摘要

AGV巡檢應用於廠務管理之策略
Keywords / System Inspection,AGV(Auto Guided Vehicle),Object Detection2,AI (Artificial Intelligence),DNN(Deep Ne ural Network)
前言
廠務的管理
廠務提供工廠生產的水、氣、電、化學品、空調、潔淨室等系統,依公司的願景「作為全球邏輯積體電路產業中 ,長期且被信賴的技術及產能提供者」[1],廠務以Delivery On Schedule、Zero Impact、Non Interruption為目標,建置系統。運轉管理,以自動監控系統,管控水、氣、電、化學品、空調、潔淨室,由人員進行工程管理,管制系統的變更,輔以各項的管理活動,如人員巡檢、作業觀察、工安稽核等現場的主動視察,以維持良好且穩定的系統供應,達成上述的目標。
其中,現場的巡檢是廠務管理暸解運轉中的設備必要而不可或缺的工作,即使已將關鍵重要的訊息納入廠務監控系統,仍然不能取代人員到現場的巡檢,許多系統的異音、異味、漏水、漏酸、風管結晶,仍無法由監控系統,得靠人的巡檢,從看、聽、觀察發現異常,或即將發生的異常。尤其是在工安意外的預防上,廠務工程師是第一線負責安全的人員,不論重點、或全程的監工,都僅能局部的監看,而有系統、密集度高的巡檢系統,是提高工作安全、系統穩定所必需的。
廠務巡檢的重要性
根據國外的統計數據顯示[2],事故發生的原因以機械失效比例43%最高、80%的風險損失主要來自20%的設備。據日本電氣協同研究調查,電氣設備是否異常,日常的巡檢是最簡易也最有效率發覺問題的方法。
隨著晶圓廠區的日益擴大,設備數量、管線愈多、系統愈益複雜,人員巡檢耗時,巡檢的項目有143項之多,包含系統供應穩定、工程管理、安全設施、用電安全、人員紀律、化學品與氣體的使用管理、環境管理等類別,培訓有經驗的工程巡檢能力,速度趕不上1年2~3個晶圓廠的擴充,且不同的人員異常經驗累積不同,能發現的異常品質不一,也不夠全面。工安環保部於TSM(Total ESH Management)系統上的統計資料,顯示在廠務的主動巡檢下,仍被工安稽核到的缺失→圖1,近4年來稽核件數並未隨廠區運轉穩定或人員訓練減少而收斂。一個能協助或降低廠務異常發生的主動巡檢系統,是廠務達到Zero Interruption目標的重要管理工具。這新的巡檢系統,必需能系統化地累積巡檢的專業,且整合水、氣、機、電的不同專業,累積異常種類,提供予系統工程師、管理者,作為分析、改善,甚或能使PM落實、品質提昇,是發展AGV巡檢系統的重要目的。
圖1、工安稽核的巡檢缺失統計
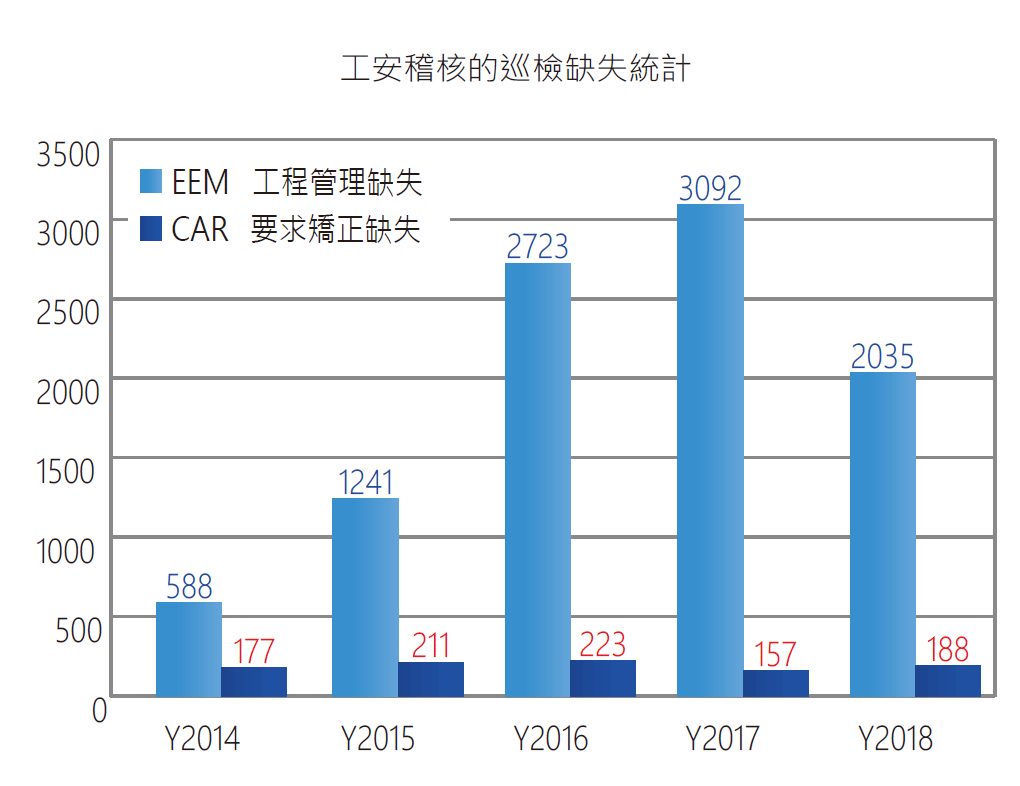
