摘要
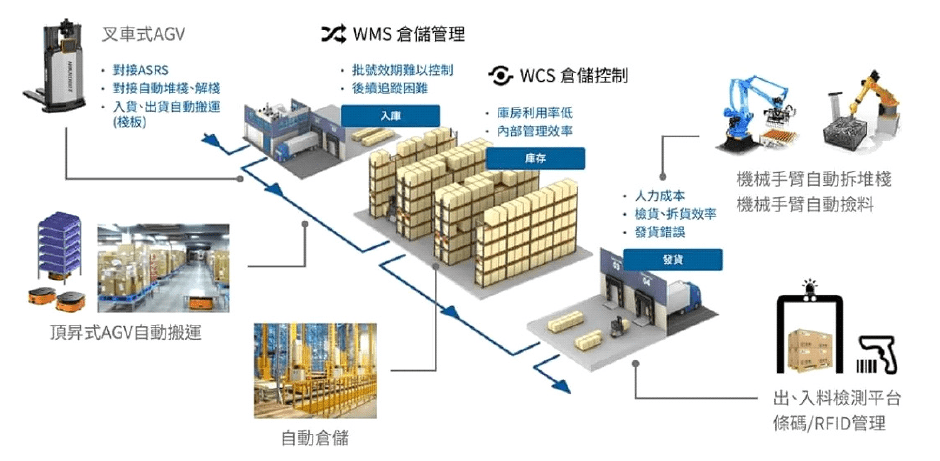
庫房永續管理
Keywords / FAC Warehouse2,Sustainable Warehouse Management
近年來廣受討論的大數據分析、AI技術、自動化設備,以及物聯網等領域也在倉儲物流作業中得到積極地運用。企業主必須能彈性的調整策略與方向來迎接市場上不斷改變的需求。倉儲庫房是支持企業穩定發展的關鍵之一,如何善用新技術與更新思維來實現庫房永續管理的目標是本文欲與各位分享的重點;其中包含了市場上已投入的新技術、新工具,以及目前廠務庫房正積極推動的優化作業等。21世紀正邁向第三個十年,廠務庫房同步於公司的穩定成長,作業管理必須更智慧化,系統必須更敏捷,目的為提供廠務同仁更高效且友善的倉儲物流服務以達成穩定運轉,快樂廠務的目標,同時實現庫房永續管理的境界。
Big data analysis, AI technology, automation equipment, and the Internet of Things, which have been positively discussed in recent years. Logistics operations have also been actively applied as well. Business owners must be able to flexibly adjust strategies and directions to meet the ever-changing needs of the market. Warehouse is one of the keys to support stable development of enterprises. How to make good use of new technologies and updated thinking to achieve the goal of sustainable warehouse management is the focus of this article to share with you. Which includes new technologies and new tools that have been put into the market. Some of the optimization actions are taking by the FAC warehouse now. The 21st century is moving forward to third decade. FAC warehouse is growing simultaneously with our company's stable growth. Operation management must be smarter and related systems must be more agile. The purpose is to provide FAC colleagues with more efficient and friendly services to achieve the goal of stable operations and happy FAC. At the same time, to realize the realm of sustainable warehouse management.
1. 前言
1.1 倉儲管理在工業發展中扮演的角色
