摘要
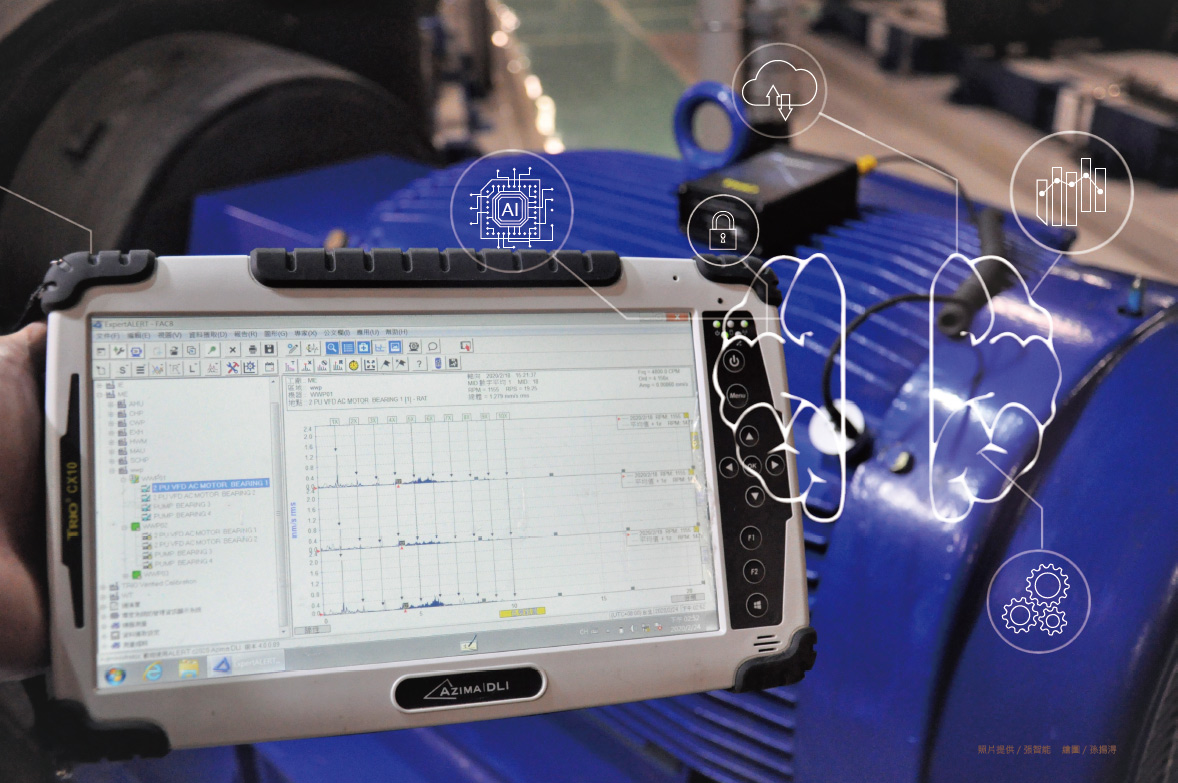
前言
轉動設備在工業製造扮演重要角色,台積廠務人員共負責運轉管理約29萬件廠務設備,其中轉動設備佔9.8%約2.8萬件,每年維護費用約NT$400M→表1,依課別所轄轉動設備的維護費用佔比→表2。
廠區 | F12 | F14 | F15 | F18 | 200mmFabs | 總數 |
---|---|---|---|---|---|---|
資產設備數量(件) | 89,882 | 77,791 | 79,614 | 21,161 | 13,658 | 282,106 |
轉動設備數量(件) | 6,808 | 7,612 | 8,002 | 3,595 | 1,648 | 27,665 |
轉動設備佔比(%) | 7.6% | 9.8% | 10.1% | 17.0% | 12.1% | 9.8% |
課別 | 機械 | 儀電 | 水處理 | 氣化 | Total | |
---|---|---|---|---|---|---|
轉動設備數量(件) | 13,534 | 783 | 12,403 | 945 | 27,665 | |
維護費用佔比 | NT$M | 190 | 120 | 70 | 20 | 400 |
% | 49% | 31% | 17% | 3% | 100% |
轉動設備維護管理目的,是讓人員能夠提前且即時了解設備運轉健康狀況,在故障失效前透過檢測工具找出異常點,適時擬定修復或更換之正解,以維持備載機組的妥善率,更要避免設備機組突然瞬間降載或停機對工廠穩定品質的影響。所以,準確分析與診斷故障失效的目標是要能夠在設備故障前期就發現真正問題原因,提早針對故障真因對症下藥,維持工廠生產品質穩定並延長設備使用壽命之外,根據美國能源局統計[17]指出設備初期故障的排除,預估可節能約5~20%,這樣的操作維護效率優於高能效IE3/IE4馬達不到5%的節能率。
台積公司廠務設備保養管理系統以單元設備來建立基本資料、保養部位組件、保養週期等,透過預防與定期兩種機制維持設備妥善率。預防/預知保養:「保養人員巡視或操作人員操作發現異常而進行故障維修」;定期保養:「依照設備零件磨損、疲勞或自然衰化進行預防性維修」,建立保養維修歷史紀錄,掌握設備健康度,並藉由維修紀錄持續改善保養工作提升運轉可靠度→圖1。
圖1、廠務保養管理系統流程圖[1]
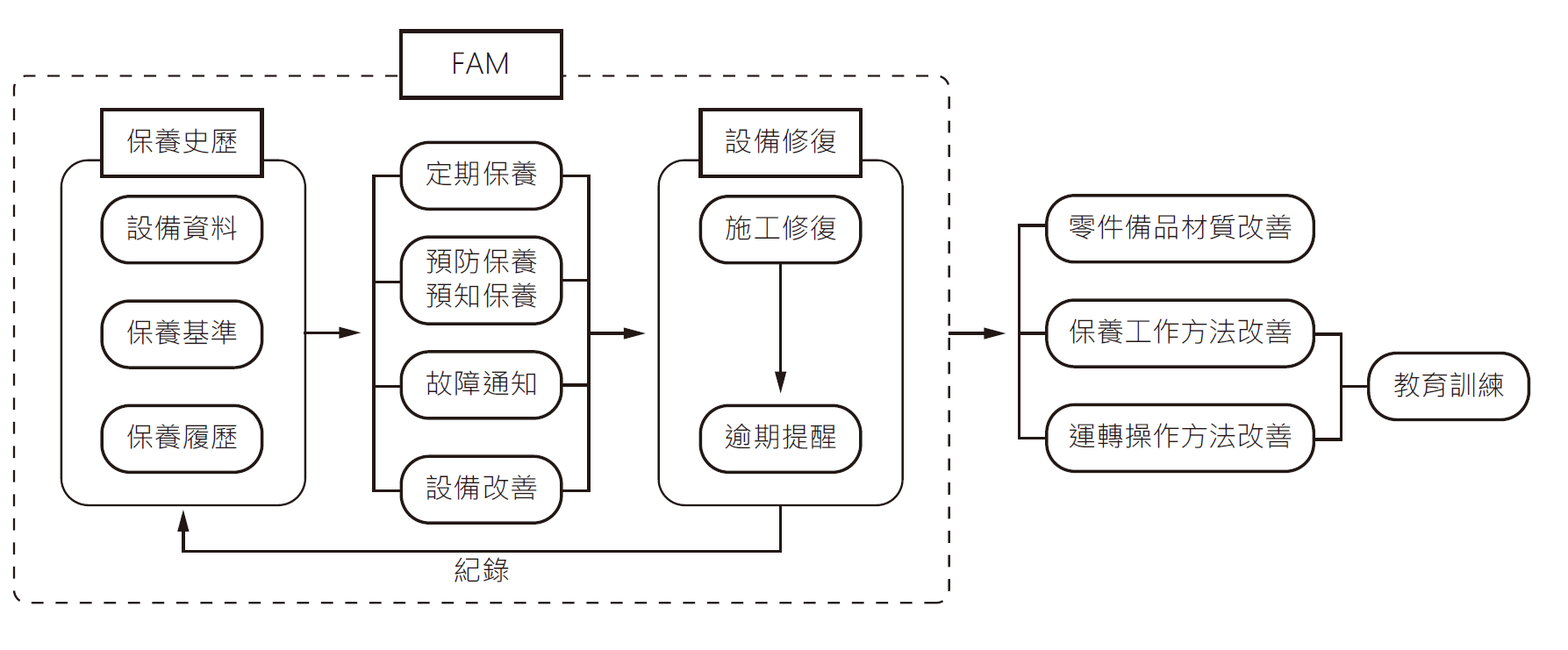
現況預知性檢測手法包含振動、噪音、溫度等作為監測轉動設備健康程度,作為設備妥善率的必要行為之安排。處於工業4.0浪潮前緣的半導體領域,我們開發人工智慧運算系統對接既有FAM平台的完整資料庫,精準判讀設備狀況以預測保養作為與期程,自動化轉動設備預知保養管理的觸發與收斂,並且系統化累積預知保養資料庫是本論文探討的主軸,以下是本文的管理方向與目標 :
- 如何讓轉動設備保持健康指標
- 如何更快更早知道設備問題
- 如何讓檢測數據更有效運用以避免延誤或誤判
- 如何讓廠務系統工程師確認預知保養的真因與品質
- 佈建AIoT人工智慧物聯網,落地轉動設備預知保養自動化
文獻探討
AI Deep Learning工業應用
NVIDA及IBM於2019年Semicon Taiwan提出設備智慧化管理方針[2],如泵浦的故障檢測及使用壽命預測,藉由提出客戶解決方案用以推展公司硬體及軟體平台相關產品,以砥礪精進自家軟硬體產品能力。見賢思齊我們也要持續精進技術層次並突破廠商技術限制,落地我們廠務專業知識的發展與深化,我們戮力協助轉動設備相關保養管理及FAM平台精實茁壯,建立屬於台積公司轉動設備最佳化管理系統搭配FAM及OneFAC管理平台是勢在必行。
AI於轉動設備維護應用
德國舍弗勒(Schaeffler)集團為全球領先高精密零件製造商,主要生產大尺寸軸承於風電渦輪發電機。更換此類軸承時會造成停機和能源耗損,不僅過程複雜且代價高昂。因此該公司與IBM達成戰略合作應用AI達成最佳化風電業的維護,並保障工人安全。該方式透過開放的資料收集平台,以主動及被動收集的資料,透過機器學習即時揭露設備性能問題,例如利用風力預報提醒渦輪機操作員能提前制訂計劃,在風力較小時更換零件。將每日運轉收集的資料增加附加價值,連接終端和流程中的資料,以人工智慧分析將原始資料轉化為有價值的洞察見解用於提升管理效率[3] 。
