摘要
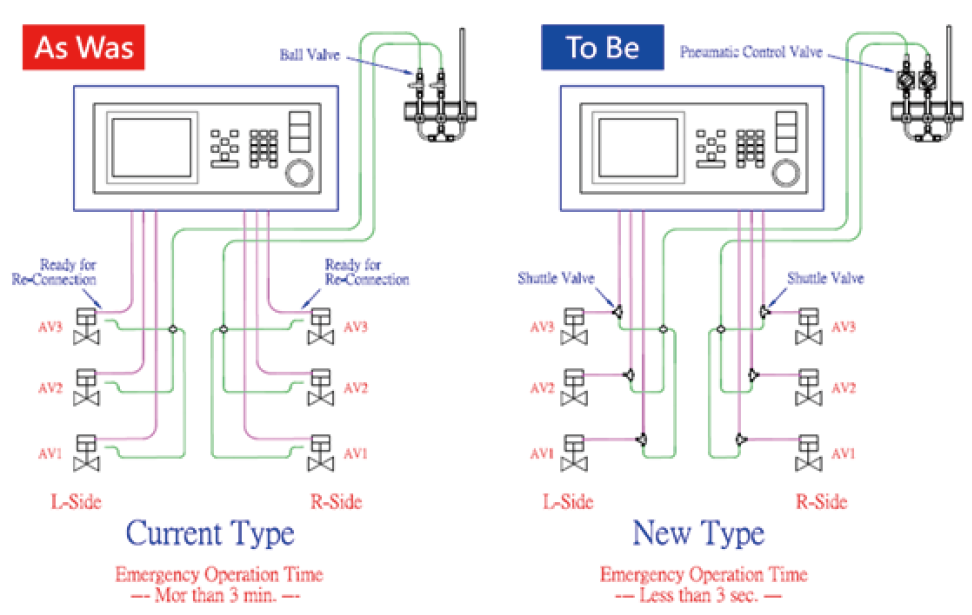
舊科技廠房氣化供應系統無痛升級方法與實務
本文主要說明高科技廠房的廠務設備會隨時間不斷的演化和進步,並伴隨著長時間的運轉經驗而提出更好的系統改善方案,老舊的科技廠房將面臨兩大挑戰。
第一 : 系統硬體部分因逐年老化需汰舊換新並藉由不斷完善改善過程(Continuous Improvement Process, CIP)提升系統穩定度與可靠度,第二 : 控制軟體部分由微處理器(Microprocessor)控制器升級為可程式化邏輯控制器(Programmable Logic Controller, PLC)的改善可符合。這兩大項改善因應工廠24小時生產不中斷之需求,必須有效安排規劃施工程序步驟做到無痛升級,並已安全穩健且不影響廠區生產為最高原則,已達到舊科技廠房氣化供應系統無痛升級之目標。
This paper mainly statement that the facility equipment of high-tech plants will continue to evolve and improve over time, and propose better methods for system improvement with long-term operating experience. In this case, the old technology plant will face two major challenges.
First : The hardware part of the system needs to be replaced due to the aging of the system year by year, and the stability and reliability of the system will be improved through the continuous improvement process(CIP).
Second : The improvement of the control software part from Microprocessor controller to Programmable Logic Controller(PLC) can be met. These two major improvements meet the needs of the fab 24-hour production without interruption. The planning and construction procedures and steps must be effectively arranged to achieve a painless upgrade. The highest principle has been safety and stability without affecting the production of the fab area. It has reached the painless gas/chemical supply system of the old technology plant upgrade target.
