摘要
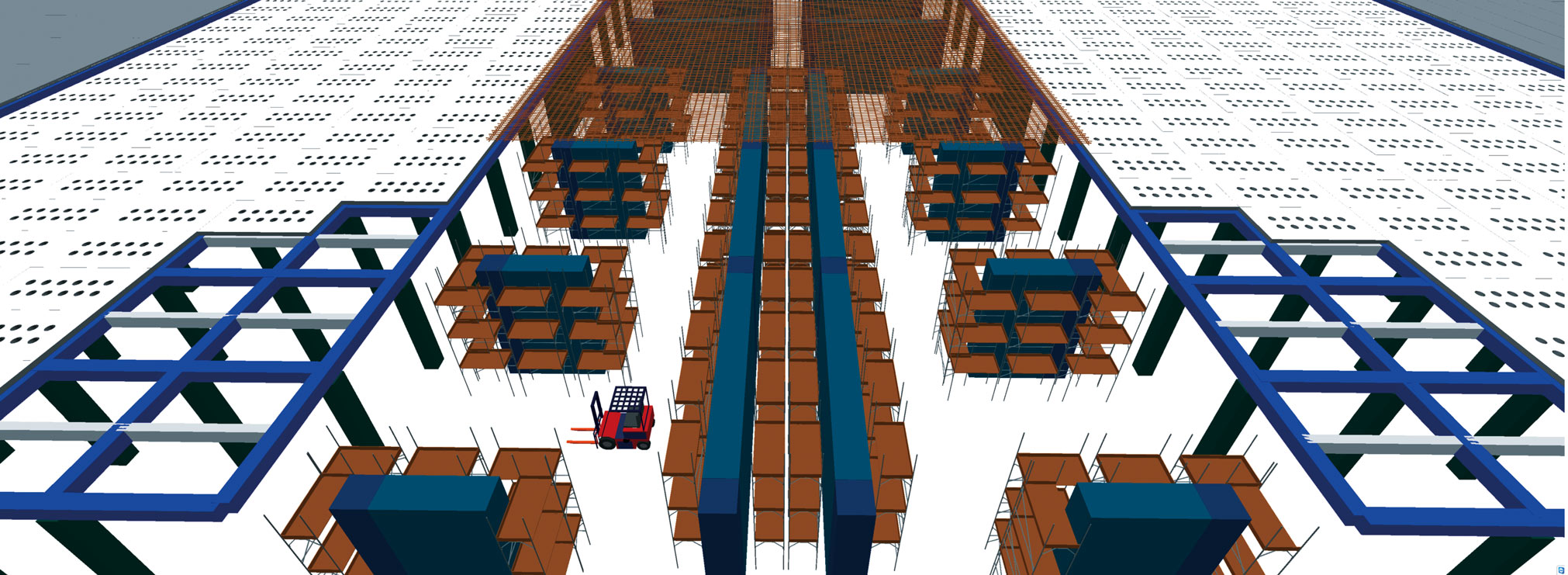
廠房建築施工多維度模擬應用
Keywords / Construction Simulation2,Building Simulation,Object Oriented
本文將介紹針對晶圓廠下部結構製作4D施工模擬之研究過程與成果,旨在探討應用電腦輔助工具於高科技廠房建廠施工優化,解決以往不易掌握之資源分配、空間衝突、排程管理等問題。研究係藉助台積電十四廠七期下部結構之場、預鑄混合施工案例,建置結合排程數學模型與3D視覺化模型之4D建廠施工模擬,以有效的預測施工期間的空間衝突、增加人員機具等資源的使用效率,藉此比較不同施工方案在成本、工期、空間衝突風險等各層面的優劣差異。
前言
在高科技產業激烈的競爭中,時間絕對是決定勝負的關鍵因素之一。廠房建造若能越快完工,製程就能越早開始運轉,產品便能在市場上取得更有優勢的競爭力,故如何有效縮短建廠工期一直是非常重要的議題。
以往建廠時程規畫往往是由一個固定的工期長度來回推每個工程項目可以運用的時間,以此推估土建可以施作的時間、機電系統建置時間、設備移入的時間等。如此的規畫方式無法預見實際施工時的空間衝突,亦缺乏一個具說服力的數學模型來評估人力、機具、物料運用的效率,因此很難在規劃階段即判定何種施工方案較佳。
為解決上述問題,筆者運用名為Arena的系統分析軟體,透過模擬程式建置排程數學模型,將人力、機具、物料等資源納入考量,以符合施工邏輯的數學模型評估各種施工方案的效率,模擬並計算不同施工方式在工期、成本、工作效率等各個層面的差異,最後再輔以目前台積電建廠所使用的Crystal 5D 系統建置4D施工模型,以檢核現場的空間衝突、甚至排程的邏輯錯誤,使專案的規畫能更有所依據。
本文首先將回顧一些相關文獻,瞭解4D施工模擬之背景現況及問題所在、再說明其研究目標、方法,排程之數學模型、相對之3D視覺化模型、4D施工模擬。此外,亦詳加討論施工模擬案例之分析、結果及未來可行性之研究與展望,最後本文將研究之精要濃縮總整完結。
文獻回顧
首先討論Bonsang Koo and Martin Fischer (2000) “FEASIBILITY STUDY OF 4D CAD IN COMMER-CIAL CONSTRUCTION”[1],此文作者發現以傳統的規畫工具如Critical Path、Bar Chart、Arrow Diagram、Precedence Diagram來描述工程計畫,雖然可以快速展現施工排程,但在缺乏3D模型輔助下,這樣的呈現方式往往造成工程人員主觀的誤解,使得施工衝突頻頻,於是作者決定著手研究藉由4D CAD是否能真正解決溝通障礙造成的施工衝突,以使施工效率提升。此篇研究以三棟設計相同的商辦建築,分別以傳統的排程方式和4D CAD規劃其施工,藉此研究4D CAD的可行性。而實驗結果顯示,雖然4D CAD的建模工作需投入多達119 man-hours的人力資源,但藉由4D CAD,工程人員能夠直觀的預見現場施工的情況,而非以想像的方式檢核施工衝突,此舉大幅減少了施工問題,更有效縮短了處理問題的時間,凸顯了4D CAD的價值。
