摘要

裝機超長米數改善對策-SP1系統化排點
供應機台需求Utility的主系統一次配(SP1)預留點若不適當,造成二次配管工程(Hookup)為了銜接SP1端點,導致超長米數的情形,除了增加裝機成本,在裝機需求大增,人力不足的情況下,對整體裝機進度無疑是雪上加霜。本文由F15裝機調帳案例出發,發現PO不足是由裝機超長米數造成,但遵循SP1系統化排點之架構,藉由資料庫的建立與追蹤SP1點位數量,可模擬出最適合的裝機位置,並提前預警SP1擴充需求,避免機台已進機但擴充工程未完成的窘境。盼未來能藉由此系統的規劃,即時盤點SP1需求、評估現場可供應數量與無塵室閒置位置查詢,快速決定機台裝機位置,藉由主系統擴充警示系統,降低二次配超長米數發生的情況,達到降低成本的目標。
The required utilities for tools are distributed from the facility system to the tools through the hookup piping engineering. If the reserved SP1 ports are not appropriate, it would lead to excessively long hookup piping, which would increase installation costs and waste manpower expenses. By using the systematic SP1 port assignment, engineers can track the quantity of SP1 ports and simulate the most suitable installation locations. It can also provide early warning of SP1 expansion requirements, allowing the expansion project to be completed before the tool move-in. In the future, this system can be used to confirm the SP1 