摘要
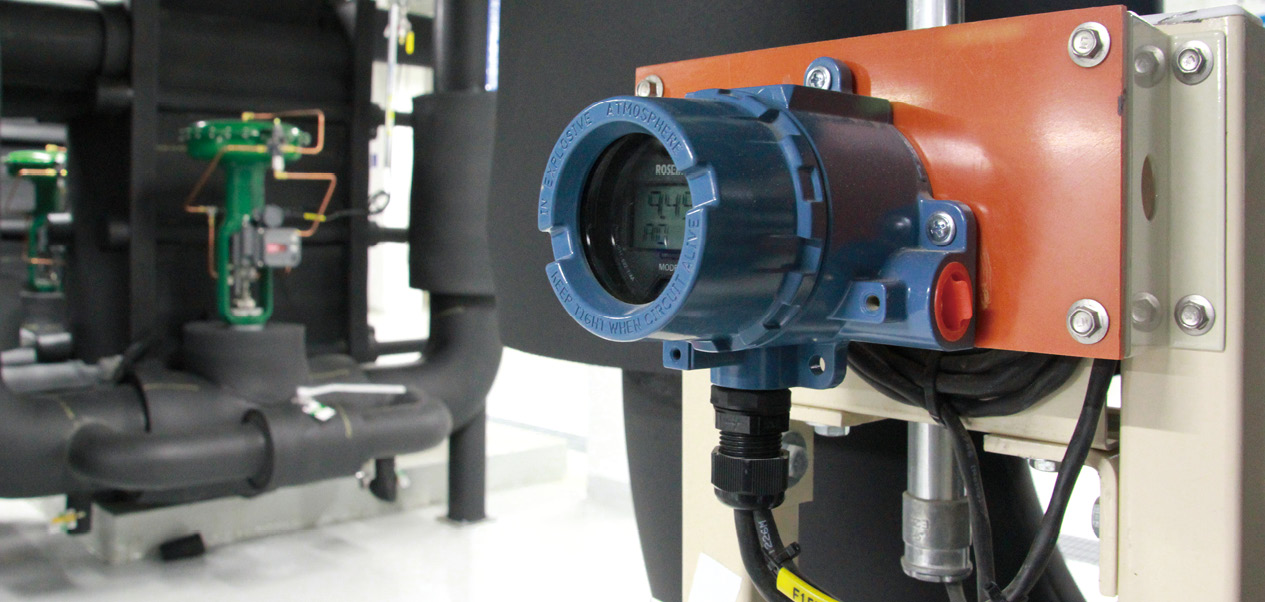
由控制閥診斷談製程效能管理
Keywords / Smart Device,Process Efficiency Management,Performance Diagnostics,Valve Signature Test
儀錶製造的技術及功能近年來因IC研發及製程的進步而日新月異,近十年來各大控制廠商也陸續設計出智能儀錶(Smart Device 或Intelligent Device)。而儀錶設備如何應用在製程生產讓控制生產更加穩定?,甚至應用於預知保養技術,讓控制生產設備減少因儀錶設備異常所產生的異常跳機事件,提高製程可利用率(Availability),做好更精準的製程效能管理。然而對於智能儀錶之認知、通訊技術之選擇及預知保養之執行及上述項目對於製程效能管理的重要性,普遍概念不明確且未有完善及細部的執行計畫。希望藉由本文章的探討,使用者對這些觀念能有更清晰的輪廓,進而發揮智能儀錶的功能及提高廠務系統之製程效能管理。
ABSTRACT 前言
一般製程工廠生產效能的穩定,主要在於操作控制回路的穩定。而控制回路的穩定,仰賴回路元件準確度與穩定性。在控制回路的元件設計上,各廠家都致力於準確度與性能的提升,各量測元件(Sensor)的準確度可改進到0.075%以上,而控制系統(單回路控制器或多回路的控制系統,如PLC/DCS..等)也在I/O轉換系統採12位元或16位元信號處理器,精確度達0.025%以上,惟獨最終控制元件(Final Control Element)控制閥部份,由控制系統送出設定開度,一直到實際控制閥開度變化,其間不只有作動時間延遲,實際開度與設定開度又有不小的誤差(閥信號I/P轉換與機械作動的問題),一般約為2~5%。此部份控制閥性能的改進,如果準確度能提升為0.5~1%,不只對單一回路控制有所改善,也影響製程前後相關控制的穩定性,相對就可提升整體製程生產效能。請參考圖一。
圖一、控制閥在控制回路的關鍵角色
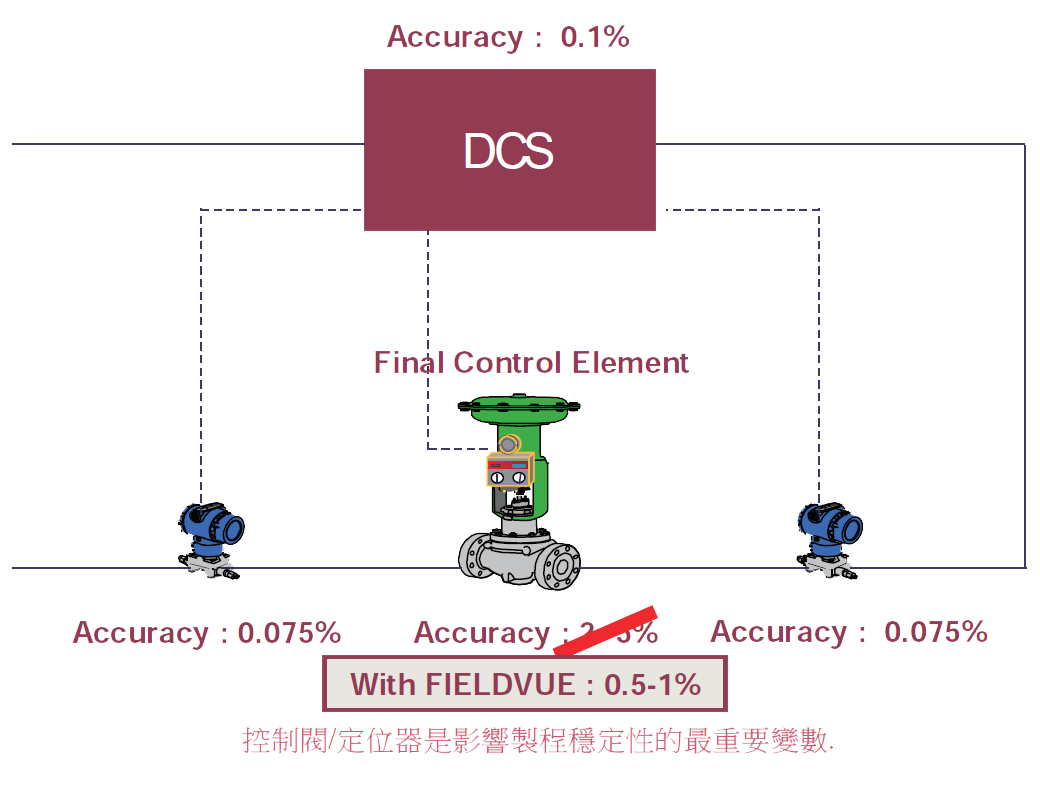
而控制閥的診斷功能,是機械閥維護保養最大的功能差異。現在最新的智慧型控制閥定位器,除了藉由診斷圖形找出閥的機械問題,避免因閥的異常問題而導致系統非預期的故障停機,同時對維護保養人員可提升保養工作的效率,減少不必要的現場往返時間。所以利用控制閥診斷功能,不只能提升生產製程效能,更可提供維護保養人員有效工具以提高工作效率,維持Facility製程設備在最佳狀態,讓生產及設備單位無後顧之憂。
