摘要
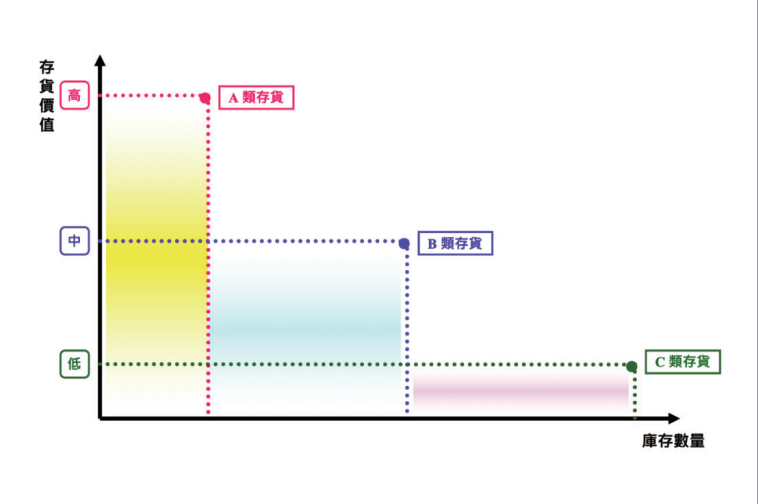
廠務庫房安全庫存量自動預警系統
Keywords / FAC Warehouse2,Safety Stock,Inventory Management,Supply Chain Management
在公司廠房迅速擴充和全球供應鏈缺料情況之下,物料的需求量與交期大幅上升,「安全庫存」的執行變得更加重要。透過廠務資產管理系統(Facility Asset Management, FAM)依據過去實際領料量建置一套安全庫存管理機制,結合物料訂購進度追蹤系統,實現廠務物料統一由廠務庫房負責備貨的目標,提供需求預估、開單訂貨、交期追蹤、點收人庫的一條龍服務。對於廠務而言,可達到節省備貨處理時間、領料步驟簡單、並可降低庫存存放空間與成本、增加庫存調撥彈性;對於供應商而言,廠務庫房為交貨單一窗口,可減少聯絡時間與交貨運輸趟次成本。本文即透過廠務庫房納管運轉領料單(Material Requirement, MR)的領料方式,說明安全庫存的邏輯設計與補貨機制、系統應用與管理、執行成效以及未來方向。
Because rapid expansion of the company's factory and Lack of materials in the global supply chain, Material demand and delivery time increased significantly, "Safety stock" becomes more indispensable.
Establish the safety stock management mechanism through the past actual material picking quantity of the Facility Asset Management(FAM). Then combined with the material order progress tracking system. To realize that facility warehouse is uniformly responsible for stocking up for facility materials, provide one-stop service of demand estimation, place an order for goods, delivery tracking, and take delivery of goods.
For the facility, it can achieve that the facility engineers only need to directly pick up materials, and the facility warehouse can save time for stocking up, reduce storage space and cost of inventory, and increase the flexibility of inventory allocation.
For the suppliers, the facility warehouse is a single window for delivery, which can reduce contact time and delivery transportation costs.