研究方法
轉動設備故障與維護模式
機械設備或元件的劣化多會依循特定的曲線,稱為P-F曲線→圖2,若能掌握到該失效模式的初期徵兆就能對症下藥 ,掌握最佳化維護保養時機,納入計畫性的維修排程而避免失效故障所產生的負向連鎖結果包含工安意外。
圖2、P-F設備維護曲線[4]
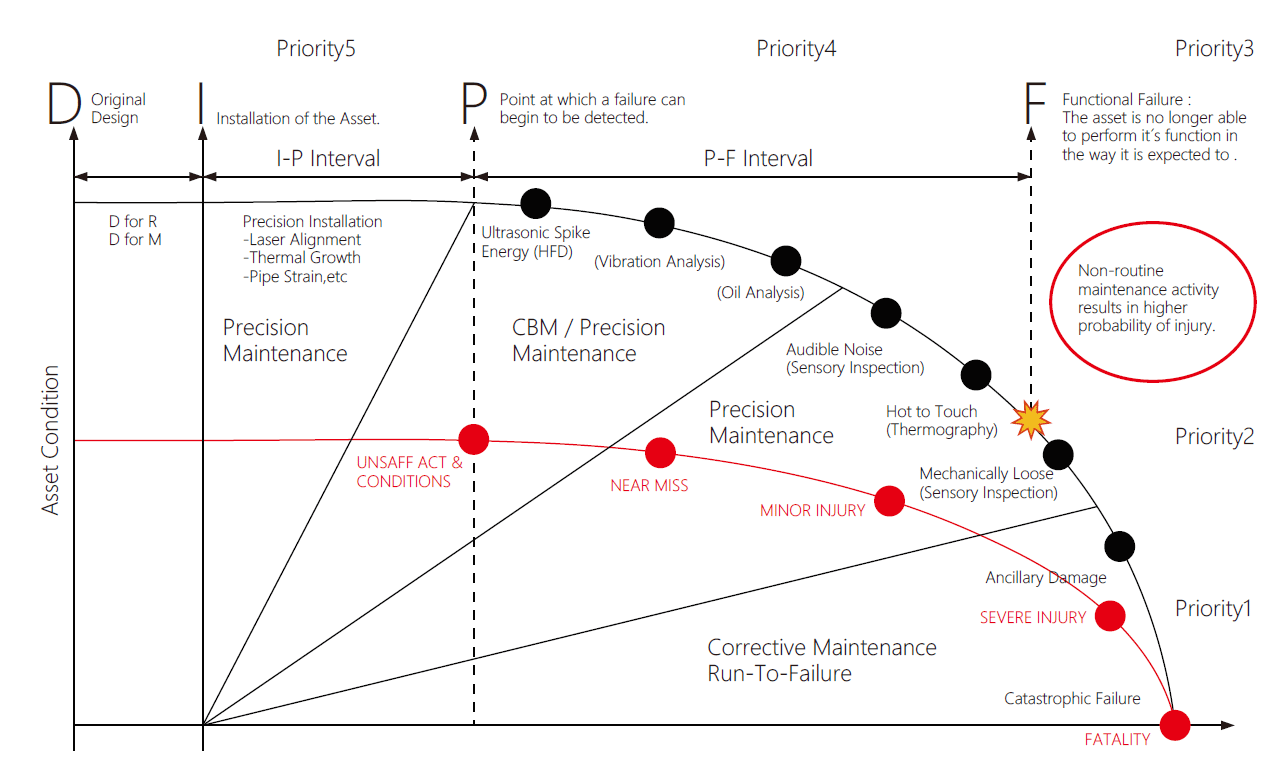
轉動設備之故障原因並非單純來自軸承劣化,是來自多方來源,如:動平衡不良、對心不良、基座鬆動、齒輪異常等[10],精確的振動診斷改善可大幅延長軸承使用壽命。導入智慧化診斷系統,才能真正掌握設備劣化徵兆與最佳維護時機,概述轉動設備保養維護策略→圖3,以下主要針對前三種方向摘要介紹:
圖3、轉動設備維護策略[5]
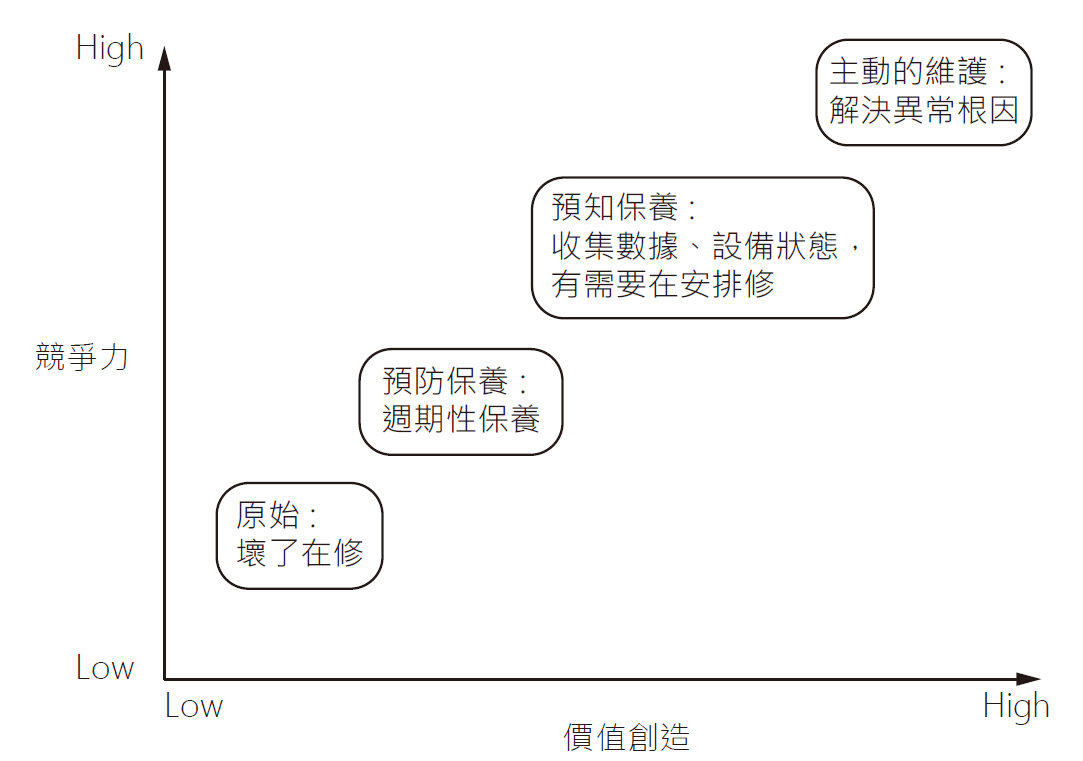
運轉到故障(Run to Failure)
維護保養計畫有瑕疵,故障發生時因備料時間過長或維修人員無法及時調度,導致沒辦法有足夠有效應變時間,可能引起設備停機、二次損壞、工廠停產,如果包含維持生命安全的設備系統就可能進一步引發工安事件。
定期保養(Preventive Maintenance)
屬於被動性保養,以定期定檢方式進行設備維護保養,維修品質較為一致,目前設備主要維護方式主流,但可能發生過度維護,維護頻率越高,人力與成本越高,然因各種設備維護週期不盡相同,如何有效管理以及維護保養品質,避免故障情形發生在維護之後短期內、重複性故障、連鎖效應故障等,為工程師及管理者的一大挑戰。
預知保養(Predictive maintenance)
藉由各種量測方法來汲取各式設備的不同狀態訊息,進而從中檢知早期異常並預測設備失效剩餘時間,降低設備無預警停機,也可能影響改變定期維護保養之需求,同時因為預知性可以提早預警而降低備料需求,以節省定期性維護所需花費的時間及成本,延長設備的使用壽命,提高設備稼動率。各種設備的預知性維護保養的檢知應用可依照→圖4美國太空總署的營運管理建議來定義。
Technologies | Applications | Pumps | Electric Motors | Diesel Generators | Condensers | Heavy Equipment /Cranes | Circuit Breakers | Valves | Heat Exchangers | Electrical Systems | Transformers | Tanks, Piping |
---|---|---|---|---|---|---|---|---|---|---|---|---|
Vibration Monitoring/Analysis | X | X | X | X | ||||||||
Lubricant, Fuel Analysis | X | X | X | X | X | |||||||
Wear Particle Analysis | X | X | X | X | ||||||||
Bearing, Temperature/Analysis | X | X | X | X | ||||||||
Performance Monitoring | X | X | X | X | X | X | ||||||
Ultrasonic Noise Detection | X | X | X | X | X | X | X | |||||
Ultrasonic Flow | X | X | X | X | ||||||||
Infrared Thermography | X | X | X | X | X | X | X | X | X | X | ||
Non-destructive Testing (Thickness) | X | X | X | |||||||||
Visual Inspection | X | X | X | X | X | X | X | X | X | X | X | |
Insulation Resistance | X | X | X | X | X | |||||||
Motor Current Signature Analysis | X | |||||||||||
