摘要
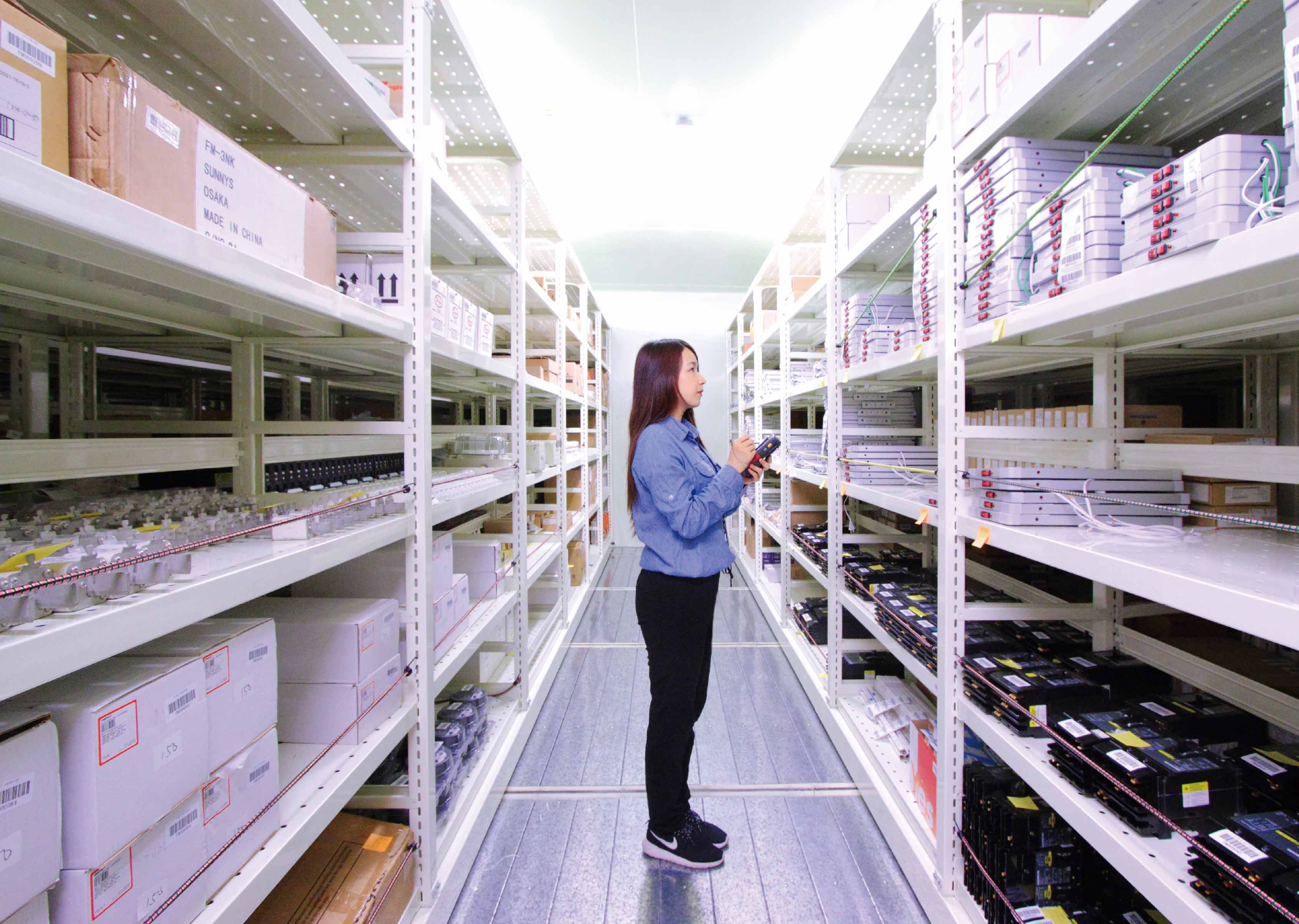
十二吋廠廠務庫房管理之蛻變
一直以來,公司內廠務相關料件皆由廠務部同仁自行負責儲存與管理。隨著廠房逐漸擴充,製程技術持續精進,廠務物料至今在種類、數量與價值上都已到達一定程度,實有必要重新檢討管理的模式與方法。隨著300mm廠務組織的合併,規劃部即著手進行此方面重整,並陸續在2015年中導入全新的管理平台、2016年五月成立專職組織、八月開始竹科實體庫房的運作。本文在此即要和讀者分享,廠務庫房建置的背景緣由、規畫理念、實際執行現況與後續的展望。
前言
公司從二廠開始皆在科學園區內建廠,除了南科在開發初期一次取得一大塊土地,可以在廠區內完整規劃一座中央庫房外,竹科與中科廠區因建廠土地有限,公司庫房僅能依附在廠房內建置,因此在空間的限制下,只能優先儲存與生產相關的物料,如晶片、parts、及一般標準耗材等,其他單位若有較大的需求,僅能自行設法解決。廠務部門負責維持廠房不間斷的運轉,需要大量的耗材、物料與零配件,其項目與分類眾多(如 表1),除MR類部份項目由公司庫房儲存管理外,其他相關料件皆由廠務部同仁自行負責儲存與管理,初期在運作上也並無問題,但隨著公司成長、廠房逐漸擴充、製程技術持續精進,至今廠務物料在種類、數量與價值上都已到達一定程度。
分類 |
公司領料(MR) |
自行採購(PR) |
其他 |
---|---|---|---|
物料種類 |
3F開頭料號 濾網耗材 L開頭料號 PPE防護用具 連身防護衣/頭盔 活性碳口罩 防酸鹼手套 吸酸棉 |
