摘要
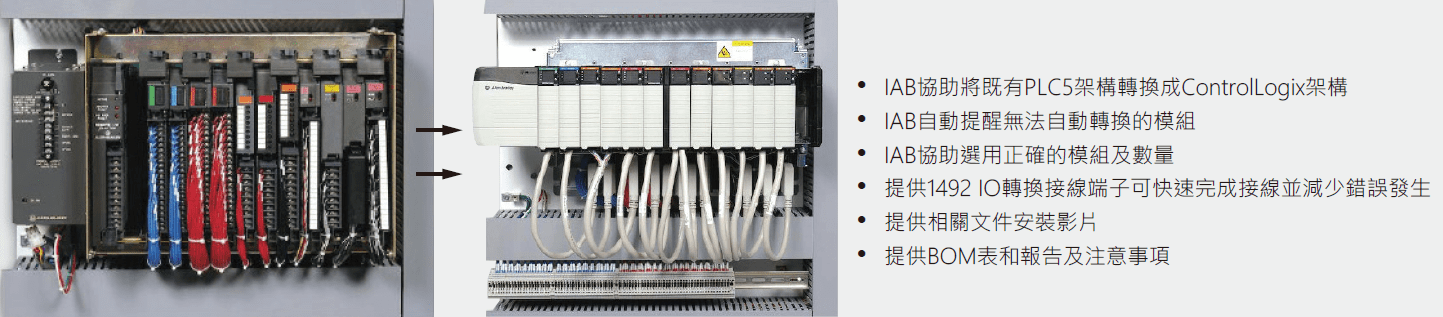
廠務系統穩定運轉–200mm Fabs品質管理
200mm Fab藉由導入「廠務開關門十件事」,來看清楚舊廠區的需求,唐太宗說:「以銅為鏡可以正衣冠,以歷史為鏡可以知興替」,Fabs經過多年運轉經驗,有很多是可取的地方,可以作為新廠未來老化的借鏡,讓新進的同仁站在巨人的肩膀上來發揚光大,透過新、舊廠區運轉彼此的交流和融合,達到全面廠務品質管理的目標。
前言
SEMI(國際半導體產業協會)公布最新全球8吋晶圓廠展望報告(Global 200mm Fab Outlook)指出,由於行動通訊、物聯網、車用和工業應用的強勁需求之下,2019到2022年8吋晶圓廠產量預計將增加70萬片,增幅為14%;而展望未來幾年全球8吋晶圓廠總產能至每月接近650萬片 ,8吋晶圓廠成為半導體業新寵,因製程技術的進步客戶的需求也會隨之改變,廠務供應品質SPC控管的目標也從 OOC(Out Of Control)到Baseline Change,跳脫既有傳統思維,有效的達到廠務全面品質控管的目標。
200mm廠區導入全面廠務品質的管理規劃,我們將藉由既設系統來導入新手法及概念,雖然設備老舊但做好維舊如新及翻新計畫,功能及品質一樣不妥協,同時也應用既有平台,作為師徒傳承的運轉經驗,發展更新手法,達到廠務全面品質控管。
全面品質控管,在廠務穩定運轉的目標下,從Design /Operation/PM來分析200mm現況及改善機會點,職人精神,讓平凡變成不平凡,品質管理就是落實在平日的運轉當中,需要從蛛絲馬跡找到改善的契機,防範異常於未然 ,就像是廚師對柴米油鹽醬醋茶,相同事情一直重複做以求精進,總是期待能夠有所進步,持續向上,沒有人知道巔峰在哪裡?在知識爆炸的今日經濟社會,如何掌握適合個人及群體所需的知識,已成為致勝的關鍵,唯有如此,才能掌握脈動與契機,領先群倫,立於不敗的境地。
文獻探討
2.1.發展背景
廠務品質管理,由TSMC FACILITY GENERIC SPC PRACTICE and SPEC. O.I.規範各廠務部門SPC的建立與執行,為了確保SPC確實有效地執行、預防不良品產生,以及使資料有效保存和運用,故建立一套TSMC廠務SPC 執行準則,SPC為「統計製程管制(STATISTICAL PROCESS CONTROL)」之縮寫,其意義是藉由製程中收集之資料,建立管制圖,運用統計手法分析資料、監控是否有異常產生,立即採取應變措施,使製程恢復正常,並提出防止再犯之法,所以SPC為一即時製程管制系統,以便監控製程之現況,提高製程穩定性,減少變異產生,另一方向則對製程的資料加以統計分析,進而採取改善措施,以提升製程能力及產品品質。
