摘要
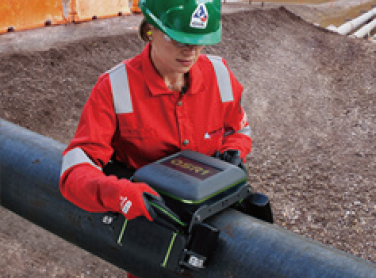
非破壞性檢測-應用電磁超音波探傷儀檢測管路腐蝕狀況
Keywords / Nondestructive-Inspection,Electromagnetic Acoustic Transducer,Pipe corrosion
隨著廠區翻新工程如火如荼進行,其中針對金屬管路以除鏽並重新油漆的方式,讓原本望過去有著鏽斑的管路煥然一新。然而實際施作時卻面臨了另一個問題,將管路表面生鏽去除、打磨後開始出現滲漏的狀況,因管路內部、焊道已有砂孔,或是長年使用造成管壁變薄,經表面處理後反而將最後一道防線破壞掉,從一根生鏽的管子,變成一根掛著導水帶的管子。為避免除鏽、打磨造成內部腐蝕狀況較嚴重的管路滲漏,使用非破壞性檢測如電磁超音波探傷儀,進行管線檢測,若腐蝕狀況嚴重,則改以更換新管路的方式取代除鏽油漆,降低施工風險。
As the renovation of the factory was in full swing, the metal pipes were descaled and repainted, which gave a new look to the rusty pipes that had been looking in the past. However, the actual application faced another problem, the surface of the pipeline rust removal, polishing after the beginning of leakage, because the inside of the