摘要
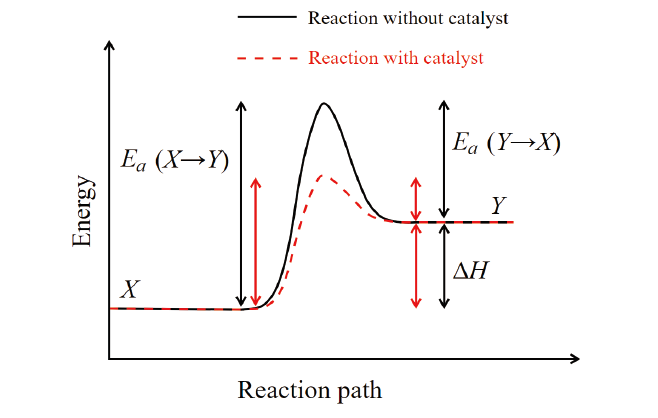
無憂無氯-低濃度廢硫酸回收效率提升及品質優化
Keywords / Solubility of hydrochloric,Catalysts,Reaction kinetics
Tsmc use the hydrochloric acid method to remove hydrogen peroxide in waste sulfuric acid, and the reaction by-product chlorine is removed by the local-scrubber system. As a result of high solubility of hydrochloric acid in low-concentration sulfuric acid. The hydrochloric acid is difficult to form chlorine, which is remain in sulfuric acid. This result effect the ammonia nitrogen system and the ammonium sulfate crystallization system operation. This study use reaction kinetics and catalysts point of view. To shorten the reaction time and reduce chloride residual concentration, by increase the initial reaction temperature to 50°C to enhance the effective collision instead of high amount of hydrochloric acid adding. And evaluate the external heat source in the low-concentration waste sulfuric acid system that not only improve the capacity but also get the high-quality sulfuric acid; furthermore, provide to the facility system without any worries.
1. 前言
硫酸為重要工業原料之一,舉凡化工、石油、肥料、清潔劑、炸藥均需使用,甚至跨足半導體晶圓代工產業。硫酸、過氧化氫與純水依一定比例混合後於半導體製程清洗矽晶圓表面使用,而矽晶圓表面的潔淨度為影響良率、產品品質及可靠度的一大關鍵,因此伴隨衍生出大量副產物-廢硫酸,以往廢硫酸僅能委外進行清運處理,轉製為工業級硫酸。
為落實循環經濟台積電於民國104年開發出業界首創「鹽酸法除過氧化氫系統」成功回收製程排放廢硫酸,於tsmc廠內完成再生工業級硫酸生產線,供廠區氨氮系統使用,去除過氧化氫主要目的為將氧化性物質移除以保護MD脫氣膜(Membranes Degasified),但氯離子本身易容於水,形成次氯酸根,一樣具氧化性,因此廢硫酸再生系統均有訂定產酸氯離子規範(<30ppm),而隨著廠區製程不同造成直接影響,使排放廢硫酸濃度有所差異。以F15P3/4廠為例,當硫酸濃度低於50%時,於鹽酸法反應過程,氯離子較難以形成氯氣型態,造成高濃度氯離子殘留於再生硫酸中;實務上為確保後段回收系統單元避免遭受高濃度氯離子腐蝕,因此無法增大鹽酸加藥量以獲得更快反應速率,因此導致反應時間過長,衍生廠內回收酸供不應求問題。
