摘要
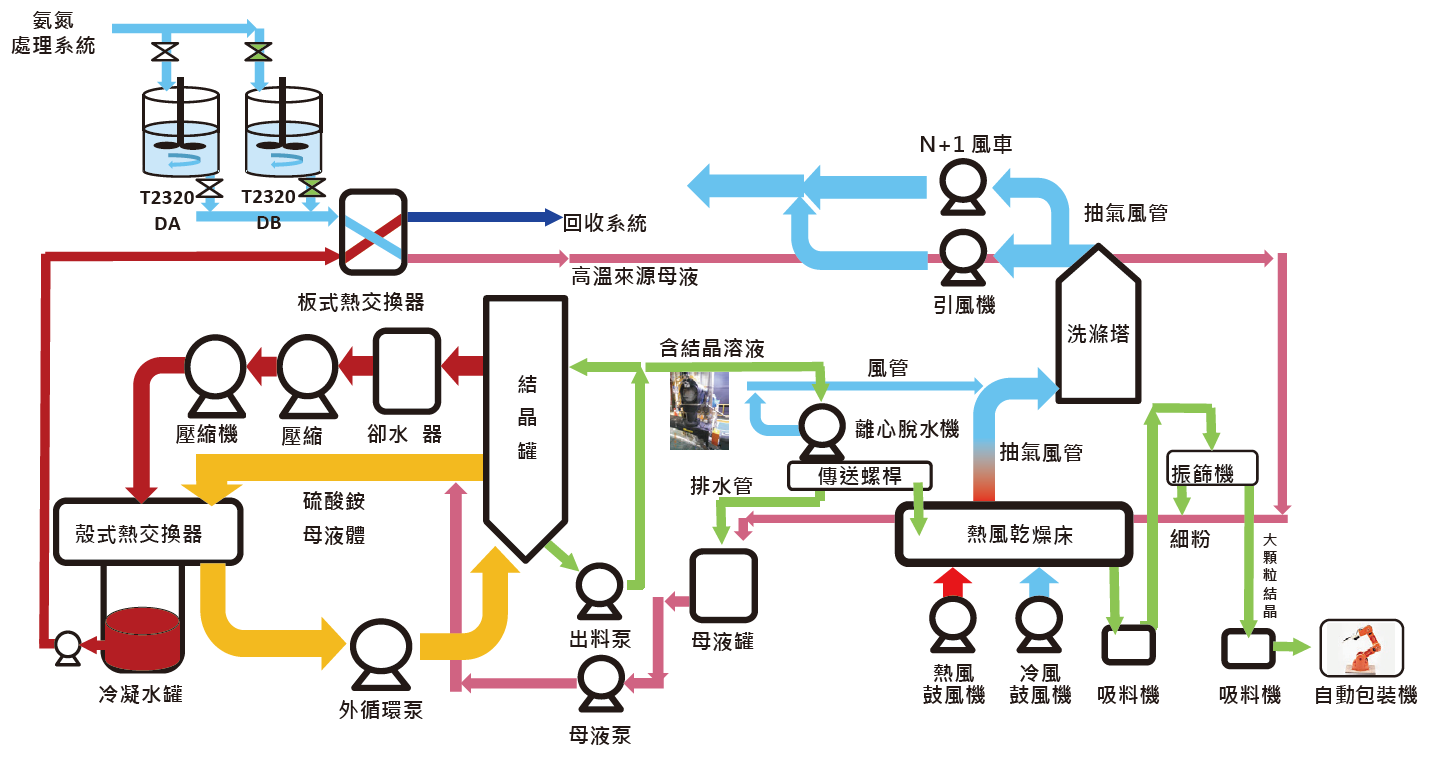
硫酸銨乾燥系統運轉實務與維護保養
前言
隨結晶蒸發系統運行時間增加,蒸發罐內部溶液雜質成份逐漸累積,導致沸點上升,使系統蒸發效能下降,為此原廠設計定量高濃度廢液排放,避免金屬離子與Cl-成份累積,以維持結晶罐內溶液濃度動態平衡,然而該股高濃度排放廢液中,金屬離子及Cl-濃度偏高,因此進入廠內氨氮處理系統進行氨氮處理,亦須考量氨氮處理系統運轉裕度及氨氮去除效率變化、脫氣膜壽命等問題,參考國內石化業者經驗,則是以小型結晶系統製成次級產品,最終以氨氮處理系統或委外廠商,進行高濃度廢液處理。
文獻探討
實地走訪國內化工業者硫酸銨乾燥系統實績,系統建置於半開放式建物內,其中一系統以緩衝槽作為來源水質調勻,調整機制為氨水加藥,參考操作pH區間為2.5~6,以OSLO(奧氏魯)結晶罐作為蒸發技術核心,由於結晶罐尺寸較大,因此有助於結晶顆粒成長,產品粒徑可達2mm以上(圖1),該廠每日以三班制進行輪班生產,每個班分別進行清洗保養工作,屬批次性生產[1](恆宜化工2018)。
圖1、恆宜化工實績現勘
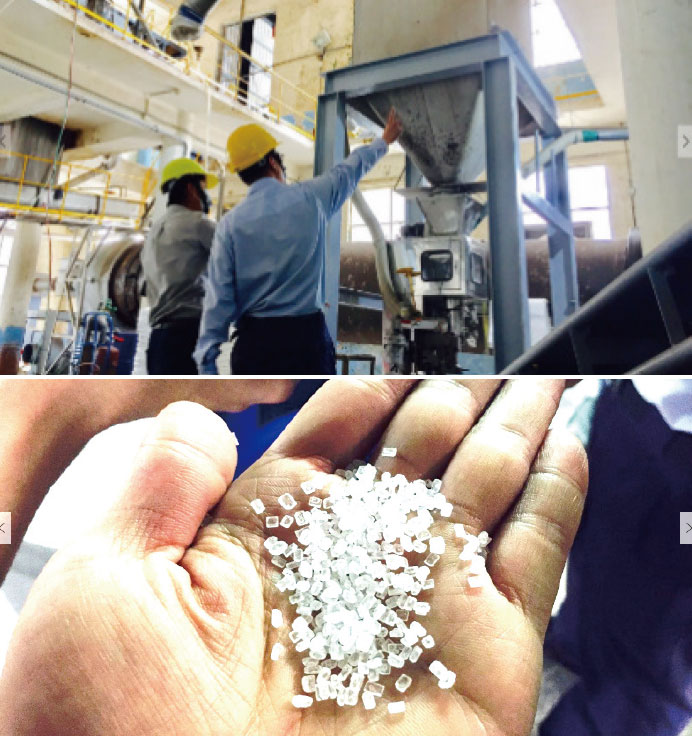
另一實績為DTB(Draft tube baffle)結晶罐作為蒸發系統,將來源硫酸銨pH調整至4,運轉過程中高濃度廢液排放pH調整至11,進入超重力旋轉床,將氨氣脫附後,以硫酸透過洗滌塔將氨氣吸附,再將該股硫酸銨輸送至另一套結晶系統,製成乾燥產品,最終含雜質量較多之高濃度廢液體則委外處理[2](中石化2019)。
據悉,國內外石化業者皆以此形式半開放建物構築結晶蒸發系統,周遭環境及設備皆有腐蝕現象(圖2),台積首套於2018年首度進行硫酸銨乾燥系統建置模廠,將結合工業製程與半導體廠房,參考上述業者經驗,將結晶蒸發系統建置於室內空間除了需考量廠房室內空間與潔淨度需求 ,尚需選用抗腐蝕材質或塗層保護設備單元,由於樓層高度限制結晶罐尺寸大小,影響結晶產品粒徑,生產過程中產生粉塵,於潔淨度要求較高之室內廠房,須將粉塵抑制列入設計考量。
圖2、國內化工業者硫酸銨乾燥系統
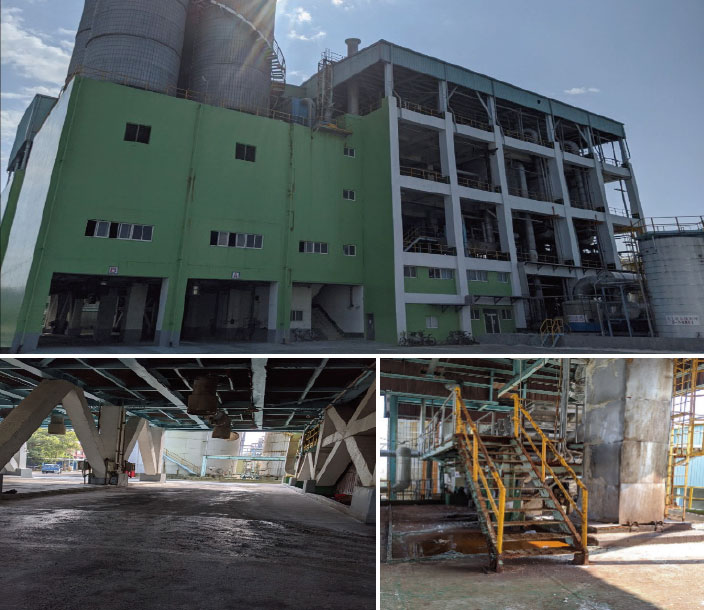
結晶成品產量高低影響結晶產品品質,出料量多寡視含晶量高低調整,含晶量以比重計測定,設定值約1250~ 1650Kg/m3之間,可以儀器或取樣測定,pH值高低亦影響結晶品質,pH值低結晶成現細小針狀[3](毛國芳1992),低pH值且高Cl-狀態,易使金屬發生腐蝕,因此建議入料操作條件pH設定4,Cl-入料濃度控制<50ppm[4](GEA 2019)。
研究方法
將無塵室生產線排放含氨廢液,與工廠回收硫酸進行吸附結合,製成約25%~30%液態硫酸銨,再將該股液態硫酸銨導入乾燥系統進行提濃固化處理 ; 硫酸銨乾燥系統包含前段蒸發設備,以串級設計蒸氣壓縮機輔助,作為系統熱源提供,達成升溫蒸發效果,蒸發後母液濃度提升,符合40%~50%濃度條件後,過飽和溶液內晶體析出,較大晶體沉澱至結晶罐底部,以出料泵將含固成份過飽和溶液輸送至中段離心脫水機進行固液分離,使含水率下降至3~8%,接著進入後段乾燥設備去除殘餘水份,最終以物料傳輸設備傳送至自動化包裝系統、自動成品疊棧儲存,為一完整硫酸銨乾燥系統流程(圖3)。