pipeline, welding beads have sand holes, or the pipe wall has become thinner after years of use. And after surface treatment, the last line of defense has been destroyed, from a rusty pipe to a pipe with a water guide belt. To avoid rust removal, polishing caused by serious internal corrosion of the pipeline leakage, the use of non-destructive detection such as electromagnetic ultrasonic flaw detector, pipeline detection, if the corrosion status is serious, a new pipeline is the solution instead of rust removal or paint to reduce the construction risk.
1. 前言
成立於1987年的台積公司,2017年迎來了第一個30年,隨著公司發展持續擴大,除了建造新廠房提升先進製程產能外,運轉已有10年以上的成廠區如何提供工廠穩定、安全的環境提供晶圓代工服務成為了廠務一重要課題,全面翻新專案隨之而生。
翻新專案藉由PM動線改善、閒置設備拆除、照明更新及除鏽油漆等方式,讓成廠廠務區,能有像新廠房般的空間及明亮乾淨的環境,扭轉大家對老廠的既定印象,亦藉此機會提升廠區運轉穩定及安全。
其中管路除鏽的部份,金屬管路因長年使用,可能有砂孔,或是焊道處較嚴重的腐蝕,造成管壁厚度變薄,在磨除鏽斑的同時,偶爾會伴隨著滲漏狀況發生,造成現場做越多漏越大的結果。若能在施工前導入非破壞性檢測,便能夠事前評估管內腐蝕狀況,根據檢測結果討論工法是否恰當、擬定正確的作戰計畫,避免專案成效打折扣。
2. 文獻探討
根據台灣中油公司的統計,民國82年至99年間管線事故共計175件,其中腐蝕洩漏45件,佔比25.7%。舉民國100年7月26於雲林縣麥寮鄉六輕廠區發生的事件為例,因氫氣管線有一鏽蝕穿孔約2mm,引發管路火警波及共同管架,所幸最後無人員傷亡。
圖1、金屬管路腐蝕外觀
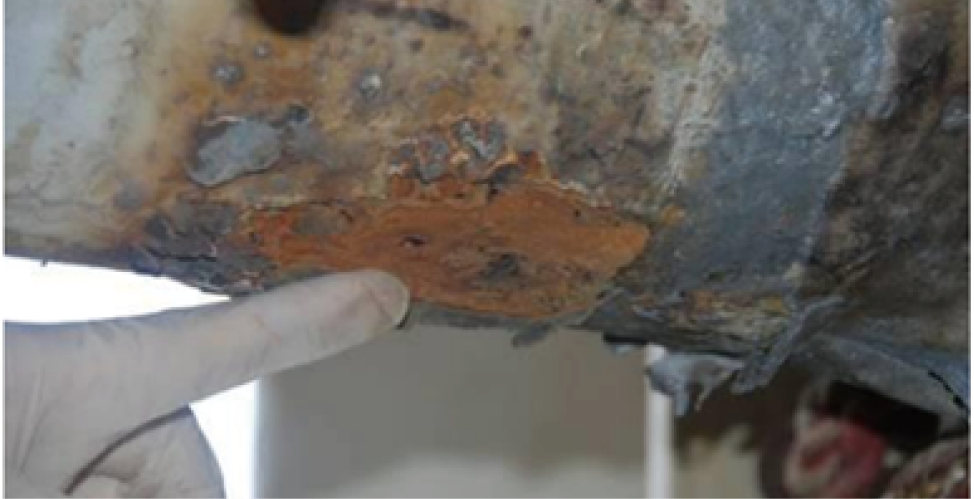
台積公司廠區內除了水系統之外,氣化Bulk gas系統亦有使用金屬管,若是管路所在環境位居戶外或是環境中有腐蝕因子等,這些原因都會造成管路使用壽命下降,若有適當的檢測機制,便能提早發現潛在風險。
腐蝕現象大致上能分為八大種類[5]:
- 均勻腐蝕 : 金屬暴露於環境造成的大面積腐蝕,如環境中濕氣較重、空氣中含較多氯氣腐蝕管路表面。
- 電位腐蝕 : 不同金屬相互接觸時,會因活性不同而產生電子轉移,使活性較大的金屬產生明顯腐蝕。
- 間隙腐蝕 : 同一金屬因幾何不連續或不溶性物質沉積在表面,使各處之環境化學物質濃度不均,造成部分區域優先腐蝕,如隙縫處較表面易腐蝕,是因為隙縫處形成的氧化保護層較薄之緣故。
- 孔蝕 : 管路製造過程中於表面有缺陷或瑕疵,在輸送含有腐蝕因子(如 : 氯離子),因缺陷處陽離子(金屬)濃度較高,優先與陰離子鍵結造成腐蝕
