摘要
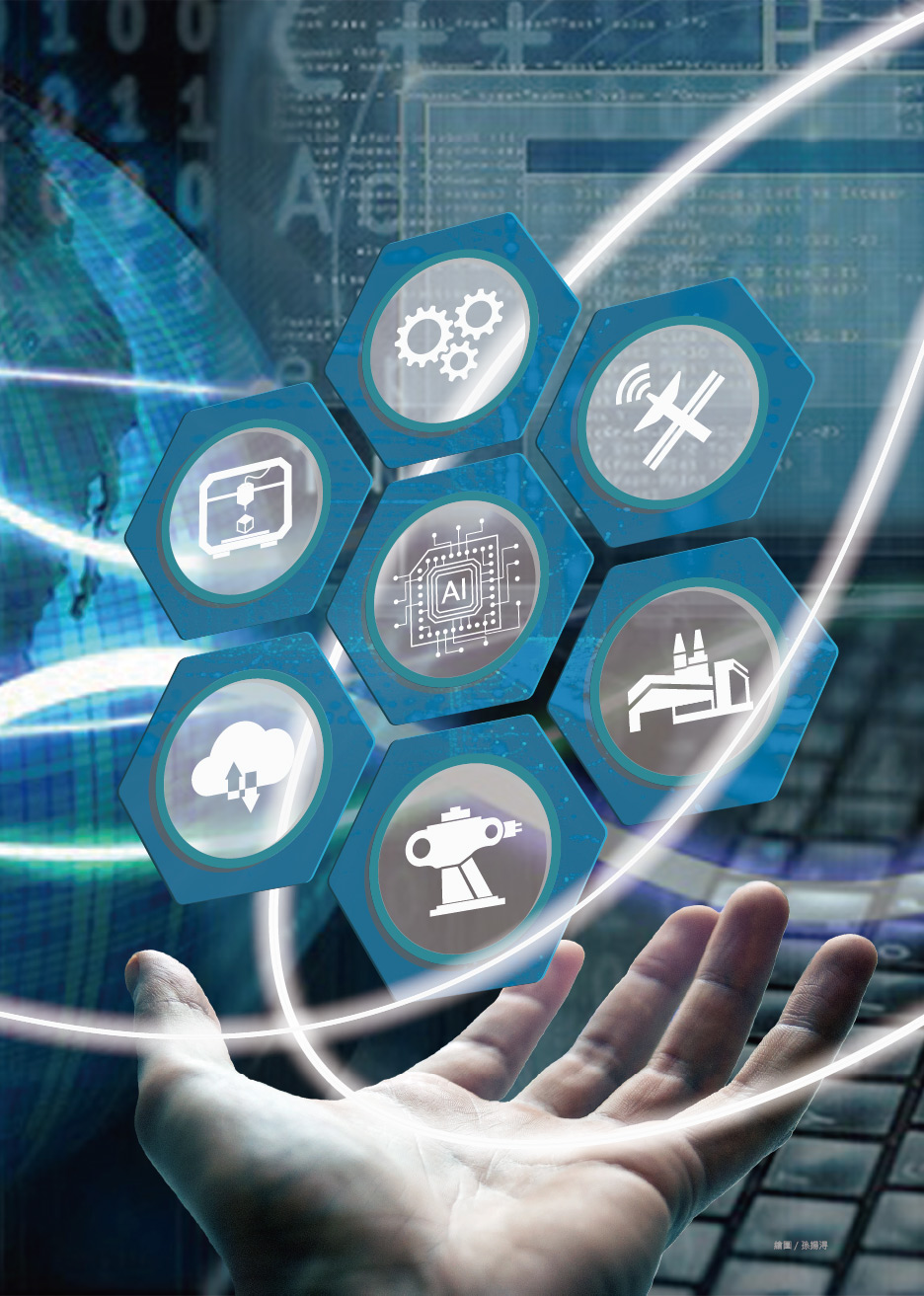
品質管理─廠務品質發展藍圖
前言
有世界質量先生之稱的P.B Crosby定義品質就是符合要求的標準,強調一次就要把事情做好,而且認為品質是來自於預防,而不是檢驗。公司在品質管理手法這一塊已發展多年並導入多項的品質管理機制如福特8D、3L5W等異常事件的分析手法及PDCA、FMEA等運轉重點管理工具。然而依實際運轉的經驗,目前的管理機制是否已經全面涵蓋所有相關資訊是值得深思的問題,以工程異常為例分析廠務近五年EAR以上的事件,人員因素影響線上生產的事件佔48% (19件),其次元件因素佔46%(18件),最後才是PM行為佔6%(2件)。 上述數據指出人員因素在廠務供應品質中佔很重要的一環,但目前的品質管理機制中卻沒有針對人員因素做預防管理措施,因此從如何做好廠務的全面品質管理達到事先預防與源頭管理開始,進一步深入探討廠務的品質管理的現狀跟未來發展方針。
文獻探討
品質的概念從很早以前就已存在,但最初認知的品質是檢驗出來的,而且掌握於生產線上的作業員之手;直至工業革命之後大量生產的時代來臨,且品質管制的責任由作業員轉移到檢驗員身上,而後品質管理隨著工業的進步也有相當發展,Dale將品質管理的發展如→圖1所示依順序分為四個階段 : 品質檢驗(QI) / 品質管制(QC) / 品質保證(QA) / 全面品質管理(TQM),根據各階段的定義及特色比較→表1,現在公司客戶的產品已進入汽車晶片等基於人身安全而對於產品品質與可靠度要求極高的階段,能掌握住每一個細節且能持續改善的TQM才能滿足現階段廠務品質管理。
圖1、品質發展四大階段 (資料來源 : 中國生產力,全面品質保證手冊)

Comparison | Quality Improvement | Quality Control | Quality Assurance | Total Quality Management |
---|---|---|---|---|
Definition | 由檢驗找出產品的缺陷 | 由檢驗找出產品的缺陷 | 預防產品缺陷,期望第一 次就做對 | 工廠全面管理 |
Focus on | 找出有缺陷的產品 | 被動的修正產品中的缺陷 | 積極主動的防止缺陷發生 | 積極主動的防止缺陷發生並 「持續改善」 |
Goal | 檢驗出有缺陷的產品 | 產品完成後找到缺陷 | 改善製造和測試流程,令產品時不會出現缺陷 | 減少產品缺陷、降低成本、提升客戶滿意度,令公司及客戶獲得 最大利益 |
How | 由工具和設備查檢驗出品質 缺陷問題 | 由工具和設備查檢驗出品質 缺陷問題並且解決根源 | 建立良好的品質管理系統 並定期review適用性 | 全員參與品質管理以客戶滿意度 為導向持續改善 |
What | 依靠檢驗過濾掉有缺陷的產品 | 依靠製程技術來維護產品品質 | 有計畫及有系統性的預防 產品的品質問題發生 | 同步工程進行方式:由行銷,產品 設計,製程設計,製造同步進行 |
Responsibility | 測試單位的職責 | 測試單位的職責 | 產品開發團隊每個人的職責 | 公司所有單位成員的職責 |
Statistical Techniques | NA | QC七大手法 | 統計流程控制(SPC) | 包含QC,QA 所有手法 |
As a tool | NA | 糾正工具 | 管理工具 | 全面管理工具 |
