摘要
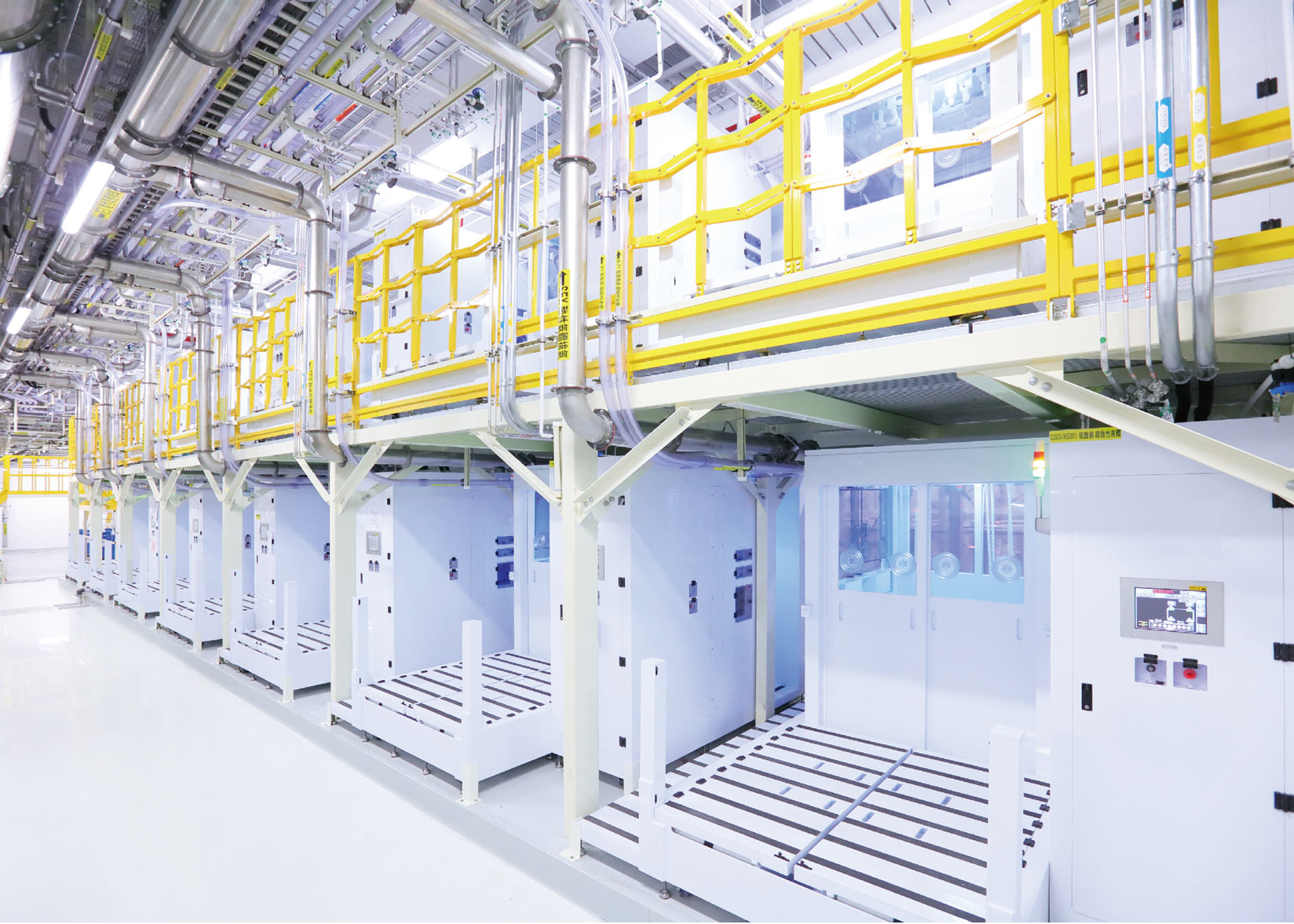
因應研發先進製程轉量產之氣體與化學供應系統運轉策略
Keywords / ICAM Definition Languages (IDEF),Gas and Chemical System,Copy Exactly,Mass Production
本研究使用目前業界廣泛應用於製造流程分析的 IDEF0 建模方式,在半導體研發製程轉大量生產過渡期間,將氣體與化學供應系統運轉方式,分為三個主要階段及五個次要程序。根據最新廠區運轉經驗及結合各廠區相關專業同仁的意見,將廠務端的氣體與化學供應系統,在 IEDF0 建模所列出各個階段中,將可能發生的運轉風險及應對方法加以彙整。最後總結出五大運轉問題以及十一項相應對的運轉策略與建議,供後續新建廠設計及運轉單位之參考。
前言
研發轉量產流程概述
當今半導體製造產業競爭激烈,除了在研究發展上需取得技術上的領先之外,如何迅速地將最先進的研發技術轉化為大量生產,即時滿足客戶需求,是全球半導體業界中取得領先勝利地位的重要因素。一座晶圓廠從開始設計、發包、建廠、裝機到正式量產約16至18個月,在這段與時間賽跑的期間,廠務系統的建置為整個專案的第一棒,當中又以對製程良率敏感的氣體與化學供應系統為最重要的關鍵之一。新專案流程一開始,公司在新製程需求掌握度約80%的研發階段,廠務的氣體及化學品供應系統即需著手設計與發包作業,並於生產機台進機前45天完成接近90%的硬體架構設置。當機台開始陸續進廠裝機後,工廠的產能便會迅速ramp-up,並以研發階段最佳化的製程配方(Recipe)與幾近100% 的機台產能利用率全力衝刺生產。在這段由研發到生產線的技術移轉階段,廠務系統嚴謹的操作管理模式及運轉方法論,是讓工廠穩定快速提升產能不可或缺之要素。
失效的完整複製模式
完整複製模式(Copy Exactly)指的是將研發廠內所有的製程配方與機台參數設定等,完整原封不動複製到新建置之量產廠上,讓量產廠能按照這些研發配方參數將最新的產品大量生產[1]。此技術移轉及量產化模式過去多次成功地運用在整合元件製造商(Integrated Device Manufacturer, IDM)之晶圓廠,然而對於近幾年所建置的超大型先進製程量產廠GIGAFAB®而言,此模式已逐漸無法符合實際的運轉需求。主因在於現今之的原物料耗用量遠遠大於研發廠,造成原物料在供應系統上的相關參數如停滯時間、流體速度、流體溫度以及液體汽化速度等運轉參數,與在研發廠內相對小量的供應模式的狀況下,存在著程度不一的差異。
一座新建廠從開始動土至量產,耗時已較過去大幅縮短,其中廠務端的氣體與化學系統由開始配管、桶槽安裝、供應機台建置到正式上線供應必須於2至3個月的時間內完成供應。原物料在新廠內新供應系統中的輸送狀況,和在研發廠內已輸送過原物料相當長時間的成熟管件和供應系統相比,也存在著一些差異,此因素也間接影響Copy Exactly模式在GIGAFAB®量產初期時的適用性。
除上述兩項和供應系統相關之因素外,原物料品質的些微差異也是另一項關鍵因素。在研發階段,為了能夠盡速地由實驗中調配出最佳的Recipe,均需選用品質最佳、濃度或是其他原物料指標最為精準的原物料(Cherry-Picked Material)。然而到了量產階段,在相對大量的原物料耗用下,其品質雖仍能倚靠原物料檢驗報告(Certification of Analysis, COA)、進料品質監控儀 (Incoming Quality Check, IQC)以及連續品質監控儀(Continous Quality Check, CQC)等方式作把關,但仍無法比照研發階段對原物料的精挑細選,使得品質上仍有些微差異存在。此因素在過去的成熟製程中或許較不顯著,但到了近幾年所建置的先進製程產廠中,隨著產品的逐漸縮小線寬,對原物料品質的要求日漸嚴苛,此項在品質上細微的差異也逐漸對Copy Exactly模式在GIGAFAB®上的適用性產生影響。
