摘要
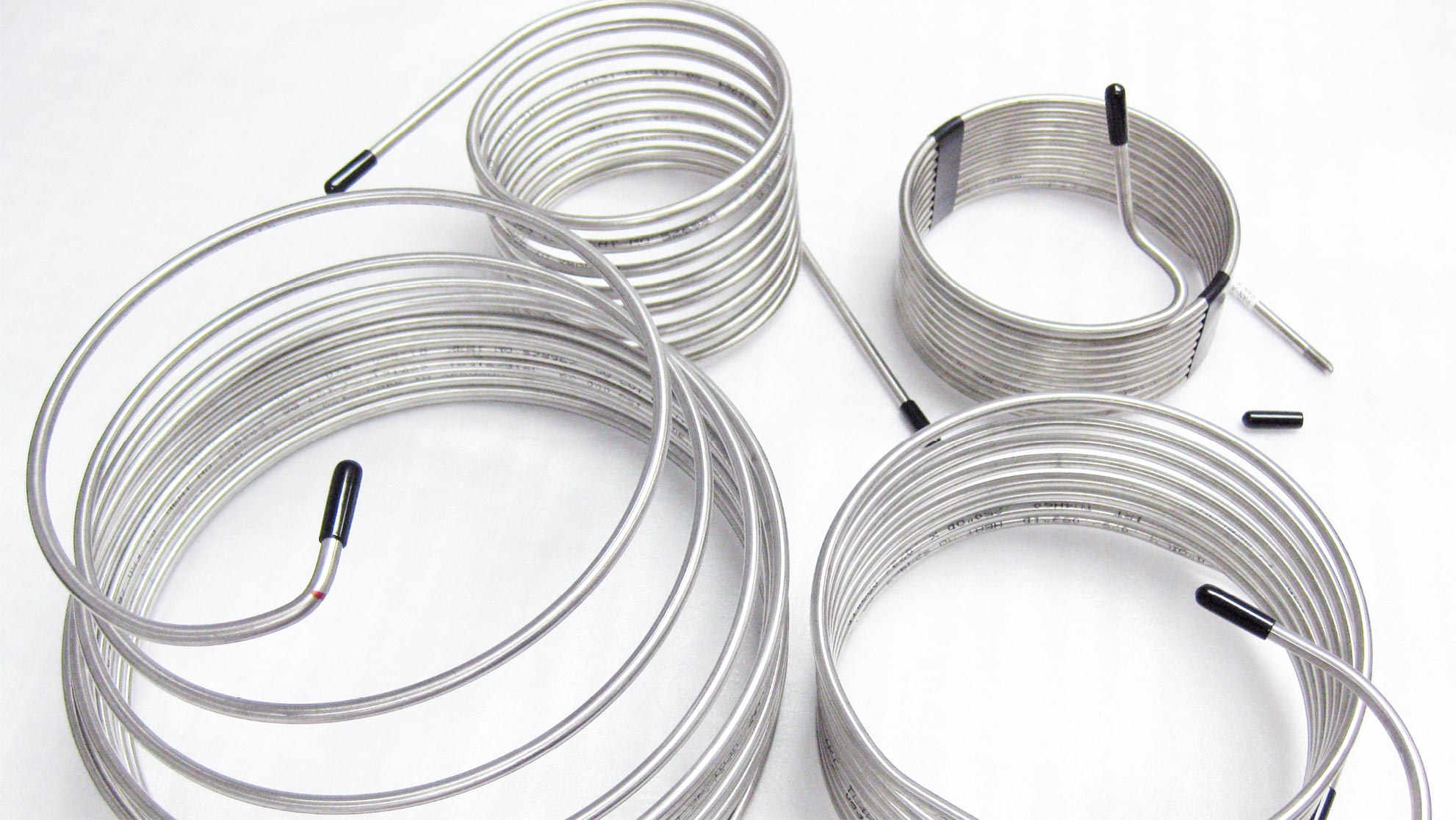
無縫盤管應用在氣體配管的可行性評估
Keywords / Coiled Tube、Straight Tube、Double Tube、Weld Zone
目前廠內使用的特殊氣體管路都以四米不銹鋼管路銲接施作方式,為其主要之工法,而其氣體管路總長度都超過百米以上,所以管路銲接的點數非常之多,耗費甚多人力與機具用以進行管路施作與品質控管。而銲接的點數過多就會有品質與安全的風險疑慮,可能會造成管路銲道的內部氧化與外部腐蝕。本研究使用無縫的不銹鋼盤狀管路(Coiled Tube),用以取代四米管路銲接施作方式,此類管路將減少整段氣體管路的銲接點數,亦可減少人力與機具的耗費並縮短工時,同時可有效確實的降低管路內部的氧化與外部腐蝕的疑慮。
前言
研究背景
因資訊產品的發展日新月異,消費的需求越加複雜,設計規格越趨精細嚴密,使得先進製程技術越加快速發展。先進製程比重亦越持續倍增,如浸潤式微影製程的發明,已將製程線寬縮小至奈米等級,其無論原料物料、製程設備、製程技術等都須要有更精密的規範與更嚴格的管理。其中特殊氣體是半導體製程最重要的材料之一,在製程線徑已縮小至奈米以下的今天,製程對氣體的品質要求越來越高,對不純物的規格要求由已往的ppb.等級提昇至ppt.等級。除了應探討提昇供應氣體的品質之外,要如何減少輸送管路對氣體的微污染,亦是目前極為重要的研究課題[1] [2] [6]。
研究目的
半導體製程氣體依照其特性可分為惰性、毒性、燃燒性、腐蝕性等,考量輸送的氣密性與安全性及減少對製程氣體污染的可能性,管路接續是以銲接為主。銲接雖能保證管路氣密性與安全性,但銲接作業卻是氣體管路安裝工程中最可能造成氣體品質污染的原因。
目前大部分的氣體管路的不銹鋼管採用每支4公尺的直管,任一管路從供應端到使用端都需數十口甚至數百口銲道,而隨著廠區的擴大,氣體管路長度亦隨之增加,銲道的口數也越來越多,更增加氣體品質污染的可能性。