2.2.SPC導入與維護[5]
選定管制點及管制計畫,製程管制計畫之產生是從 CUSTOMER 的角度出發,失效模式與效應影響分析(FMEA)而發展出來。
製程管制之分類(Classification of Process Control) :製程管制(Process Control)主要區分成Key Node SPC ,General Process和Off Line Process三類。
Process Control之Key Node及General Process皆使用Trend Chart做管制圖,因廠務控制系統有自動補償之功能,故可以Trend Chart方式來記錄製程變數(Process Value)來管制。
管制點設定及Review機制規劃 :
Median Shift(S)為中位數偏移,因廠務系統為求穩定之供應,故以Median Shift(S)為其偏移量之參考。Median Shift(S)之Monthly review公式為S=|(median _this month)-(median_last month)|/max(robust sigma1_last month, robust sigma2_last month),若S>Criteria(Initial Criteria設定為3,此Criteria會依據每年實際之運轉資料來定義,也表示每年會review此Criteria的合適性)時,則表示本月份中位數比上個月份之中位數偏移過大,即列為Low Light Chart,需review其偏移之原因為何。
若因儀表校正致使S>Criteria,而儀表校正後的讀值落在儀表本身精準度(Accuracy)之內,則此項目可不列入 Low Light Chart接受review。
Robust Sigma Change Ratio(RSR)Review Rule:
Robust Sigma Change Ratio(RSR)製程能力指標,用以偵測廠務系統供應製變異寬度變化率。
RSR(Robust Sigma Change Ratio)=Robust Sigma2/ Robust Sigma1,Where Robust Sigma=MAX{(P95- P50)/1.645, (P50 - P05)/1.645}