This article mainly aimed at the method of picking materials for the facility warehouse management facility operation Material Requirement(MR), explain the logic design and replenishment mechanism of safety stock, system application and management, implementation effect and future direction.
1. 前言
1.1 過去領料問題
以往透過領料單(MR)的領料方式,需由廠務、採購、物管、供應商、公司庫房及廠務庫房的多方配合,而因
- 廠務各自提出需求,較難掌握全貌。
- 廠務需自行向採購和供應商追蹤訂單進度。
- 廠務需與供應商協調交貨時間。
- 廠務需將物料至公司庫房過帳後再帶回廠務庫房入庫及領料。
- 採購無單一窗口確認訂單合理性。
- 供應商交期資訊不透明。
- 無法控管物料皆確實入庫。
以上種種問題造成多方單位運轉困難重重。隨著領料單需求倍增,物料管理與訂單管理面臨相當大的考驗,時常發生供應商未能及時接獲訂單而無法先行備貨,對於廠務的緊急需求難以應變,進而導致缺料之情形。
1.2 公司庫房安全庫存管理
公司庫房的安全庫存建置邏輯為當過去一年內有領用紀錄之月份數 (Month of Usage, MOU)大於9時,再啟動備貨機制。其安全庫存設定為過去三個月平均領用量,計算邏輯簡單且未考量物料的使用頻率、供應商的交期及廠區內的生產周期等因素,且對於廠務大宗的設備零件領用Material No.3Fxxxxxx不執行安全庫存機制,使得廠務的物料需求無法仰賴公司庫房,必須自食其力。
2. 文獻探討
2.1 安全庫存(Safety Stock, SS)
根據美國營運管理協會(APICS)的定義,庫存是用於支援生產、生產相關活動、以及滿足客戶需求時所需使用到的物件。其目的為了滿足預期性需求、週期性需求、變動性需求、防止短缺以及提高設備資源利用率等。庫存管理主要目的有兩項,一為維持最高客戶服務水準、二為使存貨最小化,兩者經常牴觸,必須取得平衡點,因此,透過安全庫存與訂購點的設定可促使庫存水準與客戶服務水準達成均衡,其安全庫存與再訂購點(Reorder Point, ROP)關係,主要可分為以下兩種類型:
- 定期訂購模型(P model):又稱為「經濟訂購期模型」(Economic Order Period, EOP),為時間導向,限制在固定週期後,視清點或檢視庫存量決定是否再訂購,僅在週期到達時啟動。
- 定量訂購模型(Q model):又稱為「經濟訂購量模型」(Economic Order Quantity, EOQ),為事件導向,當庫存下降至再訂購點時,即會再訂購,其發生時機是依據產品需求而定,故在任何時間均可能發生。安全庫存與再訂購點計算方式如下:
❶ 固定前置時間與周定需求率
❷ 固定前置時間與變動需求率
❸ 變動前置時間與固定需求率
❹ 變動前置時間與變動需求率
圖1:定量訂購與定期訂購兩種系統的比較
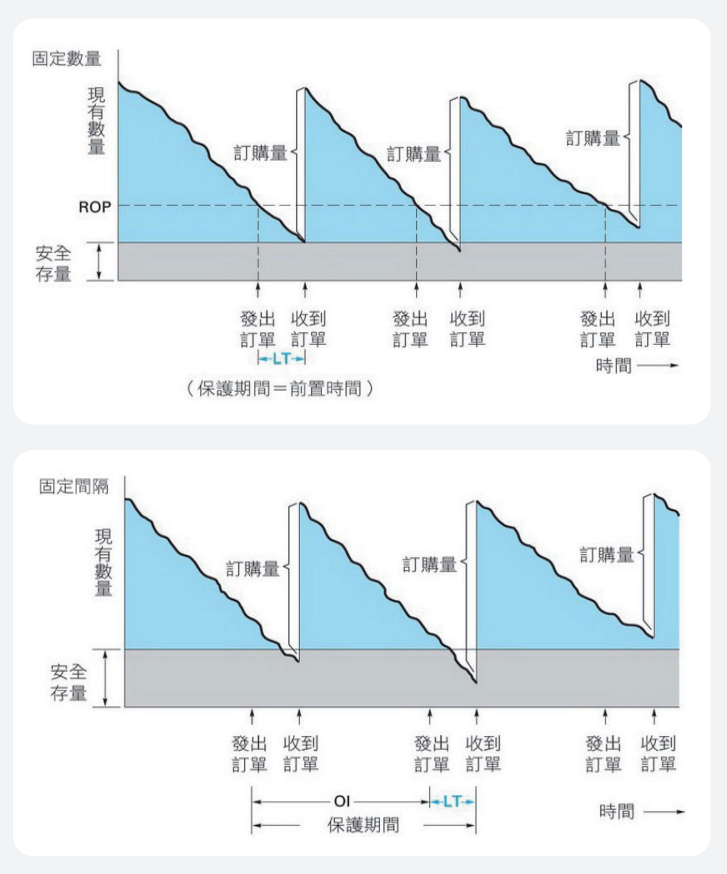
2.2 ABC分類法(Activity Based Classification)