可移動的AGV(Auto Guided Vehicle),可作為攝影機 、聲音、紅外線影像、氣體偵測器的載台,可到達原有CCTV、FMCS(廠務監控系統)所無法到達的死角,配合後端的AI(Artificial Intelligence)辨識能力,辨識異常影像,統整巡檢AGV在現場搜集的資訊,同時藉由類似廠務SCADA監控的操作介面,由異常警報與回傳影像,決定至現場的處理順序,或者在遠端遙控AGV做不同的處置,可達成一人值班監控多台AGV巡視廠區的功能。
當累積夠多的物件辨識能力後,結合AI的演算法可取代人員在現場的高風險作業監工,由AGV定點發出聲響警報、語音,同意或停止現場作業,甚或指示有作業順序的步驟。
再藉由AI演算法已發展成熟的人臉辨識系統、廠務的工程管理(EEM, Electronic Engineering Management System)、廠商預約系統(EMS, Entrance Management System)、廠務PM與資產管理系統(FAM, Facility Asset Management),可主動規劃出不定點監工的巡查路線、查核PM落實與施工品質、人員動向,做更精準的出工管理。
本文將研究巡檢AGV系統,與上述各項功能的結合,訂定發展的策略與應用。
文獻探討
廠務巡檢AGV結合兩大核心技術,一為AGV收集資訊、另一為後台AI辨識與資料處理,國內並無成熟的產品與應用實例。
行動載台收集資訊
綜觀以行動載台收集資訊的相關發展,從Google街景車(2007年)開始以移動式汽車配合全景CCTV,收集大量圖像,作為Google地圖的輔助功能,相較於巡檢AGV,街景車僅收集資訊不做判讀與處理。
波士頓動力Atlas 機器人(2016年)[3]→圖2,用於搜尋及拯救,能自主行走不靠定標導引,配備視覺處理與雷射測距儀,用以避障、閃避與選擇行走路徑,能克服各類地形障礙,可解決福島核電事故不適於人進入的搜救工作,堪稱最強雙足機器人,但未能作物件識別與資訊收集分類。波士頓動力的另一型為機器狗SpotMini(2018年)→圖3,可在有人員暴力阻擾下,自行開厚重的防火鐵門,此技術可作為巡檢AGV不會開門的借鏡,無法進入各個以防火門區隔區域的困擾。
圖2、能克服地形障礙的搜救雙足機器人
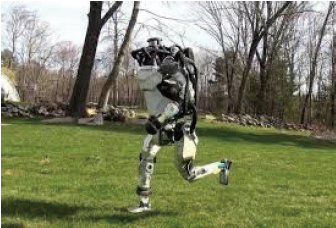
圖3、能自行開防火雙開門的機器狗
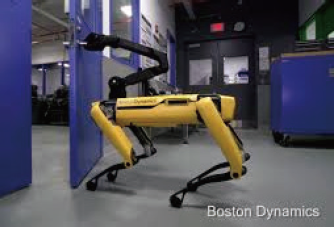
變電站巡檢機器人[4]→圖4,應用實例在中國大陸,使用於戶外變電站,配備可見光CCTV、紅/紫外光影像、RFID、超音波感測系統,收集戶外變電站高壓電力設備的特有異常,如過熱、電暈、負載資訊,適用於大區域、少人或無人看守的變電站。這是較類似巡檢AGV的功能應用,但侷限於戶外電力設備,後台僅提供監控系統的警報、報表功能,也沒有自動辨識異常能力,必需靠值班人員監控。
圖4、戶外變電站的巡檢機器人
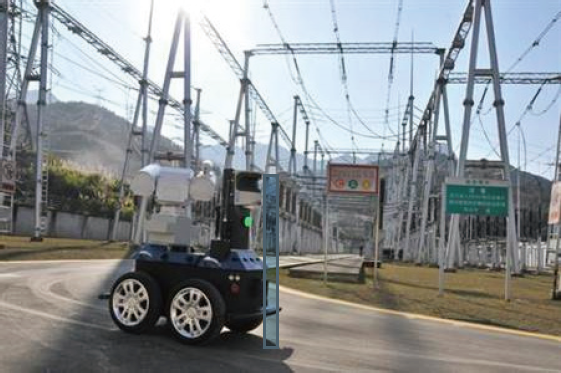
辨識與資料處理
由於行動載台拍照、截取影像的定位,包含拍攝定點、拍攝角度的精準度,影響辨識系統的辨識度,以AGV的定位點在±2.5cm,CCTV拍攝角度在±0.02,在3公尺外的物體所產生的影像位移與角度差,已是傳統影像辨識軟體無法處理的,必需採用AI中的深度學習(Deep Learning)技術,才能符合此類的影像辨識需求。
