摘要
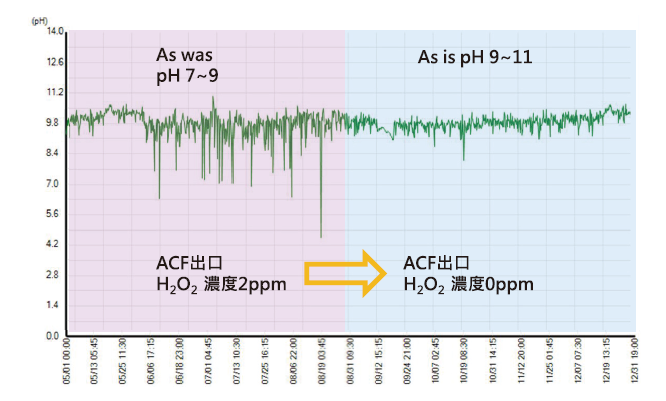
Since May 21, 2021, the HSIP began to control the concentration of acetone in the effluent(<5mg/L), and collect water pollution control fees by 3 concentration levels. In production process wastewater, Isopropanol(for wafer drying) is oxidized by an oxidant(mostly H2O2, for wafer cleaning) to produce acetone, resulting in the risk of exceeding the effluent acetone concentration. Therefore, investigation and improvement are carried out in four items, including the effluent source of acetone, wastewater optimization, wastewater treatment stability optimization and self-tracking management(target : effluent acetone conc.<5mg/L). The results show : ①the IPA source of tool: tool containing IPA is reclaimed by special management, such as high-concentration IPA is reclaimed to W-IPA, and low-concentration IPA is treated by the biological system ; ②Drain flow optimization, Such as, AWR system optimization : Replace the type of RO membrane(BW30HR-440) for improve IPA removal efficiency(40→90%) and effluent acetone conc.,W-P1 Drain and analyzer drain are reclaimed from effluent to AOR system for treatment, GC H2O2 flush bucket collection ; ③Improved stability of biological systems, such as Salix pretreatment system H2O2 Salix LSR(I) hydrogen peroxide removal rate stability improvement, Salix LSR(I) ACF installation of H2O2 