自西元1760年代,一直持續到1840年代的時期(圖1),物料生產開始轉向新的製造過程,逐步出現以機器取代人力、獸力的作業,邁向大規模的工廠生產,徹底擺脫人類發展史中的馬爾薩斯陷阱(註1);如此的工業革命開展了往後數百年間繁榮的經濟發展。其中倉儲管理在各個供應鏈中扮演策略性的角色,能穩定提供庫存配送、分類,以及加工處理,以期滿足快速成長的市場需求。
圖1:工業革命沿革
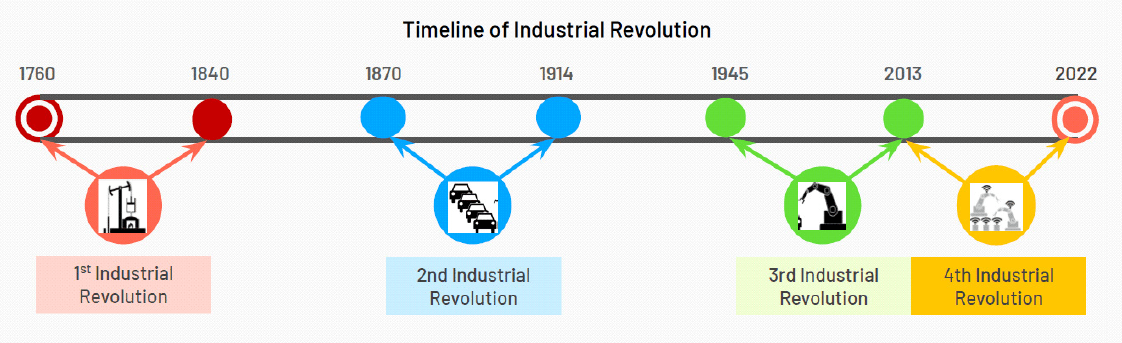
(註1) 馬爾薩斯陷阱,又稱為「馬爾薩斯災難」,以政治經濟學家托馬斯·羅伯特·馬爾薩斯命名,認為對大部分人類歷史來說,收入停滯的原因是因為技術的進步與發現僅僅造成人口的增加而沒有提高人類的生活水準。
以下列舉倉儲庫房在工業發展進化中扮演的七項主要角色與功能:
- 穩定確保產線與客戶端的物料/ 商品供給需求
- 專業保管並妥善分類不同之物料/ 商品以維護品質
- 掌握並調整物料/ 商品入出庫周轉稼動率協助成本最適化
- 高效能提供分檢及集貨服務以承接後段物流配送
- 彈性配合簡易加工服務
- 串接上下游資訊提供整體資料鏈全貌
- 針對敏感性物料/ 商品進行發表前之保密保管
倉儲物流在工業發展進化中有著舉足輕重的重要性,特別是過去幾年來全球遭遇供應鏈不穩的危機,更凸顯完善的倉儲物流服務在企業永續經營中扮演的角色。
1.2 倉儲庫房管理的演進
以傳統的人力來管理並執行倉儲作業的模式已持續了非常久的時間,直到二十世紀末隨著資訊工具以及自動化倉儲設備的突破性發展才讓傳統的倉儲管理有跨時代的進步。過往人工的進出料登帳演化成由二維/三維條碼掃描、RFID感應並結合WMS (Warehouse Management System倉儲管理系統(圖2)) + WCS (Warehouse Control System倉儲設備控制系統(圖3))系統來管理;ASRS與AGV、機器手臂、AMR等自動化設備也逐漸取代人力的作業來提升倉儲作業效率。
圖2:WMS系統圖示
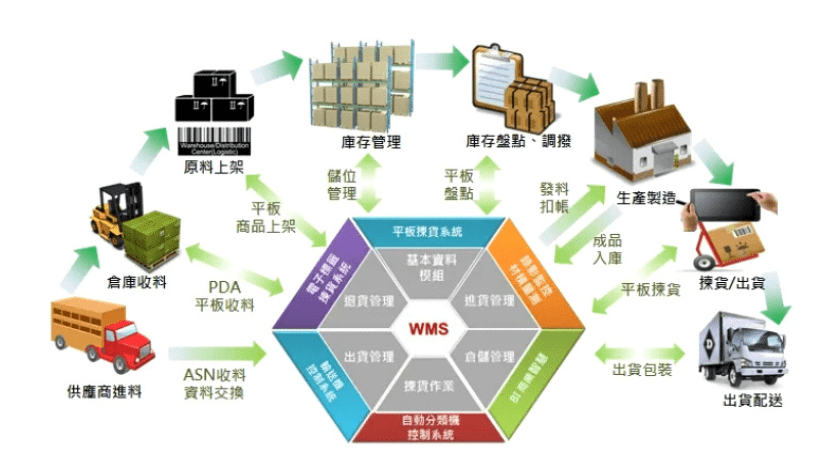
圖3:WCS系統架構圖
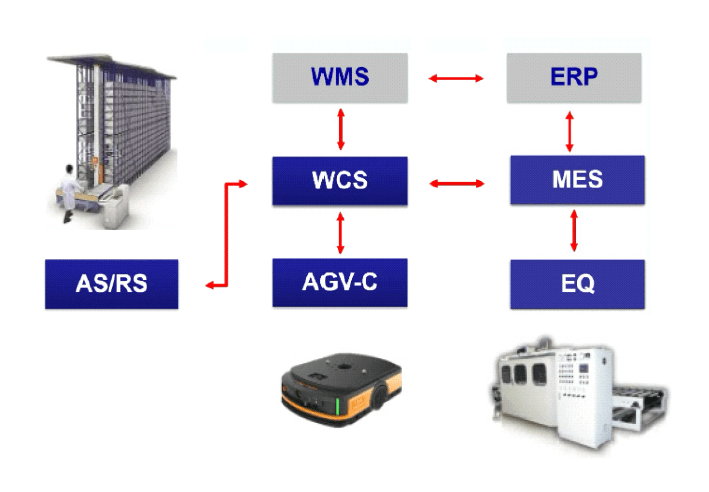
倉儲管理在未來會更進一步運用AI技術,如Digital Twin,結合大數據運算及先進的感測技術,更加智能化的提前判斷需求,提供管理者做出適當的因應。
2. 案例探討
2.1 人為錯誤(Human error)
長久以來倉儲產業的升級較不受重視,仰賴大量的廉價人力進行日常進出貨作業;其基層人力多來自社會的中下層,因整體薪資不具競爭力,勞動強度高,以致人員流動率高,業主在投資人員訓練的意願薄弱。
大量的人工作業導致管理困難,間接形成ESG公司治理的隱憂。
發生於2022年3月在桃園市楊梅區的家樂福倉儲大火(圖4),起因為倉儲工人於作業時違規吸菸所導致,損失高達新台幣39億元。
圖4:樂福家楊梅倉儲大火
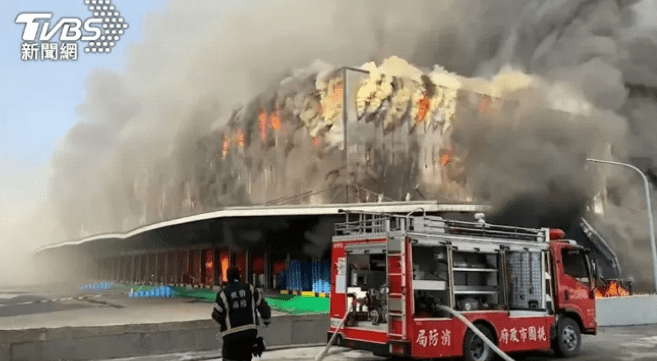
2019年2月發生的嘉里大榮物流中心火災(圖5)造成3名越南籍移工死亡,1人重傷,其起因也是廠內人員私自跨接電器造成電器火警而引發。
圖5:嘉里大榮倉儲大火
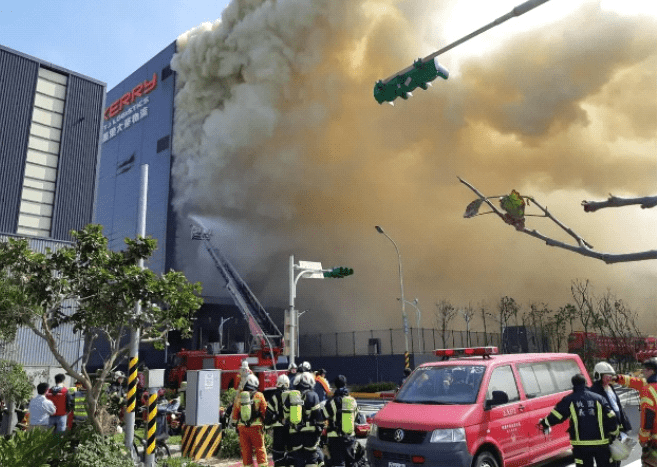
除上述兩案例外,其他因人為錯誤而招致的各種倉儲作業意外更不勝枚舉,在庫作業的人力狀態實為倉儲管理的風險因子。
參差不齊的人力素質在管理上有高度不確定性,以致重複發生人為錯誤;小則進出料發生帳差,大則嚴重的工安意外。近年來少子化的趨勢更招致傳統的倉儲業者面臨招募困難,在人力短缺的情況下,未能將作業現代化的倉儲,其單位人力的作業強度倍增,更提高發生人為錯誤的機率,造成惡性循環。
因此,如何善用自動化設備取代基層人力作業已是倉儲管理中最基本的要求。