史丹福大學的視覺研究實驗室ImageNet[5],提供1400萬個各類手工註解的圖像,包括狗、豹、車、船、人,各類一般人能辨識的物件→圖5。自2010年起舉辦大規模的視覺辨識挑戰賽(ILSVRC),3年後AlexNet演算法(2012年) 採用8層(Layer)深度的類神經網路(DNN, Deep Neural Network),首度將辨識錯誤率降至16.4%,突破傳統視覺辨識的瓶頸。隨後各研究人員大量採用多層(深度)類神經網路提高辨識率,ResNet (2015年)採用152層,辨識錯誤率低於人類的5%錯誤率,來到3.57%,確認深度學習的影像分類技術已可應用於市場,如→圖6顯示深度學習層數與辨識錯誤率的關係。巡檢AGV可導入此技術,進行靜態相片的物件辨識,逐步認識廠務區域的各項設備、風管、閥件,以辨識出異常。
圖5、ImageNet 提出的圖像辨識資料庫範例
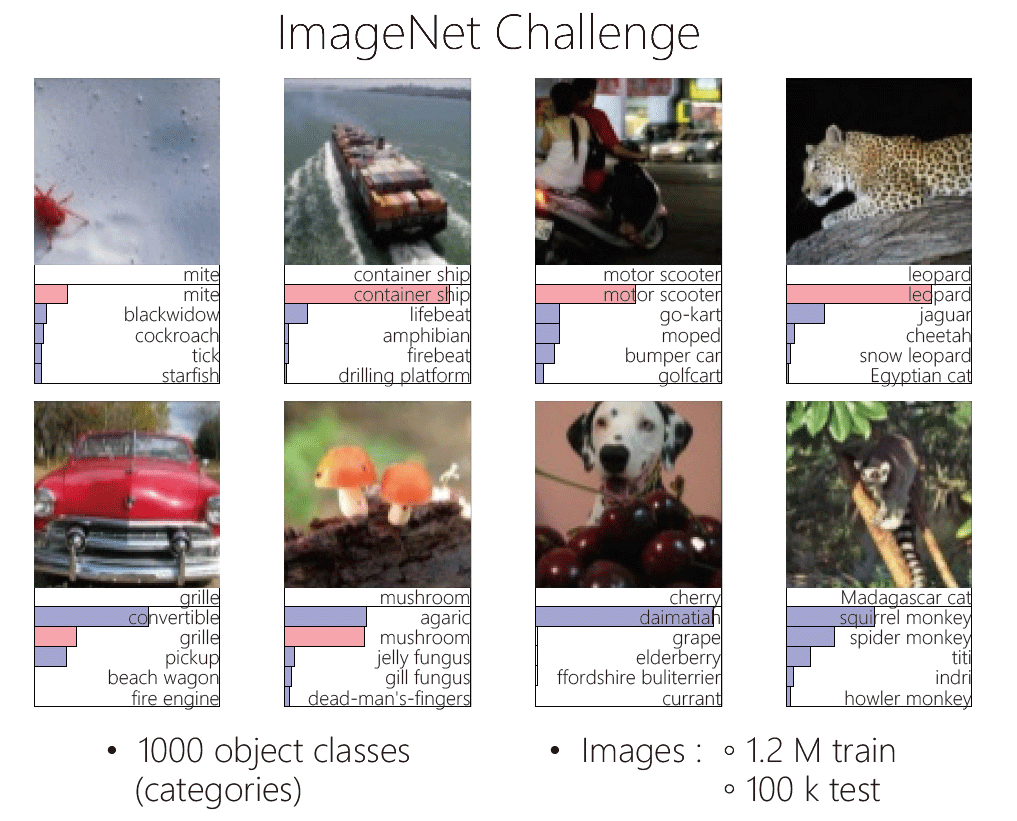
圖6、ILSVR 大規模視覺辨識挑戰賽歷年辨識錯誤率與DNN層數
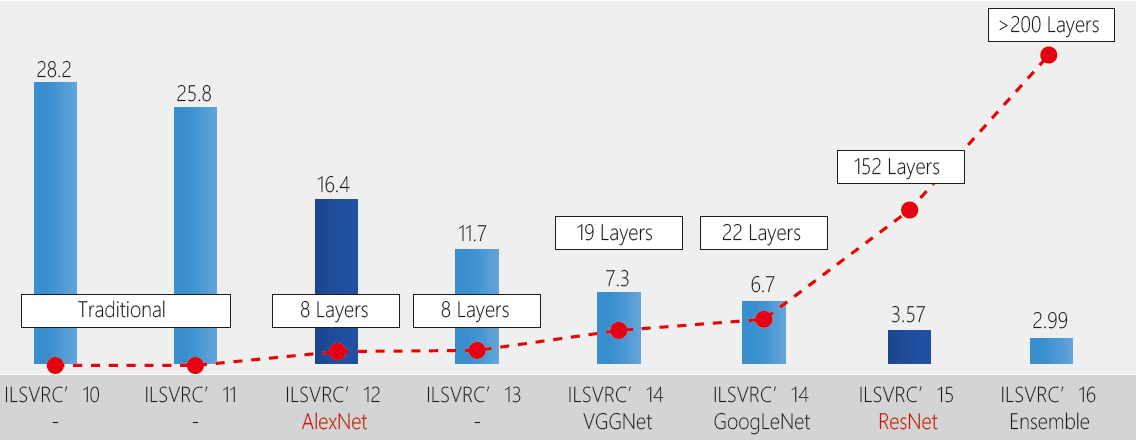
照片後傳至辨識軟體的應用,可大量累積巡檢的異常與分類,但在現場監工的應用上,需要即時的辨別與反應,偵測移動中物體的種類、工項的順序與辨別工安上的禁止事項。
YOLO(2016年)演算法[6],可以每秒45張圖的速度做物件體偵測,框出影像中的每個物件,辨識物件種類,但無法達成工安所能辨別的危險動作,發出禁止等功能→圖7。
圖7、YOLO 能框出並辨別出即時影像的物件
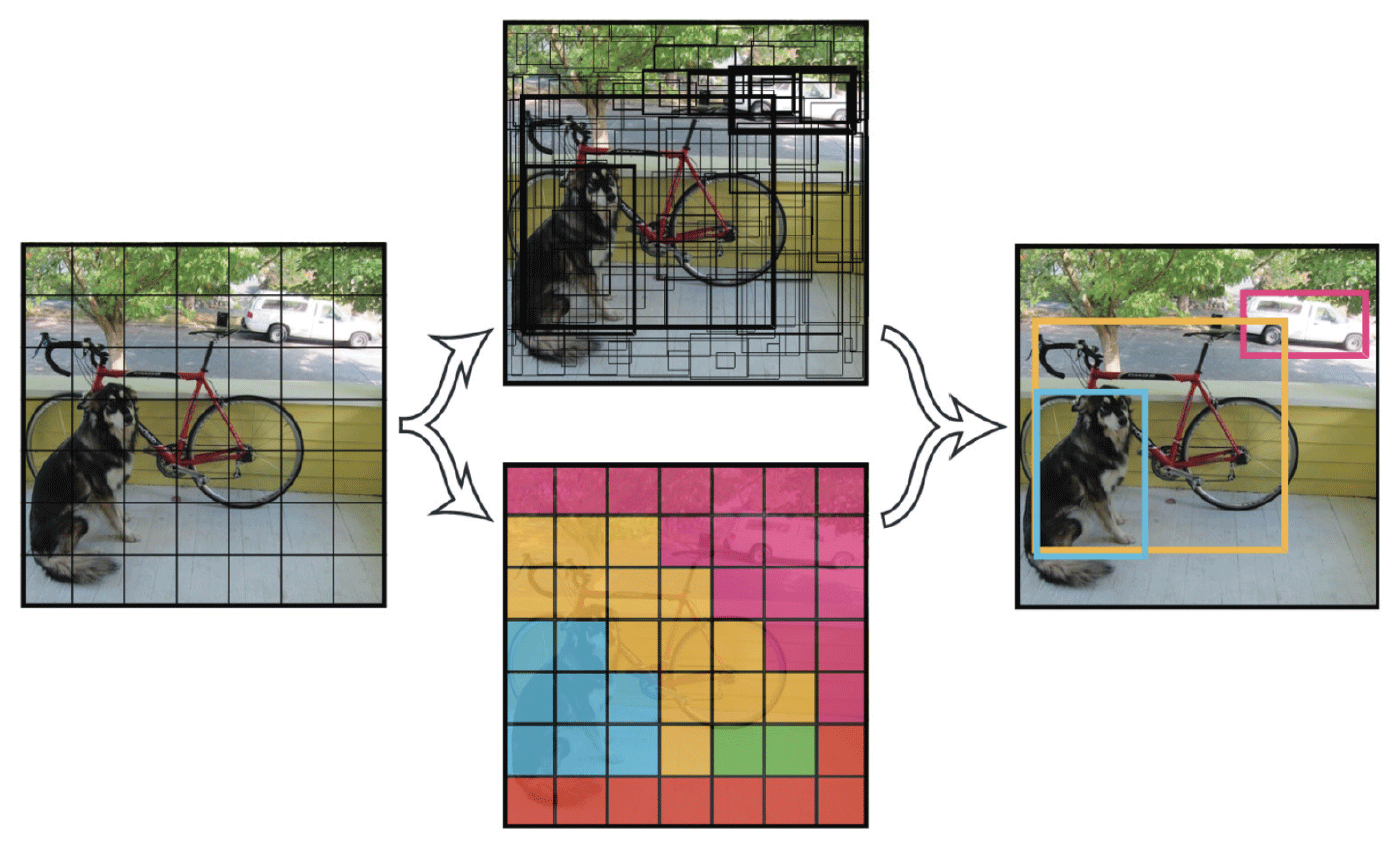
談巡檢機器人於廠務運轉之應用[7],描述廠務巡檢AGV的應用技術、機器辨識技術、可應用的視覺、AMC、巡檢範圍、網路架構等詳細的規畫。尚未涉及與廠務管理的相關監控、工程管理、工安、人員管理等相關的連結與應用。
AGV 巡檢的系統架構與方法
AGV巡檢的系統架構
AGV自動巡檢系統架構分為四大部份→圖8,分別為前端AGV收集資訊載台、監控與資料存取平台、AI辨識程式平台、AI辨識模型訓練平台。
圖8、 AGV自動巡檢系統架構
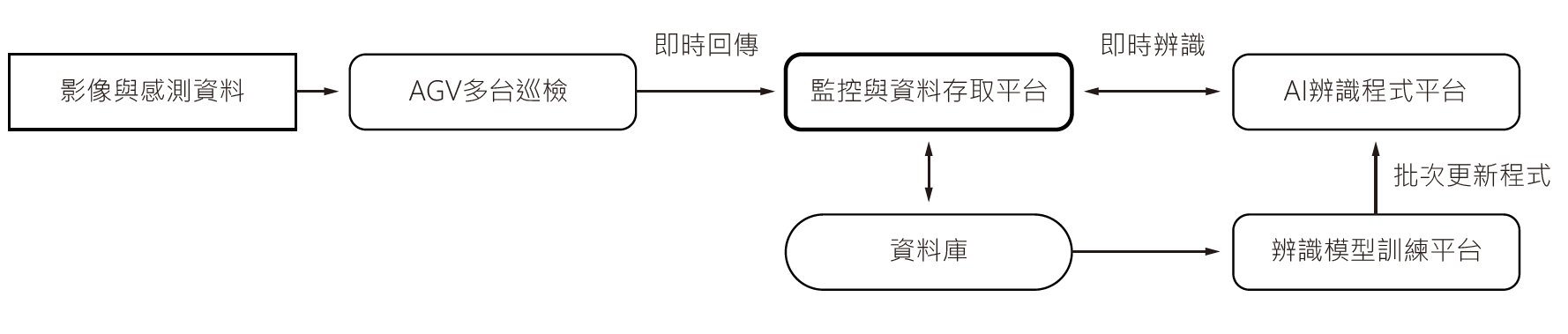
可移動的AGV搭載攝影機、聲音、紅外線影像、氣體偵測器等偵測儀器,將影像、聲音等訊息透過網路回傳資料至監控與資料存取平台,再由後台的AI辨識平台負責異常的辨識與輸出,可同時執行多個不同區域、用途的辨識程式,經由監控與資料存取平台顯示警報;其中監控與資料存取平台負責各平台間的整合工作,即時傳送前端AGV的資料、接收與顯示AI辨識程式辨識後的結果,同時作為使用者的操作監控介面,具備報表、簡訊、警報、資料庫等一般功能外,尚規劃資料分類儲存功能,準備與儲存AI辨識模型所需的訓練資料。
