摘要
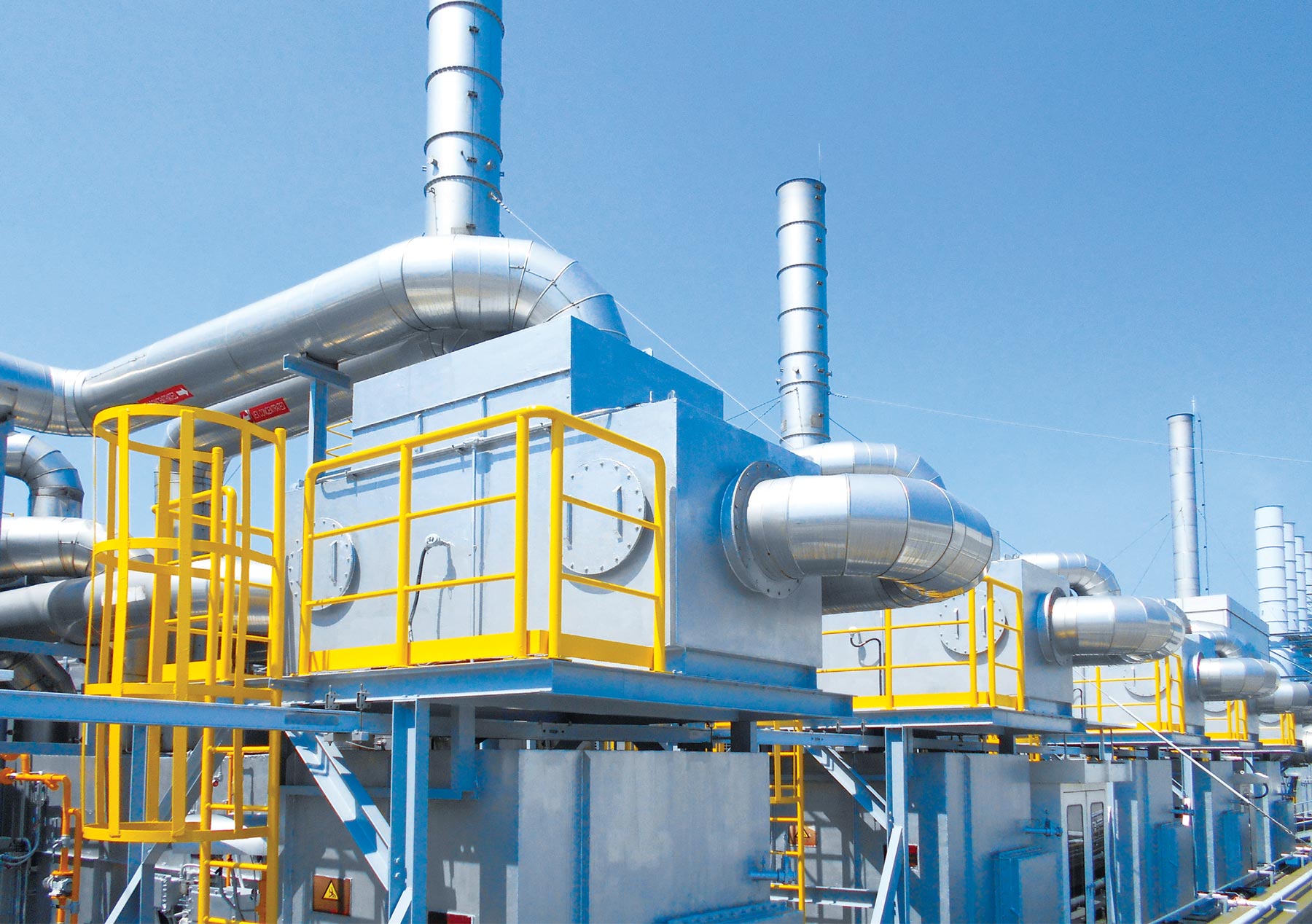
高溫逆脫附技術改善沸石濃縮轉輪去除效率
Keywords / Zeolite Concentrator3,Volatile Organic Compound (VOCs),Absorption,Desorption3
現今台積廠區均使用沸石轉輪濃縮系統作為主要揮發性有機物(VOCs)防制設備,其中沸石轉輪之吸附能力為處理效率之關鍵。而沸石轉輪藉由高溫脫附以及定期水洗兩種方式維持吸附能力。然而在長期使用後,沸石轉輪會因脫附溫度不均勻而導致效率逐漸下降。另外在歐盟全面禁用陶瓷纖維之後,沸石轉輪將逐步汰換為結構較脆弱的玻璃纖維結構。故本文研究沸石轉輪高溫逆脫附技術,在高溫脫附以及定期水洗之外,提供轉輪再生的另一方向。根據研究結果,轉輪製程氣體入口處可改善20%之吸附容量。而非甲烷總烴(NMHC)儀器分析,高溫轉輪逆脫附運轉可使出口處理濃度改善12%、去除率達到98%,單台VOCs處理設備排放預估減量可達到0.14噸/年。供成廠區運轉以及空污改善之參考。
前言
隨著我國環保法規日趨嚴格,以及社會大眾普遍環保意識提升,針對空氣污染改善之要求亦更加全面。其中揮發性有機物(Volatile Organic Compounds,VOCs)便是主要的監測污染物之一,因VOCs在陽光下經紫外線照射後易形成臭氧等二次污染物。若大量排放至空氣中,亦可能經由皮膚接觸或透過呼吸系統對人體產生負面影響,並有致癌之可能。故VOCs排放已經是空污檢測之重要指標,同時亦是空污排放之主要管制項目。
