摘要
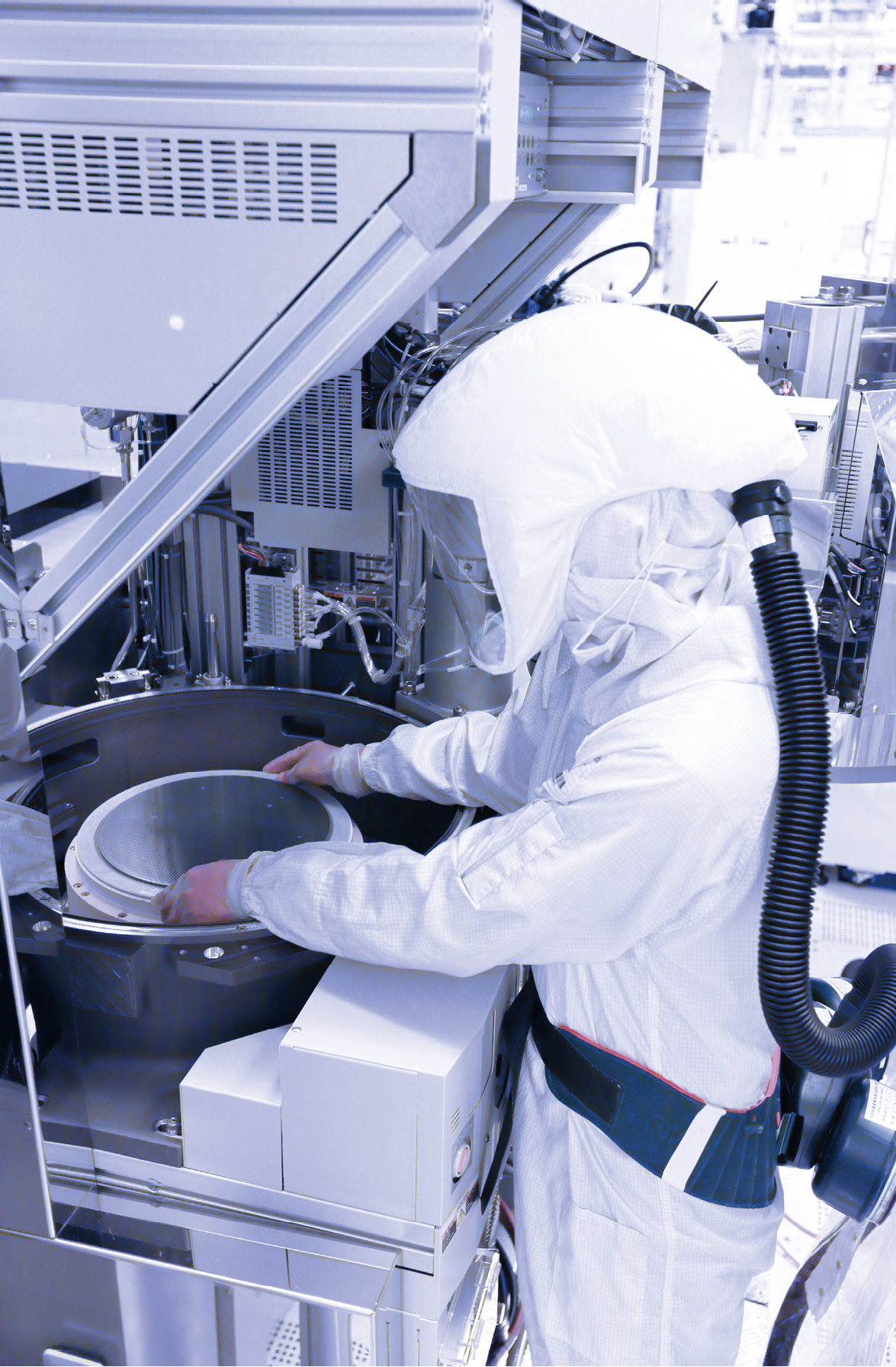
半導體廠區員工維修保養作業暴露風險管控
Keywords / Exposure Risk Assessment,Sampling2,Analysis24,Engineering Control,Workplace Enviromental Monitoring
以傳統勞委會公告之作業環境監測方法進行半導體作業人員化學品暴露評估,結果多為未檢出,且無法得知污染物即時暴露實態及作業過程危害因子。為釐清人員暴露及機台維修保養可能產生副產物,必須有不同採樣分析策略。本文運用不同類型偵測器,以其低偵測下限及連續監測的特點,進行維修保養全程即時監控,初篩具高危害副產物製程,必要時再輔以FTIR。此流程可得知高風險步驟及實際暴露副產物,並可多次實驗證明工程控制方法是否有效及節省委外監測費用。結果發現蝕刻灰化製程上一站IMP doping具AsH3危害及多道Si3N4蝕刻製程具HCN、HF等副產物,經與設備量身訂做工程控制方法,去除率皆可達90%,此外提升防護具等級,並修訂作業程序書,以達到零暴露風險的目標。
前言
因化學品暴露可能會導致職業病產生,而半導體廠區使用之化學品種類繁多,且廠內員工的工作形態及維修保養作業過程可能因機型、作業內容、擦拭使用溶劑及製程差異而隨著作業時間呈現危害物暴露濃度起伏變化,及可能產生未知副產物瞬間高濃度逸散,故作業人員面臨狀態可能為多重暴露、暴露時間短暫且瞬間高濃度,因此有必要完整評估廠區內作業環境和化學物質所造成的健康危害,並依評估結果調整作業防護:包括工程控制措施及防護具等級提升,皆可避免職業病的發生。
另外,現行半導體業採取公告之標準方法進行每半年勞工作業環境監測採樣分析,多為長時間採集勞工每天八小時的平均暴露濃度(TWA)或者短時間(STEL)15分鐘採樣分析,除因濃度稀釋作用導致人員暴露濃度均遠低於容許濃度標準或未檢出外,亦無法得知維修保養作業過程環境暴露實態及瞬間逸散副產物為何,故應對不同類型維修保養作業進行現場觀察,並選用可即時監測之直讀式儀器,找出員工維修保養過程高逸散風險步驟,並進一步了解過程中逸散之殘存製程氣體或副產物接觸空氣中水氣所產生之毒性氣體為何,因此找到適合半導體廠區監測方式及暴露評估策略,是最重要的課題。
文獻探討
半導體廠區暴露危害探討
依據半導體廠區作業特性及暴露型態,為達到可即時連續監測化學物質之目的,過去文獻中工研院有許多與半導體廠區合作量測案例,多利用霍氏轉換紅外光譜儀(Fourier Transform Infrared Spectrometer, FTIR)量測,因其具備量測迅速、可同時測得多種氣體、及化合物辨識能力等特性,利於進行現場維修保養作業之連續監測,例如:民國89年文獻以Close-cell FTIR量測不同半導體晶圓製造廠(A~F)電漿金屬蝕刻機台以去離子水或IPA進行維修保養作業之暴露情況,發現逸散污染物除IPA為擦拭用溶劑其他皆非製程原料氣體殘留,而是HCl、CCl4、CNCl、HCOOH 表1等副產物生成逸散(張振平,2000),另外,文獻(葉銘鵬、吳榮泰、余榮彬,1999)中有以開放式FTIR直接對半導體廠區各區域進行監測,量測各物種平均濃度、最高濃度,發現廠區內經常逸散之化合物為用以機台擦拭及維修保養用IPA及Acetone或各製程區有原料(光阻、顯影劑等)逸散之現象,此文獻同時利用Close-cell FTIR進行金屬蝕刻機台維修保養過程連續監測,並發現以去離子水擦拭及刮除反應腔上深褐色薄膜時,有副產物HCN逸散持續9分鐘,且濃度最高可達7ppm推測HCN產生與附著在反應腔上薄膜與空氣中水氣或去離子水反應有關。(First,1996)曾於文獻中提及,半導體廠進行蝕刻之機台,會產生碳氫聚合物附著於反應腔內,可能會與水氣反應產生有毒或腐蝕性氣體,與前篇文獻中量測結果一致。
此外,同樣有多篇論文說明蝕刻製程機台危害性較高(張振平,1997;古坤文,2004),原因為其以高能氣體電漿plasma離子化產生自由基進行乾式蝕刻,較易產生與原物料危害特性不同之製程副產物並附著在反應腔壁,如HCN、ClCN、HCl等副產物於文獻提及(Pais,1998;SEMATECH,2014),其中HCN健康危害特性為急毒性吸入/急毒性皮膚接觸第一級,最高暴露容許濃度Ceiling值為10ppm及急性吸入暴露標準值為0.34mg/m3是高毒性氣體。
廠別 |
原料氣體 |
擦拭溶劑 |
測出物質 |
Cmax (ppm) |
---|---|---|---|---|
A4 |
Cl2、BCl3、SF6、Ar |
IPA |
HCl HCOOH IPA |
14.88 0.60 66.90 |
B1 |
Cl2、BCl3、NH3、CF4 |