前言
台灣積體電路製造股份有限公司於1987年創立,為滿足生產運轉需求,建立許多自動化設施,舉凡製造部、設備工程部、倉儲管理部以及廠務部等,皆有使用自動化設備以取代高危險、單調性、高頻率的人力行為,減少人為因素的失誤以及人力費用的產生,以達到有效、快速以及品質穩定之生產。
以六廠為例,目前正邁向第25個年頭,若以當初的設計規範需求已不符合現在廠務需求。故將研究探討六廠氣化課以及新工處針對目前供應系統相互比較,再針對其優點進行改善,此研究主要針對特殊氣體供應、化學品供應系統以及研磨液供應系統,進而進行探討以及改善。
六廠目前供應系統設計除了不符合目前新工處需求之外,尚有另一件問題正面臨挑戰,即目前部分供應系統廠商以及零件逐漸停產並Phase out。故如何讓六廠能夠永續且穩定的運轉,即為當前最重要課題之一。
文獻探討
2.1 Special Gas供應系統新舊世代比較
特殊氣體供應模式主要是藉由氣體鋼瓶本身與機台使用端之壓力差,利用 高壓氣體會往低壓方向移動之特性,來達到氣體供應之目的。一般特殊氣體供應架構主要有氣櫃(供應源)、VMB/P(中繼站)、使用機台(用戶端),如 圖1所示。
圖1、氣體供應系統上下游示意圖[1]
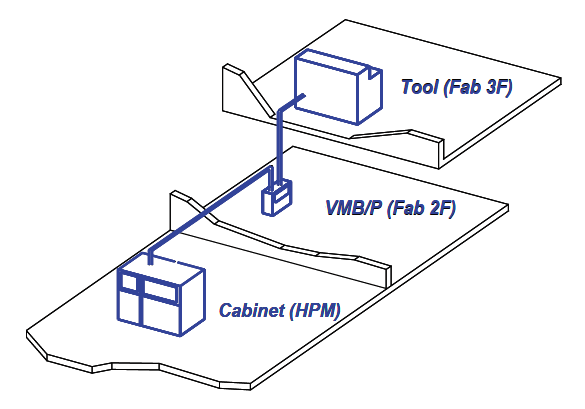
一般氣櫃設計主要皆為三鋼氣櫃型,其一鋼瓶為Purge Gas為10%He/N2鋼瓶主要作為鋼瓶更換程序中沖吹時使用之氣體。其二為Process Gas主要為供應線上機台所使用之製程氣體,一邊為供應側、另一邊為Standby側,並可透過監控鋼瓶壓力(PT1)回傳到氣櫃內控制器進行閥件控制切換與藉由手動調壓閥PCV(Process Control Valve, PCV)調整供應壓力(PT2)達到線上機台需求,並透過最後一段出口壓力(PT4)監控確保供應正常。而供應側之鋼瓶使用後透過控制器立即切換至Standby側,以達到供應氣體不間斷。使用過後之氣體鋼瓶將執行更換鋼瓶程序,Pre-Purge、Change Clinder、Post-Purge、On-Line等四大步驟將舊有鋼瓶換下,重新換上新鋼瓶。
新舊世代氣櫃設計上的差異,有硬體和控制器上的差異(表1)。從系統裝置面、通訊模式和操作面皆大不相同。新世代氣櫃具備有CSD(Cylinder Shade Device, CSD),可避免人員於更換鋼瓶時誤拆鋼瓶。且具有PGI(Purge Gas Isolation, PGI)和DPI(Daul Purge Isolation, DPI),雙隔離閥避免Purge Gas污染製程氣體,且具有PPT(Purge Pressure Transmitter, PPT)[2],可隨時監控隔離閥是否有內漏情事產生。並附加強攻模組可在氣櫃發生供應異常時,於5秒鐘以內完成氣櫃強供,降低影響線上設備需求。
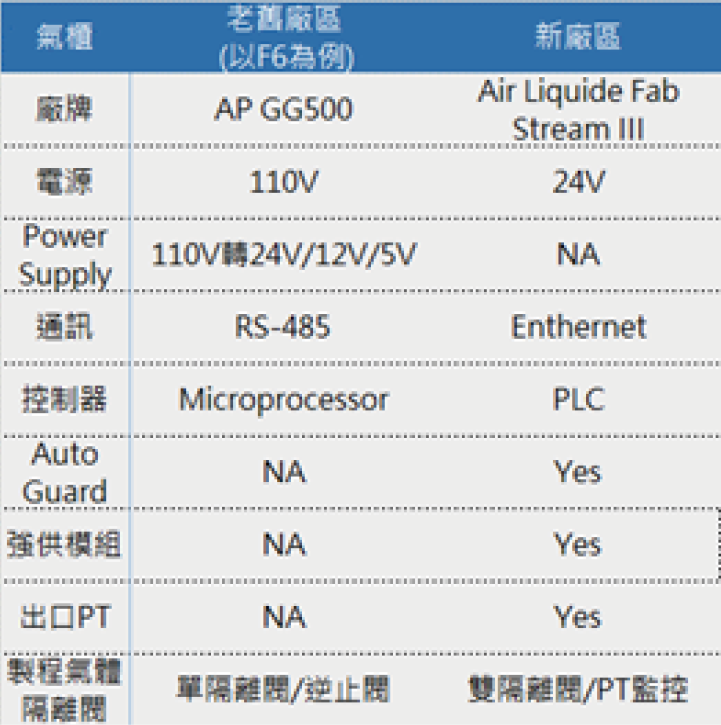
2.2 Chemical供應系統新舊世代比較
