摘要
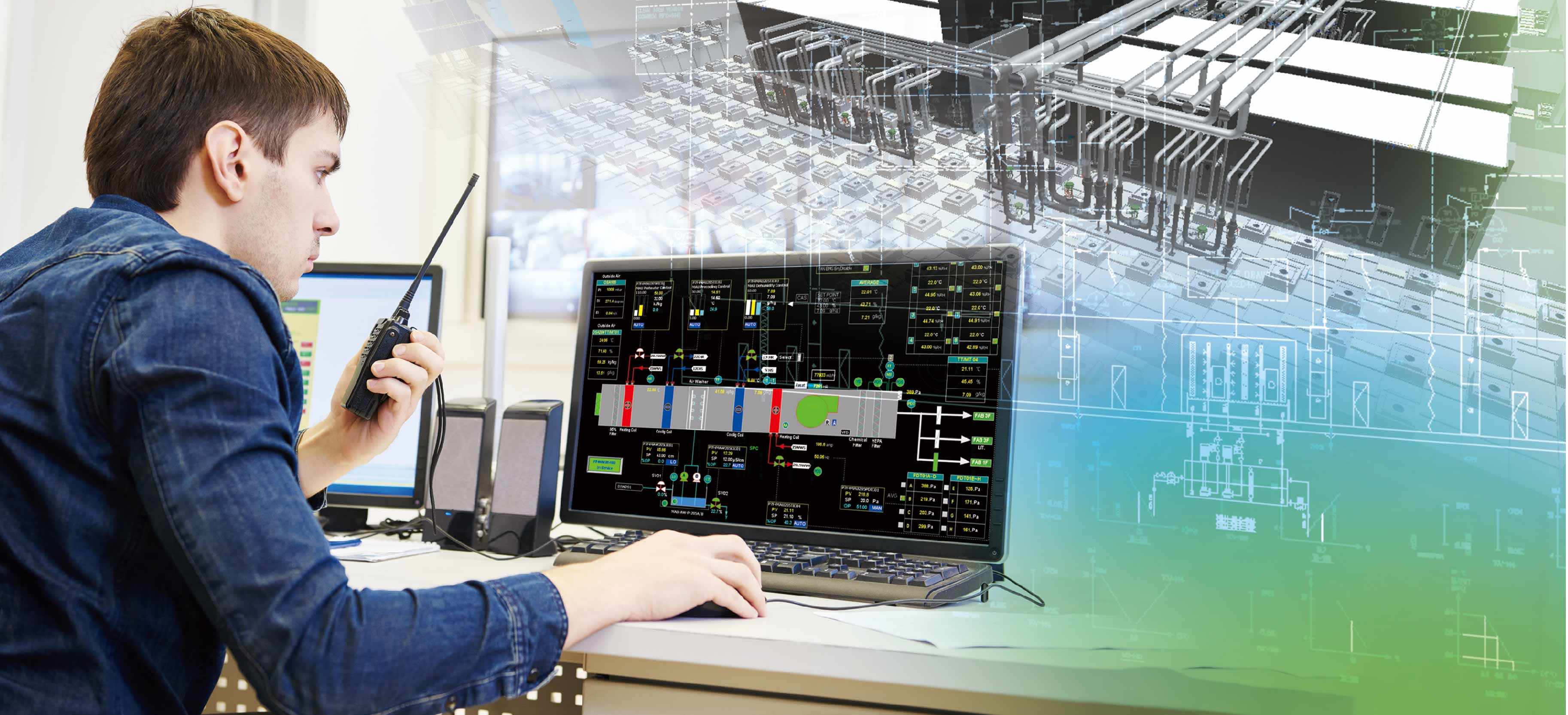
談動態製程模擬技術在半導體廠廠務運轉的應用
本文介紹模擬技術的發展及應用現況,並說明如何透過動態製程模擬技術結合控制系統,來模擬半導體廠設備運轉特性及外在環境變化,建構仿真工廠以提供一個擬真的實戰訓練環境,協助廠務運轉人員快速累積知識與經驗,在面對異常事件或緊急狀況時,能即時做出正確的處置,並期望在未來可以更進一步做為製程虛擬試俥及創新研發的實驗平台。
前言
製程模擬技術的起源與背景
20世紀60年代美國Kellogg公司推出全世界第一套製程模擬軟體Flexible Flowsheet,製程模擬技術至今已演進到了第五代(如 表1)。初期,製程模擬技術只能做到簡單的穩態分析,而今已經可以進行大量且複雜的動態即時模擬,並完整開發出與控制系統緊密結合的平台,讓虛擬工廠(Virtual Plant)得以真正實現。製程模擬在石化、核能、礦業等產業蓬勃發展已久,主要應用在安全評估、環境分析、操作與流程管理、製程優化、知識傳承、及人員訓練六大領域,來協助工廠運作得更安全、更穩定,也更有效率。舉例來說,建廠初期規劃即可藉由製程模擬技術來進行整體的評估,包括系統容量、控制流程以及製程配方等等設計;成廠後可繼續使用在製程改善、風險預測以及人員訓練,不僅可有效縮短產品開發時程與提升工廠運作效能,還可達到防範於未然的效果,減少不必要的風險損失,為產業創造更大的經濟效益。
項目 |
特點 |
公司/研發機構 |
產品名稱 |
---|---|---|---|
第一代 (20世紀60年代) |
不完善的數據庫,簡單的數學模型,以烴類加工為主,物料及能量計算 |
Kellogg University of Houston |
Flexible Flowsheet CHESS |
第二代 (20世紀70年代) |
較完善的數據庫,複雜而精確的數學模型,擴展至氣-液兩相、物料平衡及熱平衡計算 |
Monsanto Simulation Sciences |
FLOWTRAN PROCESS |
第三代 (20世紀80年代) |
擴展至氣液固三相製程,並新增經濟評價,工況分析 |
Aspen Technology Hyprotech |
Aspen Plus HYSIM |
第四代 (20世紀90年代) |
穩態和動態集成,從離線的單純穩態計算走向與工業裝置緊密相連的動態資料交換模擬 |
Hyprotech Aspen Technology SIMSCI |