DI Water IPA |
HCN IPA |
3.50 170.00 |
B2 |
Cl2、BCl3、CHF3、CF4 |
DI Water IPA |
HCN IPA |
2.34 228.70 |
C1 |
Cl2、BCl3、N2、CF4 |
DI Water |
CCl4 HCl HCN HCOOH |
2.57 28.00 63.00 2.78 |
C2 |
Cl2、BCl3、NH3、CF4 |
DI Water IPA |
CCl4 HCl HCN HCOOH |
5.40 91.00 7.20 5.18 |
D2 |
Cl2、BCl3、N2 |
DI Water IPA |
CCl4 HCl HCN IPA |
1.23 7.20 22.00 464.00 |
F1 |
Cl3、BCl3、CHF3、CF4、N2、O2、SF6 |
DI Water |
HCl HCN HCOOH |
195.00 9.30 1.06 |
表2文獻(David、Lisa, 1998)說明在蝕刻製程Si3N4 nitride film且Plasma source gases包含O2, Ar, He, SF4時會有副產物HCN產生,且逸散濃度區間為0.5-1.5 ppm, 表3則說明在不同蝕刻製程原物料使用所會產生之副產物(如:原物料使用O2/CF4產生副產物HF)及其產生附著位置為反應腔或vacuum pump前後。蝕刻製程機台危害特性不同於其他機台,其他製程所產生污染物多為製程使用之原物料未pump purge清除完整逸散而導致,而蝕刻為以電漿反應將碳氫聚合物沉積在反應腔及內部構件表面上,此聚合物懷疑會暴露於空氣或水氣反應後,結合成未知的化合物,並產生異味(Bladwin、Stewart,1989)。
Plasma source gases included O2, Ar, He, SF4 |
Wafers Coated With Si3N4 |
Bare Silicon (Si) |
---|---|---|
number of measurements |
22 |
21 |
concentration range (ppm) |
0.5-1.5 |
0-0.5 |
maximum concentration (ppm) 4 seconds |
10.7 |
3.1 |
average concentration for 1 minute |
0.905 |
0.143 |
time for HCN to disappear |
maximum 2 min. |
1 min. |
Feedstock Chemicals |
Contaminants |
Location |
---|---|---|
NF3/CF4 |
free fluorides |
before vacuum pump after vacuum pump |
BCl3/Cl2 |
free chlorides |
before vacuum pump after vacuum pump |
O2/CF4 |
HF |
debirs from vacuum pump extract port |
CHCl3/BCl3/Cl2/O2 |
CNCl, HCl, HCN, pentachlorobenzonitrile and other compounds |
Yellow polymer in reaction chamber of aluminum etcher |
BCl3/Cl2/HCl/Ar/O2 |
boric acid, silica |
white/yellow debris in reactor chamber of poly silicon etcher |
半導體廠區監測問題探討
傳統作業環境監測方法主要依勞委員會公告之「作業環境空氣中有害物標準分析參考方法」進行氣體污染物之量測,然而此方法運用於半導體廠清淨室之量測時,常遇到下列之缺點:偵測極限較高,一般而言勞委會公告分析參考方法之偵測極限約在sub-ppm範圍,較無法滿足半導體工廠氣體污染物濃度低之特性;無法提供即時濃度狀況,整體而言,半導體製程在正常作業時勞工暴露濃度絕大多數低於容許濃度標準,只有在異常狀況或維修保養時才可能發生暴露濃度超過容許濃度標準之情況,若以傳統採樣分析方法來評估暴露危害的程度,對於瞬間高濃度暴露無法確切掌握(Yeh、Wu、Yul,2000)。