EXPERIMENT 研究內容
傳統I/P信號轉換器(I/P Converter)與智慧型定位器(Smart Positioner)之比較
一般傳統控制閥,大部份安裝I/P信號轉換器,將電流信號4-20mA轉換為氣動的氣壓值信號。但因控制閥的機械摩擦特性,在機械閥開與關的兩個方向承受不同的摩擦力,而且其關係也非線性,所以透過I/P轉換器有下列兩大問題:
- 開度不準
- PID回路控制遲緩,PID參數不易調整
參考圖二,在設定開度(I/P Input Signal)改變2%以下的變化值,閥軸的實際開度(Actual Travel)幾乎不改變。而閥軸開始移動,其開度也沒有跟隨設定值一樣穩定變化,流量也就不穩。控制閥不穩定,回路控制就不好調適,生產製程當然比較不穩定。
圖二、傳統控制閥定位器的作動圖
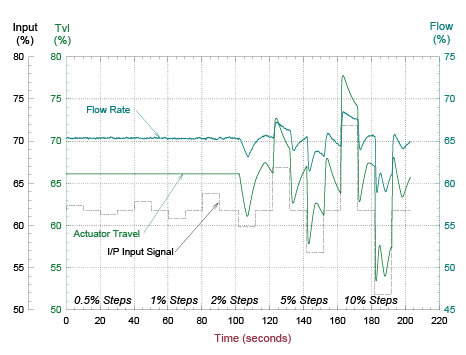
反觀智能型定位器的基本設計,就是內置微處理器(Microprocessor)以及將實際開度信號(Position)回饋給定位器參考。此實際開度會與設定開度作比較,將誤差值再計算調整輸出氣壓值,進行開度修正。此微處理器的開度修正動作,就宛如PID回路控制一般,所以控制閥的開度會更加精準,操作人員看到設定開度50%,外面實際的閥開度也是50%。請參考圖三,設定開度(I/P Input Signal)與閥軸的實際開度(Stem Travel)幾乎完全一致,相對流量就非常穩定(Flow Rate),所以回路控制也比較容易調適,製程控制也就相對穩定。
圖三、改裝智慧型定位器的測試圖
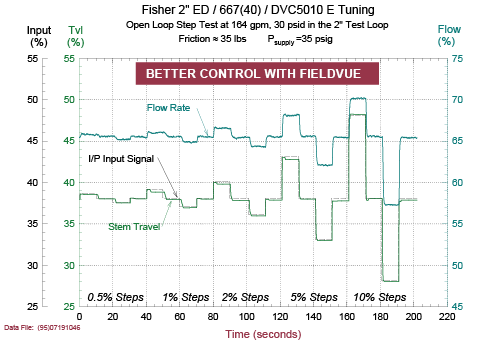
由於控制閥比較精準,所以應用在圖一的回路控制上,控制的PV(Process Value,製程值)就可獲得非常明顯的改善,請參考圖四的壓力PV值,由改善前的1%變化,穩定到只有0.25%變化。
圖四、控制回路的改善前後性能比較

由控制的角度來看,一旦控制的穩定性提高,相對的品質分布就比較集中;因此控制的設定值就不需要抓太大的前置量,由圖五的統計關係圖表來說明生產與控制值的關係,可以用最小的投入量(設定值)獲得最大的產出值。所以控制閥性能的改進,對整體工廠的生產效能有著決定性的影響。