製程管制計畫之產生是從CUSTOMER的角度出發,失效模式與效應影響分析(FMEA)而發展出來,經過世代的變化,產線產品組合也已經不一樣,所以以已往OOC(Out Of Control)為管制界線的要求,也慢慢改變為以baseline change為更嚴謹,製變異寬度變化率計算公式如下:
RSR(Robust Sigma Change Ratio)=Robust Sigma2/ Robust Sigma1
SPC的目的,幫助製程穩定地製造出好的產品。
2.3.品質策略管理→圖1
圖1、如何落實TQM全面品質管理[1]

導入知識管理,其實是一種組織變革,這種變革是企業適應能的考驗,「第五項修練」中,「煮青蛙的故事」( 郭進隆,1998年),詳細敘述不能適應環境的可怕後果[2]。在中國的歷代王朝,也大都在變革失敗後滅亡。因此,順應科技變遷的組織變革,是企業生存的不二法則,尤以知識為主導的現代競爭環境,其重要性更為顯著。
實施知識管理的案例,以印証知識管理與策略管理及TQM的密切相關性。
台積電公司(Taiwan Semiconductor Manufacturing Company)(孫德風,民90年)。
- 定義:知識管理為處理知識資產(Knowledge Asset)的事務程序,以槓桿操作系統化改善組織效率、反應、競爭力和創新速度。
- 長期目標(Goal):以創新速度建立競爭優勢,架構以知識為基礎的企業。
- 盤點知識資產存貨,訂定知識管理策略,採取T戰略,水平方向為擴充全公司知識管理文化,垂直方向為發展知識管理方法論(Methodology)。
- 訂定知識管理路途圖(Roadmap),程序(Process)及式樣圖(Architecture)。
- 進行知識整合(Integration)以及文化擴散(Culture Diffusion)。
- 建立推動組織。
- 實施策略管理。
- 架構知識管理工程,進行知識選取(Extract)、組織( Organize)之增長(Access)。
- 展開成任務小組(Task Force)、變革管理(Change Management)、系統(System)和績效與激勵(Perfor mance & Incentive)等功能。
- 實施知識管理的關鍵因素(Critical Elements)為人(People)、流程(Process)、和技術(Technology)。
