摘要
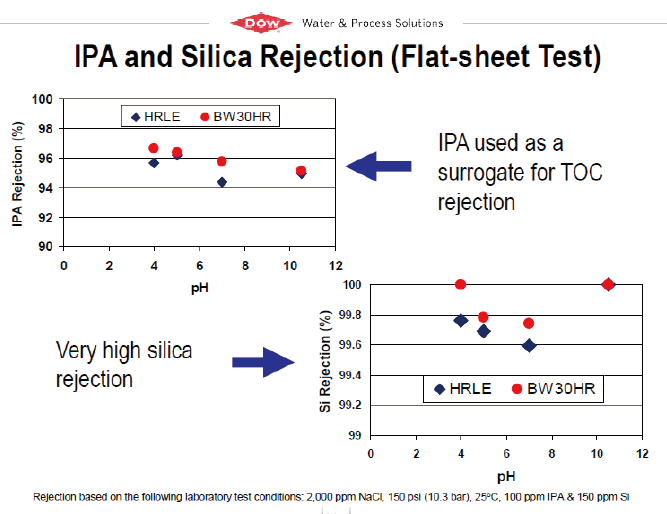
以氣提法進行IPA廢水改善評估與VOC廢熱回收展望
前言
半導體製程在晶圓清洗及乾燥程序中使用大量的異丙醇(IPA),因其有機溶劑揮發特性及製程排放廢水衍生丙酮 ,對各廠區空水污影響甚鉅。半導體廠房因次級用水之回收水量與水質需求,常見以RO膜進行廢水濃縮精煉處理 ,但經過精煉而產出的濃縮高濃度有機廢水排放至廢水中除影響化學需氧量(COD)外,也衍生出納管丙酮偏高風險 。而有機廢水常以生物處理系統進行降解處理,但生物系統所需之反應池及生物污泥脫水等附屬設備,對成廠區空間規劃上實屬一大挑戰。經評估各種物化處理方法之後,本篇文章試以氣提方式進行IPA去除效率實驗,並規劃結合半導體廠房內VOC燃燒及廢熱以去除氣態IPA,達到廢水IPA及丙酮改善。
文獻探討
2.1廠房有機廢水回收系統及放流影響狀況
半導體廠房內為提供次級用水充足水量,於機台端會將各種廢水進行分流後回收再利用,而未達次級用水水質要求之廢水則再設計以回收系統作精煉處理,近年因空氣污染法規逐年嚴峻,廠區空污防制設備的精進成為一大學問,如Local/Central Scrubber以次級用水並應用污染物於氣液溶解平衡原理將設備機台排氣中污染物捕捉至水中,但次級用水中部份污染物也有從液相揮發至氣相造成衍生污染的風險,具揮發性之IPA即為其中一項,對此部分廠房將含有IPA之有機廢水以RO系統精煉後再送至次級用水使用,以一半導體廠區之有機廢水處理系統為例,該廠區系統設計以活性碳塔與RO系統進行有機廢水精煉,其RO膜採用陶氏化學高效率RO膜(BW30HR-440i),在pH=7作條件下IPA去除率可達>94%(如 圖1),該廠利用兩級高效能RO膜處理IPA濃度約600ppm原廢水,其RO產水最佳可控制於4ppm(如 圖2),以RO精煉後產水取代原先直接回收供應Scrubber之回收水,經煙囪採樣結果可見IPA濃度減量已達85%(如 圖3),然而RO濃縮廢水IPA濃度達2000ppm 。該廠於2019年度自行檢測放流水質,部分樣品所測出Acetone濃度近12ppm,IPA濃度達34ppm,質量平衡大盤查出該股RO濃縮水為放流IPA/Acetone主要來源,依據新竹科學工業園區新竹園區下水道可容納排入之水質標準中丙酮納管限值為5ppm,有機廢水回收系統的建立雖成功改善空污,但也衍生出水污放流丙酮偏高的風險。