analyz er, Homogenization of Salix LSR(I) RO rejection flow, RO permeate/ rejection quality check by weekly, Salix LSR(I) RO membrane perform DI water flush before replacement, nitrogen source monitoring in the biological aeration tank increases the removal rate of organic matter by 97%. The Enzyme dosing system is improved, the reaction time in the wastewater system is prolonged(>8hr), and the H2O2 in wastewater is removed to reduce the conversion of isopropanol ; ④Self-management: Cooperate with the HSIP audit and submit to third-party verification independently every week to track the concentration of effluent acetone. The improvement results show that the concentration of effluent acetone will be reduced from 9.5 to 2.5mg/L from July 21, 2021, and the self-tracking will reach the standard for eight consecutive weeks.
1. 前言
科管局為確保下游承受水體與生態環境,將針對園區污水廠進、放流水水質進行優化,自110年1月1日起於放流水標準所訂定「科學工業園區專用污水下水道系統放流水水質項目及限值」中增列加嚴管制項目及園區環評承諾水質限值,同時針對丙酮等相關加嚴管制項目進行計價收費[6]。丙酮為廠區內製程原物料廢水中異丙醇(Isopropanol, IPA)與氧化劑(雙氧水)反應之衍生物,製程中常以有機溶劑作為晶圓乾燥使用其中又以IPA較為常見,當製程以氧化劑(雙氧水)將晶圓進行清洗後再以有機溶劑(IPA)進行乾燥後,此兩股廢水排放至廢水系統過程中IPA易被雙氧水氧化產生丙酮(如 圖1),使廠區放流水有丙酮超標疑慮,因此將設定目標進行改善。
園區污水下水道使用費計價基準中將丙酮列為易燃或異味性之特殊有害性污染物,其單價為為50元/公斤並依照濃度高低分為三個級距進行計算[5],其計算與分級方式如 表1。
級距 | 水質分級 | 分級費率 | 收費單價(CH)計算公式 |
---|---|---|---|
E1 | (Pd/Psd)≤1 | 0 | CH=0 |
E2 | 1<(Pd/Psd)≤2 | 1.60 | CH=Uex(10 Pd/Psd)/ 1,000x1.60 |
