摘要
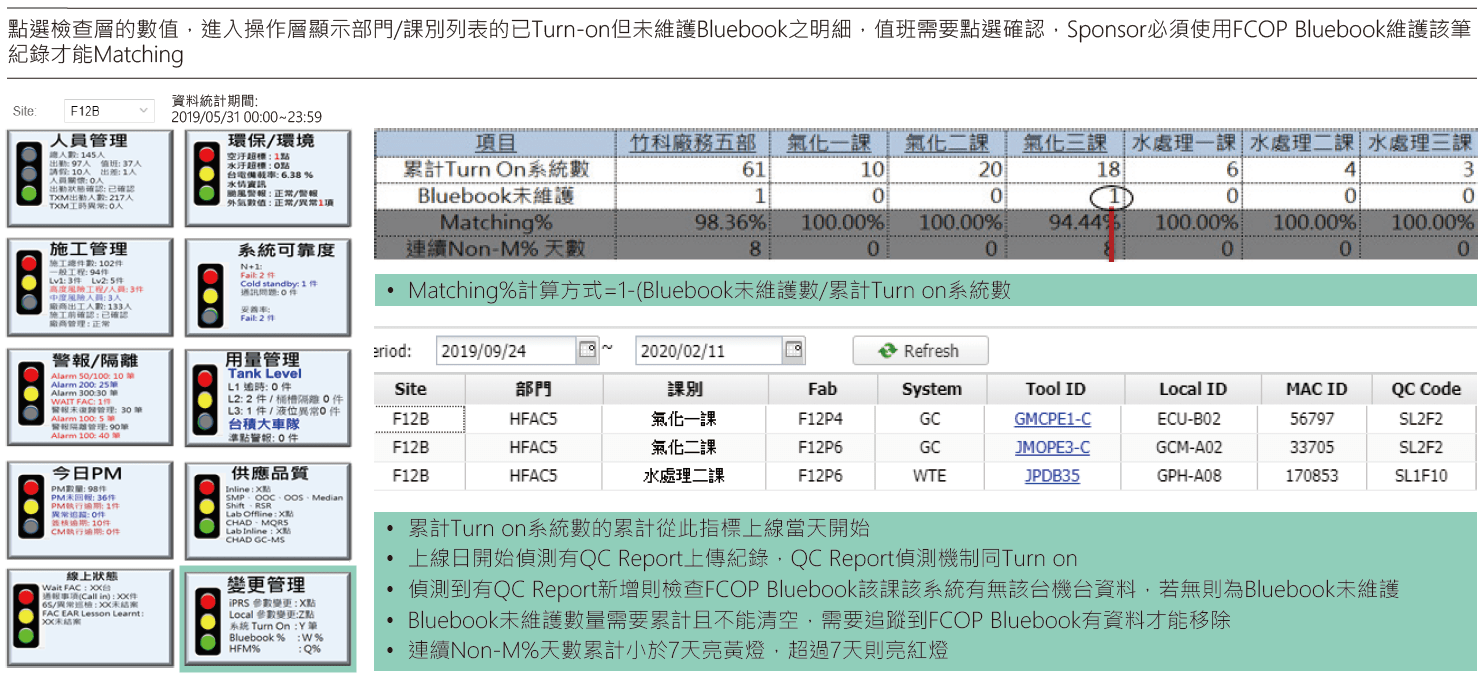
落實廠務全面品質管理的關鍵議題–廠務變更管理
前言
1.1.變更管理的重要性
變更管理目的即使是細微的變更亦可能影響系統的完整性及相容性-98年TOSHMS(Taiwan Occupational Safety and Health. Management System)王世煌,即使微小變更也許會造成巨大影響,也許大到影響一個工廠營運;1994年英國南威爾斯省TEXACO煉油廠爆炸事件因其三年前系統修改,修改範圍包含knock-out pot及控制系統,7月24日主蒸餾塔操作異常,「Overfill」導致安全閥跳脫, 大量的氣相與液相HC排放至燃燒塔,其當時財物損失四仟八佰萬英磅及26人受傷[3]。
工廠穩定生產與製程技術完美的轉移至量產是公司的首要目標,能夠產出大量良率高的產品及減少異常事件發生才能讓公司獲利。但如前所述變更管理是會影響公司營運重要指標。本文以廠務變更系統的資訊建立一跨廠區的廠務資訊整合平台至廠務看板平台「開門十件事」,在有限資訊內盡可能地將各變更資訊整合進行一致化。於本文中著墨在與廠務相關變更系統整合,未來可將此研究如何以平台簡化參數管理更有資訊整合便於適合在運轉上管理。
1.2.整合目的性
先進製程常以完整複製模式(Copy Exactly)將研發廠內的所有資訊複製到新廠區,廠區間相同製程的產線也會將良率較好的生產經驗提供給他廠效法。但此複製模式僅僅是將製程配方與機台參數原封不動的複製,此平台整合是將各廠相類似參數放置整合於相同平台,便於比較各參數是否一致,且能有公開平台相互分享各廠參數設定,藉此互享可以找到相對於穩定系統之參數,也能讓新廠區參數定義參考方向。
1.3.整合參數種類
大數據是指大量、多變且快速產生的數據,需要新的科技來處理,以便於決策、知識探索以及製程的最佳化,參數資訊可視為巨量資料,以大數據具體來說,大數據具有4個基本特征:
「數據體量巨大」「數據類型多樣」「處理速度快」 「價值密度低」,這四種特性對於廠務參數數據可以說是另一種大數據面向,但是此數據對於廠務而言是尚未將其大數據整理及利用成有用資料。
- 數據體量巨大 : 依照HFAC P4~P7→表1,廠區所納管之參數將近700萬筆參數,約一個廠區將近200萬,初估整個廠務管理參數至少4千萬以上,相當巨量數據資料。
表1、參數數量 For HFAC P4~P7
HFAC iPRS 納管參數數量 SI/Local 納管參數數量 DCS 納管參數數量 Tool Trun on 原物料參數 P45 230,886 筆 2,678,652 筆 5,937 筆 8,451 筆 1,231 筆 P6 56,210 筆 2,485,110 筆 3,711 筆 6,235 筆 985 筆 P7 2,626,333 筆 3,542,895 筆 4,637 筆 9,245 筆 3,120 筆 - 數據類型多樣 : 依照各廠區已有管理參數種類,將其資料分成監視層參數、控制層參數、Tool Turn on、原物料參數四種,涵蓋參數多元化。
- 處理速度快 : 以每日存取下來參數,每秒將近產生2.3筆參數大於大數據的「一秒定律」。
- 價值密度低 : 以單筆參數利用價值並不高。
1.4.整合參數難題
由上得知參數為大數據一種數量多且複雜、種類多,分散於各廠系統及資料庫內,且大多無統一系統管理,可以利用此次將其各參數依照種類作為分類管理。一般數據處理方式有四種 :
大數據處理之一:採集
大數據的採集是指利用多個資料庫來接收發自客戶端(Web、App或者感測器形式等)的數據,並且用戶可以通過這些資料庫來進行簡單的查詢和處理工作。比如,電商會使用傳統的關係型資料庫MySQL和Oracle等來存儲每一筆事務數據,除此之外,Redis和MongoDB這樣的NoSQL資料庫也常用於數據的採集。
大數據處理之二:導入/預處理
雖然採集端本身會有很多資料庫,但是如果要對這些海量數據進行有效的分析,還是應該將這些來自前端的數據導入到一個集中的大型分散式資料庫,或者分散式存儲集群,並且可以在導入基礎上做一些簡單的清洗和預處理工作,導入與預處理過程的特點和挑戰主要是導入的數據量大,每秒鐘的導入量經常會達到百兆,甚至千兆級別。