- 晶粒腐蝕 : 因鉻元素添加於金屬中能提升抗腐蝕力,而鉻會和碳結合析出為固體後帶離金屬,造成晶粒介面附近鉻含量不足,逐漸發生腐蝕。
- 剝離 : 合金中特定金屬因活性較大,優先溶解後留下活性較小之金屬,合金結構被破壞後機械強度降低,造成剝離。
- 沖蝕腐蝕 : 管路內流體因摩擦力造成金屬表面保護層磨損,進而產生腐蝕。
- 應力腐蝕 : 金屬結構受應力變形使表面氧化保護層被破壞,使得環境中之腐蝕因子由氧化保護層較不足處開始腐蝕。
目前工業上常使用的非破壞性檢測種類有七種[6],分別為:
- In-line Inspection(管內全檢)
- Visual Testing(目視檢測)
- Electromagnetic Acoustic Testing(電磁超音波檢測)
- PA Ultrasonic Testing(相位陣列超音波)
- Radiography Testing Profile(輪廓射線照相)
- Pulsed Eddy Current Testing(脈衝渦電流檢測)
- Guided Wave Testing(導波管線腐蝕快篩檢測)
考慮到各檢測方式使用儀器的攜帶性、準確性及量測速度,電磁超音波、相位陣列超音波、脈衝渦電流這三種方式較為適合用在廠區環境,而電磁超音波為近幾年較新技術,故選為本篇介紹的非破壞性檢測方式,如 圖2。
圖2、儀器外觀及使用方式示範
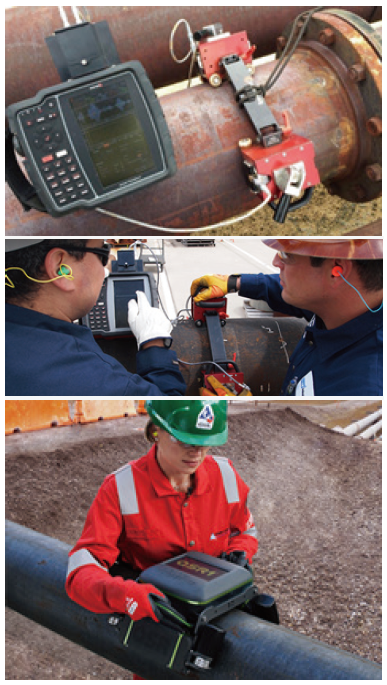
3. 研究方法
3.1 研究工具、研究變項之定義與測量