ABC分類法是由義大利經濟學家柏拉圖1897年首創,管理學家戴克1951年將其應用至庫存管理,ABC分類法的核心思想是在決定一個事物的眾多因素中分清主次,識別出少數的但對事物起決定作用的關鍵因素和多數的但對事物影響較少的次要因素,將各組成部分分為ABC類,如圖2所示,A類是管理的重點,B類是次重點,C類是一般,在庫存管理中,通常將物料依據存貨價值分為 A、B、C三類,制定不同的管理方法,如表1所示。
圖2:ABC分類法示意圖
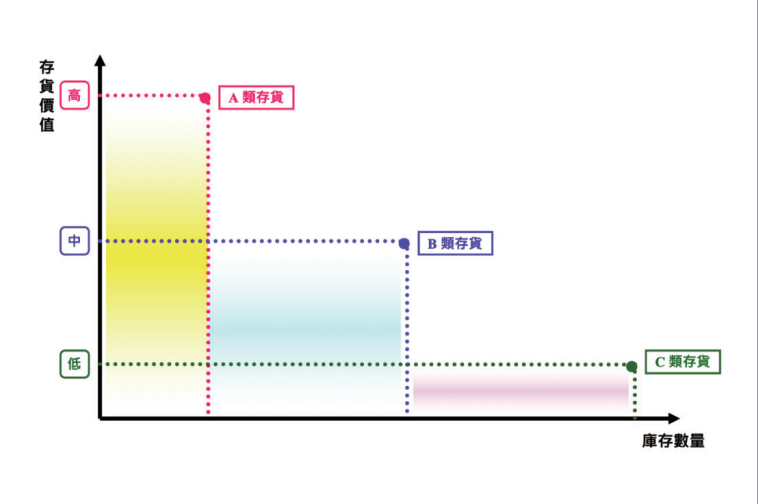
類別 | A | B | C |
---|---|---|---|
價值 | 高 | 中 | 低 |
管理重點 |
|
|
|
訂單量 | 少 | 較多 | 多 |
訂貨方式 | 定期定量接經濟批量訂單 | 定量訂貨 | 按經驗訂貨,可採用訂貨雙堆法管理庫存 |
檢查方式 | 經常檢查和盤存 | 一般檢查和盤存 | 按年度或季度檢查盤存 |
記錄 | 最準確、最完整 | 正常記錄 | 簡單記錄 |
統計方式 | 詳細統計,按品種規格等細項進行統計 | 按大類進行統計 | 按金額統計 |
2.3 盒鬚圖判別法
一批數據中的異常值值得關注,忽視異常值的存在是十分危險的,不加剔除地把異常值包括進數據的計算分析過程中,對結果會帶來不良影響;重視異常值的出現,分析其產生的原因,經常成為發現問題進而改進決策的契機。盒鬚圖(圖3)(box-and-whisker plot)是於1977年由美國著名統計學家約翰·圖基(John Tukey)發明,為我們提供識別異常值的標準,以了解資料的偏斜性(skewness)及離群值(outliers),適用於比較數值資料群組的範圍和分佈,由帶鬚值的方塊以及中間的中心線說明,鬚值代表高參考值和低參考值,用於排除異常值。
圖3:盒鬚圖示意圖
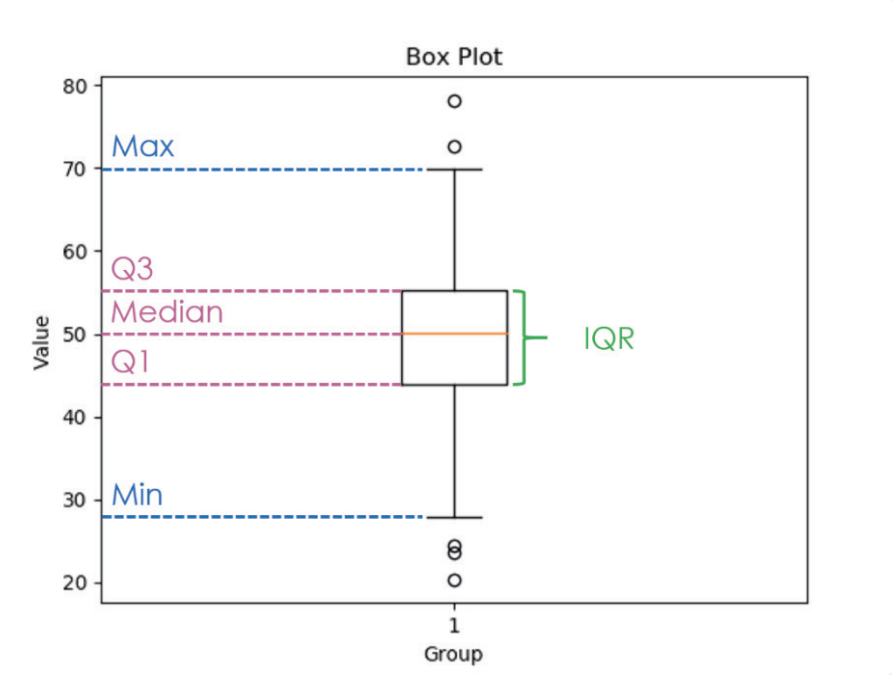
盒鬚圖使用統計學的四分位數(Quartile)的概念,所謂四分位數,就是把組中所有資料由小到大排列並分成四等份,處於三個分割點位置的數字就是四分位數。
- 第一四分位數(Q1):Y0.25=45
- 第二四分位數(Q2):Y0.5=50
- 第三四分位數(Q3):Y0.75=55
- 四分位距(InterQuartile Range, IQR):Q3-Q1=10
- 四分位差(Quartile Deviation, QD):
- 限制線範圍:Q1-1.5IQR~Q3+1.5IQR=30~70
- 異常值:限制線範圍以外的數據皆為異常值
3. 建立安全庫存措施
3.1 邏輯設計與補貨機制
廠務使用的物料有成千上萬個物料,若要使庫房完全無料號庫存不足的情況,則必定將庫房的庫存量備貨至極大值,而因考量庫存的金額與擺放物料空間,必須參考過去物料領用量來設定安全庫存值,並在庫存量與領用量間取得平衡。
廠務庫房安全庫存管理有下列四個先決條件:
- 分別建立F12、F15、F14、F18廠區的安全庫存。
- FAM料件主檔狀態為Active的30、3F料號納管。
- 依過去一年的領用量,作為物料分類的計算因素。
- 每月一號重新計算安全庫存。
主要的物料分類分為兩階層,第一層是透過MOU的高低值設定Rule,其MOU大於0即執行備貨,第二層則是藉由Rule不同有個別的安全庫存計算方式,進而進行不同的備貨方案。優於公司庫房的安全庫存管理模式,不分廠區備貨且僅針對MOU大於9再啟動備貨,兩者安全庫存管理模式比較如表2所示。
