摘要
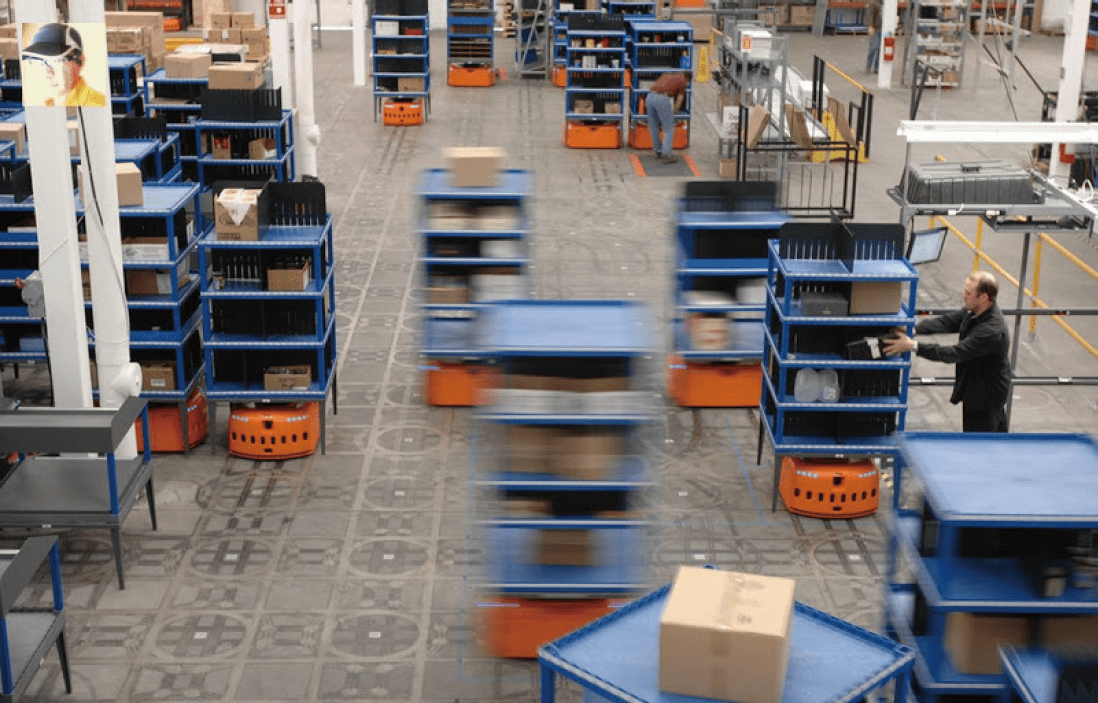
以自動化科技落實全面品質管理
Keywords / Total Quality Management2,Automation5,Robot4,AMC7,AGV
前言
我們處在一個嶄新的工業革命之中,技術的提昇之外 ,也伴隨著管理手法的創新改進,兩者相輔相成,激發出半導體製造的巨大潛力。自1960年代起,日本發展出以品質為中心的「全面品質管理」(TQM)方法,來提昇製程品質及優化企業經營。所謂全面品質管理,是指必須在生產單位中所有的人事物上,進行持續不斷改善的理念,建立零缺點(Zero Defect)的作業方式。尤其全球車用半導體的市場逐漸增加,主訴避免交通事故,配有智能導航駕駛系統、車輛事故救難系統、主動碰撞閃避與自動煞車等等協助工具的自動駕駛車輛在競爭中脫穎而出。車用晶片如何不致發生功能障礙或錯誤,導致危害人員生命的嚴重後果 ,已是車用晶片半導體製造所需面臨的重要課題。台積電身為半導體龍頭,生產大量車用晶片,必需重視各種車用晶片的可靠度。工廠的使命是生產零缺失的晶片,對廠務而言要提供工廠最佳的生產環境以及化學品供應品質。
基於全面品質管理對於生產製造上的強烈需求,製造業生產過程中使用的機器人技術,在近幾年各項感測元件日益成熟、電腦視覺及人工智慧大幅進展的條件搭配下,已能夠提供產業,在實務上具有自主移動能力、進行環境感測辨識、邏輯判斷與模仿動作的成熟機器人設備,來協助或取代以往的人工作業,應用重負荷高風險的勞務工作 、生產環境的品質與安全與巡檢。以巡檢工作為例,傳統以人力進行巡檢,現場抄錄的數據無法即時回傳系統,人力無法攜帶大量儀器進行同時採測,並有可能發生抄錄繕寫的錯誤或遺漏巡檢事項;巡檢機器配備的感測設備,能察覺任何微小的溫度升遷,濃度變化或噪音音頻變異,可當下回傳大量數據至廠務監控平台進行運算分析,查測並判斷設備運轉的問題,能積極提升良率改善產能。巡檢機器人在執行工作的頻率、風險安全性、確實完成度上,作業時程上都有較人工巡檢有更大的優勢,並可將高風險區域對於巡檢人員的工安風險降至最低。
本文以智能廠務管理課所建構的無塵室環境量測機器人、廠務巡檢機器人與自動搬酸機器人為例,針對監測無塵室環境品質、改善巡檢工作安全品質與提升高風險作業品質等面向,藉由各別機器人雛形的構建過程,說明該解決方案發展的核心,以及各專案在廠區內的應用迄今,從中歸納出的經驗與心得。探討廠務智能機器人與自動化機器人的侷限性與可行性,並包含機器人目前在廠區應用,所面臨的問題與挑戰。俾使同仁在爾後類似的工作情境中 ,能有所參考或借鏡,繼續注入新的技術力量,將廠務智能機器人的應用,推展至更寬闊的領域,解決新的問題。