本次介紹的非破壞性檢測技術「電磁超音波檢測」(Electromagnetic Acoustic Transducer, EMAT),檢測配置如 圖3,共有磁鐵、線圈、待測物體三樣部件,其原理為:儀器發射端以線圈輸入高頻交流訊號,此時待測物體表面感應出渦電流圖4,並搭配磁鐵提供的外部靜磁場圖5,使待測物體產生羅倫茲力或磁滯伸縮圖6,藉由高頻往復受力產生微振(圖7),以超音波形式在物體內傳遞。
圖3、 檢測配置示意
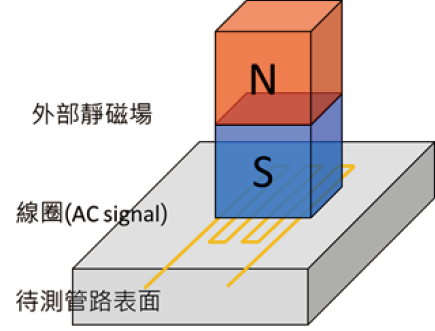
圖4、剖面示意
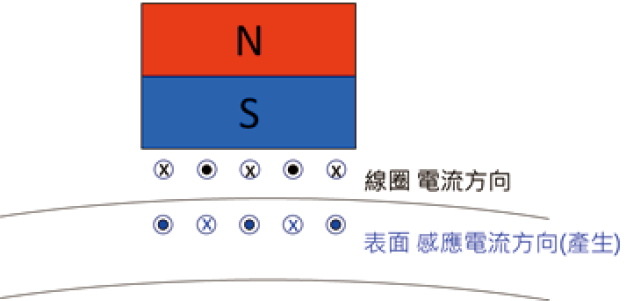
圖5、靜磁場作用示意
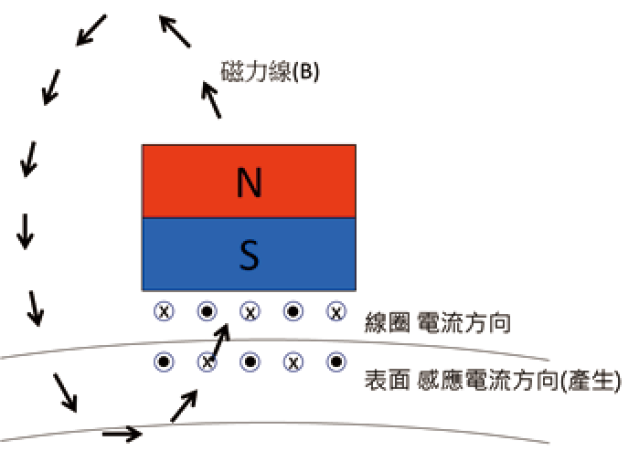
圖6、管路表面分子受力示意[發射端]
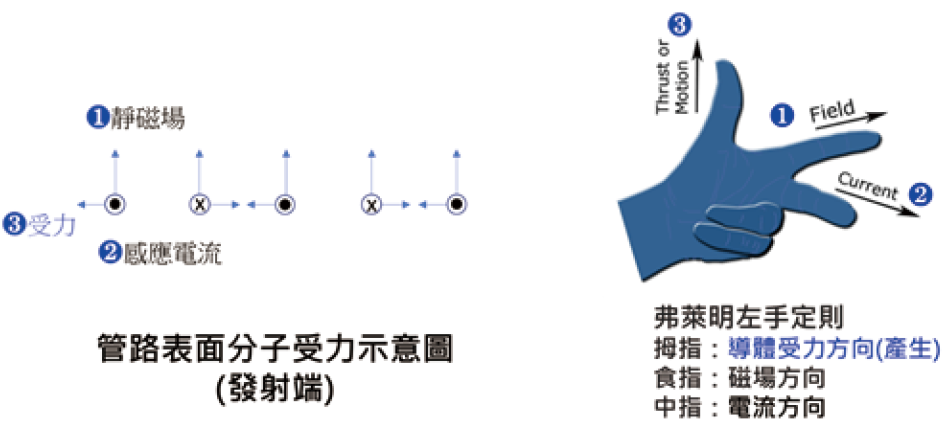
圖7、往復受力產生微振超音波
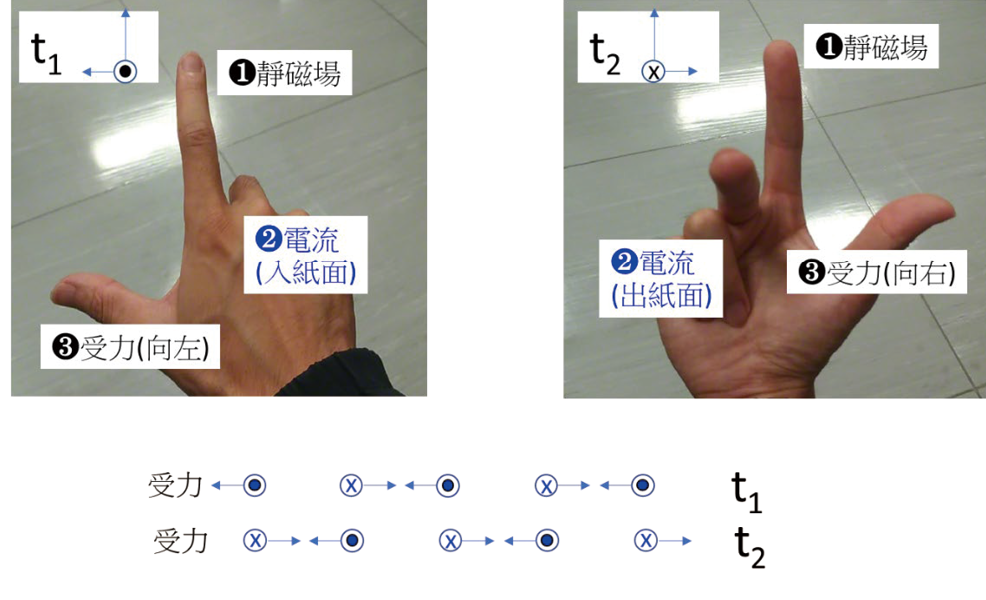
儀器接收端為同樣架構反向機制:高頻振動傳至儀器接收端下方時,會因為磁鐵提供的外部靜磁場產生出渦電流圖8、圖9,而儀器接收端的線圈會因為渦電流產生感應電流圖10,感應電流最終輸出至儀器被量測出來,進行後續資料處理、分析、解讀。
圖8、管路表面分子受力示意[接收端]
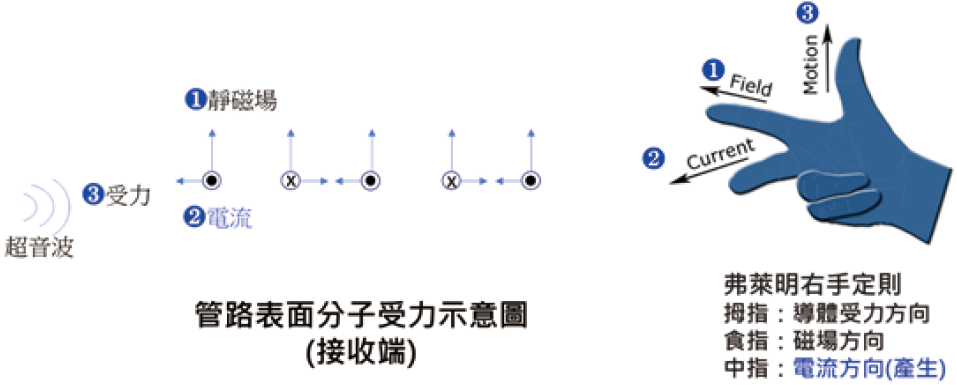
圖9、往復受力產生渦電流
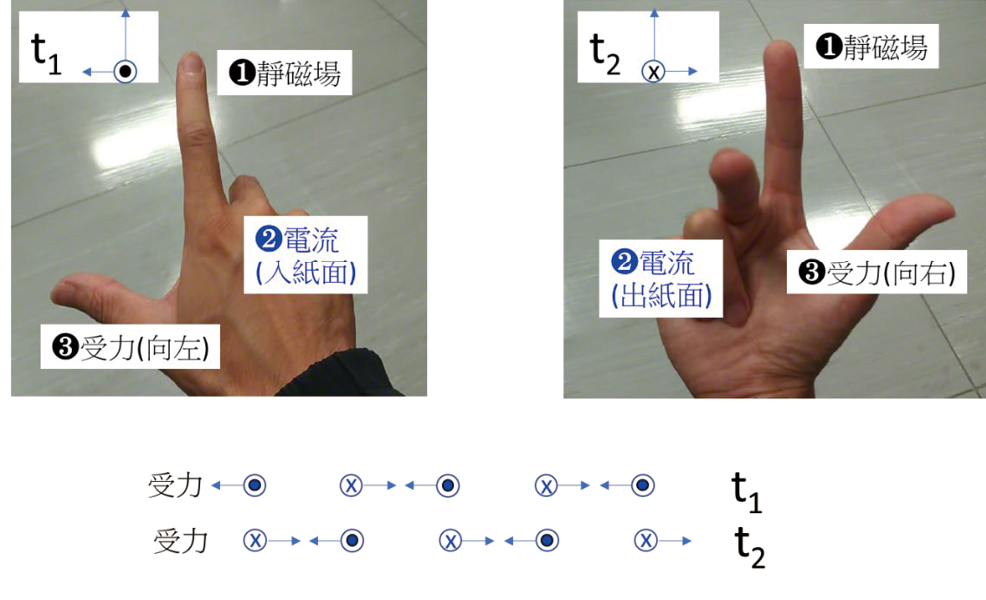
圖10、接收端線圈產生感應電流
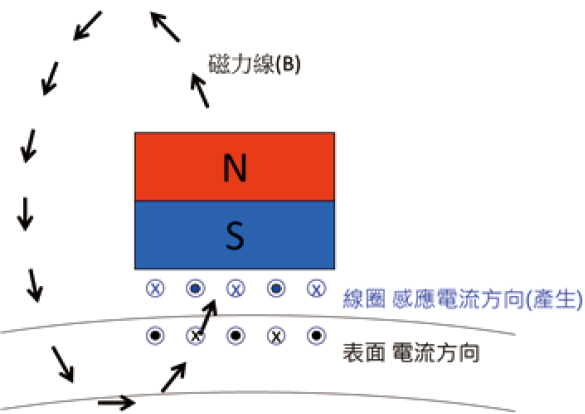
3.2 資料處理及分析方法
呈上述原理,由發射端發出訊號後,產生超音波於待測物體內傳遞,若途經缺陷便會降低原超音波震幅,並產生缺陷繞射波,與原本的超音波進行干涉圖11。