requirements of tools immediately, evaluate the available ports, and quickly determine the tool installation position. We can reduce the occurrence of excessively long hookup piping and achieve the goal of cost reduction.
1. 前言
隨著半導體產業蓬勃發展,為了因應需求,先進製程機台需求種類越來越多且變化大。有時為了增加產出或考量Q Time優化,頻繁更動裝機位置導致供應機台需求(Utility)的主系統一次配(SP1)會有來不及擴充的情況。因主系統沒擴充,機台使用的水氣電需求排點位置大受影響,常常需從更遠的管路端點連接至機台來供應Utility,除工程費用隨之增加,造成二次配管裝機工程(Hookup)請款PO不足外,需要投入更多的人力、工時及材料,才能完成機台裝機工作,讓機台順利投入生產。
近年來新建廠與裝機數量持續成長,在緊湊的裝機時程下,目前已面臨缺工缺料的難題,期盼能透過SP1系統化排點,降低裝機超長米數發生的情形,藉此有效應用市場有限的人力資源,並兼顧預算管控(Cost Saving),創造公司最大利益。
2. 文獻探討
2.1 Hookup成本估算與管理
裝機工程(Hookup)除了縮短裝機時程之外,成本與品質也是成功的關鍵因素。以往Hookup發包大多是廠商依據工程經驗與歷史資料報價,報價內容因廠商不同產生極大差異,難以估算裝機成本與預算控管。温兆寶[1]使用類神經模糊系統之學習機制與演算法,建立半導體裝機配管工程成本預估模式,提高成本估價準確性。根據國際專案管理學會(Project Management Institute, PMI)發行的「專案管理知識體系指南,PMBOK」[2],專案管理知識體系是以過程為基礎,將一系列過程分為五大基本流程及十大知識領域,對專案管理相關概念進行闡釋與定義,協助專案管理師能在此指南下進行專案管理。歐陽宏俊[3]藉由PMBOK,將五大基本流程及十大知識領域導入裝機管理流程,提高裝機進度、工安與施作品質。