圖3、硫酸銨乾燥系統BFD
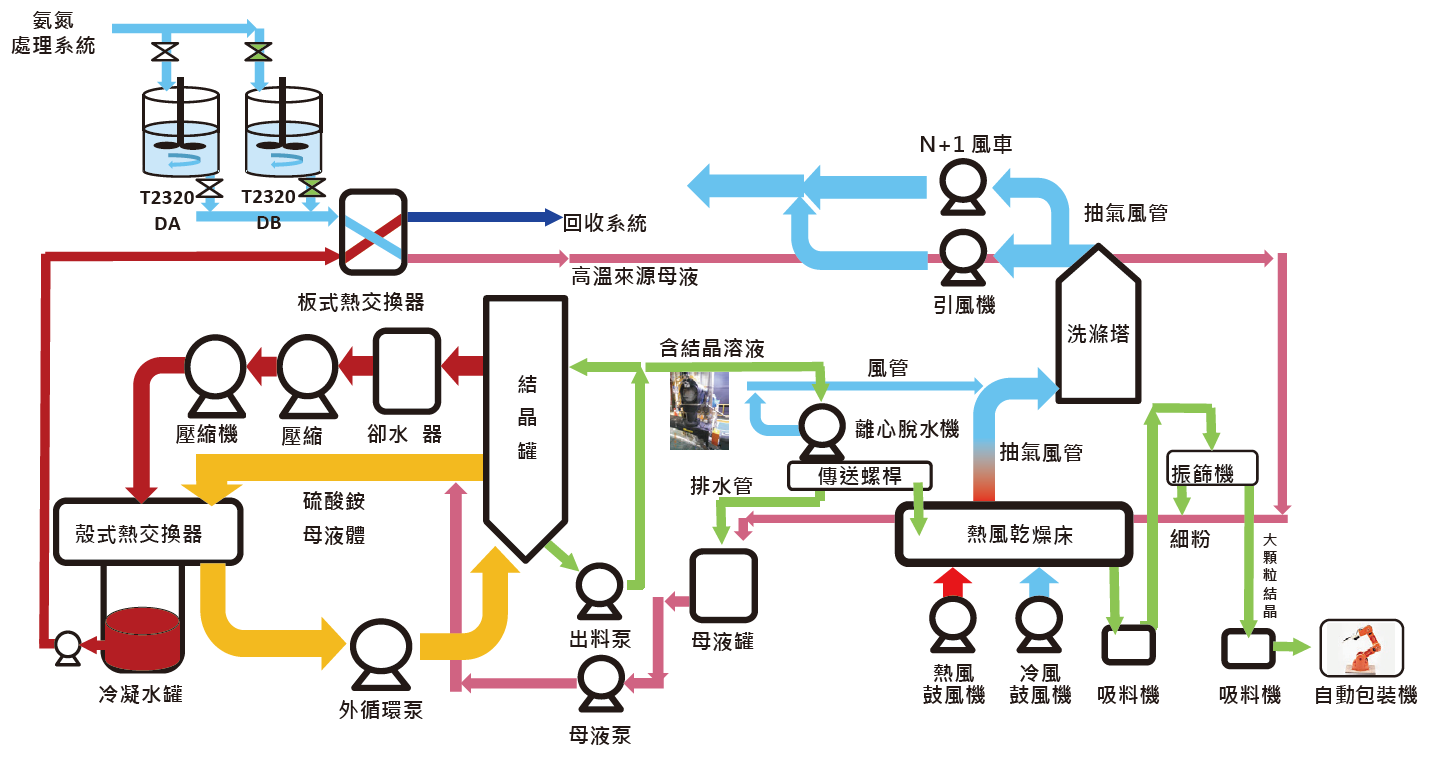
3.1操作參數
3.1.1 結晶蒸發罐/壓縮機
結晶系統啟機前以板式熱交換器進行系統升溫循環,當母液溫度提升至攝氏85度(純水於578mbar絕對壓力下,飽和蒸汽溫度),啟動真空系統,將系統壓力下降達運轉條件(400~600mbar),系統即開始產生蒸氣,由冷凝水罐視窗可目視觀察液體表面水份蒸發現象,此時啟動蒸氣壓縮機,緩慢昇載至最低運轉速度,啟機過程需特別注意共振頻率,如震動值過高,應盡速昇載壓縮機葉輪轉速,避開該共振頻率(震動值SPEC<12um/s),避免壓縮機結構損壞 ,啟機需特別注意,當轉速提升過程來源蒸氣溫度不斷上升,需密集檢視壓縮機殼體溫度,當該溫度>85度狀況,表示壓縮機吸入端開始產生過熱蒸氣,此時需開啟壓縮機葉輪噴淋水由0.4LPM開始緩慢增加,每次約增大0.05LPM ,該股噴淋水使過熱蒸氣轉換為飽和蒸汽,作為蒸氣壓縮機加壓後熱能傳遞至強制熱交換器介質,達成換熱昇溫效果,本案以PILLER A250壓縮機串聯設計,參考原廠操作手冊需特別注意,最終壓縮機出口溫度不得超過125度,該條件將觸發系統停機,於操作同時須特別注意,當飽和蒸汽壓溫度大於117度狀況下,溫度每上升一度,需同步增大噴淋水量0.05LPM,避免高溫觸發停機聯鎖條件,由於系統啟機過程抽取大量真空,造成系統熱散失,因此啟機條件須持續觀察至結晶罐內部液體溫度開始回升,方為啟機成功條件。
隨結晶罐內濃度不斷提升,可由出料泵出口科氏流量計做為結晶罐內母液密度判斷依據,當比重達1258Kg/m3為結晶發生成核之轉折點,經驗表示出料密度設定1330~ 1420Kg/m3,如需長時間停機,須將結晶顆粒排空,使結晶罐內密度控制於較低範圍,避免結晶顆粒析出,達成此條件後,方可切換升溫內循環模式,避免結晶罐溫度下降 、晶體析出,影響系統復機時間,根據原廠技師經驗表示( 密度<1258Kg/m3)低濃度啟機溫度條件為85度,(密度>1258Kg/m3)高濃度啟機溫度為88度,如此條件限制,方可確保壓縮機運轉過程母液內水份於對應500mbar大氣壓真空度下穩定產生蒸氣,做為系統循環,達成熱能再利用 ,以確保壓縮機做功於適當運轉範圍。
3.1.2 離心脫水機
推進式離心脫水機是由兩具外部轉動馬達分別帶動轉動濾籠與推進機構為主要元件所組成,當物料進入離心脫水機,將由物料分配盤均勻使含晶溶液分送至濾籠內側,利用離心脫水原理,將固體與液體進行分離,於濾籠內部表面形成濾餅,再由內濾籠往復動作將濾餅逐步往外推送至落料口,完成脫水動作(圖4),其中濾籠於運轉一段時間後,將開始發生堵塞(圖6),導致濾籠內液態物料無法充分脫除,使產出物料含水率上升,因此需視物料特性調整清洗濾籠時間,本案運轉參數以比重1340~1400Kg/m3高濃度硫酸銨溶液,來源液體流量約3.2~3.5CMH作為入料條件(圖3),入料前需經過水旋風分離器做為預增稠功能,使來源固液比由30%上升至55%,為最佳入料條件,產出成品初期含水率<1%,當運轉50分鐘後產出物料含水率將上升至大於1%以上,此時需將來源溶液切換去向,回流至結晶罐,並進行閥件、管路及離心機濾籠清洗,維持約60~120秒(圖5),使濾籠恢復較佳固液分離效能(圖7)。
