摘要
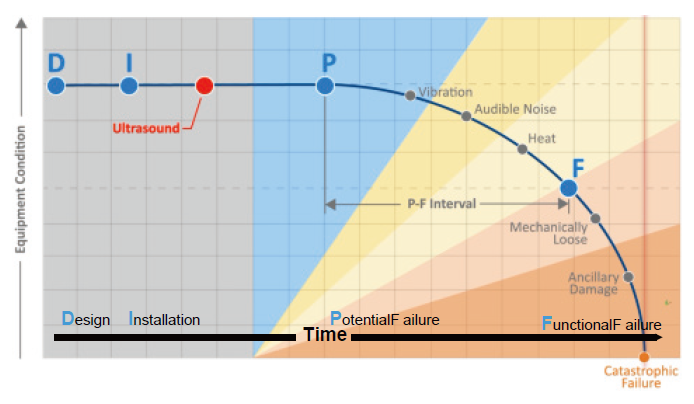
馬達軸承潤滑改善與超音波預知保養手法探討源分析
Keywords / Bearing,Lubrication,Grease,Ultrasound Measurement,Predictive Maintenance.
馬達故障原因中,軸承故障佔41%,大部分為潤滑不良造成。潤滑失效中最主要因素為潤滑不足,造成介面間直接摩擦而磨損。然而潤滑不足導致的因素卻不只是油加的不夠,反而過度注油也會間接造成潤滑不足與其他不良影響。
PMOI規範定期定量補油的方式做預防保養,然而每顆軸承潤滑的狀態不一,所需油量也不盡相同。傳統上軸承預知保養以震動量測為主流,但測得訊號時也代表軸承介面之間已產生不可逆的功能性損傷。因此若能提早測得潤滑不足並隨即補油,即可延長軸承壽命,而超音波則為潤滑狀態最早期的檢測訊號。
本文分析滑脂失效原因以及探討保養計畫來改善保養手法,並引進超音波檢測的方式來判斷潤滑狀況,使馬達軸承能從預防保養提升到預知保養的模式,並探討未來更進一步以自動注油器的全自動潤滑保養的可行性。
Bearing is accounted for about 41% in all component failure of electric motor and most of it is failed due to poor lubrication.The main reason of lubrication failure is lack of lubrication which makes the interface surfaces contact to each other directly. However, lubrication fail is caused not only by lack of lubricant but also by overfill.
Only lubricant quantity and refill interval is defined in our PMOI for preventive maintenance of bearing lubrication. In fact, the actual lubricant requirement depends on each bearing under varied operation condition. Conventionally, bearing vibration test is the major method for predictive maintenance but there is irreversible damage when vibration signal can be detected. The bearing lifespan will be extended if lack of lubrication can be found in the early stage and refill soon, which is possible by measuring ultrasound signal.
This article includes analysis of lubrication failure, investigation of lubrication plan, and introduction to determine the lubrication condition by measuring ultrasound signal. The refill schedule and quantity are based on the lubrication condition of each bearing and the maintenance work can be implemented automatically by lubricator, which is predictive maintenance for electric motor bearing.
1. 前言
馬達故障原因中,有41%為軸承故障所致[1],其中大部分為潤滑不良。因此做好潤滑保養就能大幅提升馬達的可靠度。潤滑油脂(grease,以下簡稱滑脂)對高溫敏感,70度以上時,每上升10度其壽命減少33%,高溫160度以上時壽命減半(圖1)[2]。馬達運作時因線圈本身發熱外,轉速較高且長時間持續運轉,因此其軸承對潤滑的需求與其他一般機構件的軸承相異。