吳家榮[4]藉由導入專案管理的流程,建立Hookup管理準則,使執行與管理趨於完善,獲得高品質、高效率、低成本的裝機成效。
劉庚芳[5]用族群辨識演算法應用於興建、二次配、裝機階段之探討—晶圓廠之建廠生命週期,包含投資評估、設計/發包、興建、二次配/裝機及運轉/維護等五個階段,以族群辨識演算法,分析各階段之廠務及製程系統,藉以提供建廠專案中廠務及製程各系統之關聯性,並提出晶圓廠建廠專案中廠務及製程各系統之同步流程。本研究將建廠專案中各系統之關聯性,應用在建廠專案組織、進度管控、發包計劃,以協助業主、專案經理、工程顧問公司及承包商於建廠專案執行中了解其運作流程。
林志章[6]提出晶圓廠裝機工程進度改善之研究,利用找出影響施工,造成裝機效率下降的原因,提出改善對策實施之後,總體效率提升23.5%。
2.2 Hookup發包與驗收標準流程[7]
使用專業的管理模式能幫助掌控工期,亦能降低廠房建置成本,利用物料清單(Bill of Material, BOM) [8]、確認工作分解結構(Work Breakdown Structure,WBS),建立結構化標單,將Hookup各工種所需的原物料數量,換算成點數,廠商以標準點數進行年度報價,改善以往Hookup發包時主要根據廠商經驗報價,難以判斷價格合理性,有助於加速Hookup發包速度與降低成本。(圖1)
圖1:Hookup發包流程
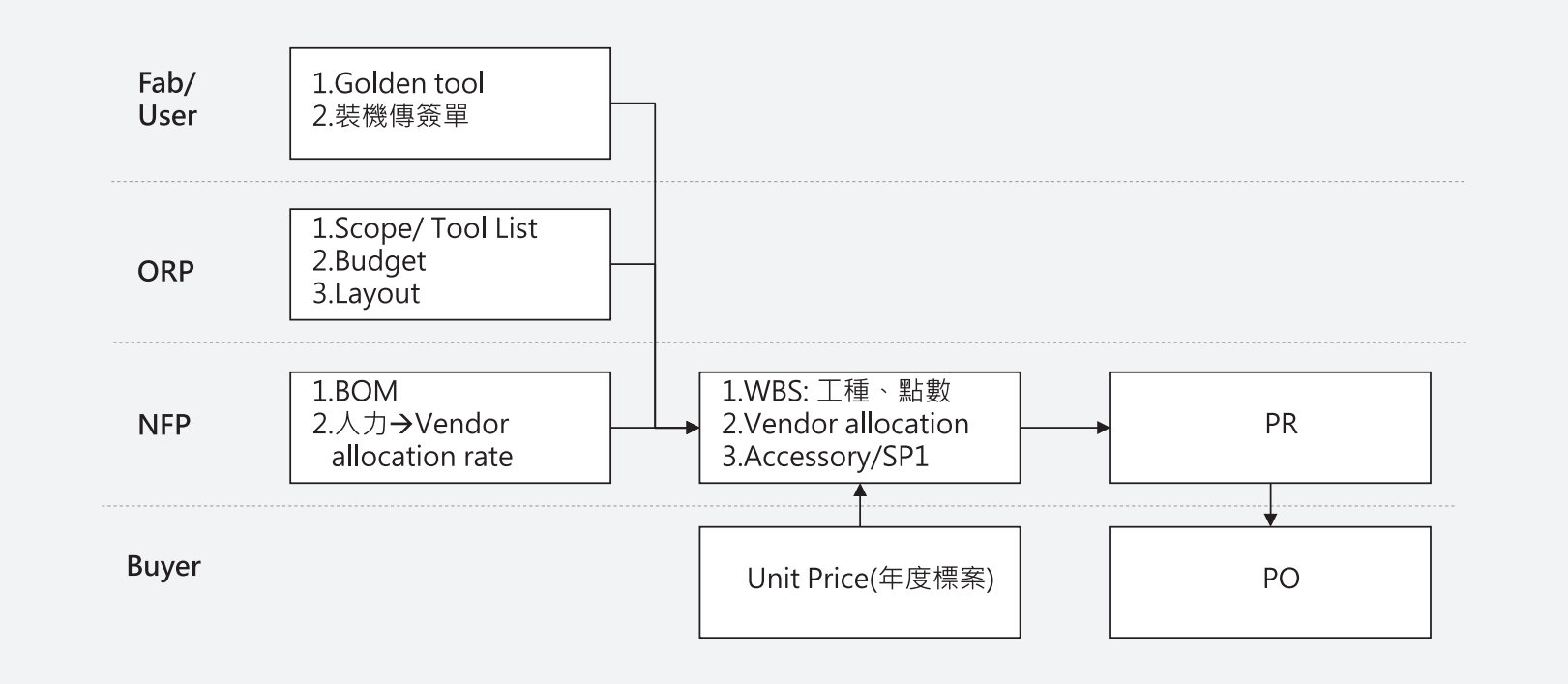
ORP提供各廠tool list及年度拆移機計畫,NFP依據BOM計算出Hookup各工種的需求點數,連結結構化WBS,作為廠商投標之依據。依照各廠區的拆裝機計畫,考量廠商工程承接人力與投標價格進行Vendor Allocation。ORP提供每次Committee整體K數的tool list,NFP統一開立PR/PO,降低PR/PO數量。
經由裝機PO資訊系統(Hookup PO Information System, HPIS)整合機台拆/裝機報價、連結Hookup PO號碼,使裝機人員能快速查詢PO與施作廠商,確實執行No PO, no service。機台完工後需進行驗收請款,請款功能透過連結Hookup Hierarchy System(HHS)的工程實際施作點數,進行點數驗收與審核,並利用此資料定期回饋至BOM及WBS資料庫,以提高資料庫準確性。
