摘要
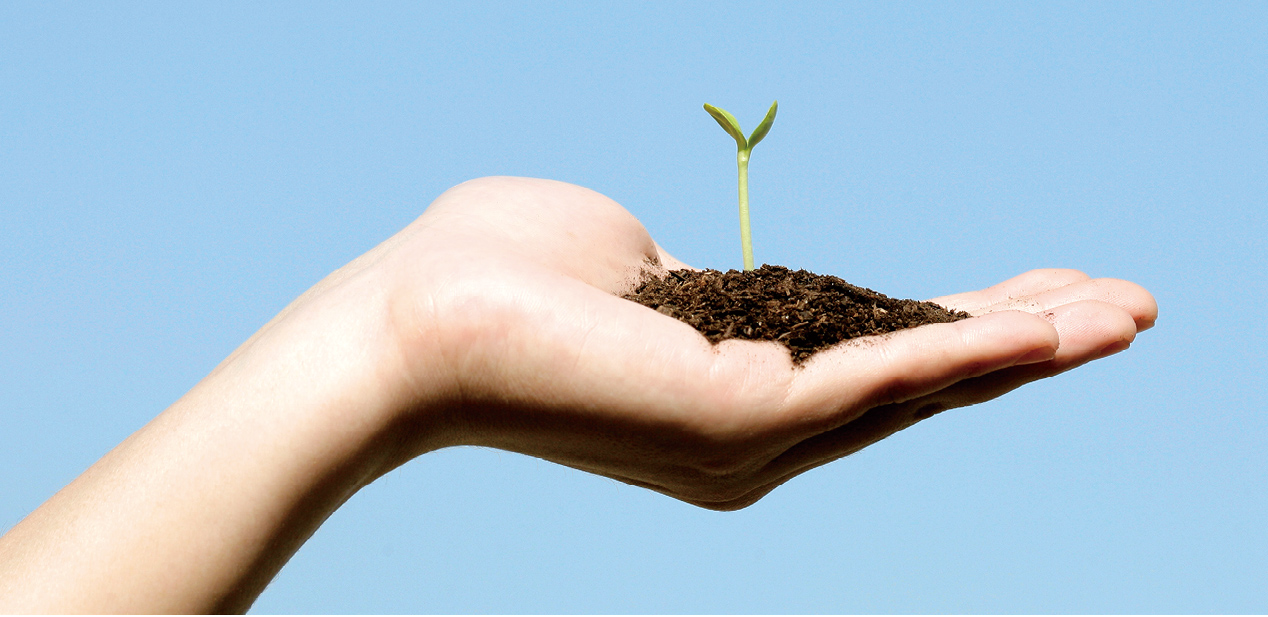
低成本與高生產力的綠色製程 - 現場製氟技術
Keywords / Speciality Gas,Fluorine Generator,Chamber Clean
氟氣(F2) 已在半導體工業中廣泛使用多年,主要應用於製程設備反應腔室(Chamber) 的清潔,由於氟自由基(Radical) 可與沉積的薄膜(Si, SiO2, Si3N4, SiON, W, WSix, TiN, Al 等) 與有機污染物發生反應形成揮發性化合物,可以很容易地經由幫浦被抽走。三氟化氮(NF3) 的導入使用是為了要取代四氟化碳(CF4) 和六氟化硫(SF6) 這兩種京都議定書(Kyoto Protocol) 列管的溫室氣體,用來提高清潔效能和對環境的保護。但諷刺的是NF3 也即將被列入京都議定書遺漏掉的溫室氣體列管,近期的測量也顯示了大氣中的NF3 含量呈現指數級的增長,目前處於和CF4 和SF6 相同的狀況。氟的自由基可以進行蝕刻和清洗反應腔室或晶圓的沉積物,氟氣的全球暖化潛能值為零,因應全球氣候變化與符合綠色製造,同時為了確保穩定的系統供應,現場製氟(On-site Fluorine Generator) 是目前可行的選項之一。本文將概述現場製氟技術,以及其可替代NF3 所帶來的潛在好處。
前言
2002年東京威力科創(Tokyo Electron Limited, TEL)和日立國際電氣(Hitachi Kokusai Electric, HiKE)開始評估以F2取代NF3和三氟化氯(ClF3),以作為低壓化學氣相沉積(LPCVD)清潔爐管之清潔氣體。最初主要的興趣是為了要降低成本和提高清潔效能,使用氟分子(F2)可在較低的溫度中進行反應腔室的清潔,延長反應腔室石英元件的壽命,這是一個熱的(Thermal)清潔製程,從化學的角度來看,特別是NF3若溫度下降時會導致較低的清潔效率。氟自由基(無論其來源是NF3、ClF3或是F2),在清洗中蝕刻的效率都是相同的,但在較低溫度情況下,NF3解離效率較低,這也導致了較低的蝕刻速率。TEL和HiKE已將F2應用在十二吋晶圓廠的氮化矽的蝕刻製程,並建立了標準製程參數,但目前F2仍以儲存在高壓鋼瓶內作為主要之供應方式。
從整體角度來看,要維持穩定供應生產之需求,最有效的方法莫過於現場製造,提供高純度F2供給到設備端。但由於氟分子具有高活性和毒性,相關的安全規定對於高壓F2的運輸與儲存做了很多限制,在晶圓生產過程中必須使用大量的F2,也因為這些的限制導致生產工廠無法使用高壓F2鋼瓶來替代NF3或ClF3。所以在一大氣壓力下生產的現場製氟是一個安全的解決方案,因為現場無需儲存大量的F2,不需要頻繁的運送和更換鋼瓶,且和傳統鋼瓶比較,現場製氟具有較低的供應壓力之優點存在。
考量半導體產品對永續環境的影響,綠色產品需要考慮到產品的整體生命週期,包括從原材料開採、運輸、產品製造與使用,到廢棄物之處理等,都須徹底評估其對環境的影響。產品的碳足跡、水足跡或其它可能對環境造成的影響,這都是在使用該產品時所需要考量的重要指標。如果F2是適合的替代產品,且它對整體的效益也有顯著地幫助,不僅是成本考量上可用來替代其它含氟氣體,潛在的好處是以此技術也可為地球之環保盡一份力量。
