摘要
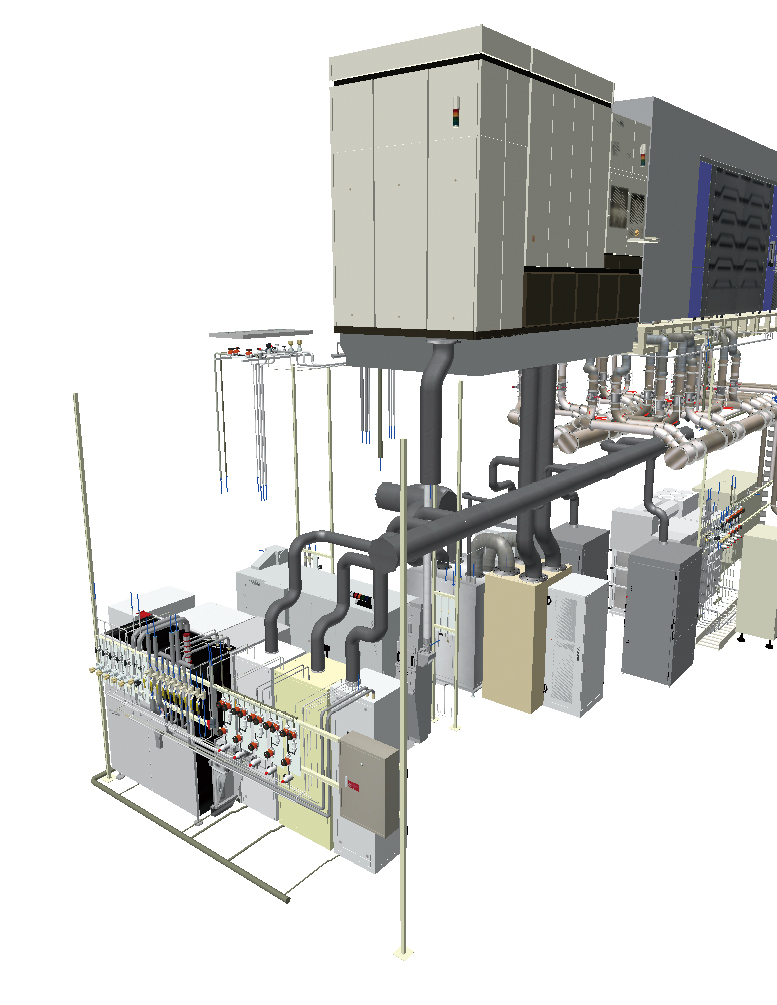
新廠規劃的前導者 - IDI系統再進化
新建廠房於規劃設計時,必須依據生產機台的需求 (Tools Utility Requirement) 進行各種廠務供應系統規劃與建造,各系統容量規劃及管路配置長度是影響建廠成本的關鍵因素;本篇將闡述建立生產機台需求資料,藉由 IDI (Initial Design Integration)進行資料庫整合精確計算建廠設計所須建置廠務供應系統之容量,並可以快速因應機台變更對廠務系統設計所造成的影響。
前言
過去的製程發展由研發廠區完成製程開發到量產工廠生產有較充裕時間,有確定的機台需求可用來規劃廠務系統,但目前新建廠房於規劃興建過程中,面臨製程仍持續開發中,往往遭遇機台需求一再變更,廠務設備也一再修改,如何在廠房同步建造狀況下,快速因應變更與減少變更成本越來越重要。
IDI(Initial Design Integration)系統自2008年發展至今,應用在竹科、中科與南科之新建廠專案,藉由機台數量及機型清單與機台廠務需求等資料庫整合計算,可以依據各廠務系統、樓層區域或依不同機台需求時程,計算各廠務系統需求容量,解決設計人員各自資料蒐集、反覆計算統計的時間,提高同仁們的工作效率。
隨著製程進入高階世代,高階製程世代轉換中所需廠務種類與用量變化幅度越來越大,加上沒有專人對後續修改情形與使用量同步更新, IDI 系統所提供的資料,逐漸與實際狀況脫節。同時各系統的設計者因資料庫的不完整,設計人員必須自行蒐集資料造成需求紊亂,以致在設計階段,無法即時因應機台的快速變更修改設計,影響專案成本。
