摘要
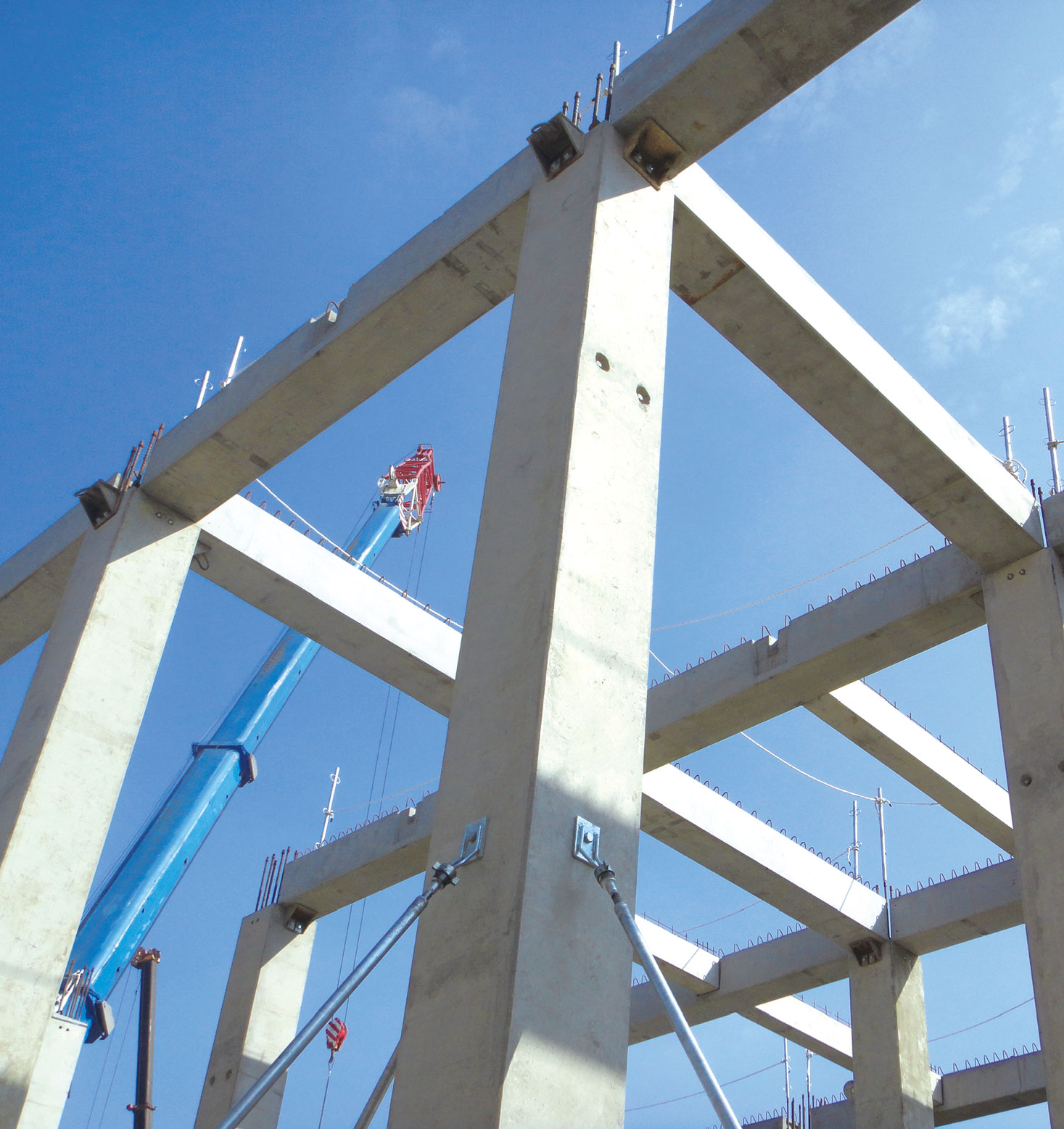
隨著台灣經濟的發展,社會環境的變遷,傳統結構體場鑄的技術工,日漸缺乏;形成以往的專案經常因缺工而導致進度延宕的風險;然而建廠的速度卻又不斷提昇,且新建廠房的數量也同步增加,因此本文主要說明預鑄工法的生產規劃的特點,並且以應用預鑄工法施作地下室結構體的F14P6 Fab專案為例。
前言
第二次世界大戰後,由於受到戰爭的被壞,房屋大量倒塌傾毀,短時間內需要大量的建築勞工進行重建,因此戰後房屋的需求造成預鑄工法在國外產生,而台灣約在民國六十年引進預鑄工法,主要以版式預鑄為主,其後逐漸發展預鑄外牆及SRC結構體預鑄。
目前在台南科學園區F14P5、F14P6 (晶圓廠房規模均為以往廠房面積的1.5~2倍),以及其他同業電子廠房,同時進行建廠工程,傳統模板工及鋼筋工不足問題,更形嚴重。就F14P6而言,預計十個月內必須完成廠房主結構體,由地下二樓至地上三樓的無塵室 華夫板(wafer slab)結構體,傳統施工需要大量模板工及鋼筋工等技術工種,要在此條件下達成十分困難,因此局部結構採預鑄工法來施工,以解決技術工不足問題。
預鑄工法
預鑄工法的起源
西元一八四○年,法國人孟尼爾(Monier)首先取得預鑄混凝土(P. C.)工法的專利,一九五一年,倫敦博覽會以不到六個月的施工時間,完成了令世人矚目的水晶宮(Crystal Palace),如 圖一,即是充分發揮了預鑄的精神。
圖一、1951 年 法國水晶宮設計圖
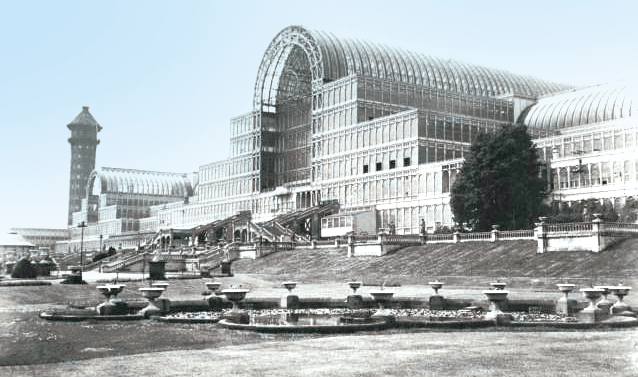
其後預鑄仍持續進展,然而當時仍視為臨時性的營建技術。直至一九三○年代,預鑄的實用化構想才漸趨成熟,並進入試驗工業化生產的階段,歐美各國預鑄工廠也紛紛成立,其間雖因第二次世界大戰而一度呈停頓狀態,但至一九五○年代,因戰後急速的復建工作,而產生大量的房屋需求;同時歐洲共同市場的建立,驟然地帶來了整體的經濟繁榮,促成勞動者與技工的缺乏,加上北歐區域地理上自然條件的限制-施工期限等各種因素的衝擊,迫使房屋建築施工法加以修正改良,因此預鑄構造開始大量應用於建築方面。
預鑄工法特性
