摘要
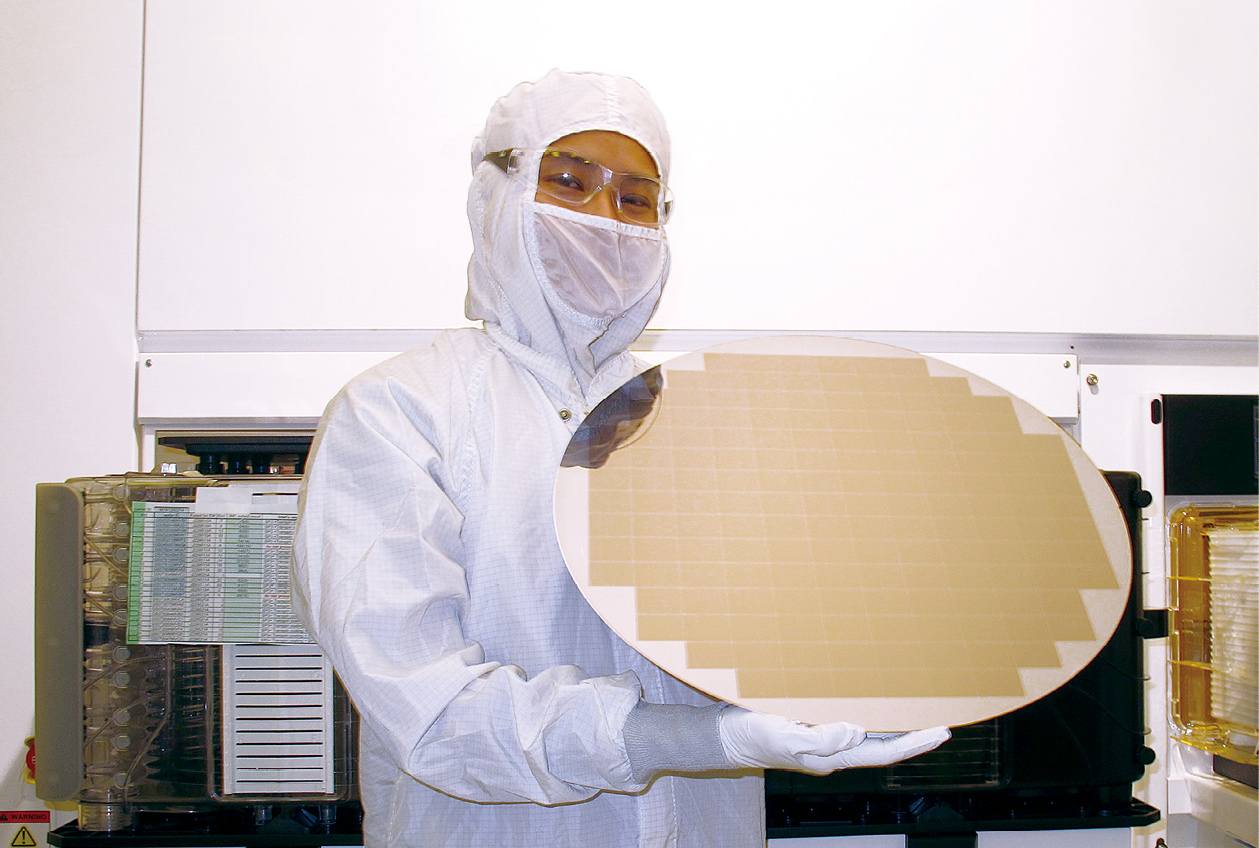
十八吋晶圓發展現況
Keywords / International Technology Roadmap for Semiconductor (ITRS),450mm
半導體晶圓廠對18吋晶圓的需求,如同過去8吋轉到12吋一樣,原因很簡單,就是為了降低成本,以能繼續維持競爭力並得以生存。去年(2012)是相當重要的一年,全球推動18吋晶圓之相關組織陸續成立,其組成結合了產學界組織、晶圓製造廠、設備與材料供應商共同合作 ; 針對未來半導體發展18吋的時程、生產製造標準與技術藍圖之規範已開始有了初步的產出與成果。此外,能源消耗亦是將來18 吋所面臨的另一大問題,如何有效節能絕對是我們最重要工作之一與未來成功的關鍵。
前言
半導體產業在技術上發展迅速,其驅使之動力總歸來說主要以提高生產力、產品良率以及降低環境上及經濟上的成本為主。就半導體產業晶圓尺寸來說,由最早期≦2吋 (50~60年代),3、4吋(70年代),5、6吋(80年代),8吋(90年代),12吋(千禧年代)乃至於目前新目標-18吋(450mm)晶圓世代,一直追循著”莫爾定律”, 一面增大晶圓尺寸,一面創新儀器設備,來提高生產率(cost/cm2)及縮短製程周期時間。以過去十年由(8吋)200mm轉型至(12吋)300mm為例,亦遵循印證大約 30% 的成本抑減。
根據2011國際半導體技術藍圖( International Technology Roadmap for Semiconductor, ITRS)之預估報告,指出國際半導體及相關產業之製程技術,將從2014年開始進入18吋晶圓之製程,廠房從施工興建至開始裝設生產設備,也估計於九個月內完成。並預計於2017年開始進入閘寬(Gate Length)14奈米之製程,此亦反映出過去30年來一直引領電子產業的幾何縮放原則(Geometrical Scaling, A.K.A. Moore's Law) ; 而今,更朝著More Than Moore邁進,部分目標已逐漸轉換為相對縮放原則(equivalent scaling),藉由創新設計改善效能、軟體設計、創新處理程序等,不斷影響未來十年的產業發展。