根據上述問題結合化學反應發現,低濃度廢硫酸之鹽酸法與觸媒反應類似,亦即代表反應前後總量不變,但鹽酸加藥量不足又導致反應速度過慢,形成兩難;因此將藉由提高反應起始溫度增加分子動能,再搭配少量鹽酸加速過氧化氫分解以達雙贏局面,若實驗結果可達預期,將可同步推廣至各廠,減少鹽酸加藥量並同時減少氯氣產生,減低運轉上的風險及設備維護負擔。
2. 文獻回顧
2.1 廠內廢硫酸去除過氧化氫機制探討
目前tsmc廠內皆藉由鹽酸法加藥去除過氧化氫,此方法優點相對於蒸餾法及活性碳法具有操作成本低的優勢,但伴隨而來的是操作過程中會產生有害氣體-氯氣,因此後段皆需搭配立式洗滌塔進行尾氣處理,避免有害氣體對環境的危害,鹽酸法於去除過氧化氫之相關反應式如下所式 :
H2O2+HCl→H2O+HOCl 式1
HOCl+HCl→H2O+Cl2 式2
HOCl+H2O2→H2O+HCl+O2 式3
H2O2→H2O+1/2 O2 式4
總反應式 : 3H2O2+HCl+HOCl→4H2O+Cl2+3/2 O2(HCl為反應物)
過氧化氫本身具有自我分解的能力並放出熱能,但常溫下過氧化氫自我分解速率非常慢,因此需藉由催化劑或添加反應物加速分解,由上述總反應式即可得知,鹽酸法對於過氧化氫的分解扮演的角色並不是觸媒而是以反應物形式參與整體反應,因此鹽酸添加量的多寡,將直接影響過氧化氫的反應速率,若為滿足廠內硫酸需求量,則需藉由增大鹽酸添加量,加快反應,但隨之而來的,則是反應過程產出更多有害氣體-氯氣,大幅增加運轉風險及設備成本,舉例 : 倘若風管腐蝕造成氯氣洩漏,人員健康及機房區域環境勢必首當其衝。
而F15P3/4來源廢硫酸濃度介於41~45%,遠低於各廠平均濃度55~70%,以此為例,F15P3/4 WSR於系統實務操作經驗得知隨著鹽酸添加量增加,確實會縮短整體反應時間,但再生之硫酸內含有的氯離子殘留濃度與鹽酸添加量成正比關係成長,而經由鹽酸添加量換算整體廢酸殘留氯離子濃度,可得證鹽酸添加量與氯離子殘留量相等,此結果意謂反應過程中並無形成逸散氯氣,導致氯離子殘留,由此結果比對上述相關反應式,即可發現反應(式2)並無發生,因此鹽酸於F15P3/4 WSR系統反應表現為擔任觸媒的角色,代表反應前後總量不變,因此總反應式如下 :
總反應式 : H2O2→H2O+1/2 O2(HCl為觸媒)
由上述機制探討,可知廢硫酸濃度是影響鹽酸於去除過氧化氫的整體反應中的重要參數。
2.2 鹽酸於不同硫酸濃度之溶解度
由2.1章節反應機制探討可發現,硫酸濃度對於鹽酸去除過氧化氫反應為關鍵參數,由文獻指出,氟氯碳化合物為催化臭氧層破洞的主要元兇,若在火山爆發活躍時機,會釋放出大量的HCL氣體至空氣中,促使氯的活化,進而催化臭氧,形成氯氧化合物,因此LYN R. WATSON et al.