燈管/安定器/指示牌 Breaker/Sensor 皮帶/電磁閥/流量計/小型馬達 Gasket/Swagelok/filter 濾心/閥件/防護用具 大型物料(變壓器/馬達/PIU…) 備用電池 PLC Card |
大型變壓器 Pump Air shower 沖身洗眼器 客製化配電盤 高架地板 工程餘料 |
各廠每年編列了相當多的預算來購買這些備品與耗材,同時也花了相當多的人力在物料的管理上;然而,隨著種類與品項越來越多,問題也隨之發生,包含料件資訊不完整、儲存位置與櫃位紊亂、庫房入出庫報表與盤點記錄也不齊全、安全庫存量未建立導致多餘庫存的產生等種種問題,也因此在面對公司稽核時,會出現料件數量或多或少以及料帳不符的情形。隨著300mm Fabs廠務組織的合併,新廠規劃部即接手重新檢討此部分管理的模式與方法。
導入專業管理平台FAM
在發展300mm Fabs廠務組織One Facility系統平台的過程中,合作的IBM專業團隊即明確指出,公司廠務的物料管理是需要優先改善的項目,並建議導入Maximo系統,整合資產、工作、採購、庫存等管理要項,建立一個專屬於台積300mm Fabs廠務的資產管理方案(FAM, Facility Asset Management),其規劃架構含括資產管理、設備運轉、維護保養(PM)與物料的管理等 圖1。
圖1、FAM 系統架構
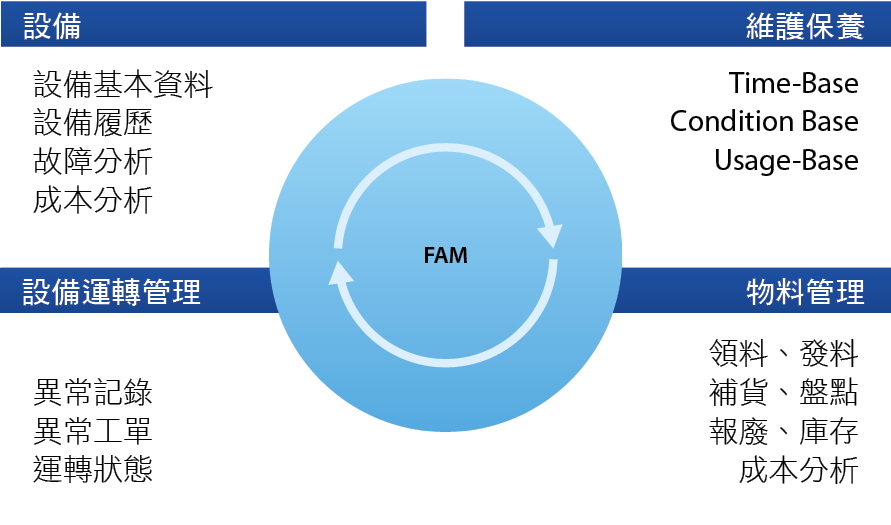