盤繞管(Coiled Tube)依管材尺寸每卷長度為30公尺至200公尺,可減少銲接作業的需求。本報告從鋼管材質與銲接的相關性,施工方式與施工安全、施工時間的比較,材料與施工成本的分析,與Coiled Tube的使用限制,探討Coiled Tube取代直管的可行性[1] [2] [6]。
文獻回顧
無塵室先進半導體製程中氣體輸送的關鍵問題
氣體管路內的殘存水氣可能會和含鹵素的氣體起反應,造成管路腐蝕,逐漸影響關鍵組件的性能。管路內層表面通常容易捕捉水氣,因此,有些失效情況是由於氣體輸送系統中殘存的水氣與鹵素氣體如氯氣、氯化氫、溴化氫及反應性氣體如矽烷、二氯矽烷等的反應所造成的。必須注意的是管路閥件的腐蝕是一個緩慢漸進的過程,引起腐蝕與污染的表面缺陷,可能存在於氣體輸送系統中與其他組件的潮濕區域,例如:氣動閥、壓力調節器與過濾器,以及在管線的銲接處,而銲接處的受熱區域則特別容易腐蝕。
目前在文獻中關於臨界水氣含量造成的腐蝕,有許多方法可以降低其風險。第一個方法是改善所有關鍵潮濕表面的表面粗度特性,使水氣較易於烘乾。第二個方法是檢討某一可疑氣體輸送系統內烘乾水氣的淨化方法。對於氣體輸送系統,大部分現存的淨化方法已經使用超過十年,而這些設計原先是為了給可以忍受製程氣體流量重複性變異的次微米科技所使用的。藉由小心地探究淨化效率與改善設計,在水氣烘乾的效能上是有可能獲得數量級程度的改良。對於某些較新的半導體製程,會在超過175℃的高溫下使用,因此,這類閥門必須是耐用、不會散發微粒且高可靠度的。製造商已經設計了具有特殊隔膜與底座材料的閥門,其耐用程度高達2,500萬次開/關。由於污染的累增或隨時間逐漸發生的腐蝕,所造成製程品質上不可重複性的問題,有部份也是來自關鍵組件。如氣動閥、壓力調節器、過濾器等潮濕表面上的缺陷所引發的腐蝕而來。有些與腐蝕有關的問題可以藉由重新檢討、及微調現有的氣體管路淨化方法,以改善水氣烘乾特性來加以克服。除此之外,使用先進製程控制與偵錯及分類所建立的技術,來預測和氣體流量相關的問題是很重要的。具備預測氣體輸送組件問題的能力,可以幫助降低晶圓報廢和機台停工的成本。整合於氣體分配盤系統的圖形化使用者介面可協助預測關鍵氣體輸送組件和整個氣體分配盤的狀況[1] [2] [3]。
