摘要
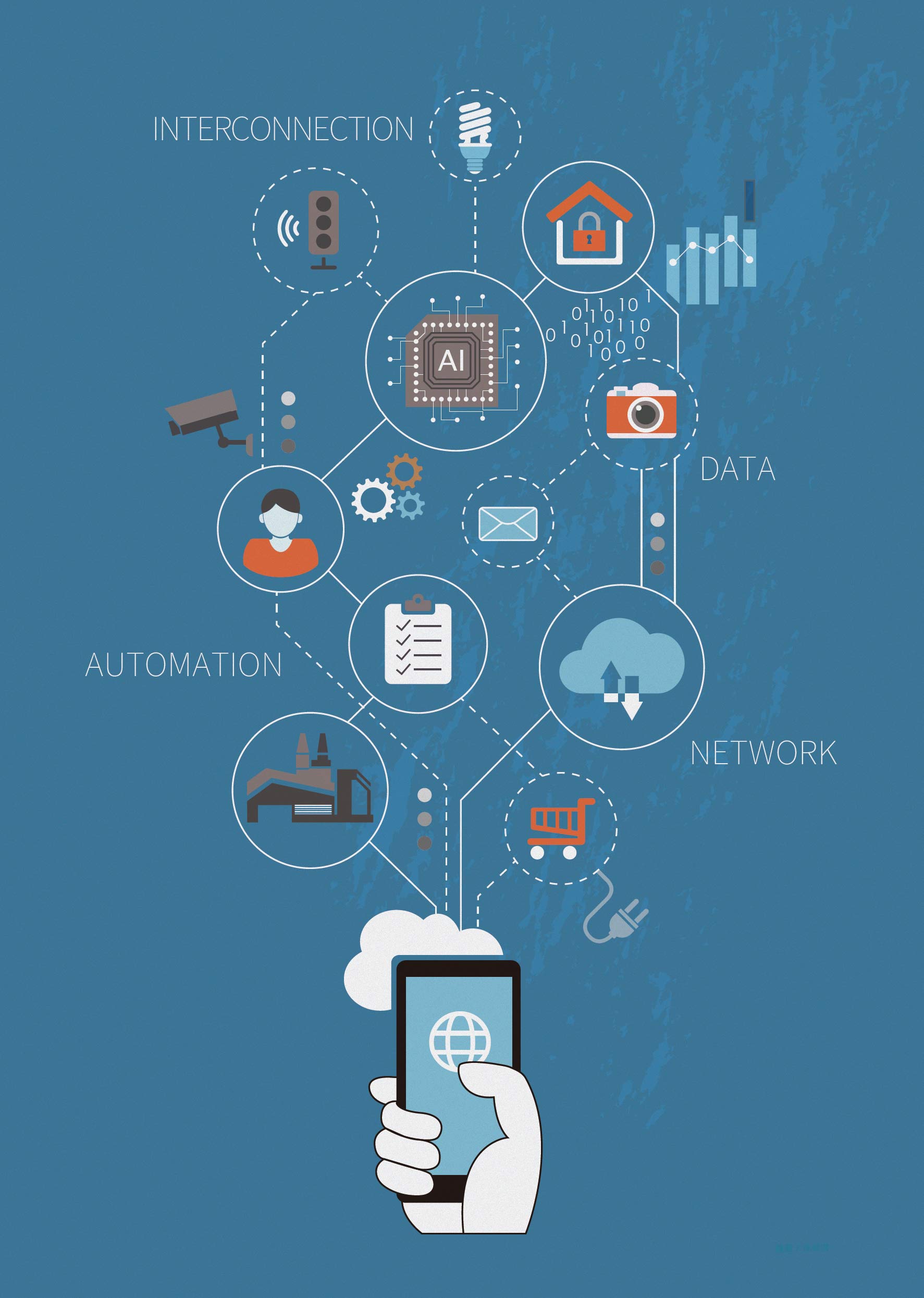
建構台積電製程機台能源管理系統
Keywords / Smart Power Grid,Process Tool Energy Management,IoT Smart Power Meter
前言
台灣是一個新興工業化國家,但天然資源相對匱乏的地區,根據經濟部能源局統計:依能源局公告106年能源統計年報資料台灣超過98%之能源是需仰賴進口。 因此台積公司深耕台灣產業發展上能源管理也是一項重要課題。雖然台積公司過去幾年節能活動已有顯著成績[2][3],但卻多以廠務系統為主,甚少著墨於生產機台的耗能改善,其主要的原因:一為生產機台肩負生產任務,在製程技術及生產步驟上能源耗用上變化極大;二為生產機台端數量多無法以經濟有效量測耗能全貌和能耗資料收集管理。
因此本文的目的在建構一個如何利用低成本IoT量測技術來一窺不同功能製程機台方法,透過資料狀態估計(State Estimation)演算[4],建立一個低成本但又高準確度的數值模型,進而利用以ISO50001為基礎的台積公司製程設備的能源管理系統,作為設備節能的管理工具→圖1。
圖1、能源管理系統 EnMS

本文將透過各項機台能源耗用報表的建立,透過相同功能機台的待機狀態之能源耗用差異分析提出機台節能的機會,供各機台節能負責人做為機台節能活動的方向。
文獻探討
本文主要跟隨著ISO 50001與SEMI S23製程機台能耗管理規範來開發一套建構台積電製程機台能源管理系統,其中運用到低能耗無線電錶、IoT與K-means大數據分析技術與方法來達到人工智慧節能管理之目標。
SEMI S23 製程機台能耗管理規範
SEMI S23規範簡介
emi S23[5]提供半導體及面板製造相關設備能源、電力及原料的節約技術、量測方式及如何將測量值換算成等效能源的方法,再利用持續改善方式提升能源使用效率及節約用量。
半導體製造設備於製造、運送、安裝、使用及廢棄等生命週期各個階段都會消耗能源。根據文獻調查結果→圖2所示,設備「使用」階段能源使用佔設備生命週期98%,因此本文挑選此階段進行能源管理,建立生產設備電力與其他非電力資源使用資訊,作為能源管理依據。
圖2、設備生命週期能源使用分析[6]
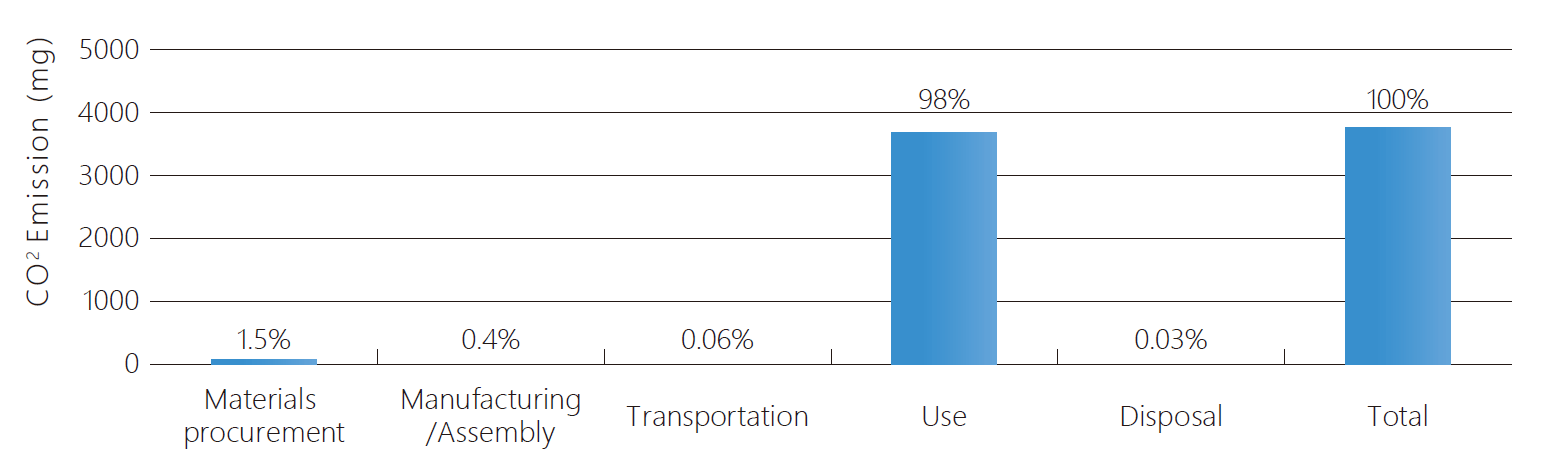
製程機台能耗分析主要建構以能源轉換係數ECF(Energy Conversion Factor)為計算基礎,可將特定製程所需要的電力與其他非電力資源使用量換算成等效能源消耗資料。量測週期必須包含設備製程時間和待機時間,再盤查紀錄製程機台運轉情況下使用廠務系統能源消耗數據,包含電力、排氣、真空、壓縮空氣、冷卻水、純水等相關量測規範紀錄於SEMI E6等相關章節,最後藉以計算機台總能源耗能,目前常用計算公式如下:
A、使用率測量值(製程或待機) x 每年時數(製程或待機) x 能源轉換係數=每年預估能源消耗
B、∑ [廠務能量轉換係數 x 機台生產所需求量] = 機台總能耗
台積公司SEMI S23 製程機台能耗計算基礎分析
如→表1為2016年台積公司某製程生產機台Top 20能耗量測結果,其中包含電力、排氣風車、製程冷卻水、超純水和壓縮空氣等能耗資源,其中以電力能源 66%為最高,因此本研究選定電力能源為優先發展,期望制定一套有效能源管理與技術開發。
部門 | 機型 | 總耗電量 |
Power kWh*ECF |
AAS CMh*ECF |
PCW CMh*ECF |
UPW CMh*ECF |
CDA CMh*ECF |
|||||
---|---|---|---|---|---|---|---|---|---|---|---|---|
部門-1 | 機型-01 | 423.9 | 353.1 | 83% | 20.2 | 5% | 50.6 | 12% | 0.0 | 0% | 0.0 | 0% |
部門-1 | 機型-02 | 422.7 | 347.2 | 82% | 22.9 | 5% | 52.6 | 12% | 0.0 | 0% | 0.0 | 0% |
部門-2 | 機型-03 | 248.2 | 142.9 | 58% | 22.9 | 9% | 8.7 | 3% | 12.8 | 5% | 60.9 | 25% |
部門-2 | 機型-04 | 247.9 | 165.6 | 67% | 29.5 | 12% | 2.3 | 1% | 12.4 | 5% | 38.1 | 15% |
部門-3 | 機型-05 | 238.0 | 125.7 | 53% | 49.4 | 21% | 21.7 | 9% | 18.2 | 8% | 23.0 | 10% |
部門-2 | 機型-06 | 202.5 | 117.8 | 58% | 4.9 | 2% | 1.6 | 1% | 71.5 | 35% | 6.7 | 3% |
部門-4 | 機型-07 | 197.2 | 121.0 | 61% | 41.0 | 21% | 24.4 | 12% | 0.0 | 0% | 10.8 | 5% |
部門-4 | 機型-08 | 188.9 | 117.9 | 62% | 32.7 | 17% | 30.9 | 16% | 0.0 | 0% | 7.4 | 4% |
部門-4 | 機型-09 | 179.4 | 107.7 | 60% | 32.7 | 18% | 20.8 | 12% | 10.6 | 6% | 7.6 | 4% |
部門-2 | 機型-10 | 175.6 | 92.0 | 52% | 18.2 | 10% | 0.2 | 0% | 36.8 | 21% | 28.4 | 16% |