比較項目 | 公司庫房 | 廠務庫房 | ||
---|---|---|---|---|
廠區設定 | 不分廠區 | 分為 F12、F15、F14、F18 廠區 | ||
納入料號 | 30 料號 | 30、3F料號 | ||
備貨依據 | MOU>9 | MOU>0 | ||
安全庫存 |
|
RULE 1 | RULE 2 | RULE 3 |
依盒鬚圖分為五種類型 | 參考去年下一季領用量 | 有需求提出 | ||
扣帳方式 | 領用再扣帳 | 提前開立 MR 且入庫即扣帳 |
3.1.1 Rule1說明
Rule1定義為MOU大於4的常用料,主要分為定量訂購與月訂購兩種模式,其邏輯設計與補貨機制如下說明。
➀定量訂購
❶邏輯設計:
藉由利用過去一年領用量的最小值(Min)、第一四分位數Q1(P25)、第二四分位數Q2(Med)、第三四分位數Q3(P75)、最大值(Max),繪製成盒鬚圖,再依盒鬚圖盒子的類型,分為五種Type設定安全庫存的計算公式,如表3所示。
Type | 系統判斷公式 | 盒鬚圖 | 圖示 | 物理意義 | 安全庫存計算公式 |
---|---|---|---|---|---|
Type1 | P75=MED=P25 | 無盒子 | ![]() |
月領用量幾乎為定量(7),偶爾有月領用量為4或是10 | P75=MED=P25=7 |
Type2 |
MAX=P75≥MED≥P25=MIN 且MAX=P75≠P25=MIN |
盒子佔滿大小值 | ![]() |
月領用量固定最高值(12)/最低值(6) | MAX=P75=12 |
Type3 |
(1).|P75-MED|>|MED-P25|且MAX=P75不能同時P25=MIN |
盒子在偏上 | ![]() |
大多月領用量高於中位數(10) | P75=13 |
Type4 |
P75-MED=MED-P25且P75≠MED≠P25 且MAX≠P75&P25≠MIN |
盒子在中間 | ![]() |
月領用量平均分配在24-28 | (MED+P75)/2=27 |
Type5 |
(1).|P75-MED|<|MED-P25|且MAX=P75不能同時P25=MIN |
盒子在偏下 | ![]() |
大多月領用量低於中位數(7) | MED=7 |
❷補貨機制:
參考定量訂購模型,當廠務資產管理系統(FAM)的01.領料(-)與13.新裝機工程領料(-)申請單結案,系統自動檢查申請單的廠區與料號,其對應的共用庫存與安全庫存之關係,可分為下列三種狀況:
- 若共用庫存不小於安全庫存,則不產生待訂購項目。
- 若申請單結案前,共用庫存不小於安全庫存,當因申請單結案後,使得共用庫存小於安全庫存,則產生待訂購項目,其數量為申請單數量減共用庫存與安全庫存之差值,成本中心為申請單的需求單位。
- 若申請單結案前,共用庫存小於安全庫存,當申請單結案後,共用庫存小於安全庫存,則產生待訂購項目,其數量為申請單數量,成本中心為申請單的需求單位。
❸舉例說明:(圖4)
- 問題:當有領料申請單結案時,系統會自動檢查料號的共用庫存是否不小於安全庫存,如果共用庫存小於安全庫存量時,該如何補足數量?
- 答案:假設共有庫存為25個,當領料申請單結案8個,六月安全庫存為20個,系統會產生待訂購項目3個,成本中心為領料申請單的需求單位。
圖4:Rule1定量訂購舉例說明

➁ 月訂購
❶邏輯設計與補貨機制:
隨著依據過去一年領用量的月份滾動,每個月一號將會重新計算安全庫存,系統自動檢查下個月安全庫存與上個月安全庫存之關係,可分為下列兩種狀況:
- 若下個月安全庫存不大於上個月安全庫存,則不產生待訂購項目。
- 若下個月安全庫存大於上個月安全庫存,則產生待訂購項目,其數量為下個月安全庫存與上個月安全庫存的差值,成本中心為上個月領用最多的需求單位。
❷舉例說明一:(圖5)
- 問題:安全庫存會隨著每個月參考前一年的領用紀錄區間不同,使MOU改變,Rule也可能改變,當Rule改變,計算安全庫存的方式也會有所變更,而安全庫存變更時,該如何補足數量?
- 答案:假設共用庫存為100個,七月安全庫存為80個,八月安全庫存為120個,系統會產生待訂購項目20個,成本中心為上個月領最多的需求單位。
❸舉例說明二:(圖6)
- 問題:領料單(MR)開立後至物料入庫結案的期間,若遇到月份轉換,系統重新計算下個月的安全庫存,而因月份轉換所產生的月訂購量,月訂購量該如何補足數量?
- 答案:假設共用庫存為75個,七月安全庫存為80個,八月安全庫存為90個,在途訂單為5個,系統會產生待訂購項目10個,成本中心為上個月領最多的課別單位。
圖5:Rule1月訂購舉例說明一

圖6:Rule1月訂購舉例說明二

3.1.2 Rule2說明
Rule2定義為MOU不大於4的非常用料,訂購模式為季訂購,其邏輯設計與補貨機制如下說明:
➀邏輯設計
透過以季領用量為單位,依據去年下一季的領用量,設定為當季的安全庫存值。
➁補貨機制
參考定期訂購模型,廠務庫房規劃每季訂購一次,於每季的第一天,系統自動產生安全庫存與共用庫存之差值的待訂購項目,成本中心為去年下一季領用最多的課別,訂購時間與進貨量參考時間對應表,如表4所示。
實際領用紀錄 | ||||||||||||||||||||||||
---|---|---|---|---|---|---|---|---|---|---|---|---|---|---|---|---|---|---|---|---|---|---|---|---|
年 | 2020 | 2021 | ||||||||||||||||||||||
月 | 1 | 2 | 3 | 4 | 5 | 6 | 7 | 8 | 9 | 10 | 11 | 12 | 1 | 2 | 3 | 4 | 5 | 6 | 7 | 8 | 9 | 10 | 11 | 12 |
Q´ty | 0 | 0 | 0 | 12 | 0 | 0 | 6 | 0 | 0 | 0 | 12 | 0 | 0 | 0 | 6 | |||||||||
訂購時間 | 使用物料時間 | 進貨量參考時間 | 進貨量(安全庫存量)計算 | |||||||||||||||||||||
2021年1月 | 2021年4~6月 | 2020年4~6月 | 12+0+0=12 | |||||||||||||||||||||
2021年4月 | 2021年7~9月 | 2020年7~9月 | 6+0+0=6 | |||||||||||||||||||||
2021年7月 | 2021年10~12月 | 2020年10~12月 | 0+12+0=12 | |||||||||||||||||||||
2021年10月 | 2022年1~3月 | 2021年1~3月 | 0+0+6=6 |
3.1.3 Rule3說明
Rule3定義為MOU等於0的物料,訂購模式為加單訂購,其邏輯設計與補貨機制如下說明:
➀邏輯設計