化學品於常溫常壓下以液態方式存在,所以其供應模式主要是藉由PV(Pressure Vessel, PV)或Pump等,提供線上機台使用化學品,供應模式為當機台需要化學品時,會透過設備端訊號傳遞給廠務,當接受到訊號時系統會同步開啟CDU和VMB閥件供應並透過pump或加壓PV,使化學品有足夠壓力可輸送至機台端。一般化學品供應架構主要有CCB(Clean Coupling Booth, CCB)、Lorry Tank、CDU(Chemical Dispense Unit, CDU)、VMB、使用機台,如 圖2所示。
圖2、化學品供應系統上下游示意圖[3]
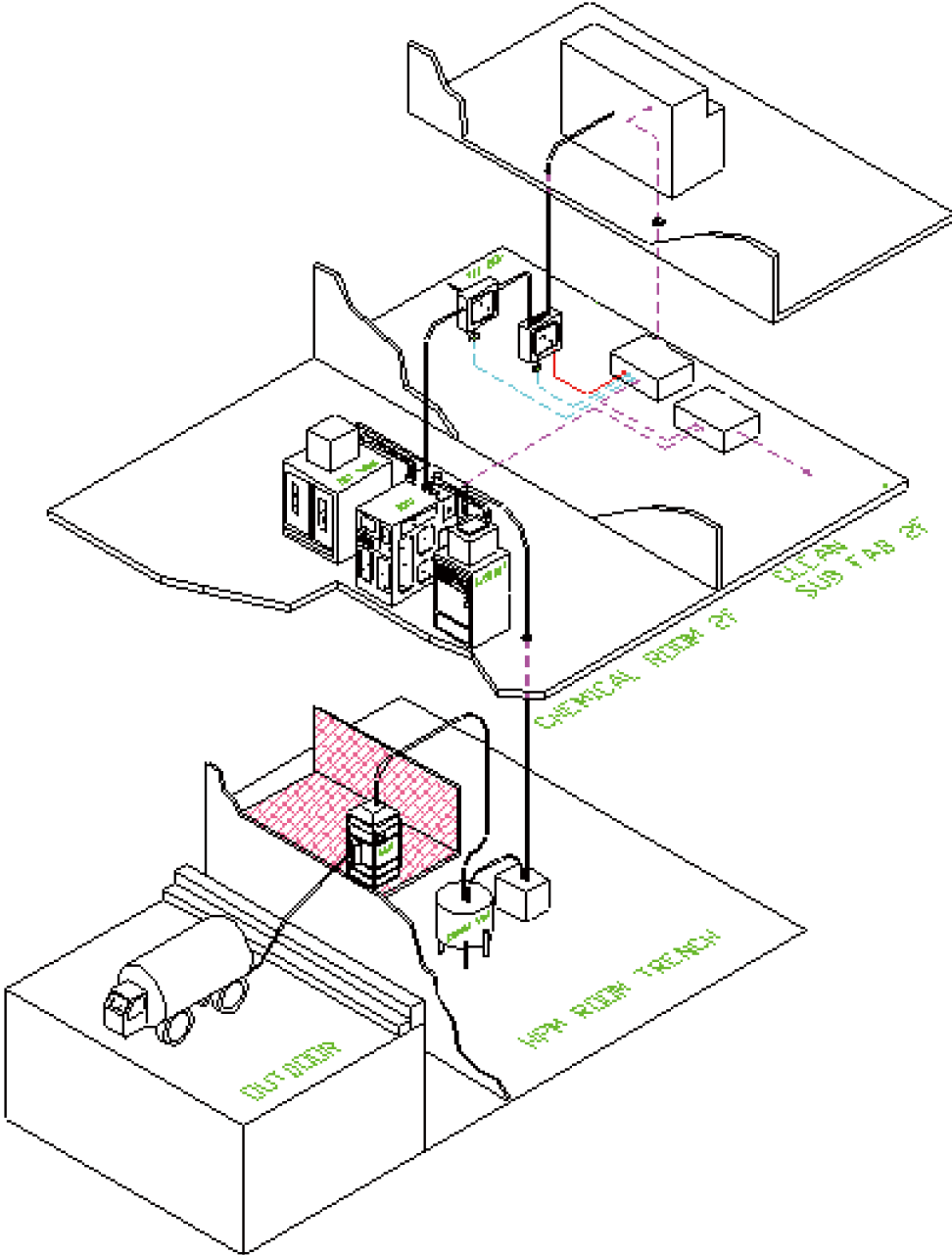
新舊世代化學供應設計上的差異(表2),以六廠為例,廠務與設備溝通介面透過OCP(Operation Control Panel, OCP),當OCP收到設備端的Request訊號時,會透過OCP內部的氣源N2傳送到VMB開啟氣動閥,同時也一併透過Arcnet網路通訊給CDU將出口閥開啟並啟動Pump或加壓PV,使化學品有足夠壓力可輸送至機台端。在這架構下Arcnet同時扮演另一個重要腳色為將OCP訊號以及CDU狀態傳送回SCADA (Supervisory Control And Data Acquisition)用以監控化學品供應系統狀態。而新廠區的設計廠務與設備溝通介面則是透過ICP(Intelligent Control Panel, ICP),不同的是ICP和CDU溝通是藉由Controlnet通訊架構回到Mater PLC統一發號指令對CDU進行運行命令,同時VMB的閥件也都會透過ICP hardwire乾接點訊號傳遞給VMB上的端子台進行控制開關。另外回傳廠務系統狀態則是改透過Enthernet傳遞。
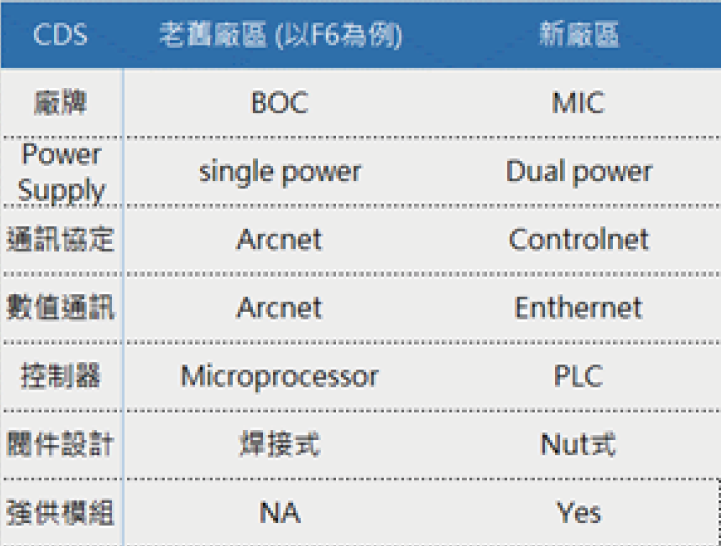
供應機台的硬體差異則是閥件和管路組裝方式的不同,舊廠區使用為焊接式的方式,優點是較不容易產生洩漏,但缺點卻是異常時影響範圍較大可能修復時間會較長。新廠區則選用Nut螺牙鎖式,優缺點與舊廠區正好相反。
2.3 化學研磨液供應系統新舊世代比較
Slurry供應架構可分為混酸系統和供酸系統,如 圖3。Slurry在供應至機台端之前會藉由混酸系統將Slurry原液、DI水和雙氧水依照重量比或體積比充分混和後,再經由分析儀器檢測雙氧水濃度或比重後,再藉由供酸系統中Pump或Pressure Vessel維持供應路徑一定壓力至機台。
圖3、化學研磨液供應系統上下游示意圖
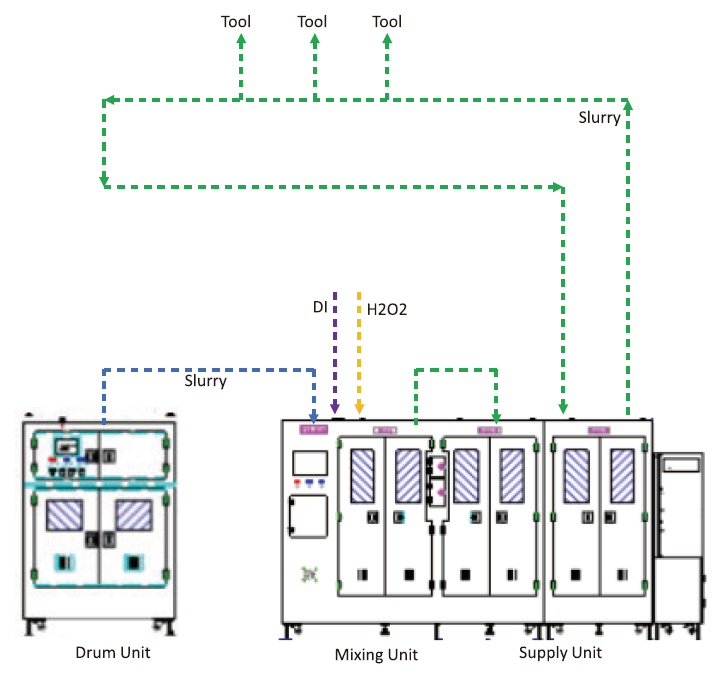
新舊世代化學研磨液供應設計上的差異(表3),以六廠為例,可分為兩種供應系統BOC Isis以及Mega系統,以Isis機台混酸的設計為藉由各自獨立的Slurry、DI、H2O2 Pump stroke次數,傳送到Mixing Module藉由定體積比內部擾流達到混和效果,並透過Control Module確認混和雙QC,再供應至Dispense Module,並藉由Wet N2將Pressure Vessel內之Slurry輸送之機台端。