大數據處理之三:統計/分析
統計與分析主要利用分散式資料庫,或者分散式計算集群來對存儲於其內的海量數據進行普通的分析和分類彙總等,以滿足大多數常見的分析需求。
大數據處理之四:挖掘
與前面統計和分析過程不同的是,數據挖掘一般沒有什麼預先設定好的主題,主要是在現有數據上面進行基於各種演算法的計算。
此次參數整合是依照數據整合方式由各廠採集參數資料於SQL Server;並由開門時十件事定義各參數INDEX,由各廠導入/預處理結果導入給開門十件事顯示;透過不同種類參數統計/分析,將其參數分類不同系統加以分析。以下分為四大Parameter Rule,將其參數分批歸類加以分析→表2,依照整合平台/跨廠狀態/管理模式皆不一致,且針對其系統衍生問題,管理模式不一致無統一平台,希望以開門十件事制定一統一平台,並Align統一管理Rule整合其參數管理。
Parameter Rule | iPRS 納管參數數量 | SI/Local納管參數數量 | Tool Trun on | 原物料參數 |
---|---|---|---|---|
System | iPRS System | Local/SI/DCS參數 |
Hookup System Bluebook System |
HFM System |
參數數量 | 2600K(F12B) | 5000K(F12B) | 25K(F12B) | 6K(F12B) |
整合平台 | 獨立IPRS System | 無統一平台 |
e-Hookup System e-Bluebook System |
HFM |
跨廠狀態 | 只有F18/F12P7 | 各廠無統一平台 | 各廠一致 | 各廠一致 |
管理模式 |
各廠區依照本身廠區 Golden管理 |
只是記錄變更Log 每日Re-view |
Tool資訊只有紀錄 並不會Re-view |