若以2011年國際半導體技術藍圖所公佈的時程來看 圖一,儘管18吋晶圓製造發生的時程已經延遲,但終究會發生,只是時間早晚的問題。
圖一、國際半導體18 吋技術時程表(ITRS 2011)
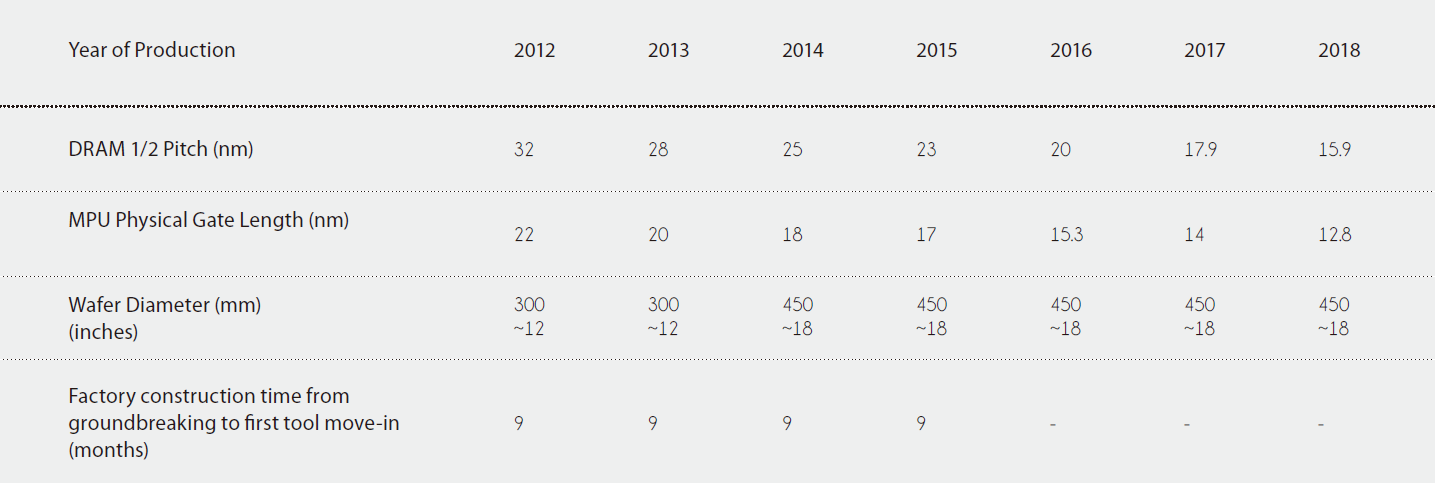
發展時程藍圖
近兩年來全球推動18吋晶圓發展之組織相繼成立,並開始積極的推展動作,我們很清楚要將 12 吋轉至 18 吋的困難度將比過去 8 吋轉至 12 吋更高,特別是面對更複雜的製程技術與成本降低問題; 18 吋要成功,必須是整個半導體產業供應鏈(Supply Chain)上游到下的共同努力才有機會,它包含了國際半導體組織、積體電路設計、晶圓供應商、晶片生產製造商、設備與材料供應商。現今對18吋晶圓生產製造的推動除國際性半導體相關的官方組織外(如ISMI,SEMATECH),全球18吋推動聯盟(Global 450mm Consortium ; G450C)與歐洲18吋設備與材料倡議計畫協會(European Equipment Materials Initiative 450mm ; EEMI 450)是目前18吋晶圓發展的最主要推手。為了使這次的轉換能順利,全球18吋推動聯盟(G450C)與美國紐約州奈米科學與工程學院(College of Nanoscale Science and Engineering ; CNSE)合作,目前已有十四台18吋晶圓生產設備在此進行測試,而其所建置的全球首座18吋晶圓無塵室,亦將於2013年第一季完工並開始進機,G450C將扮演半導體產業的火車頭,加速18吋晶圓製造時代的來臨; 此外歐洲最大的微電子研究機構,校際微電子中心(Interuniversity Microelectronics Centre ; IMEC)也宣布其將於2013年開始興建18吋無塵室,並預計於2015年完工。