AI辨識模型訓練平台,負責模型訓練前資料的分類、處理、標記,各不同類型需求與不同場域物件的AI辨識程式訓練,此部份為最耗費硬體資源、程式編譯人力、資料處理與標記人力,故獨立於例行監控巡檢的平台之外,同時為巡檢辨識能力發展與提昇的中心系統。訓練編譯完成的各個程式,放置至AI辨識程式平台各別執行,各別自資料存取平台取得前端資料,各別輸出辨識結果,由操作監控介面顯示。
AGV 巡檢的方法
原有人員巡檢以工程師的系統專業,配合巡檢清單,巡視現場,找出各類系統可能的異常,AGV則必需排定路線 、定點拍攝、錄音或取得各類感測資料。依FAB廠房約200公尺x200公尺的面積,規劃120到200個巡檢點,以影像識別為例,每點拍攝6張相片,作為類似全景的巡察,可在1小時內完整走主要、次要走道,覆蓋全區所需巡視的區域;配合AGV的充電時間,一天可巡8次,巡視間隔遠優於人力。對於需特別巡視的定點、錶頭等,需較精細的拍攝或收集,可另定時程、路線規劃,作為特定的巡檢與資料收集。
與人員巡檢或遠端的CCTV、FMCS(廠務監控系統)、GMS(氣體監測系統)比較,AGV可到達上述固定系統無法到達的死角。配合後端的AI(人工智能,CNN)辨識能力,辨識異常影像,統整巡檢AGV在現場搜集的資訊,藉由監控操作平台回傳的影像與警報,決定至現場的處理順序,或在遠端遙控AGV做不同的處置,可達成一人值班監控多台AGV巡視廠區的功能,人員與AGV巡檢的各項比較→表1。
比較 | 人的巡檢 | AGV 自動巡檢 |
---|---|---|
巡檢路線 | 規劃路線,固定或臨時應變路線 | 1. 規劃固定路線,變更需人為介入 2. 採用SLAM(同步定位與地圖構建)技術或磁軌,自行導引巡檢 |
巡檢檢查方式 | 點檢項目 | 1. 規劃定點,6秒內拍攝6張左、中、前的上下相片 2. 由點檢項目發展視覺辨識項目 |
巡檢間隔 | 1~2次/天 | 1. 例行巡檢可規劃到8次/天 2. 可規劃特定路線、特定施工區的專屬巡檢 |
巡檢記錄 | 點檢表 | 異常影像、警報清單、報表 |
巡檢區域 | 所巡的區域 | 規劃單一樓層,可與電梯整合跨樓層,無法開門 |
巡檢落實度 | 只能確定有做 | 留下影像、時間、巡檢路線、累積巡檢經驗,留下有意義的資料、報表統計、確實管理 |
當累積夠多的物件辨識能力後,結合AI的循序辨識演算法(RNN)可取代人員在現場的高風險作業監工,由AGV定點發出聲響警報、語音,同意或停止現場作業,甚或指示有作業順序的步驟。再藉由已發展成熟的人臉辨識系統 、廠務的工程管理(EEM)、廠商預約系統(EMS)、廠務PM與資產管理系統(FAM),可主動規劃出不定點監工的巡查路線、查核PM落實與施工品質、人員動向,做更精準的出工管理。
AGV 巡檢的演算法與發展策略
人的五種感官訊息接收能力,以視覺83%為主,聽覺11%為輔,其次為嗅覺3.5%,AGV的巡檢能力也依感官發展的順序發展,首先以視覺的影像辨識為主。
AGV巡檢辨識演算法
物件辨識