研究目的
承上所述,在研發轉量產階段,因供應系統與原物料品質的些微差異,Copy Exactly模式已無法完全適用,再加上產能的迅速ramp-up,將衍生出許多運轉實務上的問題。為了能對這些問題進行完整的彙整分析,進而擬出因應的運轉策略,本文使用目前國際上廣泛應用的IDEF0建模方法(Integration Definition for Function Modeling),將研發階段至穩定量展階段所有的流程進行拆解分析。接著根據 2018年新FAB運轉的實際經驗,針對各個流程可能發生之問題作探討並提出可行的解決方法。除此之外,也將此IDEF0之流程分析結果,交由先進製程量產廠內相關專業同仁,進行意見訪查,以期結合眾人力量,建立一套完整的運轉應對策略,達到讓後續新廠在產能拉升階段,氣體與化學系統供應品質對工廠產品良率提昇的最終目標。
文獻探討
IDEF方法論概述
IDEF (ICAM DEFnition)為一種目前廣泛應用於各領域的系統分析與設計方法,其利用簡單的方塊圖和指標箭頭,將複雜的系統或製造流程,轉化為淺顯易讀的系統藍圖,強化使用者之間彼此的溝通效率,並讓使用者可更容易針對作業流程分析。由於原理簡單,圖示清楚且嚴謹,IDEF已廣泛應用於學界與工業界。此外, IDEF也為多種國際組織所接收的標準,如北大西洋公約組織(North Atlantic Treaty Organization, NATO),國際貨幣基金 (International Monetary Fund, IMF)等。電機電子工程師學會(Institute of Electrical and Elec-tronics Engineers, IEEE) 也將IDEF與其他商用標準整合至規格需求中。國際標準組織(International Organization of Standards, ISO)也計畫將IDEF納入標準中[2]。
IDEF發展史
IDEF之歷史發展可追朔至1970年代末期,當時美國空軍為了要將電腦技術用來改善製造業產能,推出了整合性電腦輔助製造計畫(Integrated Computer Aided Manu-facturing, ICAM)。然而在ICAM發展的過程當中,計畫人員發現到冗長又複雜的文字敘述,大大地降低和各個協力廠之間的溝通及相關工程的認證效率,因此計畫人員採改用了由美國電腦科學家Douglas T. Ross所開發的結構化分析與設計技術方法 (Structured Analysis & Design Technique, SADT)來描述系統。在SADT之後,ICAM人員又陸續加入其他的方法論,從不同的觀點建立流程分析模型,最後這項計劃的副產品,就是四種以圖形為基礎的建立模型,分別為IDEF0、IDEF1、IDEF2和IDEF3。後續為了能基於更多不同觀點來描述更複雜的系統,目前IDEF家族已發展至IDEF14,各個成員的功能取向彙整如 表1,其中以IDEF0、IDEF1X及IDEF3發展最為成熟且被廣泛使用[3] [4]。
IDEF成員 |
模組功能 |
IDEF成員 |
模組功能 |
---|---|---|---|
IDEF0 |
功能建模 |
IDEF7 |
信息系統審核 |
IDEF1 |
信息建模 |
IDEF8 |
人機交互介面設計 |
IDEF1X |
數據資料建模 |
IDEF9 |
場景驅動信息設計 |
IDEF2 |
模擬建模 |
IDEF10 |
實施體系結構建模 |
IDEF3 |
流程描述 |
IDEF11 |
資訊製品建模 |
IDEF4 |
物件導向設計 |
IDEF12 |
組織建模 |
