摘要
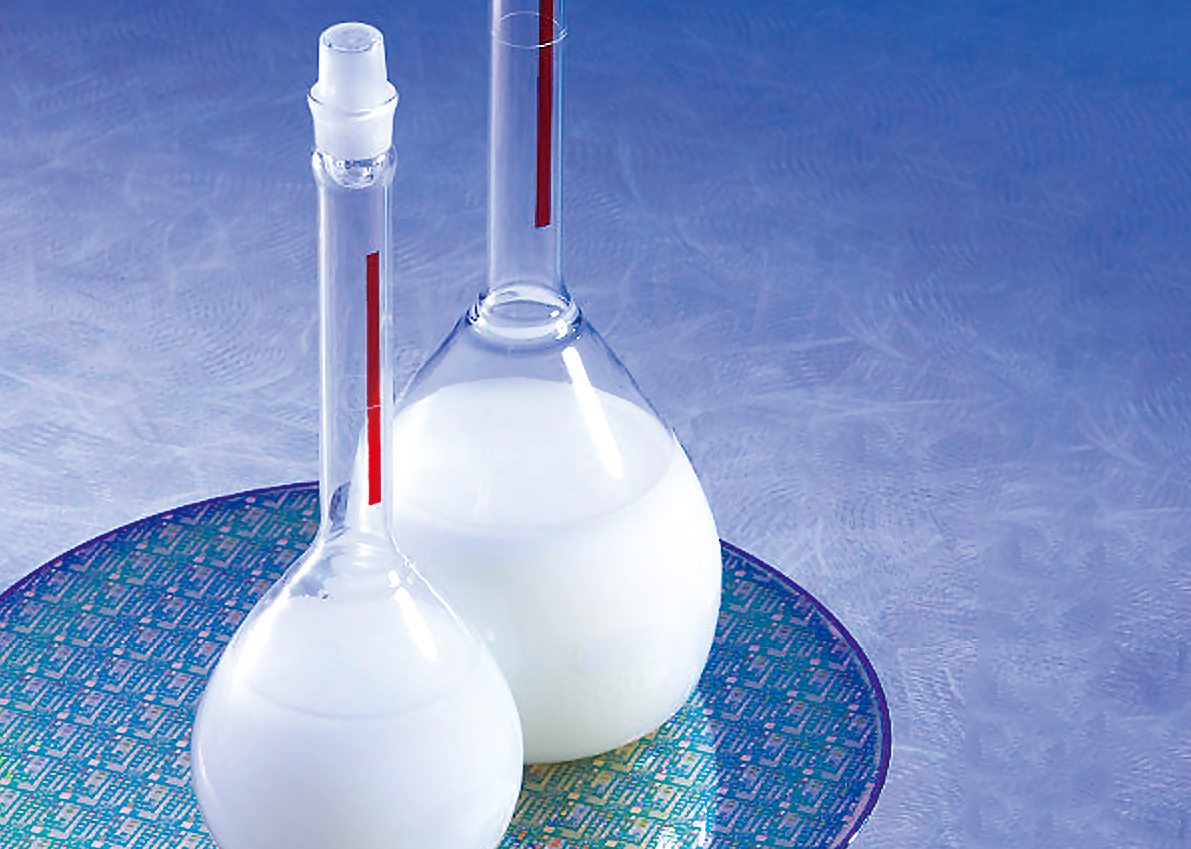
先進半導體廠化學品供應系統及微粒子控制
Keywords / Chemical Particle,Slurry Particle,Large Particle Counts (LPC)
本文將討論半導體廠化學品及化學研磨液供應系統微粒子控制的設計和改進的方向以及未來的晶圓廠化學品及化學研磨液供應系統新挑戰。其次,研究化學研磨液顆粒大小和穩定性,以管理研磨液使用時間、減少缺陷,特別是大顆粒粒子(LPC)在研磨過程中所造成的損害。
前言
近幾年來隨著我國積體電路產業的蓬勃發展,加速了我國半導體相關產業國際競爭力,目前製程能力已朝向28奈米和20奈米的先進技術推進。雖然半導體生產所需化學品及研磨液僅佔生產比例一小部份,但其純度及品質卻直接影響到最終產品的良率和元件的品質暨可靠度,因此其重要性不容輕忽。
半導體廠所使用的化學品及研磨液之供應系統,過去幾年其設計依循晶圓廠生產機台的需求持續演進,以符合製程生產需求之使用量、流量、壓力、品質等。新的需求可歸納如下:
- 增加系統的可靠性、更佳的使用點流量與壓力穩定。
- 減少化學品離子和微粒污染物,保持研磨液粒子分佈穩定。
- 混酸化學品濃度品質具有較高的準確性和再現性,提供更高的流量。
化學品供應系統
化學品供應系統如 圖一所示,其最大的挑戰之一是,必需大幅減少污染物離子和顆粒的產生,並增加其工作可靠性,以及提供長時間不中斷的運轉。由於任何化學研磨液的變化均可能會影響化學研磨製程的效能,對於化學研磨液設備,除了可靠性外,控制顆粒分佈穩定、pH值、懸浮固體含量是為重要的課題。
圖一、化學品供應系統
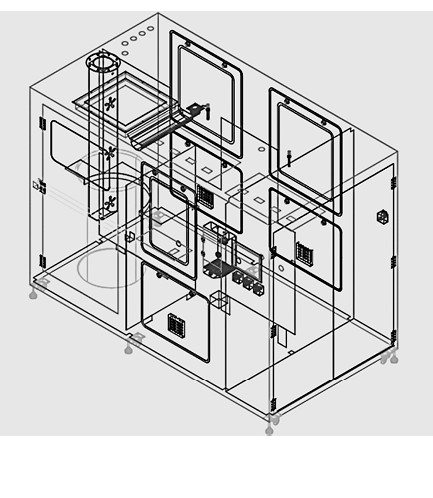
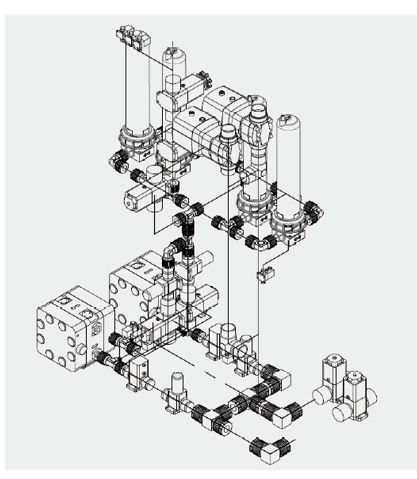
