摘要
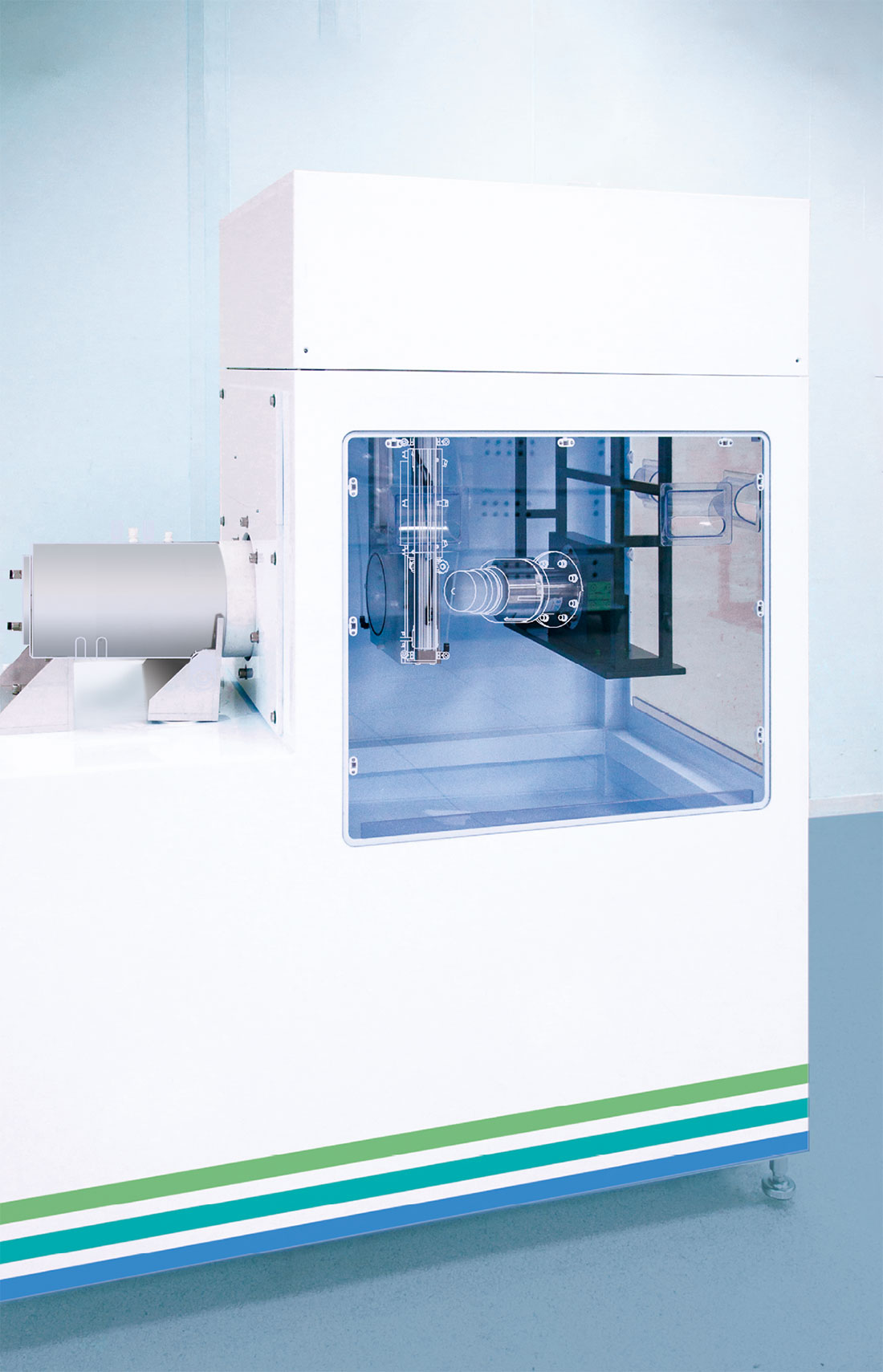
新世代化學品灌充口設計
隨著半導體製程持續演進,槽車化學品用量不斷被提高,化學品灌充作業人力也逐年上升;過去也曾因為外部環境品質影響,造成灌充前取樣量測不穩定。本文主要說明如何應用滑軌、氣壓缸與訂製夾具等動力元件於化學品灌充設備中,來設計架構簡單、易操作及防呆的自動化流程,將流程簡化以提升作業效率。另外藉由導入小環境無塵化的概念,在效率提升的同時增加品質的穩定性,維持灌充口設備的潔淨度。預期在2018 年將會投入測試及修正,讓公司在少子化、自動化的時代,可以有一項兼顧效率與品質的新選擇。
前言
化學原物料用量需求隨先進製程的突破愈來越大,圖1為統計計各世代硫酸用量的分析,單一晶片的用量不斷變高,因此灌充次數及相關的人力也大幅增加。例如長春化工的南區灌充手已經從2013年7人迄今已增加到20人。除了廠商的灌充手外,廠務於每次灌充也須派出監管確認人員,因此對人力的需求也是逐年提高的。所以我們希望開發自動化灌充流程以減緩人力成本的需求成長。 同時,我們也希望將過往造成作業上困擾的問題一併改善,即是提升灌充環境品質。過去灌充口的位置設計主要都是在戶外,即使是最新的中科十五B廠設置在房間內,相較於化學原物料供應商在一個有的HEPA封閉的環境中,仍有潔淨度上的差異(Class 10,000比Class 1,000)。如表1顯示,2017年仍有11件以上槽車因灌充接合過程退車。因此,灌充接管環境的優化也是設計的目標之一,以期符合未來更新製程發展的需求。
圖1、Lorry化學品(H2SO4代表)用量隨著製程演進不斷攀升
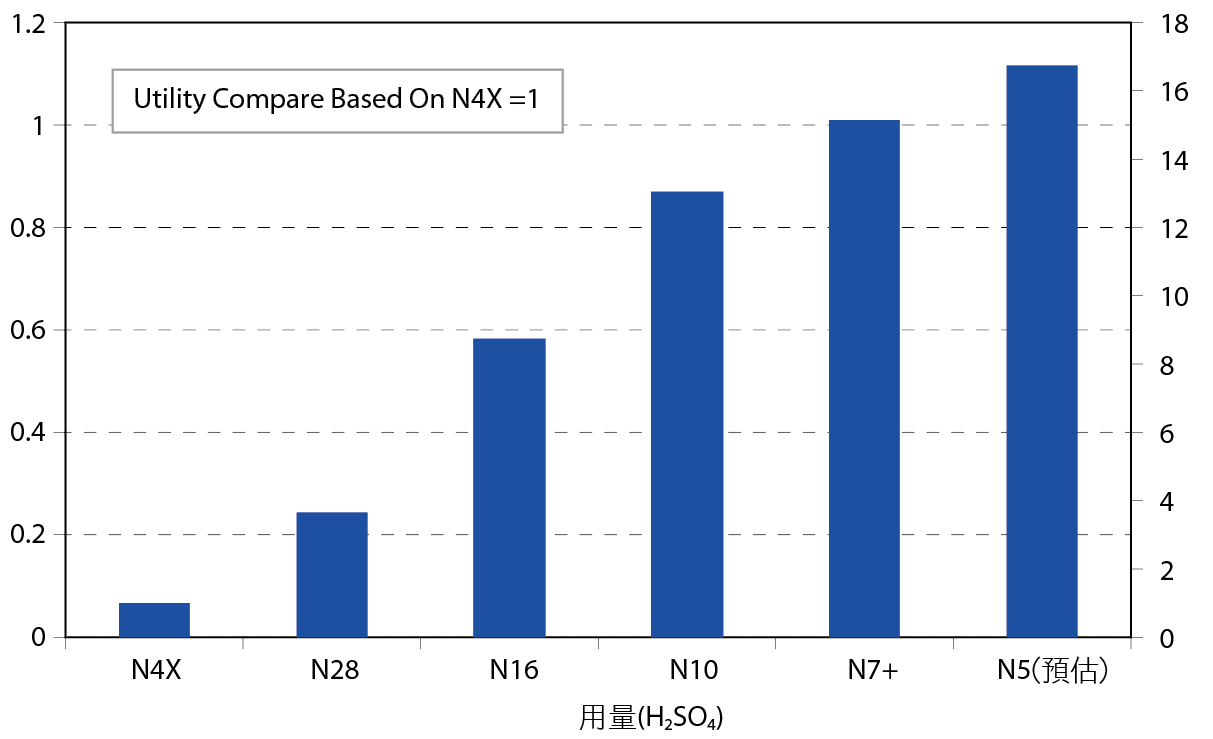
Item |
Y2016 |
Y2017 |
Y2018 |
||||||||||||||