圖五、由統計分析圖看控制穩定性對生產的影響
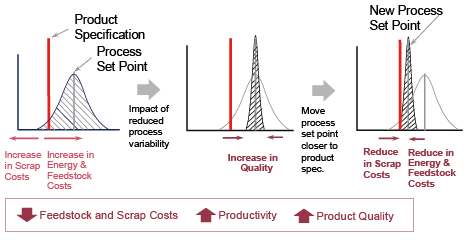
控制閥的控制性與保養性:
控制閥在整個工廠控制扮演關鍵的角色,因為大部份控制閥被設計來執行回路控制。而控制閥除定位器之外,閥體(Valve Body)及驅動器(Actuator)是機械組成,如何線上檢知機械問題是保養人員的難題。所以在控制性及維護保養這兩大部份是極大的挑戰:
控制性
試著思考底下的工廠問題是否是因為控制閥控制性不佳所引起:
a. 工廠花了鉅資購買APC (Advanced Process Control)軟體或系統,但是否未上線使用,或者使用並不穩定?
b. 控制閥控制變異性大,DCS控制迴路PID不易調試?
c. 控制閥控制不穩定,產品品質不佳,產能無法提升?
控制閥主要三個組成-定位器、驅動器及閥體。某些控制閥不採用定位器,而是傳統的I/P轉換器(I/P Transducer),相對的控制性因為沒有開度回饋,控制性會比定位器差。而I/P轉換器將控制系統電流信號4-20mA轉換為氣動的氣壓值信號,但因控制閥的機械摩擦特性,在閥開與關的兩個方向承受不同的摩擦力,而且其關係也非線性,所以採用智慧型定位器,藉由微處理器的計算修正功能,可以改善此部份問題。再者,智慧型定位器內部有增益值(Gain)可調整,調整好壞也就影響這個控制閥的作動性,增益值調得太大也會導致控制閥作動不穩。因此控制系統下設定開度給控制閥,控制閥真實開度是否依命令動作(校正好壞),多快才開到設定開度(增益值調整好壞),這些都會影響控制回路的控制性。
參考圖六,一般控制分佈曲線見左半部,因為設定值的控制變異數比較大,為避免落於規格值以下,一般設定值會高於規格值,可是設定越高,需要的能量及操作成本較高。因此,若控制回路改善,控制變異數可以降低,不但產品品質較一致,也有足夠空間調整控制設定值。此時,藉由設定值調整,一方面可以節省能量成本,產品品質也可以提升。
圖六、控制變異性改善對生產操作的影響
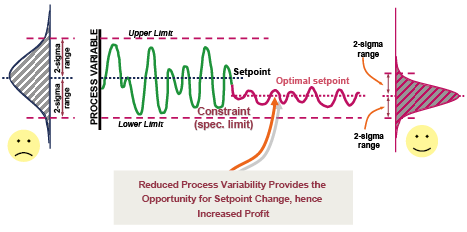
保養性
試著思考現實工廠另一層面的保養問題:
a. 工廠年度歲修,所有控制閥到底有哪一些要拆修,哪一些不用拆修?靠經驗和事件決定是否拆修?有否隱藏問題不知道而沒拆修?