完整先進化學品和混酸供應設備,已經演變成複雜的系統結合控制及管路設計,包括使用高純度PFA的材料,更耐化學侵蝕及耐溫度變化,並減少離子污染和微污染顆粒的產生。在閥件方面的演進包括PFA材料的升級及液流道優化,除了減少無染物外,還能延長使用壽命。監控設備也變得更準確、更快速的反應、以及提供良好的人機介面。
未來的化學品供應設備的另一個關注點是其可靠性,盡量減少失效機率,並提昇不中斷地運轉的時間。
對於新的挑戰,新設備必需:
- 增加流量
- 更嚴格的POU壓力控制
- 精確的監控
- 系統的可靠性
- 去除金屬離子與粒子及其品質控制,如 圖二所示
圖二、離子交換樹酯純化示意圖
為了符合新規格,化學品及研磨液供應設備由隔膜泵演變為應用磁浮泵及氮氣壓力供應。氮氣壓力系統的好處是兼容大部分的化學品。除減少化學品消耗,它可以處理高流量和嚴格的壓力控制使用點。此外,壓力供應系統還解決一些重大問題,諸如降低壓力的衝擊和壓力波動,可提高過濾器效能及減少微粒子的產生等。
磁浮泵提供技術的優勢,提供高流量及準確壓力控制,降低閥操作頻率。缺點是磁浮泵會造成化學品循環發熱。因此磁浮泵的主要設計是用於大用量供應或迴路供給,在設計上需藉循環回桶槽時用新鮮的化學品冷卻泵的熱能,如 圖三所示。如需溫度精確控制,則需加裝熱交換器,以嚴密控制溫度。此外,在供應系統使用短循環或大迴路設計,可以連續過濾化學品提高微粒子的品質管控,並且提供了一個更好的環路壓力控制。
圖三、以磁浮泵供應化學品之設備
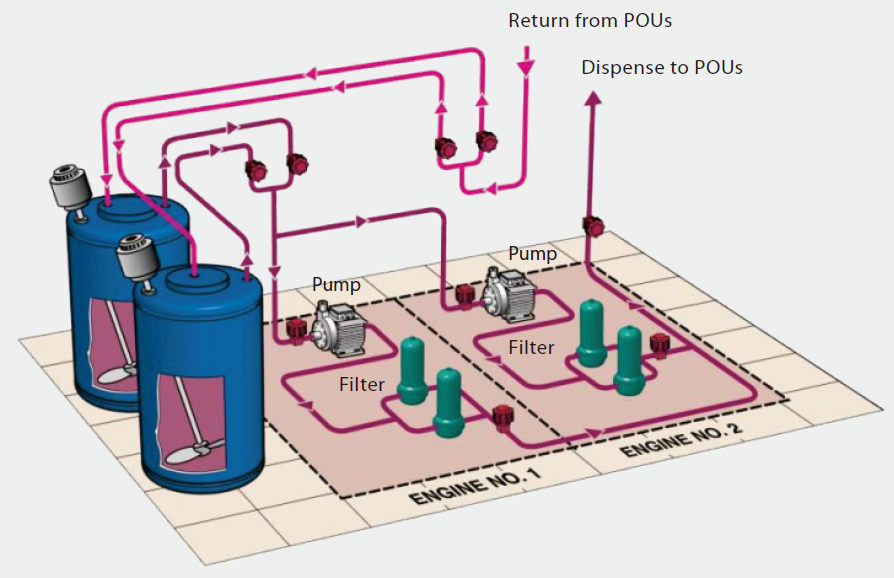
過濾為一重要的技術,化學品原物料在某種意義上被認為是“未清潔的”,因為它可能含有大量的污染微粒,無論是桶裝或槽車供應化學品,需要建立清潔的化學品路徑,在供應到工廠之前,它需要通過濾心進行循環過濾純化。最近的過濾器具有低壓降和預潤的特點,對於20奈米及以下粒子有較高的去除率。在化學品精製純化趨勢下,已使用專屬的濾心循環來過濾原物料化學品,而供應端也會使用另一組濾心分離。