PMOI中雖訂定馬達軸承的預防保養模式-定期定量補充,並未詳述具體的保養手法。因此長時間定期定量補充滑脂後,最終會將軸承室注滿滑脂。過多的油若無法適當排出,則會造成軸封損壞而往外或往線圈室內洩漏(圖2)。線圈室內堆滿滑脂會影響線圈散熱,增加絕緣裂化的風險與縮短壽命[3]。一旦線圈絕緣擊穿,馬達就壽終正寢,造成非預期性跳機與長時間拆出整修的風險。此外,滑脂也會因攪動升溫而過熱,加速滑脂氧化並產生軸承卡死造成其他機件損壞的風險。
潤滑不足時,軸承介面之間開始磨擦:表面粗糙的凸點(asperity)彼此撞擊產生超音波,透過偵測此超音波強度,可作為油膜厚度的判斷依據。NASA於1974年設計實驗證明:超音波訊號為軸承失效過程的最早期訊號[4],此時只要及早補油,對軸承還未產生顯著影響,也非傳統加速度規震動量測所能測得。從 圖3的P-F曲線中可看出:超音波位於潛在失效初期之前,因此在這階段潤滑不足時即可測得;失效初期是震動,噪音與熱的徵兆會依序出現。因此在現場聽到噪音與量到明顯高溫時,已是失效階段的後期,很快會發展成完全故障損壞的狀態。
本文透過分析潤滑失效的成因來改善保養手法,盤點滑脂適用性、保養週期與補油量以及補油程序,藉由改善保養手法來做好潤滑,提升馬達軸承使用壽命,同時降低系統運轉風險。先做好預防保養的基礎,再探索預知保養的應用,期望能提升馬達軸承的可靠度。
圖1、滑脂壽命與溫度關係圖[2]
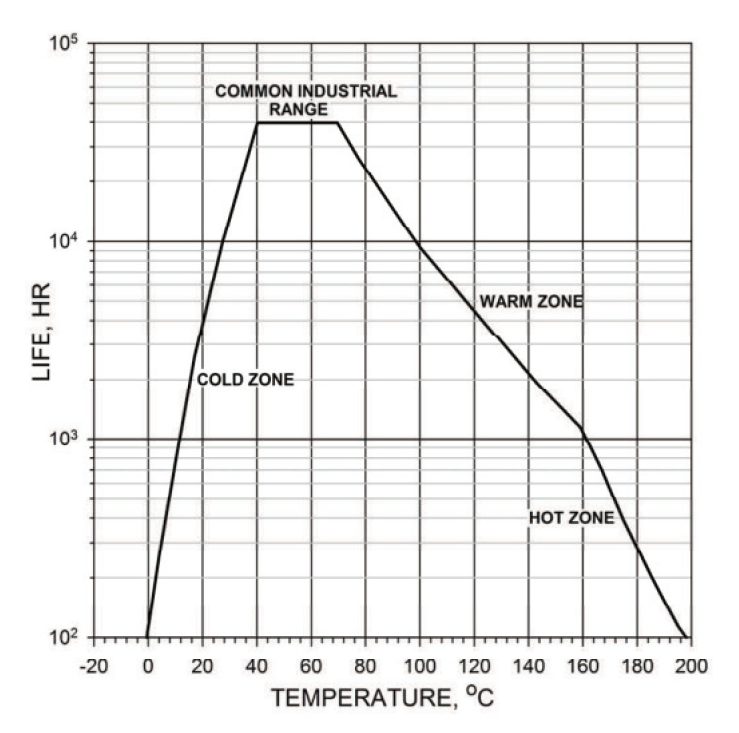
圖2、潤滑油脂軸封洩漏示意圖
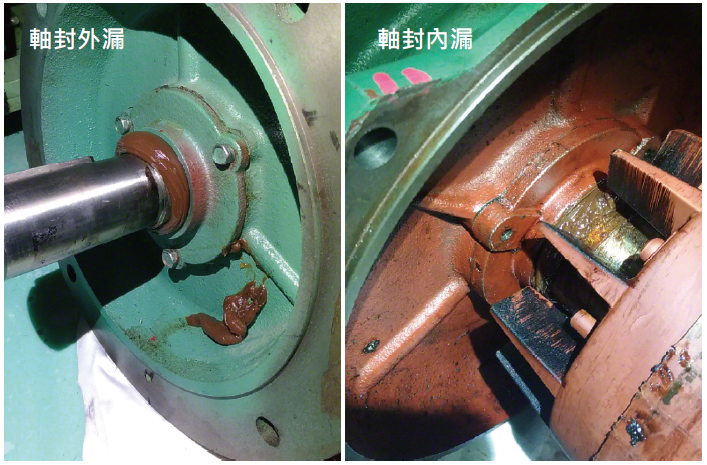
圖3、軸承失效P-F曲線[5]
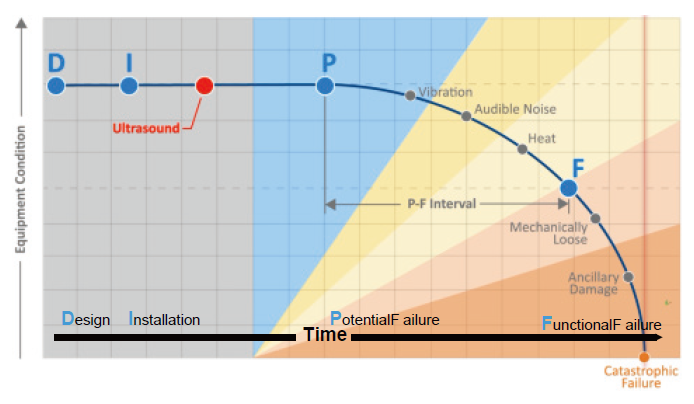
2. 文獻探討
2.1 潤滑油脂介紹
潤滑劑可分為潤滑油脂(grease,以下簡稱滑脂)與潤滑油(oil),其中滑脂以約80%基礎油(base oil)、15%增稠劑(thickener)與5%添加劑(additive)所組成,能夠簡易的塗抹與附著,不需要配管、儲槽與泵送設備,並能隔離外界汙染如雨滴、粉塵等;其缺點為增稠劑對溫度影響較大,熱傳導不良散熱性差。因此大部分馬達軸承潤滑需求主要皆為滑脂,而台積廠內的軸承也幾乎使用滑脂作為潤滑劑,選擇適當的滑脂對於設備壽命有直接影響,因此對滑脂的認識有其必要性。
2.1.1 基礎油(base oil)-黏度(viscosity)
滑脂有近80%為基礎油構成,油也是主要參與潤滑的關鍵,因此油的黏滯係數決定滑脂的應用層面。黏滯性不只影響油膜厚度,也與能量耗損有關,可想像用湯匙攪拌蜂蜜或水時施力的困難度,即為驅動力的差異。基礎油除了常見的礦物油(mineral oil)外,另有人工產生的合成油(synthetics oil),具有性能與壽命的優勢,因此常為高階油品所採用。
2.1.2 增稠劑(thickener)-稠度(consistency)
滑脂的三大關鍵組成之一,增稠劑雖然不是直接的潤滑者,但卻扮演著重要的角色。增稠劑為長鏈的纖維分子(如 圖4),與基礎油混和後,分子之間形成網目結構以凡得瓦力與毛細作用來抓持基礎油[6],使滑脂能形成半固態的狀態。
增稠劑所佔的比例影響滑脂的稠度,從000到6級共9種級別由美國國家潤滑脂協會(National Lubricating Grease Institute, NLGI)所定義,數字越大越趨近固態,反之則越接近液態(圖5)。稠度應用之對照如 表1,增稠劑種類與應用需求對照如 表2,稠度影響滑脂的重要指標如 表3。
增稠劑種類可略分為金屬皂基與非皂基,前者常見的為鋰皂基,後者為聚脲基。不同種類的增稠劑對應不同的應用需求,彼此間一般不建議混合使用。若非不得已則務必確認相容性,避免產生硬化、液化或乳化等現象而造成潤滑失效。
圖4、增稠劑微結構 : 左為Shell Alvania S長鏈型;右為Shell Sunlight短鏈型[8]
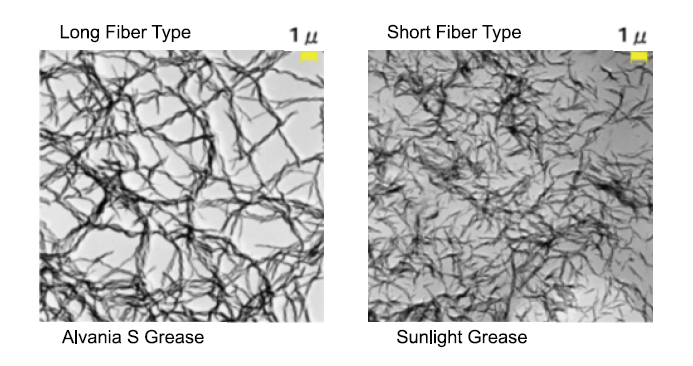
圖5、潤滑油與滑脂型態示意圖[7]
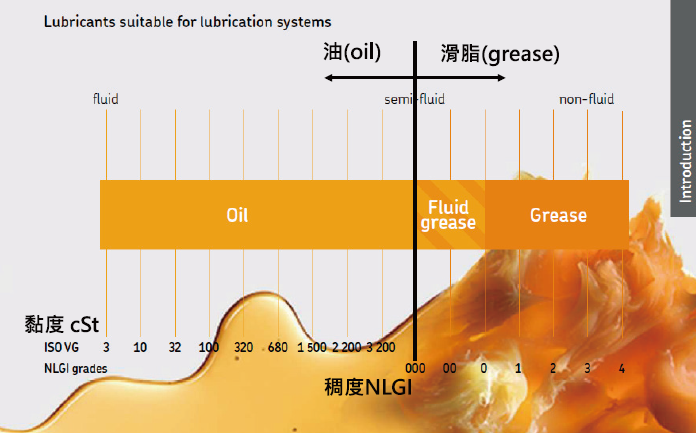
NLGI級別 | 應用類別 | 滑脂型態 |
---|---|---|
6 | 滑動軸承 | 固體(block) |
5 | 滑動軸承 | 非常剛硬(stiff) |
4 | 高速低負荷 | 剛硬(stiff) |
3 | 高速軸承 | 中等(medium) |
2 | 滾珠/滾子軸承 | 中等偏軟(medium soft) |
1 | 中央潤滑系統/低溫 | 軟(soft) |
0 | 中央潤滑系統 | 非常軟(very-soft) |
00 | 封閉齒輪 | 半液態(semi-fluid) |
000 | 封閉齒輪 | 液態(fluid) |
應用性質 | 增稠劑種類 |
---|---|
附著力、抗沖洗 | 鈣、鈣複合、鋰鈣 |
一般應用 | 鋰、鋰複合、鋁複合、聚脲 |
高溫 | 聚脲、黏土、微凝膠 |