2.3 SP1配置點不當導致Hookup超長米數
台灣半導體廠建設多採取快捷施工的方式,設計與施工同時進行,主建築施工到一半,廠務系統就進場施工,容易導致空間尺度的不足或配置不當,後續也容易需要辦理變更設計,增加修正成本。吳心玫[9]以機台對於廠務系統的需求為出發點,進行灰關聯分析,探討影響不同製程空間尺度的因子,使空間更有效利用,並降低建廠成本。
供應Utility的主系統一次配(SP1)與二次配管工程(Hookup)常由不同承商施作,考量預算與需求不確定性,SP1的規劃大多隨著產能規劃,進行漸進式的擴充。若SP1預留點恰當,Hookup工程則容易進行,反之, SP1排點不當,Hookup常面臨空間上配管的衝突,配管需拉很長去銜接SP1端點,導致超長米數情形產生。
2.4 案例-裝機請款發現超長米數
由HHS請款點數與BOM的發包點數比對發現,Hookup Power與Gas常有PO不足的情形發生,需進行PO補開作業。
以Power為例,統計Y2019~2021年F18/F15/F12裝機,總共7,395台,其中2,336台有超長問題,占總機台數約31.6%,總超長米數費用NT$336M,代表需多花21.5% Power人力才能完成裝機,可見超長米數對成本及人力的影響非常巨大。
經分析比對後,發現FAB內最常發生超長米數機台區域為ETCH / LIT (with EUV) / DIF / TF / BS,平均每台Power配線超長228M(表1),需指派更多人力來進行超長米數安裝,在大量裝機時期,可能會造成機台延誤交機。且請款PO不足,需花費更多人力與工時,進行PO調帳或是補開PR/PO,不只拉高裝機成本,還會延長請款作業時間。
2019-2021 Hookup Power 超長統計 (Top 5 Area) | ||||||||
---|---|---|---|---|---|---|---|---|
Area | 裝機數 | 超長機台數 | 裝機超長比例 | 超長米數 | 平均米數 | 總超長費用 | 平均超長費用 | 費用增加 |
Etching | 1,298 | 455 | 35.1% | 104,515 | 229.7 | 73,546,805 | 161,641 | 18.0% |