Motor Circuit Analysis | X | X | X | |||||||||
Polarization Index | X | X | X | |||||||||
Electrical Monitoring | X | X |
預知保養制度的建立
目前廠務轉動設備主要維護方式以定期保養為主,在建立完善的轉動設備管理規則後,可以提升到預知保養。預知保養是一種保養的思維,在預知保養制度建立實施前,需要先整理歸納清楚故障原因與其對應的解法,制定明確的規格與規範,階段式建立制度,循序漸進達成所有轉動設備的預知保養,並且每年PDCA(Plan-Do-Check -Act)以修正精進。
轉動設備不良或失效問題分析整理
轉動設備運轉不良可分為十類:a.平衡不良、b.機械鬆動、c.對心不良、d.軸彎曲、e.轉軸摩擦、f.馬達異常、g.滾動軸承損壞、h.齒輪振動、i.皮帶及皮帶輪振動、j.其他(葉輪異常等),可依頻譜分析量測振動頻譜發生位置,判斷造成不良原因→表3,以及利用頻譜圖判斷問題元件→圖5。
轉動設備不良問題 | 造成不良原因 | 振動頻譜發生位置 | 解決方案 |
---|---|---|---|
a. 平衡不良 | 轉動件形狀不對稱 | 1x轉速 ( 振動方向通常發生於徑向 ) | 可參考SKF軸承的應用。 ( 軸承配置、公差配合、相關零件設計 )[15] 動平衡校正參考ISO 1940。 ( 規範機械轉動件不平衡量的級數 ) |
加工製造時的公差 | |||
組裝不當 | |||
轉動件於運轉時變形 | |||
轉動件破損磨耗 | 軸承潤滑;正確對心;更換轉動件。 | ||
轉動件附著異物 | 軸承潤滑;進行異物清除。( ex. powder ) | ||
b. 機械鬆動 | 外鬆動: 結構、底板、基礎或螺栓鬆動。 | 1x、2x、3x...7x、8x 轉速( 徑向與軸向都有相同特徵 ) | 檢查負荷是否有改變; 檢查軸承座、底板基礎螺絲是否鬆動; 檢查避震器是否異常; 避震器選用按位置決定避震器自然頻率及彈性常數, 每個支撐點靜荷重等分佈安裝。 |
內鬆動: 兩配合元件鬆動。 ( 軸與軸承內圈、軸承蓋與軸承外圈、軸與葉片。) | |||
停機進行軸與軸承及軸與葉片接合處檢查固定是否鬆動。 | |||
c. 對心不良 ( 聯結兩組元件運轉中心線不再同一直線上。 ) | 軸承、軸封、聯軸器、轉軸損壞 | 1x、2x、3x轉速 ( 振動方向同時來自徑向與軸向 ) | 停機檢查。 |
軸承位置有高溫 甚至大量排出潤滑油 | 潤滑油可能變質需重新施打;機構裝配間隙檢查; 檢查軸承是否異常。 | ||
聯軸器間隙過大或破損 | 聯軸器檢查;對心校正。 | ||
聯軸器有高溫現象且 橡塑膠聯軸器會有粉末排出 | |||
馬達運轉電流偏高 | 檢查有無對地短路或相間短路; 負載是否過大或突然改變。 | ||
d. 軸彎曲問題 | 軸中心處的彎曲 | 1x轉速 | 檢查聯軸器是否不同心;轉子平衡檢查; 基座螺栓是否鬆動。 |
靠近聯軸器的彎曲 | 2x轉速 | ||
e. 轉軸摩擦 | 當旋轉件與固定件磨擦時 | 1/2x、1/3x、1/4x轉速 | 是否安裝不當;熱應力使轉軸變形,檢查負載是否改變。 |
f. 馬達異常 | 定子偏心 | 2x轉速伴隨(120Hz) 高振動 | 檢查定子鐵心是否變形或鬆動;檢查三相電壓是否不平衡。 |
f. 馬達異常 | 定子槽產生異常 | 定子槽數 x 轉速 | 定子槽絕緣異常;定子槽線路鬆動故障。 |
轉子偏心 | 2x轉速+低頻區出現極通頻率( FP:0.3~2.0Hz ) | 結構設計誤差;安裝錯位需進行動平衡校正; 轉子結構需清除;轉子上零件是否鬆動。 | |
轉子鬆動 | 轉子棒數。轉速( RBPF ) 伴隨(120Hz)振動 | 轉子磨損造成質量分布不均勻需進行更換。 | |
磁場繞組破損、聯接器鬆動 | 6x轉速 | ||
g.滾動軸承損壞 | 滾珠外徑滑軌磨損 | 0.4xN轉速 | 材料疲勞需進行更換;需進行潤滑; 檢查是否有污染物進入軸承;重新安裝。 |
滾珠內徑滑軌磨損 | 0.6xN轉速 | ||
滾珠磨損 | 2x~4x轉速 | ||
h. 齒輪振動 | 齒輪磨耗 | 齒數x轉速(GMF) 變大伴隨旁波 | 齒輪潤滑;是否有負載變化過大狀況。 |
偏心或兩軸不平行 | 齒數2x轉速變大 | ||
