摘要
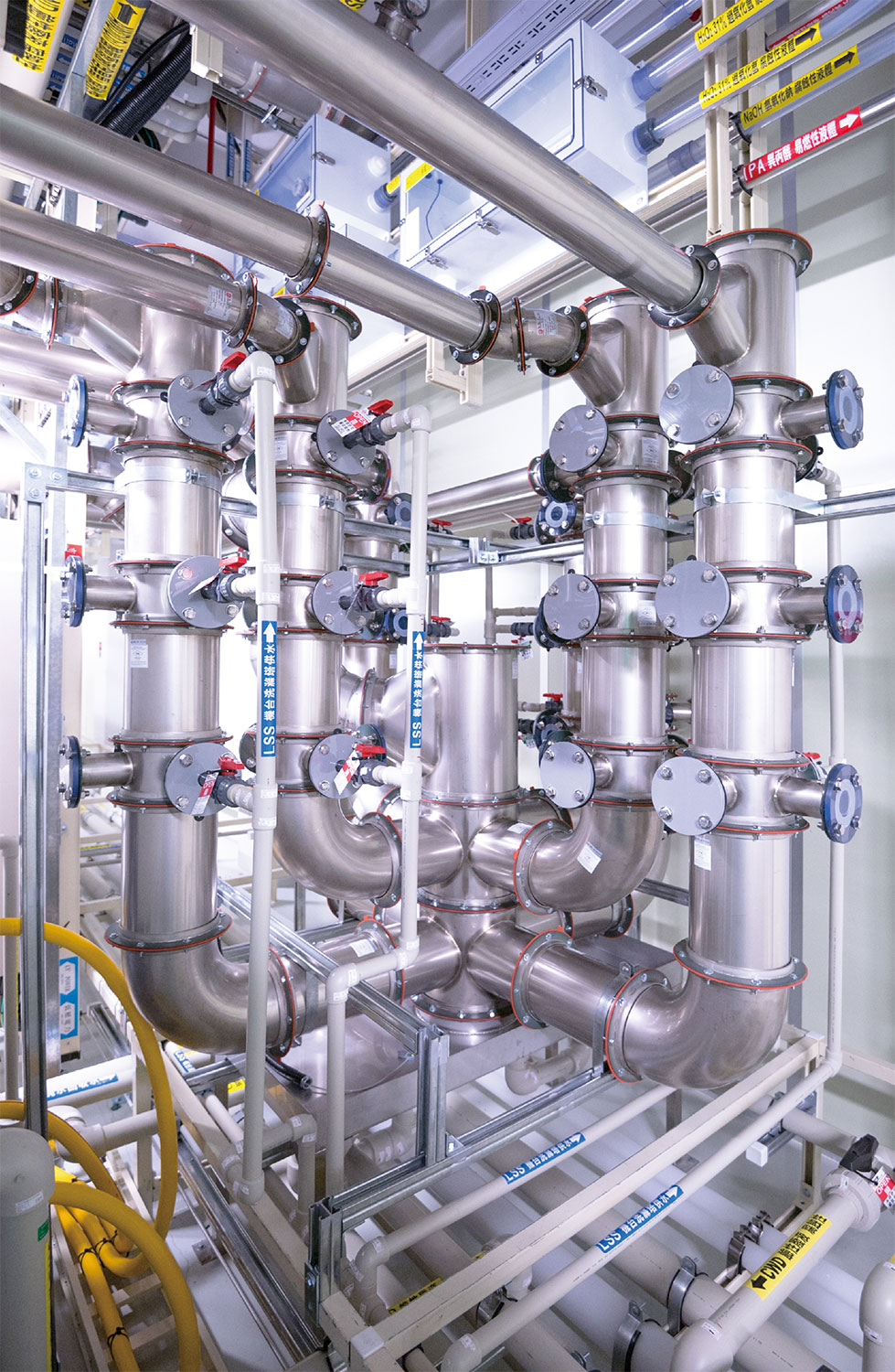
排氣分流改造應用於粒狀物減量
PM2.5空氣污染與健康危害之議題開始受到重視,近年來PM2.5超過空氣品質標準,環保署公告2017年1月1日起各縣市列為三級空氣污染防制區,面對未來將進行總量管制及排放物種削減之趨勢,各廠需進行白煙粒狀物改善。目前廠內以濕式蝕刻製程因酸鹼混排產生硫酸銨結晶的問題為最大宗,現行對策為設置現址式濕式洗滌塔及水渦流機,其中水渦流機對於0.3μm以下微粒僅有60%去除率,因此本研究重新檢討廠內水渦流機的效能,以及探討所面臨的源頭酸鹼混排真因,進行管路分流改善及前水洗設計,解決大量粒狀物白煙生成的問題,提供未來長期系統改善建置新方法之參考。
前言
多久以前,「春天來的時候門開著,風進來、花香進來。有雨、有霧的時候,人忍不住想要往肺裡面深深地呼吸一口氣,那種帶著碎雨的那種凜冽的、清新的感覺。」(柴靜《穹頂之下》)但現在呢?每天醒來就是先看空氣品質指標(Air Quality Index, AQI)關心紫爆,戴著口罩外出,空氣清淨機也逐漸成為每個家庭必備品來阻擋PM2.5。中國大陸央視前主播柴靜的 「穹頂之下」紀錄片探討了PM2.5的嚴重性。行政院主計處公布在2016年經濟合作與發展組織(The Organization for Economic Cooperation and Development, OECD)之美好生活指數(Your Better Life Index, BLI)國家排名中,臺灣空氣污染在39國中排名第37,如 表1所示。
表1、台灣美好生活指數(BLI) 各項指標國際排名(2016年) [1]
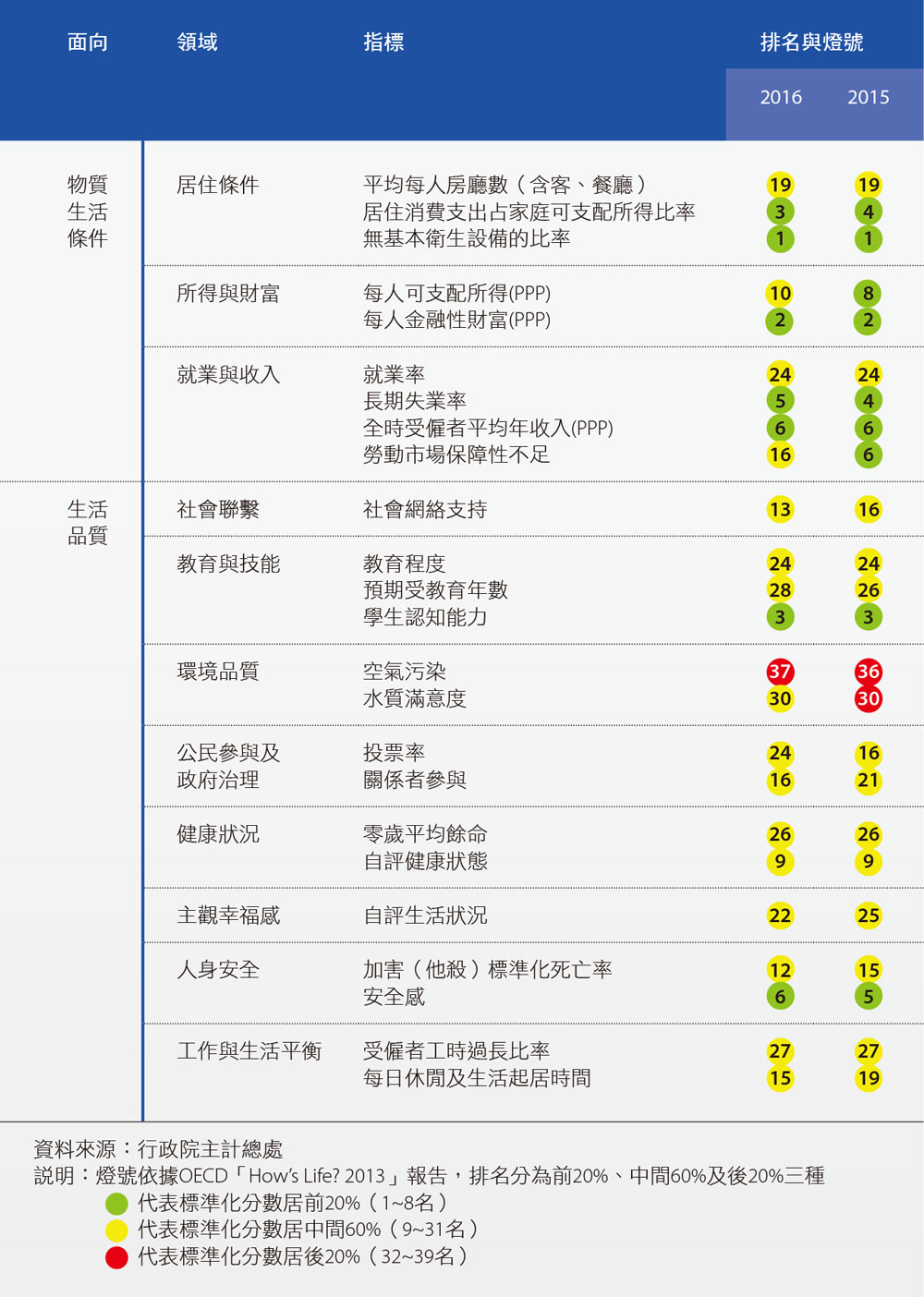
其中,BLI於2016年起將空氣污染指標由懸浮微粒(PM10)改採細懸浮微粒(PM2.5),我國PM2.5濃度值20微克/立方公尺(ug/m3),僅低於以色列及南韓[1],仍待進一步改善。粒狀污染物來源除了境外污染及交通排放之外,工業製程也會產生粒狀污染物從煙囪排至大氣,造成白煙觀感不佳等問題,廠內尤以濕式蝕刻製程因酸鹼混排產生硫酸銨微粒的問題最為困擾,因此需探討廠內粒狀污染物防制設備之效能嚴格管制源頭,以因應未來嚴苛法規的趨勢。
粒狀污染物概述
粒狀物主要來源及種類
