摘要

AMC智能監控應用於黃光Lens早期汙染預警防護及濾網效率檢測機制
前言
氣態分子汙染物Airborne Molecular Contamination(AMC)的控管,對於近年來發展迅速的半導體製程有著密切關係,為晶圓廠獲利中不可或缺的一環。尤其在黃光區,Scanner Lens機台是用來引導與控制曝光的光學元件,受汙染後的光學元件將產生霧化現象,如 圖1所示,造成機台對焦偏移問題,影響機台產品良率,如 圖2所示 ,並且影響光學元件壽命。深究其原因,往往沒有一套早期預警機制的建立。廠務端根據OI定義,無塵室內獨立迴風區需設置AMC Inline監控點來代表該區AMC的狀況,但並無法針對各機台進行把關。假設機台大量洩漏微汙染物時,第一時間無法知道對該區眾多機台影響情況,只能逐一進行機台濾網更換,並同時更換全區FFU濾網。此外也需出動巡檢人力以手持儀器或offline採樣方式對現場漏源進行偵查及防堵,流程如 圖3所示。如此耗時耗力,只因無法為機台提供早期預警。故廠務工程師與設備工程師首次合作,在Scanner Lens前端進行AMC即時監控,為提供給Lens的潔淨空氣進行有效的把關。
圖1、受AMC汙染的Lens產生霧化現象
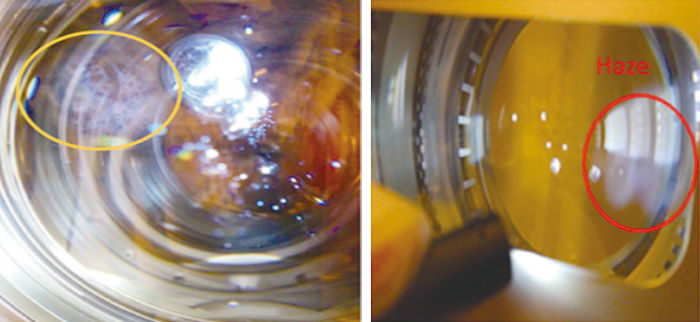
圖2、Lens霧化,影響製程良率
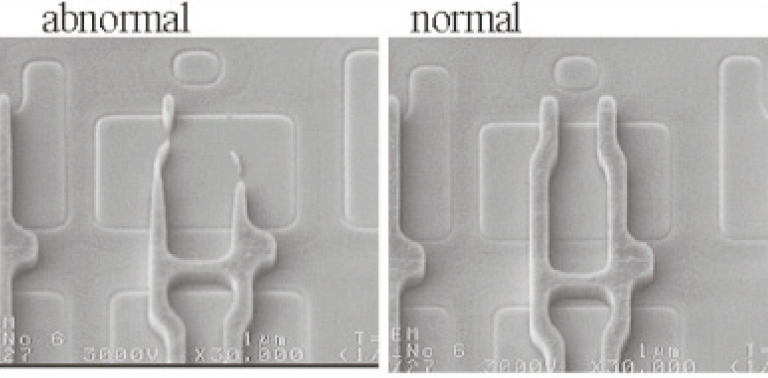
圖3、未導入AMC濃度分布圖前,AMC異常時需耗費人力進行現場漏源巡檢以及全區濾網更換
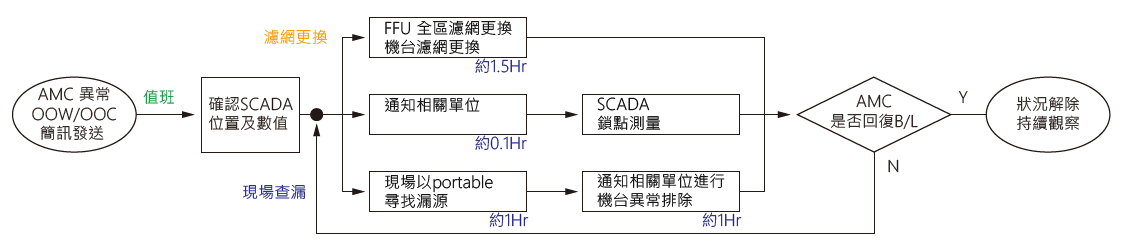
文獻探討
