摘要
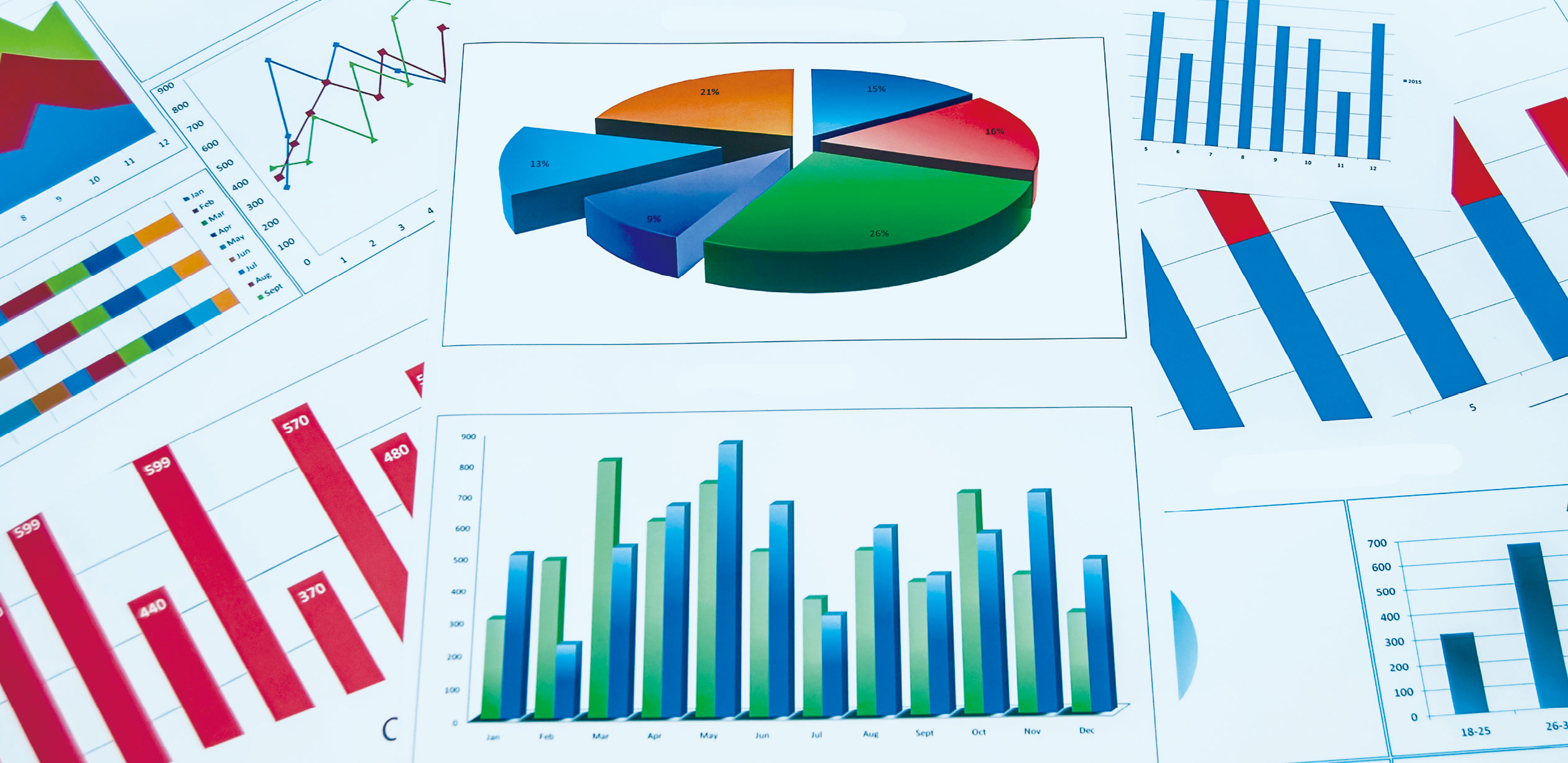
隨著製程微型化演進,任何細小的參數變化皆會影響製程的良率與機台效能。製程研發階段時,機台端及廠務端有即時偵測系統進行製程環境及供應系統參數監測,但是在兩者之間的裝機管路沒有即時監測系統或使用機械式元件,當產品有異常時,會發生資料不及時以及精準度不佳,無法符合需求。因此針對不同製程機台定義需監控元素,在管路適合位置安裝數位感測器,藉由資料擷取(DAQ)將數位感測器採集管路供應參數,通過資料分析系統即時回傳,再由錯誤偵測與判斷系統(FDC)進行監測,藉由電腦系統將數據進行即時錯誤偵測與分析資料是否離群,透過數據分析了解機台及裝機管路狀況,達到即時及預測製程品質目的。
前言
機台及廠務供應系統針對重要參數皆有安裝數位感測器進行即時監控已及參數預警,故障分析。二次配裝機管路,是連接供應端廠務系統及使用端機台的管路工程,以往要求是使用機械式感測器,採取定時抄表或是有問題時到現場檢查,然而隨著產品精密度增加,在製程時發現裝機管路的管徑,長短及所在位置會對生產良率有細微影響,因此裝機管路被要求比照機台端及廠務系統對其控制參數使用電子式感測器進行控管 圖1,利用電子式感測器,遠端即時監控系統,監控供應系統細微的變化並透電腦系統將數據進行分析是否離群及早發現異常,邁入更有效生產管理來提升產品良率。