進行新建廠各專案的設計變更比例分析 表一,各專案變更比例在2~5%,主要原因是機台配置、數量及機型與基台廠務需求的改變。針對變更需求的因應措施,除加強與規劃單位及使用單位作業協調外,生產機台的廠務需求也必須有更新的機制,期能即時掌握機台需求的變化,我們開始針對IDI系統進行補強,主要是建立機台需求的資料庫以快速因應變更的需求,以下將針對我們面臨的這些問題,對資料的重整與更新進行探討。
專案名稱 |
新建廠變更設計需求比例 |
|||||
---|---|---|---|---|---|---|
Layout, Tools list & |
Design & |
Requirement change |
Schedule issue |
Code change |
Total |
|
A |
4.4% |
0.1% |
0.2% |
0.2% |
0.0% |
4.8% |
B |
1.5% |
0.6% |
0.6% |
0.3% |
0.1% |
3.0% |
C |
0.6% |
-0.4% |
0.9% |
0.1% |
0.0% |
1.2% |
D |
2.3% |
0.0% |
0.4% |
0.1% |
0.0% |
2.8% |
E |
1.5% |
0.3% |
0.1% |
0.1% |
0.1% |
2.0% |
"F (Ongoing)" |
0.0% |
0.1% |
0.0% |
0.0% |
0.0% |
0.1% |
現況
檢視IDI系統資料庫,如 圖一所示,依製程及廠別,陸續建立了十大類,一萬三千多筆的機台需求資料。但資料眾多,每一筆資料於建立時,資料可能來自機台裝機傳簽單,也可能來自各廠區廠務、設備所提供的型錄,資料來源一致的品質標準,也未經過資料確認步驟,在進行用量計算前的資料比對時,同一型機台,可能有好幾筆不同資料,到底要以哪一筆資料為準呢?除費時外,比對後的資料,不僅與設計者手邊的資料有落差,與現場實際安裝的情形也不完全符合,如此惡性循環下,IDI雖然持續更新,但資料已非100%正確,計算的結果也自然失去大家的信任。同時在新製程仍不斷的變更機台形式與需求種類數量的狀況下,產生頻繁的設計變更與修改費用的發生。也因此引發了我們重新強化這個行之已久的系統,利用知識管理 (Knowledge Management)的手法與資料庫計算之概念與邏輯,對整個系統的流程與架構重新做檢討。
圖一、機台需求
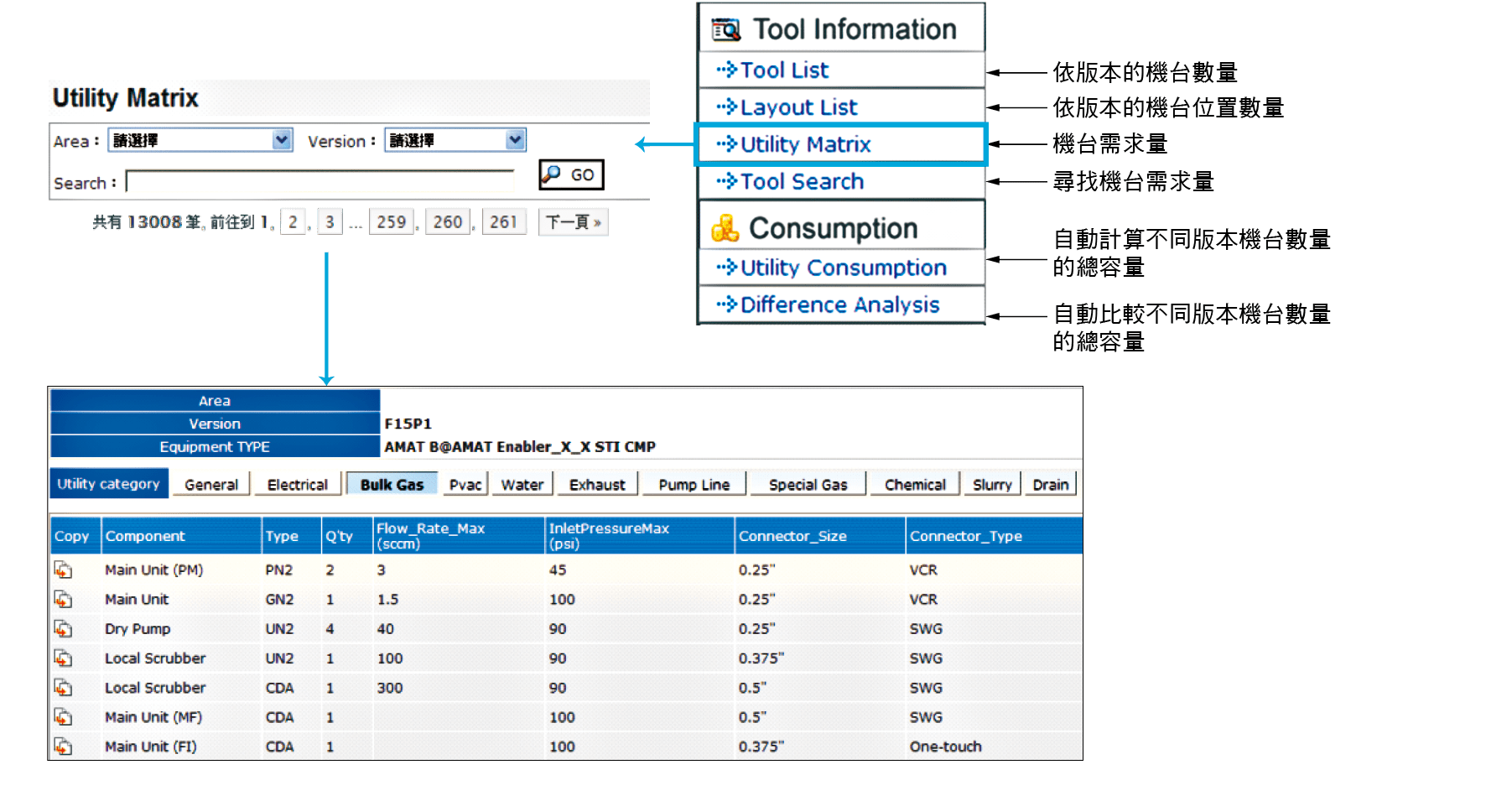
如前所述,IDI是依據穩定後的製程正確需求提供設計時所常用的機台資訊,整合計算出各系統總容量而提供給設計者,IDI系統再精進第一步的想法,就是要以製程機台的需求量與實際量建立正確的最佳化機台需求 (Golden Utility) 資料庫,讓新專案依最佳化機台需求建立所須之機台數量及機型的系統總容量,同時也能同步更新資料庫並掌握機台未來趨勢與需求的變化。
系統設計流程概念