圖1、BW30HR-440i RO膜於不同pH操作下對IPA/Silica去除率
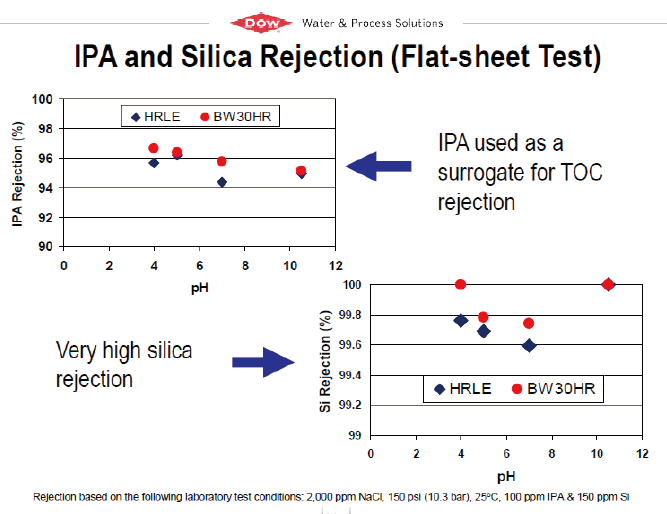
圖2、廠區有機廢水回收系統處理後IPA濃度平衡
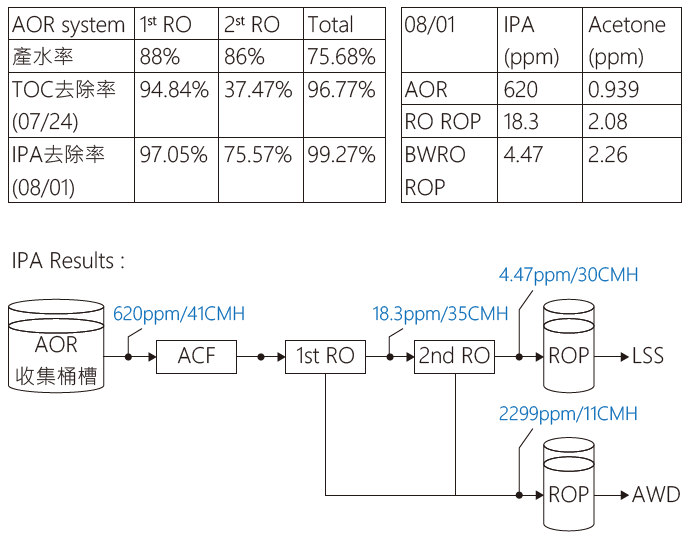
圖3、有機廢水回收系統上線後Scrubber採樣IPA濃度量測結果
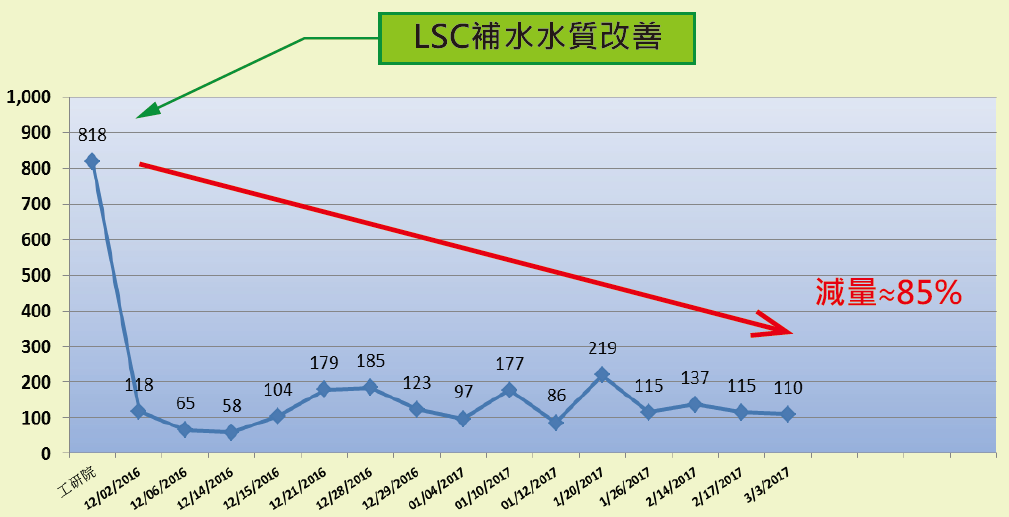
2.2IPA廢水物化處理
在永續發展的角度上,有機廢水主要多以生物處理法進行有機污染物的去毒性及降解,然建置生物系統對部分成廠區無空間可設置,因此改以評估其他具實廠運轉實績或有發展潛力之物化處理技術,文獻中IPA相關物化處理技術包含 : ①氣提法 ②滲透蒸發法 ③高級氧化法。
2.2.1 氣提法
氣提法乃是利用亨利定律及物質氣液介面間的質傳,自高濃度液相中將揮發性物質脫離至低濃度氣相中的物理過程,達到去除水中污染物的目的,其技術成熟,常見以塔式系統進行氣液質傳,王等(2002)[1]研究以氣提法方式去除半導體廢水中高濃度IPA,其廢水IPA濃度達10,000 ppm ,經氣提過程後濃度僅存500ppm,去除率可達95%,另江(2001)[2]於文獻中進行氣提脫附測試指出影響氣提脫附效率因素包含氣液相接觸時間、空氣流速壓力及溫度等。
2.2.2 滲透蒸發法
滲透蒸發法為結合滲透膜以及蒸發,以膜將物質自混和液中轉至氣態分離,其技術多用來進行醇類提濃,巫(2004)[3]與陳(2012)[4]等研究以滲透蒸發技術進行醇類提濃 ,雖操作容易,然此技術研究目前多適用於高濃度醇類再精煉,低濃度醇類回收則較無相關技術。
2.2.3 H2O2/O3/UV
使用H2O2/O3/UV進行高級氧化法,以氫氧自由基進行IPA及其氧化中間產物丙酮進行氧化,Wu et al.(2008)[5]以高級氧化法進行IPA降解實驗,其IPA降解後丙酮濃度可<100ppm,然此系統實廠操作成本高,且氧化流程需足夠反應時間。
