摘要
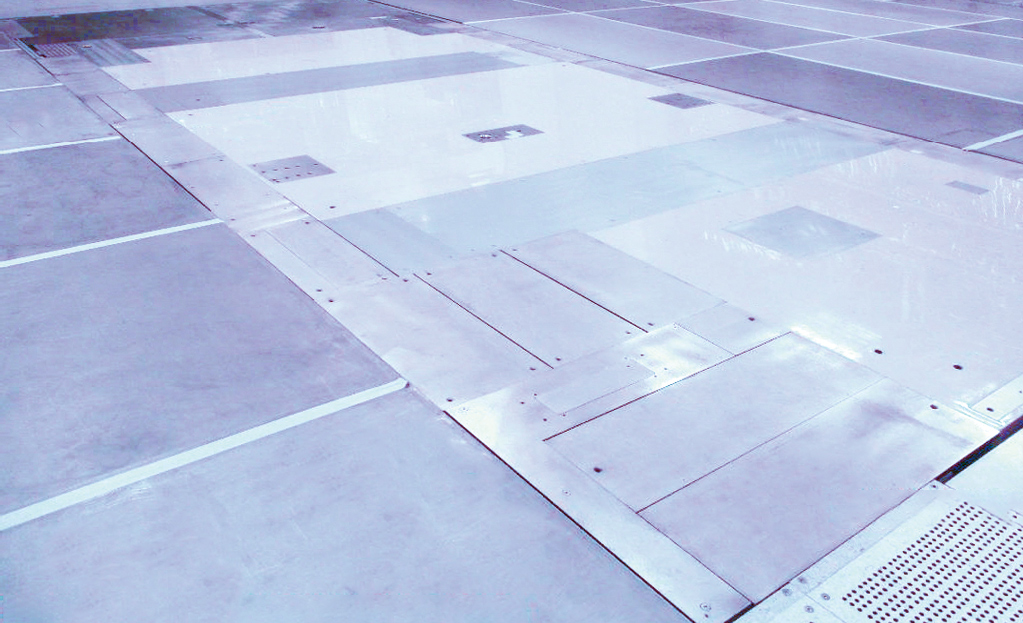
談極紫外光微影掃描設備基座安裝
Keywords / Extreme Ultra-Violet (EUV),Foundation4,High-Precision Measurement,Computer Numerical Control (CNC)
現今半導體先進製程產業已是不進步就是退步的高度競爭之中,隨著產品愈來愈精密,設備機台對於安裝環境的需求也相對愈來愈高。以基座(Foundation)而言,從一開始的載重需求至微振動需求,進而增加剛性的需求,每一個需求都會增加設計與安裝上之難度。Foundation的設計,不論在載重能力、微振動需求、剛性需求都必須達到其高精度要求規格,而安裝過程中,每個孔位之精度規格需求更是高精密規格。為達到其要求之精準度,裝機工程單位引進高科技精密萊卡3D追蹤儀進行輔助安裝檢測,如此才可達到設備要求,並順利裝機。本文將探討在各個階段中, 曝光機(Scanner)基座的發展、製作與安裝過程,而敘述重點會著重在極紫外光微影(EUV)之Foundation介紹。
前言
以往基座(Foundation)標準安裝流程,從圖面確認開始到現場放樣安裝及完工後的檢驗需求,僅使用簡單概略之水平儀、捲尺等工具,便可達到所需精度,且順利達成裝機之需求。
而本文所介紹之極紫外光微影(Extreme Ultra-Violet, EUV)Foundation則不然,從圖面確認開始即可確認該安裝所要求高精度規格,雖仍可使用水平儀、捲尺等相關工具,但因精度要求增加使現場安裝難度提高且不容易符合安裝需求,因應安裝精度的增加,工廠製作部份也由傳統加工,改由電腦數值控制(Computer Numerical Control, CNC)加工工具機製造,已達現場安裝順利符合需求。