空氣中粒狀污染物的主要來源可分兩大類。
自然產生
火山爆發噴出之火山灰微粒;自然火災如森林與草原之意外大火產生的煙霧,以煤煙、未燃燒碳化氫類、一氧化碳、氮氧化物及灰燼等形態生成大量污染物;土壤侵蝕(Soil erosion)產生的土塵微粒經常存於大氣中,濃度隨地區與季節而變動,北半球大氣中每年約有1億5千萬噸土塵由地表揚起,若加上沙漠地區則增為兩倍。[2]
人為產生
以燃料燃燒、工業製程、交通排放、廢棄物燃燒、逸散性排放或經由氣體的化學反應而形成。人為粒狀污染物的種類可依其來源及形成機制概分為:物理研磨及傳播、燃燒灰燼、同異相核凝、液滴揮發後殘留不純物及酸鹼氣體混合產生鹽類結晶等。人為排放的污染物受到地形及氣候的影響,具有區域性並且呈現梯度分布的現象,經一段時間混合後,在大氣中會發生化學變化而改變其形態及組成,形成二次污染物,這些細小的固態顆粒及液滴組成的懸浮微粒(Particulate matter, PM),又稱為氣膠(Aerosol)。
懸浮微粒之特性
懸浮微粒的粒徑大小有別,如 表2所示,小於或等於2.5微米(μm)的粒子就稱為PM2.5,通稱細懸浮微粒,單位以微克/立方公尺(μg/m3)表示之,它的直徑不到頭髮粗細的1/28,非常微細可穿透肺部氣泡,並直接進入血管中隨著血液循環全身,故對人體及生態所造成之影響是不容忽視的。PM2.5的生成機制可分為兩種,皆可能由自然界或人為產生,如 圖1所示。
名稱 |
粒徑 |
說明 |
---|---|---|
總懸浮微粒(TSP) |
< 100μm |
約為海灘沙粒,可懸浮於空氣中 |
懸浮微粒(PM10) |
< 10μm |
約為沙子直徑的1/10,容易通過鼻腔鼻毛與彎道 到達喉嚨 |
粗懸浮微粒(PM2.5- PM10) |
2.5~10μm |
約頭髮直徑的1/8~1/20大小,可被吸入並附著於 人體的呼吸系統 |
細懸浮微粒(PM2.5) |
< 2.5μm |
約頭髮直徑的1/28,可穿透肺部氣泡,直接進入 血管中隨著血液循環全身 |
圖1、原生性及衍生性PM2.5來源關係圖[2]
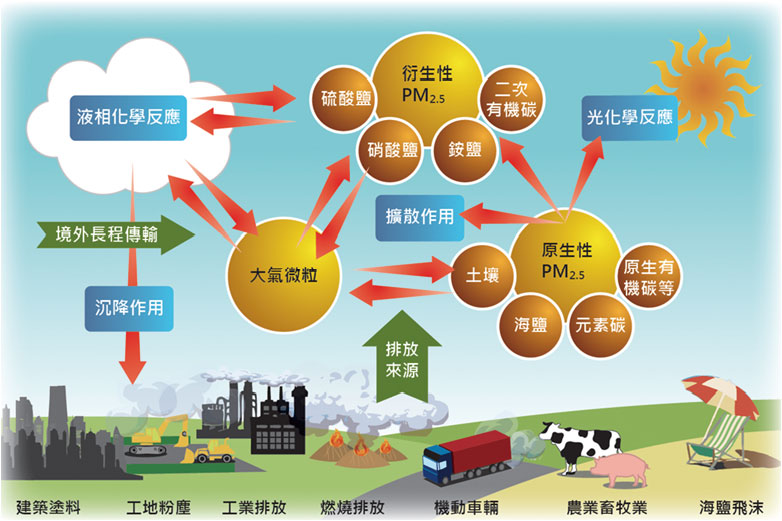
原生性(Primary)
是指在大氣中未經化學反應的微粒,主要來自物理破碎、風蝕逸散或人為污染所直接產生,包括海鹽飛沫、裸露地表揚起的粉塵,鍋爐及機動車輛引擎燃燒過程排放之微粒等。