E3 | 2<(Pd/Psd) | 2.S0 | CH=Uex(10 Pd/Psd)/ 1,000x2.50 |
本文將尋找丙酮及其衍生物(如異丙醇Isopropanol, IPA)與氧化劑(雙氧水)等源頭汙染物之管理對策並搭配提升系統運轉及穩定度等方式來達到放流水丙酮減量之目的。源頭管理為檢視將機台對IPA使用量、化學需氧量(Chemical Oxygen Demand, COD)與雙氧水質量平衡等方式檢視來源水與水處理系統之COD濃度,並藉由水路優化初步排除貢獻度較大之來源;第二階段為系統優化,可區分為源頭管理、生物系統開眼管理及放流水酵素加藥系統優化等方向。其中源頭管理為透過提升Salix LSR(I)系統對雙氧水與IPA去除效率,穩定生物系統來源水質/量並降低LSR(I)過剩回收水至AWR系統後其RO濃縮水至放流影響IPA濃度;透過開眼管理各生物曝氣槽營養源維持生物健康;最後藉由優化放流水酵素加藥系統,避免IPA與雙氧水反應生成丙酮。
2. 文獻探討
2.1 丙酮背景與危害
丙酮(Acetone)為無色與刺激性異味之高揮發性有機溶劑,人體短時間暴露於高濃度(>10000ppm)環境有致死風險,長期接觸或吸入會導致眼睛與皮膚嚴重刺激與頭暈噁心等呼吸道危害風險,其危害特性如 表2所示[2]。丙酮於工業中較常作為乾燥劑使用,而在傳統製造業中(如橡膠業、製鞋業、皮革業等)作為塗料使用。
項目 | 內容 | ||
---|---|---|---|
化學式 | CH3COH3 | ||
分子量(g/mol) |
58.08 | ||
蒸氣壓(mmHg)-(25°C) | 185 | ||
蒸氣密度(g/ml)-(20°C) | 2 | ||
沸點(°C) | 56.29 | ||
亨利常數(m3air/m3liquid) | 0.00103 | ||
8小時日時量容許濃度 (ppm) | 200 | ||
短時間平均容許濃度 (15min)(ppm) | 250 | ||
暴露途徑 | 食/吸入、皮膚/眼晴接觸 | ||
暴露後症狀 | 頭暈、噁心、嘔吐、昏迷 | ||
急性危害 | 吸入 | 吸入濃度>=1000ppm | 眼鼻喉有剌激不適感 |
吸入濃度>=2000ppm | 噁心、暈眩、嘔吐 | ||
吸入濃度>=3000ppm | 失去意識/死亡 | ||
食入 | 少量食入會剌激咽喉,大量食入有疲倦或頭痛等症狀 | ||
皮膚接觸 | 輕微刺激 | ||
眼晴接觸 | 接觸液體有強烈刺激感 | ||
慢性危害 | 每天暴露時間>3小時(暴露濃度1000ppm),7~15年後引起鼻、咽喉等器官功能障礙及四肢無力等症狀 | ||
長期接觸導致皮膚紅腫、龜裂、乾燥脫皮等症狀 |
2.2 異丙醇生成丙酮機制
在晶圓或光電面板製程中較不會直接使用丙酮於製程中而是採用IPA進行清洗乾燥,其中又以晶圓製程中濕蝕刻製程較為常見,在濕蝕刻製程中會以大量無機酸/鹼與雙氧水將晶圓進行清洗後以超純水進行清洗後再以大量IPA噴灑進行乾燥,在清洗與乾燥階段時會進行高低濃分流,高濃度以專管專收方式處理;低濃度則回收至水系統進行處理,而丙酮則在回收至水系統過程中IPA與雙氧水接觸產生氧化反應後生成[1]。圖1為晶圓製程中常見IPA廢水與雙氧水反應機制。
