摘要
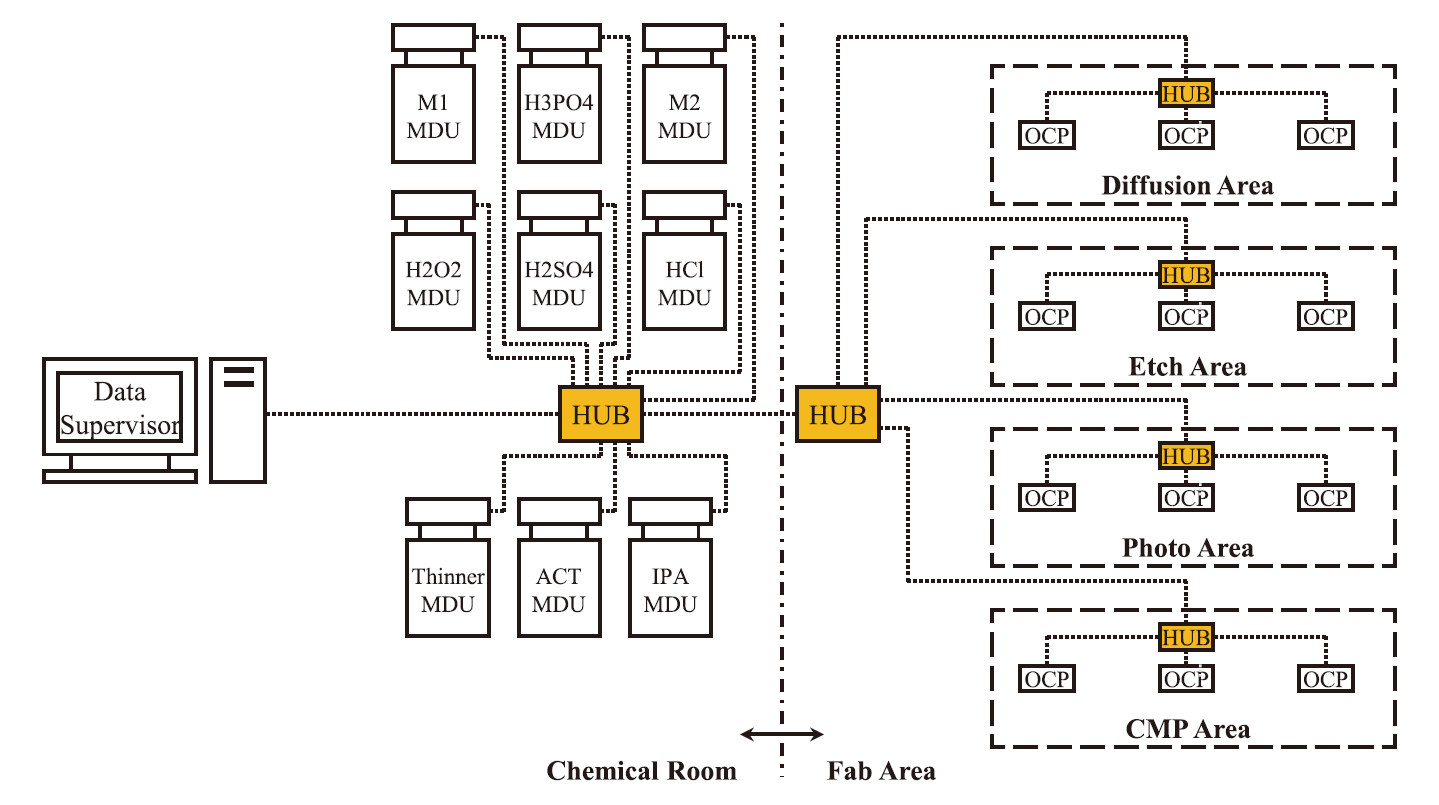
化學供應系統架構升級-生產供應不中斷之困難與挑戰
Keywords / Chemical Supply System,ARCnet,Controlnet,PLC(Programmable Logic Controller)
The chemical supply system has evolved and improved over the years, and it has been in a stable operating state in the new fabs. However, in contrast to the chemical network and controller of old fabs.
The continual improvement team activity on the old system can only be said to be a temporary solution, not the root cause. To provide comprehensive network updates and controller upgrades is the long-term solution. This article will explain the improvement plan of fab 3. Due to the complicated signal transfer steps, as long as you don't pay attention, it may cause production interruption. Especially in the transfer process of master panel and ICP(interface Control Panel).
For this project, we must first upgrade the communication architecture, from ARCnet to Controlnet, during the conversion, the fab tools will communicate with facility through two network domains ; continue to upgrade the "Chemical Dispense Unit (CDU)", upgraded from a "microprocessor" to a PLC(Programmable Logic Controller) controller. The article will detail how to completed the network transfer of 208 fab tools, realized the uninterrupted upgrade of 20 CDU controllers, and shared the problems faced during the implementation. And set a one-button back up function and a ready signal & forced supply panel to shorten the emergency response time. The stability of the chemical supply can be improved to another century.