性能指標 | 說明 |
---|---|
稠度(NLGI) | 增稠劑比例,影響半固態的程度、附著能力、泵送難易度。 |
滴點溫度(dropping point) | 超過時,滑脂會不可逆地變為液態,造成洩漏與潤滑失效。 |
機械穩定性 (mechanical stability) | 指對於剪切及負荷的耐受能力,增稠劑會因受力破碎成短鏈,造成抓油能力下降而劣化(aging)。 |
低溫特性 | 低溫時會顯得更黏更硬,因此其低溫啟動或者中央潤滑系統泵送的應用時,必須額外考量低溫特性。 |
2.1.3 添加劑(additive)
添加劑額外提供一些特殊的性質,大部分添加劑會隨時間被逐漸消耗,因此滑脂的補充也包含添加劑的補充,有時油品檢驗也以添加劑的殘餘量來判斷滑脂的壽命,常見的添加劑與說明整理如 表4。極壓添加劑通常成分含有硫、磷或氯,遇水分會形成酸而腐蝕,軸承的保持器(cage)若為銅製,就不適合使用含極壓添加劑的滑脂[9]。極壓添加劑會影響滑脂整體壽命,因此舊油的排除更顯重要。
添加劑 | 說明 |
---|---|
抗氧化劑(anti-oxidants) | 替代基礎油被氧化而延長壽命 |
抗磨耗劑(anti-wear) | 潤滑不足且成受壓力輕微時,減少介面的直接磨損以延長設備壽命。 |
極壓添加劑(Extreme Pressure, EP) | 受衝擊力與高壓時,摩擦產生高溫,使介面與添加劑產生化學反應,形成提供保護的磨損替代物。 |
2.1.4 軸承運轉速度評估指標:ndm值
軸承速度由轉數(n, rpm)與軸承大小(d, mm)決定,常見的計算方式為轉速與軸承平均直徑的乘積,即 : ndm=n×dmean,其中dm=(doutter+dinner)/2,ndm值粗略定義的高低速對照可參考 表5:
高低速定義 | 徑向滾珠軸承 Radial Ball Bearing | 圓柱滾子軸承Cylindrical Roller Bearing |
---|---|---|
非常慢 | - | <30,000 |
慢 | <100,000 | <75,000 |
中等 | <300,000 | <270,000 |
快 | <500,000 | ≧270,000 |
非常快 | <700,000 | - |
極快 | ≧700,000 | - |
2.1.5 滑脂選用方向-馬達軸承
滑脂選用的參考指標主要為軸承速度與負荷(loading),通常代表著兩種極端的應用:高轉速中低負荷,與低轉速高負荷。以台積廠務的馬達應用為例,大部分為風車、泵浦、壓縮機等,因此屬於高轉速中低負荷的應用面;反之低轉速高負荷的馬達應用如輸送帶滾輪、軋輥、傳動軸等。
其中馬達軸承又比一般軸承的工作溫度更高,除了高轉速使滑脂攪拌(grease churning)產生廢熱外,馬達本身線圈也會發熱。因此選用滑脂時,必須選擇耐高溫的滑脂,且黏度通常選擇100cSt(40度C時)或更低(圖6),避免過度耗能。稠度的部分,一般應用以NLGI 2為主;若為高溫、高速或垂直軸時,則會選擇增稠劑含量高的NLGI 3或以上,來增加滑脂壽命與附著力。溫度影響選用規範的另一個考量則是增稠劑種類,可參閱2.1.2。
圖6、黏度影響與應用對照[11]
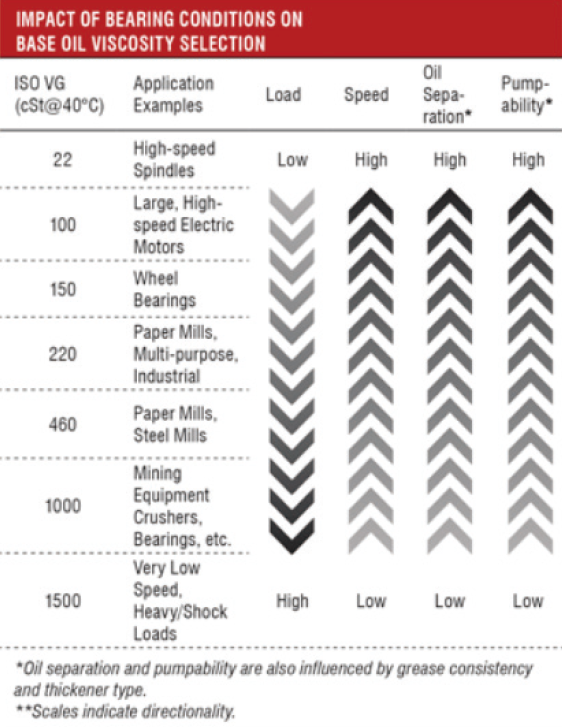
2.1.6 潤滑機制
潤滑油膜的三個型態簡介如 表6,滾動軸承潤滑良好時通常為彈流潤滑的情形,其潤滑特性與一般液力潤滑較為不同。
滑脂的潤滑機制可分為三個階段[13]:初始的攪拌(churning)、供油(bleeding)到最終的油膜崩潰(film breakdown)而產生劇烈的磨耗。攪拌階段為:滑脂被軸承動件推動而流動到動件移動路徑外的過程,攪拌時會產生較高的溫度,也說明為何剛補油時溫度容易拉升。滑脂流動到不易被排擠的地方靜置後,進入基礎油開始從增稠劑結構中流出與回收的供油階段,在介面間形成油膜。最終當基礎油流失後,油膜無法有效隔離介面而開始潤滑失效。
潤滑型態 | 邊界潤滑Boundary Lubrication | 液力潤滑Hydrodynamic Lubrication | 彈流潤滑Elastohydrodynamic Lubrication |
---|---|---|---|
示意圖 | ![]() |
![]() |
![]() |
油膜厚度 | 不足時 | 10~100um | 1um |
發生時機 | 潤滑不足、起停機、切削應用 | 介面曲率相似,如軸頸軸承、滑動軸承 | 介面曲率相反,如滾動軸承、齒輪 |
說明 | 油膜不足時介面間產生大量摩擦、廢熱與顆粒,而加速磨損。 | 介面曲率相似,因此油膜壓力不大(100psi), 黏滯性的變化小。 | 因曲率相反,受力區承受壓力大(100kpsi),黏滯性因此提升, 使介面間能完全分離。但高壓會使表面產生彈性變形,也是疲勞的原因之一。因油膜厚度薄,潔淨度需求高。 |