然而運用FTIR監測亦有其儀器使用限制,在部分無機類危害性氣體之儀器偵測下限較高,可能無法鑑別出所有副產物,如 表4為半導體廠區實際操作CC-FTIR以10m光徑進行量測,以當時儀器操作狀況AsH3偵測下限為1.74ppm,但Arsine TLV值(Threshold Limit Values)為0.05ppm比儀器偵測下限還低,且利用FTIR監測費用較昂貴,無法進行多次複製實驗或確認工程控制之有效性,因此本研究依可能面臨不同種類之危害性氣體,以廠內監測技術GMS系統及Honeywell新型手持式儀器進行PM過程即時監控,並借重其低偵測下限特點(ppb level),針對不同機台可能逸散之無機及有機污染物進行初篩,找出風險較高之製程,以評估並建立完整採樣分析策略,期準確、快速鑑定人員於PM過程之暴露實態,並找到適用於半導體廠區機台及化學品種類較多之工程控制方法。請參考 表5為彙整現行監測方法所面臨問題及本研究使用方法之評估表。
ppm |
CF4 |
AsH3 |
BF3 |
PH3 |
---|---|---|---|---|
L.D.L |
0.4 |
1.74 |
2.85 |
0.94 |
面臨問題 |
現行方法 |
本研究 |
---|---|---|
傳統採樣分析方法 |
作業環境監測方:因採樣時間為勞工每天八小時的平均暴露濃度有稀釋作用,或者短時間STEL15mins採樣,有採樣體積不足或同樣檢測結果多為Non-detected,無法反應實態 |
依半導體廠暴露危害特性,選擇合適偵測器,並以低偵測下限與即時監控特點,進行高暴露風險製程之維修保養作業監測,可調整監測方法及時間並全程即時監控 |
FTIR針對特定物種使用限制 |
文獻半導體廠維修保養作業監測多以FTIR進行,因儀器特性部分無機汙染物之偵測下限較高,可能無法完整鑑別 |
依可能面臨不同種類之危害性污染物,進行初篩,可評估挑選MDL較低之監測儀器,必要時才輔以FTIR進行確認 |
委外檢測費用昂貴 |
若委託工研院進行檢測,除了費用較昂貴(每次十萬元) |
以廠內既有監測技術,除大幅降低量測費用(如紙帶式偵測器增設點位花費約3萬),並可依作業內容調整即時監控 |
持續改善實驗困難 |
過去機台PM逸散量測多為一次性,僅鑑定是否有汙染物逸散,未進行持續改善監測,以確定副產物減量之有效性 |
可進行多次汙染物逸散去除實驗監測,利於評估工程控制方法之有效性 |
研究方法
本研究利用廠內紙帶式氣體偵測器以更快速、更即時、費用低且準確度高之採樣策略初篩300mm先進製程蝕刻機台維修保養作業逸散污染物,必要時再輔以定性分析手法,可改善以往傳統環境監測手法;導入美國EPA之健康風險量化模式,以掌握副產物暴露風險值;依量化風險高低判定是否須進行汙染物逸散工程控制改善,同時修改作業程序與人員防護具等級,以期達到作業過程「零」暴露之目標。詳細流程如下述。
同步進行維修保養作業觀察並建立人員定量暴露評估策略
執行作業安全觀察及訪談人員作業過程是否有異味產生,如開啟 chamber lid、wet clean parts及 wet clean process chamber等動作,以評估人員作業可能暴露危害 性氣體之高風險步驟。 針對汙染物特性:無機、有機汙染 物執行不同採樣策略,若為無機物 先架設Vertex偵測器(固定式),或 SPM-Flex /TLD- 1(手提式)依有害物的類型(氫化物、酸性、鹼性、 氧化性)選用分析器( HY 、MA、 NH3、CL2)來執行機台污染物監測初篩,必要時可以定性方式利用 密閉式傅立葉轉換紅外線儀(CC - FTIR)進一步確認汙染物種類,或 者以impinger+IC、Wet wipe+ICPMS 鑑別陰陽離子及重金屬元素, 有機物則先以PID (Photo Ionization Detectors)及Canister採樣GC/MS 分析有機污染物進行初篩,再以 CC-FTIR進行汙染物確認。表6為 本研究中使用各項採樣儀器比較表,儀器採樣管採樣位置為維修保 養過程皆於Chamber正上方(人員呼 吸帶高度為主),採樣時間則以維 修保養作業開始至結束回裝新Parts 為止,以模擬設備人員全程暴露實態。
採樣方法 |
適用化合物 |
分析方法 |
優點 |
缺點 |
---|---|---|---|---|
傅立葉紅外線光譜儀(FTIR) |
NH3、PFC、WF6、AsH3、SiH4、HCN、HMDS及多種VOCs |
密閉式 (CC-FTIR) |
侷限空間(CC-FTIR)的長時間連續監測 同時監控多種污染物 偵測極限低(5 ppb -100 ppb),依量測選用cell光徑長而定) 可分析數百種未知物 背景光譜製作容易 |
偵測極限較開放式霍式紅外線光譜儀高 進行遠端監測時必須架設採樣管線 檢測費用較高 部分無機汙染物偵測下限較高 |
衝擊瓶Impinger |
HF、HCl、HBr、HNO3、H3PO4、H2SO4 |
離子層析 陰離子(IC) |
偵測極限低(ppb-ppt) 不受鹽類的干擾 |
