摘要
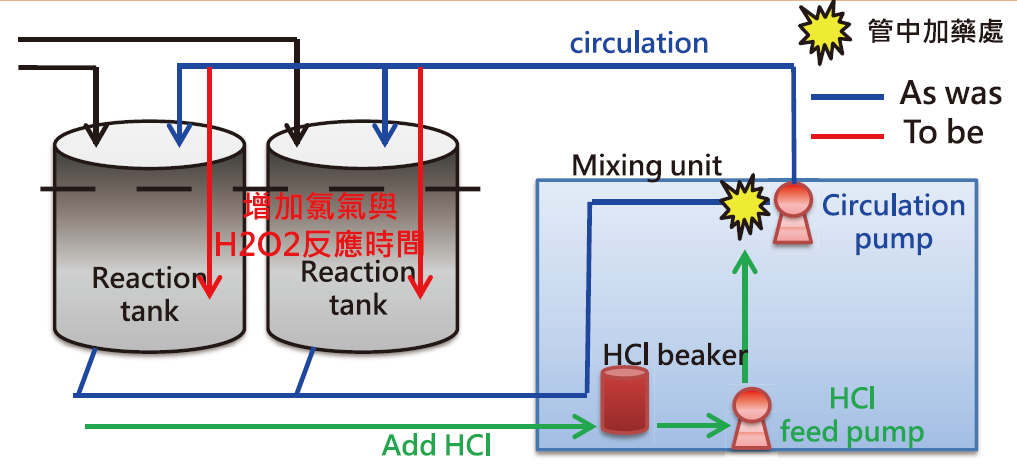
廢硫酸去除雙氧水系統最佳化探討
Keywords / Waste Sulfuric Acid3,Hydrogen Peroxide7,Optimization3,Reaction parameters,system design
本文以「最佳化探討」(Optimization)廢硫酸去除雙氧水系統,針對廢硫酸(W-H2SO4)去除雙氧水(H2O2)回收系統反應參數進行最佳化探討。本系統反應參數主要包括:①鹽酸加藥流量;②反應溫度;③操作負壓;④反應液位。
除了探討反應參數,本文亦比較各廠的系統設計之間差異,包括桶槽形式、濕式洗滌塔形式與鹽酸加藥方式,並據以彙整提出廢硫酸去除雙氧水系統之系統最佳化設計及操作反應參數,以作為未來此系統規劃的參考。
This paper uses "Optimization" of the system to remove hydrogen peroxide from waste sulfuric acid, and discusses the optimal recovery system parameters for waste sulfide(W-H2SO4) removal of hydrogen peroxide(H2O2). The reaction parameters of this system mainly include : ①salt dosing flow rate;②reaction temperature;③operating negative pressure;④reaction liquid level.
In addition to the reaction parameters, this article also compares the differences between the system designs of various plants, including the tank type, the wet scrubber type and the salt dosing method, and the optimization design of the waste and waste purification hydrogen peroxide system is proposed based on the collection. And operating response parameters, as a reference for future system planning.
1. 前言
廢硫酸主要用於光阻去除後之矽晶圓清洗,清洗後產生約45%~70%的廢硫酸,過去廢硫酸的處理方式為委由廢硫酸處理廠商清運,或提供給廠務相關系統使用,但由於廢硫酸中含有雙氧水成分,而雙氧水對廢水處理系統常用的逆滲透(RO)薄膜會造成損壞,使其Life time快速下降,更會導致氨氮廢液去除系統所使用的薄膜蒸餾過濾(MD)氧化性破壞,使其無法有效去除氨氮 ,因此過去僅少量廢硫酸使用於廠務廠內鹼排洗滌塔(AEX)之中和藥劑,其餘都委託廠商回收再利用。
本公司於民國104年成功導入廢硫酸再生系統,將雙氧水濃度降低至<0.005%,並於民國105年起全面應用於各廠區,使廢硫酸得以在廠內與氨氮廢液結合循環使用,將原有需中和的氨氮廢水轉為可用的資源—硫酸銨,除了降低廢硫酸委外處理量,同時也減少了工業級硫酸的外購量。