HYSYS Aspen Custom Modeler, Aspen Dynamics, PolymersPlus ProVision |
第五代 (21世紀10年代) |
將動態模擬提升到即時反應的層次,並且開發了與控制系統緊密集成的平台 |
MYNAH Technologies Honeywell Invensys Kongsberg SIEMENS |
Mimic Simulation Unisim Suite Dynsim Suite K-SPICE ASSET SIMIT |
動態製程模擬技術在半導體廠務的應用
儘管動態製程模擬技術可以帶來如此多的好處,但綜觀國內外半導體廠至今卻尚無任何公司將其應用於廠務製程方面。推究其原因,主要在於半導體起步較石化等產業晚了數十年,直到近幾年方真正開始有所接觸與了解;再者,模擬系統開發較強調協助優化複雜製程的設計,而半導體的廠務製程相對於石化廠較為單純,建置效益較不明顯,也就較不受到關注。此外,模擬系統開發的昂貴造價以及之後的修改維護也是原因之一。
近幾年來,隨著模擬軟體的功能越趨完善以及擬真度的大幅提升,讓使用者相對過去能更容易的建置模擬系統。工廠安全意識的提升促使將模擬系統應用在人員訓練上,降低誤操作的發生。利用其建構的仿真環境,讓操作人員進行各種應變演習,能有效的提升緊急應變能力,減少誤操作的可能性。據OREDA 2003年研究報告顯示[2],在廠房運轉中,造成工廠虧損的原因主要包含了機械故障(Mechanical Failure)、操作錯誤(Operator Error)、製程失序(Process Upset)、自然災害(Natural Hazard)、設計錯誤(Design Error)等等,其中以人為操作錯誤造成的損失金額為最大(如圖1)。而半導體屬於高投資的產業,一旦人為誤操作導致系統異常或設備停機,損失往往非常嚴重,動輒以千萬計價。有鑑於此,本公司於2015年開始嘗試導入動態製程模擬系統,初期我們將重心放在廠務人員訓練上,建置仿真的系統運轉環境進行實戰訓練,以最有效率的方式協助人員快速累積知識與經驗,在面對異常事件或緊急狀況時,能即時的做出正確的處置。
圖1、工廠營運虧損原因比例表
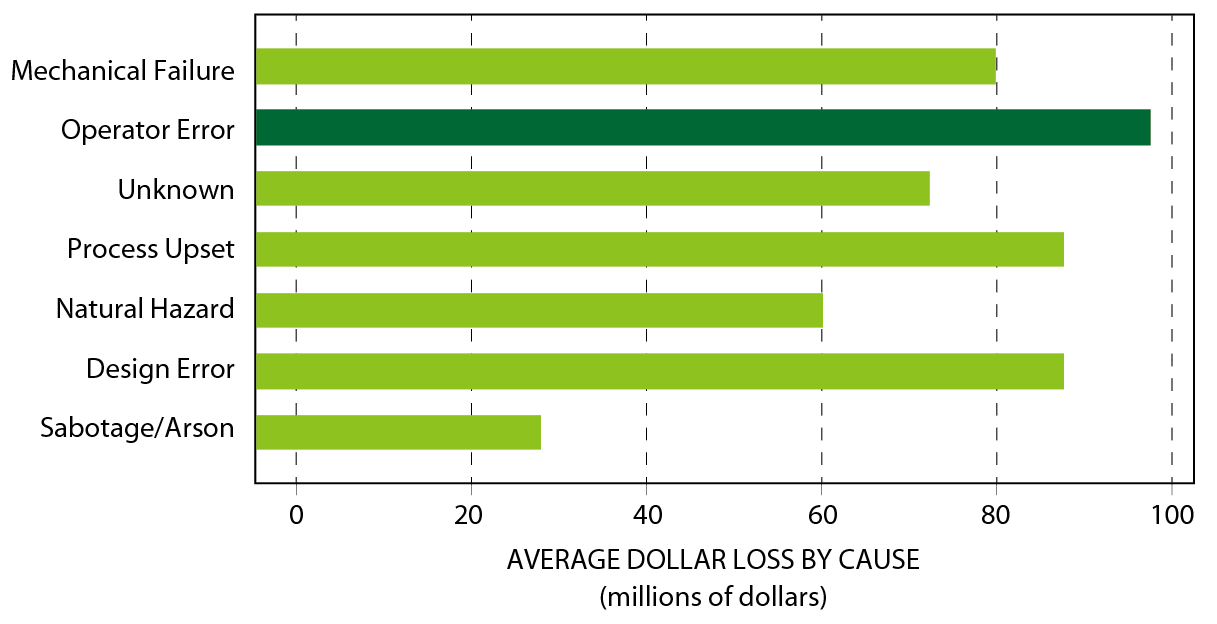
本文將以此為題展開後續之探討,並以晶圓廠最重要的心臟 - 無塵室空調系統以及緊急排煙系統之模擬做為介紹案例。
什麼是動態製程模擬系統