而Mega系統設計與化學品供應系統混酸較相近,為Primary或Secondary Module完成混酸後會藉由分析儀器測定QC,確認濃度值正常後會處於Standby狀態,等待另一側使用完後切邊使用。混酸比例主要是透過重量控制加入Slurry、H2O2、DI,並利用隔膜式Pump循環充分混勻。同時也利用此Pump當作供應Slurry之動力來源。新廠區的設計大不同於此,混酸的設計為藉由定量式的容器確認Slurry、H2O2、DI的固定量落料到Mixing tank進行混酸後QC確認無誤再打到Supply tank[4],另外不同的是整個系統設計是採用磁浮式pump進行混酸和供應。
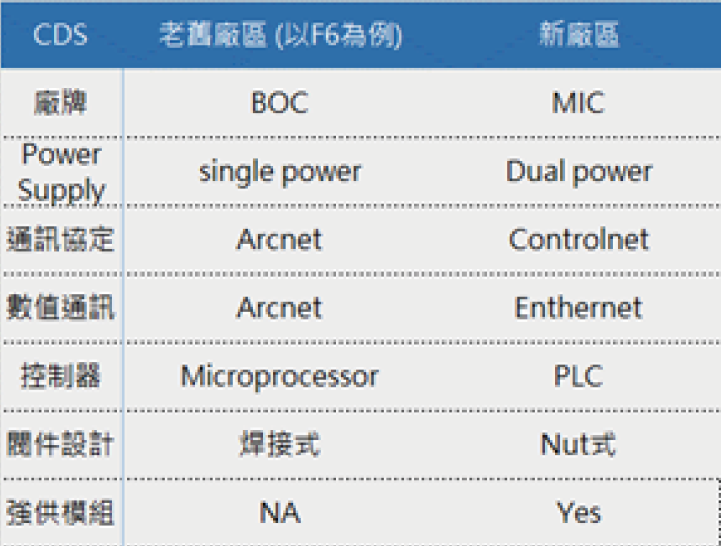
計畫方法
3.1 現行供應系統架構修改
根據六廠以及新工處供應系統相互比較,可以發現有許多地方值得去學習和參考。以特氣供應系統來說,新廠設計供應電源以直流24V中央供應為主並搭載雙電源迴路提高可靠度,控制器以PLC為主,避免Phase out廠商供應鏈不足問題。具有Auto Guard可避免人員誤拆上線中之鋼瓶風險。製程氣體與Purge氣體之間具有雙隔離閥以及PT監控,避免汙染製程氣體之情勢產生。氣櫃出口具有PT以隨時監控供應壓力於適當範圍之內。並配備強供模組於氣櫃發生不可預期之狀況能有效穩定供應氣體壓力,減少對線上機台之供應風險。
六廠化學品供應系統控制器主要以微處理器控制為主,若將變更為PLC控制器將有效解決老舊廠房設備零件來源供應問題。並同時搭載一鍵強供,讓緊急應變更快速便利。F6 Slurry供應系統BOC ISIS7000設備目前已停產,且後續維修與備品廠商已不再提供人力及物力,故為維持穩定供應運轉,將參照新工處設計模式,並合作開發更穩定之Slurry混酸和供酸系統。
3.2 建構程序、步驟
目前六廠與新工處機台設備設計差異有一段差距,理想狀態若能一次完全修改完成是最好不過,但是考慮人力物力若要一次完成修改完成其風險程度是非常高。故設備修改程序將會依照綜合風險評估來整體規劃修改程序。
3.2.1 Special Gas供應系統
特殊氣體供應系統依照各個不同存在風險性以及嚴重性來評估綜合風險(表4),並排定規畫修改優先順序。以製程氣體隔離閥為例,當單隔離閥出現內漏情況時,並不容易被察覺(風險性高),且Purge Gas很容易透過內漏處進而污染製程氣體,導致線上產品報廢情勢產生,同時會造成多台機台影響(嚴重性高),且六廠曾經有發生過案例(急迫性高)。為徹底解決此問題我們將原本單隔離閥修改變成雙隔離閥,並於雙隔離閥之間設立PT,隨時監控管路壓力,並設立警報,一但壓力高於0psig立即Alarm,人員可以立即反應處理。
特氣系統風險評估 | ||||
---|---|---|---|---|
項目 | 風險性(1-5) | 嚴重性(1-5) | 急迫性(1-5) | 綜合風險 |
製程氣體單隔離閥 | 5 | 5 | 5 | 125 |
強供模組 | 3 | 5 | 3 | 75 |
控制器更新 | 3 | 4 | 5 | 60 |
Auto Guard | 3 | 5 | 2 | 30 |