圖1、二次配管路安裝電子式感測器
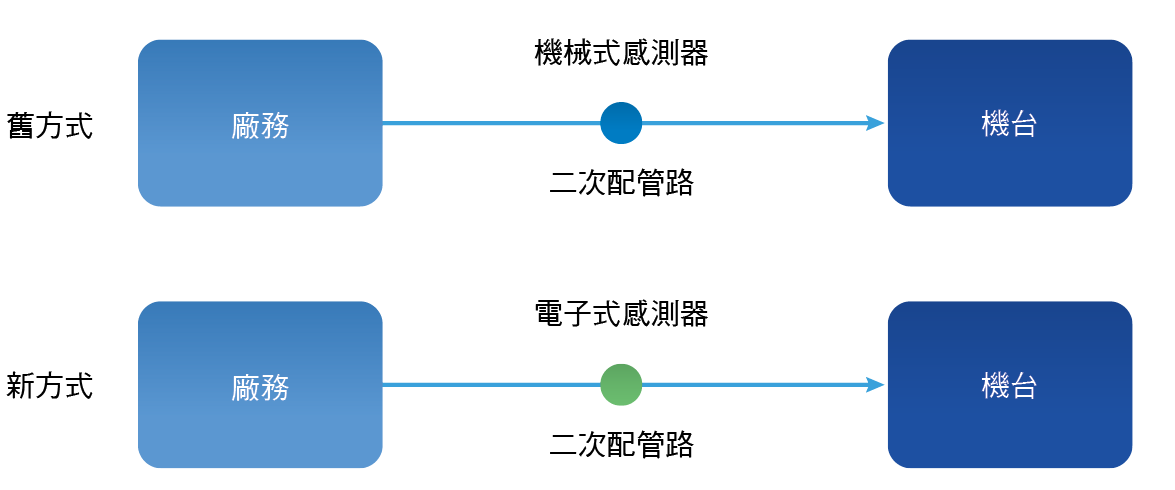
計畫方法
E-senor基礎硬體主架構 圖2,依功能流程區分為五部分:
圖2、E-senor基礎硬體主架構
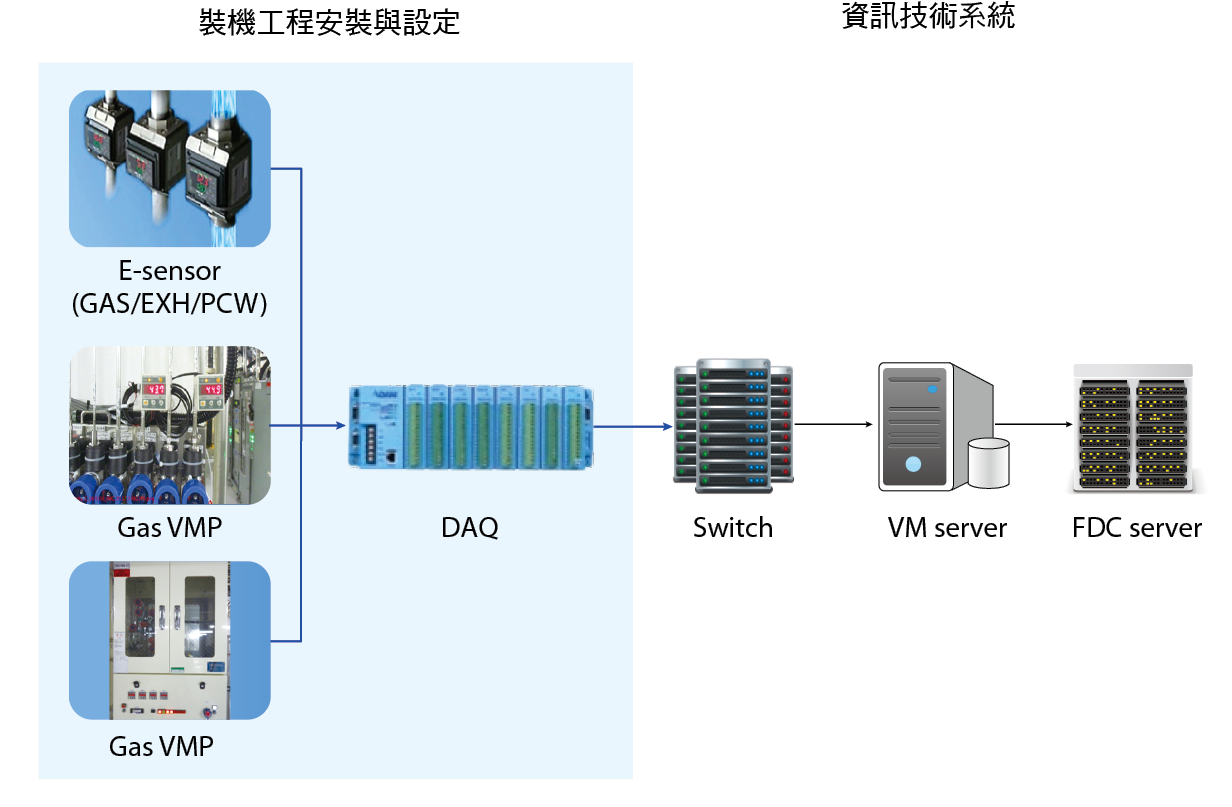
- 電子式感應器:依據機台不同製程需求,定義機台與廠務二次配管路所需安裝元件及位置進行資料收集。
- 資料搜集器:藉由訊號線連接,將此機台所有訊息傳至「資料搜集器」(Data Acquisition, DAQ)。
- 交換器:整合各機台DAQ資料透過「交換器」(Switch)將生產線中各式感測器所蒐集的資料統一整合。
- 資料整合中心:具有較高計算能力電腦軟體整合伺服器,整合更多交換器資料作為FDC運算基礎資料。
- 資料判讀中心:「失效偵測與分類系統」(Fault detection and classification system, FDC),收集製程機台之即時資料,將重要參數及步驟,進行監控與異常偵測。若有發生異常系統立即發抒警訊並對產品,與機台採取適當應變措施,避免異常產品持續發生。