[1]等人在執行平流層臭氧層破洞研究時,於不同硫酸濃度針對鹽酸氣體捕捉能力,影響氟氯碳化合物生成,進行了一系列的實驗,此研究成果可套用於鹽酸去除過氧化氫之反應,由數據(表1)可發現當硫酸濃度低於52%時,鹽酸的擴散係數約為濃度58%之17倍,亦即代表鹽酸於低濃度硫酸(<52%)具有較高的溶解能力,而進一步將鹽酸擴散係數對硫酸濃度作圖,由擴散速率曲線(圖1)可發現鹽酸擴散係數,於硫酸濃度介於40~60%區間產稱劇烈變化,當硫酸濃度大於60%,擴散係數幾乎趨近於0,由此研究結果可說明他廠藉由添加大量鹽酸於去除過氧化氫的反應中,卻無反應後氯離子濃度的殘留現象,然而F15P3/4卻只能添加少量鹽酸進行反應,使反應時間過長,並同時存在氯離子殘留濃度過高問題。
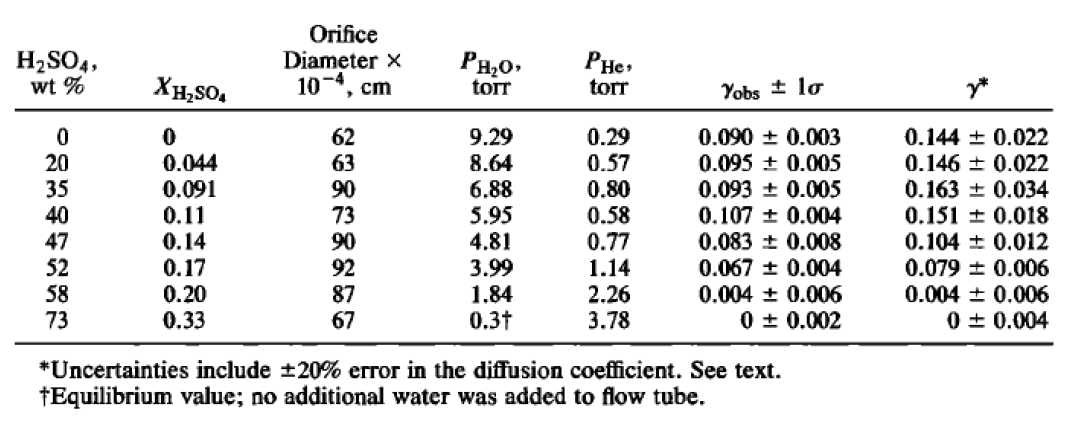
圖1、鹽酸擴散係數於不同硫酸濃度作圖[1]
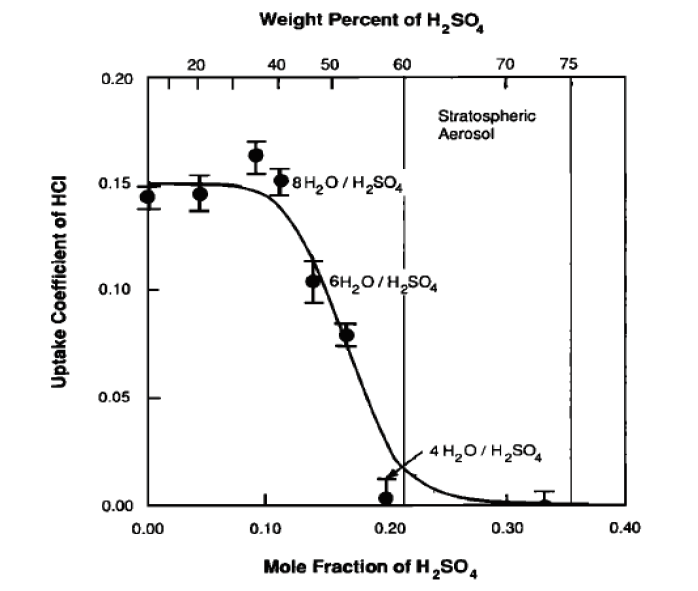
參照此文獻結論,協力廠商兆聯也分別在室溫及加熱至65°C,分別對於含有5%過氧化氫,濃度為50%及70%硫酸,進行定量鹽酸添加實驗,於室溫下針對硫酸濃度50%及70%添加定量鹽酸試驗得知,70%硫酸於鹽酸添加後隨即反應產生黃色氯氣,而於50%濃度硫酸重複上述試驗,幾近無產生任何催化反應,如量杯試驗狀態(圖2)所示,而對比相同條件並將反應溫度提升至65°C,可見70%硫酸反應轉變為更加劇烈,並產生更多氯氣,而50%硫酸雖有產生氣體,但該氣體非呈現黃色,非屬氯氣形態,且反應效果微弱,此行為模式說明僅為過氧化氫分解成氧氣狀態,如量杯試驗紀錄(圖3)所示,綜合上述實驗結果,70%硫酸濃度之化學反應,反應無論是在室溫亦或是65°C,添加硫酸均立即產生劇烈反應並生成黃色氯氣,而相較50%硫酸濃度,則可發現無論室溫或高溫的反應,皆沒濃度70%硫酸來得劇烈,且反應過程並無生成黃色氯氣,但探究此試驗結果可得知,透過反應起始溫度提高,將可增加反應速率,此結果與文獻[1]實驗相符,因此硫酸濃度確實於鹽酸去除過氧化氫之過程中,改變了鹽酸參與反應的路徑,所以各廠WSR系統鹽酸加藥量差異與產物品質的關鍵因子,不僅止於過氧化氫濃度,而廢硫酸濃度所造成影響亦不容小覷。
圖2、定量鹽酸添加於室溫下,不同濃度之硫酸反應結果
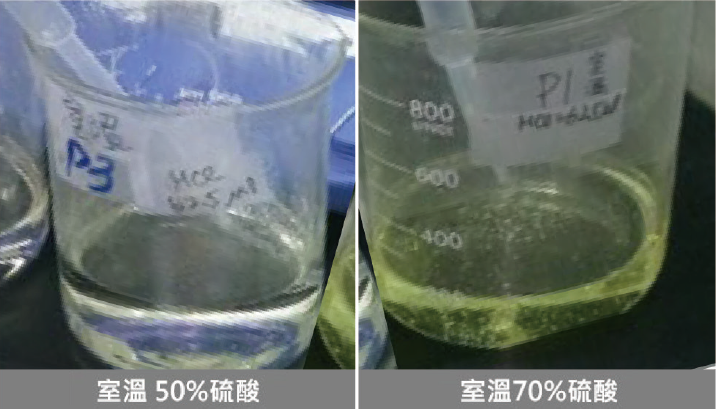
圖3、定量鹽酸添加於65°C,不同濃度硫酸之反應結果
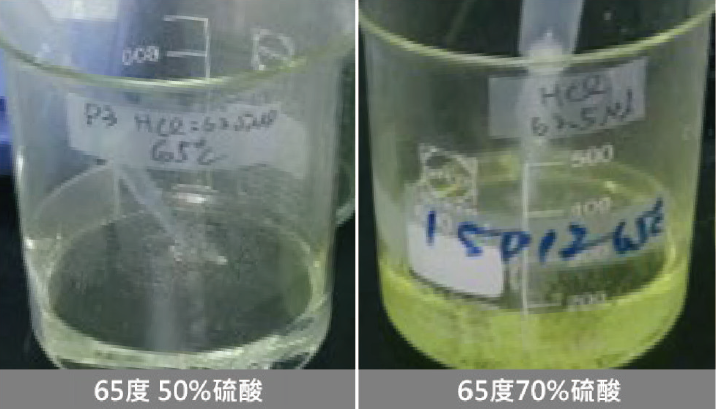
2.3 反應動力學及觸媒之應用
反應動力學是研究化學反應速率及反應途徑的一門科學,反應動力學告訴我們若一反應要發生反應粒子必需發生碰撞,但並不是所有的碰撞均會發生反應,而是要發生有效碰撞,且產生足夠的能量(活化能)才能破壞化學鍵,產生反應,因此根據反應速率方程式推導可得(式5)所示,若要加速反應有三個方式 : ①提高反應物濃度,亦即增加碰撞機率;②提高反應溫度,亦即提供分子動能超越活化能;③降低反應活化能,亦即藉由觸媒參與反應。
反應速率方程式表示法
若反應為A+B→C+D
則反應速率為-rA=k[A]m[B]n
其中-rA : 反應速率k : 反應速率常數m、n : 反應級數
又k=Ae-Ea/RT
其中Ea : 活化能R : 理想氣體常數T : 溫度
則反應速率為-rA=Ae-Ea/RT[A]m[B]n(式5)
催化劑亦稱為觸媒其本身既不是反應物也不是產物,且反應前後本身組成不變,如(圖4)所示,觸媒本身可改變化學反應的反應途徑,並降低活化能進而提高整體反應速率。