LIT (with EUV) | 1,038 | 412 | 39.7% | 109,232 | 265.1 | 79,864,241 | 193,845 | 31.2% |
DIF | 1,051 | 330 | 31.4% | 99,199 | 300.6 | 57,183,349 | 173,283 | 26.6% |
TF | 1,121 | 341 | 30.4% | 59,626 | 174.9 | 38,277,828 | 112,252 | 16.7% |
BS | 623 | 233 | 37.4% | 57,000 | 244.6 | 37,327,324 | 160,203 | 17.6% |
Total | 7,395 | 2,336 | 31.6% | 532,641 | 228.0 | 336,094,689 | 143,876 | 21.5% |
以F15的3台EUV Hookup Power工種為例,超長所造成的費用為NT$2.2M。會發生超長米數的主因為EUV機台附近配電盤已被其他機台使用,因此EUV裝機要拉線到距離機台更遠的電盤,造成實際施工米數跟BOM有顯著的差異,導致PO金額不足。在現場以柱位間距、SWB直立tray與考量凹折轉彎處,進行實際距離量測,量測出來的長度與廠商提送的超長米數相符。其中拉線距離最長的一台,SWB至AC Box經過16根柱位(約80M),總計14個迴路、55條線,平均每條線超長83.3M,超長長度總計4,579M(圖2)。
圖2:F15 EUV 電盤路徑圖

3. 研究方法 (改善構想)
3.1 SP1擴充流程
當有新裝機時,考慮各種機台有不同的Utility需求,廠務系統人員需依照裝機的機型與位置,確認該區域的SP1供應量是否足夠,若供應不足則需進行SP1擴充。
成廠區SP1擴充流程如圖3:Capital Committee過後ORP & IE提供機台清單及Bay ID,裝機廠區CST(或USER)提供對應Tool Utility Request(裝機傳簽單)或Golden tool。NFP於FR系統 (Facility Request)啟動報價流程,將ORP與CST提供的資料彙整,廠務系統人員依照各機台Utility需求與位置進行SP1評估。