製程模擬是綜合了熱力學、化學工程、系統工程、計算方法等學科,透過電腦軟硬體對系統的設備、製程以及整個運作流程進行描述的一項技術[1][3]。模擬系統的架構主要分成兩部分 圖2,一是自動化控制端的模擬,包含了虛擬控制器(Virtual Controller)、控制策略(Control Strategy)及輸入輸出(I/O)信號的規劃;二是製程端的模擬,包含了製程模型(Process Modeling)及I/O模型(I/O Models)的建立。其他像是快照[註1]、模型提/降速、劇本考核評分,指導者介面功能模組等附屬功能,亦包含在其中,可用以協助人員的訓練。
圖2、模擬系統架構
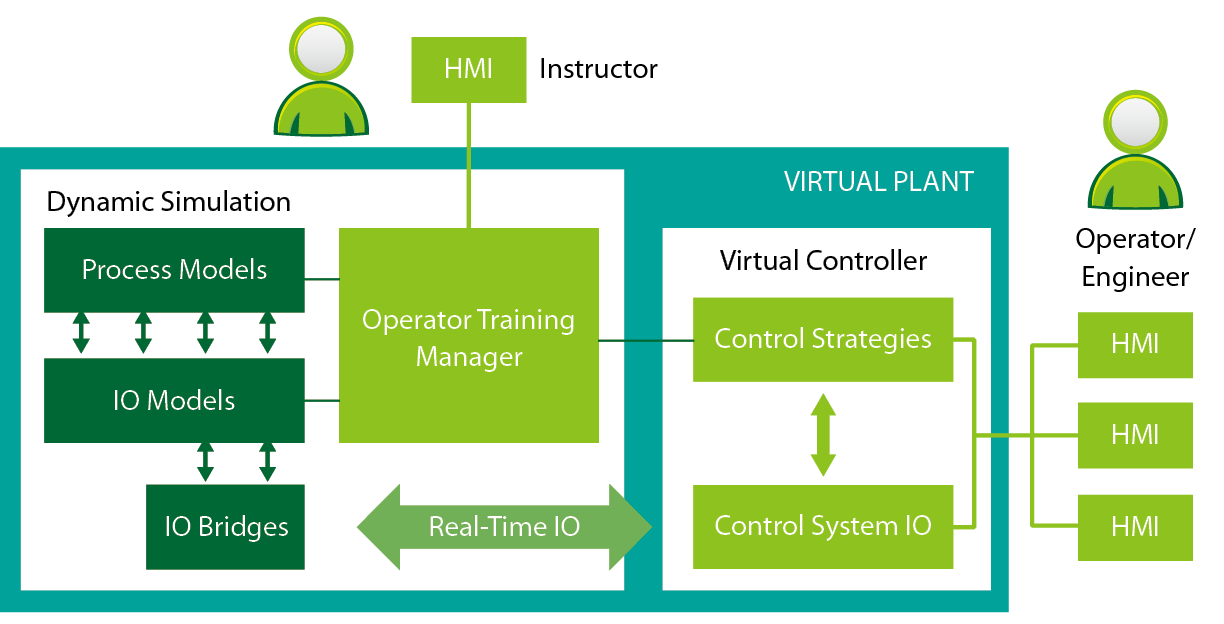
模擬器運作的基本原理,主要是透過製程模型來模仿如馬達、熱交換器設備和外在環境的特性,取代它們在真實環境下運作所產生的結果,再透過與控制系統連結進行資料交換。簡單來說,就是可以使控制系統在不連接任何實際硬體設備或裝置的情況下,透過模擬器來模擬設備及偵測器的訊號,呈現真實工廠的運行狀況。而動態製程模擬不僅模擬了穩態點的狀態,還能模擬在達到穩態前後的動態改變過程,即時呈現擾動事件發生前後的變化。換言之,就是能讓模擬的狀態隨著時間改變,達到即時反應的效果[1]。
如何建構動態製程模擬系統
要建立一個符合需求的動態製程模擬系統,必須經歷以下七個步驟,包含定義範圍、收集資料與分析、規劃製程及設備模型特性方程式、建立製程模型、建立IO模型、開發劇本及評分模組,和最後的整合測試與結果分析 圖3。
圖3、模擬系統開發流程

- 定義範圍:定義包含邊界條件、功能、所需要模擬的狀況,以及訓練用的劇本。
- 收集資料與分析:此步驟需收集製程設備與模擬功能相關的設計資料,以及系統實際運轉數據做為參考。
- 規劃製程及設備模型特性方程式:歸納出元件特性及設備運轉曲線的數學函式,確認各段製程變因以及邊界條件的假設。
- 建立製程模型:透過模擬軟體進行設備與製程的模型建立。
- 建立IO模型:連接製程模型與控制系統的訊號,進行資料的交換。
- 開發劇本及評分模組:客製化建立所需的劇本及評分模組,包含講師與受訓學員的人機介面。
- 整合測試與結果分析:與系統實際數據比對,反覆測試與調整,提高擬真度。
實際案例應用─無塵室空調及排煙系統