崔紘瑞[2]以半導體廠房土建施工界面衝突造成生產力折減程度作為研究主體,作者歸納場鑄工程所遭遇到施工衝突的原因,而其亦指出對不同工種而言,空間不足產生的功率折減程度亦不相同,並可依此歸納出整體生產力的折減函數,值得參考此篇研究結果建置排程數學模型。
江翊楷[3]以格子板工程中FRP (Fiberglass Reinforced Plastics)模具搬運與組裝流程為例,進行動線規劃應用於重複性工作之效益計算,並利用物件導向工具(Object-oriented programming, OOP)建立工作模型,以單一格子板工作群組為單位進行工期推估。而在預鑄施工模式中,吊裝一樣為重複性高的工作項目,而吊車的動線規劃亦影響吊裝的效率,故可以參考該文獻的建模、以及參數檢驗方法,以其架構建置預鑄區排程數學模型,以檢核吊裝工作效率。
研究方法
研究架構
如前述,本研究以台積電十四廠七期 Fab建築物的下部結構工程為模擬對象,此案例採用場鑄與預鑄混合的施工方式,造成現場工作疊合度昇高,而兩種工法的施工方式又有一定的差異,因此人員機具在施工期間發生衝突的機率很高,而為了避免施工衝突造成的效率折減,事前的施工規劃格外重要。
如 圖一所示,研究擬從現地觀察出發,蒐集現場資料並整理場預鑄施工邏輯以歸納施工排程的數學邏輯,待發展出適當之邏輯後即開始建置排程數學模型,後透過專案人員的檢驗,確保此套數學模型能真實的反應出施工狀況。最後再以此數學模型予以不同的條件來檢核不同施工方案的優劣,並結合Crystal 5D檢查空間衝突狀況,以求達到施工效率優化的研究目的。
圖一、計畫流程圖
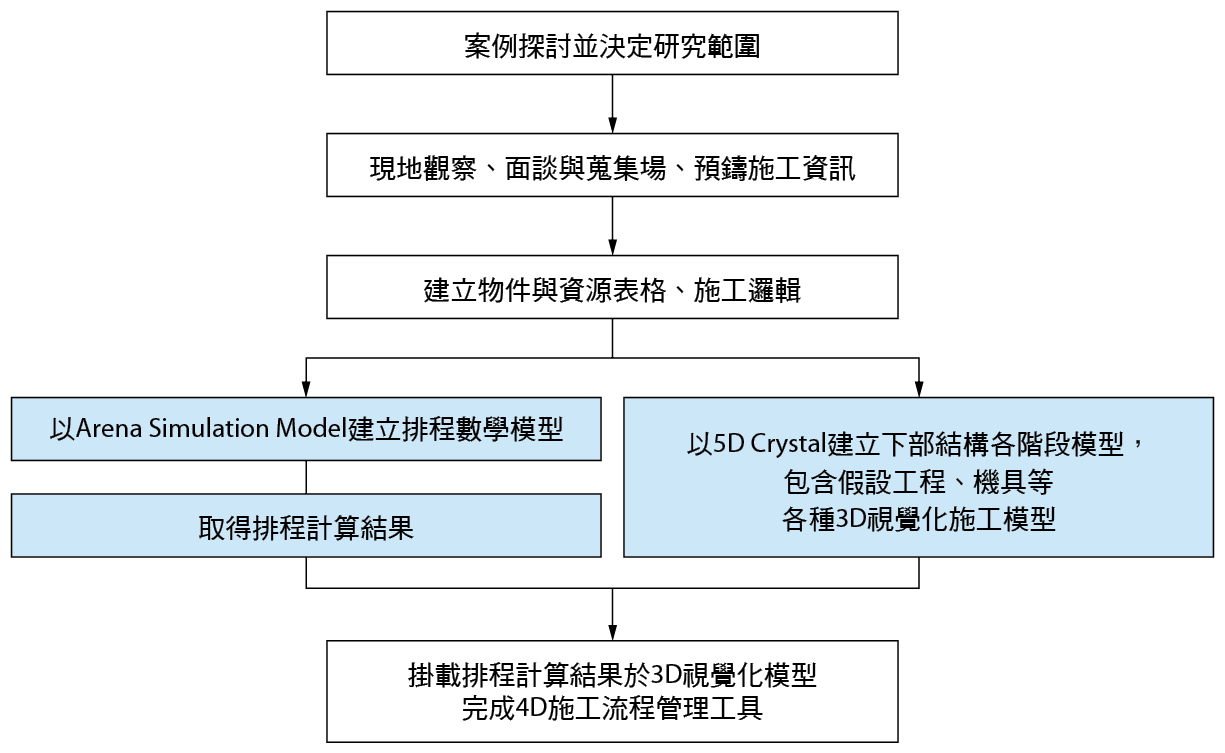
實例背景
圖一為本計劃流程,研究決定以台積電十四廠七期的FAB棟下部工程為模擬測試範圍。如 圖二,FAB下部工程以HPM側為要徑,由右側向左側施工,當一樓樓地板之進度完成百分之五十以上,鋼構廠商即可接續進行FAB上部結構之鋼結構吊裝,因此本專案選擇以S.5 line至M line及3.5 line至20.5 line之範圍作為研究區域,模擬中迴風區場鑄工程與兩側F3、B1高板區,F2、B2低板區預鑄吊裝工程的施工狀況。
圖二、研究範圍
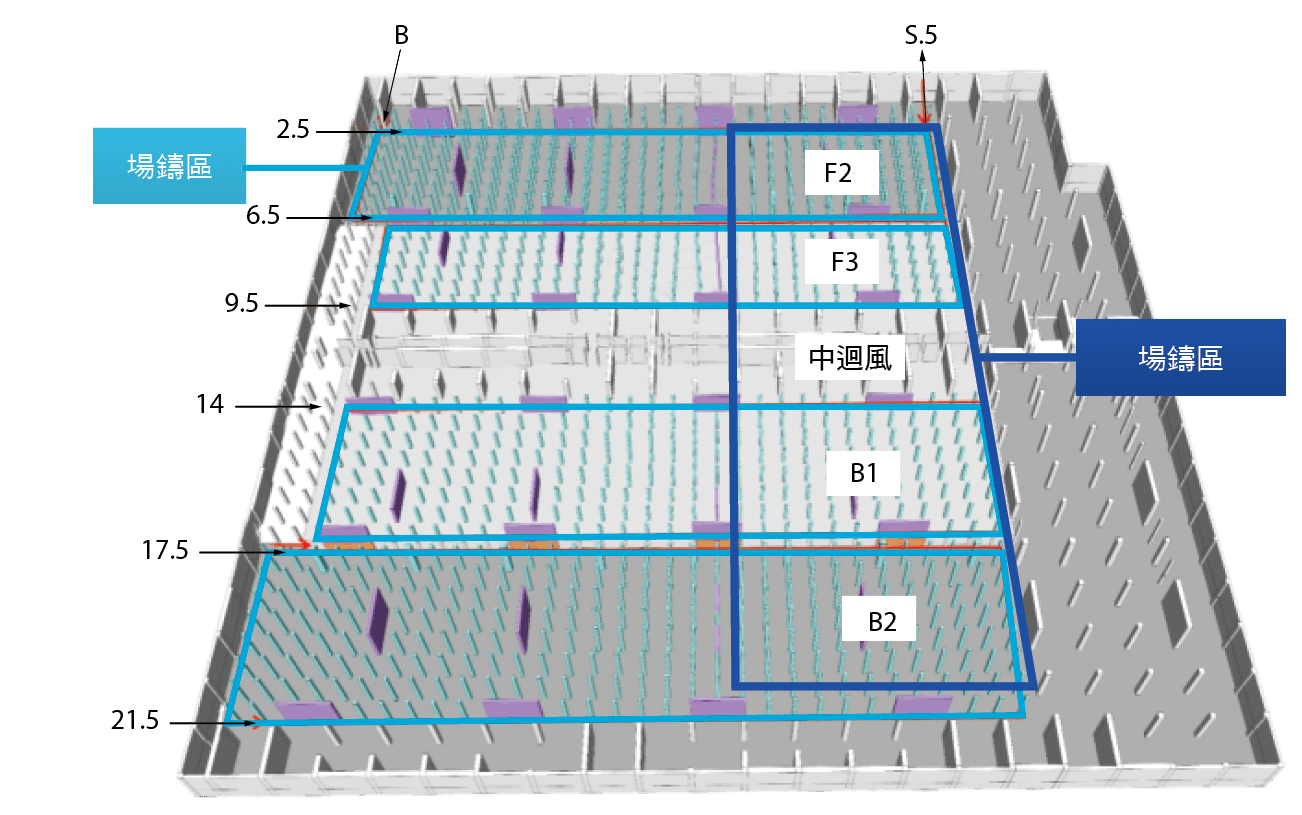
排程數學模型