經現場會勘&確認後,若SP1需要擴充,廠務需提供PR Material說明計算結果 & 需擴充的範圍,NFP進行報價內容澄清確認與比價、開立PR後,此FR報價案即結案。採購與廠商議價下訂單後,廠務系統負責人員即可與得標廠商安排擴充工程,並於機台裝機前完成施工,避免影響裝機時程。
圖3:SP1報價與擴充流程
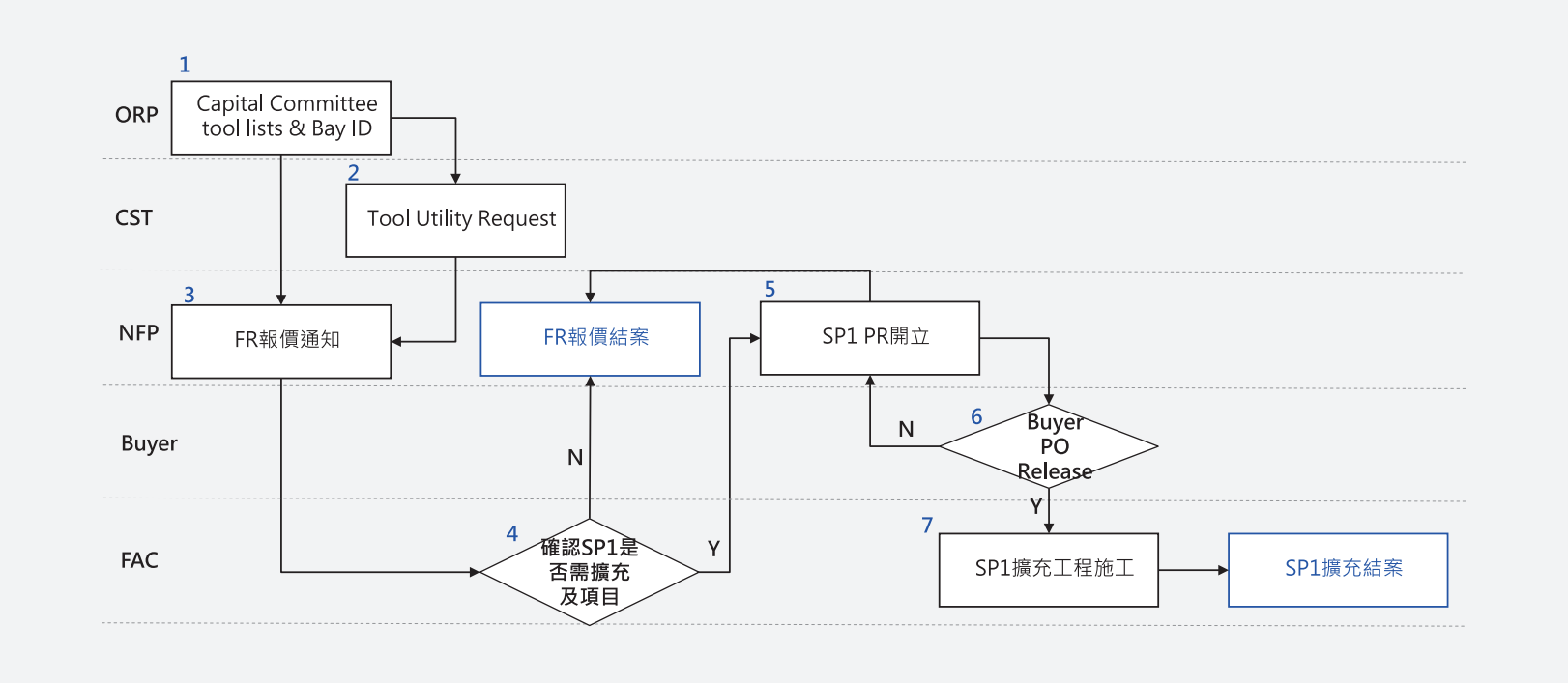
3.2 SP1系統化排點介紹
為了降低裝機成本與人力,希望發展SP1系統化排點,藉由此系統提前預警超長米數即將發生,讓廠務系統人員可以透過SP1擴充或其它應變措施來降低超長米數的情形發生。
首先要建立系統化排點的資料庫,此資料庫包含:
- Golden tool POU數量及SP1使用需求。
- 現場SP1 可用點位數量、種類及所處位置(柱位編號)。
- 正在進行擴充中的SP1盤面數量及預計完工日期、位置(柱位編號)。
系統化排點流程(圖4):機台準備裝機前,EE會先進行裝機前傳簽,傳簽完畢後交由CAD開始繪製施工草圖,並提供給EE進行需求確認,確認無誤後即回圖給CAD Team,此時由「系統化排點系統」確認資料庫內是否有同型機,如有同型機則開始以最短距離進行排點。將此初版排點資訊,提供給廠務系統工程師進行確認,確認無誤後,CAD Team進行施工圖出圖,EE開始進行現場會勘施工,排點系統同步回饋此次最終排點結果至資料庫,等待下一台施工需求。
圖4:系統化排點流程
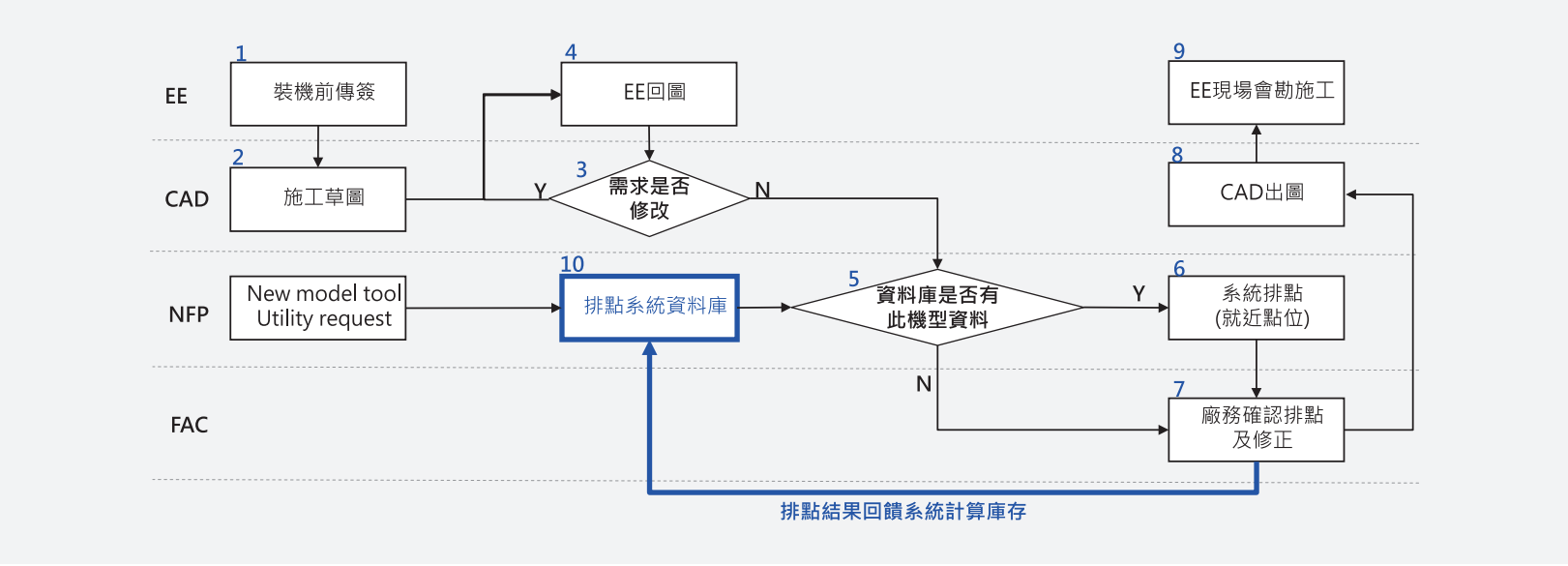
3.3 SP1擴充預警系統介紹(圖5)
目前廠區進行SP1擴充盤點報價時,常常遇到機台需求變更、裝機廠區或位置更換(Tool Layout change)或機台提前進機(Pull-in),導致原本評估完成的擴充需求需要再次進行盤點,因此SP1報價結案時間時常延期,綜合以上因素,有可能使機台延遲交機,進而影響到產能規劃。希望藉由此系統追蹤未來三個月進機(點位使用)及拆機(點位釋放),配合拆裝機時間,預估各區域SP1點位使用/釋放數量,針對點位不足的區域,提前預警廠務SP1擴充需求及安排擴充順序,避免機台來了現場還沒擴充,亦或半年後才要進機的區域卻先行擴充(急的還沒擴,不急的卻先擴),尤其是RD廠區,其需求種類、數量相對於量產廠區複雜許多,期盼此預警系統能讓資源更有效運用。