IDEF5 |
實體描述 |
IDEF13 |
樹狀概念圖建模 |
IDEF6 |
設計關聯性建立 |
IDEF14 |
網路設計建模 |
IDEF0的應用實例
上述眾多IDEF家族成員中,以IDEF0最常被用來描述公司的運作流程或是產線的生產流程。如王柏元[5]曾利用IDEF0分析微機電的各個細部生產流程,再輔以其他改善方法來縮短整個生產系統的導入時間。薛正誠[1]也曾用過IDEF0建模方式來探討半導體積體電路產業的量產模式。Gong and Shei[6]則利用IDEF0配合物件導向與分布控制結構來模擬一座IC晶圓廠內的現場管制資訊系統。Jiang and Fang[7]也透過IDEF0的建模方式,對虛擬企業生產邏輯系統進行分析模擬,並藉由模擬結果發現了生產邏輯以及原物料分配問題的瓶頸。除此之外,也有學者以概念性方法證明了IDEF0建模可有效應用於自動化生產的策略性發展與導入[8]。
計畫方法
IDEF0 模型建置基本概念
圖1為IDEF0基本的方塊架構圖。圖中右下角標註有「a-0」之方塊為欲分析或描述的主要活動或流程,亦可稱為母方塊(Parent Box, PB)。由左方指向方塊的箭頭代表輸入至此流程的資訊,由下方指向方塊的箭頭則代表讓此流程能夠順利運作的機制或是資源,而由上方指向方塊的箭頭代表要進行該項流程所面臨到的限制或是必須考慮的控制因素,最後由方塊向右方指出的箭頭即為該流程的產出結果。另外,當遇到PB無法完整描述一個流程或是對一個流程描述不夠仔細的狀況時,建模者可於PB增加陰影圖示,再由此陰影拉出對主流程更仔細或補充說明的子方塊 (Child Box, CB),如圖中右下角標註有「a-1」以及「a-2」的方塊所示。根據上述概念,本研究將站在廠務端角度,針對由研發先進製程轉至新廠量產階段的各個流程進行IDEF0建模。
圖1、IDEF基本架構圖
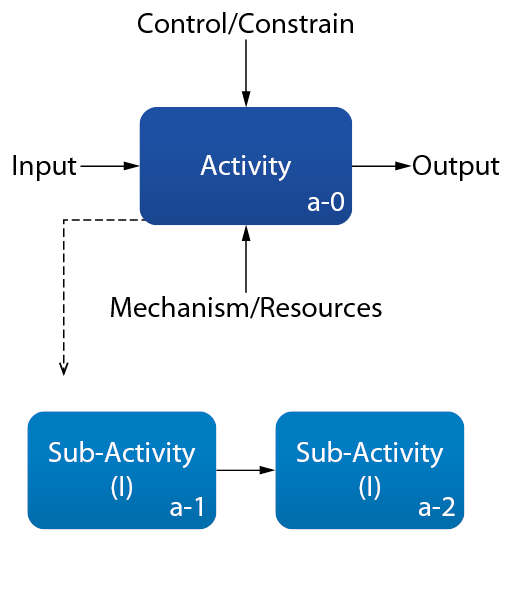
研發製程轉量產階段之IDEF0模型
本研究由研發先進製程轉至新廠量產階段的各個流程進行IDEF0建模的結果如 圖2所示。由該圖可看出,整個流程主要可區分為新研發製程階段、小量試產階段(Mini-line Production)以及量產階段(Mass Production)三個主要階段。
圖2、由研發製程至量產階段之IDEF0流程示意圖
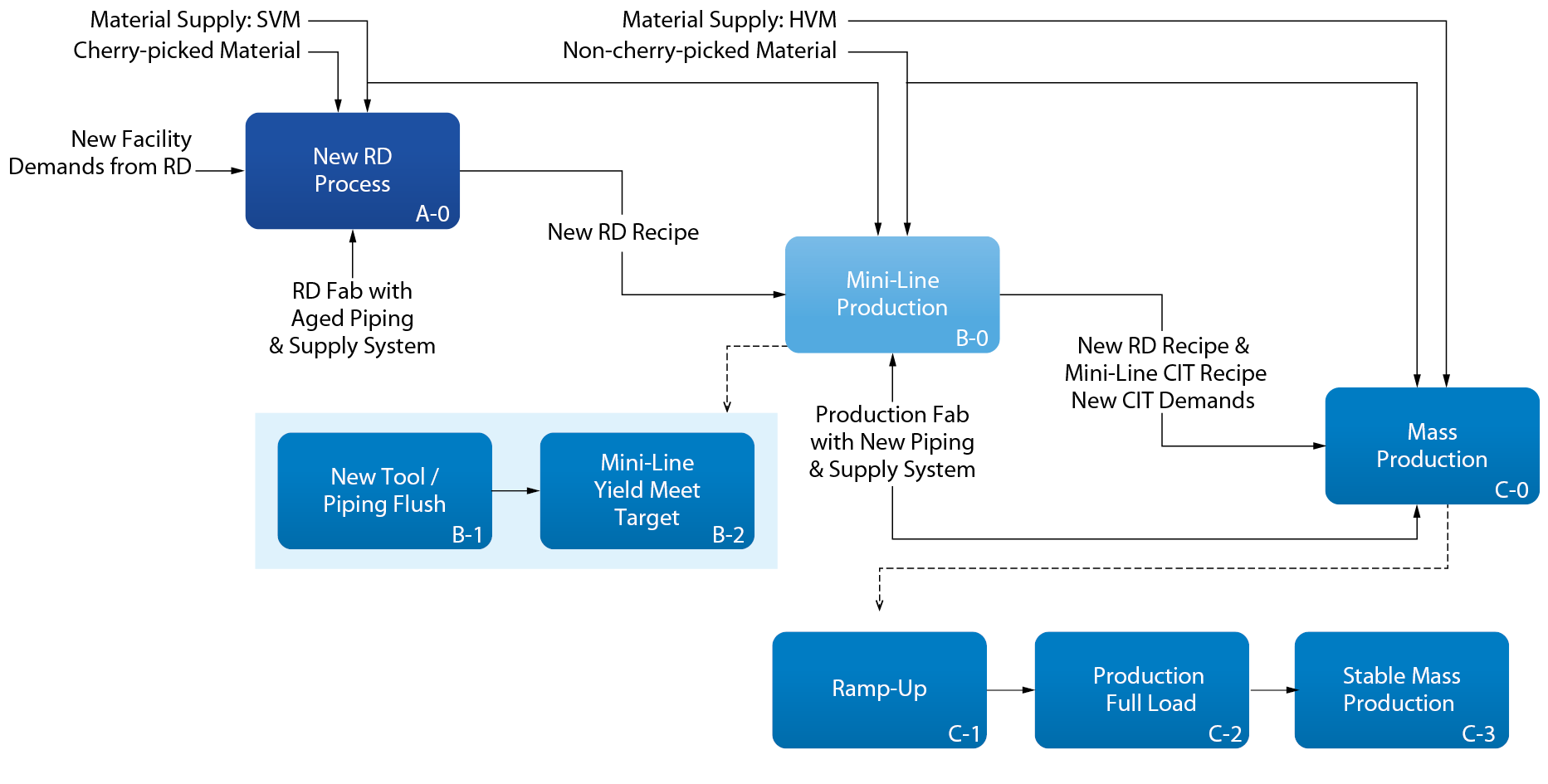
在研發製程階段(A-0),其輸入資訊為研發人員所提供之新原物料需求。促使研發活動可進行的機制,為研發廠內已輸送過原物料一段時間的管件(Aging Piping)及供應系統(Aging Supply System),此類的系統較不易受系統本身可能析出之不純物的影響,供應品質較為穩定。而該階段的限制條件主要為原物料均受到精挑細選過(Cherry-Picked),且原物料耗用為相對小量的模式(Small Volume Manu-facture, SVM)。最後的輸出則為研發人員所測出之研發製程配方。
到Mini-Line階段(B-0),所接受到的輸入資訊即為前一階段所產出的研發製程配方,促使Mini-Line生產可進行的機制則為新建廠內的新管路以及供應系統,此類系統甫建置完成,管路或桶槽內壁較易殘留有建置初期所殘存之不純物,使其供應品質會較不穩定。另外,因Mini-Line已到了量產廠,為大量生產作準備,其原物料已無法如同研發階段作精選(Non-Cherry-Picked),但原物料耗用上仍與研發階段相同屬於SVM,此兩者即為Mini-line生產時的限制條件。最後的輸出即為研發階段所傳遞來之製程配方結合小量試產階段所發現之CIP (Continue Improve Process)改善配方(Recipe)。而在此階段又可再細分出新機台與管路沖洗(B-1) 以及試產良率達標(B-2)兩個子階段。