2.2.4 ACF+H2O2
ACF+H2O2則以催化氧化的途徑產生氫氧自由基來進行有機物降解,Santos et al.(2009)[6]試以ACF/H2O2/ACF+ H2O2等不同組合搭配嘗試進行IPA去除,結果顯示以ACF+ H2O2的組合下IPA去除率達60%。既有廠區嘗試將部分有機廢水原廢水(IPA=116ppm)導入含H2O2之氨氮廢水系統進行處理,如 圖4實驗結果顯示H2O2於第一段ACF即完全降解,但IPA濃度無明顯變化,至第二段ACF時IPA才有受吸附影響減量。
圖4、有機廢水導入含雙氧水之氨氮系統測試結果
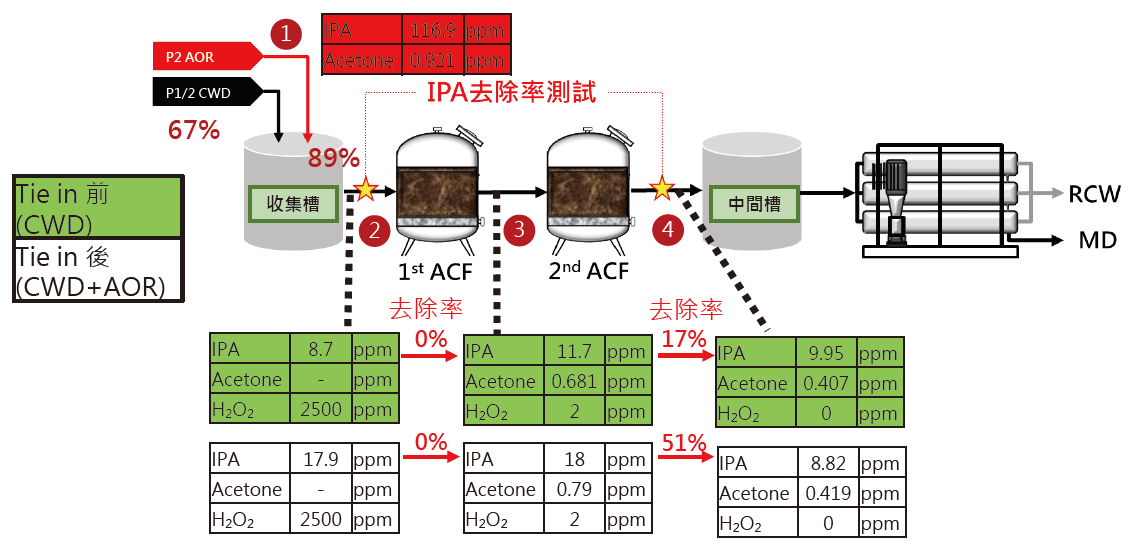
總整2.2節物化處理方式之優缺點比較如 表1所示,其中氣提法實廠化相比起傳統生物處理系統錦需較少建置空間,其經過實驗結果IPA去除率約可達到95%,另外與其他物化去除方式相比,也是一個較為成熟的運轉技術。
方法 |
去除效率 |
優點 |
缺點 |
---|---|---|---|
氣提法 |
IPA(mg/L)=10000→500 (去除率 : 95%)(王春盛2002) |
去除效率高(可至95%) |
設備操作、建置難度高、存在工安風險 |
滲透蒸發法 |
提升醇類濃度,IPA : 95wt%→99wt% (巫柔誼2004、陳登鑑等2012) |
環保、操作簡易 |
親水性膜滲透蒸發程序→成熟(王大銘2002、陳俊民2009) 疏水性膜滲透蒸發程序→技術尚不成熟 |
H2O2/O3/UV |
IPA=1000mg/L,丙酮<100mg/L (Wu et al. 2008) |
去除效率高(可至90%) |
處理費用高,若反應時間短(<2hr)丙酮>400mg/L |
ACF+H2O2 |
去除效率 : 催化氧化 (ACF+H2O2) : 60%>無催化氧化(H2O2)、吸附(ACF) : 20% (Santos et al. 2009) |
可利用現有系統(CWR), 將AOR導入處理 |
較少人使用、文獻較少 |
2.3IPA氣提法操作與影響因子