之所以決定使用IBM Maximo系統,不僅是因為其在EAM (Enterprise Asset Management)領域是業界領先的解決方案 圖2,同時也希望藉由IBM有經驗的開發團隊,配合公司需求量身訂做,檢視現行廠務的運作與管理,找出不足與機會並提出改善方法,以達成在單一平台上統合各種資產與維護管理的目標。
圖2、企業資產管理系統調查(Gartner, 2014)
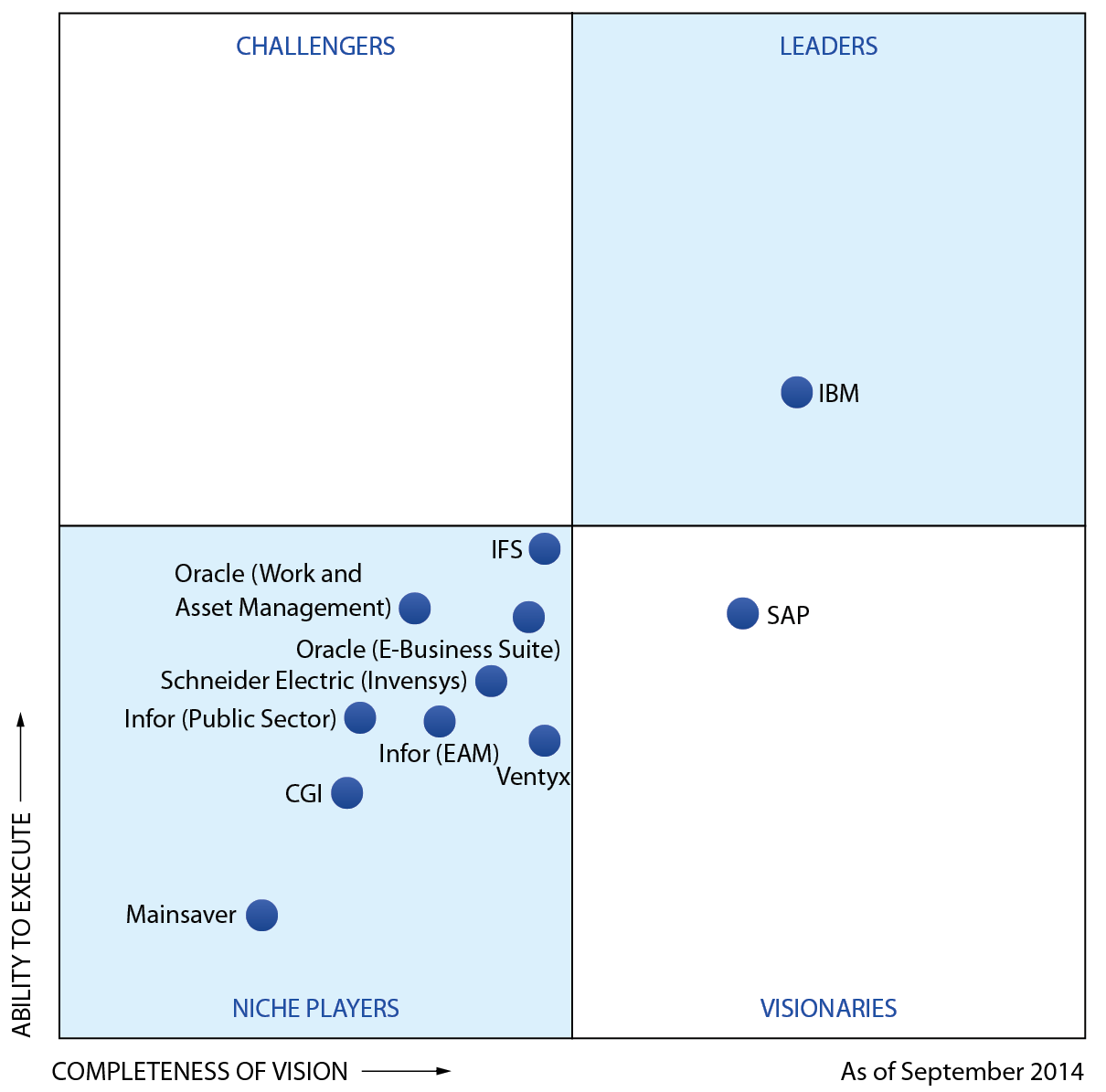
確認系統平台後,便開始分二方面導入,一是硬體部分,包含Barcode、PDA等設備的購買與套用,二是管理流程建立,包含入庫、領料/緊急領料、調撥、盤點等作業,此部分實際執行起來非常繁瑣,我們花了很多時間與各廠的廠庫房管理人員溝通,除配合廠務運轉的特性、考量斷料的風險訂定規範外,最困難的部分,其實是在解決系統改變對人的作業與習慣所造成的影響。
其次是物料料號建立,主要是讓各廠針對自己現存料件作清查,確認規格並建料號於系統,這是必要的打底工作。為了建立這些品項資料,各廠負責人員與系統開發人員耗費了數個月的時間,討論物料邊碼,清點現場料件,找出每個庫存品的廠牌、規格、數量等,再根據原則編碼,逐項建置於系統中。
最後一個步驟是訓練,為讓後續系統能順利運用,在竹、中、南科廠區共舉辦了多場次種子訓練課程與溝通會議,也收到了許多的回饋意見,並為此對系統介面作了必要調整。在參與團隊共同的努力下,系統於2015年十二月正式上線,算是成功的踏出第一步。
成立專職組織