圖11、模態及缺陷造成的干涉
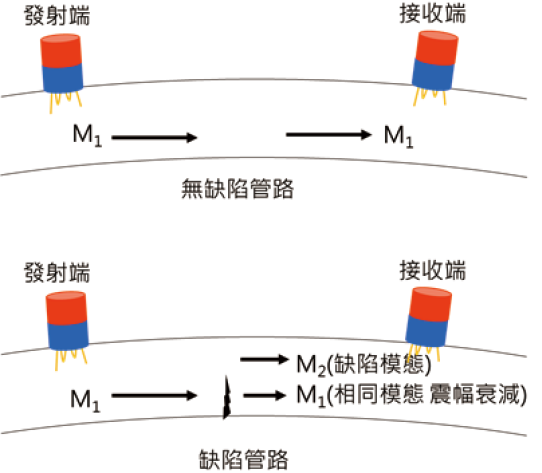
而不同的管路材質、管壁厚度、腐蝕程度、離距(探頭與管路間隙)及管內流體種類等變因會影響資料的解讀,故在分析訊號資料前,可以無缺陷管路、或是人工缺陷管路測試量測訊號作為震幅基準值(類似標準件概念)及異常訊號範例,以利實際量測時的腐蝕狀況判別。
4. 結果分析
4.1 實驗設計與過程概述
實際進行量測後會發現,接收端會收到兩次訊號,原因為發射端發出訊號後,超音波有兩種傳遞路徑能傳至接收端,稱之為T1及T2圖12。
圖12、T1、T2兩種傳遞路徑
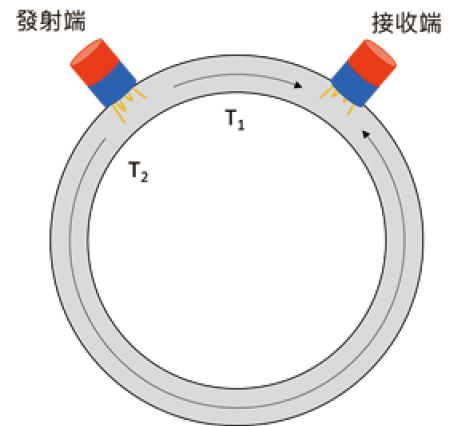
4.2 實驗數據解析
本次以三種管路特徵作為範例,藉由T1(黃線)及T2(紅線)訊號差異做為量測結果分析。橫軸為EMAT儀器移動距離,縱軸為儀器接收端訊號強度,因T1路徑上有點狀缺陷,超音波經過點蝕區域造成震幅降低,故圖13黃色線中間有一降點。
圖13、超音波經過點蝕區域造成震幅降低

若為無焊冠焊道,因焊料沿管線原周環繞一圈,EMAT儀器行經該區域時,因焊料與管路材質不同,使超音波傳遞時能量降低造成量測震幅下降,故黃色線及紅色線均發生降點圖14。
圖14、超音波經過焊道,則兩種路徑皆有震幅下降
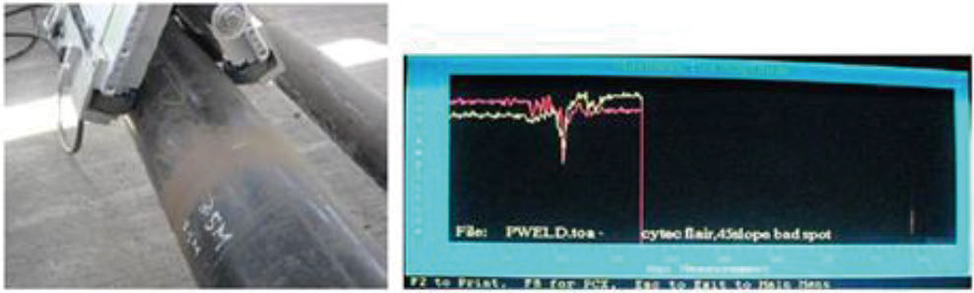
第三個範例為EMAT儀器移動路徑上有一插管,此範例與點狀缺陷範例類似不過是發生在T2路徑上,造成紅線訊號中間有一降點圖15。
圖15、超音波路徑遇到插管,亦會發生震幅降低
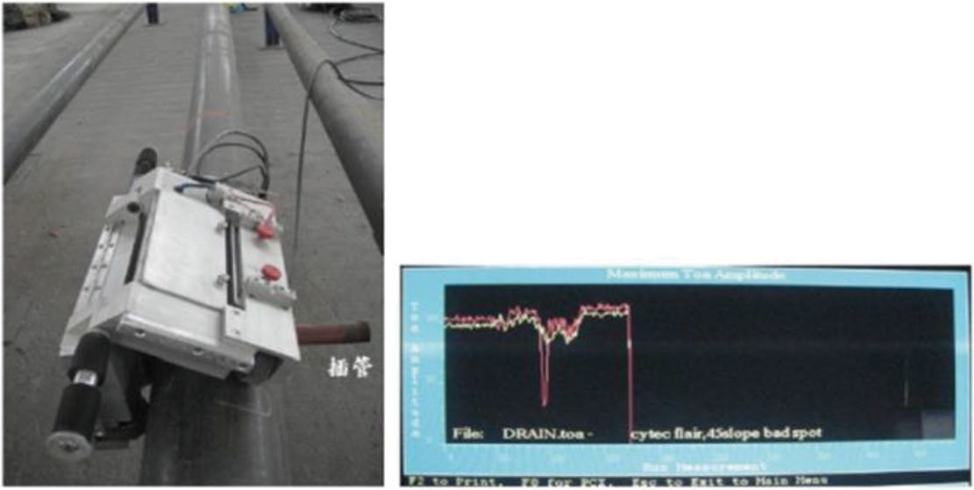