1. 前言
半導體生產使用大量的化學品,其穩定的生產有賴於廠務化學系統的穩定供應,隨著生產效率的演進與製程改善,化學系統的不中斷供應成了基本但重要的課題。
三廠建廠於西元1994年,在歷經了28年的運轉後,設備的老舊與過時成了棘手但必要面對的課題,之所以棘手,是基於化學供應網域為串聯上百台生產機台的龐大網域、等於每套CDU背負了最多達40台生產機台的使命,在不允許供應中斷的前提下如何做到化學供應網域全面升級呢?三廠初始化學供應網域為ARCnet(Attached Resource Computer NETwork) 架構,其致命缺點為網路風暴,當發生時將癱瘓整個化學供應訊號傳遞;初始CDU之控制器是「微處理器」(micro-processor),其缺點為編輯程度低,此限制對於CIT的改善工程評估無疑是個大瓶頸。
綜合評估下決定將化學供應架構升級為Controlnet+PLC 控制器。改善的同時也思考在新架構下,未來運轉過程可能會遇到的問題,同步建構所需的附屬控制設備,如 : force ready 控制盤、一鍵back up功能,使整體化學供應達到最佳的穩定狀態。表1為Controlnet & ARCnet優劣比較表。
封包限制 | 優缺點 | 綱路架構 | 優缺點 | |
---|---|---|---|---|
Controlnet | 不限 I/O 數據個數 | 速度快不塞車 | 雙環狀 | 雙環redundant |
ARCnet | 單一 token | Token未傳遞完成將造成網路風暴 | Bus樹狀 | 上游站點故障將連帶影響下游 |
2. 文獻探討
2.1 化學供應系統的演進&成廠區的困擾
三廠為台積僅次於二廠的老舊廠區,建廠時期延續二廠的化學供應系統設計,仍是採用美國BOC EDWARDS規劃之ARCnet網絡搭配BOC 4500/5100/5500型號之CDU,此設計在tsmc 6、8吋晶圓廠是建廠的標準配備,除了經收購成為tsmc 七廠的前德碁半導體(Merck體系)、成為tsmc八廠的前世大積體電路(sumitomo架構)以外,二廠、三廠、六廠使用此架構在20~30年前無疑問為當時的主流。但隨著科技的進步、產能利用率及生產品質要求不斷提升,前言所述的設計及運轉缺點也同步的被不斷放大,工廠對於供應不中斷之要求與日俱增,任何一個供應節點異常往往會造成生產的慘重損失。