化學研磨液混酸及供應設備
過去的十年裡化學研磨液最主要的進步是化學研磨液本身,研磨液材料成為一個更複雜的固體懸浮液及添加劑化學品混合液。要處理和混合這些新的研磨液材料,必須諮詢研磨液製造商處理程序。如果沒有控制好研磨液的品質,晶圓可能會受到嚴重損傷。研磨液需審慎的方式處理,若由不同的供應設備,或未遵循部分設計規則,可能造成品質不符需求。
研磨液供應設備,已從氣動泵及隔膜泵演進至磁浮泵,輸送方式則須遵循幾個關鍵的操作因數:
- 避免剪應力和大顆粒的增長
- 保持研磨液懸浮液均勻
- 在混合時避免pH值震盪
- 使用飽和濕氮氣,沖洗和壓送研磨液
- 避免流路死角
- 避免縮口節流路徑
- 雙迴路防壓降濾心設計,避免停機和供料不足
- 其他因數等……。
謹慎選擇和設計研磨液供應系統可大幅減少大顆粒粒子(LPC)的形成或增加。在一項研究中發現,隔膜泵(diaphragm pump)比波紋管泵(bellow pump)較不易產生大量LPC,原因在於較低的剪切力。而磁浮泵也因為較不易引起顆粒絮凝(flocculation),且能達到相同的效果。因此,越來越多研磨液供應系統使用磁浮泵。另外,新的串聯安裝技術也能使研磨液維持良好的品質、簡單的壓力和流量控制。
圖四指出CMP研磨刮痕的數量與研磨液LPC比值(粒徑從0.469到1.887微米)幾近線性的增加, 圖五亦呈現LPC與CMP晶圓上的刮痕相對應的關係,主要成因可推測為研磨液中大粒徑粒子在研磨過程中嵌入晶片和研磨墊之間造成刮損。新近案例顯示,在管路上Vantage LPC (1um > 200 ea/ml)大粒徑研磨液顆粒造成Al CMP Defects。於此,氮氣壓力系統提供更好的流量和壓力控制,使研磨液減少剪應力及品質變異,抑制大顆粒的生長,並增加過濾效率,減少濾心的壓力波衝擊,如 圖六所示。
