摘要
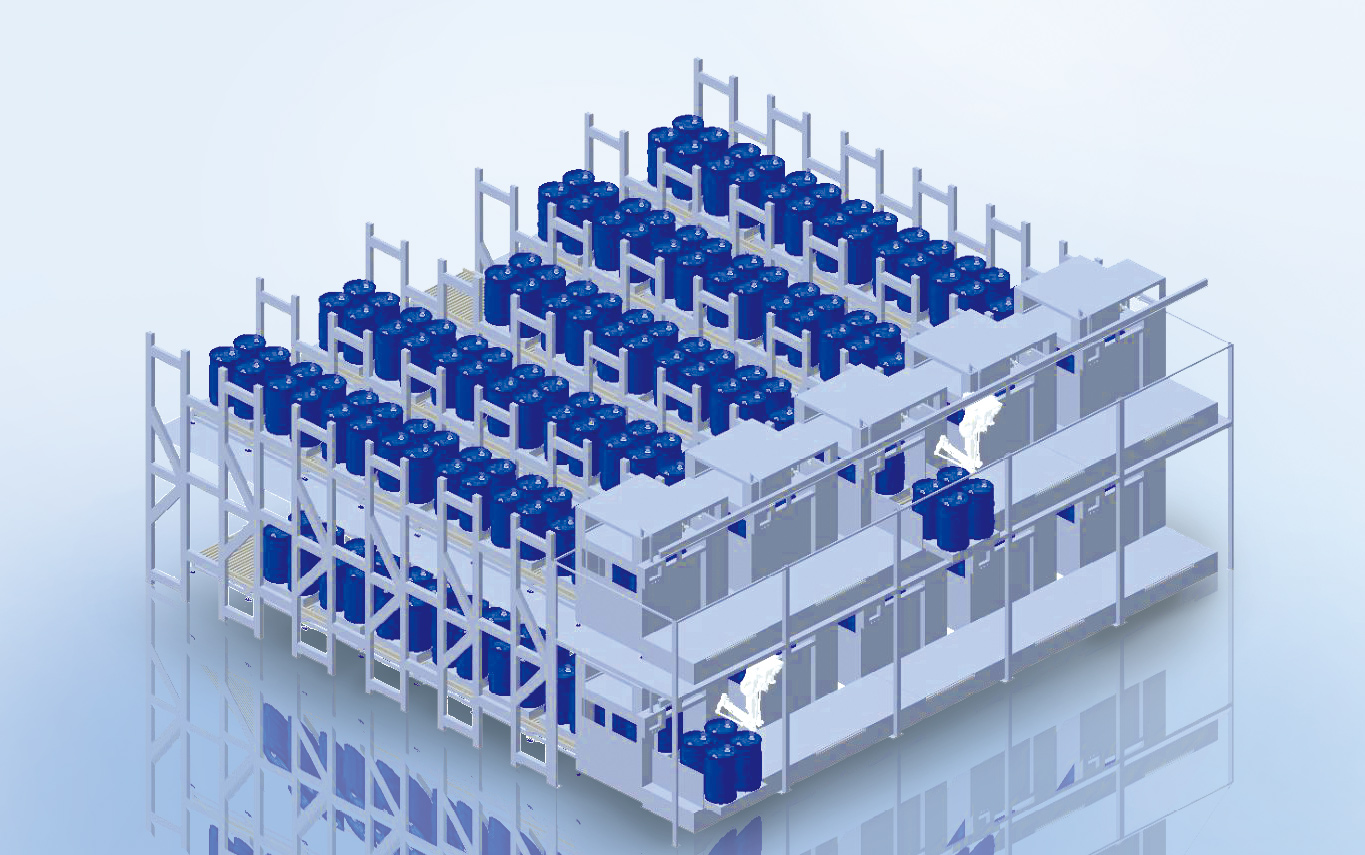
桶裝化學品高效供酸新架構
Keywords / Effectiveness3,Quality31,Drum's Hyper Logistic (DHL) System,Drum unit,Chemical Dispense Unit (CDU),DrumDrain,Chemical Consuming Defense System2
因應未來人力成本高漲以及人力資源取得不易的問題,如何設計一套兼顧效率與供應品質並有效降低因人工操作必須面對的失誤風險,已然成為半導體廠務的重要課題。本計畫設計了一套為桶裝化學品量身打造的高效率輸送及供應系統,藉由高自動化的系統架構,實現桶裝化學品供應系統的架構變更 ,有效降低系統設備的體積,達到空間使用率的大幅提升,變更後的空間節省幅度可達 20%之高,即使面對未來的新世代製程更加多樣化的化學品供應種類也能有效容納,並大幅改善化學房(chemical room)空間不足的問題。
前言
半導體製程中所使用到的化學品原料相當多,依使用量的多寡,在廠務端源頭的供應方式可大致分為槽車(Lorry)及桶裝化學品(Drum)兩種。前者僅用於少數用量較大的大宗化學品(Bulk Chemical),其餘大部分用量較小的化學品則以後者為主要的供應方式。
Drum在源頭的更換流程大致如下,供應商將物料運進工廠後,由庫房人員將Drum搬運到位於廠房內高風險生產物料區(Hazardous Production Material, HPM)一樓的流動棚,再由廠務端的化學品操作人員(Total Chemical Manager, TCM),利用夾酸車及拖板車將Drum經電梯載運到HPM二樓的化學品供應房,最後再手動將Drum桶拖運至化學品供應單元(Chemical Dispense Unit, CDU)機台內進行更換。