2.2 馬達軸承潤滑設計
2.2.1 潤滑保養方式
馬達軸承室設計會直接決定後續保養的方式,可分為以下三種方式如 表7:「免保養」、「僅可補油」及「可補油與洩油」。其中免保養軸承分為:密封軸承,軸承外環與內環藉由密封材質完全彌封阻隔外界;端蓋軸承則是外環與端蓋連接,內環與端蓋間保持極小的間隙以減少摩擦阻力(如 圖8右)。
潤滑方式 | 說明 | Sys | Equipment | hp | Avg.op. rpm |
---|---|---|---|---|---|
免保養 | 小型馬達常用,利用密封或端蓋軸承(圖7)將滑脂留在軸承內,滑脂壽命等於軸承壽命。 | CR | AW Pump | 10 | 3560 |
AAS | Recir. Pump | 10 | 3510 | ||
僅可補油 | 馬達端蓋配置較大的儲油槽,儲滿時無法有效補油,必須更換軸承同時清理。 | MEP | CT Fan | 245 | 893 |
CR | MAU Fan | 176 | 540 | ||
可補油與洩油 | 配置洩油孔,保養時應開啟排除舊油,然而舊油流動性和軸承流道設計有關,狹小流道不易排出(圖8)。 | CV | CV Pump | 20 | 3525 |
MEP | 12CHP | 373 | 1250 | ||
AAS | VEX #2 Fan | 75 | 1328 |
圖7、左:密封、端蓋與開放軸承[9];右:密封與端蓋軸承剖面示意圖[10]
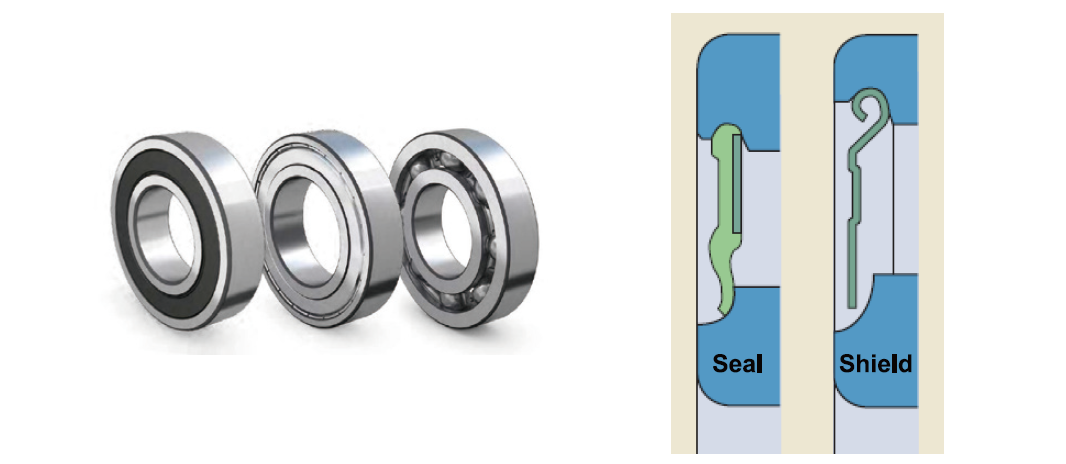
圖8、左:洩油設計不佳,油道過小轉折處易塞;右:油道設計較優
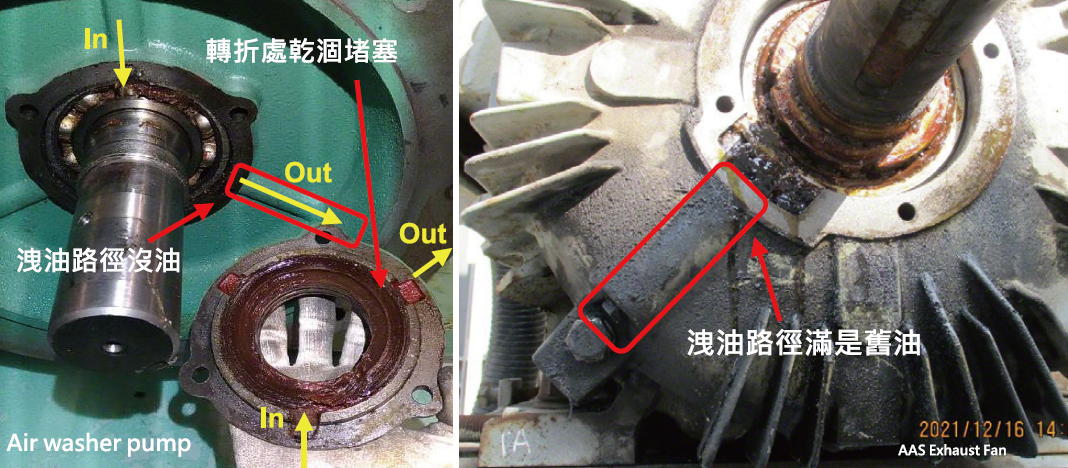
2.2.2 自動洩油設計:洩油盤、迷宮軸封與洩壓閥
較頻繁補油的馬達有時會配備自動洩油盤,其構造為利用碟盤固定於軸上並與端蓋形成微小間隙,多餘的滑脂會透過間隙往外排出,類似原理的設計還有迷宮軸封(圖9左、中)。對於僅有洩油螺絲的設備,亦可改使用洩壓閥螺絲(圖9右),其原理如同逆止閥,平時能隔離油道與外界接觸,當補油保養時,軸承室內滑脂填滿建立起壓力會使閥開啟而洩油。以F14P5為例,冰機的冰水泵就有配置洩油盤及盛油盤,多餘的滑脂會自動排出,能夠維持內部滑脂的狀態如新。
圖9、左:洩油盤[9];中:迷宮軸封[9];右:洩壓閥螺絲[14]
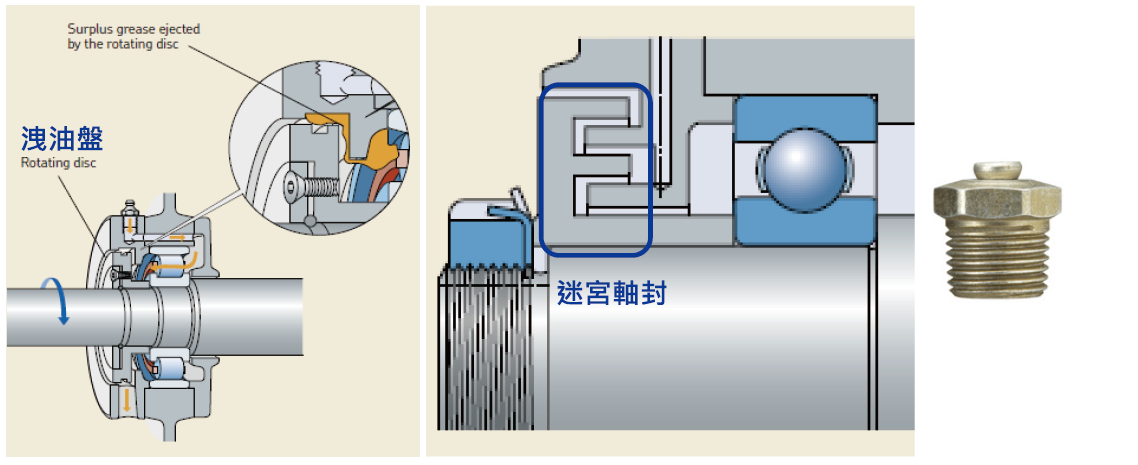
2.3 馬達軸承潤滑失效原因與影響
2.3.1 潤滑不足的原因:過熱與過度注油
一般人對潤滑的觀念是:可以多不能少,油多可以增加潤滑,有益無害。的確潤滑不足會因為油膜厚度不夠,使介面間開始直接接觸而磨損,這是潤滑失效的最根本原因。但事實上,過度注油(over-greasing)最終也會導致潤滑失效[15],只是過程較為緩慢且不易發現,整理如 圖10並說明如下:
如2.1.6潤滑機制中所介紹,攪拌階段會產生廢熱,而滑脂本身熱傳能力不佳,導致局部溫升。基礎油的黏滯性會隨溫度上升而下降,使其比設計需求黏度更低,造成油膜厚度不足,無法維持在理想的彈流潤滑狀態而逐漸潤滑失效。基礎油消耗與洩漏後,增稠劑仍持續留在軸承室內無法排除,受到溫度影響增稠劑本身會持續氧化變質,形成黑色高黏稠性狀態,最終固化卡死軸承(圖11)。
圖10、過量注油造成馬達故障示意圖
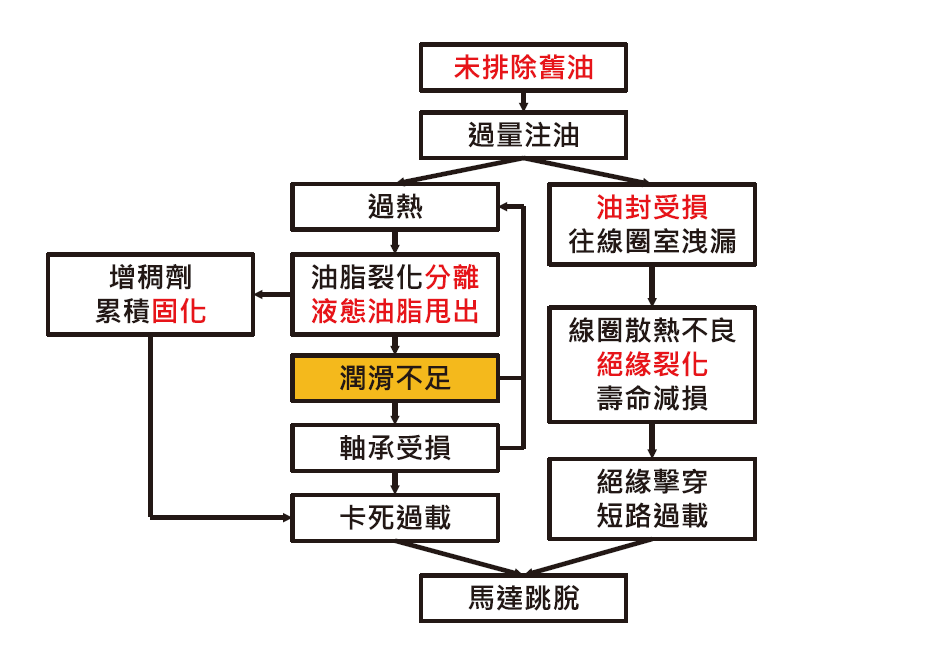
圖11、滑脂劣化變質:增稠劑變稠與固化示意圖
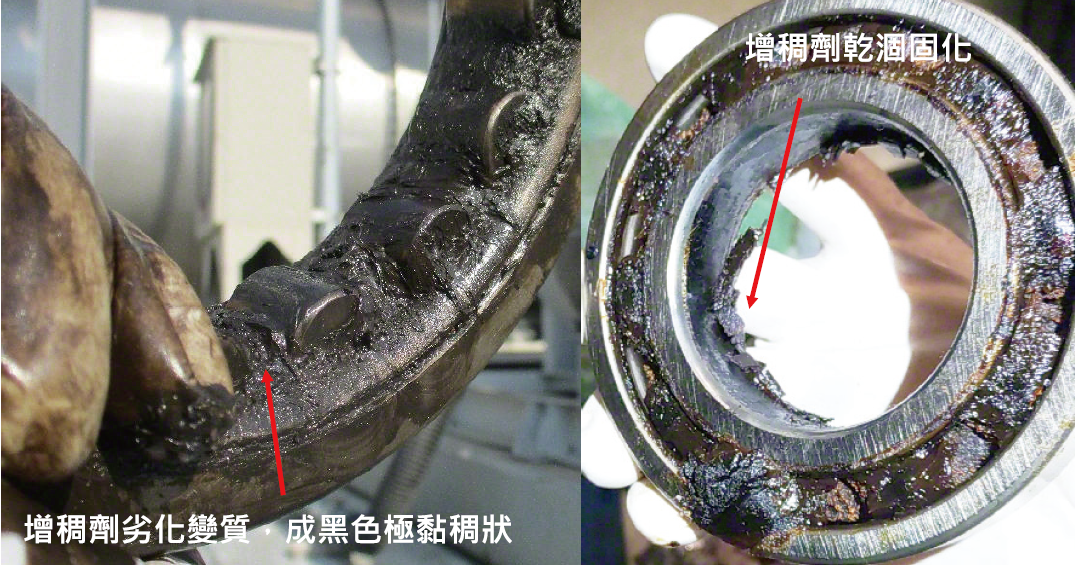
2.3.2 基礎油流失(oil separation)
基礎油除了自然蒸發損耗外,增稠劑因高溫劣化以及長時間使用後其長鏈分子被輾壓成短鏈而喪失儲油能力,造成大量漏油[6],使內部無法獲得足夠的油量而潤滑不足。常見狀況如 圖12,在馬達軸承附近會發現一攤油,也會造成環境髒污問題。
圖12、基礎油漏油
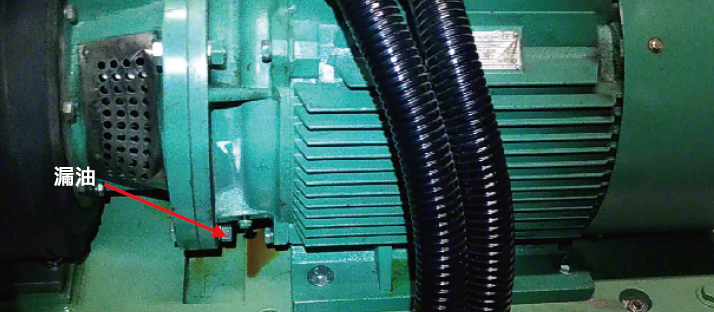
2.3.3 軸封損壞與線圈劣化
過量注油對軸承與軸封也會造成傷害。有些馬達因潤滑設計要求,會採用單邊端蓋軸承甚至雙蓋軸承,因此滿油時,油槍提供的壓力可高達15,000psi,足以對軸承端蓋以及軸封造成破壞。軸承端蓋變形後,會與內部高速轉動的滾子撞擊而迅速損壞軸承[15]。軸封因壓力而破損後,喪失其密封的能力,滑脂或基礎油容易因此洩漏。軸承蓋分為外蓋與內蓋,而軸封位於軸承蓋上,若破損為外蓋則往外漏,造成環境髒污問題也可能使皮帶打滑;內蓋則位於馬達線圈室內,此內側軸封是重要的密封件(圖13),若滑脂向內滲漏時會沾附於線圈上(圖14),除了使線圈散熱不良而減少絕緣層壽命外,滑脂吸附濕氣以及腐蝕絕緣層均增加絕緣擊穿短路的風險。