舊供應架構會面臨到的最大問題為網路風暴,除了網路風暴以外對比新廠PLC架構的供應系統,仍存在以下嚴重問題,如 表2。
工程師為此絞盡了腦汁在執行CIT工程,如 : ARCnet hub分流、ERP的強化等,但大家都明白這只是治標不治本,唯有痛定思痛的將供應系統做完整的架構改變,頻繁的供應中斷問題才會徹底根除。後續tsmc於12P1建廠開始已將化學供應架構做全面的升級,改為Controlnet網路架構+PLC控制器,此架構不但可以解決三廠面臨的網路風暴問題,PLC控制器的可編輯特性更為未來不斷突破的製程演進鋪好一條康莊大道。
No. | Issue | F3困境描述 |
---|---|---|
1 | 網路風暴 | 系統會因任何一個元件失效引發網路風暴 |
2 | 不可靠的hub | Hub可靠度低,失效會引發網路風暴 |
3 |
無診斷功能 |
當異常發生無法快速知問題點,需經過大量 try & error判斷 |
4 |
系統無編輯能力 難以升級新功能 |
CDU使用micro-processor為控制中心,其無高階編輯能力 |
5 | 無PM功能 |
無訊號by-pass功能,PM時容易誤觸導致供應中斷 |
6 | Phase out問題 |
Parts已停產無法購得 |
2.2 化學供應網路架構
三廠舊網路供應架構如 圖1,圖中的hub常常是造成網路風暴的主因,不僅可靠度低且擴充點數僅有8點,導致廠內共需25台hub才可串接完龐大的供酸網域,每當網路風暴發生時不易從中判斷故障點。而下游開啟VMB(Valve manifold box)供應閥件的設備OCP(Operation control panel)則多達67台,同屬穩定度低且維護不易之設備。新舊網路架構差異可由 圖2表示。
圖1、三廠ARC-net網路架構
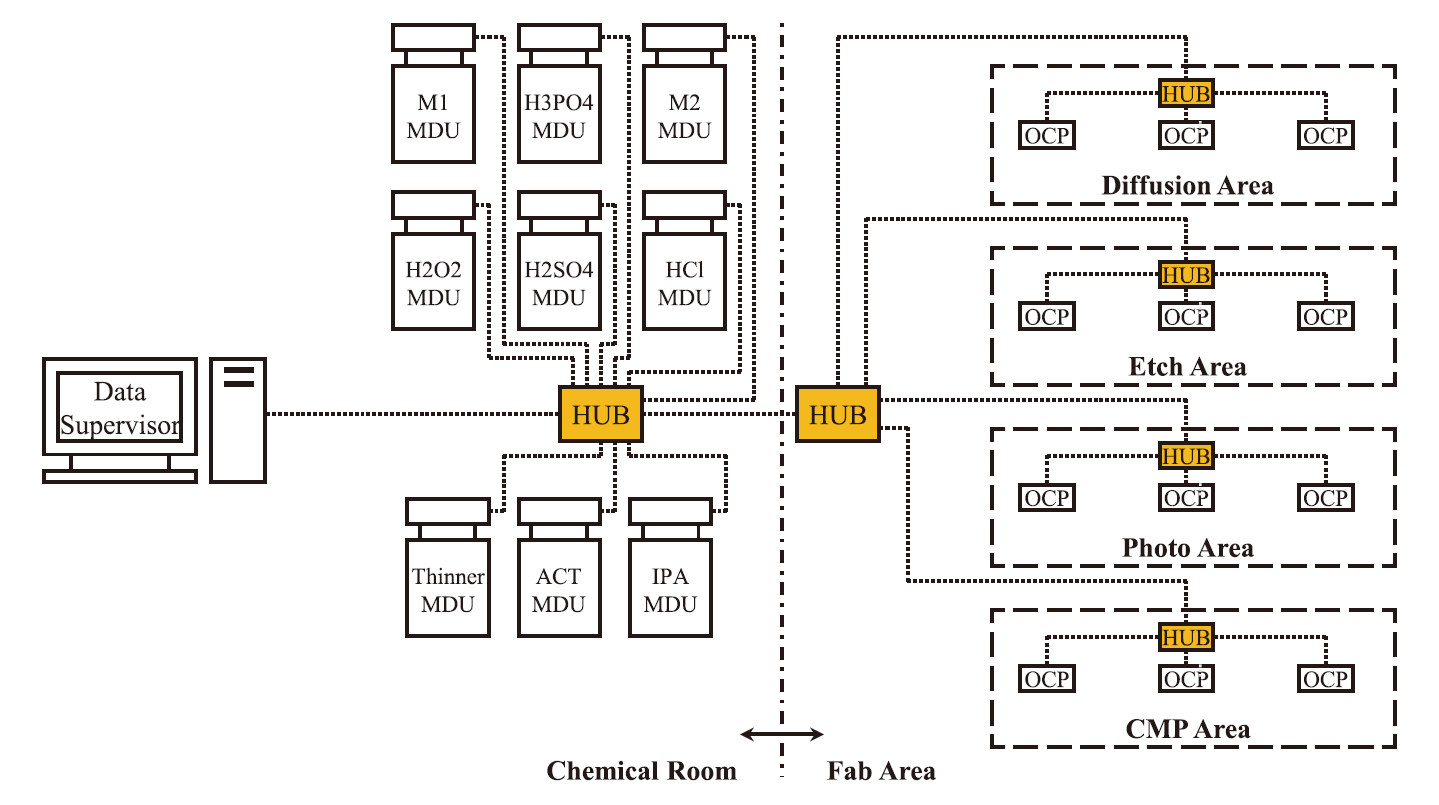
圖2、三廠新舊網路架構差異
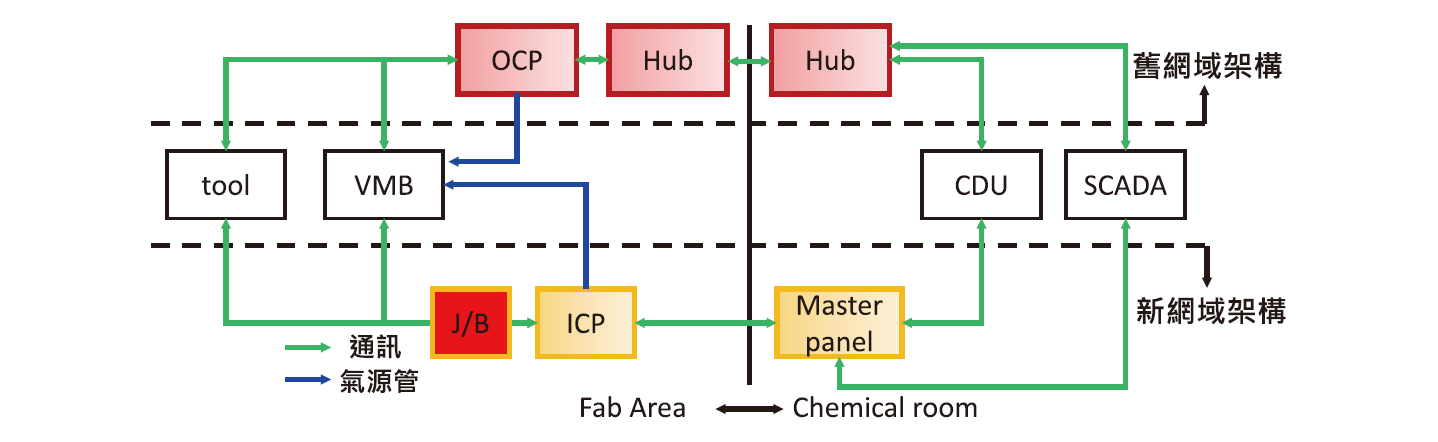
2.3 化學供應系統
三廠化學系統以D5100型號為例,如 圖3,管路閥件構造與現今主流之帆宣CDU並無太大差異,甚至可以說帆宣CDU是依此設計為基底經持續修正改善後得到現今的樣貌。