b. 拆修的控制閥發現沒問題(或找不到問題)又裝回去?歲修時沒有拆修的控制閥,開俥沒多久就壞了?會不會有“該拆的沒拆,不該拆的拆了”的感嘆?
c. 如何驗證控制閥整修、調適(Tuning)、校正一切OK?
控制閥保養,最主要的問題在於機械部份,當這個閥還在現場,保養人員如何判斷這個閥是否該拆修,尤其拆裝一個閥需要的人力、機械吊裝設備、時間,會因閥的尺寸大小而不同,當工廠產能越大,控制閥的尺寸越大,相對也越重,拆裝工程就越浩大。加上工廠並非只有一個控制閥,而是數十個、數百個,甚至上千個。在工廠年度歲修有限的人力、物力、時間,是否能對所有控制閥進行“必要的”保養檢修工作,這就成了保養單位的一大挑戰。如果能夠在控制閥拆修前就先診斷問題,不需要拆修的就可以現場處理,有機械問題必須拆修的再進行拆修工作。整修完控制閥,也可利用診斷功能驗證整修、校正、調適等保養工作,這樣的保養方式就更有效率,甚至可以訂定為保養標準作業程序(SOP – Standard Operation Procedure)。
所以,利用智慧型定位器來診斷控制閥問題,成了新的解決方案。
智慧型定位器與控制閥診斷
智慧型定位器的基本設計,就是加裝微處理器(Microprocessor) ,並將閥實際開度(Travel Position)回饋給定位器參考。此實際開度會與設定開度(Setpoint)作比較,將誤差值再計算並調整輸出氣壓,進行開度修正。此微處理器的開度修正動作,就宛如PID回路控制一般,所以控制閥的開度控制會更加精準,操作人員在控制室看到設定開度50%,外面實際的閥開度也應該是50%。在此,四個重要變數就構成控制閥診斷的重要依據-設定開度、實際開度、輸出氣壓、時間。針對這些重要變數,就可以組成非常有用的診斷工具圖:
多重步進反應測試 (Multi-step Response Test)
控制閥的反應性、靈敏性、精確性,影響這個控制回路,而操作人員也只能從製程值的反應結果來調整控制閥輸出命令。假如控制閥的反應性能夠又快、又穩、又準,這個控制回路就會容易調適,而且比較穩定。所以定位器設計診斷命令,將設定開度、實際開度、時間三個變數構成一個圖,稱為步進反應測試圖(Step Response Test Graph)。不過,大多數廠家設計單一步進測試,也就是由某一開度到另一開度進行單一步進測試,診斷結果就會比較失真,因為控制閥是一直在連續變動控制,尤其是控制系統回路放在自動控制,設定開度一直在調整,實際開度也必須動態跟得上,控制動作才有意義。所以測試命令必須多重步進,而且步進要由小到大的變化,才能看小變化的步進動作是否實際反應(靈敏性),大變化的步進命令是否會動作太慢,定位器增益值調整太小,控制閥作動時間常數(Time Constant)太大。但也有可能增益值調太大,就可以看出是否發生overshoot。再者,還可以看出設定開度與實際開度是否有很明顯的偏差(精確性)。由圖七的反應動作,由小變到大,控制閥作動反應是否良好,可以看出定位器增益值(Gain)調整好壞。
圖七、多重步進反應測試圖
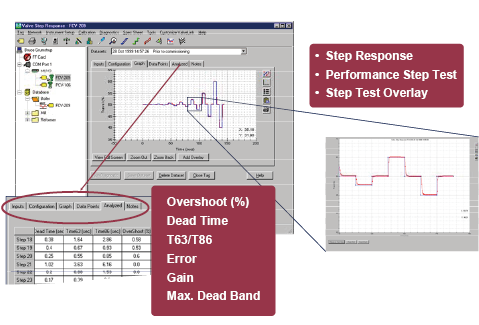
動態誤差帶測試 (Dynamic Error Band Test – DEB Test):