Mail通知原物料跟 Bluebook不一致 |
目前問題 |
非各廠都有系統 無法做到跨廠區管理 |
無統一平台,統一管理機制 | 無管理機制 | 管理模式是否進化 |
文獻探討
近年來以雲端運算、大數據所驅動的「智慧製造」,正對人類生活與產業發展掀起新一波變革,值此關鍵時刻 ,企業如能早一步利用前瞻科技,建立新營運模式,就能在迎面而來的數位浪潮上,佔據贏家的位置,尤其記憶體元件是數位化生活的關鍵要素,意味著記憶體廠商自然不能排除於這波數位變革之外。
參考成功大學製造資訊與系統研究所-發表「智慧型良率管理系統」獲得「107年經濟部智慧財產局國家發明創新獎」,並針對參數定訂規格,達到持續改善良率的目標[4] 。建構之智慧型良率管理系統透過物聯網元件(CPA)的應用抓取所需資料;透過巨量資料分析管理。其文中提到製程技術的不斷提昇與功能日趨強大,其製程也日趨精密且複雜。處於此環境下,如何能在發現產品良率不佳時,快速地找到造成此良率不佳之關鍵因子,進而能持續改善以提升良率,已成為一個重要的課題。提供其搜尋演算法包含模組有 :
- 資料前處理模組(Data-Preprocessing Module):進行資料前處理及品質的確認。
- KSA核心分析模組(KSA Core Algorithm Module):含TPOGA(Triple Phase Orthogonal Greedy Algorithm)與ALASSO(Automated Least Absolute Shrinkage and Selection Operator)演算法,分析關鍵站點供使用者參考 。
- 交互作用模組(IESA Module):利用TPOGA及Tree找出交互作用機台及參數。並針對參數定訂規格,達到持續改善良率的目標。
- 盲站搜尋模組(BSA Module):輔助KSA核心分析模組,辨識出哪些影響參數可能因為製程特性而無法分析,並提出兩階段的流程針對該些影響參數進行深入檢視。