圖13、軸承內蓋軸封示意圖
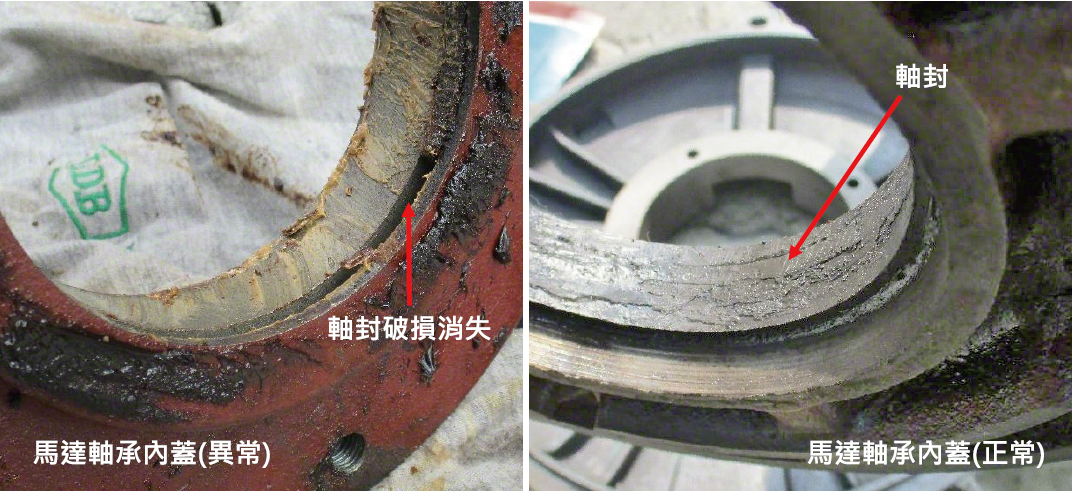
圖14、左:Air Washer Pump馬達線圈沾附滑脂;右:AAS馬達具內擋板設計
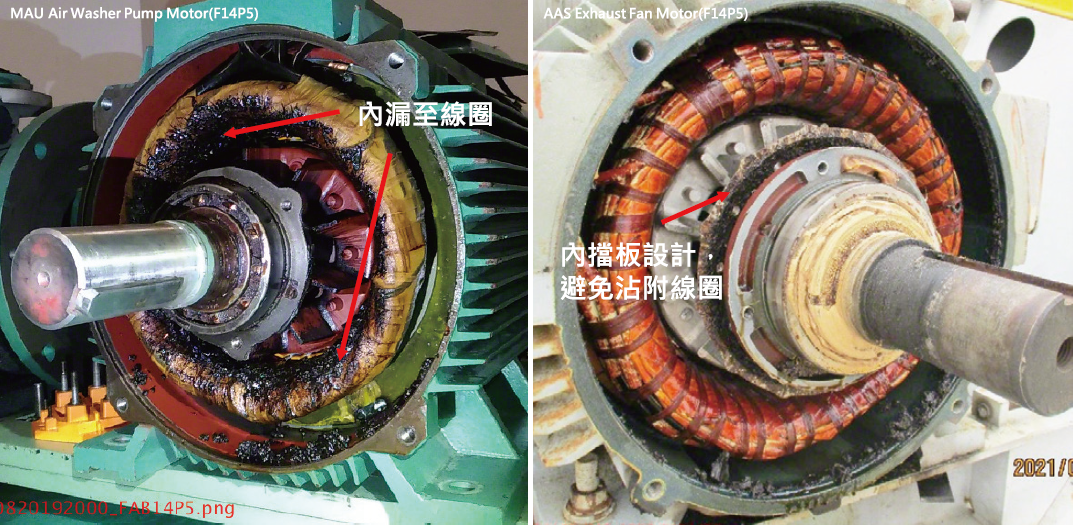
2.4 預知保養-超音波檢測
2.4.1 潤滑應用原理
NASA於1974年設計實驗證明:超音波訊號為軸承潤滑失效過程的最早期訊號[4],此階段磨損極輕微,因此非其他量測指標所能測得,如震動、噪音、溫度、應變等。透過超音波檢測儀器,可將測得的超音波訊號濾波並降頻轉為人耳可聽的頻域,讓使用者可「聽」到軸承發出的超音波強度與音色,藉此初步判斷軸承狀況,也可以連結到振動量測儀或頻譜分析軟體進行分析。
以滾動軸承為例,當油膜厚度不足時,介面表面粗糙的凸點會彼此碰撞而產生超音波(圖15),此訊號強度與頻率即可做為檢測指標,其音頻強度在28kHz較明顯,可作為第一個判斷指標;第二個指標則是不同頻譜間的訊號,根據軸承轉數之倍頻可區分不同軸承零件造成的損壞(類似振動之頻譜分析)。
圖15、摩擦時表面粗糙之凸點碰撞產生超音波[20]
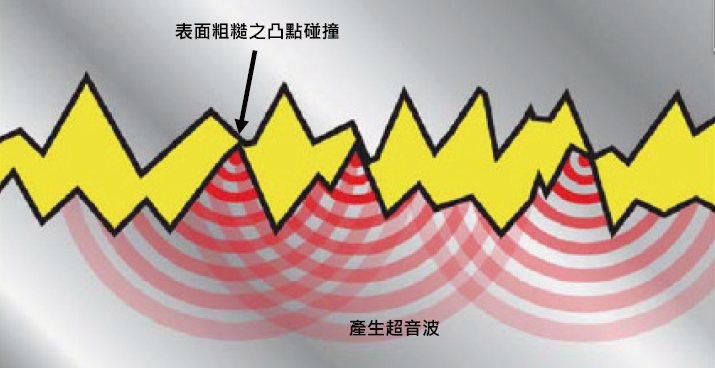
2.4.2 潤滑手法精進-依潤滑狀態保養
傳統上潤滑以預防保養的模式進行,即定期定量補油。然而每個軸承的運轉狀況與滑脂的劣化情形不盡相同,因此所需補充油量亦不同。因此,若能以軸承實際潤滑狀態作為供油量的判斷依據,將能達成最佳的保養效果,節省滑脂用量外,也能減少運轉能耗。傳統常用的振動量測,無法檢測出潤滑不足的情形;當振動能檢出異常時,軸承已進入相當程度損壞的失效過程。
超音波檢測可做為潤滑狀態之量化指標,音頻的強度以及音色能夠判斷潤滑是否正常。透過建立強度(dB值)之基線趨勢(baseline trend chart)可進行追蹤與比較,若比長期基準值高8dB內時,即為潤滑不足的情形,需補充滑脂如 圖16。
圖16、軸承補油時超音波強度變化[20]
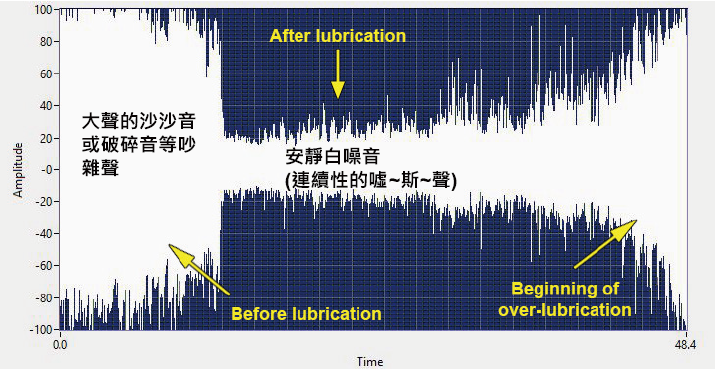
2.4.3 故障檢測
傳統上判斷軸承是否故障,主要仰賴現場巡檢時人耳聽到的異音以及振動量測。轉動設備現場噪音甚鉅,往往不易判斷異音。超音波量測具備針對性,超音波能量極低且耗損快,需將超音波探頭接觸於馬達端蓋上才能測得,不會被環境或鄰近設備所影響而造成誤判。
超音波強度在超過長期基準值的8dB內,視為輕微潤滑不足,此時尚未產生具影響性的損壞;若音頻強度高於基準16dB且音色改變,則可能是初期的磨損產生;當強度值超過35dB時,軸承損壞程度已較為嚴重,需立即安排更換[22]。如 圖17上正常軸承為安靜如白噪音般的摩擦聲,超音波時域圖為均勻且強度低;當磨損產生時如 圖17下,其聲響如破碎聲,時域圖上可看出明顯的峰值變化。如同振動頻譜分析,其峰值發生的頻率與諧波搭配運轉轉數可判斷出軸承損壞的部位。有了這些音頻強度上的差異,再加上音色變化,可作為現場初步判斷軸承故障程度的依據,進一步的做頻譜分析或振動量測可得到更詳細的結果。
軸承超音波與振動檢測的比較如 表8,振動除了軸承以外,還能偵測如安裝、對心等其他問題,因此超音波無法取代振動量測,但可作為潤滑保養的工具與故障診斷的初步篩選以節省時間。超音波檢測在低速運轉的設備上,則有相對明顯的檢測能力(圖18)。
圖17、正常與磨損軸承之超音波強度圖[23]
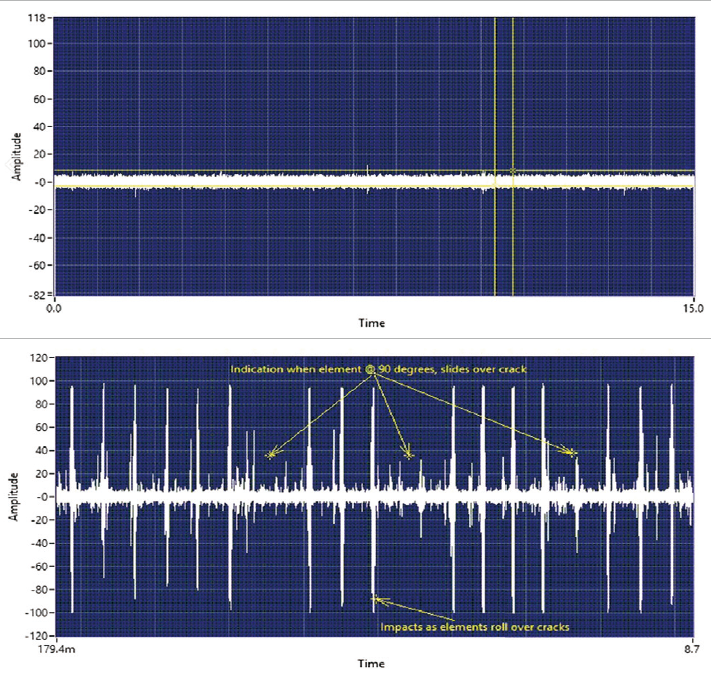
超音波 | 振動 | |
---|---|---|
預知性 | 極早 | 早 |
量測時間 | 快速、立即 | 較長 |
分析門檻 | 較低 | 較高 |
檢測設備 | 軸承、潤滑 | 軸承、馬達安裝、其他狀況 |
圖18、低速軸承之振動與超音波檢測比較[24]
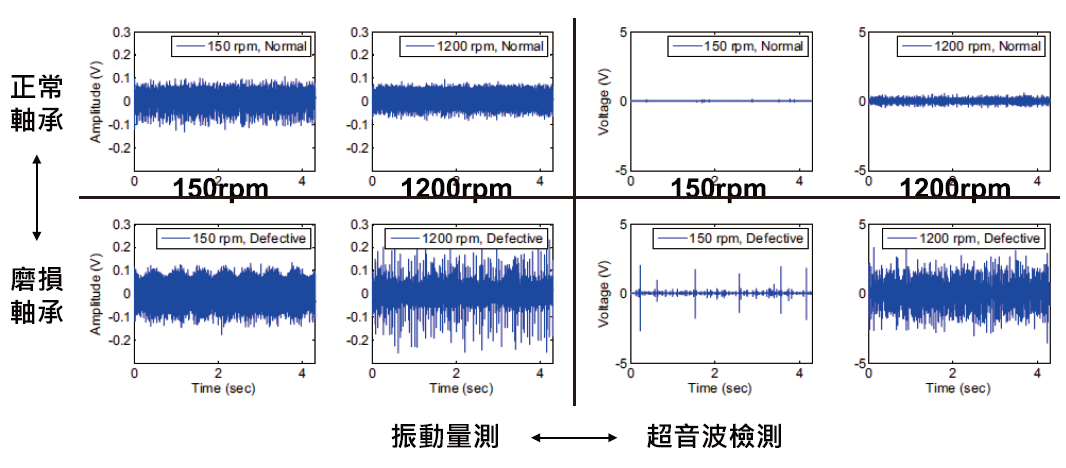
2.4.4 超音波於自動注油的應用
自動注油器可設定週期與補油量,直接安裝在注油口,依據設定值進行自動補油。實務上有其使用的限制與缺點:軸承室若有堵塞而產生背壓時則可能無法確實注入。因此雖然可大幅減少手動補油的工作,卻增加了需要人工檢查自動注油器是否正常運作的問題。
自動注油器若輔以超音波檢測,就能將潤滑作業從定期保養提升到依狀態保養的程度,藉由超音波量測來判斷是否須補油,再以自動注油器補油到足夠為止,潤滑狀態也能即時監控。目前已有此類型的解決方案,但仍屬於發展初期,對於龐大的注油點必須建置資料收集與回傳的通訊設施,可挑選重要的設備做安裝測試,以期改善設備的可靠度並加強預知設備狀態的能力,減少緊急搶修的風險。
3. 研究方法
3.1 滑脂適用性與黏度更換