Orientation | 生產為導向 | 產品為導向 | 製程為導向 | 以客戶滿意度為導向全員參與 |
對於TQM成功的關鍵因素各專家學者都有獨自的見解,根據各專家提出的文獻進行統計後→表2歸納出TQM成功的前三大關鍵因素首要為全員參與而後依序為顧客導向、主管支持。
學者 | 全員參與 | 顧客導向 | 主管支持 | 持續改善 | 品質資訊分析衡量 | 品質工具技術 | 教育訓練 | 供應商 | 品質策略 | 組織文化 | 品質資訊收集 | 品質系統與品質保證 | 產品與服務市調設計 | 溝通協調 | 執行力 | 品質部門 | 組織結構 | 品質成本 | 預防 | 勞工關係 |
---|---|---|---|---|---|---|---|---|---|---|---|---|---|---|---|---|---|---|---|---|
Snee(1986) | * | * | * | * | ||||||||||||||||
Sohalrtal.(1989) | * | * | * | * | * | |||||||||||||||
Loren(1989) | * | * | * | * | * | * | * | |||||||||||||
Oakland(1990) | * | * | * | * | * | * | ||||||||||||||
Zaire(1991) | * | * | ||||||||||||||||||
Ahmadi(1991) | * | * | * | * | ||||||||||||||||
Bossink(1992) | * | * | * | * | * | * | ||||||||||||||
James(1992) | * | * | * | * | * | * | * | |||||||||||||
Alan(1992) | * | * | * | * | * | |||||||||||||||
Saylor(1992) | * | * | * | * | * | |||||||||||||||
Porter&Parker(1993) | * | * | * | * | * | * | * | |||||||||||||
Price&Chen(1993) | * | * | * | * | ||||||||||||||||
Price&Gaskill(1993) | * | * | * | * | * | * | ||||||||||||||
Saraphetal.(1993) | * | * | * | * | * | * | * | * | * | * | ||||||||||
DahlgaardKristensen&Gopal(1993) | * | * | * | * | * | |||||||||||||||
岳林(1993) | * | * | * | * | * | * | ||||||||||||||
盧淵源(1994) | * | * | * | * | * | * | ||||||||||||||
林清河/周福星/劉漢容/譚伯群(1994) | * | * | * | * | * | * | * | * | * | |||||||||||
BlackandPorter(1995) | * | * | * | * | * | * | * | |||||||||||||
林英峰(1995) | * | * | * | * | * | |||||||||||||||