首先討論排程數學模型,模型的架構如 圖三所示,依序為參數輸入、執行運算、產出結果,而十四廠七期中使用了兩種工法,故計畫將場鑄與預鑄分開建置成兩個數學模型。
圖三、排程數學模型架構
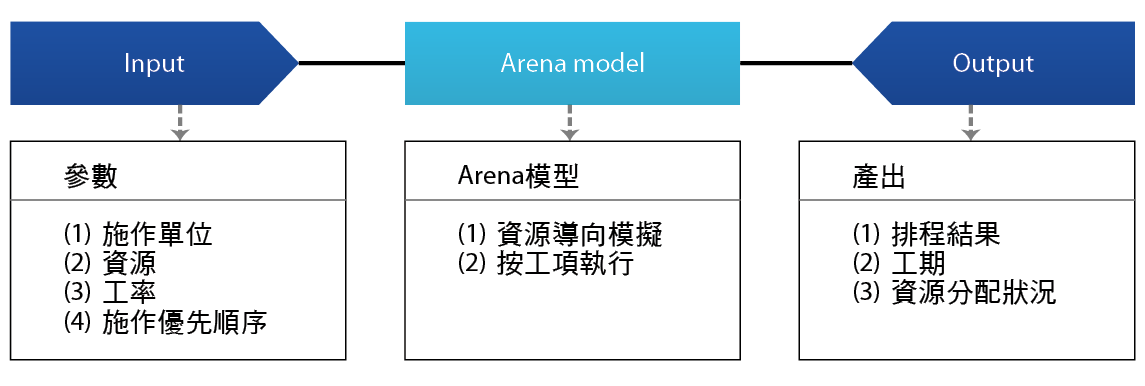
Arena是市面上一套專業的系統分析軟體,透過他建立模型來模擬真實的系統,以了解其動作行為,並進一步分析不同決策對其產生之變化,透過此一模擬實驗來得到系統改變後的量化與結果,Arena主要是以物件導向的方式執行運算,故必須釐清物件類別,並歸納其邏輯以及屬性,始得建模。Arena以往主要應用於工業工程領域中的製程優化,以產品導向做為檢核生產線效率的核心概念。於此,應用在排程計算時,需要將施工物件當作生產線中需要經過加工(Process)的產品單元(Entity),並賦予性質(Assign)使其能依循施工流程,記錄經過每個工項的時間點,以至運算完成時匯出排程時間資訊。
預鑄區排程數學模型
預鑄物件主要可分成柱、樑、板三大類,每類物件可再細分為不同項目,如柱有6米與9米兩種規格,樑可分為大小樑與雙節樑,板的部分有洞洞板和KT板,而運算邏輯的部分,因預鑄工法在吊裝時以其「施工之便利性」為主要考量,所以建製模型時將以空間因素作為吊裝優先順序的判斷依據。
歸納其施工邏輯,必須考慮到預鑄工序、數量限制、施作因素、吊裝習慣等因素。在預鑄工法中必須考量不同物件組裝之相互關係,此案例中吊裝必須依照「柱→柱底灌漿→X向大樑→Y向大樑→小樑→板」的順序進行組裝,而數量限制則是考量吊裝時該物件的先決條件,如現場必需先完成兩根柱子才能掛上一段樑等,而另外要考慮的還包括吊車的作業習慣,如在施作時要先從距離吊車較遠的物件吊裝,已吊裝之物件才不會影響吊臂的移動,因此預鑄吊裝習慣從遠吊到近。以上這些限制雖然無法在Arena裡視覺化的呈現,但仍必須將其納入,方可在計算時決定每個物件被吊裝的優先順序。
圖四是從 圖二標示之F2、F3區域,考量預鑄施工的邏輯,將其高低板區域切割成多個單元,並把每一單元視為一個Entity,預鑄區的Process為吊裝大樑、吊裝小樑等吊裝時的工序,而每一個Entity中所含柱、樑、板的數量則決定了完成該施工單位所需的時間;而F2、F3區與B2、B1區對稱,故中迴風區另一側的高低板區可依此類推。
圖四、預鑄區施工單位劃分
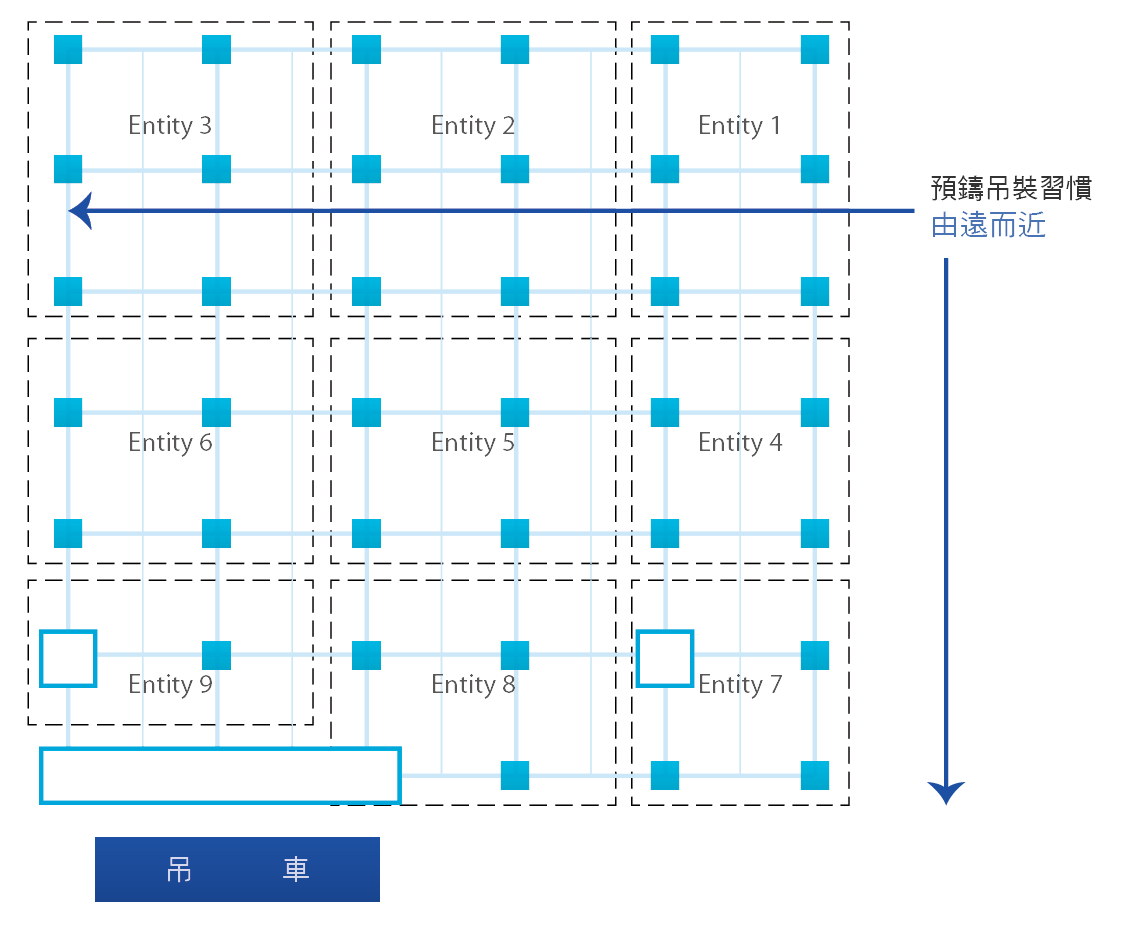
圖五為預鑄區Arena之數學模型,模擬開始時Entity會由左上角之名為Precast Unit的Create模組產出,沿著路徑經過Assign賦予屬性以及各個代表預鑄工項的Process,最後抵達Dispose,匯出途中所紀錄之時間資訊,運算模式大致為此。
圖五、預鑄區Arena 模型
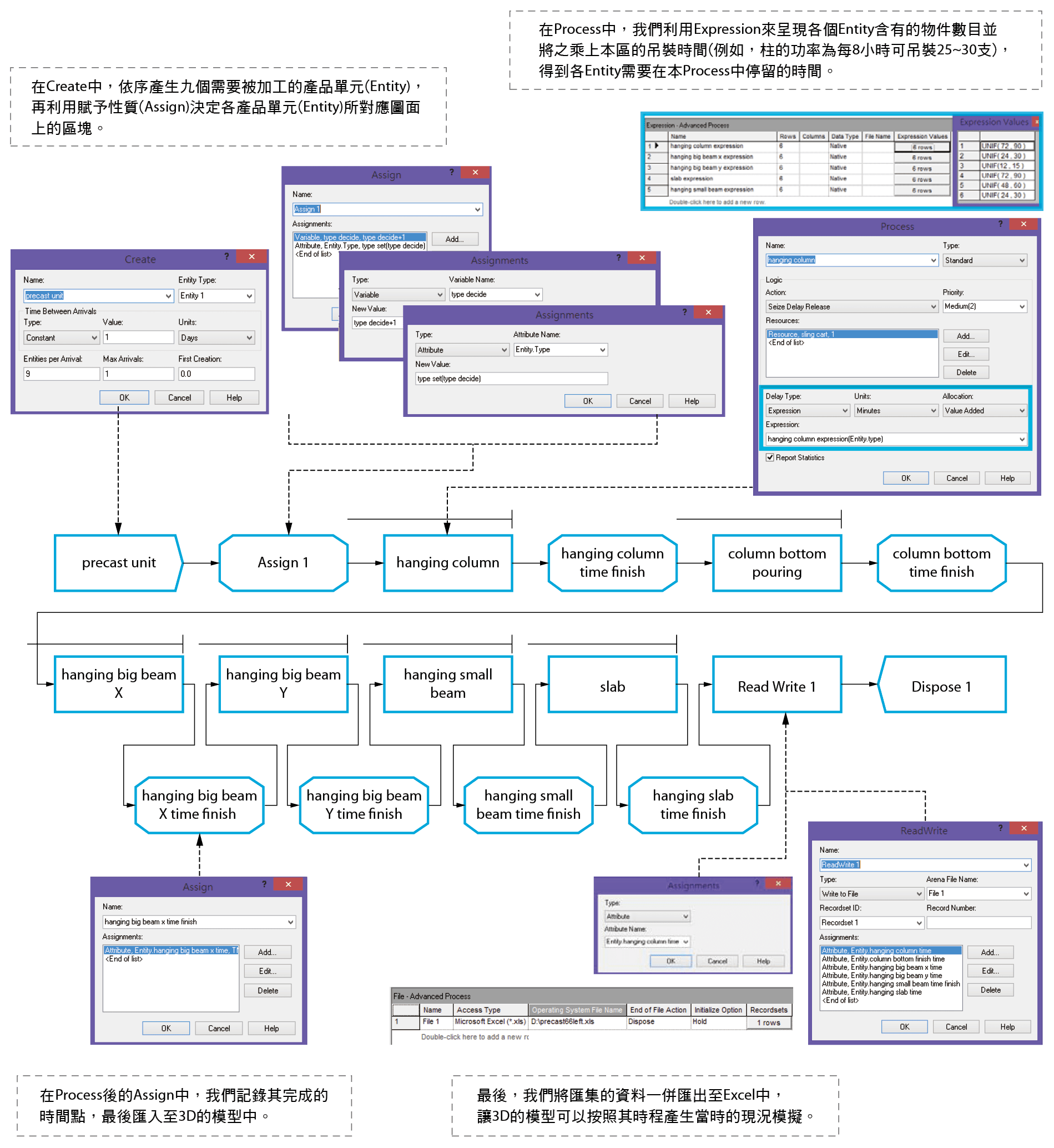