圖四、刮痕的數量與研磨液LPC 比值之關係 (from The Electrochemical Society)
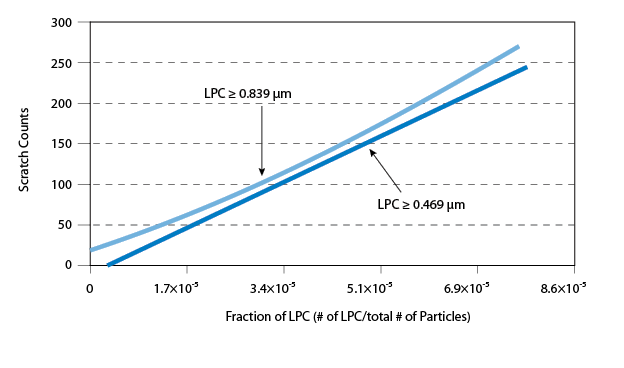
圖五、LPC 與CMP 晶圓刮痕的關係

圖六、The drawing shows a gradient dispense system using pressure vessels and pressure tank
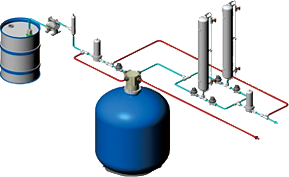
最近,有一項使用氮氣壓力配合磁浮泵供應的新技術,供應桶槽加壓供給迴路,然後運用磁浮泵將研磨液保持循環。由於幾乎沒有大能量需求,研磨液在非常低的轉速運行循環,可維持低熱量產生和避免劇烈攪動。
對於研磨液而言,為了控制研磨液的品質,混合有幾個參數需要控制,例如混酸步驟順序、濃度的控制,以及管理研磨液的使用壽命,並利用分析儀器嚴格監控研磨液幾項物理參數品質,如pH值、電導度、添加劑的濃度、密度、流量、壓力、顆粒大小、界達電位等。
圖七說明混酸步驟順序的重要性,此案例之研磨液及添加液分別為鹼性及酸性,混酸前需加入去離子水稀釋以緩衝pH變化的影響(方法1、2、4);但不適當的混酸順序(方法3)則受pH劇烈變化而導致粒子嚴重凝聚,在粒徑分佈圖(PSD)呈現異常分佈,且研磨液也極易沉降(sedimentation)。
圖七、在不同混酸順序下之粒徑分佈及沉降結果
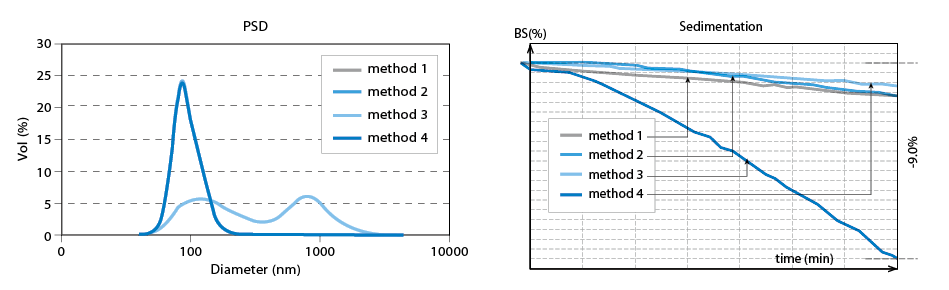