而後續之檢測(微振動、剛性、硬度、平坦度檢測)工具等,也因規格的增加皆需使用較精密之微振動、剛性測試儀器,並且在儀器操作者的熟練操作下使可完成檢測。安裝量測器具部分,由傳統之捲尺、水平儀,增加了3D追蹤儀以及安裝制具,以縮短現場安裝量測時間。
另外,EUV Foundation完全跳脫2D平面之設計概念,所有安裝及尺寸檢測,任一個順序環節錯誤,即可能造成安裝精度上之誤差,且針對高剛性的需求,更是對設計與安裝人員提出更高的挑戰,目前經歷過這麼多已安裝完成之基座,每一座不論在工廠製作、現場安裝、安裝完量測上都有持續再進步及精進的空間。EUV Foundation各組成的配件,如 圖1所示。
圖1、EUV Foundation組合圖與光束傳輸系統(BTS)
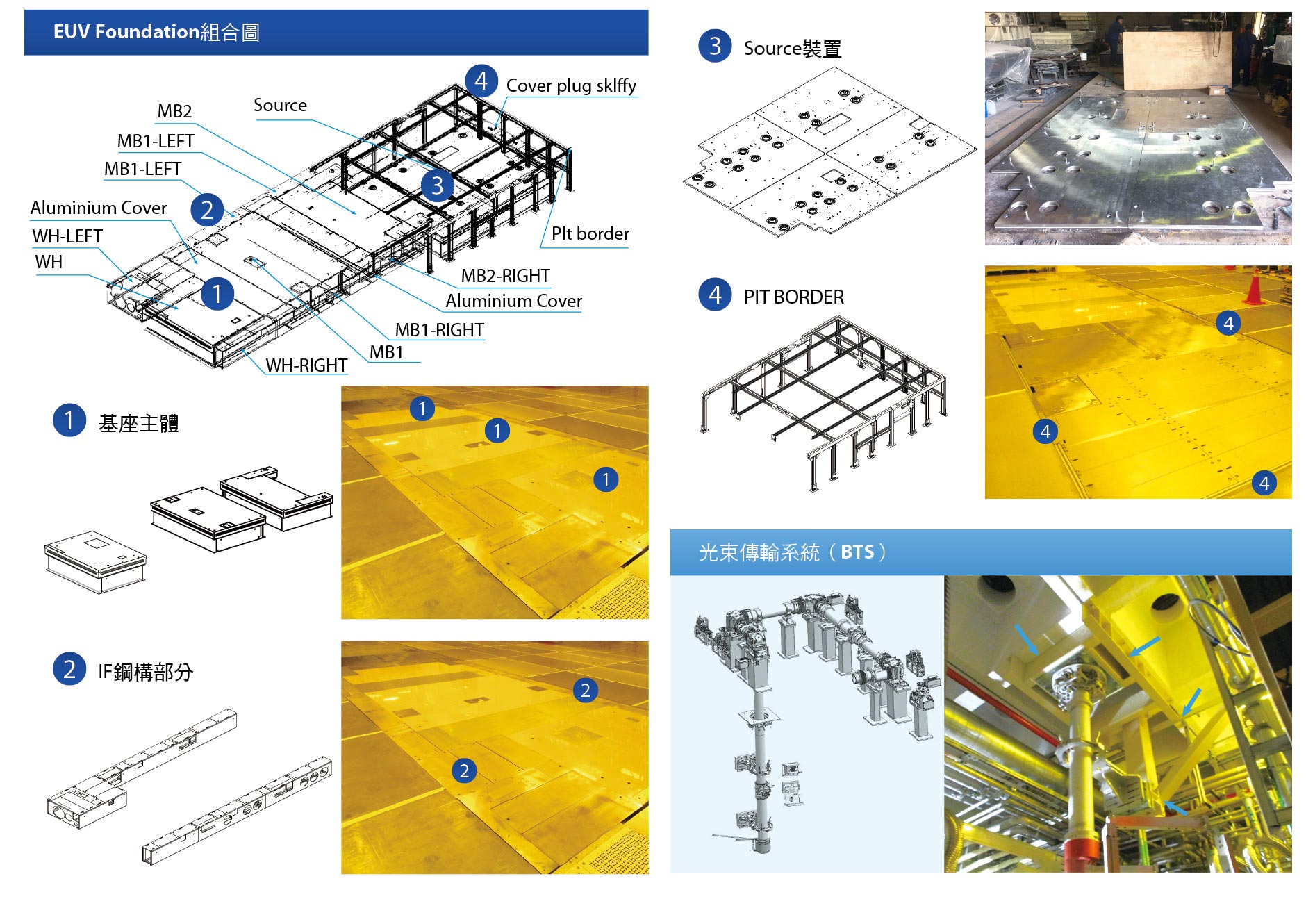
EUV Foundation的演進
簡述曝光機(Scanner)Foundation的演變過程 圖2:
圖2、Scanner Foundation 的演變過程
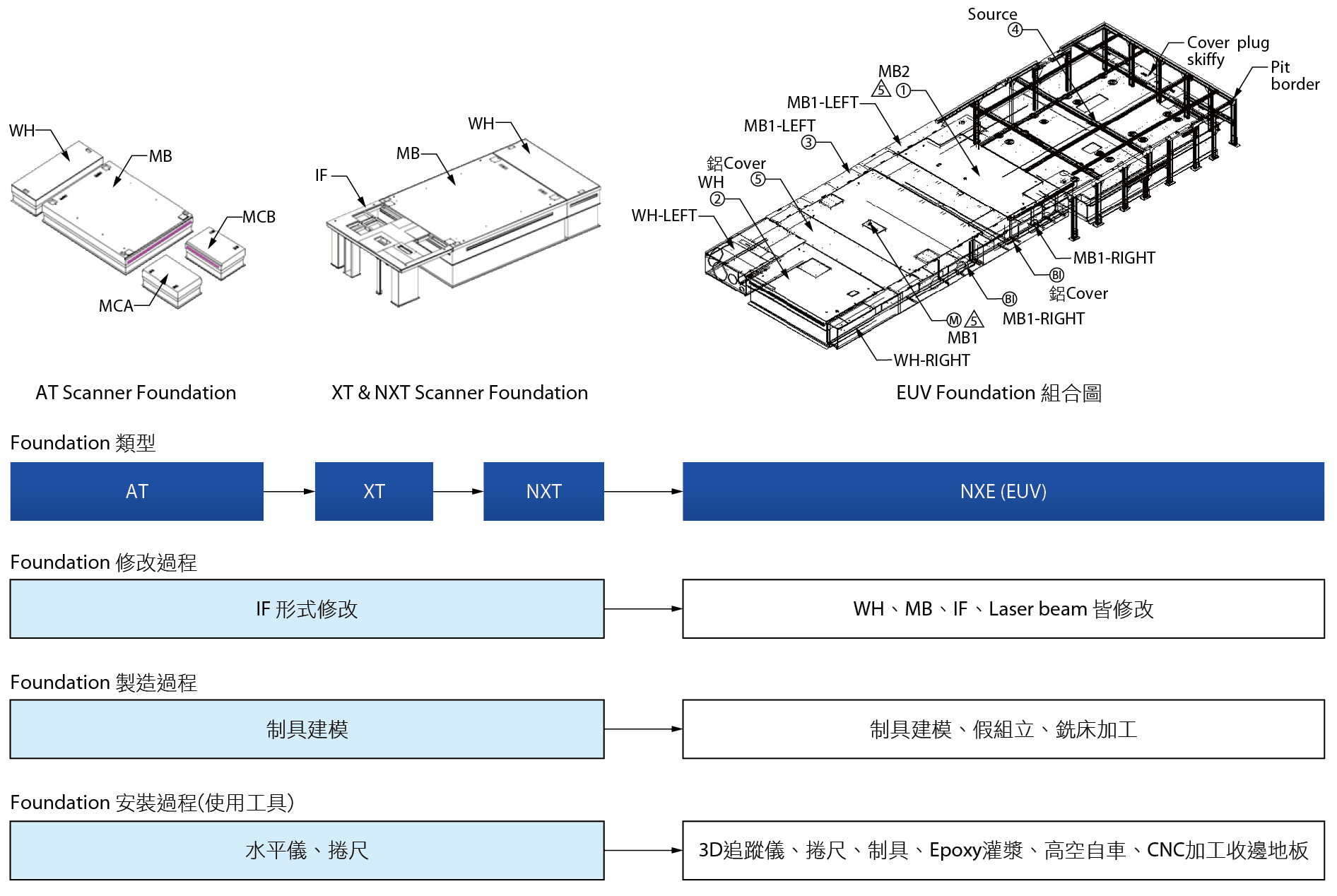
- 投影機尺寸為以往的三倍大,約10米平方變成為 30米平方。
- 剛性規範為原有兩倍,1E+08 N/m變成為2E+08 N/m。
- 增加了光束傳輸系統(Beam Transport System, BTS)的振動(Vibration)與剛性的測試需求。
- 料件製造工期增加1.5倍,35天變成為57天。
- 安裝測試工期增加10倍,5天變成為51天。