場鑄區排程數學模型
場鑄區的施工邏輯與預鑄區有很大的差異,相對於預鑄區的物件只需要考慮吊裝與鑄底灌漿,場鑄的物件卻要從頭開始施作,從綁筋到拆模一個都不能少。不過相對而言,在撰寫場鑄Arena模型時卻不需要分成多個施工單位,因為其工作面大,區域中的進度亦沒有顯著差異,故可以將多個物件以分包的概念組成一個大施工單位,在劃分施工單位時較預鑄區容易許多,如 圖六即為場鑄中迴風區的施工單位的劃分,可簡單的以藍色虛線分成上下兩個部分以及三種剪力柱牆規格(Type1~3),表一為實際施工與Arena模擬邏輯的對照。
圖六、場鑄區施工單位劃分
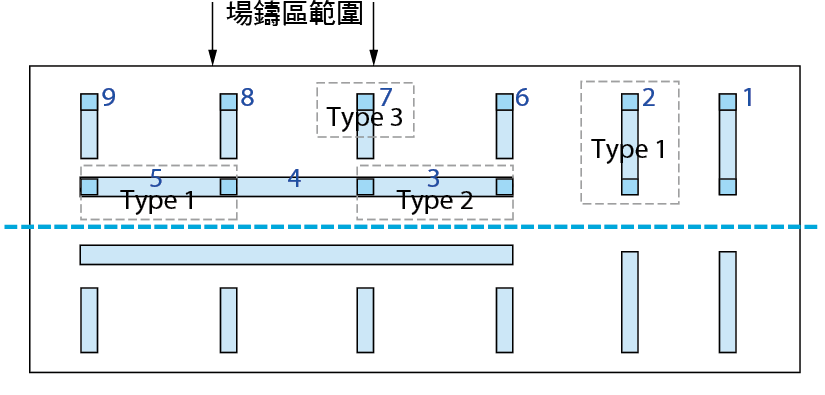
實際施工 |
Arena施工邏輯 |
---|---|
Frontend、Backend由不同包商同時施工 |
以單邊為模擬對象(Frontend) |
場鑄區內以剪力牆為主要物件,而剪力牆上會再連接樑、板 |
以各堵剪力牆為Entity,模擬區域內有9個物件,可歸類成三種類型 |
場鑄區施作時間受到物件量體大小影響 (僅可調查到各工項全區完成時間) |
某工項全區施作時間×某物件量體/總量體 = 某物件施作時間 |
架重型支撐架、組樑版模板及樑版灌漿等工項,乃是大範圍同時施作 |
該工項施作時不再以單一物件為單位,而必須等待其他物件完成才進行 |
因應場鑄之工種繁多,場鑄Arena模型的重點在於建立資源(Resource)分配邏輯式。在資源分配邏輯中,要設定不同工項對應不同工班,而同工項的工班亦不互相共用,且需另外設定物件對資源需求的上下限,以反映資源不足造成的功率折減。
圖七為模擬缺工狀況下產生工率折減的範例,目前在Arena模型中以線性折減作為缺工狀況計算,只要滿足可施作的人數限制,即可以當量方式計算該工項完成時間。
圖七、資源分派方式的差異
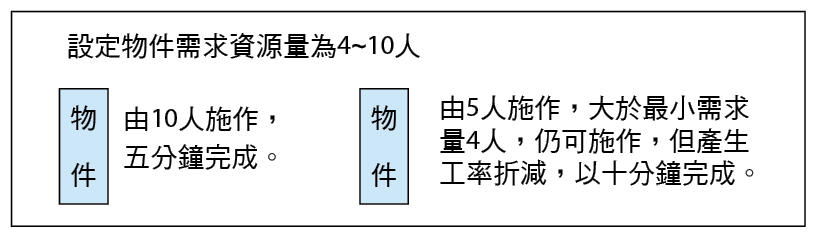
由以上邏輯限制,依照場鑄區的特性規劃了以資源池分派資源的運算模式。如 圖八所示,運算時可將資源依工項中設定的資源擷取邏輯從資源池中取得資源,使該工項能夠以工率折減的方式計算在缺工情況下的完工時間,而不會因人數不足而持續停滯。有了此一概念,資源模型的架構大致如 圖九所示,轉換成Arena模型設計則如 圖十所示。
圖八、資源池邏輯概念
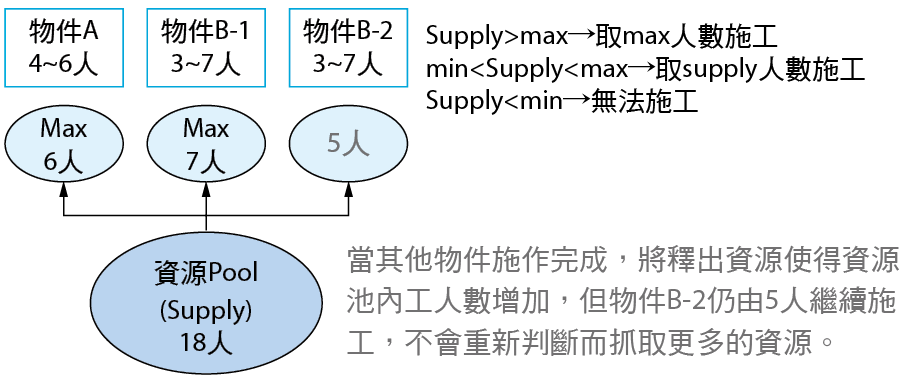
圖九、場鑄Arena 模擬流程
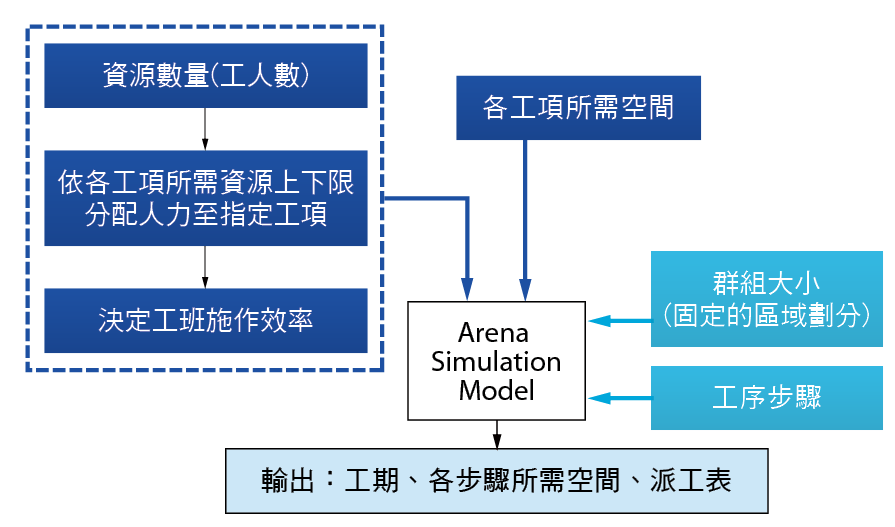
圖十、場鑄區Arena 模型
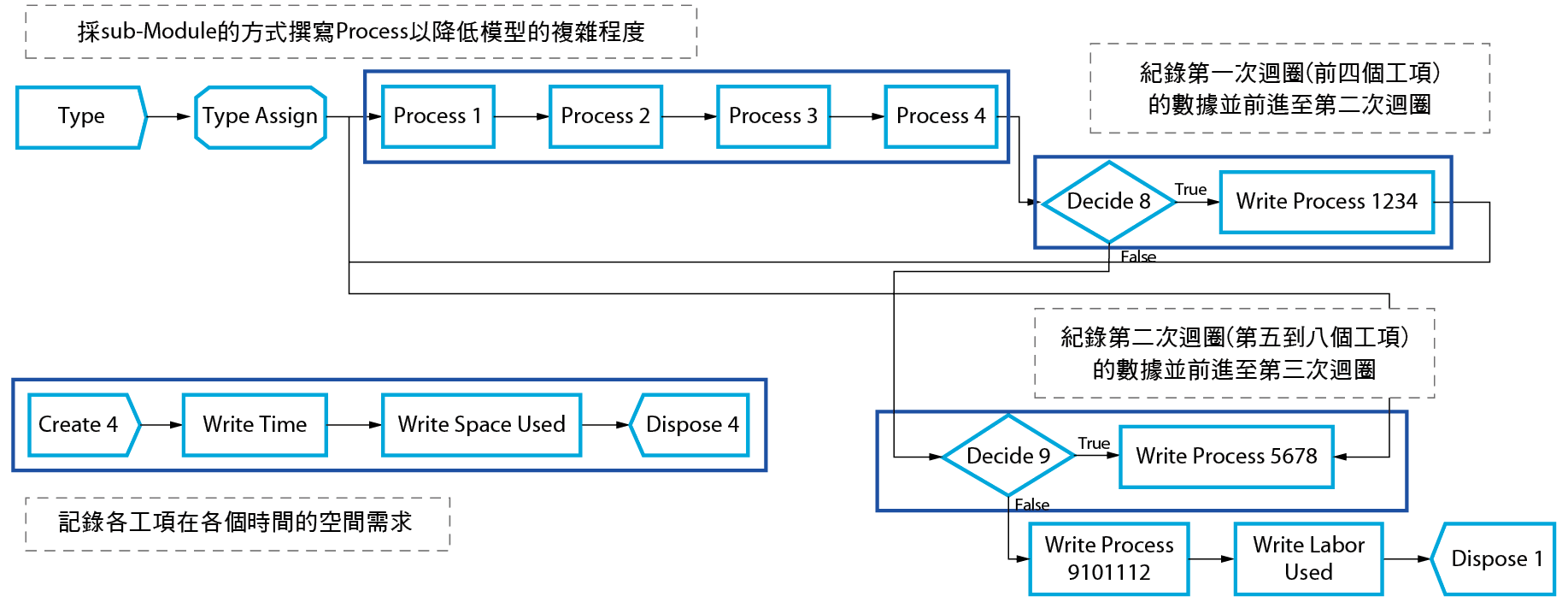
圖十一、Process 細項