只知瞬間或平均濃度無法得知時間趨勢 採樣時間較長 |
NH3、NH3+ |
離子層析 陽離子(IC) |
偵測極限低(ppb-ppt) 不受鹽類的干擾 多點同時監測 |
只知瞬間或平均濃度無法得知時間趨勢 採樣時間較長 |
|
TLD-1 Vertex SPM |
毒性氣體(如:AsH3, B2H6, PH3, NH3, HCl…) |
紙帶式 |
Detection limit較低(可達 ppb level) 操作便利&選擇性高 |
無法定性,判別待測物為何(僅可由色卡比對) |
健康風險評估
依據PM污染物逸散監測結果,除比對汙染物容許暴露標準(PEL)外,可參考吸入性急毒危害指標進行風險評估,因PM作業實際暴露時間大約為1hr,可適用鑑別最大小時暴露濃度之風險值。健康風險評估流程應包括危害確認、劑量效應評估、暴露量評估及風險特徵描述等四部分。其中危害確認是針對化學物質種類及毒性進行確認,劑量效應評估方式,則可經由實驗數據或流行病學資料作為基礎,判別物質是否具有閾值效應;如具有閾值,則推估參考劑量RfD (reference dose)或參考濃度RfC (reference concentration),劑量效應是以最低的劑量所可能產生的嚴重效應或是導致嚴重效應開始發生的前驅效應作為風險評估依據;其潛在假設就是如果這樣的劑量不會產生上述的嚴重效應或是前驅效應,則其他的效應也應該就不會發生。暴露量評估是指量測或估計人類暴露在某一存在於環境中危害性化學物質之期間、頻率及強度之過程。而其中急毒性之暴露評估以最大小時濃度計算急毒性危害指標AHQ。最後風險特徵描述係針對危害確認、劑量效應評估及暴露量評估所得之結果,加以綜合計算,以估計各種暴露狀況下對人體健康可能產生之危害性,並提出預測數值,風險特徵描述包含二個部分,第一為關於風險度數值之估計,第二則為可以用來判斷風險度之顯著性。
急性非致癌風險度: 計算吸入性急毒危害指標(Acute Hazard Quotient, AHQinh)如下: AHQinh = Cacute‧0.001/AIEC 其中Cacute採最大小時模擬濃度:Acute Toxicity summary-for 1 hour exposure (ug/m3),AIEC (Acute Inhalation Exposure Criteria)為美國環保署(第6區)發展之急性吸入暴露標準(mg/m3),包含434種物質之資料庫檔案(ACCESS)。當AHQ大於1時表示有急毒性危害之可能。
依據監測結果及風險值擬定工程控制方法
依據定量暴露監測結果及吸入性急毒危害指標之風險值,導入工程控制方法,與設備同仁合作依製程機台硬體設計及操作流程,量身訂做工程控制方法,並調整各項參數:維修保養作業時間、工程控制方法及人員操作難易度,以期達到各項參數最佳化,降低人員暴露風險,並可兼顧人員作業時間及便利性。
結果與分析
本研究以三種蝕刻製程PR Asher、Metal ETCH AlPad、Poly Metal Gate之改善案例進行說明,並強調定量暴露監測手法之選用、風險量化指標及如何量身訂做工程控制方法。
PR Asher 暴露評估及工程改善
Vertex「(試)紙帶式氣體偵測器」量測氣態污染物
PR Asher為IMP後段灰化光阻機台,使用製程氣體為4%H2/N2,CF4, O2,但因IMP製程可能doping殘留As, B, P在Asher灰化及電漿反應後產生氣態副產物(暴露途徑:吸入)及粒狀污染物(暴露途徑:接觸/食入),因此其採樣分析策略:以「(試)紙帶式氣體偵測器」Vertex佈點(AsH3, L. L)進行全程即時監測鑑別氣態污染物及利用砷擦拭採樣鑑別固態污染物。結果發現:
- 機台前置作業先行降溫,降至50度以下後即開啟Chamber lid並裝上safety collar防夾,開啟十分鐘後AsH3濃度即快速上升,最高至60ppb
- 以無塵布加D.I. water擦拭shower head,人員為擦拭到腔體內部,頭部會伸到chamber內,此時呼吸帶AsH3濃度為7.7ppb
- 擦拭Chamber wall,呼吸帶AsH3濃度值上升至50ppb – 擦拭e-chuck及Robot,呼吸帶AsH3濃度約為4.2ppb,濃度趨勢圖如 圖1所示。
項目 |
內容 |
|||
---|---|---|---|---|
圖示 |
|
|
|
|
PM步驟 |
開啟chamber lid |
Clean shower head |
clean chamber wall |
clean chuck & Robot |
AsH3 |
60 ppb |
7.7 ppb |
50 ppb |
4.2 ppb |
![]() |