新建廠的廠務系統容量設計必須以實際機台用量為基準, 圖二所示為新建廠之系統容量設計之概念,由生產機台需求資料庫,查表得知各種廠務系統的需求量,再根據產能規劃的機台數量與機型,與過去專案的經驗係數,計算出系統設置容量,再加上機台的位置資訊可以決定輸送主管(Main)及次主管(Sub-Main)的配置。
圖二、系統容量設計之概念
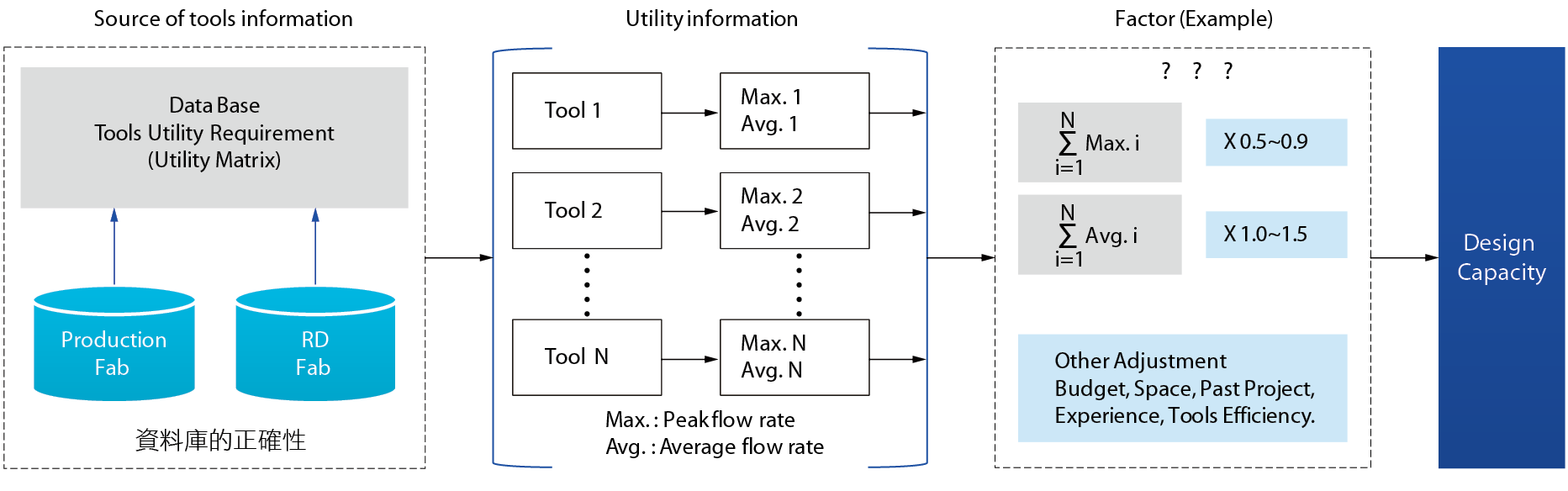
系統容量的設計取決於生產機台的需求,其中設計重點是「量」的計算基礎,若採最大值(Max.)為設計基準則會擔心系統容量是否會設置過大(Over Design)造成成本的浪費,若採平均值(Avg.)為設計基準則又會擔心系統容量是否會設置太小造成未來系統運轉容量不足,這就是在決定系統容量設計時最常遇到的核心問題,但若有相關廠區全系統實際運轉的「量」當參考,設計量會更貼近實際使用的容量。
資料庫建立的運用方法
為了有效解決上述的困難,經過很多討論並參考知識管理架構的概念,我們重新建構一個需求管理方法,分成三個部分強化目前的系統。
整合知識資源
找出機台需求決定流程,從研發單位機台選用,現場裝機資料與運轉量之取得開始,將這些分散於各部門之資料,進行篩選、確認與優化,重新依各個不同製程世代(如N2X, N1X)的機台需求,更新現有資料庫。
知識轉化
藉由與設計部設計者資料之相互比對,設計總量參數之調整,以至於一些關鍵績效指標(KPI, Key Performance Index)的建立,重新歸納現有的計算邏輯,可以避免因為不同人員設計時造成的落差。