i. 皮帶及皮帶輪振動 | 皮帶發生磨破、鬆動或配合錯誤 | 1x 皮帶頻率 ( 3.14*皮帶輪直徑*轉速/皮帶長度 ) | 皮帶張力檢測;對心校正。 |
皮帶輪不對心 | 1x 轉速 | ||
j. 其他異常 | 葉輪異常 ( 設計不當,擴散片磨損,管路陡彎,擾流阻礙或轉軸偏心 ) | 葉片數x轉速 ( BPF ) | 停機檢查葉輪是否破損。 |
流體擾流 ( 空氣在進出風車,壓力或速度產生突然之變化 ) | 隨機且低頻的振動( 1~30Hz ) | 檢查負載是否異常。 | |
孔蝕 ( 泵浦入口壓力不足產生氣穴, 對泵浦內部機件造成腐蝕 ) | 隨機高頻且寬頻域的振動 | 避免滿載運轉;減少吸入側管路水頭損失; 減少吸水揚程,避免葉輪入口部分真空或壓力降至蒸氣壓。 | |
共振問題:軸承滑動 | 1x轉速伴隨高頻區段(1600~3000Hz)振動 | 檢查軸承是否異常; 檢查椎套間隙是否過大。 |
圖5、轉動設備不良問題對應振動頻譜位置簡圖[5][7]
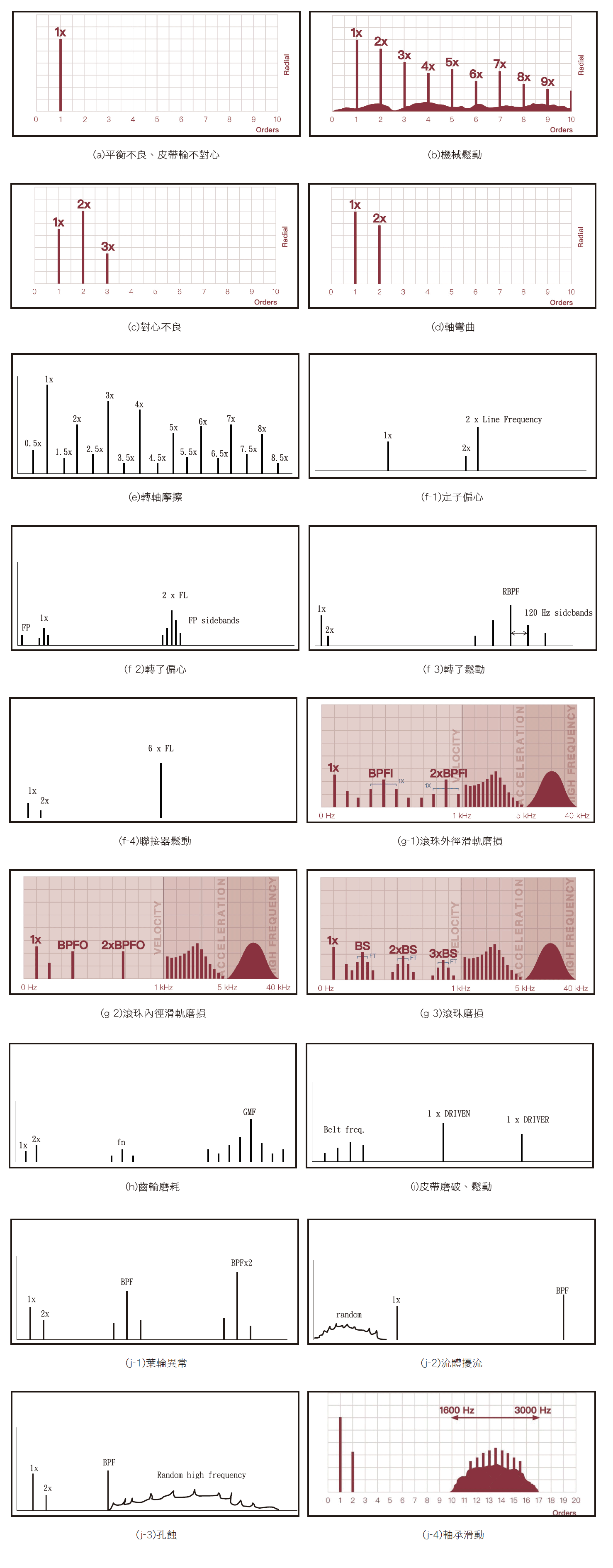
舉例常見馬達故障53%源於機械原因,如軸承故障、轉子偏心、不平衡或鬆動,其中主要原因為過載引起,其次為潤滑不良,再者為潮濕、軸承失效→圖6;若以原件分類,47%則源於電器原因,其中10%為轉子故障、37%源於定子繞組故障→圖7。
圖6、引起機械故障外在因素統計圖[8]
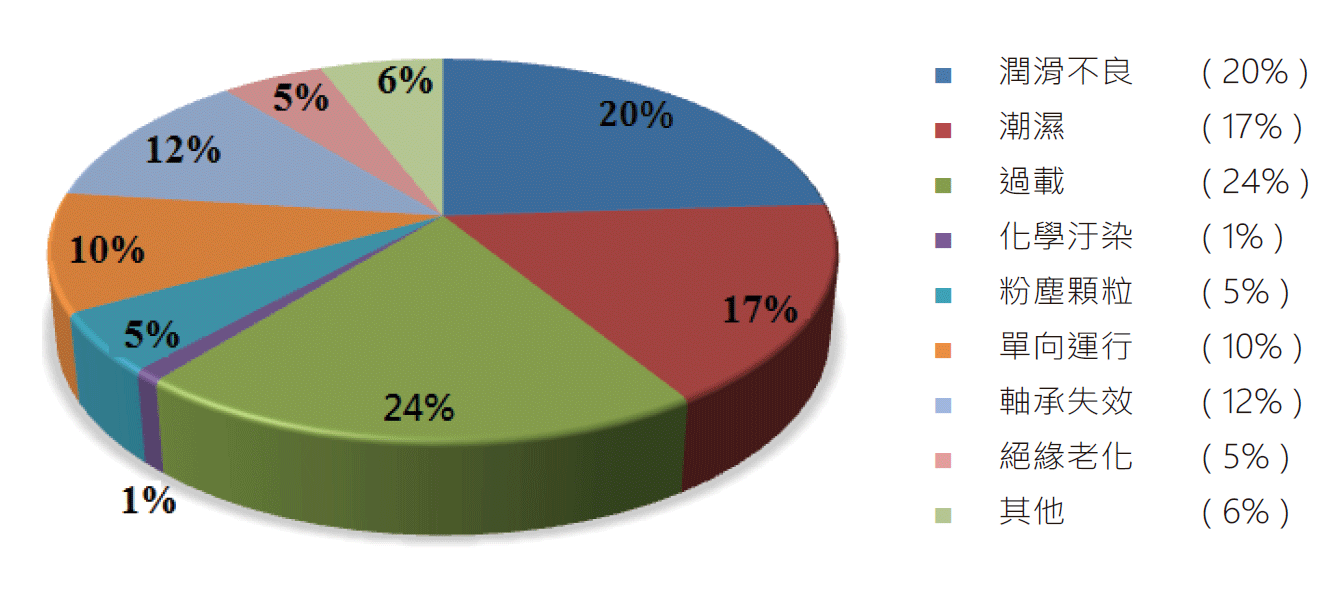
圖7、馬達故障原因統計圖[9]
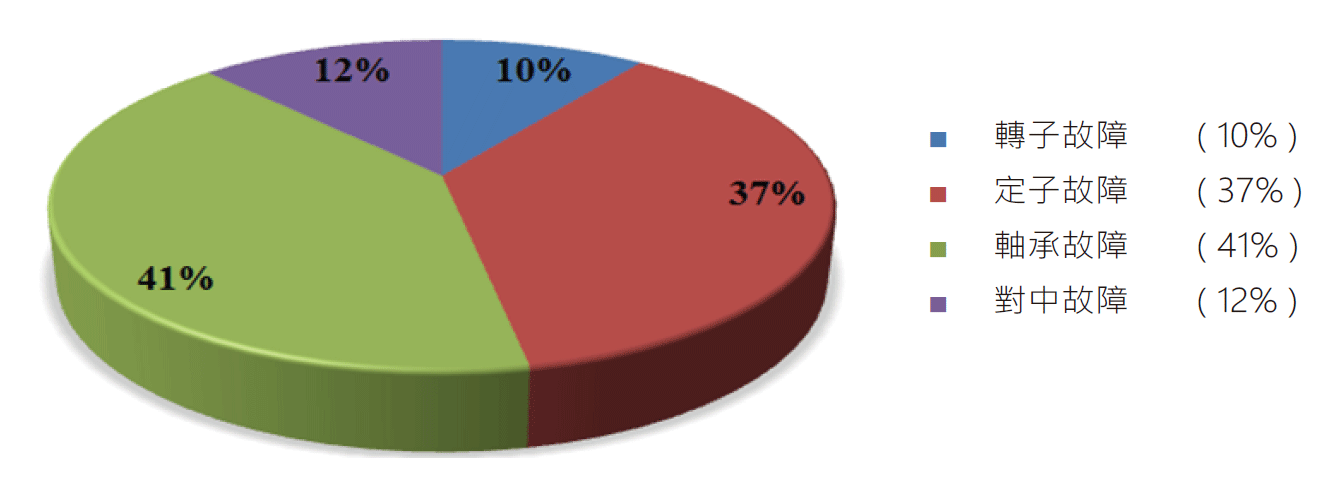
轉動設備健康管理機制基礎
轉動設備依循ISO 10816-3為基礎提出五個管理規則,量測和評定在非轉動組件上的機械振動,針對機械振動擬定的管控機制為額定功率大於15kW且額定轉速120rpm~15,000rpm。
管理機制一:
每個月進行轉動設備振動量測,量測位置共4處→圖8,各處量測三向(水平、垂直及軸向),當振動值大於4.5mm/s且頻譜分析振動峰值大於7.1mm/s或振動值大於7.1mm/s,進行停機維修檢查。
圖8、轉動設備振動量測位置
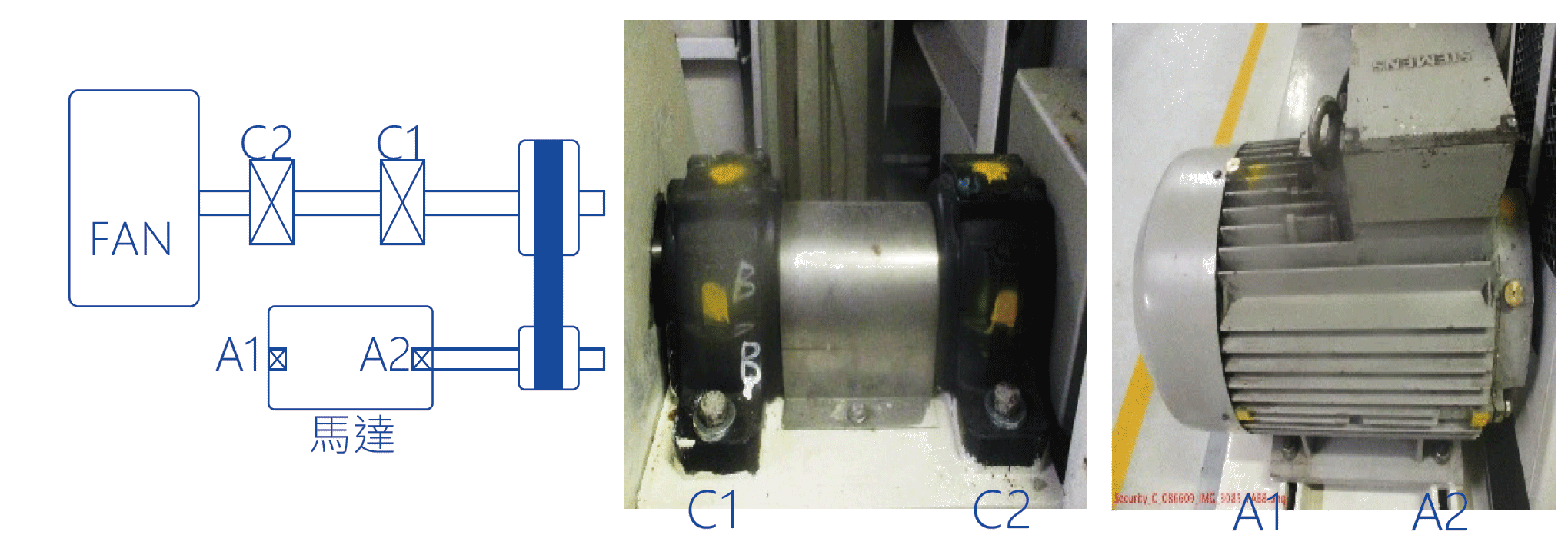
管理機制二:
每半年進行轉動設備頻譜分析,建立設備頻譜資料庫,依頻譜分析結果進行不良問題分析。
管理機制三 :
每三年停機檢查軸心磨損,以厚薄規檢查軸承錐套的間隙,當軸心磨損的公差大於軸承錐套的配合間隙,應速更換軸心與軸承→圖9。
圖9、量測軸心磨損與軸承錐套的間隙
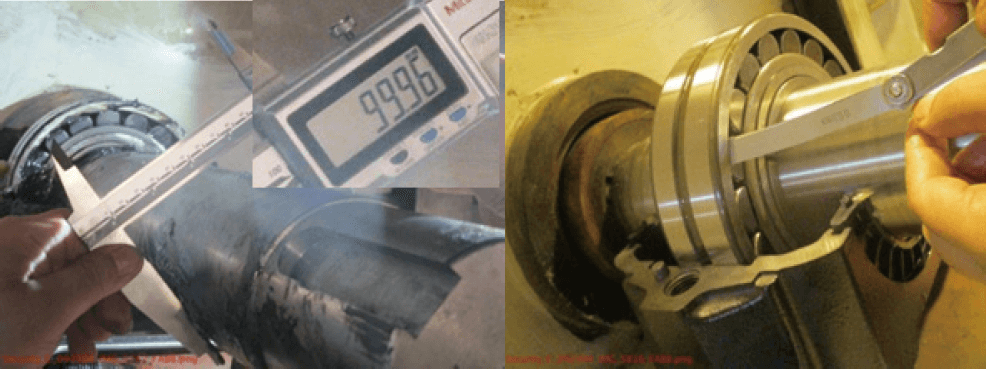
管理機制四 :
每個月進行轉動設備潤滑油補充或依規範更換,潤滑對軸承的摩擦、磨損、溫升、振動有重要影響,軸承損壞40 %都與潤滑不良有關。
管理機制五 :
每個月進行聽診器對運轉中的軸承滾動聲的大小及音質進行檢查。軸承即使有輕微的剝離等損傷,也會發出異常音和不規則音,用測聲器能夠分辨。
如何套用五個管理規則於實際現場運轉管理,本文以空污防制處理設備為實例並提供完整管理流程圖→圖10,以利後續更深入的預防性維修保養探討。
圖10、空污防治系統轉動設備管理流程圖
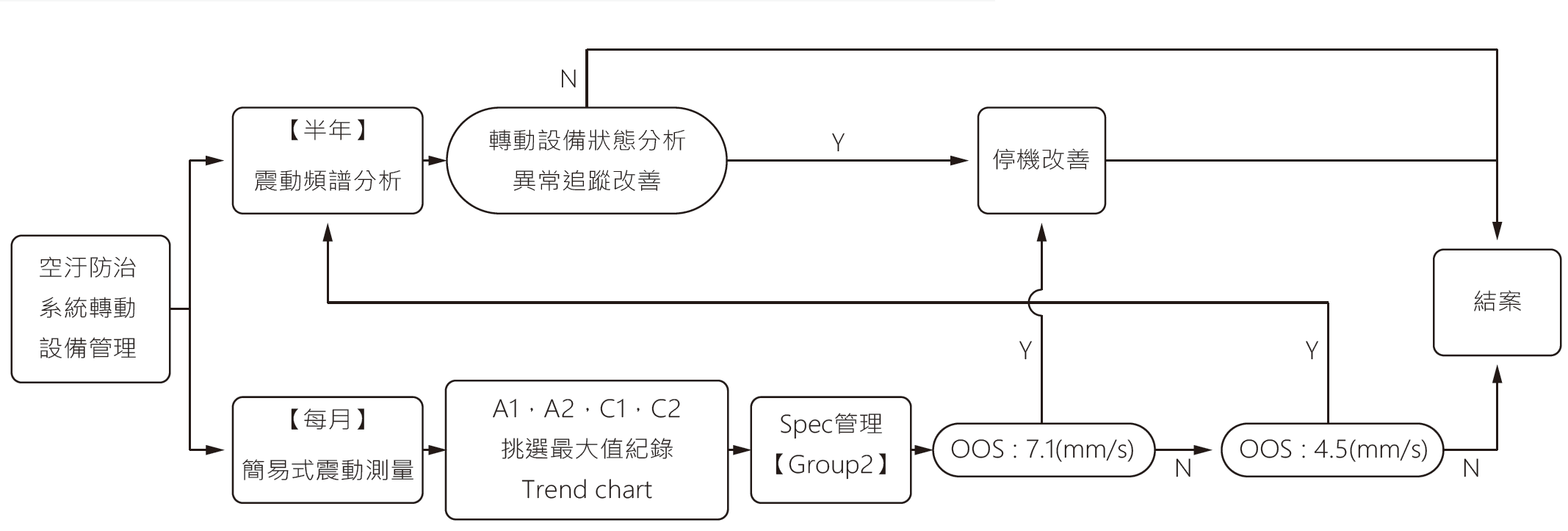
轉動設備狀態監測,主要是建構加速度及速度兩種指標,制定允收規格,作為後續建立人工智慧機器學習模組所需的量化指標。加速度 : 設備健康度檢視,利用加速規量測重力加速度作為分析對象,收集N筆資料數,Xi為第i筆資料,X為所有資料筆數平均值,相關定義→表4;速度 : 振動管制,利用振動計可量測速度值,其管制標準→圖11。
指標編號 | 指標名稱 | 指標定義 |
---|---|---|
Index 1 |
標準差 (Standard Deviation) |
![]() |
Index 2 |
均方根值 (Root Mean Square Value) |
![]() |
Index 3 |
峰值 (Peak Value) |
![]() |
Index 4 |
波峰因素 (Crest Factor) |
![]() |
Index 5 |
峰度 (Kurtosis) |
![]() |
Index 6 |