回溯過去,供應給黃光區機台內Scanner Lens的潔淨空氣,若含有雜質及有機物則會在Lens表面上產生結晶,當惡化到一定程度時需以特殊藥水清潔Lens表面結晶,但如果供應給Lens的氣體持續受汙染只能進行更換,且更換價格昂貴,造成鉅額損失[1]。為確保導入Scanner機台內的潔淨空氣不受AMC影響,早期設計經由廠務系統CAS(Clean Air Supply)經由ACC(Air Control Cabinet)直接供應MA(Makeup Air)進入Scanner機台內[2]。ACC主要為控制溫度供應給Scanner之單元設備,如 圖4所示,位於Clean Room 2F Sub-FAB。在CAS system風管出口端設置AMC採樣點即可監控下游端進入機台內AMC濃度現況[3],如 圖5所示。但是CAS供應給Scanner Lens的潔淨空氣容易受CAS停機及外氣條件變化影響供應溫濕度 、及AMC等現象,故後期廠務淘汰CAS供應方式,改在ACC前端設置Local Filter,環境空氣先經由Local Filter後再進入ACC內的Charcoal Filter兩道關卡後,提供乾淨空氣再進入Lens內。機台環境MA經由Local Filter後經由ACC供應至機台內,除了可降低外氣條件或CAS切換機對Scanner的影響外[4],也防止該區機台因PM過程中機台產生的微汙染物影響Lens。至於各ACC入口處則使用手持儀器進行人力巡檢,確認有機物濃度是否正常[5]。
圖4、ACC(Air Control Cabinet)示意圖,內部安裝Charcoal Filter
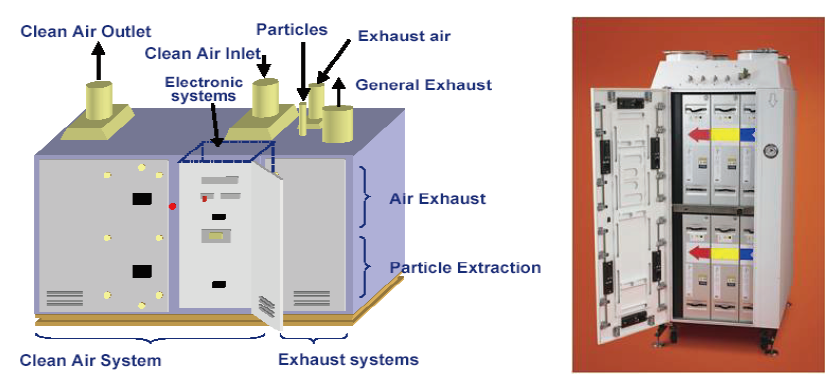
圖5、CAS系統供應ACC潔淨空氣示意圖,風管內設有AMC採樣點
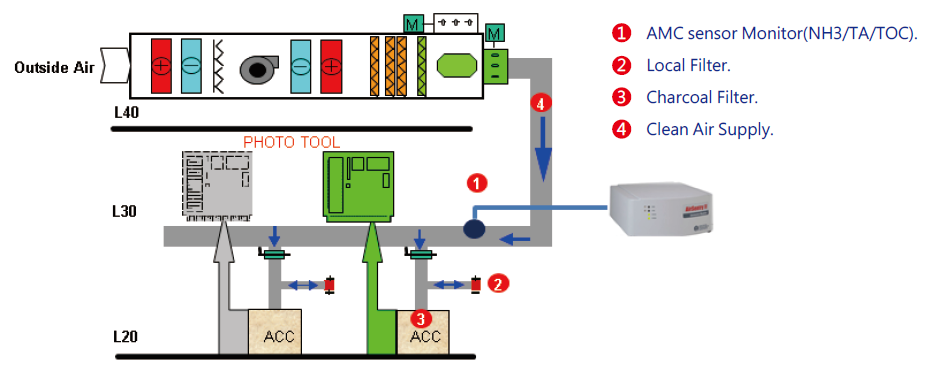