「預鑄工法」即將結構物的組成單元分別預先製作,再經由不同或類似構件單元的組合或配合場鑄混凝土組合成結構體,有時為了實際的需要,預鑄構件亦可施加預力以增加結構的強度。而預鑄工廠就是生產預鑄單元的工廠,將生產完成的版片單元運送到現場利用吊車或其他吊裝機具進行組裝,如同鋼結構一般。因此,預鑄結構的單元生產無論是場鑄或預鑄,其生產流程和現場製作的流程大致上是相同的,所不同的是在預鑄廠會考慮到自動化生產及生產力的提升問題,所以將原來的生產流程,分成幾個並行的作業,同時進行,將傳統現場施工的營造業轉變成工廠生產的製造業模式。預鑄工法示意流程如 圖二。
圖二、預鑄工法流程示意圖
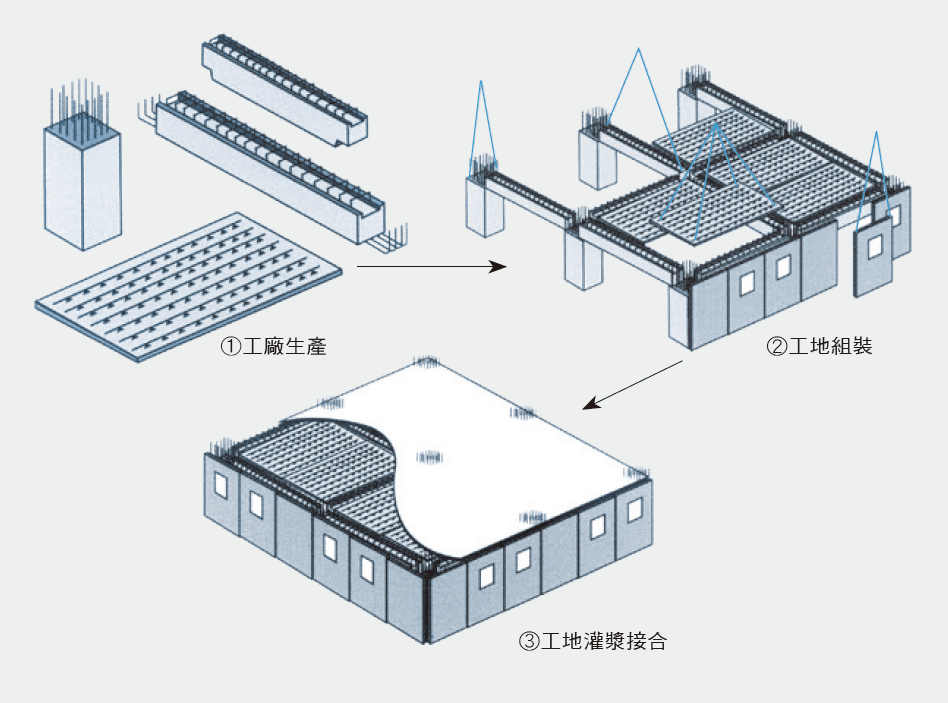
而在晶圓廠房短時間內需完成大量結構體工作的專案特性,預鑄工法可以有效大量降低對傳統人力的依賴、現場假設工程的鷹架、模板物料,降低施工環境的複雜度和維持施工動線的暢通,可有效提昇管理的效益。
預鑄工法優點
預鑄工法主要優點為穩定品質,例如地下2樓的9公尺高柱,預鑄的柱子可在工廠生產時,穩定的控制品質,主要因為預鑄生產將傳統工法站著垂直生產的柱,改成躺著水平生產,使得混凝土品質均勻穩定,減少產生蜂窩的可能性。
然而預鑄現場施工時不需要支撐以及不需模板的物料,由於假設性工程及模板大量減少,工地現場容易創造安全工作環境,如 圖三。
圖三、十四廠六期預鑄與場鑄區域的比較
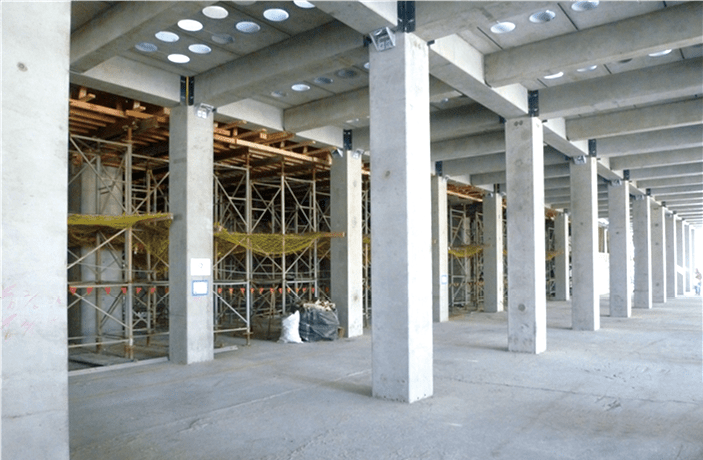
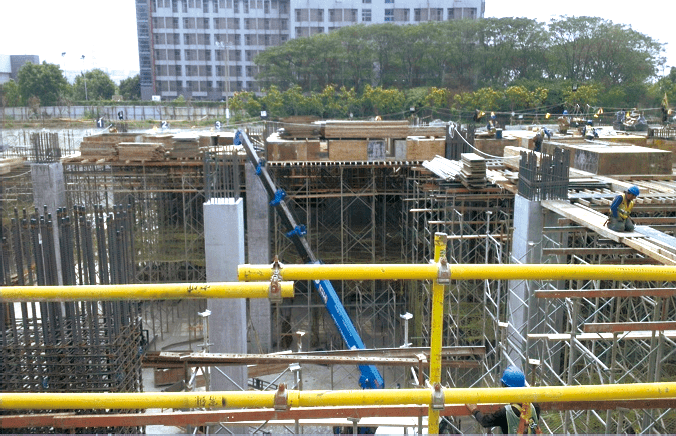
以機械吊裝,配合少量吊裝工,對模板及鋼筋等技術工依賴性降低,尤其現今台灣的社會環境變遷,一般青年人大多不願意從事高勞力的現場營造工作,導致傳統場鑄的鋼筋工及模版工人力逐日減少,以現今台積專案中鋼筋及模版工年齡分布為例,40歲以上勞工佔70%,而40歲以下僅佔30%,如 圖四。
圖四、專案鋼筋及模版工人力年齡分布
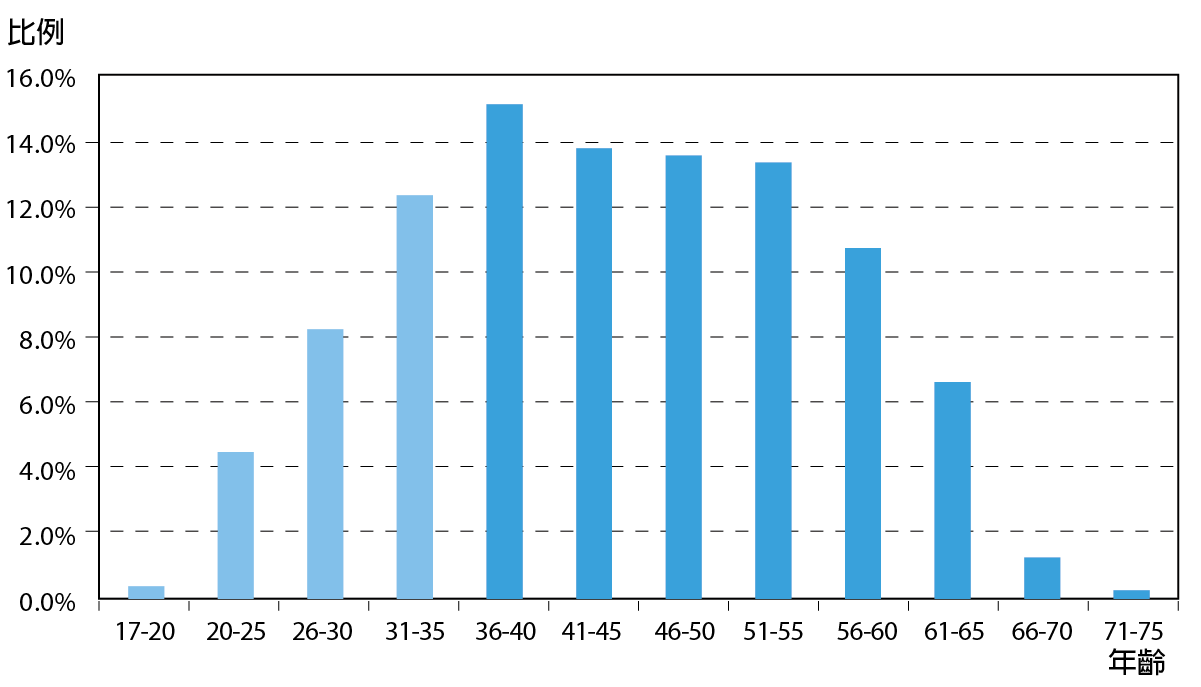
預鑄的結構構件在工廠生產,不受天候影響,可以提前生產,等到基礎完成時,即可進場組裝,減少許多傳統場助工法極容易受天氣因素影響出工而導致進度延宕的風險,同時因樑版下施工無支撐,除了可確保施工動線順暢,增加其他工程施工的效率,例如裝修工程以及管線、設備系統皆可以提早進場,不如場鑄工法,需要現場澆置的混凝土強度達設計規範的時間以及後續模版拆除、清模的工期。