衍生性(Secondary)
是指排放到大氣中的化學物質(稱為前驅物,可能為固體、液體或氣體),經過複雜的化學變化與光化反應後生成,PM2.5前驅物包括:硫氧化物(SOx)、氮氧化物(NOx)、揮發性有機物(VOCs)與氨(NH3),在大氣中反應生成硫酸鹽、硝酸鹽及銨鹽等微粒組成PM2.5。
半導體業白煙粒狀物生成機制
一般而言,半導體業非燃燒製程所產生的粒狀污染物通常為排氣中酸鹼氣體混和而生成白色鹽類微粒,至煙囪排放出去就會產生白煙。例如:硫酸(H2SO4)與氨(NH3)反應由銨離子和硫酸根離子產生離子化合物硫酸銨(NH4)2SO4,化學反應式如下,這類酸與氨反應之化合物統稱為銨鹽。
H2SO4+2NH4OH → (NH4)2SO4+2H2O
針對酸性排氣煙道對PM2.5進行採樣及分析,如 圖2所示,陽離子部分以銨根離子之濃度最高,陰離子部分則以硫酸根離子濃度最高,由數據推測採樣之管道此二種離子來源應為硫酸銨鹽類。
圖2、酸性排氣煙道粒狀物PM2.5成分分析
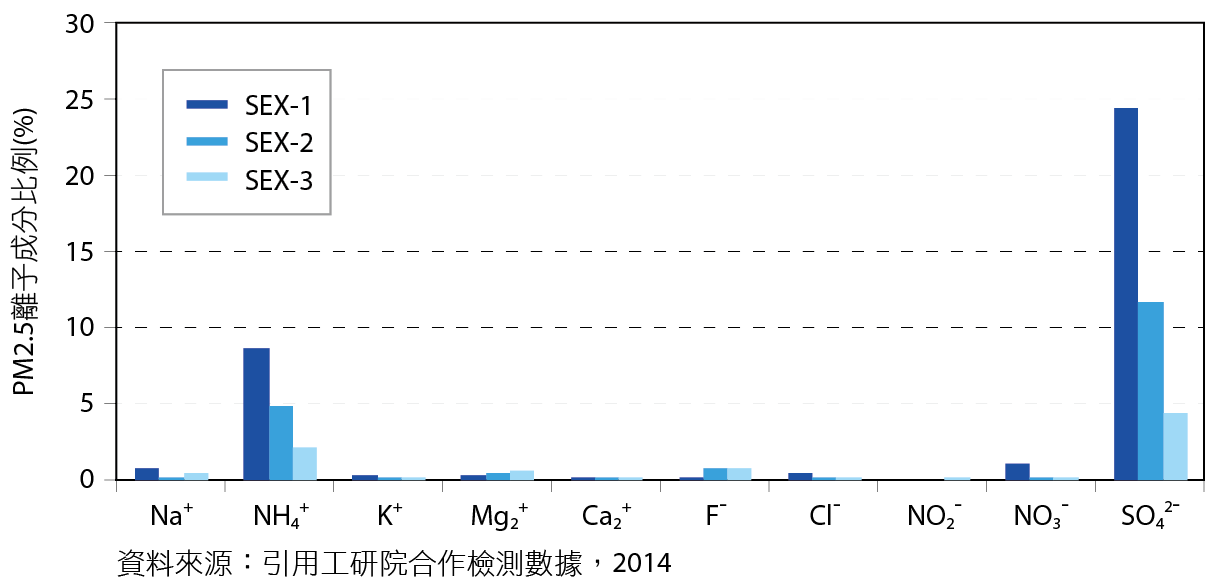
2014年中科廠區率先執行PM2.5煙道排放調查,廠區煙道PM2.5排放比例主要來源為酸性廢氣系統(SEX, 55%)及揮發性有機廢氣系統(VEX, 40%),如 圖3所示。其中,SEX PM2.5主要來自濕式蝕刻製程酸鹼混排產生的硫酸銨;而VEX PM2.5來自沸石濃縮轉輪與直燃式焚化爐燃燒時產生的碳微粒(本研究中暫不討論)。因此,比對製程機台化學品用量及針對濕式蝕刻製程區上游風管進行污染物採樣分析,可找到造成白煙粒狀物產生之關鍵製程機台,本研究將針對酸鹼混排製程產生粒狀污染物之防制技術進行探討。
圖3、中科廠區煙道PM2.5排放比例估算
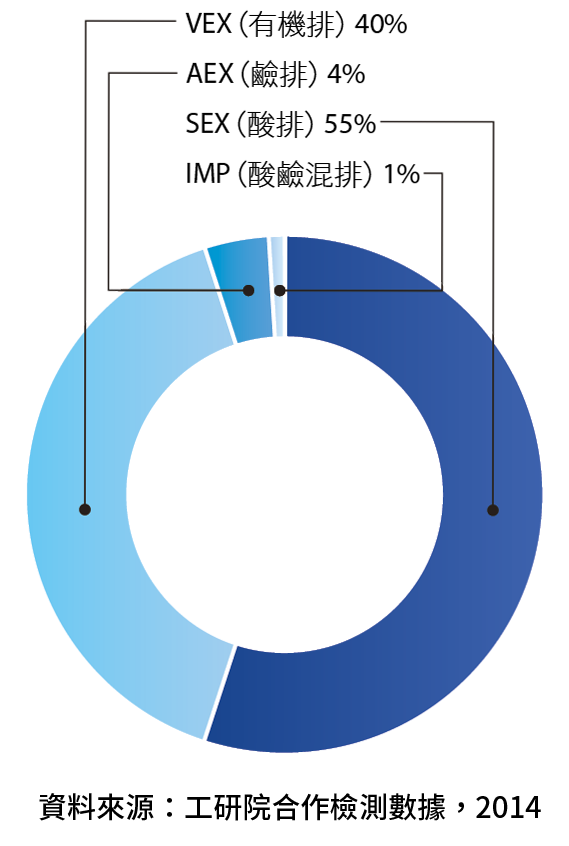
粒狀污染物防制技術
粒狀物控制設備通常依粒徑尺寸、特性及處理風量不同而選定適合之集塵方式,大致可分為重力式、離心式、過濾式、靜電式、濕式洗滌等,其中傳統常見之粒狀污染物防制技術包括重力沉降室(GS)、旋風集塵器(cyclone)、袋式集塵器(FF)、靜電集塵器(ESP)、濕式洗滌塔(wet scrubber)等五種,其各種技術特性彙整如 表3所示。
控制設備 |