目前科學園區內主要之VOCs防制設備為沸石轉輪濃縮系統,此系統可將製程廢氣經由疏水性沸石轉輪進行吸附後再行排放。針對VOCs之去除效率可達90%以上。而沸石轉輪處理系統設計有脫附功能區。可將處理過之製程廢氣升溫,並藉由貫穿轉輪之方式將轉輪內有機物進行濃縮並脫附。而此吸附、脫附交互循環之流程,便是沸石轉輪系統之基本處理架構。然而經由高溫廢氣進行脫附之轉輪,會因為轉輪進出口兩側長期溫度不均勻。導致沸點較高之有機物如PGME、PGMEA等累積在轉輪出口內,進而影響處理效率。而除了高溫脫附方法外,沸石轉輪亦常經由水洗的方式去除吸附在轉輪內部的VOCs並達到轉輪再生之目的。故沸石轉輪在製作時普遍採用陶瓷纖維作為主體結構,此種結構對於水洗的壓力有較好的耐受性。然而在2011年9月,歐盟勞工與社會事務署(Employment, Social Affairs & Inclusion-European Commission)發佈了針對陶瓷纖維的禁用規定,在此之後製作的沸石轉輪漸漸改用玻璃纖維[1]。而玻璃纖維在水洗時容易損壞,造成了廠區運轉時的困難。而本文介紹並探討針對沸石轉輪之高溫逆脫附作法及影響,希望能藉由此一方式達到運轉中持續對轉輪進行全面再生,在維持轉輪效率的前提之下,減少預防性停機保養水洗的時間以及次數,也避免玻璃纖維轉輪在頻繁水洗後結構受損,進而導致使用壽命縮短。
文獻探討
一般而言,VOCs主要用於有機溶劑之塗裝或清洗用途,廣泛使用於半導體業、光電業、汽車業、PU合成皮業、石化業與乾洗業等行業。根據排放管道所排放之主要污染物調查,以異丙醇(IPA)及丙酮(Acetone)為主,其次為乙酸甲氧基異丙酯(PGMEA),其中異丙醇及丙酮排放量約佔總排放量50-80%[2]。而沸石濃縮焚化系統處理之設計處理量以及處理濃度 圖1,是現行VOCs污染防制設備中最能符合國內「半導體製造業空氣污染管制標準及排放標準者」,同時亦是台積廠區以及新竹科學園區內半導體產業最廣為使用 表1之VOCs污染防制設備[3]。