圖八說明部分的研磨液其界達電位(zeta potential)與移除率(removal rate)有明顯的關聯,研磨液在高界達電位時有較高的移除率;然而,在混合研磨液時,須有一定的熟成時間(aging time as conditioning),界達電位才能達到平衡。所以,利用分析儀器檢查的研磨液品質,研磨液的管理就顯得十分重要。
圖八、界達電位熟成時間(上圖),及其與移除率之關係(下圖)
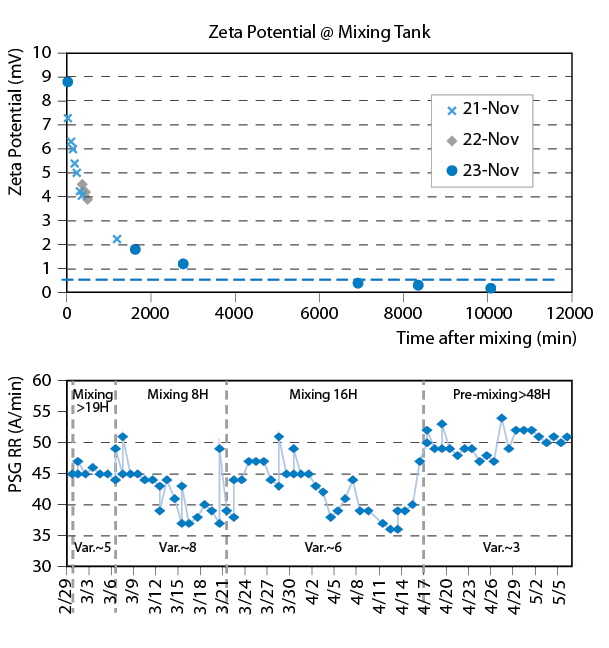
此外,經由幾個桶槽之間切換,可連續供給研磨液。批次混合是最常見的技術,即使一些即混即供的混合技術最近已經出現。批次混合仍具有優點,可允許一些備份存儲,有兩個主要的方式可替代批次混合:
- 研磨液在一個桶槽混合,然後使用泵輸送到供應槽 圖九。
圖九、研磨液供應系統
- 研磨液使用混合/供應兼用的桶槽。至少兩個桶槽,每個桶槽交替使用於混酸供應。當一個桶槽是在供應模式,第二個是在混合模式下,或在等待模式。
第二種替代方法具有的優勢來管理研磨液壽命。當桶槽完成其供應步驟,它可以使用純水清洗,並準備混酸步驟。我們可以決定啟動或延遲時間,以更短的混酸後等待時間,讓研磨液盡可能保持新鮮度。供應研磨液的另一種方式是使用線上混合技術(static Mixer),在供應端(POU)線上即混即用,線上混合有幾個優勢。
- 多種原液混合配比容易,混合比例可變化設定
- 研磨液新鮮混合,即混即用,混合快速
- 研磨液混合過程無剪應力,無泡沫產生
- 混合比例濃度精確
- 無機械裝置,低故障
研磨液供應技術最重要的方面之一是輸送環路,研磨液根據一定的流速範圍需要不斷再循環。供應方式包含單管迴路及雙迴路。
新的研究利用超音波震盪器,將凝聚研磨粒子再重新分散, 圖十為超音波震盪器組裝的方式,可組裝在桶槽內或外掛在循環管路或是連續流動的管路上。
圖十、超音波震盪器組裝的方式
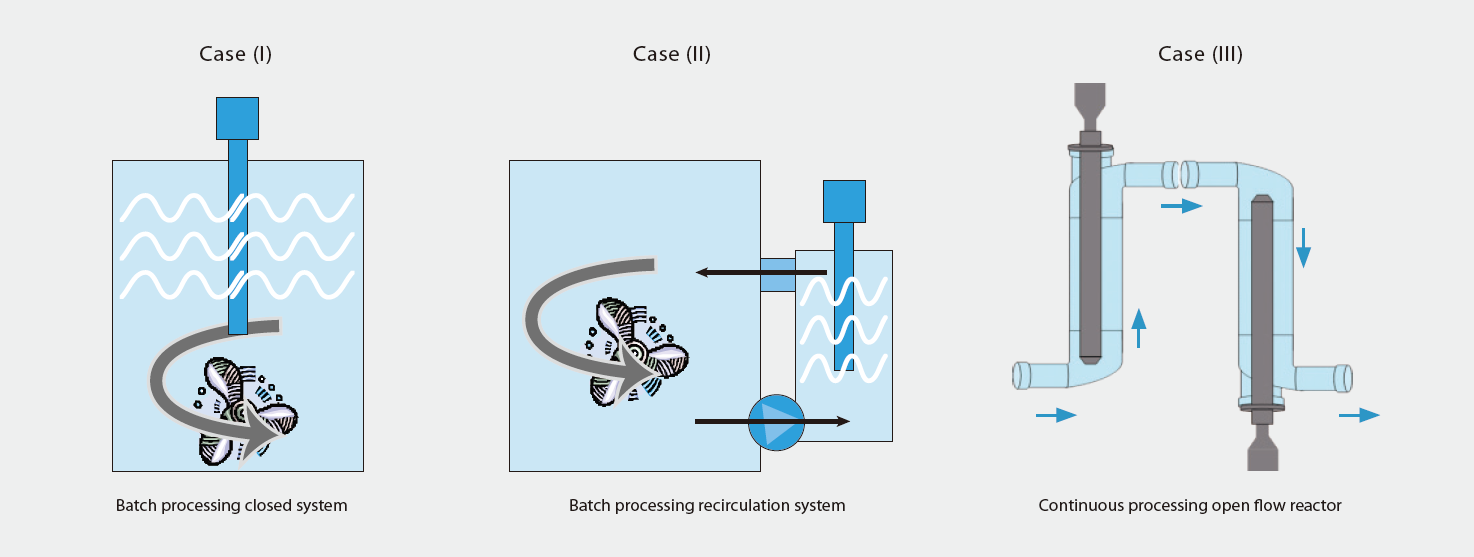