最後到量產階段(C-0),前一流程所輸出之研發與Mini-line試產出之CIP Recipe即為該階段之輸入資訊。讓量產得以順利進行的機制和Mini-Line階段相同均為新建廠內的新管路與新供應系統。此階段的限制除了Non-Cherry-Picked原物料之外,耗用量大幅增加進入大量生產模式(High Volume Manufacture, HVM)也成為另一需考量的限制。最後的輸出當然就是穩定且順利的量產。而在此階段則可再細分出產能拉升(C-1)、產能滿載(C-2)以及穩定量產(C-3)三個子階段。
結果與討論
根據前一節IDEF0流程分析結果,所探討出由研發至量產各階段可能碰到的運轉問題及解決方法簡彙如表2,共包含了五大項運轉問題以及十一項應對的運轉策略與建議。本文也另外針對這運轉問題及應對策略資訊繪製成IDEF0流程圖,這些流程圖及完整內容則詳述於以下各小節。
No. |
問題發生階段 |
Problem / Potential Issue |
Operation Strategies |
---|---|---|---|
1 |
B-1 |
新系統 & 管路內殘餘不純物過高,影響新機台Flush進度。 |
以Hot DI 對新建管路進行Flush。 VMB Flush改由Tool端Drain管排放。 新系統送酸三個月後,所有Filter進行一次預防性全面更換。 |
2 |
C-1 |
線上機台Slurry用量增加,影響slurry供應之新鮮度 / Aging time,造成線上Defect。 |
建置 Batch Size可調整 / buffer tank 可擴充式的混酸系統。 建置溫控系統。 |
3 |
C-1, C-2, C-3 |
有機溶劑類化學品供應系統易受靜電放電效應攻擊。 |
針對高比阻抗之化學品,建置抗靜電供應系統。 |
4 |
C-1, C-2, C-3 |
B2H6類之混氣鋼瓶,須配合製程排出濃度微笑曲線,線上再根據不同濃度進行Recipe手動微調。有人為誤操作風險。 |
建置原物料濃度自動微笑曲線,與機台根據COA自動調整Recipe功能。 設置混氣濃度更精準之Mixer (比照GeH4)。 |
5 |
C3 |
大宗化學品原物料COA符合標準,供應至線上仍造成Wet-pa defect,造成大量報廢。 |
建立化學品過濾次數指標。 建置完整有效的 pi-run系統。 建置 particle counter monitor (@20nm)。 |
新建置之化學品供應系統洗淨時間長,影響機台生試產進度
發生階段: B-1
問題
新FAB的運轉經驗上,在化學品供應系統及管路建置完成之初,線上機台進行機台洗淨(Flush)的階段,常發現有Flush效率不佳,機台在Flush大量化學品後,微粒子污染物(Particle) 數目仍居高不下的狀況,不僅延遲機台生產時間,也造成化學品浪費 圖3。
圖3、新機台及管路flush階段之IDEF0流程圖
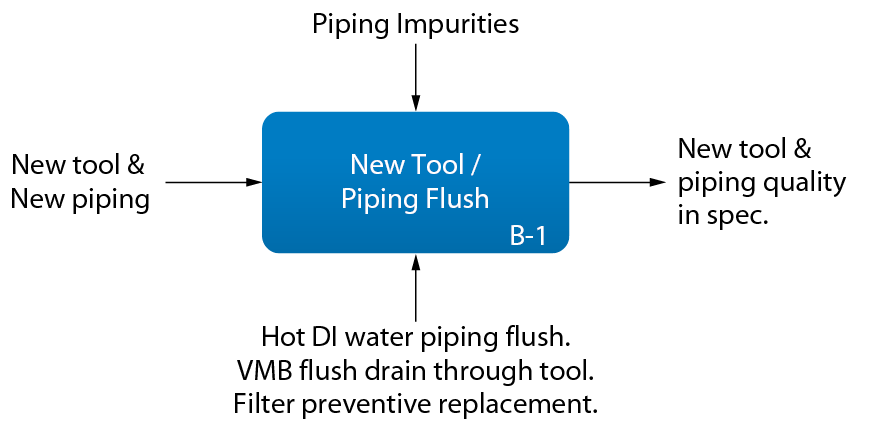
運轉策略1
首先在供應管路建置之初,以40℃之高溫去離子水(De-ionized, DI)取代常溫DI水來對管路作Flush,根據過去實測經驗,此作法可縮短30%新管路內微粒污染物濃度下降的時間。
運轉策略2
後續到化學品對閥箱(Valve Mani-fold Box, VMB)洗淨階段時,傳統廠務端自行利用化學桶自VMB排放管路(Drain Port)承接廢液的方式作Flush,改為請設備端協助,從線上機台端的Drain Port排放,此作法不僅較為安全,也讓Flush的流量及效率較傳統作法提昇3 ~5倍。
運轉策略3