PMOI並未明確規定馬達軸承適用的滑脂規範,因此各廠間除參考馬達供應商規格外,也會參考建廠時使用的滑脂持續沿用。以F14P5為例,延續過去建廠使用的滑脂Shell Gadus S2 V220 2,此款滑脂為鋰皂基增稠劑與礦物油基礎油,黏度220cSt(40˚C)與稠度NLGI 2級,並含有極壓添加劑。此滑脂為泛用型滑脂,原廠建議可用在機構活動軸承以及承受瞬間受力之高負荷應用,如輸送帶滾輪軸承等[16]。
一般而言風車與泵浦用的馬達軸承通常速度較高(ndm值,詳2.1.4)且負荷較輕,因此手冊皆建議採用黏度100cSt(40˚C)甚至更低黏度的規格,以減少廢熱與運轉能耗。盤點機械系統使用的馬達手冊[18][19],建議使用Shell Gadus S2 V100與Mobil UNIREX(皆為100cSt),為方便管理與考量過去使用滑脂之相容性,建議皆更換為Shell Gadus S2 V100[17]。
3.2 保養週期與注油量
不同應用的馬達所需的保養週期與注油量不盡相同,可依據原廠設計手冊為基準值,再根據實際應用做調整。若手冊無標示者,則可尋找類似應用的馬達做參考。如2.1.5所述,廠內應用主要為水泵與風車,偏向中低負載之高轉速應用,因此ndm值為重要參考指標。
補充油量可依據SKF手冊之定義,計算軸承內部容積之滑脂重量:0.005xDxB,其中D=軸承外徑,B=軸承厚度。一般以油槍保養時常用「幾下」為單位,因此可以秤重方式量測出10下的滑脂克數再除10,即可得每下之油量。
3.3 保養手法
以往保養時,不會開啟洩油孔。導致舊油無法順利排出,長期下來新油不斷補入,軸承室與儲油空間仍會滿油,容易造成過熱外,舊油無法排除會使增稠劑在內部累積,長期裂化變質後,會變黏稠最終硬化卡死。
保養手法改善如 圖19,針對有洩油孔的馬達,每次保養補油前,必須先開啟洩油孔,並在補油完成後放置1小時以上,使其有足夠的時間受熱膨脹與攪拌流動而排洩舊油。另外是補油時,皆須緩慢注油不可快速打入,避免造成油封損壞。
圖19、保養手法改善
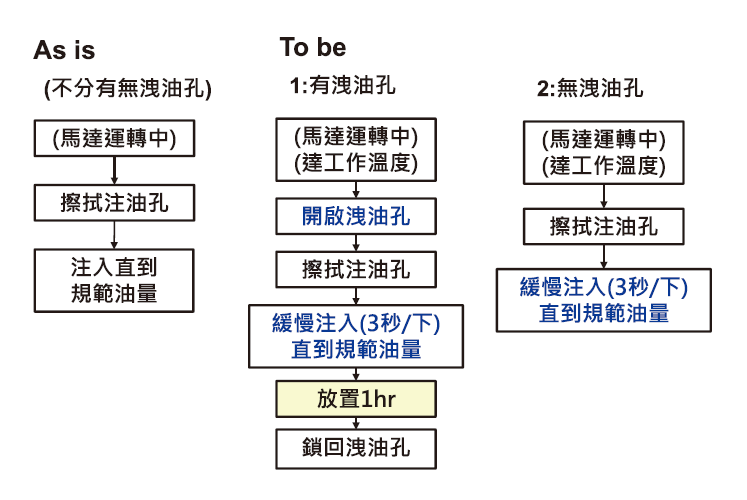
4. 結果分析
4.1 滑脂更換
4.1.1 舊油混油測試
挑選MAW-117A與-115B(air washer pump)作為混油測試,原本內部舊油(Shell Gadus S2 V220)直接以新油(Shell Gadus S2 V100 2)打入。觀察4個月後,沒有特殊異常發生,馬達端蓋(軸承座)量測溫度可降低約3度。
4.1.2 軸承更換新油測試
MAW-501B因機械軸封滲水更換,順便更換馬達前後軸承,並將滑脂直接改用新油。以往air washer pump馬達月保補油後,容易因打油後溫度上升而產生漏油。MAW-501B更換軸承與新油後,觀察3個月發現漏油情形能獲得改善;且電流更換前後,從57Amp降到54Amp,再持續觀察。GER104更換馬達軸承與風車軸承,並改用新油,觀察3個月無特殊異常。
4.2 保養週期與注油量
盤點F14P5廠務機械系統之馬達應用與軸承潤滑保養計畫並整理如 表9,其中軸承速度(ndm值)分佈範圍從80,000到300,000之間,因此各自的保養週期與補充油量也不盡相同。
保養週期如冷卻水塔風扇馬達原廠建議6000小時補油60g,實際保養若調整為月保(720hr)時,補油量應等比例調整為4.8g。若原廠手冊無建議值時,可參考軸承速度相近的馬達,以CV為例可參考MAU air washer pump,軸承速度相似且轉速皆為3600rpm之定頻馬達,因此保養週期應為月保(720hr),補油量則可參考SKF之計算建議量13g。
保養計畫之建議值需參考現場實際狀況以及過去保養經驗做調整。來調整時仍需經過測試與密切觀察,避免一次全部調整。如 表9所列之冰水泵,雖將建議補油量分攤到月保中,但補油量與修正量有所差距(35g與57.6g),調整時先逐步增加每次油量為佳。而CV泵若需從季保調整至月保且增加補油量時,也應挑選特定機台做實驗與觀察。
4.3 保養手法
可洩油的馬達設計中,每次保養時應先將洩油孔打開再進行補油。而實際測試AAS與MAU Air washer pump的馬達後發現,不見得能正常洩油,主要原因為:受限於過往軸承室內累積的舊油,可能已堵塞油道;或者軸封已造成破壞,會從軸封處流出。然而保養手法上,仍應遵循正確的保養方式:將洩油孔打開並靜置1小時以上再關起,往後軸承更換時,必須一併更換軸封,再搭配正確的保養程序才能確保舊油能從設計的流道排出,避免過度注油的問題。
5. 結論