這方面需要修改的地方有三大部份,第一部分就是管路硬體修改設計、第二部分為控制器軟體程序修改、第三部份為SCADA顯示頁面修改。再執行的過程中除了與廠商協同合作之外,並同時申請工程變更安全管理(Safety Management of Change, SMOC)與ISEP共同確保變更前、中、後之安全評估與施工管理。執行第一部份硬體管路修改時,除了會申請廠務高風險作業單之外,還有建立一套標準更換流程,如 圖4所示,以降低修改管路時所有可能產生之風險。第二部份控制器軟體程序修改完後,會先於備用氣櫃測試,並具備功能測試Check List。測試功能流程無誤後再將程式安裝於變更氣櫃,安裝完後會再執行功能測試一次,確保氣櫃功能正常,降低氣櫃誤操作風險。第三部份為SCADA頁面修改,修改完後會確認氣櫃狀態及壓力回傳是否正常,並測試雙隔離閥之間壓力變動是否會有警報產生。
圖4、製程氣體隔離閥改善流程圖
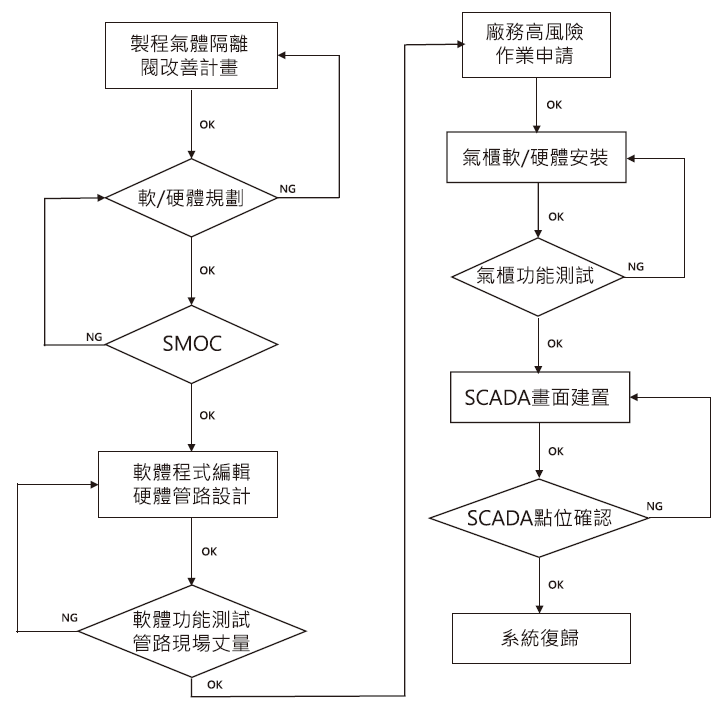
目前六廠氣櫃在失去供應氣體能力時,為了保持正常之氣體供應無虞,每一組氣櫃皆有加裝強制供應氣體系統(圖5)。強制供應氣體系統主要目的在於,當發生電力系統中斷、電力壓降、偵測儀器系統異常、氣瓶櫃設備異常或其它人為操作失誤等問題,而造成氣瓶櫃不能正常供應氣體於現場設備機台時,此時就可使用強制供應氣體系統將氣櫃之氣動閥強制驅動達到供應氣體之目的,使現場設備機台無氣體中斷之虞並保持良好之運作模式進而減少產品大量報廢之財物損失。目前氣櫃強制供應氣體系統使用以及操作較為複雜,故在氣體中斷緊急危機狀況下,其操作時間較為冗長故無法於氣體中斷之第一時間強制供應氣體至現場設備機台,使用方式較為複雜所以在人為緊張的操作條件下容易有操作失誤的情況產生。故將強制供應氣體系統模組化使操作簡單且快速化,縮短緊急應變時間、提高應變效率、減少人為失誤。於變更的過程中依循SMOC的精神,並制定氣櫃強供模組修改SOP,且定義合適強供時機以及流程,如 圖6所示。
圖5、強供模組示意圖
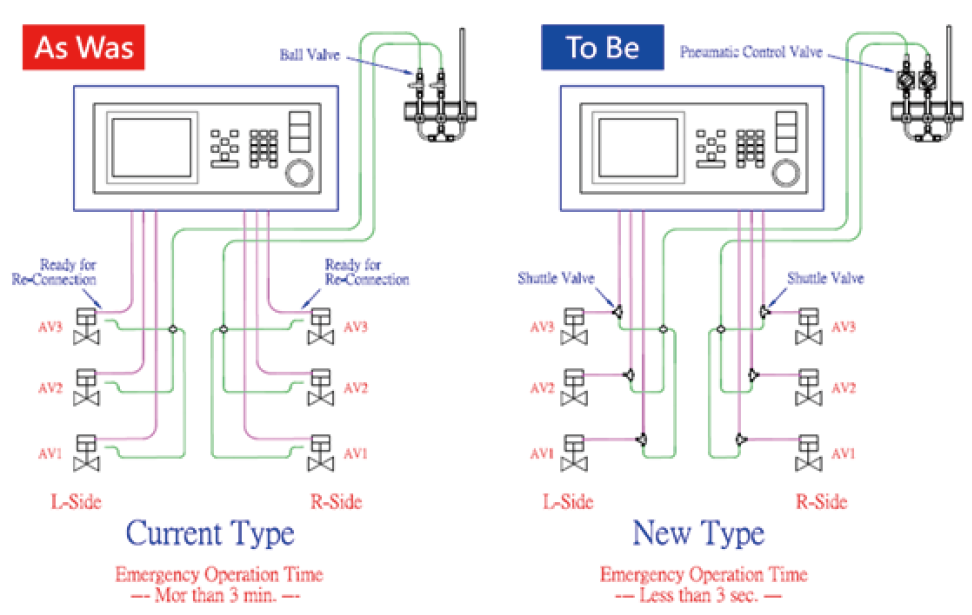
圖6、強供模組改善流程圖
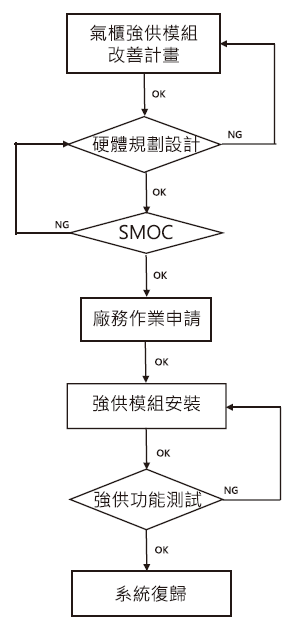
目前F6P1 Gas Cabinet(GC)於建廠初期皆以微處理器作為控制器,但陸續原有供應商已停產且不再提供零件備品以及維修,以至於日後控制器損壞將面臨系統無法復歸之窘境。故為避免此事件發生,將於每年編列預算,逐步將舊有微處理器控制器升級為PLC控制器。並可將舊有汰換下來之控制器暫時作為零件備品,以防尚未升級更換之控制器之不時之需。
控制器相當於整個氣櫃之大腦,運轉之核心。當更換控制器時將會使氣櫃失去控制能力將無法自動運作,故更換控制器時必需仔細思考施工前、中、後應注意觀察事項。施工前與廠商共同規畫控制器硬體設計配置,並確認軟體程式邏輯。控制器完成後必須先於廠外測試整體鋼瓶更換程序以及相關安全作動機制,確認無誤後再安排入廠安裝動作。入廠安裝大致上可分為兩天,第一天主要為控制器硬體更換,更換時要先確認是否完成強供,並盡量使兩邊鋼瓶與滿瓶狀態下更換(確認鋼瓶剩餘量),且要隨時注意管末PT壓力,若管末壓力降至Low Alarm將要立即採取相關應變措施。第二天主要為氣櫃功能測試、安全作動機制及訊號回傳測試。以上動作皆有規畫相對應Check List,如 圖7所示。