部門-5 | 機型-11 | 175.2 | 92.2 | 53% | 14.5 | 8% | 0.0 | 0% | 6.9 | 4% | 61.6 | 35% |
部門-6 | 機型-12 | 171.7 | 117.0 | 68% | 33.6 | 20% | 12.5 | 7% | 0.0 | 0% | 8.7 | 5% |
部門-7 | 機型-13 | 167.1 | 93.1 | 56% | 54.4 | 33% | 3.6 | 2% | 0.0 | 0% | 16.0 | 10% |
部門-4 | 機型-14 | 154.5 | 83.0 | 54% | 5.4 | 4% | 6.0 | 4% | 0.0 | 0% | 60.0 | 39% |
部門-7 | 機型-15 | 147.2 | 76.6 | 52% | 19.4 | 13% | 6.8 | 5% | 0.0 | 0% | 44.3 | 30% |
部門-6 | 機型-16 | 136.6 | 111.7 | 82% | 8.5 | 6% | 10.8 | 8% | 0.0 | 0% | 5.6 | 4% |
部門-7 | 機型-17 | 133.5 | 86.4 | 65% | 21.1 | 16% | 2.2 | 2% | 0.0 | 0% | 23.9 | 18% |
部門-7 | 機型-18 | 122.8 | 68.9 | 56% | 49.6 | 40% | 2.6 | 2% | 0.0 | 0% | 1.7 | 1% |
部門-8 | 機型-19 | 111.5 | 82.3 | 74% | 22.7 | 20% | 4.8 | 4% | 0.0 | 0% | 1.8 | 2% |
部門-5 | 機型-20 | 100.0 | 86.5 | 87% | 11.4 | 11% | 1.6 | 2% | 0.0 | 0% | 0.4 | 0% |
3,944.2 | 2,588.6 | 66% | 515.0 | 13% | 264.6 | 7% | 169.2 | 4% | 406.8 | 10% |
ISO 50001能管管理[7]
國際標準組織(ISO)為提供各界於能源管理上有統一標準可依循,故於2011年6月正式發行ISO 50001能源管理系統(Energy Management System, EnMS)之國際標準版,作為能源管理推動之共同標準。
ISO 50001能源管理系統標準之目的是讓組織建立有效的制度與程序,以提供其能源績效,包含能源效率、能源使用、能源消耗以及能源強度,並予以文件化、建立制度化。該標準基於持續改善,並運用與ISO 9001和ISO 14001管理系統標準相似的「規劃PLAN-執行DO-檢查CHECK-行動ACT」(PDCA)的方法以改善提升能源效率的機會。藉由實施新的能源管理標準,以系統化進行能源管理,將可降低能源成本、溫室氣體排放和其他環境影響。綜上所述,ISO 50001的架構含括了能源管理的管理元素與技術元素,一個有效的能源管理必須呈現與整合這兩種元素,亦即包含技術最佳範例與管理最佳典範→圖3。
圖3、ISO-50001 能源管理系統 EnMS
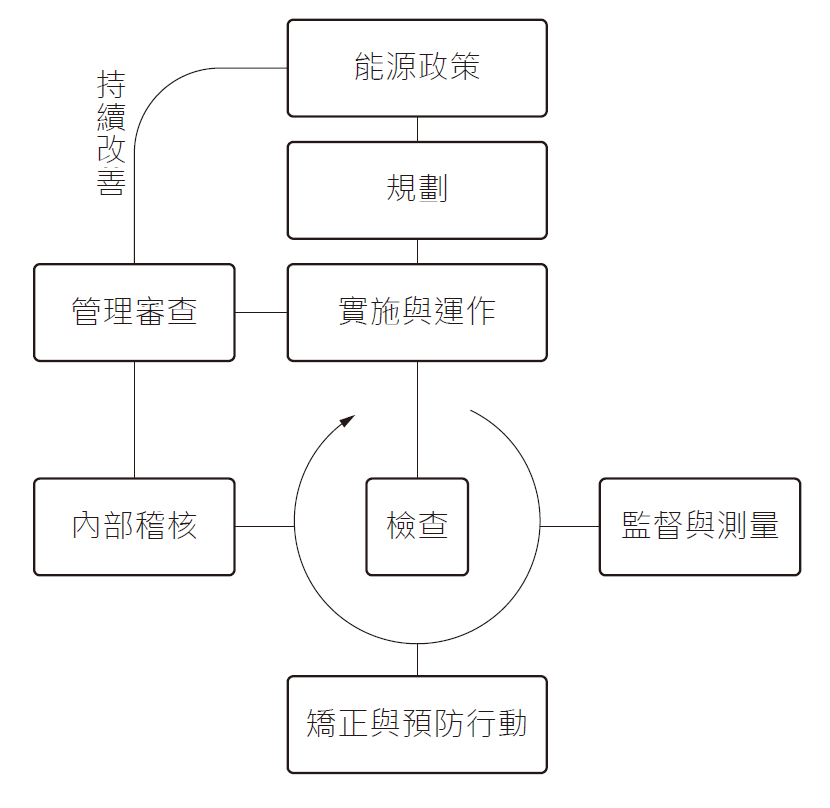
製程機台能源管理系統研究方法與流程
本章節所提出之資料收集、數據分析及管理之方法有IoT技術、K-means大數據分析方法與智慧電網之能源管理,請參考以下介紹。
能源量測資料收集方法
低成本及低能耗無線IoT智慧電錶能源量測資料收集
A、無線IoT智慧電錶與傳統數位電錶之差異
傳統上數位電錶內部架構圖→圖4,主要是由電能運算晶片(Energy Metering IC, EMIC)與微處理機所組成[8]。其中 EMIC為了運算出目前負載所消耗之用電量,必須分別對電壓與電流信號取樣進行電能運算,其中電壓取樣是利用電阻分壓方式取出電壓信號後輸入至EMIC。電流取樣則是透過比流器(CT)方式進行電流信號轉換。由於需進行複雜浮點運算需額外提供電源,最後再透過實體通訊線回傳訊算資料。
圖4、傳統數位電錶內部架構圖
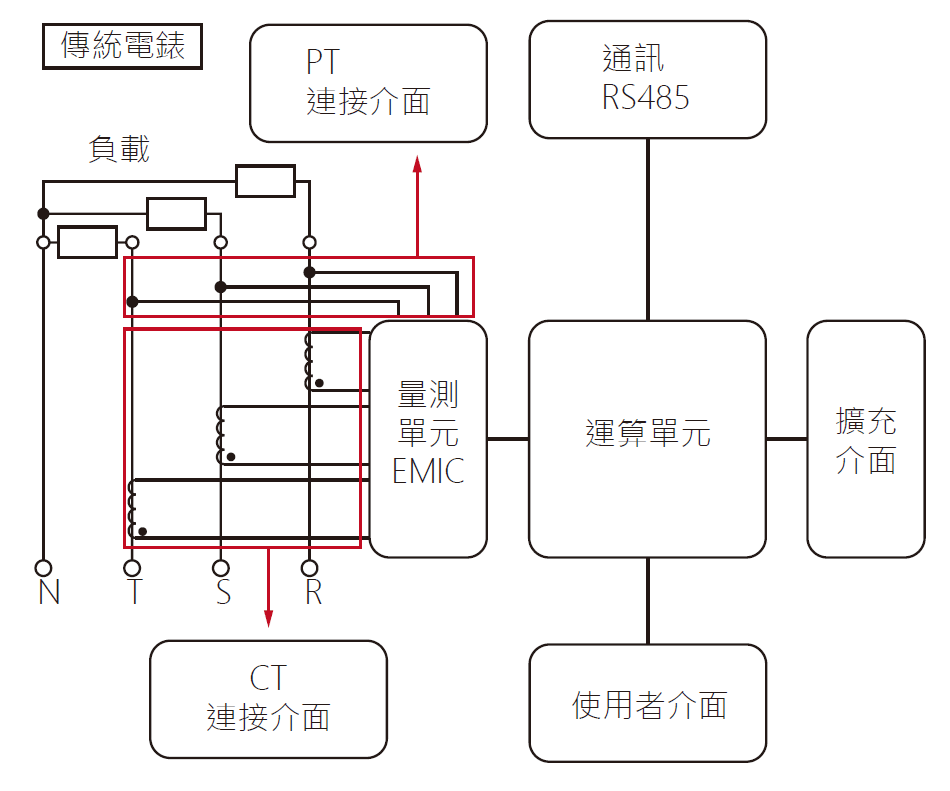
有鑑於半導體工廠要佈建傳統電錶做為能源消耗資料收集是一大投資、施工困難、拉線安裝風險性高及擴充不易等缺點。因此本研究提出有效且低成本IoT能源量測想法,並委由專業廠商實現產品開發,其流程圖→圖5。
圖5、低成本IoT能源量測電錶流程圖
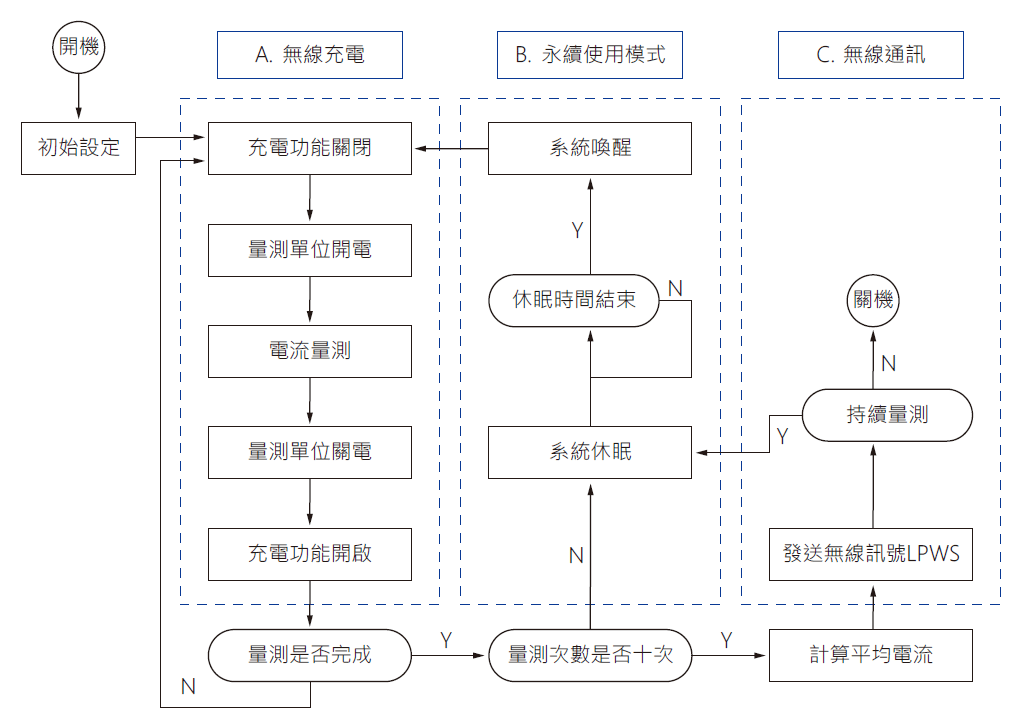
- 步驟一:開發無線充電技術,不須額外電源
透過法拉第磁生電原理感應電動勢 e = –(磁通變化量/時間變化量dt),感應擷取待測線路能源訊號,除可有效使用量測計算電能數值,並捕捉剩餘電力儲放於儲能單元,不需由外部再額外提供工作電源給予電錶。 - 步驟二:長期儲能運作模式
透過每次(秒)需擷取能源數值自動啟動量測單元,量測完成後自動關閉,永續使用循環運作模式。 - 步驟三:運用無線低功率網路技術(LPWS)
可省去信號回傳的佈建拉線需求,期望達成建構低總成本且解決了成熟工廠施工不便的限制。
B、無線IoT智慧電錶能源量測器功能確認
根據IoT智慧電錶應用的架構理念,分別驗證電錶低功率能源平衡、通訊品質以及單顆電錶測誤差之驗證以確保資料回傳之正確性,如下說明:
- 個別電錶測誤差驗容許值確認
IoT電錶硬體實現架構→圖6,並實際測試IoT電錶誤差範圍,驗證方法為同電源之分路負載,對照組為Fluke 435電錶,其驗證方式為相同時間誤差值驗證比較,個別電錶測誤差驗容許值首先須符合基本誤差值須
<2%之設計要求。圖6、IoT電錶內部架構圖
- 低功率能源平衡計算