文獻探討
2.1.自動化科技的趨勢
現代社會普遍出現人口結構老化、勞動力短缺的問題 。以機器人取代人工,已成為全球產業發展必然趨勢,也促成智能機器人相關產業的蓬勃成長。機器人的應用,走進社會各個領域,在工業生產以外的機器人,比如前述的亞馬遜的倉儲物流機器人,全球部屬超過10萬台,讓物流中心的運作效率更上一層樓。而倉儲物流機器人的應用,更從簡單的無人運輸功能,演進成包裹分揀機器人,能將當前系統的包裹分揀錯誤率大幅降低50%,大幅提升亞馬遜的企業競爭力。當前另一個多元化的機器人發展,即是巡檢機器人的普及應用。當機器人具備對環境的感測、辨識能力,並能自行決定行動時,便可漸漸取代人力進行廠務巡檢工作。配備音頻視訊監控設備及同步定位與地圖構建(Simultaneous Localization And Mapping, SLAM[1])技術的定位功能,巡檢機器人可在白天和黑夜,為遠端中控系統提供即時的現場情況,即便是光線不足,也可以利用紅外線成像,進行遠距離的識別。而電池科技日趨成熟,巡檢機器人亦可長時間續航,相較人力,有更長更彈性的工作時間。在安全性、環境感測、資訊紀錄及作業工時上 ,具有人力所不及的優勢,越來越多的巡檢機器人被應用到企業與工廠的運轉之中。機器人可以二十四小時不間斷工作,替代人工在複雜、危險環境下執行巡檢。
2.2.自動導引車的發展與應用
自動導引車(Automated Guided Vehicle, AGV)是一種輪式移動機器人,沿著地板上的導線或標記塊或磁條運動 ,或者通過視覺導航或雷射導航,多用於工業生產,在車間、倉庫運輸貨物[2]。如→圖1所示為亞馬遜(Amazon)公司以AGV協助貨物分類、搬運狀況,透過AGV的協助可以大量減少人力需求並提升搬運效率,避免人員出錯,提升物流品質。
圖1、亞馬遜物流中心以AGV協助貨物搬運
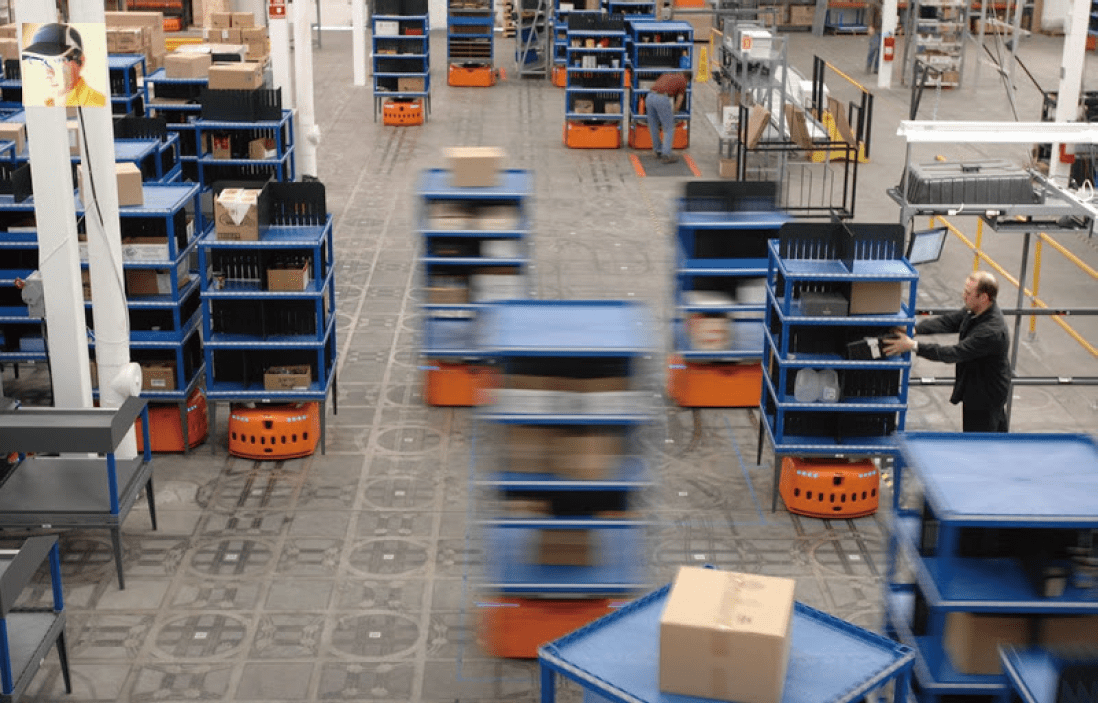
雖然AGV一開始開發的主要能力是搬運,但是因應各式領域不同的需求,以AGV為主體搭載各式感測器,開發出不同功能應用的機器人已經是一種趨勢。例如在保全巡邏上,搭載高解析度鏡頭,遇到犯罪行為,透過無線傳輸技術將影像即時回傳中控室,保全人員可以透過麥克風與現場對話, 讓保全人員不需直接面對歹徒,透過即時錄影可提供警方作為破案線索和法律證據。如→圖2所示為矽谷新創公司Knightscope所開發的保全巡邏機器人。