圖7、氣櫃控制器更新流程圖
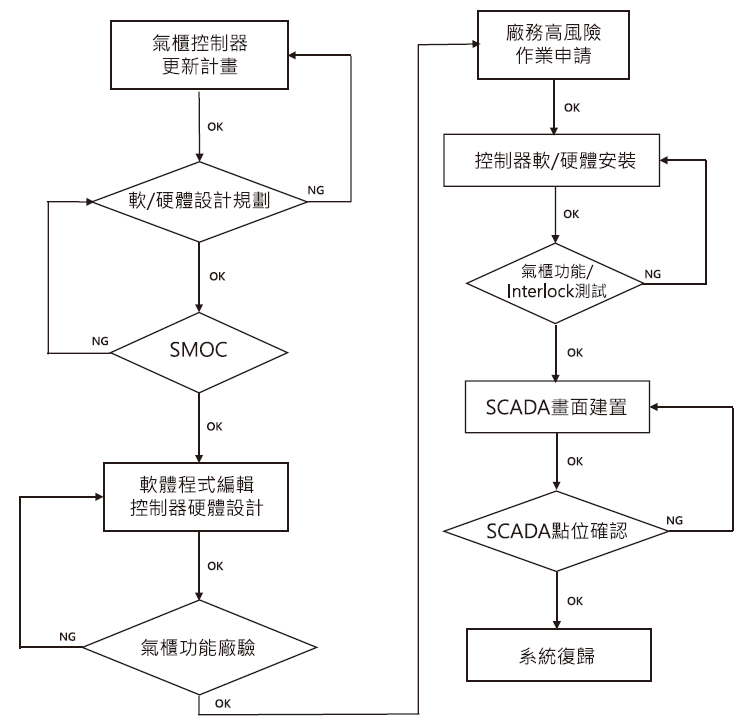
3.2.2 Chemical供應系統
目前六廠化學品供應系統控制器主要使用微處理器設計模式,且訊號傳遞採取Arcnet通訊模式,與台積目前新工處設計之化學供應系統架構不同。因人力物力等風險考量,無法同一時間修改所有化學品供應機台,故利用風險性以及用量大小評估綜合風險(表5),排定各化學品供應機台更換順序。同步改善舊有之強供系統,將原本複雜之強供方式,改良成「一鍵強供」使強供方式更方便、快速、可靠。
化學供應系統控制器更新 | |||
---|---|---|---|
化學品名稱 | 風險性(1-5) | 用量大小(1-5) | 綜合風險 |
Dev-1 | 5 | 5 | 25 |
Dev-2 | 3 | 2 | 6 |
Thinner-1 | 5 | 4 | 20 |
Thinner-2 | 3 | 2 | 6 |
HCl | 3 | 3 | 9 |
H2O2 | 4 | 4 | 16 |
H2SO4 | 4 | 4 | 16 |
NH4OH | 5 | 4 | 20 |
化學品供應系統更新,首重通訊方式。由原本Arcnet通訊模式轉變為目前普遍之通訊模式Controlnet/Ethernet,將建立Master Panel及New SCADA以Ethernet網域串聯溝通,再建立其ICP以Controlnet通訊方式連接(圖8),用以取代目前OCP。陸續持續規劃升級化學品供應機台之控制器(圖9),以達到化學品供應系統無痛升級之目的。
圖8、化學供應系統通訊架構圖
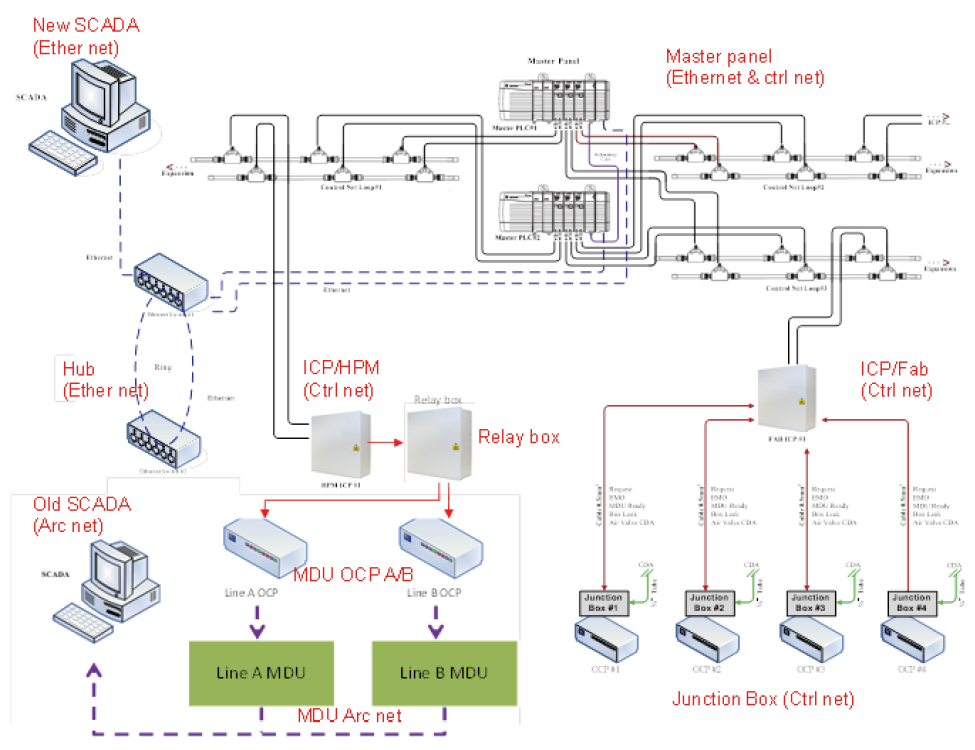
圖9、化學品供應系統更新流程圖
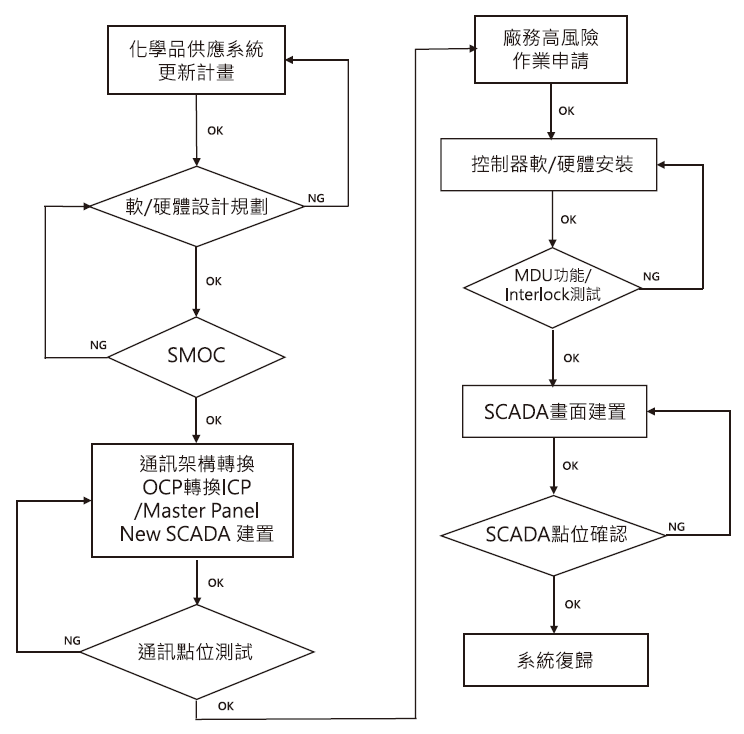
3.2.3 Slurry供應系統
目前六廠Slurry共有兩大供應系統,一是Maga Slurry供應系統、二是BOC Isis Slurry供應系統,目前Isis Slurry供應系統也面臨到供應廠商及零件短缺問題,但目前Isis供應系統硬體設計存在許多問題,如系統無法執行強供等。故如果只單純更新控制器將無法改善其Isis系統本身缺陷問題,最根本解決問題方式是將整體Isis系統汰除,故如何在轉換過程中,使線上影響降至最低將是最重要課題。
目前Isis系統共有5個Loop,其中4個Loop為供應K1730 Slurry共42台CMP機台,1個Loop為供應W8500 Slurry共20台CMP機台。為了達到供應不中斷目的,將提出兩種方案。方案一 : 移星換位法(圖10):採取轉一換一方式進行,即先將欲更換之Loop上之機台轉移至其他相同Slurry Loop供應使用,利用設備PM時轉移,可將機台停機時間縮短影響最少。至於供應W8500 Slurry Loop因為只有單一Loop使用故無法以移星換位方式進行。故提出方案二 : 物換星移法(圖11):因目前Maga Slurry供應系統中有一Loop目前沒再使用,故可將W8500 Slurry Loop轉移至此,即可解決更換SDS系統時無W8500 Slurry可供應之問題(圖12)。