由現場量測結果發現chamber lid開啟及clean chamber wall會有50 ppb以上AsH3讀值,主要原因為此製程會將PR crust層上doping As污染物吃出,且接觸到水氣及無塵布濕擦時而產生AsH3氣體逸散。另外,以此製程為例AsH3之監測方法若直接以CC-FTIR量測,會因偵測下限較高(表4:1.74ppm),導致無法量測到暴露狀況。
ppm |
CF4 |
AsH3 |
BF3 |
PH3 |
---|---|---|---|---|
L.D.L |
0.4 |
1.74 |
2.85 |
0.94 |
計算AsH3吸入性急毒危害指標
AHQinh = C acute‧0.001/AIEC分別代入下列數值
- AsH3急性吸入暴露標準(mg/m3)為0.16mg/m³
- Cacute為AsH3最大小時暴露濃度值平均值0.158ppm=50ug/m3= 0.05mg/m3
可計算出AsH3之AHQinh=0.05/ 0.16=0.32<1,表示作業期間無急毒性危害可能。但仍需關注其瞬間暴露濃度高且超過TLV值,應透過工程控制降低逸散量。
利用表面砷擦拭Wetwipe「NIOSH 9102」+AA原子吸收光譜儀
鑑定機台端是否有doping物質微粒殘留,是否具有砷危害暴露風險,採樣位置以設備人員作業過程中較易接觸機台部位進行MCE濾紙擦拭採樣(暴露途徑:接觸/食入)。Asherchamber較易接觸位置為:Chamber wall、tool robot、shower head、e-chuck,由實驗數據發現chamber wall位置砷(As)殘留量最高可至19368μg/100cm2,遠大於工業建議標準值100μg/100cm2,其他擦拭點約15μg/100cm2均低於建議標準值。此製程機台電漿能量強,且加入CF4進行蝕刻以F-去除上一站High dose implan-tation (HDI)於製程反應後所生成carbonized layer (crust)層,crust上方即有Arsenic 等污染物殘留。
工程控制、防護具等級提升
維修保養過程發現人員穿戴防護具不足,過程僅配戴安全眼鏡及無塵口罩,並無呼吸防護具且PM O.I.無規範,因此立即要求人員配戴PAPR (動力空氣濾淨式呼吸防護具),並水平展開至其他廠區修改PPE O.I (如 表7)。由於Chamber wall會附著大量砷微粒,同樣會於清潔腔體時沾染到無塵服,因此與製造部溝通比照IMP離子佈值設備人員,將此蝕刻課別設備之無塵服每日清洗更換,避免無塵服沾染造成人員誤食或皮膚接觸。
改善前 |
改善後 |
---|---|
護目鏡、無塵口罩 |
PAPR、防酸鹼手套、無塵服每日更換 |
經與設備討論後發現此機型於PM前並無任何Clean recipe亦無pump purge,因此評估以工程控制方法降低汙染物逸散。
圖2、Clean Recipe與Air Purge 濃度變化
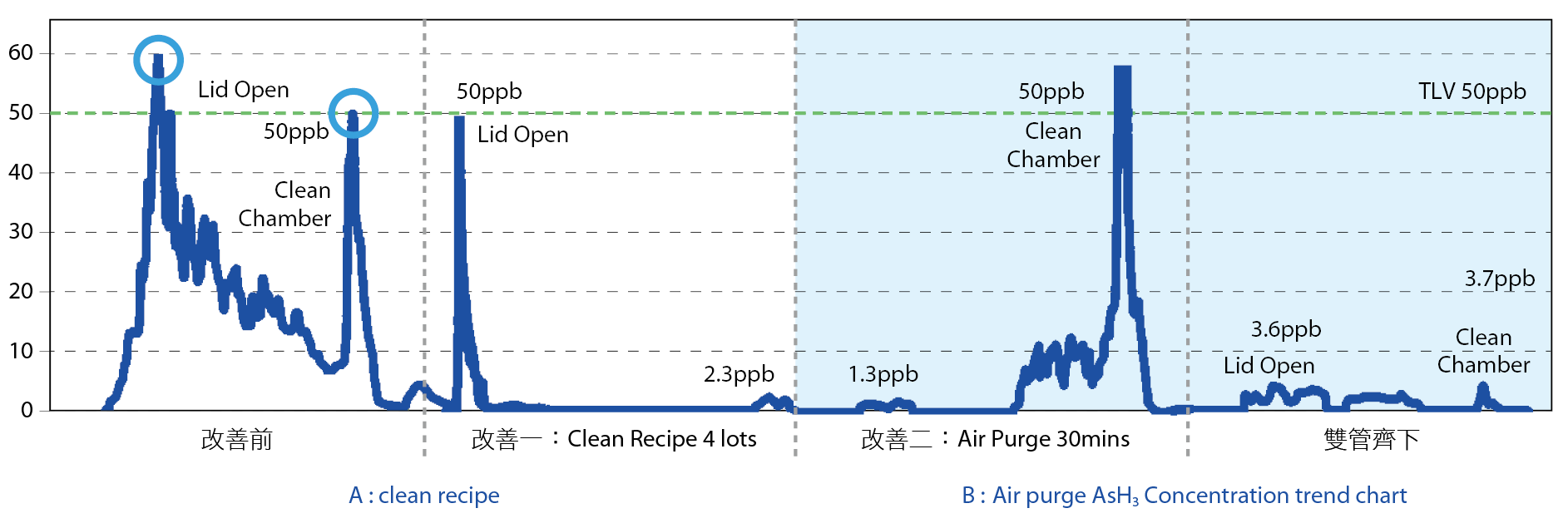
- PM執行前通入CF4輔以Plasma進行pre-clean,利用F-及plasma去除chamber wall coating沉積物。先嘗試執行4個lot Clean recipe (約80mins),發現清潔chamber階段讀值大幅下降至2.3ppb,但chamber開啟時讀值亦達到50ppb無顯著改善,如 圖2A。
- 若單純執行pump purge並無法流入水氣帶走沉積副產物,因此設計於PM前利用真空系統CV銜接於Pumping line之manual valve,並微開啟Load lock door,以形成氣流,帶入新鮮空氣與副產物反應再由CV抽走,避免汙染物有機會逸散。發現PM前以此動作進行30mins purge,chamber開啟chamber讀值可大幅下降至1.3ppb,但clean chamber階段讀值仍會達到50ppb,如 圖2B。
結合上述結果,合併clean recipe及fresh air purge兩項做法,並調整Clean recipe 次數,減少影響設備PM前置作業時間,找出最佳化參數設定為Clean recipe 3次合併Fresh air purge 30mins,可將關鍵步驟瞬間濃度降至4ppb以下。機台為單一腔體設計,因此無法架設PM Hood隔離亦無法加上蓋板施作。
綜合評估AsherTool PM事項:
PM過程中具有AsH3暴露健康風險,危害關鍵步驟為:open chamber lid、Cleanchamber wall,PM過程中同時具砷(As)微粒暴露風險,因此除透過工程控制改善將AsH3瞬間濃度降至4ppb以下,並將人員呼吸防護具由無塵口罩規範提升為PAPR並定期更換無塵服。將上述步驟標準化修訂PM O.I.及PPE O.I.,同時將此課別PM人員納入年度特殊健檢清單檢查尿中砷。