維持一座半導體廠房的正常運作是需要由多個的廠務系統共同相互配合[4]。雖然全域模擬可以提供最完整的訓練環境,但考量成本效益,我們優先從重要的廠務系統開始著手,像是廢氣處理系統(Air Abatement System)、製程冷卻水系統(Process Cooling Water System)、氣體氣瓶櫃供應系統(Gas Cabinet Supply System)以及無塵室空調與緊急排煙系統(Cleanroom HVAC and Fire Desmoke System)等等。而無塵室是半導體晶圓生產最重要的地方,其溫度、濕度或壓力若不穩定就會對整個產線造成極大的影響。本文選擇無塵室空調 圖4及排煙系統來說明開發流程。
圖4、無塵室空調架構圖
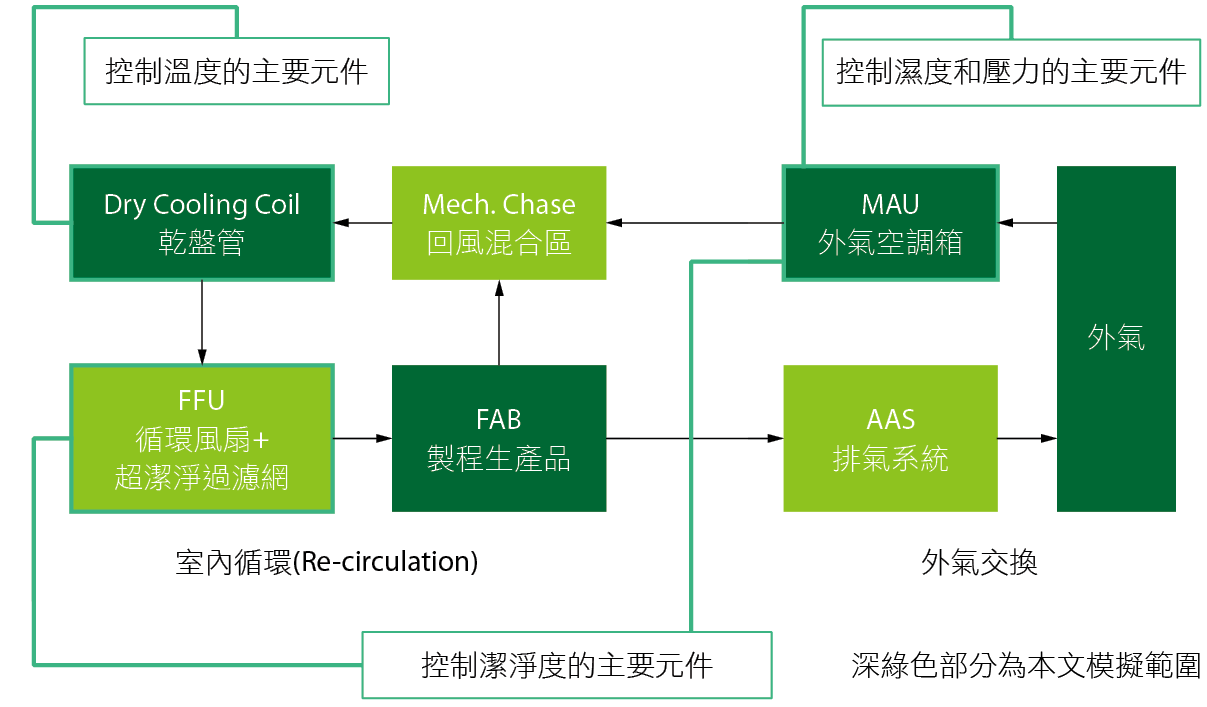
定義範圍
因無塵室各區系統的操作方式及內部環境大多相同,考量開發效益,我們選擇模擬製程中最重要的黃光區 圖5,包含了4台外氣空調箱(Make-up Air Unit, MAU)、60個風門、31個偵測器(包含溫度、濕度、以及壓差)、6個控制溫度調節的乾盤管(Dry Cooling Coil, DCC)以及無塵室的空間。其他假設與邊界條件,包括了像是外氣壓力的大小、系統初始狀態和空氣為理想氣體等等,此外,訓練考核的內容,如突發狀況、應變步驟、完成時間及評分條件等等 表2,也都必須在此階段被定義清楚。
圖5、黃光區無塵室內相關聯動設備及風門
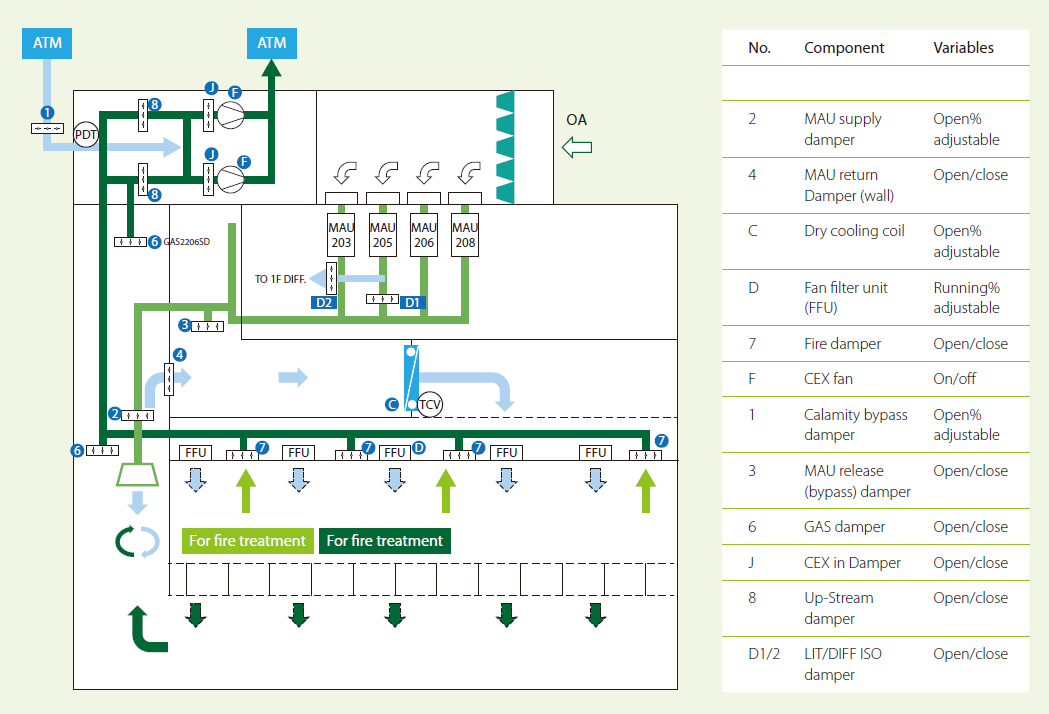
劇本名稱 |
溫度傳送器故障 |
---|---|
初始狀態 |
黃光區MAU (203/206/208/205 backup) 所有變頻器( 4 SETS )轉速設定在Manu Mode 無塵室壓力(P7F3LIT201PDI01)在Manu Mode, CR pressure = 40 Pa MAU P7F4MAU206TIC03 SPC控點勾選P7F3LIT201TIC04;改選2號溫度傳送器 |
狀況 |
P7F4MAU206TIC03溫度傳送器故障,需選用其他偵測器 |
處理需求 |
回復時間780秒內 |
處理程序 |
1. 確認MAU206 TIC03已切換至MANU mode;MAU206警報全數隔離 ( Score : 10%, Time : 90 secs ) 1.1 觀察TIC03歷史趨勢圖(克數與閥開度) 1.2 確認閥開度已維持故障前的數值 2. 切換目前使用的溫度傳送器(從2號改成1號)手動調整TIC03 OP%… ( Score : 20%, Time : 600 secs ) 2.1 手動調整TIC03控制閥開度 2.2 監測控點溫濕度(P7F3LIT201TIC04/MI04) 2.3 針對No.1 TIC03依據現場溫溼度調整SP值 2.4 調整完成後將TIC03切回Auto mode 3. 