然此一更換流程除將耗用掉了大量廠務端TCM的人力,且整板物料重量將近1噸不易控制,偶有不慎即會讓Drum桶翻倒,造成環境破壞甚至人員壓傷,讓此一人力更換作業流程目前仍存在著許多潛在的風險。此外,TCM在最後CDU機台換Drum的階段,為了避免吸入管路卸除時揮發出來的化學品,更須身著全套的安全防護衣,十分不便。
隨著半導體N10世代製程之後,生產用的化學品種類及數量逐漸增加,Drum供應系統在廠房內的空間擺設規劃也是一大問題。如何在有限的廠務設備使用空間中,滿足生產線上大量且種類繁多的化學品需求,成了目前新廠規劃設計人員們的一大挑戰。目前的Drum裝載於CDU系統內進行供應。而除了裝載Drum的空間之外,CDU系統還包含了用來濾除化學品內金屬不純物的過濾系統、供應時緩衝用的日桶槽(Day tank)、以及最後輸送化學品供機台使用的壓力桶槽(Pressure Tank)或壓力罐(Pressure Vessel)。上述這些單元,使得Drum與CDU結合型的機台體積相當龐大,這也讓目前新廠規劃設計人員,進行空間設計規畫時相當困擾。除此之外,Drum的空間利用率問題也困擾著運轉單位。由於從庫房領出Drum後再拖運至HPM二樓的化學房內進行更換將耗掉相當多的時間,在避免運轉中斷的考量下,廠務端均會從庫房端一次性領較多的Drum放置於HPM二樓的空間,讓運轉上保有安全庫存量。視化學品用量的多寡,安全庫存量少則4桶,多則可高達20桶。這也讓原本空間利用率已相當吃緊的HPM二樓,情況更是雪上加霜。
為了解決現行因Drum供應方式所存在著運轉人力以及空間利用率的兩大問題,本計畫為了Drum供應化學品設計了一套高效率輸送及貯存系統(Drum's Hyper Logistic System, DHL System)。該套系統目前仍在設計階段,尚未有實體機台實際運作,故本文僅針對該套系統的運作模式進行介紹。
系統介紹
DHL System主系統簡介