預鑄生產規劃及應用
預鑄工法為一系統化工法,從規劃設計、生產製造到施工,是一連串的規劃,必須從源頭端便開始定義,由於預鑄的構件都是提前在工廠生產,並且經過仔細的規劃構件安裝的限制,所以在構件上的鋼筋的搭配,都必須考量安裝時的幾何空間條件,因此在設計變更的彈性不大,而且所影響的範圍較多。
例如預鑄模具必須配合調整、生產的進度也會因此變動、物料進出場的順序調整等等;不同於場鑄工程的彈性,可以在施工尚未進行前,進行設計的變更,因此對結構體構件:柱、樑、樓版等,都必須確認設計的彈性考量、接頭處理、構件生產製造的成本、搬運及工地現場的施工性等詳加考慮,對整體結構,哪些部分採取預鑄,何者採半預鑄、場鑄,做出最佳的抉擇與組合。
而在結構體上,適用預鑄工法的必須為結構單純簡易,形式單一,無需因應許多形式類型而增開大多的模具,且量體數量大的範疇,才能發揮預鑄的效益,例如晶圓廠房內大量的CP柱結構(724支),且柱斷面尺寸單一。
然而適用於場鑄工法,必須為數量少、結構類型多樣或是單一結構重量過重,不易以吊裝進行組立的構件,例如少量且構件重量不易吊裝的1.2m x 1.2m斷面大柱或是結構形式多樣且複雜的剪力牆。
預鑄生產規劃流程
預鑄生產規劃標準流程,如 圖五。當預鑄工廠取得訂單後,前期規劃進行場鑄及預鑄適合的範圍進行研究及評估,決定預鑄範圍後,則開始標準構件設計圖的繪製,約二週即可以讓預鑄工廠執行模具開設作業,通常模具的材質均為鋼模;並且配合施工計劃分區的吊裝工期,來回饋計算各種構件所需鋼模基本需求套數,因晶圓廠構件數量龐大,開模時間長達二個月,約一個月後即可生產標準預鑄構件,構件能滿模生產約需一個月至一個半月;在生產的過程中需確認鋼模的尺寸、鋼筋配筋量及分布、混凝土品質、預鑄構件成品的尺寸及表面修補處理;最後進行構件的編碼、分類儲藏,安排運輸至工地施工的規劃。
圖五、預鑄生產規劃標準流程
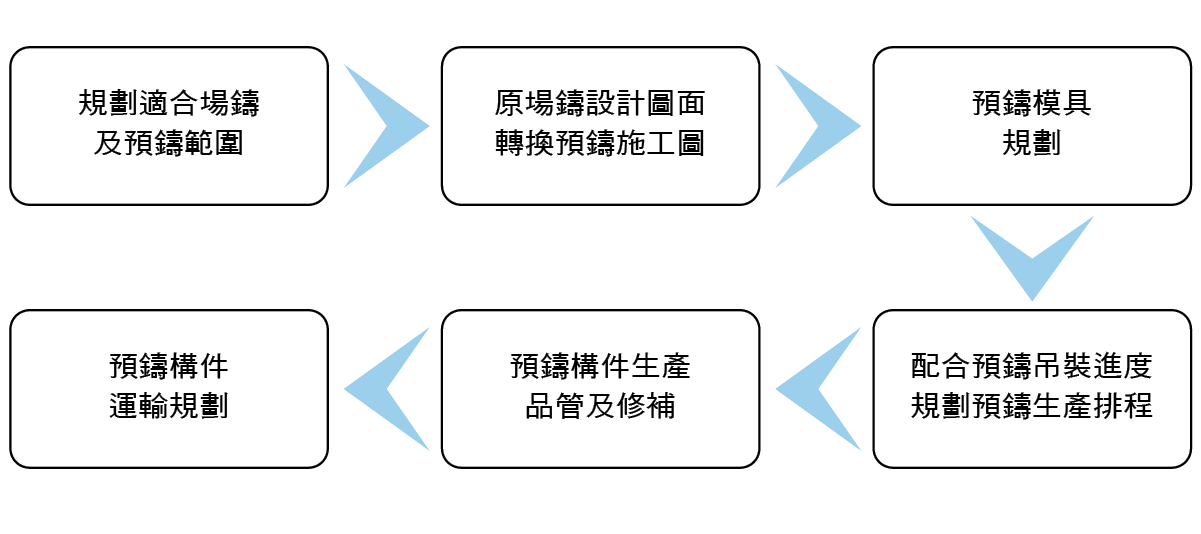
模具規劃
根據設計的圖說文件資料及施工規劃所提供之吊裝排程,按構件型式分類預排生產進度,計算出所需模具套數及模具場地,並依分類逐一設計以完成鋼模製作。
然而鋼模製作品質之優劣足以影響構件精準度及反覆使用次數,因此預鑄場在鋼模的製作有以下標準:
- 鋼模主要部份鋼版厚為4mm以上,且於樑、柱模具上加設橫向繫件,避免側向變形,期使生產構件品質達到最高要求。
- 鋼模承商於廠內配合底模鑽孔施作,避免孔位不合情形。
- 柱、樑鋼模採側模與底模焊死,並留些許餘裕於拆模時可供調整之用;此法可有效防止側模與底模處漏漿之情況產生,並可維持產品的均一性。
- 模具製作完成之驗收需由專案人員依模具製作圖面量測鋼模尺寸,以期符合預期之標準。
預鑄構件生產流程及進度規劃
當模具生產完成後,則開始預鑄構件的生產,其生產流程如 圖六。然而專案構件生產順序之依據,需考慮吊裝進度、相關物料進廠時程等問題。以各模排定之構件生產建立此一生產排程,並對照吊裝需求,在符合最佳工作度及儲存量下做適當之調整,如 表一所表示。
圖六、構件標準製作流程

各構件預訂生產支數 |
單日 |
各構件預訂生產支數 |
單日 |
||||||||
---|---|---|---|---|---|---|---|---|---|---|---|
日期 |
柱 |
大樑 |
小樑 |
版 |
小計 |
日期 |
柱 |
大樑 |
小樑 |
版 |
小計 |
101/12/10 |
102/1/14 |
10 |
12 |
10 |
25 |
57 |
|||||
101/12/11 |
102/1/15 |
10 |
12 |
10 |
25 |
57 |
|||||
101/12/12 |
1 |
1 |
102/1/16 |
11 |
12 |
10 |
25 |
58 |
|||
101/12/13 |
2 |
2 |
102/1/17 |
11 |
12 |
10 |
25 |
58 |
|||
101/12/14 |
3 |
3 |
102/1/18 |
11 |
12 |
10 |
25 |
58 |
|||
101/12/15 |
4 |
4 |
102/1/19 |
10 |
25 |
35 |
|||||
101/12/16 |
4 |
4 |
102/1/20 |
||||||||
101/12/17 |
5 |
1 |
1 |
1 |
8 |
102/1/21 |
11 |
12 |
10 |
25 |
58 |
101/12/18 |
1 |
1 |
2 |
1 |
5 |
102/1/22 |
11 |
11 |
10 |
25 |
57 |