系統建置至今經歷二次架構更新,初期架構建置完畢施工過程發現三個問題:
- VMP原設計為機械式表頭,安裝時會將機械式表頭拆除改為電子式感應器,雖然VMP是供應惰性氣體,但是拆除已供氣盤面會有破壞VMP結構風險。
- VMB是一個盤面供應給許多機台,位置分散於「次潔淨室」(Clean sub-fab),由分散區域銜接至機台端DAQ,距離及成本可觀。
- DAQ依據銜接點Port點數量有8CH,32CH,64CH三種規格,當VMB/VMP銜接回來,大部分機台皆需使用到64CH,成本增加。
針對這些問題經討論進行架構更新 圖3。
圖3、第一次更版E-senor 基礎硬體主架構

- 不進行機械表頭拆除,直接於VMP出口加裝電子式感應器,降低拆除及安裝風險。
- 運用廠務VMB即有訊號傳輸迴路,在廠務端加設Local伺服器,在銜接至FDC伺服器。
- 藉由VMB傳輸路徑改變減少傳輸Port數量,降低DAQ點數。
系統運行後又發現二個問題,因此進行第二次系統架構改版:
- Local伺服器是裝機工程購買進行安裝,但是網路系統並不是裝機工程專業,導致後續維護,網路更新無法同步執行。