圖1、製程中IPA廢水與雙氧水轉化機制[1]
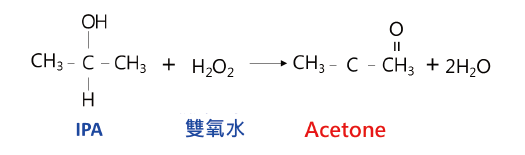
2.3 異丙醇&丙酮廢水處理技術
目前常見的異丙醇/丙酮等有機廢水處理主要可分為物理處理、化學處理與生物處理等方式,其中物理處理主要透過吸附劑生物不易降解之有機物,大多作為生物處理之前處理(適合低COD濃度之廢水);化學處理為透過強氧化劑將有機物進行分解[3]。表3為常見異丙醇/丙酮廢水處理技術。表4與 表5為常見生物處理技術與差異。
方法 | 特點 | ||
---|---|---|---|
物理方法 | ACF吸附法 | 可用於生物無法處理之有機廢水,平均每公斤活性碳可吸附5~50g COD | |
化學氧化法 | 高級氧化法 (Advanced Oxidation Processes, AOPs) | 常見方法:H2O2+Fe2+(Fenton 操作費用最低)、H2O2+UV, H2O2+O3, O3+UV, H2O2+O3, H2O2+O3+UV, O3+TiO2, UV+TiO2 | |
生物處理法 |
好 氧 |
活性污泥法、氧化渠、 批式活性污泥法(SBR)、 活性污泥膜濾法(MBR) |
|
厭 氧 |
厭氧接觸系統 厭氧污泥床(UASB) 厭氧流體化床 |
項目 | 好氧 | 厭氧 |
---|---|---|
能源消耗 |
高 需進行嚗氣提供氧氣,每去除1kg COD需1kg O2,約使用1度電 |
低 (僅需pump或攪拌動力用電) |
污泥產量 | 每公斤COD約產生0.2~0.5kg污泥 | 每公斤COD約產生0.05~0.1kg污 &0.35m3甲烷 |
產物 | CO2、H2O、SO42- 、NO3- | CH4、CO2、H2O、H2S、NH3 |
營養需求 | 去除150kg COD約需5kg氮及1kg磷 | 去除150kg COD約需0.5kg氮及 0.1kg磷 |
反應槽容量 | 去除1kg COD/day約需體積 0.5~2.0m3 | 每去除1kg COD/day約需體積 0.1~0.5m3 |
COD入水濃度 | 100~1,000mg/L | >1,000mg/L |
活性污泥法 | MBR | |
---|---|---|
污泥濃度 |
低 (2000~5000mg/L) |
高 (5000~30000mg/L or >30000mg/L) |
有機負荷耐受度 |
低 (不易處理多種污染物) |
高 (可處理多種污染物) |
反應速率 |
慢 (污泥濃度低) |
快 (污泥濃度高,SRT(污泥停留時間)可>30day,使生長緩慢的微生物得以滯留與增殖,有利於多種污染物分解) |
污泥量 | 多 |
少 (維持低食微比(F/M)操作,污泥產率可以降至 0.2SS/kg COD) |
空間需求 | 大 |
小 污泥濃度高,HRT可縮短至1~4小時,可減少反應槽所需空間 |
能源消耗 | 低 |
高 介於0.3~2kwh/m3 |
3. 研究方法與結果分析
3.1 源頭盤查