---|---|---|---|---|---|---|---|---|---|---|---|---|---|---|---|---|---|
M701 |
M702 |
M703 |
M704 |
M705 |
M706 |
M707 |
M708 |
M709 |
M710 |
M711 |
M712 |
M801 |
M802 |
M803 |
M804 |
||
退車數 |
11 |
0 |
0 |
1 |
1 |
0 |
2 |
1 |
1 |
1 |
0 |
1 |
0 |
0 |
0 |
0 |
|
退車廠區 |
F15 P2 KM |
F12 P4 KM |
F15P5 F14P4 KM |
F14 P2 PPC |
F15 P2 KM |
F15 P5 BASF |
F15 P5 KM |
————— 無退車 ————→ |
|||||||||
DIW Flush Turn-on |
F14 P5/6/7 |
F12P1/2 |
F12P4/5 F12P7 |
F12P6 F14 P1/2/3/4 |
F15P5/6 |
||||||||||||
Thinner-1 退車廠區 |
3 |
F14 P5 TOK |
F12 P0 TOK |
F14 P4 |
F12 P2 TOK |
F12 P2 TOK |
F15P2 F12P4 TOK |
||||||||||
NTD 退車廠區 |
0 |
F12 P7 |
F12 P7 |
F15 P5A |
文獻探討
本研究文獻主要透過政府規範及業界實務來探討作業安全及品質的設計規範,也透過參訪半導體展學習業界導入自動化實務案例。本段就安全、自動化與品質三方面來探討設計方向。首先,化學槽車灌充作業主要是參考行政院勞工委員會化工安全作業標準參考手冊第三章圖2,來定義大用量化學品的傳輸與使用方式,其中管路銜接部分主要依靠人力執行;這些程序都是基於安全而訂出,因此即使導入自動化,也是必須遵守的程序。我們也訪查業界作業方式有無可效法之處,但安全標準上看來仍是一致的。