在供應系統送酸三個月後,將所有的化學品Filter進行全面的預防性更換。須進行此做法之主因為建置完成的新管路內殘餘有較多的不純物,這些不純物容易於送酸初期機台進行大量Flush時,累積於Filter上進而降低其過濾效果。過去新建廠區即曾發生黃光機台在送酸初期,經長時間Flush醋酸丁脂後,機台的Particle值仍居高不下的狀況,而當廠務端進行首次的預防性Filter更換後,Particle值立即降下,讓機台順利通過驗機。
化學研磨液供應品質受時間與溫度效應的影響
發生階段: C-1
問題
部分在廠內自行混酸供應的化學研磨液(Slurry),其供應品質指標如雙氧水濃度與導電度等則會受到時間效應的影響,有些Slurry在使用上需控制在一定時間內讓線上機台使用完畢,避免品質指標變化過大而超出標準範圍,而部分Slurry則為相反供應模式,混酸完畢後需靜置一段時間(Aging Time),待品質指標趨於穩定並落在標準範圍內才可使用。在耗用量劇增的產能拉升階段,要維持此類Slurry的供應品質,對廠務端也是一項相當大的挑戰。除時間之外,溫度效應對部分Slurry供應系統也有相當程度的影響。Slurry的供應方式為封閉式連續循環迴路(Close Loop),為降低供應過程中產生的機械應力,避免Slurry中的微粒子增加,Slurry系統供應動能均採用感應式轉子的磁浮馬達。此種馬達的優點是低機械應力,但在運作過程中會有放熱反應,導致Slurry在供應過程中會被加溫 圖4。
圖4、Slurry供應系統於C-1階段之IDEF0流程圖
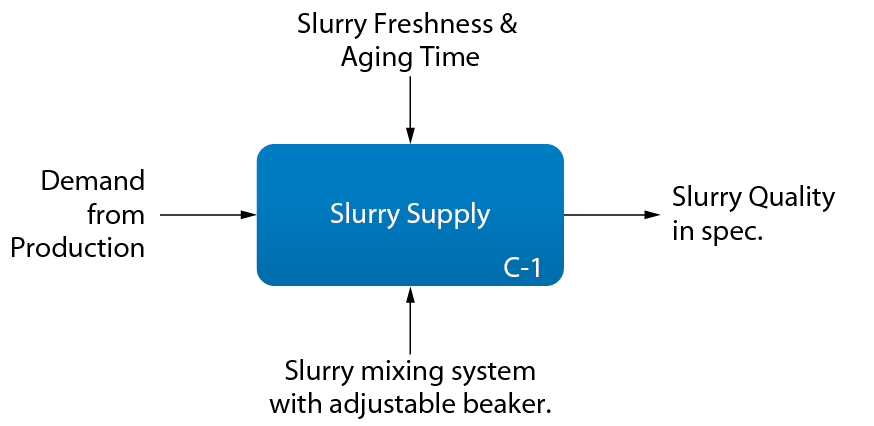
運轉策略1
針對Slurry新鮮度的受影響部分,設置每次落料批次(Batch)可調整式的混酸系統。而會受到Aging Time影響品質的Slurry,則設置可擴充緩衝桶槽(Buffer Tank)式的供應系統。
運轉策略2
針對溫度影響品質的部分,過去曾在Slurry供應系統出口端設置熱交換器,讓出口溫度較高的Slurry和循環回系統溫度較低的Slurry進行熱交換,然而由於進出口的溫度差異不顯著,且流速不夠低,使得Slurry在熱交換器內的停滯時間不足,造成溫控成效不顯著,使得此套系統目前仍未上線啟用。也有其他廠區曾提出對Slurry供應桶槽包覆熱盤管以及製程冷卻水管的方式進行溫控的想法,雖尚未經過實測,但根據理論評估,可預想其成效應會較熱交換器佳。關於此溫度效應議題,雖後續反覆測試後,確認為Aging Time才是主要影響因素,溫度影響僅列為參考,但未來對於原物料有更嚴苛標準的先進製程而言,此溫度影響的要求恐捲土重來,故既有 FAB 所提出的溫控方式仍可列為參考。
靜電放電效應攻擊有機溶劑類化學品供應系統
發生階段:C-1 ~ C-3
問題
圖5靜電放電效應(Electrostatic Discharge, ESD)對有機溶劑類化學品供應系統的攻擊問題,在原物料耗用量較大的新廠開始變得較為明顯。ESD不僅會攻擊管路或幫浦造成滲漏,甚至也曾發生過讓線上製程的微粒子污染物指標升高的情況。一般在化學品輸送的管材選用上,基於抗腐蝕、減少化學反應以及不鏽鋼管路可能釋出金屬不純物等考量,會選擇具有良好耐化學腐蝕性的四氟乙烯(Poly-fluoroalkoxy,PFA)或聚四氟乙烯(Polytetrafluoroethene, PTFE)材質,然而卻忽略了這種絕緣管材在輸送有機溶劑類化學品時可能產生的ESD效應。有機溶劑類化學品通常具有較高的比電阻抗(Specific Resistance),不易導電,使得流體流動時跟管內壁摩擦所產生的靜電不易被流體帶走,再加上PFA材質的管路與幫浦本身為絕緣材質,使得電荷會累積於管壁或幫浦元件上,當電荷量累積至一定程度時,電流便會釋放而造成供應系統元件的破損而終致漏液的狀況發生,更甚將管材或幫浦元件內一些長碳鏈物質釋放出來,使得供應品質受到影響。 表3為負顯影醋酸丁脂供應幫浦受到ESD攻擊的狀況。過去的成熟製程上,ESD效應或許較不明顯,但在最新製程上,醋酸丁脂供應系統的ESD效應就對黃光機台產生了顯著影響。