在系統導入初期,廠務物料的建立,都是仰賴各廠區各課負責物料管理工程師或外包人員進行,雖然他(她)們對物料最為熟悉,但因同時負責其他業務並非專職管理物料,也因此衍生了權責歸屬困難、帳料資訊維護困難等管理問題。為能有效且徹底改善此問題,由專人辦理庫房管理業務,妥善管理料件的入出庫、確保正確的管理流程並能即時提供料帳相符的資訊,專職的物料管理團隊是不可或缺,也因此新廠規劃部於2016年五月成立了廠務庫房管理課。
面對跨廠區的運作,對庫房管理而言是一個挑戰,因此在思考這個問題時,是朝向分工型的組織架構規劃 圖3,由管理中心負責統籌擬定物料採購計劃與執行、存貨控管與盤點計畫、料、帳異常追蹤和稽核、橫向溝通與協調竹中南廠區庫房等相關事項,各廠區配置二位管理人員來負責每日收料、發料、配送與執行盤點作業。如此可分工明晰、權責對等並可達到統一指揮的目的,且在有限的人力下發揮最大的組織效益。
圖3、庫房組織圖
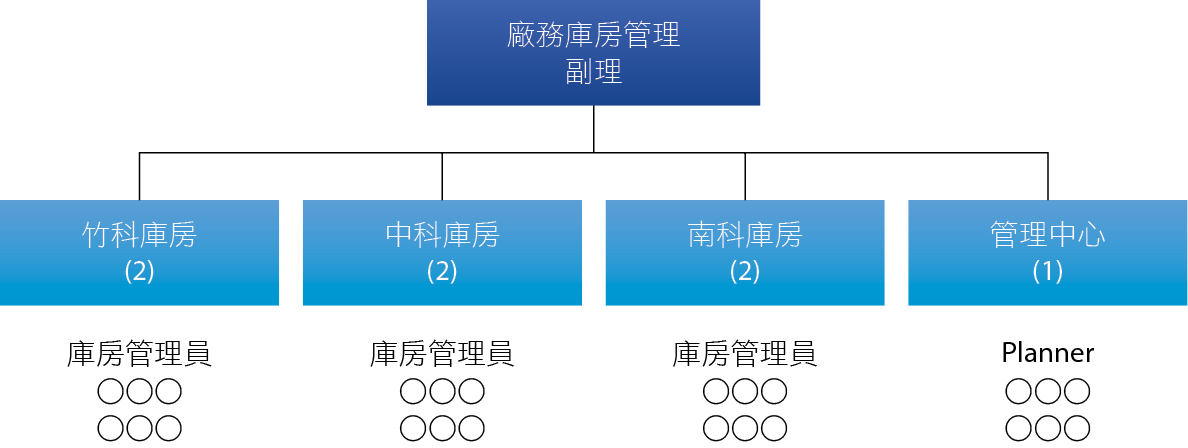
組織成立後的第一項任務,就是針對已輸入系統的數萬件物料進行校正與清查,這是為了降低系統資料錯誤率與有效管制物料的必經流程,雖然繁複耗工,但是卻非做不可。以竹科為例,初期由廠務建置料項數量高達一萬多項,然而校正完後,扣除一些重複與多餘料項,僅餘約三千項,不僅增強了料件管理效率,找不到或找錯料的情形也不再發生。而庫房管理人員也透過與廠務物料管理人員合作的期間熟悉物料規格,並完成不必要與重複料號的修正,在實體庫房完成前,做好入庫前的準備工作。
建置實體庫房
在系統建置時期,曾對當時之廠務庫房進行盤點,發現在各廠區大大小小的儲存空間高達211個;這是很驚人的數字,要改善管理績效,就要從減少庫房數目著手。