圖2、行政院勞工委員會化工安全作業標準流程建議
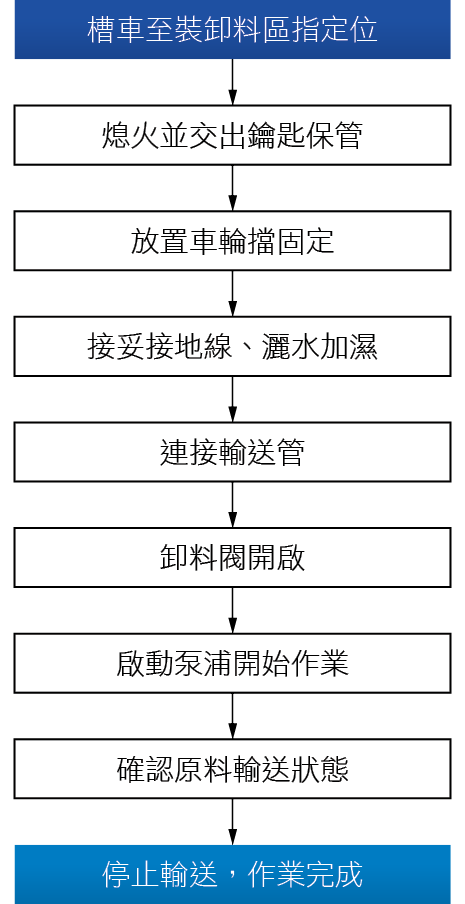
在2017年的半導體展中,我們發現在有廠商已經發展自動化灌充接管的創新應用,並且在海外已有實績。這讓我們在灌充流程作業自動化上更有信心,如圖3所示其設計主要是利用機器手臂、滑軌與氣壓缸等元件組合的應用,讓人員將公頭放置在固定位置後即可離開,之後透過滑軌將公頭往前推進到定點後,機器手臂會來夾取公頭進行接合動作;在接入母頭之前,其保護蓋自動打開後再進行接合。這讓我們確信了自動化可以達成,但同時我們也在想:是否有更簡易的方式呢?因為這個設計的複雜度相當高,也使用了相當多的自動化元件,將會提高維護的複雜度。因此,我們會取自動滑軌移動公頭,與母頭自動開關保護蓋的優點,來作為我們未來設計的基礎;至於機器手臂,我們認為可以透過部分人為來進行,畢竟此設計還是需要人去放那個公頭。就如同Elon Musk說在解決Tesla Model 3生產瓶頸時說的,過度依賴的自動是敗筆(Elon Musk, @elonmusk, 2018/4/13);因此在應用上循序漸進保留小部分人為作業,以確保非預期異常可被檢知。
圖3、HOSAN自動化CCB:接頭保護蓋自動開啟

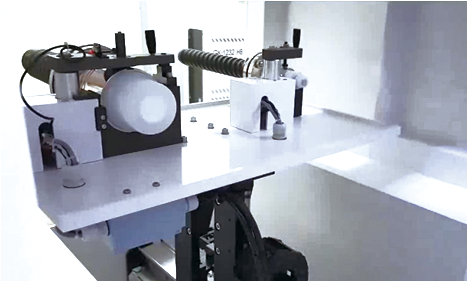
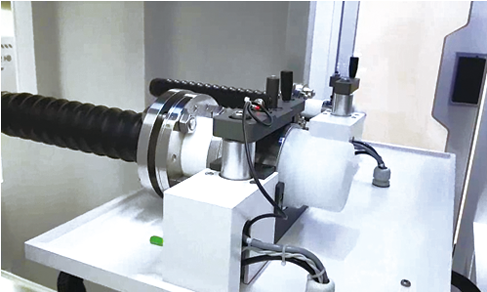
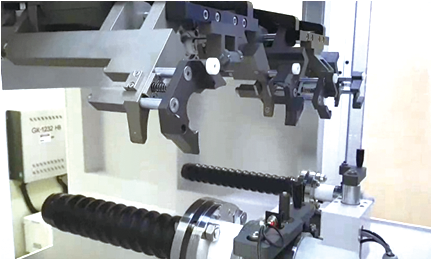
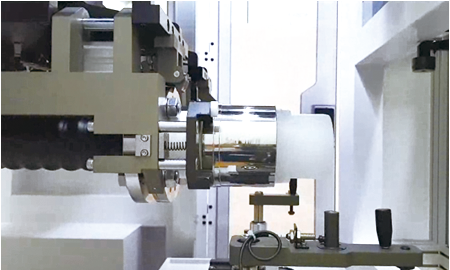