圖1、VOCs處理設備之適用範圍
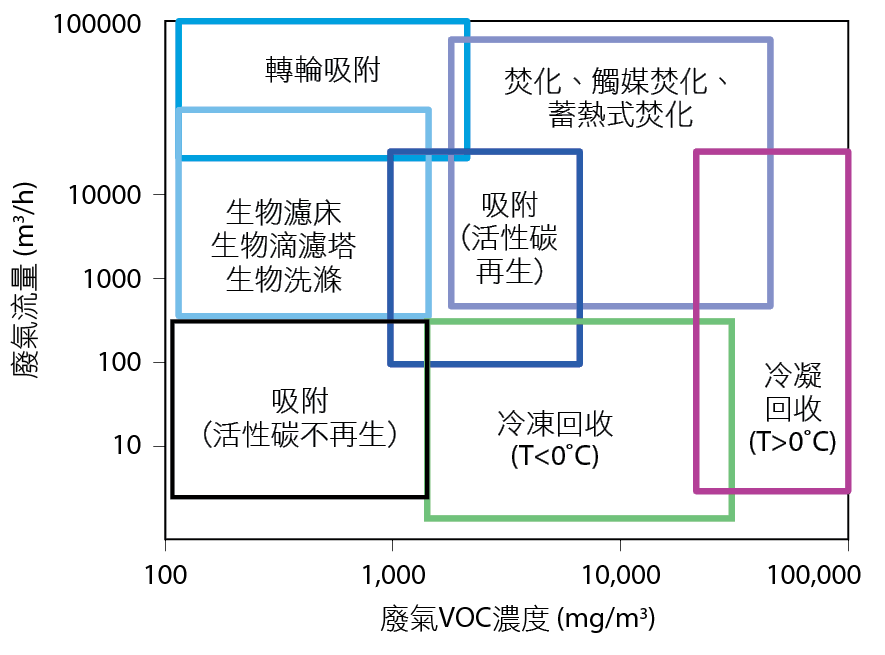
設備名稱 |
處理效率 |
污染防制設備說明 |
---|---|---|
活性碳吸附塔 |
25%~98% |
正常操作下去除率可達90%以上,但當活性碳吸附塔出現超飽和狀況時,去除效率會明顯降低。 |
填充式洗滌塔 |
33%~67% |
半導體廠所排放之VOCs廢氣中部份屬於水溶性較低的物質,故採用濕式洗滌法,但去除效率有一定之限制。 |
沸石轉輪+ 直熱焚化爐 |
78%~92% |
本法為較佳之空氣污染控制技術,一般操作條件下可達90%之去除率。 |
生物濾床 |
60%~80% |
此去除方法的效率較難達到90%,且場地之需求與限制也較多,難以符合半導體廠設備排放標準要求。 |
而沸石轉輪濃縮系統搭配高溫焚化系統,可將高流量、低濃度之製程廢氣經由疏水性沸石轉輪進行吸附,對於VOCs去除效率可達90%[4]。沸石轉輪處理系統內部可分為吸附區、再生脫附區以及冷卻區,吸附區一般而言較大,脫附區及冷卻區為兩個較小且面積相等之處理側,面積比例為10:1:1[5],如 圖2所示。大部份製程廢氣於轉輪上進行吸附後排出至大氣,少部分製程廢氣經過冷卻區後,與焚化系統進行預熱交換升溫至200℃並回流到沸石轉輪脫附區。藉此高溫將轉輪內已吸附之有機物進行濃縮並完成脫附並送至焚化系統燃燒裂解,最後排放至大氣中。而此吸附、脫附交互循環之流程便是沸石轉輪濃縮系統之基本處理架構 圖3,且沸石轉輪經由此再生程序後,即可反覆使用。