圖4、離心脫水機入料
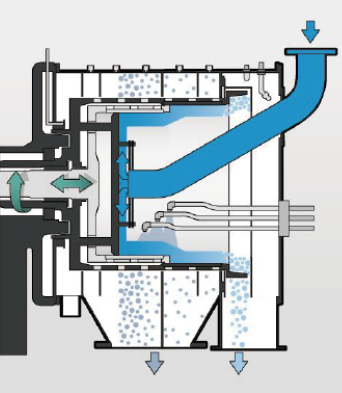
圖5、離心脫水機清洗
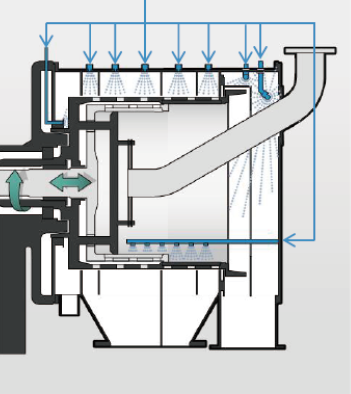
圖6、離心脫水機清洗前
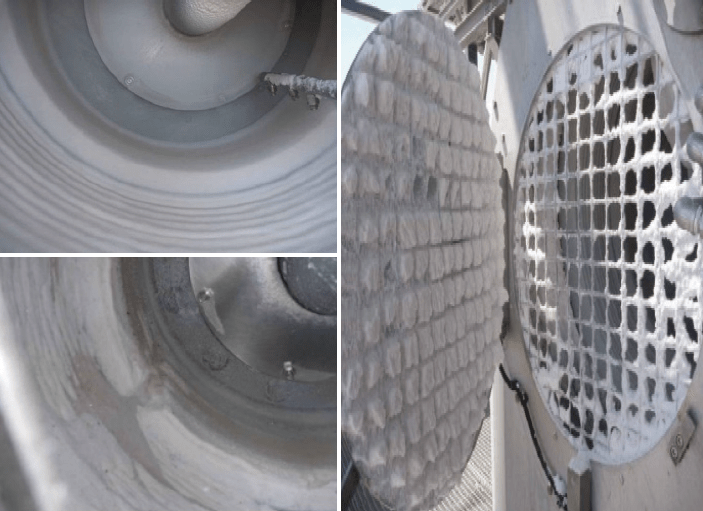
圖7、離心脫水機清洗後
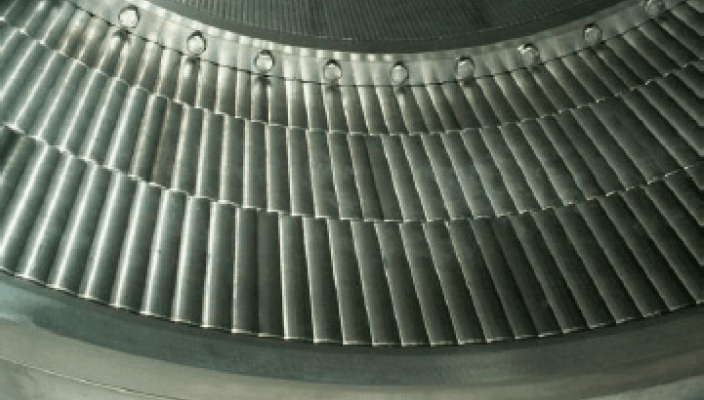
3.1.3 採樣機制,參數管理
由運轉數據得知系統蒸發效能與結晶蒸發罐內母液溫度關係密不可分,當溫度下降,將使產能下降,然而影響系統溫度其中因素為結晶罐內部雜質濃度,該濃度多寡直接影響液體溫度傳遞,經驗表示,雜質含量成份高,系統升溫效果較差 ,易導致結晶罐溫度下降,進而影響蒸發量(系統產能),因此針對各項離子濃度進行採樣分析,追蹤結晶罐內濃度變化,如氯離子、鐵離子、鈉離子皆為影響蒸發效能重要指標,應訂定取樣機制及管理標準,追蹤系統內部離子濃度,作為系統健康度監控依據(表1)。
日期 |
9月7日 |
9月7日 |
9月7日 |
日期 |
9月7日 |
9月17日 |
9月22日 |
10月5日 |
10月6日 |
10月15日 |
11月2日 |
11月9日 |
11月16日 |
---|---|---|---|---|---|---|---|---|---|---|---|---|---|
來源桶槽 |
P1/2 外運槽 |
P3/4 外運槽 |
混合中繼槽 |
週別 |
W038 |
W039 |
W040 |
W041 |
W041 |
W042 |
W045 |
W046 |
W047 |
每日減廢產能(>70) |
63 |
76 |
80 |
72 |
80 |
72 |
68 |
64 |
74 |
||||
結晶罐溫度(86~89) |
85 |
88~90 |
88~90 |
86~88 |
86~88 |
86~88 |
84 |
82 |
89 |
||||
壓縮機轉速(3200~3400) |
3350 |
3320 |
3350 |
3300 |
3300 |
3300 |
3350 |
3350 |
3320 |
||||
PH |
3.4 |
2.8 |
3.1 |
T1670 PH(3~4) |
3.2 |
3.2 |
3.2 |
3.2 |
3.2 |
2.97 |
3.4 |
3.4 |
3.2 |
比重 |
1.1667 |
1.1269 |
1.1501 |
T2320 PH(3.5~4) |
3.7 |
3.7 |
3.5 |
2.6 |
2.6 |
3.23 |
4.2 |
4 |
4.1 |
COD |
230 |
198 |