Metal ETCH AlPad暴露評估及工程改善
Vertex「(試)紙帶式氣體偵測器」量測氣態污染物
Lam 2300 Versy型式AlPAD使用製程氣體為Cl2、BCl3、O2、N2、He、Ar,PM頻率高:每天都有chamber PM,先以vertex分析器搭配HCN及MA紙帶進行量測,如 圖3發現開啟GDP (上蓋)接觸空氣時並無HCN讀值,但開始Clean E-chuck接觸水時則量測到HCN瞬間濃度達24.2ppm,及clean chamber wall時HCN瞬間濃度約9ppm,皆遠大於HCN Ceiling值:4.7ppm,且同時有HCl瞬間濃度約1ppm。依文獻資料[4]可推估,Chamber wall coating若為ClCN於開啟Chamber接觸空氣中水氣時,因水解速度較慢未產生HCN,待PM作業wet clean大量接觸水時才會量測到HCN逸散。
圖3、AlPAD機台維修保養過程氰化氫濃度變化
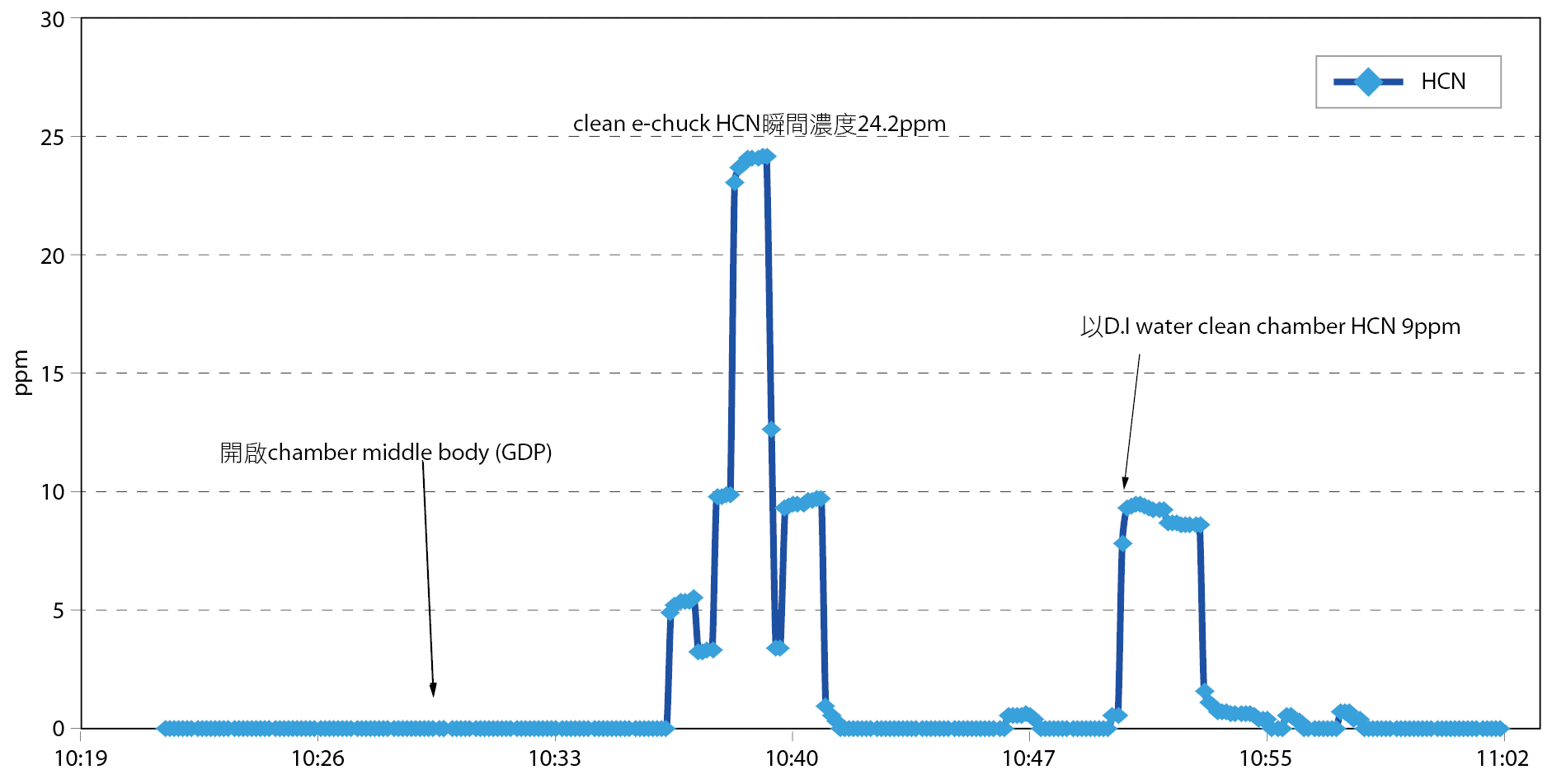
計算AlPad Tool PM HCN吸入性急毒危害指標
AHQinh = Cacute‧0.001/AIEC分別代入下列數值:
- HCN急性吸入暴露標準(mg/m3)為0.34mg/m3
- Cacute為HCN最大小時暴露平均值1.3ppm=1440ug/m3=1.44 mg/m3(HCN分子量27.03)
因此可計算出HCN之AHQinh=1.44 /0.34=4.23>1,代表PM作業期間有急毒性危害之可能,需進行工程控制降低汙染物逸散量。
CC-FTIR進行氣態污染物定性確認及同步鑑別PM hood外圍是否亦有汙染物逸散
以FTIR監測同樣發現Clean E- chuck時可量測到HCN瞬間濃度達23.8ppm,及clean chamber wall遇水時瞬間濃度約9.1ppm,發現CCl4於Clean E-chuck時有4.2ppm (如下頁 圖4),同步量測此製程PM作業所架設 hood之有效性,Hood外圍並未量測到汙染物逸散。
圖4、AlPAD機台維修保養過程FTIR監測HCN/CCl4濃度變化
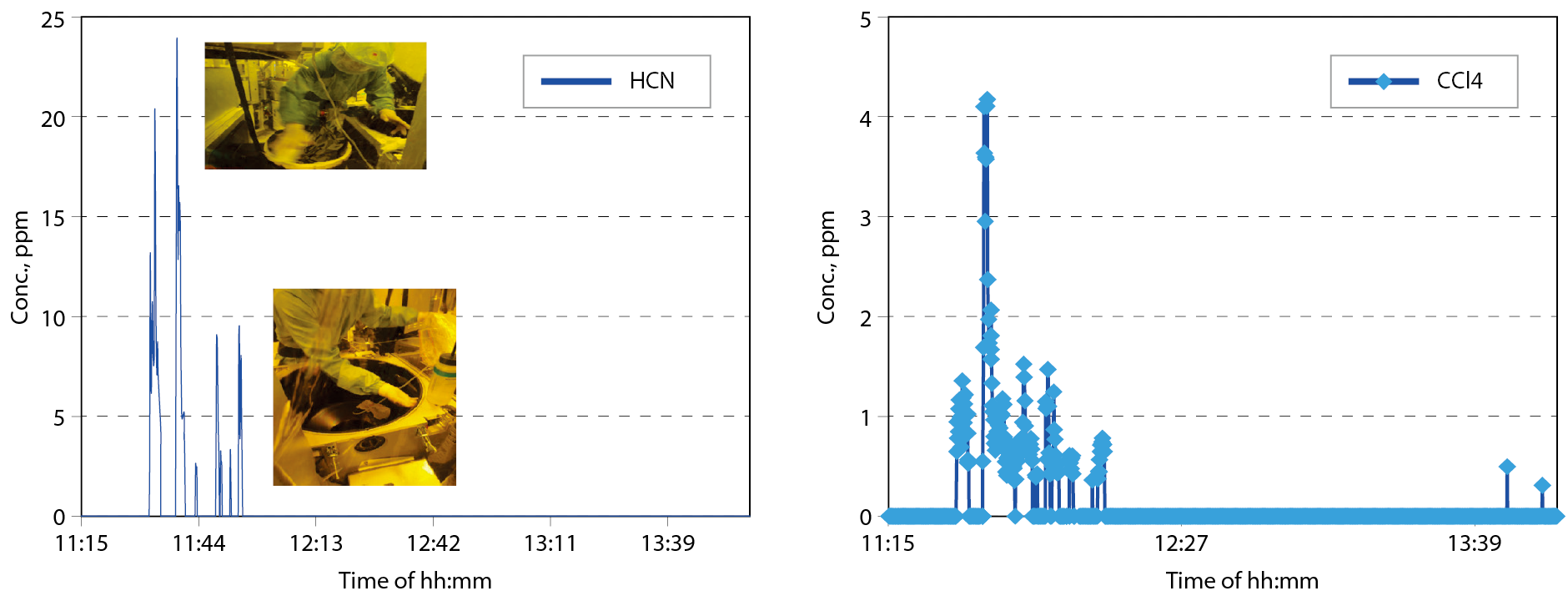
依據量測結果,與設備討論防護具等級是否足夠並合作執行By-product減量實驗,因PM過程具有HCN暴露危害,確認設備作業有依PPE O.I.配戴PAPR,並搭配防酸鹼手套進行作業。作業過程為避免污染物逸散環境,PM hood與house vacuum皆有架設確實,以達到防護效果。
執行工程控制By-product減量實驗
利用軟體已設定好PM前BCl3 Plasma clean recipe之次數調整,加強ion bombardment to dislodge,使chamber wall副產物減少,再進行pump purge,同樣以Vertex持續監測汙染物,確認副產物瞬間逸散濃度可降至Ceiling以下。實驗方法:PM前BCl3 Plasma clean次數由原先2次逐步提升至5次,可發現clean e-chuck HCN濃度由24.2ppm大幅下降至3ppm,具有顯著效果如 圖5。
圖5、測試BCl3前處理次數增加濃度變化圖
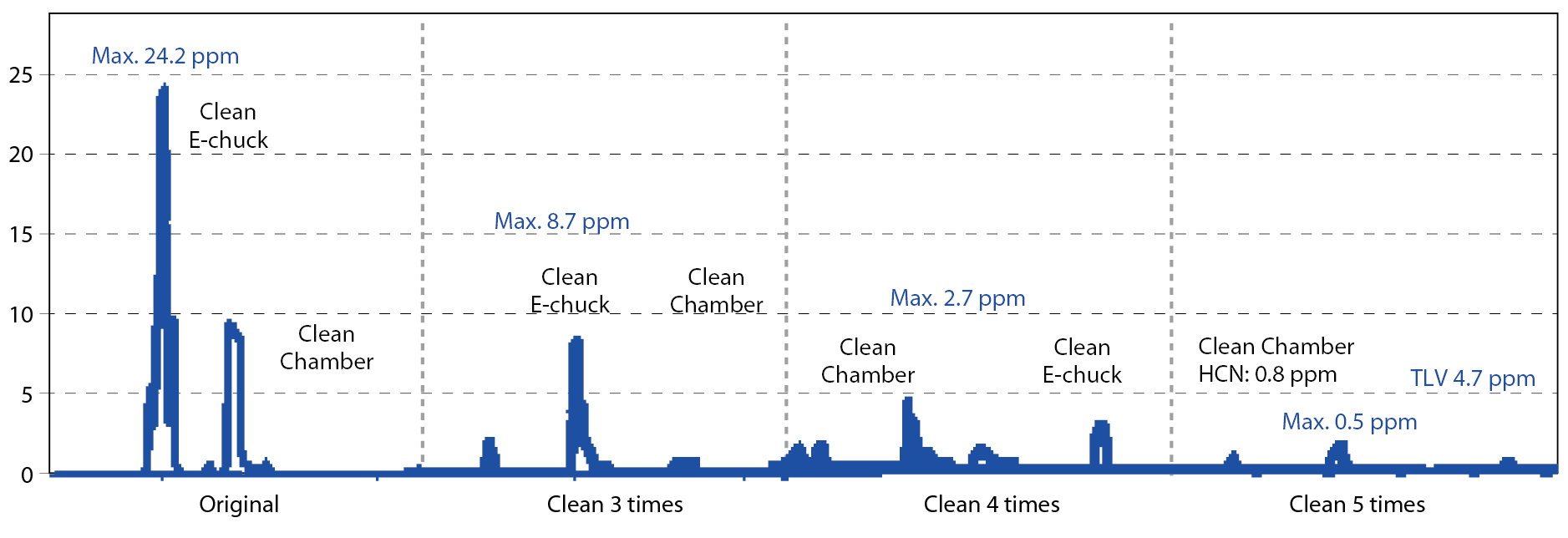
依工程控制後Vertex量測結果重新計算HCN吸入性急毒危害指標,AHQinh=Cacute‧0.001/AIEC分別代入下列數值,其中:
- HCN急性吸入暴露標準(mg/m3)為0.34mg/m3
- Cacute為HCN最大小時暴露濃度值平均值0.09ppm=0.1mg/m3 (HCN分子量27.03)
可計算出改善後HCN之AHQinh= 0.1/0.34=0.29<1,表示經工程控制後PM作業期間已無急毒性危害之可能。
綜合評估AlPad Tool PM事項:
PM過程中具有HCN暴露危害,危害關鍵步驟為:Clean chamber wall 、clean E-chuck,其中clean E-chuckHCN濃度最高達24ppm具吸入性暴露危害風險,因此透過與設備合作利用工程控制將HCN瞬間濃度降至1ppm以下,並確認人員有確實遵守PPE O.I.穿戴呼吸防護具PAPR,及作業期間確實使用PM hood避免汙染物逸散。將上述步驟標準化修訂PM O.I.及PPE O.I.。
Poly Metal Gate etch(機型HITACHI)
Vertex「(試)紙帶式氣體偵測器」先期量測是否具氣態污染物,並以廠內實驗室儀器impinge+ IC協助鑑定無機物種類