- 為配合VMB分散於各處的特性,所以伺服器也需分區規劃數套安裝於現場,硬體及軟體成本昂貴。
針對這些問題經討論進行第二次架構更新 圖4。
圖4、第二次更版E-senor 基礎硬體主架構
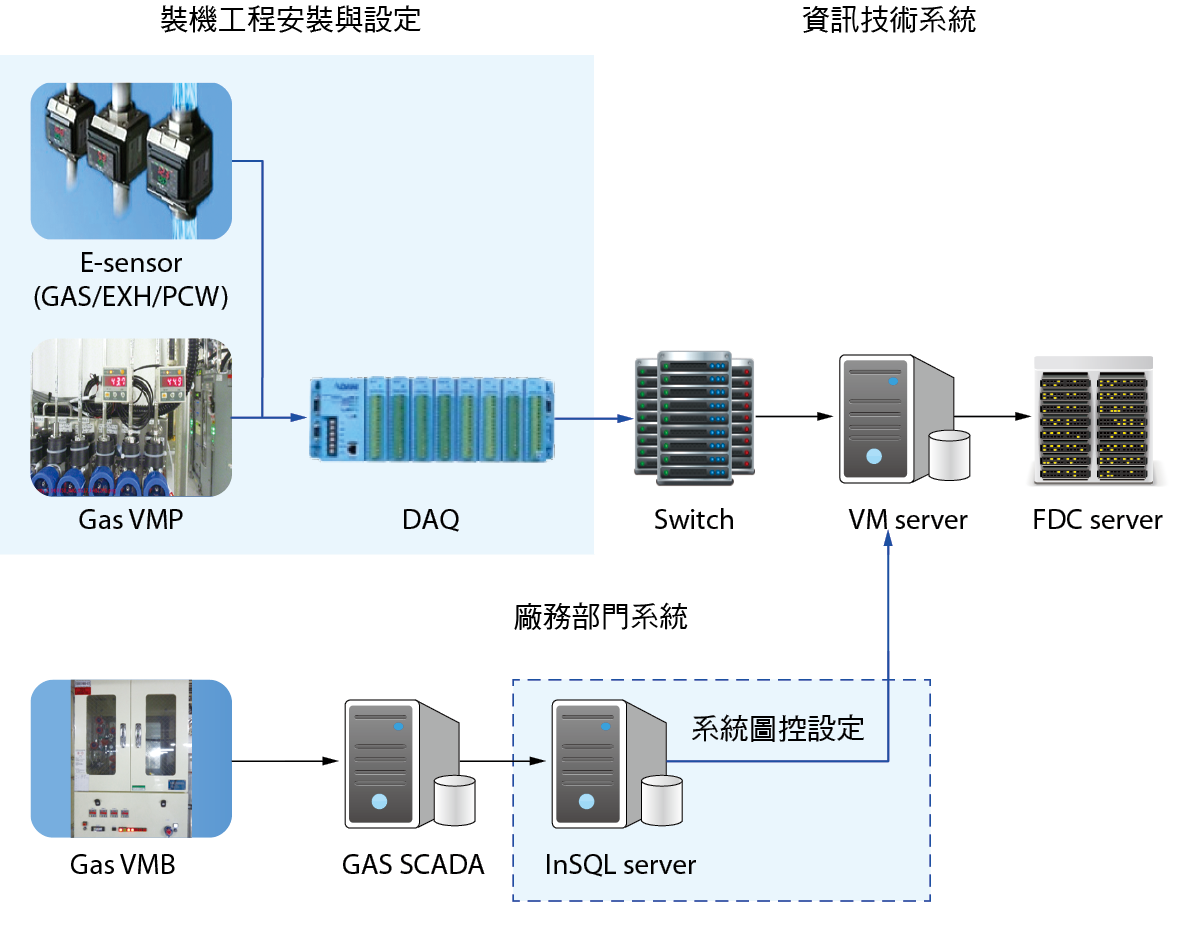
- VMB系統原本就有網路架構連接到VM伺服器,經與廠務及IT部門討論,藉由原VMB「可程式邏輯控制器」PLC (programmable logic controller),將訊號傳遞至廠務氣化課SCADA (supervisory control and data acquisition),廠務InSQL伺服器與IT VM伺服器進行連結,新增控制點數由兩系統原預留點或新增點執行。
- 機台安裝完成後裝機工程課將相關資料進行圖控設定,連結InSQL伺服器及VM伺服器。
結果與分析
利用FDC系統建置管理參數,可達到兩項控管目的
- 利用即時資料可進行裝機管路及機台內部資料參數比對,達到及早偵測目的。
圖5為機台端與二次配管路端氣體供應管路壓力圖,機台控制He氦氣的「質量流量控制器」(MFC)閥件開啟時,依據流體力學白努利原理,流體的速度增加時,流體的壓力能或位能總和將減少,機台內連管路測壓力會由32psig降至約29.5psig穩定此壓力。