一個有效管理的庫房,最好是依使用地區,設置單一集中庫房來管理,但廠務管理的物料,相較於公司物料,有特性上的不同,舉例來說,像是廠務會有又大又多之耗材(如FFU/AMC filter、PIU等),或是太重搬不動之備品(如變壓器、Pump等),雖然集中管理有其好處,但考慮到領用時之人力耗損,不得不務實的在各使用廠區另外設置一個在線庫房(稱之為線邊倉)。
在此取得有效管理與使用效率的雙重考量下,300mm Fabs廠務實體庫房的架構將依使用型態的不同規劃,於竹、中、南科廠區各設置一座中央庫房並搭配各廠設置一座線邊倉,互相支援,取代原本各廠散落設置之220座倉庫 圖4。
圖4、庫房架構圖
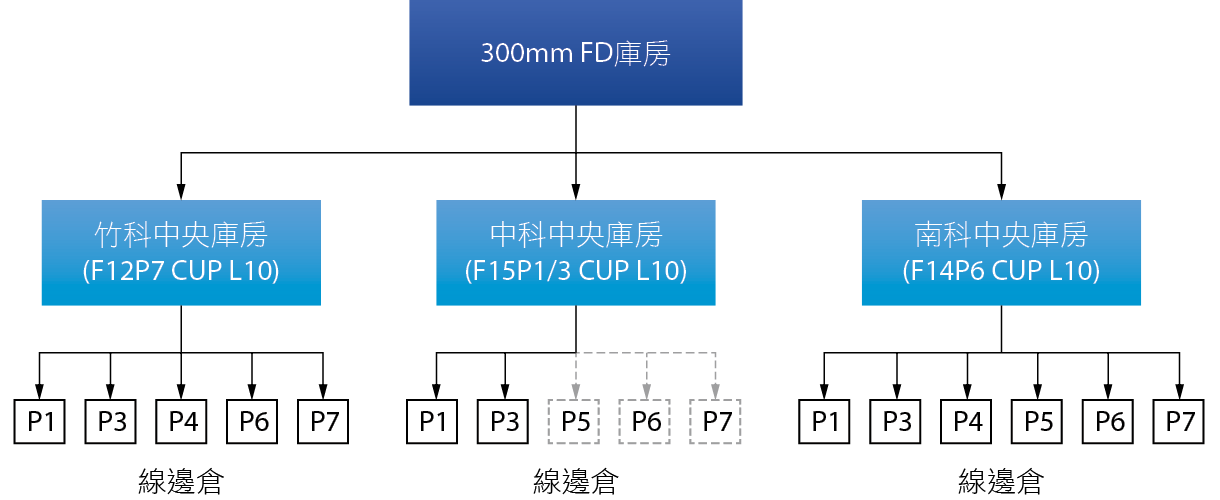
庫房設置的地點是另一個難題,在空間有限的既有運轉廠區,如何找到適合的空間呢?主要考量點在動線與空間管制上,動線需順暢鄰近碼頭以利未來貨車上下貨與物料的入出庫,空間則須完整獨立以方便物料與人員管制。在各廠廠務人員的協助下,看了很多地點也規劃了許多方案,最後將中央庫房設置於CUP一樓的冰水機房剩餘空間,參照公司庫房硬體建置規格,以防火隔間與標準料架設計來進行,在儲位規劃上,因為受限於有限空間要達到最大儲量,採取的是調整儲位的設計、減少走道與不必要的空地,與設計移動櫃,增加儲位密度來解決;整個下來,雖用地未增加,但儲位數增加了約1.5倍,也降低了設置成本。在廠務人員多方支援下,於2016年七月起於竹科開始陸續將各廠實體庫房建置完成並開始入庫納管 圖5、圖6。而線邊倉設置則是在Fab非裝機區域的空間,因MAU區料件最多,所以規劃上也以該區為主,利用隔柵圍籬做管制並收納物料 圖7。
圖5、竹科中央庫