台積電廠務部水處理課廢硫酸去除雙氧水系統主要是藉由加入鹽酸作為催化劑,去除廢硫酸中的雙氧水,反應生成氯氣、氧氣與水。由於各廠所使用反應參數皆為該廠建廠試車漸漸演進而來,建廠系統設計及運轉反應參數不同,可能造成批次反應時間拉長,進而影響系統供酸,甚至可能導致系統反應槽、風管與濕式洗滌塔損壞。
本文主要使用最佳化手法及收集各廠區運轉經驗探討廢硫酸去除雙氧水系統反應參數,並比較各廠系統設計,據以彙整提出此系統之系統最佳化反應參數及系統設計,作為未來此系統規劃的參考。
2. 文獻探討
2.1 廢硫酸來源與成因
晶圓清洗製程廢水及處理方法簡介晶圓清洗的目的,是以整個批次(batch type)或單晶片式(single wafer type)系統,藉由化學品的浸泡或噴灑來去除髒污,並用超純水來洗濯雜質,主要是清除晶片表面所有的污染物,以濕式清洗製程為例早期以如 表1的批式為主(每批25片),主要配合:
- APM(NH3/H2O2/UPW):主要進行晶片上顆粒去除(particle removal)
- HPM(HCL/H2O2/UPW):主要進行晶片上金屬離子及金屬氧化物去除(metal ion/oxide removal)
- SPM(H2SO4/H2O2/UPW):主要進行晶片上有機物去除(organics removal)
- HF Clean:主要進行晶片上二氧化矽去除(SiO2 removal)
- IPA Dry:主要進行晶片上水份去除(water removal)
Wafer |
APM |
QDR |
HPM |
QDR |
SPM |
QDR |
HF |
QDR |
IPA |
Wafer |
---|---|---|---|---|---|---|---|---|---|---|
Loading |
(NH3/H2O2/UPW) |
(quick Drum Rinse) |
(HCl/H2O2/UPW) |
(quick Drum Rinse) |
(H2SO4/H2O2/UPW) |
(quick Drum Rinse) |
Clean |
(quick Drum Rinse) |
dry |
unloading |
半導體業晶圓代工廠在晶圓製程中以高純度之硫酸清洗矽晶圓表面,主要用於光阻去除後之矽晶圓清洗,使用的硫酸添加了過氧化氫(H2O2),使其成為一強氧化劑,而將晶片中的有機物氧化分解為CO2和H2O,因此產生了廢硫酸。主成份廢硫酸的濃度大於70%;過氧化氫約4∼5%左右;其他主要為水份。
2.2 廢硫酸去除雙氧水方法探討與機制
傳統廢硫酸處理包括以下三種方法:①真空蒸餾法;②活性碳催化法;③加HCl催化法,各方法說明及優缺點比較彙整如 表2。
項次 |
處理方法 |
方法說明 |
特色說明 |
---|---|---|---|
1 |
真空蒸餾法[3] |
利用常壓蒸餾方式,將廢硫酸溶液加熱至沸點以上,以去除水分與雜質 |
優點 : 常壓操作,無操作上之安全顧慮,廢硫酸回收率可達95%以上 缺點 : 耗能 |
2 |
活性碳催化法[4] |
粒狀活性碳作為雙氧水催化劑, 以催化機制將其分解為水及氧 |
優點 : 安全性高,不需添加HCl等化學品,亦不會有氯氣等副產品 缺點 : 處理成本較高 |
3 |
加HCl催化法 |
加入HCl作為催化劑,將雙氧水分解為氧氣及氯氣 |
優點 : 處理成本低 缺點 : 反應過程產生有毒氯氣,有工安問題 |