現行四米直管施作與盤管施作的分析比較
特殊氣體管路採用316L EP級不銹鋼,主要成份除Fe外其餘為C、Mn、P、S、Si、Ni、Cr、Mo。其中JIS-G3459 規範較高成份的Ni,具較佳的抗蝕性,故國內各半導體廠大多採用日系管材。
成份中Mn雖可提升鋼材的延展性與韌性,並降低鋼材的熱裂性。但在銲接時會氣化形成煙(fume),生成微粒子(Particle)披覆於內管表面。另外銲接中金屬重融形成的偏析,及內銲道的不平整,都會增加金屬離子溶出與腐蝕的機率。
而四米直管與盤管在管路材質與製造流程 圖一,表面處理上並無不同,差別只在於成品的長度不同。一般直管在抽管後裁切成四米一截,而盤管則可將管材盤成環狀至所需長度 圖二。
圖一、管路製造流程[5]
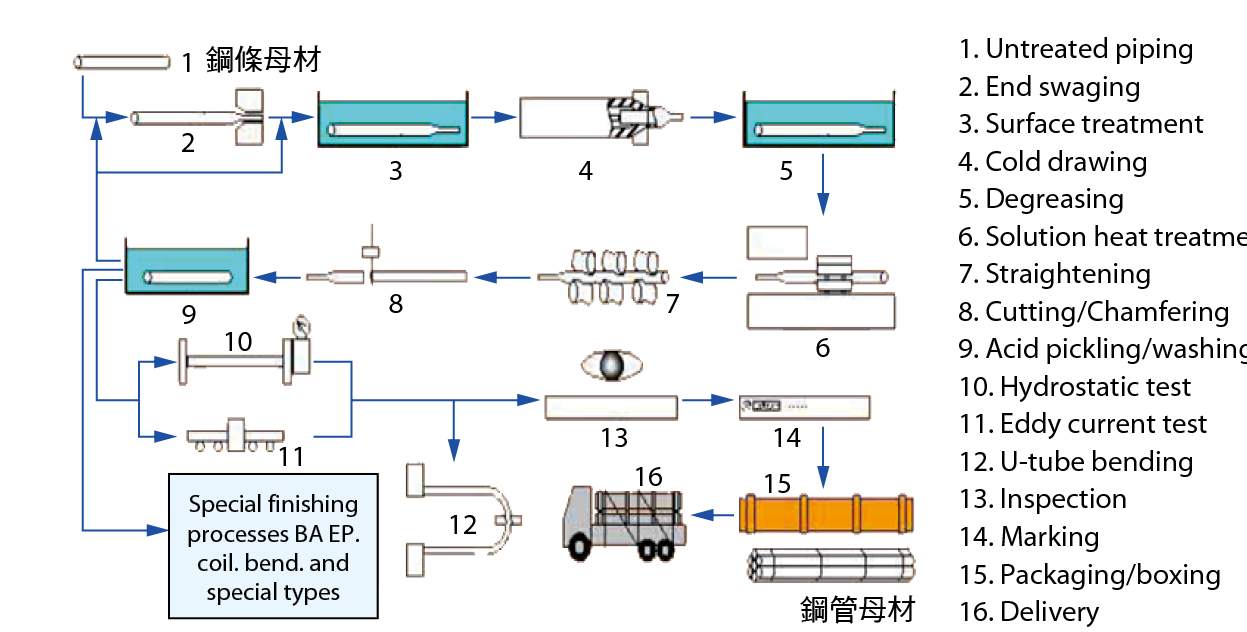
圖二、Coiled Tube 實品照片[7]
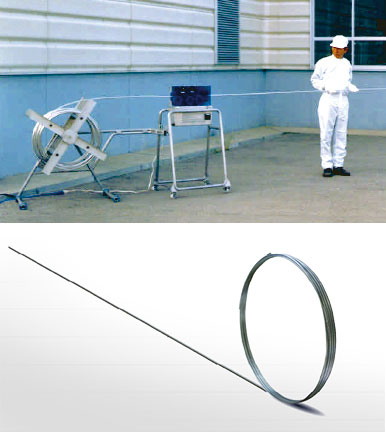
現行氣體管路施工方法
廠內現有的氣體管路施工使用四米直管銲接為主要方式,需要大量的銲接作業,故需耗費大量的時間與管材來製作銲接試片。且部分區域如需彎管作業時需進行切管、修整端面等作業。而基於安全上的考量,腐蝕性與燃燒性以及毒性、氧化性氣體管路皆採用雙層管路方式,其施工則更為繁複。
雙層管的設計方式如下。 圖三
圖三、各式雙套管設計方式[2]
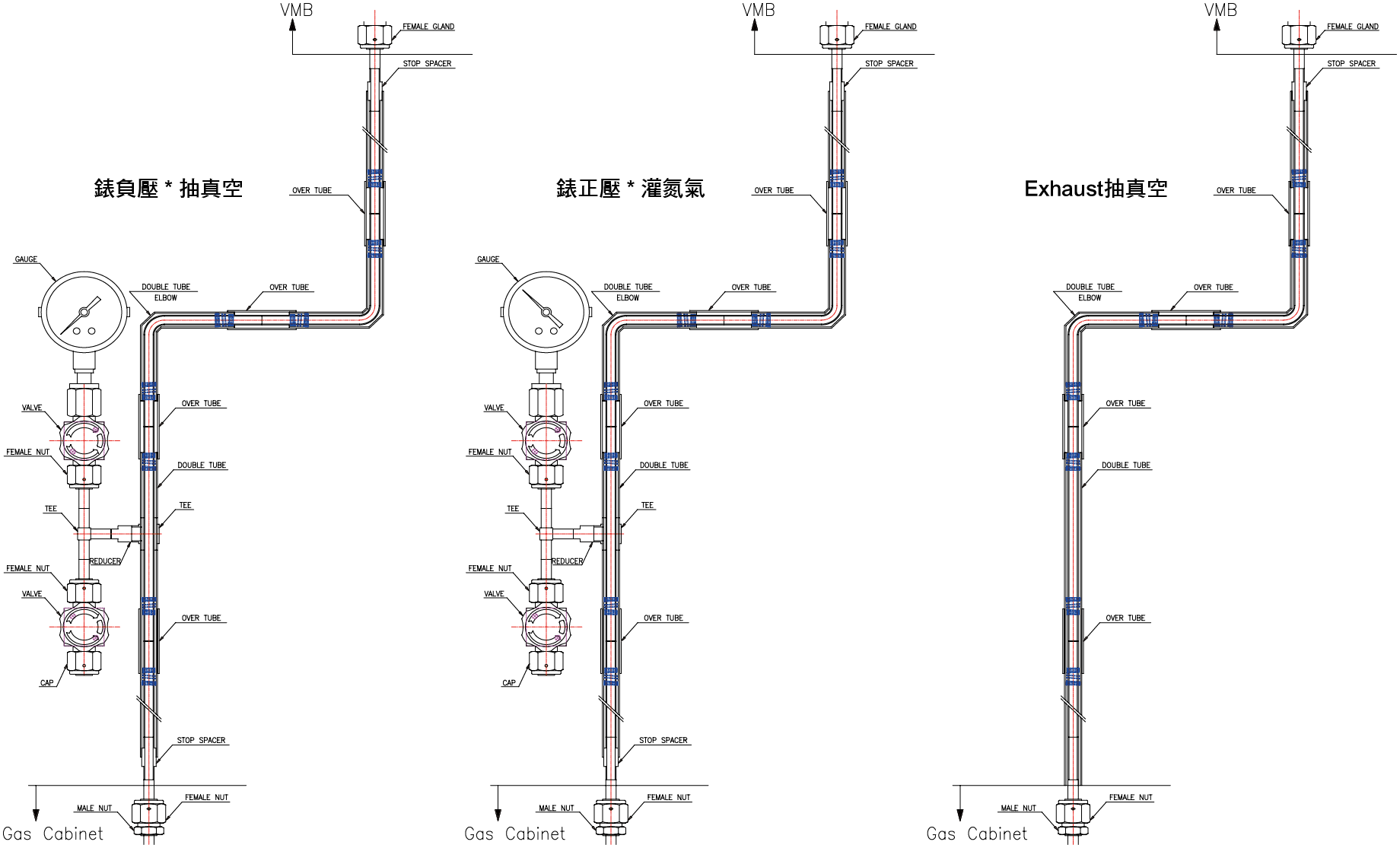
- 內/外管材質分別為SUS 316L EP / SUS 304 AP
- 外管內可抽成負壓或灌氮氣維持正壓
- 外管可接壓力錶或接抽氣(Exhaust)抽氣並連接氣體偵測器
雙層管的優缺點如 表一。
設計方式 |
優點 |
缺點 |
---|---|---|