把控制閥由關到開,由開到關,進行一次全行程開關測試,並把設定開度當橫軸,實際開度當縱軸畫成一個分析圖,這就是動態誤差帶測試圖,這是看整個控制閥的整體性能,含定位器、驅動器及閥體。在這個測試圖中,每一設定開度值會有兩個實際開度值,一個是由關到開,一個是由開到關。這兩個實際開度差異值稱為誤差帶(Error Band),主要原因是整個控制閥的內部阻力形成,控制閥由接受設定開度命令到實際開度移動,中間有許多電子與機械的作動元件,每一組件都有或多或少的延遲(稱為內阻力)。但因為是定位器,開度誤差值會在下一次開度的運算中修正,因此控制閥可以到達設定的要求開度。本測試圖就是要看開度計算修正前的內阻力特性,同時也有分析數據提供維護保養的參考。
參考圖八,由所繪出的曲線,可以看出哪個部分有問題,例如當訊號逐步增加時,開度並不呈直線上升,表示控制閥實際開度不呈線性變化,可能需重新校正,也可由分析資料的線性數值判斷(Linearity > 1%)。至於DEB(動態誤差帶)數值,每一開度都計算出一組DEB,把所有的DEB數值計算最大值、最小值、平均值,就可提供非常有用的訊息,例如平均值過大(Average DEB > 5%),表示控制閥整體內阻力過大,控制性不佳,需要拆修。假如最大值與最小值差異過大,表示控制閥開度某些位置內阻力差異過大,也是有檢修的必要。
圖八、動態誤差帶測試圖
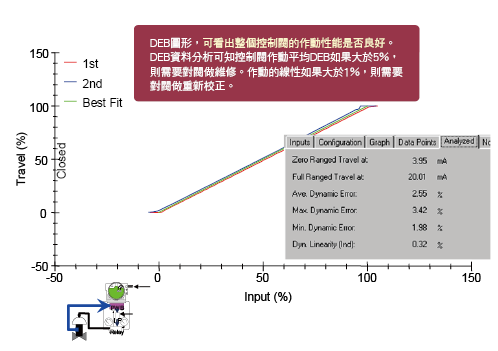
閥特性曲線測試(Valve Signature Test):參考圖九
圖九、閥特性曲線測試圖
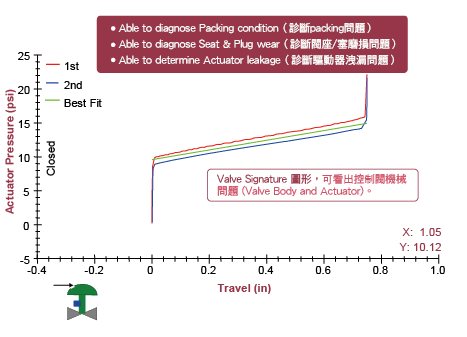
把控制閥由關到開,由開到關,進行一次全行程開關測試,並把實際開度當橫軸,輸出氣壓當縱軸畫成一個分析圖,這就是閥特性曲線測試圖,只看閥體及驅動器的機械相關性能與問題。因為在定位器的微處理器電路板有裝設輸入與輸出氣壓訊號感應元件,診斷命令會將氣壓訊號逐步送至最大,再反向減少訊號,來檢測機械閥桿實際的位置及氣壓的相關性。同一開度有兩個壓力值,一個是由關到開,另一個是由開到關,因為開與關的方向有著各別不同方向的動摩擦阻力。由於壓力乘以膜片面積就是力,由此確實的力去計算摩擦力、關斷力等,才能確實分析控制閥的機械問題。
由圖九所繪出的曲線,算出每一實際開度的摩擦力,再分析平均值、最大值、最小值。平均值與閥填充物packing有關,不同材質的packing(如石墨、鐵夫龍PTFE等)有不同標準摩擦力,保養人員換裝packing之後,到底鎖得太鬆或太緊,除了靠壓力鈑手以外,就只有靠經驗判斷,如果鎖得太鬆,就會外漏;如果鎖鎖太緊,不只閥作動力被摩擦力抵消,有內漏的可能性,packing也會因過度磨耗而減損壽命。在這個診斷圖,除了平均摩擦力是否妥當,也可看最大摩擦力與最小摩擦力的比值,也可看閥關斷力(Valve Seat Load),如果關斷力不夠,就會內漏。除此之外,膜片是否有裂縫,彈簧彈力是否老化,……,相當多的閥機械問題都可在這個診斷圖與分析數字判斷,當年度歲修APM時先對控制閥進行診斷,由診斷圖形與分析數字判斷是否需要拆修,或者現場維修而不需拆卸。藉由診斷圖的幫助,讓保養工作對症下藥,在有限的停俥時間,能對控制閥進行必要的維護保養工作。
性能診斷(Performance Diagnostics)
由於控制閥在線上使用,由控制系統控制,不容許測試命令對它任意開關,所以前述三種診斷都是歲修期間或製程有(By-pass)管路設計才能夠進行診斷命令,稱為離線診斷(Off-process Diagnostics)。在線上生產中(On-process)把診斷命令當成監督與資料收集,檢測控制閥內部或元件狀態,此為線上診斷(On-process Diagnostics)。一般常見定位器自我診斷,診斷定位器內部是否有問題,並用警報方式通知,所以on-line連接讀取警報變得非常重要。部份定位器廠家利用壓力值計算閥作動特性,算出當時閥工作摩擦力,此摩擦力是當時控制閥的工作性能指標,此為線上性能診斷(On-line Performance Diagnostics)。再運用長期趨勢圖與上下限方式進行性能監督,以供保養人員對此控制閥的工作性能得以監督,在性能衰退但還沒嚴重影響製程時就事先發覺,並採取必要措施,這就是預知保養。