但其在控制架構上的差異卻是天差地遠,三廠CDU大腦是由微處理器所組成,顧名思義它不像傳統電路板或繼電器單純只有開或關等陽春功能,它能擁有部分可變參數的功能調整,所以稱為微處理器,但此「參數變更」的功能是無法修改的,意指所有的功能是固定的,超出說明書範圍的功能無法新增,這對CDU的持續改善及演進無疑是個嚴重的阻礙。大部分高階設備經多年的運轉勢必遇到須調整或修改的情形,而我們因此受限只能以「外掛」的方式從旁介入CDU運作,如 : 加裝ready force on繼電器、外掛主管路空管預警sensor等等功能,這些作法雖能解燃眉之急,但缺乏整合及本質變更的做法,導致新增的功能顯得越來越雜亂無序。
因此,將CDU控制器升級為PLC顯得勢在必行,整理PLC相較微處理器有以下優點 :
- 配線少、體積小、減少硬體設備。
- 程式修改容易、控制彈性大,具有擴充性。
- 設計裝配時間短、維修容易,可靠性高。
- 可預先作運轉模擬,容易檢查修正。
- 控制層次提升,可與電腦連線控制。
圖3、F3 D5100 CDU
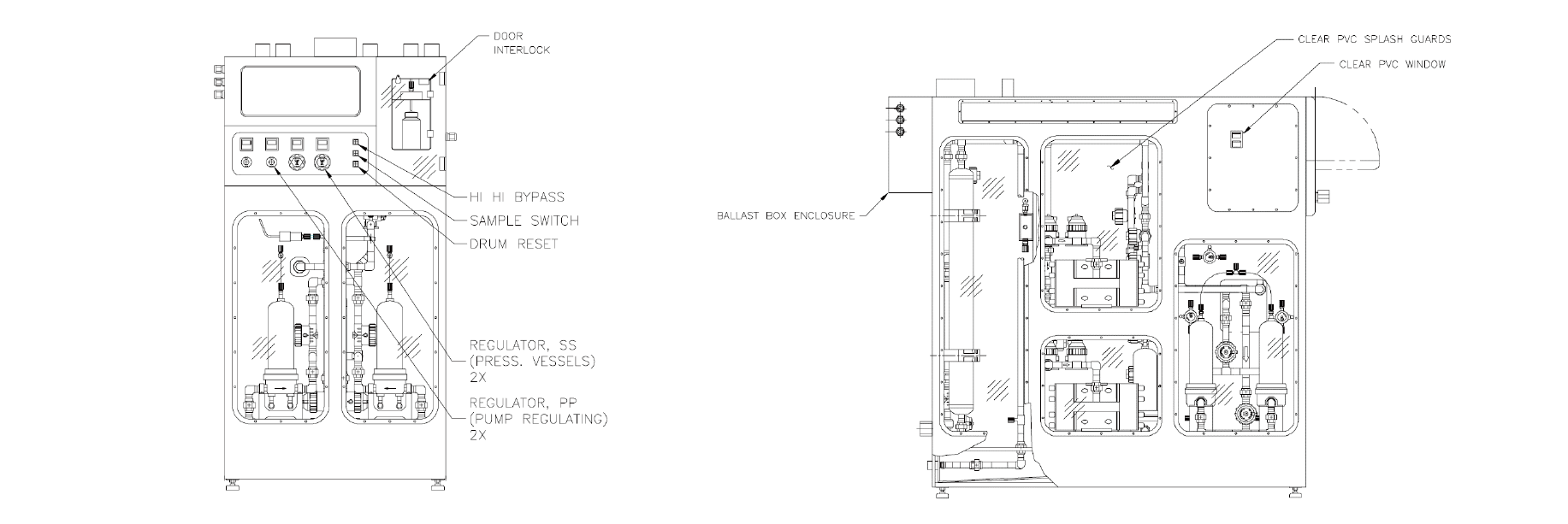
3. 研究方法
3.1 網路架構升級規劃
我們規劃以下四大步驟作為網路架構升級的主軸,目的是由簡入深、先打基礎再逐點轉換擊破。
❶ 乙太網路架設(Ethernet)
專案規劃初期先建置乙太網路,工程以「主控制盤」(Master Panel)為中心,盤內規畫兩組MOXA 16-port Ethernet switch hub,以放射狀連接至各CDU,如 圖4。主要目的為接收CDU運轉狀態及警報,為值班室監控之用。
圖4、Ethernet佈線圖
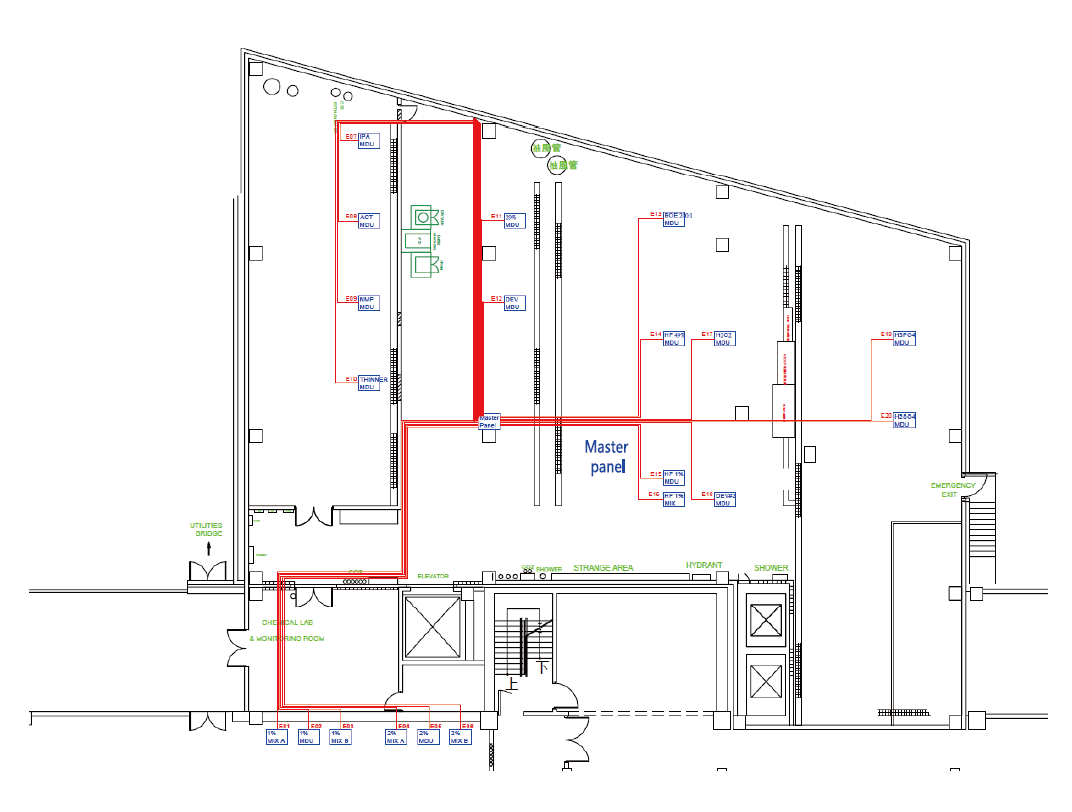
❷ Master Panel/ICP網路架設(Controlnet)
此階段為master Panel與ICP(interface Control Panel)溝通之網路架設,master panel內由PLC控制器往無塵室延伸架設三組Controlnet迴路,三組迴路下掛各2~5台ICP,如 圖5。
圖5、Controlnet佈線圖
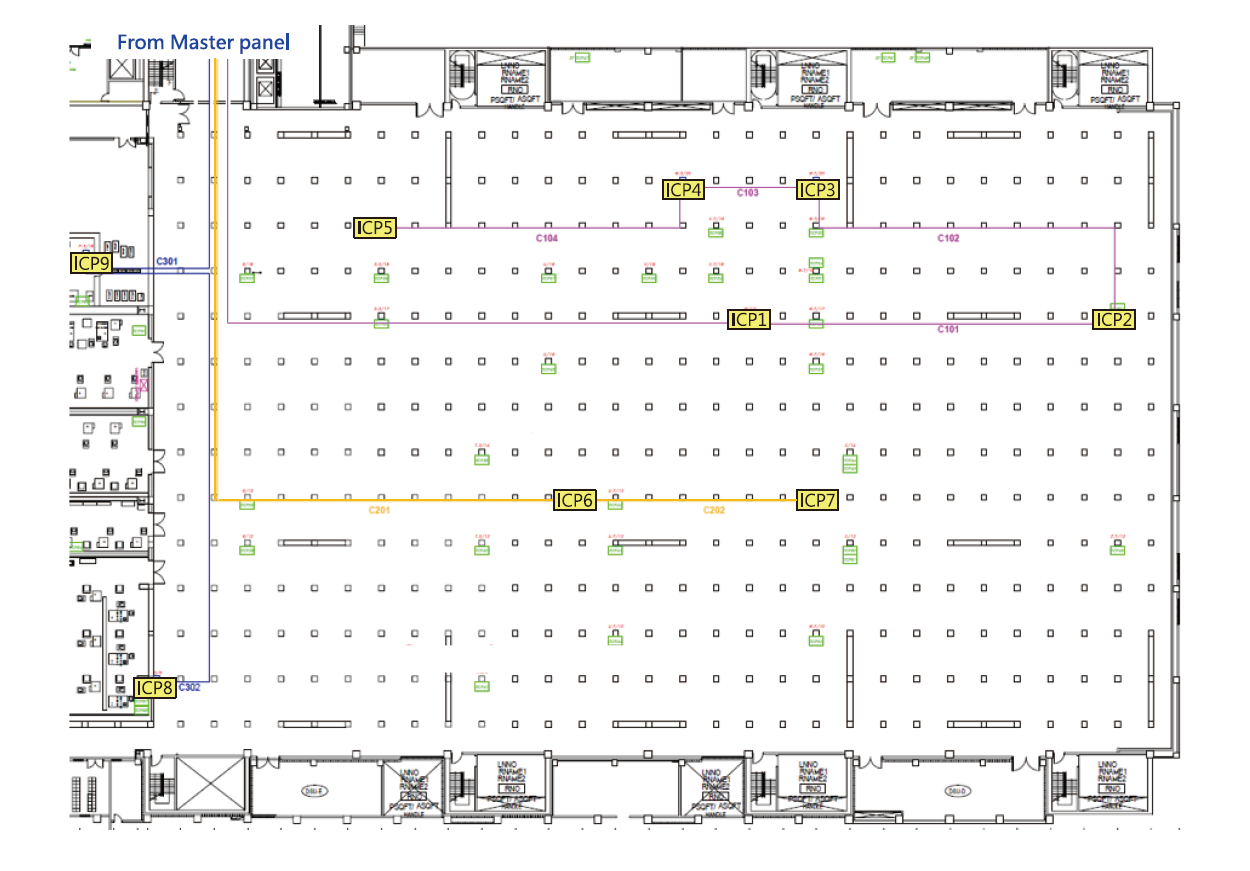