可收集最小粒徑 |
收集效率 |
優點 |
缺點 |
適用時機 |
---|---|---|---|---|---|
重力沉降室 (GS) 圖4 |
>30-50μm |
<50% |
構造簡單、低壓損 成本低廉、維修容易 |
需佔用大面積 對細微粉塵無法去除 |
不單獨使用 (其他設備之預淨器) |
旋風集塵器 (cyclone) 圖5 |
>5-25μm |
50-90% |
設計簡單 乾式粉塵處置方法無廢水產生 對大顆粒及大流量氣體處理效果好 |
對小顆粒粉塵效率低(<10μm) 無法處理黏著性微粒 噪音高(80-100dBA) |
粉塵粗大 粉塵濃度高 |
濕式洗滌器 (wet scrubber) |
>10μm (噴淋式) >0.5μm (文氏) |
>80% (噴淋式) >99% (文氏) |
同時去除酸鹼性氣體 處理高溫廢氣 處理黏著性微粒 |
易有腐蝕問題 壓損較高 需處理大量廢水 |
氣體需降溫 可燃性粉塵 欲同時去除氣狀物 |
袋式集塵器 (FF) 圖6、圖7 |
>0.3μm |
>99% |
對小顆粒粉塵效率高 可回收塵料 無廢水、腐蝕問題 |
不適用高溫廢氣 濾布老化問題 對濕度敏感 對過濾速度敏感 |
除塵效率要求高 具有粉塵回收 氣體溫度需先降溫 |
靜電集塵器 (ESP) 圖8、圖9 |
>0.3μm |
>99% |
對小顆粒粉塵效率高 廢氣壓力損失較小 耐酸鹼及耐濕性較佳 |
設備成本高 不適用易燃氣體 |
除塵效率要求高 高溫廢氣 粉塵不具爆炸性 |
圖4、具隔板之重力沉降室[3]
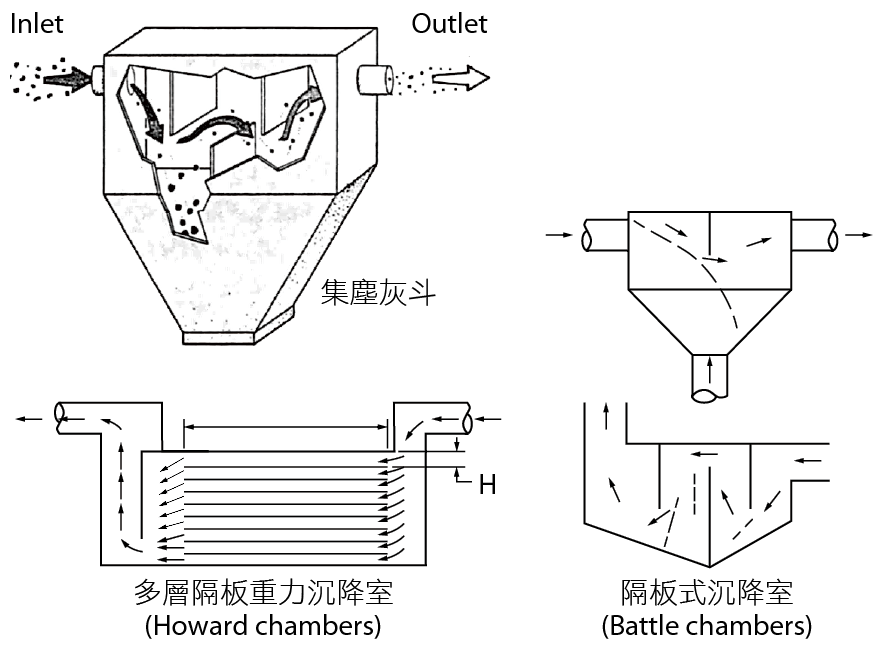
圖5、典型旋風集塵器之微粒收集機構[4]
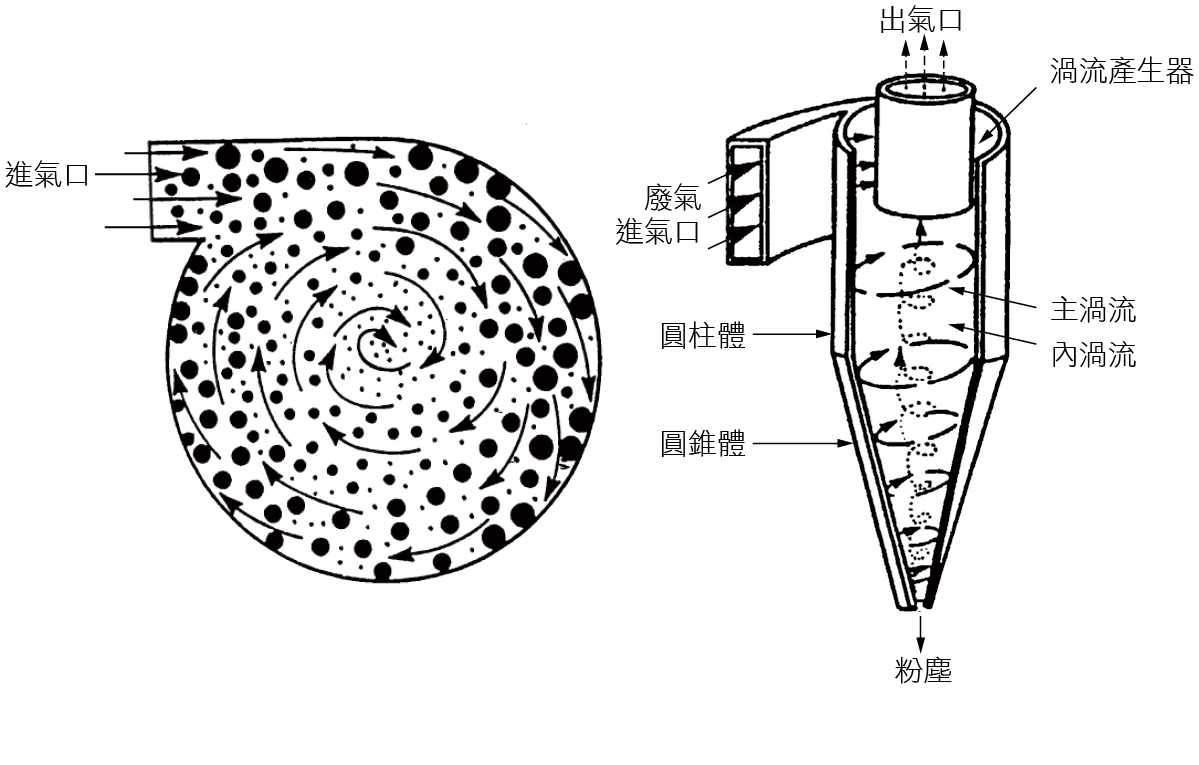
圖6、袋式集塵器之過濾機制[5]
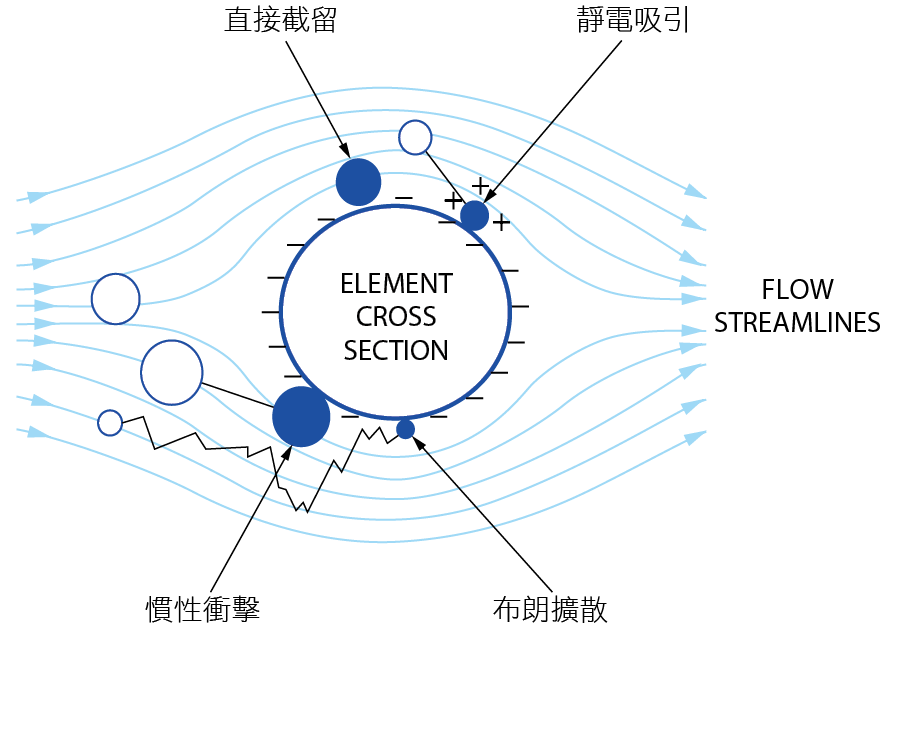
圖7、濾餅效應之集塵機制[6]
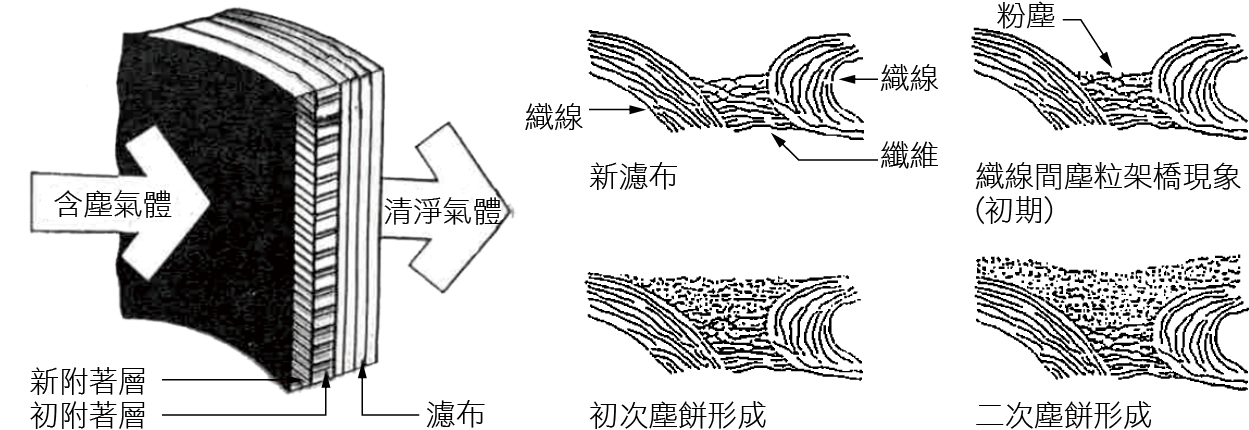
圖8、ESP 微粒集塵示意圖[7]
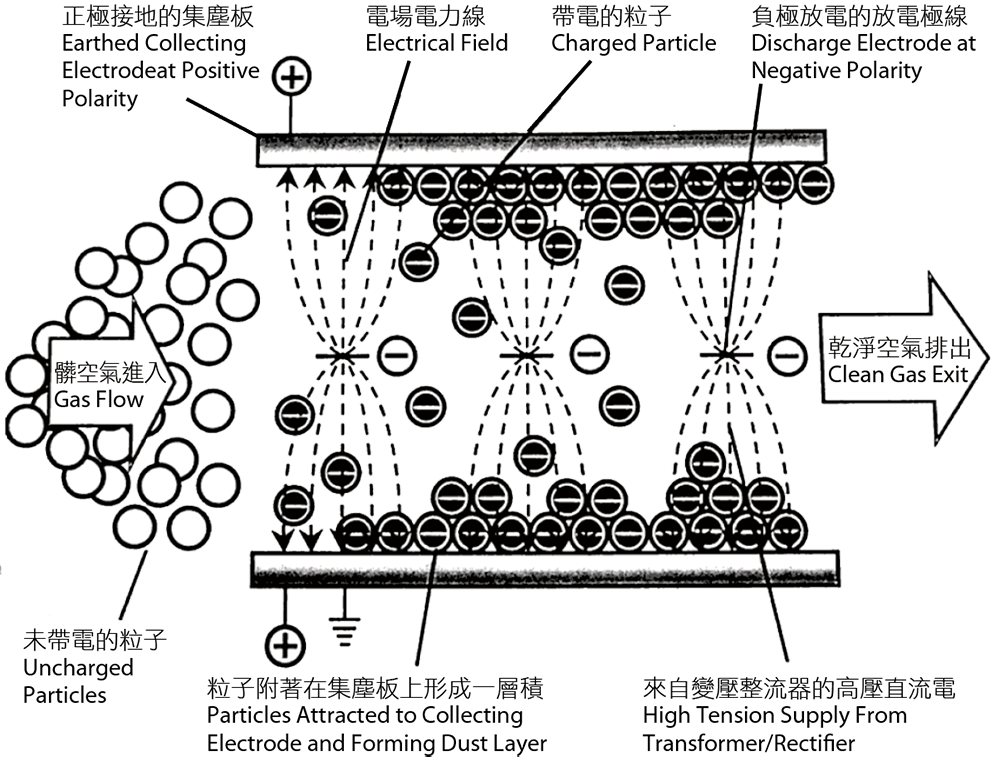
圖9、靜電集塵之基本流程[8]
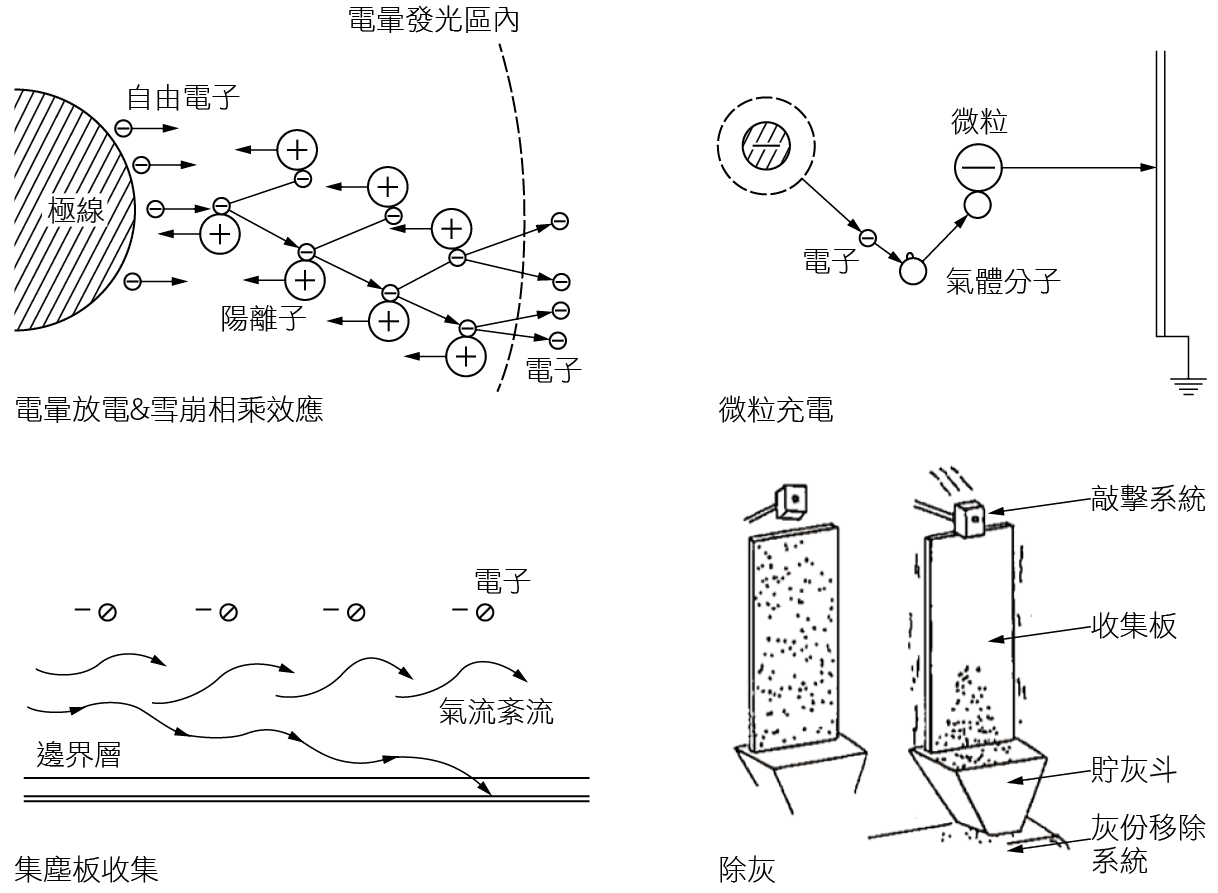