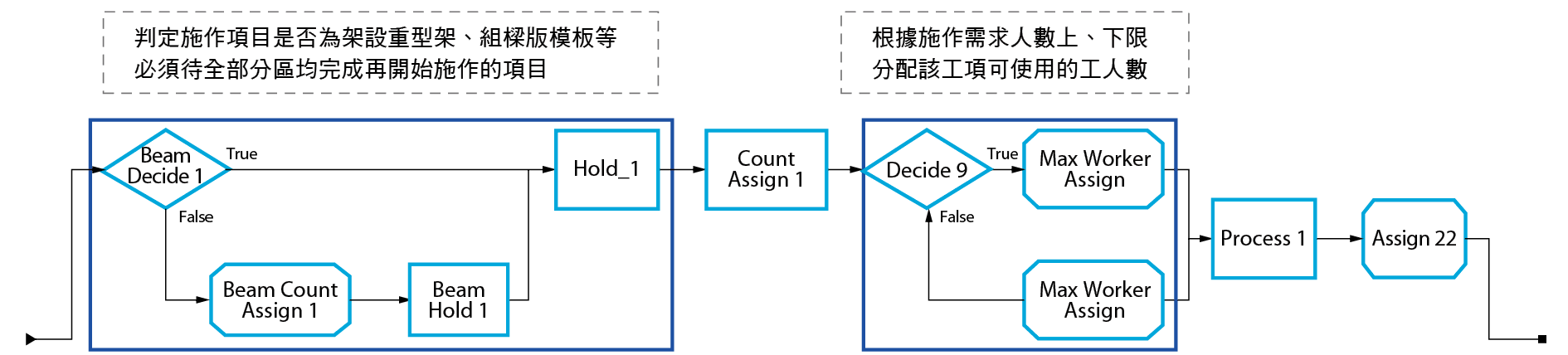
3D視覺化模型
此研究之3D視覺化模型採用Crystal 5D作為建模工具,其多人協作功能可減少建模時間,且可在同一套系統架構下匯入排程製作4D施工模擬,減去檔案轉換的問題,故預期使用此套系統能達到最佳的效益。
透過 圖十二所示之Sketch up→ Auto-desk 3DsMax→Crystal 5D元件建置方式,在統計完模擬區域內之構件、2D圖說等資訊後,透過這樣的路徑製作並匯入元件,即可完成3D模型,接著檢驗模型的準確度,確保製作之4D施工模擬能符合現場施工情況,而最後完成之3D模型如 圖十三所示,中間區域為場鑄施作之中迴風區,左右兩側為預鑄高低板區,其中建置了假設工程如鷹架與重型支撐架,且於剪力牆內繪製了鋼筋物件,如此可搭配不同施工進度呈現工地變化。
圖十二、元件製作流程
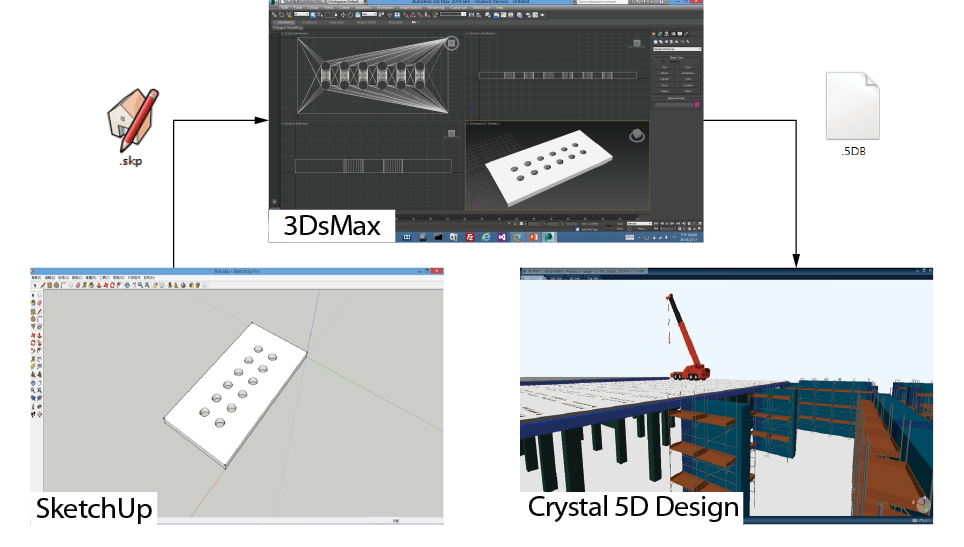
圖十三、F14P7 下部結構3D 視覺化模型
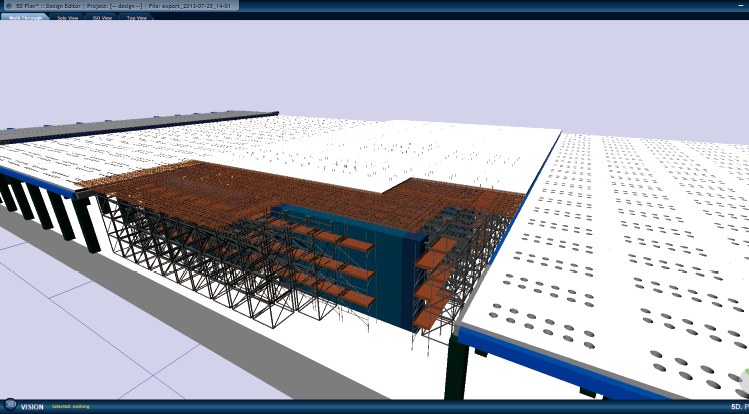
資料分析結果及討論
預鑄區排程結果
F2、F3預鑄區模擬結果如 圖十四以及 表二,經過Arena模型計算可以得到吊車每天的吊數與吊裝物件,藉此分析吊裝工期總和以及每天吊車的功率,而中迴風區另一側的B1、B2區域與F2、F3同時施作且雷同,故計算單邊即可。
圖十四、F2‧F3 區吊數統計圖
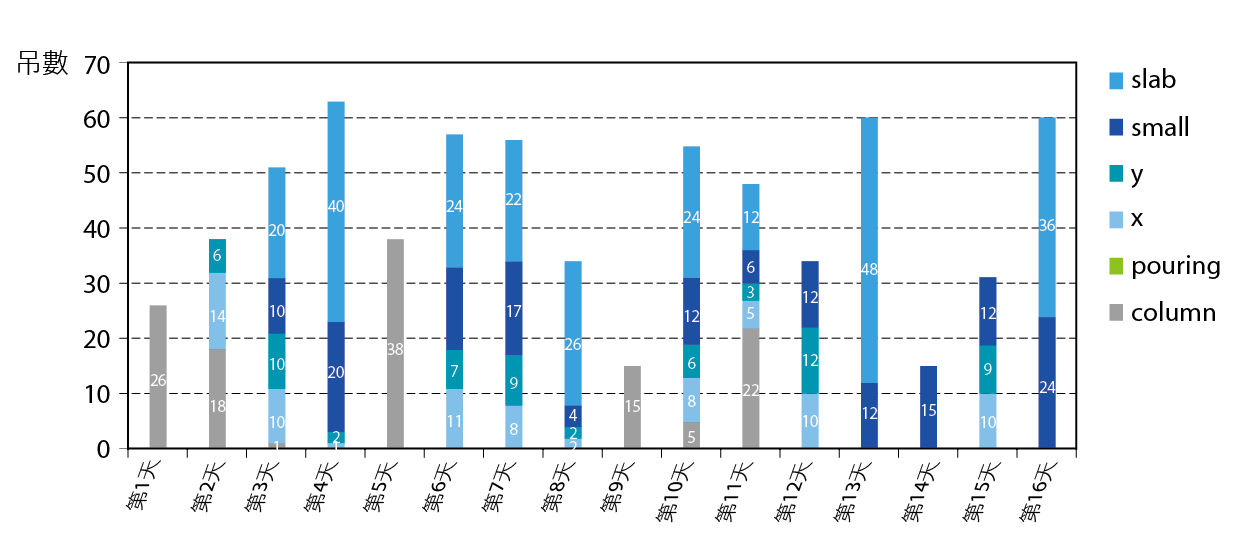
分析結果(F2、F3區單台吊車施作) |
||||
---|---|---|---|---|
區域位置 |
吊數 |
總施作時間 |
優先順序 |
施作群組 |
F2區(低板區) |
363 |
175小時 |
板>樑>柱 |
1 Entity/Group |
F3區(高板區) |
318 |
187小時 |
板>樑>柱 |
1 Entity/Group |
F2+F3區 |
681 |
362小時 |
為了檢核不同方案的優劣,在此架構下調整模擬參數,又接續分析了三種不同施工方案。 表三為更改吊車資源數量由一台變成兩台所呈現出的不同結果。理論上吊車數量變成2倍,吊裝時間應該減少為一半,但因吊數消耗太快以至於需等待柱底灌漿完成,造成吊車在第1、3天無法發揮100%工率,因此最後時程只由原本的175小時(等同八個工作天)縮短成115小時(等同五個工作天),而此部分的吊車成本則增為原本的1.25倍。
- 比較一:增加吊車資源 表三
表三、增加吊車數量分析結果
F2區吊裝
Resource 1
Resource 2
變數
1台吊車
2台吊車
總施作時間
175小時
115小時
吊車效率
100%
76.1%
成本