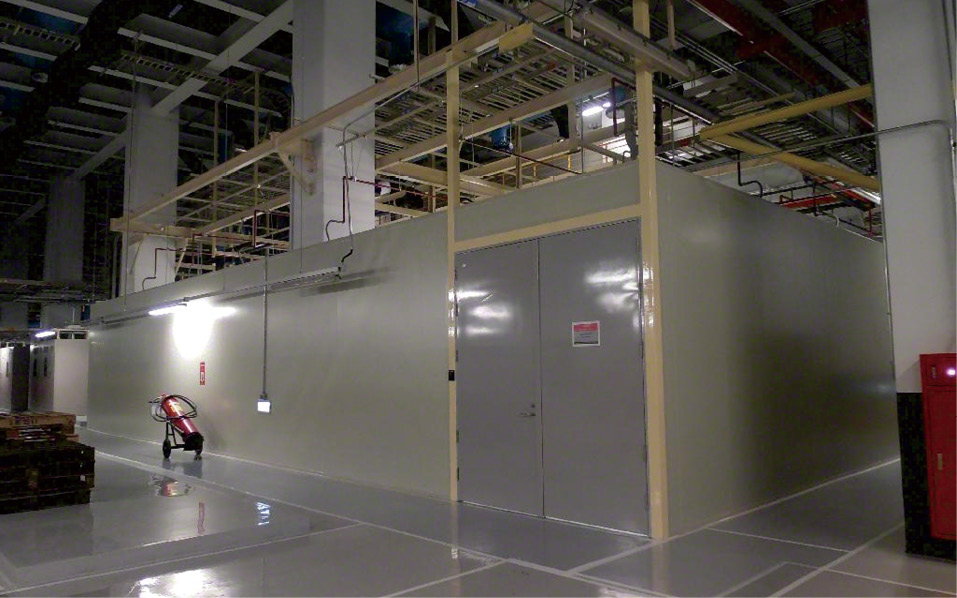
圖6、竹科中央庫房內部儲存現況
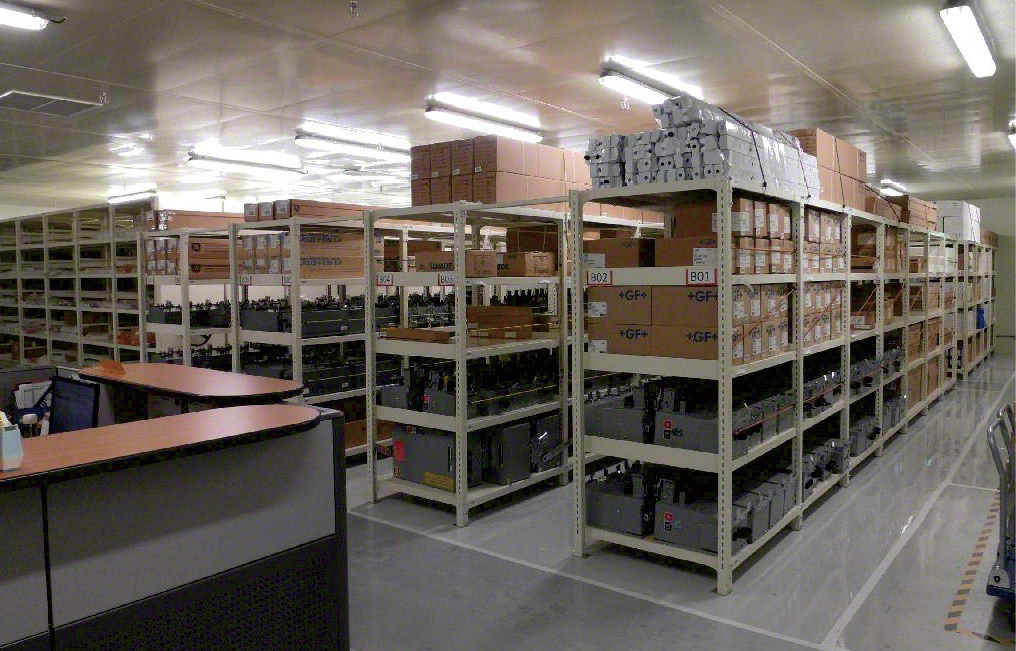
圖7、十二廠第一期Fab L40 線邊倉圖

相較於從前廠務料件的儲存,實體庫房的建立,在消防、空調、櫃體、門禁等方面,均以高規格的設計標準來規劃,符合公司風險與安全控管的要求(RM&ISEP),不僅達到了料件管控的目的,同時也確保了儲放的品質與安全性,在長期運轉支援上,也因為位置統一與櫃位明確,不會造成找不到料或料件損壞,提高了廠務設備維護保養的妥善率,強化了運轉的成效。
實際執行現況
庫房自2016年七月物料入庫後便開始正式運轉,提供各廠領料入庫等服務。至目前為止,以竹科廠區庫房來看,經常庫存量將近五萬件,主要是以照明與濾網類為大宗 圖8,入出庫作業則相當活絡,每月平均有150筆、600項次以上之入出庫作業,總出入料件數量迄十一月底已高達15萬件,在這麼大量的倉儲作業下,人員時間的調派就相形重要。為了兼顧中央庫房與各廠線邊倉,目前採取的是分倉庫,定時定點方式來解決,例如上午均在中央庫房入庫發料,下午則固定時間於線邊倉駐點提供現場領料,這樣可以讓庫房運作固定下來,人員也不會因為至各廠應付領料,趕得人仰馬翻。
圖8、竹科庫房庫存現況

以本公司各廠區廠房配置來看,不管是十二廠區、十四廠區甚至未來十五廠區,都會面臨一個問題,那就是物料配送。依目前各廠間的距離,從幾百公尺到幾公里,如讓各單位自行取料,在人力上是一種浪費,在參考公司晶片車運作模式後,採取配送車每日巡迴發料方式解決,可提高運送的品質與料件的安全性,同時也因主動將料件送至使用者手上,降低廠務工程師管料取料的負擔,提升運轉效率。