此外濾網與零件相同,皆受使用年限的限制,濾網吸附飽和後將喪失過濾效能,若無法在效能降低前更換濾網,機台將受環境AMC汙染[6]。如何有效確認供應Lens的潔淨空氣不受AMC汙染將是我們本研究改善的重點。
研究方法
ACC擺放於黃光區2F,既有的AMC採樣點設置在環境 ,以往當黃光區2F環境AMC讀值偏高時除確認外氣是否異常外,另外必須藉由手持儀器現場確認是否有漏源。在troubleshooting的過程中,若環境已受汙染,那ACC內部濾網效率如何?進入Scanner內的潔淨空氣AMC品質是否正常?往往都到是否影響產品良率才能得知。
根據以上情況,廠務工程師率先與設備工程師合作,希望能以即時偵測、濾網防護以及早期應變三個方向進行改善,目標及預期成果如 圖6所示。依照與Scanner設備談定alarm標準,如 表1所示,主要測項為TA、NH3及TOC三種,採樣點設置在Local Filter後,若數值達到alarm設定 ,除了SCADA產生Alarm警報外,立即傳送簡訊給廠務值班及設備工程師確認機況是否正常來達到即時偵測的目的 ,完整黃光區機台架構及AMC佈點位置如 圖7所示。
圖6、ACC AMC監控期望達到即時偵測、濾網防護、早期應變的目標
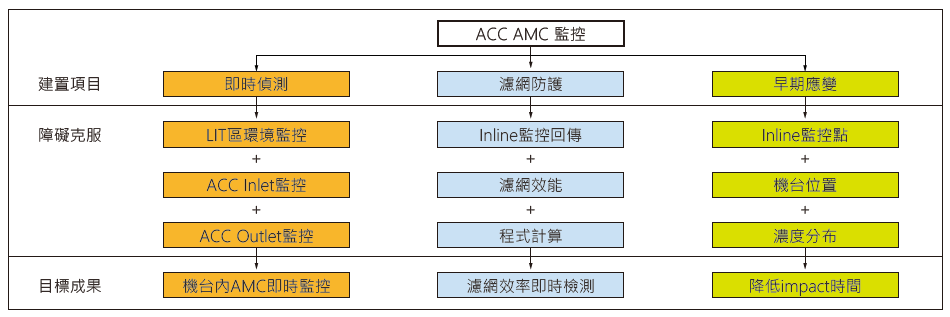
Item | Spec | ||
---|---|---|---|
TOC | NH3 | TA | |
Local Filter outlet concentration | <12ug/m3 | <1ppb | <1 ppb |
圖7、黃光區ACC及機台完整設置及AMC監控佈點
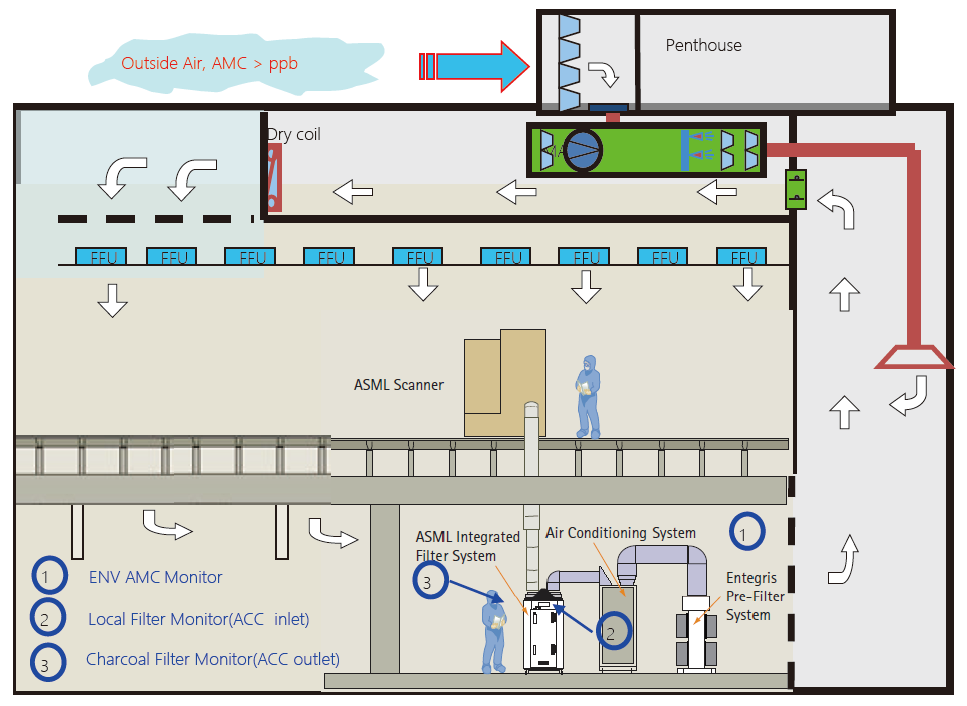