偏斜度 (Skewness) |
![]() |
Index 7 |
直方圖上限數值 (Upper Bound Value of Histogram) |
![]() |
Index 8 |
直方圖下限數值 (Lower Bound Value of Histogram) |
![]() |
圖11、ISO 10816轉動設備振動規範[11]

AI-ML化被動為智慧主動
利用AI-ML(Artificial Intelligent–Machine Learning)化被動為智慧主動,近年來被各公司列入未來發展重點項目 ,我們以發展程序來說明進化過程→圖12,從故障發生才進行了解的一般性分析,逐漸轉往預知保養,甚至主動控制進行故障迴避,其中人工智慧必須平衡人為智慧,人工智慧並非取代人為智慧,而是精準幫助我們避免非預期狀況並降低工作負擔,提高工作效能與效率。
圖12、故障發生分析圖[12]
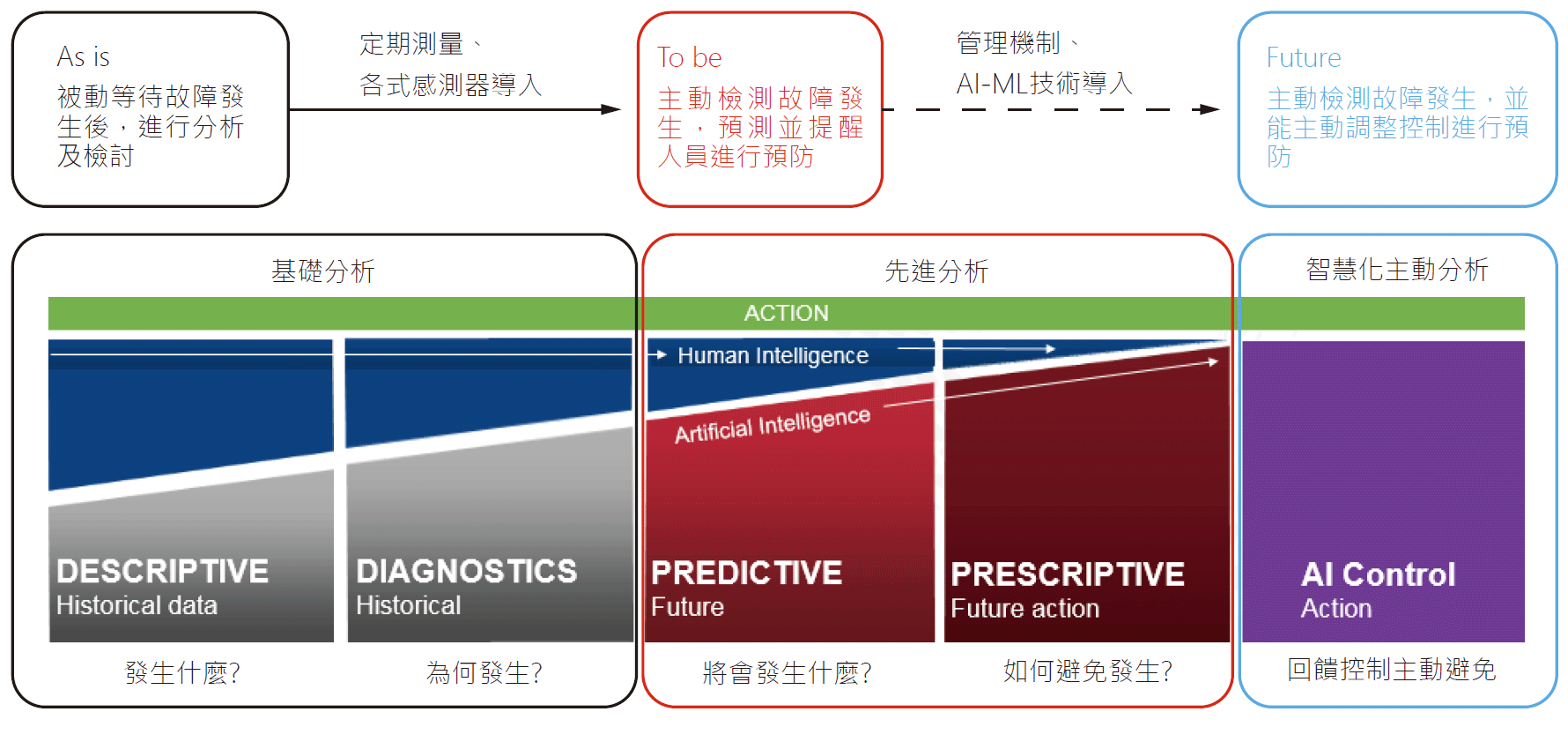
故障預測的神經網路模型
導入AI-ML(Artificial Intelligent–Machine Learning)於轉動設備以達成智慧化管理目標,基於深度學習的卷積神經網路(CNN)來達成轉動元件的軸承故障診斷,依此排定預防保養或備料更換,讓工程師有充足時間進行準備與應變:
我們提出利用卷積神經網路對軸承的時域訊號進行診斷,利用人工智慧模組自動提取軸承訊號特徵,用以改進傳統訊號處理的故障診斷演算法。匯入定期量測所取得振動資訊包含正常運轉及各種故障,利用滾動軸承的特有振動模式判別軸承響應是位於內圈、外圈的時域,以及頻域之振動響應,並將結果數據作為卷積神經網路模型之訓練資料。
為了驗證提出的卷積神經網路模型在類似的故障特徵診斷上有一定的通用性,我們將經過大量數據訓練過後的卷積神經網路,利用轉移學習將訓練過的滾動軸承故障演算法應用在實際故障軸承振動資料分析,藉由較多的訓練樣本以及較深的神經網路架構可使模型擁有較佳的泛化能力,詳細轉動設備故障診斷詳細判別流程→圖13:利用卷積神經網路診斷時域訊號經過人工智慧神經網路的特徵提取級與分類級,將輸入結果轉化為總和為1的概率分佈,其中輸出結果分別對應不同軸承部位的故障類型,搭配目標函數來衡量正確目標以及預測結果的分佈一致性[13],振動所造成的故障分類、判別、診斷流程→圖14。
圖13、卷積神經網路基本單元及架構

圖14、人工智慧神經網路振動故障診斷流程
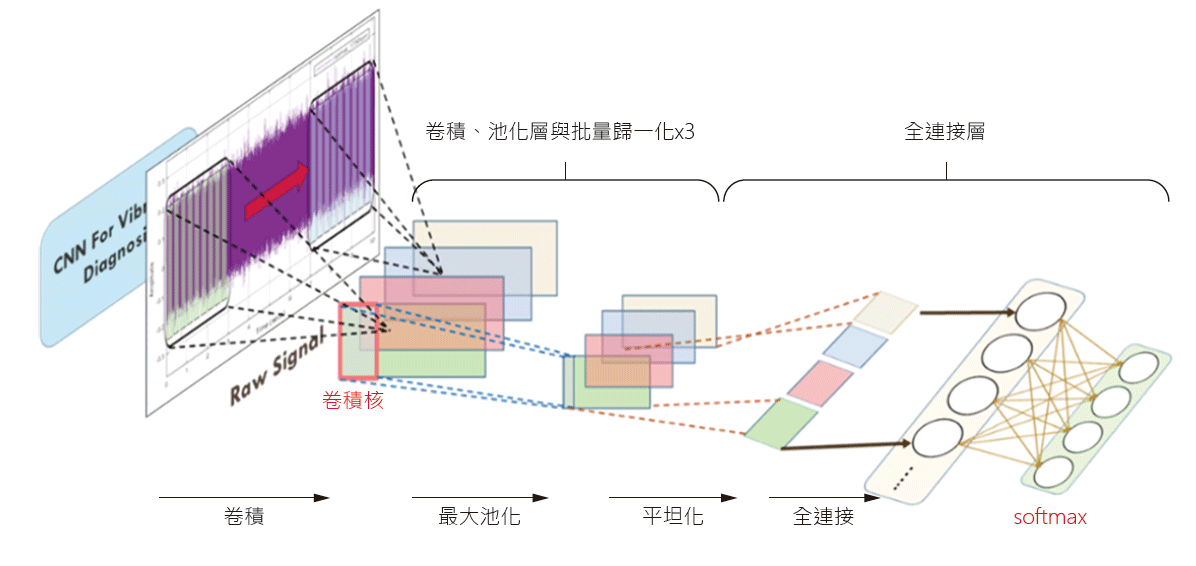
建立訓練資料集與模型準確率驗證
如何將基於控制的自動化轉變為基於機器學習的智慧化:自動化系統曾被認為是工業智慧的核心。然而,單純的自動化仍無法完全滿足工業智慧化的需求。自動化系統能夠解決的是能夠被相對清晰、明確定義的問題,即可見問題;而智慧化系統要暴露的往往是可見問題暴露之前的隱性問題。同時,在現代工業系統變得越來越複雜的情況下,人工智慧演算法能夠與自動化模型相結合,彌補傳統控制的局限性,達到增強系統強健的目的。
設備運轉可靠度隨著時間衰退,其對應的特徵分佈就慢慢偏移,特徵的分佈與正常狀態分佈的重疊部分表徵設備當前狀態對比健康狀態的相似度,即為系統的「健康值」。為了使設備軸承的故障診斷能在實際情況正確應用,除了正常無損傷情形外,還需要分別對每一種損傷位置收集振動資料,此外對於訓練資料集的建立,應該盡可能地包括多種的故障情形、不同的工作及運轉狀態以及包含不同負載狀態下的工作情形。以下針對軸承的三種主要缺陷進行驗證,分別為滾動體損傷(Rolling Element),外圈損傷(Outer Race)與內圈損傷(Inner Race),分別標籤0至3以分別對應為正常、滾動體損傷、外圈與內圈損傷四種轉動狀態所呈現的波型狀態,隨機收集樣本資料進行模型訓練。再比對振動訊號資料進行驗證,驗證結果如→圖15大部份的預測標籤與真實標籤分佈趨於一致,準確率約92%,因此,可以認定該神經模型診斷有一定的準確性。
圖15、混淆矩陣模型真實與預測標籤判斷結果[14]
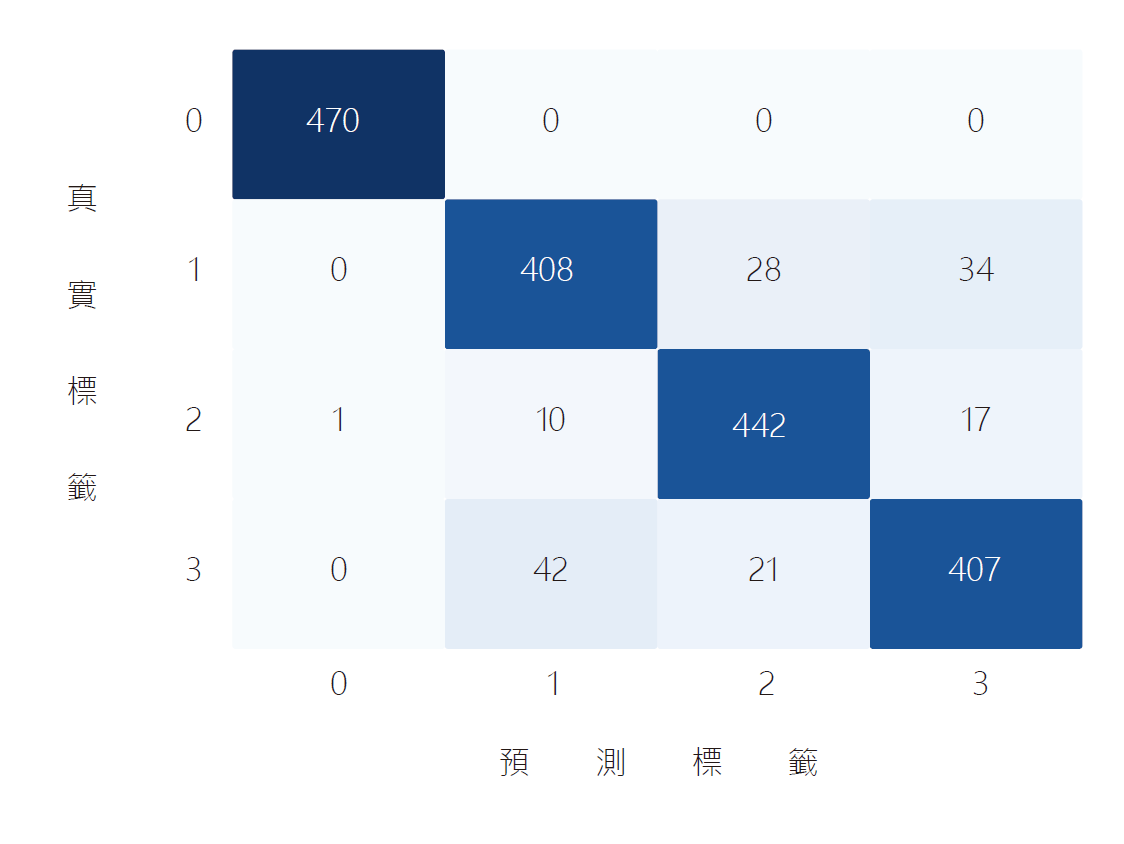
轉動設備智慧化管理
將線上/線下(80% Offline-General / 20% Online-Critical)振動量測資料上傳彙整到FAM雲端大數據,透過人工智慧機器學習的預測模型將轉動設備壽命、故障預測與維修建議,提供給跨廠區工程師與管理者執行停機保養或零件更換的判斷覆核→圖16。