負壓設計 |
靈敏度較高 若洩漏,不會影響製程 |
需要抽真空 若洩漏,易造成外管腐蝕 |
正壓設計 |
以PN2保壓方便 若洩漏,較不易造成外管腐蝕 |
靈敏度較差 若洩漏,會污染製程 |
開放式設計 |
簡單方便 |
危險性較高 無法迅速判定洩漏源 |
優點為
- 可避免外管直接受到撞擊
- 可將洩漏氣體阻隔於外管內
缺點為
- 擴充不易、施工困難、建製成本昂貴
- 洩漏源位置難以確認、維護困難且經費高
Coiled Tube的施工方式
Coiled Tube的使用材料與四米直管相同,同樣採用316L EP級不銹鋼,但其銲接施工方式較為簡單,只有管路開頭端與管路結尾端須以銲接方式與設備銜接(銲接點皆於設備內部),安裝時則以整直機將管路整直。因銲接點皆在封閉保護空間(氣瓶櫃或氣體閥箱)內,故目前設計上都只使用單層管,施工較為簡便 圖四。
圖四、Coiled Tube 氣體管路銲接位置[2]
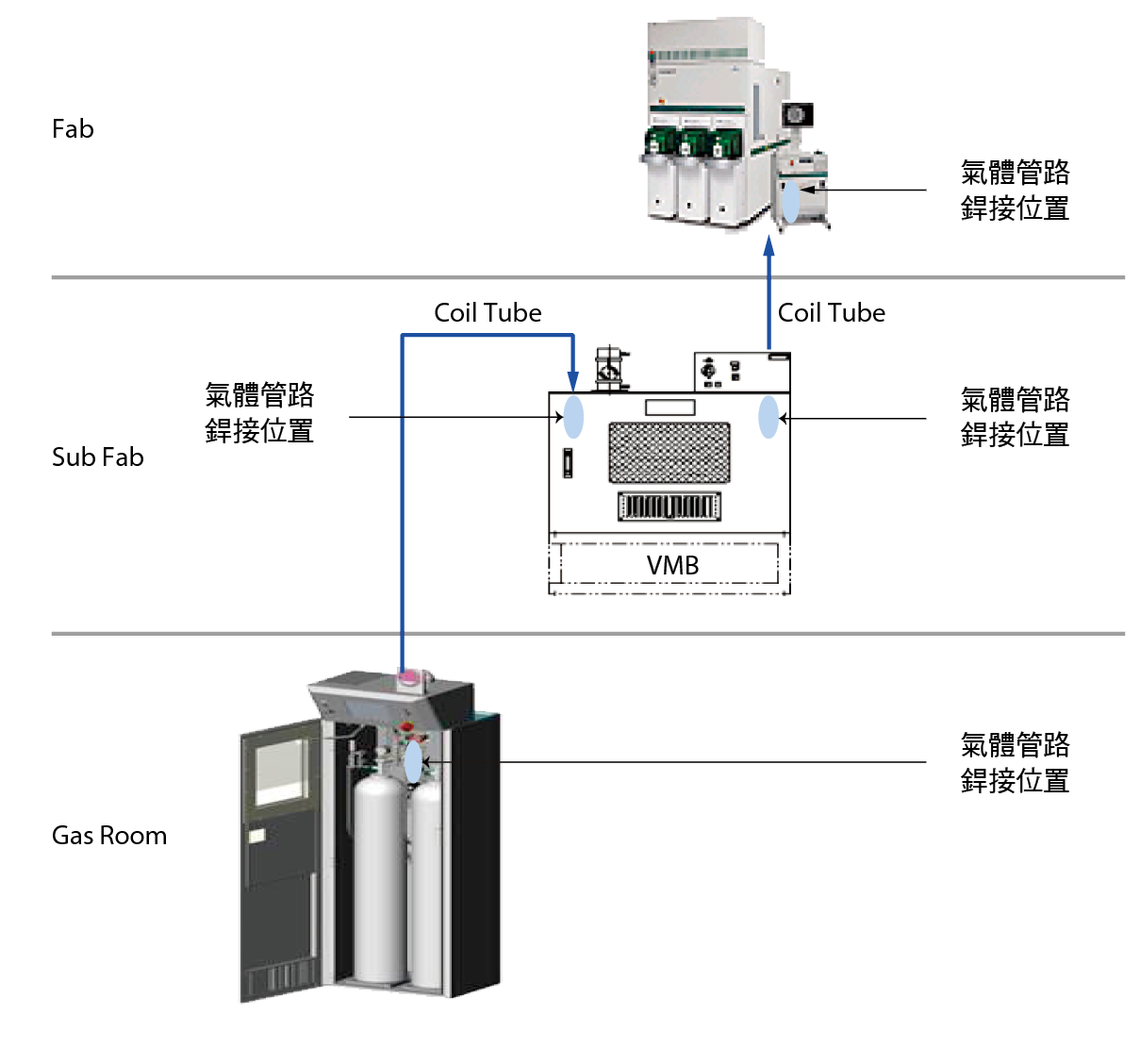
Coiled Tube在工程上的優缺點如下。
優點
Coiled Tube可減少大量的銲接作業,在工程上的優點如下。
- 提升管路品質
可大幅降低銲道與熱影響區附近的離子溶出與腐蝕的機率,減少製程氣體的污染,有效延長管路的使用年限。
- 節省材料耗損
大量減少製作銲接試片的材料成本。
- 節省配管工時
大量減少製作銲接試片的時間,以及管路銲接的總時數,故可有效提升工程進度。尤其在腐蝕性與燃燒性氣體管路取代雙層管路施工,更可節省一半以上的施工時間。
- 減少工安問題
大量減少配管人員在高處進行銲接的機率,故可大量減少高架作業的風險。
- 降低銲接風險
「銲接不良」是氣體管路工程主要的施工缺失,更經常因切管重銲造成微粒子(particle)污染、閥件內漏及工程進度延誤。採用Coiled Tube可大幅降低切管端面時對管內的刮傷機率、銲道的不良率、因銲接不良而切管或重銲的機率。
- 降低測試風險