對於廠務巡檢的視覺能力,「發現異常」,並無可直接應用的AI演算法,必需結合現有的演算法發展,有二種方法可發展:
- 先認識再辨別異常物件:累積認識的廠務設備物件後,再巡檢辨別異常與正常。
- 由正常背景分類異常物件:建立正常背景相片,逐日巡檢累積「不同處」,再篩選出異常物件。
一種的說明→圖9,為先建立各項廠務設備、物件的辨識能力,訓練AI的辨識分類程式,以此程式辨識影像中「 不能辨識的影像」,將其分類為未知的異常,再交由後台人員辨別為何種異常,註解並分類儲存,待儲存夠多的異常種類後,再重新將原有的AI演算法與所累積的異常,訓練新的演算法,讓新的演算法,能直接認識異常,在上線後直接發出異常的警告。不斷循環這個過程,以累積認識的異常,提昇巡檢的能力。
圖9、先認識再辨別異常物件
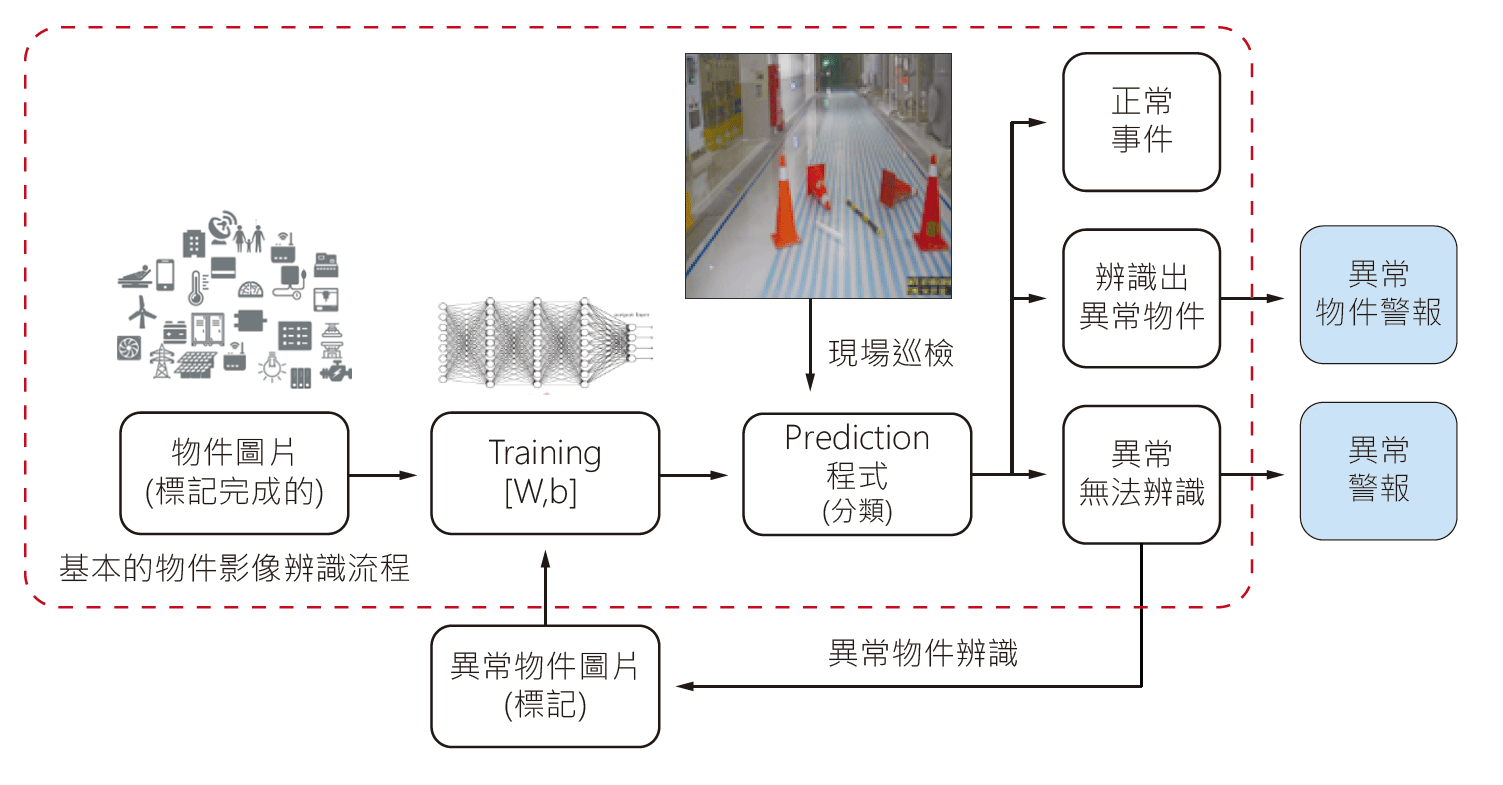
第二種的說明→圖10,以廠務各區的正常影像為背景,程式上線直接比對出「不同」的影像,再由後台人員判斷,歸類異常相片,累積後再訓練AI分類程式分辨出異常的種類並發出警報。
圖10、由正常背景分類異常物件
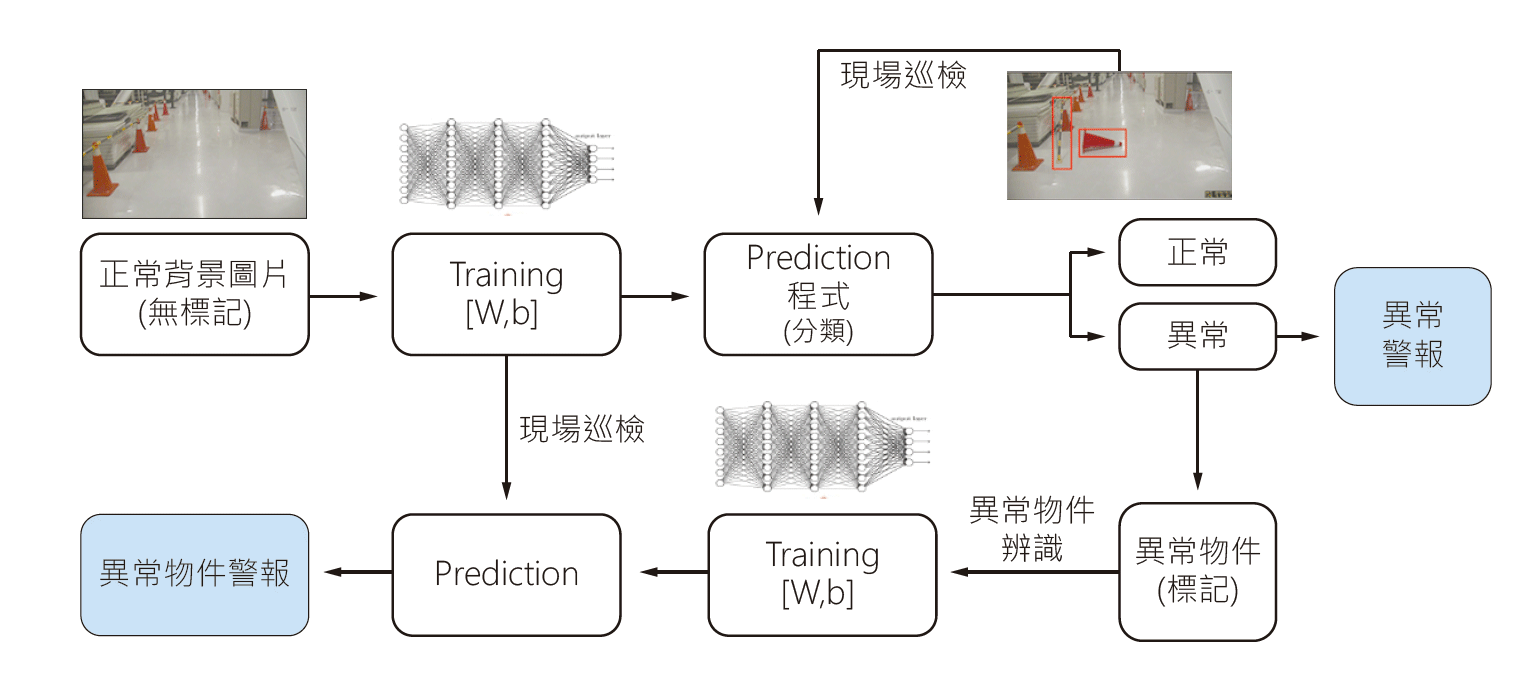
此二種方法均有別於現行演算法的輸入標記完成的訓練資料、訓練模型、調參數、測試、上線的程序,在訓練資料需要人工框選物件、異常予辨識程式訓練(AI用語為Labeling)的工作,可由程式自動框選「不同處」,節省初期的人工框選動作,產生AI影像辨識所需「高品質」的「大量訓練資料」,能有效降低在廠內的資料處理人力,以提昇辨識率。
事件辨識
需兩個「物件」或兩個以上「物件」合併辨識,才能判定的異常,稱為「事件」,例如:人員「腳」站立「A字梯梯頂」、在「施工圍籬內」未著「防護衣」均為違規的「異常事件」。「事件」 的辨識演算法,基於「物件」的辨識輸出結果,再進行異常與正常事件的AI訓練,演算法架構→圖11「事件」的辨識架構。
圖11、「事件」的辨識架構
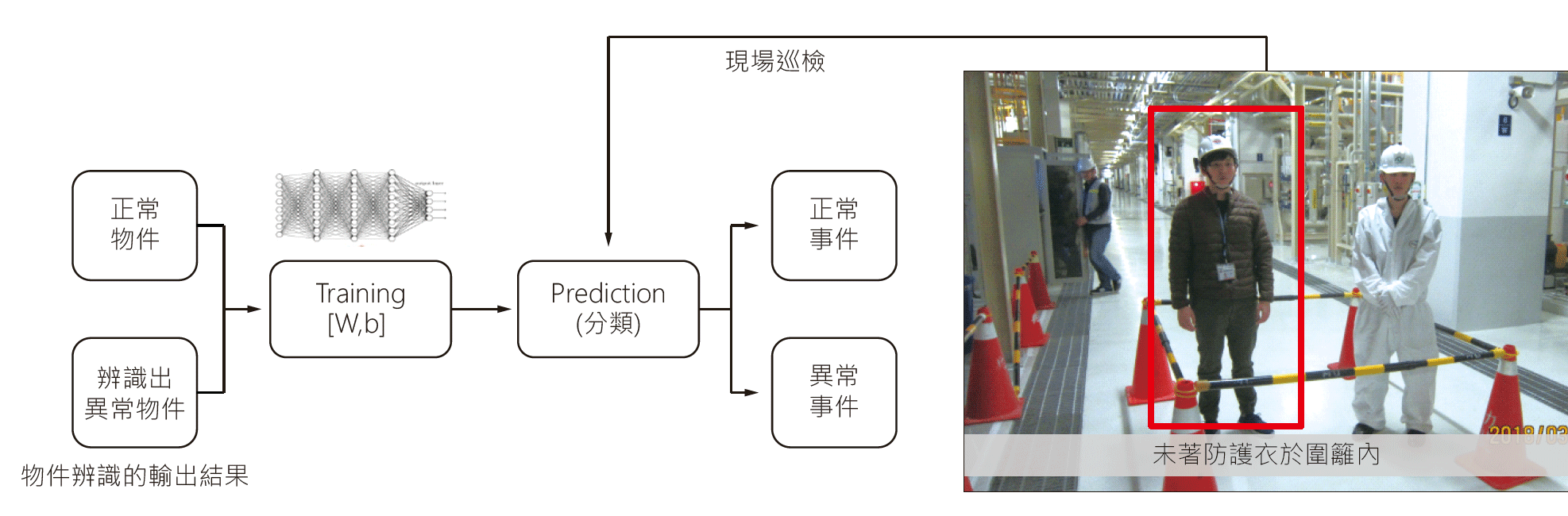
循序影像辨識
最後一部份,需工程師全程監工的高風險作業,必需基於「物件」、「事件」的辨識基礎,利用AI中的循序演算法,對此類有工程順序的作業,進行辨識,不同於前述三種巡檢模式,廠務多達56項的高風險作業,需發展不同的循序程式獨立運算,需另設硬體或單獨的AGV處理運算。例如:槽車的充填作業,必需先圍籬穿著防護衣後,才能接管作業等,有多項步驟有先後的順序,不能前後對調。而此類作業特性需長時間、在固定地點,需另設獨立的AGV於作業地點,或就地利用原有的CCTV影像。
AGV巡檢的辨識發展策略
由一般例行巡檢、找系統異常,對單一物件的「物件異常」到「事件的異常」,已進入「施工巡檢」與「作業安全」的管理範圍。在系統的「物件」、工作安全的「事件」,均訓練足夠的數量後,接著可同時發展設備保養與工程巡視,與高風險作業需工程師程監工的作業。其中工程巡視,應結合EEM、廠商管理、高風險作業認證系統 ,人臉辨識,每日依施工地點規劃不同的巡檢路線,可對廠務系統為數最多的「系統變更管理」,增設一道主動的機制與自動的防線。綜合上述AGV巡檢應用於廠務的管理規劃→圖12發展。