Lin et al.(2004)[7]應用氣提原理結合冷凝與回性碳吸覆進行半導體廠IPA廢溶液回收試驗,並於試驗中進行操作條件與回收率表現比較。如 圖5,其測試中在70度下僅需153分鐘即可於冷凝液中回收近90%IPA,然隨溶液溫度逐漸遞減至40度時需花費2265分鐘才可達到回收率平衡,然此平衡點也僅只有62.1%。圖6為總整不同操作溫度對去除率以及操作時間之曲線,可看到若操作溫度達50以上有更佳的最大去除率,隨溫度提高則是能縮短達到最大去除率的時間。圖7、圖8在操作溫度50度下,不同操作風量對IPA去除率之變化以及最大去除率影響,操作風量從1.0L/ min至2.5L/min其最大去除率變化區間僅於92~93%之間變動,然而操作風量對於達到最大去除率的時間影響仍屬顯著。
圖5、不同操作溫度對IPA去除率
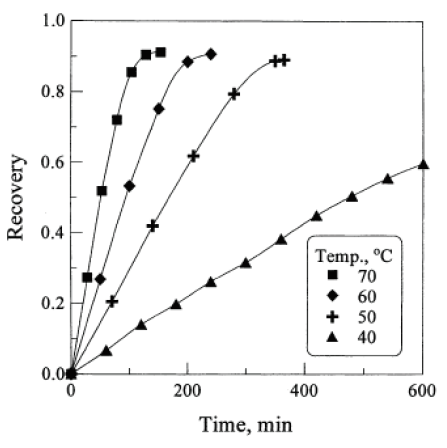
圖6、不同操作溫度下之最大IPA去除率
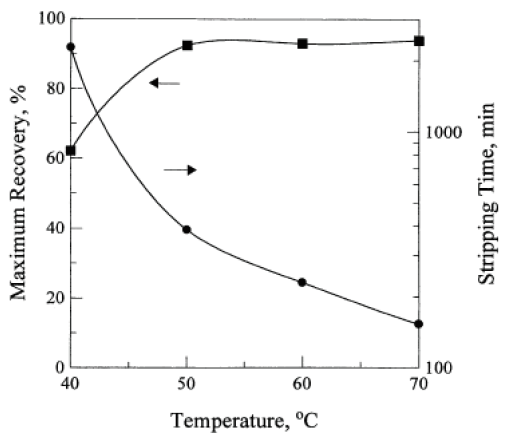
圖7、不同操作風量對IPA去除率
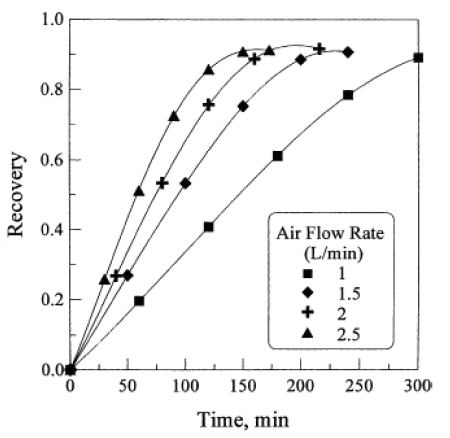
圖8、不同操作風量下之最大IPA去除率
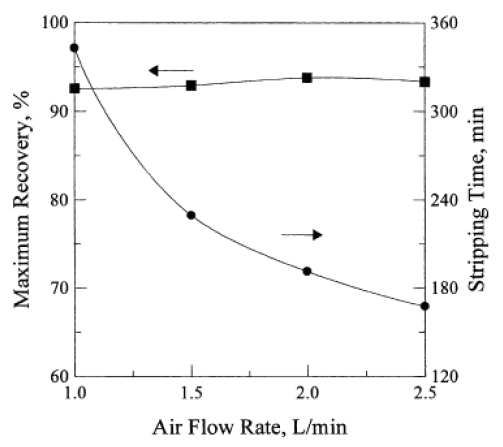
Guan et al.(2015)[8]結合Gas Stripping和Vapor permeation技術進行IPA溶液分離測試,而其中比較以GSVP與滲頭蒸發及蒸餾技術分離75度之3wt%IPA溶液之蒸發耗能如 圖9所示,參考IPA VLE data(圖10)探討在相同操作溫度下GSVP有較低耗能表現之原因應在於其實驗設計上以Vacuum pump操作使操作環境為負壓,IPA蒸氣壓下降 ,相同75度3wt%IPA溶液在此環境則提供較大能量使其轉換至氣態。
圖9、GSVP、蒸餾與滲透蒸發對3wt%IPA蒸發耗能比較
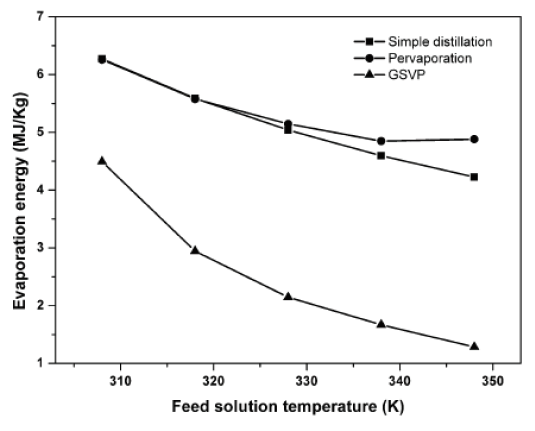
圖10、IPA Vapor-Liquid Equilibrium data