- 轉動設備健康趨勢與維修及故障紀錄建置雲端集中管理。
- 將20%佔比的重要轉動設備配置線上量測,即時分析與故障預測。
- 轉動設備廠務雲端大數據提供神經模型機器學習,避免或降低跨廠相同設備的重複學習。
- 「專屬設備故障預測模型」,降低依經驗導致錯誤判斷可能性,取代委外頻譜量測與人為判斷。
圖16、廠務轉動設備智慧化管理預測
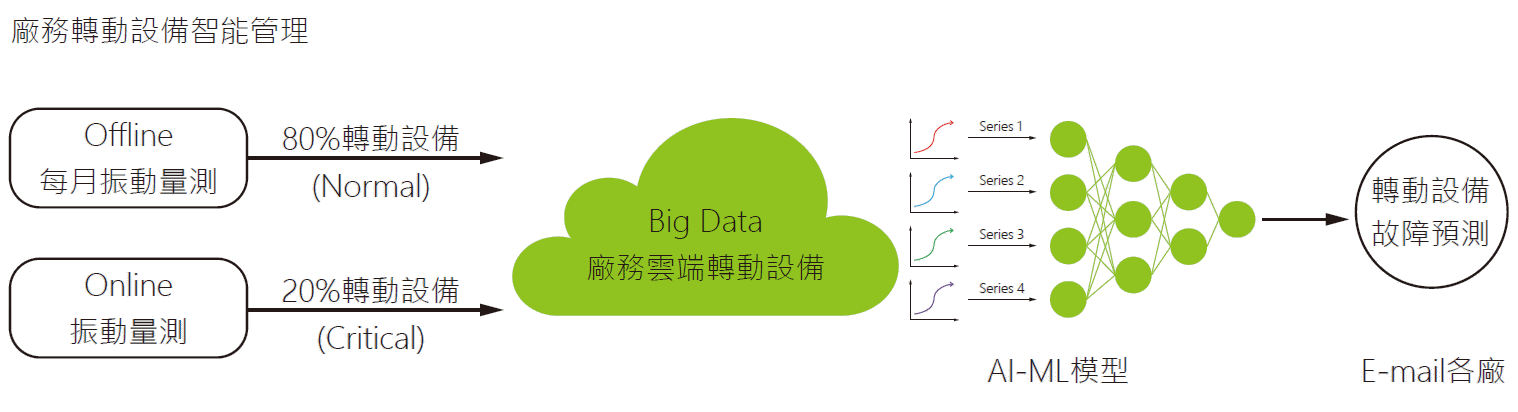
「轉動設備預知保養智慧化」的建構類似整合廠務各項轉動設備端的邊緣運算功能,包含行動感測元件、設備物聯網、大數據、內部人工智慧演算法,只是我們將各項轉動設備端的晶片轉化成智慧管理架構與程序,透過雲端資料的人工智慧演算法及神經網路預測模型,將現場所收集到的轉動設備資訊加以賦能,化被動為主動積極改善痛點,提供轉動設備健康趨勢、元件壽命,並串聯保養維修執行,更快更早知道問題而加以預防,落實轉動設備預知保養的管理品質→圖17。
圖17、廠務轉動設備智慧化管理架構
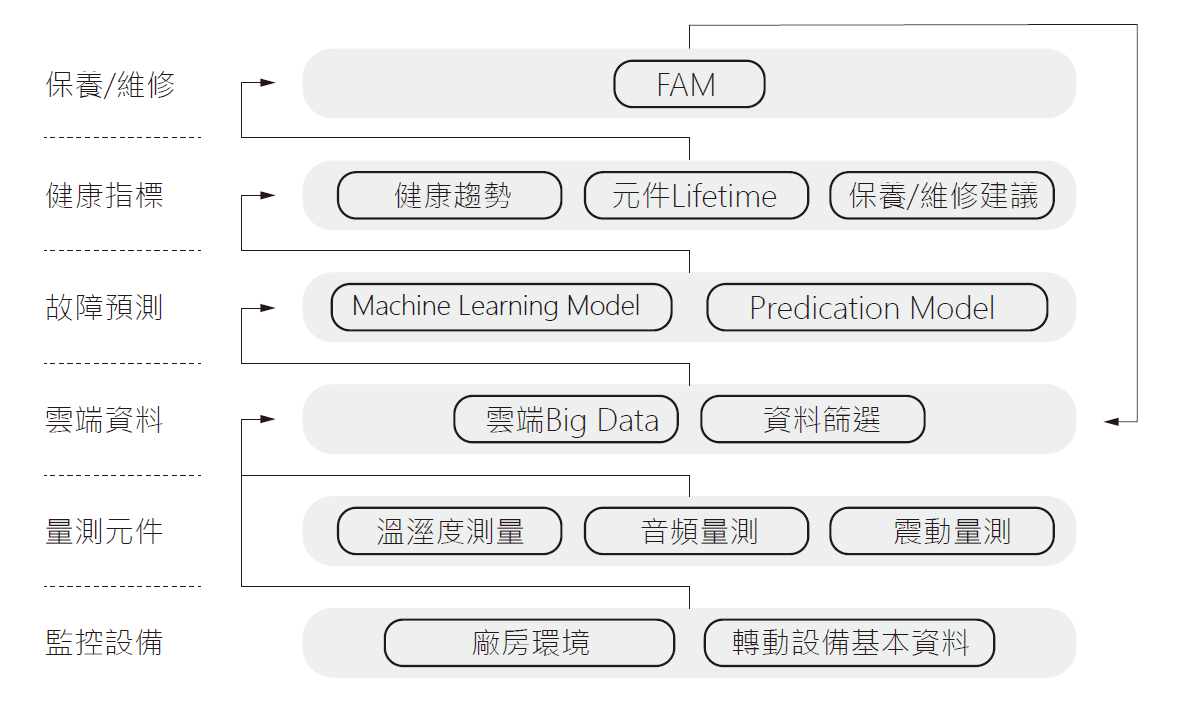
結果與分析
首先列舉三件近年轉動設備保養改善實例,藉以驗證前述定義的規範規格與管理機制是否正確適用,接著再以我們建立的人工智慧機器學習演算法與神經網路模型來驗證轉動設備故障診斷模型。
案例一、風車附著粉塵異物造成轉子不平衡
SEX#02(120hp,89.5kW,flexible,ISO10816 Group2)於例行性振動量測時,振動值最高為5.5mm/s→表5,振動值大於4.5mm/s(short-term operation allowable),進行停機維修檢查(管理機制一)。
設備編號 | SEX#02 | |||||
---|---|---|---|---|---|---|
馬達 | A1垂直 | A1水平 | A1軸向 | A2垂直 | A2水平 | A2軸向 |
4.0 |
4.5 |
4.2 | 4.3 | 4.2 | 4.4 | |
風車 | C1垂直 | C1水平 | C1軸向 | C2垂直 | C2水平 | C2軸向 |
4.8 |
4.8 |
5.3 |
5.5 |
5.2 |
4.6 |
頻譜分析振動峰值8.3mm/s發生位置於1x轉速→圖18,判斷為風車葉輪附著Powder,重心偏移造成平衡不良,清洗完成後頻譜分析峰值降至0.9mm/s,振動值3.0mm/s→圖19。
圖18、SEX#02風車頻譜分析
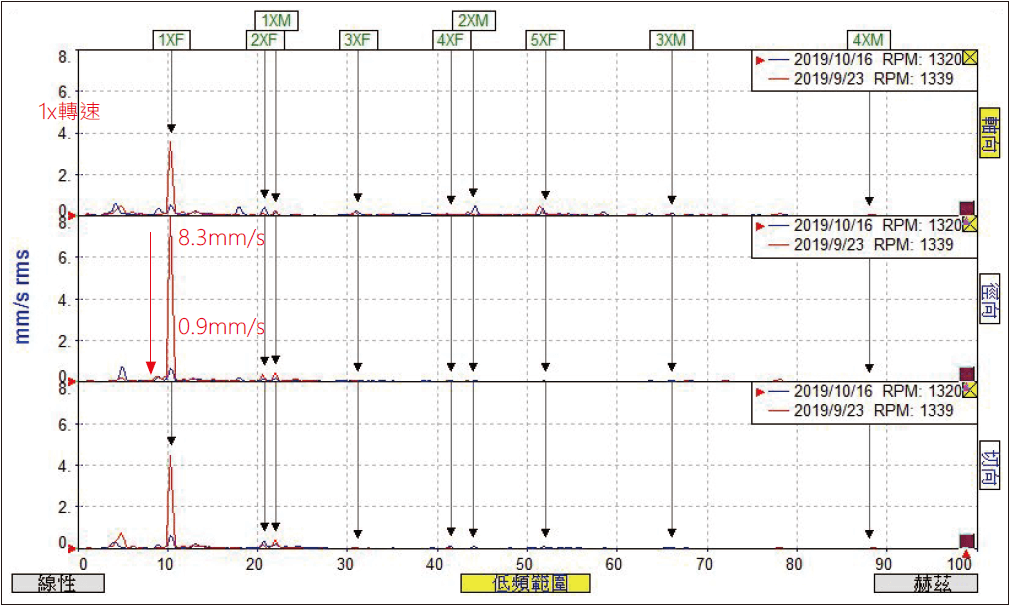
圖19、SEX#02振動量測
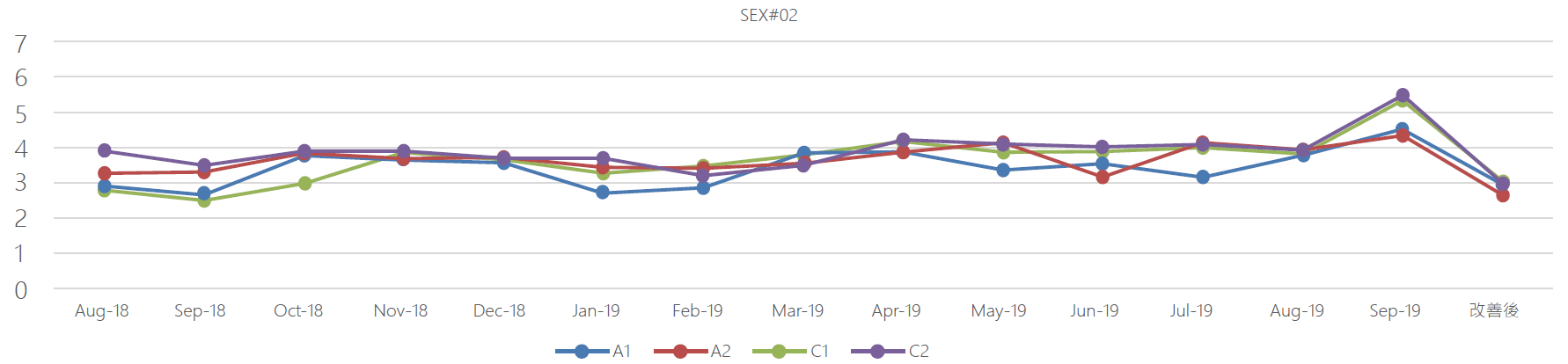
案例二、基礎結構鬆動造成機械外鬆動
SOX#22(70hp,52.2kW,flexible,ISO10816 Group2)於例行性振動量測時,振動值最高為5.5mm/s→表6。振動值大於4.5mm/s(short-term operation allowable),頻譜分析振動峰值3.1mm/s,未達停機標準,列管監控。
設備編號 | SOX#22 | |||||
---|---|---|---|---|---|---|
馬達 | A1垂直 | A1水平 | A1軸向 | A2垂直 | A2水平 | A2軸向 |
3.2 |
4.5 |
4.5 | 2.5 | 3.1 | 3.2 | |
風車 | C1垂直 | C1水平 | C1軸向 | C2垂直 | C2水平 | C2軸向 |
3.5 | 3.0 | 2.9 | 2.6 | 2.9 | 3.7 |
頻譜分析峰值發生於1x、3x轉速→圖20,於年度停機保養排除對心不良與機械內鬆動問題,判斷為馬達基礎座避震器老化造成機械鬆動(外鬆動),安排避震器更換後根治。
圖20、SOX#22馬達頻譜分析

案例三、軸承故障導致運轉異音
SOX#02(70hp,52.2kW,flexible,ISO10816 Group2)於每月聽診器檢測時發現異音,進行振動量測,振動值最高為3.8mm/s→表7。
馬達測點 | 1H | 1V | 1A | 2H | 2V | 2A |
馬達軸承更換前(6/2量測) | ||||||
