摘要

5D系統在建廠實務應用的探討
Keywords / Space Mamagement,5D Facility Information Modeling,Space Conflicts
新工處導入5D軟體來輔助建廠已歷經十餘件專案,本文主要探討建廠階段在導入5D後的作業流程與傳統流程的差異。文中說明將以5D的作業流程為主軸,並針對5D與傳統做法的差異做進一步的分析,最後以表列方式彙整各項差異,並對5D軟體提出後續改善的建議。希望以此給未來有心在此領域深入研究與應用的讀者一個參考。
前言
空間管理(Space Management)是新建廠工程管理中,雖不起眼但甚為重要的一環,空間管理主要工作是承接上游各廠務系統的細部設計圖面,經排除管線/設備的空間衝突與整合後,兼顧各系統功能性、人員操作性以及基本的整齊美觀,才能將細部設計圖轉變為可以交給施工單位的施工圖。「整合」就是空間管理的核心工作,早期的整合工作主要是依賴2D的電腦軟體,將各系統的設計平面圖套疊在一起,以便找出衝突點,經討論修改後再依相同的套圖步驟直到空間衝突問題解決為止。然而在建廠施工階段圖面套繪工作,需依賴有豐富建廠經驗、對各系統管線及設備熟悉之空間管理工程師來執行,但在施工完成前,空間管理工程師的規劃,很難快速的讓人了解,故旁人無法協助檢查套繪結果,為幫助設計及施工人員快速了解空間管理工程師的規劃,新工處目前在空間管理上所使用的工具就是導入Crystal 5D軟體,因該軟體除了既有的3D圖形外,並兼具可同時多人多工及智慧型資料庫之功能,因此統稱5D系統。透過5D系統,所有管線及設備均在同一環境內繪製,使用者可看到同空間中所有之管線佈置狀況,若發生碰撞可於繪圖時立即修改,5D模型建置完成後,透過虛擬實境之巡檢功能,可讓所有人都能直接檢核套繪結果是否正確及符合整齊美觀要求。由於每個專案的工期都非常緊迫,因此如何有效利用工具來提升工作效能是非常重要的,希望透過本文的探討,可讓5D應用的效益更加的明確。
導入5D系統與傳統方式的空間管理流程介紹及比較