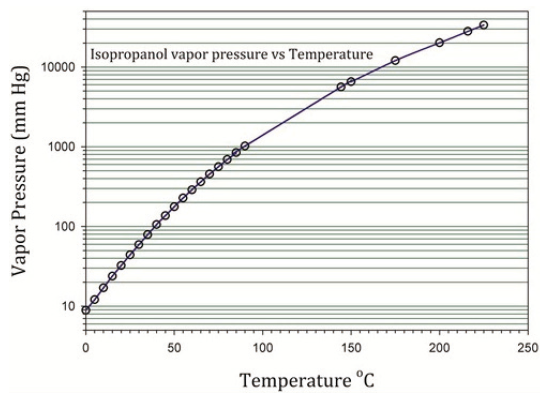
研究方法
3.1操作情境選定
參考各文獻中選定對IPA去除率有影響之重要參數做實驗操作情境,目前實驗規劃之操作情境有 :
① 曝氣量變化對IPA去除率影響
② 曝氣槽氣提與氣提塔對IPA去除效率比較
③ 於氣提塔系統內,操作溫度對IPA去除率影響
④ 於氣提塔系統內,真空度(負壓)對IPA去除率影響
⑤ 實廠取樣水質與配置(純IPA混和DI水)之去除率影響比較
3.2實驗設備配置
依據3.1節操作情境選定結果,實驗配置包含曝氣氣提與氣提塔兩系統。曝氣氣提系統包含打氣機與一10L桶槽,打氣機管路至桶槽底部則有安裝散氣設備。氣提系統設備則設計以一長型透明PVC管柱做為氣提塔,除打氣機送氣外另增加抽氣馬達進行真空度操作,溫度試驗則是以加熱器將試驗廢水熱交換升溫,試驗廢水再以馬達打至氣提管柱頂部做進樣,整體配置如 圖11所示。
圖11、IPA氣提去除實驗設備配置
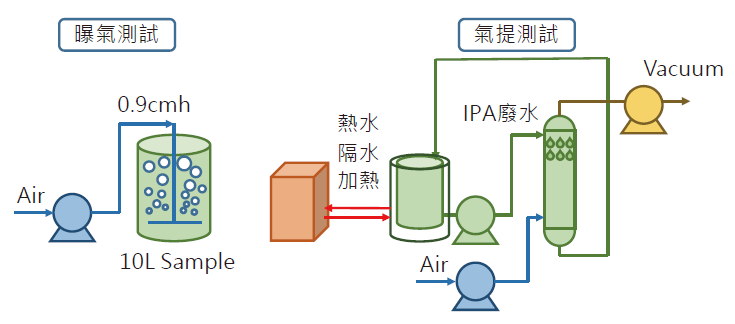
結果與分析
4.1曝氣量對IPA去除率之影響
曝氣量對去除率之實驗設置如 表2所示,在室溫25度C下,以IPA濃度450ppm廢水分別於曝氣量0.9、0.6、0.3 CMH的狀況進行去除率測試,測試結果如 圖12所示,在反應初期不同曝氣量對去除率影響差異不大,隨反應時間增加至24小時後,通過0.9CMH曝氣量的試驗水樣可將液體中IPA降至300ppm以內,比起僅使用0.3CMH曝氣量的試驗水樣,去除率的差異約有15%,結果表示曝氣量的提升有助於破壞IPA廢水的氣液平衡狀態,使溶於試驗廢水中IPA傾向往氣態方向進行平衡,然而僅使用一般曝氣設計若須於特定時間內將IPA濃度減至期望去除率,仍須考量其他操作參數或對設計進行改善。
IPA曝氣實驗 |
|||||
---|---|---|---|---|---|
溫度(℃) |
溶液總量(L) |
IPA初始濃度 (mg/L) |
曝氣量 (CMH) |
氣液比 |
|
操作條件 |
25 |
10 |
450 |
0.9 |
90 |
0.6 |
60 |
||||
0.3 |
30 |
圖12、不同曝氣量對IPA去除效率