參考圖十,控制閥在線上由控制系統控制,閥設定開度伴隨控制系統的控制需求而變化,定位器的氣壓輸出因此而修改使實際開度伴隨設定開度移動,此時定位器依據開度值的變化及氣壓的變化計算當時的摩擦力,所以控制閥的真實工作性能用摩擦力等數值量化並記錄。由於性能是長期趨勢變化,把這些摩擦力進行長期趨勢圖追蹤,就會很容易察覺控制閥性能變化,在還沒歲修前就先警覺控制閥的性能是否衰減,必要時可先請購必須的備品或零件,以避免至歲修時才發現,受限於有限的歲修時間來不及請購必要的零件物料,歲修保養工作與時程就受影響。
圖十、控制閥線上性能診斷摩擦力值
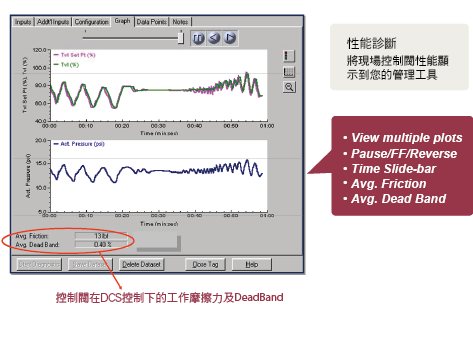
控制閥診斷對製程效能的影響
一般製程工廠對維護保養的謎思(Myths)
在一般製程工廠,由於生產至上,其他單位是輔助單位,因此維護保養單位相對比較易被忽視,而且受限於儀錶資訊的取得困難,大部份的工作是on-call(有問題再叫修)與現場作業(人員必須要到現場儀錶所在地工作)。綜觀一般工廠對維護保養的謎思有五大類:
- 操作為主,維護為輔
事實上:儀錶故障,工廠停擺,所以生產操作與維護保養兩者應並重,不應該輕維護,重生產。 - 儀錶資訊不足,以人員經驗為主
事實上:智能儀錶功能較完備,資訊充足,可輔助人員經驗及能力不足的問題。 - 儀錶資訊必須在現場取得
事實上:利用多工器(Multiplexer)連接,把HART儀錶資訊傳到維修室,即可遠端進行所有HART儀錶即時(Real-time)與在線(On-line)的儀錶監督管理與維護保養工作,省卻人員現場往返的時間。 - 故障維修及定期保養為主
事實上:大部份儀錶工作都是事後的故障維修與定期保養,但因智能儀錶資訊充足,在還沒發生故障之前就能針對問題進行預知保養。 - 公司網路管理,難納入生產及維護的即時資訊管理
事實上:生產與儀錶的即時資料透過OPC (OLE for Process Control)的技術,加上歷史資料庫的ODBC/SQL等格式,很容易跟公司網管系統ISO/CMMS/ERP等結合。
控制閥診斷系統架構
控制閥的診斷功能,在定位器上的微處理器進行,接受診斷命令之後,將控制的輸入信號與輸出信號送給診斷工具收集記錄,繪成圖表,並計算成控制閥的物理量,如線性(Linearity)、摩擦力(Friction)、關斷力(Seat Load)、......等,提供給維護保養人員很好的分析工具,以便對控制閥進行必要的保養工作。在此以Fisher DVC (Digital Valve Controller)控制閥定位器以及ValveLink診斷工具配合,其架構如圖十一。此架構圖的優點是不影響現有生產控制系統,就可架構on-line & real-time控制閥診斷系統。
圖十一、控制閥診斷系統架構圖
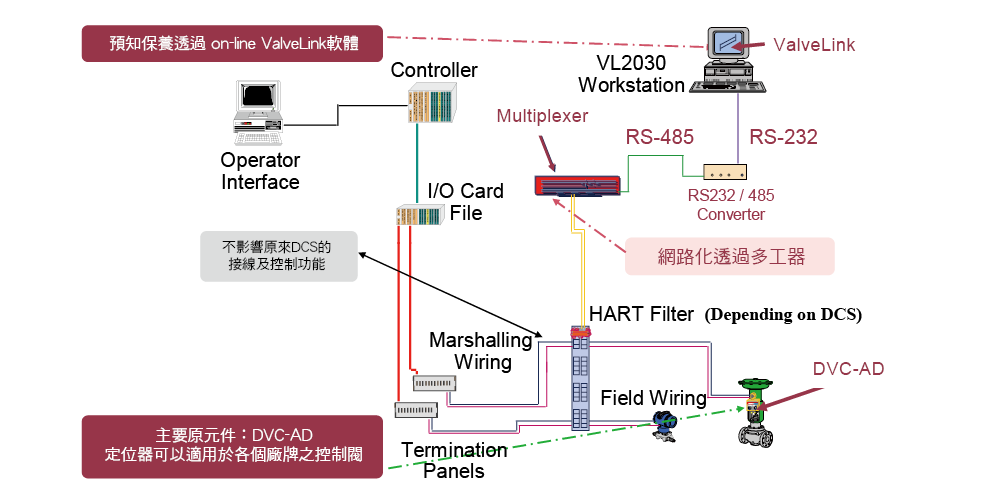
控制閥診斷功能與診斷圖表