圖4、觸媒與活化能關係圖[2]
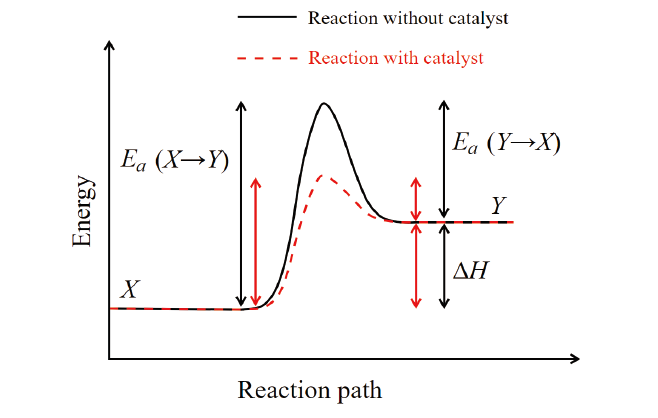
由上述化學反應動力學與觸媒反應及鹽酸去除過氧化氫反應機制,我們期望藉由少量鹽酸添加,降低過氧化氫分解之活化能,並提高反應初始溫度加快反應速度,並藉由一系列實驗找出最佳反應初始溫度及最少鹽酸添加量減少反應過程氯離子殘留,並提高整體反應速率,以達低濃度廢硫酸產酸品質提升之可行方案。
3. 研究方法
3.1 低濃度廢硫酸過氧化氫與鹽酸反應機制建立
本實驗方法主要以F15P3/4廠內WSR系統測試鹽酸添加量,由0.83Litter提高至40Litter對於鹽酸與過氧化氫整體反應行為分析,並藉由測量再生後硫酸氯離子殘留量來證明,於低濃度廢硫酸狀態下鹽酸與過氧化氫反應過程,氯離子是否可藉由形成氯氣逸散,進而找出鹽酸最大殘留量,並與文獻中探討之反應機制相互驗證。
3.2 不同溫度及濃度廢硫酸於定量鹽酸反應分析
本實驗方法主要藉由廠內系統前次產酸的餘溫,並藉由不同留底量,在反應總體積為5300Litter條件下分別以不留底、留底700L及1300L,作為達成改變下一批反應的起始溫度目的,並添加定量鹽酸,藉此探討硫酸溫度及濃度對於整體反應速率之影響。
4. 結果分析
4.1 低濃度廢硫酸過氧化氫與鹽酸反應機制
本章節藉由提高鹽酸加藥量,探討過氧化氫與鹽酸反應機制,並於46%硫酸濃度下分別做了四次實驗結果如昇溫曲線顯示(圖5)及殘留氯離子量測表(表2),由數據(實驗一)可得知當少量鹽酸添加量(0.83Litter)對於過氧化氫分解結果顯示,氯離子實際殘留量79ppm與計算結果75ppm幾乎相符合,顯示氯離子於低濃度廢硫酸反應,無法藉由形成氯氣達成逸散,最終完全殘留於硫酸溶液中。
圖5、WSR於不同鹽酸加藥量之升溫曲線
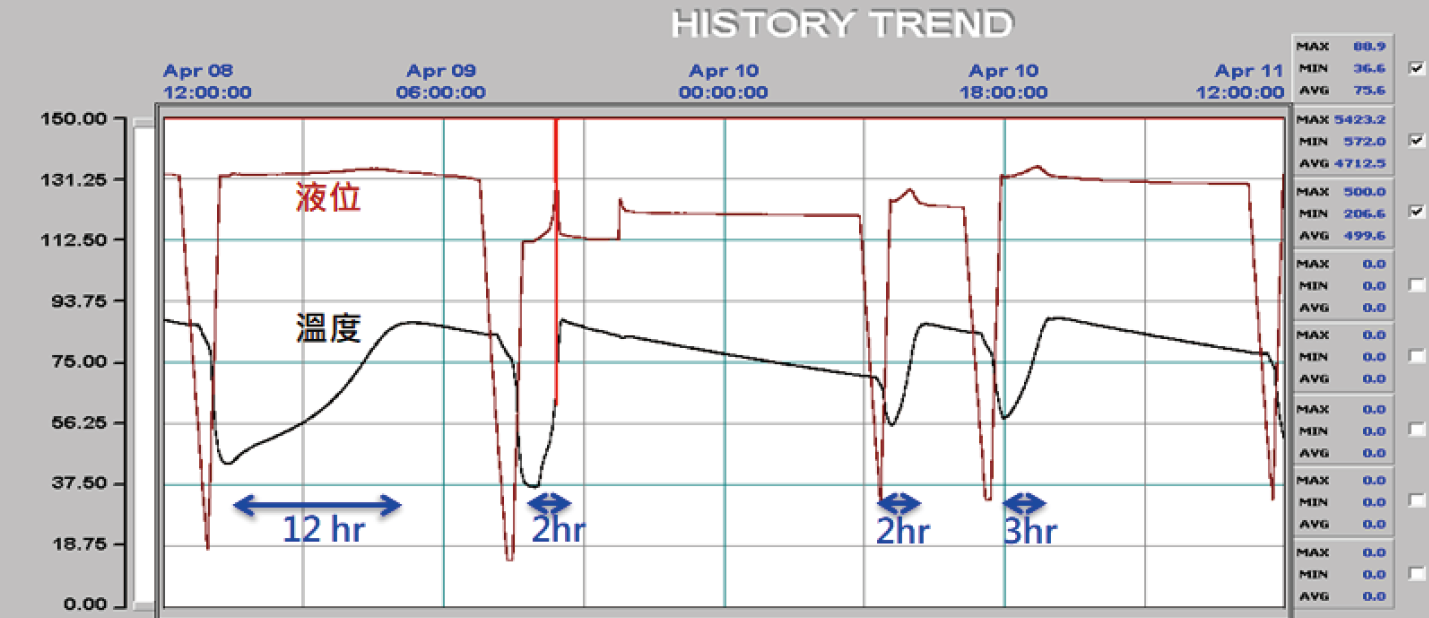
實驗 |
初始 H2O2 (%) |
前次留底量 (L) |
反應體積 (L) |
底溫 (°C) |
HCl 加藥量 (L) |
升溫時間 (hr) |
反應後 H2O2 (ppm) |
反應後Cl (ppm) |
預計殘留Cl (ppm) |
---|---|---|---|---|---|---|---|---|---|
1 | 4.5 | 700 | 5300 | 43.8 | 0.83 | 12 | 8.18 | 79 | 75 |
2 | 5.2 | NA | 4000 | 37.0 | 40 | 2 | 5.11 | 2400 | 3700 |
3 | 3.1 | 1300 | 5000 | 55.7 | 0 | 2 | 1.77 | 652 | 624 |
4 | 3.1 | 1300 | 5300 | 55.8 | 0 | 3 | 1.59 | 188 | 159 |
為了進一步確認氯離子無法形成氯氣原因是否是來自鹽酸添加量過少,導致分子間無法與生成物HOCl有效碰撞,減少反應機會,實驗中嘗試拉高40倍鹽酸添加量於反應中測試,結果(實驗二)顯示添加40Litter鹽酸於反應中,預期氯離子殘留量為3700ppm,但實際量測反應後氯離子濃度發現,殘留濃度僅存2400ppm,顯示當鹽酸添加量增加的情況下,氯離子會形成氯氣逸散,換算氯逸散率35%,由於反應後過氧化氫<10ppm,為了交叉驗證無法完全形成氯氣原因,探究是否因無過氧化氫分解可形成HOCl,因此導致此反應中止,實驗利用留底的方式,於實驗過程中添加新鮮酸重新參與反應,並無額外添加鹽酸,確認殘餘氯離子可否再次形成氯氣於溶液中移除,反應結果顯示氯離子殘留量為652ppm,與計算殘留量624ppm相符,再以相同方式,再次留底添加新鮮酸,反應結果氯離子殘留量為188ppm與計算殘留量155ppm同樣相符,此三次結果說明,若要於低濃度廢硫酸中將氯離子藉由形成氯氣去除,必須透過大量的鹽酸添加方可促進反應發生,但此添加量需大於2400ppm,換算鹽酸加藥量為25Litter,代表於46%廢硫酸溶液的反應中鹽酸最大殘留量為2400ppm,因此我們可以將反應機制分為2種模式如下所示。
H2O2+HCl→H2O+HOCl 式1
HOCl+HCl→H2O+Cl2 式2
HOCl+H2O2→H2O+HCl+O2 式3
H2O2→H2O+1/2 O2 式4
總反應式 : 3H2O2+HCl+HOCl→4H2O+Cl2+3/2 O2 氯離子>2400ppm
總反應式 : H2O2→H2O+1/2 O2 氯離子<2400ppm
雖然實驗確認了反應機制,其結果也符合文獻[1]所述,因此藉由大量鹽酸添加雖可產生氯氣逸散,但2400ppm的氯離子殘留量對於後段MD膜的運轉上產生非常大的運轉風險,因此並不適用於實廠運轉的操作條件,而由此結果也證實了低濃度廢硫酸於低鹽酸加藥量下,鹽酸參與反應行為等同觸媒催化效果,而增加觸媒量,確實會增快整體反應速率,但由於反應前後量體不便又無法透過其他方式於液相中分離,因此限制了整體反應效果。
由實驗結果(實驗一、四)結果比較,理論上過氧化氫濃度高,應當貢獻更多的熱能,以致反應加速,但可發現(實驗一)於低溫43.8°C到(實驗四)起始溫度55.8°C卻需額外增加3.5小時進行升溫反應,而(實驗四)卻僅需花費3小時即可達到反應最高溫,而由(實驗三、四)結果可得知,相同反應初始溫度及過氧化氫濃度條件下,氯離子濃度差異3.5倍,對於整體升溫反應時間只相差1小時,說明了起始溫度對於整體反應時間重要性遠大於鹽酸的添加量,因此4.2章節將針對不同反應起始溫度對於產酸時間影響進一步探討。
4.2 硫酸起始反應溫度及濃度對於反應速率影響
本小節主要藉由廢硫酸系統操作,以不同的硫酸留底量改變反應起始溫度,而起始溫度的選擇,主要依據廠內廢硫酸系統升溫曲線而來,由(圖6)中可發現廢硫酸升溫曲線主要有2個轉折點,分別為45°C及50°C,每個轉折點後,升溫斜率皆明顯加快,其原因當然來自於溫度升高,造成整體反應速率變快,但由曲線可以看出36°C到45°C需花費約4~6小時,而45°C到50°C需花費3~5小時,因此藉由拉高底溫來避免低溫升溫緩慢的情況,加快產酸速度可能為一可行方案,因系統本身並無加熱裝置,所以利用留底的方式來達到我們預期的初始溫度分別為留底700Litter及1300Litter。
圖6、WSR系統升溫曲線
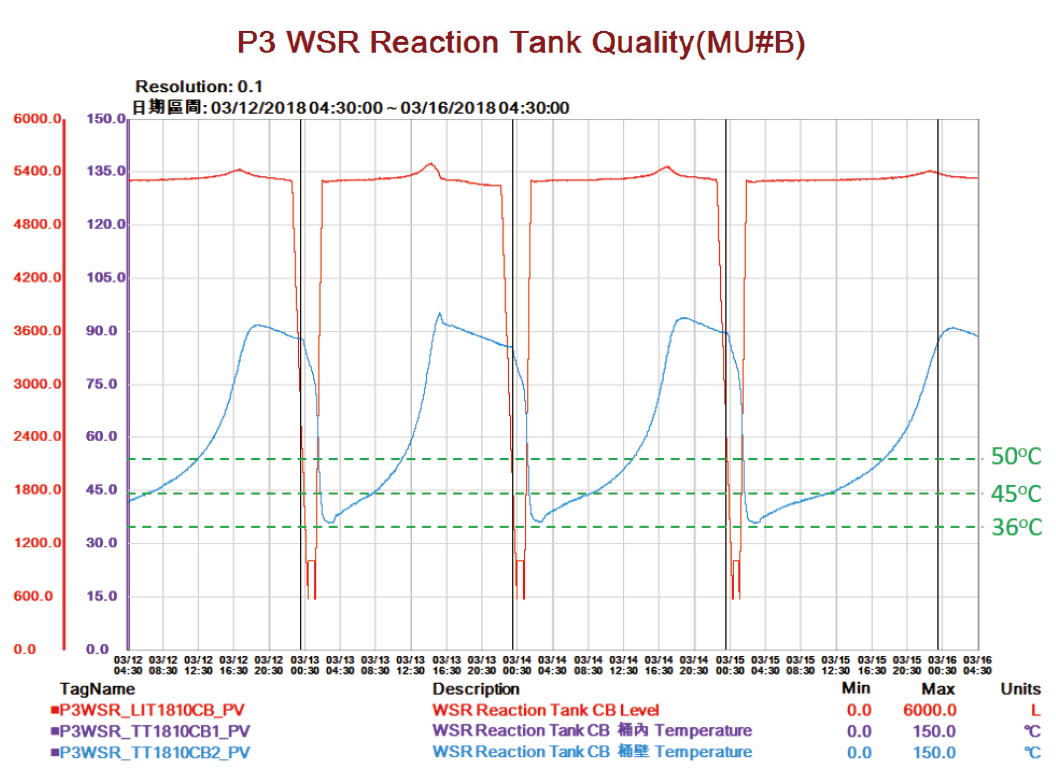
由於實驗是藉由廠內系統進行測試,因此無法將硫酸濃度固定進行比較,但我們仍可藉由相近濃度實驗進行比較及探討,由 表3中(實驗二、五)在硫酸濃度約47%的情況下進行比較,可發現藉由留底改變,將底溫由36°C提升至約44°C,整體反應時間由22小時縮短至16小時,與相較預期的4~6小時結果相符。由 表3中(實驗二、八)比較將底溫由36°C提升至50°C整體反應時間由22小時縮短至11小時,同樣符合預期縮短7~11小時,在不考慮廢硫酸的濃度情況下綜合整理,比較九次實驗的平均結果,說明初始溫度的提高能加快鹽酸分解過氧化氫的速度,且可提升整體產能達53.3%,有了這個實驗數據,也訂定了F15P3/4廠內現行的操作參數,透過留底的方式將初始溫度維持在50°C反應加速反應以符合廠內各系統用戶需求用量。