NASA,潘浙楠譯(1996) | * | * | * | * | * | * | * | * | * | |||||||||||
黃崇烈(1996) | * | * | * | * | * | |||||||||||||||
中國生產力中心(1996) | * | * | * | * | * | * | * | * | * | |||||||||||
梁翰鳴(1997) | * | * | * | * | * | * | ||||||||||||||
簡佩宜(1998) | * | * | * | * | * | * | * | |||||||||||||
次數小計 | 22 | 18 | 16 | 14 | 10 | 09 | 09 | 08 | 07 | 07 | 06 | 06 | 04 | 03 | 03 | 03 | 02 | 02 | 02 | 01 |
全員參與 :
以公司化學品原物料供應流程為例→圖2 : 原物料由供應商製造出來後經過槽車運送到廠內灌充,待灌充完成後經採樣分析確認原物料品質符合公司規範的標準後才會進到廠務系統,最後才輸送供應給線上機台使用,在廠務端亦有online monitor隨時監測以確保供應品質。在上述說明可以看到供應流程中有供應前的檢驗與供應中的監測,倘若我們更進一步探討,可以發現在每個流程都跟人員有密切相關,也就是說整個供應流程有相關的人員都是品質管理重要的一員。所以除了藉由檢驗結果報告及監測系統來控管原物料品質外,建立一套完善的管理機制讓所有成員依循機制做好應該做好的事就是讓全員參與品質管理。
圖2、原物料供應示意圖
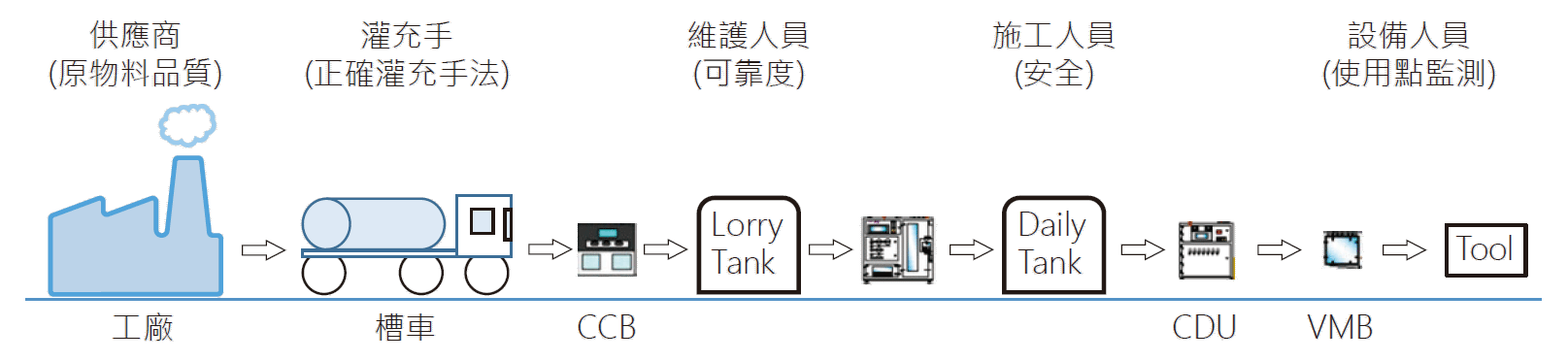
廠務的全面品質管理需涵蓋各面向,其中包含 : 人員、施工、警報、資安、PM、品質、變更、系統備援能力、水電穏定供給、環境大氣壓力的變化等都要有相對應的管理機制。廠務所有的變更都需要有所掌握 ,且變更後造成的影響更是得及早評估,以擬定應對措施,避免因為沒掌握到又或是缺乏考量變更後的影響而造成了本可預防的事故發生。但是廠務的品質資訊是分布於各個平台,而且多年來竹中南的獨立發展有部份系統已經是大相逕庭,導致各系統皆只是部分人員參與造成管理上的遺漏,因此如何涵蓋所有管理範圍,提升日常管理執行效率以及說服全員願意執行為全員參與的重要方向。
顧客導向 :
如→圖3所示隨著技術的演進,伴隨著日益精密的製程所要求的也是越來越高精度的、穏定的原物料供應品質。目前廠務在SPC已經有OCAP與Baseline Control的控管手法,然而工廠隨著技術的演進對品質的要求不斷提高,廠務亦需要引進新的技術與觀念來建立領先工廠的預警機制以滿足工廠對品質管理的需求。此外,廠務如何與工廠的品質平台介接與整合需進行有效的溝通,以達到即早預防而非事後的補救乃是一大課題。
圖3、品質管理需滿足技術發展需求

主管支持 :
高階主管對品質承諾的支持與決心是全面品質管理成敗最重要的關鍵。只有獲得主管的支持,之前所述的全員參與及顧客導向才能在組織內順利推動。
而唯有讓高階主管在活動中有參與感而且必須滿足主管對品質管理的需求,才能獲得管理者全力支持,因此以達到上述條件來爭取主管支持為目標,作為主要的研究方向。
綜合以上探討歸納出未來發展方向→表3。
成功關鍵 | 研究方向 |
---|---|
全員參與 | 全面涵蓋且一致的指標 |
全面適用的管理機制 | |
提升日常管理執行效率 | |