- 信心指標模組(RIK Module):透過比較KSA核心分析模組分析結果的重合程度,產出信心指標。
基於先進製造物聯雲所建構之智慧型良率管理系統透過物聯網元件(CPA)的應用抓取所需資料;透過巨量資料分析管理大量生產線上的資料;應用虛實整合技術順利部署關鍵站點搜尋演算法,如此便可將智慧型良率管理系統實際應用於業界,達到提升良率和減少搜尋時間之目標。
以此模組架構參考資料前處理模組及交互作用模組,將廠務品質管理-廠務變更管理可突破以往單區域管理模式 ,以整廠為出發點,無論是在監視層、控制層、原物料或廠務Utility,以廠務參數指標INDEX為起點,讓同仁於各不同參數層加以管理,找出變更後問題的癥結點,下達正確的管理指示。
整合各廠區參數管理在強化原有各廠自動化資訊的規畫上,廠務Utility部分會將每日廠務Utility Turn on Tool資訊、原物料串接機台資訊、廠務監視參數資訊(SCADA)、廠務控制層資訊(PLC)等統合到整合式管理介面中,因為在現有各參數都分散式於不同系統之上,且廠區資訊是獨立運作無法互相連結。透過廠務品質系統整合之,將各個廠區原先各自獨立的系統與各廠資訊整合到系統中,整合各廠區的資訊外,更可協助管理階層全面掌握現場情報,採取最佳決策[2]。此架構的管理目的主要從廠務管理KPI四大面向進行規劃,包含Tool Turn資訊、控制層參數資訊、監視層參數資訊、原物料資訊,讓管理者透過整合式管理資訊介面,完整掌握廠務參數變更參數資訊。
計畫方法
於前言所說,資料前處理模組及交互作用模組比較方式來做到參數整合方式,打造IT視覺化系統&各廠資訊分享善用深度學習達到穩定運轉模式,上述參數變更管理分為廠務參數規則,分為4大面向→圖1,包含控制層參數/監視層參數/Tool Turn On/原物料參數,全面性將廠務參數合併其內。
圖1、參數變更廠務四大參數INDEX
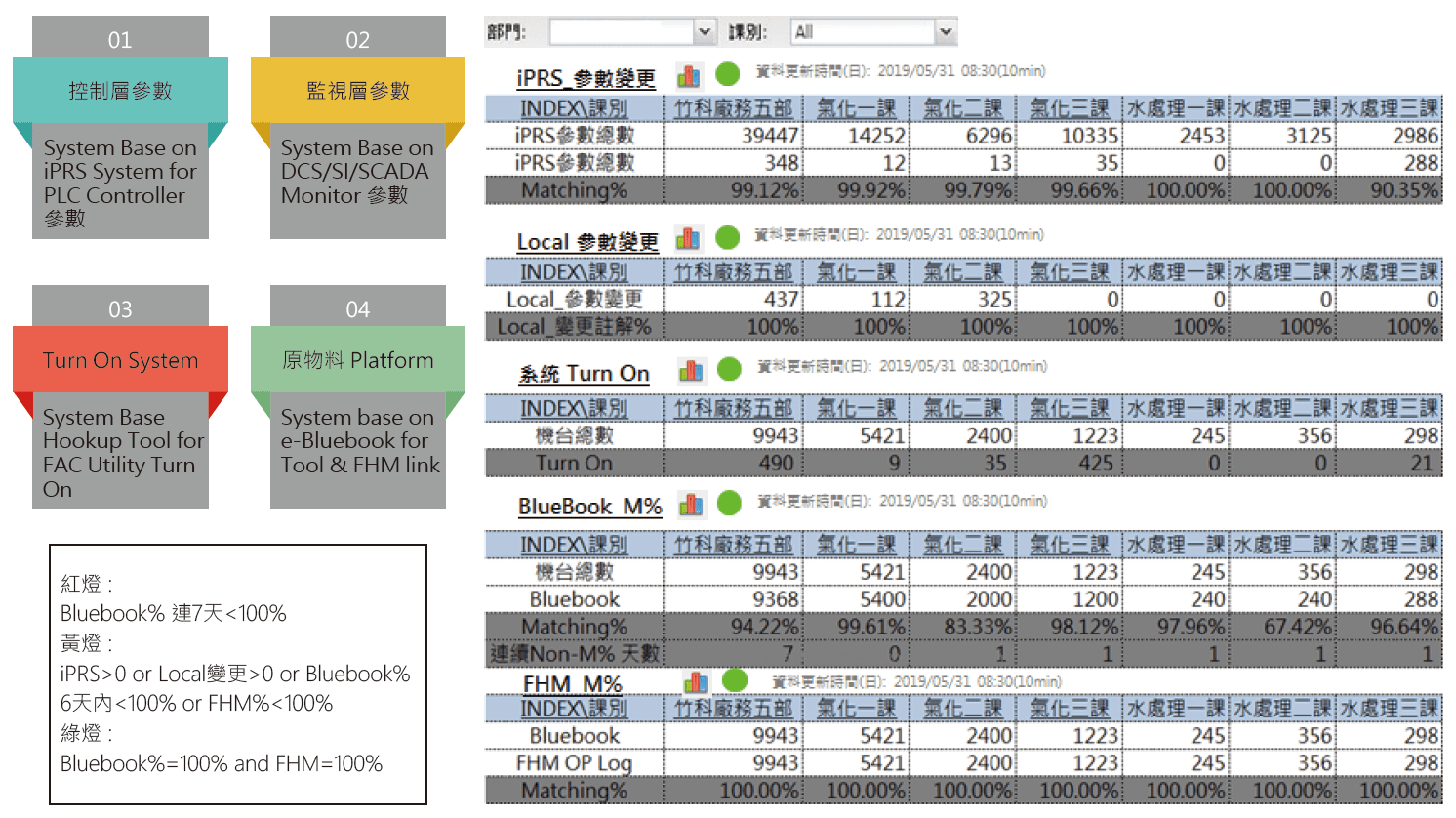
3.1.控制層參數 (iPRS)→圖2
圖2、iPRS Data Flow