圖10、BOC Isis K1730 Slurry機台切換示意圖
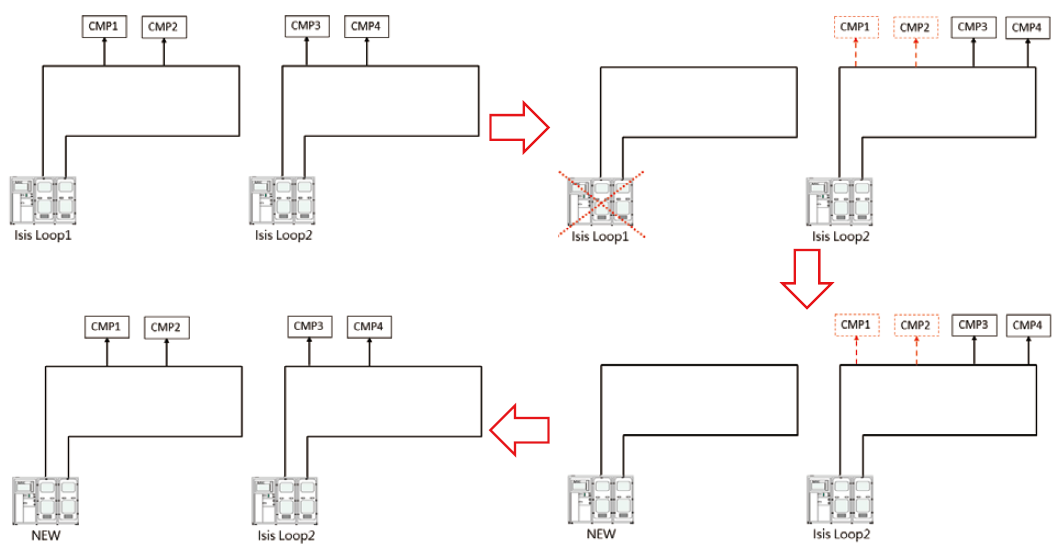
圖11、Isis W8500 Slurry機台切換示意圖
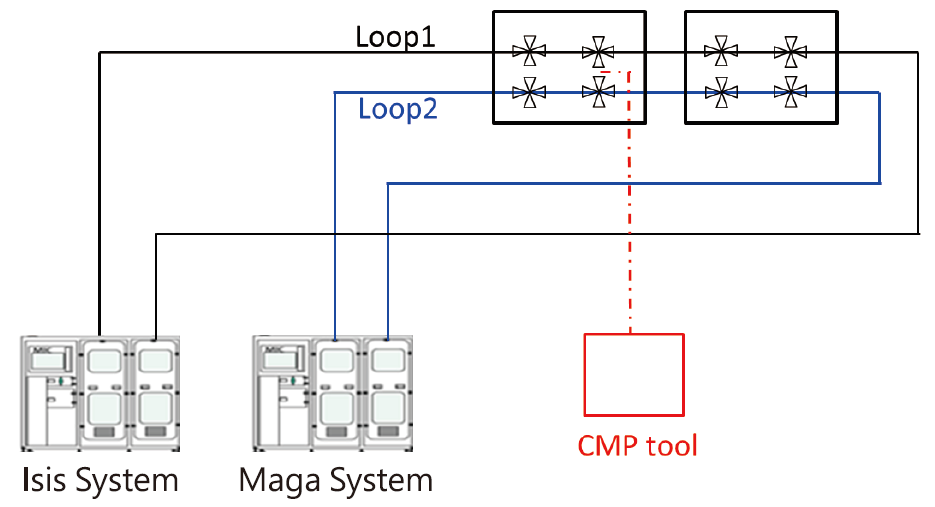
圖12、Slurry供應系統更新流程圖
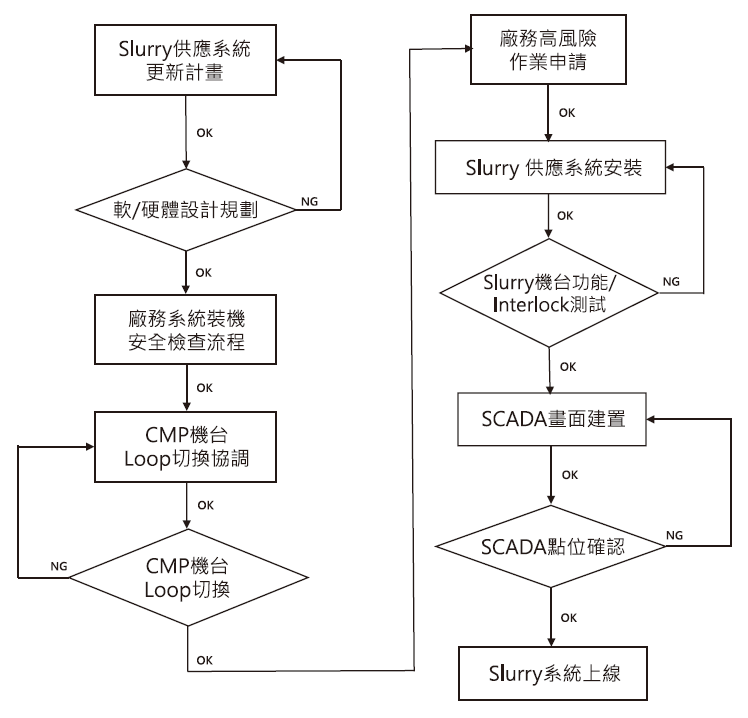
結果與分析
4.1 Special Gas供應系統
4.1.1 氣櫃製程氣體雙隔離閥
目前針對六廠需要改善之氣櫃共101櫃,目前78櫃已完成修改(圖13~圖14),陸續依照規劃預計於2023年全部修改完成。截至目前為止已成功有效預防因製程氣體隔離閥內漏進而污染製程氣體事件共三件,成功守護供應氣體之品質安全,減少線上產品報廢危機。
圖13、三福GG500氣櫃畫面前後對照圖
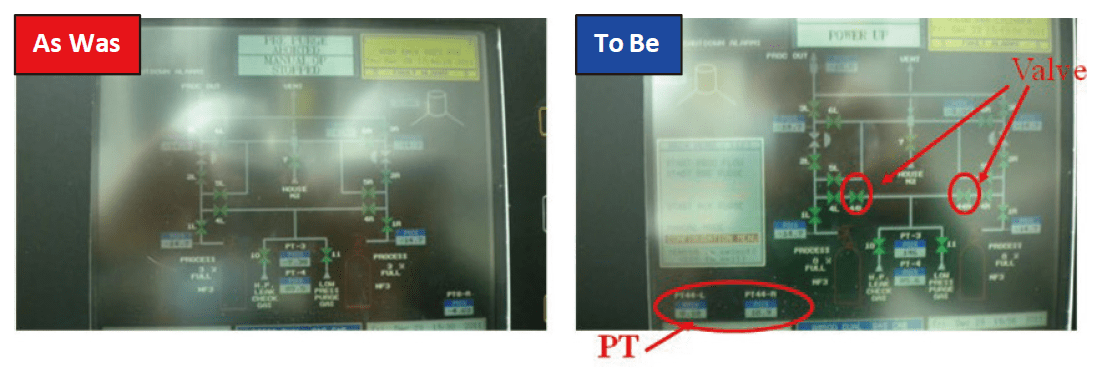
圖14、三福GG500氣櫃管路修改前後對照圖
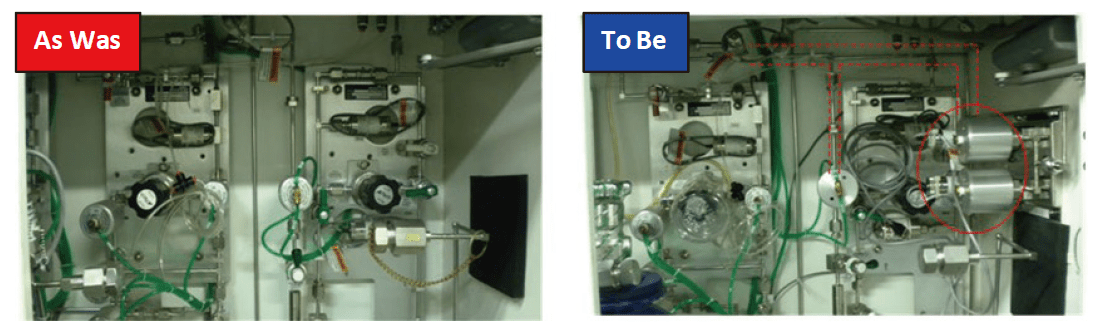
4.1.2 氣櫃強供模組
改善前之強制供應氣體系統因需要將各別氣動閥之氣源軟管執行拔插動作,故其程序較為複雜,經由TGM人員實際操作下需耗時3分鐘,一旦發生嚴重之中斷供應氣體事件將無法在短時間內有效提供應有的氣體至現場設備機台端。而使用改善後之氣櫃強供模組所需時間不需3秒鐘。確實能夠有效將時間縮短為原先之60分之一,減少設備機台斷氣危機,提高危機時的反應能力,也可以有效的減少人在緊張的環境時所發生的人為操作失誤現象,提高啟動強制供應氣體系統效率(圖15)。至今確實已經數次成功搶救突發性氣櫃供應中斷之問題。
圖15、強供模組修改前後對照圖
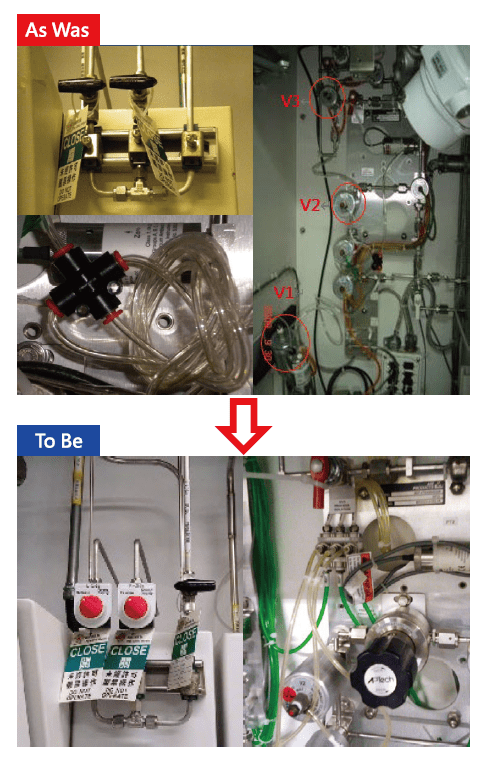
4.1.3 氣櫃控制器更新
六廠三福GG500型的氣櫃共有101櫃,控制器皆為微處理器模式,目前已完成25台氣櫃控制器升級(圖16),並將原有控制器零件做為備品,以備不時之需,並陸續規劃往後氣櫃控制器更新作業。更換下來之控制器零件,除了解決六廠舊有氣櫃控制器零件問題外,還曾幫忙協助F2&5廠氣櫃控制器零件短缺問題。
圖16、氣櫃控制器更新前後對照圖
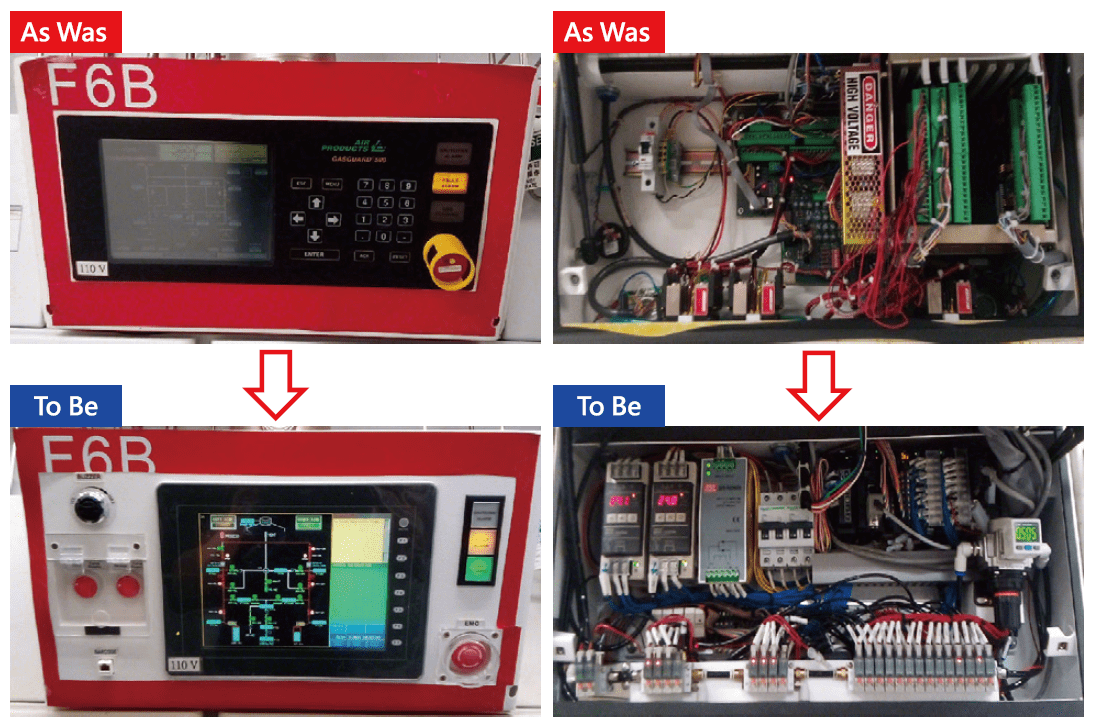
4.2 Chemical供應系統
4.2.1 通訊系統轉換
化學品供應系統將建立新通訊架構取代原本通訊模式,建立Master Panel以及ICP取代原本OCP,並建立New SCADA取代原本SCADA。目前Master Panel及New SCADA已建立完成,ICP取代OCP已完成96%(圖17)。
圖17、化學品通訊架構更新圖
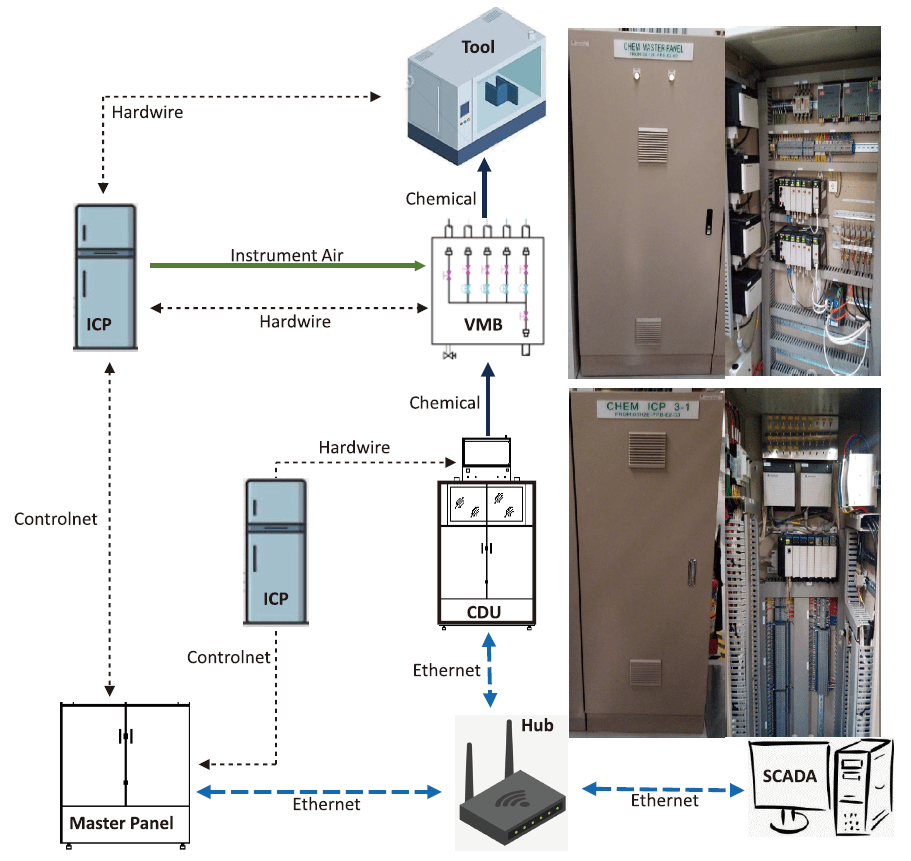
4.2.2 MDU控制器更新
目前六廠MDU控制器為微處理器模式共有42台,目前已完成10台MDU控制器升級(圖18),並將原有控制器零件做為備品,以備不時之需,並陸續規劃往後MDU控制器更新作業。