依照目前18吋機台發展預估的時間表(圖二),多數機台設備到2014年都能完成試驗機台的開發,2015~2016年間可以達到量產的標準,唯獨複雜度最高之微影(Lithography)機台設備要到2017~2018年才能達到成熟量產的標準,這將使18吋晶圓的量產時程同步遞延,這也使 ITRS 2012年重新修正其18吋發展時間表(圖三)。
圖二、18 吋晶圓設備就位時程規劃(2012 Semicon Taiwan)
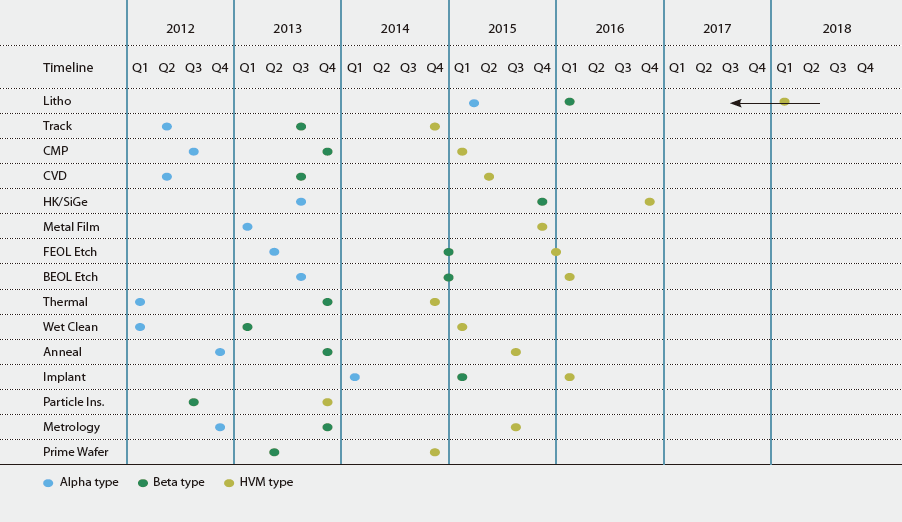
圖三、18 吋FAB 時程藍圖更新(2012 ITRS Conference)
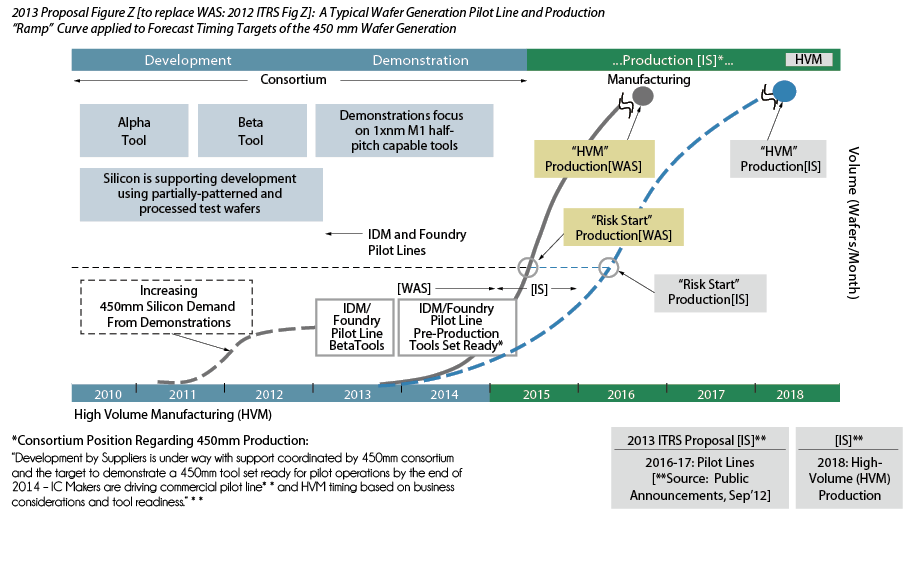
發展時程藍圖
近兩年來全球推動18吋晶圓發展之組織相繼成立,並開始積極的推展動作,我們很清楚要將 12 吋轉至 18 吋的困難度將比過去 8 吋轉至 12 吋更高,特別是面對更複雜的製程技術與成本降低問題; 18 吋要成功,必須是整個半導體產業供應鏈(Supply Chain)上依照目前18吋機台發展預估的時間表 圖二,多數機台設備到2014年都能完成試驗機台的開發,2015~2016年間可以達到量產的標準,唯獨複雜度最高之微影(Lithography)機台設備要到2017~2018年才能達到成熟量產的標準,這將使18吋晶圓的量產時程同步遞延,這也使ITRS 2012年重新修正其18吋發展時間表 圖三。
發展現況
2012年對18吋晶圓來說是相當重要的一年,許多重要的工作都在去年陸續開始有了成果,國際半導體設備材料產業協會(SEMI)亦積極推展18吋晶圓通用標準,助力半導體業者部署。目前針對矽晶圓、實體介面與輸送機制,以及機械裝配和產品封測三大範疇,已公布15項18吋晶圓規範 圖四,涵蓋晶圓乘載介面(Load Port)、晶圓傳送盒(Front Opening Universal Pod;FOUP)/運輸盒(Front Opening Shipping Box;FOSB)、自動化物料搬運系統(Automated Material Handling System;AMHS)儲存與傳送介面等,未來還將新增14項標準。