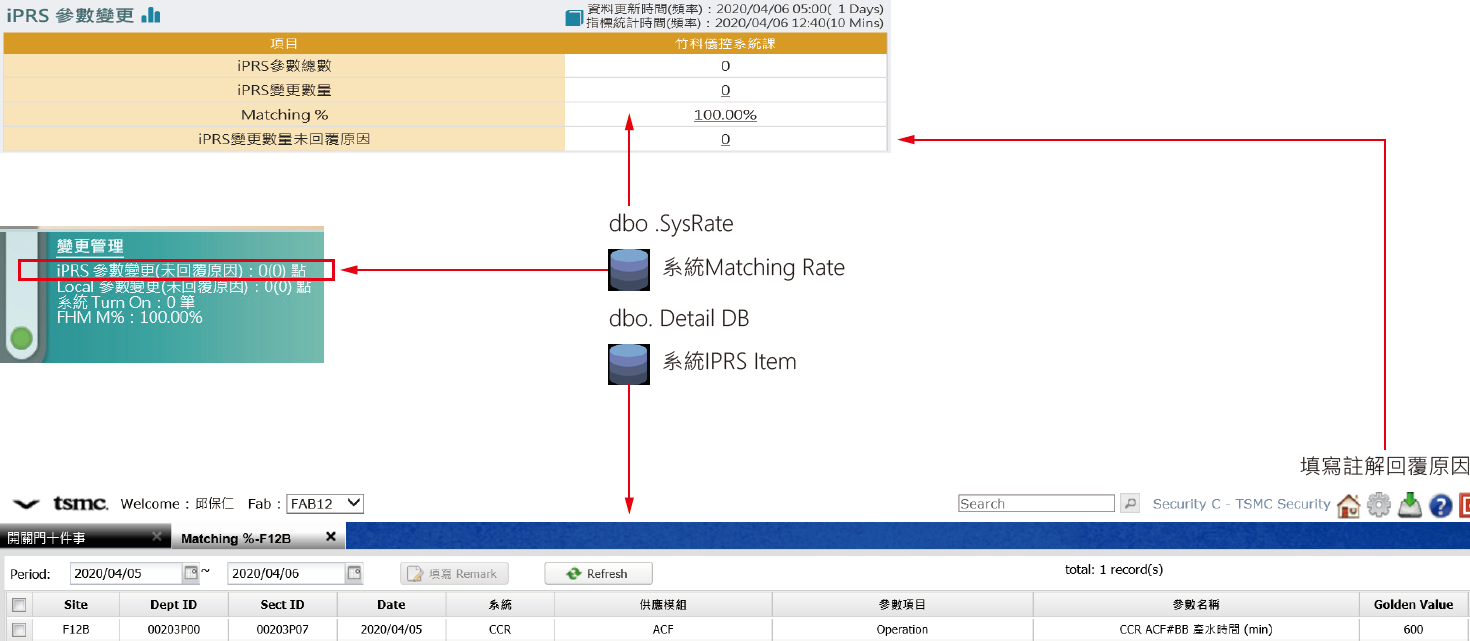
i-PRS的設計理念則是針對系統重要參數變更從源頭管理,直接到PLC(控制器)撈取機台系統參數再將參數上傳至資料庫再進行資料前後比對。全面監控現場HMI可設定之系統參數。例如Chemical壓力設定、Slurry泵浦轉速設定、混酸比例(Slurry、Chem 、DIW 、H2O2)、H2SO4壓力設定、更換鋼瓶Purge次數,建立參數管理及Benchmark功能,alignment 各廠以符合One Facility之目標透過iPRS System預先處理將資料庫計算完成後每日把結果傳給開門十件事。
iRPS管理層級操作層邏輯部分,將每日iPRS變更參數將各廠區參數總數及變更數量資料庫提供外,另外提供Non- Matching參數細項部分提供之,並由系統可填寫註解,所以INDEX除了Matching%之外,也包含註解填寫完成率也是另外一項指標→圖3。
圖3、iPRS控制層參數INDEX指標
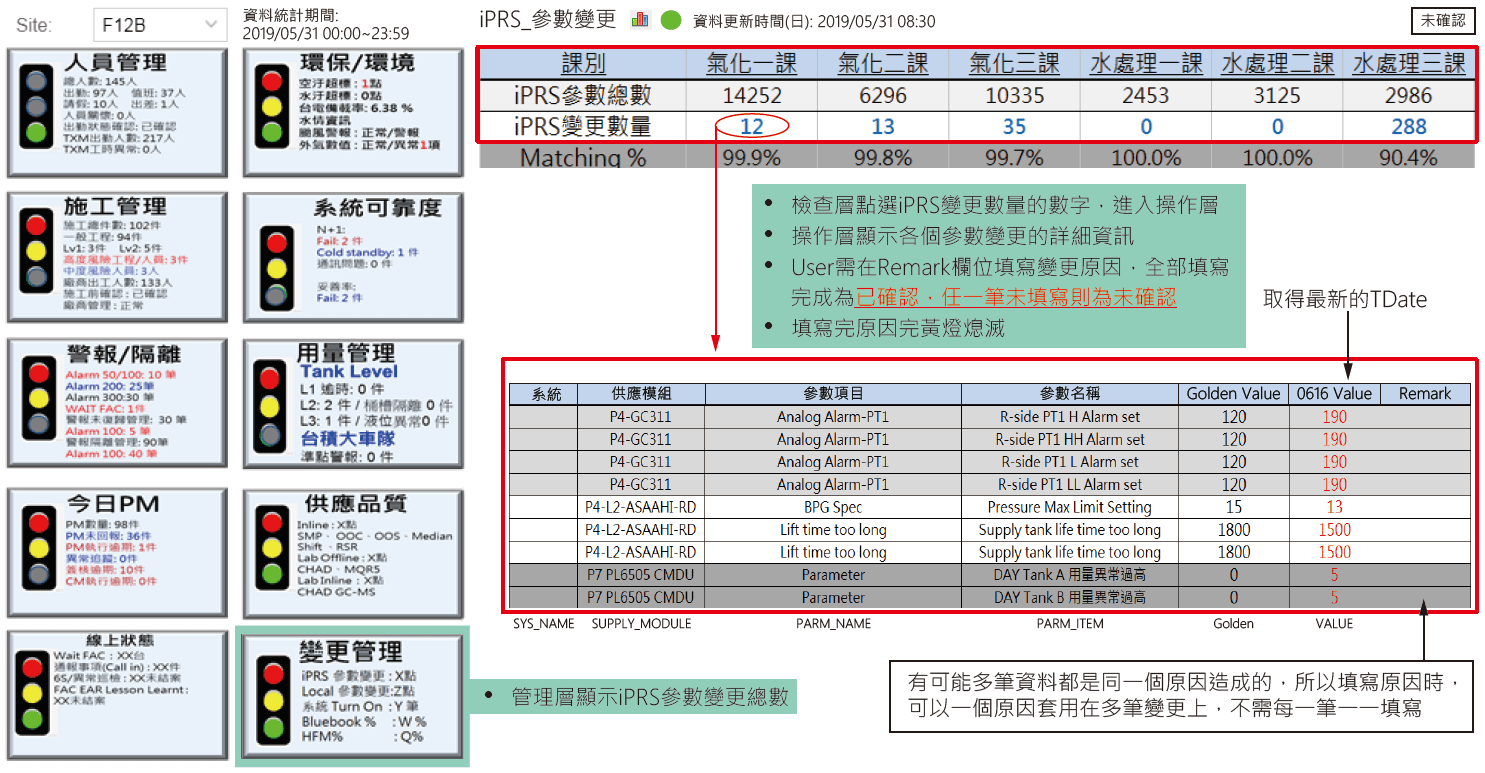
3.2.監視層參數 (Local Change)
監視層參數定義為各廠區DCS/SI/Local SCADA內參數變更,由於各廠區系統皆不一致,且並不像iPRS有參數總數定義,所以在Local參數變更只會紀錄當日有變更其參數數量,由各廠區將其每日變更寫入資料庫且計算變更數量後先處理完成再完整給開門十件事→圖4a,所以在管理層以變更參數數量跟參數變更註解完成率→圖4b。
圖4a、Local Change監視層參數Data Flow
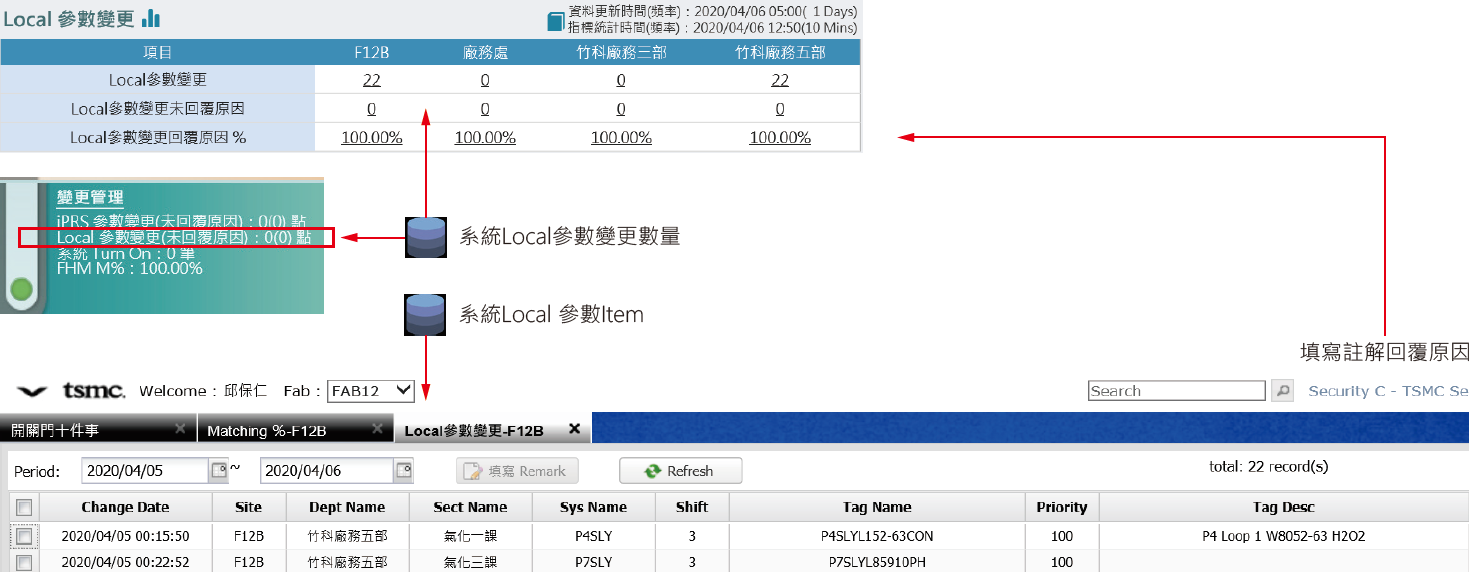
圖4b、Local Change監視層參數INDEX指標
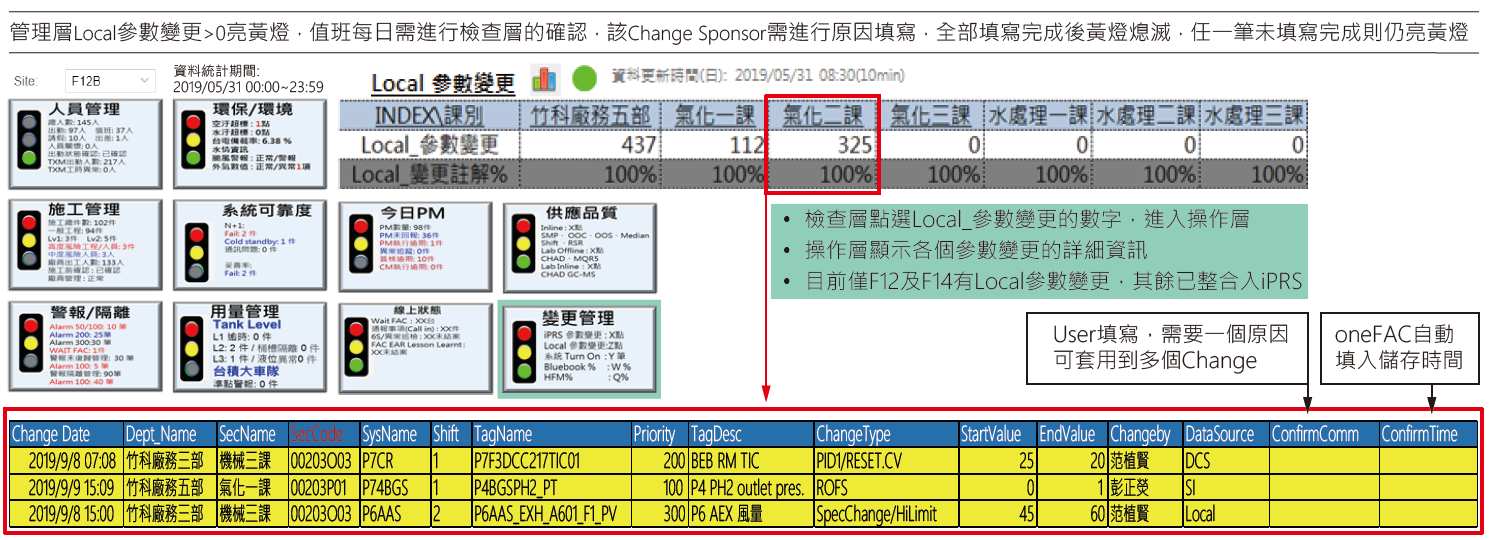
3.3.Turn on (e-Hookup System)