控制閥的診斷功能與圖表有很多種,在此利用Dynamic Error Band (DEB)圖表展示診斷功能的功效。在現有的控制閥定位器,先利用FlowScanner產品對控制閥的執行效能進行診斷,之後將定位器改裝為Fisher DVC,透過ValveLink進行相同的診斷測試工作,可得圖十二的參考圖表。橫座標是控制閥的設定開度,縱座標是閥軸的實際開度,診斷測試動作是由關到開,再由開到關,邊動作邊把資料送給診斷工具記錄,再由診斷工具繪出圖表。在此圖(Dynamic Error Band)的關係,越接近一條直線越好。由分析數據Dynamic Linearity的數值比較,改善前2.45,改善後0.45,原廠建議值小於1.0,很明顯改善後的控制線性比較精準。至於Average DEB,改善前9.08,改善後1.09,原廠建議值小於5.0。很明顯的控制閥Dead Band經定位器更換後,有很明顯的改善。
圖十二、控制閥定位器改善前後的作動關係圖

由於改善前後的控制閥作動性能圖表以對比方式展現,可一目了然地看出控制閥改善的情形,只針對定位器更換,並不更改閥體(Valve Body)與驅動器(Actuator),對控制閥的執行效能有很明顯的改善,也對製程控制的穩定性有所提升,也就對生產效能有很明顯的幫助。
控制閥診斷與製程效能改善的執行步驟
控制閥診斷與製程效能改善的計劃工作,如同品管手法的PDCA,請參考圖十三。
圖十三、製程效能改善方法
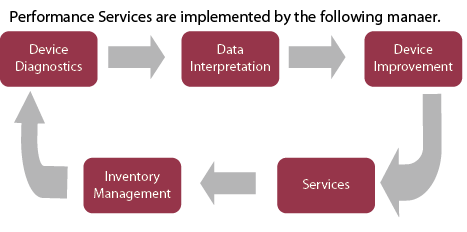
在Device Diagnostics階段,必須先做的是
- 控制閥資料庫的建立:將控制閥資料建立資料庫,包括設計值及採購型號等所有資料,建立一個容易搜尋與使用的資料庫。並將特殊的資料以不同的顏色區分,例如高壓,腐蝕性等,由於這些是控制閥容易發生故障的原因,所以由資料庫中的各種顏色標示,就容易追蹤哪一些控制閥容易發生哪幾種故障現象,也容易根據這些資料提出對應的改善或預防措施。
- 狀態及警報的監督:控制閥的內部診斷狀態與警報訊息,可即時通知維護保養人員事先預防問題發生,以避免異常的停俥事故發生,減少生產、工安、環保等事件。當發生警報,並不代表控制閥已故障失能,可能代表控制閥性能已衰退到某個危險程度(預設值)。維護保養人員如果由狀態與警報資訊仍無法斷定原因,並不一定要先拆修控制閥,可先對控制閥進行測試診斷工作,再決定下一步工作。
- 測試資料的收集:控制閥的測試資料很多種,但因大多數的測試動作會影響控制閥的開關與開度,也就會影響生產製程的正常操作,所以大部份的診斷測試工作是on-line but off-process(在線,但無製程操作),也就是停俥診斷,或者製程切到by-pass診斷。至於要做到on-line and on-process(在線製程)診斷,則另有性能診斷的技術與產品。診斷測試的圖表,除了有上述的Dynamic Error Band以外,還有Step Response、Valve Signature等。除了可判斷控制閥作動速度性能以外,還可分析判斷Diaphragm、Packing、Seat Load等是否有問題。
在Data Interpretation階段
必須做的是測試資料的解讀與判斷。在此部份,需建構區域與遠端監督診斷系統(Local/Remote Monitoring and Diagnostics Services)。工廠內維護保養人員架構區域的監督與診斷工具,可即時有效的解決製程上的問題。對於一般診斷圖形的分析與判斷,現場維護保養人員具有基礎解讀能力。至於診斷圖形的特殊問題分析與解決,可透過的診斷中心協助分析,以便能更精準的分析與解釋問題,並提供專家的改善意見。
在Device Improvement階段
承續著上一階段,把測試資料的解讀與判斷找出問題原因,並提供可行的改善意見。改善方案可能不只一種,而是根據所有可行方案中找出最佳,最經濟,或最可行的解決方案,解決製程瓶頸。