待現場溫溼度回至基準後,將MAU206切回CAS ( Score : 20%, Time : 90 secs ) 3.1 確認CR溫溼度(P7F3LIT201TIC04\P7F3LIT201MI04)回至基準 3.2 確認新調整後的SP不會觸發P7F4MAU206TIC03上下限警報, 若超出警報範圍需修改上下限 3.3 將MAU206警報隔離全數解開 |
評分規則 |
*劇本執行時最低要求限制( Critical Score ) 1. 如果以下任一項目發生,扣除30%的分數 P7F3LIT201MI04 PV out of +- 1.7% of SP P7F3LIT201TIC04 PV out of +- 0.5°C of SP 2. 如果以下任一項目發生,扣除20%的分數 P7F4MAU206TIC03觸發上下限警報(+- 0.5g/kg) |
收集資料與分析
問題及範圍確定後,接下來就需要收集系統設計資料,以及模擬所需的現場實驗數據,像是P&ID (Piping and Instrumentation Diagram) 圖6、設備或元件運轉曲線 圖7、PFD (Process Flow Diagram)、空氣線圖等等,以協助模型的設計及後續程式邏輯的撰寫。而無法取得的實際運轉數據可根據經驗或者其他相關實驗數據進行假設,並透過第一原理(First Principle)[註2]來協助推算,當未來取得真實運轉數據後再進行修正。
圖6、無塵室MAU 空調P&ID
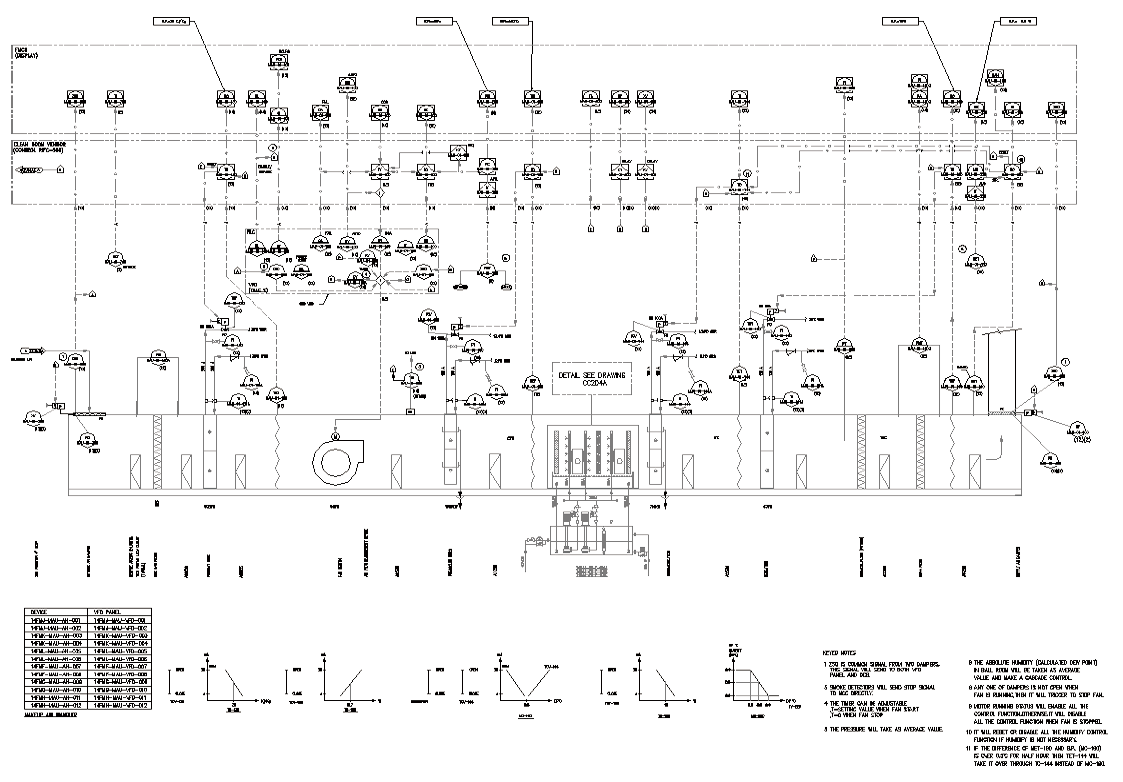
圖7、風車運轉特性曲線
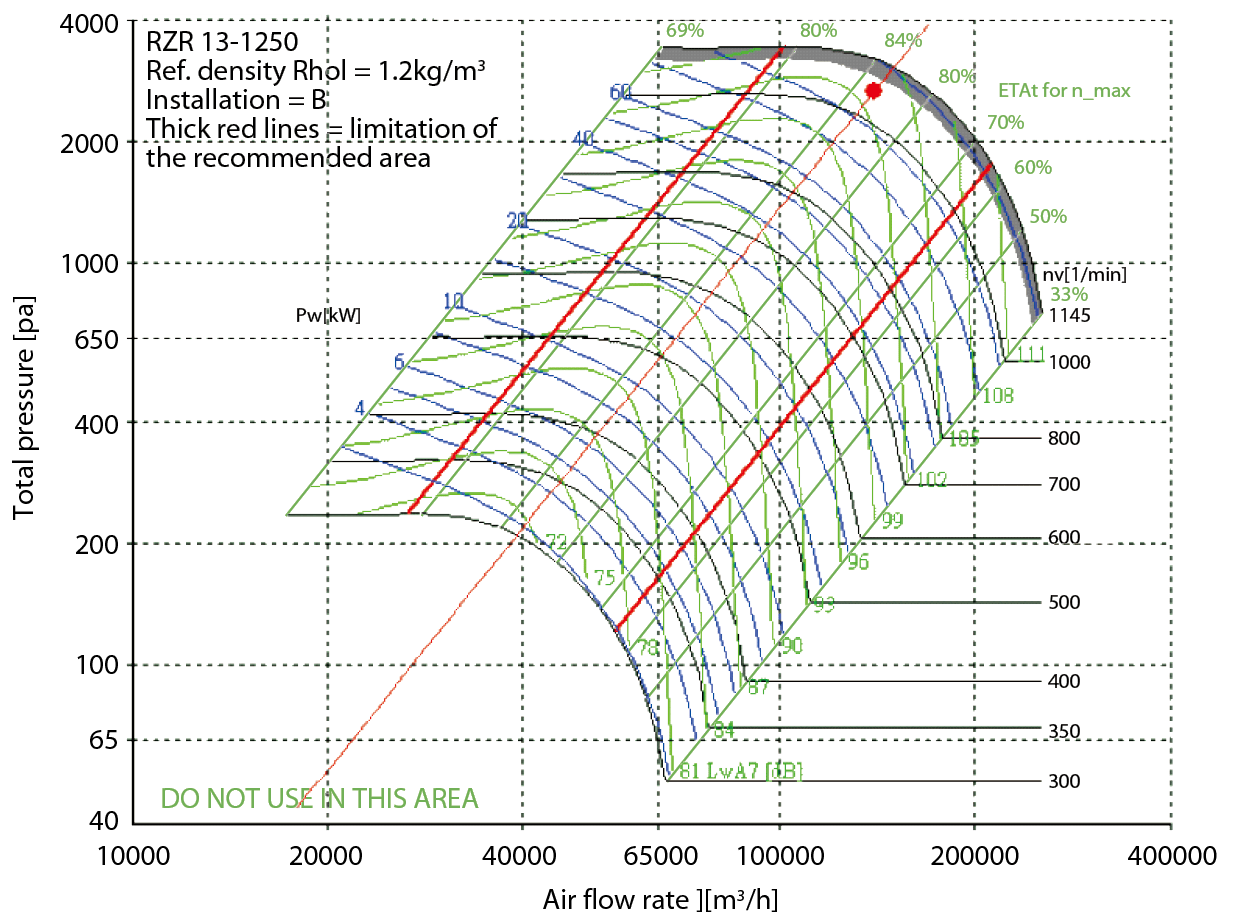
規劃製程及設備模型特性方程式
製程流程的分析與數學模型的規劃,包含了模擬範圍的邊界條件及各設備的運轉特性方程式。現實製程中不但有多重變因,彼此還環環相扣,因此要模擬參數的運作變化是非常複雜的。在大多數情況下,我們需要以第一原理為準則,同時考慮製程中的其他變因來調整模型。我們將無塵室前端的空調送風MAU系統拆解成七道程序 圖8,包含了外氣狀態、預熱、預冷、水洗、除溼、再熱、風扇的模擬,無塵室內則包含了乾盤管、風車與各風門的相關連動 圖9,此外,無塵室空間距離、轉態處的熱平衡及能量守恆變化等變因亦被納入,歸納出不同控制程序的特性曲線與計算式 圖10。
圖8、MAU 模擬系統七道模擬程序對照圖
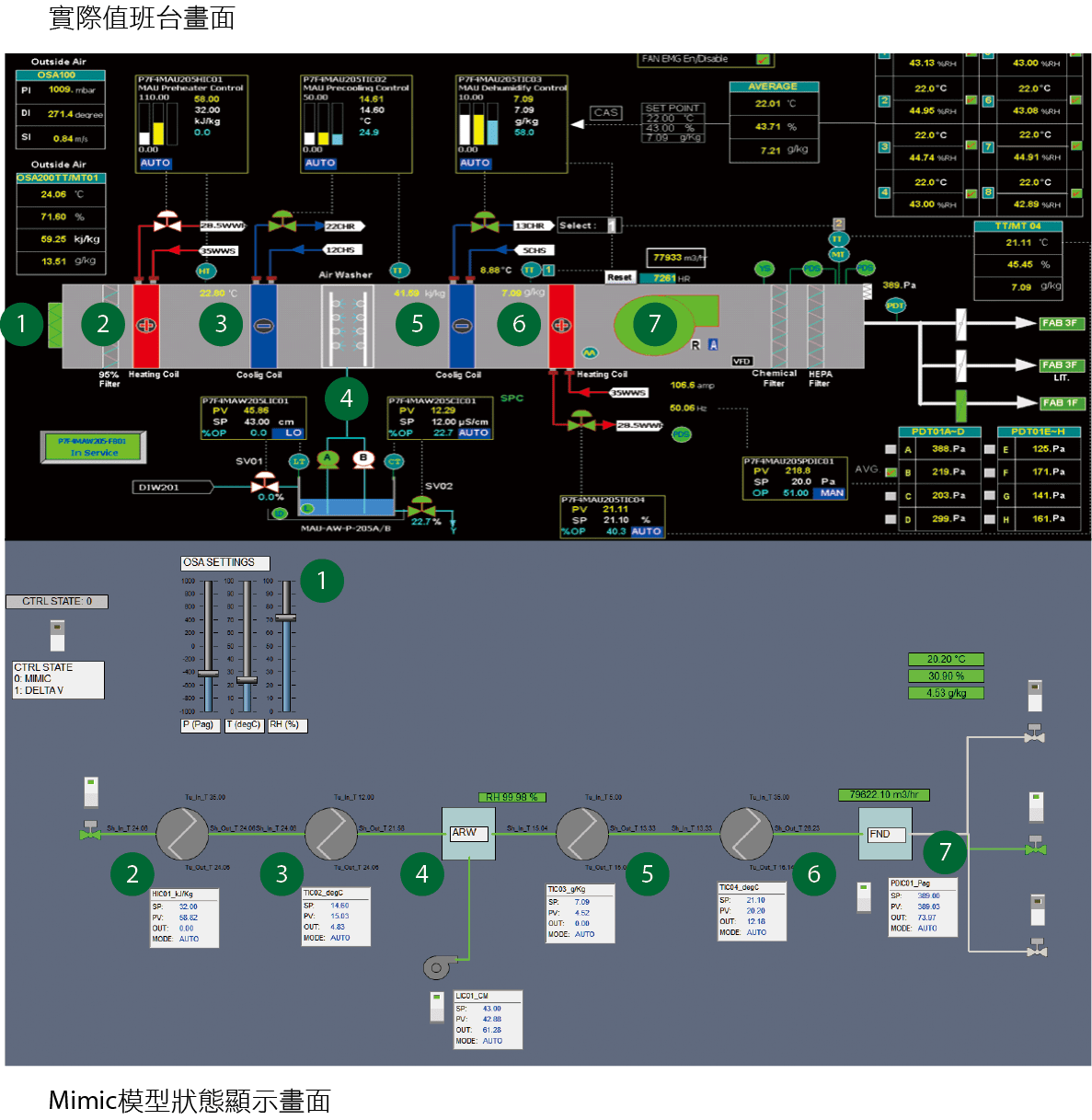