另外針對濾網效率,目前依據OI規定以time base計算更換周期為一年,容差為30天。依據ITRI提供之濾網性能曲線,以甲苯為例,如 圖8所示,以高濃度9.12ppm測試濾網,以初始效率95.3%降至90.0%,約經過1260分鐘,計算吸附量約為191,520ppb*Hr,若以黃光區2F TOC濃度約20~30ppb,換算濾網壽命約為9,576~6,384Hr。故若該區環境常因PM等因素造成環境TOC濃度常常偏高至30ppb以上,濾網使用效率不到8,760Hr將低於90%,即Lens亦有可能受到環境AMC異常汙染。
圖8、濾網效能曲線圖,圖為Local Filter針對苯甲過濾之效能曲線
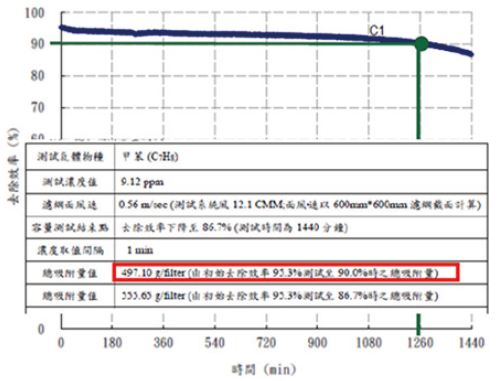
故在濾網防護部分,利用每次Inline的讀值來計算濾網吸附量,可顯示濾網效率殘值,如此一來,可針對部分ACC常暴露在濃度稍高於環境的濾網效率進行把關外,若發生異常時,亦可優先針對效率殘值較低的濾網進行更換來達到濾網防護的功能。
此外在早期應變方面,應當以立即防堵為首要工作,若能減少影響時間則可將產能損失降到最低。在偌大的無塵室裡,AMC微汙染物看不見、摸不著,只能依靠手持儀器數值告知可能方向及位置,此過程往往耗費大量時間及人力。利用廣布的採樣點,結合成一張濃度分布圖,利用濃度的細微變化,便能在短時間內判斷漏源位置,來達到即早應變的功能,如 圖9所示。
圖9、導入系統自動化濃度分布圖
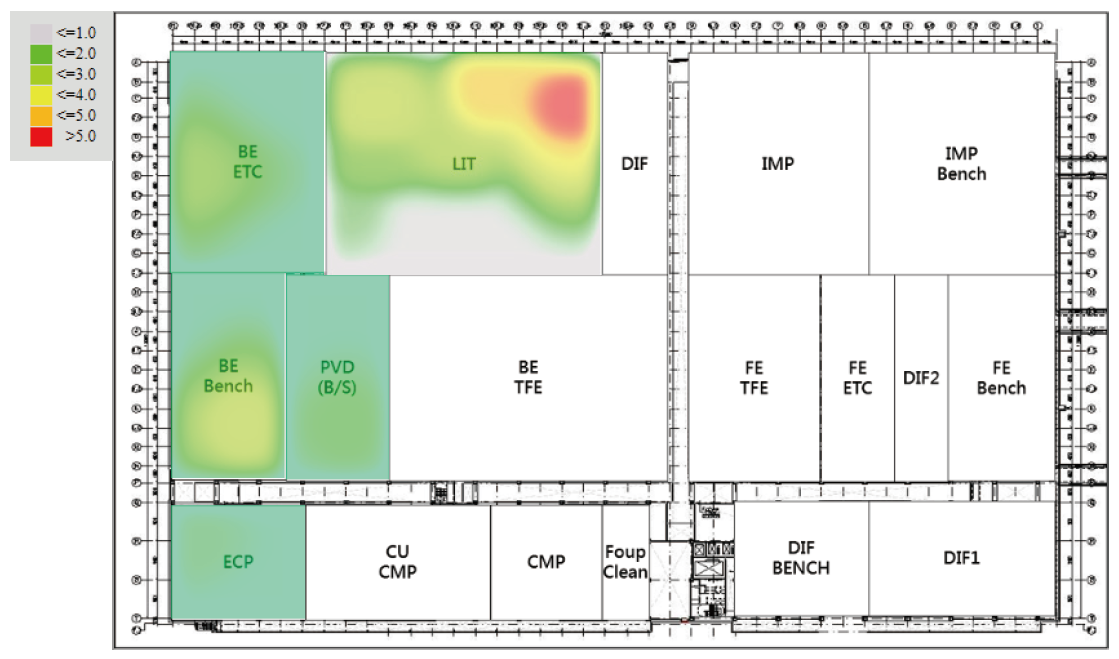
結果與分析
即時偵測回傳及簡訊通知到相關單位,可讓現場人員第一時間確認機況及現場環境是否異常,如 圖10所示, ACC自上線以來Alert次數逐漸降低,歸功於簡訊的通知可使設備工程師PM時,加強自主防護的結果,避免觸動簡訊發送。
圖10、AMC即時監控ACC觸發alert次數統計,上線後次數逐漸遞減