master panel主要功能為接收ICP的訊息,判斷訊息後產生對應指令,將指令回傳ICP並同步將訊息傳遞給CDU及SCADA;而ICP的功能為接收來自生產機台的「要酸需求」(request)及「緊急停機訊號」(EMO)、傳送MDU Ready訊號給生產機台,並依機台需求開啟VMB Air Valve電磁閥,最後是接收各閥箱「漏液」(Leak)訊號。
❸ J/B(Junction Box)架設
第三階段為J/B之架設,因舊網絡有大量的OCP散佈於無塵室各地,機台可就近連接各OCP,但新規畫之ICP僅需1/4 的OCP數量,故ICP定位後將距離大部分機台甚遠,若所有機台皆重新拉設訊號線至ICP,將耗費大量的時間及成本,所以我們規劃J/B架設於原OCP旁,再利用預置線路將J/B與ICP一次串接,達到快速線路預置的目的,如 圖6。
圖6、J/B架設&線路預置示意圖
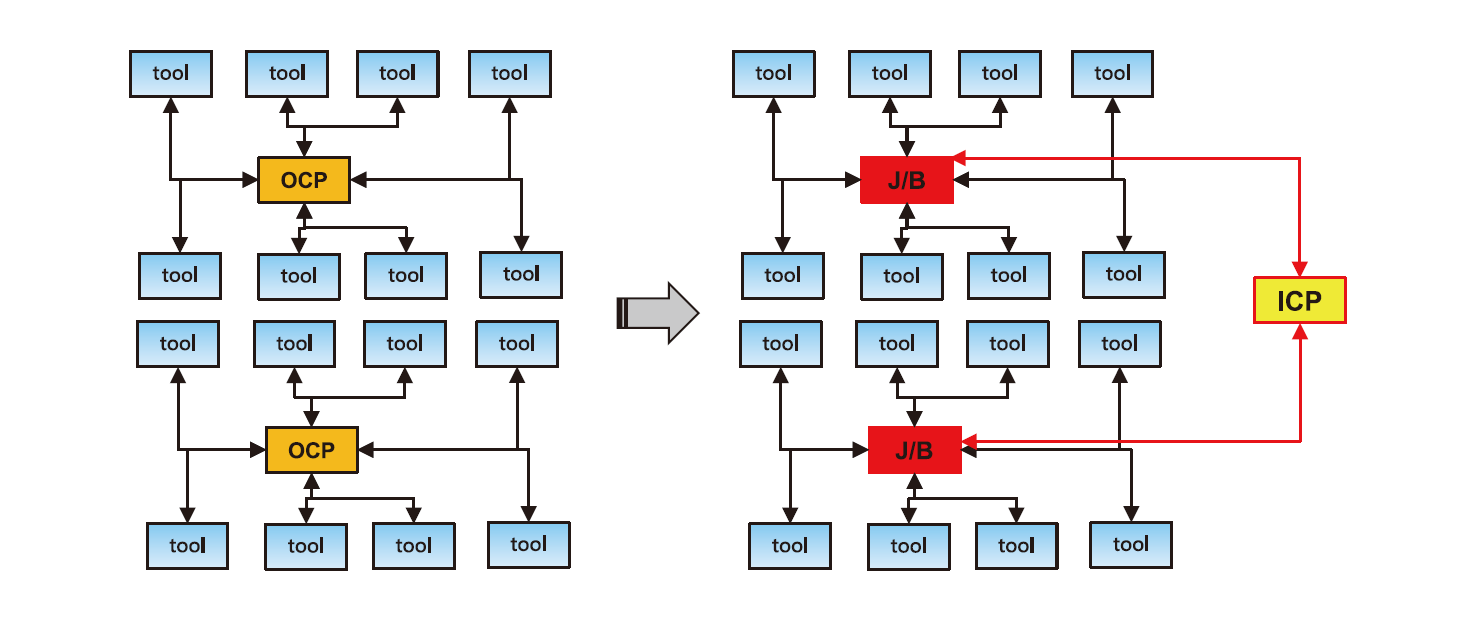
❹ VMB Air valve氣源管拉設
由ICP內的電磁閥拉設氣源管至下游VMB上的氣動閥,目的在於取代OCP上的電磁閥控制。
3.2 化學供應系統升級規劃
CDU的升級工作則focus在大腦的升級,即為PLC控制器的安裝。有賴於三廠80% CDU皆有chemical back up功能,工程得以在無斷酸風險疑慮之下施作,以下是升級的主要工序:
- 施工前取樣確認back up loop QC正常。
- 啟動back up功能確認供應正常。
- CDU斷電斷氣後執行氣源管及電控元件拆除。
- 新機殼固定焊接/電控元件安裝/氣源管拉設。
- 功能測試 : ⓐCDU送電/utility送氣;ⓑ氣動閥點對點確認;ⓒDrum Recycle/Transfer/supply功能測試。
- CDU取樣QC正常後back up復歸。
基於以上的作業流程,升級作業可於3~5天順利完成。但這都是有賴back up這個得天獨厚的功能才得以順利升級,令人困擾的是,三廠存在4套單機CDU,施工勢必遇到斷酸的問題。但試想生產機台不可能為此停產至少3天,於是我們再評估歲修施作的可能性,依據往年歲修經驗,最多能爭取到24小時停機時間,這時段必須不休息的趕工,才有機會將一套CDU完成升級。另一個問題是有能力的廠商只有一組,無法使用人海戰術同年將4套CDU進行升級,因此勢必要分4次歲修施作。要讓如此老舊的CDU再多撐4~5年,日常供應將承受相當大的壓力。