圖9、無塵室乾盤管、排煙系統及其相關聯動閥門對照圖
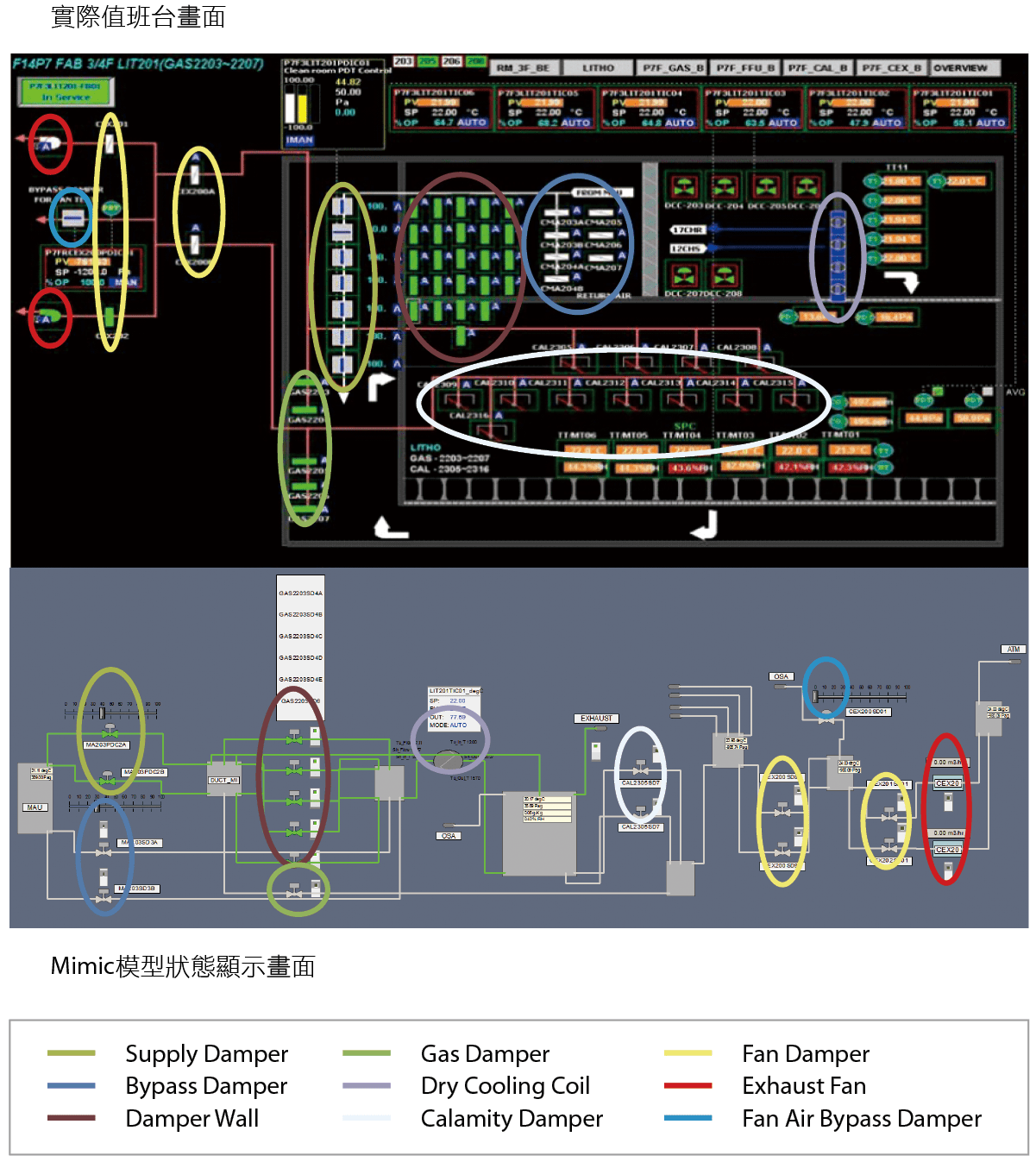
圖10、冬季MAU 設備內盤管於空氣曲線趨勢圖
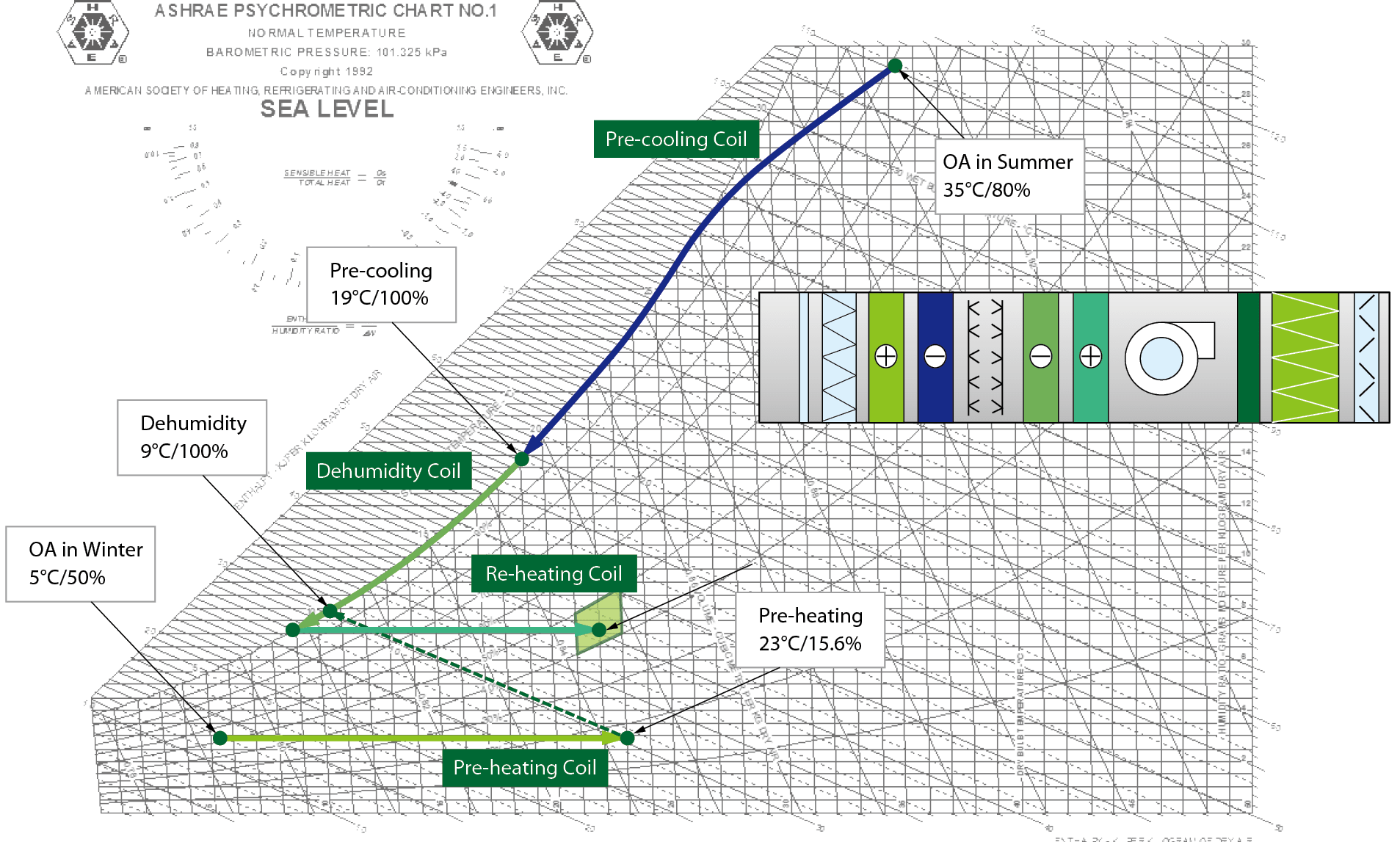
建立製程模型
使用模擬軟體建立製程模型時,除使用軟體所提供的基本功能模組外,還可以自行定義計算式的功能模組來增加程式撰寫的靈活性。但此種作法將會消耗更多系統效能,當模擬範圍變大或運算需求增多時,可能因系統負荷過重而導致反應速度變慢,影響到模擬的結果。進階建模元件(如Mimic的Advanced Modeling Objects, AMO),提供了熱力學屬性數據庫和動態流量解算器等成熟的計算工具,讓使用者只需輸入特定的參數即可根據設備上下游條件自動計算出即時的動態變化值,省去大量且複雜的特性曲線推導運算 圖11。以MAU中的預熱程序為例,只需使用單一熱交換器功能模塊(Dynamic Heat Exchanger, DynHX),輸入設備參數即可完成預熱程序的模擬。此外,此類元件還可依實驗數據進行補償,如管道中的K factor,可讓使用者根據不同材質,來進行阻力係數的調整,最後再配合實際實驗數據修正模型功能及反應速度。
圖11、MAU 製程模組主程式規劃
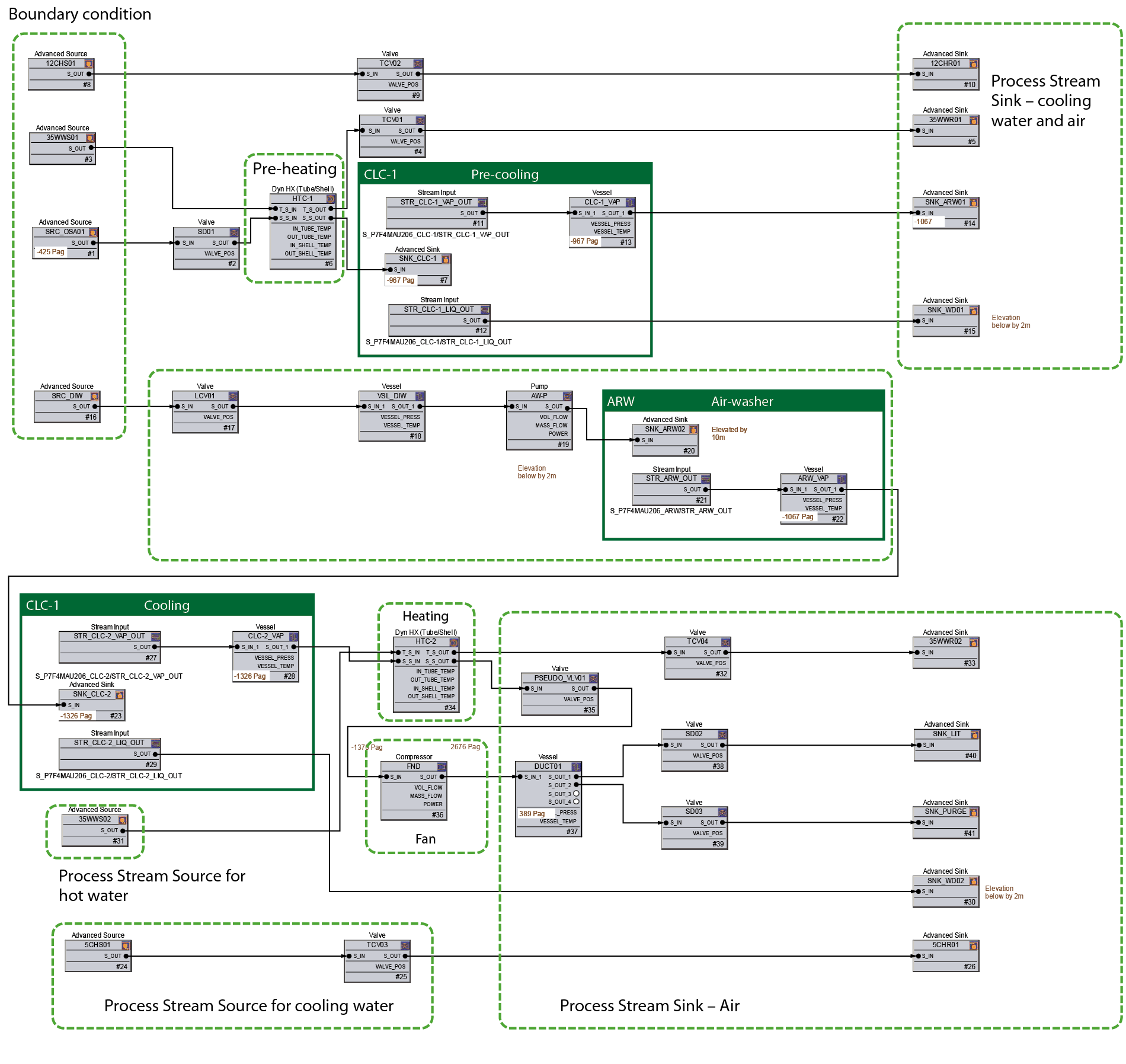
建立IO模型
當製程模型建立完成,接下來就要連結控制系統進行資料交換。製程模型模擬的數值及狀態,透過OPC即時傳送給控制系統,同樣控制系統端的資料透過相同的方式回傳給製程模型。此次的無塵室空調及排煙模擬系統共使用了368個虛擬I/O點與控制系統進行連接 圖12。
圖12、IO 映射定址編輯
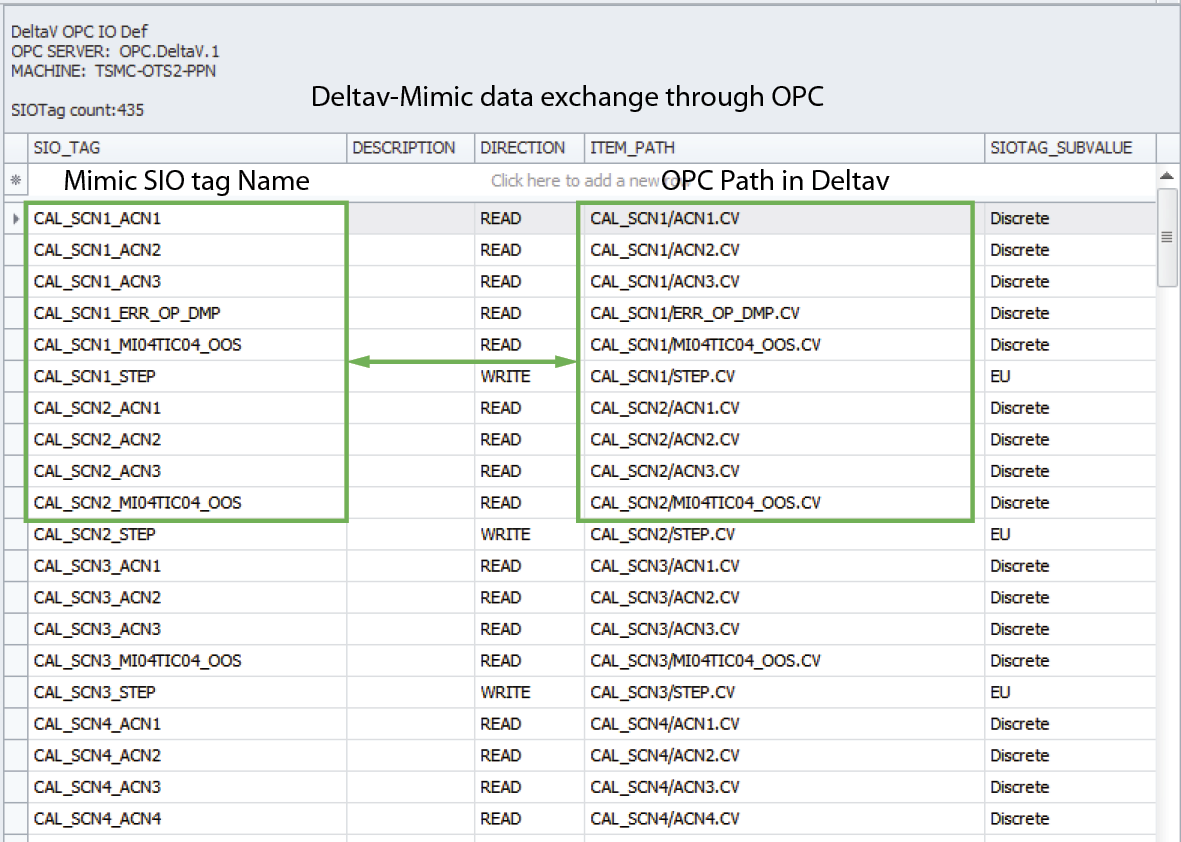
開發劇本及評分模組
透過模擬軟體內建的操作員訓練管理介面(Operator Training Management, OTM)功能模組,可進行劇本與評分標準的規劃,使系統觸發預先建置的各種突發狀況,如設備故障、火警或氣體洩漏等等,以此來檢測受測者是否能在限定的時間內正確完成所有應變步驟。此外,客製化的指導者介面 圖13,將協助導師觀看學員在系統上的應變操作行為,給予適時的糾正。
圖13、指導者操作介面
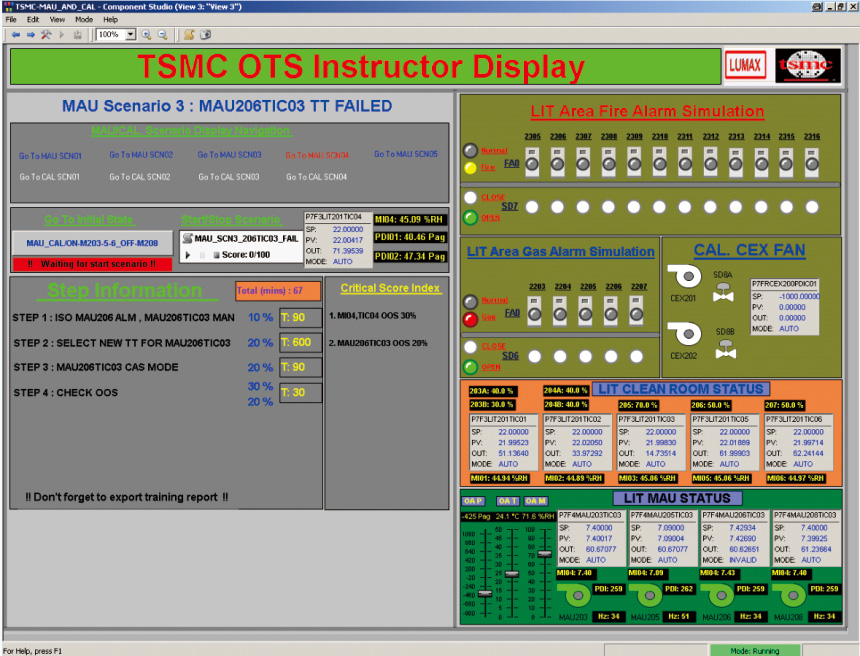
整合測試與結果分析