施工階段運用5D系統執行空間管理之工作流程
如 圖一所示,在施工階段施工圖面將經繪圖、套圖、檢查、出圖等流程後產生,流程開始於CAD室的成立,截止於竣工圖的驗收,後續將說明5D系統被如何應用於上述各步驟中,以及各步驟的目的及做法。
圖一、5D 系統執行工作流程
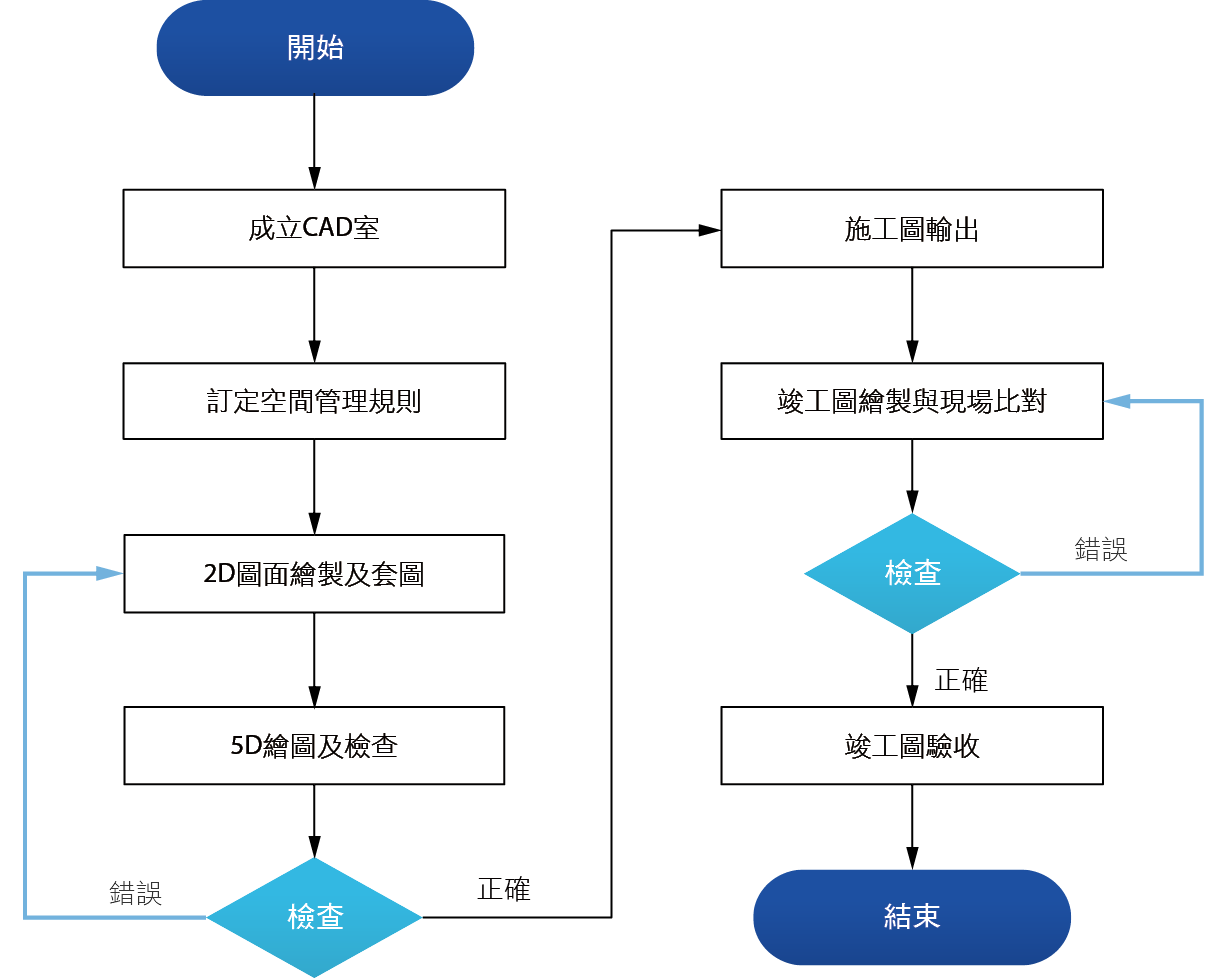
步驟一:成立CAD室
系統廠商之主要套圖工程師各自負責所屬之套圖區域,並互相協調跨越各區域間的管路位置,將管路及設備調整至最佳位置,以達到系統效能及整齊美觀之目的。CAD室為整個專案施工圖面整合中心,現場所有施工圖面都需經此整合中心確認後才會發到施工人員,確保施工圖面的正確性。
工地CAD室是各專案執行時必要的組織,CAD室通常選在工務所明顯的位置,讓所有工程師都習慣進到CAD室討論或查閱圖面,CAD室成員組成除了台積電空間管理工程師外,主要為各系統廠商之套圖工程師及5D繪圖人員,總成員約為25~30人,主要工作是在施工前完成整個專案施工圖繪製及5D模型建立,提供給工程師在施工前了解管路及設備位置,同時看到其他平行包管路的相對關係,施工過程中,施工人員若對圖面標示有疑慮時,直接進CAD室查看5D模型,問題即可獲得解決,同時利用5D更能清楚的討論施工順序的步驟,以避免施工時產生干涉。
在傳統作業流程中,各空間的管路配置狀況需靠空間管理工程師以2D剖面圖及平面圖來說明,若圖面標示不清處還需靠套圖工程師以口述的方式來說明,施工廠商就必需找套圖工程師才能獲得圖面正確的資訊,往往會造成工進的延宕或施工錯誤的情況產生。
步驟二:訂定空間管理規則
施工階段的空間管理工程師承接規劃及設計階段的圖面,透過與廠商的套圖會議及圖面的說明,讓所有廠商清楚瞭解規劃及設計的規則,並補充施工時必需遵守的空間配置規則,讓各系統廠商繪製施工圖面時能清楚各自管線應該繪製的位置,避免廠商各自發展施工圖面,屆時將造成空間無法整合的困境。整個廠房空間,除廠務系統的管線設備配置空間外,還包含了生產機台及其附屬設備之裝機空間及搬運、維修動線等,這些空間都必需於施做廠務系統階段被完整的保留。