無線儲能部份,本IoT電錶使用0~400Aac 開口式CT,換算至二次側可感應0~80mAac,若以電錶最低啟使電流10A(2.5%)計算,有效儲能時間為9,450ms,可儲能3.64uWh→圖7。圖7、無線IOT智慧電錶運作所需能源平衡
- 通訊能力品質確認
→圖8為該廠區無線網路架設拓譜配置,以FAB2F分為4個幹線,每個幹線串聯7個無線網路基地台AP,每個區域半徑為20m。每個AP接收IoT電錶數量能力架構→圖9,每個AP連接31傳送器,每個傳送器傳送1~6個CT的規劃方式進行無線通訊能力確認是否符合>120dbm之要求。圖8、無線網路架設拓譜配置圖
圖9、AP接收IoT電錶數量能力架構圖
- 無線IoT智慧電錶應用於能源管理系統之網路架構
能源管理網路→圖10,是將每個IoT電錶透過新建立的無線網路基地台(AP,Access Point)連接,再透過通訊骨幹收集至既有SI Network 的資料收集器(DAQ,Data Acquisition)儲存,再進到Mr.Energy能源管理平台分析處理,最後呈現於OneFAC用電量報表和FDC (Fault Detection and Classification) 資料平台。圖10、IOT能源管理網路
狀態估算進行能源量測資料誤差驗證
A、狀態估測簡述作法[9]
完成電網模型後透過狀態估測功能,進一步分析各個設備彼此間的電力資訊之正確性與合理性,以確認量測的結果是可以被使用的。PowerFactory的狀態估測功能之流程→圖11。主要包括以下程序 : (1)量測資料的合理性檢驗(Measurement Data Plausibility Checking)、(2)可觀察性分析(Observability Analysis)、(3)狀態估測(非線性最佳化)(State Estimation (Non-Linear Optimization))。
圖11、狀態估測流程圖
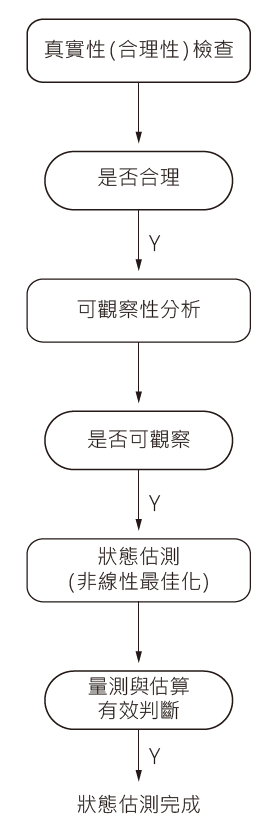
第一階段:量測資料真實性(合理性)
檢測和排除所有量測值的一些明顯錯誤,以避免不合理或完全錯誤的量測值造成嚴重的網路狀態估計值之扭曲。主要完成以下檢查項目:
- 檢查功率潮流大小之合理性。
- 檢查功率潮流方向之合理性。
- 檢查節點的總功率潮流之合理性。
第二階段:檢查電網的可觀察性
主要分析待估測狀態的電錶相依性,透過此步驟可得知冗餘和相關的電錶,並給予每個電錶相對應的權重值,根據相依性較高的電錶進行更精準的估測。
如果系統中測量值有足夠(非冗餘)的資訊去估測電網的部分狀態之訊息,則稱此區域電網為可觀察。可觀察系統的必要條件為可用量測值的數量必須大於或等於估計變數值的數量。即使量測值總數足夠,但也可能發生電網某些部分是不可觀察的,因此不僅是要有足夠的量測值之數量,也要有良好的分佈位置。假如此電網的每個狀態可以根據給定的量測值進行估計,則此系統稱為可觀察;若此電網為不可觀察,但仍可用此方法來判斷電網裡的孤立群是否為可觀察的。可透過以下方法進行分析。
- 方法1:冗餘電錶:
規則一:如果靈敏度向量(senx(mi1) and (senx(mi2))均線性相依,則mi1與mi2有「相同的訊息內容」來區分𝑋狀態。
規則二:若且唯若相對應的靈敏度向量(senx(mi1) and (senx(mi2))均線性獨立,則M的mi1…mii每個子集均具有非冗餘量測值。 - 方法2:個別狀態的可觀測性:
規則一:如果靈敏度向量(senM(mi1) and (senM(mi2))均線性相依,則給定的一組量測值M並無法區分xi1與xi2之狀態,換言之,xi1與 xi2之狀態只能將其納為一群觀察,不能單獨觀察。
規則二:若且唯若相對應的靈敏度向量(senM(mi1) and (senM(mi2))均線性獨立,則一個X的xi1…xii狀態之子集為可觀察(單獨的情況下)。
第三階段:狀態估測。
此階段為本研究之重點,狀態估測用來評估整個電力系統的狀態,利用前兩個步驟篩選出較好的電錶權重值,使用非線性Lagrange-Newton最佳化演算法,求其電錶計算值和實際量測值的最小誤差量,以估測每個負載狀態的實功值和虛功值。以數學角度來看,其目標是最小化分路流量和匯流排的估計值與測量值之間的所有誤差量加權平方之總和,並同時滿足所有電力潮流方程式(Load Flow Equations)。
目標函數:
........式(1)
........式(2)
calcVal : 狀態估測的計算值
meaVal : 電錶的量測值
剔除異常量測值的容忍因子:
........式(3)
B、系統架構
利用現場用電架構圖→圖12:
SUS-625 22.8KV/480V變電站包含UPS和多功能電錶紀錄,三分路分別為N2-625C、EU2-625E、N4-625B,其中N2-625C和EU2-625E兩迴路則透過變壓器將480V降為213V供機台使用。
圖12、SUS 625變電站迴路架構圖
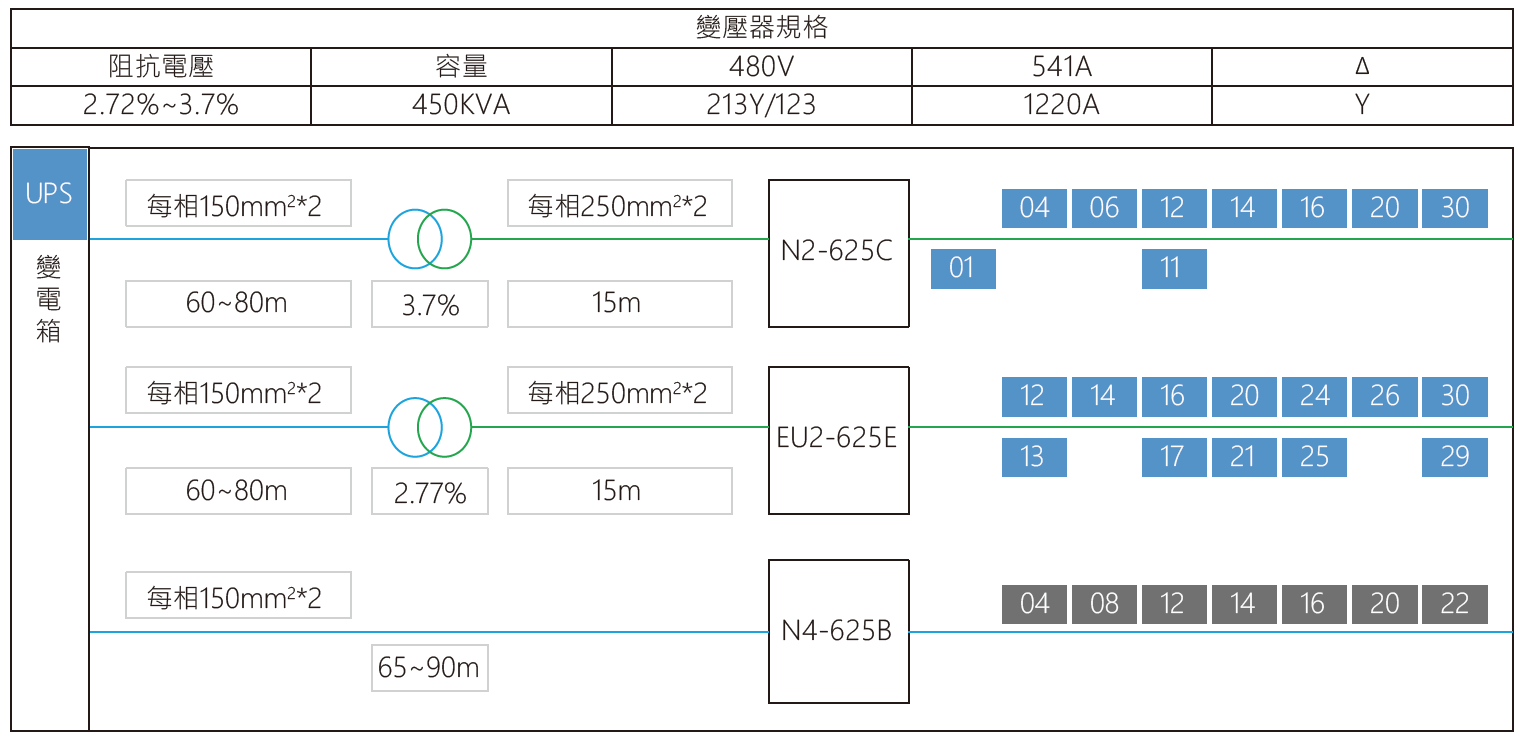
利用變電站各分路ACB配置有多功能電錶及安裝於各下游設備饋線源頭的無線IoT智慧電錶(I),以測量各個機台的用電量,目前是取10筆每秒的量測電流資料進行平均,再將每10秒的平均電流值回傳至資料庫,供後續分析使用 。然而這些資訊並無同步採集,因此透過狀態估測將此無法同步而產生的影響降至最低。
- N2-625C迴路共有九個負載(編號:01、04、06、11、12、14、16、20、30)。
- EU2-625迴路共有十二個負載(編號:12、13、14、16、17、20、21、24、25、26、29、30)。
- N4-625B迴路共有七個負載(編號:04、08、12、14、16、20、22)。