本階段為系統開發的最後一個階段,目的是將所蒐集到的運轉實際數據與模擬模型所產出的結果進行比對,透過反覆的測試與參數調整,達到所需要的擬真度或縮短製程模擬的反應時間,提升訓練的效率。而透過學員考核的測試報告 圖14可了解其對異常發生應變的熟悉度與能力。
圖14、模擬系統考核報告
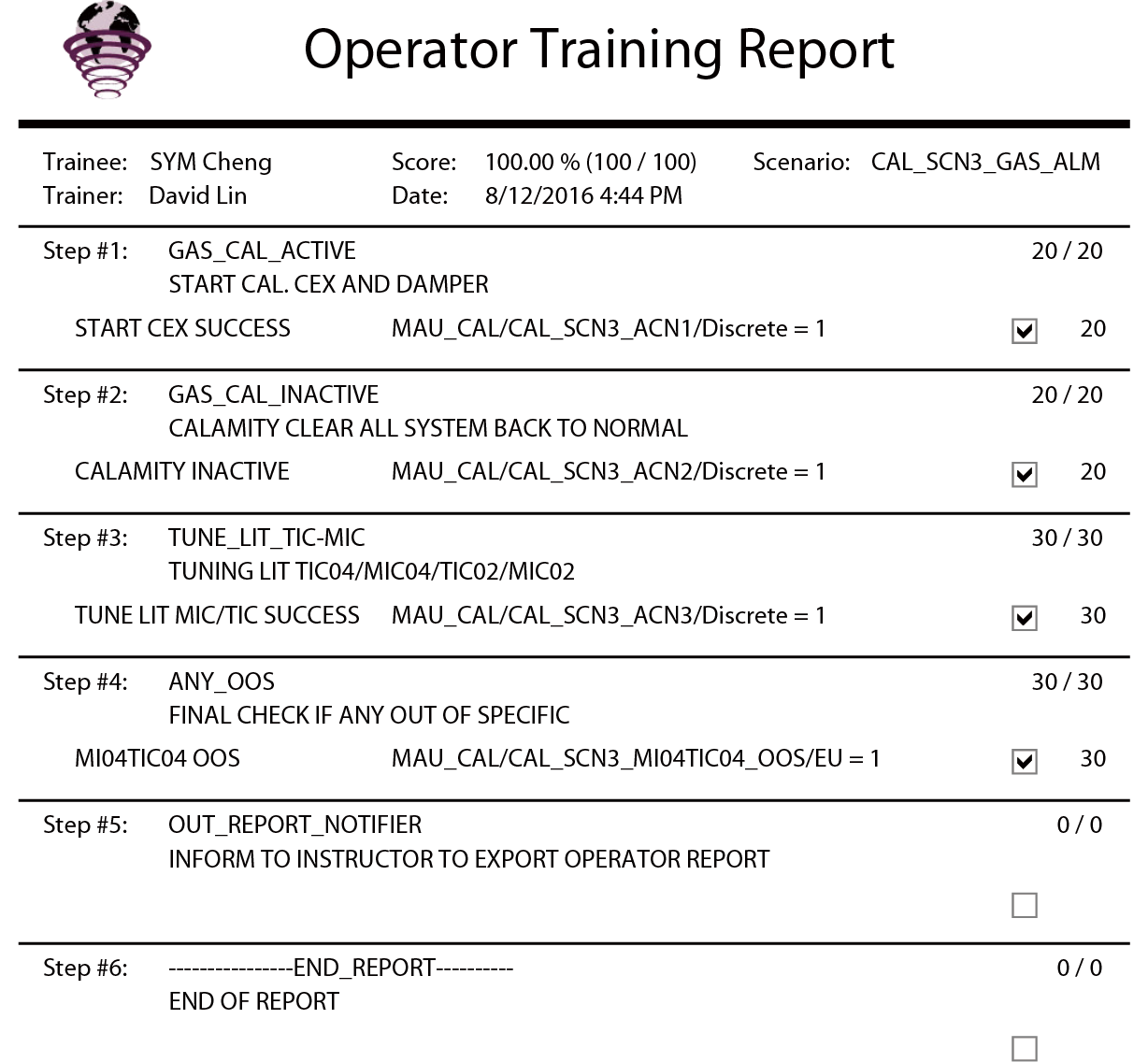
動態製程模擬在半導體廠房應用的挑戰
構建一個動態製程模型是很複雜的,要達到好的擬真度,龐大且繁複的數學計算常會讓人望而怯步,若是沒有良好的工具輔助,這將會是一項非常耗費時力的工程。而模擬系統開發出來後的更新及維護也是一大問題,大多數的工廠會因提升產能或其他需求修改製程,但常會因為變更後的真實數據取得不易或不完整,增加模擬系統維護的困難。此外,隨著擬真度要求的提升,動態即時運算增加也容易造成系統效能不足,延遲模擬系統的反應。
進階建模元件對於程式開發效能的提升有顯著的幫助,但目前所提供的套裝元件大多以支援石化產業為主,對於像無塵室這種很大開放空間(Ball Room)的氣流流場變化,如擴散、傳導行為及流場分佈的模擬支援較少。以此案例而言,由於開放空間比起密閉環境內的流體行為更加複雜,在規劃的階段要考慮的變因也更多,而在成廠取得特定完整的運轉數據,或各種突發與極端狀況的實驗資料也比建廠時期困難,因此,如何透過僅有的資料盡可能的提升擬真度是一大挑戰。此外,雖然模擬軟體俱有內建的加速功能,用以提升整體反應速度以符合實際工廠運轉情況,或者作為縮短訓練時程使用,但由於模擬引擎軟硬體計本身效能的限制,常會導致系統的不穩定,造成數值瞬間變化過大,無法達到穩態平衡,在這些部份的應用還有很大的進步空間。
擬真程度的選擇也是一個相當重要的課題。若是以人員訓練為主要目的,中低擬真度的模擬系統通常即可符合需求。因此,在設計模型時,只要針對關鍵製程要求其較高的擬真度,其餘部分做到整體反應趨勢式合理與正確即可,無需要求每一道程序與細節。例如之前開發的酸鹼排氣模擬系統,初期設計的邏輯是由風車頻率來推算出口風量,再計算出口壓差。此種規劃雖然符合實際物理原理,但由於環境變因考慮太多,導致系統在反應速度上太慢無法符合真實現況;後來將風車的出口壓差改用風車頻率直接推算,簡化模型邏輯,並參考實際經驗,把多次方的實際複雜風車運轉曲線簡化為二次曲線的方式 圖15,降低系統計算量,大幅提升了系統的反應速度。
圖15、透過經驗值將複雜的二次以上的曲線簡化
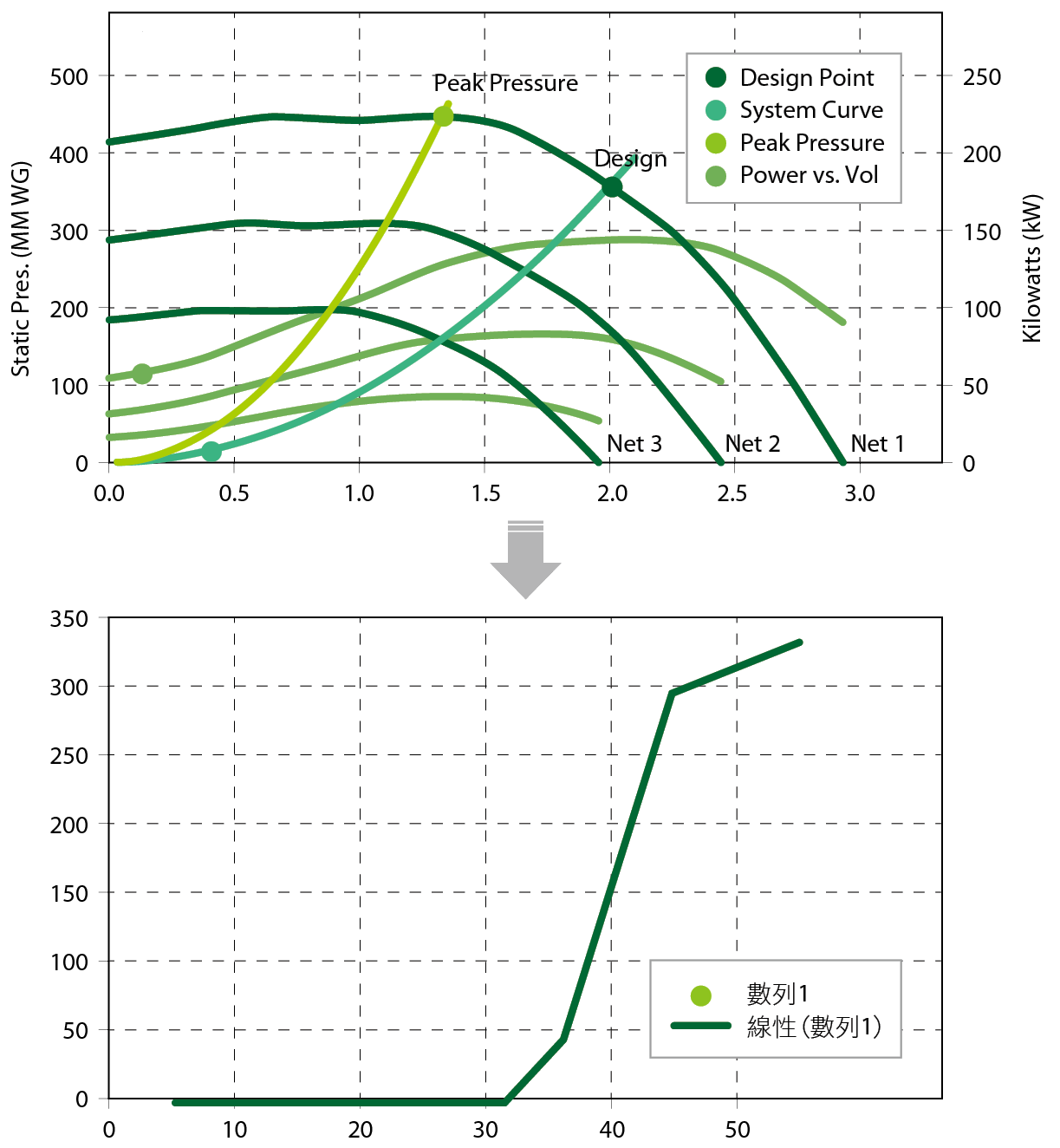