計畫方法
F2是自由基中最簡單的來源,其比NF3或SF6有更低的鍵能(通常指在標準狀態下氣態分子拆開成氣態原子時,每種化學鍵所需能量的平均值),如 表一所示,從分子氟(F2)中離解出1莫耳原子氟(F)只需80 kJ,而從NF3和SF6中離解出1莫耳原子氟分別需要281 kJ和323 kJ。因此採用分子氟清洗能夠節省大量的能源消耗。NF3或SF6所需的高離解能,也解釋了為什麼從這些分子中離解出的氟在清洗過程中經常僅能部分的被利用。
F2 |
NF3 |
SF6 |
|
---|---|---|---|
Total Activation Energy |
1 mol F from F2 80 kJ |
1 mol F from NF3 281 kJ |
1 mol F from SF6 323 kJ |
Bond Strength |
F-F 159 kJ / mol |
F2N-F 248 kJ / mol |
SF5-F 326 kJ / mol |
FN-F 278 kJ / mol |
SF4-F 222 kJ / mol |
||
N-F 316 kJ / mol |
SF3-F 351 kJ / mol |
||
SF2-F 264 kJ / mol |
|||
SF-F 385 kJ / mol |
|||
S-F 339 kJ / mol |
F2是在低壓下所製造生產,F2製造技術整合了電解、純化、壓縮和儲存功能,可依照需求調整生產量。這種的電解方法是業界標準的生產方式,與Moissan于1886年第一次分離氟元素時所使用的方法是相同的,它與其它氟化氣體的製造步驟第一步亦相同(例如NF3),此方式可降低氣體生產的能耗。
參考 圖一與 圖二,從氣體或液態無水氫氟酸(AHF)加熱後輸送到電解槽(KF.2HF),電解液工作溫度約90℃,放置在蒙耐合金(Monel)製成的電解槽中,電流通過後陽極會產生F2,另一端陰極則會產生氫氣(H2),再利用實體的隔板進行分隔,以防止F2和H2再重組。H2會直接稀釋處置(<0.05%),生產出的F2會再進行過濾與純化,其F2內殘餘的氫氟酸濃度低於20ppm(通常會比高純度鋼瓶中的含量還要低),其後可以在一大氣壓下使用,或再使用加壓裝置加壓到安全工作壓力(約20psig)後儲存至儲槽中,並可因應不同的需求和應用再做調整,使用「氣體混合器」設備可和其它之惰性氣體再做混合(例如20% F2/N2),可在0~100%範圍內做適當之調整。
圖一、氫氟酸電解槽( 資料來源:Linde Electronics)
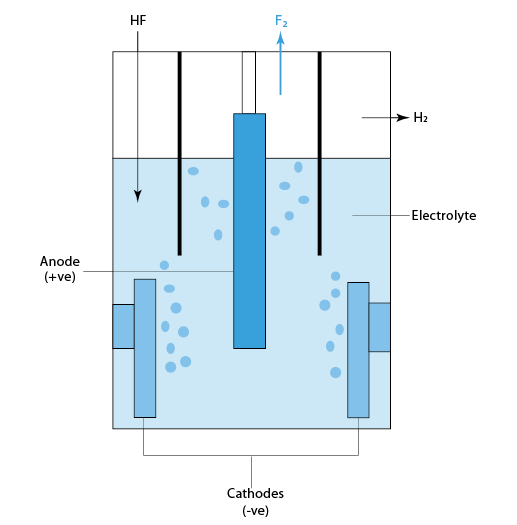
圖二、現場氟氣製造設備( 資料來源:Linde Electronics)
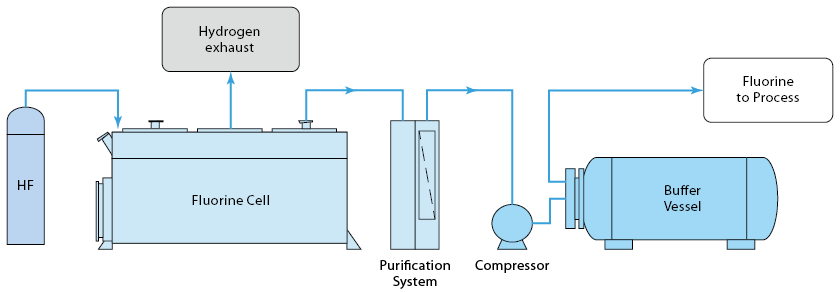