2.2 前瞻思維(Forward thinking)
全球電商巨擘亞馬遜Amazon配合電子商務的業務推展,在自主倉儲技術的發展方面上領先同業甚多;這間2022年出貨量超過50億件包裹的公司,繼2012年收購機器人公司Kiva後持續研發倉儲機器人,首款全自動移動機器人Proteus已正式服役於日常作業中,針對自身作業需求量身打造。(圖6)
圖6:亞馬孫AI倉儲機器人亮相,物流全面自動化
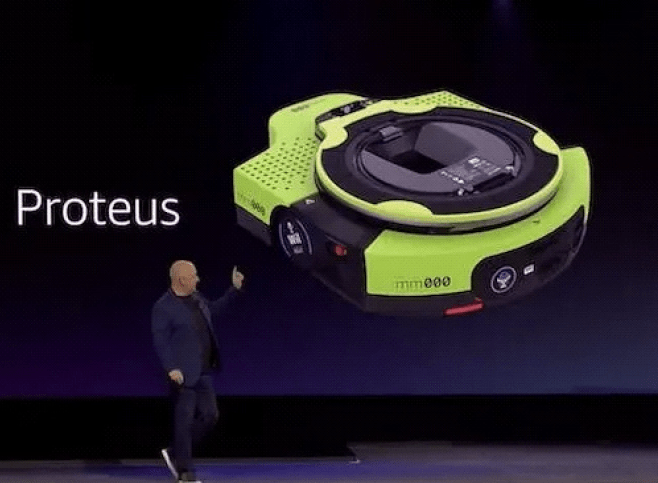
另外名為Cardinal的機器手臂可舉起50磅重的包裹並運用AI及電腦視覺系統準確挑選單一指定包裹放置到物流籠車或輸送帶上銜接後續作業。(圖7)
圖7:由Amazon Robotics打造的機器人-Cardinal
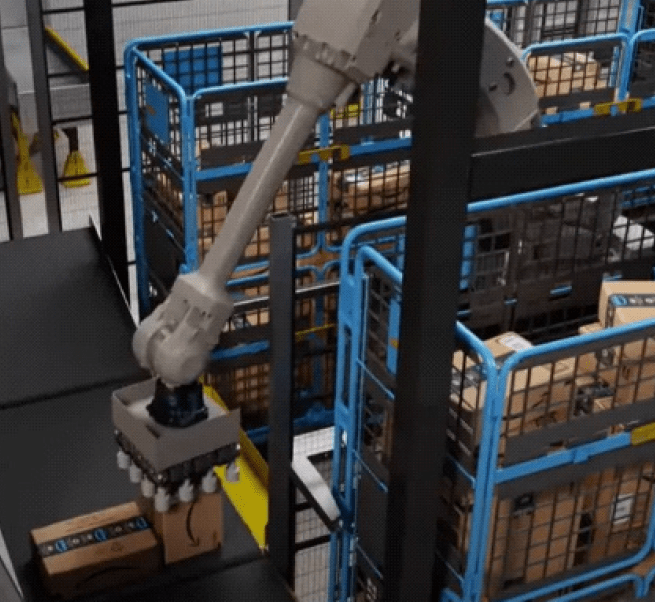
亞馬遜還設計出Amazon Robotics Identification (AR ID)結合電腦視覺及機器學習以省去人力掃碼的作業。作業流程中還有一個負責辨識與存取裝箱容器的系統: Containerized Storage System來負責把已經分類完成的物流箱放置到儲存櫃位交給作業員工,除了可大量減少倉儲人力配置,避免勞安風險外,對於提升作業的正確性也有顯而易見的正面效果。
亞馬遜針對倉儲作業管理投入大量資源,並以具前瞻性的規劃支持其積極的業務拓展,維持市場優勢迄今。
2.3 倉儲管理數位化(Warehouse digital management)
近年來順應ESG議題,倉儲管理也積極邁向數位化的推進。數位轉型前必須先思維轉型,在人力資源上投入教育訓練,廣泛利用已成熟的IT技術與SaaS服務,結合IoT物聯網及相關感測設備針對各項倉儲作業做出數據分析,以使管理者依據客觀數據做出最合適的工作安排,同時可回饋給客戶端分享需要的資訊來確保供應鏈的安全;「經驗」一詞將不能再是工作安排的依據。DHL在全球的快遞運輸以及倉儲服務上投入大量的資源來發展倉儲物流數位化的技術;藉由這樣的運用,DHL始終是業界所公認的領頭羊,ASML、KLA、Lam Research等第一流的半導體設備供應商都與DHL合作使用其提供第三方物流服務。(圖8)
圖8:利用影像辨識進行揀貨作業

3. 庫房永續管理的關鍵工具
3.1 數位化Digital + 智慧化Intelligent
倉儲作業管理成千上萬種不同料件,在服務需求不斷提升的現代面臨更高的挑戰。Zebra Technologies的《2022年全球倉儲願景報告》針對管理、倉儲配送中心維運狀況,訪問企業版圖橫跨北美、拉丁美洲、歐洲與亞太地區的製造、零售、運輸、物流和批發等業者,受訪的1,500多名決策者及員工中,高達80%表示,未來將透過倉儲自動化因應挑戰。逾60%的決策者表示,未來五年內將提高倉儲庫存、資產及供應鏈可視化有關的技術投資;高達90%的受訪者認為,未來五年內,感測和機器視覺等技術將更為普及。
在後疫情時代,全球面臨供應鏈不穩的挑戰,物流產業除了加速數位轉型的工作外,擴大倉儲智慧化的運用可以協助業主以精簡的人力完成繁雜的庫內作業,提升品質,並即時紀錄相關數據以沉澱寶貴的資訊供管理者做出正確的決策。利用數位化技術結合智慧化的自動化設備將會是庫房實現永續管理的關鍵方法。智慧倉儲含蓋許多面向,需要資訊化系統串接、物聯網及機電一體等條件相互搭配,更重要的是高素質的管理人才。除了要能熟悉相關設備及系統的操作之外,管理者對於利用AI技術所輸出的資訊要能有效的利用及解讀,將投入的資源極大化,方能發揮智慧倉儲的效能,永續彰顯其價值所在。
典型智慧倉儲運用的相關設備有下列六大類:
- GTP(Good to Person) : 包含輸送機、分揀轉盤及垂直升降系統。
- AS/RS(Automated Storage/ Retrieval System) : 自動化倉儲料架。
- AMR(Autonomous Mobility Robot) : 自主移動機器人。
- AGV(Automated Guided Vehicle) : 無人搬運車。
- Pick-to-Light/Put-to-Light System : 電子標籤 揀貨系統。
- Automated Sortation System : 自動化分揀系統。
利用數位化技術加上智能化設備的智慧倉儲可以減少超過40%人力,物料進出庫時間約減少60%,整體產能相較於傳統人工倉可提升10倍以上。在勞安與相關作業品質上的提升更是實現永續管理的最佳解答。(圖9)
圖9:自動化倉儲設備及系統示意
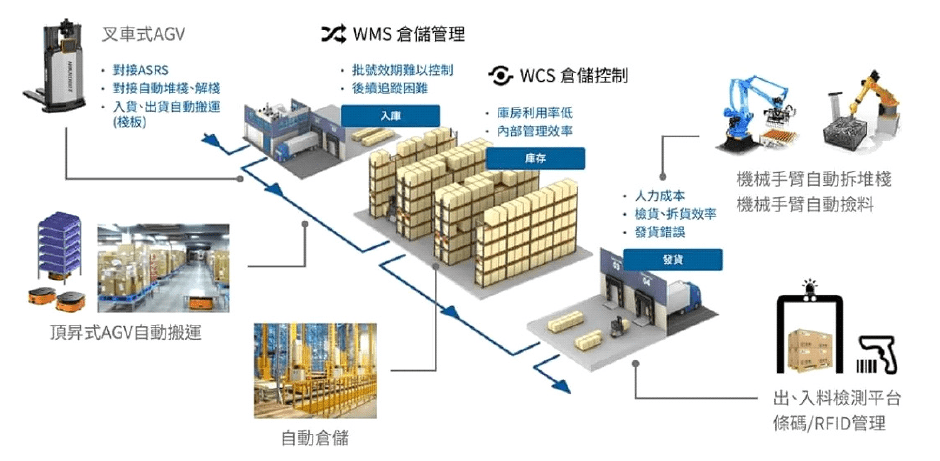
百事可樂PepsiCo於美國的物流倉儲中心廣泛使用NVIDIA的IoT感測技術,結合系統串接,使輸送帶能依照作業時的覆蓋率及負載狀況自動調整速度,來配合檢查員作業。(圖10)
圖10:美國百事可樂倉庫利用數位雙生技術,自動調節滾帶運行速度
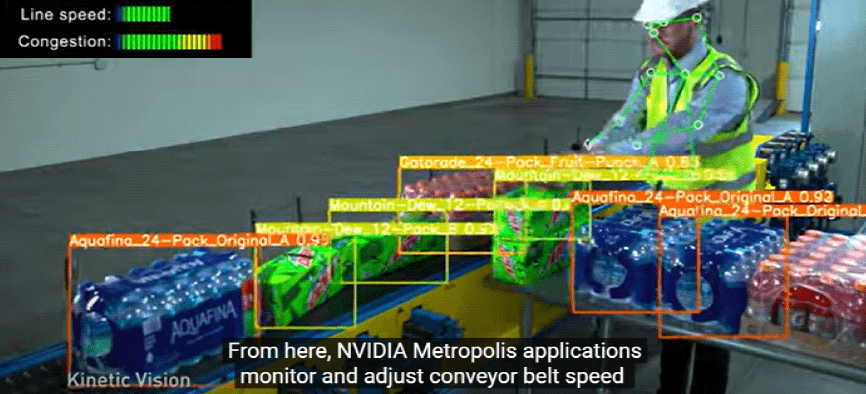
3.2 數位雙生Digital Twin + 軟體即服務SaaS
實現庫房永續管理的關鍵方法,除前述的自動化設備及數位化資訊串接之外,能否善用更智能化的中心系統來因應隨時變動的庫房作業是其核心。庫房的進出料與儲放作業是根據上游供應商及下游客戶需求來做最適化設計;但這些需求會隨景氣與各方策略而隨時改變,庫房必須具備彈性做出調整。利用Digital Twin以及SaaS的服務可以在不影響現實作業的狀態下精確模擬調整後的結果並且以較低成本來彈性使用合適的管理系統滿足需求。
3.2.1 數位雙生Digital Twin
Digital Twin 一詞由美國密西根大學的Michael Grieves教授,於2003年在他所講授的產品生命周期管理課程上引入,並且於2014年在其所撰寫的白皮書中進行了詳細的闡述。
Digital Twin 是以數位化方式為物理對象創建的虛擬模型,來模擬該物件在現實環境中的行為。簡單來說,就是在實體與數位世界之間搭建橋樑,並透過數據無縫傳輸,使一件物品、甚至生物,同步存在於實體與虛擬世界中。
印度知名市場研究機構Research Dive於2022年六月發佈的調查報告指出,全球數位雙生市場預計從2021年到2030年,以39.48%的年複合成長率成長。(圖11)
圖11:數位雙生技術發展預測

Digital Twin會持續回饋現在正產生的資料及數據,實體設備當下的運作狀態可以同步投射到數位雙生系統之上,因此庫房的管理者,可即時在遠端監控庫房的重要設備與現場作業狀態;未來若有需要更改或安裝新設備(例如安裝新的機械手臂或是擴充AGV作業站)時,可先透過數位雙生技術在虛擬環境模擬運作,在不影響當下現實作業的情況下,確認調整後的運作是否符合預期效果。
全球知名的發動機製造商勞斯萊斯(Rolls Royce)利用Digital Twin建置管理平台,為每具出廠的發動機預先產生一組數位雙生,實現遠端監控個別發動機的即時運作狀況,並同步蒐集相關數據協助優化運轉時的燃油效能與廢氣排放;除此之外,個別發動機何時該進行保養檢修,該注意何種零件耗損,也不再只是倚靠統一規格的技術手冊來做依循,因每具發動機的使用狀況各異,藉由同步監視其使用狀態並提供最適化的保修服務才能確保運轉安全,這些都來自Digital Twin的技術支持。(圖12)
圖12:Digital Twin應用範例