在Services階段
就是真正把解決方案執行。執行以後再檢查是否已真正解決原有問題,還是必須再進行改進。
至於Inventory Management階段
則結合第一階段的資料庫,將控制閥設計資料與實際型號,物料等資訊結合在一起,同時配合倉庫備品物料管理,如此就可統計管理所有備品備件,針對消耗性或需求量大的備件,可由廠裡準備,至於不常用或原廠分公司/代理商能夠區域快速提供的備件,可簽備件供應合約,省卻備件準備的資金屯積與備件倉儲管理問題。此部份管理工作,相當於把CMMS(Computerized Maintenance Management System,電腦化維護管理系統)以及ERP(Enterprise Resource Planning,企業資源計劃)的管理機制融入。
所以,由PDCA的執行步驟來看控制閥診斷工作,並探討其如何提升製程效能。在控制閥診斷前,建立完善的資料庫可事半功倍,這是P (Plan)階段。在製程效能有問題時,相關控制閥的狀態與警報收集是非常必要的。由於發生異常,但尚未將控制閥拆卸維修之前,可先進行診斷工作,這是D (Do)階段。診斷之後,根據診斷圖表與分析數據,以及控制閥狀態與警報資料,進行問題探討,並設法找出解決方案,這是C (Check)階段。有方案,就要去執行,真正將問題解決,例如把故障閥體拆卸維修,或者只需現場保養與校正。同時,把資訊結合資料庫,進行有效的維護保養與備品備件管理,這是A (Action)階段。透過如此有計畫,有效率的控制閥診斷維護保養工作,可以很容易解決製程問題,提升效能,甚至在問題還未發生影響製程安全之前,就透過警報等方式提醒維護保養人員進行必要的保養工作,以避免發生非預期的停機事件。
CONCLUSION 結論與建議
在一般工廠的控制,所追求的就是以最少的進料,獲得最大的產出,同時產品都要符合高品質要求。簡單的說,就是把工廠的生產效能提升到最大。製程的效能之提升有很多方法,本文主要探討未來在新建廠時,智能控制閥如何針對會直接影響生產的系統,例如: PCW System of HEX Chiller control Valve, MAU System of DCC control valve,去建置相應的控制閥診斷工具或系統,有效地去提早發現問題並解決問題,提升製程效能。在此,要提出幾個議題當參考:
- 儀錶是否重要? 控制閥是否重要?
- 是否一定要現場往返才可進行儀錶維護工作?
- 有何工具協助儀錶工作?
- 如何提升與驗證儀錶功能?
- 如何利用控制閥診斷功能進行製程去瓶頸工程?
- 如何利用有效的管理工作來提升製程效能?
儀錶技術不斷更新,經常會有新功能,及新技術發展。如何建立有效的工作環境來提升工作效能與產品品質,這是我們追求的方向。所以在控制閥的診斷功能,如何在製程生產中架構on-line and on-process,來追蹤並提升控制閥性能,以提升生產效能,這是未來探討智慧型控制閥定位器的一個重要課題。
參考文獻
- "HART Communication Application Guide", HART Communication Foundation (HCF), HCF_LIT-039 Rev. 1.0 Preliminary, Date of Publication: March 25, 2010.
- Emerson Process Management Performance Service Materials.
- Emerson Process Management DVC & AMS Reference Materials.
留言(0)