C、狀態估測自動化程序架構
主要分為三個步驟,步驟如→圖13:
圖13、狀態估測自動化架構
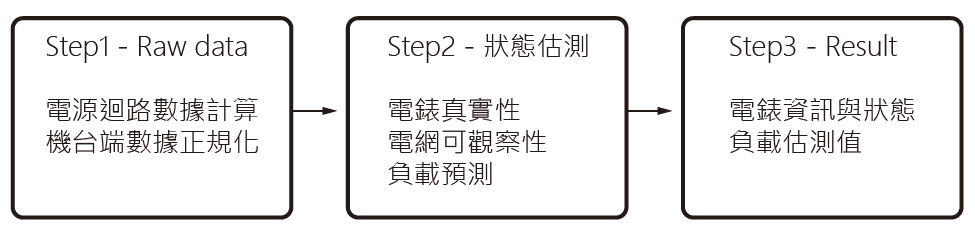
步驟一:建立四個分路的電壓、電流、功率與各迴路中各機台之電流資料(Raw Data取樣頻率為10秒鐘一筆)。
步驟二:透過用Python程式,自動擷取數據Raw Data,並饋入至DIgSILENT建置完成的電網模型,進行狀態估測分析,透過此功能可得知電錶真實性、電網可觀察性和負載估測。
步驟三:透過Python程式自動將步驟二的狀態估測之估測結果(含電錶資訊和狀態、負載估測值、Bad Data顯示)記錄,供下一階段資料分析使用。
狀態估測採用商業軟體DIgSILENT PowerFactory建置電力網路拓樸,並將各設備的電力資訊匯入至模型中,此電力網路模型→圖14。
圖14、SUS 625 之電網模型
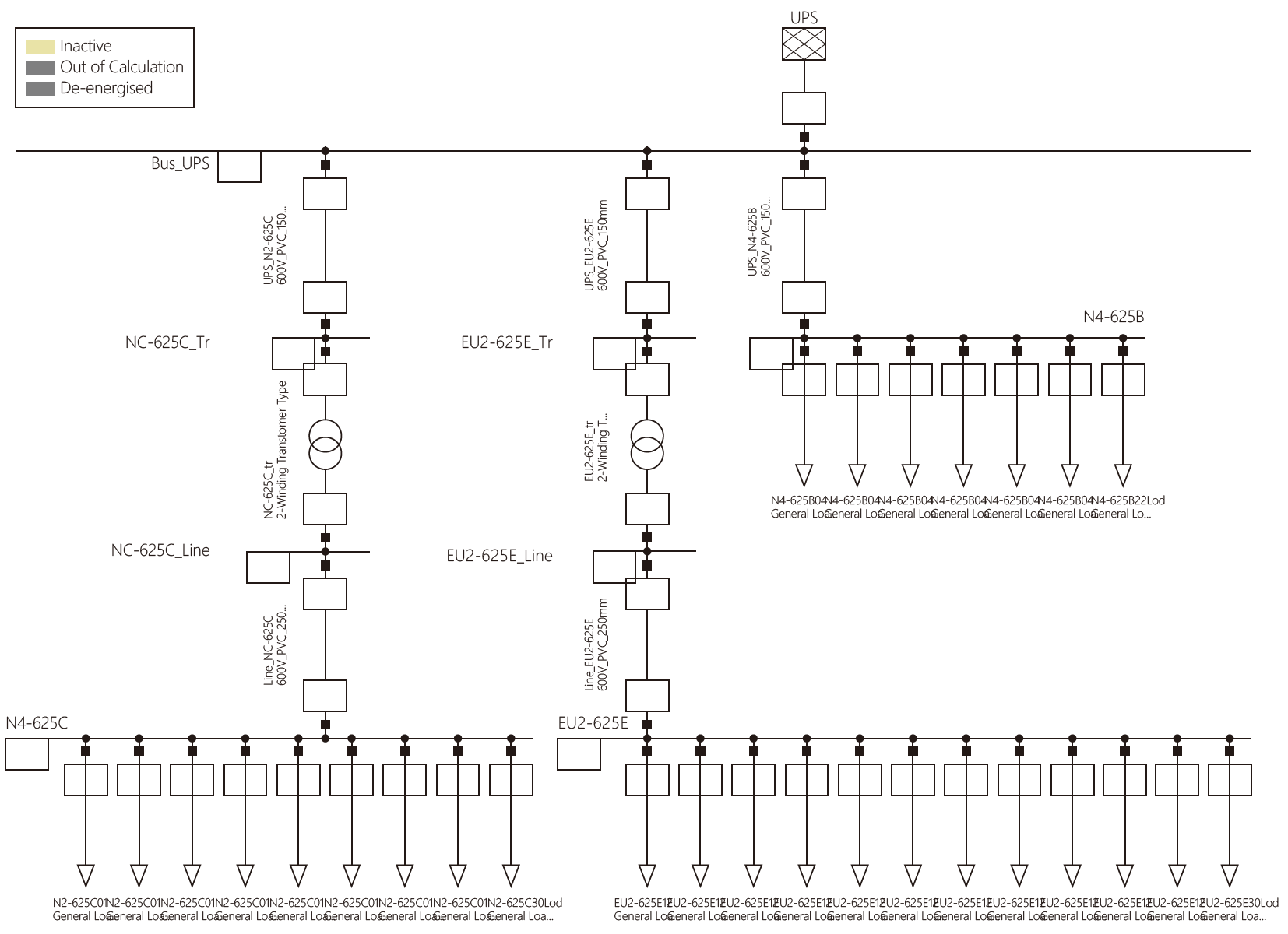
D、量測標準差修正法
由於半導體工廠機台電力使用多為非線性負載,在電力諧波必然存在上游電錶True RMS數值不等於下游IoT電錶True RMS之總和,因此本文需透過標準差修正流程,校正一次側與二次側電流之間的誤差關係,標準差修正流程圖→圖15:
圖15、標準差修正資料處理流程圖

標準差,其中𝑥₀為平均值,𝑥i為各筆電流量測值,𝑁為資料數量(單位:每筆)。
根據625E實際量測數據→圖16,可發現625E迴路之二次側總電流(橘線)與一次側總電流(藍線)存在著誤差量。
圖16、625E_I 修正前電流比較圖
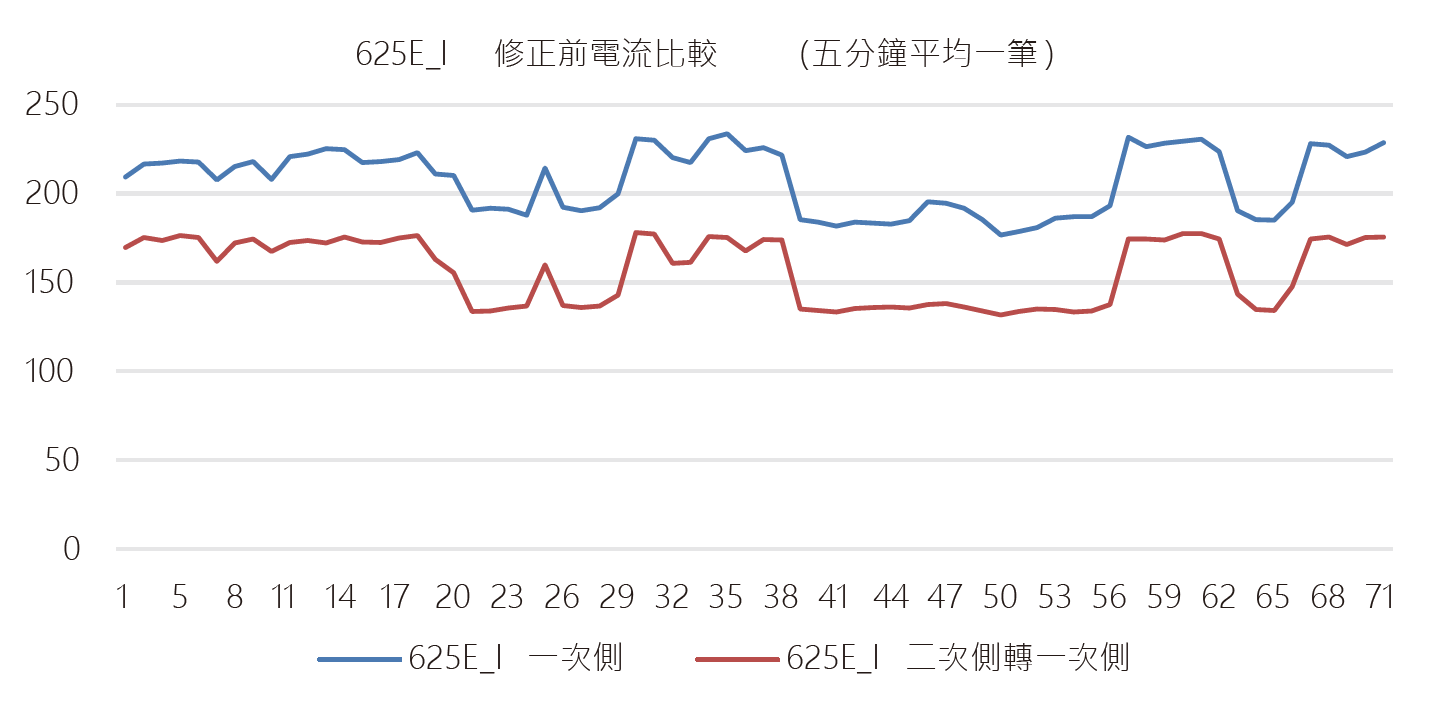
根據標準差修正法→圖15,經由計算後可得出標準差為+50.61A ,再將標準差加入二次側電流,可發現與一次側電流趨勢相符→圖17。
圖17、625E_I 修正後電流比較圖
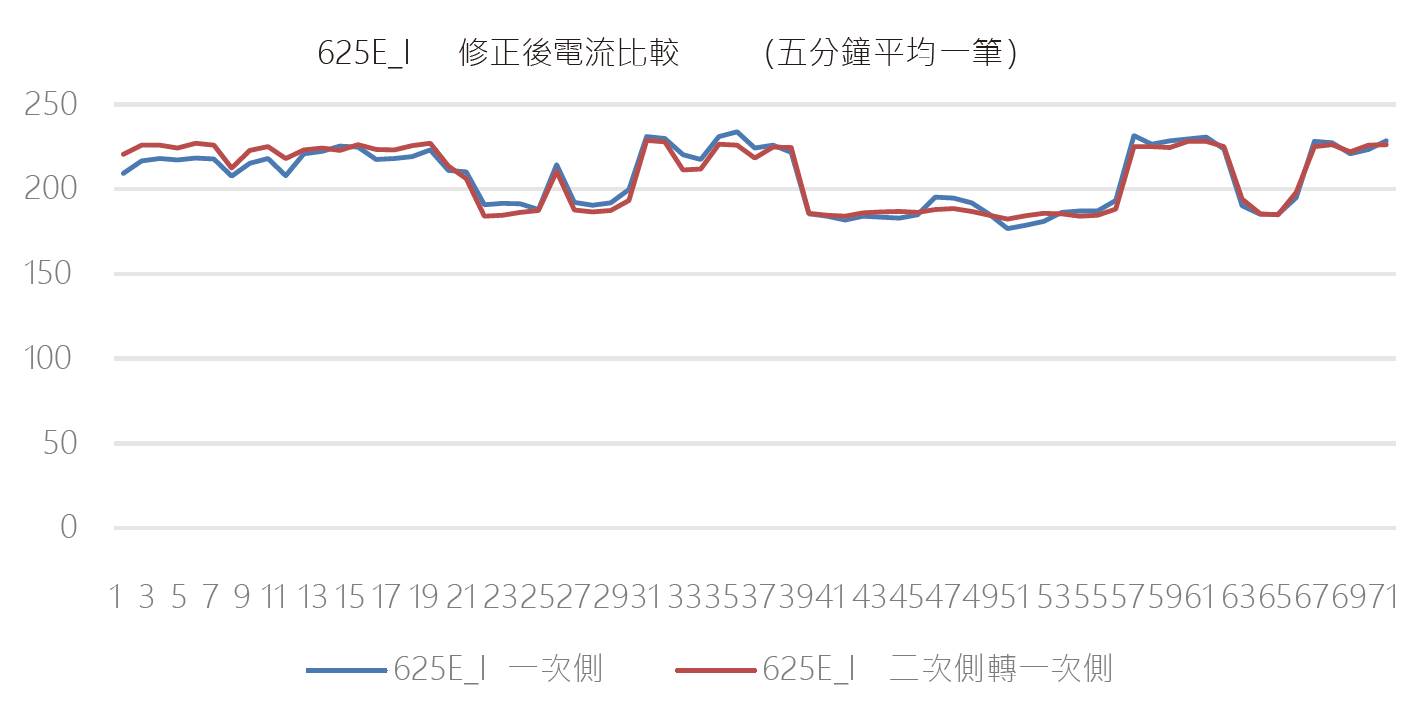
625E修正過後透過狀態估測後可得知原誤差平均值為24% 修改後為2.19% ,由數據得知誤差值降低21.81%,且由→圖18所示,可看出原始最大誤差率29.79%,修正後最大誤差率6.4%。
圖18、625E狀態估測誤差率圖
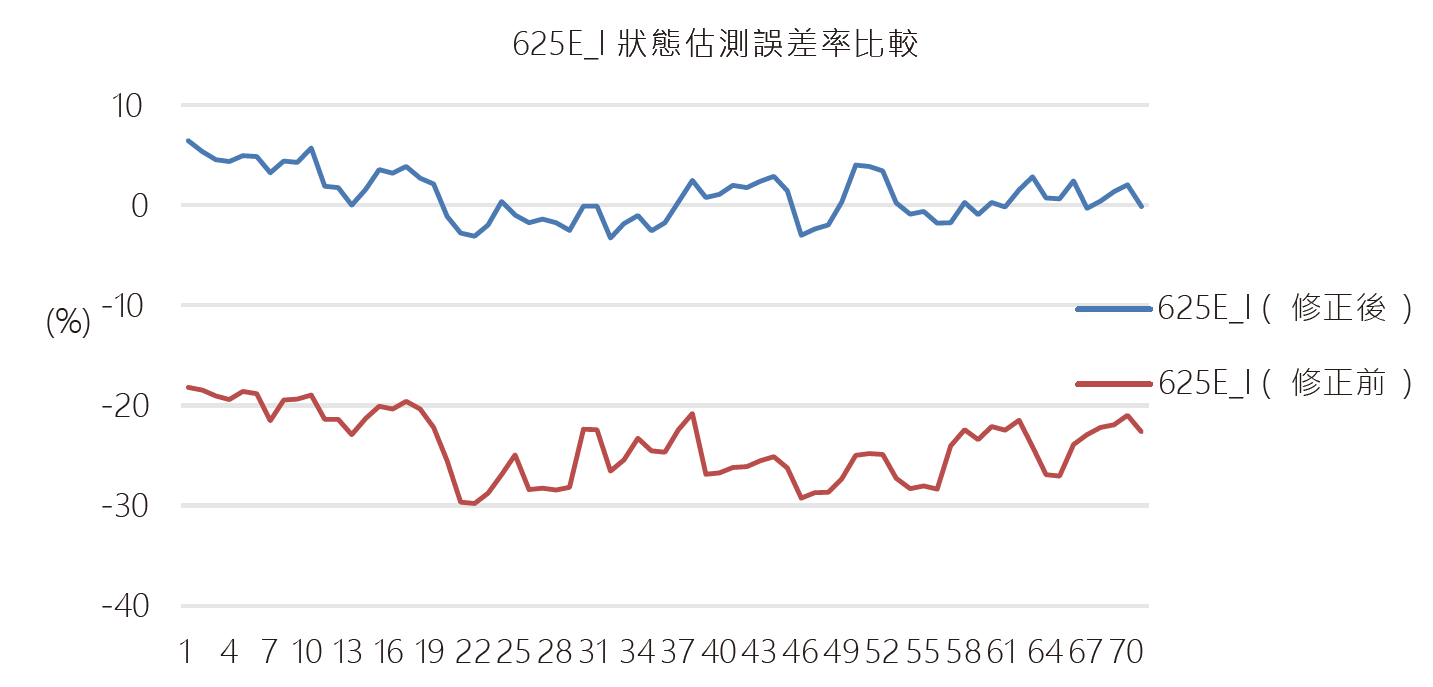
K-means大數據分析與機台端用電量差異自動比對[10]
K-means大數據分析方法
此演算法為資料分群中最簡單也最常被使用的演算法之一,其演算法如下所示 :
- 設定重心 : 決定要分幾個群,如→圖19決定分成三群,所以初始重心有三個,這三個點是隨機產生的。
圖19、K-means資料分群流程圖(取自stack overflow)
- 分群 : 找到分別最靠近這三個點的所有資料點,並做第一個迴圈的分群。
- 尋找重心 : 分完群之後,計算所有資料點的重心(Element-Wise的平均),做為下一個迴圈的分群標準。
- 停止 : 重複上述方法,只到不會有資料點因為重新尋找重心而改變群組。
K-means主要是為了將公式(4)最小化
........式(4)
所有資料點𝑥𝑗到其對應群中心𝑢𝑖的距離總合是最小的,目的就是要找到最佳的群中心𝑢𝑖及𝑥𝑗所屬的群來符合上面的要求。
機台端用電量差異自動比對
當全機台用電Raw Data經由IoT智慧電錶成功上傳至Mr.Energy平台資料庫後的資料分析便是尋找機台端用電差異的關鍵,本節將說明其步驟:
步驟一:廠區機台製程功能分群,此步驟是將收集之用電資料整合後依機台製程功能分群,做為同組群機台放置一起來進行分析與比較之最小群組單位。
步驟二:機台用電狀態分類,此步驟是將同組群機台用電狀態之資料進行資料分類,將每台機台之用電資料區分為RUN/IDLE/DOWN等基本區分群組。
步驟三:於同群組之機台自動運算同群組間用電量差異,此步驟是將上一步驟所取之IDLE類群的資料進行自動比對後找出能耗最低來當Golden Tool,接下來將同組群機台與Golden Tool作比較將所有能耗差值總合,這就是本文所提之機台端用電量差異自動比對以找尋的節能機會點。
上述所提的機台端用電量差異自動比對,是應用K-means資料分群方法來進行機台「IDLE用電量」狀態資料分群之資料後,利用Mr.Energy平台運算功能進行比較並自動產出預估節能機會量。
台積公司內部智慧電網之能源管理平台
智慧電網
傳統電網透過集中式發電廠發電(如核能、水力、煤炭和天然氣等)再透過變電系統和輸電線路將電能送到每個用戶→圖20。
圖20、智慧電網 : 電力產生、輸送與分配圖[11]
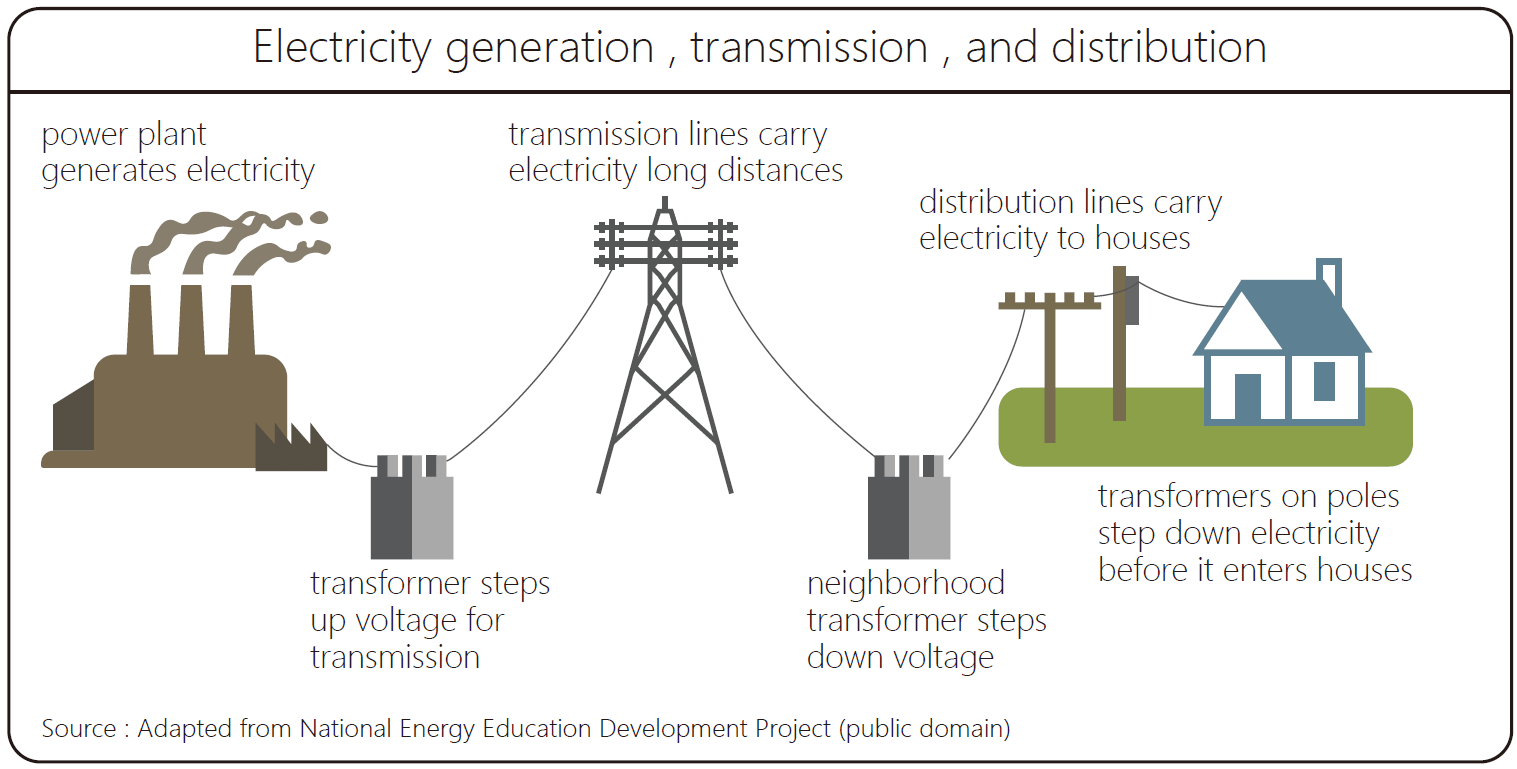
時至今日,因再生能源蓬勃發展(如風能和太陽能產生的電能和智慧儲能等),消費者用電需求已非單向電力消費而轉而具售電需求雙向交換機制,這種藉由數位通訊、自動化、即時控制等應用使電網更高效、更可靠、更安全,稱之為智慧電網(Smart Grid)→圖21。
圖21、智慧電網的概念[12]
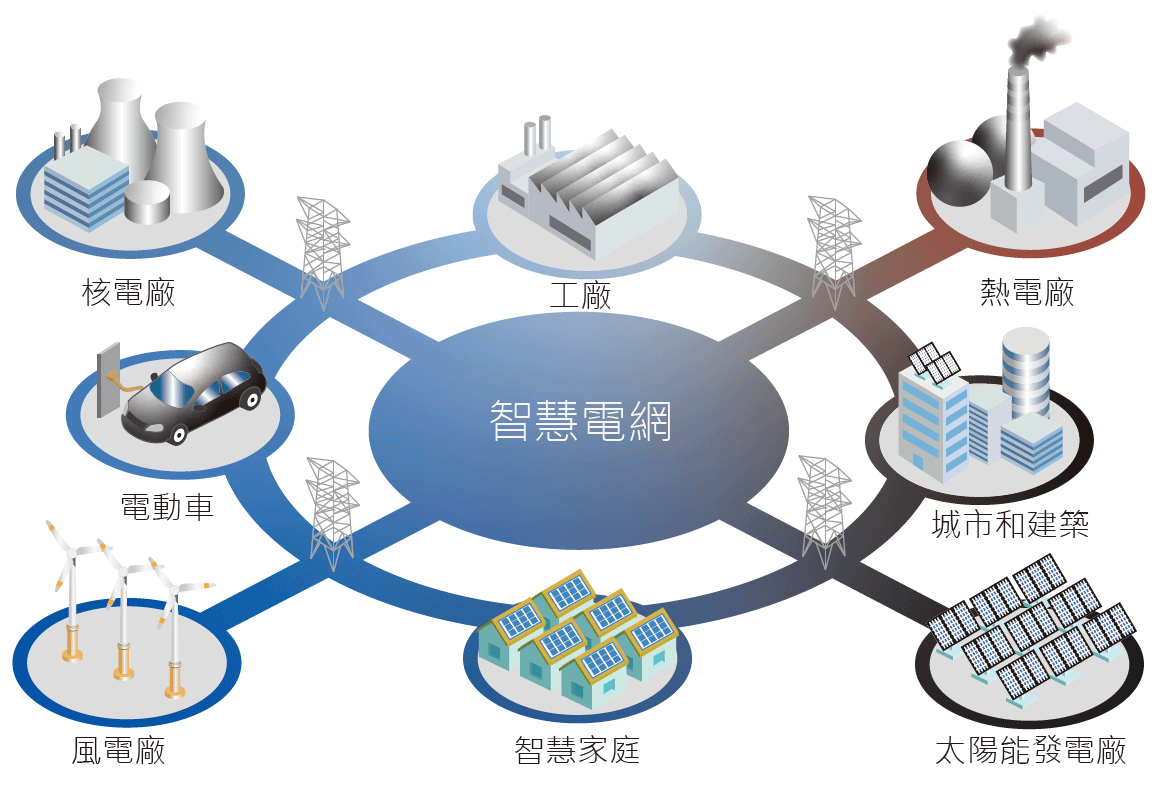
能源管理平台
微觀台積公司電網供應架構,從電力公司透過輸電系統將電力送至工廠,廠內透過廠務系統提供生產Utility至生產機台,也是屬於單向供應行為模式猶如傳統電網精神,但從能源管理精神而言,是必須要管理到每單一設備用電行為。因此建構能源管理平台,再予以分類及分層精神做為有效能管手法。
步驟一:參照既有分類能管法則
參考經濟部能源局能源用戶節約能源查核申請表(附表1-工業及其他生產性質行業)→圖22,其中能源查核主要以電能平衡圖追蹤,其追蹤之用電種類主要以照明、空調、空壓機、製成動力、汙水處理、集塵設備等區分,但這些追蹤指標只能評定單一負載用電總量增減,無法有效細緻化管理。因此台積公司需自行建立用電種類階層與指標。