HITACHI型式Poly ETCH製程機台,分成兩種Process type:Metal gate1、Metal gate2,其製程氣體為4%CH4/AR, CHF3, Cl2, HBr, NF3, SF6, SiCl4, Ar, He, O2, H2,PM頻率約為每週一次chamber PM,先以vertex分析器搭配MA/Cl2紙帶進行監測,發現Metal gate1,2皆為開啟chamber lid並移除shower plate瞬間接觸空氣後會產生瞬間高濃度HF讀值,其中Metal gate1開啟時濃度最高可達10.8ppm,metal gate2瞬間濃度約8ppm 圖6,而開始進行Wet Clean chamber內部時HF瞬間濃度較低約0.4ppm,再利用impinger採樣+以IC鑑定負離子確定為F-,因此HF濃度值遠大於HF ceiling值6ppm須進行工程控制改善汙染物逸散實驗。
圖6、Metal gate1、Metal gate2 維修保養過程HF濃度變化
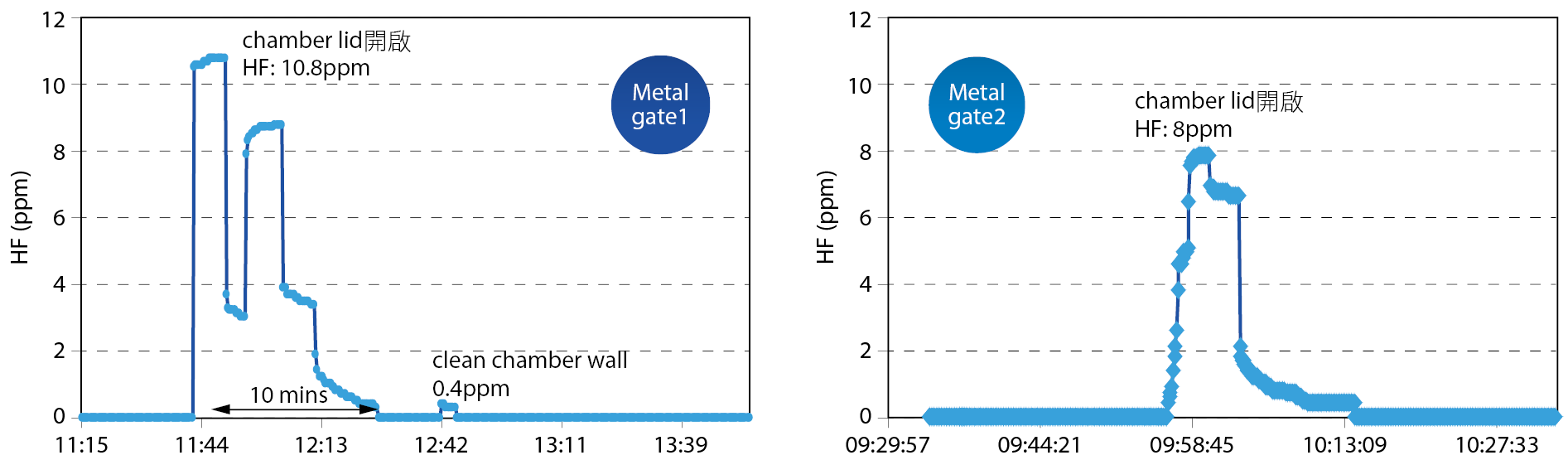
計算Metal gate 1 Tool PM HF吸入性急毒危害指標
AHQinh=Cacute‧0.001/AIEC分別代入下列數值,
- HF急性吸入暴露標準(mg/m3)為0.24mg/m3
- Cacute為HF最大小時暴露平均值0.9ppm=740ug/m3=0.74mg/m3 (HF分子量20.01)
計算出Metal gate 1之HF之AHQinh=0.74/0.24=3.07>1,表示此process type PM作業期間有急毒性危害。
Metal gate 2之Cacute=0.76ppm= 0.62mg/m3,計算出AHQinh=0.62/ 0.24=2.59>1,此機台PM作業期間有急毒性危害。依據吸入性急毒危害指標計算結果,須立即進行工程控制,以確保改善至AHQinh<1。
依上述監測結果:PM過程中具有HF暴露危害,需確實配戴呼吸防護器,確認設備現場有依PPE O.I.規範配戴PAPR呼吸防護具及搭配防酸鹼手套進行作業,並於PM作業期間確實使用House vacuum進行助抽,但量測結果顯示僅至於旁邊助抽效果並不顯著。
執行工程控制By-product減量實驗
依現場機台硬體狀況設計工程控制方法,Vertex監控發現HF逸散皆於Chamber lid開啟並移除shower plate階段,因此評估開啟前執行Fresh air purge,使汙染物在未開啟前及早接觸空氣中水氣反應,並由House vacuum抽走,但HITACHI機型於chamber 接觸空氣前並無其他gauge或閥件可拆除供空氣流入,藉由現場作業觀察發現chamber接觸空氣前最後一個步驟即為移除shower plate,因此評估chamber lid開啟後留下shower plate,藉由其上方之微小孔洞當作外界空氣進氣口,再由 pumping line 測漏manual valve以House vacuum抽氣,形成氣流帶走副產物 圖7。
圖7、工程控制示意圖
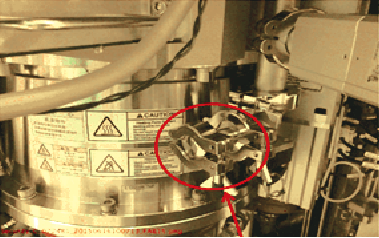
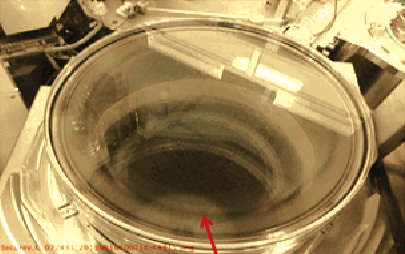
計算Metal gate 1 Tool PM HF吸入性急毒危害指標
以metal gate 1機型進行實驗PM前Fresh air purge 5 mins,發現HF濃度於shower plate開啟瞬間約降至3.4ppm,wet clean cham-ber wall僅有0.6ppm,成功削減HF逸散濃度,因此持續進行10 mins,發現shower plate開啟瞬間HF可大幅降至0.5ppm (如 圖8)。複製同樣手法進行metal gate2 HF削減測試,結果HF濃度於shower plate開啟降至0.4ppm,wet clean chamber wall讀值降為0,驗證此工程控制之有效性。
圖8、MG1、MG2工程控制後HF濃度變化圖
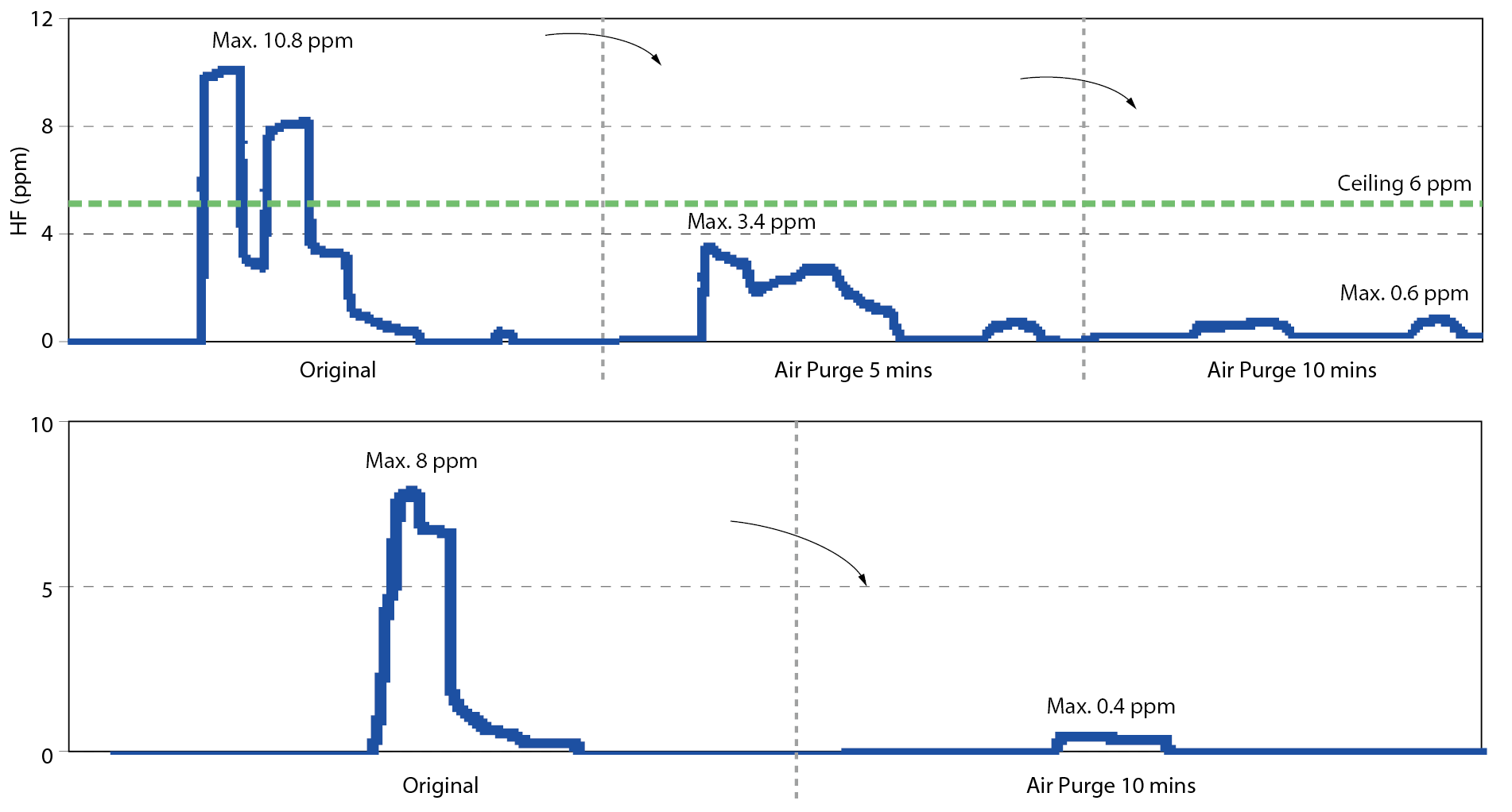
依工程控制後Vertex量測結果重新計算Metal gate1 HF吸入性急毒危害指標,AHQinh=Cacute‧0.001/AIEC分別代入下列數值,其中:
- HF急性吸入暴露標準(mg/m3)為0.24mg/m3
- Cacute為HF最大小時暴露濃度值平均值0.06ppm=0.04mg/m3 (HF分子量20.01)
計算出改善後HF之AHQinh=0.04/ 0.24=0.2<1,工程控制後作業期間已無急毒性危害。
綜合評估HITACHI Tool PM事項:
PM過程中具有HF暴露健康風險,危害關鍵步驟為:chamber開啟並移除shower plate瞬間,HF濃度最高達10.8ppm具吸入性暴露危害風險,透過與設備合作利用工程控制將HF瞬間濃度降至0.5ppm以下,並確認人員有確實遵守PPE O.I.穿戴呼吸防護具PAPR。將上述工程控制步驟標準化PM O.I.。
具體貢獻及成效
依上述鑑別方法進行廠區所有蝕刻製程暴露評估,執行成效如下。
- 利用本研究定量暴露評估策略,共發現300mm N28蝕刻製程有9項具有副產物逸散風險,且檢視各製程防護具穿戴等級,發現須提升1項製程之呼吸防護具至PAPR,並量身訂做各製程維修保養作業之工程控制方法。
- 重新修訂維修保養作業之前置作業流程,共標準化維修保養程序書5份,以達到防止再發之目的。
結論
本研究開發了適合半導體廠區之採樣策略,以直讀式儀器進行初篩,必要時再輔以定性監測方法,可以更快速、更精準且費用低並達到研究設定目標,同時藉由暴露風險評估方法鑑別出以往未發現之副產物逸散及員工維修保養作業確實有瞬間高濃度污染物暴露疑慮,並且以吸入性急毒危害指標將作業風險量化,可有效執行工程控制方法確效及驗證,供廠區作業人員一個安全無虞的工作環境。總結本文結論如下:
本研究採樣策略為利用GMS/Honeywell等直讀式儀器,具有偵測下限低、更快速、可即時取得數據且費用便宜之特性,可補足傳統環境監測方法之不足,除鑑別300mm機台PM作業暴露風險,未來可運用來評估其他新製程機台暴露危害。
透過研究執行過程,發現可強化與現場設備同仁互動溝通,因直讀式儀器特性可立即取得量測數據之變化,除了可依監測結果進行工程控制持續改善,更重要的是讓同仁知道可能暴露的危害及風險,更加願意合作共同開發控制方法,這對日後推展暴露風險評估計畫有極大的幫助。
透過導入健康風險評估模式之吸入性急毒危害指標,以量化風險值,有效改善以往缺乏特化指標,並可評估工程控制前後機台逸散污染物對人員造成的危害及驗證方法之有效性。
藉由TB平台將本計畫暴露風險評估模式推廣到其他廠區,以改善各廠區不同製程機台維修保養作業之副產物逸散風險,達到員工作業零暴露的目標。
參考文獻
- 張振平、宋隆佑、朱振群、林宜長,半導體廠維修作業勞工有害氣體溢散調查,國立台灣大學環境衛生研究所,2000
- 葉銘鵬、吳榮泰、余榮彬,應用霍式紅外光譜法調查半導體廠製程危害性氣體,工業技術研究院工業安全衛生發展中心,1999
- First, B.G., “Exposure Characterization of Preventive Maintenance Activities on Semiconductor Manufacturing Equipment,” SSA Journal, 10:27-41, 1996
- 張振平,半導體業紅外光偵測技術評估與建立研究計畫,勞工安全衛生研究所,IOSH86-A310,29-35,1997
- 古坤文,半導體金屬蝕刻機台於預防維修時之污染物逸散控制,國立交通大學碩士論文,2004
- Pais,DS., “Industrial Hygiene Assessment of Metal Etch Preventative Maintenance Activities”, SSA confe-rence, April1998
- SEMATECH, Working Group Meeting, Exhaust line safety analysis final report, 2014
- David Rainer and Lisa, “Brooks Recognition, Evaluation and Control of Some Plasma Processing Hazards”, 1998
- Baldwin DG, StewartJH. Chemical and Radiation Hazards in Semiconductor Manufacturing. Solid State Technology. 131-5,1989; Aug
- Ming-pengYeh, Rong-Tai Wu, Jung-Pin Yu1. Probing Airborne Chemicals of Semiconductor Work Place Using Gas Chromatography Mass Spectrometry. Center for Industrial Safety and Health Technology, Industrial Technology Research Institute, 2000; Feb
- 任新兵編著,化學工業出版社,太陽能光伏發電工程技術,2012初版。
留言(0)