綜合上述各式粒狀污染物處理技術之比較可知,控制設備的效率由高到低依序為袋式集塵器、靜電集塵器、濕式洗滌器、旋風集塵器及重力沈降室。雖然前兩者對於粒徑大於0.3μm之微粒,去除率大於99%,但是,袋式集塵器並不適用高溫氣體,濾布老化更新成本高,需常清理,若過濾有機質易生爆炸;而靜電集塵器耐酸鹼及耐濕性佳,但設備成本高,且不適用易燃氣體,應避免錯誤物質進入之機會。
廠內粒狀物防制技術檢討與改善
目前廠區現況與難題
濕式蝕刻製程裝設濕式洗滌塔
廠內目前以現址式濕式洗滌塔(local wet scrubber)處理濕式蝕刻製程機台廢氣,將源頭高濃度氨氣及硫酸做初步的削減,以減少酸鹼於風管中混排產生之粒狀污染物,並於中央設置大型濕式洗滌塔處理酸鹼氣體以及較大粒徑的微粒,作為最後的把關,但是濕式洗滌塔對於1μm以下微粒之去除效果不佳,收集效率低於50%, 圖10顯示流動床洗滌器收集效率與粒徑(Dp)的關係,由圖可見,很大及很小的微粒分別藉由慣性衝擊與擴散效應機制有較高的收集效率,粒徑0.5μm時效率最差。
圖10、流動床洗滌器之收集效率與微粒粒徑(Dp) 的關係
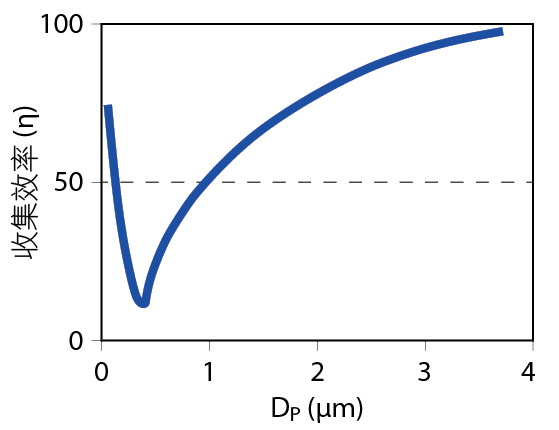
濕式蝕刻高溫硫酸製程裝設水渦流機
後續導入新式設計「水渦流機」處理濕式蝕刻製程高溫SPM機台所產生的硫酸銨微粒,水渦流機為獨特離心氣旋裝置,藉由風機牽引氣流及桶槽存水產生氣旋水霧,進而使水霧化與空氣有效率接觸混和,提供較佳的液、氣混和效果及粉塵捕捉效率。根據各Submain PM2.5質量濃度採樣分析結果顯示 表4,以IMP Submain測得之PM2.5濃度最高,而其元素及離子佔PM2.5之83.8%,由此可知管道中PM2.5主要成分為高溫SPM機台產生之高濃度硫酸銨鹽類。因此,水渦流機主要針對於高溫硫酸機台之廢氣進行源頭削減。
項目 |
內容 |
||||||
---|---|---|---|---|---|---|---|
(2015) 採樣日期 |
5月26日 |
5月28日 |
6月1日 |
6月8日 |
6月11日 |
6月15日 |
6月22日 |
Submain |
FSED-LB1-103 |
FSED-LB1-105 |
FSED-L10-106 |
FSED-L20-102 |
HSED-L30-108 |