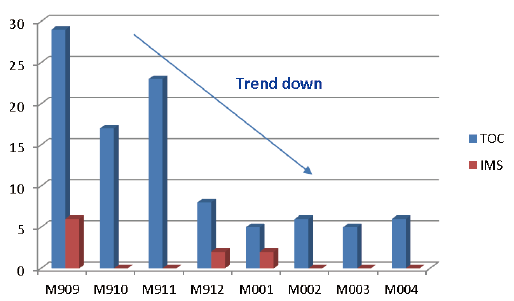
目前除了已將黃光區2F採樣點數值回傳於SCADA管理以外,針對濾網效率部分也進行即時運算,如 圖11所示,在更換Local Filter後,SCADA便會根據環境與Local Filter後的數據與時間計算濾網吸附量,呈現出濾網剩餘效率,剛更換後的濾網效能仍有99%,隨使用時間逐漸下降, Trend chart,如 圖12所示。當數值降低時,可設定Pre- alert進行提醒,當作是否更換濾網的參考依據,亦能針對各ACC機台濾網效率進行把關。
圖11、濾網效率計算呈現於SCADA內
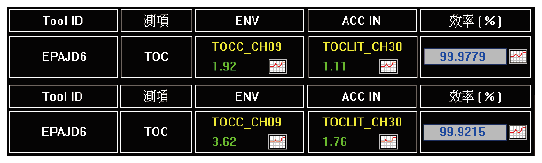
圖12、濾網因吸附損失之呈現逐降下降趨勢
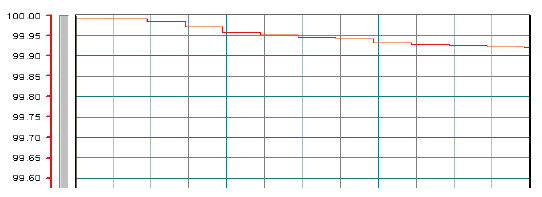
利用回傳的AMC inline數值上傳到SCADA數據庫,將個數值結合成一張濃度分布圖,為ACC inlet端監控點位結合而成,雖不能代表實際環境現況,卻能透過濃度細微變化確認該區環境是否有異常。以TVOC為例,黃光區TOC 濃度便可一覽無遺,濃度分布圖可與機台位置對應後,若為機台異常影響,便能第一時間以視覺判斷哪些機台是否有影響環境的疑慮,如 圖13所示。此功能上線後,便可省去大部分時間進行現場異常巡檢,達到早期應變的目的,縮短impact時間,流程如 圖14所示。
圖13、手動導入機台位置呈現濃度分布圖
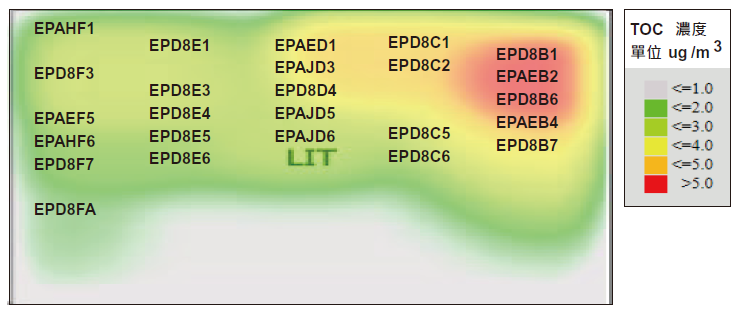
圖14、導入AMC濃度分布判斷後,可節省trouble shooting時間,使AMC異常影響時間大幅降低
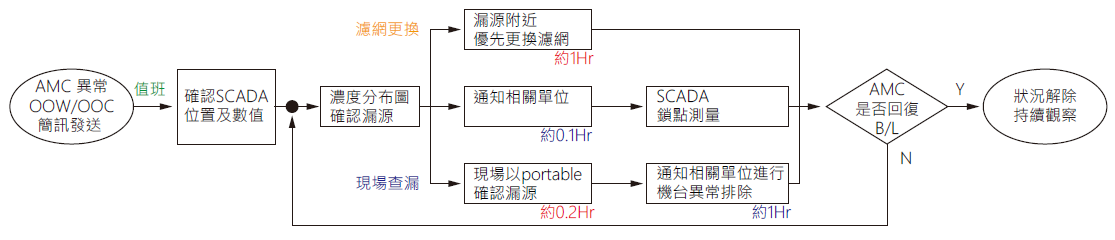
結論