圖22、電能平衡圖範本[13]
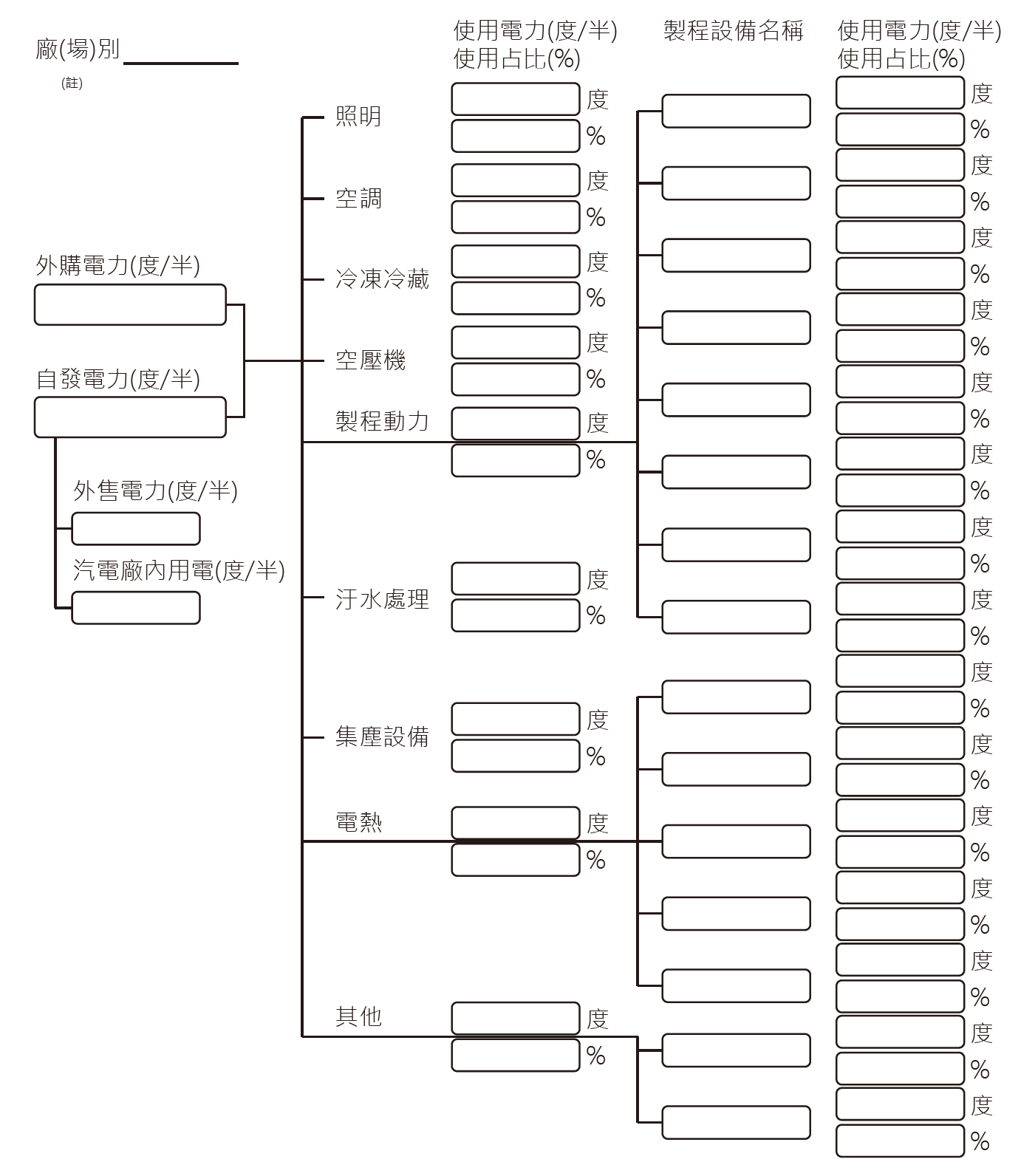
步驟二:建立台積公司用電分層管理追蹤
- 階層一,工廠總量(Level1):長期追蹤單一廠區用電趨勢,是否背離產能與用電指標,同時可做為跨廠區電量趨勢追蹤
- 階層二,用電屬性(Level2):單一工廠分為生產機台、廠務、辨公室與其他用電趨勢追蹤,同時可分析機台直接耗能源與環境耗能綜合性指標
- 階層三,用電部門(Level3):生產機台依製程功能分類如CVD、PVD、DIF等;廠務分類依水、機、電和氣體等耗能區分,同時可做為節能驗證成效追蹤
- 階層四,單機用電(Level4):透過系統效率標竿學習和相同機型耗能差異比較,同時可做效能衰退指標,經矯正措施改正後,與能源基線成效驗證,重新回到Level2/Level3總量追蹤能源循環管理,能源管理流程→圖23。
圖23、電能源管理流程
步驟三:統計可用電錶資源與額外電錶構建需求
統計可用電錶資源主要用來紀錄供應端用量(台積公司某一廠區約2,000個有線電錶),仍不足反映每一生產機台用電於製造行為資訊。該廠區仍需額外約3,000個電錶,但裝設之困難度及費用的解決就是應用低成本無線IoT電錶建構技術發展的主要目的,藉以了解所有用電設備能耗的用電狀況。
製程機台能源管理系統資料驗證
由第三章所提出之研究方法經由本章節進行驗證,由驗證資料證明本文所提出之研究方法是符合SEMI S23製程機台能耗管理規範與ISO 50001能管管理規範,並且預估機台待機節能量是符合實際狀況與可執行的。
能源量測資料驗證
IoT智慧電錶低功率平衡驗證
使用示波器來量測無線IoT低功率能源平衡驗證,IoT電錶消耗功率於每10秒量測週期內,每秒量測1筆資料,累計10筆後將計算結果發送至無線網路基地台,所需時間550ms耗費能源為3.14uWh(<3.64uWh),驗證符合供需能源平衡設計,達成低功率自給自足電錶。
IoT智慧電錶通訊能力品質驗證
使用無線發送器來量測廠內點對點RF訊後強度,藉此來評估無線網路基地台AP架設範圍,測試結果由→表2所示,機台區內距離資料收集器半徑27公尺內無線接收信號強度(RSSI)可達127dbm(>120dbm代表訊號穩定),故機台區以半徑27公尺作為群組劃分的依據,穿樓層則因會受到管路與樓板阻礙,所以群組劃分皆以水平方式進行,通訊品質符合需求。
方向 | 無障礙 | 機台區 | 穿樓層 |
---|---|---|---|
發射強度 dbm | 250 | 250 | 250 |
通訊距離 (m) | 86 | 27 | 14 |
接收強度 dbm | 135 | 127 | 135 |
IoT智慧電錶量測誤差驗證
依現場三組迴路進行實際驗證無線IoT智慧電錶與FLUKE435量測電流平均誤差比對其誤差值<1%→表3,確認符合設計要求。
測試迴路 |
Fluke435 (平均負載) |
無線CT (平均負載) |
平均誤差比 |
---|---|---|---|
F20B_BUS_EU2_625E_12 | 31.06 A | 30.95 A | -0.36% |
F20B_BUS_EU2_625E_25 | 31.32 A | 31.05 A | -0.87% |
F20B_BUS_EU2_625E_29 | 27.73 A | 27.72 A | -0.03% |
機台端用電量差異資料分析結果
K-means資料分析機台端用電量差異結果
本實驗應用某廠區機台分為158群組來作節能機會點自動預估之模擬,首先利用某一製程功能中選擇23台機台,稱之為A類群組→表4來當Demo Case進行模擬。
Group 分類 | A類 | A類 | A類 | A類 | A類 | A類 | A類 | A類 | A類 | A類 | A類 | A類 | A類 | A類 | A類 | A類 | A類 | A類 | A類 | A類 | A類 | A類 | A類 |
---|---|---|---|---|---|---|---|---|---|---|---|---|---|---|---|---|---|---|---|---|---|---|---|
負載分類 | 2 | 2 | 2 | 2 | 2 | 2 | 2 | 2 | 2 | 2 | 2 | 2 | 2 | 3 | 3 | 3 | 3 | 3 | 3 | 3 | 3 | 3 | 3 |
分類整合 ID | A類-1 | A類-1 | A類-1 | A類-1 | A類-1 | A類-1 | A類-1 | A類-1 | A類-1 | A類-1 | A類-1 | A類-1 | A類-1 | A類-2 | A類-2 | A類-2 | A類-2 | A類-2 | A類-2 | A類-2 | A類-2 | A類-2 | A類-2 |
Tool ID | A類F | A類4 | A類A | A類C | A類7 | A類3 | A類G | A類K | A類8 | A類6 | A類M | A類1 | A類P | A類E | A類L | A類D | A類2 | A類J | A類H | A類5 | A類B | A類9 | A類N |
其節能機會點自動預估之模擬步驟將分三個,如以下敘述。
步驟一 : A類群組機台用電資料分群
將A類群組的每一台機台之用電資料依大小區分為10類群組進行驗證後第二類群之資料與Idle狀態之能耗趨於一致,A類F機台能耗→圖24,A類C機台能耗→圖25,與A類M機台能耗→圖26,在三張圖中都有所標示之兩條線之區間就是Idle狀態之能耗,接下來將進行下一步驟相互比對找Golden Tool。