圖2、沸石轉輪各功能區分示意圖
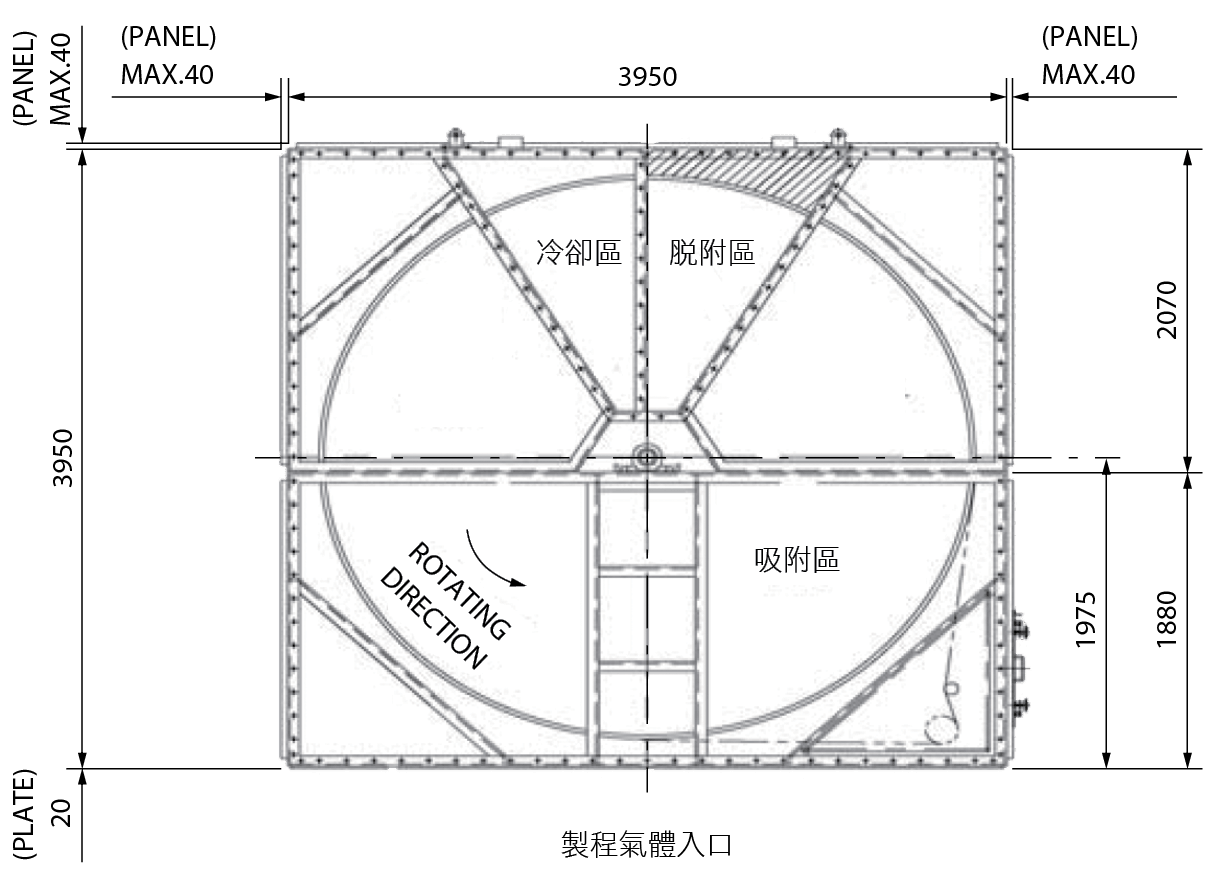
圖3、沸石轉輪濃縮系統之基本處理架構
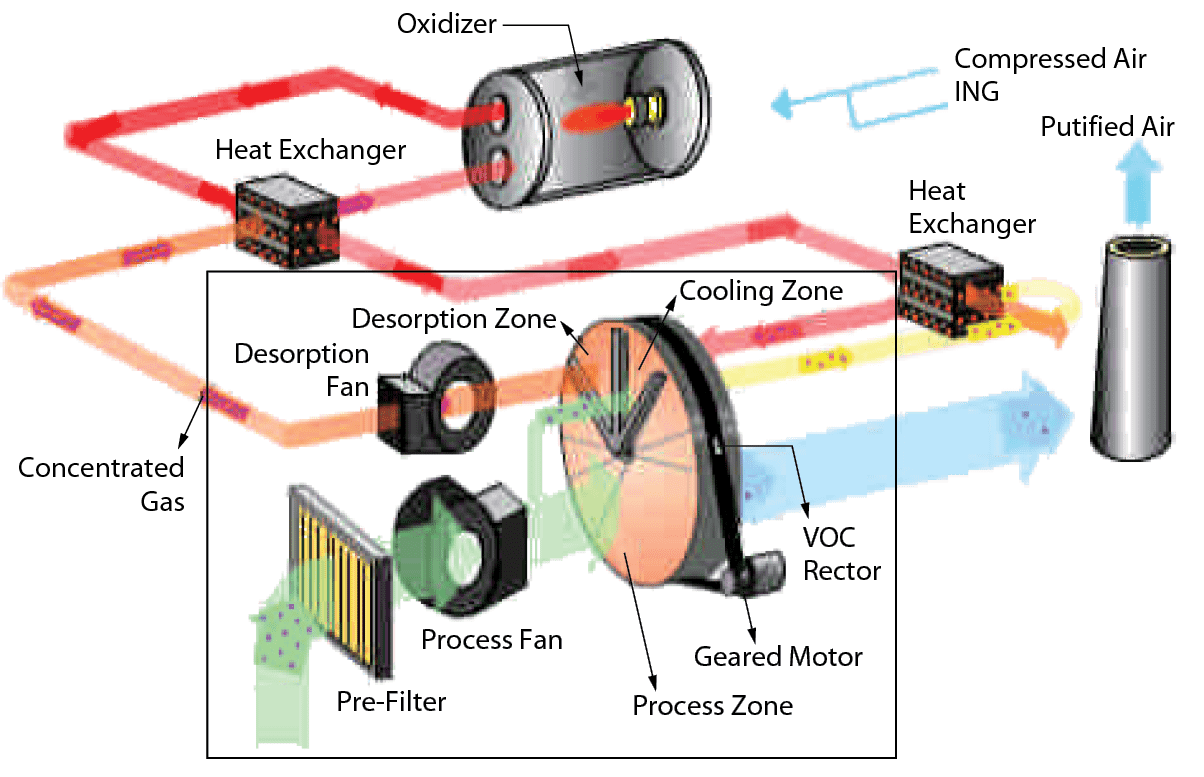
針對沸石轉輪之效能改善,設備運轉溫度是相當重要的參數之一,若是脫附溫度增加,可使轉輪於脫附區獲得充足熱能、將吸附其上之VOCs全數脫附出來,如此進入吸附區之轉輪吸附效率也隨之增加[6]。脫附用的載流氣體濃度越低,則沸石轉輪針對VOCs的去除率越佳。該研究利用不同濃度之載流氣體(180ppm vs 4ppm)進行測試 圖4,實驗組相對於對照組出口濃度降低0.6ppm,總排放量降低12%,另外作為脫附用載流氣體,若是可提升附出口溫度(T5),則當T5溫度由40℃上升至55℃時,去除效率可以額外增加0.3%[7]。
圖4、沸石轉輪脫附氣體濃度改善前後設計圖
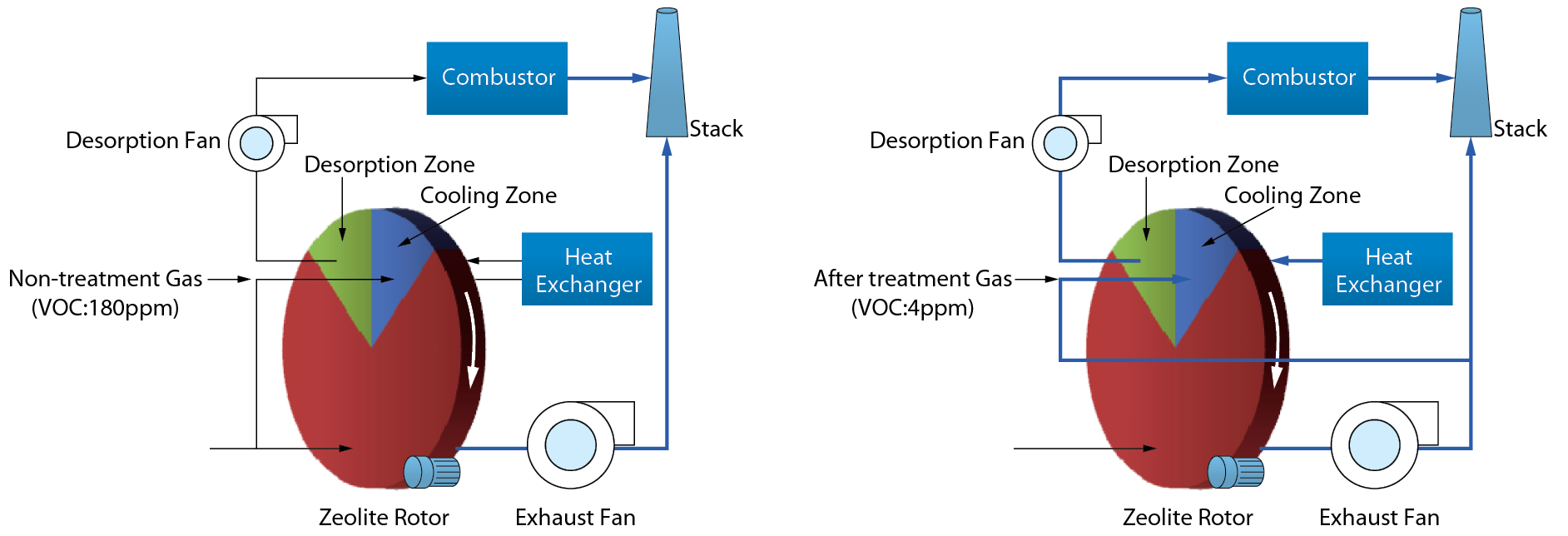
另外,亦有研究提出高沸點VOCs冷凝分離概念,避免高沸點VOCs殘留在轉輪中影響轉輪吸附效率[8]。然而經過長時間的連續運轉,即使是使用高溫載流氣體行脫附之轉輪,仍會因為轉輪進出口兩側長期溫度不均勻,導致沸點較高之有機物如PGME、PGMEA等累積在轉輪出口側無法脫出,進而影響處理效率。陳仲祥(2018)提出使用調高脫附溫度至250℃,脫附出口溫度調高至100℃,並調降轉輪轉速等做法,可將去除效率僅剩下91%之沸石提升至96%。
而本文介紹並探討針對沸石轉輪之高溫逆脫附作法,能藉由改變氣流方向的作法,達到運轉中持續對轉輪進行全面再生,解決轉輪受熱不均的問題,能提升轉輪效率並減少停機保養以及水洗轉輪之頻率。