人與程式的連接
目前IDI介面,除了輸出報告格式,機台數量及機型之資料匹配程式能力仍無法滿足各子系統不同需求,也因此降低設計人員使用意願,使得資料被使用的機會大大的降低。
本篇文章主要就整合知識資源與知識轉化這二個部分進行介紹。
系統再精進機台需求(Utility)資料庫建立
先進製程的發展及進入量產階段,設計初期產能組合不斷改變,生產所需要的製程機台種類、數量與需求配合調整,計算系統用量時,例如超純水(UPW)、製程冷卻水(PCW)、電力(Power)等等,機台數量動輒數百多台以上,種類也多達數百多種以上,建立正確之製程生產機台需求的資料庫就非常重要,除了可大幅減少人工搜尋及計算的時間,並能有效因應快速變動的產能規劃及設計。
首先導入正確的生產機台資料庫,依不同的製程建立機型的標準需求,如 圖三所示,以往我們經由經驗資料或依不同單位提出的機台需求當成其機台標準需求,常造成相同先進製程跨廠區因沒有相同的標準而有不同數據,於是採用研發部門、先進製程運轉廠及先進品質精實管理部門共同定義的最佳化機型為依據。此方面的資訊如 圖四所示依製程技術至工程文件流程系統(EDW, Engineering Document Workflow)查詢最佳化機型之定義。接下來搭配產能規劃的機台數量與機型,進行系統再精進時,一併納入最佳化機型的定義,建立標準資料庫。
圖三、生產機台需求與實際使用量的核對
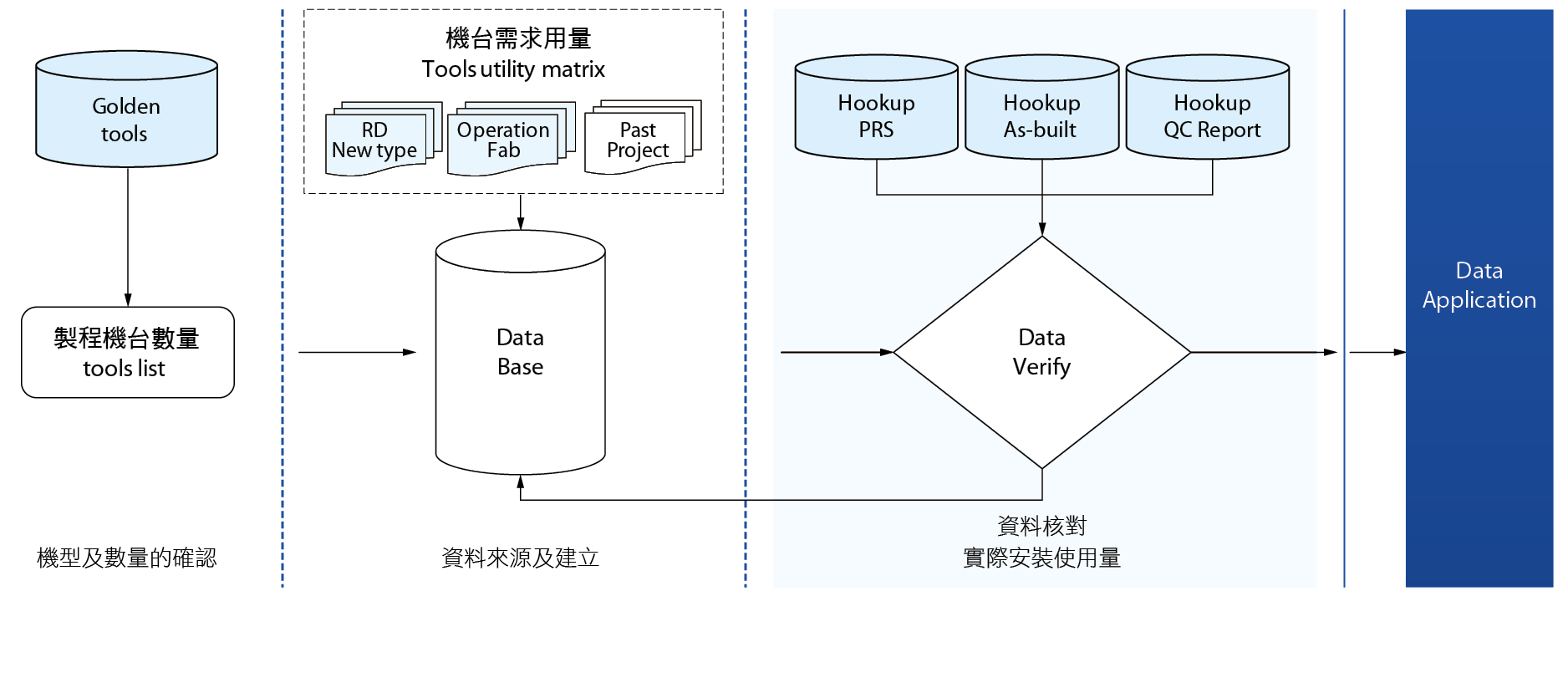
圖四、最佳化機型