由 表3中(實驗一、二)結果得證,硫酸濃度對於整體反應時間的差異性,在相同反應條件下,當硫酸濃度由50%下降至45%的反應時間增加8小時,而 表3中(實驗四、六)硫酸濃度由49%下降至46%,反應時間延長了3小時,研判原因為酸的濃度下降,導致溶液中水的成份上升,由於水的比熱係數較大,造成系統升溫需花費更多的熱量,因此拉長整體的反應時間,但可發現初始溫度的提高可稍微彌補濃度上的差異。
實驗 |
初始 H2O2 (%) |
前次留底量 (L) |
反應體積 (L) |
底溫 (°C) |
HCl 加藥量 (L) |
反應時間 (hr) |
反應後 H2O2 (ppm) |
反應後Cl (ppm) |
硫酸濃度 (%) |
---|---|---|---|---|---|---|---|---|---|
1 | 5.8 | NA | 5300 | 35.6 | 0.8 | 21 | 2.1 | 52 | 50.0 |
2 | 5.8 | NA | 5300 | 36.2 | 0.8 | 22 | 2.9 | 70 | 47.0 |
3 | 5.8 | NA | 5300 | 35.6 | 0.8 | 29 | 5.9 | 65 | 45.3 |
4 | 4.6 | 700 | 5300 | 43.2 | 0.8 | 16 | 5.5 | 72 | 48.7 |
5 | 4.8 | 700 | 5300 | 43.6 | 0.8 | 16 | 2.1 | 68 | 46.8 |
6 | 4.8 | 700 | 5300 | 44.1 | 0.8 | 19 | 5.3 | 69 | 46.0 |
7 | 4.1 | 1300 | 5300 | 51.9 | 0.8 | 11 | 5.7 | 75 | 46.5 |
8 | 4.2 | 1300 | 5300 | 50.2 | 0.8 | 11 | 4.9 | 69 | 46.5 |
9 | 4.1 | 1300 | 5300 | 50.0 | 0.8 | 13 | 8.5 | 76 | 46.2 |
綜合以上實驗可得知,廢硫酸濃度是主要影響反應速率的重要因子,而透過拉高底溫的方式,確實可以加速反應速率,但由於廠內系統並無加熱裝置,因此若遇製程排放廢硫酸酸濃度較低之狀況,將延長低溫反應時間,同時影響到反應最高溫,由於實廠操作上是以其批次留底進行溫度拉升,若高溫過低將影響下一批次底溫,使底溫下降,起始溫度偏低將形成系統降溫的惡性循環,為避免此問題影響產能,若遇高溫過低情況,現行作法只能藉由拉高批次鹽酸加藥量,進而加速過氧化氫分解速度,以彌補因升溫過程中的熱散失,而得以維持相同的高溫,但同時帶來的副作用為氯離子殘留量提高,由於受溫度及濃度兩項因子相互牽制,導致WSR系統不穩定,無法全面以自動化加藥執行反應,因此若能將其中一項因子固定,即可將系統切回自動加藥模式,由於廢硫酸來源濃度受限於製程端,因此濃度無法控制,因此可藉由系統CIP增加熱源提供穩定的起始溫度,假設熱源穩定,即可以取消留底機制,並可增加單位時間產酸量,若以實驗數據換算單位產酸量(表4)可由現行的345Litter提升至454Litter/hr,使產能提升31.6%,若以原始設計量計算,則產能提升率可達100%,又因為取消留底機制,因此來源過氧化氫濃度可以提高,將可以增加反應的有效碰撞,再進一步減少鹽酸加藥量。