3.3 工程執行面之挑戰
在如此龐大複雜的工程項目中,許多關鍵步驟皆存在供應中斷的高風險,訊號的轉移尤其需要工程團隊反覆的思考測試,最後才能放手一搏,相較之下,龐大但危險性低的預置工作量著實顯得微不足道。而其中又以下列兩工項風險最高。
3.3.1 OCP訊號轉移至J/B
在預置工程中,須再三測試確認下列①&②路徑已暢通。
- J/B→ICP→master panel→CDU。在J/B短接訊號線模擬要酸訊號,確認可使CDU進行加壓供應動作。同樣的模擬EMO訊號,確認master panel可收到正確資訊。
- CDU→Master panel→ICP→J/B & VMB。測試CDU提供之ready & trouble訊號於J/B可測得正確資訊。另外ICP聽從master panel指令產生正確的電磁閥氣源使VMB閥件開啟。經上述兩路徑測試無問題後才可進行訊號轉移,其中再分以下步驟。
- 將ICP氣源管tie in至VMB,接著立即進行電磁閥強供、酸房對應CDU強供,如此可確保訊號轉換期間不至斷酸。
- 訊號線tie in : 因ready訊號斷開勢必會造成設備警報,當CDU產生不預期的Ready訊號中斷可能會影響設備機台,但計畫性工程若有事先通知設備工程師,ready失效便不致造成影響,設備工程師只要即時reset警報即可繼續生產,故此步驟務必執行告知的動作,通報後再執行ready訊號轉移,同時一併將EMO/request/trouble及VMB leak訊號tie in。歸功於J/B就近設置於OCP旁,每點訊號轉移僅需耗時30秒,不影響生產機台要酸。其中訊號轉移過程如 圖7所示。
圖7、OCP訊號轉移J/B示意圖
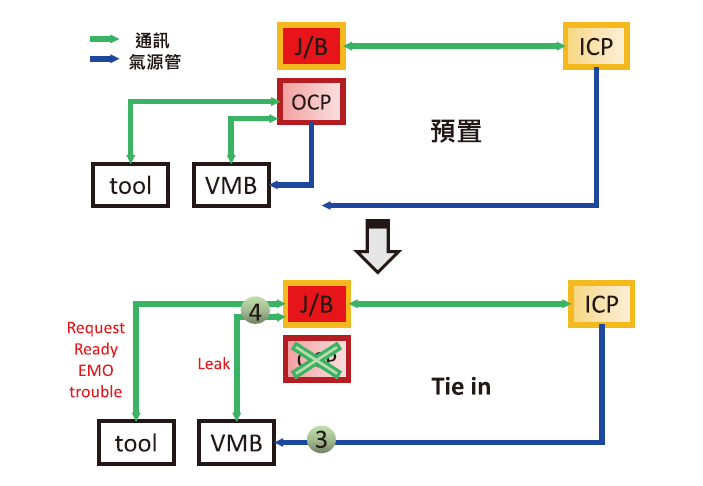
3.3.2 單機CDU之PLC升級
在無計可施的情況下,我們轉而思考將CDU強制供應並同時進行升級的可能性。原先三廠為了縮短系統異常反應時間,設計出一套外掛的pump強供器,只要利用此工具將①pump強制啟動;②供應路徑閥件開啟,即可以讓CDU形成一條強制供應路徑,我們想利用此概念作為工程執行且不中斷供應的方法。
但經仔細思考,上述功能只適合短時間的緊急應變,用來爭取異常排除時間,若長時間使用此功能則會面臨部分斷酸問題,如 : 換drum的空檔即無法供應。因此我們將pump強供器做了升級,讓此模組同時擁有供應及補酸的功能。