268 |
結晶罐內PH(2.5~4) |
2 |
2 |
1.7 |
1.7 |
2 |
2.1 |
1.7 |
1.5 |
1.6 |
CL- |
0 |
94.9 |
11.1 |
結晶罐內CL-離子濃度(<700) |
877 |
334 |
790 |
944 |
456 |
441 |
950 |
1620 |
400 |
Na |
309 |
2410 |
1610 |
結晶罐內鈉離子濃度(<50000) |
51100 |
12300 |
12000 |
20200 |
5250 |
3290 |
10000 |
8000 |
8200 |
Fe |
0.2 |
0.9 |
0.8 |
結晶罐內鐵離子濃度 |
2.5 |
1.3 |
2.5 |
4.88 |
1.37 |
3.8 |
2 |
15 |
4 |
(NH4)SO4% |
20.5 |
16.1 |
23.8 |
每日濃排量(>100L/HR) |
0 |
100L/HR |
100L/HR |
100L/HR |
100L/HR |
100L/HR |
100L/HR |
100L/HR |
150L/HR |
Ni |
0.5 |
0.7 |
0.7 |
結晶罐濃排指標比重(<1.3) |
1.31 |
1.28 |
1.28 |
1.29 |
1.29 |
1.28 |
1.28 |
1.28 |
1.28 |
由實際運轉數據得知,當離子濃度大量累積,可藉由高濃度硫酸銨液體外排量調節,使結晶罐內母液離子濃度得到控制,增大高濃度(母液罐外排濃度約35~38%)硫酸銨外排流量100L/hr為150L/hr,可觀察到離子濃度回穩(表1) ,屆時強制熱交換器之熱交換效果恢復,結晶蒸發罐內液體溫度回升,系統蒸發效能回升至基準值。本案於氨氮處理系統進行pH循環終點調整,操作條件為pH3~4,易使顆粒長成粒狀,pH偏低時成品呈針狀外觀(圖8)。
圖8、針狀/粒狀成品
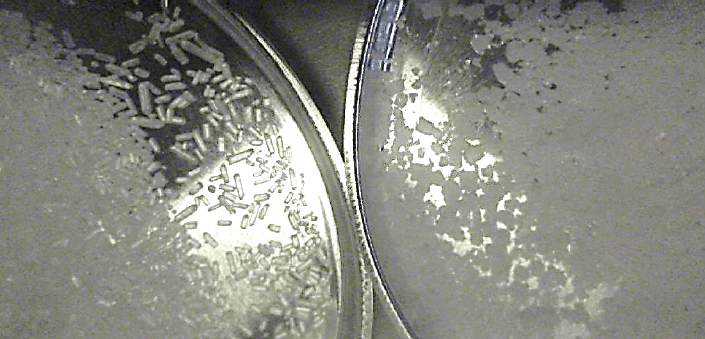
3.1.4 產品取樣
產品每日需取樣測量含水率(含水率<1%) 。
粒徑分布以每日取樣三筆平均計算,粒徑>0.5mm佔比98%(圖9)。
圖9、粒徑分布取樣分析
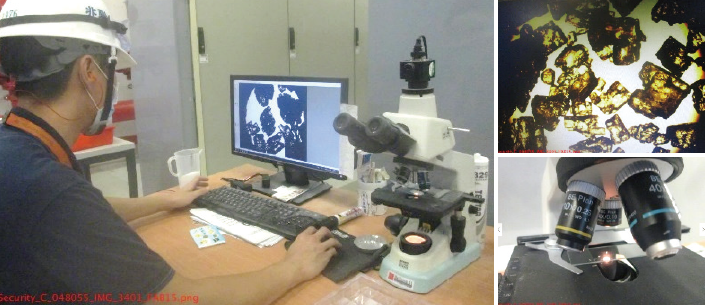
3.1.5 實驗數據
pH2.5逐步調升至3.5,觀察顆粒由細長針狀變化為等邊顆粒狀(圖10)
圖10、產品粒徑變化
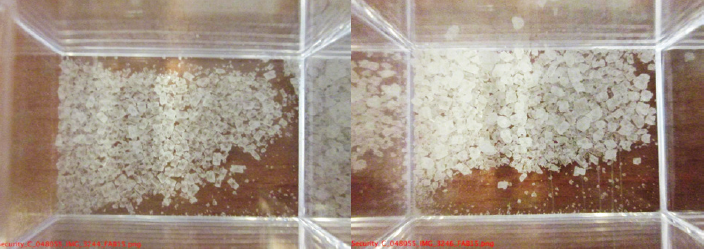
>2.7MM顆粒比例增加(表2)。
5月4日 |
5月5日 |
5月8日 |
5月11 日 |
5月13日 |
5月14日 |
5月15日 |
5月18日 |
5月20日 |
5月21日 |
5月25日 |
5月26日 |
5月27日 |
5月28日 |
5月29日 |
|
---|---|---|---|---|---|---|---|---|---|---|---|---|---|---|---|
PH |
2.62 |
2.34 |
3.02 |