8單位
10單位
- 比較二:改變施作群組(Group)大小 表四
表四、改變施作群組大小之分析結果
Group 1
Group 2
Group 3
變數
1 Entity/Group
3 Entity/Group
3 Entity/Group
模擬時程
175小時
174小時
175小時
吊車效率
100%
100.5%
100%
成本
8單位
8單位
8單位
- 比較三:改變物件處理的優先順序 表五
表五、改變物件處理之優先順序所得之分析結果
Priority 1
Priority 2
變數
板>樑>柱
板<樑<柱
模擬
時程
175小時
175小時
吊車
效率
100%
100%
如 表三至 表五顯示吊車數量的增減會較明顯的改變分析結果,而相對的施工單位的劃分與吊裝優先順序的改變對於工期、效率、成本等並沒有顯著的影響,不過我們仍可藉由這兩項參數的調整改變施工空間、施作模式的模擬,因此這兩項因素也並非對施工模擬完全沒有影響。
場鑄區排程結果
根據前述的場鑄區施工邏輯及input excel表格設定內容,得到的場鑄區施工時程為29天。
圖十五反映了場鑄中迴風區的人力資源分配情況,透過分析,我們可以得知每天人力資源需求。
圖十五、場鑄區人力資源進度表
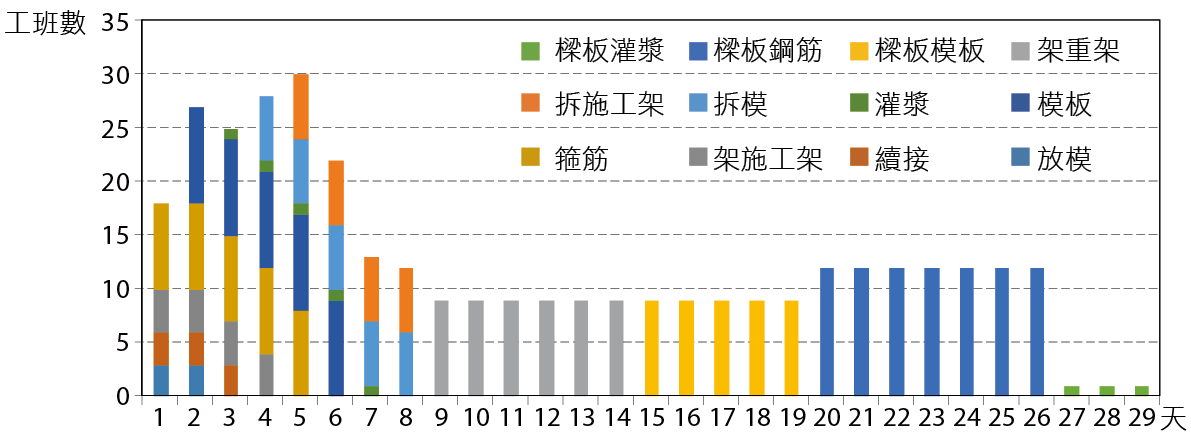
另外,本研究亦嘗試以Arena作空間使用的分析,以量化空間的方式,如設定1.2米乘4.8米為基本單元,設定每個工項所需的空間,得到場鑄施工期間每天所需的總空間量,提供預鑄進場時程規劃使用。
唯目前僅量化空間,未針對空間的形狀、位置、邊界進行幾何描述,故模擬結果並未呈現因空間不足而造成工項進度停滯或功率折減的狀況,如 圖十六所示。
圖十六、場鑄區空間需求分析結果
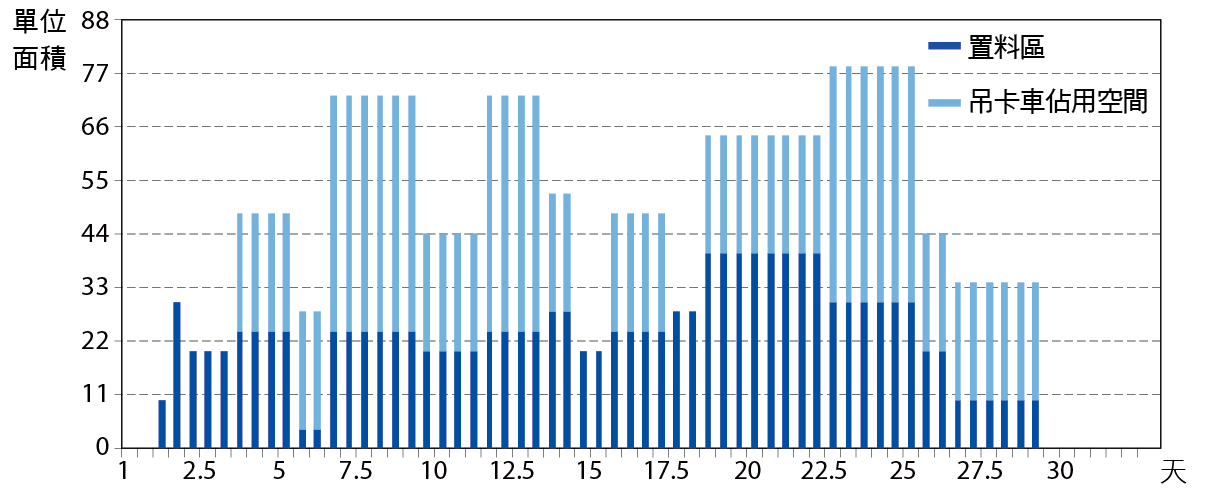
4D建廠施工模擬
表六為物件時程之對照表,依此便可開始在Crystal 5D中將對應的3D物件群組起來,並設定顯示時間。
工項 |
中迴風區下半部 |
中迴風區上半部 |
時間對應之物件模型 |
||
---|---|---|---|---|---|
放樣 |
2013/7/15 |
2013/7/15 |
2013/7/15 |
2013/7/15 |
|
柱牆鋼筋續接 |
2013/7/15 |
2013/7/15 |
2013/7/16 |
2013/7/16 |
|
鷹架架設 |
2013/7/16 |
2013/7/17 |
2013/7/18 |
2013/7/19 |
鷹架 |
柱牆綁筋 |
2013/7/18 |
2013/7/20 |
2013/7/21 |
2013/7/23 |
鋼筋 |
柱牆模板 |
2013/7/21 |
2013/7/24 |