圖四、18 吋晶圓製造通用標準發展現況(SMEI 2012)
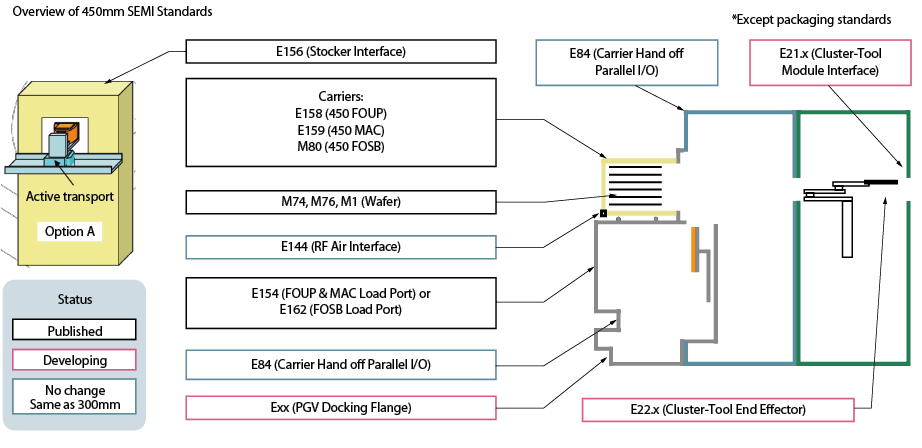
目前18吋晶圓(Wafer)之控片與所需之晶圓傳送盒皆已開發完成,其中台灣廠家所製作的前開式晶圓傳送盒(450mm FOUP)、多功能應用晶圓傳送盒(450mm MAC)與極紫外光光罩傳送盒(EUV POD) 3項產品皆已通過G450C、Intel與ASML的認證,是台灣現階段唯一通過認證的半導體設備公司,其產品目前已陸續交至設備機台供應商進行相關測試。大多數的設備製造商已完成其18吋實驗室(Lab)設置並開始其原型機之生產與測試,從去年的國際半導體展陸續所舉行的18吋研討會發表,我們不難看出歐洲與日本在未來18吋材料與設備上的佈局與積極態度。而黃光顯影技術絕對是關鍵瓶頸,未來在更高階製程是否可繼續採用目前浸潤式微顯影曝光技術(Immersion Lithography)來克服,還是採用多電子光束無光罩微影技術(Multiple-E-Beam M;MEB)或極紫外線(Extreme Ultraviolet;EUV)顯影技術也一直在討論與觀察;光刻系統使用光將電路圖案投射到芯片上,問題是,傳統光的波長現在是大於所定義的需求,有點像是試圖用一把特大號的畫筆,來勾勒出一根細線。為解決這的問題,廠家使用不同的方式來延伸對目前技術的使用,其中包括目前所謂的浸潤式顯影技術的使光線通過液體,透過折射率改變來獲得更加精細的圖像。與目前的光刻工具相比,EUV可製造出更加短的光的波長,相當於提供了一只更加精細的畫筆。但EUV也存在問題,因更短的波長,使得EUV光線能被幾乎所有的東西所吸收,其中包括空氣,因此它必須通過在真空環境下使用反光鏡來製作,此外,其目前的高建置費用與低產出效能亦是急需要克服的問題;全球18吋晶圓世代要能順利達成,設備廠商是否願意全力參與研發的態度是非常重要。