除了日常的作業外,庫房人員還有一件重要工作,便是整理長期庫存之閒置料件,經由系統資料的核對,針對一些不再使用、規格不符或是庫存過多料件提出清單,與各廠廠務與新廠設計部合作,針對這些料件提出再利用的需求,在出收方都同意的狀況下,進行調撥。這部分可產生的效益也相當驚人,至目前為止,已累計完成約NT$ 150M的資產活化再利用。
在庫房建置的過程中,我們也曾分別就系統開發、請購領料(PR/MR)與管理流程這幾個部分與公司稽核進行討論,除了給予正面的肯定外,公司稽核也提供了必要建議,期望在維持合理庫存與料帳相符基礎上,由系統面與實體物管上雙管齊下,確保執行上不致產生弊端。
後續的展望
經過幾個月庫房的運轉觀察,廠務庫房團隊已初步展現以下成果:
- 物料集中管理,提高物管作業效率。
- 專職分工,服務水準提昇,讓廠務能專注在本職上。
- 掌握料件庫存,逐漸減少資產積壓。
- 整合各廠資源,進行活化資產。
在各廠庫房陸續完成與物料入庫,後續重點將放在物料的合理儲存量與使用分析,讓相關管理能漸漸上軌道。再接下來的挑戰,就是要將裝機使用所採購的料件(Hook-up material)納入管理,這部分主要是一些高潔淨的氣體管材(BA/EP, Piping & fitting)與管路錶頭類(如差壓計、流量計)等,屬於與廠務同質性較高的料件,儲放於潔淨室下迴風層(Sub-Fab),目前已有專人負責,依序由系統導入、流程建立開始做起,一步步將其物料納入管控範疇。