Tool Turn on資料以e-Hookup為Base,因各廠區於e-Hookup皆有資料且這是有強制性平台,Tool Turn必須在此平台上傳資訊,並以針對拆機Code移除將Tool Turn on資訊更正確,e-Hookup系統只有廠區別並無系統及課別分類,此資料透過Turn-On種類依照對應表取的系統及課別分類→圖5a,以每日Tool Turn on機台總數對應Facility System是否正確,得知每日廠務utility Turn on給機台→圖5b。
圖5a、Turn on參數Data Flow
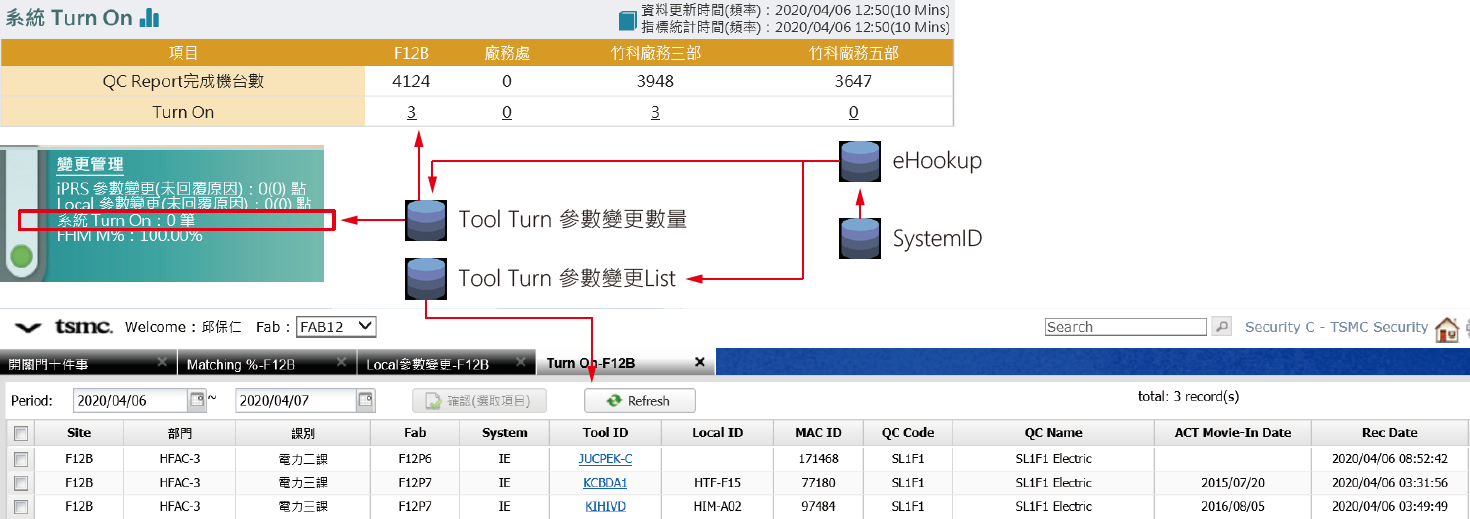
圖5b、Turn on參數INDEX指標
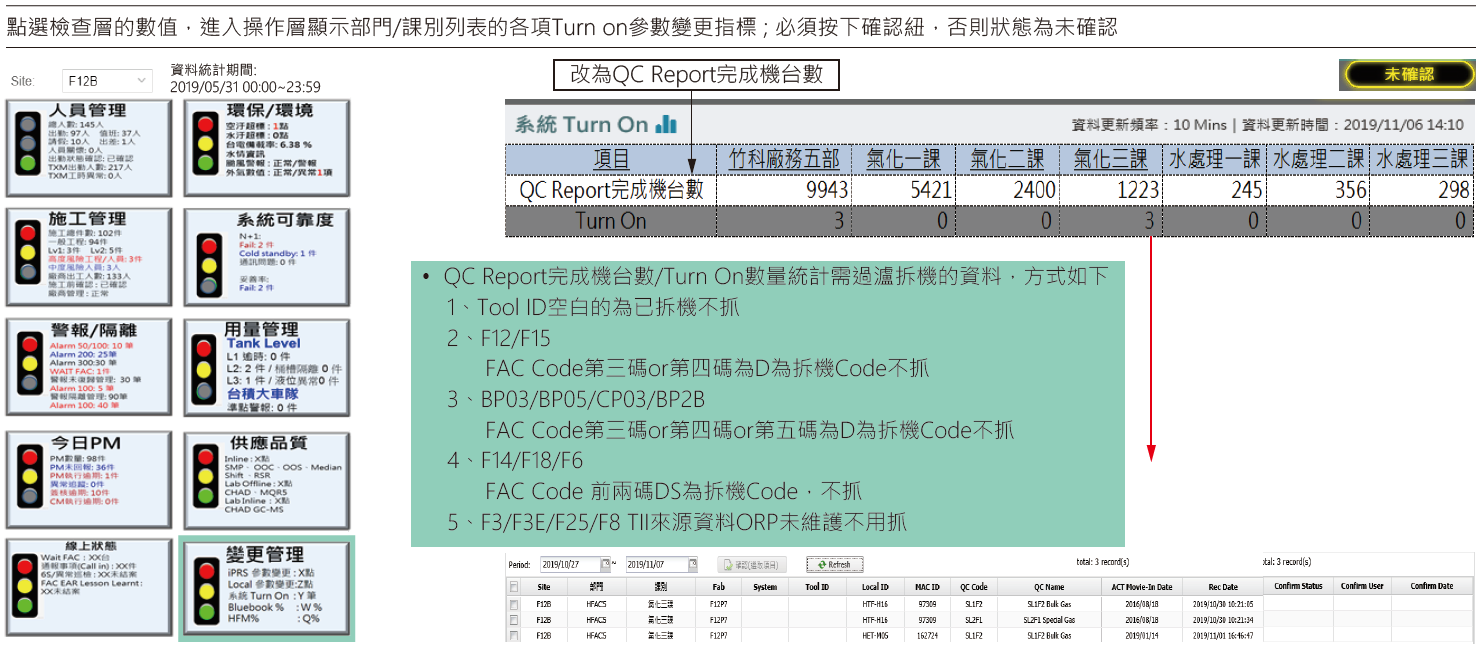
3.4.廠務機台參數 (e-Bluebook System)
透過參數管理平台取得Tool-Turn on資訊,可以得知每日有多少機台Turn-on FAC Utility與FAC Bluebook比較是否有更新Bluebook機台資訊,由串接Turn-on & Bluebook資訊並要求廠務人員強制維護Bluebook→圖6,並記錄連續Non-Matching天數,只要Bluebook未更新,連續Non-matching天數會一直累加至超過7天會由黃燈變成紅燈狀態。
圖6、Bluebook機台參數INDEX指標
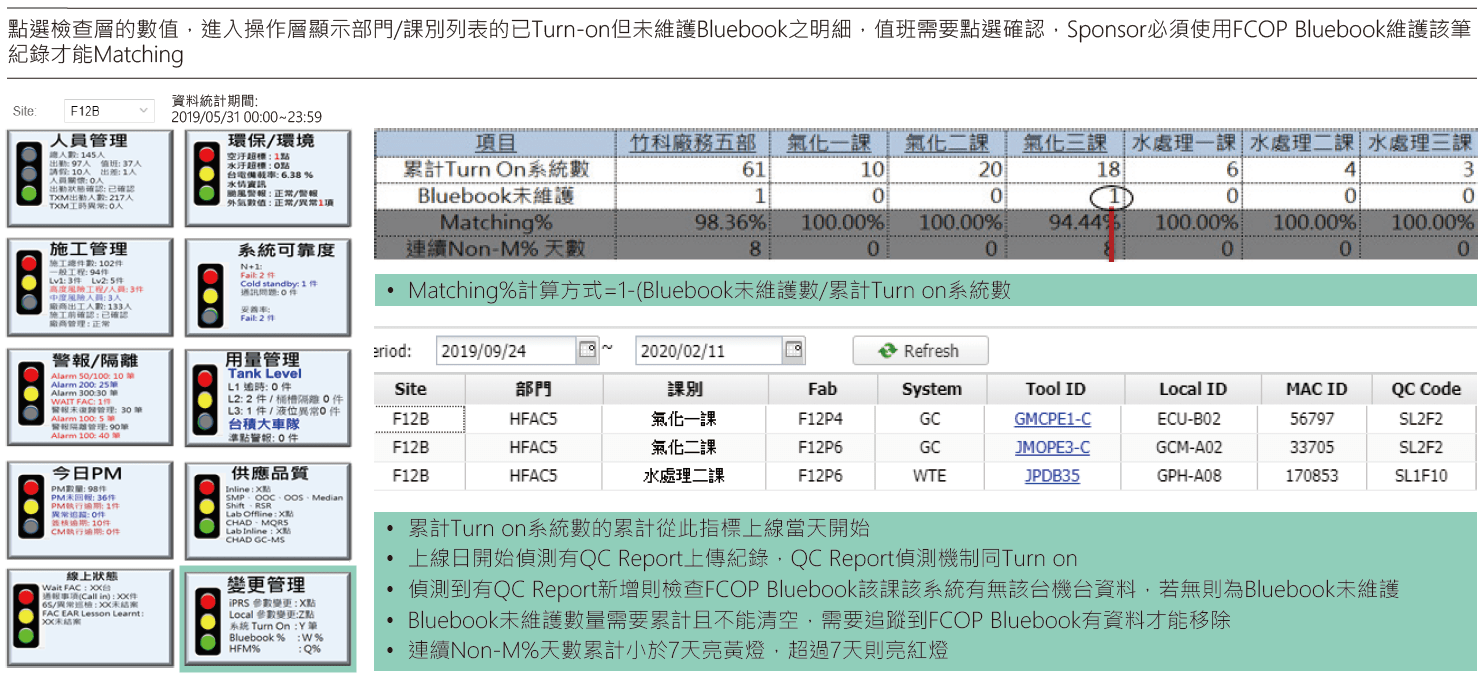
3.5.原物料參數(e-Hookup System)
透過Bluebook & FHM OP Log,比對FHM OP Log(GAS/CHEM/SLY) & Bluebook→圖7,原物料對應設備資訊是否有遺失,並通知Sponsor手動更新Bluebook。
圖7、FHM原物料參數INDEX指標
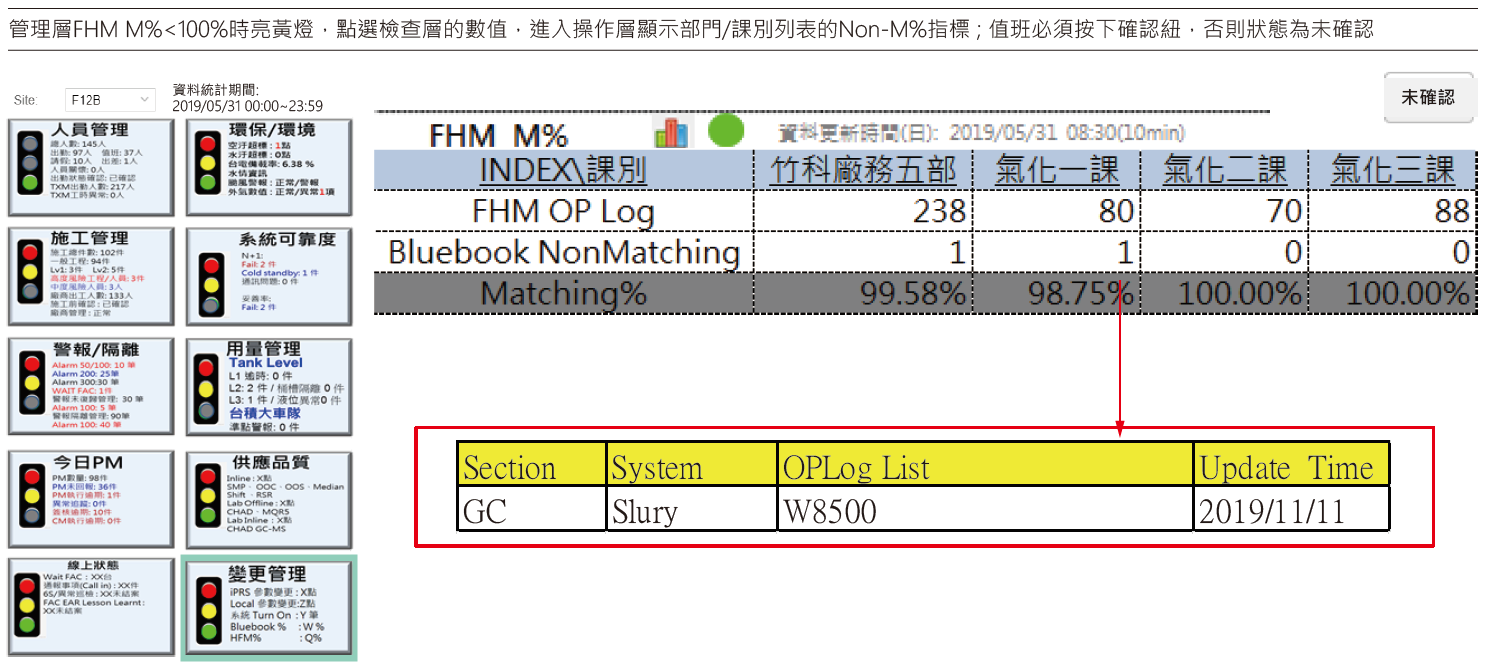
結果與分析