圖五、黃光浸潤視微影技術(Nikon)
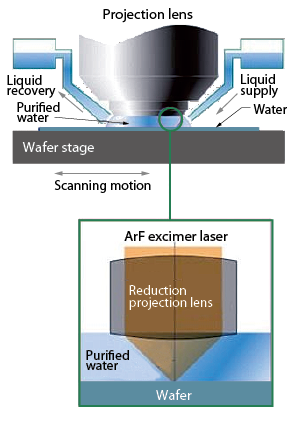
自動化物料搬運系統(Automated Material handling System;AMHS)在18吋上也有不錯的進度,幾個主要系統供應商都已完成STOKER與CART原型機(Prototype)之製作,G450C預計於2013年開始將其安裝於最新完工的18吋無塵室進行測試,廠商宣稱所有系統預計可於2015年全面測試完成上線供量產使用。
圖六、18 吋黃光AMSL Twinscan 機台設計雛型

儘管大部分設備供應商至今還無法清楚勾勒出其未來18吋設備較細部設計與需求,但尺寸的改變如更寬、更高與更重是可預見的;重量的增加將致使其元件組裝與維修更換變得更加困難,以天車(Crane)方式來進行更換看起來是很難避免,而使用天車移動所產生的電磁波干擾問題必須被解決;同樣的在面對更大更重的18吋晶圓,由於無法再使用人為方式來進行搬運操作,真正全自動化的晶片傳輸絕對會是未來AMHS設計的重點,更大的挑戰是如何在後段封裝製造上達成全自動化傳輸(目前的12吋後段封裝並無AMHS之設計)。
廠務的挑戰-節能
18吋的晶圓對半導體晶圓生產製造來說,絕對不是只有單純晶圓放大的問題,真正的挑戰是進入10奈米、7奈米甚至更先進製程複雜問題的克服,當然,問題不只是在製程端,廠務端亦是如此;電磁波干擾( Electro-Magnetic Interference, EMI )、空氣分子污染( Airborne Molecular Contamination, AMC )、微振動( Micro-vibration )的控制及更微小奈米粒子的量測與分析( Nano Particle Measurement and Analysis )等議題,絕對是我們未來在18吋成敗與否的最重要關鍵。我們必須確保轉換過程的順利,使18吋的生產製造能維持如同12吋的效率,才能保有具競爭力的成本與品質。針對18吋晶圓的廠房,廠務系統設計需達成以下幾個目標:
- 全面自動化運作從廠務運轉操作、品質管控到維護服務,提供工廠生產製造所需穩定的環境與資源。
- 有效滿足高階製程生產製造的環境要求,如無塵室微振動、電磁波干擾、空氣微污染之防治與更微小粒子量測等的問題。
- 設計創新以降低能源與資源的使用,如減少水、電、氣體與化學品的用量以降低生產成本;未來18吋晶圓廠的節能目標應做到與12吋晶圓廠相同的單位晶圓耗能。
- 符合綠色工廠生產製造,真正做到對地球的節能減碳與環境保護。
如何做到節能?無庸置疑的,廠務與設備絕對是推動節能最重要的關鍵,以目前一個12吋半導體廠房之電力能源總體消耗分佈來看,幾乎各佔了一半 圖七。
圖七、12 吋晶圓廠電力能源消耗分佈
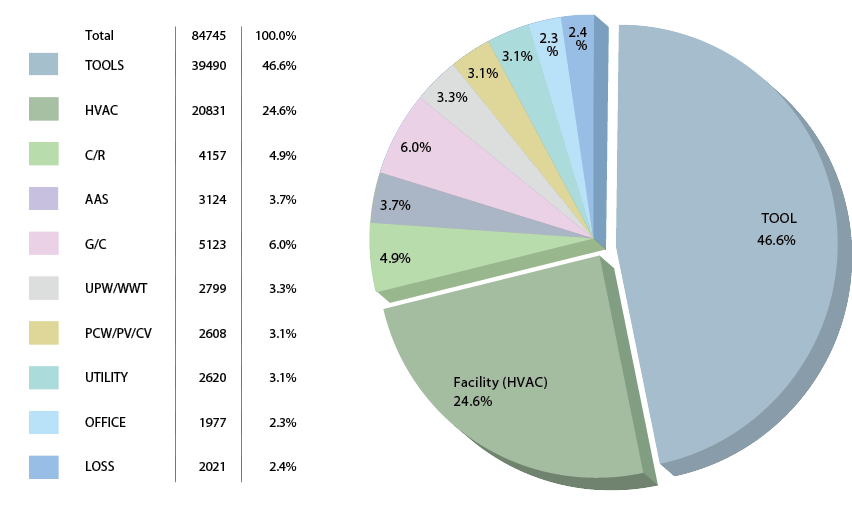
省能在設備機台方面,應該還有很大的空間可努力,但考量製程難度與生產效率等因素,必須循序漸進一步步的達成;機台若能做到其製程行為與廠務能源供應盡量同步,即在機台閒置時同步停止廠務系統之能源供應或減量,就能有效減少不必要的能源消耗 圖八。而透過製程調整或是能源回收技術來達到最佳化能源使用亦是可行的一個方向。
圖八、設備製程與廠務供應同步來達到節能( 資料來源:Applied Materials)
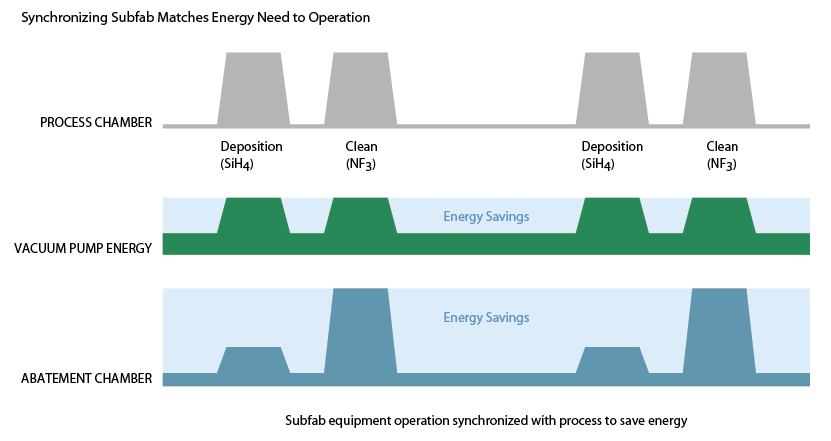
廠務系統能源的最大消耗來自無塵室空調,特別是當由無塵室所抽出的空氣越多,由外氣補回的也就越多,其結果導致冰水的用量相對增加,即越耗能;同理在化學原料的使用上,消耗越多即產生越多的廢液,處理的成本與複雜度自然就增加,而對環境的傷害易增多。