除了MOU等於0,下列三種類型的物料皆設定為Rule3,並將安全庫存設為等於0。
- Life Time物料,例如:儀電課電池、氣化課Scrubber吸附劑與化學品。
- 再生濾網,例如:FFU TOC Regen Filter、Tool TOC Regen Filter。
- Sunset物料,例如:機械課LSC物料轉Turnkey與AMC堆疊非再生濾網。
➁補貨機制
為避免因備貨導致庫存變為滯料,因此廠務庫房不進行備貨,若廠務有需求,則需提早提出加單申請,當加單訂購物料到貨後,廠務庫房透過庫存櫃位課別的管理,將庫存建置於加單庫存,僅保留給申請加單訂購的課別做領料,保障申請課別的使用權益,如表5所示。
安全庫存:設定為0 |
---|
NOTE |
|
3.1.4 小結
綜合3.1.1、3.1.2、3.1.3所提的安全庫存邏輯設計與補貨機制,其訂購與扣帳模式統整如表6所示。而廠務庫房的安全庫存邏輯設計,除了透過過去一年領用量計算安全庫存之外,並加入交期的因素,於系統設定交期與倍數之關係,再將安全庫存乘以倍數,可得最終安全庫存值。若廠務欲調整系統計算的安全庫存,可向廠務庫房申請調整安全庫存,以避免需求上升而不及備貨造成斷料的情形。
項目 | 1.定量訂購 | 2.月訂購 | 3.季訂購 | 4.加單訂購 |
---|---|---|---|---|
Rule | Rule1 | Rule1 | Rule2 | Rule3 |
訂購時機 | 共用庫存小於安全庫存 | 每個月的第一天 | 每季的第一天 | 加單申請核准 |
訂購數量 | 安全庫存-(共用庫存+在途量) | 下月安全庫存-下月安全庫存 | 去年下一季的共用庫存總領用量 -(共用庫存+在途量) | 加單申請數量 |
扣帳對象 | 領用後使共用庫存小於 安全庫存的成本中心 | 上月領用最多 的成本中心 | 去年下一季領用最多 的成本中心 | 加單申請成本中心 |
扣帳依據 | MR單的成本中心 | |||
扣帳時間點 | 公司庫房GI |
3.2系統應用與管理
廠務庫房安全庫存納管料號千千萬萬,每月的MOU、Rule、Type及安全庫存計算,加上定量訂購、月訂購、季訂購及加單訂購的待訂購項目計算,接續待訂購項目開立領料單(MR)後的訂單與入庫追蹤,日理萬機,因此必須仰賴系統計算安全庫存與待訂購項目,以及管理並追蹤訂單跟入庫資訊。
3.2.1 安全庫存管理系統
安全庫存管理系統建置於廠務資產管理系統(FAM),其主要頁面包含安全庫存、待訂購及加單申請,頁面進入方式如圖7所示。
圖7:安全庫存管理系統
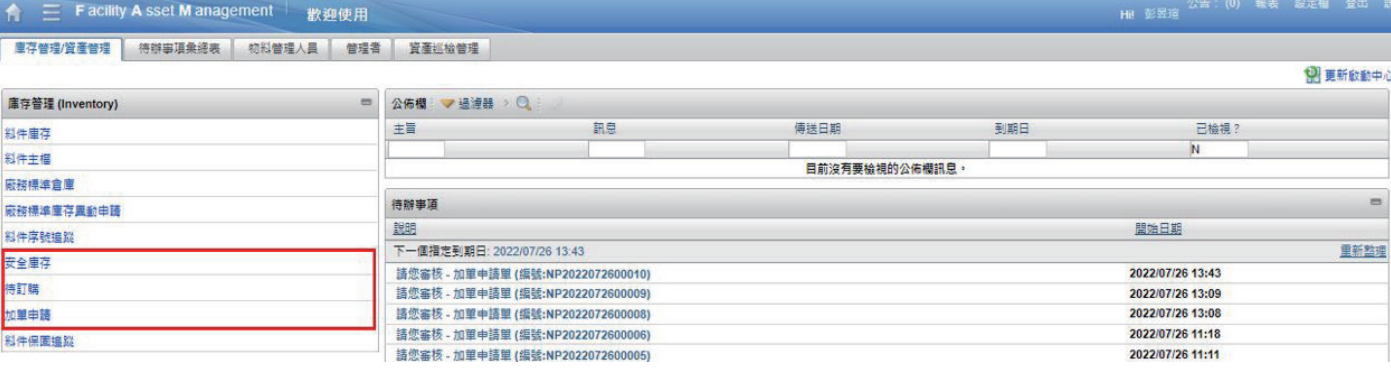
➀ 安全庫存
- 主要功能:提供查詢每月安全庫存的相關資訊,例如:廠區、料號、MOU、Rule、安全庫存、即時庫存、共用庫存、加單庫存以及Lead Time等資訊,如圖8所示。
- 效益:對於廠務而言,可藉由此頁面檢視安全庫存是否合理,與迅速查詢共用庫存欄位得知可領料數量,對於廠務庫房而言,可藉由此頁面紀錄Lead Time與廠務申請調整安全庫存的原因。
圖8:待訂購頁面
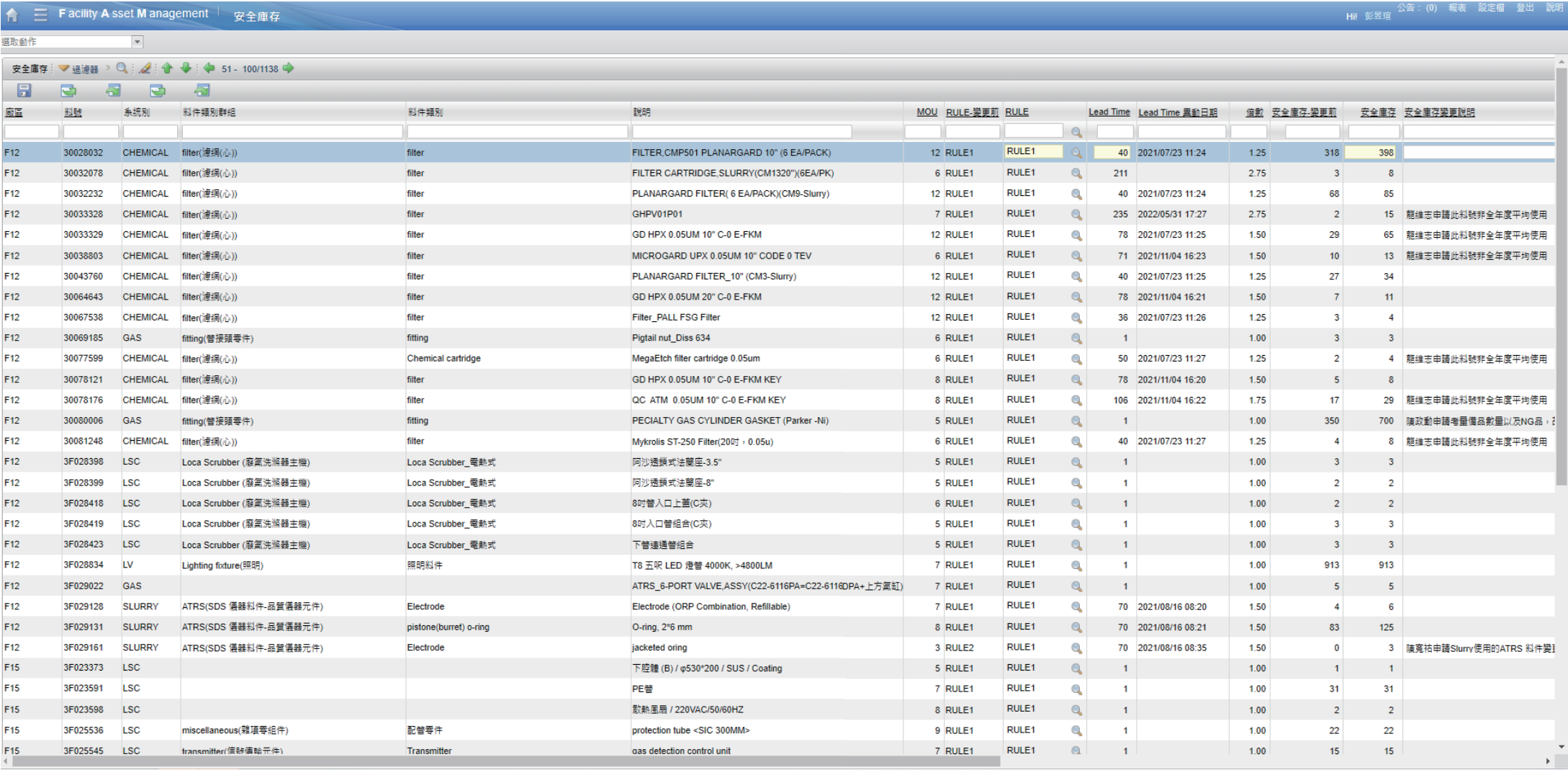
➁ 待訂購
- 主要功能:顯示系統依計算邏輯自動產生與加單申請核准的待訂購項目,提供查詢安全庫存訂單的相關資訊,例如:料號、數量、提貨人工號、成本中心、提貨廠別、領料單(MR)單號等資訊,如圖9所示。