從知識管理的預期效果來看,品質、成本、效率也是全面品質管理(TQM)所追求的目標,而從→圖2可知,由認知覺醒所引導之策略、設計、原型開發與測試、導入、評估與維護,事實上與策略管理的原理與方法,也是互相吻合的。由此觀之,TQM、策略管理與知識管理實有相輔相成的密切關係。
圖2、知識管理績效提升螺旋
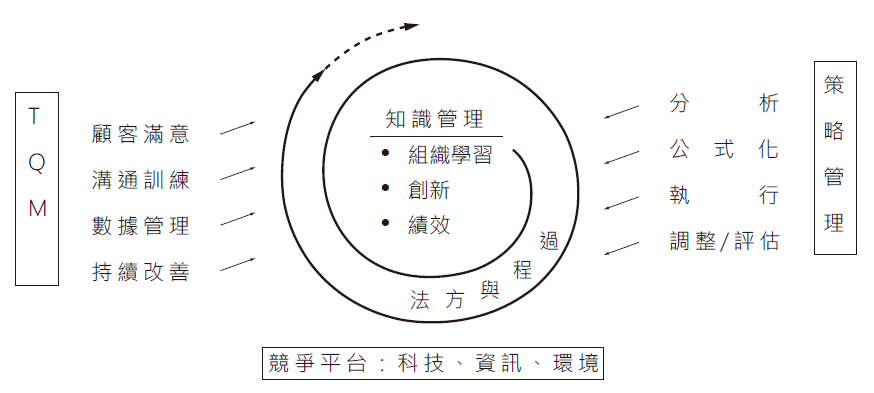
前述的分析,可以彙總歸納整理。在→圖3中,左縱軸表示知識管理應用層級與策略管理關聯性之高低,右縱軸表示知識管理應用層級與TQM實施之強弱關係,而每個層級皆依P-D-C-A(Plan, Do, Check, Action)管理循環運作,依此循序架構知識管理的基礎。
圖3、依策略管理和TQM架構的知識管理結構圖(資料來源:本研究整理)
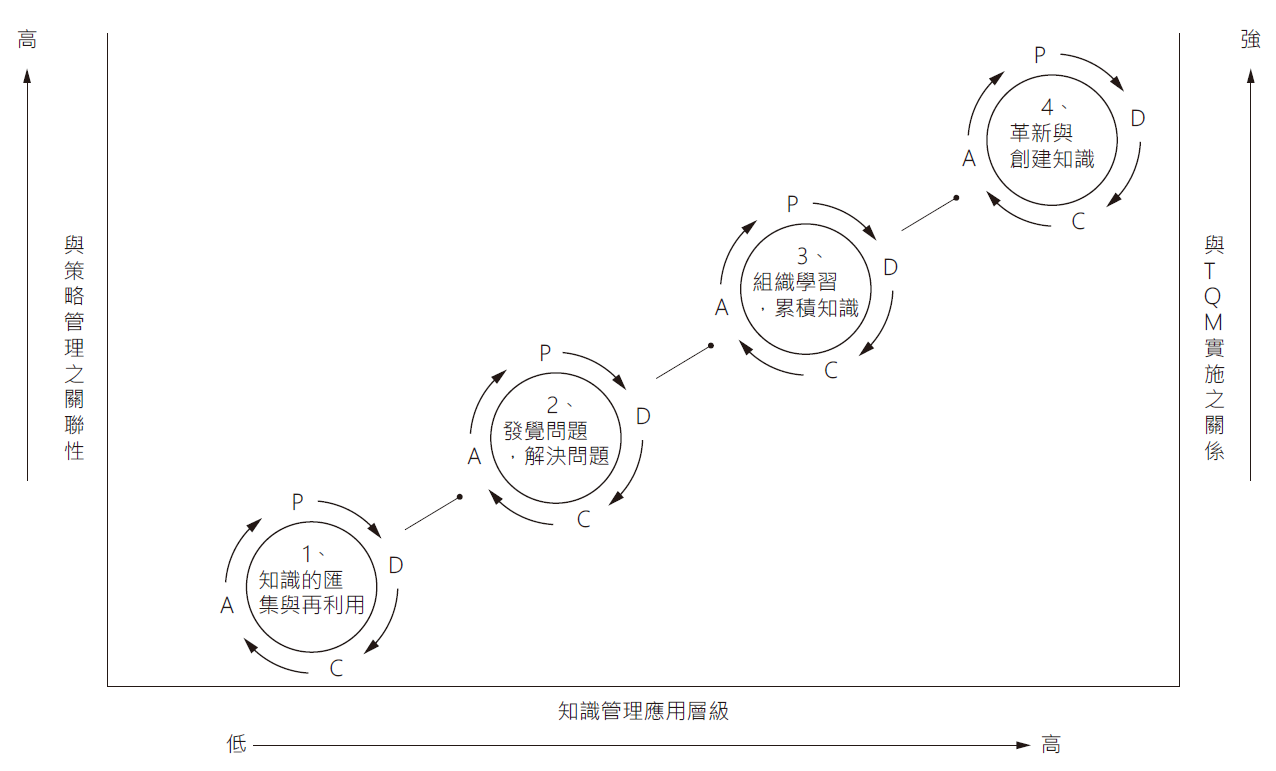
因此,本研究定位於以策略管理和TQM架構知識管理的基礎作為探討對象→表1。
傳統觀點 | 現代觀點 |
---|---|
生產力與品質是兩項相互衝突的目標。 | 可經由品質的改進,提高生產力。 |
品質係指符合某些條件或標準。 | 品質係指符合使用者需要的特定條件。 |
品質衡量的標準並不一致。 | 品質衡量的標準為過程的持續性、產品改進和使用者的滿意度。 |
不斷的檢驗可確保品質。 | 最初產品的正確設計和有效率的過程控制可確保品質。 |
假如產品符合品質標準,那麼允許其也些微小的瑕疵。 | 經由過程控制技術,可以避免不必要之浪費。 |
品質是一項獨立的功能,用以衡量產品。 | 品質是產品製作過程中每個階段功能的部分。 |
品質有瑕疵是員工的責任。 | 品質有瑕疵是組織管理有問題。 |
與供應商的關係是短期的,並以成本作為取捨標準。 | 與供應商的關係是長期的,並以品質作取捨的標準。 |
(資料來源 : 葉炳煌,民84 : 38)
研究方法
品質管理為達成品質目標的方法。
包括品質三部曲的所有步驟:①品質規劃,②品質控制,③品質改善。
在廠務穩定運轉的目標下,200mm/300mm SPC O.I 系出同源 : TSMC FACILITY GENERIC SPC PRACTICE AND SPEC : F-GQC-01-03-001 已定義6"/8"/12"廠務系統監測項目規格表項目一樣,在SPEC(OOC/OOS)300mm較200 mm Tighten,由品質規劃上系出同源是一致的。