圖1為廠務換酸作業流程比較圖。由圖可知,DHL System將傳統的CDU分拆為兩個主要單元,分別為Drum單元(Drum Unit, DU)及供應單元(Supply Unit, SU)。DU設置於HPM一樓,並和原有的流動棚結合。流動棚的物料輸送方式也由原本的滾輪改為自動式輸送帶 圖2。當Drum用空需更換時,DU會透過內部的可程式邏輯控制器(Programmable Logic Controller, PLC)下指令給輸送帶,將實桶的Drum送進DU,同時將用畢的空桶Drum送出DU,並存放於空桶暫存區,待TCM協助交由供應商進行回收。為了能更進一步地提升廠房空間利用率,本計畫也比照原本的流動棚,將此DU供應線設計為雙層式,讓可供應的化學品數量加倍。DU內的化學品會再經由幫浦輸送至位於HPM二樓化學品房內的Day tank暫存,最後再由SU將化學品供應給無塵室內的生產機台做使用。
圖1、換酸作業流程比較示意圖

圖2、自動式輸送帶示意照片

Drum單元 (Drum Unit, DU)
和傳統的CDU相比,DU於硬體上做了相當大的改變, 圖3為DU主要的元件示意圖,以下將針對其做進一步介紹。首先,DU增設了無線射頻識別系統(Radio Frequency Identification, RFID),對經由自動輸送帶運進DU的Drum桶進行自動掃描,確認化學品是否正確,避免庫房人員將Drum桶誤置於不對的輸送線上,造成上錯酸的情況發生。此設計不僅為化學品入料增設了一道自動防線,也取代了傳統人工刷Drum桶上條碼(Barcode)來確認化學品是否正確的動作。在操作便利性上的考量之下,DU也將傳統固定於機台上的人機介面(Human Machine Interface, HMI)改為懸掛式,讓操作者可不僅限於同個位置操作系統。此一設計大大增加了操作便利性,讓系統維護人員可一邊操作HMI一邊觀測內部自動閥件或幫浦的作動,增加人員對系統除錯或維護的工作效率。
圖3、Drum Unit 主要元件示意圖