可有效降低QC人員因測試技巧或程序不足,導致無法有效檢出「銲道微漏」的機率。
缺點
- Coiled Tube 除了成本上的考量外,管材有尺寸與長度上的限制 表二,因此無法應用在大流量需求的氣體管路,而在取代長距離的雙層管路時,可能須增設連接箱,造成工程成本增加。
表二、KUZE Coiled Tube EP 管製造尺寸與最大長度[7]
外徑×肉厚
(mm)
OD×WT
製造長度 Length (m)
30
50
100
150
200
6.35×1.0
Ο
Ο
Ο
測試中
Under trial
測試中
Under trial
9.53×1.0
Ο
Ο
Ο
12.7×1.0
Ο
Ο
- 進行管路安裝時需先使用直管器進行整管,增加施工設備成本。
- 管路上架時需單管拉設,而且從頭到尾依順序拉設不可間斷,無法分段施工將較耗管路上架施作時間。
- 因設計以單管施作無外管保護,故在安全上可能有安全上的風險考量。
成本效益與安全性及供應品質分析
Coiled Tube與直管的工程成本分析
- 材料成本
Coiled tube單價約(2100元/米)為直管的三倍。在一般氣體管路有較大的材料成本差異;但腐蝕性與燃燒性氣體、毒性氣體管路直管須採雙層管路施工,雙層直管及相關的管配件成本幾近於Coiled Tube。因雙層直管需要內管、外管、支撐彈簧及固定滑套,材料成本只低於將近Coiled Tube材料成本的15%。
- 施工成本
在一般氣體管路施工成本Coiled tube單價只佔直管的3/5以下,但腐蝕性與燃燒性、毒性氣體的Coiled tube與雙層管路施工比較,其相對成本可節省一半以上的施工成本。
因此總括Coiled Tube在一般氣體管路與直管工程成本大致相同,但在双層氣體管路則可節省更多的工程成本。
Coiled Tube與直管的施作工時比較
- 雙層直管的施作工時
因雙層直管除了內管必須四米一段一段銲接,所以其銲接所耗時間甚長之外,其銲道甚多故於氦氣測漏時間亦耗費甚多。且其尚需裝設外管故整段管路從上架、銲接到測試完成需耗費較多的工期與施工設備(如銲機與氦測漏儀),以及銲工人數增的加與試片銲接數的增加等。