顧客導向 | 建立與工廠有效溝通的平台 |
領先工廠需求的預警機制 | |
主管支持 | 滿足主管對品質管理的需求 |
提高主管的參與感 |
計畫方法
根據文獻探討的結果逐項進行方法研究。
全員參與_全面涵蓋且一致的的指標(全面性、一致性)
為避免因不同廠區面對線上要求不同且人力及時間受限的情況下選擇式的過濾掉review的項目,根據「破窗理論 」(Broken Window Theory)說明不良現象的存在,會因為放置不理的態度而導致該現象的擴散,因此彙整竹中南既有review的機制與平台進行交叉比對並彙整比對結果與建議執行的方向→表4→表5。
分類 | Review item | F12 | F15 | 14 |
---|---|---|---|---|
人員管理 | 總人數/出勤/值班/請假/出差/需關懷 | OneFac | onefac | onefac |
各課值班人員/電話 | 值班公告資訊 ▲ | Alarm 即時通(廠務值班與 製造部值班/副理/部經理) | efac ▲ | |
TXM人數 | TXM工時管理系統 | TXM工時管理系統 | TXM工時管理系統 | |
施工管理 | 施工總件數/LV1/ LV2/一般工程/ 高風險區工程 | OneFac | onefac ▲ | onefac ▲ |
高風險人員/廠商人數 | Construction Plan ▲ | VMS | 風險控管平台 | |
環保/環境 | 空汙/ 水汙未達標點數 | OneFac | THC污染物雲端監控 | onefac |
台電備轉容量 | OneFac | onefac | onefac | |
外氣數值 | OneFac | onefac | onefac | |
天然災害預警 | OneFac | onefac ▲ | onefac ▲ | |
系統可靠度 | 電力/機械/水處理/氣化KPI異常點數 | SI ▲ | onefac DIP | X |
N+1 Fail | OneFac | onefac | onefac | |
空污/水污設備狀態 | SI ▲ | X | SI ▲ | |
警報/變更 | Alarm 數量,警報隔離,即時警報未復歸 | FMP | onefac DIP | onefac ▲ |
用量管理 | Tank Level(Level 1/Level 2/Level 3) | OneFac | onefac | onefac |
PM管理 | PM數量/PM未回報/PM執行逾期/ 異常追蹤/簽核逾期/CM執行逾期 | OneFac | onefac ▲ | onefac ▲ |
供應品質 | SMP點數 OOC, OOS, Median Shift>30%, RSR>3% | OneFac | onefac | onefac |
F-Charter warning點數 | F-Charter ▲ | F-Charter | F-Charter | |
Off-line(COA, SCAD, MQR) | Chemical Lab on ECP ▲ | X | Chemical Lab on ECP ▲ | |
線上狀態 | 值班交接宣導通報事項(Call in) | 值班組長Daily Mail & 值班守則 : ▲ | X | 值班組長Daily Mail & 值班守則 ▲ |
FAC EAR | OneFac | onefac ▲ | onefac ▲ | |