圖2、矽谷新創公司 Knightscope保全巡邏機器人[3]
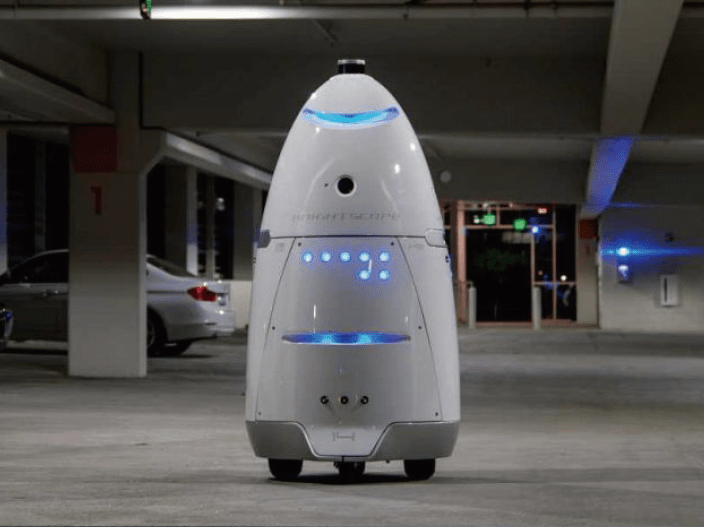
另外,針對極端惡劣氣候與廣大面積之戶外變電站巡檢所開發出的電力巡檢機器人→圖3,在大陸也已經廣泛被應用。搭載紅外線攝影機與可見光攝影機,可以針對電力設備做紅外線溫度檢測,也可以針對表頭數值與開關狀態做影像判讀,免除了人員在酷熱、酷寒環境巡檢對人體傷害的風險,透過可充電電池的續行效果,提升了巡檢的效率,確保每日對電力設備要求的巡檢品質。
圖3、山東魯能智能公司電力巡檢機器人[4]
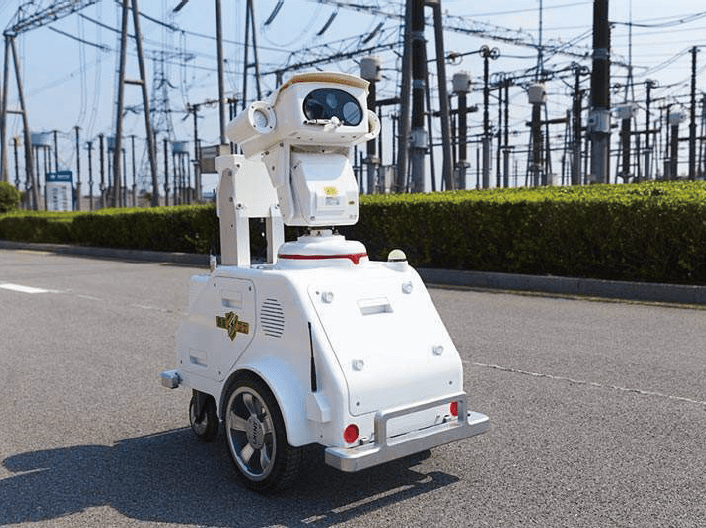
廠務機器人開發→表1
AMC巡檢機器人 | 廠務巡檢機器人 | 自動搬酸機器人 | |
---|---|---|---|
問題 | • 無塵室sensor密度不足,需靠人力巡檢補足 • 人工巡檢花費時間太高,且無法滿足資料即時更新 | • 廠務系統巡檢品質沒有標準化 • 巡檢結果無法即時回傳 | 廠務人員每日需花費大量勞力搬運化學品 |
目的 | 提升無塵室環境監測品質 | 提升廠務系統管理品質 | 提升原物料搬運品質 |
作法 | • AGV搭載AMC分析儀器自動化巡檢 • 透過無線傳輸即時回傳,結果即時呈現 | • AGV搭載感知器自動化巡檢 • 透過無線傳輸即時回傳,結果即時呈現 | AGV搭載搬運台車,協助將化學桶搬運至化學房 |
有鑑於機器人技術發展的日新月異,廠務從2017年開始發展廠務機器人系統,主要目的除了取代高風險、高勞務人力外,希望能夠藉由24小時運作的機器人系統,提升廠務以往透過人力無法做到長時工作需求,提升整體運轉品質。2017年開始針對巡檢、無塵室環境量測、化學桶搬運等三個需求,發展整合攝影機與各種感測器做巡檢與量測的AGV應用,以及可以搬運1.5噸化學桶的AGV應用。
3.1.AMC巡檢機器人的開發
2017年開始無塵室的自動巡檢量測開發,是將AMC分析儀器裝在一台推車上,並使用人力作為動力來源,在無塵室內巡檢,且透過3G簡訊(SMS)將儀器資料回傳。後來發展到使用AGV作為動力來源→圖4,並建立無塵室內行走圖資,配合SMS傳輸方式作資料回傳,發展到最後由4G網路取代SMS傳輸方式,就正式邁入廠務自動化巡檢的第一步。
圖4、AGV結合量測推車自動巡檢