此階段在5D模型中繪入生產機台及保留空間範圍,讓繪圖人員可避開保留區域繪製管路及設備。在傳統做法,很難將這些保留空間清楚標示,容易造成廠務系統管路進入保留空間而不自知,直到裝機階段才發現時,往往就必需拆除重新施作,除了造成重覆施工,亦會影響裝機進度。
步驟三:2D圖面繪製及套圖
各系統廠商依照空間管理工程師的規劃路徑,進行施工圖面的繪製後,將圖面匯入CAD室的公用電腦中,由各區主套工程師將圖面進行套疊的動作,並檢查各管線及設備是否碰撞,此工作目的為讓各區主套初步檢查各系統圖面是否依照規則繪製,避免繪製5D模型時產生大量的管路碰撞,影響繪圖進度。在傳統的作法中,此階段就必需將所有管路及設備明確的繪製,套疊後仔細反覆的檢查是否有碰撞,若檢查有遺漏,錯誤即會發生於施工現場,無法事先預知。
步驟四:5D繪圖及檢查
此步驟正式進入5D環境進行設備及管路的配置模擬,5D繪圖工程師依照2D圖面所標示的位置,逐步將所有設備及管線以物件的方式,一個一個的繪入5D系統內,依照目前廠房規模,各專案大約有140萬個以上的物件將被繪入系統中。繪圖的同時可即時的看到其他系統的配置情況,若發現有碰撞可即時反應給套圖工程師,由工程師進行調整及修正。
依傳統2D繪圖系統的做法,套圖工程師需匯整各系統總共約600~700張圖面,重新調整管線及設備平面複合圖, 圖二訂出管線及設備的平面位置(X、Y 2D座標),再繪製管路剖面圖 圖三訂出管線高程定義Z軸座標,才能明確表示管路設計的位置,各系統再依套圖工程師所定義之圖面修改施工圖提供給施工人員施工,每張圖面如同 圖二所示,都是是密密麻麻的交疊,要確保圖面正確性,需要經過無數次的反覆檢查及修改,工作的困難度極高,也容易出錯,這些錯誤的代價往往就是時間跟金錢的付出。
圖二、冰水機房設備及管路平面圖
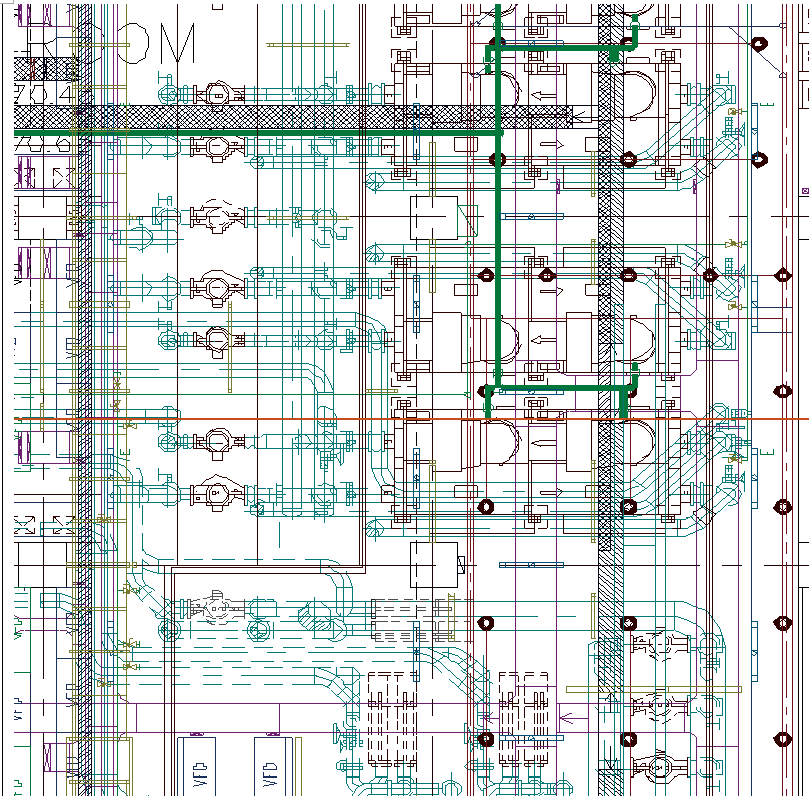
圖三、冰水機房設備及管路剖面圖