以美國能源局統計資料做保守效益推估:「預知保養可節省12%保養費用,預防無預期停機70~75%,設備初期故障的排除可節能約5~20%,優於高能效IE3/IE4馬達不到5%的節能率。」相當於台積公司推動預知保養後的效益為:「每年可節省轉動設備保養費用NT$48M,每年可節省轉動設備電力損失費用NT$560M,及每年緊急搶修人力500工,並減少系統無備機約77,000小時的空窗風險」[26]。因此做好潤滑保養,並提升至預知保養的模式,不只減少停機風險外,也間接達成節能效益。
No. | Sys | 設備 | hp | 運轉轉速(rpm) | 軸承速度ndm(rpm*mm) | 規範注油週期(hr) | 規範注油量(g) | 實際注油週期(hr) | 實際注油量(g) | 修正注油週期(op hr) | 修正注油量(g) | SKF建議量(g) |
---|---|---|---|---|---|---|---|---|---|---|---|---|
1 | MEP | CT Fan | 245 | 893 | 131,718 | 6000 | 40 | 720 | 5 | - | - | 45 |
2 | CR | AW Pump | 49 | 3540 | 300,900 | - | - | 720 | 9.8 | - | 12 | 12 |
3 | CR | MAU Fan | 176 | 540 | 79,650 | 6000 | 40 | 2160 | 28 | - | 14.4 | 45 |
4 | MEP | CH Pump | 373 | 1250 | 174,930 | 1500 | 120 | 720 | 35 | - | 57.6 | 41 |
5 | CV | CV Pump | 20 | 3525 | 255,563 | - | - | 2160 | 7 | 720 | 14 | 13 |
6 | AAS | GEX Fan | 120 | 1328 | 165,938 | 1200 | 50 | 720 | 21 | - | - | 24 |
7 | AAS | VEX #2 Fan | 75 | 1328 | 165,938 | 2160 | 50 | 720 | 21 | - | 16 | 24 |
8 | AAS | VEX D Fan | 50 | 3550 | 337,250 | 1200 | 30 | 720 | 21 | - | 18 | 20 |
5.1 潤滑簡介與改善
本文簡介潤滑的基礎知識並介紹設備潤滑設計的差異與影響,以利後續分析問題與選用滑脂規範。潤滑問題的根因皆為潤滑不足,鮮為人知的是:過度給油會造成過熱使基礎油流失,最終也會造成潤滑不足。滑脂黏度的選用不當,除造成過熱問題與耗能外,也增加滑脂劣化乾涸而卡死軸承的風險。保養計畫與手法也會造成潤滑問題,若沒有確實排出滑脂,長期累積下仍會造成過度注油的問題。當軸承室佈滿滑脂時,注油會造成巨大的背壓使軸封破損而滲漏,滑脂沾附於線圈上造成散熱不良,增加絕緣劣化與擊穿的風險。針對滑脂規格、保養計畫與手法分別提出改善方式,並持續測試與觀察。
5.2 未來展望-超音波檢測預知保養
做好預防保養的基礎後,可評估跨入預知保養的模式,降低產線停機影響的風險與維護成本。超音波可作為軸承潤滑狀態的先期指標,藉由超音波檢測輔助,可從原本定時定量補油的保養方式,變成依據軸承潤滑需求而供給,避免潤滑過不足或過度注油的問題。超音波檢測再搭配自動注油器的使用與無線通訊的應用,可實時回傳各設施的運轉狀態與自動注油器補油的情形,大幅降低潤滑保養作業的人力成本,提升保養的可靠性與延長設備壽命,達成穩定運轉的目的。
已初步測試超音波檢測於故障判斷的應用:巡檢時發現GEX101風車軸承溫度高於其他台,但聽診器、振動及超音波檢測皆正常,因此判斷非異常磨損,而是滑脂攪拌過熱所致。讓其持續運轉幾天使其適度排油後(進入滑脂潤滑的第二階段-供油),溫度降回基準值。潤滑上的應用仍在持續蒐集資料與測試,期待未來能在季刊上分享成果。
參考文獻
- MOTOR RELIABILITY WORKING GROUP, "Report of Large Motor Reliability Survey of Industrial and Commercial Installations, Part I," IEEE, 1985.
- E.R., Booser, "Grease Life Forecast for Ball Bearings," Lubrication Engineering, 30 (11), pp. 530-540, 1974.
- V.M. Montsinger, "Loading Transformers by Temperature," in Transactions of the American Institute of Electrical Engineers, vol. 49, no. 2, pp. 776-790, April 1930, doi: 10.1109/T-AIEE.1930.5055572.