圖24、A類F機台能耗圖
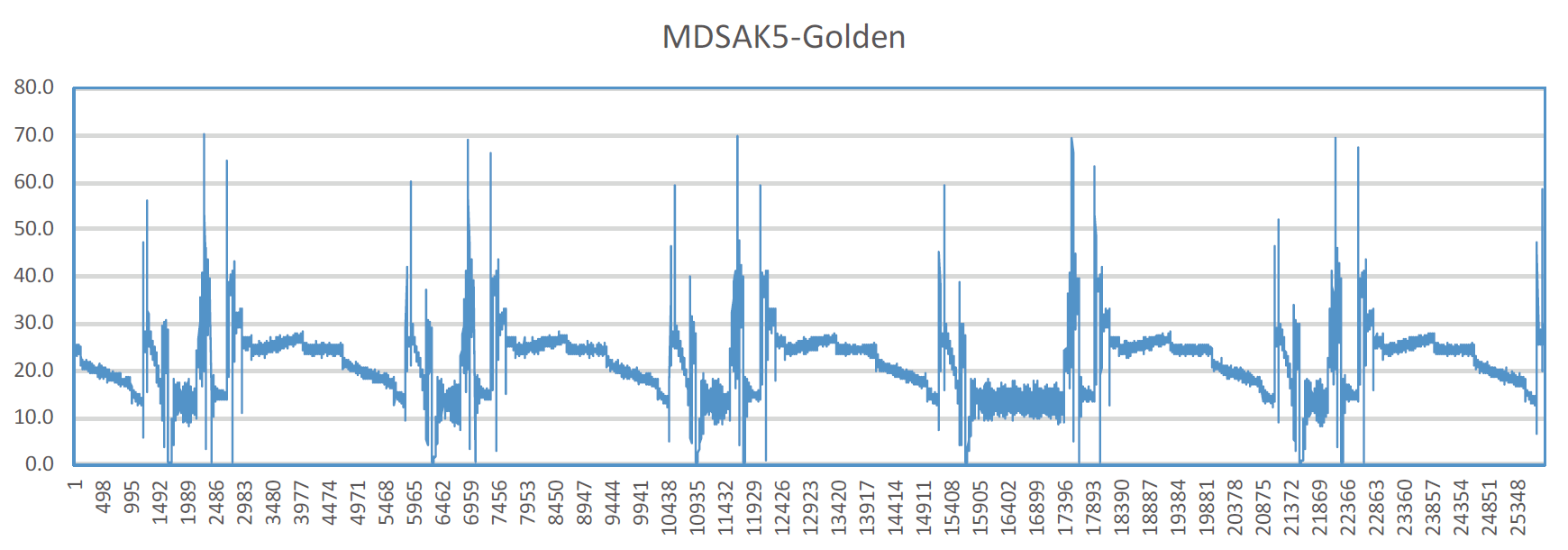
圖25、A類C機台能耗圖
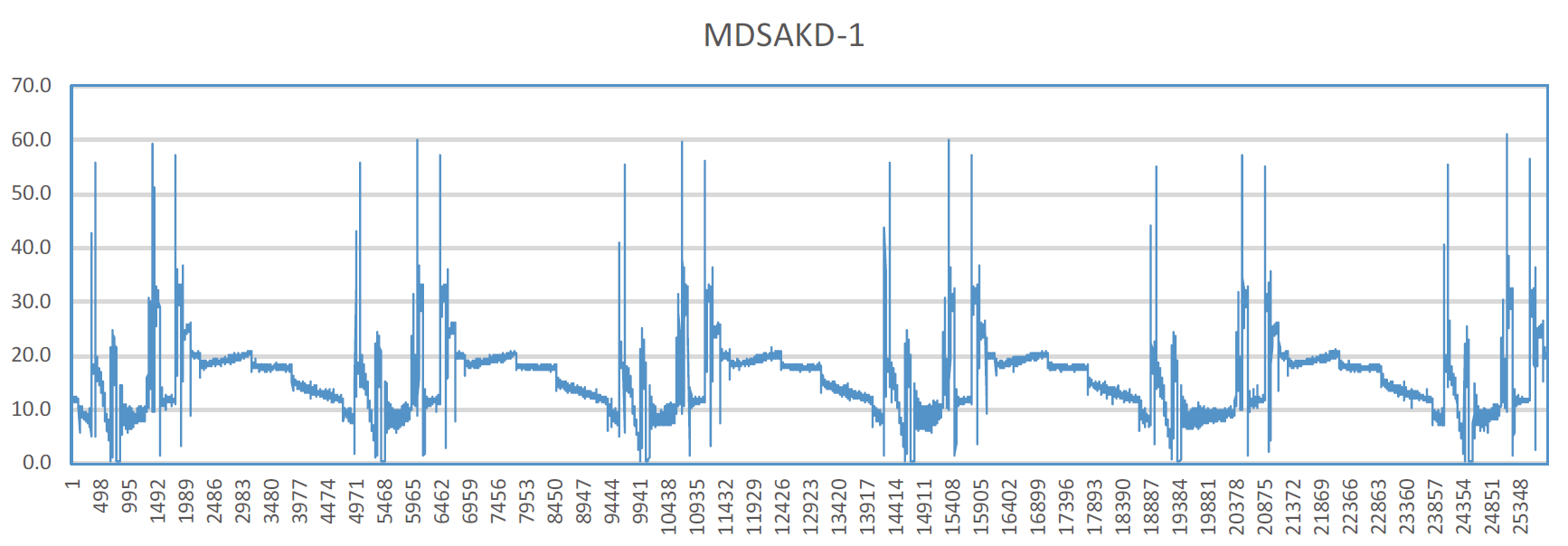
圖26、A類M機台能耗圖
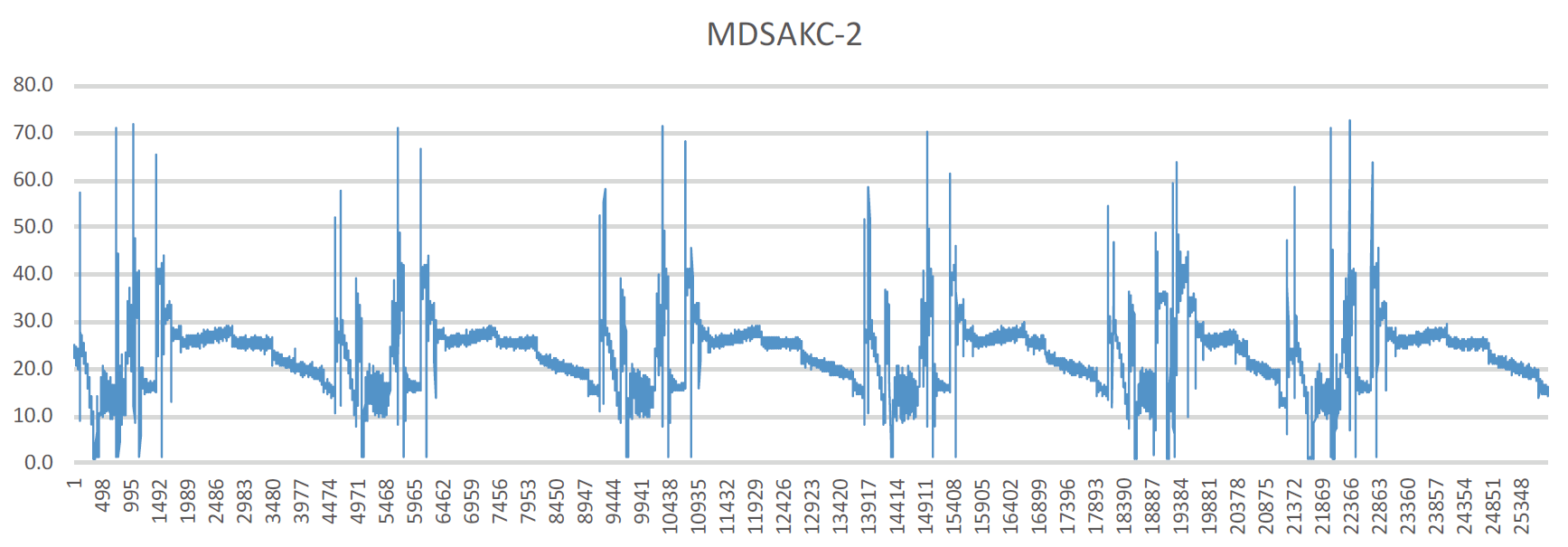
步驟二 : A類群組機台找Golden Tool
將A類群組的每一台機台之Idle能耗進行比對後,依能耗量最低當作Golden Tool,之後再進行下一步驟自動尋找機台用電量差異。
步驟三 : A類群組機台節能機會點自動尋找
將自動計算A類群組所有機台與Golden Tool之Idle能耗差值,之後再進行加總成為A類群組機台之節能機會點→表5,其A類群組機台依負載特性又可分成兩個類組,自動預估機台Idle狀態總節能機會點為79.3度 /hr。
Group 分類 | 負載分類 | 分類整合ID | Tool ID | Idle狀態耗能 | 與golden 之差異 | 機台迴路數 |
---|---|---|---|---|---|---|
A類 | 2 | A類-1 | A類F | 20.31 | ★ | 2 |
A類 | 2 | A類-1 | A類4 | 20.43 | 0.1 | 2 |
A類 | 2 | A類-1 | A類A | 21.13 | 0.8 | 2 |
A類 | 2 | A類-1 | A類C | 21.30 | 1.0 | 2 |
A類 | 2 | A類-1 | A類7 | 21.70 | 1.4 | 2 |
A類 | 2 | A類-1 | A類3 | 24.02 | 3.7 | 2 |
A類 | 2 | A類-1 | A類G | 24.53 | 4.2 | 2 |
A類 | 2 | A類-1 | A類K | 24.98 | 4.7 | 2 |
A類 | 2 | A類-1 | A類8 | 25.68 | 5.4 | 2 |
A類 | 2 | A類-1 | A類6 | 26.30 | 6.0 | 2 |
A類 | 2 | A類-1 | A類M | 28.41 | 8.1 | 2 |
A類 | 2 | A類-1 | A類1 | 28.60 | 8.3 | 2 |
A類 | 2 | A類-1 | A類P | N/A | 0.0 | 2 |
Total | 43.7 | 26 | ||||
A類 | 3 | A類-2 | A類E | 14.87 | ★ | 2 |
A類 | 3 | A類-2 | A類L | 16.13 | 1.3 | 2 |
A類 | 3 | A類-2 | A類D | 16.66 | 1.8 | 2 |
A類 | 3 | A類-2 | A類2 | 17.63 | 2.8 | 2 |
A類 | 3 | A類-2 | A類J | 18.00 | 3.1 | 2 |
A類 | 3 | A類-2 | A類H | 19.82 | 5.0 | 2 |
A類 | 3 | A類-2 | A類5 | 19.85 | 5.0 | 2 |
A類 | 3 | A類-2 | A類B | 19.90 | 5.0 | 2 |
A類 | 3 | A類-2 | A類9 | 20.26 | 5.4 | 2 |
A類 | 3 | A類-2 | A類N | 21.13 | 6.3 | 2 |
Total | 35.6 | 20 | ||||
總合 | 79.3 度 |
內部智慧電網之能源管理系統實現
能源管理平台
台積公司能源管理平台主要以分層管理架構建置,分為四階層→圖27,由最高層工廠範圍(Level1)、特定負載屬性(Level2)、用電部門(Level3)和單機設備(Level4)均採用量身訂做圖形介面與報表架構,有效監控工廠內每一點用電資訊整合至能源管理平台,可建立能源基線制定能源績效指標進行分析比較,找到能源使用基差後,經改正措施後可追蹤成效,符合ISO50001監測、分析、規劃及查核之能管精神。
圖27、台積公司用電群組四階層架構圖
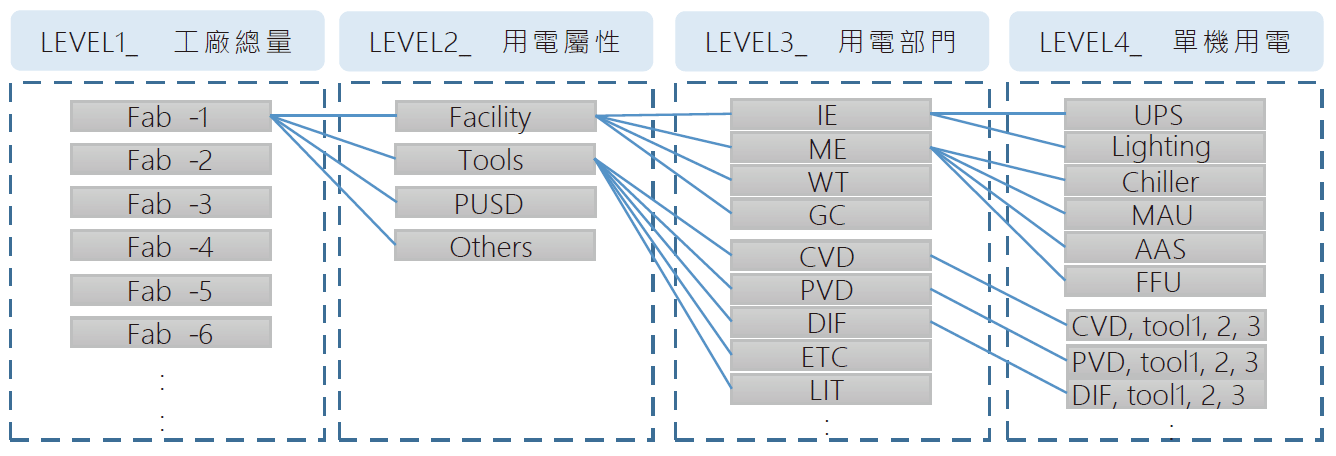
A、Level1管理報表
Level 1定義為單一廠區用電總量,可長期追蹤單一廠區用電趨勢,同時可做為跨廠區電量趨勢比較,其管理報表→表6。
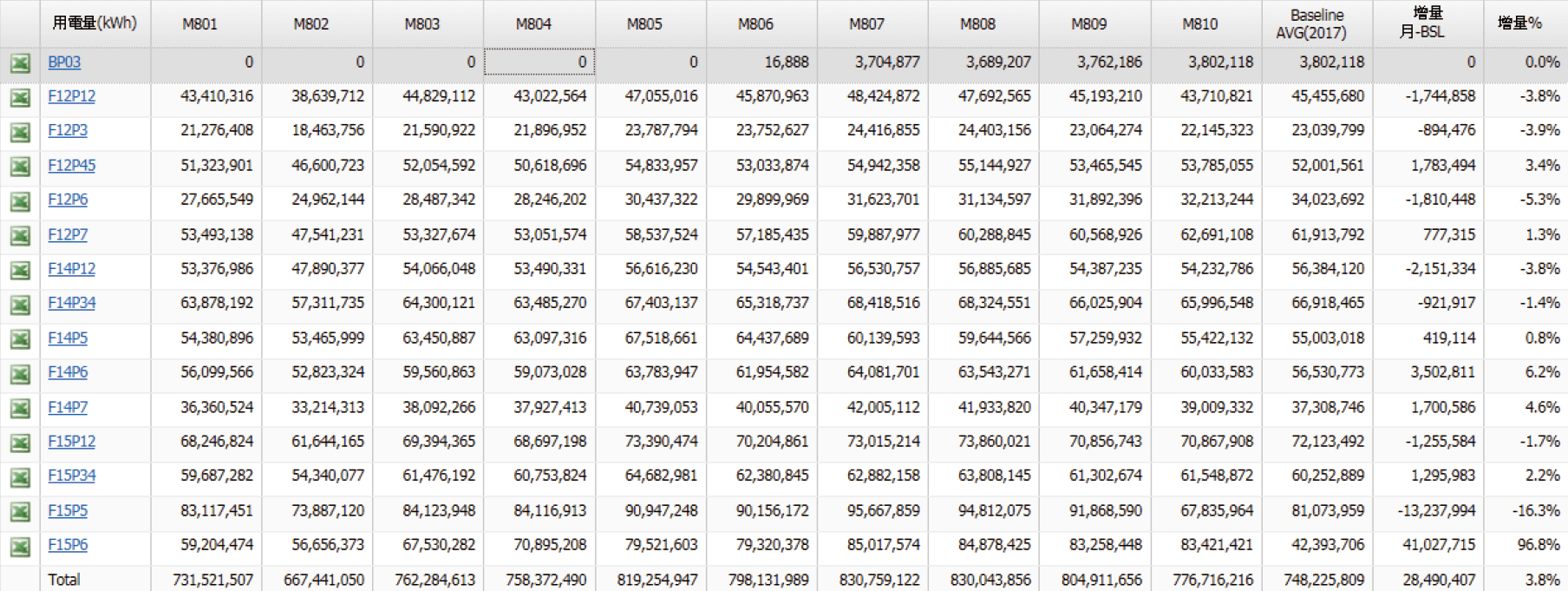
B、Level2管理報表
Level 2定義為用電屬性趨勢追蹤,單一工廠用電屬性分為生產機台、廠務、辨公室與其他等,其管理報表→表7。
M810 FAC 總用電較Baseline 減少 96.8萬度
M810 Tools 總用電較Baseline 增加 56.2萬度
M810 PUSD 總用電較Baseline 減少 13.7萬度
用電量 (kWh) | M801 | M802 | M803 | M804 | M805 | M806 | M807 | M808 | M809 | M810 | Baseline AVG(2017) | 增量 月-BSL | 增量% |
---|---|---|---|---|---|---|---|---|---|---|---|---|---|
FAC | 25,466,165 | 22,393,236 | 25,973,722 | 26,534,402 | 29,316,568 | 28,747,492 | 29,618,113 | 29,265,061 | 28,020,877 | 26,124,764 | 27,092,792 | -968,028 | -3.6% |