目前廠區丙酮主要藉由製程排放之IPA與雙氧水反應而成,因此將透過機台對廠區IPA使用量、COD與雙氧水質量平衡檢視來源水與水處理系統之COD濃度,並藉由水路優化初步排除貢獻度較大之來源。如 圖2顯示共四台機台之IPA直接排放至放流(占廠區IPA使用量15%,對放流水COD貢獻200ppm);水系統COD質平如 圖3顯示主要來源為HF系統(對放流貢獻77%)之HFD Drain(對HF貢獻77%),原因為AOR LSC Drain分流不佳影響;雙氧水質平顯示在氣化課灌充前進行管接頭flush至放流影響(對放流貢獻60ppm,頻率1次/1天、濃度32%),如 圖4。透過水路盤清將IPA回收至系統處理(高濃度專管外運;低濃度至生物系統處理),並將氣化課灌充flush廢液規劃以專桶回收後少量至RCW,藉由水路優化後放流水COD濃度由450ppm→350ppm。
圖2、F12P6廠區IPA使用量
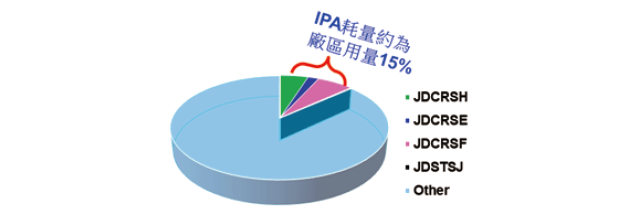
圖3、水系統水路優化與COD質量平衡圖
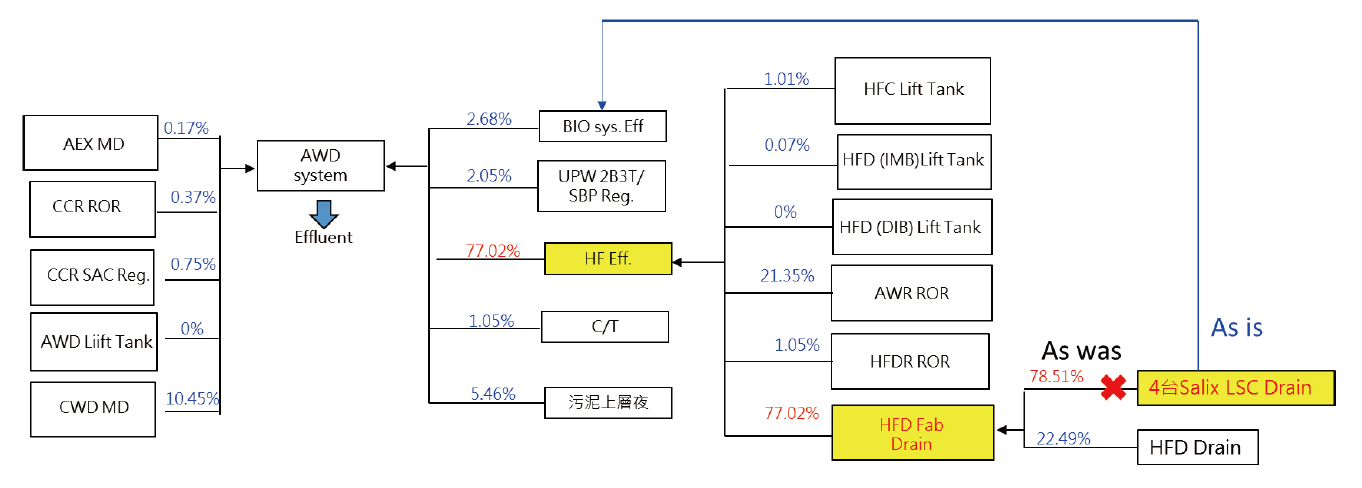
圖4、水路優化前/後放流水COD濃度(ppm)
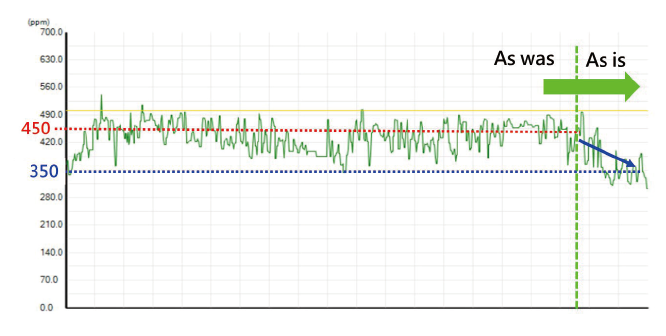
3.2 系統優化
透過水路優化初步降低對放流貢獻度後,透過優化系統處理穩定度來降低IPA與雙氧水對放流之影響,其項目包含酵素加藥系統穩定度提升、AWR回收水優化與生物系統處理穩定度提升等三方向進行。生物系統運轉初期因曝氣槽生物健康不穩定導致反應不完全產生大量泡沫影響放流水質(SS/COD/NH3-N),檢視原因為:①來源水質與量變化大於20%;②氧化性物質(H2O2)的進入,直接衝擊微生物的成長;③微生物營養源不均衡等因素影響。
源頭管理機制可分為前處理Salix LSR(I)系統氧化性物質與RO水質/量管理,透過調整源水pH至鹼性範圍(pH>9.5)穩定ACF對氧化性物質去除效率,並於ACF入出口監測雙氧水濃度即時掌握ACF健康狀況。最後透過 : ①管控IPA高效能RO膜(型號BW30HR-440)(圖5),如濃縮水水量勻化與水質定檢(週檢)、RO膜進廠更換前進行DI Flush(新膜浸泡抑菌液重亞硫酸鈉)等方式來掌握RO對IPA處理效率(>70%);②藉由穩定來源水質/量後生物系統入水TOC濃度變化由1500~2300ppm降低至1800~2000ppm(Dev. 20%→10%)(圖6);入水雙氧水濃度2~5ppm→<0.5ppm(圖7)。
圖5、RO膜(BW30HR-440)對IPA處理效能測試[4]
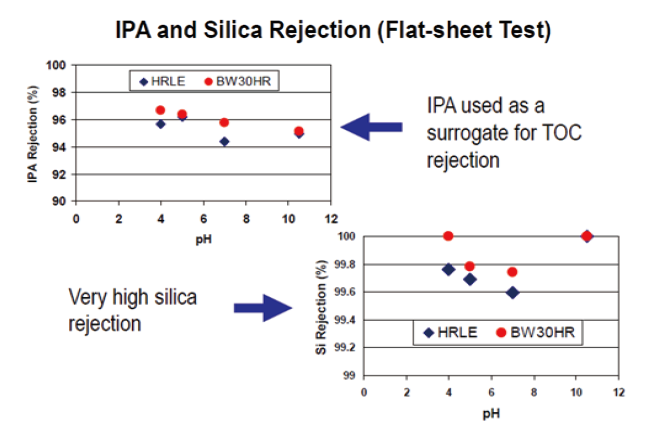
圖6、生物系統入水量(上)與TOC濃度(下)變化趨勢

圖7、Salix LSR(I) Buffer Tank pH與ACF出口雙氧水濃度(ppm)
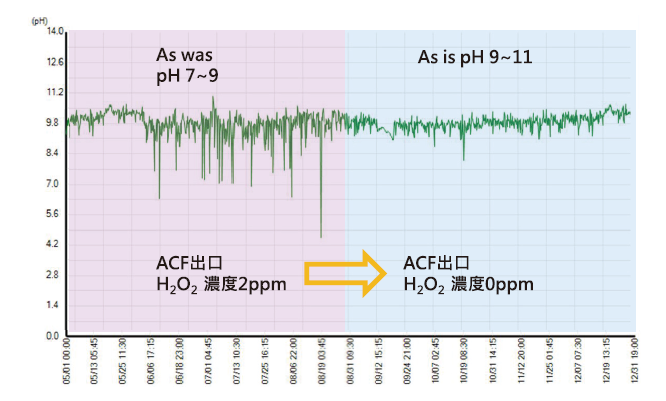
前者透過源頭管理穩定源水質/量後將針對生物系統氮源進行開眼管理,因廠區生物系統僅觀察產水NH3-N測值(>0ppm)來判斷氮源量(尿素)是否充足,但細觀後發現曝氣槽A/B/C三槽是以並聯Inlet、串聯Outlet設計(如 圖8),生物產水NH3-N出口僅代表C槽出口,不足以代表A/B槽出口,間接影響微生物生長與處理效能,因此將於曝氣槽A/B新增取樣管路進行氮源監測,即時調整營養源防止微生物營養不足導致死亡。在建立生物系統營養源管理機制結果顯示,生物出口TOC可穩定<25ppm(去除效率>97%)(如 圖9所示)。