圖5、機台chamber A 與二次配管路He 壓力比對(psig)
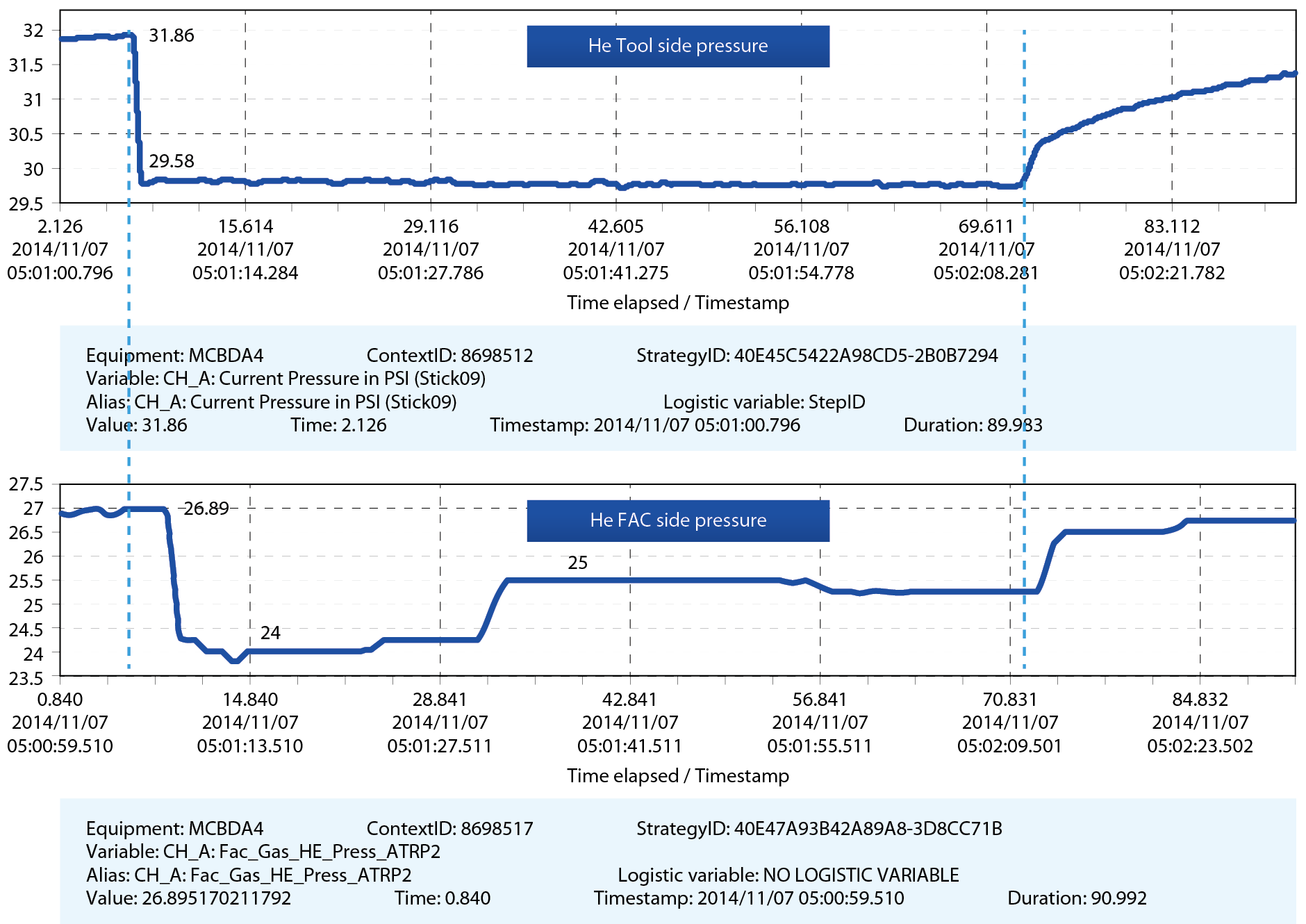
二次配管路e-sensor偵測內壓力緊接著,壓力會由26.89psig迅速降至約24psig,再緩升至25.5psig,當完成製成後MFC關閉後,管內壓力回至原始狀態,實現人員對機台設備及二次配管路的統一監控管理。
- 利用FDC 大數據資料進行分析,可集合眾多機台比較數值是否離群及早發現異常,並從中取得有價值得見解。
圖6為兩機台製成腔體A/B/C氬氣供應壓力分析資料,不同顏色代表氬氣供應壓力於機台製程腔體, Tool B生產記錄數據分析得知氬氣工應壓力已離群,以及供應壓力不穩定,製程腔體C供應壓力已超出同型機之標準。
圖6、同型機Chamber A/B/C 氬氣供應壓力比較分析(psig)
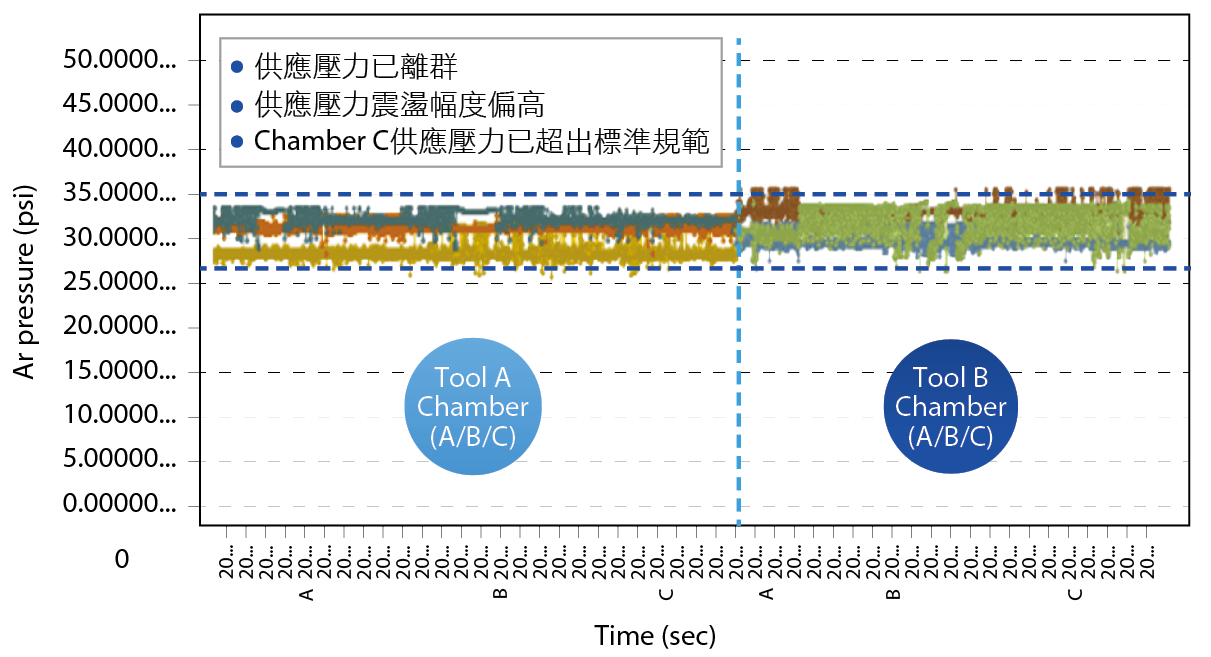
結論