在品質控制系統方面,廠務系統FMCS架構主要是要可分成DCS(Distributed Control System,分散控制系统 )/PLC(Programmable Logic Controller)兩種主要大型控制系統為主。
從Design/Operation/PM來分析200mm廠區的現況及改善機會點,同時也藉由廠務開關門十件事統一平台,來審視200mm有哪些指標需要再改進和強化→表2。
穩定運轉 | 200mm FMCS功能 | 廠區 | ||
---|---|---|---|---|
系統 | 200mm現況 | 300mm規格 | ||
Design | 重要系統備援 | 1、控制器 | Controller(Master+backup) | (Master+backup) |
PROVOX Y2013 Phase Out (無備品供應)10年計畫更新 |
PROVOX升級至Delta V 更新中 | |||
2、I/O卡 |
重要系統(PCW/AAS/PV)I/O卡片 Redundancy (多對1) |
1對1 | ||
PROVOX Y2013 Phase Out (無備品供應)10年計畫更新 |
PROVOX升級至Delta V 更新中 | |||
3、網路() | RING(環狀)備援/樹狀無備援 | RING(環狀)備援 | ||
4、FMCS SCADA | 無備援/All(xx/xxx) | FMCS/Local互相備援 | ||
風險分散 | 5、控制點 |
DOx1(On) (PCW/AAS/PV) |
Dual DO(On/Off) | |
重要同系統(PCW/AAS/PV)分散至不同卡片 | ||||
Operation | 參數管理 | DCS | 與IPRS管制同方式 | iPRS |
Intouch(FMCS) | 無參數管理 | iPRS | ||
Local PLC SCADA | 無參數管理 | iPRS(LSC,Chem/Sly/氫瓶櫃) | ||
一鍵起停 | 自動化 | 一鍵起停(PM) MAU/AAS(PROVOX) | 一鍵起停(PM) | |
聯合交接 備援機制 |
FMCS值班台 整合數位電子看板 應變流程/廠務資訊 |
Ploycam(視訊聯合交接&支援) | Ploycam(視訊聯合交接&支援) | |
值班空間須整合 建議Relayout & SI 戰情畫面 |
FMCS值班台 整合數位電子看板 應變流程/廠務資訊 |