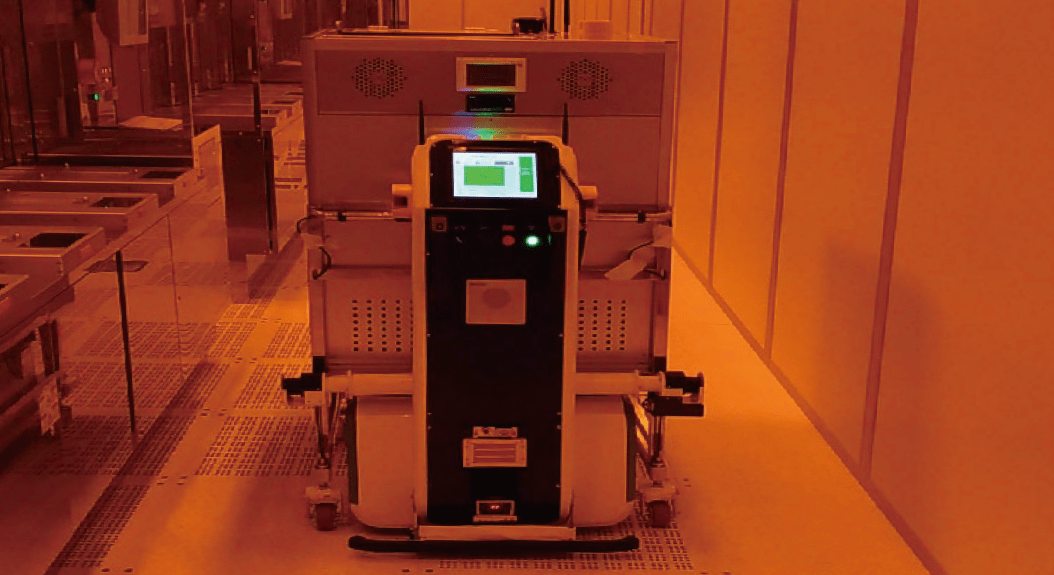
目前已規劃F14P34 AGV主走道(Inter Bay)巡檢動線,分成A、B兩個主走道動線→圖5,並後續規畫生產走道(Intra Bay)巡檢動線→圖6。AGV在巡檢過程中將AMC分析儀器資料回傳,彌補Inline分析儀器量測點位分布不足的問題,當發生異常時能夠在最短時間內找出異常原因。
圖5、AGV主走道巡檢動線
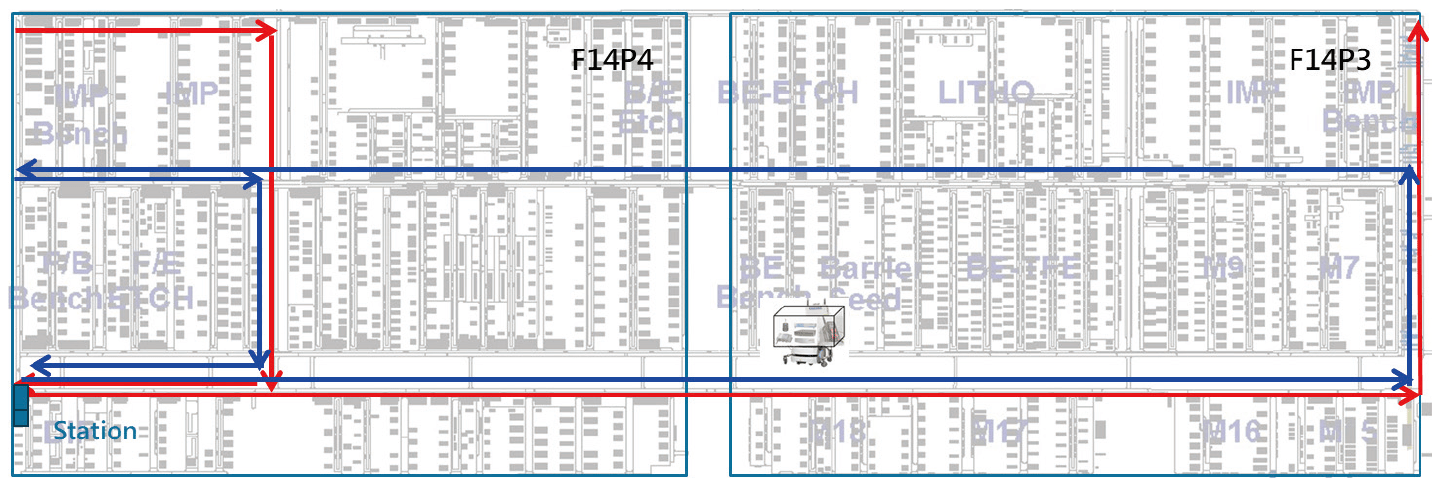
圖6、AGV生產走道巡檢動線(Intra Bay)
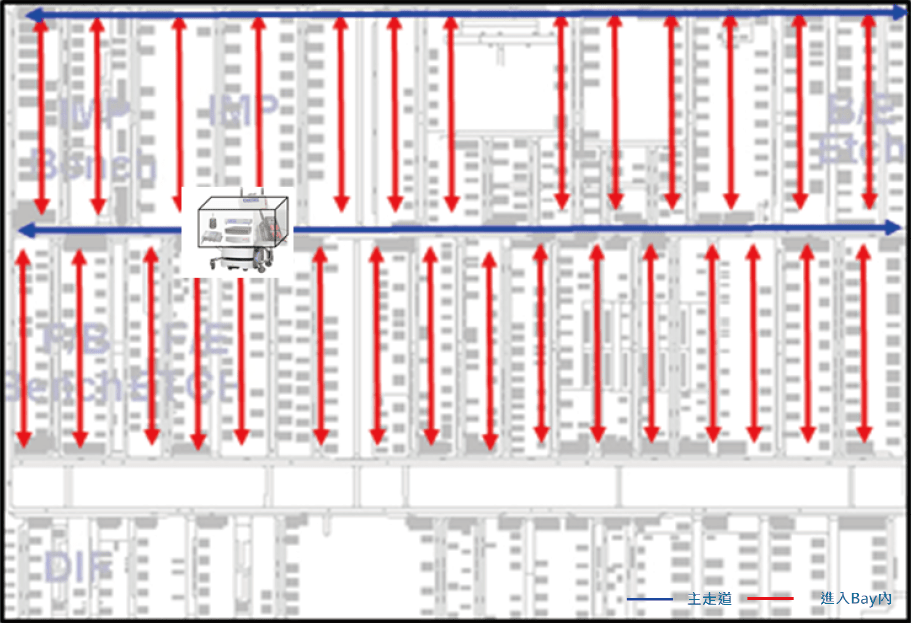
如何讓AMC巡檢機器人在巡檢過程中,將分析儀器資料即時回傳至廠務值班室,確保無塵室環境供應品質?因此 ,我們設計了台積電特有的AMC自動巡檢架構,透過中華電信4G網路回傳AMC分析儀器量測資料,結合AMC濃度分布圖呈現,達到無塵室環境品質即時監控的功能→圖7。
圖7、AMC巡檢AGV通訊架構規劃
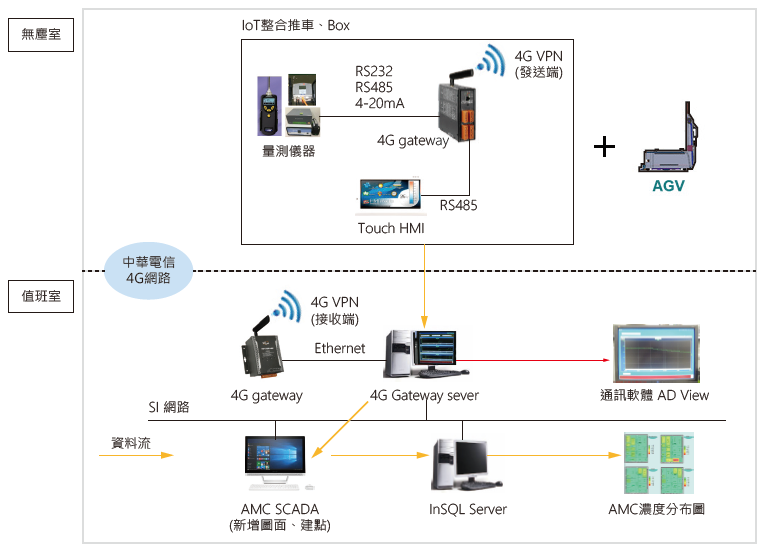
3.2.廠務巡檢機器人的開發
在廠務區的自動巡檢機器人規劃是以無軌導引AGV為主體,透過前後各一顆的二維光達雷射(LiDAR)掃描出環境地圖特徵→圖8,再建立機器人要巡視(量測、拍照)的巡檢點,達到自主行走的功能。目前的規劃在F14P7 B2六條走道每10公尺建立一個巡檢點,一條走道設定20個巡檢點,總共120個巡檢點,在約200公尺x200公尺的B2區可完整走完主要、次要走道,並對特殊的定點作加強巡查,覆蓋全區所需巡視的區域。
圖8、F14P7 LB2 SLAM地圖
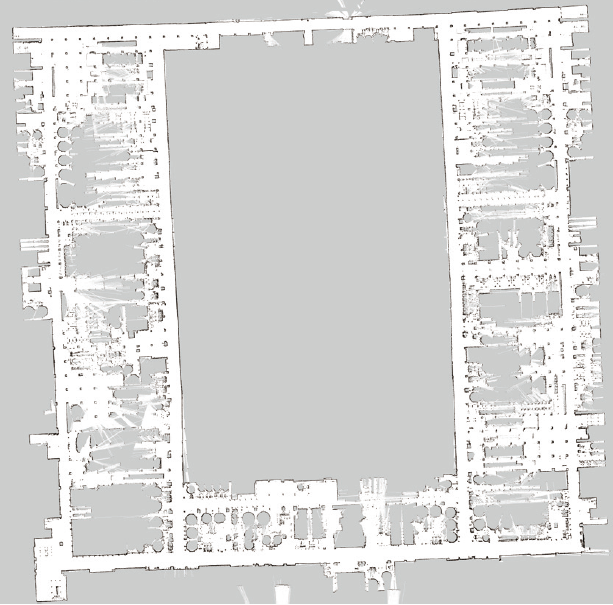
機器人自主定位則利用了機器人學中的LiDAR SLAM ,在巡檢時藉由分析LiDAR回傳的機器人周圍二維環境平面特徵資訊後,再與建立好的地圖資訊比對,找出機器人在地圖中的位置來做即時定位,並導入最佳路徑導航來做巡檢點與點間規劃,若是路徑中有障礙物時,機器人則會重新計算路徑來閃避障礙物,即時找出地圖中新版最佳路徑。
巡檢機器人本體配備無線網路通訊,將機器人的狀態 、現場臨時狀況及巡檢的結果透過無線方式傳輸。機器人的派車系統(Local Server)藉由無線網路與機器人做控制與資料交換,這些相關的資料再藉由廠內現有的廠務區SI網路層,由派車系統傳輸回CUP值班台的監控電腦,值班人員在值班台就可以掌控機器人的所有相關資訊,若是有現場環境的安全與工安問題也可以即時掌控,整體架構圖→圖9。