- (螺絲孔距、安裝水平度、面積大小、各部件安裝相對距離)安裝精度增加約2.5倍,±0.5mm變成為±0.2mm。
- 安裝品質管控(QC)自檢表單約122頁,約610點位以上需檢測精度。
- 振動測試點位增加4倍,6點變成為24點。
- 剛性測試點位增加13倍,9點變成為115點。
EUV Foundation各項安裝檢測需求
於接獲設備通知放樣完成後,隨即安排至現場針對樓板高度作放樣,一片高架地板需放樣五點,依安裝範圍需放樣至少6×16=96片地板共480個點,才能確保地板下高度誤差值不會影響到後續下料安裝,但此時尚未引進量測儀器,所以非常的耗時耗工。
- 此機型裝機之定位點,也跟以往由機台四周圍(X/Y)作為裝機基準點,改由MB2 SF作為裝機及定位之基準(X/Y/Z) 圖3,所有裝機之順利度,皆靠此中心為基準依據,故此點為非常重要核心,為避免安裝位置與基準點產生誤差,在下料安裝前與現場安裝過程中仍然與原廠再次至現場確認,剛開始相關位置也因皆使用人工進行量測確認,量測結果仍被質疑誤差不準確,為了如何達到澄清此規範無誤而困擾。
圖3、EUV Foundation 安裝基準點
- 於基座安裝過程中,為了配合BTS的安裝,原廠同時也要求基座與後方基準板(Source)之間,必需有420~426mm需求,而廠區既有的環境放樣平均高度為450mm,在於高度不足的情況下造成了Source安裝上極大的挑戰。為了配合BTS高架地板下裝機高度需求,廠區環境將高架地板銑平增加20mm 圖4,主要也是因應此安裝需求之變更。
圖4、現場環境迴風孔洞全面填實與銑地磨平,已達符合需求