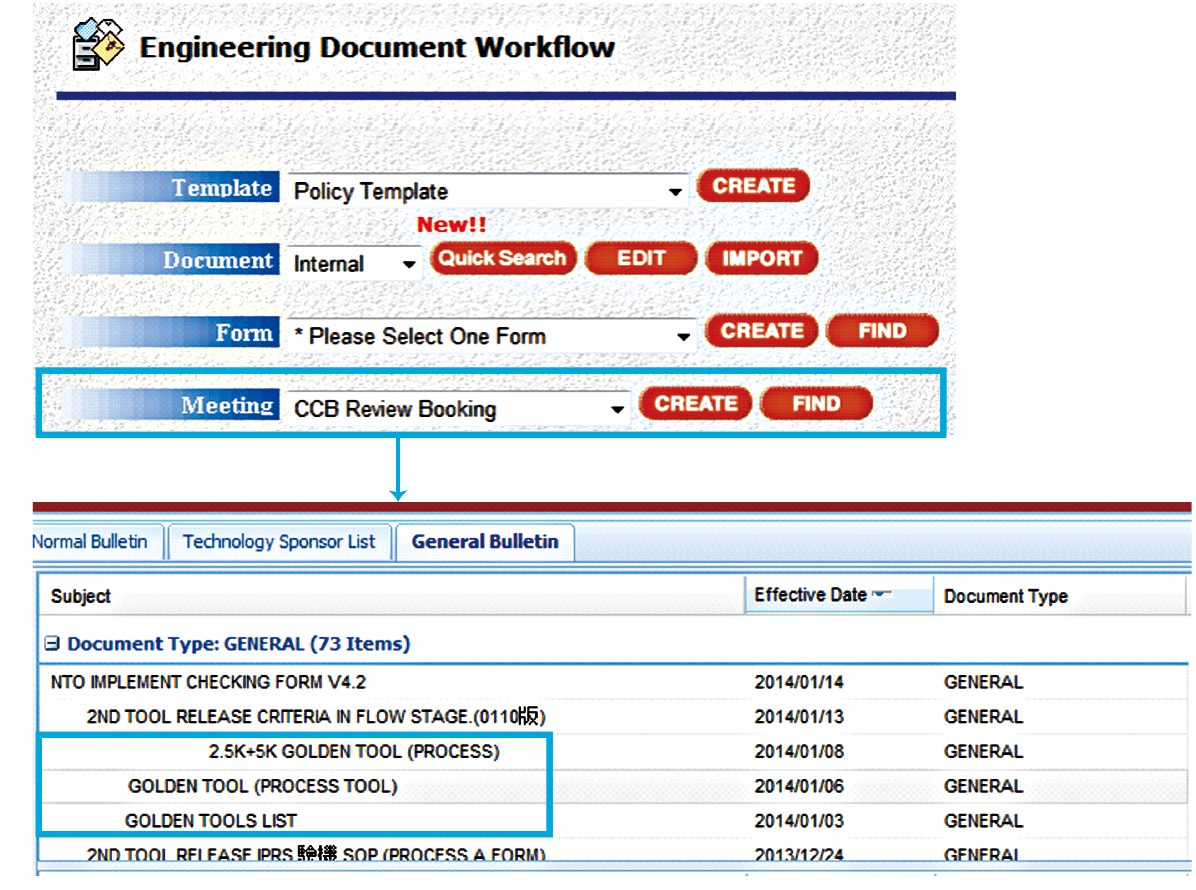
而針對機台需求用量的正確性,多數以過去專案書面的製程生產機台的需求資料為主,並沒有實際安裝後的使用量資訊來比對或修正,造成只有需求而沒有實際安裝使用量,讓設計者對資料庫的需求量有質疑,針對此疑慮必須進行驗證實際安裝使用量的方法,運用了機台安裝資訊如現場的機台配管品質驗收系統(Hookup QC Report)、機台配管竣工圖面及機台配管標準型式(Hookup PRS)等方式來進行使用量核對。
製程機台的實際需求可以運用現有機台安裝相關資訊平台核對,也同步建立資料庫(但對其他特殊需求則需至現場實際確認,如新機型的新需求或其他需求) 表二運用機台安裝資訊進行核對的說明。
機台安裝資訊 \ 項目及特性 |
機台配管品質報告系統 |
機台竣工圖面 |
機台配管機準型式 |
---|---|---|---|
系統平台名稱 |
eHookup |
Site Hookup Server |
iHookup |
機台資訊 |
每一機台安裝後的裝機配管相關品質檢驗報告之記錄平台 |
每一機台實際裝機配管的安裝圖面 |
最佳化機型(Golden tools)定義其標準裝機配管型式 |
可核對資訊 |
核對每一機台實際裝機配管數量安裝的現場狀況 |
核對每一機台需求量與實際安裝之正確性 |
核對最佳化機型(Golden tools)定義的標準裝機配管型式 |
機台配管品質報告系統是針對機台安裝後配管相關的品質檢驗合格報告之記錄平台,透過此系統可查詢每一機台實際安裝的現場狀況,如 圖五所示,機台需求與實際安裝可相互核對其正確性。