實驗 |
前次留底量 (L) |
反應體積 (L) |
產酸體積 (L) |
反應時間 (hr) |
單位時間產酸量 (L/hr) |
平均單位時間產酸量 (L/hr) |
產能提升率 (%) |
---|---|---|---|---|---|---|---|
1 | NA | 5300 | 5300 | 21 | 252 | 225 | - |
2 | NA | 5300 | 5300 | 22 | 241 | ||
3 | NA | 5300 | 5300 | 29 | 183 | ||
4 | 700 | 5300 | 4600 | 16 | 288 | 273 | 21.3 |
5 | 700 | 5300 | 4600 | 16 | 288 | ||
6 | 700 | 5300 | 4600 | 19 | 242 | ||
7 | 1300 | 5300 | 4000 | 11 | 364 | 345 | 53.3 |
8 | 1300 | 5300 | 4000 | 11 | 364 | ||
9 | 1300 | 5300 | 4000 | 13 | 308 |
因現行廠內運轉模式已達到系統產能最大化,由於廠內用量逐年上升(圖7)而F15P3/4仍持續進行裝機,若要再加快產能勢必得藉由更多的鹽酸添加加快反應,但氯離子殘留量將持續增加,而有了上述實驗數據的建立,提供外部能源確實為一可行方案,因此將於4.3章節將針對現行WSR系統改造設計與討論可行方案。
圖7、歷年廠內廢硫酸用量
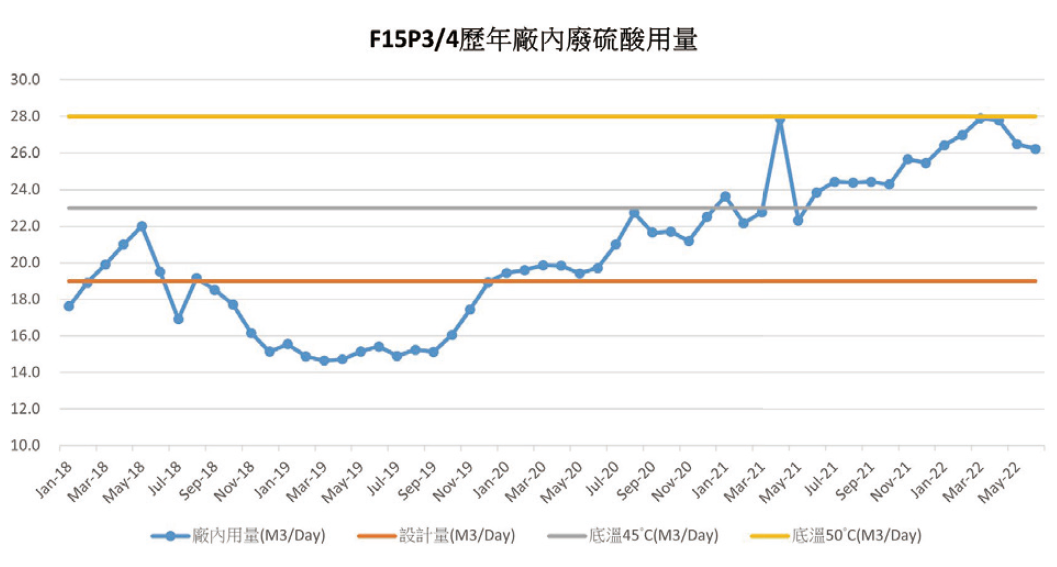
4.3 現行廠內WSR系統改造與流程分析
如4.2章節討論結果,若要改善低濃度廢硫酸氯離子殘留問題,提高反應初始溫度是一項可行辦法,但目前廠內廢硫酸系統並無外部熱源提供,因此需加設電熱水罐來作為昇溫熱源,本章節將以設備成本、操作成本及操作風險等指標比較兩個可行方案,方案一 : 系統熱交換器改造 ; 方案二 : 增設新熱交換器。
方案一 : 系統熱交換器改造,如(圖8、圖9)系統架構及流程圖,於WSR系統中有一條路徑可經過熱交換器,並回到本身反應槽,紅色路徑(圖8),此路徑的用途是當系統異常升溫、GMS作動、高溫冷卻、熱交換器沖洗及產酸壓力過高所使用之路徑,因此我們可利用此路徑於系統補酸完成後,將熱交換器冷卻水來源切換至熱水罐來進行廢硫酸的預熱升溫,根據廠內熱交換器的設計量若要將廢硫酸由36°C升溫至50°C至少需花費1小時,而此作法在設備成本上雖少了新熱交換器初設成本,但卻面臨較大的運轉風險,以下將列出3點分析 : ①熱交換器水側長時間冷熱交替,將減少熱交換器使用年限;②若在預熱升溫過程遇到系統異常降溫,冷熱水將同時接觸降低降溫效率;③升溫路徑連結產酸路徑,若遇產酸閥件異常狀況,將造成含有高濃度雙氧水硫酸直接進入成品槽,影響後段MD系統。
圖8、WSR系統架構圖
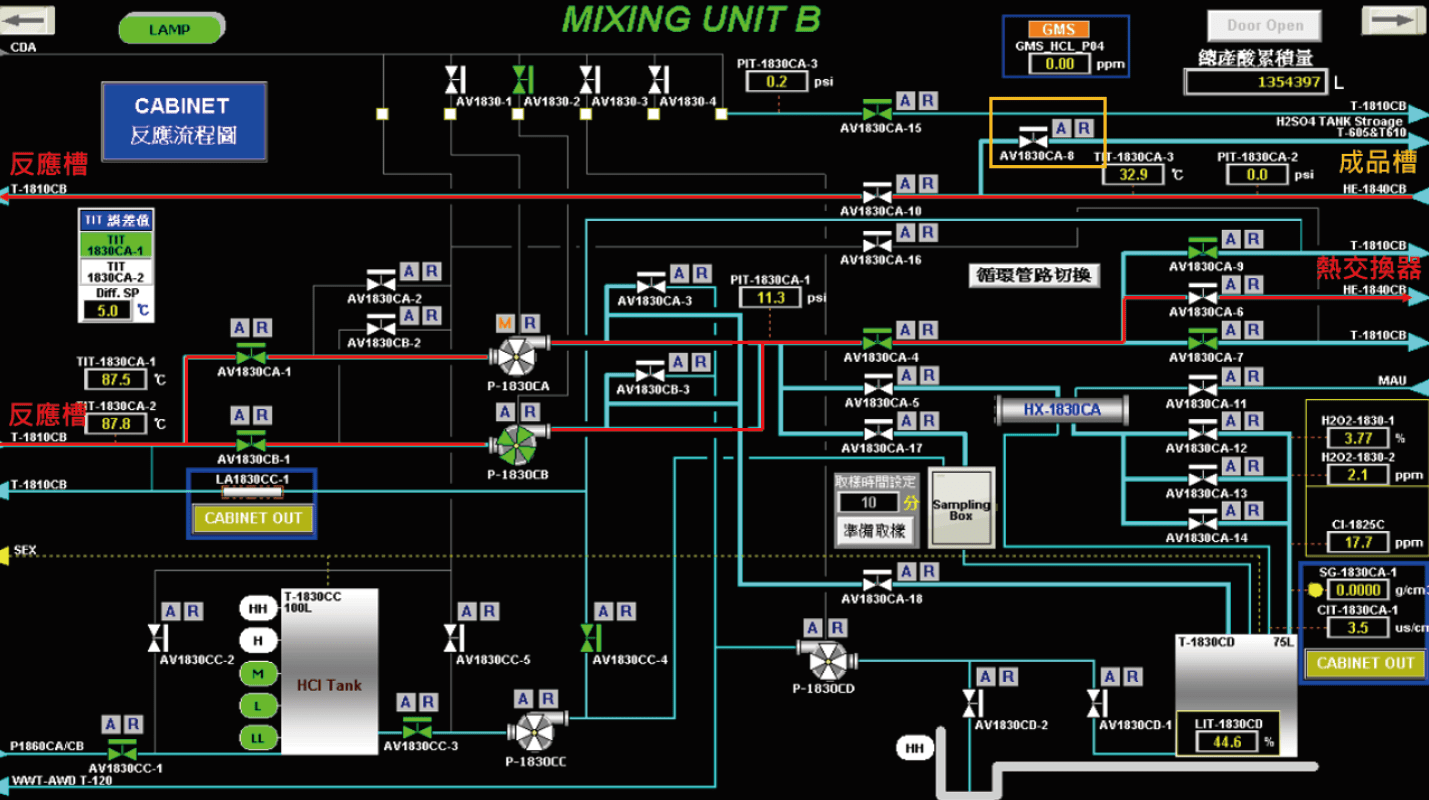