計畫方法
本文為探討高溫逆脫附對於轉輪再生程度之影響,先針對廠區內之進行取樣分析確認轉輪使用狀態,並於廠區F12P1/2廠區安裝正逆脫附切換閥件組於設備VOC-06 (設計方式如 圖5所示),持續進行正逆脫附切換後,分析轉輪去除效率之變化。正逆脫附切換之氣流方向相對於轉輪吸脫附方向如 圖6。
圖5、正逆脫附切換氣流方向示意圖
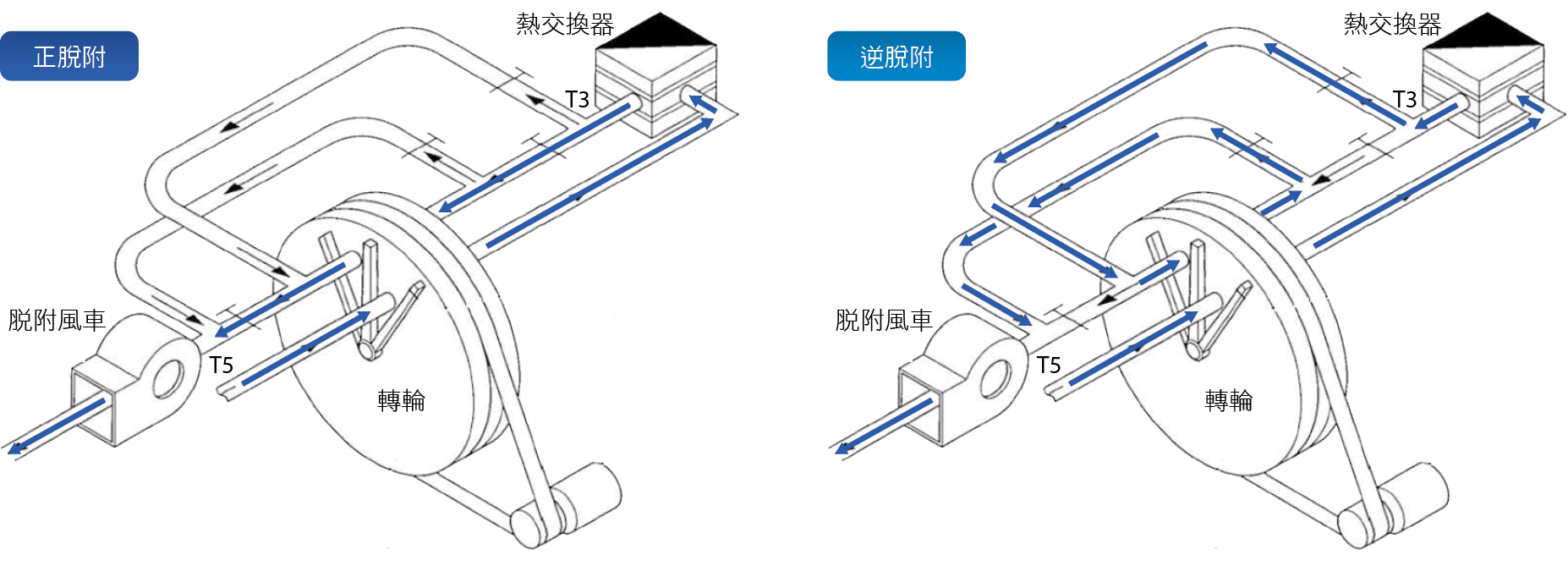
圖6、正逆脫附切換之氣流方向
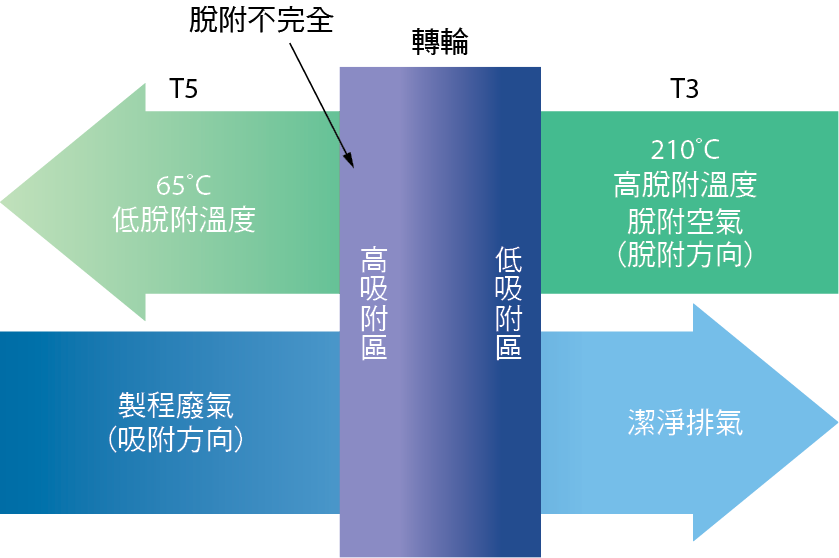
由F12P1/2使用之轉輪達15年之VOC-05/06之沸石轉輪取樣樣本 圖7,可看出轉輪在製程氣體入出口處有明顯的變色情形,針對圖中的藍色區塊進行轉輪切片,取出厚度為10mm之樣本 圖8。另外取相同尺寸的新鮮沸石共七個樣本進行吸附測試。
圖7、F12P1 VOC-05/06轉輪樣本

圖8、F12P1 VOC-05/06轉輪樣本切片
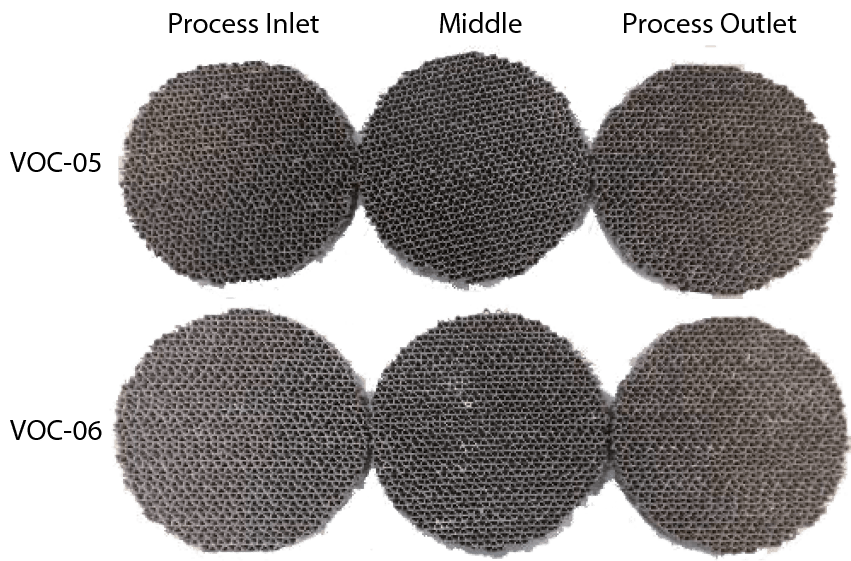
首先將新鮮轉輪切片加熱至200℃一小時後,浸泡在甲苯(toluene)化合物中兩小時,使其吸附甲苯化合物。藉由量測新鮮轉輪切片與吸附甲苯後之轉輪切片重量差,做為新鮮轉輪吸附容量基準,另各自針對VOC-05/06轉輪樣本進行複製實驗,可得出吸附測試結果如下。若新鮮轉輪吸附量為100%,VOC-05/06製程氣體入口處吸附容量僅剩下64%~67%,製程氣體出口處還有82%~84%之吸附容量 圖9,此實驗可以看出轉輪經過反覆的高溫脫附再生,受熱較高的一側能保有較佳的吸附能力,而脫附出口處的吸附能力明顯較差。按此結果推論,如針對轉輪進行高溫逆脫附,應可使得製程氣體入口處之轉輪吸附量恢復約20%以上,惟仍需進行較長期的測試後方可驗證此結果。