廠務在節能的設計,就空調系統來說,大部分仍是透過熱交換方式來達到能源的再利用,若要有更顯著的節能效果,我們必須有所創新找出其他不同的做法。目前我們已經設計將無塵室所抽出的乾淨空氣重新回收至非無塵室區域再使用,但其所佔整體排出氣體量的比例相當有限。我們知道現在運轉廠排氣系統的抽氣量都是較大的,其主要原因是生產機台對排氣壓力相當敏感,在實務操作上為求其壓力穩定、足量,因此會將供應量增加,以確保機台運作正常,但卻衍生超抽、耗能等問題;有鑑於此,壓力自動平衡的功能在排氣中就越顯重要,若能透過自動平衡風門的設計 圖九,將可穩定風管內二次側壓力(機台側),不但可以提供更穩定的排氣壓力,更能降低不必要的能源消耗,這是我們現在努力所要達成的重要節能目標之一。
圖九、自動壓力平衡風門設計概念圖
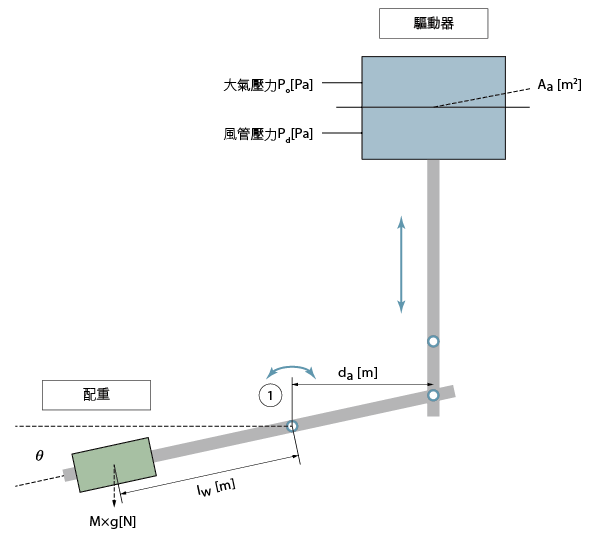
再來看看無塵室空調系統的節能設計的想法,晶圓的製造過程多屬於「非大氣」製程,即晶圓與生產設備在製造過程不與一般大氣直接接觸;無塵室區域通常以涵蓋主機台全區之範圍來設計,透過「高換氣率」或「HEPA/ULPA高覆蓋率」來滿足「全區」高潔淨度的需求,此一做法需要非常大的能源消耗。「小環境」(Mini Environment)潔淨室設計的導入,將所需較高潔淨度製程區劃在一定的範圍內,從而有效降低以全區高潔淨度設計所需的耗能。
在未來18吋(450mm)晶圓廠之潔淨室環境,比「小環境」更進一步的「微小環境」(Micro environment)設計概念將有助於達成更有效的能源減量。潔淨室環境將依製程需求做不同潔淨程度的區劃,針對與晶片接觸的製造環境提供較高的潔淨等級,而機台操作區與維修區將可依序調整降低。藉由提高氣流的「單一方向性」(Unidirectional)與提高氣流對製程區吹掃(Purge)的能力,讓潔淨循環氣流真正有效地提供製程所須的潔淨程度,如此許多非製程區劃潔淨循環氣流量便得以降低,進而減少潔淨循環氣流所需動力 圖十。若未來製程設備能大量採用此一設計概念,使機台完全覆蓋在「微小環境」概念的無塵室中,將大幅降低潔淨循環氣流的需求量,潔淨室的製冷與潔淨循環氣流耗從而大幅降低。依據SEMATECH對半導體工廠無塵室潔淨等級的規範,到2014年時,潔淨室用於廠務端空調的潔淨等級應降至ISO 7,到2020年甚至可降至ISO 9,而該等級已經可以用非潔淨室空調的條件來設計,若與現行潔淨室規格ISO 6相較,整體耗能將可減少25%以上。