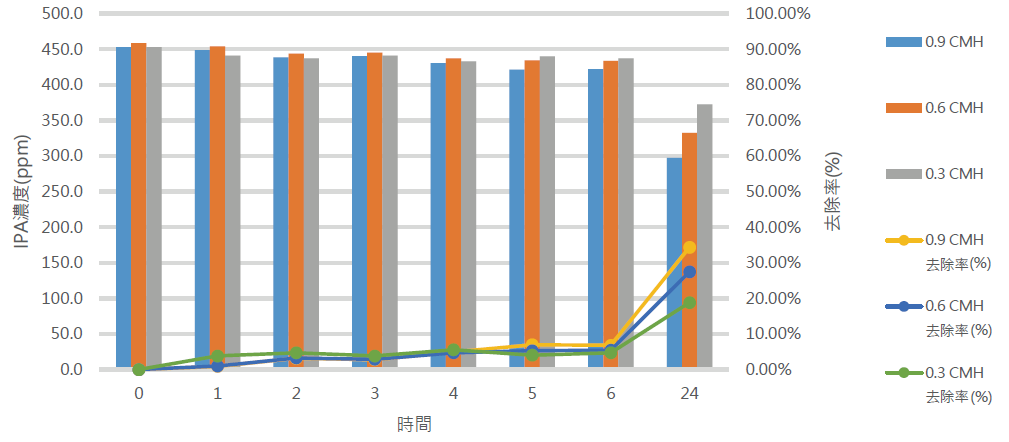
4.2曝氣與氣提機制比較
測試同樣在室溫25度、1kg/cm2氣壓下,以420~450 ppm之IPA廢水進行曝氣與氣提反應器比較,其實驗設計如 表3所示,測試結果如 圖13所示,隨反應時間進行,在各階段氣提操作對IPA之去除率優於曝氣操作,主要是因氣提設計內含有噴頭、隔板等設計增加氣液接觸面積與停留時間,且其氣提操作氣液比(G/L)僅75即比曝氣操作有更好的去除效果,因為氣提對IPA去除效益明顯比曝氣大,後續將以氣提進行其他參數對去除率影響之試驗。
IPA氣提實驗(反應器比較) |
|||||||
---|---|---|---|---|---|---|---|
溫度(℃) |
曝氣量(CMH) |
液體體積 (L) |
Lab Test 氣液比 |
液體循環速率 (CMH) |
初始濃度(mg/L) |
絕對壓力(Kg/cm2) |
|
Buffer Tank |
25 |
0.9 |
10 |
90 |
- |
450 |
1 |
Stripper |
0.15 |
2 |
75 |
24 |
420 |
1 |
圖13、曝氣桶與氣提塔對IPA去除率比較
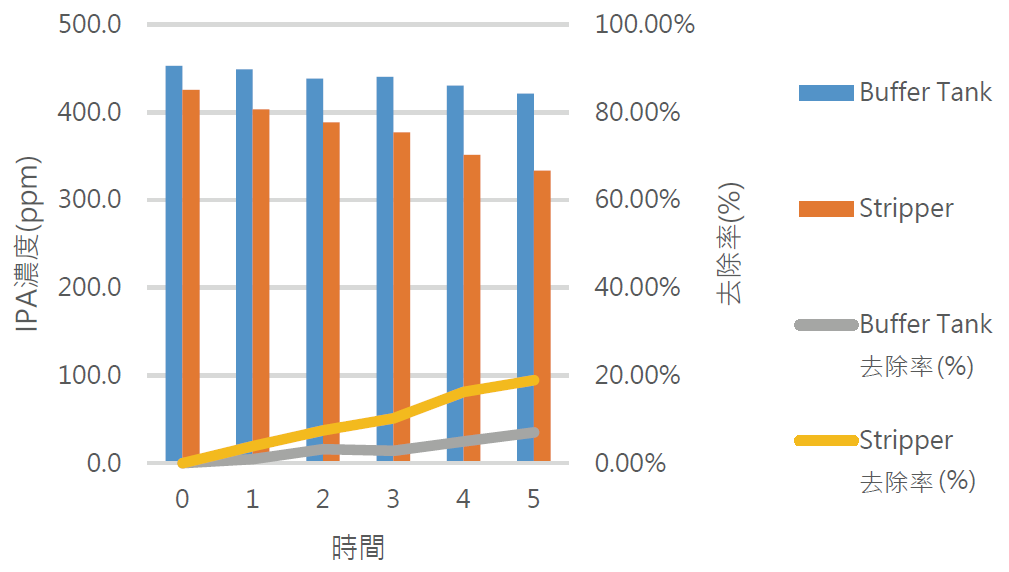
4.3操作溫度對氣提IPA去除率影響
在氣提系統中測試以室溫、50度、60度的操作條件下IPA廢水去除效果,實驗設計如 表4所示,測試結果如 圖14所示。在開始反應的第一小時即可觀察到,以操作溫度60度下,其IPA去除率可達30%,相較於室溫其IPA去除率於第一小時後僅有10%,隨反應時間進行後,可發現隨操作溫度上升,IPA廢水去除效率越好,此外在IPA濃度降至200ppm以下時,較高的操作溫度也能保有一定去除率。
IPA氣提實驗(溫度) |
||||||
---|---|---|---|---|---|---|
操作條件 |
溫度 |
液體 體積(L) |
IPA初始 濃度(mg/L) |
絕對壓力 (kg/cm2) |
曝氣量 (CMH) |
氣液比 |
室溫 |
2 |
420 |
0.75 |
0.15 |
75 |