巡檢異常 | 值班Excel控管 ▲ | X | X | |
Wait FAC | FMP | onefac | onefac | |
變更管理 | 參數變更(IPRS) | iPRS/FMP | 廠務系統參數變更管理系統 ; 即時參數(P1234) IFPMS(P5/P6) | ECM |
Blue book matching rate | 窗口Mail通知 : ▲ | X | X |
需改善 ▲ 、無: X
管理層 | 檢查層 | 說明 | 燈號 | |
---|---|---|---|---|
1 | 人員管理 | 工程師人員資訊 | 出勤狀態未確認 | 黃燈 |
2 | TXM人員資訊 | TXM工時超時 | 紅燈 | |
3 | TXM人員資訊 | TXM工時加班 | 紅燈 | |
4 | 環保/環境 | 空污超標 | 空污超標>=1點 | 紅燈 |
5 | 水污超標 | 水污超標>=1點 | 紅燈 | |
6 | 台電備載容量 | 台電備載容量<90萬瓩 | 紅燈 | |
7 | 大氣壓力超標 | 大氣壓力超標 | 黃燈 | |
8 | 颱風警報 | 颱風警報 | 黃燈 | |
9 | 施工管理 | 今日工程 | 施工前未確認 | 黃燈 |
10 | 廠商管理 | 夜間入廠 | 黃燈 | |
11 | 廠商管理 | 連七 | 黃燈 | |
12 | 廠商管理 | 超14小時 | 黃燈 | |
13 | 施工品質管理 | 高度度風險工程(監工) | 紅燈 | |
14 | 施工品質管理 | 高度度風險人員 | 紅燈 | |
15 | 施工品質管理 | 中度風險人員 | 黃燈 | |
16 | 系統可靠度 | 系統可靠度異常資訊 | N+1 Fail | 紅燈 |
17 | 系統可靠度異常資訊 | N+1 Cold Standby | 黃燈 | |
18 | 系統可靠度異常資訊 | N+1通訊異常 | 黃燈 | |
19 | 系統可靠度異常資訊 | 系統妥善率異常 | 黃燈 | |
20 | 系統可靠度異常資訊 | 資安妥善率異常 | 黃燈 | |
21 | 當日系統可靠度異常資訊 | N+1 Fail當日數 | 黃燈 | |
22 | 當日系統可靠度異常資訊 | 資安妥善率當日異常 | 黃燈 | |
23 | 警報/隔離 | 警報資訊(歷史警報) | 警報100已復歸 | 紅燈 |
24 | 警報未復歸資訊 | 警報100未復歸 | 紅燈 | |
25 | 警報未復歸資訊 | 警報200未復歸 | 黃燈 | |
26 | 警報隔離資訊 | SPC隔離逾期 | 紅燈 | |
27 | 警報隔離資訊 | Tag隔離逾期 | 紅燈 | |
28 | 用量管理 | 桶槽用量管理資訊 | Level-1逾時警報 | 黃燈 |
29 | 桶槽用量管理資訊 | Level-2警報 | 黃燈 | |
30 | 桶槽用量管理資訊 | Level-3警報 | 紅燈 | |
31 | 桶槽用量管理資訊 | 桶槽隔離 | 黃燈 | |
32 | 桶槽用量管理資訊 | 液位未變動 | 黃燈 | |
33 | PM 管理 | 今日 PM 資訊 | PM執行逾期 | 紅燈 |
34 | 今日 PM 資訊 | 簽核逾期 | 紅燈 | |
35 | 今日 PM 資訊 | CM執行逾期 | 紅燈 | |
36 | 供應品質 | SPC資訊 | Median>50% | 紅燈 |
37 | SPC資訊 | RSR 10% | 紅燈 | |