2013/7/25 |
2013/7/28 |
|
柱牆灌漿 |
2013/7/25 |
2013/7/25 |
2013/7/29 |
2013/7/29 |
|
柱牆拆模 |
2013/7/26 |
2013/7/27 |
2013/7/30 |
2013/7/31 |
柱牆 |
樑板重型支撐架 |
2013/7/28 |
2013/7/31 |
2013/8/1 |
2013/8/4 |
重架 |
樑板模板 |
2013/8/1 |
2013/8/4 |
2013/8/5 |
2013/8/8 |
|
樑板綁筋 |
2013/8/5 |
2013/8/7 |
2013/8/9 |
2013/8/11 |
樑板鋼筋 |
樑板灌漿 |
2013/8/8 |
2013/8/8 |
2013/8/12 |
2013/8/12 |
|
樑板拆模與拆重架 |
2013/8/9 |
2013/8/10 |
2013/8/13 |
2013/8/14 |
樑板 |
圖十七即為Crystal 5D施工流程模擬之顯示。4D動畫播放時可以做視角的移動,故使用者能在不同時間點以不同角度檢核施工流程之空間衝突問題。左上角的時間控制面板,可以拖拉時間軸至其上的標籤,此標籤代表著該時間點有物件顯現,故可藉此觀察工地施工流程中各個milestone的時間點,亦可以輸入特定時間點以觀察該時間點工地預定的狀況。
圖十七、4D 施工流程模擬

未來研究-可行性分析
整體來說排程數學模型達到了分析施工效率的目的,藉由預鑄區的三種吊裝比較方案,即可看出透過資源導向的方式在工期、效率、成本上呈現量化的差異。
唯現階段小範圍的場預鑄模型並未合併在一起,若未來進行至整體空間衝突的分析,則有兩者合併之必要。此外,目前模型未能以幾何方式考量空間、位置、動線等因素,只以純量的方式量化空間資源,此為接下來研究的重點。
另外,Arena之排程模型類似於Precedence Diagram,接下來的應用將不止於施工流程的效率分析,亦可進一步延伸做為廠商的投標依據或專案人員的溝通平台,唯先決條件是必須訂定出一套建模規則,使專案人員循一定的方式製作模型。如此才能製作易於理解的施工模擬,以達到溝通的效果。
工程資訊的可信度也是一個議題,如Arena運算時需要模擬資源的變動方式,因此必須知道出工數折減機率,抑或將天氣等因素納入工率折減的考量,這些條件皆十分重要,而目前尚沒有這些資料的整理,因此只能依靠假設的方式暫時設定這些參數。
在3D視覺化模型的部分,Crystal 5D的4D模擬功能目前只能依時間堆疊物件,無法模擬假設工程對空間衝突造成的影響,此外,場鑄置料區若能如預鑄般作好完整的規劃,將其納入模擬範疇,必能提供各承包商更好的協調方式。
未來展望-4D Simulation專案開發