2.8 |
2.92 |
3.16 |
3.04 |
2.9 |
2.74 |
2.45 |
3.1 |
3.11 |
3.22 |
3.47 |
3.4 |
<0.5mm(%) |
0.3 |
0.4 |
0.45 |
1.11 |
0.51 |
0.51 |
0.7 |
0.76 |
1.09 |
1.35 |
1.4 |
1.34 |
1.35 |
1.38 |
1.56 |
0.5~2.7mm (%) |
73.6 |
99.6 |
99.55 |
98.89 |
92.18 |
82.18 |
82.01 |
84.45 |
84.57 |
85.83 |
80.2 |
80.6 |
80.63 |
80.61 |
82.19 |
>2.7mm(%) |
26.1 |
0 |
0 |
0 |
17.31 |
17.31 |
17.29 |
14.79 |
14.2 |
12.82 |
18.39 |
18.05 |
18.02 |
18.01 |
16.25 |
3.2保養維護
結晶主系統運轉維護
高濃度硫酸銨位於系統內,長時間無運轉,氨離子轉換為氨氣逸散,負壓抽氣裝置將氨氣抽離後,系統內溶液pH逐漸下降 :
- 硫酸銨解離方程式 : (NH4)2SO4 ↔ 2NH4++SO42-
- 氨離子解離方程式:NH4+ ↔ NH3(gas)+H+
當exhaust持續抽氣時,會有NH3被移除,根據亨利定律,較容易破壞氣體液體平衡。另一個原因為勒沙特略原理,當NH3被移除時,為了達到平衡,會有更多的NH4+解離成NH3+與H+,使溶液內pH下降,因此原廠建議,進料pH需為3.5~4.5,如停機時間大於三日,必須將管路排空並完成清洗,避免pH持續下降,造成設備腐蝕。
3.3故障排除
當系統發生異常狀況,短時間內(<1小時)無法持續生產,需進行壓縮機停機操作,避免系統濃度持續上升,導致固成份過多,使系統高濃度管路堵塞,然而壓縮機停機操作將使系統喪失熱源補充,進而使系統內母液溫度下降 ,使壓縮機無法於短時間內恢復啟機,因此異常停機需關閉真空系統,避免系統內熱能抽散失,如需長時間停機(>2小時),則需將系統內固成份排空,或將系統導入高溫母液或熱水進行稀釋,使系統濃度下降,避免顆粒持續循環、碰撞增長而引發管路堵塞問題。
將結晶罐底部高濃度出料管路切換為塔體上半部澄清液,將該股母液導入板熱,以電熱水罐高溫入水透過板熱進行換熱,保持結晶系統內液體高溫狀態,如此方可快速恢復壓縮機運轉及生產作業,然而切換管路需注意避免含晶母液進入板熱,易造成堵塞,因此需擬定管路清洗流程 ,執行管路沖洗後方可進行循環路徑切換工作,閥件均需導入沖洗水進行清洗後方可關閉,操作人員執行手動清洗步驟亦為訓練重點。
管路疏通
如管路發生堵塞,建議以高壓熱水(壓力3.5Kg以上,溫度>60度)進行推送疏通,如仍無法排除堵塞,須以熱水入水並由另一側排水以換水稀釋方式疏通,或以較小管徑軟管導入稀釋水進行穿管方式,逐步稀釋推進 ; 高濃管路建置階段盡可能截彎取直,直管每5米設計清洗PORT,管路彎頭增設清洗PORT,於物料堵塞時可加快疏通效率。
結論與建議