黃光區ACC導入AMC即時監控後,簡訊發送可使現場第一線人員確認機台是否有異常,執行數月下來簡訊發送次數已減少。另外因濾網效能可即時反應,避免濾網效率降低汙染Lens,目前亦增加總硫(TS)的監控於ACC端,此方式已準備登錄BKM並Fan out到其他廠區。另外黃光區導入濃度分布圖判斷後,藉由濃度變化可預判環境是否有異常現象,若遭遇異常洩漏等突發狀況,藉由濃度分布的預判可將impact機台時間縮短1~2Hr。如前面章節所述,現階段自動導入的濃度分布可針對大環境確認AMC情況,再以手動方式導入機台位置,便可更精準監控機台AMC情況及計算汙染源位置。故目前已與廠商合作開發以演算法方式導入濃度分布圖於SCADA內,不但可以整併機台位置與濃度分布圖,並能即時新增或修改Inline點位更新於SCADA系統,範例如 圖15所示,更方便系統工程師維護及應用。
圖15、利用演算法於無塵室內呈現AMC濃度分布

參考文獻
- Kychen,Gas sample for local filter & Charcoal,EKM Document No. 82430.
- 張文龍,ASML Scanner ACC架構與溫濕度控制研究,EKM Document No. 48770.
- 施文彬,Stable Air Condition to ACC,EKM Document No. 80390.
- 田浚致,F14 Local filter取代CAS之效益評估,EKM Document No. 70832.
- 林孟學,Charcoal filter TOC measure tool,EKM Document No. 87754.
- 劉興學、鄧志偉、蔡春進、李壽南,應用化學濾網去除某晶圓廠黃光區潔淨室的氨氣,工業安全衛生月刊27,2018。
留言(0)