圖9、對比新鮮轉輪之靜態吸附測試結果
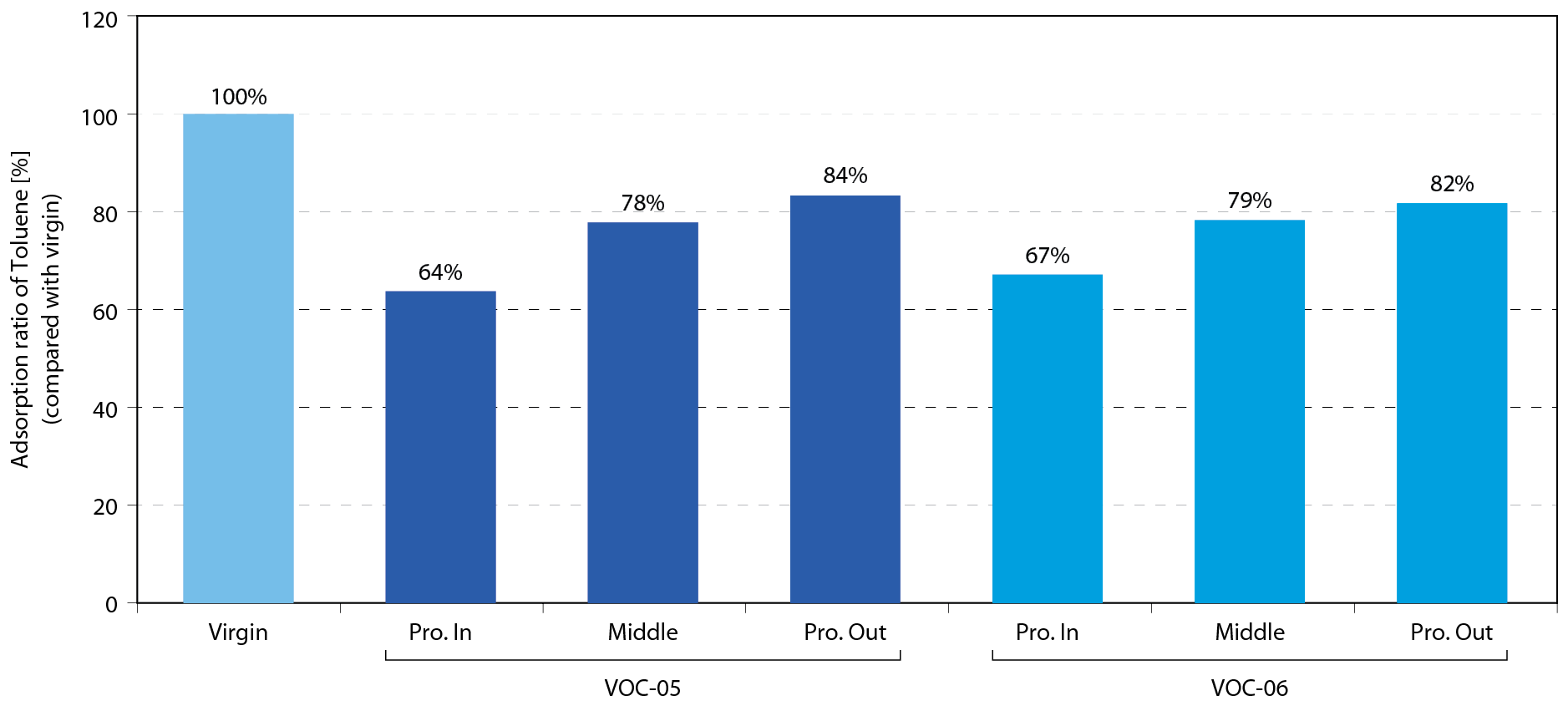
結果與分析
在VOC-06安裝逆脫附裝置完成後,首先持續進行高溫逆脫附但並不投入運轉,接著在約30天的逆脫附測試期間,VOC-06出口VOCs濃度持續保持在1.6ppm以上,並針對VOC-06出口端進行氣體取樣 表2。可看出在進行逆脫附時,較高沸點的PGME、PGMEA會被大量脫附出來,進而導致逆脫附初期VOC-06出口濃度偏高的現象,同時也驗證了轉輪取樣切片的分析結果,亦即有大量高附沸點有機物,因長期受熱不均而累積在轉輪出口處。而隨著持續的正逆脫附切換,VOCs出口濃度在一個月後已可以穩定小於1.4ppm以下 圖10,出口處理濃度改善12%、去除率超過99% 圖11,單台VOC處理設備排放預估減量可達到0.3噸/年。若持續進行正逆脫附切換,可持續改善去除效率。對比廠區內其他VOCs處理設備,也可看出經逆脫附處理後之轉輪效率有大幅提升,僅次於廠區新設之五年內轉輪 圖12。
Unit:μg/m3 |
|||||
IPA |
Acetone |
PGME |
Toluene |
PGMEA |
|
---|---|---|---|---|---|
沸點(°C) |
82 |
56 |
118 |
110.6 |
145 |
正脫附 |
3.6~163 |
6.0~8.4 |
9.2~79 |
1.4~5.6 |
6.5~18 |
逆脫附 |
237~316 |