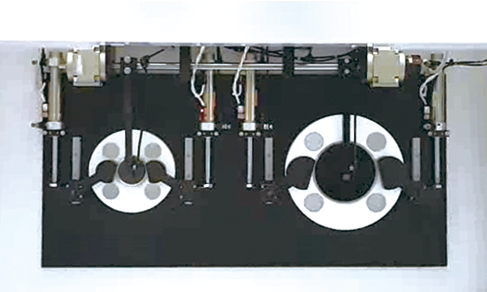
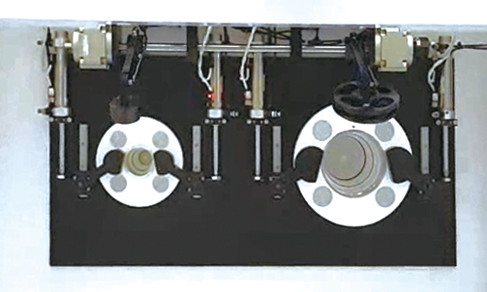
而品質管理方面,在參訪數家主要供應商之後,我們發現有兩個值得學習的地方:一是在HEPA過濾後的正壓無塵環境中進行接管作業圖4;二則為灌充管路接合前,針對接頭先作純水清洗加強清潔圖5,目前在既有廠區也已導入執行,可參考圖6;在圖6中也可看到,灌充口在戶外確實會在接頭上殘留髒汙,即使灌充前會有化學品沖洗等程序,但仍有疑慮。另外根據ITRS 2.0半導體技術發展針對液態化學品的規劃,除了品質量測技術外、整體供應系統及其元件必須也要往消除particle方向發展,如表2所示。因此我們審視整體槽車化學系統如表3後,主要為灌充接管部分有接觸環境風險,因此我們將會納入這兩點做為設計的基礎概念。
圖4、供應商化學品灌充環境與設備設計原則
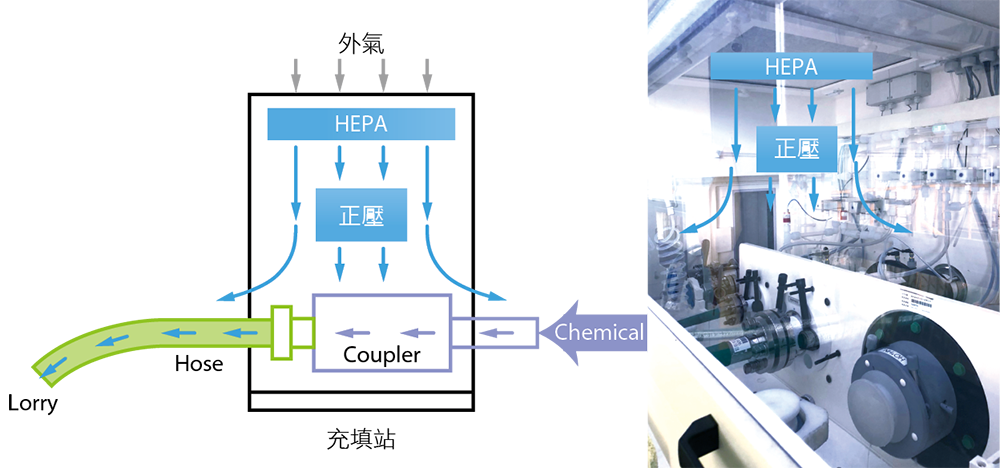
圖5、供應商接頭清洗流程

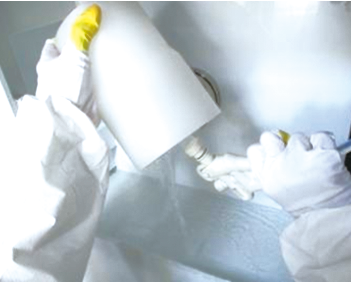
圖6、化學灌充接頭接合前清洗
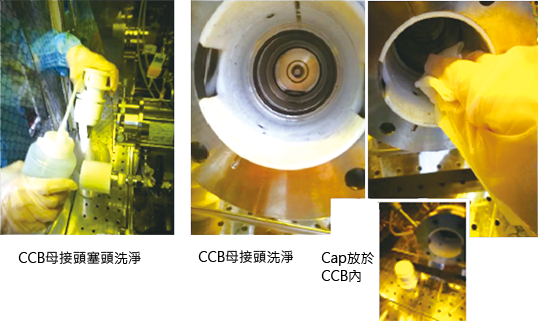
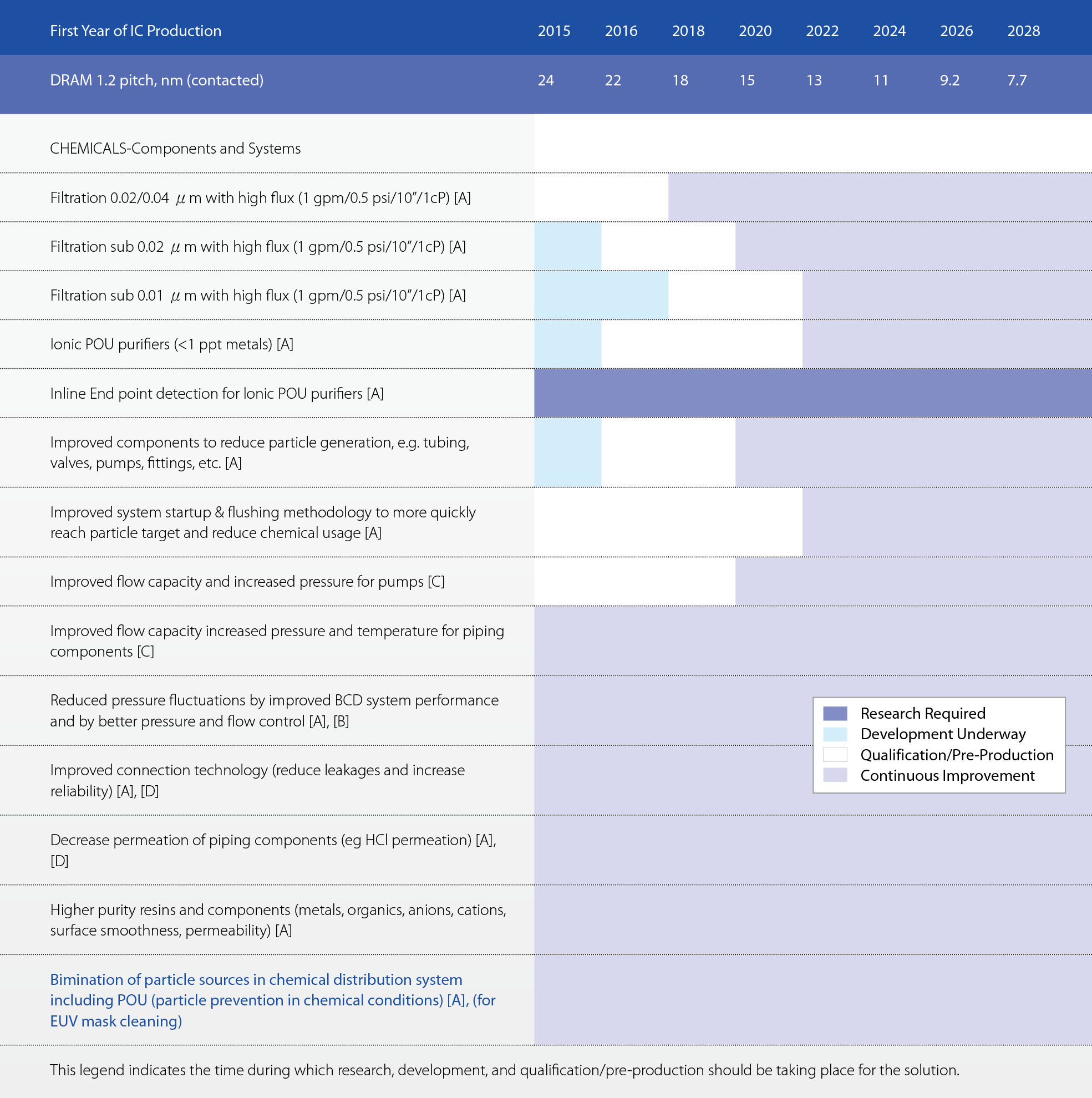
廠務單元 |
作業項目 |
作業頻率 |
位置 |
接觸外氣風險 |
---|---|---|---|---|
CCBTU |
灌充接管 |
每天 |
戶外/室內(15B後) |
高 |
取樣 |
每半年 |
管路排出 |
無 |
|
濾心更換 |
每半年 |
室內/PVC布區隔 |
低 |
|
RU |
取樣 |
每半年 |
管路排出 |
無 |
濾心更換 |
每半年 |
室內/PVC布區隔 |
低 |
|
CDU |
取樣 |