圖18、MDU控制器更新前後對照圖
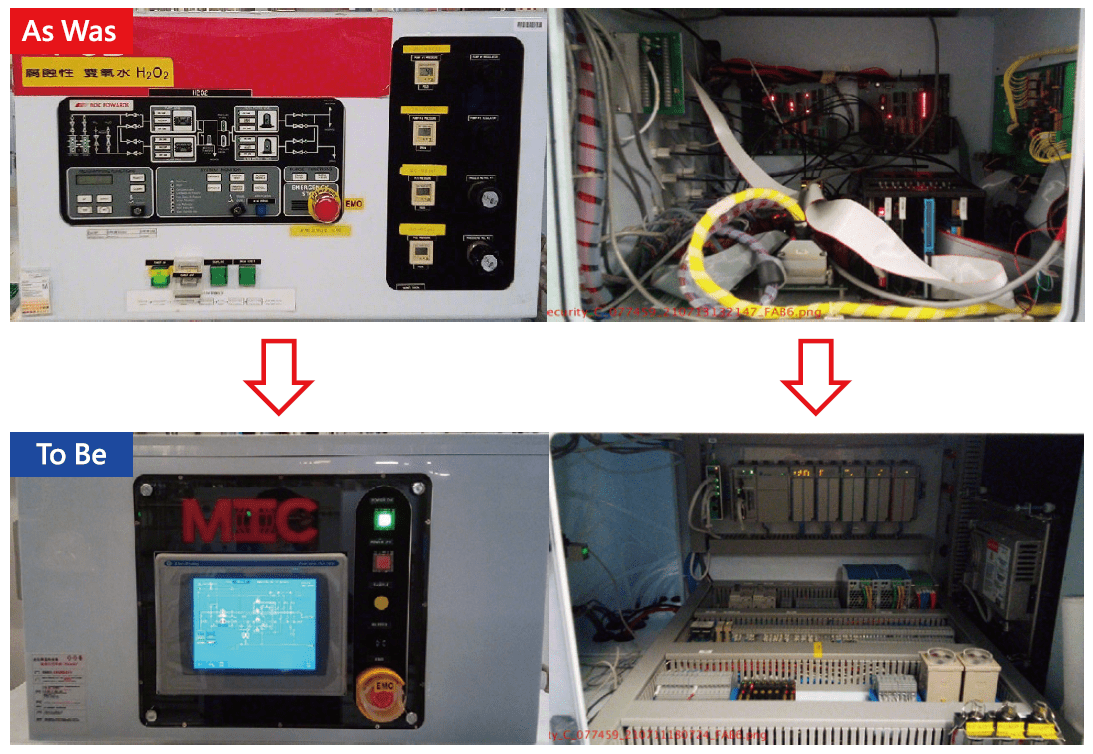
4.2.3 MDU一鍵強供
目前MDU執行強供時,必須緊急額外拉設電源,並外掛定時計數器,且強供供應路電磁閥鍵,故其程序複雜,經由TCM人員實際操作下需耗時超過5分鐘,一旦發生嚴重之中斷MDU供應事件,絕對無法在時間內有效提供應化學品至設備機台端。而使用改善後之一鍵強供模組所需時間不需5秒鐘。確實能夠有效將時間縮短為原先之60分之一,減少設備機台斷酸危機,提高危機時的反應能力,也可以有效的減少人在緊張的環境時所發生的人為操作失誤現象,提高啟動化學品供酸系統強供效率(圖19)。
圖19、MDU強供器修改前後對照圖

4.3 Slurry供應系統
六廠與新工處及廠商共同合作,改良開發新Slurry供應系統,為結合新工處Slurry供應系統優點,以及符合六廠Slurry供應需求進而設計出新產品。六廠Slurry Isis供應系統目前共有五套,已完成更新一套,目前上線使用功能測試穩定度皆正常。並陸續規劃往後Slurry供應系統更新作業。
新SDS架構主要可分為Drum Unit、Buffer Tank、Mixing Unit、Supply Unit四大部份。Drum Unit主要用為更換Slurry桶酸、自體循環以及補充Slurry至Buffer Tank。Buffer Tank為Drum Unit以及Mixing Unit之間的緩衝站,主要功能為提供Mixing Unit混酸所需的Slurry來源,並具備自體循環功能,避免Slurry之間顆粒沉澱。Mixing Unit則是利用Beaker體積比的方式來執行混酸作業,加入一定比例之Slurry原液以及DI Water後,經由Pump執行循環動作,以達到充分混和,在經由分析儀器確認導電度、pH值及比重於正常範圍內,才能輸送至下一站Supply Unit。Supply Unit除了具備自體循環功能外,最重要的是能將合乎規格之Slurry傳送至線上機台端。Supply Unit供應動力主要為兩顆串聯之磁浮式Pump,藉由雙磁浮式Pump以維持供應線上穩定平順之壓力(圖20)。
圖20、新Slurry供應系統比較圖
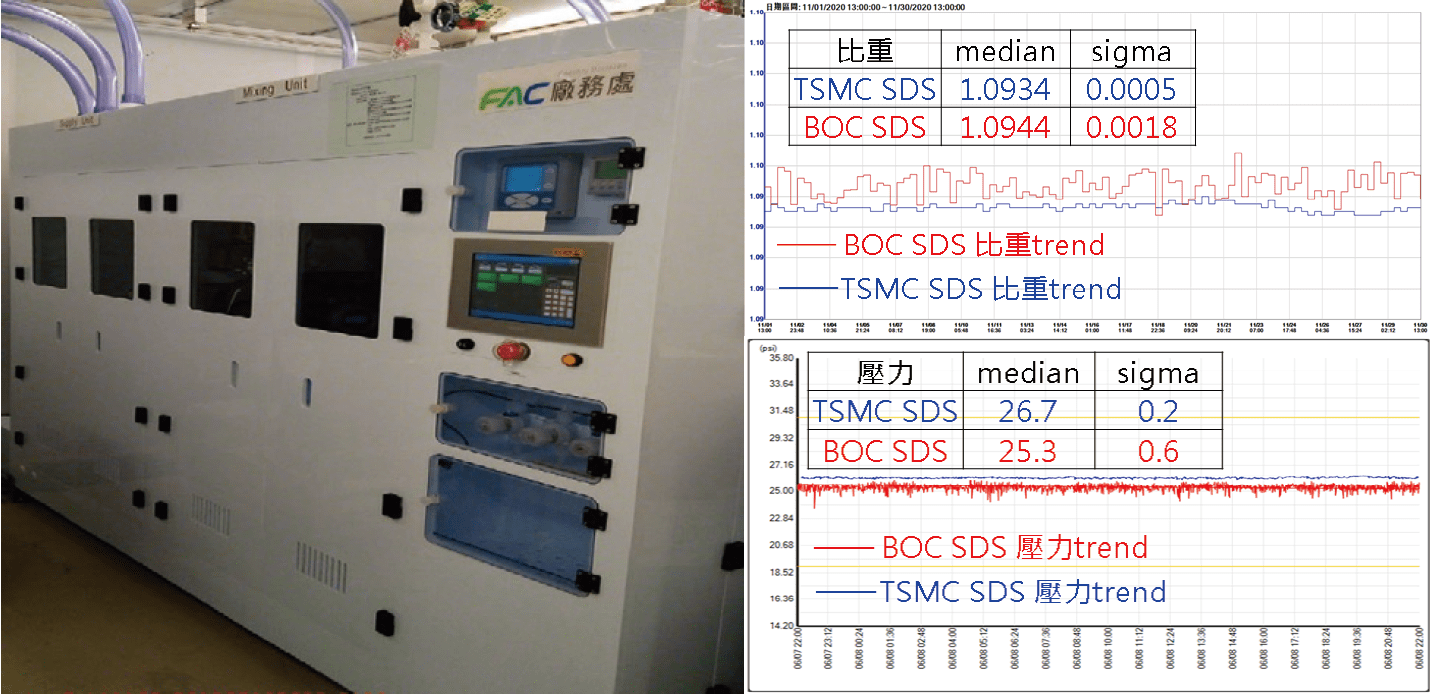
結論
舊有科技廠房經過時代變遷、系統功能演進,造成多項系統已不適合目前供應需求。如何規劃舊有系統與新系統相互共存便是一重要課題。舊有廠房每一個廠房空間設計皆不一樣,且後續擴充系統架構也不同。故如何的有效應用空間、維持舊有系統穩定度以及擷取他廠系統優點,且延續老舊供應系統原有壽命週期等,將是值得好好關注之問題。因每一廠原先設計理念以及供應系統廠商皆不同,故無法以同一方法如法炮製,但最重要的精神概念皆不變。致使運轉20年以上廠區期許能夠再持續運轉下一個20年。
參考文獻
- 特氣系統初階概論_Ver1.4,台積廠務學院,2020。
- Air liquid FABSTREAM III user manual.
- Chemical系統基礎概論_Ver2,台積廠務學院,2021。
- Slurry系統基礎概論_Ver2,台積廠務學院,2021。
留言(0)