圖十一為目前初步進行超音波震盪器的研究結果,有效將凝聚粒子轉變為工作粒子(working particle),且研磨液之粒徑有顯著的改善。不僅能改善大顆粒子數(large particle counts),過濾時亦能降低濾心的負荷量,未來若能引入研磨液供應機台內,對於線上良率將有莫大的助益。
圖十一、使用超音波震盪器前後之粒徑分佈及大顆粒子數的變化
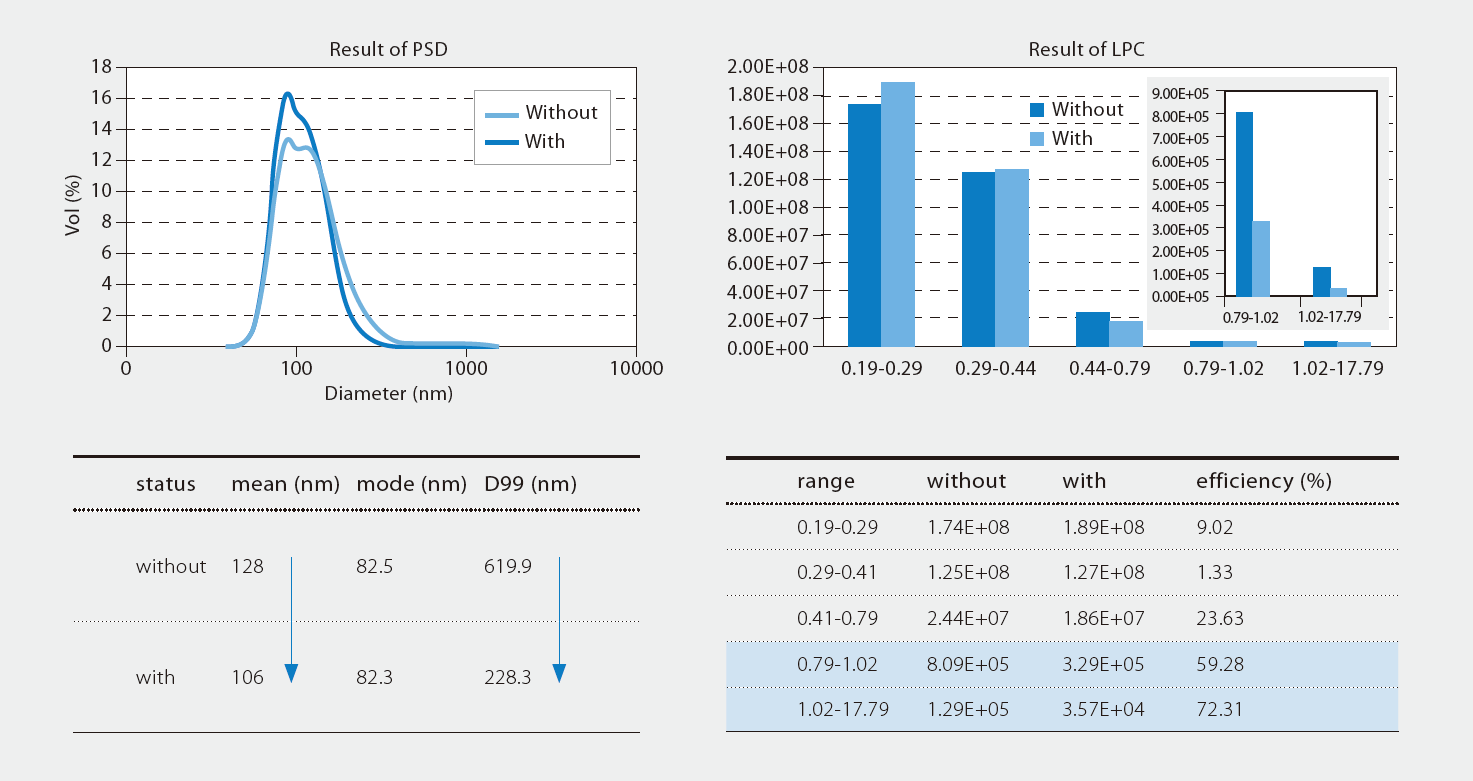
供應的流速會影響研磨液的品質,必須視研磨液特性調整最佳流速,若控制不當則易形成凝聚而影響製程良率。對於二氧化鈰(CeO2)為基底的研磨液(Hitachi 9201、Asahi F2.5、F4.0)和氧化鋁(Al2O3)研磨液(Cabot A7100),由於磨料(固體含量)是相對沉重顆粒物質,研磨液供應管路循環迴路需要保持流體雷諾數高於9000(液體流動形成紊流turbulence flow)的流動避免沉澱。概略而言,上述CeO2的管路循環流速需達到1.4 m/s和Al2O3在1.2m/s。 圖十二實驗說明以(CeO2)為基底之研磨液,在低流量時(17 LPM),界達電位(zeta potential)呈現較不穩定的現象,且研磨粒子粒徑(D99)也逐漸變大,若將流量調整至30 LPM,較能維持研磨粒子穩定性及其粒徑大小。
圖十二、研磨液在不同流速下之D99 及界達電位的變化
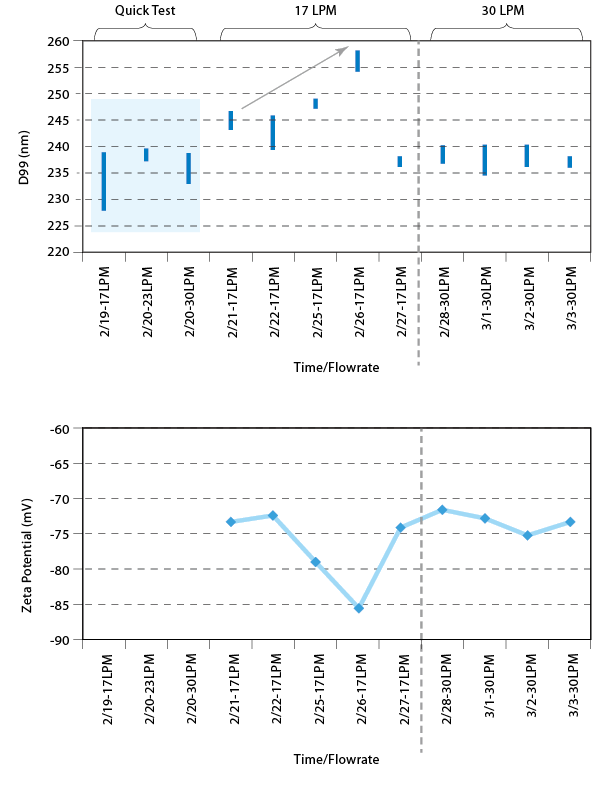
二氧化矽(SiO2)為基底的研磨液(Cabot SS12、JSR K1)從他們的凝集特性來看,過於激烈攪動會破壞添加劑(Surfactant)的磨料外層保護,進而使二氧化矽本身增長較大顆粒,因此不可使用過快速度,避免循環供應管路上大顆粒增長,大致而言,流動速度應為0.5m/s以上到0.7m/s之間。