但若是為了虛擬試俥或創新實驗等目的,複雜的數學模型的設計就無法避免。萬丈高樓平地起,想要蓋多高的房子,地基就需要打得多深。同樣的,想要建立一個良好且適用性高的動態製程模擬系統,雖然不同的程式寫法可以達到相同的功能,但若是架構規劃的不夠完善,或者不符合實際運轉的物理特性,儘管階段目能夠達標,但未來想要再進行擴增或修改,就如同在沒有足夠穩健的地基的建築上進行頂樓加蓋,會有很大的侷限,即使投資更多的時間及成本,效果也可能也不盡理想。因此,擬真程度的選擇在評估階段是必須慎重考量的課題。
結論及動態製程模擬的未來展望
就如現今的3D模擬幾乎已是所有建設項目的必要步驟,相信在未來動態製程模擬也終將成為工廠追求營運優化不可或缺的一部分。動態模擬讓虛擬工廠不再只是單純外型的靜態模擬,它可以讓工廠「活起來」。離線仿真的特性在半導體廠廠務運轉目前最大的應用,在於為人員緊急應變的訓練和經驗傳承帶來最佳的實戰訓練效果,可大幅減少誤操作帶來的損失。
接下來,我們將著重在實際資料蒐集,結合廠內的真實運轉資料來提升現有模擬系統的仿真度,透過長期累積的大數據資料,協助工廠運作得更安全、更穩定,也更有效率。
未來希望隨著動態製程模擬技術在半導體廠務運轉的應用越趨成熟,能更進一步將其應用在協助系統容量的評估、流程的控制,以及製程的配方調整,實現在設計規劃階段就可以完整模擬建廠後的運轉狀況,在施工階段藉由虛擬試俥來預先進行系統上線測試,提早發現實際試俥過程中可能產生的問題、縮短建廠的時程,成廠後也能繼續使用在工廠製程改善,提升營運效率。
附註
- 快照(snapshot)–與自動化系統的快照相似,提供用戶凍結並保存製程參數和狀態,以便之後快速省時地恢復系統。
- 第一原理(First Principle)是指不必經過驗證,即已明白的原理,即是理由已經存在於原理之中,也是自證原理。就範圍大小區分,第一原理可以是解釋所有事件的終極真理,也可以視為一個系統一致性、連貫性的一種根源性的解釋。[6]
參考文獻
- 曹湘洪,石油化工-流程模擬技術進展及應用,中國石化出版社,2010。
- http://www.oreda.com/
- 楊光輝,化工流程類比技術及應用,山東化工,37卷8期,頁35-37,2008。
- 范恩祖,建築資訊模型於半導體廠房系統數量計算之應用,交通大學,工學院專班工程技術與管理組,碩士論文,2014。
- 徐嘉立,全面廠務服務方案之研究-以半導體產業為例,清華大學,高階主管經營管理碩士專班,碩士論文,2005。
- 國家教育研究院-雙語詞彙、學術名詞暨辭書資訊網 http://terms.naer.edu.tw/detail/1310644/
留言(0)