---|---|---|---|---|---|---|
振動(mm/sec, pk) | 2.982 | 2.677 | 2.118 | 3.818 | 2.520 | 1.995 |
馬達軸承加速度包絡能量,gE | 3.350 |
7.044 |
馬達軸承更換後(7/4量測) | ||||||
---|---|---|---|---|---|---|
振動(mm/sec, pk) | 3.475 | 3.195 | 2.716 | 2.818 | 3.231 | 3.198 |
馬達軸承加速度包絡能量,gE | 1.372 | 2.763 |
振動值雖未大於4.5mm/s,頻譜分析峰值於0.4xN轉速且高頻信號仍有明顯訊號,查修後確定滾珠外徑有磨痕,進行更換後高頻信號消失如→圖21。
圖21、軸承更換前後頻譜分析圖
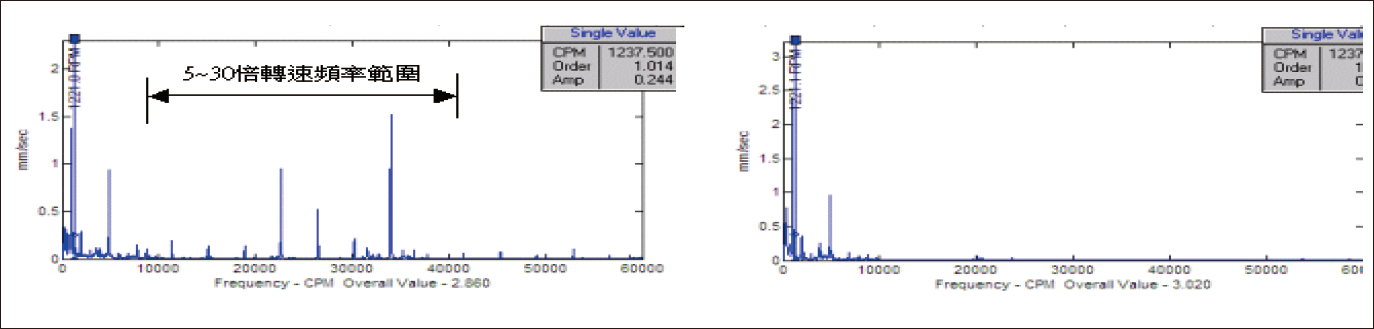
透過以上三個案例可以驗證對於故障的管制標準與健康度探討的正確性,確認適用於廠務轉動設備預知保養人為判斷。
AI-ML診斷結果與實際驗證
轉動設備每月以簡易式振動量測進行基本健康度的管控,針對轉動設備四處量測分別為水平、垂直、軸向共12點建立資料庫,我們發覺有一台製程冷卻水泵浦的振動有增長趨勢,列入追蹤改善並標示為AI-ML比對對象。
訓練完成後進行同類型轉動振動訊號類別判斷,發覺模型給出的判斷結果為內圈損傷,再經簡易震動量測發現馬達有較大之震動值(8.74mm/s),同步比對委外專業廠商以頻譜量測亦判斷馬達有內元件損壞,因為其量測結果顯示馬達1、2號軸承在3倍頻以及其諧波均出現較高測值[16]。因此,AI-ML模組的正確診斷經由軸承內圈損壞頻率量測結果相符來進一步獲得驗證。
更換軸承後再次進行頻譜分析作交叉比對,觀察到更換軸承後頻譜顯示3倍頻及其諧波振幅超越基頻的問題已經根治如→圖22。
圖22、更換軸承前/後頻譜分析圖(縱座標比例不同)
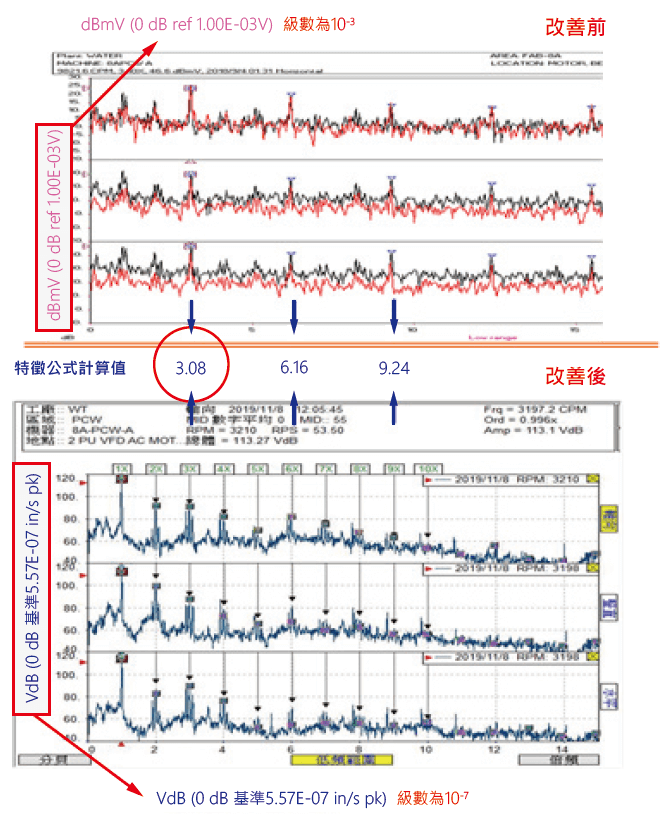
因此,我們所開發的人工智慧機器學習演算法與神經網路模型,對接FAM雲端資料庫的轉動設備相關量測訊號進行不斷的故障種類分析訓練,持續深化機器學習的能力以作為後續進一步演化的準備。
結論
既有轉動設備保養管理方式是當振動量測發現異常,再委外進一步頻譜分析,由其專業人員歸納頻譜圖逐一排除問題,發現真因之前已經耗時拆機全面檢修。本文以人工智慧機器學習模型,進化轉動設備預知保養成工業4.0的智慧化管理,研究結果顯示,透過AI-ML技術導入,該模型能夠準確有效診斷故障原因與對策,精準掌握設備的健康狀況,協助工程師自主專業判斷,即早發現問題並提供正確解決方案,將轉動設備由定期保養(被動)走向預知保養(主動)。
既有廠務中央監控系統所收集的巨量數據與運轉參數只是原料,仰賴廠務專家的 Domain Knowledge才能夠將這些巨量數據(原料)烹調出不同附加價值的星級料理,運用機器學習演算法的驗證獲得人眼未曾洞見額外知識(Insight),搭配系統性的FAM管理平台能夠使設備管理者做出有效且精準的決策,就像人體抽血般可以從中判斷出轉動設備的健康評價,更可將轉動設備的健康診斷輔以中央看板紅、黃、綠燈的顏色管理,讓所有人一目了然。
在計劃探討階段先援用美國能源局統計[17]資料做保守效益推估:「預知保養可節省12%保養費用,預防無預期停機70~75%,設備初期故障的排除可節能約5~20%」。相當於台積公司轉動設備預知保養全面智慧化後的效益分別為:「每年可節省轉動設備保養費用NT$48M,每年可節省轉動設備電力損失費用NT$560M,及每年的緊急搶修人力500工,並減少系統無備機約77,000小時的空窗風險」→表8。
轉動設備預知保養智慧化 | 效益計算方式與根據 |
---|---|
保養費用/年 | NT$400M[表2] x 12%[17]=NT$48M |
緊急搶修人力/年 | (496+227工)[2020轉動設備整合採購] x 70%[17]=500工 |
無備機風險時間/年 | 27,665台[表1] x 4小時[預估停機時間] x 70%[17]=7.7萬小時 |
節省電費/年 | (750M+4,630M kWh)[2019 Power Consumption] x 88%[轉動設備用電量佔比推估] x 5%[17] x NT$2.4/kWh=NT$560M |