|
50 |
||||||
60 |
圖14、不同操作溫度對於IPA氣提塔去除率影響
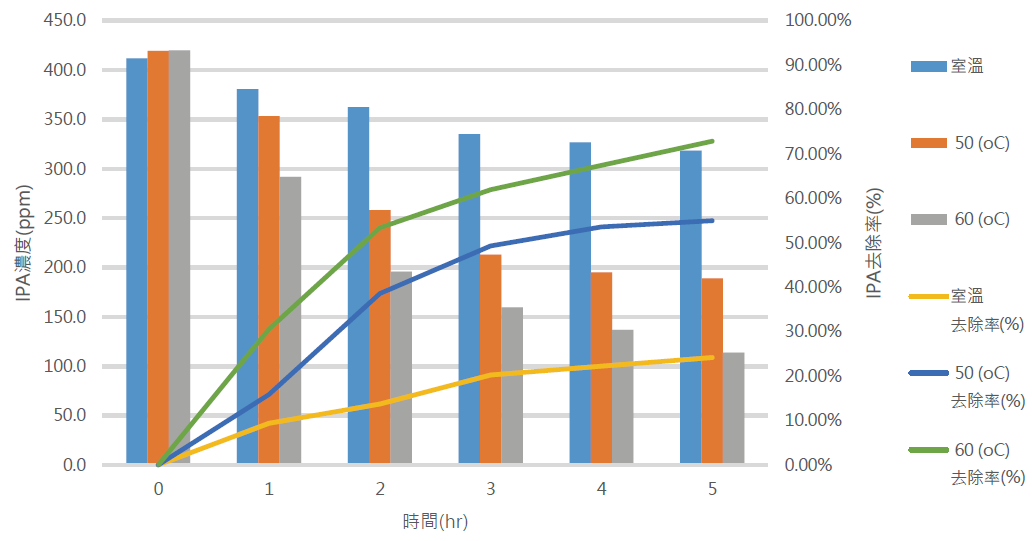
4.4操作真空度對氣提IPA去除率影響
藉由調整氣提系統內的環境壓力,並以60度之IPA廢水進行測試,將IPA沸點降低提高去除效果,實驗設計如 表5所示,其中在操作0.6kg/cm2氣壓的設定情境需調整曝氣量以避免曝氣量過大破壞真空效果,測試結果如 圖15所示,氣提系統在負壓操作環境下對比常壓操作整體反應過程有較佳的IPA去除率,在反應初期各操作壓力的IPA去除率相差不大,其去除效果主要來自於操作溫度之效益,隨反應時間推移,負壓系統破壞氣液平衡對於IPA去除之貢獻趨於明顯。而在0.75與0.6atm的負壓操作比較上對IPA去除率無明顯差別,此項可作為未來操作成本考量上之參考。
IPA氣提實驗(真空度) |
||||||
---|---|---|---|---|---|---|
溫度 |
液體體積 (L) |
IPA初始 濃度(mg/L) |
絕對壓力 (kg/cm2) |
曝氣量 (CMH) |
出氣量 (CMH) |
氣液比 |
60 |
2 |
420 |
1 |
0.15 |
0.16 |
75 |
0.75 |
0.15 |
0.15 |
75 |
|||
0.6 |
0.1 |
0.11 |
50 |
圖15、不同真空度對於IPA氣提塔去除率影響

結論與後續規劃
總結第四節氣提實驗結果,氣提塔比起曝氣槽較適合作為廢水IPA去除設備,並且需進行廢水升溫與負壓操作。低濃度(IPA=450ppm)實驗結果去除率可達70%以上,而廠區經過RO系統精煉後之高濃度IPA廢水目前以應用化工模擬軟體CHEMCAD進行模擬評估,模式中進入氣提塔之有機廢水IPA濃度約1,200ppm,其氣提塔水質水量平衡後模擬結果如 圖16所示,經氣提後產水IPA僅剩250ppm,而氣提後廢氣IPA濃度可到6,000ppm以上供應VOC燃燒,並結合燃燒廢熱再利用,以氣提塔處理IPA除可達到放流目標 ,應用廢熱節能,對於成廠區空間利用上也是一個優於生物系統等較佳的選擇。