5D模型以3D立體方式顯示各設備管路之位置 圖四,大幅降低了檢查碰撞的困難度並提高正確性。以實際執行過的專案為例 表一,潔淨室面積約為24,000平方公尺,整個專案統計的碰撞點數為687處,其中有682處於5D檢查的過程中被發現,代表5D協助專案中99%現場可能發生的碰撞點。
圖四、5D 模型以3D 立體方式顯示各設備管路之位置
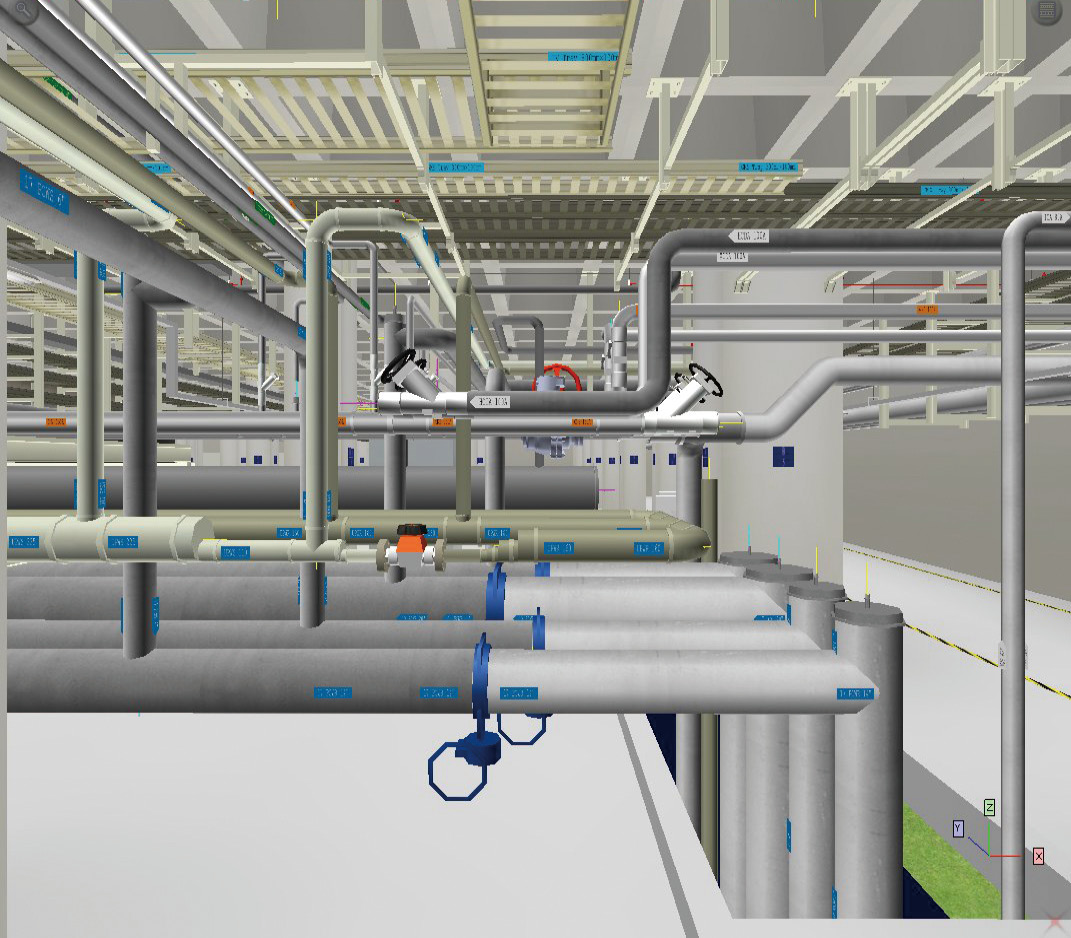
發生時間 |
管路碰撞點數 |
---|---|
5D套圖階段 |
682 |
施工階段 |
5 |
碰撞點總計 |
687 |
5D系統提供了2種檢查的模式,介紹如下。
- 虛擬實境的巡檢 (Walk through)
就字面上的意思而言,『虛擬』就是無中生有;而『實境』就是現實的環境,所以『虛擬實境』就是由電腦無中生有出一個現實的環境。使人在電腦中就可以獲得相同的感受,如同身處在真實世界一般。虛擬實境的實現使我們可以「不出門而達到身歷其境」的境界。
與其說5D是虛擬的環境,不如說5D是一個未來環境的模擬可能更為貼切,5D中Walk through的功能就能提供巡檢的功能,讓使用者得以瞭解完成後的環境,包括人員與物料搬運的動線、開關閥與儀表位置的妥適與否、安全設施與逃生動線、以及設備管線是否整齊美觀等等,均可藉由這個功能逐一檢查,以直接的視覺來檢查是最簡單的方式,每個人看到的畫面都是同一個,可排除認知上的落差。
- 全系統展示(Solo view)
透過5D系統Solo view功能的使用,可瞬間將選取的系統獨立展示,一個畫面就可看到所有管路的路徑,讓設計工程師檢查管路設計的合理及正確性,這個功能對檢查管線穿越整個工廠的系統而言,助益甚多,如消防系統、空調/排煙系統、廢氣處理系統等,均可利用此功能發現不合理的設計,或因兩承包商於界面點的誤解造成應銜接而未銜接的「掉棒」現象等。
步驟五:圖面的輸出