- 效益:對於廠務而言,可藉由此頁面查詢所屬課別有哪些訂購項目,與查詢加單申請的領料單(MR)單號,對於廠務庫房而言,可藉由此頁面彙整待訂購項目進而開立領料單(MR)訂單,並於物料到貨後,可藉由此頁面點選需入庫的訂購項目一鍵轉開02.採購入庫(+)申請單,節省手動建立02.採購入庫(+)申請單的作業時間及避免人為填寫資訊錯誤之問題。
圖9:待訂購頁面
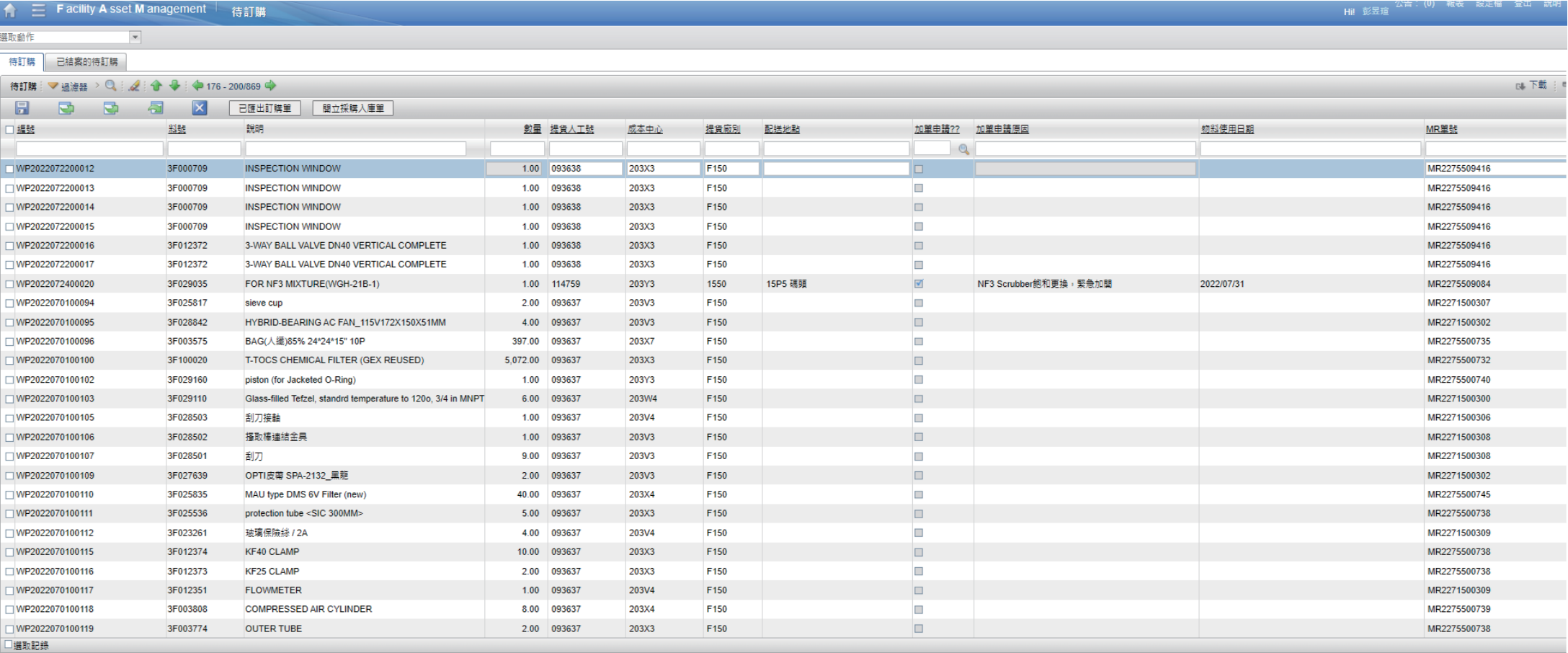
➂ 加單申請
- 主要功能:提供廠務加單申請,可依使用情境不同選用單筆與批次送出申請單,如圖10所示。
- 效益:對於廠務而言,可藉由此頁面查詢加單申請的處理進度,當庫房核准或退件加單申請,系統將會自動寄信給廠務申請者通知審核結果,對於廠務庫房而言,以系統管控廠務的加單申請,取代用信件提出需求的方式,可避免疏忽信件而導致無法及時處理。
圖10:加單申請頁面
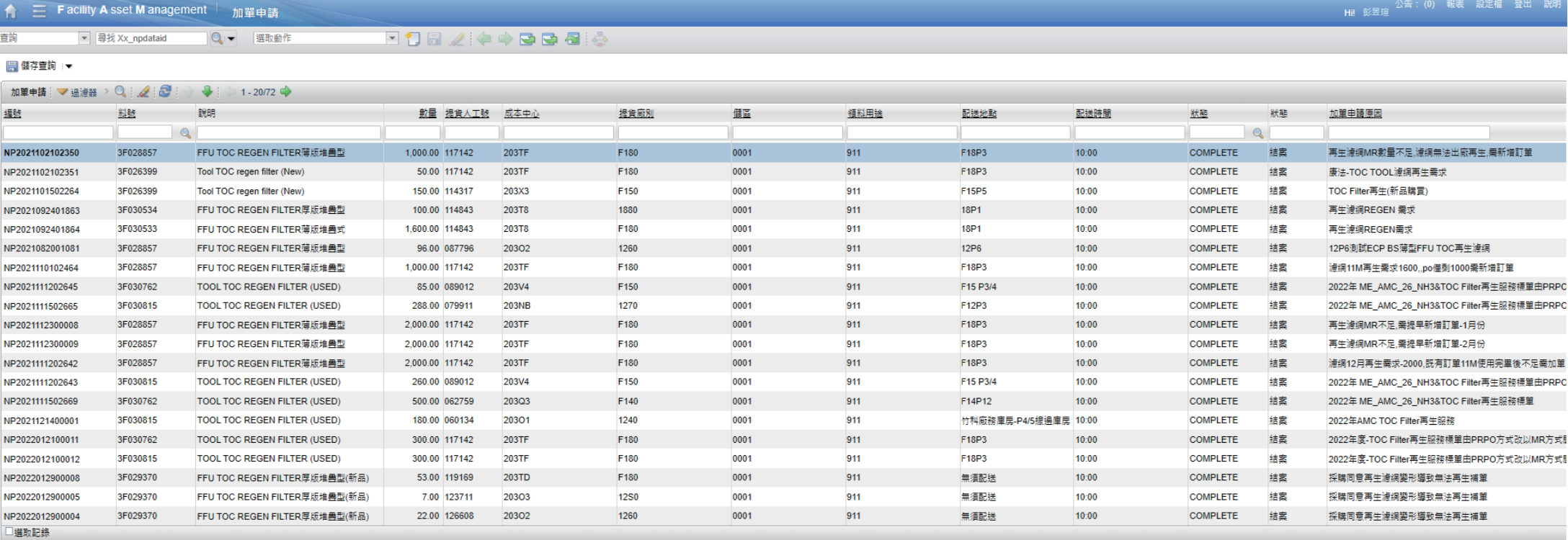
3.2.2 訂購進度追蹤系統
訂購進度追蹤系統建置於整合採購平台(EIS),其主要頁面包含扣帳總表、訂購進度查詢及訂購進度異常清單,頁面進入方式如圖11所示。
➀ 扣帳總表
- 主要功能:每周更新每個成本中心的30、3F料號扣帳費用,並可透過一鍵發送扣帳項目清單信通知各成本中心的負責人,如圖12所示。
- 效益:對於廠務而言,可藉由此頁面主動或被動查詢得知所屬的課別成本中心花費狀況,對於廠務庫房而言,可藉由此頁面取代手動整理各成本中心扣帳資料再使用信件寄送給廠務的作業時間。
圖11:訂購進度追蹤系統

圖12:扣帳總表頁面
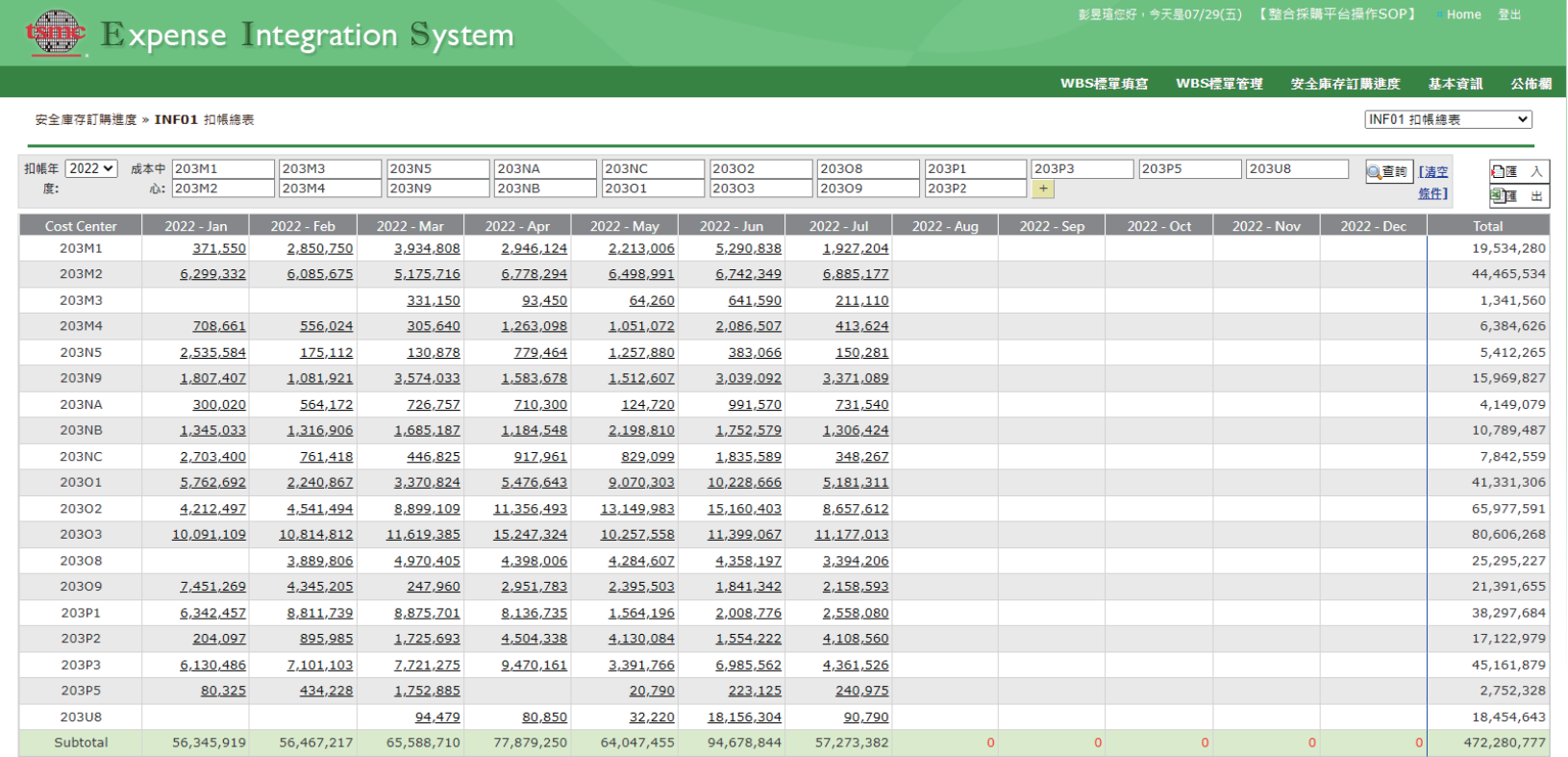
➁ 訂購進度查詢
- 主要功能:檢視廠務資產管理系統(FAM)待訂購頁面裡,每筆訂單與實際入庫的相關資訊,例如:廠區、料號、成本中心、領料單(MR)單號、訂單號碼、需求數量、訂單開立日期、廠商、目前進度、入庫數量與日期等資訊,如圖13所示。
- 效益:對於廠務而言,可藉由此頁面查詢所屬課別訂單的交貨狀況,進而計算預估花費,對於廠務庫房而言,可藉由此頁面得知訂單物料入庫情形,以及針對查詢未交貨訂單,請廠商盡速交貨,以避免庫存不足之問題。
圖13:訂購進度查詢頁面
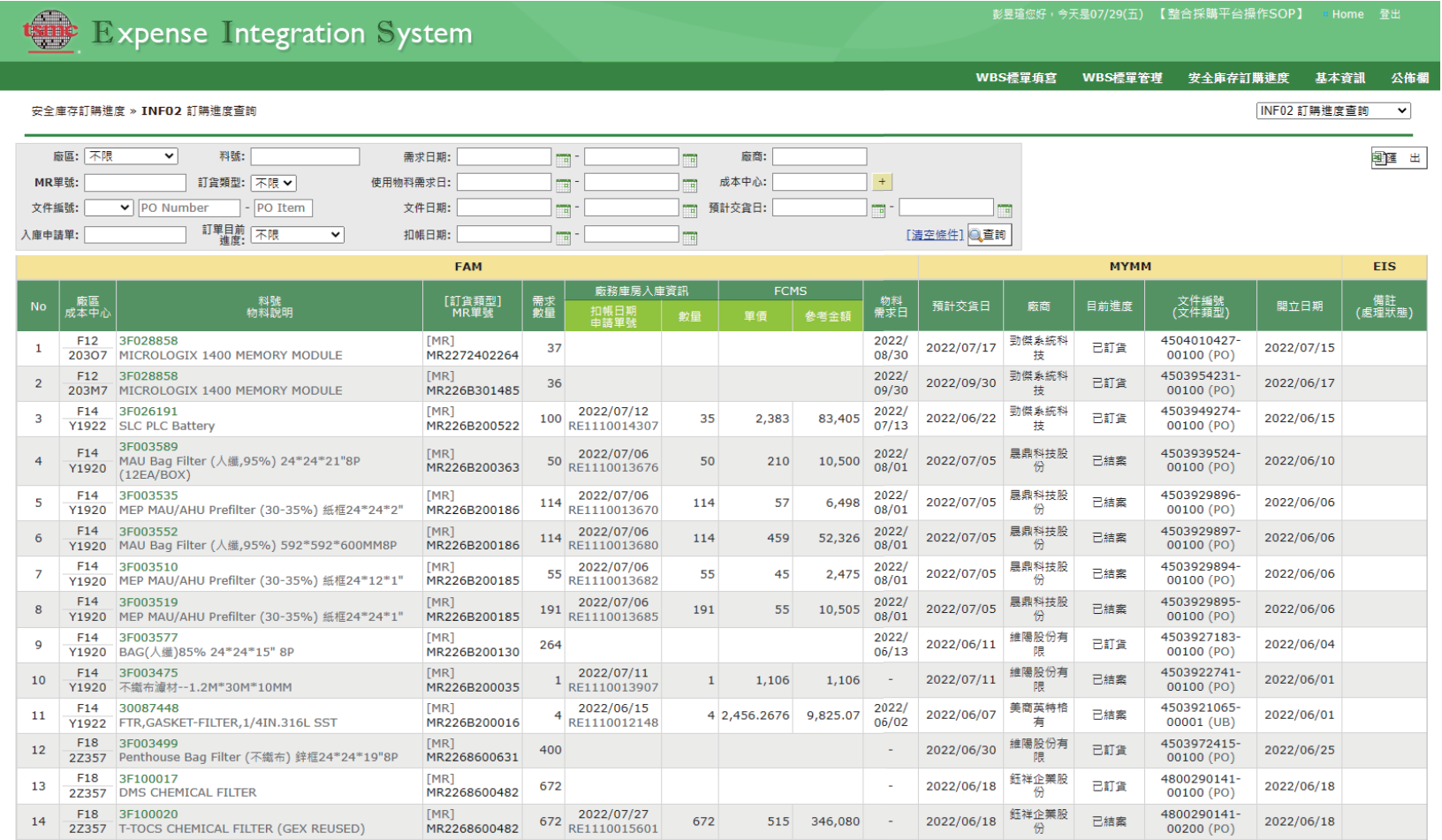
➂ 訂購進度異常清單
- 主要功能:此頁面為廠務庫房追蹤異常訂單,主要分別追蹤處理天數逾期、需求入庫數量不一致兩種異常,處理天數逾期為將每個訂單狀態設定合理處理時間,若訂單狀態停留同個狀態超過合理處理時間,系統將此筆訂單視為異常,並顯示在處理天數逾期頁籤,廠務庫房再依此頁籤的異常項目請公司庫房、採購、物管、廠商協助處理,需求入庫數量不一致為檢視實際入庫數量大於訂單需求數量,即可能代表入庫申請單填寫的領料單(MR)單號有誤,系統將此筆訂單視為異常,並顯示在需求入庫數量不一致頁籤,廠務庫房再依此頁籤的異常項目確認及校正入庫申請單資訊,如圖14所示。
- 效益:對於廠務庫房而言,可藉由此頁面追蹤有異常的訂單,並即時解決訂單問題,使廠商盡早收到訂單備貨與出貨、使物料在公司庫房扣帳不滯留、使訂單物料皆有在廠務資產管理系統(FAM)入帳且入庫申請單資訊正確,得以將訂單物料的狀態一手掌握。
圖14:訂購進度異常清單頁面
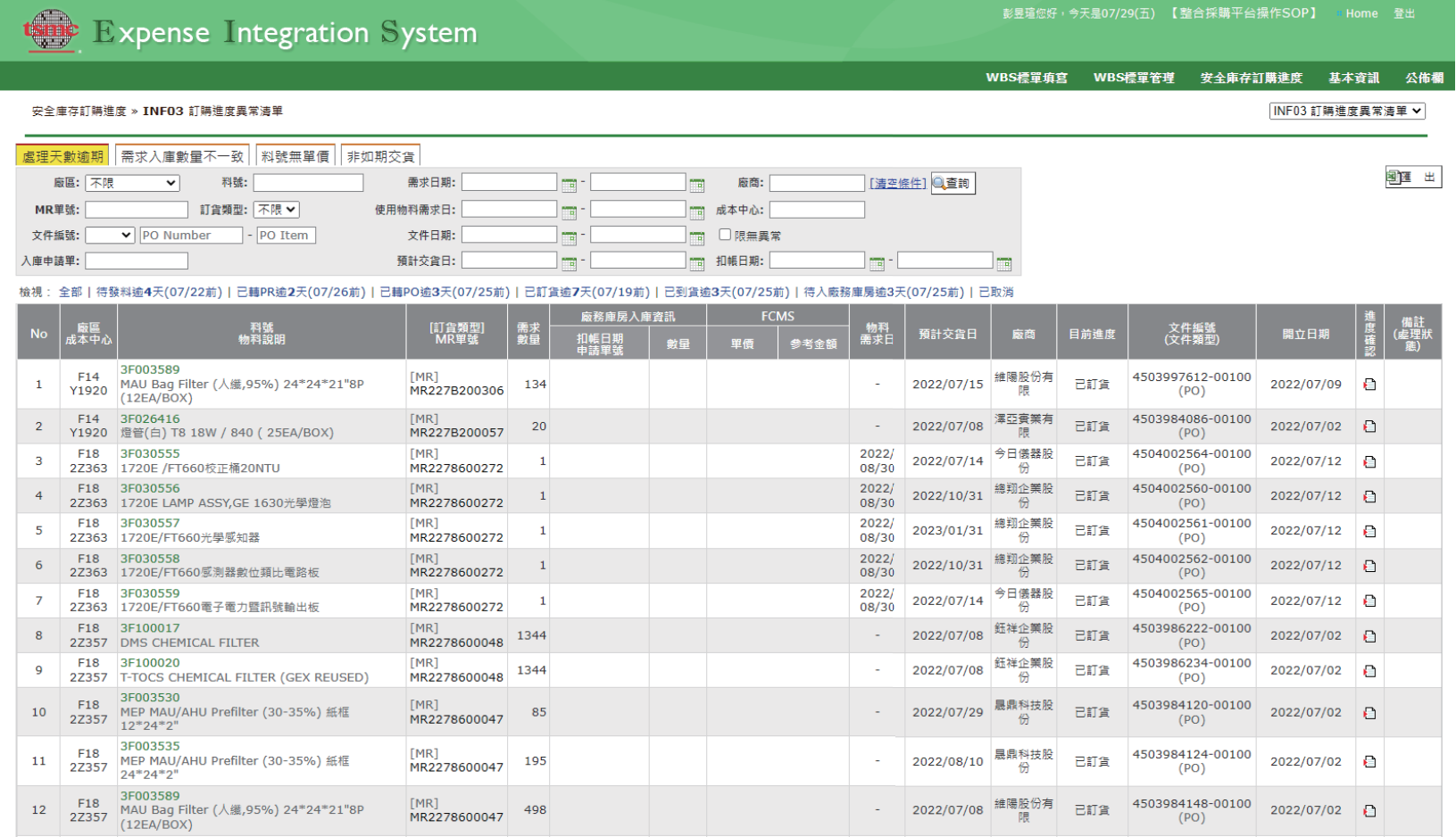
4. 執行成效與未來方向
4.1 執行成效