2.2.1 真空蒸餾法[1]
真空蒸餾法流程如圖1所示,利用常壓蒸餾方式,將廢硫酸溶液加熱至340℃(硫酸之沸點),以去除水分與雜質,回收硫酸溶液經冷凝收集與成分調整後,可回送至製程使用。廢硫酸之回收率可達95%以上,回收液之硫酸濃度可高達97%以上。
由於此方法需將硫酸加熱至340℃,是非常耗費能源,不管是使用電產熱或是燃燒產熱,都必須使用大量能源才能分離廢硫酸中的雙氧水。
圖1、真空蒸餾法流程圖
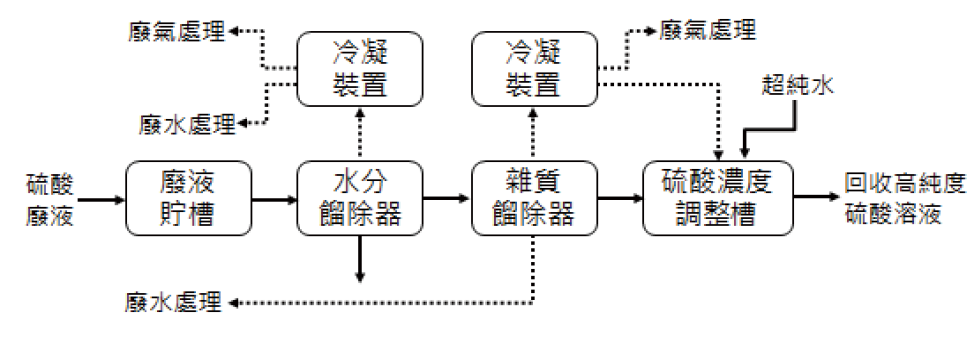
2.2.2 活性碳催化法[2]
以活性碳進行H2O2催化的機制包含直接催化(direct catalysis)及間接催化(indirectcatalysis)分別說明如下 :
- 直接催化(direct catalysis) : 活性碳表面的氫氧根離子會與離子態的雙氧水(HO2-)進行交換進而產生過氧化自由基,此自由基會再與雙氧水反應進而產生氧氣並進一步再生活性碳表面活性位置。
[M-O]OH+H2O2 → [M-O]OH H2O2
[M-O]OH H2O2 → [M-O]+HO2-+H2O
- 間接催化(indirect catalysis) : H2O2在活性碳間接催化下產生OH‧及HO2‧自由基,進行後續反應。
AC+H2O2 → AC++OH-+OH-
AC++H2O2 → AC+H++HO2-
2.2.3 鹽酸催化法
以HCl為催化劑,與廢硫酸中的雙氧水反應生成氯氣、氧氣、水。
H2O2+HCl → H2O+HOCl
HOCl+HCl ↔ H2O+Cl2
HOCl+H2O2 → H2O+HCl+O2
H2O2+Cl2 → 2HCl+O2
總反應:2H2O2 → O2+2H2O(HCl為催化劑)
鹽酸催化法雖不必耗用大量能源,但因反應過程會釋出大量有毒氯氣,考量環境工安問題,使其在推廣應用上受到一些限制。
如果將整個反應系統隔間架設完善與環境抽風排氣維持一定壓力,將能排除氯氣洩漏造成人員誤吸入造成健康危害的風險。
2.3 廢硫酸去除雙氧水系統介紹
F14P34廢硫酸去除雙氧水回收系統的流程如 圖2所示,廢硫酸收集至暫存槽後,經由輸送泵浦傳送至硫酸反應器槽與鹽酸HCl進行反應,廢硫酸在系中持續循環反應,當雙氧水濃度降至50ppm,經熱交換器進行降溫後,完成去雙氧水程序。而循環反應過程中產生的廢氣,會經由洗滌塔(Local Scrubber)洗滌後排放至中央廢氣洗滌塔(Central Scrubber)處理後,排放至大氣。
目前廠內廢硫酸回收系統主要分為兩家系統設計廠商,分別為信紘與兆聯,兩者廠商設計有不同之處,下列為系統設計與反應參數介紹與對於廢硫酸去除雙氧水的影響,分別有:①桶槽形式;②鹽酸加藥形式;③鹽酸加藥體積;④反應溫度;⑤操作負壓;⑥反應液位。針對這些參數,後續第三章研究方法會進行探討,並建議系統設計與最佳化參數。
圖2、廢硫酸去除雙氧水系統流程圖
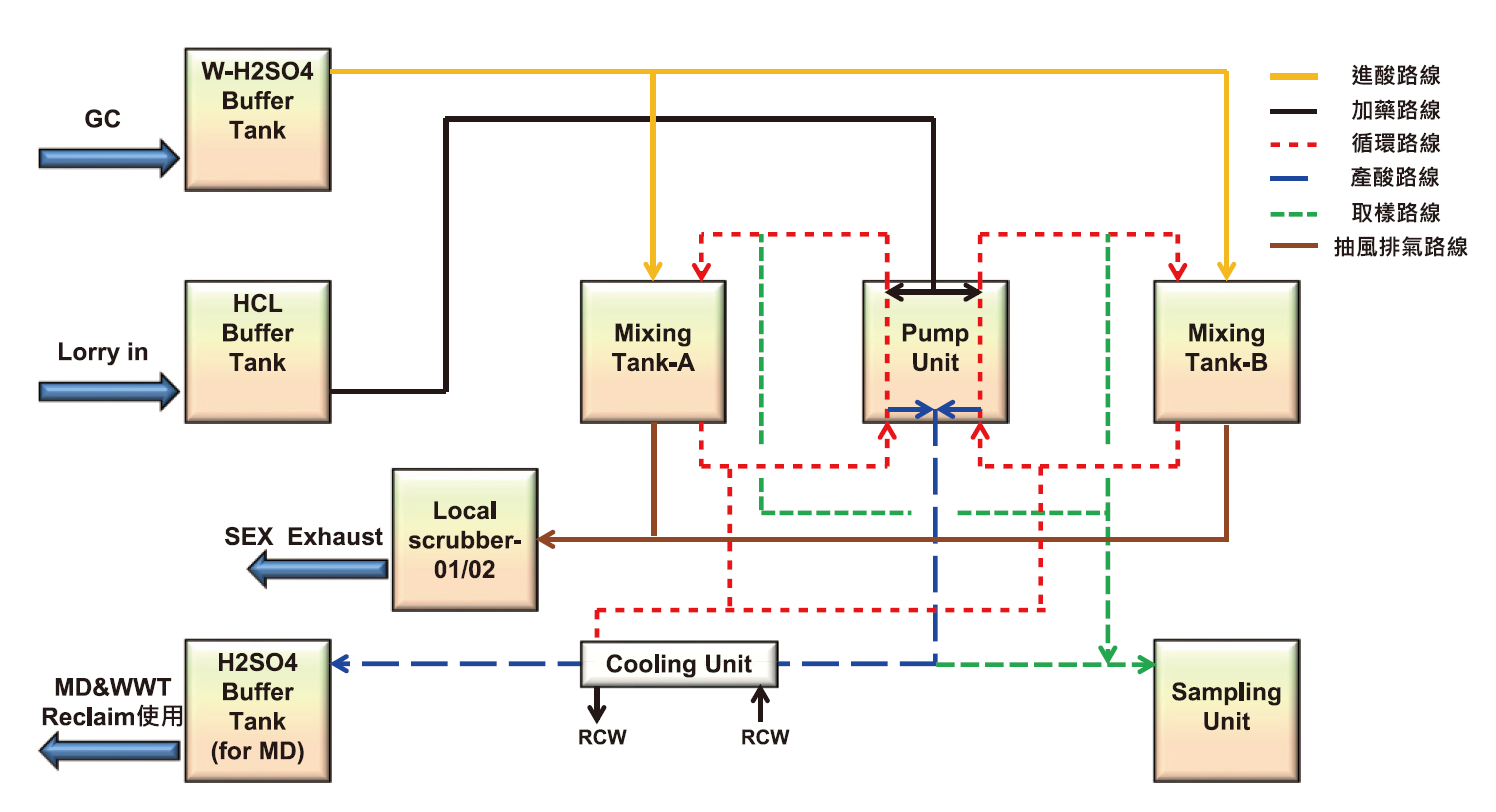
- 進酸路線(補酸):補新一批廢硫酸至硫酸反應槽內
- 循環路線(降溫):當產酸後槽內溫度過高時,預防處理新一批廢硫酸後溫度過高,廢硫酸會經過熱交換器進行降溫
- 取樣路線(量測與加藥):內循環並測量H2O2濃度,及計算出需添加之HCl量,做去除H2O2處理
- 產酸路線(產酸並降溫):處理完後經熱交換器降溫後產酸
3. 研究方法
3.1 研究架構