建議
〝Make Experiences to Evidence〞將廠務運轉經驗內嵌在各式設備上,不因人員變動造成經驗及知識斷層,影響運轉安全及穩定度,對於台積無預期停機損失,所造成的產品損失與客戶信譽是難以估算,所以預知保養的智慧化管理不只是節省保養費用,更是讓廠務設備防護網更加圓滿,以達成理想中的運轉零故障。
「讓轉動設備自己說話」妥善運用廠務中央監控系統的巨量資料與運轉參數,從高風險轉動設備優先導入智慧化機器學習管理系統,例如中央廢氣處理系統與生產機台端廢氣前期處理等環保相關風車及馬達之類的轉動設備,高耗能的各類流體輸送泵浦、冷卻水塔扇葉、冰水主機壓縮機、空壓機之類的轉動設備,除了確保轉動設備保持於最佳狀態,也可避免台積公司的工安或環保意外風險。
參考文獻
- FEM設備保養管理系統,台塑網科技,資料來源:http://www.efpg.com.tw/ftc/zhtw/products/FEM.do
- SEMICONDUCTOR AI DEEP LEARNING AND BEYOND,藏經閣,SEMICON TAIWAN,2019.
- Strategic Partnership between Schaeffler and IBM, Schaeffler,資料來源:https://reurl.cc/9z964j
- Production-technology, Production Technology,資料來源:https://production-technology.org/tag/p-f-curve/
- 劉國青、吳順德,「ㄧ般動力機械預知保養檢測技術研究」勞動部勞動及職業安全衛生研究所,民國107年6月。
- Common Predictive Technology Applications, NASA, 2000.
- 蔡有藤、諶其騮、陳永增、曾一中,「振動量測診斷系統的發展」德霖學報,第二十四期,民國99年8月。
- 林彥廷、鄭強、張宏展,「智慧電網之高壓馬達狀態檢測與診斷系統開發應用」台灣電力股份有限公司,民國105年3月。
- Greg C. Stone, Edward A. Boulter, Ian Culbert, Hussein Dhirani,"Electrical Insulation for Rotating Machines:Design、Evaluation、Aging、Testing and Repair", John Wiley & Sons, 2004.
- D. Miljković, "Brief review of vibration based machine condition monitoring", H DKBR INFO Magazin, vol. 5, no. 2, pp. 14-23, 2015.
- ISO-10816-3 MECHANICAL VIBRATION, 2009.
- POWERING YOUR FACILITIES THROUGH MACHINE LEARNING AND ARTIFICIAL INTELLIGENCE,藏經閣,SEMICON TAIWAN,2019.
- M. A. Nielsen, "Neural Networks and Deep Learning", Determination Press, 2015.
- Confusion Matrix,維基百科,資料來源:https://en.wikipedia.org/wiki/Confusion_matrix
- Deep Groove Ball Bearings, SKF, 2019.
- R. B. Randall and J. Antoni, "Rolling element bearing diagnostics—A tutorial",Mechanical Systems and Signal Processing, vol. 25, no. 2, pp. 485-520, 2011.
- G. P. Sullivan, R. Pugh, A. P. Melendez, W. D. Hunt, "Operations & Maintenance Best Practices, FEMP",2010.
留言(0)