38 | SPC資訊 | OOC>0 | 紅燈 | |
39 | SPC資訊 | Median>30% | 黃燈 | |
40 | SPC資訊 | RSR 3%>0 | 黃燈 | |
41 | SPC資訊 | SMP<100% | 黃燈 | |
42 | Lab Offline | Offline超標OOC>0 | 紅燈 | |
43 | Inline GCMS | Offline超標OOC>0 | 紅燈 | |
44 | 線上狀態 | 線上狀態資訊 | Wait FAC | 紅燈 |
45 | 線上狀態資訊 | 通報事項(Call in) | 黃燈 | |
46 | 線上狀態資訊 | 6S/異常巡檢未結案 | 黃燈 | |
47 | 當日狀態資訊 | Wait FAC當日數 | 紅燈 | |
48 | 變更管理 | 系統Turn on | 系統Turn on | NA |
49 | iPRS參數變更管理 | iPRS參數變更>0 | 黃燈 | |
50 | Local參數變更管理 | Local參數變更>0 | 黃燈 | |
51 | TII & Bluebook M% | 連續七天<100% | 紅燈 | |
52 | FHM & Bluebook M% | 連續七天<100% | 紅燈 |
全員參與_全面適用的管理機制(適用性)
管理指標並非單獨的存在,必定先有合適的管理機制,而後才能產生適用的平台功能。在平台設計過程及試運轉過程中,預期使用者一定會反映許多管理機制方面的問題,為此必須設計出管理機制決策流程,使相對應的指標得以維持一致性,進而維持使用者的共識及信任。因此適用性決定管理機制是否能被落實執行,而適當的系統決策成員及流程的建立,則是適用成敗的關鍵。 如→圖4所示,需要有個系統專業決策功能,以確保適用性。
圖4、系統決策成員及流程
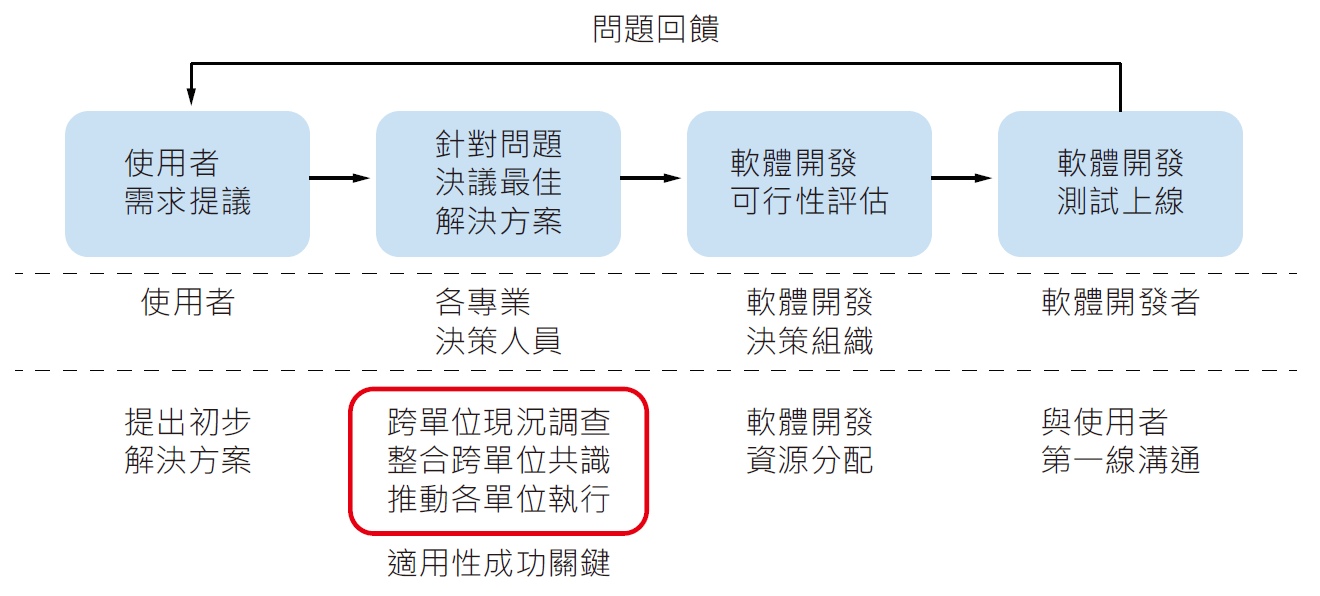
全員參與_提升日常管理執行效率
整合平台 :
由多年開發平台的經驗告訴我們,若是開發者忽略運轉的需求其結果往往是開發出來的產品沒辦法有效的協助負責日常運轉人員,導致該平台的使用率不佳,而為了要補足舊平台的不足有些單位又開發出新的平台 ,如此疊床架屋的狀況下最終結果就是一個廠區同時存在很多個系統;根據手錶定律敘述「當一個人只有一隻手錶時可以有效的掌握時間,但是同時擁有兩隻手錶時反而會對時間準確失去了信心」說明過多的系統反而會導致工程師無所適從且疊床架屋的系統在操作上浪費過多時間而錯失了掌握變異的最佳時機,因此品質管理平台的設計與管理指標定義有沒有將所有人員的運轉經驗充分導入,便決定了該平台所輔佐的制度於未來執行成功與否。
盤點竹中南各廠區人員針對控管相關事項,每日需確認的指標共有142項功能。但就現階段而言上述管理指標分散於各平台無法有效率的將所有相關的資訊迅速連結,因此耗費過多的操作時間會影響工程師配合意願。所以將上述142項功能整合為單一看板讓管理者可一目了然,在最短時間內掌握系統運轉狀況→圖5。
圖5、廠務資訊看版資料來源示意
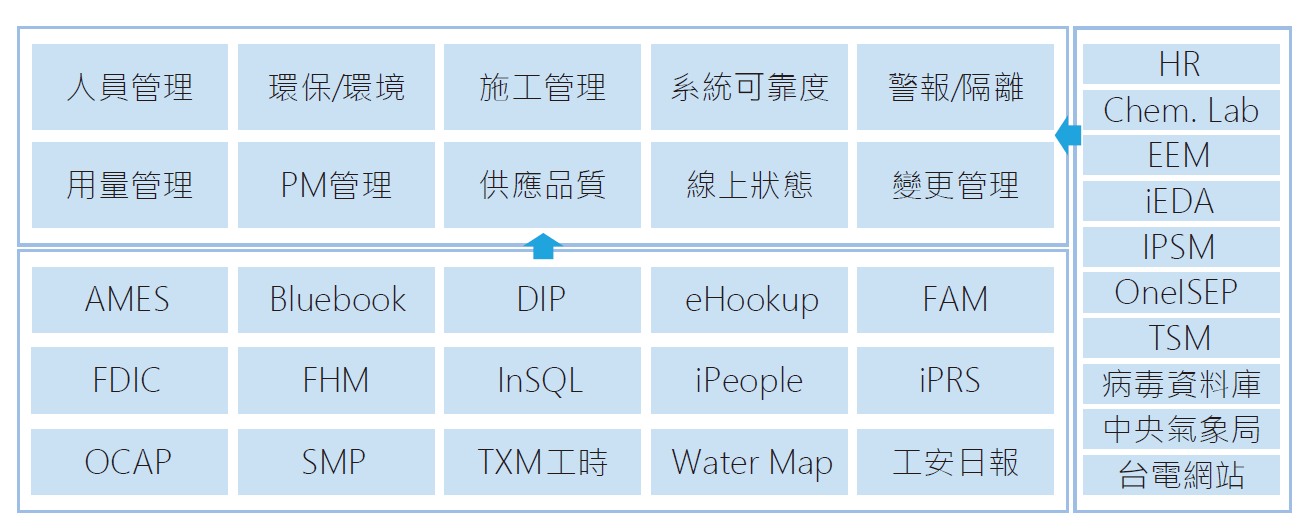
導入AI :