本研究對於廢硫酸去除雙氧水系統最佳化探討,區分為系統設計與反應參數兩部分,其中系統設計分為 : ①桶槽形式,②濕式洗滌塔形式,③鹽酸加藥形式,④鹽酸加藥體積;而反應參數則分為 : ①反應溫度,②操作負壓,③反應液位。評估上述系統設計與反應參數對於廢硫酸去除雙氧水系統影響與最佳化探討,以作為未來新廠規劃此系統與各廠系統運轉反應參數參考依據。
3.1.1 桶槽形式
廠商原始設計廢硫酸去除雙氧水系統反應桶槽形式分為兩種,分別為直立式與臥式如 圖3,將比較直立式與臥式桶槽內裝同樣八分滿體積其受力面積的差異。
圖3、廢硫酸去除雙氧水系統反應桶槽形式
⒜臥式 ⒝直立式
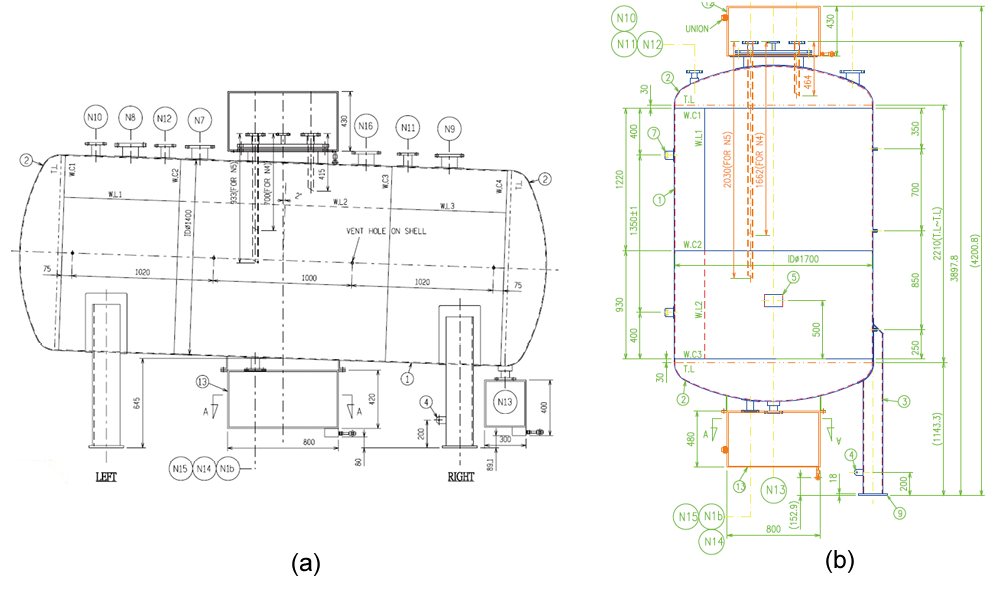
假設直立式與臥式桶槽皆為5L桶槽且內裝同樣含八分滿體積,計算受力表面積如下 :
直立式桶槽受力表面積:4.5m2
臥式桶槽受力表面積:10.27m2
結果顯示臥式桶槽受力表面積為立式2.3倍,長期處於負壓狀態可能導致臥式桶槽內襯萎縮變形,使得系統無法正常運轉。
3.1.2 濕式洗滌塔形式
根據廠商原始設計廢硫酸去除雙氧水系統濕式洗滌塔形式分為兩種形式如 圖4所示,分別為台禹本體使用氯化聚氯乙烯(Chlorinated polyvinyl chloride, CPVC)材質的濕式洗滌塔與中昕、千附及晃誼本體採用玻璃纖維強化塑膠(fiber-reinforced plastic, FPR)材質的濕式洗滌塔,其中CPVC為聚氯乙烯(Polyvinyl Chloride, PVC)樹脂氯化生產的熱塑性塑料,FRP材質則為玻璃纖維及乙烯基酯樹脂所組成,其兩者設計處理量皆為1000CMH,且去除效率皆能達到95%的去除酸性氣體效果。
圖4、廢硫酸去除雙氧水系統濕式洗滌塔形式
⒜台禹CPVC材質濕式洗滌塔 ⒝中昕FRP材質濕式洗滌塔
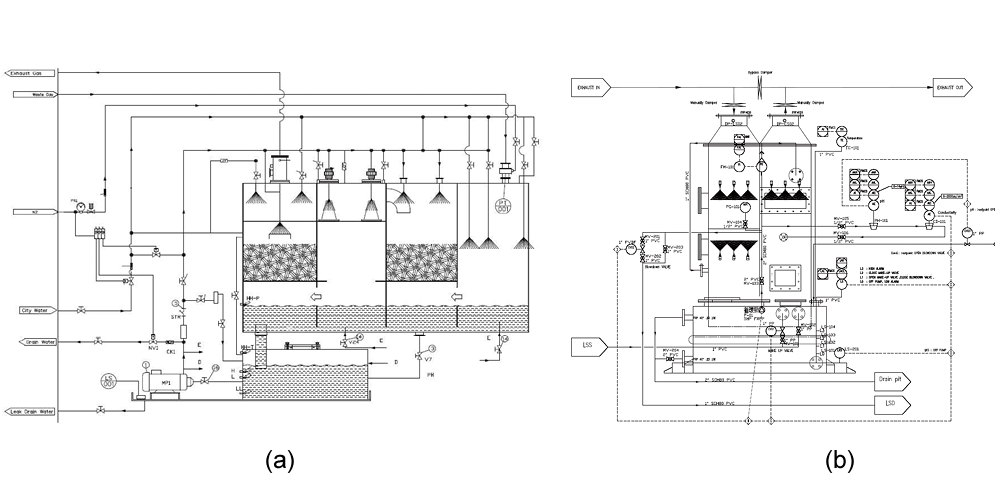
3.1.3 鹽酸加藥形式
廠商原始設計廢硫酸去除雙氧水系統鹽酸加藥形式分為兩種,分別為信紘所設計之循環管路管中加藥與兆聯所設計之管路直接加藥示意圖如 圖5,兩者明顯差異為信紘所設計鹽酸加藥形式為鹽酸循環管中加藥形式為桶槽上方噴灑至液面上方,而兆聯所設計鹽酸加藥形式則為鹽酸管路直接加藥形式則為桶槽液面之下加藥。
圖5、廢硫酸去除雙氧水系統鹽酸加藥形式
⒜信紘所設計鹽酸循環管中加藥模式
⒝兆聯所設計鹽酸管路直接加藥模式
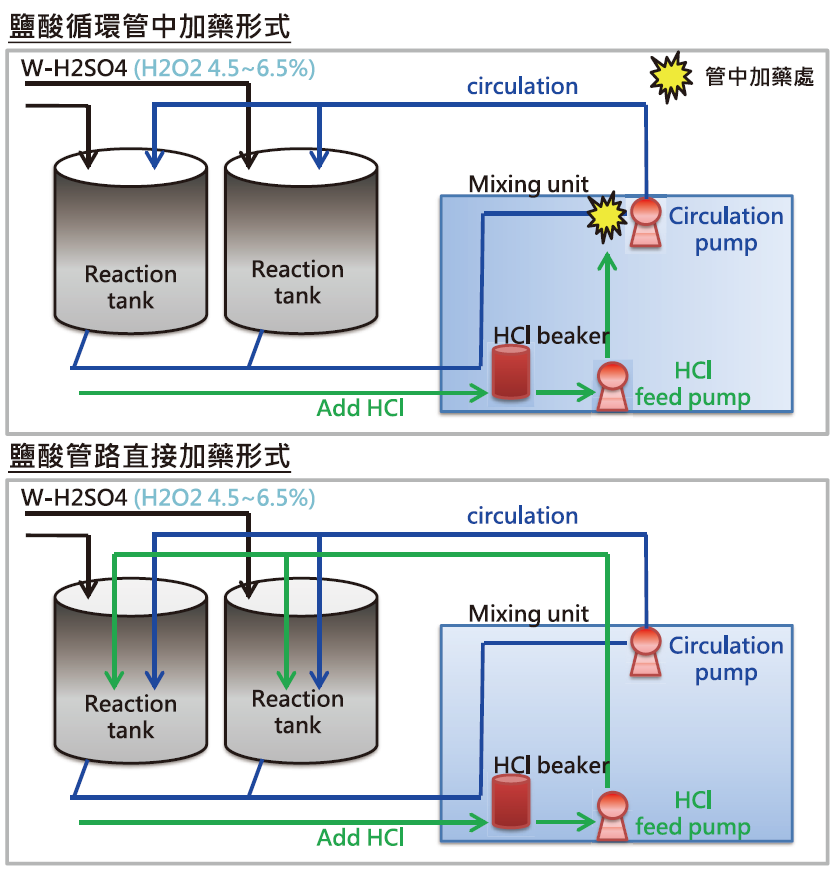
3.1.4 鹽酸加藥流量
廠商原始設計廢硫酸去除雙氧水系統鹽酸加藥流量分為三種,分別為1.0L/min、1.5L/min及2.0L/min,根據上述文獻探討中所提廢硫酸去除雙氧水鹽酸催化法,鹽酸催化法去除雙氧水反應速率方程式如 圖6所示,根據反應速率方程式找出影響反應速率的因素如下 :
- 廢硫酸去除雙氧水反應速率與雙氧水濃度成正比,即廢硫酸中含有越高濃度雙氧水有較高的反應速率:
- 反應速率常數k則受到反應溫度影響,反應溫度越高則k越大,反應速率也就越快。
- 鹽酸加藥流量與鹽酸加藥量皆會影響反應速率,兩者越高反應速率皆越快。
根據上述結果為鹽酸加藥流量控制在2.0L/min,能使廢硫酸去除雙氧水反應速率達到最快,反應時間縮短。
圖6、鹽酸催化法去除雙氧水反應速率方程式
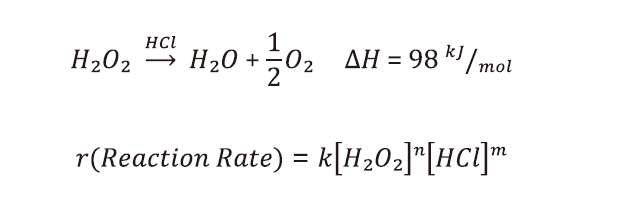
3.1.5 反應溫度