圖5、醋酸丁脂供應系統於C-1至C-3階段之IDEF0流程圖
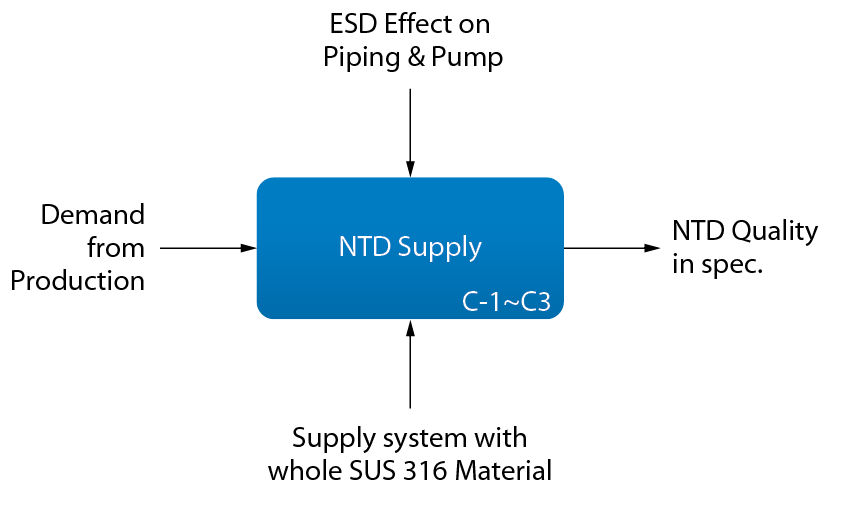
Site |
Pump Status |
|
|
|
---|---|---|---|---|
A |
Used for 18 Mon. |
嚴重ESD受損焦黑痕跡 |
明顯ESD受損焦黑痕跡 |
ESD輕微焦黑痕跡 |
B |
Used for 12 Mon. |
輕微ESD焦黑痕跡 |
輕微ESD焦黑痕跡 |
無異常 |
圖示 |
|
運轉策略
建置一套全部管件均為SUS 316不鏽鋼材質的負顯影醋酸丁脂原物料供應系統,供應幫浦則針對上述易受到ESD攻擊的部分,改為SUS 316材質並接上接地線,如 圖6所示。由目前已建置全SUS 316負顯影醋酸丁脂供應系統的新廠運轉經驗得知,此套供應系統穩定,至今尚未發生過ESD攻擊造成幫浦破損或是管路滲漏的情況。此外,由此系統供應的線上機台,定期測得的微粒子的數量均在10顆以下的基準,幾乎是尚未採用全SUS供應系統的一半水準,由此可見此全SUS供應系統也確實對負顯影醋酸丁脂供應品質有實質上的幫助。有鑑於此,近期正在興建的新系統均採納此項建議,將負顯影醋酸丁脂全SUS 316供應系統列為標準設計。
圖6、抗ESD攻擊之改善幫浦
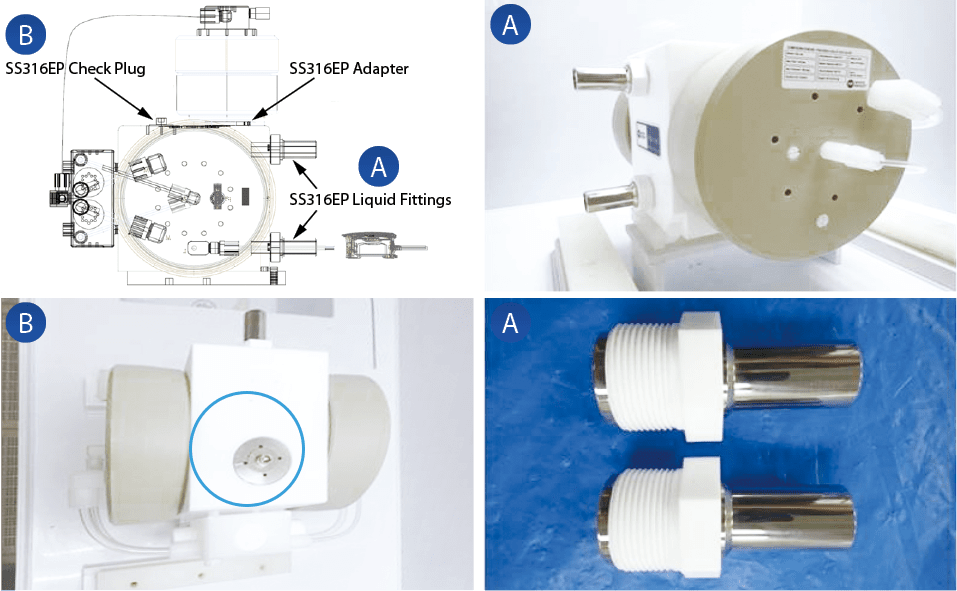
原物料規格無法符合線上需求
發生階段:C-1 ~ C3
問題
圖7過去藉由公司品管部門透過統計製程控制(Statistical Process Control, SPC)以製程能力指標Cp (Capability of Precision)及Cpk,Cpk=Cp (1-Ca),Ca (Capability of Accuracy) 來要求供應商對原物料品質提升,再透過廠務系統直接輸送供應的模式(Clean in & Clean out),但在先進廠區有越來越多原物料規格無法符合製程需求的狀況。如乙硼烷(B2H6)類的混氣鋼瓶,供應商受限其製程能力,對此類鋼瓶的混氣濃度誤差精準度僅能提供控制在±0.03%,然而近年來的先進製程對混氣濃度的需求範圍逐漸通常在±0.005%。生產線上為了克服此原物料問題,均須倚靠人工方式,依照每支鋼瓶的原物料檢驗報告(Certification of Analysis, COA)不斷地對製程Recipe作調整。此外,為了讓製程不會因每支鋼瓶濃度變化而有過大的Recipe調整,廠務端也須根據COA,依照鋼瓶濃度進行所謂的微笑曲線排序,盡量降低鋼瓶與鋼瓶之間的濃度差異。另外一個風險就是有人為操作的地方就有可能發生失誤,也確實曾發生過製程人員調整Recipe操作錯誤,造成產品的 Defect 問題。
圖7、混合氣體供應系統於C-1至C-3階段之IDEF0流程

運轉策略1
讓B2H6混氣鋼瓶的原物料COA隨著進廠後,即自動交由廠務危害性生產原物料管理平台進行資料彙整。首先將進入廠內的B2H6混氣鋼瓶,自動進行原物料微笑曲線排列,再結合條碼系統(Barcode)卡住鋼瓶的使用順序,避免發生上錯鋼瓶的狀況。另外,當鋼瓶換上氣櫃之後,也可透過FHM系統,將該隻鋼瓶的COA連結線上機台,讓機台根據COA上的濃度值自動進行Recipe微調,取代過去人工調整的作法,進而避免人工操作失誤。
運轉策略2
於廠內自行對B2H6進行混氣供應。由於B2H66混氣的濃度須控制在±50ppm以內,故須倚靠一種配備有聲波腔濃度即時量測器(Acous-tical Chamber)的特殊濃度恆定混氣系統,才有辦法自行混出濃度範圍如此精準的混合氣體。此套系統在先進製程FAB已大量使用於GeH4/H2混氣上,而在B2H6混氣的應用上,過去則已有相關研究證實其可行性,其混氣實測結果如 圖8所示,輸出濃度可落於±15ppm內[9]。