圖9、廠務巡檢機器人架構圖
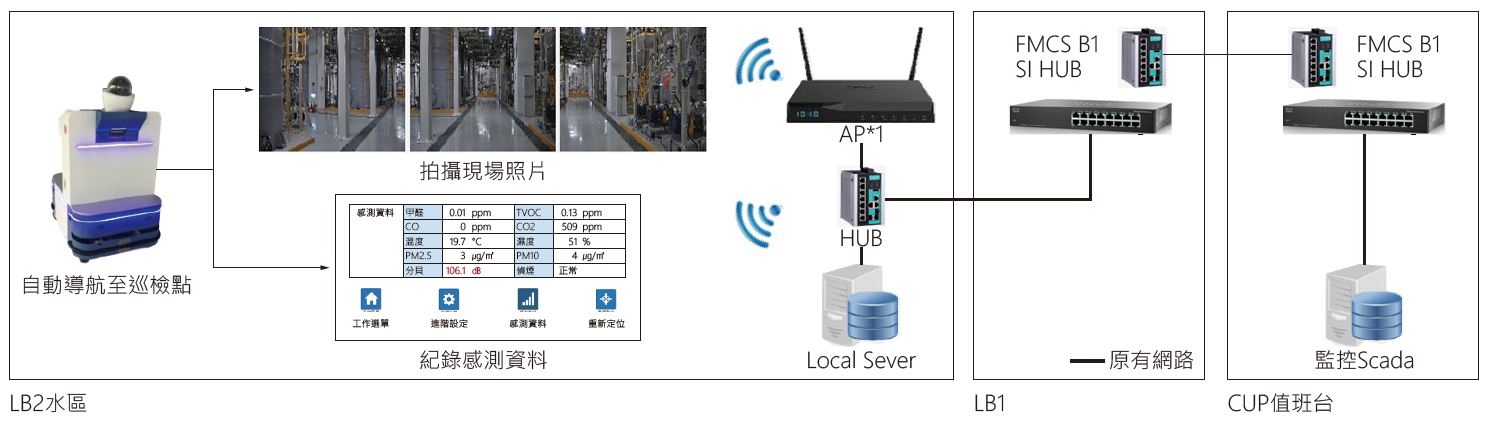
廠務巡檢機器人除前述行走能力外,為了能更貼近人員巡檢時所具備的能力,在機器人上搭載了各式感測器來模擬人的四感:視覺、聽覺、嗅覺與觸覺→圖10,並就四個主要面向來開發以提升巡檢品質,分別是6S管理、系統狀態、施工管理與人員安全→圖11。下面就感知能力來分別說明這些項目。而機器人在巡檢時也會記錄下現場環境與設備的運轉狀態,並自動判別巡檢結果即時通知值班人員 。值班人員也可透過監控畫面,指定機器人至異常發生區域確認狀況,協助值班人員第一時間判斷現場危害。
圖10、巡檢機器人上的擬人化感知能力

圖11、廠務巡檢機器人功能規劃
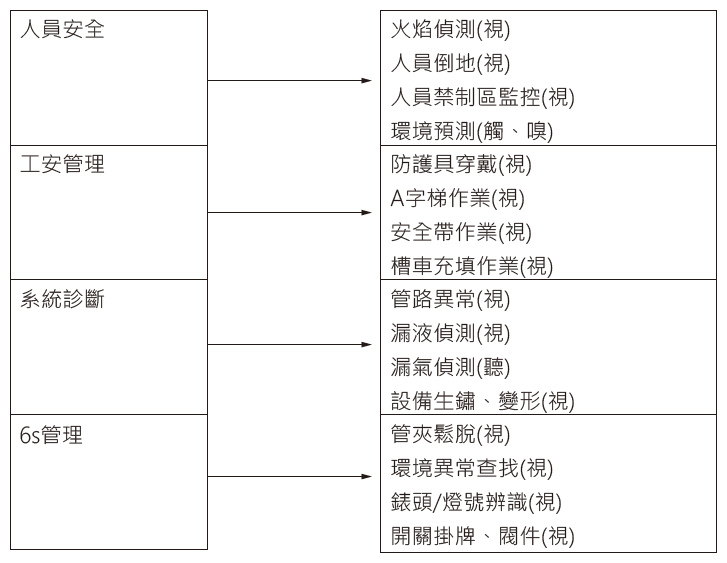
視覺:
在機器人上整合PTZ camera,模擬人員巡檢時眼睛的可視範圍,並導入機器學習中視覺部分的深度學習Deep learning,來建立機器人的視覺能力。待建立起正常環境的golden picture後,此時若有環境異常的相片進來即可比對出環境中異常部分;再訓練出機器人對物件的辨識能力,進一步辨識出環境異常部分是什麼物件,並判斷物件異常的狀態通知值班人員。如6S管理中:錶頭/燈號辨識、開關掛牌、閥件狀態、燈管不亮、管夾鬆脫;系統狀態中 :設備生鏽/破損、管路異常變形、漏液偵測;在人員安全部分自動判斷人員倒地。如施工管理中:人員站立A字梯梯頂、在施工圍籬內未著防護衣等工安違規事件。
聽覺:
整合聲音照相機與分貝計,藉由聲音照相機拍攝聲音照片並錄下設備不同音頻的聲音與噪音值,模擬人員巡檢時耳朵聽到的異常設備(環境)聲音,後續將透過機械學習中的數據挖掘Data mining,開發出機器人的聽覺能力。讓機器人可藉由聲音辨識出是哪個特定設備(環境)的聲音,並更進一步分析出此設備機台的表現現在有無異常。如系統狀態中:漏氣檢測及設備異音辨識。
嗅覺與觸覺:
整合了多合一氣體偵測器及煙霧偵測器,可偵測多種項目包括溫度、濕度、二氧化碳、一氧化碳、PM10、 PM2.5、有機氣體TVOC、甲醛、及火警煙霧。大幅強化了人員巡檢時嗅覺與觸覺可感知的項目。後續收集長期環境資訊後,規劃開發Data mining技術,在人員安全中預測出環境安全品質,可及早發現環境惡化的趨勢,避免人員財產因環境異常造成損害,建立出廠務人員安全又舒適的工作環境。