廠商原始設計廢硫酸去除雙氧水系統鹽酸操作反應溫度建議至少80°C以上,根據上述所提廢硫酸去除雙氧水鹽酸催化法反應速率方程式,理論上反應溫度越高使得反應常數k越大,使得廢硫酸去除雙氧水反應速率也就更快。
3.1.6 操作負壓
廠商原始設計廢硫酸去除雙氧水系統操作負壓600PA以下,依照各廠實際試車運轉情形作調整,操作負壓需將廢硫酸去除雙氧水反應過程中產氣給完全去除,根據下列計算求出操作負壓。
① 氯氣產生的計算基準:
HCl的添加量=每一批次H2O2/H2SO4添加總重量的0.6%的32%HCl。
添加32%HCl重量=4300Lx1.5kg/Lx0.6%=38.7kg。
其中所含的HCl=38.7kgx32%=12.38kg(HCl淨重)。
- 假設一 : 最終所加入的HCl總重有70%HCl在反應過程中轉化成Cl2,其餘的30%HCl則以氣體逸散進入Scrubber進行酸鹼中和,則可計算每批次產生Cl2總量如下 :
12.38kgx70%x35.4/36.4=8.43kg(Cl2)=8430g(Cl2)= 119.07mol(Cl2)。
119.07mol(Cl2)液體氣化成氣體體積=119.07molx22.4L/mol=2667L(Cl2)。
每批次4300L,6%H2O2/H2SO4分解產生O2的體積= 85.47m3。
H2O2 → H2O+1/2 O2 1mol H2O2產生0.5mol O2
4300Lx1.5x6%(H2O2)=387kg(H2O2)=387000g(H2O2)= 11382mol(H2O2)。
每批次產生O2體積=11382molx0.5x22.4L/mol= 127478L=127.48m3。
- 假設二 : 桶槽內主要的氣體成分組成為Cl2/O2
平均濃度=2.667m3/127.48m3=2.09%(Cl2/O2)
- 假設三 : 桶槽主要反應產生氣體時間為120分鐘(實際每批次反應時間為240分鐘,Scrubber處理量有考慮安全係數)
平均氣體流量=(2.667+127.48)/120=1.08m3/min= 64.8m3/hr
② 以操作負壓為100PA(=10.197Kgf/m2)計算風管抽氣流量基準:
風管截面積=πD²/4=(3.1415926/4)*0.1016M^2= 0.0081m2。
風管風速=(PT*2g/γ)^1/2=(10.197Kgf/m2*2*9.8M/s2) ^1/2=12.973m/s=46704.538m/hr。
風管抽氣流量=0.0081m3*46704.538m/hr=378.65m3/hr。
根據上述計算結果顯示負壓操作在100PA,就已經足夠將廢硫酸反應過程中所產出的氯氣與氧氣抽至Scrubber處理。
根據上述文獻指出氯氣能與雙氧水反應形成鹽酸,使得反應過程中不需添加過多鹽酸,但當操作負壓過大時,會將產生氯氣大部分透過抽風至洗滌塔洗滌,則需要加過多鹽酸來去除廢硫酸中的雙氧水。
3.1.7 反應液位
廠商原始設計廢硫酸去除雙氧水系統反應液位為反應桶槽8分滿液位,並將反應完硫酸皆排空至硫酸儲存桶槽,根據各廠實際運轉情形作調整,實際反應液位介於6~8分滿之間。
4. 結果與分析
本研究欲探討廢硫酸去除雙氧水系統設計與反應參數最佳化結果,比較各廠系統設計與反應參數如 表3所列,依據F14P34實廠運轉經驗與調整反應參數實廠測試作為參考依據。
表3、廢硫酸去除雙氧水系統各廠系統設計與反應參數
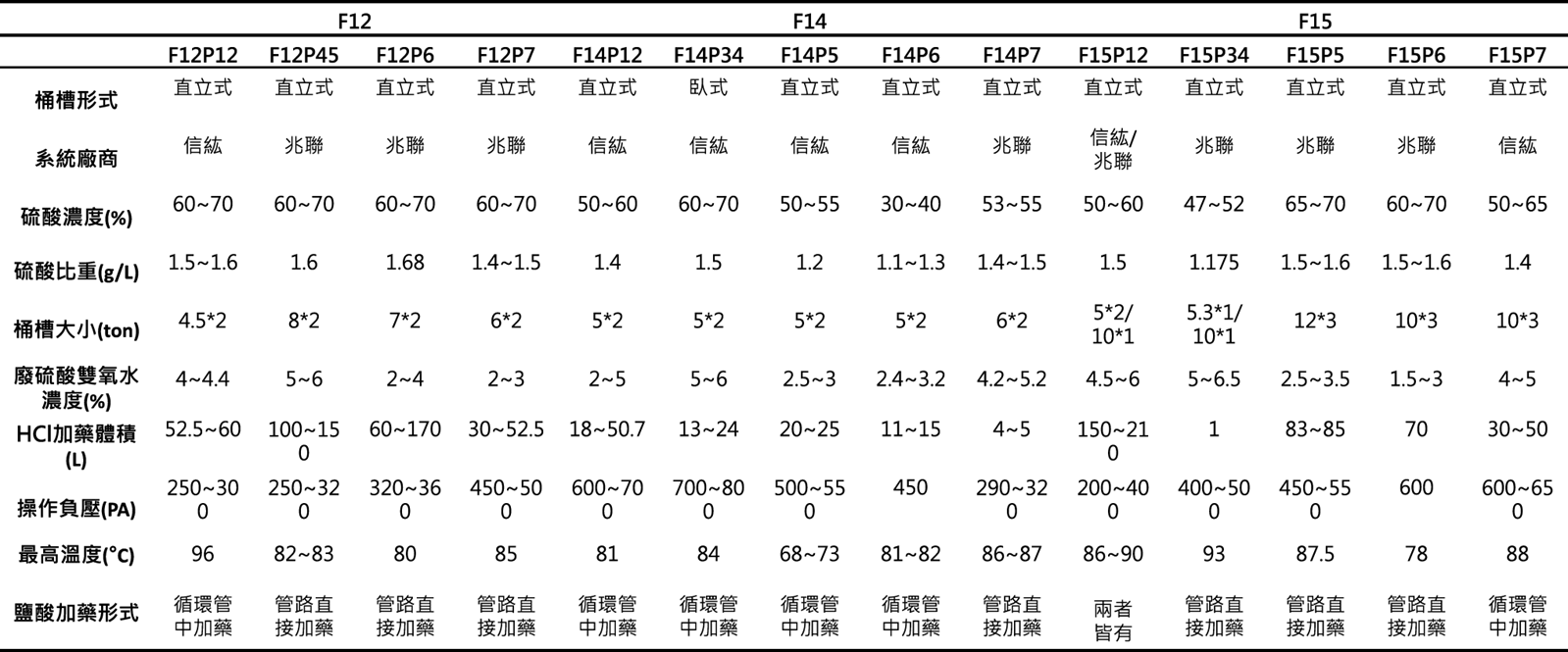
4.1 廢硫酸去除雙氧水系統設計最佳化結果