4.1主系統參數監測
於結晶罐真空度為400~600mbar條件下,硫酸銨母液建議操作溫度適當範圍為86~93度,取水檢測母液金屬離子濃度與運轉後濃縮倍率可觀察到(圖11),鈉離子佔雜質最大宗,且雜質累積與結晶罐內循環比重上升成正比關係,但與產能為反比關係,觀察運轉數據得知,鈉離子於系統運轉生產開始一週後,濃縮倍率達20倍,系統效能由70 CMD下降為63CMD(表1) ; 其中氯離子與pH值則為系統健康度首重監測指標,過低pH及過高的氯離子濃度將使系統發生腐蝕,由取樣數據可觀察到腐蝕現象發生時,將伴隨鐵離子濃度上升現象(圖11),屆時需增大系統高濃度液體排放量,以降低溶液內氯離子濃度,而鐵離子上升須盡速檢視各項運轉單元狀況是否良好,如攪拌機扇葉、泵浦機械軸封等元件較易發生腐蝕與洩漏問題,綜合以上兩點,固定之高濃度雜質廢液排放或委外清運處理,必須列入運轉參數管理重點項目,以維持系統動態平衡,然而將該高濃度廢液排放至氨氮處理系統亦須考量鐵離子與氯離子濃度 ,避免影響氨氮系統脫氣膜壽命,建議每週取水檢測系統濃度變化分析,如數據異常需停機進行高濃度廢液排放或委外清運處理,方可確保系統效能及設備單元壽命。
圖11、結晶罐內母液金屬離子濃度變化
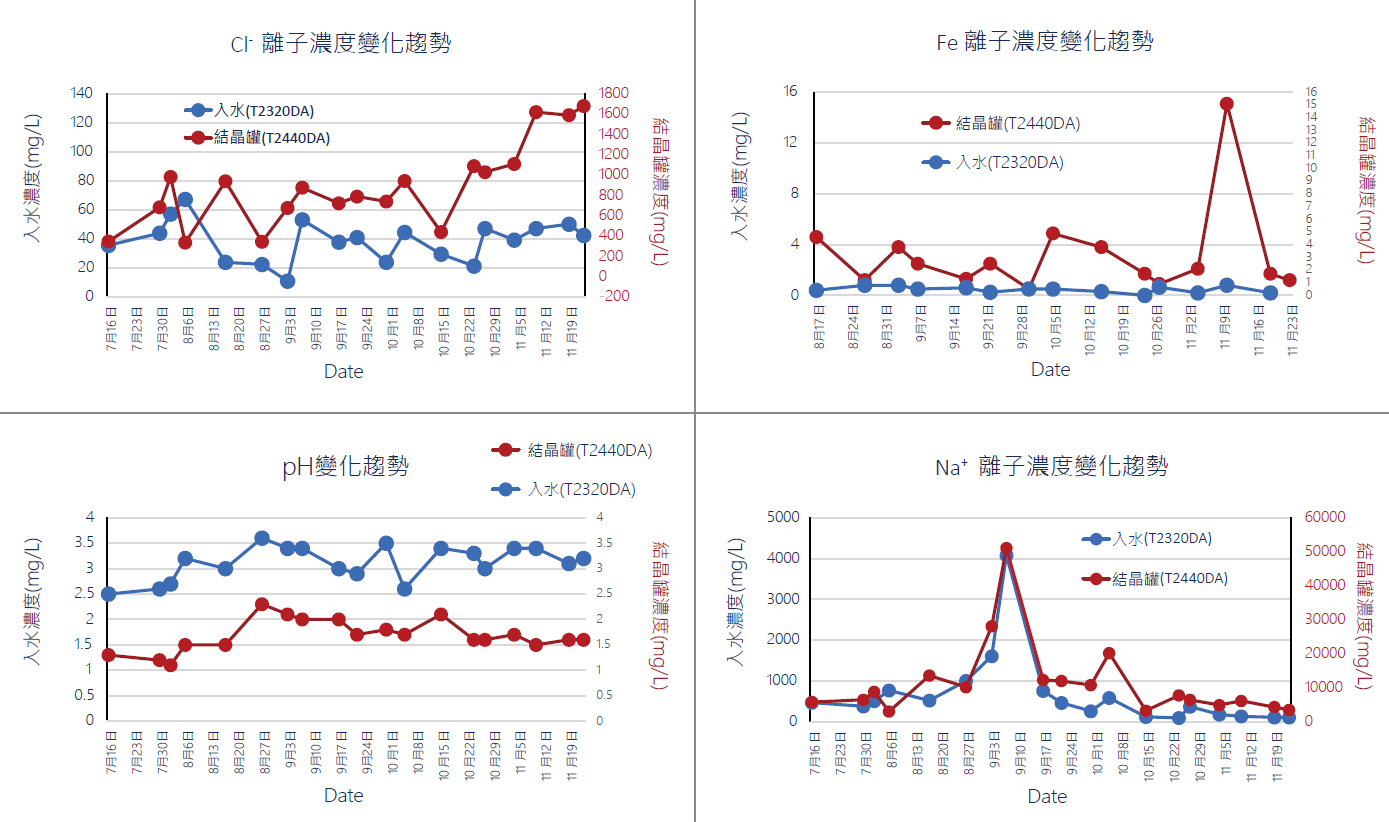
4.2轉動設備單元維護保養
各項設備定期維護保養是維繫設備壽命的不二法門,如PILLER蒸氣壓縮機,原廠建議9000小時需進行齒輪箱機油更換 ,離心機及循環泵黃油、攪拌機油等均依照原廠建議執行,離心機皮帶更換皆為必要執行項目[5](Ferrum,2019),各項設備原廠建議保養週期(表3)。
保養單元 |
檢查項目 |
標準 |
日保 |
週保 |
雙週保 |
月保 |
年保 |
---|---|---|---|---|---|---|---|
暫存槽 |
PH儀表 |
校正 |
V |
||||
強制循環泵 |
黃油添加 |
添加原廠指定型號黃油 |
V |
||||
軸流泵 |
黃油添加 |
添加原廠指定型號黃油 |
V |
||||
氨氮分析儀 |
標準液 |
標準液補充 |
V |
||||
分析儀校正 |
V |
||||||
壓縮機 |
軸心 |
停機狀況需適當轉動避免軸心變形 |
V |
||||
黃油嘴 |
添加原廠指定型號黃油 |
V |
|||||
機油 |
機油更換 |
V |
|||||
離心機 |
皮帶檢查 |
依原廠規格以張力計檢查或更換 |
V |
||||
黃油添加 |
依原廠規範添加對應潤滑油 |
V |
|||||
攪龍傳送裝置 |
排水管路檢查 |
確認清洗水流與管路是否堵塞 |
V |
V |
|||
物料傳送螺桿 |
螺桿表面結構清潔 |
||||||
乾燥床 |
空氣電加熱器吸入口濾網 |
濾網更換 |
V |
||||
乾燥床 |
內部床板表面孔洞 |
表面孔無堵塞,物料無堆積 |
|||||
下床體內部 |
下床體物料乾淨無堵塞 |
||||||
氣壓彈性底座 |
床體水平,底座高度13CM |
V |
|||||
吸料機 |
空氣濾芯 |
濾芯表面無堵塞 |