圖12、AGV巡檢應用於廠務的管理規劃發展
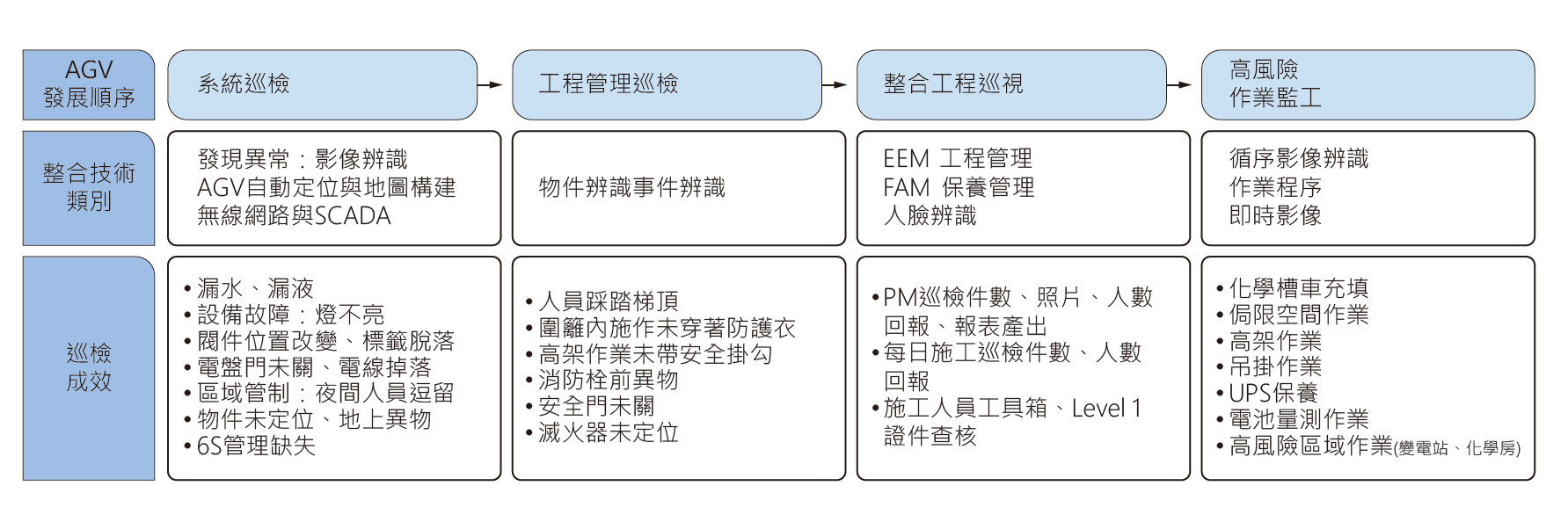
驗證測試與討論
AGV巡檢的辨識成效驗證
物件辨識成效
AGV上線巡檢的功能,由AGV現場拍照、回傳至後台辨識軟體判別、輸出警報與異常相片,已完成全功能的測試 ,→圖13為廠務控制室(FMCS Room)的遠端監控畫面,→表2為實際巡檢回傳的成果,→圖14為AGV現場巡檢的現況 。為了即時擴展辨識能力,人為製造的異常,包含系統管理與安全管理的巡檢異常警報回傳共有22項→表3→表4。
圖13、AGV巡檢的遠端監控畫面圖
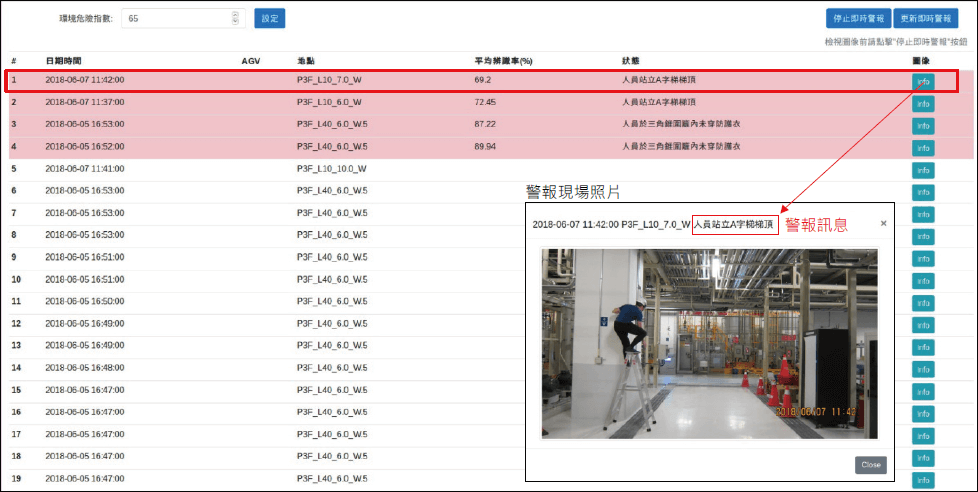
圖14、AGV現場巡檢的現況AGV巡檢的遠端監控畫面
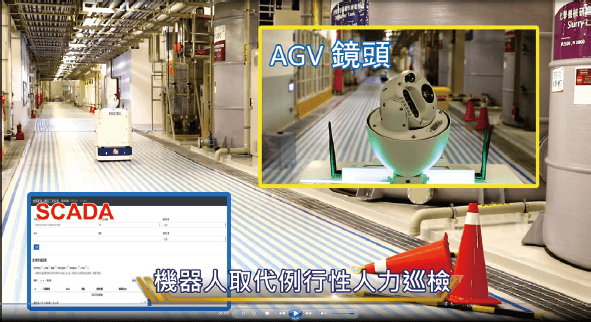
穩定運轉(6項) | ||
---|---|---|
6S缺失-閥件標籤脫落 | 設備故障-燈管不亮 | 6S缺失-三角錐圍籬倒地 |
![]() |
![]() |
![]() |
6S缺失-手工具遺落 | 區域管制-人員擅闖(19:00後) | 6S缺失-三用電表&地上異物 |
![]() |
![]() |
![]() |
穩定運轉(19項) | ||
---|---|---|
運轉風險-MAU腔體門開啟 | 運轉風險-地上電線未防護 | 收工缺失-LSC盤門未關 |
![]() |
![]() |
![]() |
漏液風險未處理地上吸酸棉 | 施工缺失-水溝蓋未放回原位 | 暫存區管理缺失濾網擺放不整齊 |
![]() |
![]() |
![]() |
1.MAU腔體門開啟。2.地上電線未防護。3.LSC盤門未關。4.地上吸酸棉。5.水溝蓋未放回原位。6.暫存區物料未定位。7.手工具未收。 8.無塵包未收好。9.推車未定位。10.三角錐傾倒。11.閥件標籤脫落。12.安全帽放置地上。13.施工廢料未清運。14.延長線未收。15.A字梯未收。 16.雙勾安全帶未收。17.三用電表放置電盤上。18.防護衣未收。19.輪檔未放。 |
安全相關(3項) | ||
---|---|---|
防火門被打開 | 滅火器移位 | 消防栓前放置A字梯 |
![]() |
![]() |
![]() |
此測試包含使用第一種方法「先認識再辨別異常物件」,先認識5個物件,以網路上找得到的相片作為訓練資料,易於框選出高品質、不同角度的相片供予辨識模型提取特徵,在廠外訓練模式調整完辨識參數後辨識率達90%以上再進場,包含三角錐、A字梯、安全帽、圍籬、防護衣,完成現有辨識演算法的部份。但在異常的辨 別上,因異常的訓練照片不夠多,會讓辨識率變低,適合的異常、正常相片比例要各約佔半數較佳,此點可如下方式克服 ,例如:人為製造異常、擴充異常的相片數,即同一異常,拍攝不同角度的相片。