- Source安裝階段性完成後,原廠到場檢視時,才告知Source下方需全面填實不可有空隙,為了改善此問題,將迴風孔洞全面填實且Source原本除了AB膠安裝固定外,也依照裝機需求,提出使用環氧樹脂(Epoxy)進行填充。
但是第一次在灌注Epoxy完畢後,又發現因樓板地面不平,Epoxy無法全數展延,導致空氣之產生,為此再次與原廠討論解決,在不影響裝機相對位置的鐵板上加鑽孔,由這些孔洞灌充Epoxy並排除空氣改善底下無法填隙的問題 圖5。圖5、Source 板安裝示意圖
- 料件製作與安裝工法上原本使用最原始之安裝方法及以往的傳統手工加工,為了減少安裝工序工時與安裝誤差,後續精進開始使用CNC銑床製作定位制具與料件製作 圖6,除了皆可滿足料件的精度品質外,在大尺寸不做變動之下有了制具也讓現場安裝速度的明顯提升。
圖6、制具的加工,皆以CNC 銑床加工
- 在完成基座主體的製作與安裝後,則必須進行BTS的安裝:該BTS包括一個垂直光束路徑(VBP)和水平光束路徑(HBP)的和是需要的CO2激光驅動器光束在潔淨室下回風層(Sub-fab)運輸到最終聚焦在裝配曝光單元 圖7。
於三樓安裝BTS時,則遇到了BTS面板上無固定孔,但下方又須以AB膠填實,且鋼板為光滑面,不易黏著,經討論後決定製作制具,用來固定BTS板。圖7、BTS 安裝位置示意
檢測儀器:3D追蹤儀(Tracker)
剛開始BTS現場安裝前,得知自主檢查表須跨樓層之數據,此數據使用以往的測量方式,已經無法達成安裝需求,為了能夠完成安裝進度,尋找儀器「航太業專用之3D追蹤儀」 圖8,其精度可達小數點之第二位,特別與廠商協調租借樣品機,進廠與原廠討論試用後,原廠也認同此儀器所量測的數據。
圖8、3D 追蹤儀