V |
||||
鼓風機皮帶 |
皮帶張力與外觀檢查 |
||||||
旋轉閥 |
添加原廠指定型號黃油 |
V |
|||||
振篩機 |
濾網 |
濾網表面無堵塞 |
V |
||||
細粉落料斗 |
細粉落料漏斗檢查與結垢清除 |
V |
|||||
成品落料斗 |
結垢清除 |
V |
|||||
包裝機 |
熱封條 |
加熱絲及隔熱膠布更換 |
V |
||||
落料斗 |
內部表面結垢清潔 |
V |
|||||
光電開關 |
光電感應開關表面清潔 |
V |
|||||
落料計量磅秤 |
磅秤粉塵清潔與零點歸零 |
V |
|||||
機械手臂 |
位置校正 |
V |
|||||
自動棧板 |
鍊條上油 |
V |
|||||
自動捆膜機 |
鏈條上油 |
V |
4.3產品包裝設備運轉與日常維運作業建議
當包裝機異常狀況發生時結晶罐濃度仍持續上升,將暫時切換出料至太空包作為承接,廠商收受太空包之允收重量為1噸重,因此建議各廠建立大於6小時產品暫存空間 ,搭配自動秤重落料機制以及磅秤校正功能,並考量密閉式落料及集塵設備,加強環境粉塵防護,避免粉塵逸散(圖12),操作人員PPE穿戴等級 : 安全眼鏡/戴維克/R95以上/防酸手套。
圖12、太空包成品落料及搬運作業
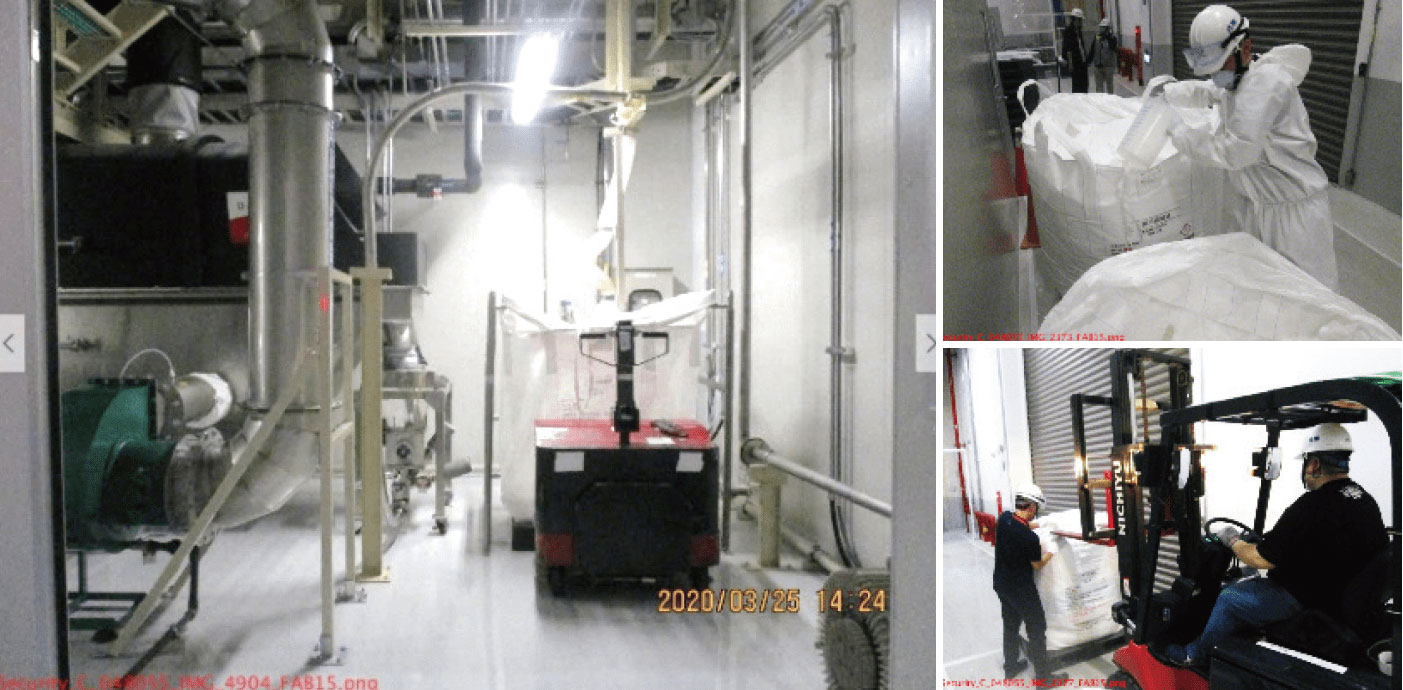
以台積首套系統為例,每日生產24棧板(24噸),以35噸大小卡車清運,每次清運量為18噸(18個棧板),約兩天須加派一車清運車趟,每車趟清運時間90分鐘,且清運操作須由堆高機搬運方可完成(圖13),人員訓練管理以四班二輪,並加派一名常日協助清運作業時間控系統狀況,該名技術人員負責日常水質、產品取樣分析與清運產品編號紀錄與車趟安排、抄表申報、人員調度等工作,例行工作項目安排(表5)。
圖13、成品清運作業
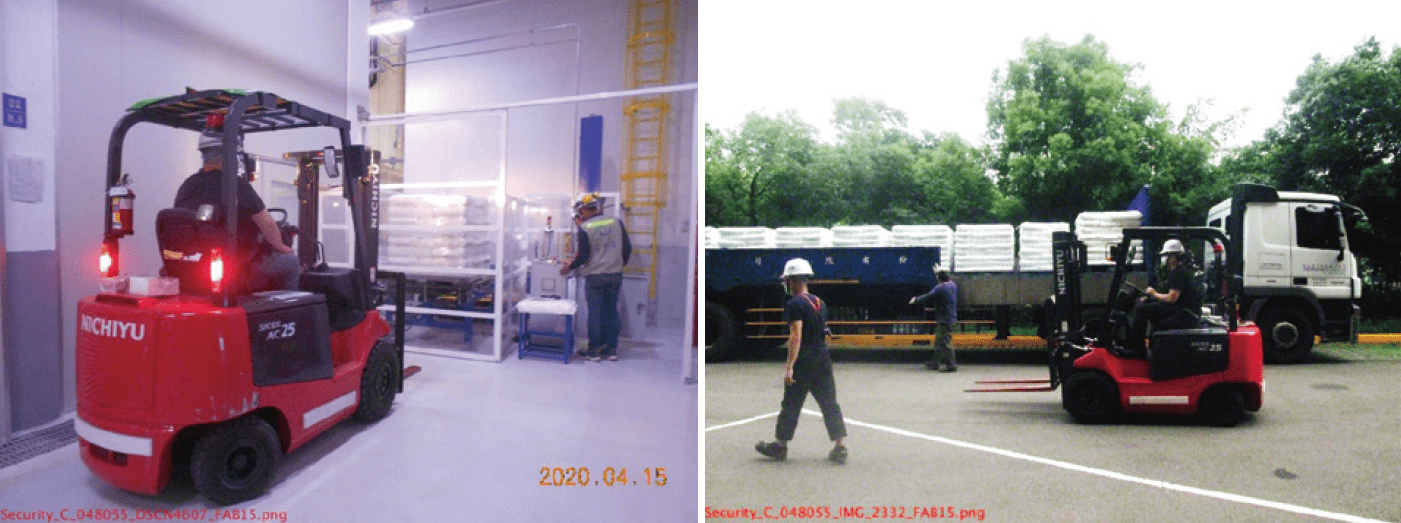
執行人員 |
工作項目 |
所需時間 |
所需人力 |
操作頻域 |
允收標準/所需工具 |
---|---|---|---|---|---|
常日班 |
T1670外運派車 |
0.5 |
1人 |
1次/日 |
|
T2315槽車灌充派車 |
0.5 |
1人 |
1次/日 |
||
灌衝硫酸銨水質量測 pH COD比重 |
0.5 |
1人 |
1次/日 |
COD<300 |
|
TSMTSM處理量/成品產出/ 清運申報 |
0.5 |
1人 |
1次/日 |
||
成品結晶每日取樣留樣 |
0.5 |
1人 |
1次/日 |
||
成品清運派車 |
0.5 |
1人 |
1次/日 |
||
T1670水質ph比重取樣 抄表 |
0.5 |
1人 |
1次/日 |
pH3.5~4,比重 >1.15,COD<300 |
|
T2320水質ph比重取樣 抄表 |
0.5 |
1人 |
1次/日 |
pH3.5~4,餘氯<100 |
|
T2390水質ph比重取樣 抄表 |
0.5 |
1人 |
1次/日 |
||
T2390緊急排放槽外運派車 |
0.5 |