為了安全可靠的生產,對於任何有潛在危險的製程皆採用系統化的方式進行評估,如危害控制與分析(Hazop)、失效模式影響分析(FMEA)和專案安全審查(PSR)。HF和F2為半導體製程中經常使用的毒化物,如何妥善處理以降低對人員危害皆有標準之程序,現場生產氟氣的考慮方向主要是「減量」、「減壓」和「隔離」。
現場製氟設備之設置,在設計規劃上首要就是要降低現場F2之儲存量,以盡量避免及減少可能產生之風險,可依工廠生產之需求來調整製造供應量,舉例說一個十二吋半導體晶圓廠PECVD的反應腔室之清潔氣體需求量約為每天1公噸之F2,現場動態F2之儲存量將可低於50公斤內(低於法規限制),這些少量的儲量壓力也低於2.5 Bar(a);其次在廠務設施上設計規劃如下:
- 製造場所之建築物須符合HPM (Hazardous Production Material)儲存要求,即適當場所位置、兩小時防火時效牆與消防系統等。
- 製造場所內設置適當之SEX排氣處理系統,根據法規要求於以1 cfm/ft2換氣量做規劃,且亦須有緊急處理之除害裝置。
- 於適當位置安裝氣體偵測系統與CCTV監視系統。
- 氣瓶櫃與現場製氟設備須符合法規之各種連鎖安全機制,如EFS (Excess Flow Switch)、EMO (EMergency Off)等,如發生氣體洩漏時,能將氣源關斷以阻隔氣體之洩露量。
- 氣體偵測系統(GMS)配置ESOV(Emergency Shutoff Valve)與地震感測系統,可遠端控制設備之關斷,不致於造成人員於危險環境中冒險搶救。
- 所有設備與安全設施皆採不斷電或緊急電電源,以確保安全防護無虞。
- 在氣體配管部份,從F2儲存槽連接到Fab內之設備端的全部氣體管路,一律使用不銹鋼無縫雙套管(SUS316L EP + SUS304AP)的設計,且全部以自動焊接並經五項品管(保壓測漏、氦測漏、水、氧與微粒子檢測)以確保品質,並在內外管間抽成負壓狀態,配合以GIS持續監控內外管間壓力的變化,若有壓力之變化亦會透過GMS連鎖關斷氣源供應。
- 製造場所亦會配置緊急處理設備,如ERCV( Emergency Response Containment Vesse)、SCBA (Self-Contained Breathing Apparatus)等,可充分應付洩漏時緊急應變之所需。
F2是很強的氧化劑之一,也是最容易與其他物質反應的元素,由於氟原子的高負電性,氟原子易與其它元素結合。儘管F2的高反應性,純氟還是能夠在許多合金之金屬中使用,第一步是在生產過程中直接除去F2中的氫氟酸,F2與HF的混合物為路易斯酸(Lewis Acid)會引起腐蝕作用。鈍化(Passivation)的程序是以純氟先在局部逐步升高的壓力管路中生成金屬氟化物,以取代原生金屬氧化層,這一氧化層中無任何碳氫化合物,不易生成微粒子。高純度的F2是源於高純度的氫氟酸和選擇適當材料的電解槽,以及有穩定的工作電流,密閉性也須有良好的設計,以避免在生產F2時造成之洩漏,最重要的是對F2電解槽安全適當的設計,以及高完整性的隔板設計,以避免在生產時陽極的F2和陰極的H2發生再結合。
結果與分析