隨著庫房的完成,物料的納管,管理上已進入過渡階段的後半段 圖9,未來將持續與現行公司相關流程做整合,包括MR/PR、採購進料,並結合設備PM模組進一步做好廠務資產管理,最終期望能在明年底回歸公司資材組織,由公司庫房正式接手廠務庫房。
圖9、物料管理進程與目標

結論
孫子兵法提到的「全勝」概念,主要在整合既有資源,創造個人與組織最大的利益。廠務庫房在短短的一年之內,自系統發展開始到物料入庫管理,除了第一線系統開發與庫房管理人員的努力外,背後各廠區廠務人力與資源的投入也是成功的關鍵因素。到目前為止僅算踏出第一步,未來還有許多事項需要持續不斷的努力與改善,期望能為公司與廠務同仁創造雙贏的局面。
參考文獻
- A-MCM-03-02-033 TSMC WAREHOUSE MANAGEMENT PROCEDURE
- A-MCM-03-03-023 TSMC WAREHOUSE GOODS RECEIVING C.I.
- A-MCM-03-03-024 TSMC WAREHOUSE GOODS ISSUE C.I.
- A-MCM-03-03-030 TSMC WAREHOUSE ROUTINE OPERATION C.I.
- A-MCM-03-03-039 TSMC WAREHOUSE STORAGE MANAGEMENT C.I.
- F-GBU-03-03-019 TSMC 300MM FABS FACILITY WAREHOUSE MANAGEMENT C.I.
- 平野欲之(原著),葉德芬編譯,庫存管理,臺北市:書泉,2010.
留言(0)