101/12/19 |
6 |
2 |
3 |
1 |
12 |
102/1/23 |
11 |
12 |
10 |
25 |
58 |
101/12/20 |
6 |
2 |
4 |
1 |
13 |
102/1/24 |
11 |
12 |
10 |
25 |
58 |
101/12/21 |
6 |
2 |
4 |
1 |
13 |
102/1/25 |
11 |
12 |
10 |
25 |
58 |
101/12/10 |
6 |
2 |
8 |
102/1/26 |
11 |
12 |
10 |
25 |
58 |
||
101/12/11 |
102/1/27 |
||||||||||
101/12/12 |
6 |
2 |
8 |
5 |
21 |
102/1/28 |
11 |
12 |
10 |
25 |
58 |
101/12/13 |
6 |
2 |
8 |
5 |
21 |
102/1/29 |
11 |
12 |
10 |
25 |
58 |
101/12/14 |
6 |
2 |
8 |
5 |
21 |
102/1/30 |
11 |
12 |
10 |
25 |
58 |
101/12/15 |
6 |
2 |
8 |
5 |
21 |
102/1/31 |
11 |
12 |
10 |
25 |
58 |
101/12/16 |
6 |
2 |
8 |
5 |
21 |
102/2/1 |
11 |
12 |
10 |
25 |
58 |
101/12/17 |
6 |
2 |
8 |
16 |
102/2/2 |
10 |
10 |
11 |
31 |
||
101/12/18 |
102/2/3 |
||||||||||
101/12/19 |
6 |
2 |
8 |
9 |
25 |
102/2/4 |
11 |
12 |
10 |
25 |
58 |
101/12/20 |
2 |
2 |
102/2/5 |
11 |
12 |
10 |
25 |
58 |
|||
101/12/21 |
6 |
5 |
8 |
11 |
30 |
102/2/6 |
11 |
11 |
10 |
25 |
57 |
102/1/3 |
10 |
8 |
10 |
13 |
41 |
102/2/7 |
11 |
12 |