隨著新開發的產品製程,2003年半導體產業很明確方向是在推動新的熱清潔的應用,2002年因為NF3新的產能開發後,高價位的NF3價格開始下降,減少潛在的經濟效益。新開發的RPS (Remote Plasma Source)電漿清洗有助於提高NF3的分解效率,然而這一種情況並不適用在當時新興的TFT-LCD產業以及後來的太陽能光電業,隨著面板尺寸增加致使電漿輔助化學氣相沉積清洗氣體需求量也大量的增加,如何確保下一世代的應用是值得思考的問題。
將RPS(mks ASTRON®ex,最大功率為10KW)用來解離NF3和F2(參照 圖三),當氣體的流量超過最大的解離能力時,電漿將失效停止輸出氟自由基,解離NF3的最大流量為9slm,F2為44slm,F2所產生的氟自由基是NF3的3.3倍。NF3的鍵能是281kJ/mol F,F2的鍵能是80kJ/mol的F,由於在反應腔室的清洗蝕刻反應物是有限的,清洗時間和氟自由基的數目是成正比,這意味著使用相同的能量,在不需要變更設備的硬體條件下,就能夠顯著地增加刻蝕速率。
圖三、PRS 解離不同流量下之NF3 和F2 能耗差異( 資料來源:Line Electronics)
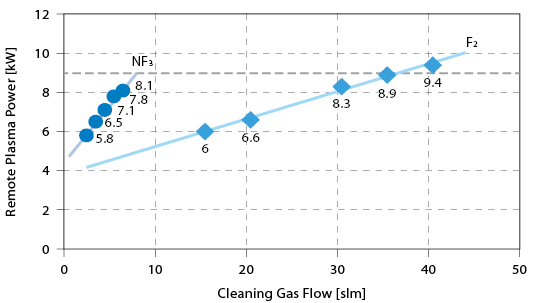
這測試也證實了電漿清洗僅僅是利用氟自由基進行清潔,在同一的氟原子流速下NF3和F2的清潔率是相同的,但鍵能低的F2可以在較高的流量下有較高的蝕刻率,因此在同樣的能量下可以實現更高的蝕刻速率,額外的好處是獲得較低的功率消耗和產生的熱量較低(參考 圖四所示)。在反應腔室內解離的情況是不同的,特別在高流量下NF3需要較高的活化能量以及更容易再結合,故導致NF3轉換成氟自由基的效能降低(參考 圖五所示)。
圖四、NF3 和F2 的清潔速率與氟原子流量( 資料來源:HSC Chemistry)
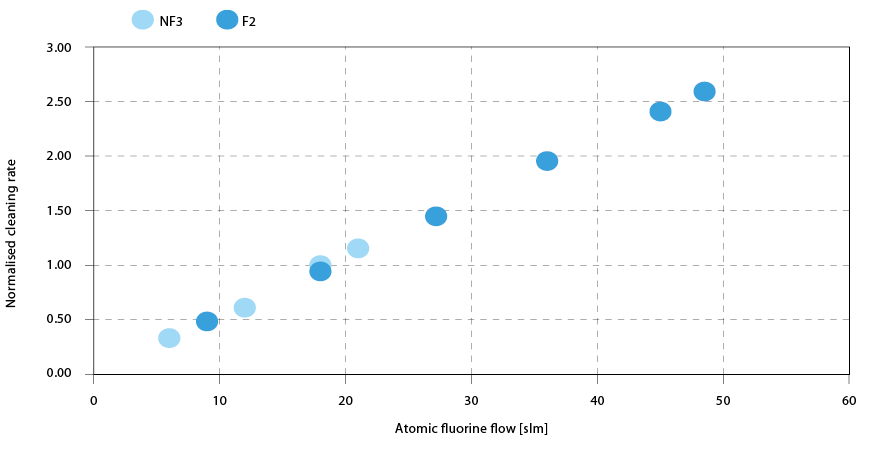
圖五、NF3 和F2 的清潔速率與氟原子流量( 資料來源:HSC Chemistry)
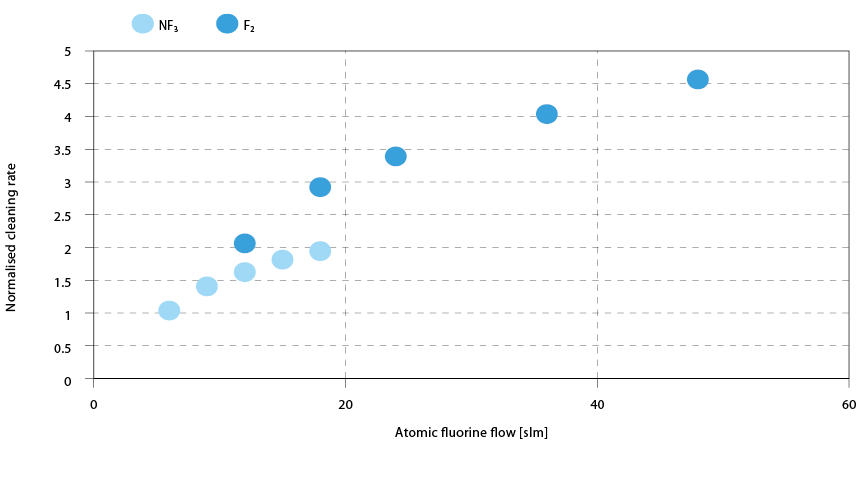
把F2應用在大型PECVD之反應腔室清潔,相同證實了其效能和可靠的數據,也已開始在十二吋的半導體設備上測試,用以證實是否可以有相同的優點。在一個半批次式的原子層沉積系統(ALD)和一個單片式的熱化學氣相沉積系統(CVD)進行清洗評估,NF3和F2的清潔效能整體影響總結果如 表二與 表三所示。製程參數需要進行最佳化以得到最佳結果,它不是直接用F2替換NF3那樣的簡單。這可能是由於一系列因素,如氣體的流動均勻性、電漿密度、壓力和溫度等,每個設備需要進行最佳化以得到最佳結果。
Gas |
Mass gas / clean |
RPS Power |
Total clean + seasoning time |
---|---|---|---|
NF3 |
128.9 g |
8.5 kW / 500 sec |
2,816 sec |
F2 |
76.34 g |
4.5 kW / 450 sec |