部份先進銅製程研磨液含有許多的有機添加劑(如介面活性劑、抑制劑等),大量循環時(包含使用磁浮式離心泵),因剪切力及有機添加劑分子間頻繁接觸,進而在循環管路上造了很多氣泡,泡沫嚴重影響研磨率(Removal Rate),甚至造形成大顆粒子。加速研磨液品質衰退,減短使用期限。氣泡產生部份原因是磁浮式離心泵過熱造成過氧化氫分解加速。必要時使用熱交換器,PCW或冷卻水,冷卻研磨液。為抑制過氧化氫分解,研磨液溫度宜維持低於23℃。另外為避免供應管路循環形成泡沫,操作條件至少需要0.6〜0.7 m/s,如此可兼顧避免形成剪應力和氣泡產生。
討論與結論
化學品和研磨液供應/混合技術,在過去的15年已有長足的發展,藉著閥件及各項元件的進步使化學品和研磨液供應設備商設計製造完整系統,以滿足使用者更嚴格的規範,如流速、壓力控制需求、減少的離子污染物、降低微粒子,並提升化學品潔淨度…等。然而,為使設備設計的系統更可靠、使用更便利、更清潔、更容易控制、和更具價值性,未來,混酸設備和循環供應的設計方法將持續朝以下幾個方向演進:
- 使用低壓降有效地提供供應大流量;
- 將循環迴路使用磁浮泵,並增加流量和壓力控制;
- 過濾步驟清潔和未清潔前化學液體管路獨立分開;
- 增加純化精製速率;
- 增加先進監測儀器,控制化學品質;
- 建立備援模式,以減少停機;
- 使用完整的連續穩流循環迴路;
- 提供強大的智慧監控網絡系統,精確的檢測儀器,建立可靠的化學品的供應管理;
- 探討未來引入研磨液利用超音波震盪器,將凝聚研磨粒子再重新分散。
參考文獻
- Boni Guarneri, Jean-Louis, Air Liquide Advanced Chemical and Slurry Dispense System, 2011.
- Boni Guarneri, Jean-Louis Marc, 2012, Particle management in slurry.
- G. Bahar Basim, 15 February 2011, Effect of slurry aging on stability and performance of chemical mechanical planarization process, Advanced Powder Technology Journal.
- S. Raghavan, M. Keswani, R. Jia, Department of Materials Science and Engineering, The University of Arizona, July 2, 2008, Particulate Science and Technology in the Engineering of Slurries for Chemical Mechanical Planarization.
- Jo De Messemaeker*, Fabrice Sinapi, Patrick Ong, Stijn Put*, Daniël Nelis*, Jeroen van den Bosch*, Yvan Strauven*, Paul Lippens* and Katia Devriendt, Olen, Belgium, International Conference on Planarization/CMP Technology • October, 2007 Dresden, Impact of ceria properties and CMP parameters on STI CMP performance.
留言(0)