每半年 |
管路排出 |
無 |
濾心更換 |
每半年 |
室內/PVC布區隔 |
低 |
研究方法
呼應文獻根據前段討論,我們設定了兩大方向來設計新系統:透過自動化來精簡接管作業與環境無塵化;基於上述方向,本段更進一步說明此設計。
機台外構具彈性
基於未來新舊廠都可應用的理念,我們預計採用外掛式設計,在既有系統不做額外大改造的前提下來研發。原則上材質必須和既有相容,遇施工須焊接時可確保一定強度,故酸鹼類化學引延續採用PP材質,而有機類化學品則使用SUS304材質。但考慮在許多廠區灌充位置會在戶外,因此針對日曬和風吹雨打的防護也將是必要的。
另外各廠灌充區的規劃也不盡相同,例如灌充口外的止水墩設置各廠不一,考慮到機身標準化的前提,本設計就需要有高度調整的彈性來因應,這部分預計會在支撐腳的部分增加可調整的範圍,由原本標準機台的5~12公分的彈性要增加到5~30公分。
接管自動化
接管自動化可以說是整個設計的核心,具有把人為動作流程轉為數位化的能力。目前預設流程是灌充手將公頭放置於搭配key code設計的固定夾具後,將作業門關閉後就開始自動流程。自動流程包含三大動作:灌充公頭自動移動、母頭防塵蓋的開關與接合前清洗(DIW+N2)。以下針對三大流程分別說明。
灌充公頭自動移動
參考Hosan的設計後,考量到整體複雜度高還有機台內機器手臂維護不易,故我們預計使用較簡易且可靠度較高的滑軌來進行。這部分保留人員對位並確認的動做,對準key code後將公頭擺放正確並固定,同時進行後續流程正確性核對。接下來機構移動採用氣壓缸滑軌來移動,主要做單純的直線傳送,該動作首重精準度以確保動作完成後的保壓正常。與Coupler原廠商討論後認為誤差要在1mm內,故選用的元件定位準確度達10條(即重複誤差<0.1mm)。另外機構荷重須符合設備需求,目前估算整體接頭荷重約40Kg (公頭、法蘭、支撐架、與含硫酸管材),故至少選擇缸徑32mm、操作壓力5~6kg的元件,可產生40~48Kg推力始可符合本應用。