10 |
25 |
58 |
102/1/4 |
10 |
10 |
10 |
17 |
47 |
102/2/8 |
11 |
10 |
10 |
25 |
56 |
102/1/5 |
2 |
6 |
20 |
28 |
102/2/9 |
||||||
102/1/6 |
102/2/10 |
||||||||||
102/1/7 |
10 |
12 |
10 |
25 |
57 |
102/2/11 |
|||||
102/1/8 |
10 |
12 |
10 |
25 |
57 |
102/2/12 |
|||||
102/1/9 |
10 |
12 |
10 |
25 |
57 |
102/2/13 |
|||||
102/1/10 |
10 |
12 |
10 |
25 |
57 |
102/2/14 |
|||||
102/1/11 |
10 |
12 |
10 |
25 |
57 |
102/2/15 |
|||||
102/1/12 |
6 |
12 |
10 |
11 |
39 |
102/2/16 |
|||||
102/1/13 |
102/2/17 |
十四廠六期廠房預鑄生產應用
以十四廠六期為例,於2012年11月15日給予預鑄廠商訂單,在一個月內完成結構及預鑄上的規劃設計後,預鑄廠隨即於2012年12月12日投入生產,並且在一個半月內便達足以吊裝施工的數量,於2013年2月4日開始現場吊裝,而全數構件規劃於4月19日完成;共計預鑄生產總工期從發包到設計、生產全數完成共153天完成,預鑄構件數量共4,008件,如 表二。
構件別 |
構建數量 |
體積(m3) |
平均體積 |
平均重 |
模具數 |
||
---|---|---|---|---|---|---|---|
柱 |
長柱 |
358 |
1,090.14 |
3.0 |
7.31 |
4.8 |
11 |
短柱 |
366 |
700.89 |
1.9 |
4.60 |
4.9 |
||
大樑 |
兩截樑(有K) |
340 |
724.2 |
2.1 |
5.11 |
4.6 |
12 |
兩截樑(無K) |
358 |
762.5 |
2.1 |
5.11 |
4.8 |
||
兩截樑(有版) |
28 |
77.6 |
2.8 |
6.65 |
0.4 |
