用於常規I/O 點數據的傳遞;一種是現場匯流排,應用於自帶控制櫃和網路介面的成套設備的資料傳遞,以及遠端I/O 模組與主控制器之間的通訊。現場控制器層至管理層的數據傳輸,以及控制器層本次通信、管理層本層通信主要依靠的是乙太網。最上層的企業管理層網路,主要用於企業的計畫、銷售、庫存、財務、人事以及企業的經營管理等方面資訊的傳輸。
FMCS 軟體管理層(SCADA)
分為現場子系統管理和全廠管理。管理層包括操作站、工程師站、主要伺服器、OPC 伺服器、WEB 伺服器、熱備份伺服器、圖形印表機、報警印表機、SCADA 用的HMI 軟體等。現場子系統管理主要完成各子系統的監視和操縱,進行現場資料的提取,並將資料作為集成系統的OPC Server 資料來源,現場子系統管理是確保各子系統獨立運行的基礎。全廠管理是監視和管理中心,負責整個系統協調運行和綜合管理。全場管理系統接受各子系統的運轉資料、狀態、報警,趨勢圖,歷史資料,遠端監控 資料管理與分享,異常和故障狀況排除,運轉模式建立,控制策略修正。
廠務能源管理
製造業能源消耗主要包括水、電、氣三大部分。水包括生活用水、工業用水和冷凍水等;電包括工廠總用電和單台設備用電等;氣包括壓縮空氣、天然氣、蒸汽和各類工業用氣等。企業的能源品質直接影響產品的優劣,能源消耗直接影響產品的成本,進而影響到企業的競爭力。此外,能源的合理使用與平衡調配,對環境保護也有著極高的重要性。透過建設全廠級集中統一的能源管理系統可對能來源資料進行線上採集、計算、分析及處理,從而實現能源物料平衡、調度與優化、能源設備運行與管理等。
林口某製造工廠辦公大樓為例,其水電氣相關之廠務設備布設感應器,將數據結合進能源管理系統,運用於能源計量設備、能源採集設備、能源網路、能源監控中心管理分析軟體等能耗相關系統,其功能分別為:
一屏總管
匯集資訊,統一警示,融合分散式控制架構,提升系統穩定度。