- Coiled Tube的施作工時
而Coiled Tube的施作只需整管拉管,減少銲接數量與減少外管安裝,且所需進行氦測漏的銲道數量大量減少,試片銲接數量亦大量減少,故可大幅縮短施作工期,以及減少施工設備使用數量。
Coiled Tube 與直管的安全性分析
- 雙層直管的施作安全與供應安全風險分析
在施工建置時期雙層直管其銲接數量較多,所以其人工與設備機具數量同樣較多,故施作安全風險相對提高。
而運轉供應時期雙層直管的內管有外管的保護,在受到外力撞擊時與供應氣體洩漏時,會有緩衝間隙與時間,相對安全風險較低。
- Coiled Tube的施作安全與供應安全風險分析
盤管在施工建置時期其銲接數量相對減少很多,所以其人工與設備機具數量同樣減少很多,故施作安全風險相對降低。
而運轉供應時期盤管無外管的保護,在受到外力撞擊時與供應氣體洩漏時,會有較高的安全風險存在。
Coiled Tube 與直管的管路內部品質實驗分析
將有銲接銲道氣體管路與無銲接銲道的氣體管路進行腐蝕性實驗研究,以驗證銲接銲道增加腐蝕與金屬離子溶出的機率 圖五、圖六。
圖五、Coiled Tube 和直管銲道的腐蝕性研究試驗圖[5]
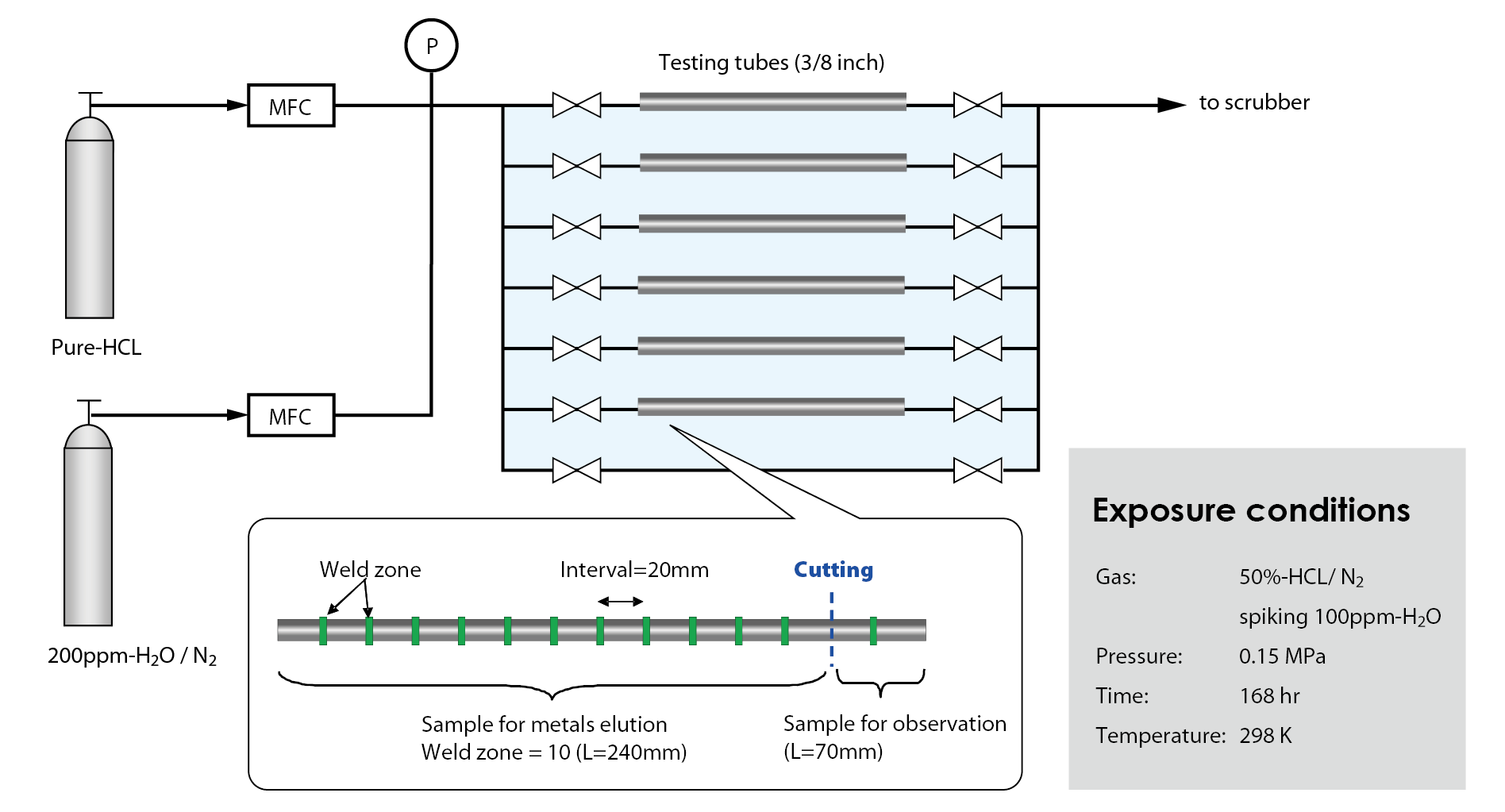
圖六、Coiled Tube 和直管銲道的腐蝕性研究分析[5]

- 大型微像攝影機檢視無銲接銲道管路內部表面正常 圖七。
圖七、無銲道腐蝕性分[5]
- 大型微像攝影機檢視銲接銲道管路內部表面有些微白點生成 圖八。
圖八、銲道腐蝕性分析[5]
- 掃瞄式電子顯微鏡檢視視銲接銲道管路內部表面同樣有白點生成 圖九。
圖九、管內腐蝕性分析[5]
- ICP-MS作銲道管內金屬離子成分分析 圖十。
圖十、管內金屬成分分析[5]
- 實驗結果發現銲接銲道已產生管路內部表面的化學變化,包括白點的生成,與金屬離子的溶出情形。這些情況也就會導致管路銲道的腐蝕與供應氣體的汙染,將會影響到氣體供應的安全與氣體供應的品質,甚至影響產品良率。