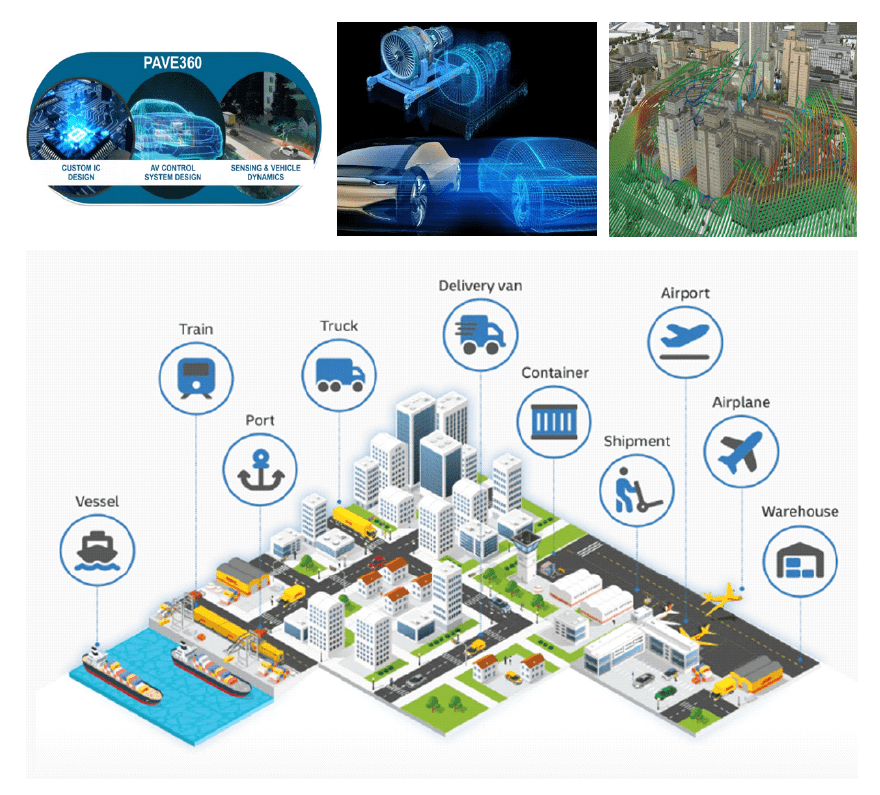
- 作業安全與設備維護方面:
- 透過數位雙生,得以在虛擬世界進行模擬,減少真人與實物測試成本。
- 可即時同步重要設備的運行狀態,掌握機具狀況並預估可能的風險,提早因應進而預防意外發生。
- 提供整體倉儲的量能監控,及時調整瓶頸項目,確保作業順行。
- 減少人員於高風險環境中的資料收集與作業評估,並確保資料回饋的準確性。
- 作業流程設計與改善方面:
- 利用數位雙生可提供更客觀的數據評估 *data-driven decisions*。
- 對於新方案的導入可以更大膽的設計與試行。
- 提升管理者對於整體作業實況的即時掌握能力。
- 預測性價值(predictive value):透過數位分身模型可以預測出實體模型的未來情境。
- Digital Twin運用的挑戰:
- 關於IoT物聯網的前期佈署與運用。
- Digital Twin運用規模的定義與規劃。
- 預算規劃及成效評估分析。
- 軟體/系統應用及5G數據快速傳輸介面的整合能力。
- 人力素質的訓練與養成。
- 協力廠商的系統整合。
3.2.2 軟體即服務SaaS
SaaS中文稱之為「軟體即服務(Software-as-a-Service)」。(圖13)
圖13:Software as a Service

就是使用者向雲端供應商「租借」服務(軟體),透過網路訂閱,線上支付與下載,就能擁有 SaaS 應用程式的使用權;可相當程度精簡自有IT團隊的規模,並節省一次性軟體買斷的費用,後續還需要自行面對軟體維護與更新等問題。
SaaS 平台的運作大致有以下 3 個流程:
- 由SaaS供應商開發一系列完整的軟體設備,並為使用者搭建前期所需的實施與服務。
- 企業、個人使用者向 SaaS 供應商「訂閱」所需的軟體設備,並通過網路使用系統,使企業免去購買軟硬體、招聘專業人員的額外花費,也讓個人使用者,解決缺乏資源的問題。
- SaaS供應商將負責所有後期的軟體維護等一系列服務,並持續更新軟體設備,以提供使用者更好的使用體驗。
庫房作業的永續管理需要高效率的WMS系統支持,善用SaaS服務可以在節省人力管理與IT軟體成本的狀況下享受以下的優點: (圖14)
圖14:SAAS 應用優勢
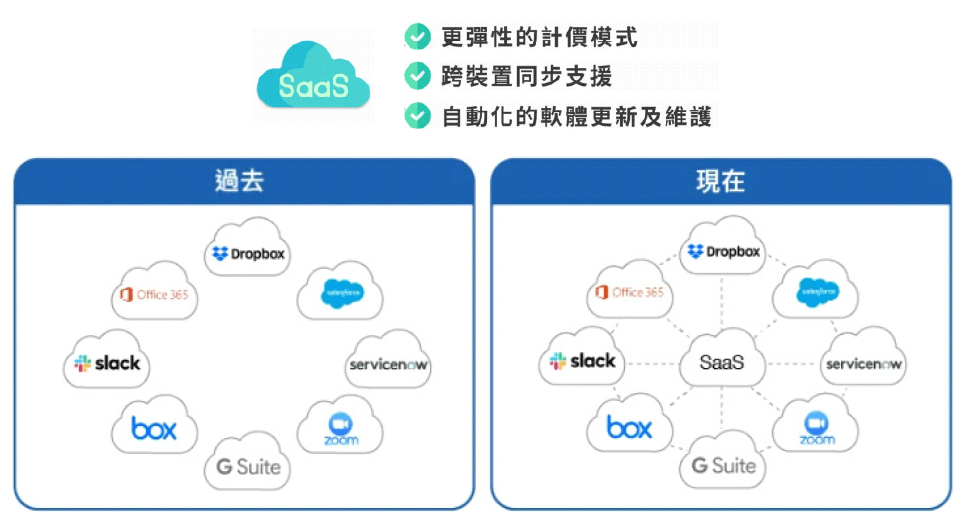
SaaS雲端企業服務的實例有: Microsoft Office 365、Google G Suite、Salesforce、Slack等廣大的使用基礎;在WMS方面,市場上也有許多客製化的選擇可以提供量身訂做的服務,並且擁有彈性的計價模式。
SaaS WMS具有開放的應用程序編程接口(Open API),能輕鬆與不同系統對接及整合,當市面上出現新的軟件或平台時,SaaS WMS能在短時間內進行對接。同樣地,要連接公司現有的ERP/SAP系統,SaaS WMS也能輕鬆配對。
簡單來說,針對庫房管理的需求可以考慮使用SaaS WMS提供的彈性訂製服務來建置便捷且即時的管理系統,省卻IT人力招募與Server等硬體及軟體購買成本,並能同步市場上最新的技術,可以有效邁向庫房永續管理的目標。(圖15)
圖15:SAAS 使用效益
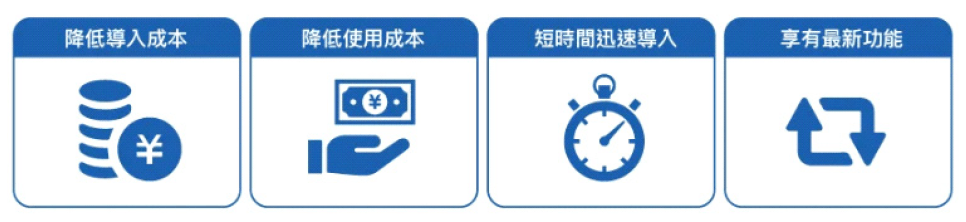
4. 關鍵管理
庫房基本的作業大致上包含了: 入庫、倉管、出庫三個大項目(圖16);其中各涵蓋許多細部作業並相互串聯。本文暫不針對逐一細項進行說明,僅分享實現庫房永續管理的關鍵因素,強調善加利用前文提及的工具及思維在管理層面上完善規劃,獲得1-10-100的作業效率。
圖16:倉儲管理作業內容

4.1 敏捷化作業流程