||
短樑(有K) |
53 |
56.2 |
1.1 |
2.54 |
0.8 |
||
短樑(無K) |
61 |
65.0 |
1.1 |
2.55 |
0.9 |
||
短樑(有版) |
3 |
4.1 |
1.4 |
3.32 |
0.1 |
||
小樑 |
深挖區 |
460 |
240.12 |
0.5 |
1.25 |
6.2 |
12 |
高版區 |
355 |
231.64 |
0.7 |
1.57 |
4.8 |
||
格子版 |
高版區 |
710 |
1,129.73 |
1.6 |
3.82 |
13.0 |
13 |
KT版 |
深挖區 |
916 |
670.53 |
0.7 |
1.76 |
12.3 |
11 |
合計 |
4,008 |
5,752.63 |
59 |
十四廠六期預鑄構件種類
以FAB14P6為例,主要構件有預鑄柱,樑分成單節樑及雙節樑,版分成半預鑄KT版及全預鑄的格子版等,如 圖七。
圖七、十四廠六期預鑄構件種類

十四廠六期預鑄構件生產流程
以FAB14P6為例,主要構件有預鑄柱,樑分成單節樑及雙節樑,版分成半預鑄KT版及全預鑄的格子版等,如 圖七。
預鑄柱
F14P6柱尺寸(60X60),長度有6公尺及9公尺,尤其9公尺長柱在傳統施工上,鋼筋、模板及混凝土施工十分不易,且施工期間需大量施工架,改用預鑄後,不僅可減少危險性高的施工架,而且結構品質也容易確保,同時減少技術工的需求,生產流程如 圖八。
圖八、十四廠六期預鑄柱生產
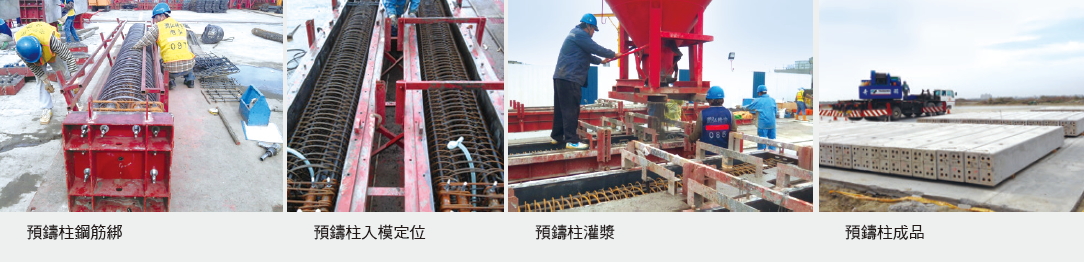
預鑄樑
F14P6預鑄樑斷面尺寸(50X80),長度短,但因樓高,傳統施工需大量支撐排架,改用預鑄後,不僅可免支撐,樑下施工動線順暢,同時減少技術工的需求,並且為更有效縮短工期,部分樑的設計採取雙節樑,將兩節樑的結構,設計為單一構件以減少吊裝數量;預鑄樑生產流程,如 圖九。
圖九、十四廠六期預鑄樑生產
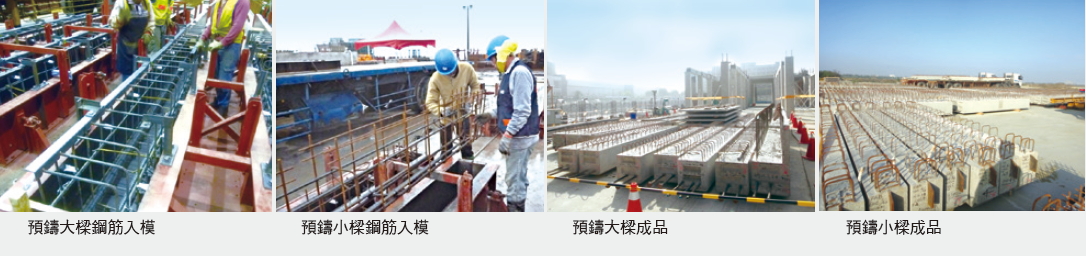
預鑄樓版