物聯運算
透過資料分析實現智慧操作。自動生成客製化報表,提升人員工作效率。
舒適節能
以最佳體感為基礎,結合氣象資料,最佳化室內溫度。追蹤重大設備運作效率,作為大樓健檢的管理平台。
結果與分析
以某林口製造工廠辦公大樓能源管理為例,採取智慧控制,並持續改善管理效果。 圖6顯示,經歷一年的摸索與實踐,2016年與2015年相比,節能效益達19.4%。預計2015全年節約46.7萬度電,節費達163.4萬,每年減少碳排2,967公噸。
圖6、某林口製造工廠辦公大樓2015 年間能源管理成果
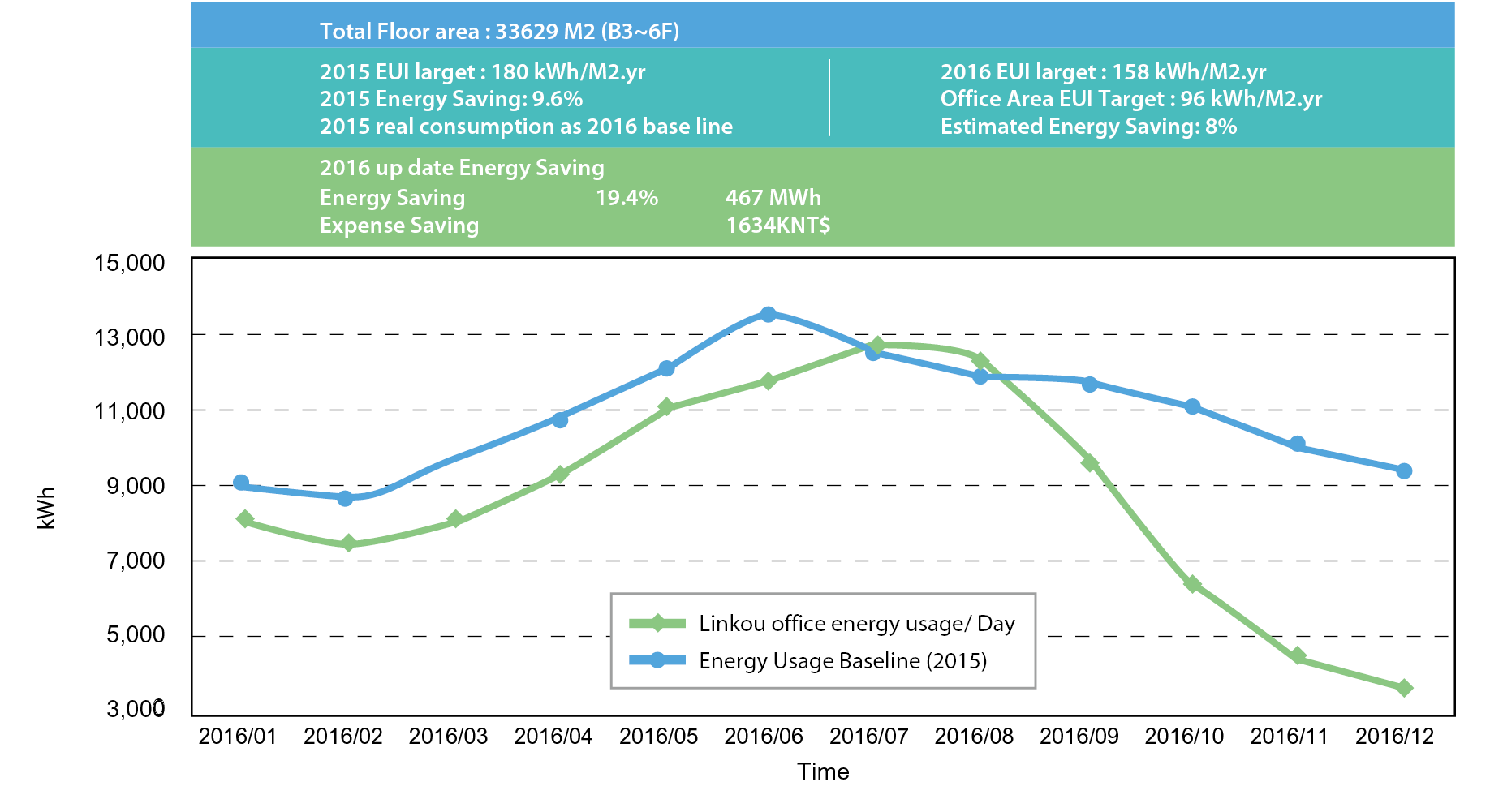
生產與廠務自動化綜合管理
某從事印刷線路板之設計、開發、製造、銷售一體的電子企業,中國多個城市設有生產基地,每個分基地工廠有逾15個廠房的加工車間,各廠產品皆有不同流程,由不同機台組成生產過程,所需及消耗的原料與配件也不盡相同。該企業提倡將生產基地的機台狀況、生產過程、品質管制、公共安全、物料管理等組成完整的管理系統,實現「生產與廠務自動化綜合管理」。因此,管理者需建立一套綜合管理系統,可將有形機台、物料與數位錄影連接起來,從而便捷精准的掌握生產過程、生產品質與效率、產量與進度、公共安全、物料消耗等,最終在提高對生產過程的科學管理的同時為改善生產過程、降低消耗提供基礎資料。
設備網路化整合
生產車間以表面焊接、電鍍、蝕刻、顯影、清洗、曝光機、PLC控制為主,輔助設備包含空壓機、儀錶、變頻器等所有設備通過多類串口通訊設備或類比信號模組。部分車間與廠區間已有存在的網路佈局、伺服器、防火牆安全,可方便接入,而不存在網路的區域得增設設備通訊佈線經過交換機實現跨廠區資料穩定交互同時具備網路管理功能,用以檢測設備與輔助生產設備協定轉換調試。
監控系統化管理