1,815 sec |
% reduction |
40% |
52% |
35% |
Gas |
Mass gas / clean |
Total clean + seasoning time |
---|---|---|
NF3 |
197.5 g |
10,971 sec |
F2 |
151.4 g |
6,771 sec |
% reduction |
23% |
38% |
結論
氟氣分子(F2)在質量方面包含了100%的氟(F),而NF3分子中只有80%的氟,SF6分子只有78%的氟。將NF3轉換到使用F2,先不論前述的優點,在氣體的質量消耗量方面可減少百分之二十。氣體購買價格是以重量做計價單位,若NF3和F2價格相同,清潔速率也相同時,使用F2將可節省百分之二十的氣體成本。再加上前述F2的獨特性能,優點遠高於節省百分之二十的氣體成本,如果F2每單位成本比NF3低的話,從現場製氟的效益來看每年可節省的總成本是更加可觀的。
再者F2之全球暖化潛勢(Global Warming Potential, GWP)為零,而NF3(GWP為17,200),SF6(GWP為22,600)是眾所周知的溫室氣體,若使用F2將有助於顯著減少製造過程中產出之二氧化碳(CO2),為了盡量減少在生產過程中之排放,大部分工廠都安裝了高性能的洗滌系統,然而在現今整個材料生命週期中排放的風險來看,NF3在大氣中的存在量正在快速的增加中,相當於全球生產的NF3有高達16%被排放到大氣中。因此為降低全球暖化潛勢,使用低GWP的原料可減少造成全球環境的危害。
經證明F2在PECVD和LPCVD系統的反應腔清潔可以取代NF3,其帶來更快的清洗時間和較低的氣體用量和能量。不過若要完全實現這些好處,可能仍需要經過最佳化的調整過程。使用F2可得到的好處是可顯著提高設備的生產力,降低能源和氣體的消耗,顯著減少整個材料生命週期中的CO2排放量。我們須盡最大的努力實現永續環境,相信這是一個值得進一步的研究探討評估,讓這世界的環境保持在最佳的狀態。
參考文獻
- Linde Electronics
- S. Petri, P. Stockman, J.-C. Cigal, P. Szych, W. Beyer, H. Stiebig APPLICATION OF MOLECULAR FLUORINE TO CHAMBER CLEANING FOR THIN FILM SILICON SOLAR CELL FABRICATION
- C.H. Oh, S.J. Ko, D.K. Shin, Y.Y. Jeong Improving Eco-Efficiency Via Elimination of Greenhouse Gases from Semiconductor Dry Cleaning Processes
- Solar International Magazine, Issue IX 2011, Efficient improvements with on site solution, Page 12~15
- 維基百科
留言(0)