原本各廠區參數平台,皆無統一平台可讓同仁共同使用,利用此機會將所有資訊整合並可有回饋資訊將公開讓各位同仁參數變更狀態→圖8,以利運轉上系統因參數變更後是否是更穩定與否,也可以藉此讓各廠區參數相互比較達到一個最佳 Golden參數。
圖8、開門十件事參數管理平台管理層
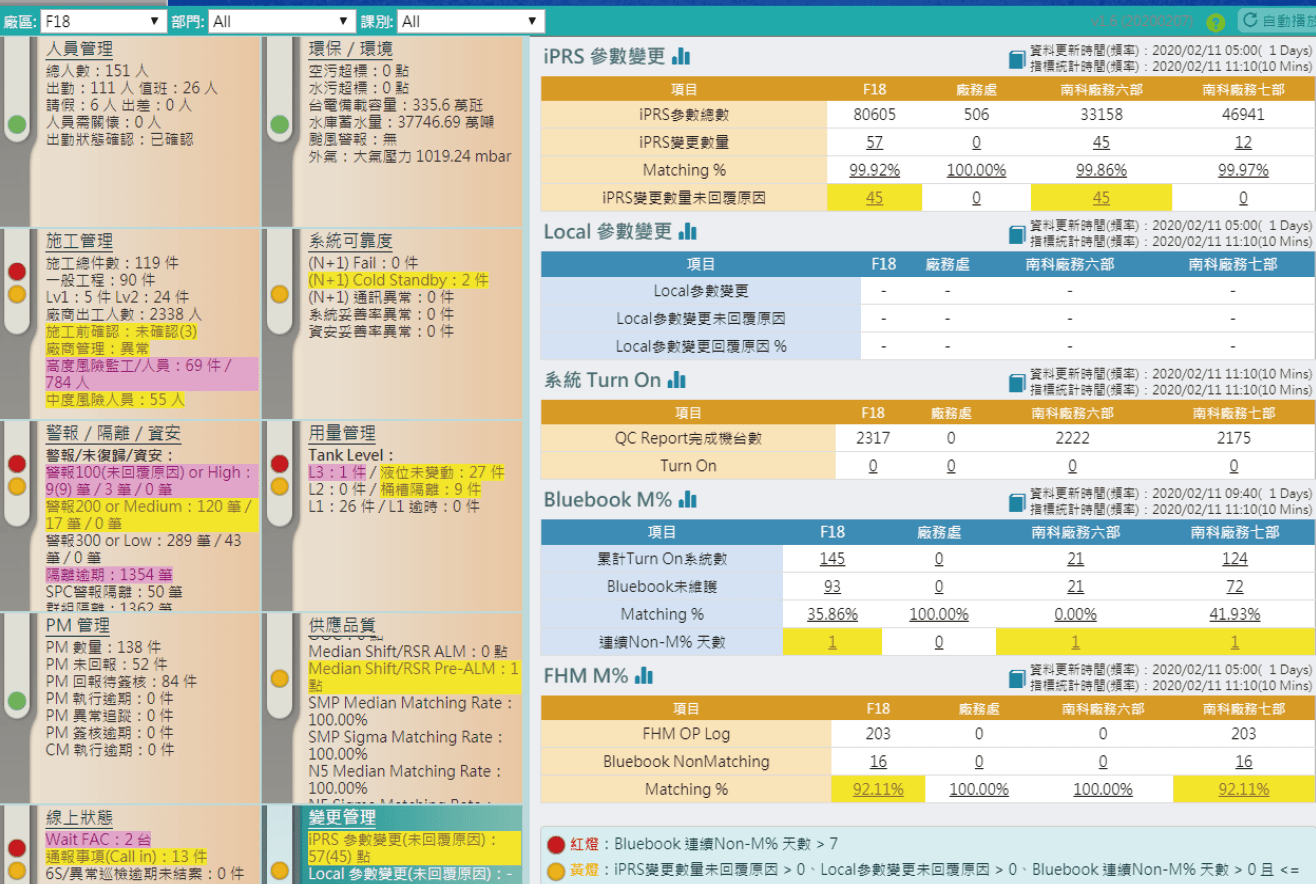
從機台由原物料或廠務中央提供Utility供給狀態,包含廠務各Utility控制監控參數完整記錄都在這參數管理平台呈現給同仁,都是各自獨立分散資訊,在未來可以評估將這資訊有所串接,由Tool ID可得知對應原物料批號及使用FAC Utility各系統如何供給詳細資訊,且其監控參數為何,能夠一條龍以機台Base取得所有廠務參數。
而其實有些參數在於現場才能取得,如管路材質/大小/廠牌/型號,甚至有部分控制器參數無法回傳監控系統(如Local PID控制器等),這些並無在這參數管理平台內,如何將這些資訊一併整合,可以未來可以探討題目。
結論
對於參數未來是否有可能自動上線比對如何達到,計畫規劃底層參數定義,由各廠Naming Rule定義後將資料自動上線到iPRS,廠務參數未來以iPRS為參數基礎IT系統讓管理All-IN-One且自動化→圖9。
圖9、iPRS參數管理未來發展
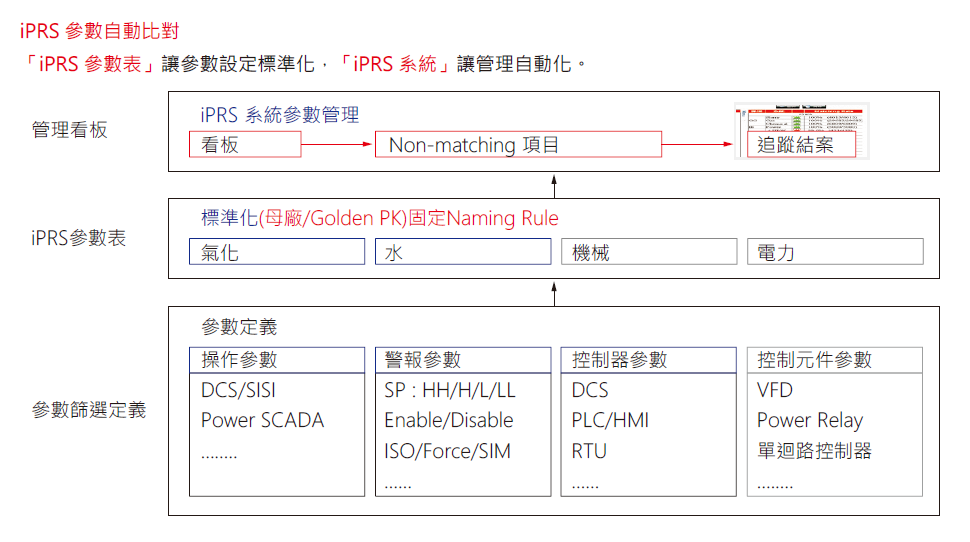
參考文獻
- 2019品質管理Workshop報告資料。
- 2019廠務資訊看板90% design review會議報告資料。
- 王世煌, TOSHMS(Taiwan Occupational Safety and Health. Management System)專業訓練 變更管理相關法規/規範及運轉實務,2009。
- 謝昱銘、林晉逸、鄭芳田,國立成功大學 製造資訊與系統研究所【107年經濟部智慧財產局國家發明創作獎】得獎人專刊-智慧型良率管理系統 ,2019。http://research.ncku.edu.tw/re/articles/c/20191115/1.html
留言(0)