本研究利用廢硫酸去除雙氧水系統設計不同,透過比較信紘與兆聯兩者系統設計商所設計與實廠運轉經驗,來探討廢硫酸去除雙氧水系統設計最佳化結果。
4.1.1 桶槽形式對廢硫酸去除雙氧水探討
根據 表3所列,顯示兆聯所設計桶槽形式皆為直立式,而信紘所設計桶槽形式則可分為直立式與臥式兩種,依照3.1.1計算桶槽直立式與臥式同樣體積裝8分滿受力面積,根據計算結果顯示臥式桶槽受力表面積為直立式2.3倍。如同受力上述表面積計算結果,於實廠運轉經驗與各廠比較結果,臥式反應桶槽較直立式反應桶槽內襯損壞情形較為明顯,立式桶槽相較於臥式桶槽則能有較常使用壽命,因此建議未來規劃廢硫酸去除雙氧水系統使用直立式反應桶槽較為能有較長的使用年限。
4.1.2 濕式洗滌塔形式對廢硫酸去除雙氧水探討
根據調查各廠廢硫酸去除雙氧水系統濕式洗滌塔形式如 表4所示,各廠廢硫酸去除雙氧水系統大部分皆使用中昕、千附及晃誼本體為玻璃纖維強化塑膠(fiber-reinforced plastic, FPR)材質的濕式洗滌塔,其中有發現濕式洗滌塔的FRP decade與鹽酸加藥體積有關,兩者存在正相關,廢硫酸去除雙氧水系統所使用鹽酸體積越多顯示其濕式洗滌塔的FRP decade越嚴重。
表4、廢硫酸去除雙氧水系統各廠FRP材質濕式洗滌塔腐蝕狀況
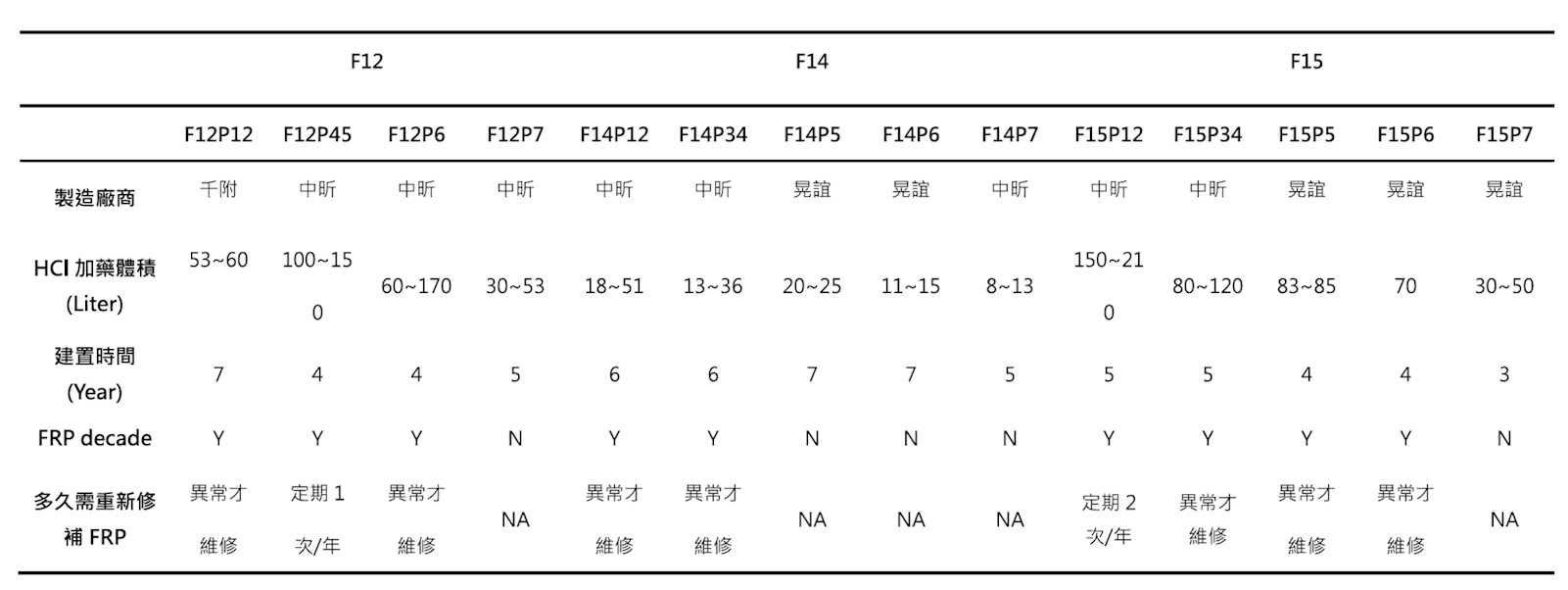
實廠比較案例為F14P34有兩種不同形式行濕式洗滌塔,分別為台禹氯化聚氯乙烯(Chlorinated polyvinyl chloride, CPVC)材質濕式洗滌塔及中昕玻璃纖維強化塑膠(fiber-reinforced plastic, FPR)材質濕式洗滌塔,發現中昕FRP材質濕式洗滌塔入口端本體有變薄與穿孔現象如 圖7所示,實際使用膜厚計量測兩種濕式洗滌塔,發現台禹CPVC材質濕式洗滌塔入口端及出口端本體厚度無太大差異如 圖8,顯示台禹CPVC材質濕式洗滌塔適用於廢硫酸去除雙氧水系統中的鹽酸催化法,而中昕FRP材質濕式洗滌塔則發現入口端與出口端本體厚度有明顯差異如 圖9所示,顯示中昕FRP材質濕式洗滌塔不適用於廢硫酸去除雙氧水系統中的鹽酸催化法。
圖7、FRP材質濕式洗滌塔本體變薄與穿孔示意圖
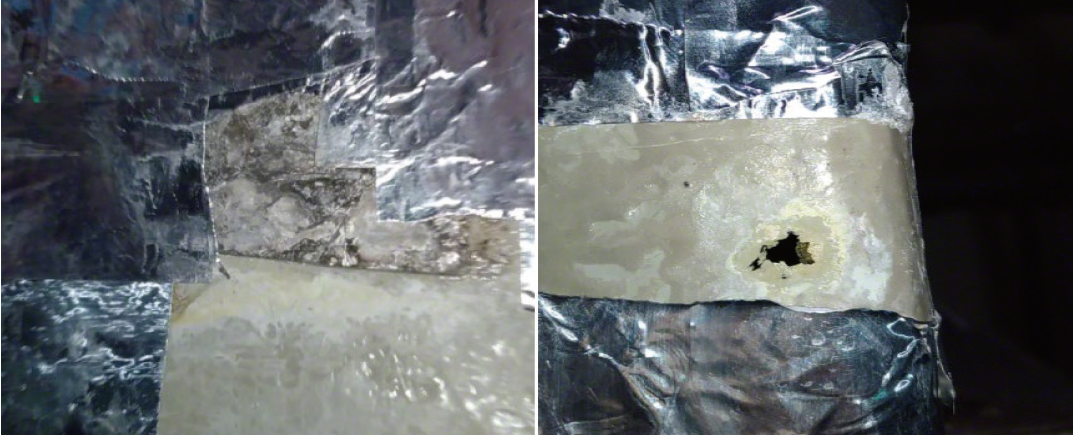
圖8、CPVC材質濕式洗滌塔厚度計量測示意圖
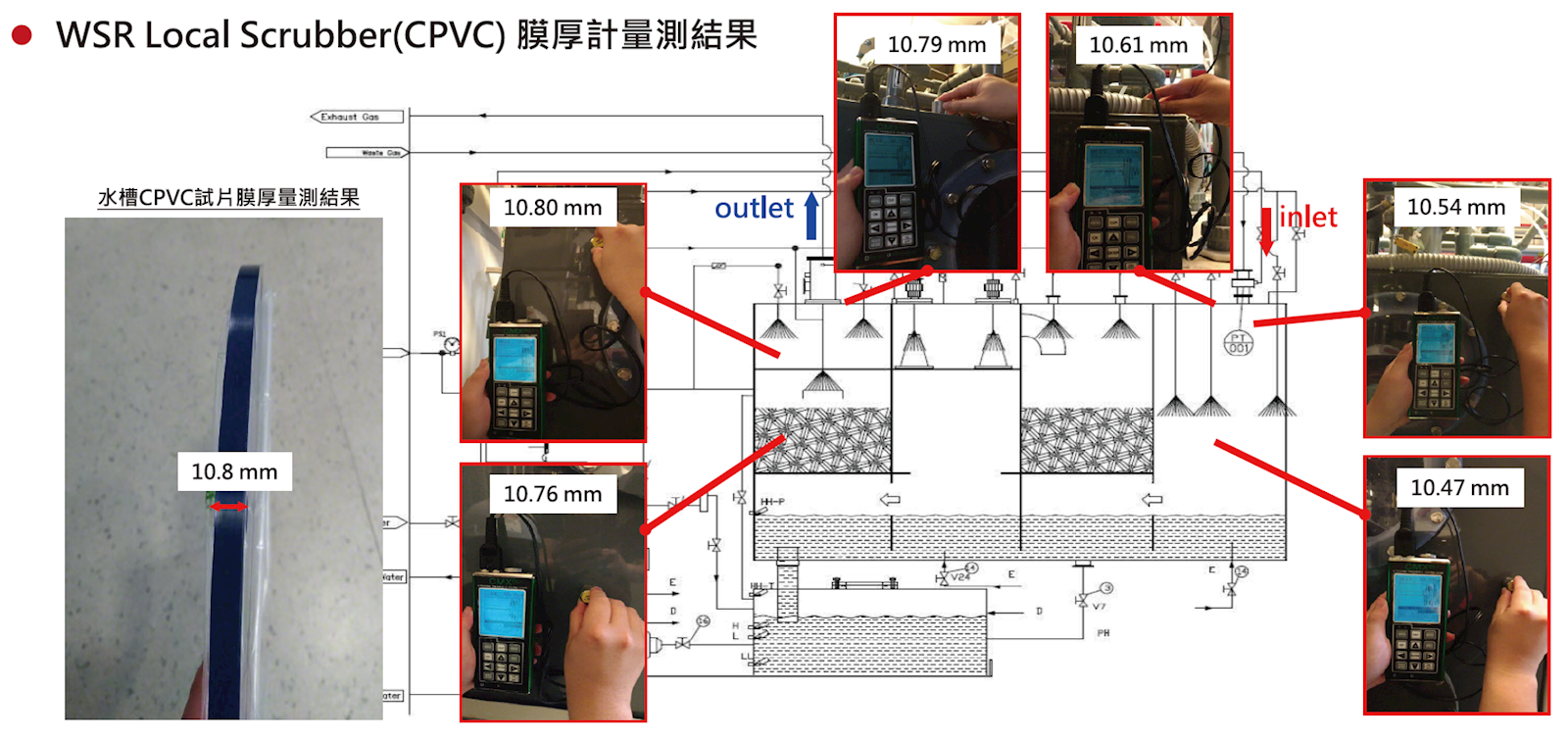
圖9、FRP材質濕式洗滌塔厚度計量測示意圖
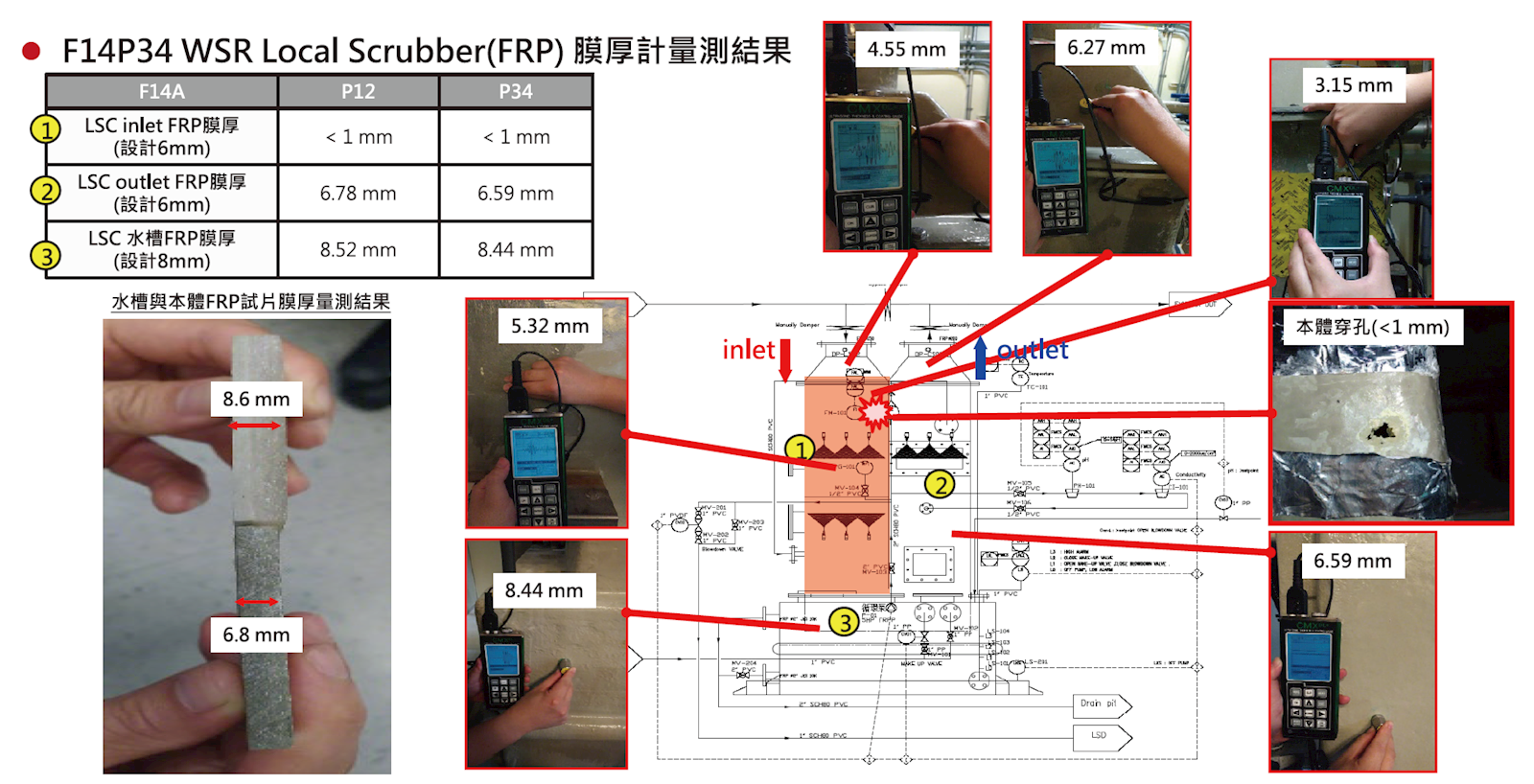
根據比較兩者材質其耐化性與耐溫性,FRP耐化性與戴溫性如 圖10所示,結果顯示FRP材質對於鹽酸和雙氧水兩種化學品耐溫性只能達到65度,CPVC則可耐溫至82度,由於廢硫酸去除雙氧水系統反應過程為放熱反應,根據調查各廠運轉反應溫度會達到80度以上,結果顯示確實FRP材質濕式洗滌塔無法應用於廢硫酸去除雙氧水系統中的鹽酸催化法。
圖10、FRP材質耐化性與耐溫性
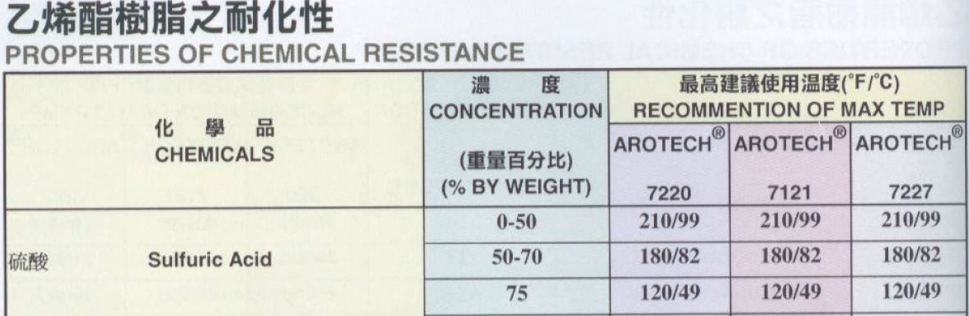
4.1.3 鹽酸加藥形式對廢硫酸去除雙氧水探討