庫房建置的主要目的為確保物料的供給安全與配合下游需求進行入出庫與庫存管理,首先管理者必須針對主要需求做出明確的分類與分析,利用工具將需求數據化管理並訂出清楚的流程與目標以求整體效率提升與優化使用者/ 客戶體驗,這部分將藉由廠務庫房近期之重點作業為例來向各位加以說明。
廠務庫房主要任務為提供廠務單位可靠的倉儲物流服務,以達成穩定運轉,快樂廠務的目標。除一般的庫房任務外,積極進行優化的作業有以下四項:
- 簡化作業流程:統一由廠務庫房開立領料單(MR),每月廠務單位約減少開立共776張領料單(MR)共1,891個項目,節省廠務過去自行開立領料單(MR)作業時間。
- 善用Power BI工具:將庫房營運之庫存、領用、盤點等數據以Power BI 工具進行分析,針對不同項目建立個別資料庫持續收集數據,以數位化及客觀 數字更精準的進行作業規劃與管理。(圖17)
圖17:Power BI 資料分析範例
- 優化領料作業:廠務庫房目前管理超過270個線邊倉,領料過程需事先聯繫並互相配合,造成耗時費力不效率。現已規劃RFID無人倉並預先整合PM所需套裝料件(保養包),提供領料單位更友善的一站式服務。(圖18)
圖18:領料流程優化說明
- AI影像辨識:建立廠務物料的圖像資料庫,以方便使用者進行搜尋比對,避免錯料失誤發生。現已完成超過4,800種物料建檔,使用者可於FAM系統中以料號搜尋物料圖像,同時利用AI比對技術將相同物料卻被賦予不同料號的物件進行整理。(圖19)
圖19:FAM系統物料主檔可呈現該搜尋料號影像
4.2 智能化物流中心
隨著新建廠房的增加與廠務運轉的需求,建立一座高效能的智慧物流中心來整合目前的庫房業務已是勢在必行的任務,庫房永續經營必須要以智能系統取代傳統人力,以數位化及AI的分析替代過往經驗,以先進的WMS系統靈活串接上下游資訊實現敏捷的作業路徑。廠務庫房正積極規劃建立智能化物流中心來提供廠務第一流的服務。新建立的智能物流中心將配備自動化倉儲料架、無人搬運車、自動分揀機、機器手臂等自動化設備,結合量身訂製的WMS系統串接FAM上下游資訊,並搭配規劃於各FAB的RFID無人倉來大幅降減人力作業並提升整體效能,同時為將來成長的廠務需求做出準備。(圖20)
圖20:廠務智能化物流中心規劃平面圖與評估設備

4.3 安全庫存
4.3.1 邏輯設計與補貨機制
廠務使用的物料有成千上萬個料號,若要達成庫房完全無斷料風險的情況,在考量庫存的成本與有限儲存空間下,必須以各物料實際領用量來設定安全庫存值,並在庫存量與領用量間取得平衡。
廠務庫房安全庫存管理有下列四個先決條件 :
❶分別建立F12、F15、F14、F18廠區的安全庫存。
❷FAM料件主檔狀態為Active的30、3F料號納管。
❸依過去一年的領用量,作為物料分類的計算因素。
❹每月一號重新計算安全庫存。
主要的物料分類分為兩階層,第一層是透過MOU的高低值設定Rule,其MOU大於0即執行備貨,第二層則是藉由Rule不同有個別的安全庫存計算方式,進而進行不同的備貨方案。優於公司庫房的安全庫存管理模式,不分廠區備貨且僅針對MOU大於9再啟動備貨,兩者安全庫存管理模式比較如表1所示。
比較項目 | 公司庫房 | 廠務庫房 | ||
---|---|---|---|---|
廠區設定 | 不分廠區 | 分為F12、F15、F14、F18廠區 | ||
納入料號 | 30料號 | 30、3F料號 | ||
備貨依據 | MOU>9 | MOU>0 | ||
安全庫存 |
|
RULE 1 | RULE 2 | RULE 3 |
依盒鬚圖分為五種類型 | 參考去年下一季領用量 | 有需求提出 | ||
扣帳方式 | 領用再扣帳 | 提前開立MR且入庫即扣帳 |
4.3.2 區分領用量