在移動之前,會有自動確認key-code位置動作圖7,來確認灌充手是否正確安裝,我們稱做“校正滑蓋”。此設計是為確保灌充母接頭不會因為人為異常而損壞,故它是很重要的動作。其設計邏輯與接頭一樣,透過滑軌來執行圖8,但需要兩個行程,一是水平移動來作主要動作,二是主要動作完成後需要往上移動避免干涉接管動作;而元件的選用邏輯則與接頭移動滑軌相同,當然其負載需求就相對較低(僅滑塊本身,小於5Kg)。
圖7、校正滑塊確認公頭安裝keycode
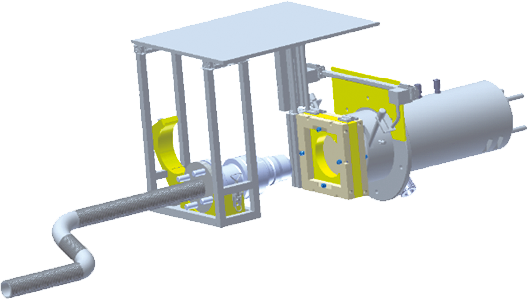
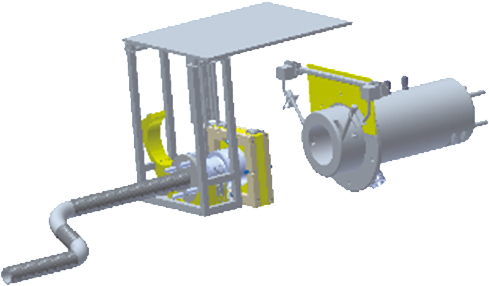
圖8、校滑軌將接頭直接導入母頭
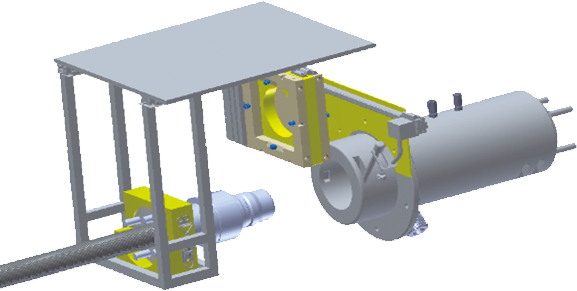
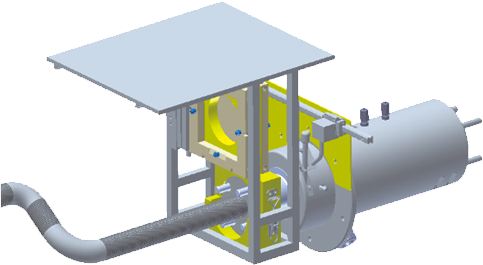
多功能母頭防塵設計
目前設備上CCB母頭的塞子主要功能為防塵和避免化學蒸氣逸散,避免無使用的狀況下不會有異物進入接頭中。因此本設計將透過多功能型的校正滑蓋與作業流程的連動,在確保接合空間清潔之前,不會暴露母頭避免汙染,同時達到設計簡化的概念圖9。
圖9、校正滑塊、母頭保護蓋與清洗模組一體化設計
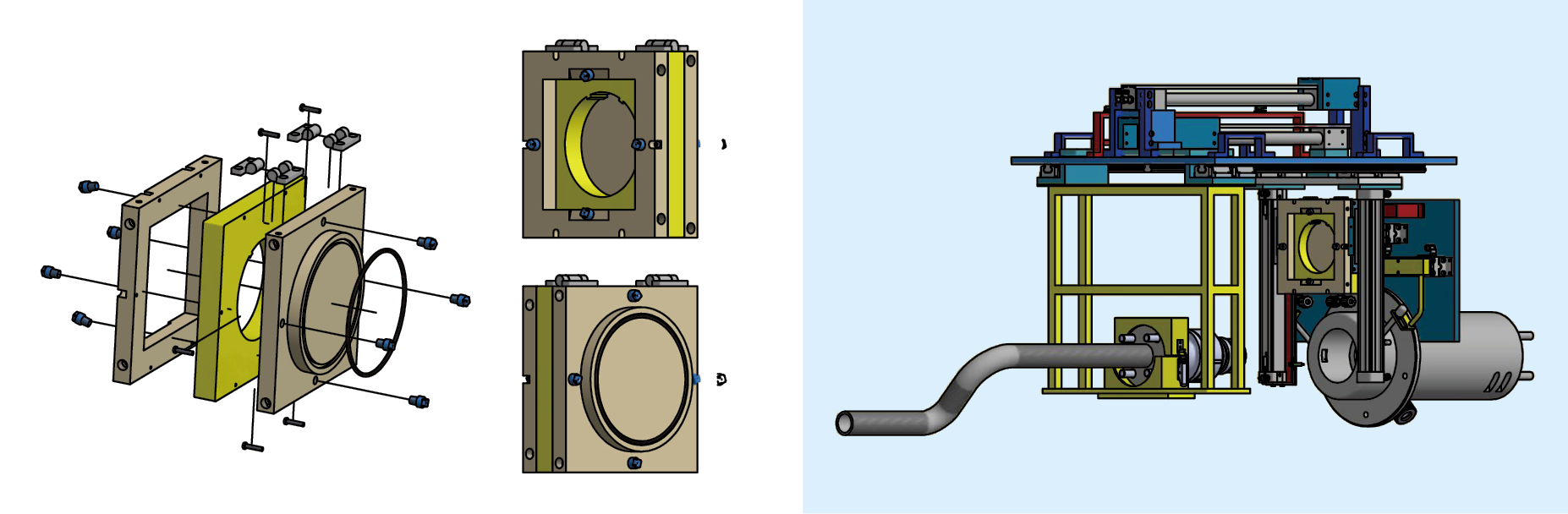
接合前洗淨
如第二段所提重點,供應商在接管作業中有一個動作是針對公頭的清潔被認為有助於品質維護,因此本設計將在接管前導入此流程,做法為由四周噴嘴先後以DIW與N2做清洗,與供應商做法相同。設計概念如前述重點,簡單、易維護且維持品質,故此清洗模組與校正滑塊也是結合一體的。