結論
Coiled Tube在施作上有施工方便與快速,以及施作成本較高等特性,若要使用於廠內,則建議使用在燃燒性以及毒性、氧化性等氣體管路,若以近期新建廠的裝機速度做比較,尤可應用在二次配管的快速配管需求。然而因其有管徑與管長限制無法使用於大流量、遠距離之氣體(如SiH4/HCL/NH3/NF3等),以及一般氣體與惰性氣體管路因成本與管徑問題無法使用。而腐蝕性氣體有安全疑慮考量,目前亦暫不建議使用。
理論上Coiled Tube本身並不存在從外部腐蝕或內部滲漏的可能性,唯在施工上若有不當的動作行為造成管路表面的嚴重損傷,又或者是管路環境存在著會造成管路腐蝕的危險因素,如此情況下無外管保護的Coiled Tube,在防止氣體洩漏的安全風險上相對提高,故在既有的安全風險考量模式下,若輔以施作外管保護雖然技術上可行,但其施作成本與施作時程亦將增加,所以若針對腐蝕性氣體的適用性,還須長時間的實驗與評估其可行性。
Coiled Tube在氣體管路的應用,具有減少離子溶出與腐蝕的機率、提升管路品質及提升工程進度等優點。
以日本為例,其管路銲接的施工成本極高,因此採用Coiled Tube可節省大量的施工成本,而被廣泛的應用,包含 Sharp、FUJITSU、Mitsubishi Electric、Toshiba、Panasonic、Epson等等。而在台灣則有Power chip、C.P.T、Micron,另外韓國Samsung Electronics亦從2013年開始採購Coiled Tube,Intel於2014年已開始進行評估,應是重視Coiled Tube在先進製程中減少金屬離子溶出的優點。
綜合上述各種結果,針對先進奈米製程上,可考慮使用Coiled Tube,但不建議加裝外套管,因廠內的無塵室存在不安全的人為及設備與環境的風險甚低,且參考國內與國外的使用經驗亦無曾發生過因Coiled Tube造成的氣體洩漏危害情事。而在施作成本與工時以及施工安全的層面上,也應考慮Coiled Tube的相對實用性,使其做為晶圓廠的氣體供應管材。