Rule1說明 : Rule1定義為MOU大於4的常用料,主要分為定量訂購與月訂購兩種模式,其邏輯設計與補貨機制如下說明。
❶ 定量訂購
➀ 邏輯設計:
藉由利用過去一年領用量的最小值(Min)、第一四分位數Q1(P25)、第二四分位數Q2(Med)、第三四分位數Q3(P75)、最大值(Max),繪製成盒鬚圖,再依盒鬚圖盒子的類型,分為五種Type設定安全庫存的計算公式,如表2所示。
Type | 系統判斷公式 | 盒鬚圖 | 圖示 | 物理意義 | 安全庫存計算公式 |
---|---|---|---|---|---|
Type1 | P75=MED=P25 | 無盒子 | ![]() |
月領用量幾乎 為定量(7), 偶爾有月領用量 為4或是10 | P75=MED=P25=7 |
Type2 | MAX=P75≥MED≥P25=MIN 且MAX=P75≠P25=MIN | 盒子佔滿 大小值 | ![]() |
月領用量固定 最高值(12)/ 最低值(6) | MAX=P75=12 |
Type3 |
|
盒子 在偏上 | ![]() |
大多月領用量 高於中位數(10) | P75=13 |
Type4 | P75-MED=MED-P25且P75≠MED≠P25且MAX≠P75&P25≠MIN | 盒子 在中間 | ![]() |
月領用量 平均分配 在24-28 | (MED+P75)/2=27 |
Type5 |
|
盒子 在偏下 | ![]() |
大多月領用量 低於中位數(7) | MED=7 |
➁ 補貨機制:
參考定量訂購模型(圖21),當廠務資產管理系統(FAM)的01.領料(-)與13.新裝機工程領料(-)申請單結案,系統自動檢查申請單的廠區與料號,其對應的共用庫存與安全庫存之關係,可分為下列三種狀況:
圖21:Rule1定量訂購舉例說明

- 若共用庫存不小於安全庫存,則不產生待訂購項目。
- 若申請單結案前,共用庫存不小於安全庫存,當因申請單結案後,使得共用庫存小於安全庫存,則產生待訂購項目,其數量為申請單數量減共用庫存與安全庫存之差值,成本中心為申請單的需求單位。
- 若申請單結案前,共用庫存小於安全庫存,當申請單結案後,共用庫存小於安全庫存,則產生待訂購項目,其數量為申請單數量,成本中心為申請單的需求單位。
➂ 舉例說明:
- 問題:當有領料申請單結案時,系統會自動檢查料號的共用庫存是否不小於安全庫存,如果共用庫存小於安全庫存量時,該如何補足數量?
- 答案:假設共有庫存為25個,當領料申請單結案8個,六月安全庫存為20個,系統會產生待訂購項目3個,成本中心為領料申請單的需求單位。
❷ 月訂購
➀ 邏輯設計與補貨機制:
隨著依據過去一年領用量的月份滾動,每個月一號將會重新計算安全庫存,系統自動檢查下個月安全庫存與上個月安全庫存之關係,可分為下列兩種狀況。
- 若下個月安全庫存不大於上個月安全庫存,則不產生待訂購項目。
- 若下個月安全庫存大於上個月安全庫存,則產生待訂購項目,其數量為下個月安全庫存與上個月安全庫存的差值,成本中心為上個月領用最多的需求單位。
➁ 舉例說明一:
- 問題:安全庫存會隨著每個月參考前一年的領用紀錄區間不同,使MOU改變,Rule也可能改變,當Rule改變,計算安全庫存的方式也會有所變更,而安全庫存變更時,該如何補足數量?
- 答案:假設共用庫存為100個,七月安全庫存為80個,八月安全庫存為120個,系統會產生待訂購項目20個,成本中心為上個月領最多的需求單位。(圖22)
圖22:Rule1月訂購舉例說明一

➂ 舉例說明二:
- 問題:領料單(MR)開立後至物料入庫結案的期間,若遇到月份轉換,系統重新計算下個月的安全庫存,而因月份轉換所產生的月訂購量,月訂購量該如何補足數量?