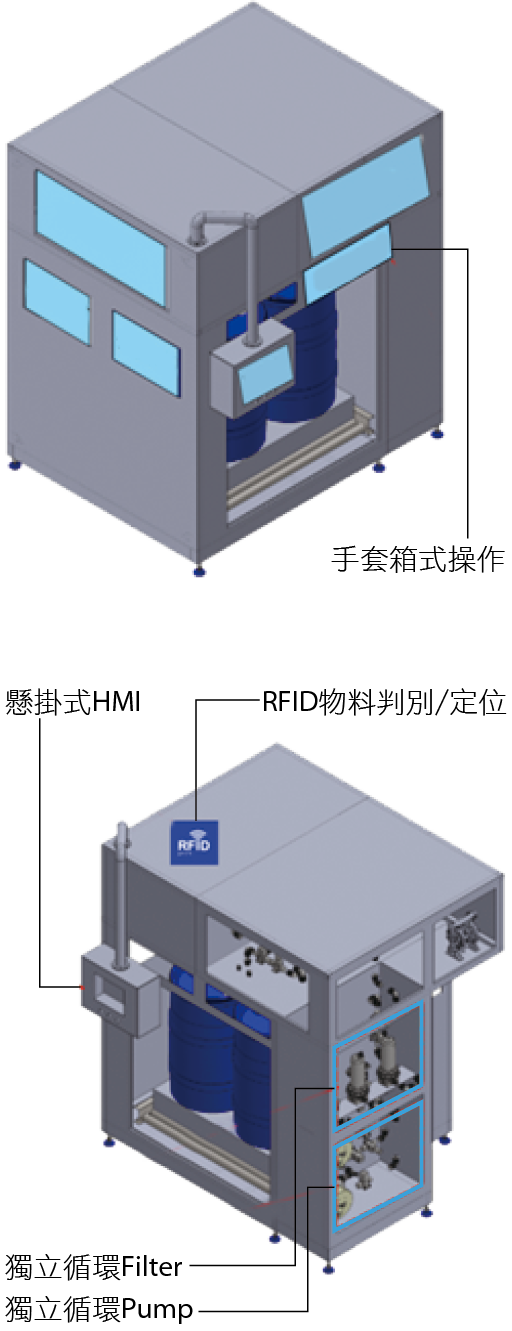
在DHL System系統中,雖然Drum桶於已可經由自動輸送帶送進DU,但將化學輸送管路於Drum桶上的拆裝作業還是需仰賴人力操作。對於傳統的CDU,人員若要對Drum桶的化學管路進行拆裝作業,均需身著全套的安全防護衣,以避免人員接觸到Drum桶內所揮發出來的有害性化學蒸氣。為了更進一步降低TGM的人力成本,並縮短更換Drum的作業時間,DU也加入了手套箱的設計 圖4。此一設計因已經將DU內的空間和外界作隔離,因此可讓TGM人員在無需穿戴防護衣的情況下,透過手套對DU內的Drum桶進行管路更換作業。
圖4、手套箱操作示意照片(測試時為非實桶操作故人員未著防護器具)
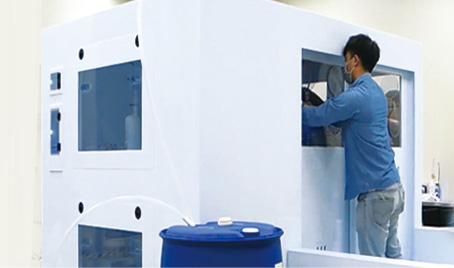
獨立式Drum桶循環過濾系統
傳統CDU系統 圖5內的幫浦,除了要負責供應化學品給線上機台使用之外,還要肩負將化學品由Drum桶補液至Day Tank以及Drum桶內化學品預先過濾循環共三項任務。內部的濾材也是一人分飾兩角,除了要過濾由Drum桶輸送至Day Tank的化學品之外,也要負責備用端Drum桶的過濾循環。在供應不中斷的前提之下,當系統大量要酸,或是其中一顆幫浦故障的情況發生時,上述的化學品輸送路徑往往是以供應優先,Drum桶的過濾循環程序則會因此中斷。為了改善此問題,DU 圖6也新增了獨立式過濾循環系統的設計,讓Drum桶的過濾循環流程不受線上供應的狀況影響,達到化學品供應品質再強化的目標。
圖5、傳統CDU 循環路徑(簡化)
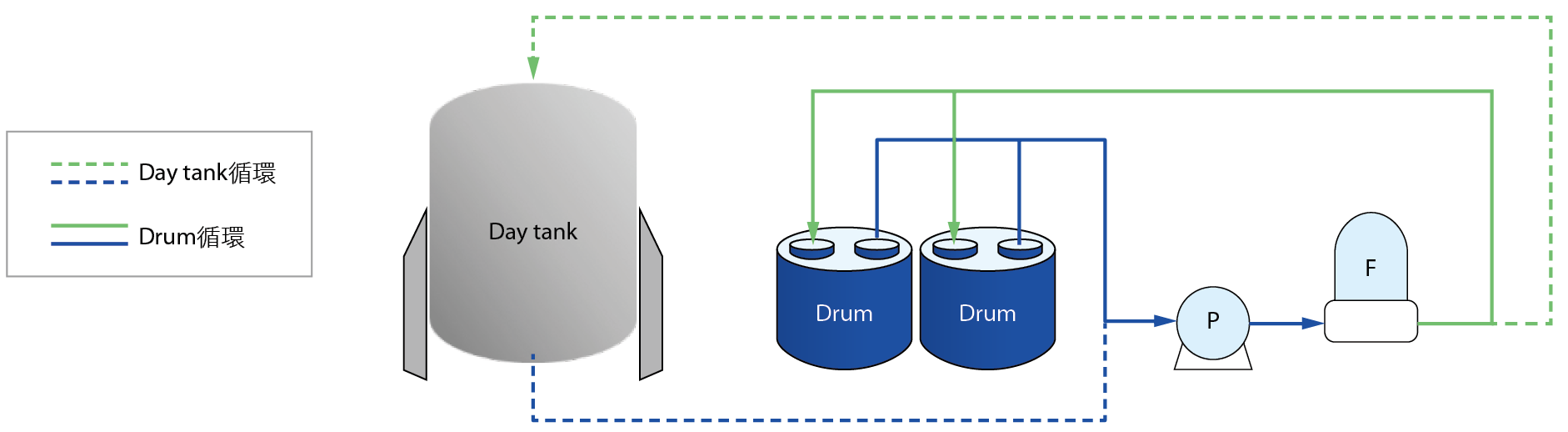
圖6、DHL SYSTEM 循環路徑(簡化)
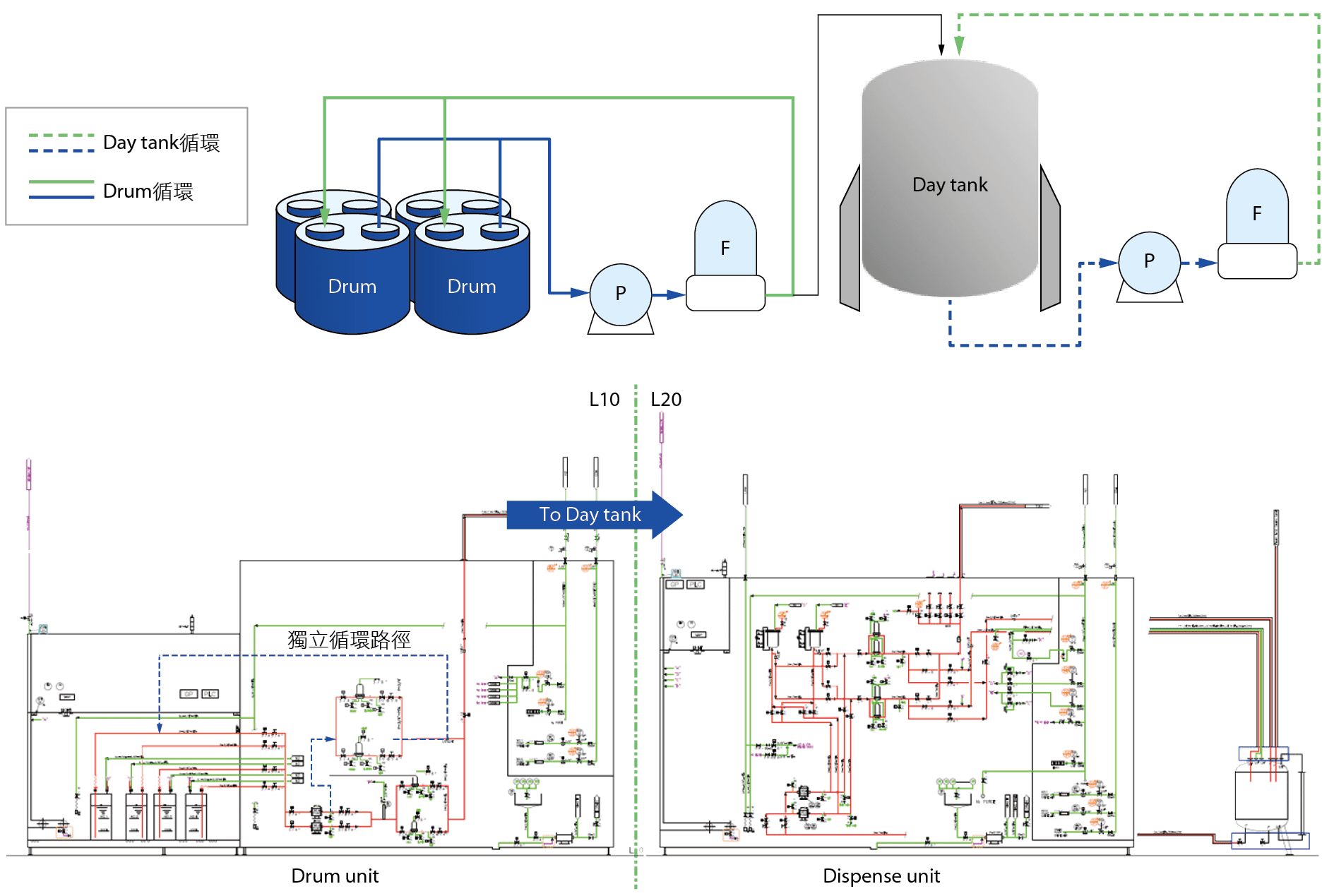