圖9、WSR系統流程圖
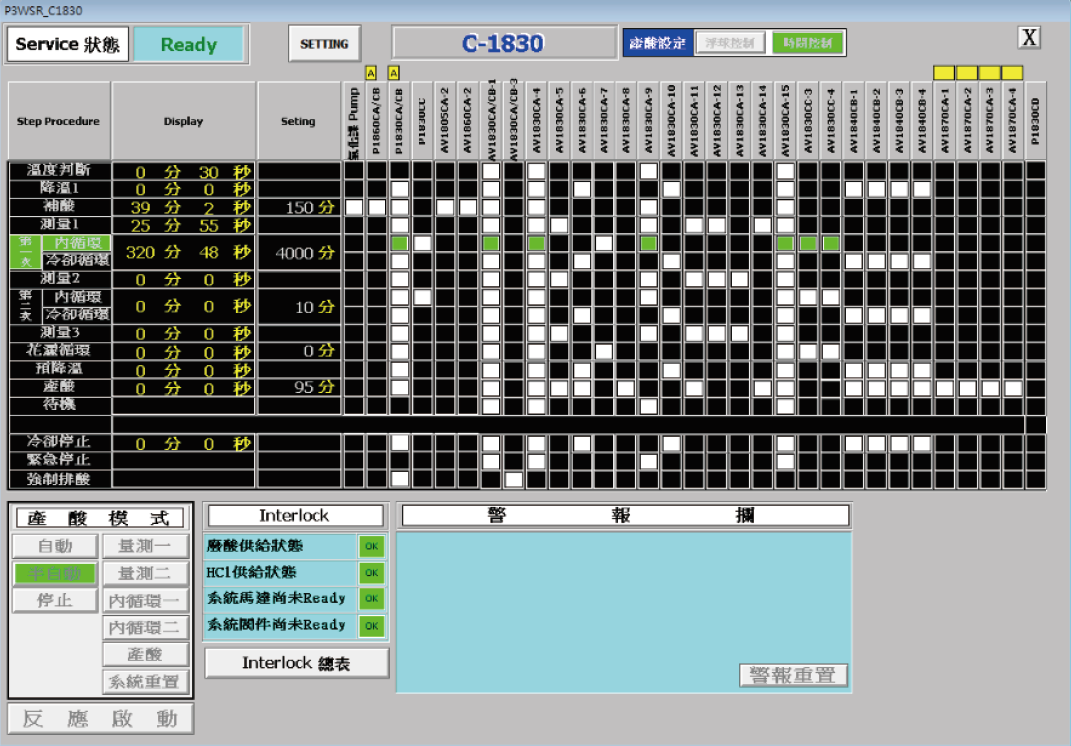
方案二 : 增設熱交換器,雖然熱交換器初設成本較高,但由系統架構及流程圖發現系統初始補酸,達操作液位共需花費約40分鐘,因此若將此時間同時利用於預升溫過程,勢必將可直接提升系統產能,此方式對於系統現行流程操作,只需透過進酸閥件切換並可達成此目的,而系統其餘Interlock機制,則可保持原系統設定無需變動,且與產酸路徑並無連結,減少污染風險。因熱交換器為外掛型式,若遇熱交換器異常,亦可將系統回復到原始操作模式,此舉可望大幅提升運轉靈活度。
綜合以上所述,將兩個方案進行比較,結果如(表5)所示,雖然增設新熱交換器的初始設備及維護成本相對昂貴,但對於後續操作及運轉風險相對較低,且系統本身可操作的靈活度也因此大幅提升,因此(方案二)對於實務運轉屬較佳的選擇。
方案— : 熱交換器改造 |
方案二 : 增設熱交換器 |
|
---|---|---|
設備成本 |
低 |
高 |
維護成本 |
低 |
高 |
操作難度 |
高 |
低 |
運轉風險 |
高 |
中等 |
系統產能 |
中等 |
高 |
系統可靠度 |
低 |
高 |
5. 結論與未來展望
鹽酸法於廢硫酸去除過氧化氫反應中,硫酸濃度扮演重要的角色,在高濃度廢硫酸(>55%)的反應中,鹽酸是以反應物的角色參與反應,並可透過形成氯氣逸散降低氯離子的殘留,因此可透過大量的鹽酸添加,加速反應 ; 而在低濃度廢硫酸(<55%)的反應中鹽酸反應角色則可分為反應物及觸媒,但由於低濃度廢硫酸對於鹽酸的溶解度高,因此添加量需大於2400ppm,鹽酸方可藉由形成氯氣型態逸散,進一步造成氯離子殘留量過高,因此無法以添加大量鹽酸促使反應加速進行。
於低濃度廢硫酸提高反應的初始溫度,可以有效加速鹽酸分解過氧化氫的能力,以F15P3/4 WSR系統操作方式,透過前一批次廢硫酸餘溫與新酸結合,可有效將反應初始溫度提高至50°C並加快反應的進行,將整體產能提高53%,但此操作方式仍受來源濃度影響,根據實驗結果,硫酸濃度下降1%,將影響整體反應時間達2~3小時,為了維持產能,只能透過提高鹽酸加藥量,維持反應速度,進而造成氯離子殘留量提高。
參照低濃度廢硫酸實驗結果,過氧化氫濃度的高低,並非影響整體反應時間的因素,而是來源硫酸濃度及反應初始溫度,因來源濃度的不均一性,進而導致留底的操作模式,使初始反應溫度不穩定,因此透過增加外部熱源進行反應初始溫度的控制,為可行之方案,而由現行廠內WSR系統評估改善方式,新增熱交換器及電熱水罐的方案,對於未來系統的操作及運轉皆有較低的風險且可維持原系統設計,因此未來可藉由此方式提升低濃度廢硫酸回收效率及供酸品質的優化。
參考文獻
- Lyn R.Watson , Jane M.Van Doren,et al. Uptake of HCl Molecules by Aqueous Sulfuric Droplets as a Function of Acid Concentration. Journal of Geophysical Research, Vol.95, NO. 5, AGES 5631-5638, April 20, 1990.
- 維基百科https://zh.m.wikipedia.org/zhtw/%E5%82%AC%E5%8C%96%E5%89%82
留言(0)