透過特製具內部通道的方框加上噴嘴來作4方向的DIW清洗與N2吹淨,清洗後的液體將直接流到下方集液槽後排出。因為作了這個整合,流程的複雜度就大幅降低,但相對地元件就會稍微複雜;因此我們將其設計成三個模組透過活動式連結片結合,如此未來維護上將會較為容易,未來甚至可以考慮以3D列印方式來製做的可能性。
環境無塵化
根據廠商的正壓設計的基礎,以及化學桶槽N2正壓避免汙染的經驗,本設計也會將採用持壓的方式避免環境汙染物進入作業區。
比較過品質如 表4後我們決定採用CDA,因其品質的能力相對廠商使用之HEPA佳。其次是相對N2也對人員作業較安全,因此選用CDA維持微正壓(15pa)會是較易維護的選擇,且運轉成本也會較低圖10。 針對人員操作口的防護除正壓外,也將設計入口CDA氣簾與門感應sensor連動,只要打開操作口就要啟動CDA氣簾更確保髒空氣無法進入;另外為了避免人員帶入汙染,將參考Air Shower設計利用氣簾對人員的手套吹淨,故於操作口下方設計排氣口與氣簾連動開關。
|
Quality |
安全性 |
PM成本 |
---|---|---|---|
CDA正壓 |
<1 count, @0.1μm |
高 |
無 |
N2正壓 |
<1 count, @0.1μm |
低, 窒息風險 |
無 |
HEPA |
<100 count, @0.5μm |
高 |
高 |
圖10、封閉的接管環境,維持接管作業環境CDA微正壓
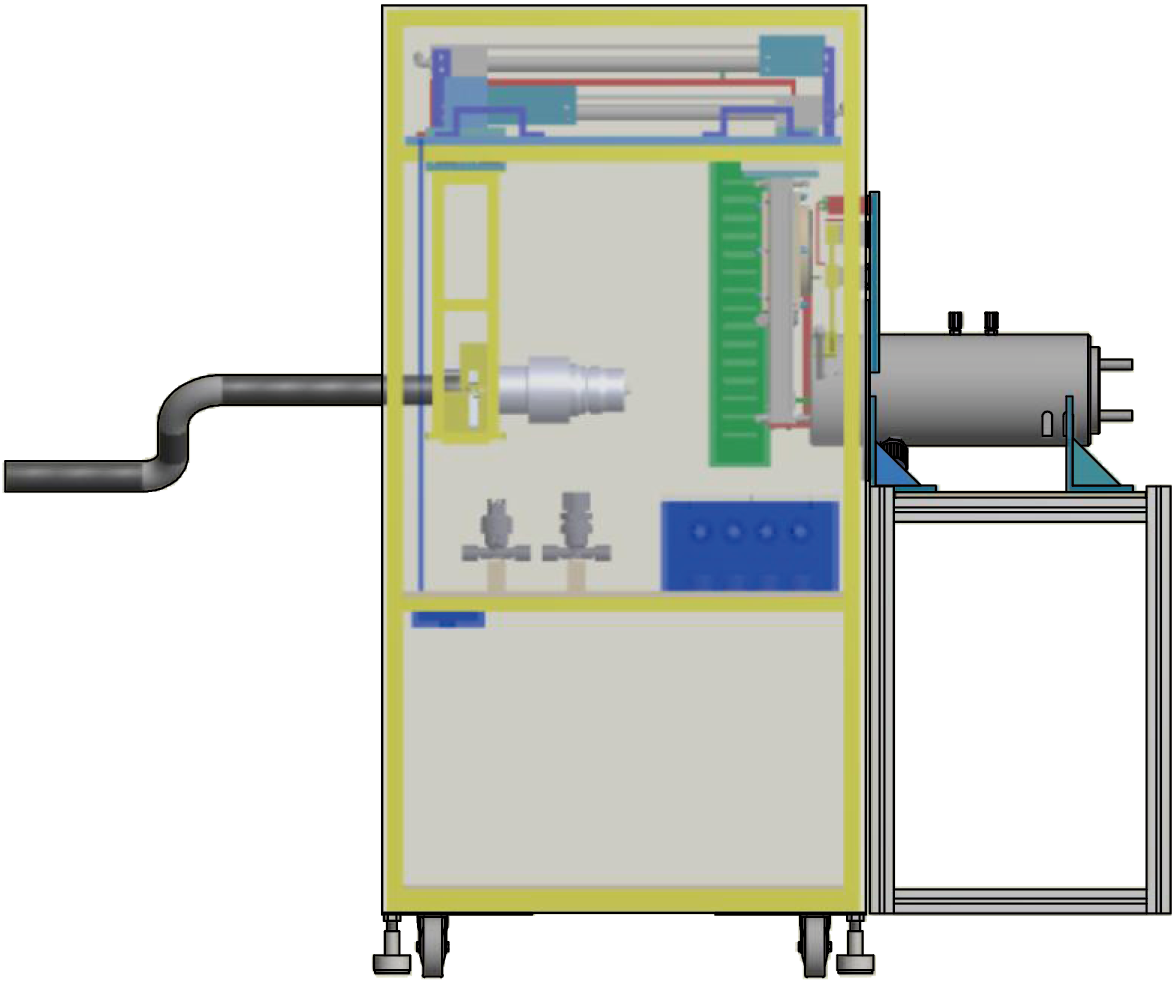
安全設計與流程防呆
除文獻探討提到的作業規範外,機台安全設計乃根據SEMI S2規範與ITRI防爆認證要求(針對有機化學品)來規劃外,本設計也特別將確保新設計不破壞既有元件列入考量,尤其是昂貴的CCB;因此公頭安裝座的防呆設計為搭配不同化學品去客製化避免人員錯誤安裝,再加上前述的校正滑塊做雙重確認,更確保元件不易因誤動做而損壞。其次在所有自動化設備做動時,是不能開啟操作口的,其為整體流程中人員與機械的唯一介面,故此操作口將設計磁扣做連鎖,須關閉才能啟動自動作業流程,以避免人員造成傷害。