5. 結論
5.1 研究發現
電磁超音波與傳統超音波檢測技術最明顯的差異處在於,傳統超音波檢測需輔以耦合劑(超音波膏)方能進行檢測,而電磁超音波檢測因無需塗抹耦合劑,在廠務系統這種長距離管線檢測上有極大的優勢。
5.2 研究限制
因EMAT運作原理為利用待測物體之導電性(感應電流)、鐵磁性(靜磁場)交互作用產生體積變化進而分析量測訊號,故檢測對象僅限具導電性或鐵磁性材料,塑材管如PVC、PVDF無法藉由EMAT方法檢測。另外受掃描器構造限制,檢測路徑上不得有彎頭、法蘭及焊冠較突出之焊道,避免探頭損害。
5.3 建議
除了施工前管線檢測,可參考API 570(製程管線檢驗),訂定管線壁厚檢查週期依管線等級及評估管線剩餘使用壽命。若為新增管線,應於使用初期(試俥後3個月內)執行第一次檢驗,一年後再測一次以計算其腐蝕率,後續之週期可依最大檢查週期與1/2剩餘壽命取小值,或由各單位自行決定。
參考文獻
- 勞動部勞動及職業安全衛生研究所,103年度研究計畫。ILOSH103-S307,沈育霖、張銘坤,電磁超音波安全檢測應用技術-管線腐蝕檢測評估。
- 中國鋼鐵,超音波導波法於工業管線檢測之簡介,蔡坤義,T423 NDT。
- 台灣電力公司,地下管線非破壞檢測技術研習,林炳宏,107-082出國報告。
- EMAT ULTRASONIC INSPECTION, EMAT principle - ULTRAKRAFT https://www.youtube.com/watch?v=HyBzjsrdrcU
- 腐蝕概論,防蝕工程第六卷第二期第57~65頁,楊聰仁。
- 中華民國防蝕工程學會,公共管道檢測-導波檢測技術,李秉鴻,2019。
留言(0)