Tools | 28,246,392 | 26,503,566 | 29,424,098 | 28,494,224 | 29,473,325 | 28,242,009 | 29,103,717 | 28,841,925 | 27,815,005 | 27,868,541 | 27,306,340 | 562,201 | 2.1% |
PUSD | 638,299 | 545,711 | 639,992 | 604,868 | 642,803 | 618,682 | 641,310 | 527,903 | 464,699 | 462,777 | 600,091 | -137,314 | -22.9% |
Others | 30,039 | 4,023,486 | 7,413,075 | 7,463,822 | 8,085,966 | 6,829,506 | 776,453 | 1,009,677 | 959,352 | 966,050 | - | - | - |
C、Level3管理報表
Level 3定義為部門用電趨勢追蹤,用電屬性分為各個不同功能部門首先需清查所有負載清單,再將對應電源歸納至對應部門,其管理報表→表8。
M810 FAC 總用電較 Baseline 減少 96.8萬度
用電量(kWh) | M801 | M802 | M803 | M804 | M805 | M806 | M807 | M808 | M809 | M810 | Baseline AVG(2017) | 增量 月-BSL | 增量% |
---|---|---|---|---|---|---|---|---|---|---|---|---|---|
F14P5 FAC | 25,466,165 | 22,393,236 | 25,973,722 | 26,534,402 | 29,316,568 | 28,747,492 | 29,618,113 | 29,265,061 | 28,020,877 | 26,124,764 | 27,092,792 | -968,028 | -3.6% |
用電量前三名: Chiller, CDA, MAU+FFU
用電量增加: UPS Power(21.4萬度), WWT(7萬度), UPW(2.1萬度)
F14P5 FAC | M801 | M802 | M803 | M804 | M805 | M806 | M807 | M808 | M809 | M810 | Baseline AVG(2017) | 增量 月-BSL | 增量% | |
---|---|---|---|---|---|---|---|---|---|---|---|---|---|---|
FAC-ME | Chiller | 6,458,684 | 5,733,551 | 7,290,267 | 8,100,121 | 10,132,741 | 10,298,195 | 10,546,100 | 10,354,482 | 9,818,051 | 8,340,112 | 8,460,047 | -119,935 | -1.4% |
FAC-GC | CDA | 3,470,633 | 3,322,377 | 3,774,728 | 3,839,693 | 3,856,311 | 3,593,215 | 3,703,618 | 3,658,707 | 3,571,669 | 3,412,559 | 3,485,726 | -73,167 | -2.1% |
FAC-ME | MAU+FFU | 2,588,890 | 2,347,190 | 2,650,267 | 2,589,658 | 2,655,974 | 2,608,577 | 2,604,888 | 2,584,392 | 2,515,009 | 2,514,533 | 2,537,058 | -22,525 | -0.9% |
FAC-ME | AAS | 2,572,609 | 2,314,241 | 2,575,611 | 2,492,972 | 2,594,873 | 2,512,148 | 2,588,350 | 2,567,426 | 2,535,957 | 2,498,118 | 2,497,333 | 786 | 0.0% |
FAC-WT | PCW | 2,567,089 | 2,345,831 | 2,568,712 | 2,461,307 | 2,536,472 | 2,439,203 | 2,519,536 | 2,519,981 | 2,445,202 | 2,449,814 | 2,521,451 | -71,638 | -2.8% |
FAC-IE | Utility | 3,086,919 | 2,070,796 | 2,293,363 | 2,214,814 | 2,295,528 | 2,227,531 | 2,314,079 | 2,271,907 | 2,162,320 | 2,170,641 | 2,990,688 | -820,047 | -27.4% |
FAC-IE | UPS Power | 1,633,286 | 1,465,835 | 1,633,658 | 1,583,869 | 1,636,777 | 1,593,539 | 1,684,051 | 1,676,604 | 1,480,688 | 1,589,429 | 1,375,098 | 214,330 | 15.6% |
FAC-ME | Chiller Pump | 1,520,062 | 1,361,245 | 1,594,590 | 1,701,663 | 2,012,653 | 1,956,868 | 2,072,959 | 2,001,433 | 1,862,582 | 1,563,132 | 1,713,665 | -150,533 | -8.8% |