HSED-L30-106 |
FSED-L10-103 |
製程 |
BE Bench (STD) |
DIF Nitride |
CVD SiH4base tool |
IMP (FSI) |
ECP |
Cu CMP |
FE Bench, Dry etch |
PM2.5平均濃度 (由高到低排序) |
6 |
4 |
3 |
1 (最高) |
5 |
7 |
2 |
元素及離子佔 PM2.5比例(%) |
18.4% |
24.9% |
28.2% |
83.8% |
39.9% |
67.3% |
55.0% |
由工研院使用電子式低壓衝擊器(Electrical Low Pressure Impactor, ELPI)進行管道之粒徑分析 圖11,發現高溫硫酸機台產生白煙粒徑主要為0.4μm以下佔80% (藍色及綠色區塊),比對水渦流機效率檢測結果如 表5、圖12,大於1μm粒徑其去除效率可大於90%,但對於0.3μm以下微粒處理效率不佳僅有60%去除效率,顯示水渦流機並無法完全去除高溫硫酸機台所產生之粒狀物污染物。
圖11、高溫硫酸機台排放粒徑分佈百分比( 資料來源:工研院合作檢測數據,2014)
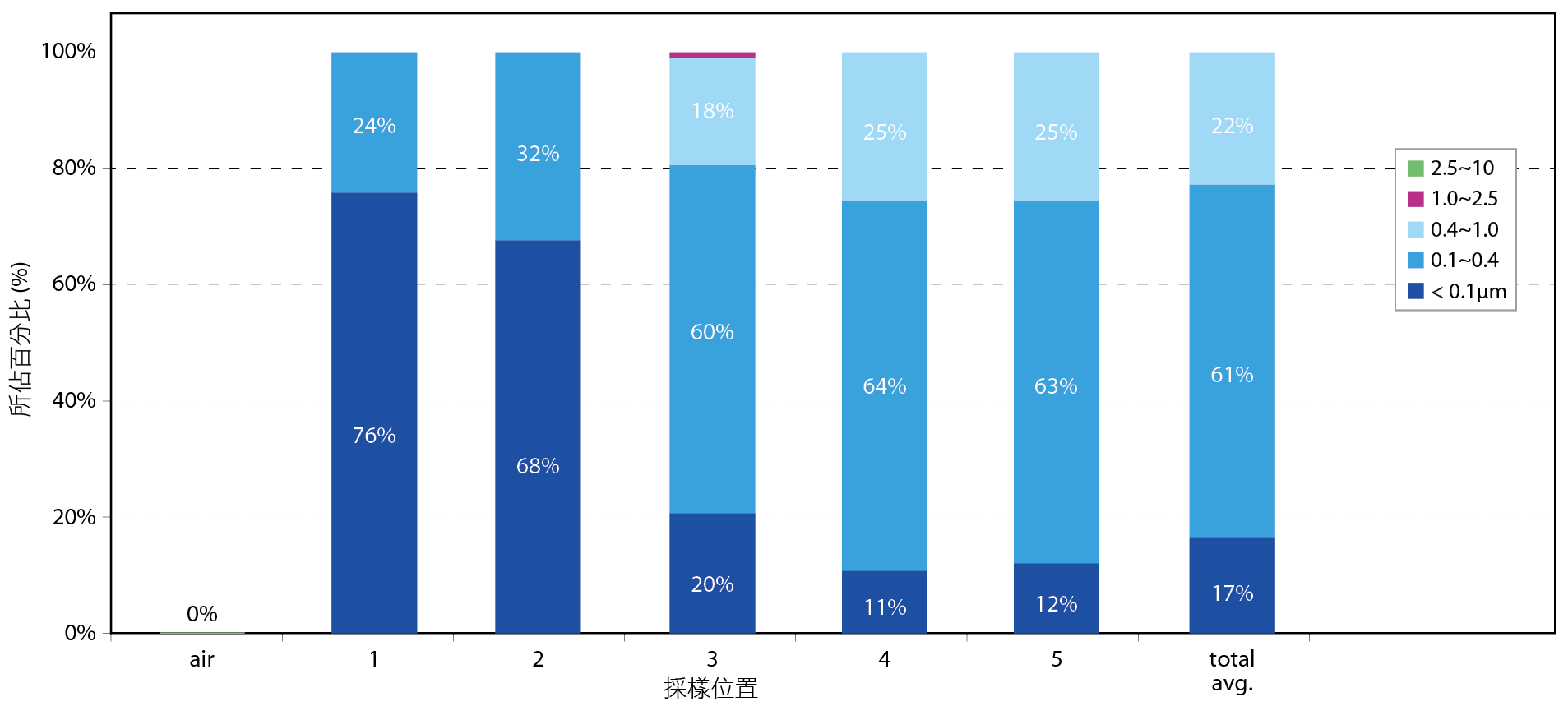
項目 |
內容 |
|||
---|---|---|---|---|
Powder diameter |
0.3μm |
0.5μm |
1μm |
≥5μm |
Removal efficiency |
60% |
75% |
90% |
95% |
Pressure drop -Pa |
1250 |
1250 |
1250 |
1250 |
資料來源:工研院合作檢測數據,2014 |
圖12、水渦流機對不同粒徑之集塵效率曲線圖
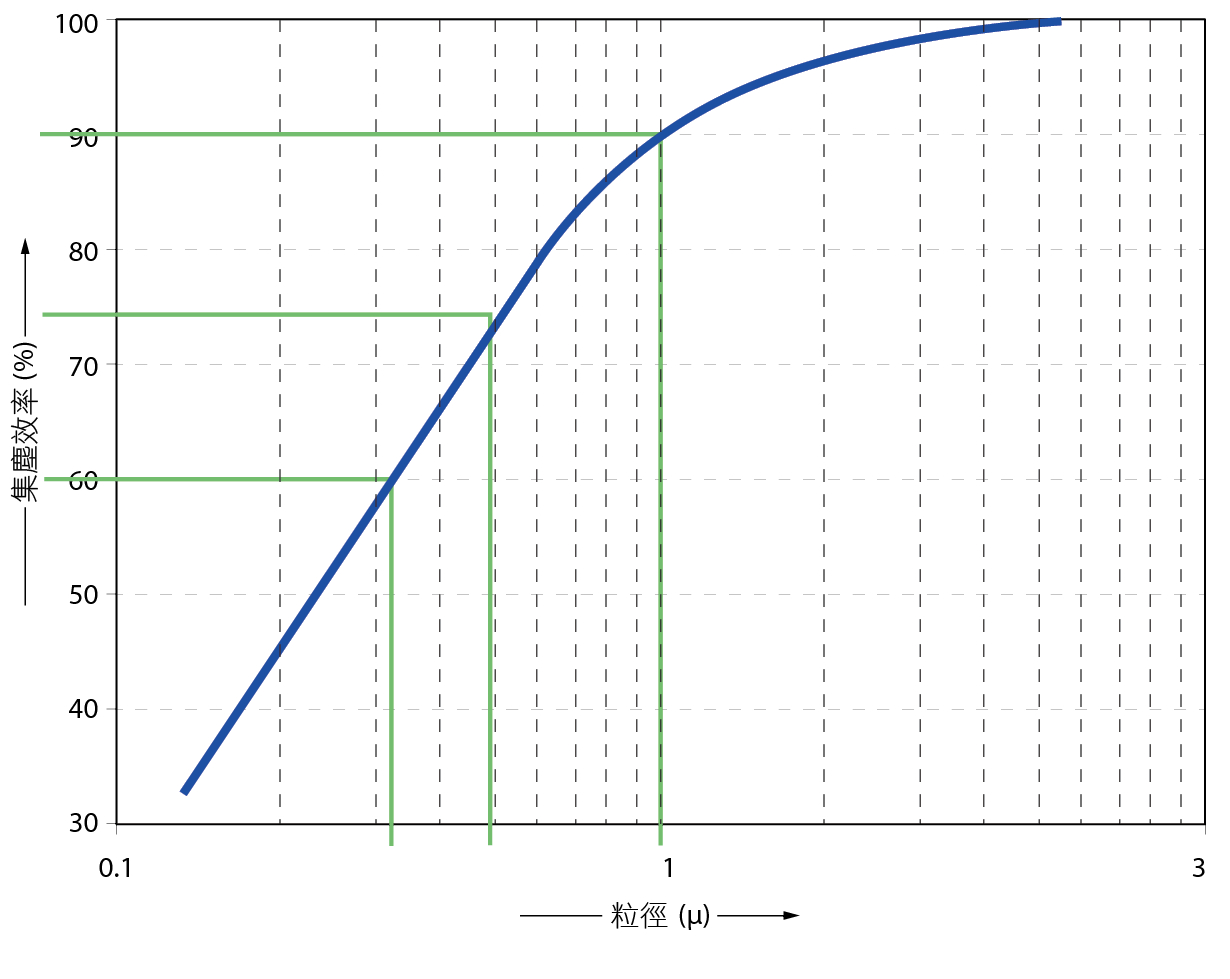
真因探討與設計規劃
Chamber Exhaust共管導致酸鹼混排
濕式蝕刻高溫硫酸製程使用高溫SPM (高溫硫酸)及SC-1 (液態氨)進行蝕刻, 其程序如 圖13,高溫硫酸(H2SO4)與雙氧水(H2O2)反應後產生220~240℃之霧化硫酸,經過去離子水(DI)潤洗過後,接著使用氨水(NH4OH)與雙氧水,再使用去離子水後則進行下一次循環,由於不同chamber使用化學品的時間不一致,chamber exhaust內連線為共管,則不同chamber的酸鹼皆混排而形成大量硫酸銨粒狀物,造成風管結晶及煙囪白煙問題。