3.3.自動搬酸機器人的開發
化學品本身具有危害的特性,因此,廠務化學品的搬運與換酸,常常被視為一種具有潛在風險的作業,為提升廠務化學品供應的穩定與人員作業的安全,我們開始評估透過AGV自動搬運的方式,協助廠務每日的化學品搬運。
自動化搬酸的作業流程從廠商入料到廠務換酸共有六個步驟,分別為 : ①廠商入料 ②庫房收貨 ③庫房入庫 ④庫房發料(廠務領料) ⑤廠務搬運(酸) ⑥換酸。從這六個步驟去規劃自動化搬酸系統,達到從廠商入料到搬運至化學房「一條龍自動搬運」流程→圖12。
圖12、一條龍自動搬酸
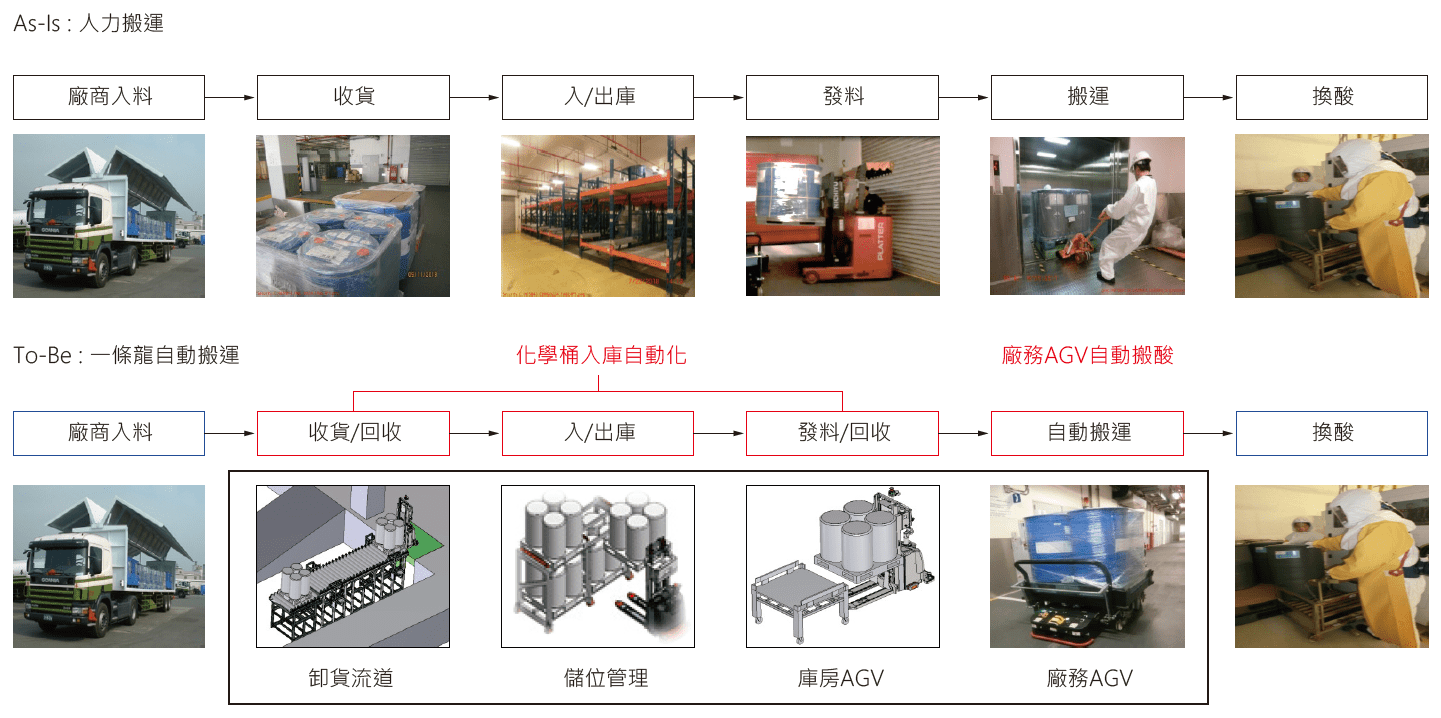
首先在碼頭區規劃新增一個卸貨流道,原物料廠商送貨時,直接將棧板放上卸貨流道,自動掃描條碼(Barcode) ,並經過庫房自助系統電腦確認無誤後,由庫房AGV自動搬運入庫儲存。當廠務有領料需求時,僅需遠端透過PDA觸發自動領料指令,庫房AGV會自動將物料棧板運出庫並放置於轉接區,待廠務AGV來轉接區將物料棧板搬運至2樓。反之,當有空桶回收的需求時,僅需透過PDA觸發空桶回收指令,廠務AGV會將空桶搬運至轉接區,待庫房AGV來轉接區將空桶搬運入庫,並等待廠商進廠運回。完整作業流程→圖13,其中紅線為廠務AGV負責範圍;藍線為庫房AGV負責範圍。
圖13、廠務與庫房自動搬酸示意圖
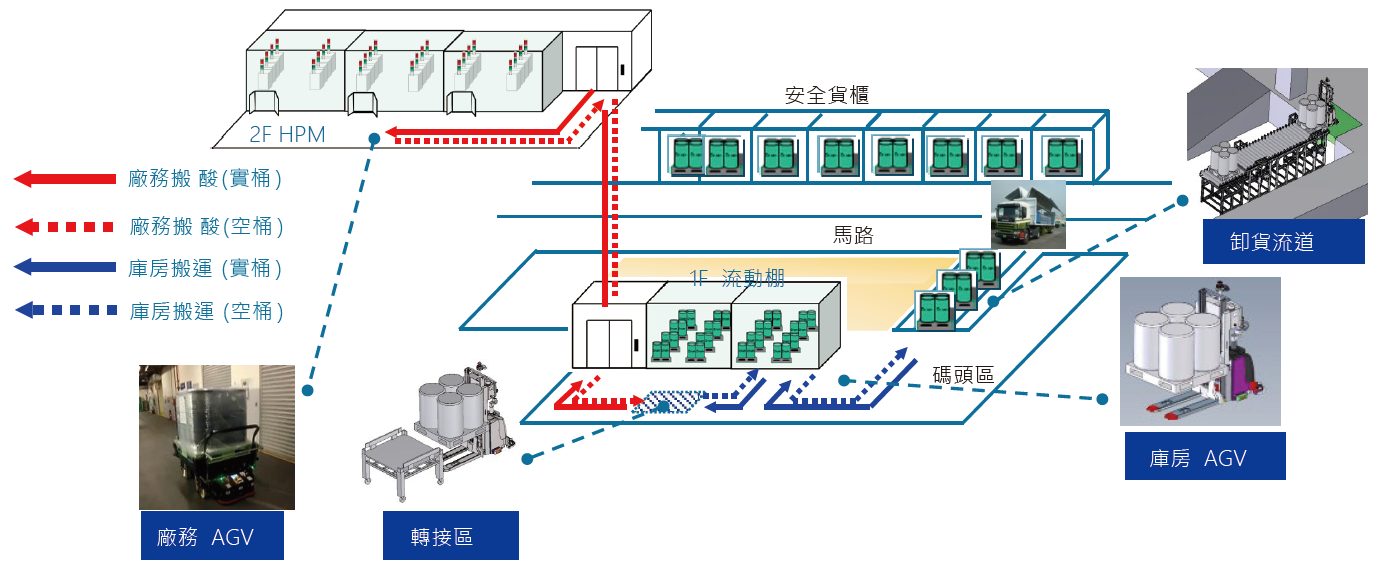
結果與分析
4.1.AMC巡檢機器人
目前共開發了8種量測儀器的整合(溫溼度計、TOC、 Particle Counter、Picarro、Mitap、TS、NH3、EMI),回傳至廠務值班室4G VPN的接收端,資料再透過乙太網路傳入廠務系統資料庫,供廠務工程師透過SI的Trend Chart系統查詢資料,並同時以濃度分布圖呈現無塵室全區的AMC濃度分布狀態。
無塵室AMC巡檢機器人,是廠務第一台自動巡檢機器人,主要是針對無塵室內環境狀況及廠務供應的品質的確保,配合緊急應變,並作及時回報,未來計畫在現行架構上,持續開發其他功能,如故障照明自動巡檢、無塵室環境EMI自動量測等,提供工廠更好的無塵室生產環境品質 ,同時在無塵室環境發生異常時,能透過AGV派車系統,在第一時間內,即到現場提供環境品質的監測,作為指揮官下達指令的參考依據。
4.2.廠務巡檢機器人
目前AGV與四感的感官元件已整合完成,做現場資料收集與回報→圖14,並在F14P7 B2水區每日巡檢4次,1次巡檢共120個巡檢點約65分鐘。巡檢結果可從「巡檢機器人UI介面」進入查詢→圖15,提升工程師對廠務區的系統與環境管理。