1人 |
1次/日 |
||
T2390緊急排放槽水質取樣 pH比重 |
0.5 |
1人 |
1次/日 |
||
包裝袋安全庫存清點/叫料 |
0.5 |
1人 |
1次/日 |
>2週15680袋 |
|
棧板安全庫存清點/叫料 |
0.5 |
1人 |
1次/日 |
>2週392EA |
|
加熱條清點/叫料 |
0.5 |
1人 |
1次/日 |
>2週28EA |
|
包裝噴印機墨水線上補充/ 耗材清點/叫料 |
0.5 |
1人 |
1次/日 |
||
結晶罐取樣測量餘氯 |
0.5 |
1人 |
1次/日 |
pH3.5~4,餘氯<100 |
|
四班二輪 |
空棧板補充 |
0.1Hrs |
1人 |
2次/日 |
堆高機 |
2.5噸堆高機每日檢點表 |
0.5 |
1人 |
1次/日 |
||
機械手臂每日安全檢點表 |
0.5 |
1人 |
1次/日 |
||
物料傳送攪龍排水管路清洗 |
0.1Hr |
1人 |
1次/5分 |
||
包裝機加熱條外層膠膜更換 |
0.5 |
1人 |
1次/日 |
||
25公斤包裝空袋補充 |
0.5Hr |
2人 |
1次/日 |
||
包裝機磅秤清潔校正 |
0.5 |
1人 |
1次/日 |
||
粒徑分佈取樣分析 |
0.5Hr |
1人 |
1次/日 |
0.5mm>80% |
|
含水率分析 |
0.5Hr |
1人 |
1次/日 |
<1% |
|
堆高機成品下機 |
1Hrs |
2人 |
4次/日 |
堆高機 |
|
物料傳送攪籠清洗 |
1Hrs |
1人 |
1次/日 |
||
離心機清洗 |
1Hrs |
1人 |
1次/日 |
||
堆高機產品清運 |
2Hrs |
2人 |
1.5次/日 |
堆高機 |
|
乾燥床清洗 |
1Hrs |
2人 |
1次/週 |
||
一段吸料機空氣濾芯更換 |
1Hrs |
2人 |
1次/週 |
||
二段吸料機空氣濾芯更換 |
1Hrs |
2人 |
1次/週 |
||
成品棧板封膜更換 |
0.5Hr |
1人 |
1次/週 |
||
包裝機電加熱條更換 |
1Hr |
1人 |
1次/週 |
||
成品送樣委外分析 |
0.5 |
1人 |
1次/日 |
含氮量,含硫量分析 |
|
氨水drum桶更換 |
1Hrs |
1人 |
1次/月 |
運轉管理、PM OI與FAM機制建立、自動化改善方向
各項單元依形式訂定保養規範,建立OI,並納入FAM工單管理系統,依歸範執行 ; 熱風乾燥床及化學設備、濕式洗滌塔、堆高機另需參照自動檢查表,並需建立檢點項目標準,列入年度檢查項目留存。
參考文獻
- 恆宜化工,2018苗栗頭份廠實績勘查。
- 中石化,2019苗栗石化廠實績勘查。
- 毛國芳,1992硫酸銨結晶技術及品質探討。
- GEA,2019 C5 1801-E03-0001-Rev-02-Operating Conditions.
- Ferrum,2019 01.00_D11_1088_0_CN_IM_Pusher_Centrif uge_PM-230+23_06.
留言(0)