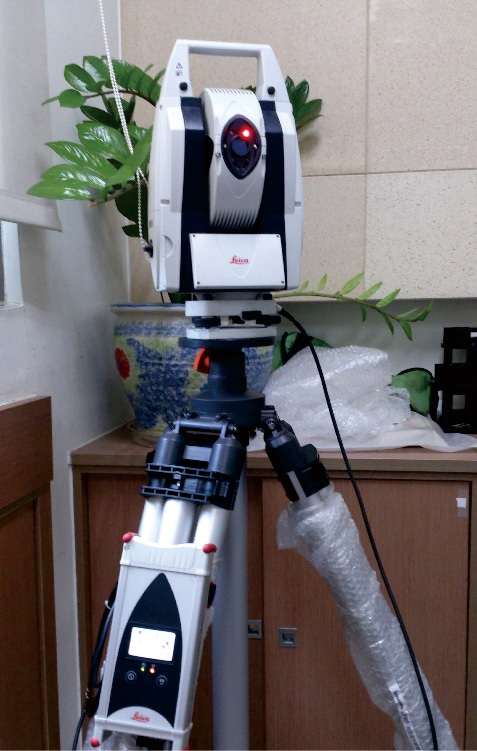
也發現其精度達小數點第二位的強大效能,能在安裝流程上增加安裝速度及使其符合原廠要求之精度準確性,再加上針對自主檢測高達一百多頁之檢測報告,可以更快的將結果準確的測量出來,減少現場的耗時耗工。
結論
從開始確認規範需求,到增加複雜度的圖面、高精度要求的安裝料件、精密低誤差需求的現場安裝,以及安裝環境的嚴苛要求,我們從耗時、耗工且被質疑量測結果的傳統作業方式,漸漸的改變工法、工序及料件製作模式,設計、使用制具並導入了新的檢測儀器,使現場安裝的精度更加準確快速,量測效率省時而準確。
有關安裝基座前的環境改造,因有了失敗安裝的經驗,後續安裝前能先將需求位置的迴孔孔洞封實,並將安裝位置改造成能配合BTS安裝高度,達到順利符合規格基座安裝與檢測。
因高精度規格要求,在安裝過程中採用CNC加工製作料件產品,如能再條件允許的情況下使用於其他的安裝機台,能減免因傳統加工產生基座誤差,機台與基座定位孔距無法安裝的問題。
高精度規格要求的安裝量測,因人工安裝量測方式不被信任,從而引進讓人放心使用的高精密量測儀器與CNC加工安裝制具;這讓人省思,其他的安裝工法或是檢驗手法是否仍有精進的空間。
期許未來能夠以這些精進的結果為基礎,更上一層樓,挑戰並取得更進步的技術與跨越。
參考文獻
- ASML NXE3350 Foundation Test Report-4022_641_68175-160-001-01自檢表。
- ASML-EUV BTS-2016版本Support Frame Verification。
- 譜威科技PW705G操作手冊。
- Leica AT401 3D追蹤儀操作手冊。
留言(0)