圖8、生物系統開眼計畫
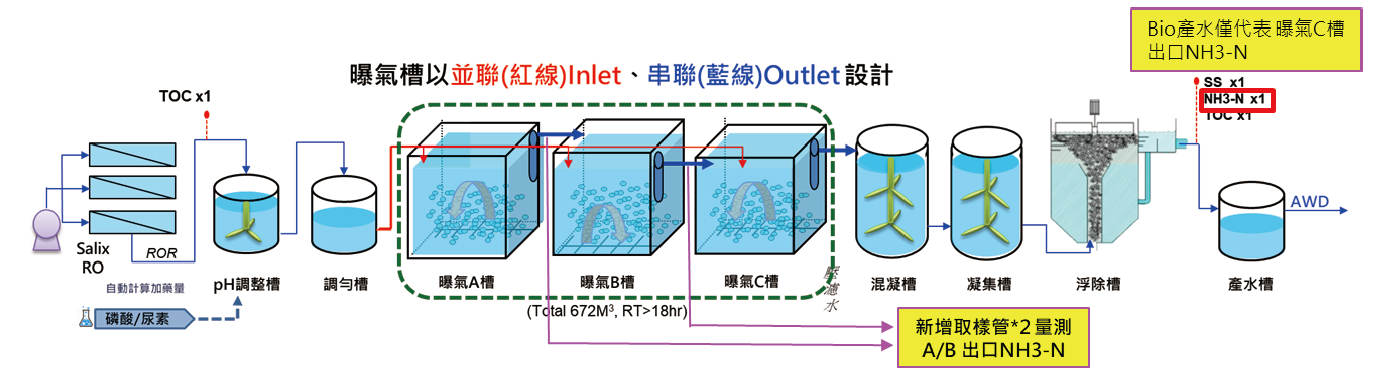
圖9、生物系統出口TOC濃度(ppm)(左)與去除效率(%)(右)變化
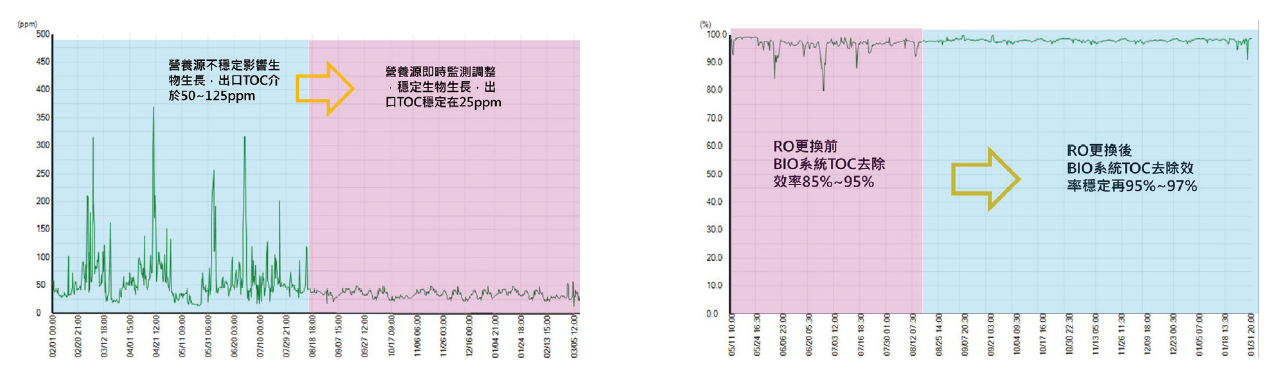
穩定IPA主要來源後將針對廢水系統之酵素加藥系統穩定度進行提升,避免放流水中IPA有被雙氧水氧化生成丙酮之風險。目前放流水雙氧水主要來源為HF系統(baseline 400ppm)經酵素處理後仍有135ppm,細觀HF系統水路發現主要為反應停留時間不足影響,因此將調整HF系統水路(桶槽由並聯→串聯)延長酵素反應停留時間(5→13小時),經水路調整後HF系統與放流水雙氧水濃度由135→20ppm與50→10ppm。
3.3 成效管理
在經過IPA源頭盤查與水路優化後初步將高低濃度進行分流,在透過處理系統穩定度提升(Salix LSR(I)/ 生物系統運轉穩定度提升)與酵素停留反應時間優化後F12P6廠區放流水丙酮已連續8週達成<5ppm之標準(如 圖10)。除了透過廠區自主連續監測與科管局(雙週檢)抽檢放流水丙酮外亦委託第三方檢驗機構進行水質驗證(週檢),以確保廠區內水質監測無誤(圖10)。
圖10、廠區放流水丙酮/COD自主檢測與第三方水質檢測趨勢

4. 結論
廠區放流水丙酮減量與管理可透過源頭盤查分流、前處理與生物處理系統穩定優化、放流水氧化性物質去除效率提升與自主追蹤管理等方式管制,其中各項管制策略如 表6所示。
改善項目 | 系統 | 處理單元 | 改善措施 | 改善成效 |
---|---|---|---|---|
機台分流盤查 | - | - |
機台IPA高低濃度分流 (高濃度專管外運;低濃度至生物系統處理) |
放流水COD濃度450ppm→350ppm |
系統運轉穩定提升 | Salix LSR(I) | ACF |
|
源水pH>9.5,ACF出口雙氧水濃度2~5ppm→<0.5ppm |
RO |
|
生物系統入水TOC濃度變化由1500~2300ppm降低至1800~2000ppm(Dev. 20%→10%) | ||
生物 | 嚗氣槽 | 各嚗氣槽營養源監控 | 生物出口TOC可穩定<25ppm(去除效率>97%) | |
WWT | HF/AWD | 酵素反應停留時間延長(5→13小時) | HF系統與放流水雙氧水濃度由135→20ppm與50→10ppm | |
自主追蹤管理 | - | - | - | 廠區放流水丙酮已連續8週達成<5ppm之標準 |
參考文獻
- 高科技產業含異丙醇廢水經氧化轉換為丙酮之研究。
- 開發填充式陽極之生物電化學系統進行丙酮廢氣處理及操作性能之研究。
- 有機性廢水處理第五冊。
- FilmTec RO膜元件與其特性訓練教材,杜邦水處理(原陶氏水處理),2011年。
- 國家科學及技術委員會新竹科學園區管理局新竹園區污水下水道使用費計價基準,2022年。
- 科技部新竹科學園區管理局竹南園區污水下水道可容納排入之水質標準第二條修正總說明,2021年。
留言(0)