圖面是施工的依據,如何讓5D的內容可以被正確的實現是非常重要的一環,建立圖面的權威,必需提高施工圖的正確性,5D附加於autocad的轉圖功能,能將5D的內容轉成2D的施工圖面,如 圖五,並列出材料表,工程師可依據材料表備料及圖面施工,然而此功能於Crystal 5D中,由於軟體的問題,一直無法正確的實現,這是5D未來首先必須要改進的地方。傳統做法於步驟三完成後,即由各廠商出圖給施工單位施做。
圖五、5D 圖面輸出範例
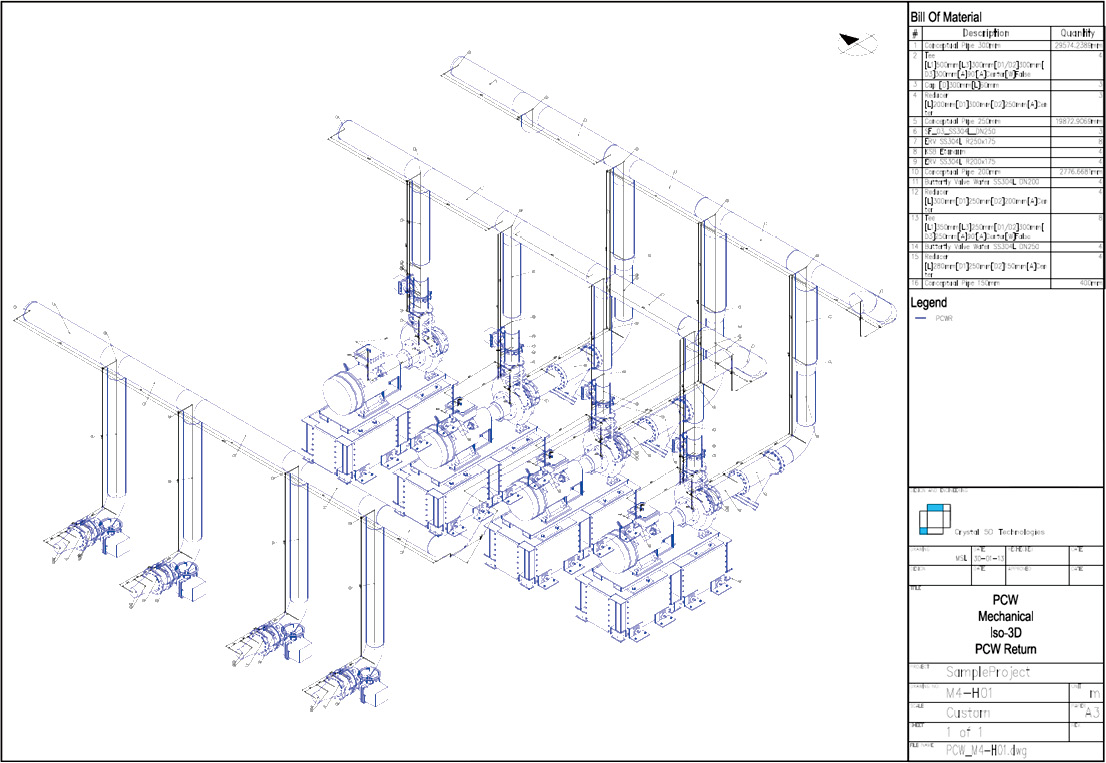
步驟六:現場圖面比對
施工人員未按圖施工是常發生的問題,在上述專案統計中92%現場施工錯誤,原因為未按圖施工 表二,因此需要求各系統監造工程師落實按圖施工,而空間管理工程師定期會同各主套工程師至現場做圖面的比對,若發現錯誤即刻要求拆除或修改,了解錯誤發生原因,並要求對施工人員進行教育訓練,避免錯誤持續發生及擴大。此步驟與傳統做法大致相同。
碰撞發生原因 |
管路碰撞點數 |
---|---|
未按圖施工 |
57 |
套圖錯誤 |
5 |
碰撞點總計 |
62 |
步驟七:竣工圖的驗收
竣工圖面對爾後的運轉及維護相當重要,所以正確性是必需要求的,經由現場實際量測的數據,修改施工圖面成為竣工圖,同步5D亦需更新,以求現場、2D竣工圖面及5D內容一致,至此步驟結束即完成圖面驗收。此步驟與傳統做法一致,但增加了5D的竣工驗收。
作業流程評比
經由上述的流程產生的圖面品質為評比的主要項目 表三,因為圖面品質的好壞直接影響施工的品質與工程進度。
評比項目 |
5D作業流程 |
2D作業流程 |
---|---|---|
溝通便利性 |
以視覺化的方式呈現,非專業人員均可容易了解設計結果,便於溝通及討論。 |
以工程圖說方式呈現,需專業人員才能正確閱讀圖面資訊,溝通時會因圖面理解能力不同而受阻。 |
圖面查閱便利性 |
僅需提供現場位置即可查閱該位置所有系統管線及設備 |
需提供位置、系統、圖名、圖號等等才能查閱到所需的圖面。 |
空間規劃正確性 |
以3D 立體化方式呈現,可從360度檢查,正確性可達100%。 |
多張圖面複疊,需靠不斷的重複檢查才能提高正確性。 |
工序安排的便利性 |