利用e-sensor強化監控機台運作過程,實現遠端監控、降低營運成本,控管二次配管路之供應參數,精確掌控產品生產品質。巨量資料必須藉由計算機對資料進行統計、比對、解析方能得出客觀結果,大數據的技術與方法持續優化生產方法,尤其在半導體製造上持續產出大量、多樣、即時數據,從這些巨量資料中發現優化製程、改善良率的關鍵程序,再從數據裡挖掘創新商機與更高的產量與獲利資訊,即時記錄製程機台的運行狀態,搭配大數據分析找出製程優化關鍵。
巨量數據分析可以切割成現場即使生產所使用的分析結果、與生產記錄數據的分析結果兩大塊,針對生產線長所需的即時數據需求,可在機台採集生產數據送至伺服器時,即直接運用即時報表產生視覺圖形呈現,讓生產線主管可以透過資訊面板在巨量資料中快速查找問題、同步監控。
卓越企業應該是「決策型組織」,每個人都可參與決策,裝機課不僅只負責裝機,透過e-sensor累積大量的動態數據進行分析,做到提早預測可能出現生產問題的設備狀態與參照歷史資料預知可能錯誤狀態,進行新廠管路設計,與舊廠區管路調校改善,才能因應時代的快速競爭,掌握決策契機提升台積電的製造智慧。
參考文獻
- 徐明照、朝永成,"Run-to-run control簡介與APC framework架構設計",機械工業雜誌 258期 (2004年9月)
- 劉廷哲 SMD自動化測試機台之設計與實現,碩士論文2013年9月
留言(0)