|||
PM | PM | ePM/FAM | ePM → FAM | FAM |
從Design部分廠務FMCS架構,主要可分成DCS(Distributed Control System,分散控制系统)/PLC(Programmable Logic Controller)兩種 :
- DCS架構廠區 : 有F2&5/F3/F3E/F6
- PLC架構廠區 : 有F8(原世大),F3E(原德基)
DCS是分散式控制系統,系統定位在於大型應用,尤其是重工業應用,其適合用在連續性的控制,且因為該系統的I/O點非常多,其考慮到的因素比較偏重在於Redundancy,因此較無法接受系統出問題,容錯備援的需求性很高,同樣的DCS系統建置完成之後是很難去進行更動的,因此它適用於較穩定、在市場上的Life Cycle較長的產品需求;PLC的定位則是在於比較中型或是中大型的應用,它的特色在於價格較DCS具競爭力,而且適合做離散的邏輯控制應用,不過PLC與DCS相同的地方在於,較穩定、Life Cycle較長的產品。
我們將200mm Fabs FMCS安全再運轉30年當成我們規畫運轉目標,整個FMCS DCS Over All分為四個世代,DCS原4個世代(Delta V(2010年代)/SRX(2000年代)/SR90(1990年代)/HW1(1990年代),將整合為2個世代(Delta V/SRX),主要需要改善為F2/F5離群的架構及孤鳥的設備,SRX Controller運轉維持安全備品量,逐年計畫性升級成Delta V→圖4。
圖4、200mm Fabs FMCS安全運轉30年計畫
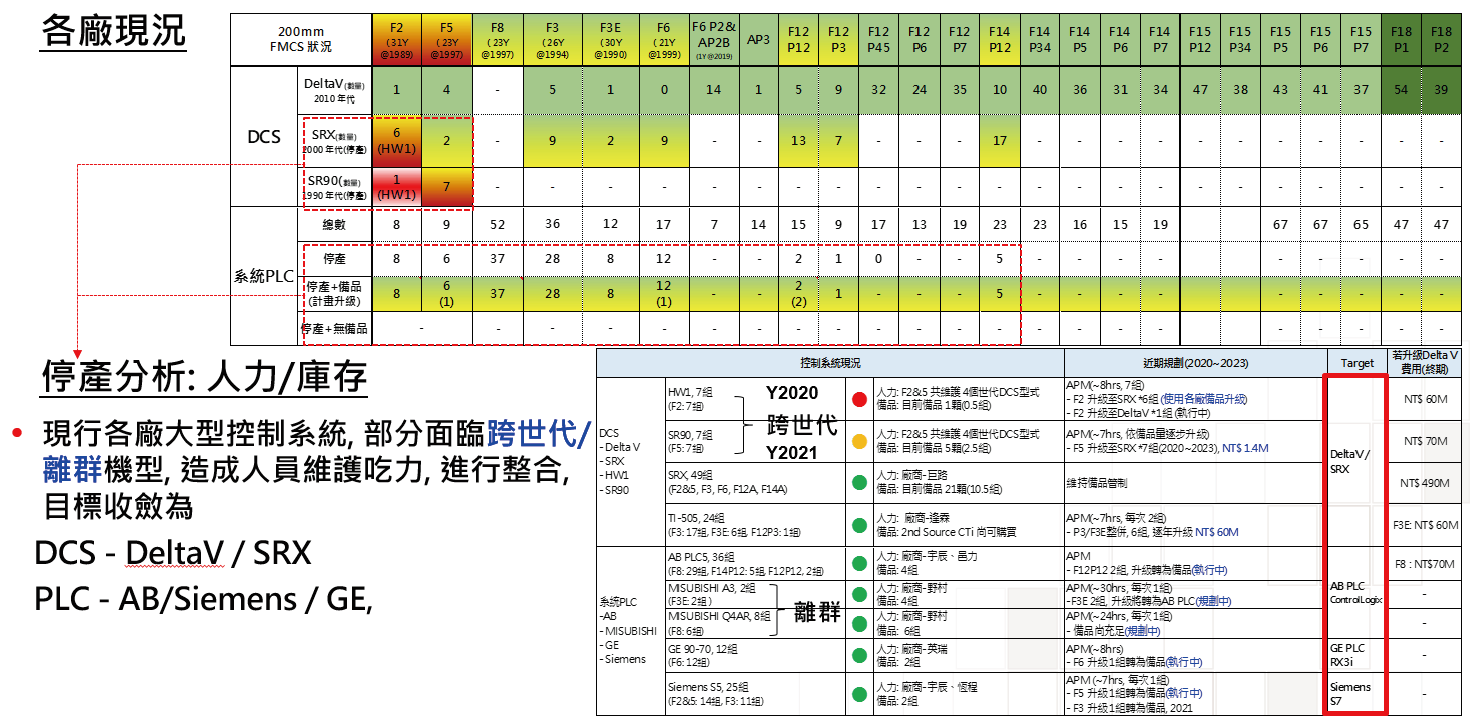
PLC部分 : 全面性調查各重要系統PLC面臨Phase Out/停產/備品不足等問題展開調查,先鎖定問題的範圍,再根據各家PLC廠牌提出升級的解決方案→表3。
停產PLC數量 | F3 | F3E | F12P12 | F12P3 | F8 | F2&5 | F6 | F14P12 | F14P34 |
---|---|---|---|---|---|---|---|---|---|
TI-505 | 17 | 7 | 1 | ||||||
AB PLC5 | 2 | 29 | 5 | ||||||
Siemens S5 | 11 | 14 | |||||||
MISUBISHI A3 | 2 | ||||||||