在使用第二種方法「由正常背景分類異常物件」,以正常的背景照片比對出異常,可找出大量並框出「不同處」 ,並回傳警報,已可達到巡檢發現異狀,回傳影像供遠端判斷的功能,但無法辨識「異常」是何種「異常物件」 ,尚需人力註解後再批次訓練新模型。→表2的第1項精細地比對出與前一日的不同,多個閥件上的某一個On/Off名牌掉落,若人員未仔細巡檢是不易看到的。
事件辨識成效
事件辨識選擇的二項能力測試,一為「人員站立A字梯梯頂」→圖15、另一為「施工圍籬內未著防護衣」→圖16。此二項的辨識率約在65~70%,意即約有30%會漏判,原因在部份拍攝角度A字梯的特徵不明顯、未能拍到人體腳的特徵,必需增加多重角度的訓練照片,重新訓練模型。
圖15、事件辨識:人員站立A字梯梯頂
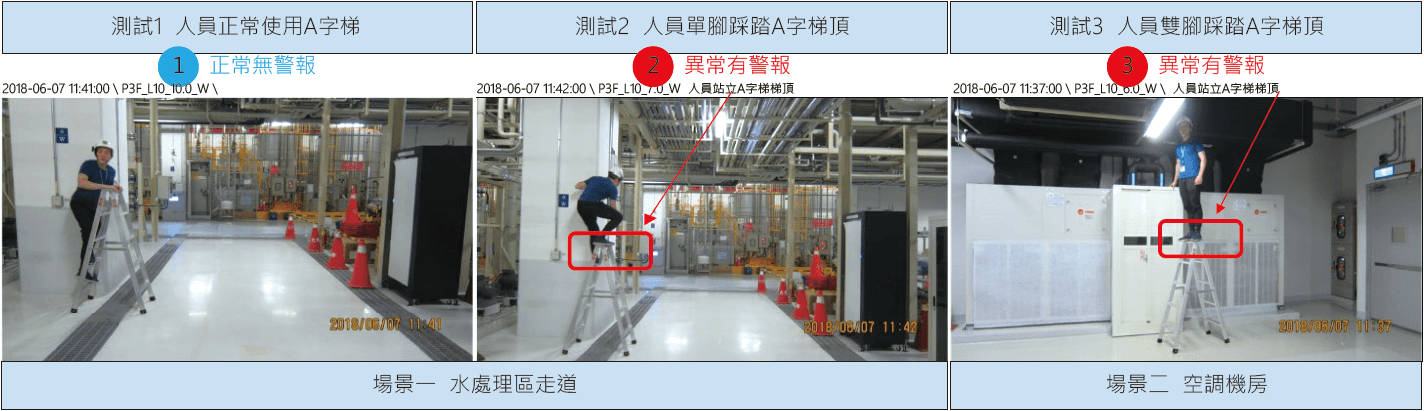
圖16、事件辨識:施工圍籬內未著防護衣
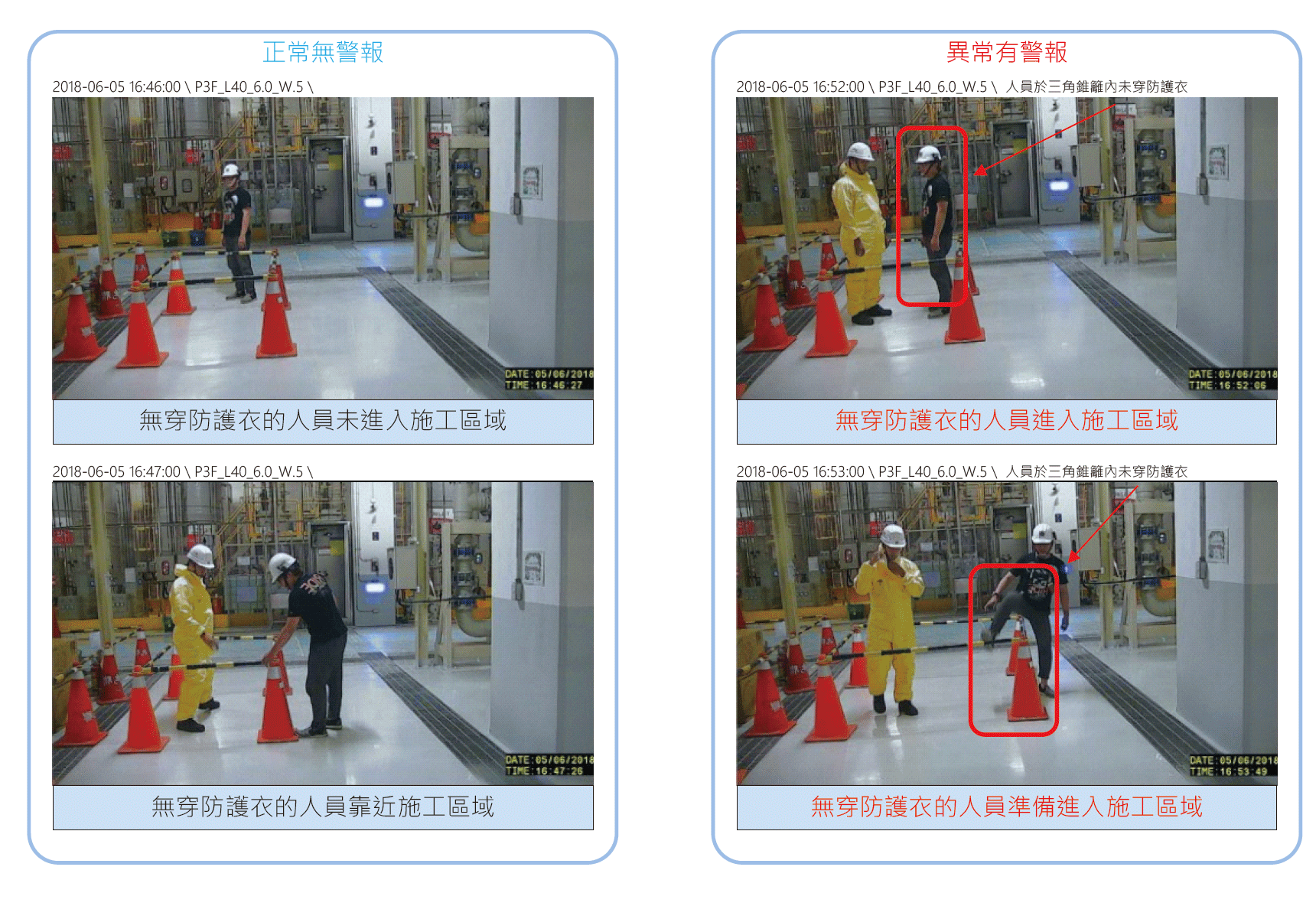
AGV 與工程師協同作業的討論
AGV在能擔任例行性巡檢工作後,可在下列方式相互協同,提高巡檢的有效性,成為系統工程師的最佳助手:
AGV每天多次巡檢,列出異常處理清單
巡檢次數多於原有人力巡檢1~2次,增加為8~10次,監控的死角時間變短,可由巡檢系系統列出異常清單,再由系統工程師決定處理的優先順序,有系統、有輕重緩急地處理異常。
分擔工程定點監工與不定期巡查
高風險作業的定點、多項檢查作業、過程中可能的安全疏漏,可由AGV或CCTV搭配巡檢系統的影像、聲音功能,輔助甚或代替人員在現場的監工。也可搭配工程管理系統,排定不定期、不定路線的工程巡查,提供工安巡視的密度,就像高速公路上的定點測速與巡邏中不定點測速,對有僥倖心理的違規者,形成一個由點而線而面的遏阻的作用,減少違規、工安的意外。
AGV搭配工程師一起例行巡檢
在已減輕工程師對一般性異常的負擔,工程師可著重於AGV巡不到的死角視線、專業上需由工程師判斷的異常、還可搭配錄影、照像、錄音功能,將異常作更完整、即時的記錄,提高處理、解決問題的效率。
結論與建議
本研究實證巡檢AGV,能結合自動導引與AI中的影像辨識兩項技術,主動到現場搜集資訊,可排除人員的不可靠因素,取代約62%的巡檢項目,可讓工程師巡檢集中心力在必需多重技能與專業判別的工作上,除了可自動獨立巡檢外,也可成為工程師巡檢時的好助手,主動收集不易注意的系統細節。管理上,則可藉自動化巡檢,由後台的SCADA有系統的收集異常、次數、類別,協助廠務在系統、工程、變更管理各項制度如實、如預期的穩定供應。