圖8、濃度恆定混氣系統,混氣測試結果(劉俊男,2015)
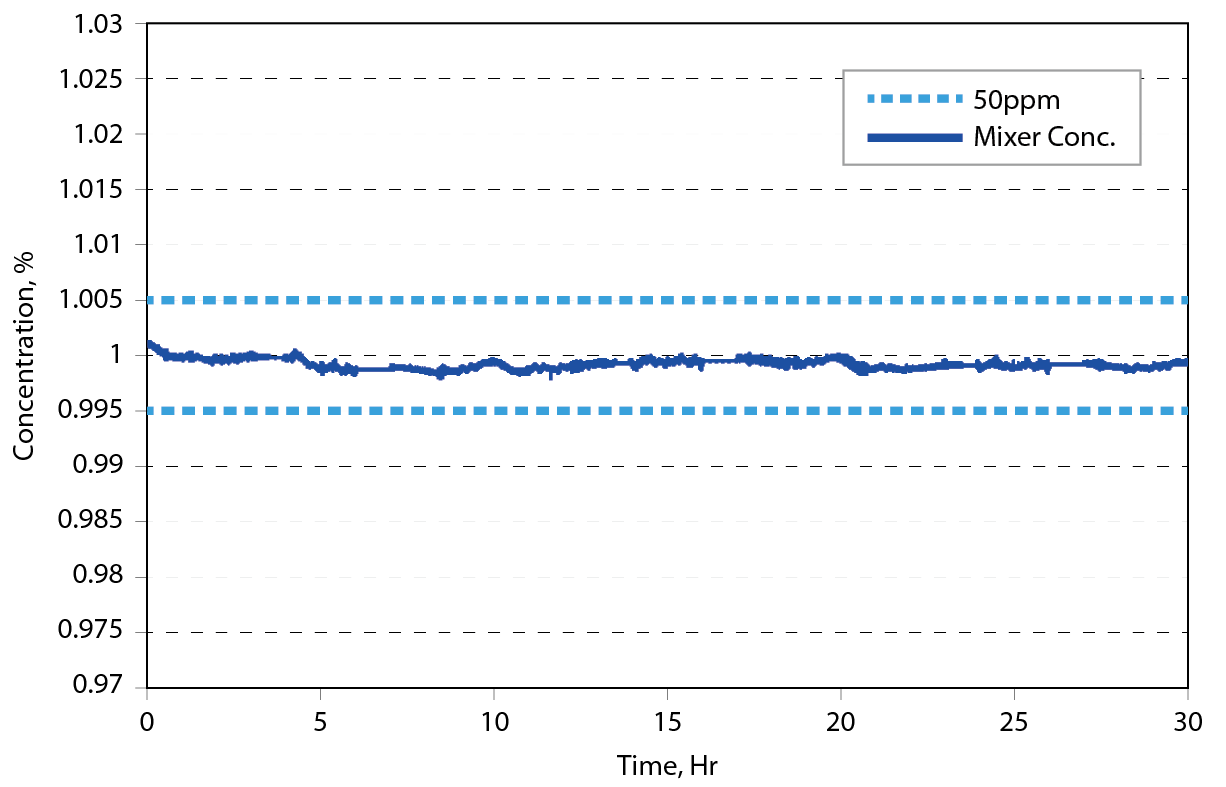
大宗化學品的供應風險
發生階段:C-3
問題
圖9一些對線上製程良率敏感的大宗化學品原物料如異丙醇與硫酸,在先進製程 FAB即曾遇過即使原物料COA均符合規格,灌充前微量金屬不純物量測值也小於規範,但供應到線上仍有Particle問題造成晶圓缺陷的狀況。其中部份的原因推測為大宗化學品用量增加,提高了槽車灌充頻率,使得桶槽內的化學品在切上線供應前的循環過濾次數降低所致。以高溫硫酸為例,在工廠量產初期,槽車灌充頻率約每24小時灌充一車,此時化學品在供應至線上之前的平均過濾次數可達7.2次。然而隨著產能提高,原物料耗用量增加,槽車灌充頻率增加到約每15.5 小時灌充一車,平均過濾次數降至僅剩3.6次。
圖9、大宗化學品供應系統於C-3階段之IDEF0流程圖
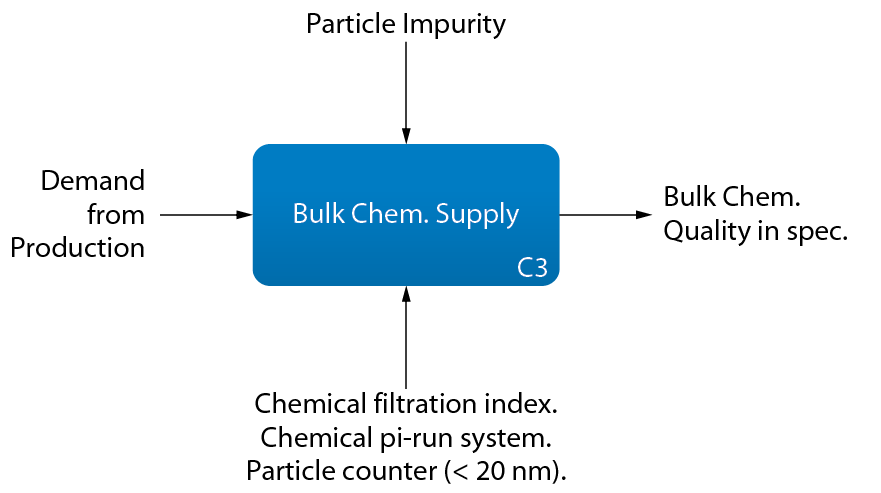
運轉策略1
透過FHM建置化學品過濾次數指標自動計算功能。透過此資料庫的建置,明確訂定Lorry桶槽內的化學品於切上線供應之前的過濾次數標準。
運轉策略2
建置大宗化學品試供應系統(Pilot Run, Pi-run)。大宗化學品由槽車(Lorry)供應,標準建置為兩顆Lorry桶槽,當其中一顆正在供應給工廠生產時,另一邊桶槽即進行灌充作業,讓兩顆桶槽可輪流切換供應。2016年新廠所建置之Pi-run系統,其模式為讓剛灌充完畢內桶槽的酸,直接供應給線上一台專門負責Pi-run的機台進行量測,確認原物料內的Particle符合標準後,此桶槽內的酸才可正式切上線給生產機台。此做法之優點為Pi-run邏輯較為單純,缺點則是若Pi-run發生問題,需要將整桶Lorry桶槽的化學品排除,不僅耗時耗力且會增加大量的廢棄物。
2018年新廠進建置化學品的Pi-run系統,做法和2016年新廠不同,其另外設置了一套Pi-run專用的化學品供應系統,當槽車準備灌充前,會先將少量的化學品灌入此Pi-run 系統,再由其供應給特定的Pi-run機台進行測試,待Pi-run確認品質無虞後,槽車才會把剩餘的化學品全數灌入Lorry桶槽內。此作法之優點為發生Pi-run失敗的情況,僅須將Pi-run CDU較小顆桶槽內的化學品排掉即可,不會耗費太多人力及造成大量廢液排放。
此兩種Pi-run方式雖不盡相同,但均須注意同一件重要的事情:Pi-run之前,供應管路內的化學品須作足夠量的Flush,讓管路內的舊化學品完全置換,確保Pi-run機台使用到的化學品為當次灌充的原物料,尤其是黏滯性較高的硫酸,其在管路內的流速較慢,更須對Pi-run前的機台Flush時間嚴謹設定。近期2016新廠即發生硫酸Pi-run前機台Flush量不足,使得有問題的原物料灌入桶槽後未被Pi-run機台抓到,切上線供應後導致線上機台Particle全數跳起而影響生產。
運轉策略3
目前大宗化學品灌充前僅量測金屬不純物,建議未來加裝可測得粒徑小於20奈米以下的微粒計數器(Particle Counter),針對最主要影響線上生產機台的Particle不純物增設一道防線,為原物料品質多設一道把關。
結論與建議
本研究透過IEDF0的優勢找到Copy Exactly的可能盲點,改善量產 FAB氣體化學供應系統控制質與量的完整性與一致性的(Con-sistence)。對廠務系統來說,廣義的Copy Exactly要做到的不單是每一套系統硬體及運轉參數的alignment,如何讓原物料在量產FAB與RD階段,原務料品質行為都是一致性的,才能算是成功的Copy Exactly先進製程轉量產的廠務系統。