圖五、機台配管品質報告系統
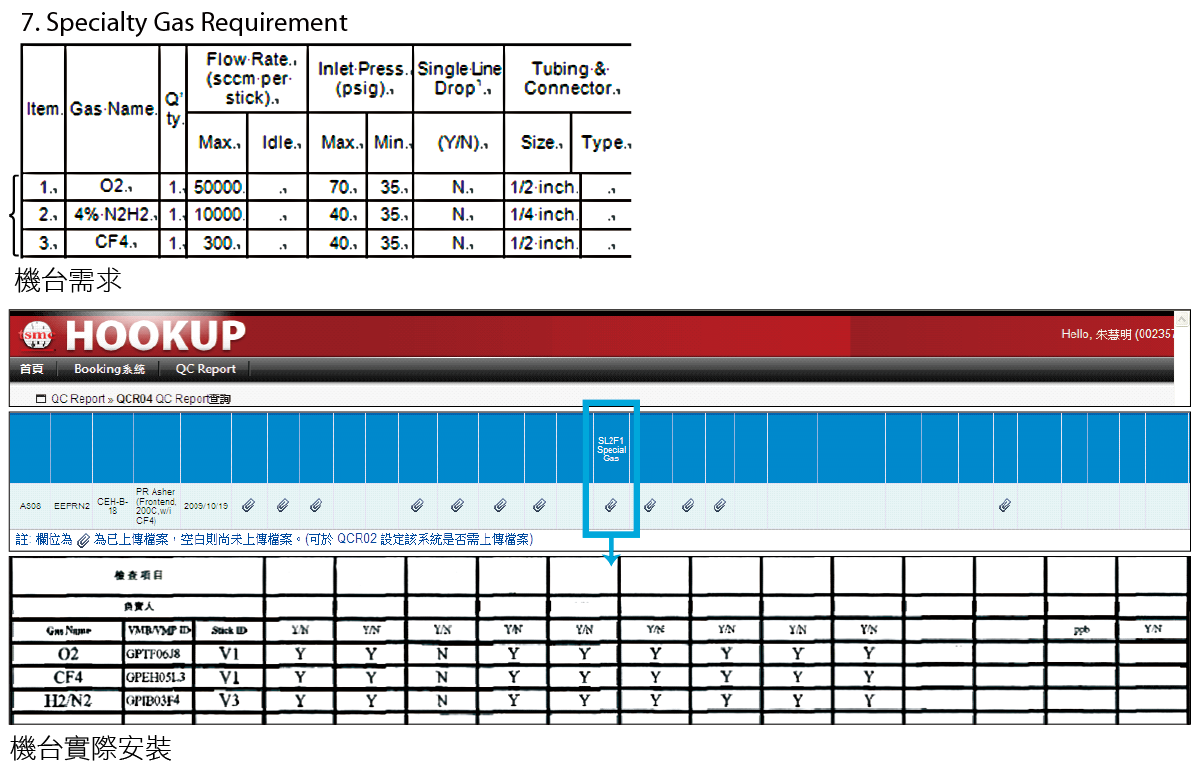
而運用機台配管竣工圖面可查詢每一機台實際配管安裝圖面,如 圖六所示,進一步對機台需求量與實際安裝來進行相互核對。
圖六、機台配管竣工圖面
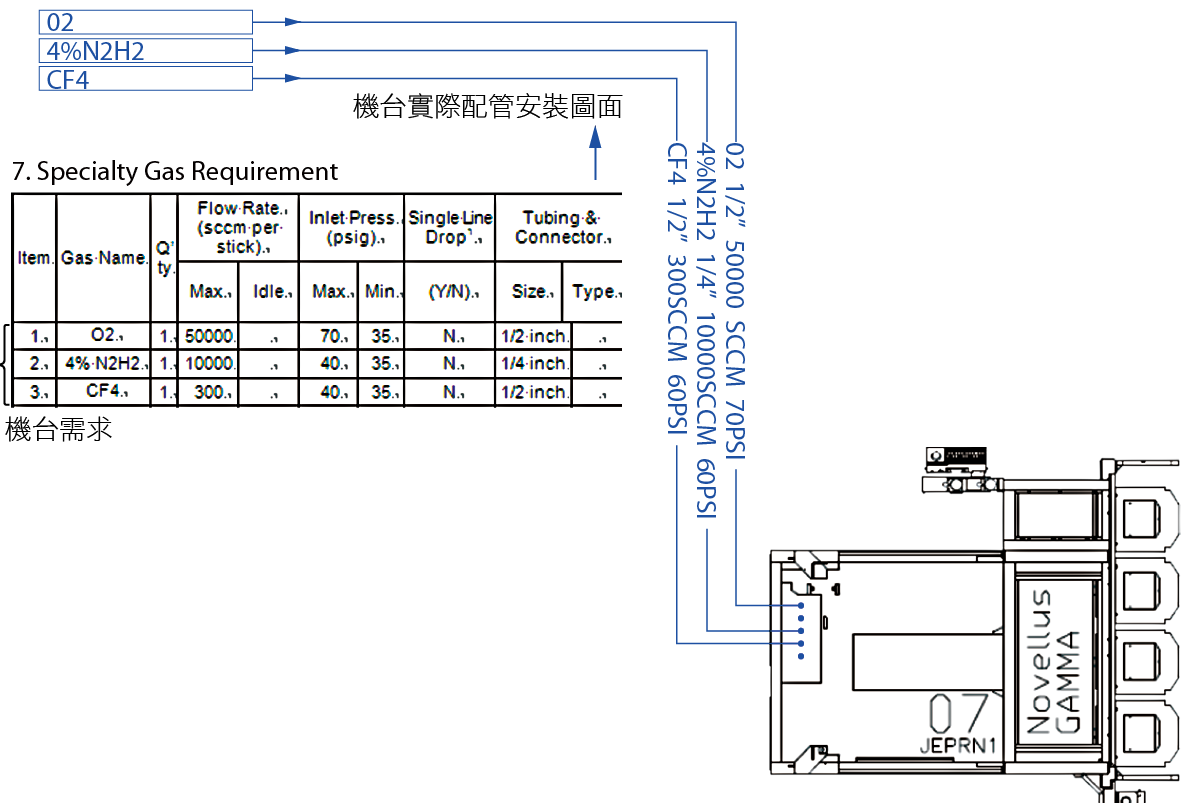
機台配管標準型式將針對標準機型定義其標準配管型式,由先進製程的研發母廠與量產廠共同定義,讓跨廠區遵循相同標準的配管型式以減少因配管型式不同而在製程上有所偏差,機台配管標準型式正如製程應用的PRS (Process Standard Release)系統將其功能延用至配管標準型式以防止跨廠區之間的差異。運用此系統可查詢每一種最佳化機型的標準配管型式,如 圖七所示,可運用此平台將機台需求與標準安裝型式相互核對其正確性。
圖七、機台配管標準型式
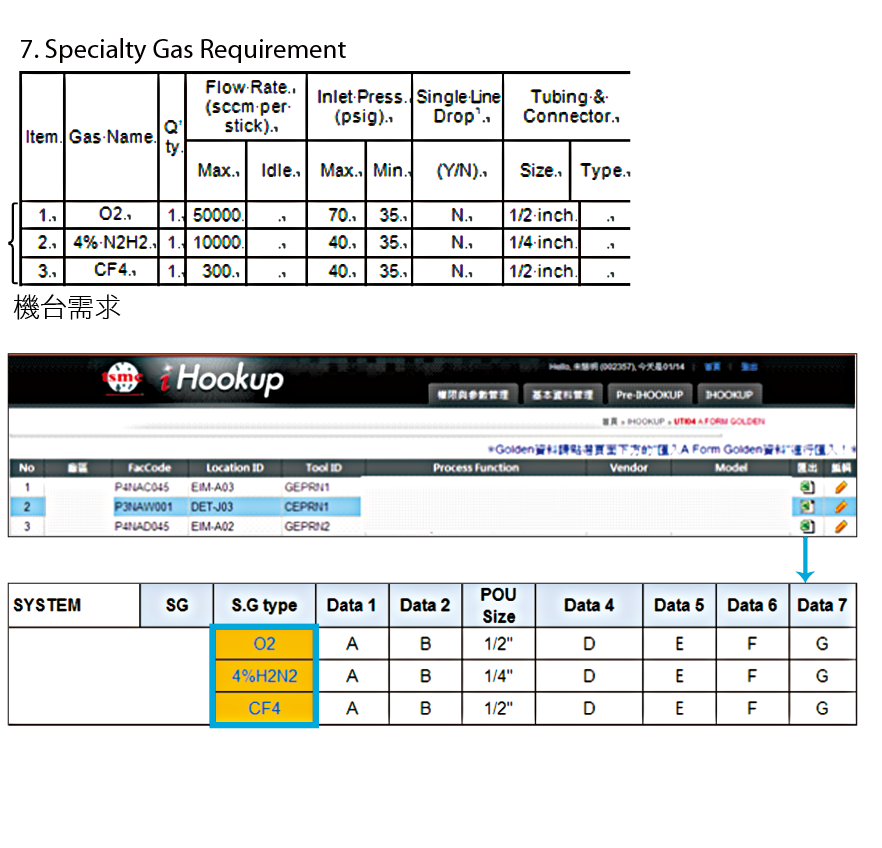
我們透過以上的核對方法提昇IDI系統機台需求的正確性,也建立機台需求的完整資料庫。而加強後的IDI更適用於製程機台持續更新中之專案,縮短規劃時間及提高設計的掌握度,並可應用於研發中的先進製程導入快速量產的新專案。
結論
IDI的概念與做法並不複雜,只是要如何保持持續性的管理與更新。更重要的是,藉著系統化的資料整合與分析,能夠在各專案完成後,繼續蒐集機台需求設計資料,統計並分析系統運轉容量,在未來的專案上,能縮短前期規劃與設計的時間。同時也藉著對製程機台需求掌握度的提升,合理設計系統容量,達到控制建廠成本,而且更快、更有效率的完成新專案之設計。
建立機台需求正確性的資料庫只是IDI精進的第一步,如 圖八所示,本篇文章主要是就整合知識資源與知識轉化這二個部分進行的機台需求資料庫建立之介紹,至於系統發展運用的程式及產出應用部分,未來完成後將再以專文介紹。最後期望透過好的工具提高同仁們的工作效率,正是所謂『工欲善其事,必先利其器』的道理所在。
圖八、系統發展運用

參考文獻
- TSMC OI Document (2013): Tool installation sign-off O.I. (A-RMS-07-03-181).
- TSMC OI Document (2013): Facility hookup PRS golden tool list O.I. (F-CQC-02-03-003).
- 林進忠(2003),產品需求不確定環境下半導體製造之機台需求分析 Tool Requirements Analysis under Uncertain Environment in Semiconductor Manufacturing.
- TTV: Time To Volume,產業策略評析:從即時到對時─企業管理第二招 http://cdnet.stpi.org.tw/techroom/analysis/pat_A059.htm
- 顏登通(2011),全華圖書,「高科技廠務(第三版)」,第10章:建廠設計評估及施工監造管理。
留言(0)