MISUBISHI Q4AR | 8 | ||||||||
GE 90-70 | 12 |
以Allen Bradley PLC5為例子,PLC-5可程式邏輯控制器在過去30年來一直是極受歡迎的產品之一。但只要是技術就一定有進步的空間,PLC5控制系統進化成ControlLogix,此款高效能的平台能讓您將生產領域(離散、運動管理、製程與安全性),包括極端環境與高可用性應用等,轉換成一個能達到企業聯網目標的全廠式架構。透過安全的網路分享資訊技術(IT)與營運技術(OT)間的資訊可以放大生產能見度→圖5。
圖5、PLC5架構轉換成ControlLogix架構[4]
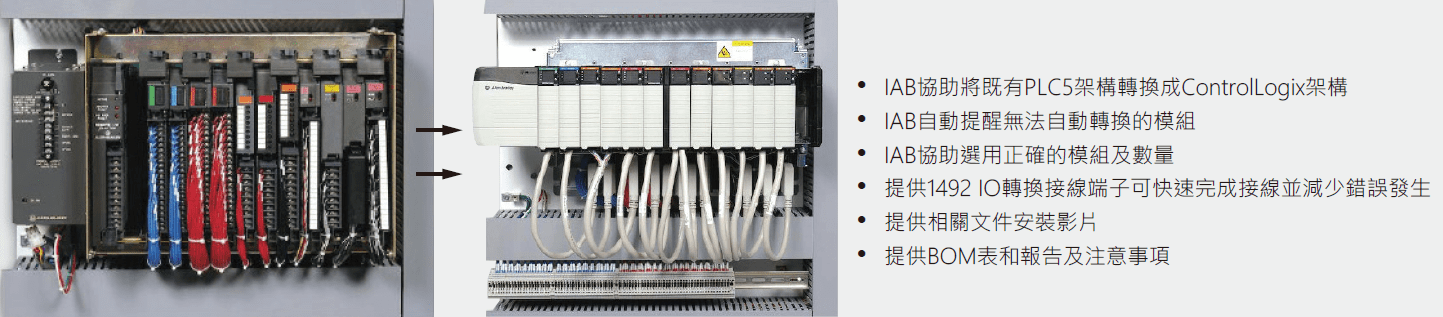
原廠牌PLC的升級計畫提供升級Kit(快速接頭),解決升級面臨的問題 :
- 縮短95%接線時間(系統需要停止生產,大量接線人工及時間)
- 程式可直接轉換or部分修改,不需要全部程式重寫及試車(一般至少需要2~3天時間)這2大優點,讓工廠可以在短時間歲修期間,完成PLC控制系統升級的機會→圖6。
圖6、PLC5轉換成ControlLogix時間比較
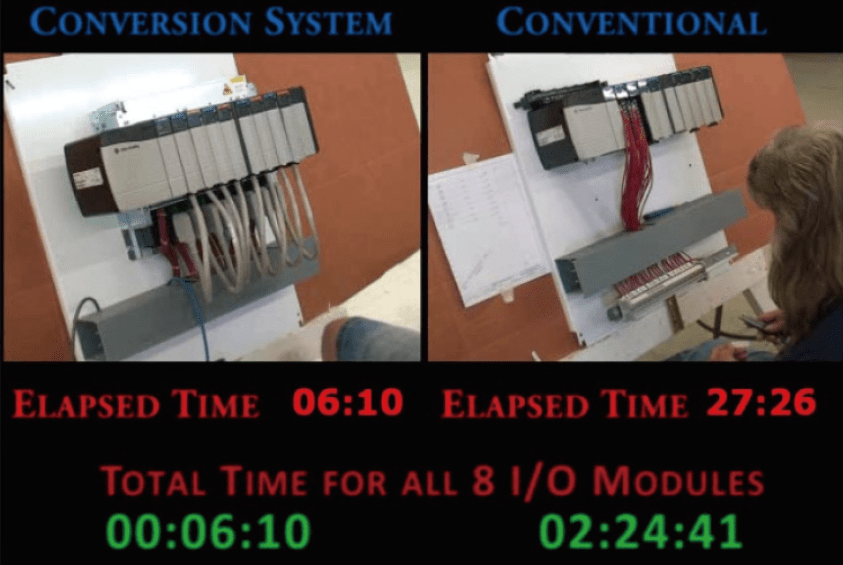
結果與分析
200mm Fab yield約略99%,廠務品質管理,由TSMC FACILITY GENERIC SPC PRACTICE and SPEC. O.I.規範各廠務部門SPC的建立與執行,對廠務供應品質最大的壓力,來至於Utility 水、電、氣、化不預期中斷,而這狀況又以控制系統零件最多且複雜,又面臨產品停產和斷料問題最為嚴重,控制系統全面性翻新是個花大錢且對生產影響時間最久,不是現在唯一的選項。
中期的目標,先善用各廠庫存PROVOX SRX(NT$3M)來取代直接DeltaV升級計畫(NT$130M),透過微型的改善,將離群&高風險控制架構改善到與各廠系統架構一致,達到互相資源共享,且再依廠級重要度排定升級計畫,讓退役下來的備品繼續在200mm廠區延壽,達到最高的經濟效益→圖7。
圖7、DCS & PLC專案目標
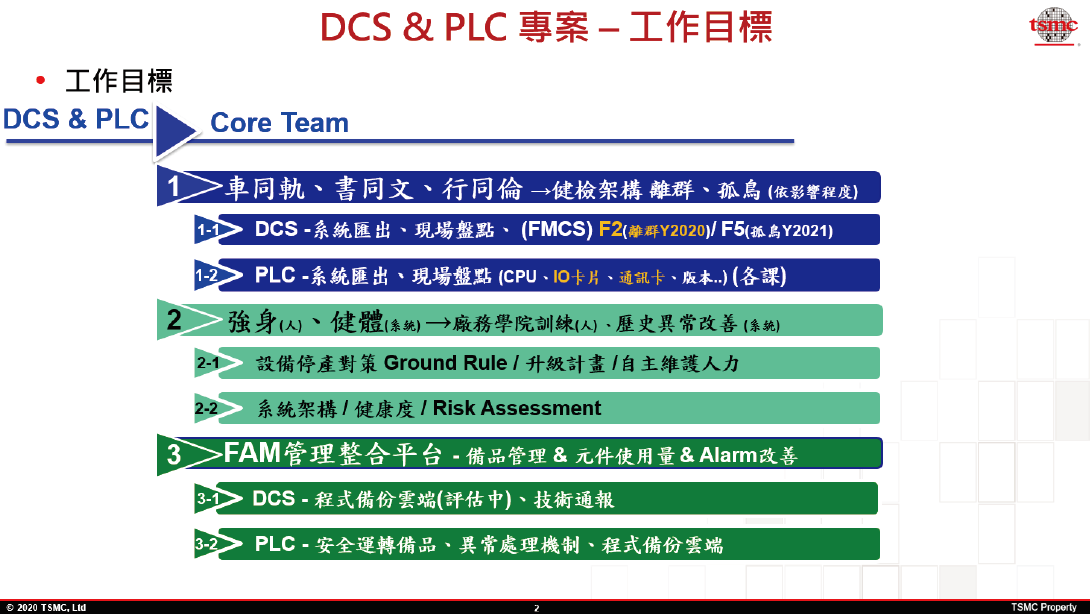
日常運轉的品質 : 使用廠務「開關門十件事」共同平台,來做管理層面的把關,讓整個廠務運轉都使用同一平台來做管理,包含 : ①人員管理,②環保/環境,③施工管理,④系統可靠度,⑤警報/隔離,⑥用量管理,⑦PM管理,⑧供應品質,⑨線上狀態,⑩變更管理等全面性的運轉控管,讓各廠廠務日常運轉能夠做到車同軌、書同文、行同倫→圖8→圖9。