圖14、機器人上量測的感測項目
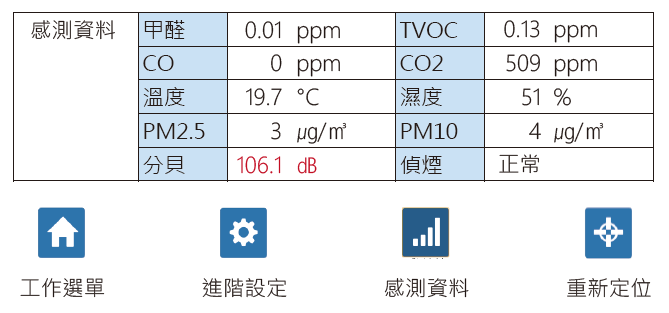
圖15、巡檢機器人的UI介面
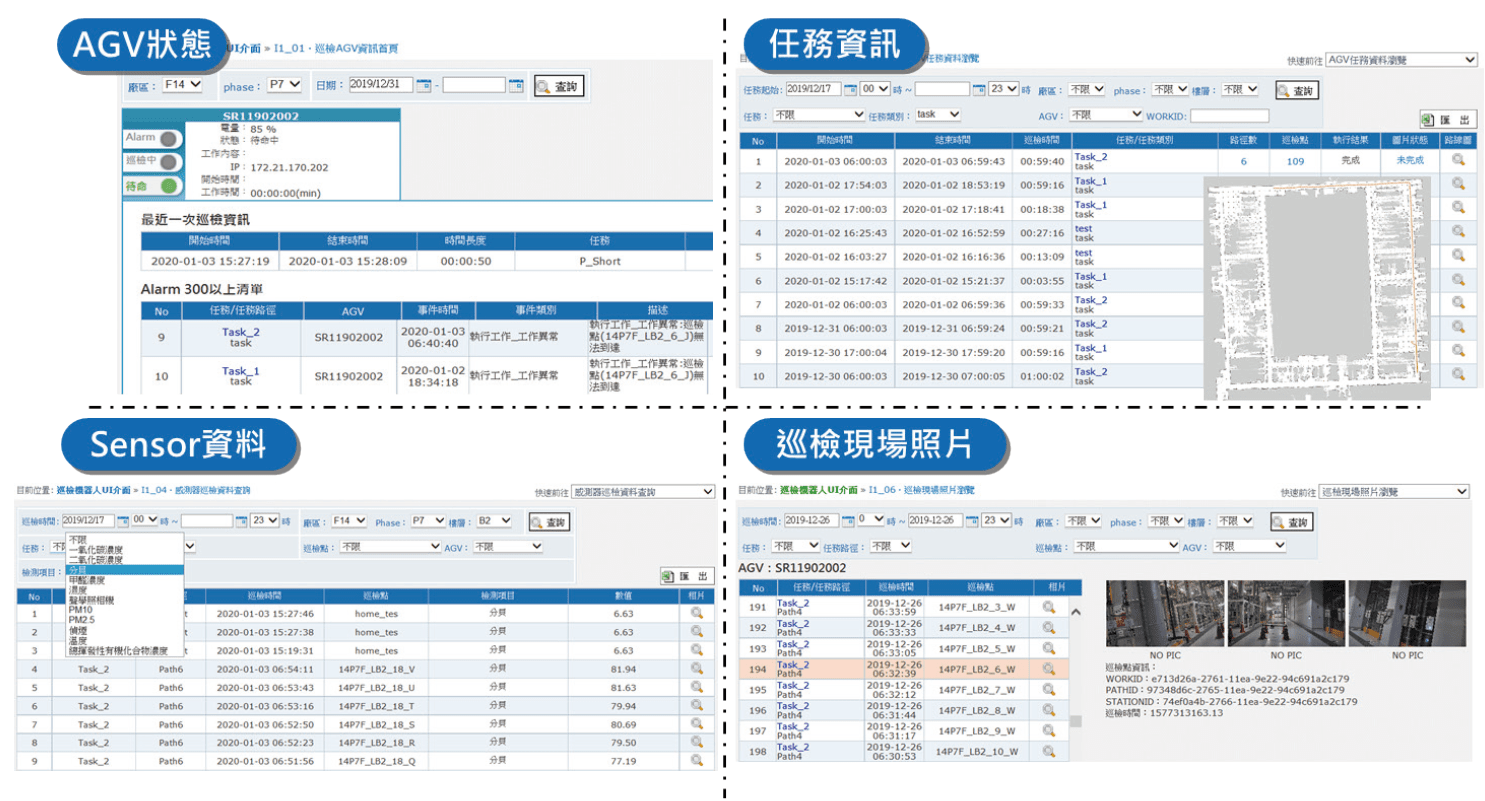
在「巡檢AGV資訊首頁」內可查詢機器人目前的狀態 、工作任務、最近一次巡檢資訊、即時警報及環境值超標訊息;在「AGV任務資料瀏覽」內可查詢機器人歷史任務資料:包含巡檢點數、任務路徑及每次任務路徑圖的檢視 ;在「AGV event(alarm)歷史資料查詢」內可查詢機器人歷史警報資訊,並模仿TSMC廠務系統警報等級機制,將警報依緊急程度分為100、200、300、400,使廠務人員可更清楚分辨機器人警報程度,且加入警報該如何應對處理的對策(action)項,讓不熟悉的使用者使用起來也會清楚該如何緊急應變。
在「感測器巡檢資料查詢」內可查詢上一小節提到的偵測項目,並可對整體環境或是特定區域環境做查詢,並可依照時間畫出trend chart,能更清楚掌握並監控環境值的上升下降趨勢;在「感測器Baseline設定」可訂定整體環境或是特定區域環境的基準值,當偵測數值一旦超過基準值,便會發出警報通知使用人員環境異常;在「巡檢現場照片瀏覽」可查詢機器人在設定巡檢點所拍攝的現場照片,讓使用者可藉由現場照片清楚了解現場狀況,逐步自動化廠務的現場巡檢。
4.3.自動搬酸機器人
庫房搬酸AGV已完成設計並發包建置中,廠務搬酸AGV已完成Pilot Run,每日最大搬運量可達到40個棧板,符合日常運轉需求。而自動搬酸機器人於導入的過程中也遇到了一些困難與挑戰,在解決問題的過程,也得到了許多寶貴的經驗,在未來推廣到各廠區時可做為借鏡。
問題一 : AGV的載重規格為1,500Kg,當搬運較重的H3PO4或M2時,遇到不平整或有斜坡的路面,AGV輪胎會有受力不均或爬坡爬不上的現象,探究其原因為台車的強度有過度設計的疑慮,因為初期台車為了能一次順利通過國震中心的地震搖晃測試,不斷強化台車的結構,導致台車重量重達到220Kg,加上4桶H3PO4(315Kg*4=1,260 Kg)與棧板重量,已經幾乎達到AGV載重能力1,500Kg的上限了。未來解決之道是提高AGV載重能力。
問題二 : AGV的磁條與定位卡容易遭受堆高機等重物的輾壓而破壞、雖然已經有使用加厚型的強固膠帶保護,損壞率仍然太高,解決的方法是將磁條與定位卡埋入Epoxy下。