39~90 |
491~677 |
1.3~5.7 |
225~339 |
圖10、VOC-06執行高溫逆脫附後之轉輪出口濃度變化
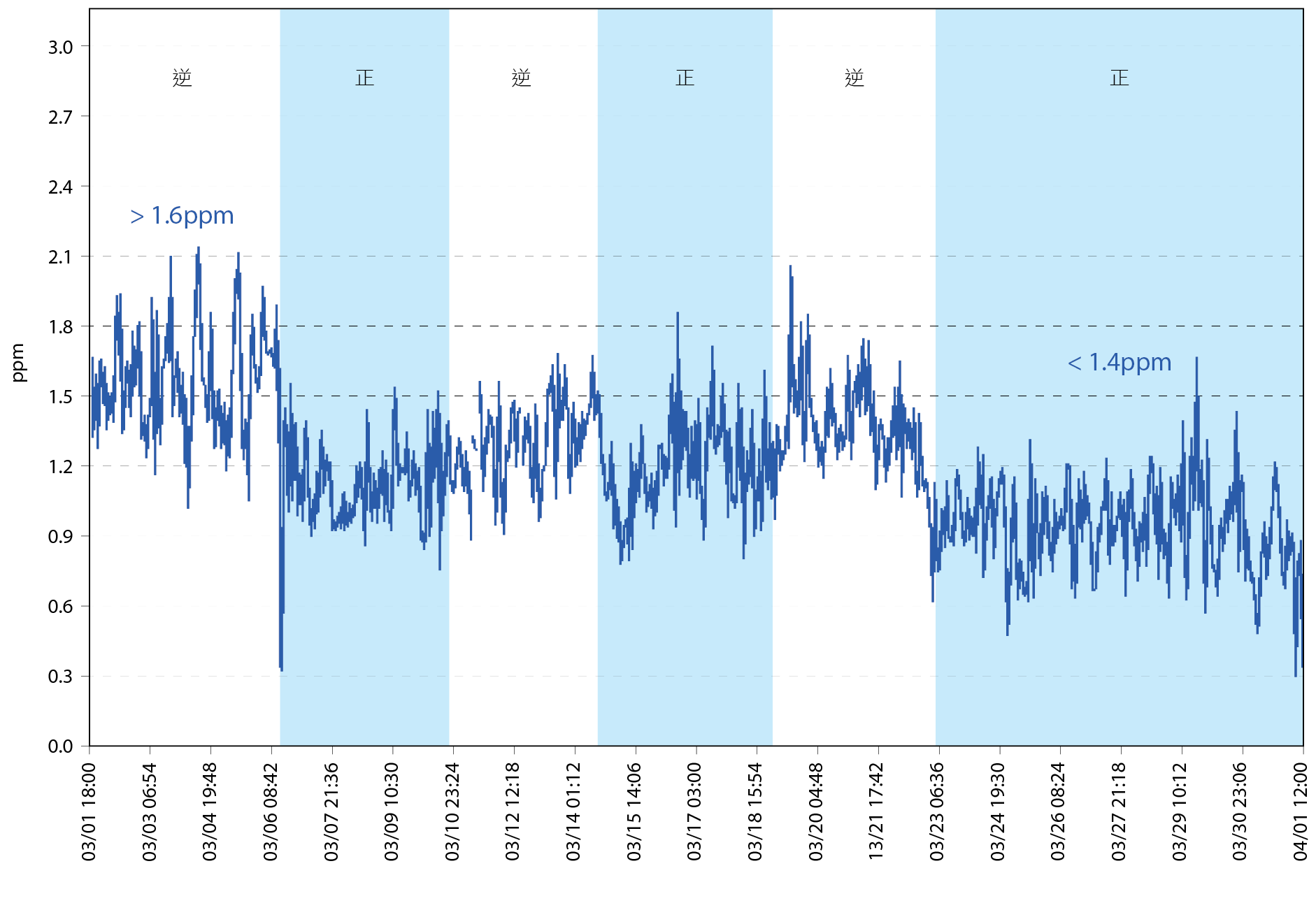
圖11、VOC-06執行高溫逆脫附後轉輪對VOCs之去除率變化

圖12、F12P1/2 VOC設備去除率F-chart
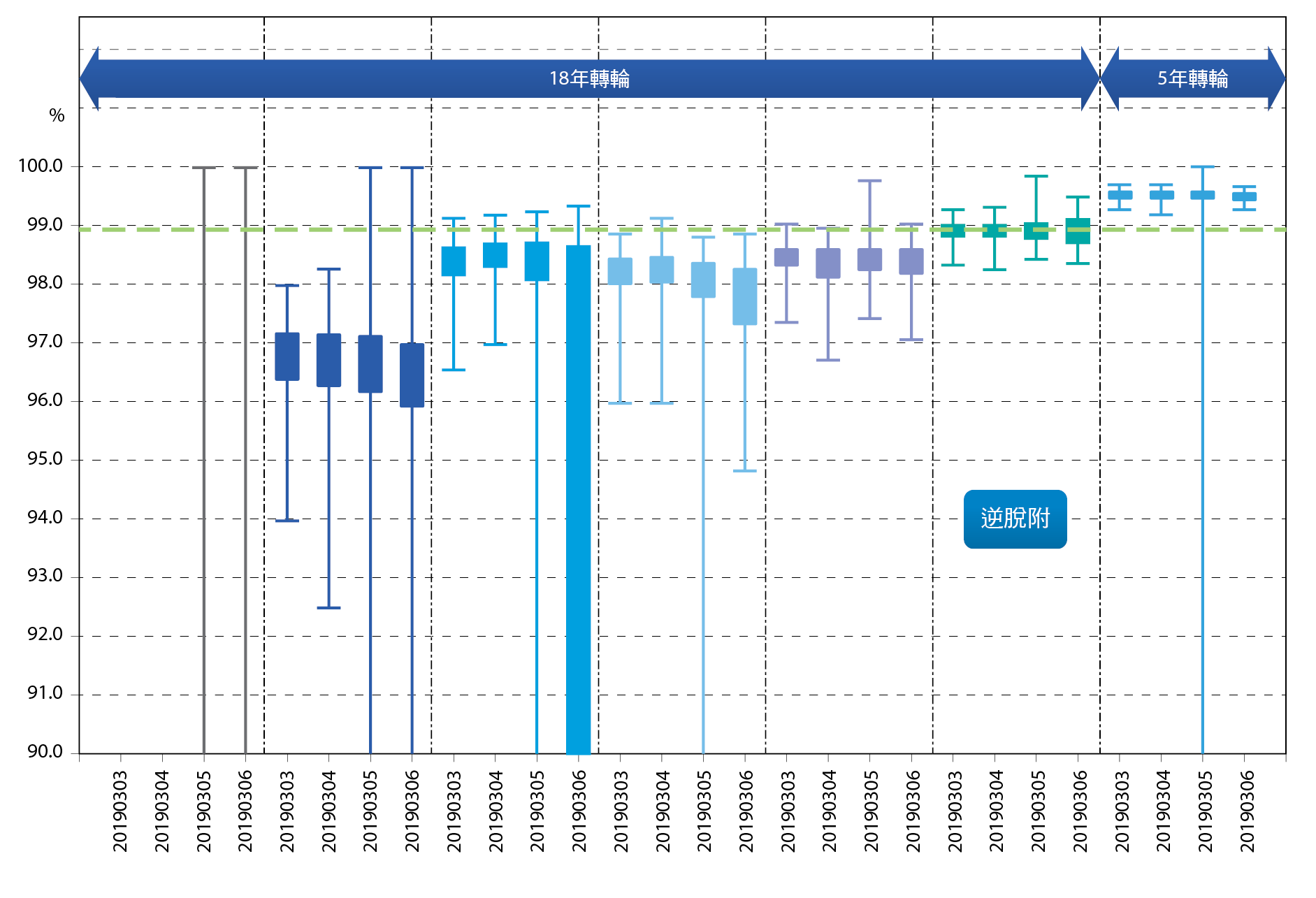
結論
針對沸石轉輪之效能改善,廠務先進已有提出許多做法。如使用潔淨空氣進行轉輪熱脫附,以4ppm的潔淨空氣相對於原本180ppm進行測試,轉輪出口濃度降低0.6ppm,總排放量降低12%,另外作為脫附用載流氣體,若是可提升脫附出口溫度(T5),則當T5溫度由40℃上升至55℃時,去除效率可以額外增加0.3%。而陳仲祥等人於2018年提出使用調高脫附溫度至250℃,脫附出口溫度調高至100℃,並調降轉輪轉速等做法,可將去除效率由91%提升至96%。
而本次經由轉輪高溫逆脫附,可使轉輪進行更全面的再生,是以往的高溫脫附以及例行預防保養的水洗方式時所無法做到的。本次執行高溫逆脫附專案,針對廠區VOC-06的轉輪進行取樣分析,確認轉輪在長期使用下,吸附容量衰退至70%以下,高沸點有機物累積在轉輪出口側並影響VOCs處理效率。故於VOC-06安裝高溫逆脫附裝置,使用GC-MS分析轉輪出口氣體樣本,發現在逆脫附運轉下,內部高沸點有機物(PGME/PGMEA)被脫附出來,進而使VOCs出口濃度上升至1.6ppm以上。而隨著持續的正逆脫附切換,VOCs出口濃度在可穩定小於1.4ppm以下,出口處理濃度改善12%、去除率超過99%,實際VOCs排放預估減量可達到0.3噸/年。