根據機台廢氣流程圖來看 圖14,每兩個chamber透過歧管(manifold)將製程廢氣匯集至酸性排氣管道(SEX),因此排至水渦流機處理之前,早已產生大量的銨鹽粒狀物。
圖13、濕式蝕刻高溫硫酸製程化學品使用程序

圖14、濕式蝕刻高溫硫酸製程機台排氣 構造與流程圖( 改善前)
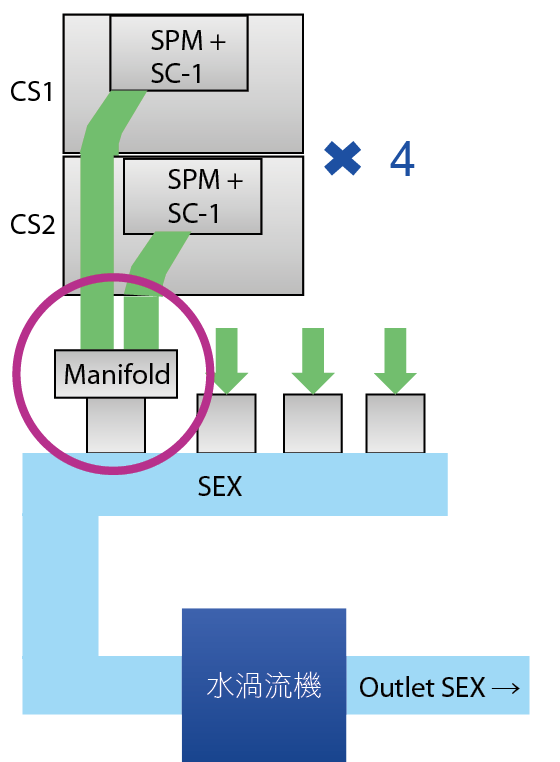
內連線分流及前水洗設置
由上述單一chamber化學品使用程序可知,關鍵點在於H2SO4與NH4OH兩者使用的時機並不重疊,且中間以去離子水潤洗數百秒,因此若將各chamber內連線由共管改為獨立管分流,當不同chamber進行不同酸鹼程序時,單一chamber專管專收不互相混排影響,可大幅降低高濃度酸鹼產生大量粒狀物的機會。因原廠機台設計本身底部已設有專管接點,由此接點後之製程排氣管路修改設計 圖15,兩支chamber exhaust出機台後各自走獨立專管,取代舊有歧管匯集至酸性排氣管道的設計,並於獨立管內設置前灑水頭進行初步水洗,以降低管內酸鹼氣體濃度,減少後續混合形成硫酸銨的機會,當廢氣經分流及細水霧灑水後再送至水渦流機進行少量粒狀物的處理。此設計與以往不同的是,針對濕式蝕刻高溫硫酸製程不再只是處理生成之粒狀物而已,而是解決源頭的酸鹼氣體問題,同時改善混排造成大量粒狀物進入水渦流機增加效能負荷之問題。
圖15、濕式蝕刻高溫硫酸製程機台排氣改管及灑水示意圖(改善後)
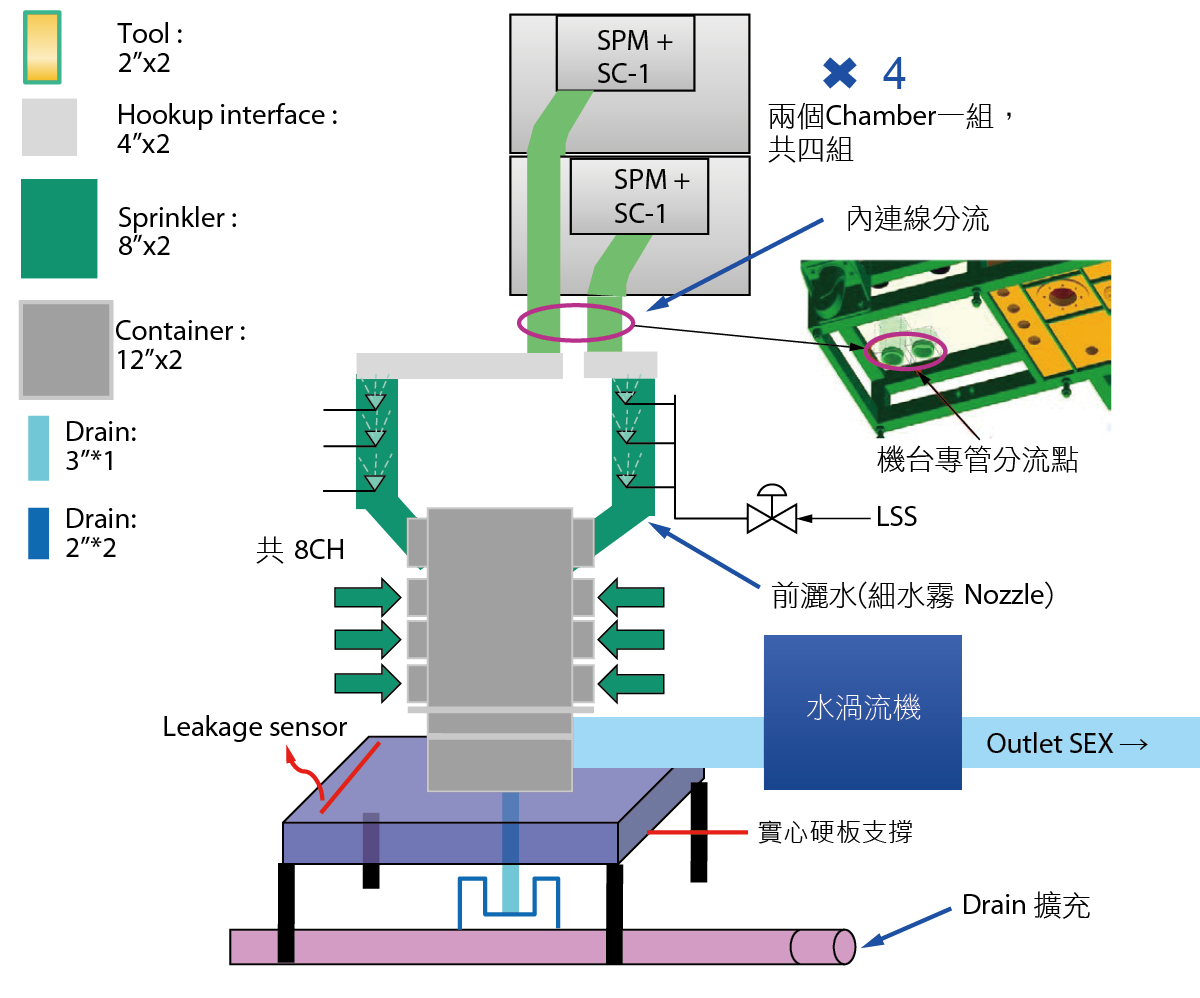
改善結果及後續研究發展
以粒狀物等速吸引採樣法求得質量濃度進行改善效率驗證,採樣流量為2L/min,採樣時間為10分鐘,濾紙孔徑為0.45μm,採樣點為水渦流機入口及出口,排氣中粒狀物濃度計算如下式:
CN = md / V'N
式中:
CN:排氣中粒狀污染物濃度(g/m3)
md:捕集粒狀物之質量(g)
V'N:吸引排氣量(m3)
與設備配合dummy run,實驗結果顯示 圖16,改善前chamber內連線共管酸鹼混排造成水渦流機入口粒狀物濃度(粒狀物產生量)為120mg/m3,而改善後內連線分流及前灑水降低酸鹼混和機會,則粒狀物濃度僅為40mg/m3,粒狀物產生量大幅減少67%。