我們觀察P&ID,選擇pump#1作為補酸路徑、pump#2作為供應路徑,讓兩個pump各司其職。而參考 圖8我們可將供應模組功能表示如下 :
圖8、CDU臨時供應路徑示意圖
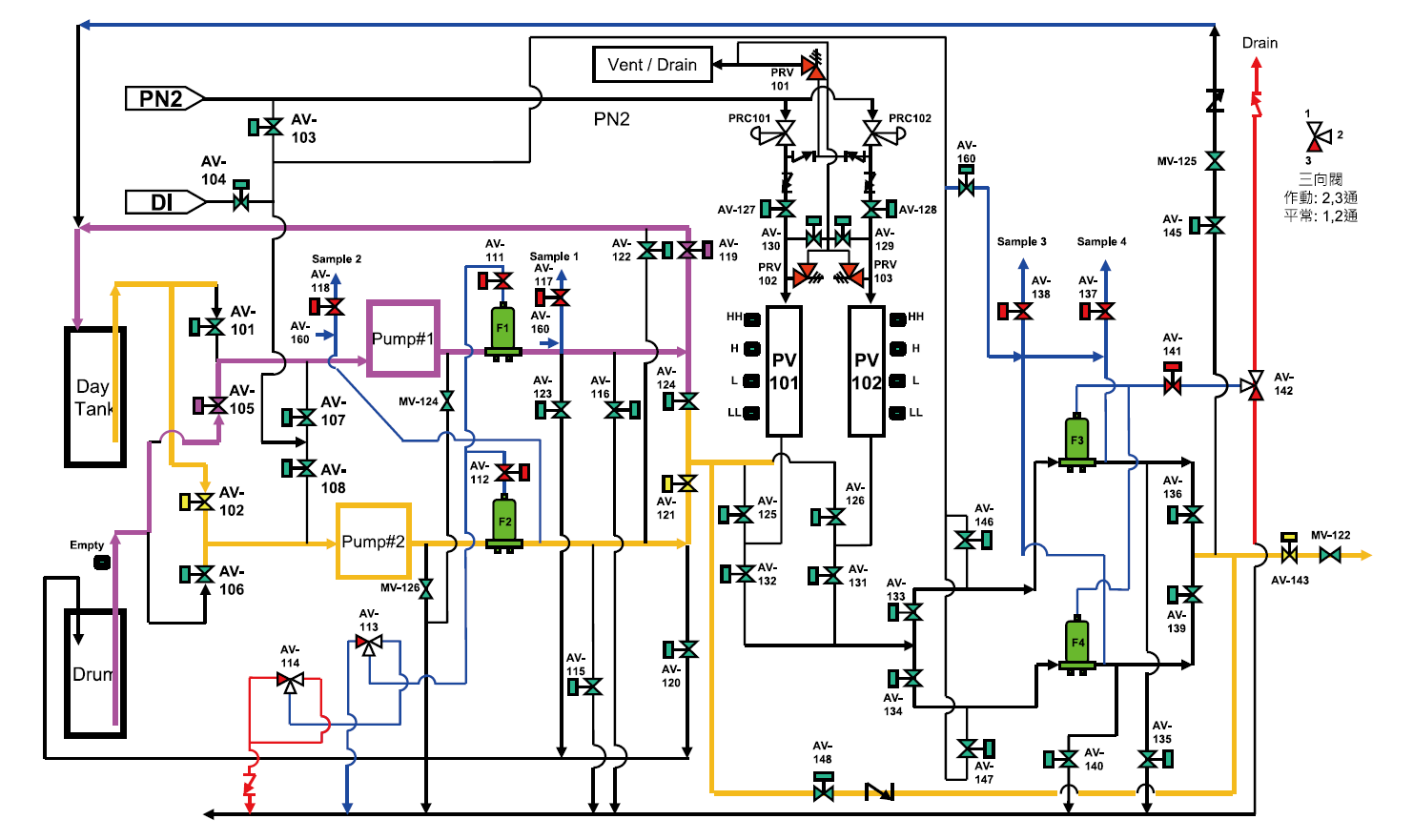
- 供應模組(黃路徑)
Day tank→AV102→Pump#2→AV121→AV148→AV143→tool
- 補酸模組(紫路徑)
Drum→AV105→Pump#1→AV119→Day Tank
供應模式有了雛型後,我們再逐一的思考可能會遇到的問題並進行優化修改。使強供器作動模式可以更接近CDU的運作。
我們考量了幾個重要問題如下 :
- 此供應為pump持續強供模式,長時間持壓恐有safety疑慮→對策 : 供應模組採自動化設計,當設備提要酸需求時pump才啟動。
- 補酸功能若為手動控制,人員將耗費大量時間→對策 : 採用自動化設計外掛桶槽H&L sensor,當L燈滅時補酸、當H燈亮時停止。另加上HH sensor連鎖停止pump運作以防止桶槽溢流。
- 防止用量大時桶槽液位過低且同時遇到drum空造成換酸不及→對策 : 新增手動補酸按鈕,操作人員可隨時將桶槽補充至高液位。
- 為了在工程施作前能實際測試供應模組功能,利用2 in 1 out的梭動閥銜接新舊氣源管,使CDU可以同時被舊大腦及供應模組控制。防止在控制器轉換期間發生無預期的問題。圖9為強供模組外觀及施工架設情形。
圖9、強供模組外觀及架設情形
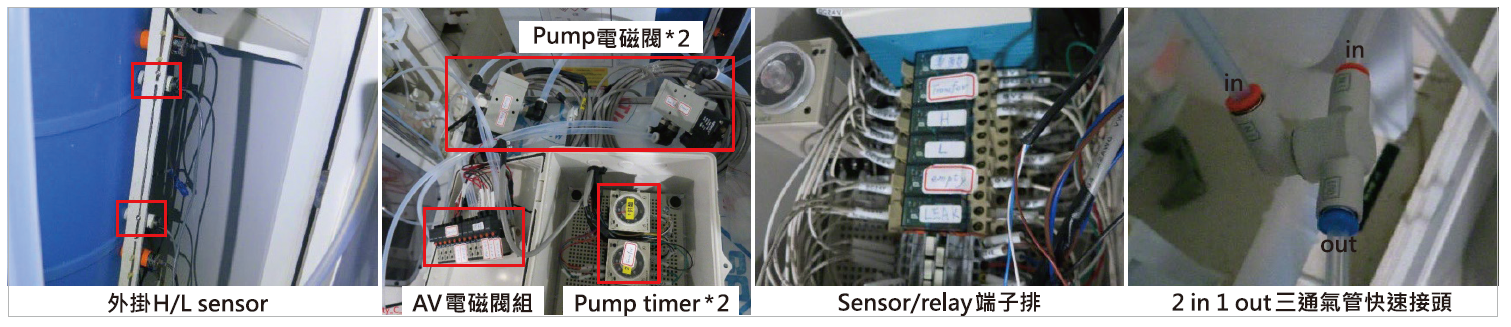
4. 結果與分析
4.1 化學供應網域升級
廠內化學供應網路經改頭換面成為以下面貌如 圖10,不僅大腦核心為redundant的設計,在ICP之間之線路亦為雙通道之模式,當主PLC fail將由備援PLC直接接手,若ICP之纜線有問題,同樣有另一通道可以暢通無阻。升級後對於日常運轉幫助甚大,統計在ARCnet時期,平均每3年可能遇到一次嚴重的網路風暴,將造成上千的move impact,而轉換成Controlnet之後,統計2017至2022/04通訊皆維持暢通,使用同樣架構的友廠亦無網路中斷之情事發生。
圖10、F3D Controlnet架構