IEDF0將研發先進製程轉量產的過程中,分為三個主要階段與五個次要流程,針對這些流程,依新廠運轉經驗與各廠專業人士的意見,彙整出五大問題及十一項運轉策略與建議。這些問題涵蓋了從建廠初期改善管路Flush效率的議題,到穩定量產後供應系統的運轉風險考量。而相對應的運轉策略及建議則包含了,現場的工法、FHM系統和機台之間的智慧連結、到對新廠規劃的設計建議等等。
在這些運轉問題之中,以化學品的供應品質最為關鍵,目前化學品的金屬離子不純物及混酸濃度的監測技術均已發展完備,且在各廠內均已成熟運用。然而對於線上影響最為重要Particle指標,相關的量測技術仍相當缺乏,尤以製程將邁入更新的製程階段,對於粒徑更小的微粒偵測技術將更顯重要,故針對粒徑小於20奈米以下的微粒計數器開發,將會是未來廠務氣化系統運轉品質相關技術中最為重要的發展重點之一。
最後,由於先進製程量產廠的產值佔公司營收重要的比例,且比重將會逐年增加,建議公司依照每年營收之一定比例,配給預算用於增加廠務關鍵供應系統備用機制(Backup)的建立,如大宗氣體或化學管路跨廠區的串接或是備用(Backup) 管路的建立等,以降低供應系統重大中斷風險而造成公司營收損失受到巨大影響。
參考文獻
- 薛正誠,2006,A Study on the techno-nogy Ramp-up Models in the semicon-ductor integrated circuts industry,國立台灣大學碩士論文。
- 王嘉玲,2006,CALS 之模型分析方法–IDEF、ARIS與OOA/OOD,取自:http://www.ixon.com.tw/
- Mayer, R. J., Painter, M. K., Dewitte, P. S., 1994. IDEF Family of Methods for Concurrent Engineering and Business Re-engineering Application, Knowledge Based System Inc.
- 陳世榮,1995,設計變更管理系統參考模型,國立交通大學碩士論文。
- 王柏元,2007,以IDEF模型化製造現場監控系統之研究-以為機電生產管制系統為例,國立中央大學碩士論文。
- Gong, D. C., Shei, Y. W., 1997, The IDEF0 Reference Model for the Shop Flow Control Information System. Journal of the Chinese Institute of Industrial Engineers, Vol 14, 29 – 37.
- Jiang, Y. L., Fang, Z. M., 2015, Modeling and Simulation of Virtual Enterprice Production Logestic System, Jounral of Ninbo University (Natural Science & Engineering Edition).
- Waissi, G. R., Demir, M., Humble, J. E., Lev, B., 2015, Automation of Strategy Using IDEF0 – A Proof of Concenpt. Operation Research Perspectives, Vol 2, 106 – 113.
- 劉俊男、黃介然,(2015),一個新穎的穩定濃度供氣技術:高活性劇毒氣體的應用。新工季刊,Vol 18,56 – 61。
留言(0)