管理指標的訂定與異常狀態判斷以現階段的技術都是由人來定義相關規則,之後才經電腦要依規則的運算結果進行預警,也就是由人來決定認為要看哪一些指標,挑出來以後要用哪一種規則去卡也是由人員自行去定義,但是該判斷規則是不是最周延的往往需等到所有可能的異常事件都發生後才能確認;如果能從收集到的大數據中分析出該系統的運轉特性從而找出最周延的預警機制就能達到事先全面防範的目的。但是要做到這一點就必須先有完整的、大量的、長時的數據收集再加上匯整各領域專家的知識與經驗作為分析的基礎,逐步以AI 為基礎進行架構才有能力達到運轉時及早告知變異即將發生,讓運轉人員有充分時間可事先去除造成變異的原因,用最輕鬆的方式做好廠務全面品質管理。
顧客導向_與工廠有效溝通
跟工廠做好有效溝通的第一步就是了解工廠怎麼樣在做品質管理,知彼知己才能達到滿足客戶需求做好全面品質管理的目標。比如目前工廠以ICCI做為異常變異檢知的系統,廠務如何與其搭接才能整合出全面的、即時的、不掉棒的品質管理機制,做到站在工廠的角度來解決問題的高度→圖6。
圖6、廠務導入ICCI評估
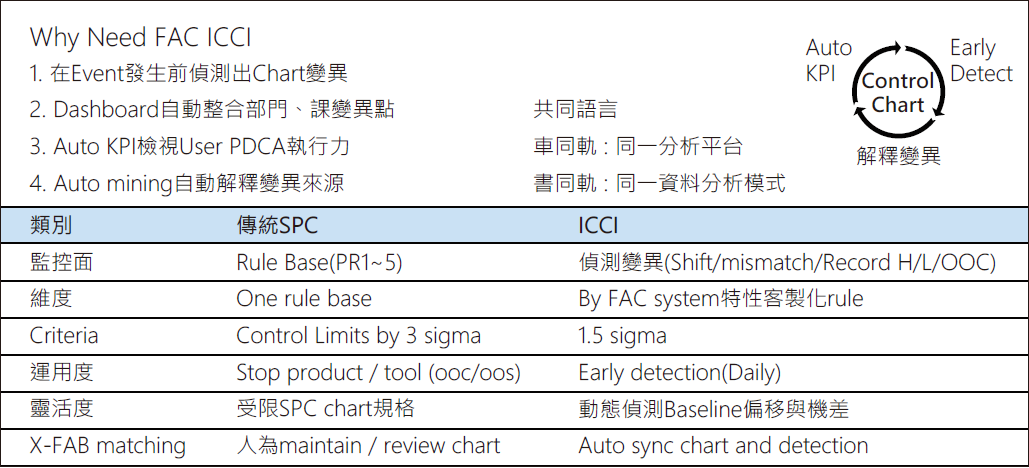
顧客導向_領先工廠需求的平台
廠務的品質管理依據製程技術的提升、新技術轉移到投產的組織流程規劃等必需更早地進行自我檢視並調整進化到為新技術的大量投產做好事前準備,達到任何廠務的變異都可以在這最新的機制下得到全面的、完整的掌握。廠務針對變異發生的處理方法可依發生時的應變處理時間前後分階段論述 :
事後處理:
主要是廠務品質的異常發生後工程師被動的確認供應品質有受到影響,更甚者該變動已經影響到生產時就需要啟動EAR及L/L機制預防未來再次發生。
現時預警:
該機制是在廠務的品質發生變異當下立即有告警機制如 : OOW、OOC、OOS、base line shift,由工程師立即確認該變異是否是在計畫中且已有對應的管控機制,若確認該警報實屬非計畫中的變異即須立即應變以防止影響擴大造成生產線上的影響,目前的主要強化機制是擴大品質異常判斷規則的涵蓋範圍。
事先預防:
目前在SPC上有OOB、Pre OOB的即早預警機制,而在系統的元件有FMEA分析以預知變異發生的機率及預測出影響的嚴重度可早一步強化系統增加系統穩定度,目前已經開始評估導入IoT、Big data與Expert system的技術藉由更全面更即時的製程掌握可在變異發生前就可以得知,進一步能控制每一項的變異,預防事件的發生。這個事先預防部分的強化是本文要研究的重點。如→表6所示,整合廠務及工廠現行的管理方式及技術,並規畫出未來可能導入的預警方法及技術。
Existing | New Tech | |
---|---|---|
事後處理 | EAR (3L5W)、L/L | iPRS、mismatch、8D / KT |
現時警報 | OOW / OOC / OOS、MS / RSR | iFlag、F-Charter rule |
事先預防 | FMEA、OOB、Pre OOB | IoT、Bigdata、Expert system |
主管支持_滿足主管對品質管理的需求
比起廠務系統變異後的即時通報機制,管理者更在意的是如何預知變異的發生來進行預防跟改善,分析了各廠區間多年的運轉(含event)經驗後即可針對每件event來建立有效的領先指標,其中包含人員管理與施工管理預防MO問題以及PM管理來預知元件異常的問題等→表7。
Component Fail | MO | PM Activity | Total | |
---|---|---|---|---|
G&C | 5 | 9 | 2 | 16 |
MSS | 1 | 2 | 0 | 3 |
Power | 9 | 5 | 0 | 14 |