FAC-WT | UPW | 1,059,617 | 966,006 | 1,071,112 | 1,029,176 | 1,058,375 | 1,026,085 | 1,078,857 | 1,084,718 | 1,049,185 | 1,017,284 | 995,854 | 21,430 | 2.2% |
FAC-WT | WWT | 339,021 | 310,979 | 347,520 | 347,765 | 360,681 | 324,366 | 330,270 | 353,322 | 355,329 | 346,755 | 276,509 | 70,246 | 25.4% |
FAC-GC | BSGS/TMAH | 98,046 | 93,166 | 104,729 | 101,288 | 103,655 | 98,006 | 102,323 | 102,073 | 99,908 | 99,422 | 98,721 | 701 | 0.7% |
FAC-GC | CDA dryer | 71,309 | 62,019 | 69,166 | 70,158 | 70,551 | 67,817 | 71,082 | 68,643 | 65,967 | 62,315 | 62,315 | 0 | 0.0% |
FAC-IE | SPARE | 0 | 0 | 0 | 0 | 0 | 0 | 0 | 20,253 | 57,926 | 59,570 | 59,570 | 0 | 0.0% |
FAC | 無載 | 0 | 0 | 0 | 1,917 | 1,979 | 1,940 | 1,999 | 1,120 | 1,083 | 1,081 | 1,081 | 0 | 0.0% |
D、Level4管理平台
Level 4定義為機台用電及節能趨勢追蹤,應用IoT智慧電錶收集資料後經過K-means大數據分析之方法自動運算各部門機台待機狀況的耗能與預估節能量,並可透過此功能共各製程群組之機台負責人來管理與追蹤其各製程群組的機台是否可以達到節能預估量→圖28。
圖28、同組群機台待機用電狀態分析畫面
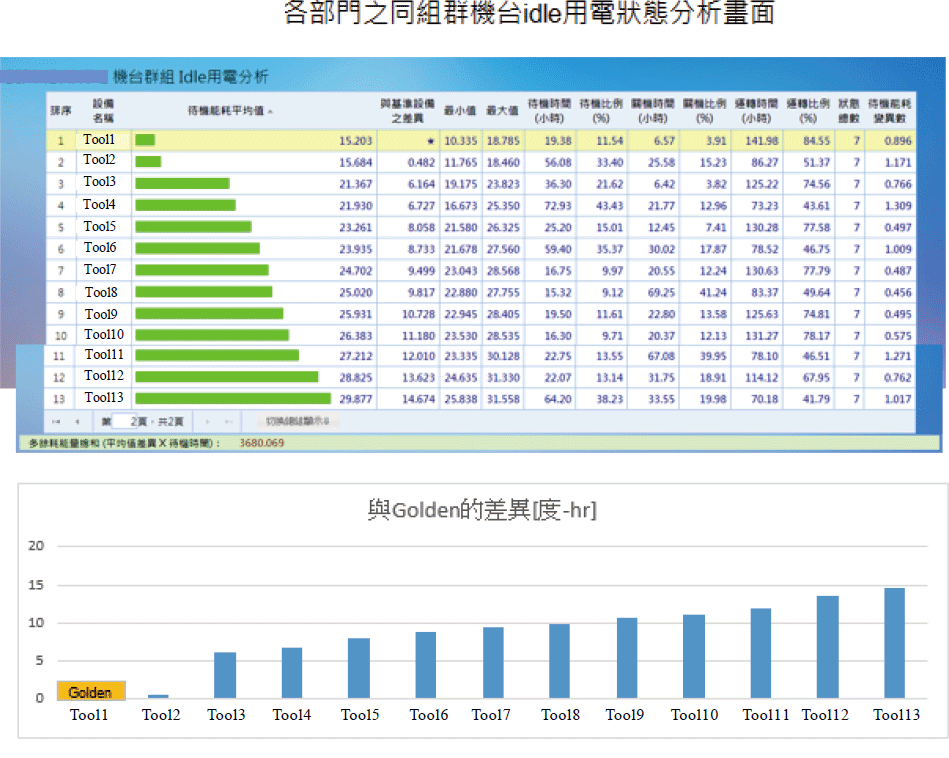
結論
本文依據ISO 50001與SEMI S23製程機台能耗管理規範來開發一套建構台積電製程機台能源管理系統。這套管理系統所需要的機台用電資料取得已成功運用到全新開發低能耗無線電錶IoT的技術,團隊經由近一年時間與開發廠商合作,領先業界實際建構於一個完整廠區的資料收集無線網路,證明在比傳統有線數位電錶低75%的成本與90 %的能耗之IoT電流量測應用上,驗證其取樣頻率、儲存功率平衡及精準度上皆足以被廣泛應用於機台端用電資料 。
本文利用狀態估測分析手法也證明將IoT電流取得的單相電流資訊與既有數位功率電錶數據結合計算後,可說明在建構能耗資料擷取的過程中,不需所有用電節點皆須以完整耗能量測,亦可形成一個兼具成本優勢且滿足數據可備使用性高。依此次研究模型採用60%單向電流資訊與40%完整用電資訊結合建立這些參考數據建立後經製程設備用電耗能分析流程,即可建立由上層廠區、部門分類、功能群組再至每個單一製程機台耗電量,得以形成一個明確的用電量追蹤管理及差異管理。
根據能源管理實務經驗,半導體製程機台所需其他非電力資源配置佔比以電力能源約 66%為最高,在本研究選定電力能源為優先發展,已發展一套有效能源方案與技術,待將來其他其他非電力能源感知器成熟,可將此方法擴大應用達到全方位製程機台能源管理的目標。
誌謝
本研究非常感謝泓格科技股份有限公司於產品開發之協助,僅此致謝。
參考文獻
- 台灣電力公司民國106年發電總量為2,310.8億度,台積公司民國106年度企業社會責任報告書揭露電力使用總量108億度,佔台電售電量的4.7%。
- 台積公司民國105年度企業社會責任報告書,單位產品用電量較民國99年減少8.5%,總節能度數為0.91億度。
- 台積公司民國106年度企業社會責任報告書,單位產品用電量較民國99年降低11.4% ,總節能度數累積為6億度。
- J. Alber , State Estimation in PowerFactory: Algorithmic Aspects, RTE-VT workshop, Paris, May 29-30, 2006.
- SEMI S23-0813 - Guide for Conservation of Energy, Utilities and Materials Used by Semiconductor Manufacturing Equipment.
- SEAJ-E-003E — Guideline for conducting an LCA (Life-cycle Assessment)of Semiconductor Manufacturing Equipment.
- ISO 50001 : 2018(en)-Energy management systems.
- 陳朝順、辜德典、林科亦、康晉承、賴宥杰、吳美靜,整合需量反應之智慧型數位電錶設計,國立中山大學電機工程學系; 義守大學電機工程學系。
- DIgSILENT PowerFactory 15, User Manual, Chapter 41State Estimation.
- 陳榮昌、林育臣 (民91年)群聚演算法之比較及群聚參數的分析與探討。第三屆網際網路應用與發展研討會。
- https://www.etip-snet.eu/
- https://www.eia.gov/
- https://www.moeaboe.gov.tw,經濟部能源局能源用戶節約能源查核申請表(附表1-工業及其他生產性質行業)
留言(0)