視覺化的畫面,可方便工序的安排,提高管理便利性。 |
需要有經驗的工程師安排工序。 |
繪圖人力及時間 |
2D繪製後還需繪製5D模型後才能出圖施做。 |
2D繪製完成後,即可出圖施做。 |
以評比結果說明,5D系統確實能讓施工圖品質提升,但需投入較多的人力及時間來繪圖,以整體性來評估,利用5D軟體來輔助提升圖面品質的方向是正確的也是趨勢,故提升的5D系統的效能及工程師的操作技能,是縮短繪圖時間的關鍵。
5D系統發展的建議
在前述的作業流程中,2D圖面的繪製及套圖步驟若能省略,能大幅度提升圖面繪製的效率,如何能擺脫2D的思考邏輯,讓工程師可以在5D的環境中做設計,需透過工程師技能的提昇及軟體功能的增加才能達到,以空間規劃的功能而言,目前軟體功能已能百分百達到模擬效果,達到提高施工效率目的,但以施工管理及設計的需求,期望軟體能增加以下幾項功能。
施工時序顯示功能
「物件」是目前5D軟體計量的單位,若能在每個物件加上施工時間的資訊,利用時間點選擇來顯示時間點前需施工的物件,可有效管理施工的進度及檢查工序的安排是否順暢,對未來施工管理有很大的幫助。
防止碰撞功能
現實施工狀況,管路是不會發生碰撞,因為在碰撞前就會發現而停止施工,但目前5D軟體能允許管路或設備碰撞,這些碰撞若工程師未即時解決,需靠後續檢查才會發現,增加了錯誤發生的可能性。軟體設計應讓管路在發生碰撞時無法繪入,設計工程師必需立即解決碰撞的問題之後才能繼續進行繪圖,真正符合即時更新的目的。
全區域的展示功能
目前軟體受限於視野的距離,容易被侷限在小區域內檢討,無法大範圍的觀看設計狀況,若能增加全區域的展示功能,就如同2D圖面一樣方便,相信對設計及施工的工程師都更加便利。
結語
本文主要以應用5D來執行空間管理的流程來說明與傳統2D做法上的差異,其中分析可知5D具有溝通的便利性、圖面查閱的便利性、空間規劃的正確性、工序安排的便利性等優點,確實能有效提升效率及正確率,但需投入較多的人力及時間在繪圖,此點仍要持續的改善。希望透過此分析,能讓未來有心從事相關研究的人參考。
留言(0)