圖5:SP1擴充預警系統
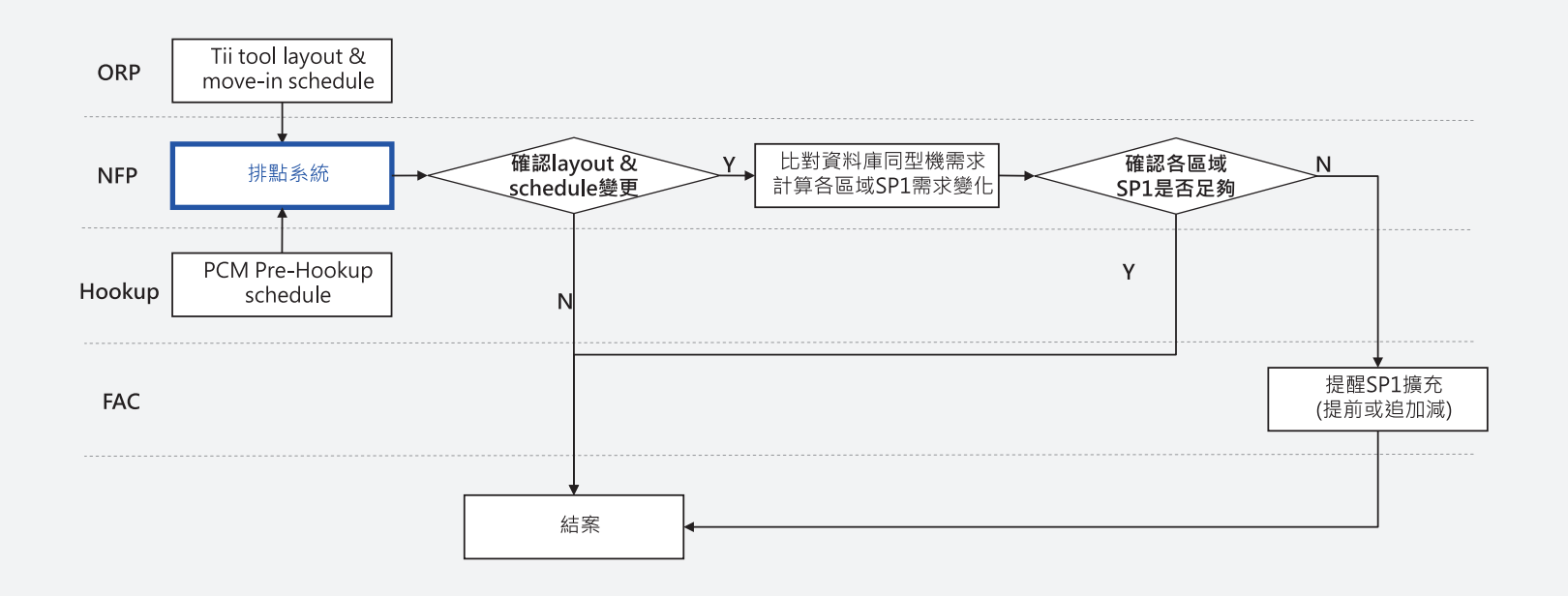
4. 預期結果與分析
4.1 預估超長米數成本
現場SP1擴充可能因為工、料交期而延後完工,但是產能規劃進機時間無法延後,因此Hookup可能需要跨區供應,使得管線距離增加,進而提高裝機成本,透過此系統預估超長米數所增加的費用,作為日後追加PR/PO依據。
4.2 裝機位置最佳化
IE進行機台Layout時,無法清楚掌握現場SP1庫存量,時常到了會勘時才發現此機台Layout雖然裝得下,但是現場SP1供應量不足,現場擴充所需時間可能又無法配合進機時間,或者是擴充費用太高等問題,只能再更改Layout,重複動員大量人力進行確認,藉由此系統模擬出最適合的裝機位置,以減少人員確認時間。
5. 結論
期望透過此系統建立,機台裝機位置或進機時間變動時,可以即時盤點現場SP1可供應數量與SP1庫存水位預警,即時回饋給系統Sponsor進行系統擴充或工程調配,降低超長米數情形發生,讓機台順利完成裝機、量產的同時,又能兼顧預算控制,達成雙贏目標。
參考文獻
- 温兆寶,半導體裝機配管工程成本估價模式之探討,國立交通大學(2010)。
- Project Management Institute, A Guide to the Project Management Body of Knowledge.(1996)
- 歐陽宏俊,應用工安專案管理於裝機工程-以晶圓製造廠為例,國立雲林科技大學(2014)。
- 吳家榮,半導體製程設備裝機工程管理之研究-以t公司12吋晶圓廠為例,國立成功大學(2008)。
- 劉庚芳,族群辨識演算法應用於興建、二次配、裝機階段之探討(2006)。
- 林志章,晶圓廠裝機工程進度改善之研究-以X公司為例(2020)。
- 陳椀煜、陳志雄、林宥芯,裝機整合管理系統的建置,廠務季刊第24期(2015)。
- 陳椀煜,BOM在新建廠成本估算的應用,新工季刊第9期(2013)。
- 吳心玫,半導體廠房空間之研究-以廠務設施為例,中華大學(2008)。
留言(0)