- 答案:假設共用庫存為75個,七月安全庫存為80個,八月安全庫存為90個,在途訂單為5個,系統會產生待訂購項目10個,成本中心為上個月領最多的課別單位。(圖23)
圖23:Rule1月訂購舉例說明二
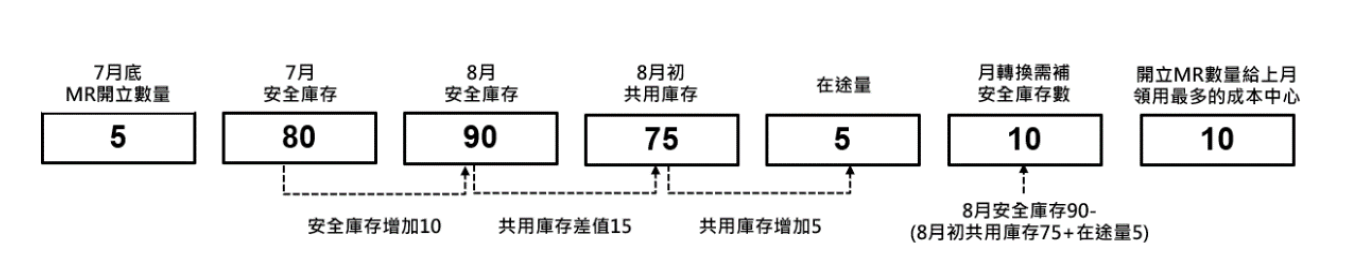
Rule2說明 : Rule2定義為MOU不大於4的非常用料,訂購模式為季訂購,其邏輯設計與補貨機制如下說明。
➀ 邏輯設計:
透過以季領用量為單位,依據去年下一季的領用量,設定為當季的安全庫存值。
➁ 補貨機制:
參考定期訂購模型,廠務庫房規劃每季訂購一次,於每季的第一天,系統自動產生安全庫存與共用庫存之差值的待訂購項目,成本中心為去年下一季領用最多的課別,訂購時間與進貨量參考時間對應表,如表3所示。
實際領用紀錄 | ||||||||||||||||||||||||
---|---|---|---|---|---|---|---|---|---|---|---|---|---|---|---|---|---|---|---|---|---|---|---|---|
年 | 2020 | 2021 | ||||||||||||||||||||||
月 | 1 | 2 | 3 | 4 | 5 | 6 | 7 | 8 | 9 | 10 | 11 | 12 | 1 | 2 | 3 | 4 | 5 | 6 | 7 | 8 | 9 | 10 | 11 | 12 |
Q'ty | 0 | 0 | 0 | 12 | 0 | 0 | 6 | 0 | 0 | 0 | 12 | 0 | 0 | 0 | 6 | |||||||||
訂購時間 | 使用物料時間 | 進貨量參考時間 | 進貨量(安全庫存量)計算 | |||||||||||||||||||||
2021年1月 | 2021年4~6月 | 2020年4~6月 | 12+0+0=12 | |||||||||||||||||||||
2021年4月 | 2021年7~9月 | 2020年7~9月 | 6+0+0=6 | |||||||||||||||||||||
2021年7月 | 2021年10~12月 | 2020年10~12月 | 0+12+0=12 | |||||||||||||||||||||
2021年10月 | 2022年1~3月 | 2021年1~3月 | 0+0+6=6 |
Rule3說明 : Rule3定義為MOU等於0的物料,訂購模式為加單訂購,其邏輯設計與補貨機制如下說明。
➀ 邏輯設計:
除了MOU等於0,下列三種類型的物料皆設定為Rule3,並將安全庫存設為等於0。
- Life Time物料,例如:儀電課電池、氣化課Scrubber吸附劑與化學品。
- 再生濾網,例如:FFU Tool TOC Regen Filter、Tool TOC Regen Filter。
- Sunset物料,例如:機械課LSC物料轉Turnkey與AMC堆疊非再生濾網。
➁ 補貨機制:
為避免因備貨導致庫存變為滯料,因此廠務庫房不進行備貨,若廠務有需求,則需提早提出加單申請,當加單訂購物料到貨後,廠務庫房透過庫存櫃位課別的管理,將庫存建置於加單庫存,僅保留給申請加單訂購的課別做領料,保障申請課別的使用權益,如表4所示。
安全庫存:設定為0 | |
---|---|
NOTE |
|
4.3.3 小結
前文所提之安全庫存邏輯設計與補貨機制,其訂購與扣帳模式統整如表5所示。而廠務庫房的安全庫存邏輯設計,除了透過一年間領用量計算安全庫存之外,並加入交期的因素,於系統設定交期與倍數之關係,再將安全庫存乘以倍數,可得最適安全庫存值。若廠務使用端因需求改變欲調整系統計算的安全庫存,可向廠務庫房申請調整安全庫存,以避免需求上升而不及備貨造成斷料的情形。
項目 | 定量訂購 | 月訂購 | 季訂購 | 加單訂購 |
---|---|---|---|---|
Rule | Rule1 | Rule1 | Rule2 | Rule3 |
訂購時機 | 共用庫存小於安全庫存 | 每個月的第一天 | 每季的第一天 | 加單申請核准 |
訂購數量 |
|
上月安全庫存與下月安全庫存之差值 | 去年下一季的領用量與共用庫存之差值 | 加單申請數量 |
扣帳對象 | 領用後使共用庫存小於安全庫存的成本中心 | 上月領用最多的成本中心 | 去年下一季領用最多的成本中心 | 加單申請成本中心 |
扣帳依據 | MR單的成本中心 | |||
扣帳時間點 | 待訂購訂單物料入庫後 |
結論
兵無常勢、水無常態。在地緣政治影響供應鏈穩定的現況下,維持庫房穩定而高效率的運作是關係著企業能否持續成長的關鍵。倉儲作業受益於自動化工具與智能化系統的發展而擁有新的面貌,我們有更好的策略來因應少子化的人力缺口,同時能利用先進的技術減少勞務工作並遠離工安危害。廠務庫房肩負著提供全廠務單位的物料庫存及領用,每月進出量以數百萬件計,在配合公司新增廠房的節奏下,必須同步擴增量能,發展更智慧化的方式來操作,以滿足上下游的作業需求並實現庫房永續管理的目標。文中介紹的觀點與實例都是倉儲作業不斷進步的實證,也是廠務庫房正努力的方向。很榮幸能將相關資訊彙整撰寫與各位分享,歡迎對於此議題有興趣的同仁相互交流學習,一同成長。
參考文獻
- Amazon Web Service.
- Preface Coding.
- Outlook科技發展觀測平台。
留言(0)