圖十、未來450mm Fab 潔淨室設計概念圖
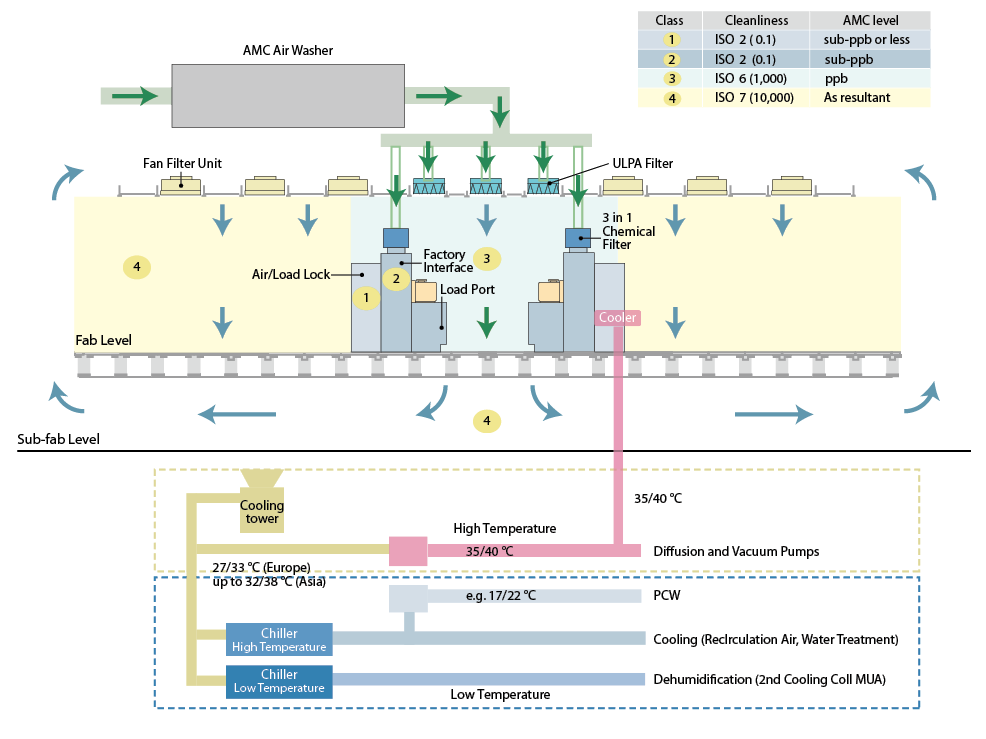
此外,潔淨室大部份的熱負載來自機台,其中超過60%的廢熱以製程冷卻水(Process Cooling Water)排出,現有之設計仍仰賴冰水機提供冷卻水(12℃)以熱交換方式將廢熱攜出,而實際上許多機台的廢熱大多高於冷卻液甚多;若能依據不同製程設備的需求,將部份設備的冷卻方式由低溫熱沉(由冰水機提供的冰水)改為高溫熱沉(如冷卻水塔),充份利用自然大氣溫度設備排熱的概念,將製程廢熱直接自冷卻水塔排入大氣,將可大量減少製冷所需之耗能。
回收(recycling)代表可重複再使用,它一直是節能的重要推手;回收效率愈好,所能省下的能源或資源就越大。水電是晶圓廠最大的能源消耗,很不幸的,他們已漸漸成為地球有限的資源,我們必須努力去找到更好的方法;儘管過去我們在水回收上已有不錯的成果,但未來18吋所面對的將是更大的需求;同樣在氣體與化學原料的減量上,除了從生產製程與設備上去努力外,廠務對回收技術的研發更是刻不容緩,像是氫氣(H2)及廢硫酸(H2SO4)與廢氨液(NH3)的回收。18吋代表著各種能源與資源的使用將大幅增加,回收技術與應用將更顯重要。
結論
18吋晶圓的放大直接反映了資源與能源消耗的增加,所使用的水、電、氣體與化學原料皆會大量增加,生產製造所產生的廢水、廢氣與化學廢液也會大量增加;如果能找到更有效的方法將這些消耗大幅減量,無論是從製程設備或是廠務系統,最終所帶來的效益除使我們更具競爭力外,更重要的是對地球環境與資源的保護,這也是每一個企業所應當負起的責任。
我們未來在18吋晶圓生產製造所面對的挑戰,也絕對是我們的機會。
留言(0)