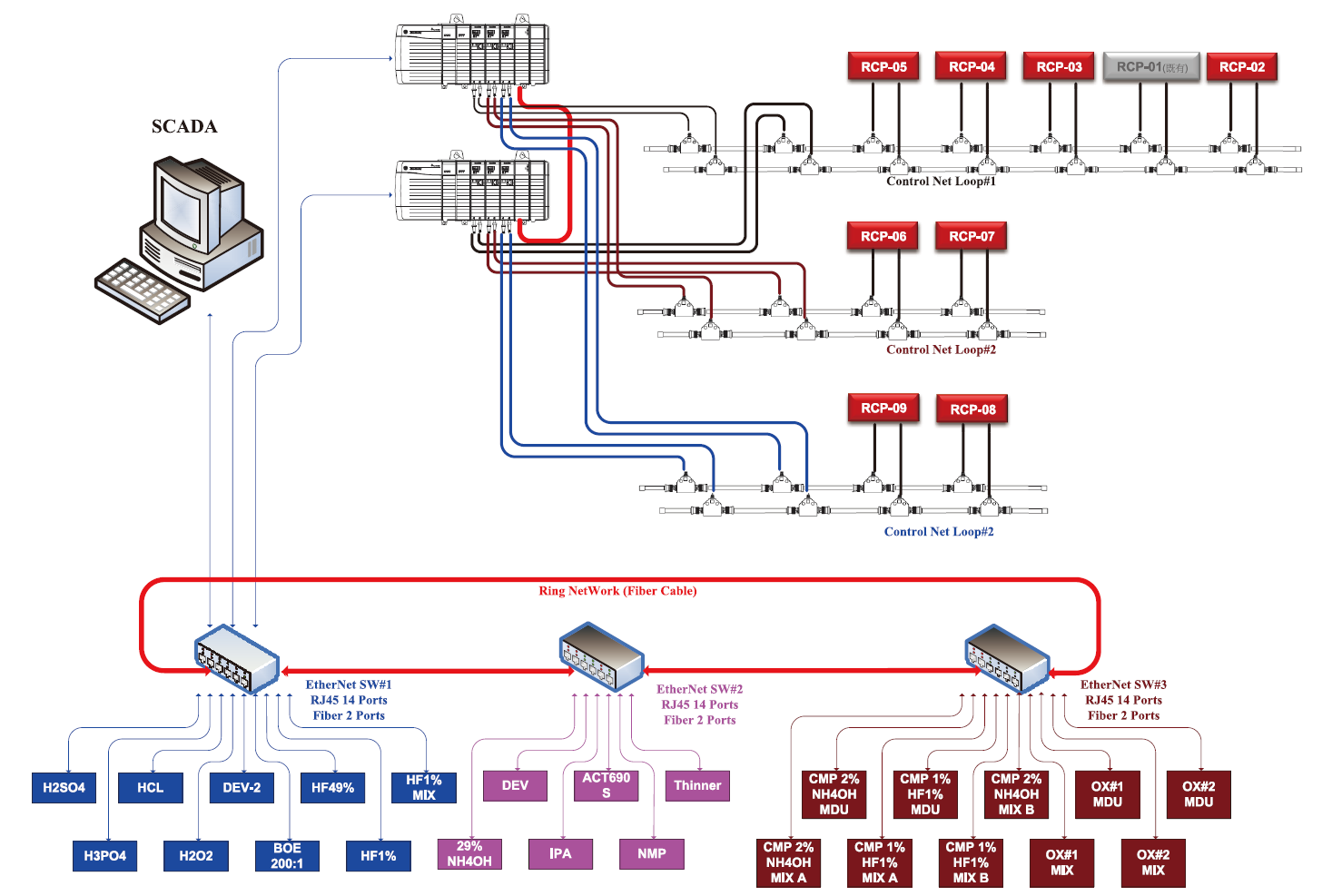
4.2 供應系統升級
單機CDU升級工程最關鍵的步驟在於供應模組將掌管CDU供應的轉換過程,氣源管tie in梭動閥時會使閥件暫時失去功效,故步驟需快速且確實。在要酸訊號線轉移後也必須立即進行測試,確認強供器可運作正常再進行下一步驟,一步一步來才不會出錯。歸功於事前check list的撰寫,仔細思考每一條氣源管及每一條訊號線的轉換工法,不搶快的確實執行,使得工程得以順利完成,達成CDU不中斷供應的電控升級作業。雖此做法比一般back up CDU施作多耗時一天,但相對卻為線上省下了寶貴的三到四天生產時間。此供應模組亦可應用在多種pump base的CDU上,當有電控元件無法修復的情形時,它將是個珍貴的救命法寶。
5. 未來展望與結論
F3雖已在2017完成化學網路汰換、於2019完成了全數20套CDU的PLC升級,但穩定供應的精進之路卻沒有因此停歇,在以上兩大核心工程執行完畢後,電控設備的升級使我們獲得了以往所缺乏的擴充能力,基於廠務設備的首要宗旨「穩定運轉」,我們首先進行緊急應變的功能提升。
- 將chemical back up功能提升到另一個層次。 以往back up的執行須進行 : ⑴人為force要酸相關訊號;⑵現場打開連通手動閥,如今我們設計back up控制盤,將聯通管路的手動閥變更為氣動閥。在一個按鈕的驅動下,利用繼電器完成了要酸訊號轉移及聯通管路的氣動閥開啟,實現了一鍵back up的功能,將back up執行速度由180 秒縮短到3秒。
- 於化學控制室內設置了ICP的ready訊號及氣動閥強供盤,當有誤警報發生時可於fab外快速復歸Ready訊號以及開啟VMB供應閥,此功能亦可將ICP異常的緊急應變時間由300秒縮短為3秒。
綜合以上改善及新功能,化學品供應中斷影響機台之次數已從平均2次/1年下降至約1次/3年,相當於提升了84%的系統穩定度。
最後總結,穩定供應的精進之路仍不可停歇,未來三廠將朝向品質提升的方向努力,化學系統之微汙染一直是老舊設備會面臨到的問題,目前廠內仍有混酸濃度計金屬汙染的隱憂存在,期許在解決自身問題的同時亦能不斷吸收汲取新廠的嶄新知識,融合兩者以找出符合老廠的最佳解法,持續跟上不斷進化的化學品供應世界。
留言(0)