在十四廠七期施工模擬的研究中,發覺空間衝突對工程的進行有著顯卓的影響,如前面所述,Crystal 5D所產出的假設工程、置料區等無法於給定之完成時間點消失,這些暫時性物件造成空間上的衝突,為改善此一問題決定開發另一項4D視覺化模擬程式,期達到空間衝突檢查與動線規劃之成效。
程式執行結果畫面如 圖十八,可以設定假設工程出現與消失的時間,如此便得以觀察鷹架與重型支撐架交替出現的過程,更完整的呈現施工現場的狀況。
圖十八、程式執行畫面
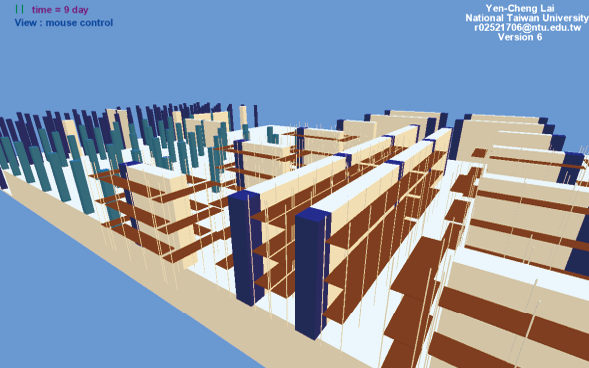
而為解決原先無法做到的機具行為模擬,程式中亦加上機具物件的模擬, 圖十九為堆高機模型以及控制方式, 圖二十為以第一人稱視角控制堆高機運作,使工程人員於動工前知悉現場狀況,期許未來能以此發展出更好的機具路線設定方式,以達到更完善的空間衝突檢核功能。
圖十九、簡易堆高機控制說明
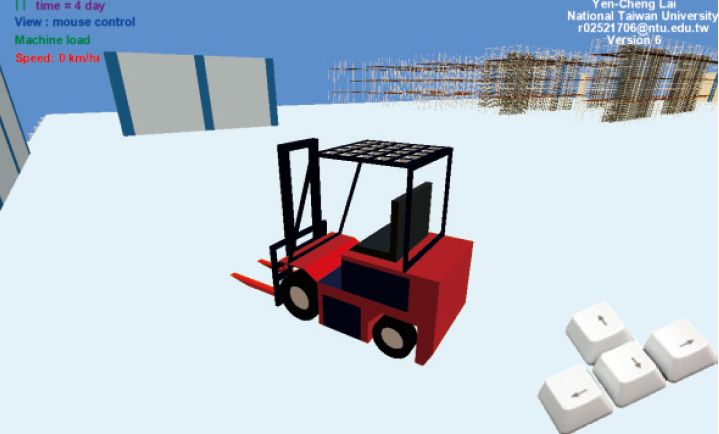
圖二十、堆高機視角切換
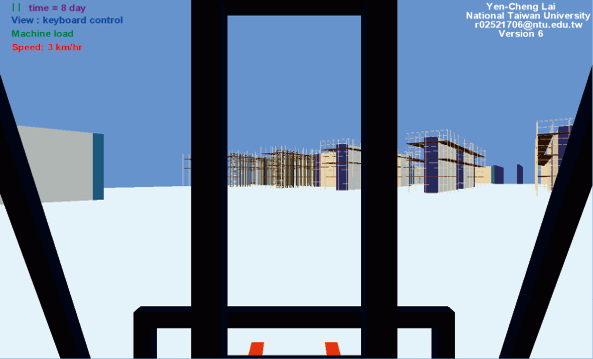
結論
透過4D施工模擬的可行性研究,其結果顯示排程數學模型可用以整合人力、資源、施工邏輯等因素,計算出專案的工期、執行效率、成本,作為評估不同施工方案的客觀依據,這是以往所無法達成的部分。
接下來的工作尚須建立適當的啟發式演算法(heuristic algorithms),以便更智慧地(intelligently)推導最短時程及最佳資源分配方式,並將研究觸角延伸至實際動工後的即時資訊整合,以自動資訊回饋機制搭配多種行動裝置,透過4D之虛擬實境快速反應瞬息萬變的現場狀況,這將會成為下一階段的研究目標。
參考文獻
- Bonsang Koo and Martin Fischer (2000). “FEASIBILITY STUDY OF 4D CAD IN COMMERCIAL CONSTRUCTION” Journal of Construction Engineering and Management, ASCE, 2000, pp. 251-260
- 崔紘瑞,2009,「半導體廠房土建施工界面衝突造成生產力折減程度」,碩士論文,國立台灣大學土木工程研究所。
- 江翊楷,2009,「應用物件導向技術計算動線規劃於重複性工作之效益—以高科技廠房格子板工程為例」,碩士論文,國立台灣大學土木工程研究所。
- 台積電南科十四廠六期預鑄工程完工報告書,潤泰營建集團/潤弘精密工程事業股份有限公司,中華民國一零二年六月。
- 謝濟安、賴彥程、張貴博、許哲瑋、許君豪、王敬一,「建立資源導向之4D施工模型─以台積電F14P7下部結構場、預鑄工法為例」,2013年度台積電暑期實習期末報告。
留言(0)