根據 表3所列,顯示信紘所設計廢硫酸去除雙氧水系統主要是採用鹽酸循環管中加藥形式,兆聯所設計則採用鹽酸管路直接加藥形式。根據上述3.1.2所提到兩者差異為為鹽酸循環管中加藥形式為桶槽上方噴灑至液面上方,鹽酸管路直接加藥形式則為桶槽液面之下加藥,加上與各廠比較運轉實際情況,發現管路直接加藥較循環管中加藥所使用的鹽酸量較少,整體批次反應時間也較短,原因推論為循環管中加藥會使得鹽酸在管中與廢硫酸反應產生氯氣被風管負壓抽走,使得鹽酸加藥量增加,並導致批次反應時間拉長。
實廠改善案例為F14P34將鹽酸循環管中加藥管路延伸至桶槽液面之下如 圖11所示,批次反應時間縮短1小時與鹽酸加藥量減少20%,整體硫酸產量增加13%,因此建議未來規劃廢硫酸去除雙氧水系統使用鹽酸加藥模式將加藥管路延伸至液面之下,能使鹽酸與廢硫酸反應較為均勻,減少批次反應時間與鹽酸加藥量,並增加整體產酸量。
圖11、鹽酸循環管路延伸改管示意圖
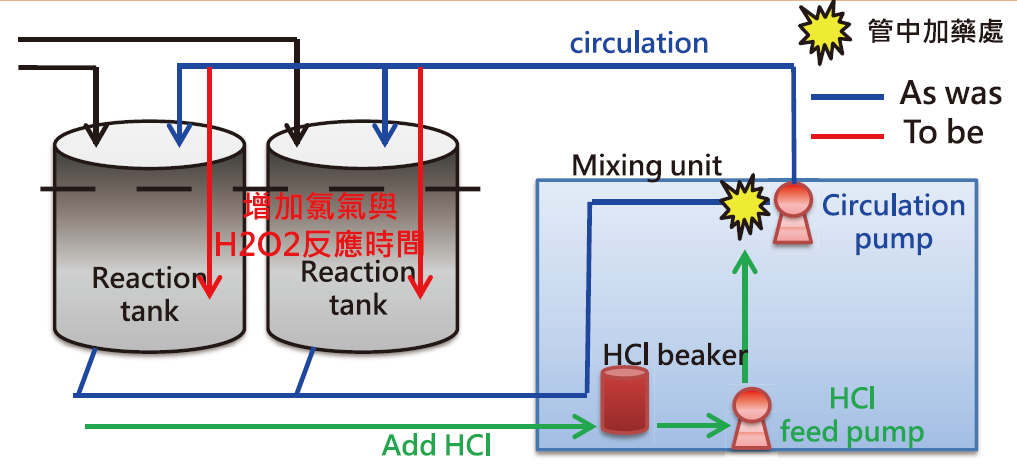
4.1.4 鹽酸加藥流量對廢硫酸去除雙氧水探討
上述3.1.3所提到鹽酸加藥流量分為1.0L/min、1.5L/min及2.0L/min三種模式,各廠目前所使用加藥流量皆為實廠系統試車所採用的鹽酸加藥量與鹽酸加藥體積如 表3所列,顯示各廠所鹽酸加藥量與鹽酸加藥體積皆有所不同。根據文獻探討反應式與反應速率方程式可得知鹽酸作為廢硫酸去除雙氧水反應中催化劑,當催化劑濃度越高整體反應速率將會越快,使用2.0L/min為鹽酸最佳加藥體積。
使用2.0L/min作為鹽酸加藥流量,前提是反應過程中瞬間產氣量要小於系統風管抽氣量,若瞬間產氣量大於系統風管抽氣量將會有氯氣洩漏的安全疑慮風險,取決於各廠實際運轉操作負壓、風管尺寸大小與洗滌塔去除效果。
4.2 廢硫酸去除雙氧水系統反應參數最佳化結果
本研究利用廢硫酸去除雙氧水系統操作反應參數不同,比較各廠實廠運轉經驗,來探討廢硫酸去除雙氧水系統反應參數最佳化結果。
4.2.1 反應溫度對廢硫酸去除雙氧水探討
根據 表3所列,顯示各廠所反應最高溫度有所不同,與各廠實際進熱交換器所設定溫度有所關聯,以F14P34為例,設定82°C進熱交換器溫度,實際最高溫度則會到達85°C左右,與初始雙氧水濃度、鹽酸加藥流量與加藥體積有關;根據模擬廢硫酸去除雙氧水反應實驗如 圖12所示,此實驗初始溫度控制在66°C與初始雙氧水濃度為1.946%,反應期間記錄鹽酸填加時間、加藥體積與雙氧水濃度,結果顯示反應溫度落在85°C為最佳反應溫度。
實廠改善案例為F14P34將近熱交換器反應溫度上修,使得原先最高溫為79度變成84度,批次反應時間所短,整體產酸量提高,因此建議各廠廢硫酸去除雙氧水系統操作反應溫度控制在85°C上下,能有效縮短批次反應時間,並增加整體產酸量。
圖12、模擬廢硫酸去除雙氧水反應過程曲線圖
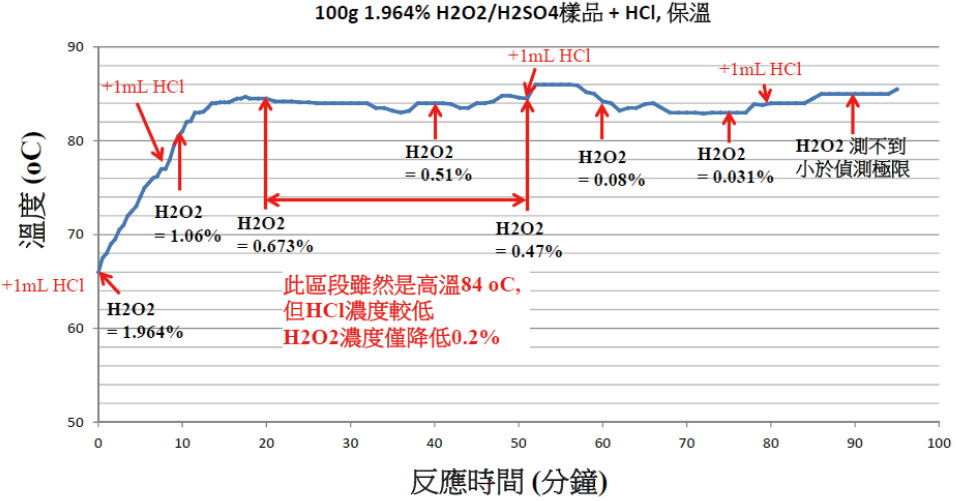
4.2.2 操作負壓對廢硫酸去除雙氧水探討
根據 表3所列,顯示各廠操作負壓有所不同,介於200~800PA不等,上述3.1.5所提到操作負壓所提到控制在100PA皆能將廢硫酸去除雙氧水系統反應所產生氯氣與氧氣氣體量給完全去除。
根據F14P34實廠運轉情況,當初因為氯氣洩漏風險將操作負壓提高,確發現操作負壓過大時將造成反應桶槽內襯損壞如 圖13所示,造成反應桶槽需出廠作桶槽重新修補內襯維修,比較各廠實際操作負壓,建議各廠操作負壓控制400~600PA,較不會有安全疑慮風險與桶槽受損疑慮,各廠因實廠運轉反應瞬間產氣量不同,有所操作負壓控制不同。
圖13、廢硫酸去除雙氧水系統反應槽內襯萎縮損壞示意圖
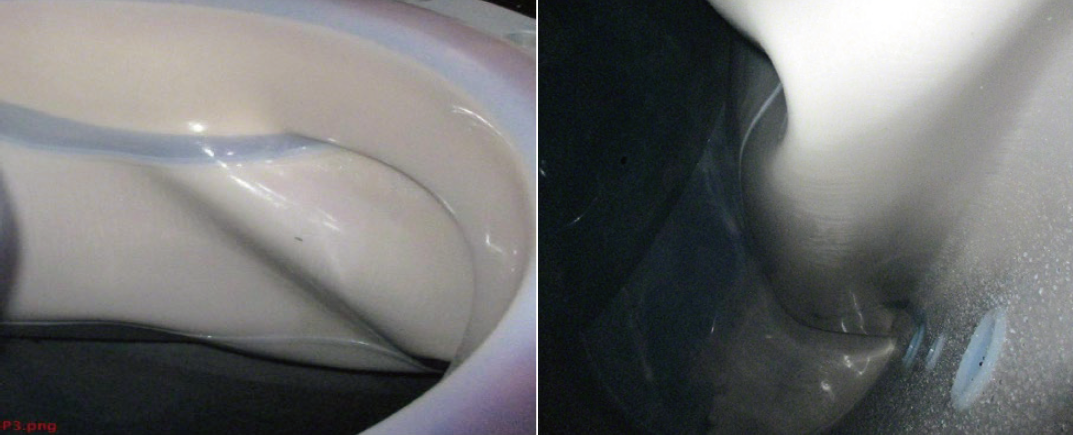