結論
雖本設計目前尚在Demo機製造階段,尚未有實際測試結果。但我們透過在化學品的安全、自動化與品質相關文獻的探討,來找出一套新世代化學品灌充口需要的設計元素;並加上綜合已有實務經驗上的應用,將其轉換為可行的做法。相信跨出的這小小的一步,將帶出未來許多可能性:例如讓灌充接管作業數位化後,在未來的管理上有很多彈性可以應用,包含建立指標、流程優化、自動報表,甚至到未來的AI應用。另外元件的取得如何使用3D列印來產出,避免減少運轉維護成本也是未來可以發展的一環,畢竟CCB元件需求量並不算大。本設計以安全為根本,加上CDA微正壓進行接管環境的品質管控與自動化的接頭外部清洗與接合應用,再輔以簡易維護的理念,希望能與讀者取得共鳴,將設計更精進來提升公司、甚至台灣產業界的競爭力。
參考文獻
- 行政院勞工委員會化工安全作業標準參考手冊
- HOSAN, http://www.hosanco.com/eng/
- 2017 SEMICON Show
- https://technews.tw/2018/04/16/musk-is-finally-admitting-mistakes-too-much-reliance-on-automation-is-a-failure/
- Figure YE5 Wafer Environmental Contamination Control Potential Solutions-Liquid Chemicals, THE INTERNATIONAL TECHNOLOGY ROADMAP FOR SEMICONDUCTORS 2.0: 2015
留言(0)