WTS | 4 | 2 | 0 | 6 |
總計 | 18(46%) | 19(48%) | 2(6%) | 39 |
除了強化品質控管之外,主管對於品質管理所投入的人力成本是否合理是很在意的,幾乎所有品質相關規劃都會被要求不要增加工程師的負擔,因此還需建構一個可以同時管理廠區數十個品質管理的領先指標而不會增加人力負擔的方法。應用先前所提及的整合平台及導入AI將是降低品質成本的主要方向。
主管支持_提升參與感
透過研討會中的彙報方式引導討論是提升主管參與度有效的方法。在開發流程中,我們設立了常設的品質方法提升會議,其中包含所有利害關係人的成員。並連結各系統連線會議收集意見且定時的回報進度,讓所有主管都能成為開發、設計及推廣的一員。
結果與分析
上述方法經多方面的推廣後成立了常設的品質精進會議,並依此成立開關門十件事開發專案,橫向功能包含人員管理、施工管理、外排及環保/環境、系統可靠、警報、用量控管、PM管理、供應品質、線上狀態、變更管理→圖7。
圖7、開關門十件事
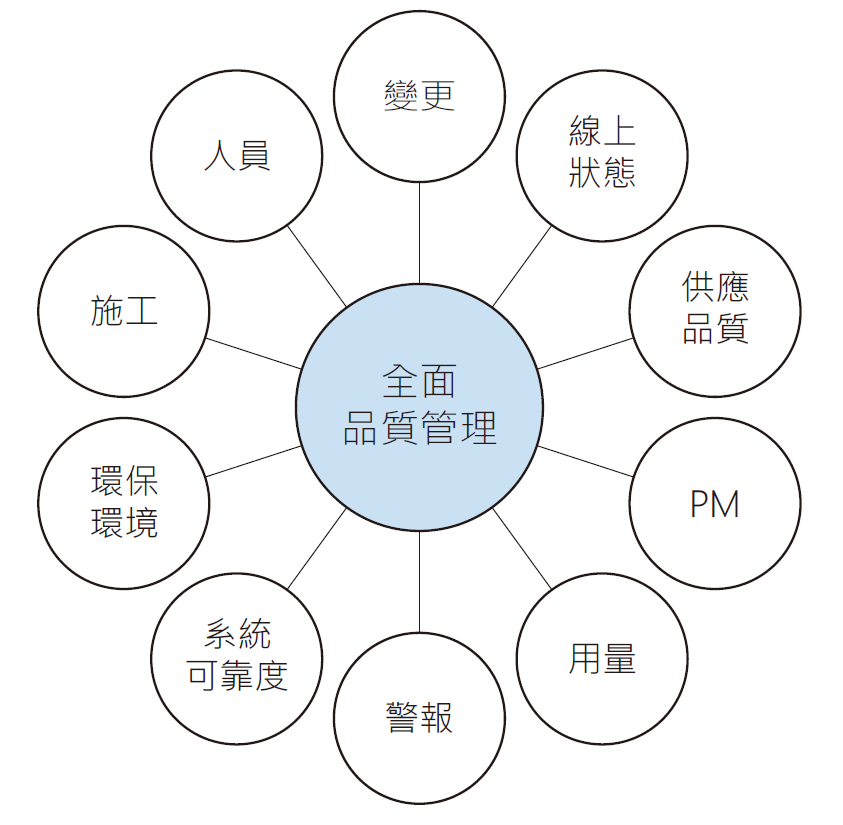
縱向則含蓋部門主管做好日常管理所需的管理層、第一線主管所需的檢查層、線上工程人員所需的作業層;未來將以本研究所提到的由全員參與、顧客導向及主管支持延伸出的七大方向作為廠務品質管理藍圖的主軸→圖8。
圖8、廠務資訊看板設計概念

結論
成功的廠務品質管理系統必須具備全面涵蓋且一致的品質指標,合適的管理機制以及實務上具備簡單、容易操作又能透明快速地與工廠同步的操作平台;達到即時又精確的異常預警及異常快速定位的功能。而要建立高品質的管理系統則必須透過滿足主管對品質的管理需求以及提高主管的參與感與認同來取得主管支持。
開關門十件事看板將是達成上述目標第一步的解決方案,未來發展會隨之與時俱進發展為更全面的品質管理系統→圖9。
圖9、廠務品質管理發展歷程
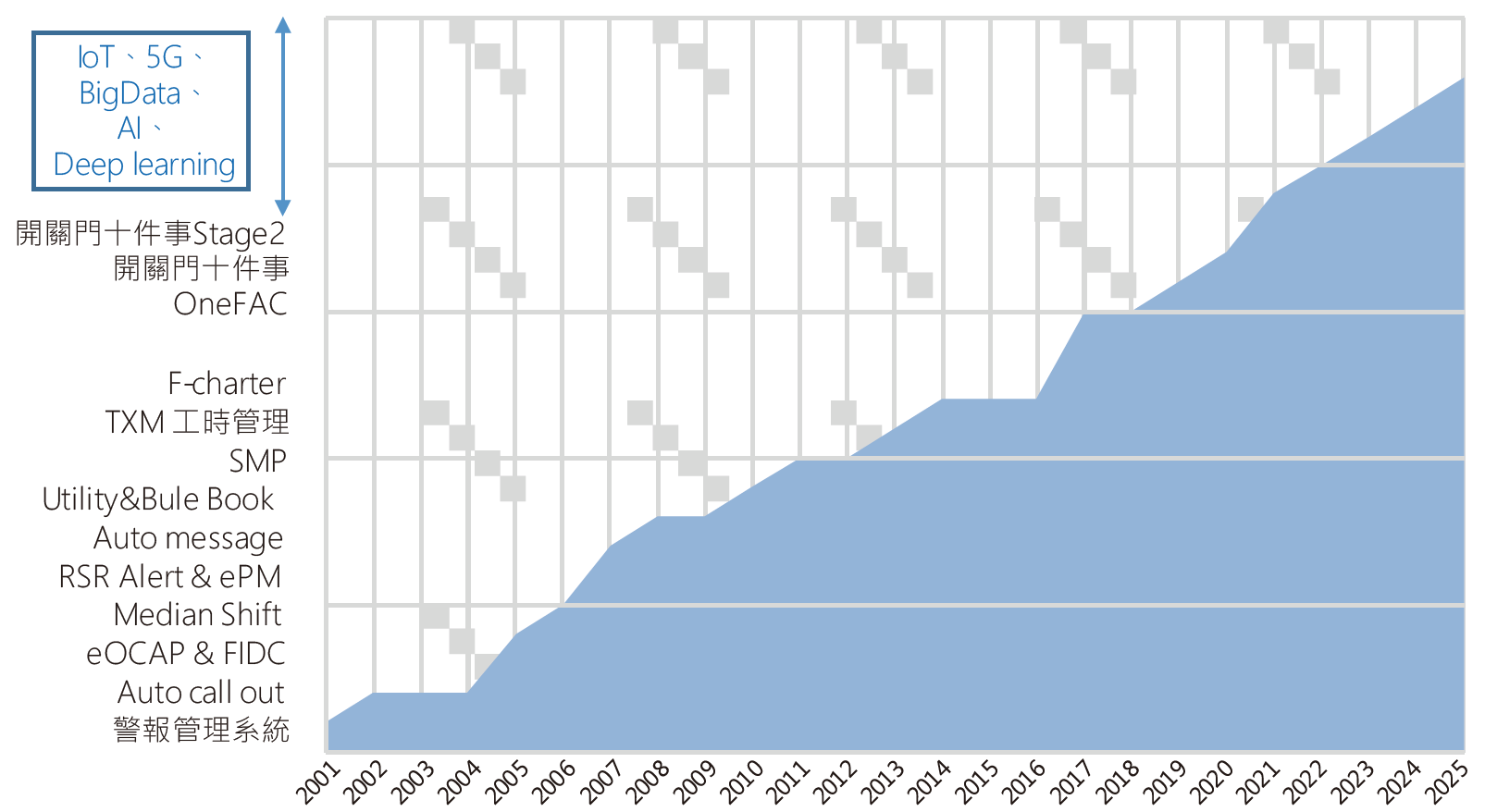
參考文獻
- 林宜隆,主計資訊系統建立風險預警與監控機制之研究,2016。
- 蘇桂月,全面品質管理於壽險新契約流程之應用研究,政治大學 ,2003。
- 張俊源,品質管理的成長與未來,品質管制月刊,1998。
- 中國生產力中心 全面管理組,TQA 全面品質保證手冊,台北市,中國生產力中,1998。
- 王宗華,可靠度工程與管理品質,品質學會,2010。
- 吳鄭重,裘蘭品質領導手冊,初版,台北,中國生產力出版, 1994。
- 周旭華,戴明的管理方法,第一版,台北,天下遠見出版,1997 。
- 徐世輝,全面品質管理,華泰文化,2006。
- 陳怡芬,不流淚的品管,第二版,台北,天下遠見出版,1984。
- 潘浙楠,品質管理:理論與實務,第三版,華泰文化,2016。
- 鄭榮郎,生產與作業管理,第五版,全崋出版社,2018。
- Kanji, Gopal k., " Total Quality Management in Action" , Fist Edition, Chapman & Hall, 1996。
- Webber Larry, Wallace Michael, " Quality Control for Dummies" , For Dummies, 2012。
- tsmc品質管理Workshop報告資料,2019。
- tsmc廠務資訊看板90% design review會議報告資料,2019。
留言(0)