圖16、CHEMCAD模擬高濃度(>1,000ppm)IPA經氣提塔平衡之結果
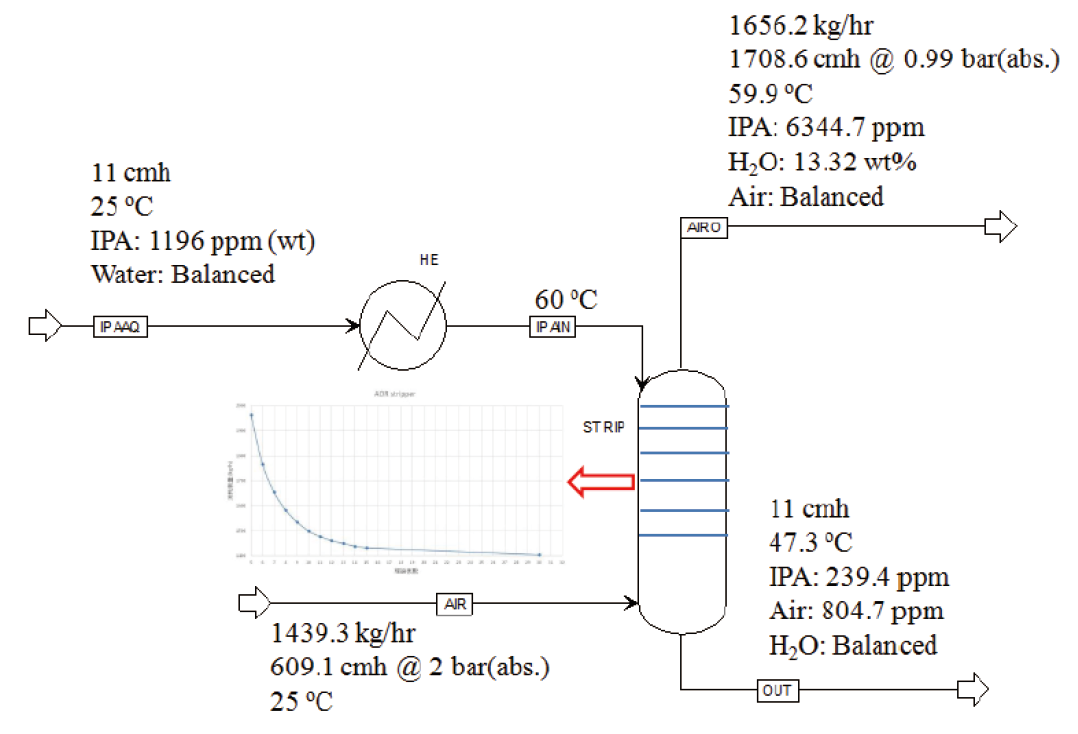
參考文獻
- 王春盛,半導體高濃度廢水之高級氧化處理與有機廢液之異丙醇回收,2002。
- 江昌達,高濃度半導體廢水之處理與回收,2001。
- 巫柔誼,以滲透蒸發技術分離醇類水溶液及酯化反應之研究, 2004。
- 陳登鑑,運用超音波氧化脫硫技術將廢輪胎裂解油成為再生能源之研究,2012。
- J.J. Wu, J.S. Yang, M. Muruganandham, C.C. Wu,The Oxidation study of 2-propanol using ozone-based advanced oxidation processes,Separation and Purification Technolo gy,2008。
- V.P Santos, M.F.R. Pereira, P.C.C. Faria, J.J.M. Órfão, Decolourisation of dye solutions by oxidation with H2O2 in the presence of modified activated carbons,Journal of Hazardous Materials,2009。
- Sheng H. Lin, Chuen S. Wang,Recovery of isopropyl alcohol from waste solvent of a semiconductor plant,Journal of Hazardous Materials,2004。
- Yu Guan, Song Hu, Ying Wang, Peiyong Qin, M. Nazmul Karim, Tianwei Tan,Separating isopropanol from its diluted solutions via a process of integrating gas stripping and vapor permeation,RSC Advances,2015。
留言(0)