未來發展方向將與管件供應商及氣體供應商合作,進行材料分析,包含彎曲金相測試、腐蝕測試、抗拉測試、衝擊測試等。並於工研院,中鋼、金屬中心等公正檢驗機構進行相關測試,確保實驗之正確與完整性,以達Coiled Tube可行性評估程序之完整。
Subject |
直管(傳統4米銲接管路) |
盤管(Coiled Tube 100米) |
---|---|---|
真空抽氣時間 |
≤ 6 hours |
≤ 2 hours |
真空度 |
1×10-9 atm.Cc/sec |
1×10-9 atm.Cc/sec |
氦測漏總點數 |
26點 |
2點 |
沖吹時間 |
≤ 36 hours |
≤ 8 hours |
含水量 |
≤ 10 ppb |
≤ 10 ppb |
含氧量 |
≤ 10 ppb |
≤ 10 ppb |
微粒子含量 |
0.1μm ≤ 0 pcs/scf |
0.1μm ≤ 0 pcs/scf |
參考文獻
- 陳清庭,氯氣氣瓶櫃洩漏危害分析與改善研究,工業安全科技,2006. June。
- 吳志平,特殊氣體供應系統規劃與設計,2001,工研院電子所。
- Hubert Dinh, Mohamed Saleem, Sowmya Krishnan, Ultra Clean Technology [無塵室] 先進半導體製程中氣體輸送的關鍵問題2008/7/24:半導體科技。
- 全華科技圖書股份有限公司,配管實務設計。
- TAIYO NIPPON SANSO, Evaluation of coiled tube corrosion-resistance characteristics 2013. JULY.
- 徐偉翔,加熱用於特殊氣體管路附著去除效應“工業安全衛生月刊”2012. Oct.
- KUZE BELOOWS KOGYOSHO CO., LTD.
留言(0)