圖16、濕式蝕刻高溫硫酸機台排氣分流改善結果(2016年2月12日)
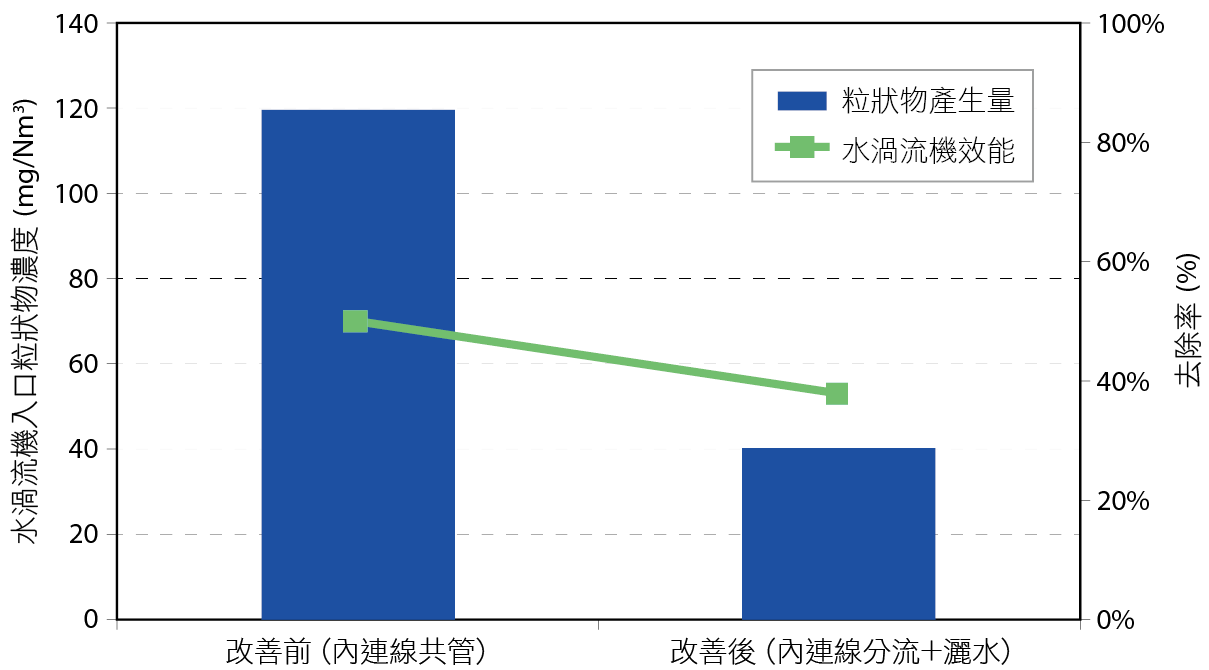
為了有更佳的改善效率及完善的安全防護,應將下列幾點設計列入考量:
- 水洗段風管氣液比及灑水頭(nozzle)的選用
- 是否因改管灑水後管路壓損過高影響原水渦流機之效能
- 安全設計問題包括排水管容量、存水彎及漏液 interlock 功能
結論
在選擇最佳之粒狀物防制設備之前,尚須考量微粒的生成機制、物化特性、粒徑分布、處理風量、空間大小及安全性等因素,經過一連串調查評估後,可能有多項設備皆為「適用設備」,故需再應用整體評估的方式選出「最佳可行控制技術 (BACT)」,其選用流程可參考 圖17,其主要是評量各項設備之特性、設備性能及技術可行性。廠內濕式蝕刻高溫硫酸機台原先設置水渦流機處理粒狀物效率為60%,此為治標不治本,本研究重新檢討高溫硫酸機台既有的設計與排氣管路,探究大量粒狀物的生成來源,發現關鍵點為H2SO4與NH4OH兩者使用的時機並不重疊,將各chamber內連線由共管改為獨立管分流,解決源頭的酸鹼氣體問題,同時改善混排造成大量粒狀污染物的問題,粒狀物產生量成功減少67%。若進一步改善水渦流機處理效能或中央濕式洗滌塔導入新型多孔性除霧器等新技術,要徹底解決廠內白煙問題將勢在必行。
圖17、空氣污染防制設備選用程序[4]
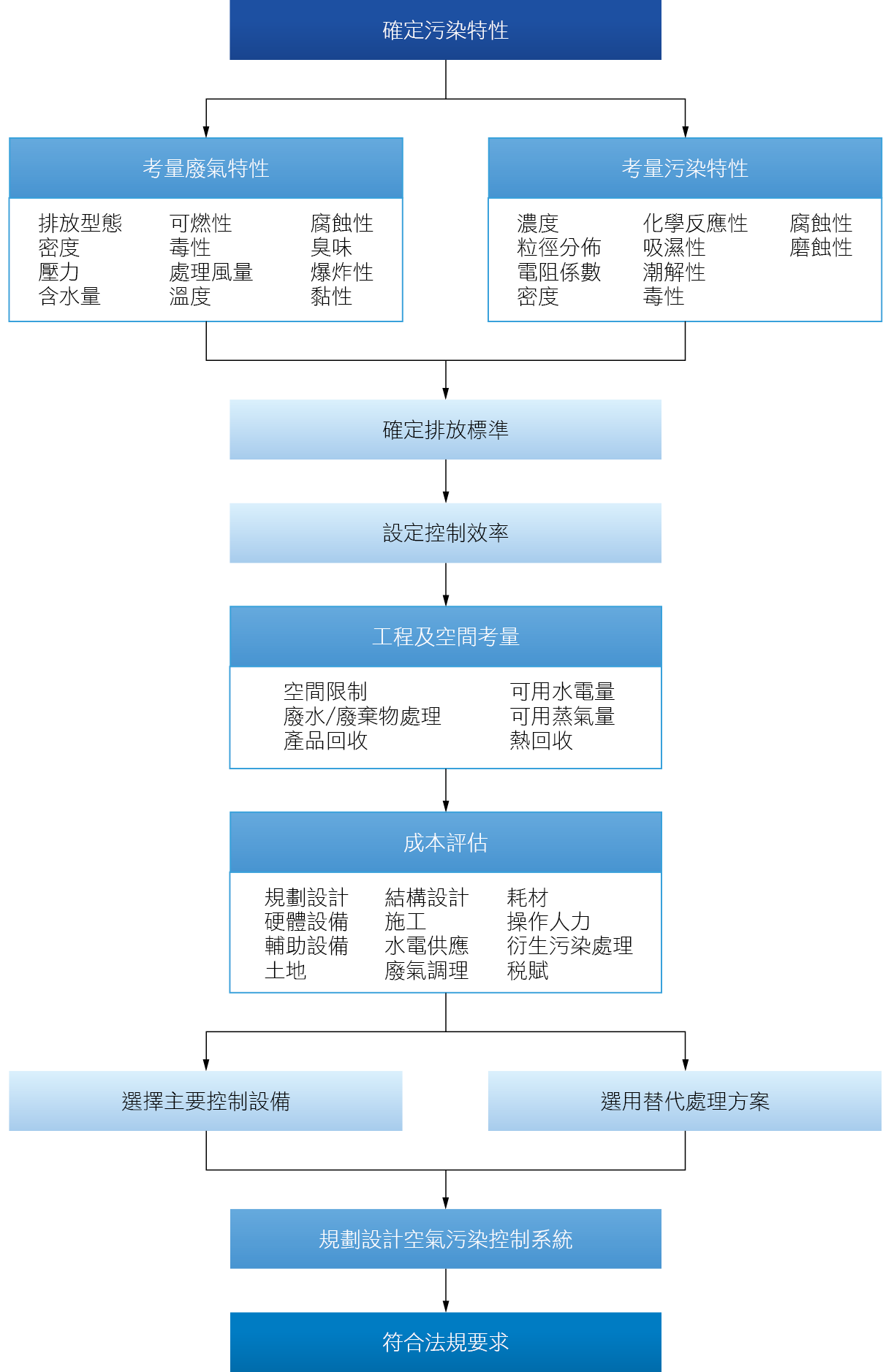
參考文獻
- 行政院主計總處,國民幸福指數年報,2016。
- 行政院環境保護署,認識細懸浮微粒( 初版),2015。
- 蔡俊鴻,粒狀污染物控制設備之評估與選用, 工業污染防治技術手冊之三十一,經濟部工業局,1991。
- 中山環工所,空氣污染控制與設計。
- 環訓所甲級空氣污染專責人員訓練教材。
- 司洪濤、郭志軍,空氣污染防制系統規劃設計與操作維護,2007。
- 李灝銘,空氣污染物之防制原理說明,2014。
- 國立台北科技大學,蘇暘堤,固定污染源空氣污染防制成效實場查核與管制之研究,2012。
- 余騰耀,總量管制空氣污染物削減技術手冊,經濟部工業局,2002
- 鄭宗岳、林鴻祥,空氣污染防治理論及設計,2005。
留言(0)