預鑄樓版主要有半預鑄KT樓版及全預鑄格子版,主要依建築物之設計類型、施工需求及揚重能力來決定採用類型。半預鑄KT版生產設備較簡單,而半預鑄的設計如 圖十,為減少KT版預鑄構件的重量以利現場吊裝,因此設計為版厚8公分;待現場吊裝完成後,再進行場鑄12公分厚度的澆置,共20公分厚。格子版生產設備較複雜,樓版採用預鑄,不僅可免支撐,版下施工動線順暢外,同時減少洞洞阪孔洞混凝土表面修補的工作,而在管架預埋件(unit strut) 的安裝,在預鑄工廠也比工地施工來得簡易。
圖十、十四廠六期預鑄樓版生產
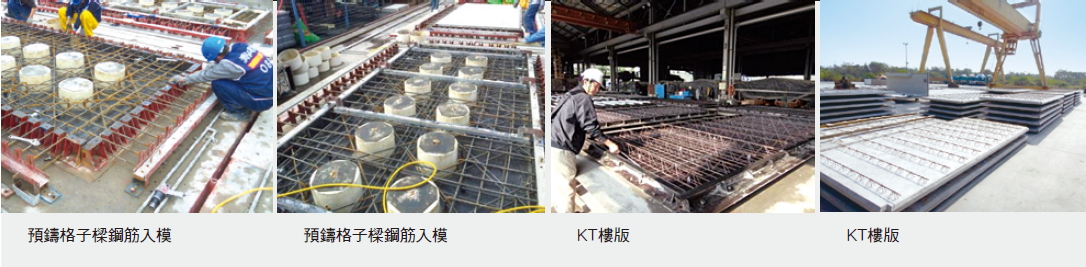
預鑄生產排程
以大樑為例,根據工地分區與分區進度,確定各分區構件數,如 圖十一大樑生產-吊裝進度比較表,即可計算出所需鋼模套數,每區生產時間,依生產後七日可以吊裝原則,做出大樑生產-吊裝進度比較圖,過程實際生產完成日必需比預計完成日早,即可符合工地需求。
圖十一、大樑生產─吊裝進度比較表
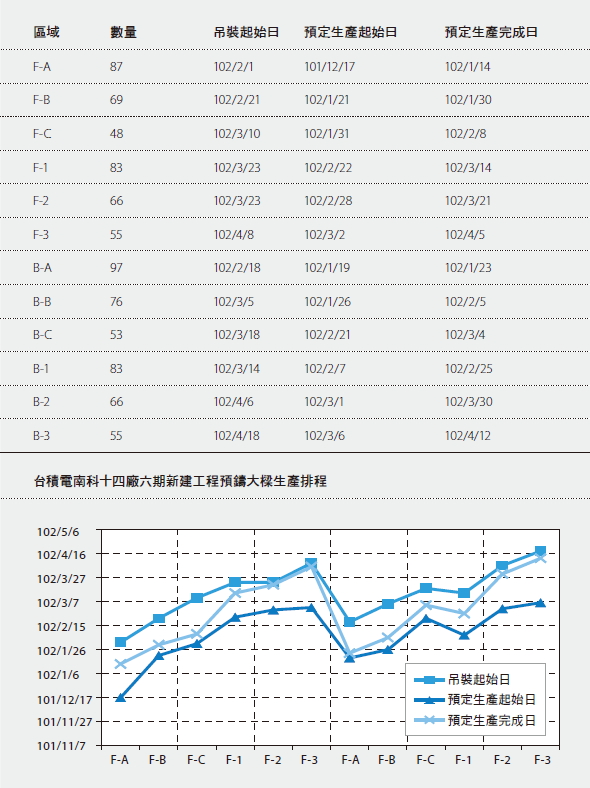
結語
總結預鑄工法在建廠過程中主要的優點如下:
降低天候因素影響
因各組件預先在工廠鑄造後再運至工地組合,因而各構件品質,可在工廠以系統化、標準化方式加以管制,不受天候影響,解決場鑄常因天候因素影響出工人力而造成進度延宕的風險。
縮短工期
預鑄工法只需在現場將預製組件加以吊裝組立即可,減少傳統場鑄方法在現場釘模、紮筋、搗築、養護、拆模、清模等步驟所占用的時間,可提前完成土建結構,移交給下一階段系統及管路工程施工。
大量減少場鑄所需之人力
由於現今蓋廠速度越來越快,且同時間竹科、中科、南科廠房以及其他同業電子廠房皆進行新建工程,造成場鑄的技術人工大量重疊、導致資源不足,而預鑄的大量生產製造的方式,使得鋼筋、模版人工需求可減至最小限量,解決人力資源不足的問題。
參考文獻
- 潤泓精密工程,「F14P6預鑄生產計劃書」(2013)
- 潤泓精密工程,「F14P6預鑄施工吊裝計劃書」(2013) 。
- 葉冠志,「建築物生命週期之環境成本模擬分析:混凝土預鑄與場鑄工法之比較」,國立臺灣科技大學營建工程系 (2012)
- 章舜欽,「房屋建築自動化施工之初步研究 -以RC建築預鑄工法為例」,台灣大學土木研究所,(2008)
- 陳啟仁,「建築預鑄工法與傳統工法於台灣及泰國之成本分析探討」,台灣大學土木研究所,(2008)
- 尹衍樑,賴士勳,「台灣地區預鑄技術發展與應用」,技師月刊No.46 (2007/09)
留言(0)