廠務庫房安全庫存管理自2021年9月起上線,目前近十一個月的執行狀況如下列四點說明:
- 安全水位控管 : 依每月安全庫存水位計算,廠務庫房每月備貨約599,553件物料,由廠務庫房補足水位,滿足廠務單位運轉需求。
- 接手訂單:統一由廠務庫房開立領料單(MR),每月廠務單位約減少開立共776張領料單(MR)共1,891個項目,節省廠務過去自行開立領料單(MR)作業時間。
- 訂單追蹤:廠務庫房每月約追蹤6,481筆物料訂單狀態,並催促供應商備貨與交貨,以避免造成斷料之情形。
- 入庫作業:安全庫存訂單由廠務庫房負責至公司庫房扣帳領料,並將物料帶回廠務庫房入庫,每月約開立4,390張入庫申請單與入庫搬運1,145,840件物料,廠務僅須確實執行工單領料。
4.2 未來方向
因全球供應鏈缺料的問題不斷蔓延,訂單的供應商交貨日顯得格外重要。廠務庫房過去的安全庫存管理,雖然已將Lead Time加入安全庫存的計算因子,但若隨著供應商的交期逐漸拉長,而並未同步將最新交期資訊提供給廠務庫房在系統中做更新,或是訂單數量的多寡影響交期長短,皆仍有可能造成安全庫存值設定過低的問題,甚至導致缺料情形,因此,若能與供應商協商,當收到訂單後,必須針對逐筆訂單在採購系統(Supply Online)回覆交貨日,以利提供廠務庫房提早確認是否有斷料風險,得以提前做緊急應變,例如:調撥物料、第二供應來源、開源節流等處理方式。目前廠務庫房已將採購系統(Supply Online)中的供應商回覆交貨日資訊,串接於整合採購平台(EIS)並將系統欄位建置完成,如圖15所示,後續將著手向供應商宣導需如實如期回報每筆訂單的交貨日。
圖15:供應商訂單交貨日欄位
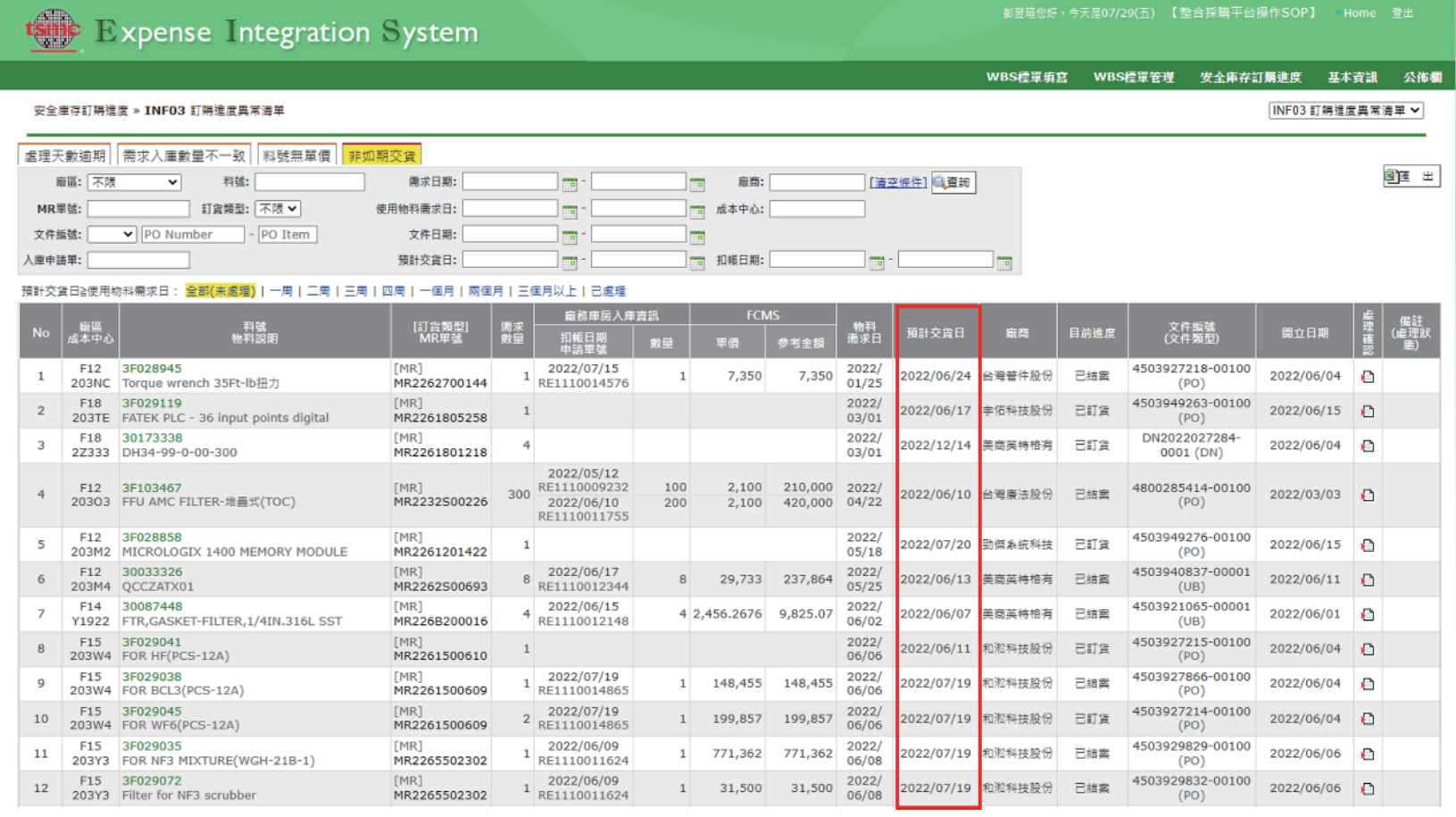
5. 結論
在廠務庫房安全庫存管理未上線前,廠務備貨的困難在於無法全面掌握需求、訂單轉單相關問題無單一窗口詢問、需不斷與供應商協調交貨時間等繁雜作業問題,需有採購、物管、供應商、公司庫房及廠務庫房多方單位協助處理,使得在備貨過程中花費許多作業時間,甚至無法有效掌握,而面臨供應商無法如期交貨的困境,導致廠務需延後保養更換時程。
而因廠務庫房安全庫存管理上線,由廠務庫房負責備貨,包括廠務物料的需求預估、開單訂貨、交期追蹤、點收人庫的一條龍服務,大幅降低廠務備貨的處理時間,可使廠務專注於運轉。除此之外,過去廠務備貨是以Phase為單位自行備貨,廠務庫房安全庫存管理備貨是以Fab為單位統一備貨,因此對於公司而言,可降低庫存存放空間與囤貨成本,且對於廠務而言,可增加庫存跨廠區調撥的彈性,減少斷料之情形,並可達用較低的空間與成本,滿足廠務的用料需求。
參考文獻
- 張育昇,利用庫存管理遊戲進行不同補貨策略之比較,國立交通大學(2010)。
- 賴建庭,根據ABC分類改善庫存管控與預測:T公司為例,國立高雄應用科技大學(2016)。
- 王翊和,供應鏈管理:觀念運作與實務,全華科技圖書有限公司(全華圖書),3版,頁3-2~3-19,2021。
- 洪興暉,供應鏈,不是有料就好:工業4.0時代的採購實戰力,美商麥格羅希爾國際股份有限公司臺灣分公司,2017。
- 歐宗殷,蔡文隆,圖解生產與作業管理,五南文化事業,3版,2022。
- Donald Bowersox, David Closs and M. Bixby Cooper,Supply Chain Logistics Management,McGraw Hill,5th Edition,2020.
留言(0)