未來發展藍圖的進展,決定於物件辨識的數量與辨識率的提昇速度,「數據量愈大,演算法就愈精準」,即使是中等水準的演算法,只要數據量夠多,也能比頂級但相對較少數據作出的演算法精準[8]。本文所提出二種演算法流程,先行「大量」收集各類的「異常」,做為辨識的訓練資料,可彌補演算法與硬體的不足。要依藍圖的進展,在相片不能外傳的情況下,尚需有能熟悉影像辨識演算法的AI工程師調校模型,並建構出符合影像辨識的軟體環境與硬體設施,同時需有廠務暸解AI技術上的限制與各類演算法應用範疇的工程師,能暸解廠務的需求與問題,作為廠務的專業與影像辨識技術之間的橋樑。短期不易有同時具備兩種專業的工程師,建議可由公司指派IT具AI專業的工程師,或藉外部專家,專職協助廠務建立環境與人才。
AI的影像辨識與AGV的自主導航技術,是兩項發展中技術應用於廠務巡檢的新領域,最具挑戰的是如何整合兩種不同技術的專家,結合廠務的專業,成為一套可執行、快速收集異常、友善地提供資訊予運轉管理所需。從AGV與攝影機的控制、相片資料與影像辨識的資料交換、SCADA監控的規劃到軟硬體規格的訂定,是本研究隱而不顯 ,卻會影響未來此系統的順利運行,能提供「友善的使用者經驗」,加速推廣巡檢AGV的應用,成為廠務主動管理的重要一環。
參考文獻
- 董事長談話,公司願景、核心價值與經營理念,2018。
- 以資訊化巡查點檢系統應用於石化廠工安管理,2006,高苑學報。
- BostonDynamics:https://www.bostondynamics.com/spot,2016。
- 李祥、崔昊杨、曾俊冬、江超、唐忠,變電站智能機器人及其研究展望,上海電力學院學報,33卷1期,2017。
- Alex Krizhevsky, Ilya Sutskever, Geoffrey E. Hinton, ImageNet Classification with Deep Convolutional Neural Network,Advances in neural information processing systems,2012. https://medium.com/academic-origami/imagenet-classification-with-deep-convo-lutional-neural-networks-da7cea972cb7
- Joseph Redmon, Santosh Divvala, Ross Girshick, Ali Farhadi; The IEEE Conference on Computer Vision and Pattern Recognition (CVPR), 2016, pp. 779-788Bazant, Z.P., and Oh, B.H., "Strain-rate effect in rapid triaxial loading of concrete," Journal of Engineering Mechanics, ASCE, Vol. 108, No. 5, pp. 764–782 , 1982. https://pjred-die.com/darknet/yolo/
- 余宗賢、張書豪、談巡檢機器人於廠務運轉之應用,廠務季刊29期, 2018。
- 李開復,AI 新世界,Page 43,天下文化,2018。
留言(0)