過濾循環除了程序不中斷之外,其過濾時間也是相當重要的一環。傳統CDU一次僅可放兩個Drum桶,以目前雙Drum桶的CDU系統來看,進行循環過濾的Drum桶,其過濾時間常會受到另一顆供應側Drum桶的供應時間所影響,使得預先循環過濾的時間無法拉長。DU系統中也針對了此一問題作了改善,將每次進入DU的Drum桶數由2顆增加為4顆,降低循環過濾受到線上供應干擾的情況,使過濾時間得以拉長。
結果與分析
利用Chemical DHL System對於過往所受到的諸多限制以及供應運轉上的諸多困難,提供有效的解決辦法,大致可分為幾個面向解釋。
- 大幅降低運轉人員工作量:針對作業人員工作量進行分析 圖7後可以發現,目前以領料以及供料的作業時間達26%。如使用此系統則僅需要6%,節省成本效益為每年、每廠約9,000,000元。
圖7、運轉人員工作量分
- 大幅降低運轉人員暴露於化學品之風險 圖8:藉由自動化入料/出料及手套箱等設備,運轉操作人員除進行 PM工作外可不需穿著防護設備,降低人員暴露風險26%,增進工作環境健康指數及TCM工作意願。
圖8、運轉人員暴露風險分析
- 藉由獨立循環模組,大幅增加循環時間 圖9達一倍,增進供應品質。
圖9、Drum 過濾模式
表1、原物料循環時間與次數比較系統設計
(以15桶/天計算)Drum 循環
Drum 循環 KPI
Drum 循環時間
Day tank 循環
補液 (tank+vessel)
hrs
次/桶
hrs
hrs
hrs
既有設計:pump共用
(補液+drum循環+day tank循環)12
9.6
0.8
12
2.5
新設計:獨立循環pump
24
19.2
1.6
24
1.25
- 有效提升HPM利用率:與既有 CDU體積減少20%,提高閒置空間以利未來擴充,以十五B廠為例,變更前HPM L20可容納 CDU總數為104套,藉由此一設計可容納CDU總數可達128套。面對未來更加多樣化的化學品種類,將有足夠裕度以符合供應需求。