最後,把未來廠務的新廠與既有廠的自動化搬酸做個總結 : 既有廠區可導入一條龍自動搬酸(AGV自動入庫與搬酸),新廠區則可採用ASRS。自動換酸機構則持續開發中 ,未來有機會可達到一條龍全自動搬酸與換酸→圖16。當這些自動化目標達成時,人員不再需要去接觸這些高風險作業,不管是安全上、品質上都更加有保障,除降低廠務運轉成本,並提供廠務穩定的化學品供應品質。
圖16、一條龍自動搬酸與換酸
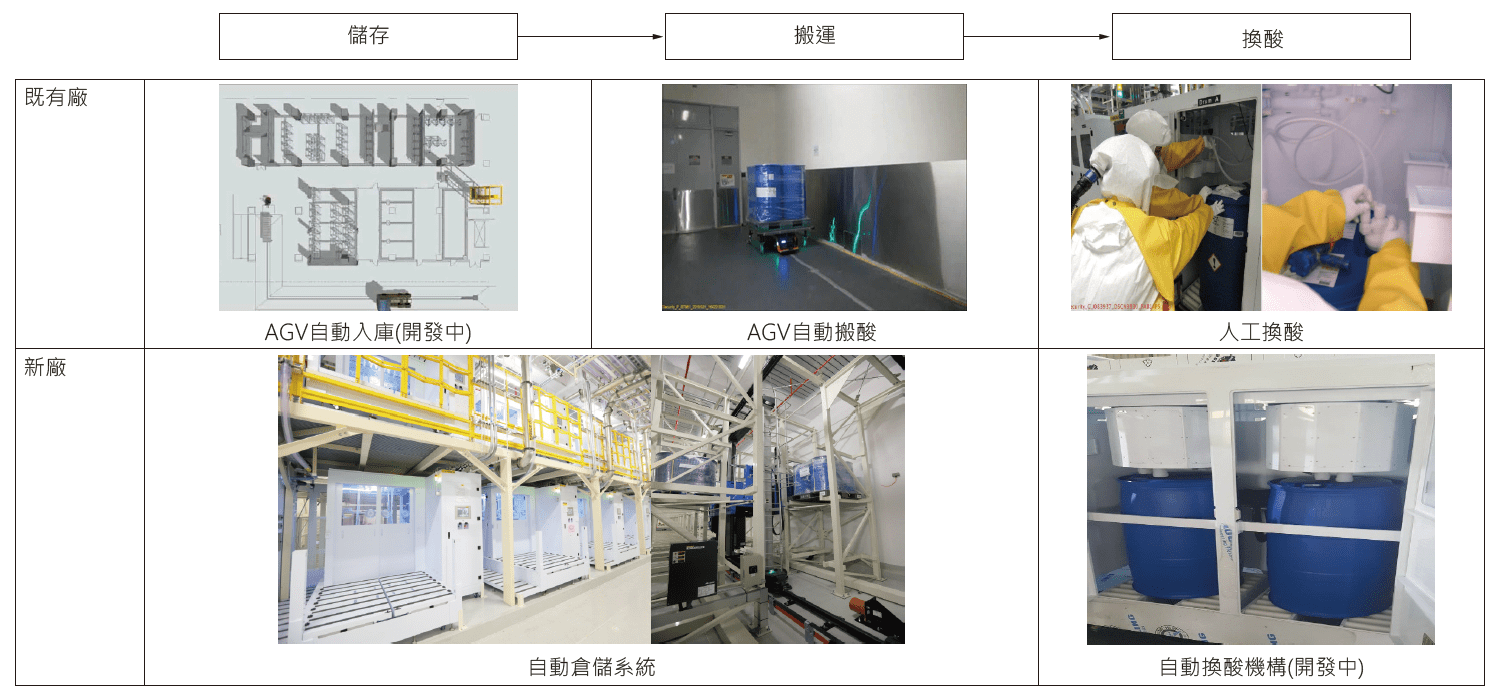
結論 Conclusion
無塵室的環境品質會影響晶片的良率,所以對於無塵室環境的品質,我們必須以最準確、最及時的方式去監控 ,而原有的巡檢方式,除了Inline的AMC量測點不足以外 ,人力巡檢也會有人力不足與標準不一的缺點,因此我們開發了AMC巡檢機器人,只需將量測儀器整合到推車內, AGV便會依照指定的路線執行巡檢的動作,解決人力與量測點不足的問題,同時也達到巡檢標準化的目標,這就是落實巡檢品質管理的具體作為。而且,未來若要新增量測項目,只需再把量測儀器新增到推車內,便可自動執行巡檢並且把巡檢資料回傳。
同樣的方式也可以應用在非無塵室的區域,把廠務巡檢變得自動化、標準化,大大提升巡檢的品質,甚至功能上更整合了視覺、聽覺、嗅覺與觸覺的擬人化感知能力,及時自動判別巡檢結果,並回傳到廠務巡檢管理系統上,若有異常,也可即時回報給相關人員,達到早期預防的效果,落實品質管理的目標。
除了無塵室的環境品質量測與非無塵室的廠務自動巡檢外,化學品的搬運也是一項高風險、高勞力的作業,其自動化的需求也是勢在必行。在一條龍自動搬酸的規畫之下,未來化學品可以自動入庫、自動開立領料單、自動掃barcode或RFID、自動發料、自動搬酸,達到zero MO的目標,如此一來,不僅節省了人力,也降低化學品搬運的風險、提高作業安全,避免領錯、換錯料,提供了穩定的生產環境與化學品供應品質。
參考文獻
- https://zh.wikipedia.org/wiki/即時定位與地圖構建
- https://zh.wikipedia.org/wiki/%E8%87%AA%E5%8A%A8%E5 %AF%BC%E5%BC%95%E8%BD%A6
- http://technews.tw/2016/07/08/k5-uber-preservation/
- http://www.sohu.com/a/246380926_20918
留言(0)