而從F-chart可看出,對比廠區內其他VOCs處理設備,經逆脫附處理後之轉輪效率有大幅提升(98.2%→99.2%)。以實驗結果來看,經高溫逆脫附手法,轉輪可以恢復其吸附容量,使得VOCs出口濃度及去除效得到明顯改善。亦即是在目前的高溫脫附以及冷凝方式外,更進一步提升轉輪效率之方法。
參考文獻
- Recommendation from the Scientific Committee on Occupational Exposure Limits for Refractory Ceramic Fibres, 2011.
- 張書豪,科學園區空氣污染物排放特性之探討,1999。
- 白曛綾,沸石濃縮轉輪焚化系統操作績效自我評估管理制度,2003。
- 許菁珊,沸石對於光電產業揮發性有機化合物之吸脫附研究,2006。
- Mitsuma, Y., Ota, Y., Kuma, T., Hirose, T., “Practice of The VOC Abatement by Thermal Swing Ceramic Monolith Adsorbers,” Proc. 4th Japan-Korea Syposium on Seperation Technology, p479-482, Tokyo. Japan, 1996.
- 竹科氣膠課程Absorption theory.
- 錢立行、陳庭鈞,排氣革命-揮發性有機物減量新思維,300mm FABS廠務季刊第二十二期,2016。
- 葉峮甫、林哲冠、周家祿,先進製程之高沸點揮發性有機物處理技術應用, 300mm FABS廠務季刊第二十六期,2017。
留言(0)