綜合管理系統需容納多個廠,數百個車間眾多設備的統一管理,其系統包含整合生產及量測設備過程效率管理、機電設備運維管理、電力調度監控管理、視頻即時監控及門禁(車間閘門控制)納入系統整合,系統整合管理之簡易架構圖如 圖5所示。通過跨設備、跨平臺、跨系統的集中管理,針對不同的監控物件設置相應的閥值統一展現與告警,使得管理人員可以快速準確發現被管理的設備設施故障之處,在尚未故障前維修完畢來降低生產風險。
圖5、生產機台系統整合管理架構
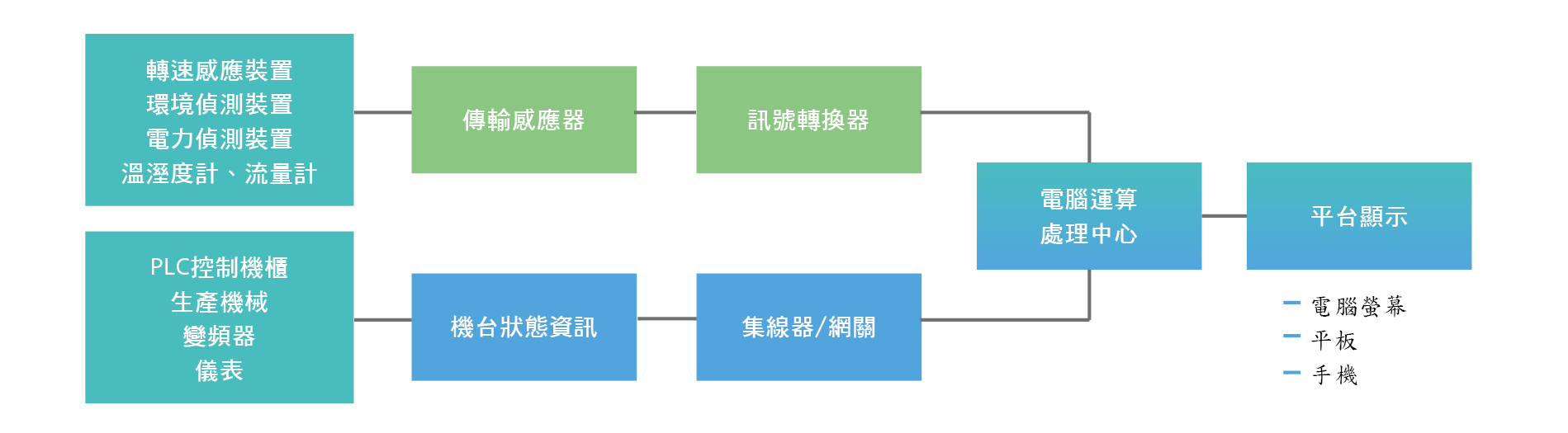
結論
伴隨工業4.0概念深植人心、多項技術漸趨成熟到位之下,製造企業從傳統生產模式轉型為智慧製造模式。然而工業4.0與現階段自動化製造最大的差異在於「整合」,目前製造業其功能系統大都獨立分工,且現場設備數據仍有多數是透過人工抄寫或尚未資訊即時化,透過工業4.0的智慧整合,讓不同設備可以互相溝通、即時監控周遭環境,製造流程也將更靈活,智慧製造不僅有助提升生產效率、降低營運成本,還可幫助企業妥善因應客製化生產趨勢。
然而製造業要真正全面落實「智慧工廠」非一蹴可及,而是階段性來達成,工業4.0六大範疇—設備自動化、設備監診與效益優化、機台監診與預防保養、MES整合及生產履歷、廠務能源管理、廠務環境監控,其執行模式也非全面性導入,而是以企業本身生態鏈所面臨的痛點去理出階段性的解決方案,來逐步落實工業4.0轉型目標,以期能提升產能與在品質上發揮統籌運用的綜效及企業競爭力。
參考文獻
- 研華期刊 Autumn 2016 NO.38 P.16, 21.
- 李傑,工業大數據:工業4.0時代的智慧轉型與價值創新,天下雜誌股份出版,2016。
- AIfons Botthof, Ernst Andreas Hartmann,譯者劉欣,工業4.0:結合物聯網與大數據的第四次工業革命,四塊玉文創出版,2015。
- 研華產業應用型錄-智慧工廠監控與製造業訊息管理解決方案。
留言(0)