- J.J. Broderick, R.F. Burchill, H.L. Clark, "A System for Early Warning of Bearing Failure," NASA Tech Brief, August 1972.
- https://sdtultrasound.com/using-ultrasound/
- P.M., Lugt, "A Review on Grease Lubrication in Rolling Bearings," Tribology Transactions, 52(4), pp 470–480, 2009.
- SKF Group, "Fittings and accessories for lubrication systems," Product Catalogue, pp 9, 2021.
- https://shell-lubes.co.jp/lubes-grease/lubes-technology/tech-grease/1138/
- SKF Group, "Rolling Bearings and Seals in Electric Motors and Generators," Handbook, 2013.
- SKF Group, "Bearing Maintenance Handbook," Handbook, 2013.
- https://www.machinerylubrication.com/Read/30210/high-speed-grease
- https://www.machinerylubrication.com/Read/30741/lubrication-regimes
- P.M., Lugt, "Grease Lubrication in Rolling Bearings," John Wiley & Sons: Chichester, UK, 2013.
- https://www.skf.com/alemite/products/fittings/industrial-lubrication-fittings/relief-fittings/threaded-relief-fittings
- https://www.machinerylubrication.com/Read/28664/dangers-of-overgreasing-
- Shell, "Shell Gadus S2 V220 2," Technical Data Sheet.
- Shell, "Shell Gadus S2 V100 2," Technical Data Sheet.
- 大同公司,「電動機維護保養手冊」,2019。
- Siemens, "Low-Voltage Motors Operation Instruction," 2020.
- N. Camilli, "Nuclear Maintenance Applications Center: Effective Grease Practices," Electric Power Research Institute, 2010.
- M. Adrian, "How to use ultrasound to improve lubrication practices," Plant Service Article, 2013.
- International Organization for Standardization, "Condition monitoring and diagnostics of machines — Ultrasound(ISO 29821-1)," 2018.
- H. Christopher, "Slow Speed Bearing Inspection with Ultrasound," Article of maintworld, 2019.
- Y.H. Kim, A.C. Tan, J. Mathew, B.S. Yang, "Condition Monitoring of Low Speed Bearings: A Comparative Study of The Ultrasound Technique Versus Vibration Measurements," Engineering Asset Management. London: Springer; p. 182–91, 2006.
- SKF Group, "SKF Automatic Lubricators," 2021.
- 張智能,「轉動設備預知保養智慧化管理探討」,廠務季刊,37期,2020。
留言(0)