新設計增加HPM 2F空間20% (337m2、暫存區5%、 CDU15%),換算可增加擴充11 sets CDU空間,HPM 1F流動棚增加147m2 (15%),因增加drum unit &維修空間,既有空間足夠擴充,並規劃人機動線區隔以符合安全要求 圖10。
圖10、原物料儲存架構差異

結論
著眼半導體製程不斷精進,對廠務端來說,化學品原料的供應品質及供應多樣性將是一大挑戰。藉由本計畫所設計的DHL System,未來的廠務系統得以實現低運轉風險與低人力運轉的目標,藉此自動化運轉模式大幅降低運轉成本與人員工作量。此外,該系統也讓原本HPM二樓空間利用率相當吃緊的問題得以解決,使得未來的新廠設計人員不必再苦惱化學品供應單元的擺放問題,後續運轉人員也能夠有較為寬敞的操作空間。未來若能再增加DHL System的機械自動化功能,如自動更換Drum桶或是自動清運空Drum桶等,相信對於廠務運轉將會是另一個革命性的進步。
參考文獻
- 林惠玲、陳正倉 (2001),「工廠自動化與經濟效益關係之研究─台灣製造業之實証研究」,《國家科學委員會研究彙刊:人文及社會科學》,11(3),256-270。
- 鄒孟文、劉錦添 (1999),「先進技術與工資報酬:台灣電子業之實證」,《經濟論文叢刊》,27(3),285-309。
- MIT Press, Cambridge, MA.
- Autor, D. H., L. F. Katz, and A. B. Kreu-ger (1998), “Computing Inequality: Have Computers Changed the Labor Market?” Quarterly Journal of Econo-mics, 113(4), 1169-1213.
- Loveman, G. (1994), “Information Tech-nology and the Corporation in the 1990’s”, MIT Press, Cambridge, MA.
留言(0)