圖8、開關門十件事(車同軌、書同文、行同倫)
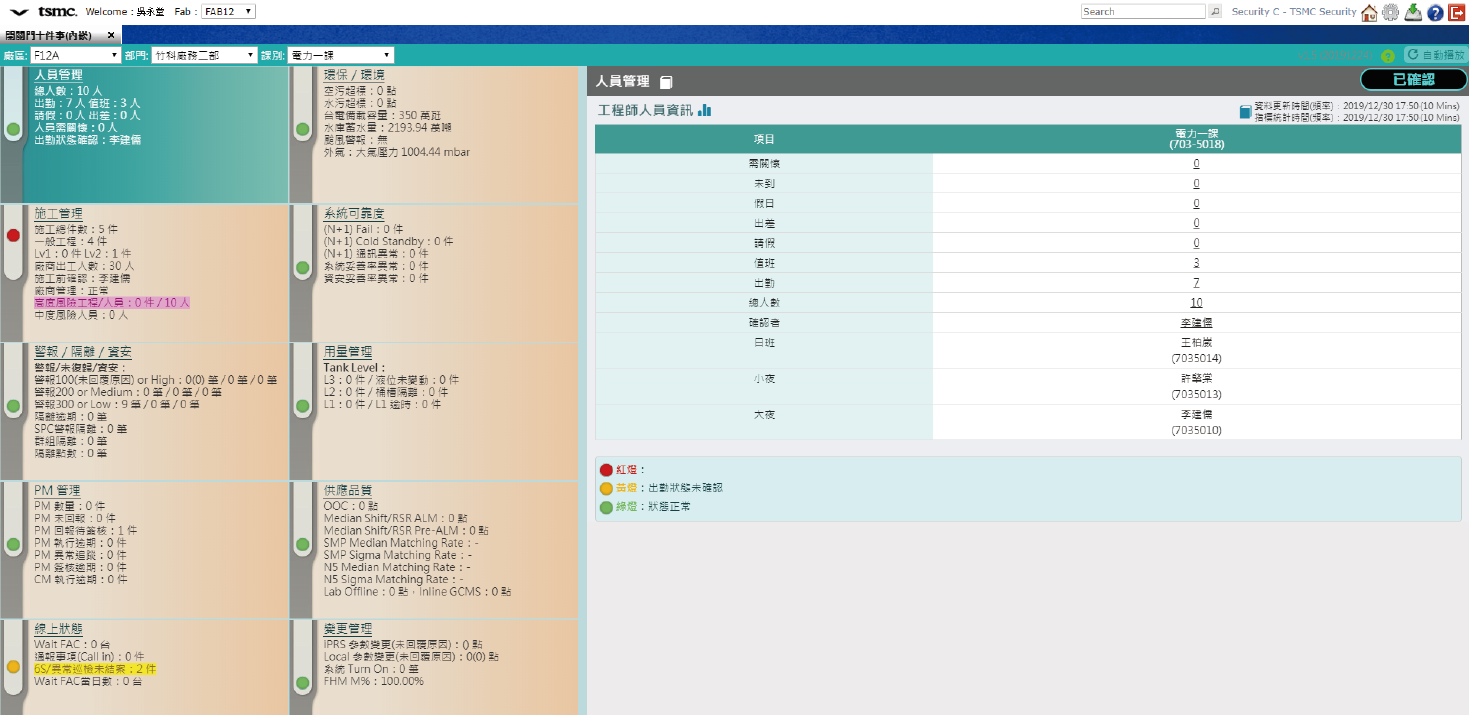
圖9、開關門十件事細部項目
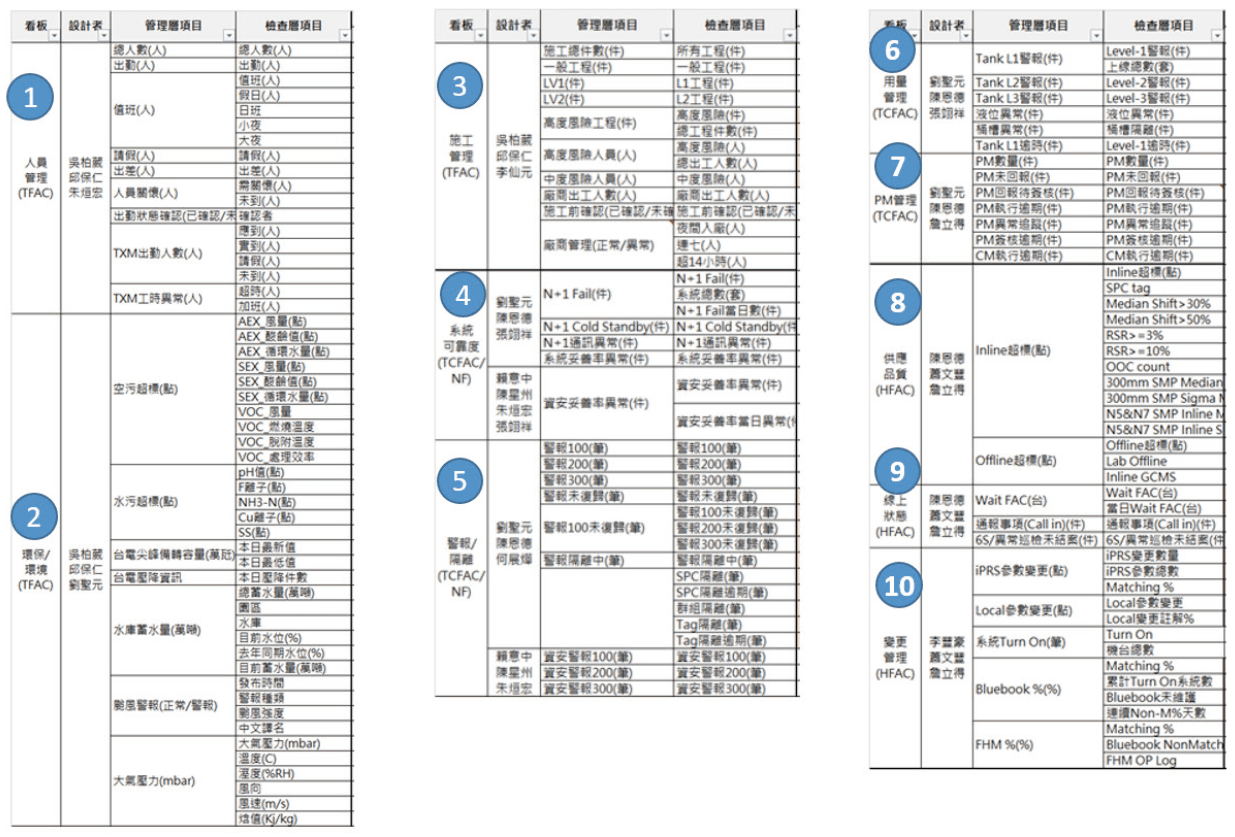
結論
200mm Fab對品質最大的壓力,來至於Utility 水、電、氣、化不預期中斷,而這狀況又以控制系統零件最多且複雜,又面臨產品停產和斷料問題最為嚴重,控制系統全面性翻新是個花大錢且對生產影響時間最久,現階段暫不可行。
200mm Fabs FMCS安全運轉中期計畫如下 :
- DCS原4個世代(Delta V/SRX/SR90/HW1),將整合為2個世代(Delta V/SRX),主要改善為F2(HW1改為HW2與各廠一致)/F5(SR90→SRX),SRX Controller會使用各廠備品支援,共需12顆SRX(F14 : 6/F3 : 2/F12 : 4),重新建構與其他廠一致HW2 DCS架構。
- 未來300mm PROVOX DCS升級後備品可移至200mm繼續沿用,達到最大經濟使用效益。
- 重要系統PLC原4個廠牌(AB/Mitsubishi/GE/Siemens),將整合為3個廠牌(AB/GE/Siemens),維持備品安全管制漸進式升級→圖10。
圖10、200mm運轉改善計畫
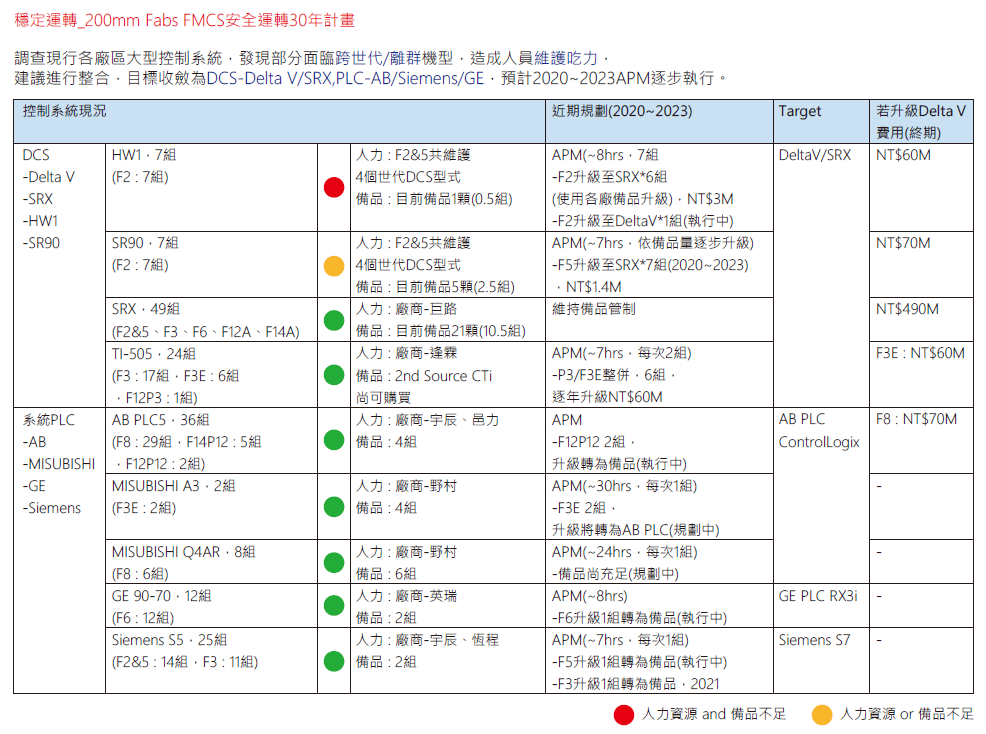
日常運轉品質使用廠務「開關門十件事」共同平台,等全面性的運轉控管,讓各廠廠務運轉能夠做到車同軌、書同文、行同倫,各廠區在同一平台上不斷學習,藉由彼此的交流和融合,達到全面廠務品質管理的目標。
參考文獻
- The Juran Trilogy 朱蘭品質三部曲Posted on 09/15/2013。
- The Fifth Discipline:The Art出版社:天下文化,作者:彼得˙聖吉,譯者:郭進隆,出版日期:1994/07/15。
- 策略管理和TQM架構知識管理的基礎 葉炳煌,民84:38。
- PLC-5 Migration Strategies,Rockwell Automation 2015.
- TSMC FACILITY GENERIC SPC PRACTICE and SPEC. O.I.
留言(0)