4.2.3 反應液位對廢硫酸去除雙氧水探討
根據 表3所列,顯示各廠反應液位有所不同,介於6~8分滿不等,上述3.1.6所提到反應液位所提到系統設計在八分滿。
根據F14P34實廠運轉經驗,初始雙氧水濃度過高,雙氧水濃度達到7~8%,造成瞬間產氣量過大與初始反應溫度過低問題,後續將反應液位調整,留下部分反應完硫酸作為下一批廢硫酸作混合,降低初始雙氧水濃度與提高初始反應溫度,經過反應測試,將初始反應溫度控制在40度上下為最佳初始反應溫度與實際反應液位為3000L,能有最短得批次反應時間,因此建議各廠將初始反應溫度控制在40度上下作實際反應液位調整。
5. 結論與建議
5.1 結論
本研究欲釐清廢硫酸去除雙氧水系統設計與反應參數之影響,經過文獻回顧與比較各廠實際系統設計與參數,並利用實廠運轉經驗作系統設計與反應參數最佳化探討,所獲得之結論如下:
- 同樣操作負壓條件下與相同為八分滿液位,直立式桶槽形式相對於臥式桶槽受力表面積較小。
- FRP材質濕式洗滌塔無法適用於廢硫酸去除雙氧水系統中的鹽酸催化法。
- 經比較各廠系統設計與實廠運轉測試後,兩者鹽酸加藥形式最大差異為鹽酸管路有無在桶槽反應液面之下,鹽酸管路於反應液面之下,能使鹽酸與廢硫酸反應較為均勻,減少批次反應時間與鹽酸加藥量,並增加整體產酸量。
- 使用2.0L/min作為鹽酸加藥流量,廢硫酸去除雙氧水有最佳反應速率。
- 經模擬廢硫酸去除雙氧水實驗與實廠運轉測試後,最高反應溫度控制在85度,能有效縮短批次反應時間,並增加整體產酸量。
- 經比較各廠系統設計與實廠運轉經驗後,建議各廠操作負壓控制400~600PA,較不會有安全疑慮風險與桶槽受損疑慮。
- 根據實廠運轉測試後,將初始反應溫度控制在40度上下作實際反應液位調整,能有最佳批次反應時間,並達到產酸量增加。
5.2 建議
本研究以廢硫酸去除雙氧水系統設計與反應參數最佳化探討,為了進一步證實廢硫酸去除雙氧水系統設計與反應參數影響,未來建議方向如下:
- 建議未來新廠規劃廢硫酸去除雙氧水系統中桶槽形式,採用直立式桶槽,同樣操作負壓條件下與相同為八分滿液位,其受力表積較小,且有較長的使用壽命。
- 建議未來新廠規劃廢硫酸去除雙氧水系統中濕式洗滌塔形式,採用CPVC材質的濕式洗滌塔,其對於廢硫酸反應過程中的鹽酸與雙氧水較好得耐化性及耐溫性,適用於廢硫酸去除雙氧水系統中的鹽酸催化法。
- 建議未來新廠設計與既有廠系統供應商為信紘且為鹽酸管中循環加藥形式,進行鹽酸加藥管路改管至反應液面之下,批次反應時間與鹽酸加藥量減少,達到整體產酸量增加。
參考文獻
- ①Hiroshi Ogata, Norio Tanaka, Reduction of Waste in Semiconductor Manufacturing Plant(Sulfuric Acid Recycling Technology), Oki Technical Review 160, January 1998. ②Yoshihiro Koyama, Sulfuric Acid Recovery and Purification Technology, Ultra Clean Technology, 9, 3, 1997, 159-162.
- 李崑池,以活性碳進行半導體廠含雙氧水清洗製程廢液回收處理之研究,2011,崑山科技大學環境工程系。
- 台積電工業工程年會論文-創新氨氮廢水資源化。
- 經濟部產業節水再生技術手冊。
留言(0)