摘要
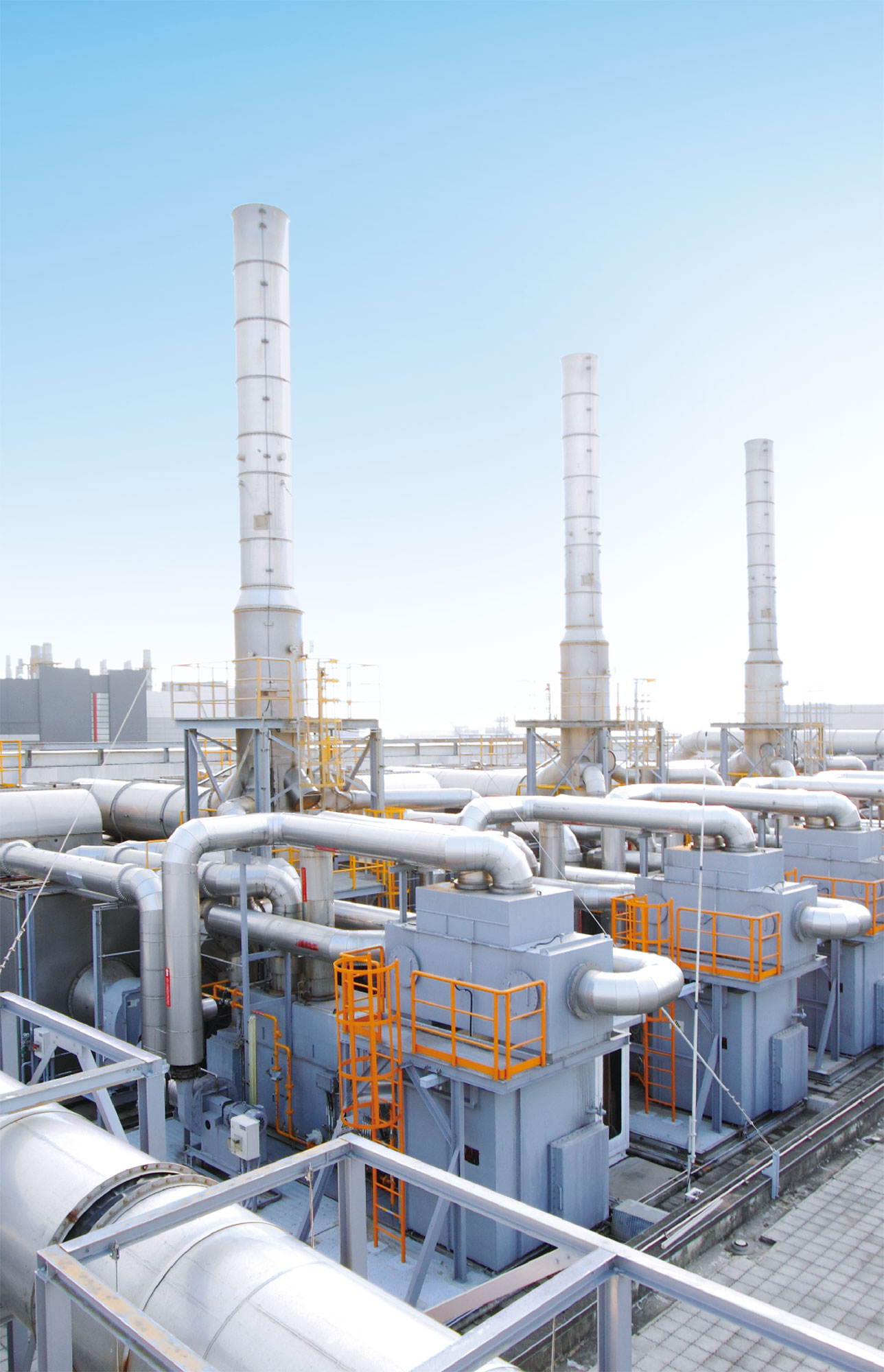
排氣革命 - 揮發性有機物減量新思維
本文主要探討半導體廠排氣中揮發性有機物處理設備─沸石濃縮轉輪系統之設計改善,將脫附用載流氣體從入口高濃度廢氣變更為脫附後乾淨空氣,嘗試以新思維降低揮發性有機物排放量,並針對轉輪後確實殘留高沸點VOCs進行實證,供後續進行相關改善之參考。
前言
半導體製程使用大量揮發性有機物(Volatile Organic Compounds; VOCs),依據世界衛生組織(World Health Organization, WHO)之定義,VOCs為沸點介於50~260℃之間的有機物質,其特性為常溫常壓下具有高蒸汽壓和易蒸發性能。於生產晶圓的流程中,黃光製程在光罩、顯影等過程需以丙二醇甲醚(PGME)及丙二醇甲醚醋酸酯(PGMEA)來當作顯影及光阻劑,酸槽機台則利用異丙醇(IPA)對清洗後之晶圓進行乾燥,其自然揮發經由廠務排氣管路送至廠務系統處理後排放。
目前半導體公司處理VOCs多選用沸石濃縮轉輪系統加上直燃式燃燒爐,其處理能力皆能達成行政院環保署公布之「半導體製造業空氣污染管制及排放標準」排放削減率應大於90%或工廠總排放量應小於0.6 kg/hr之規範,由於台積公司的環保目標為「致力達成環境永續發展,成為世界級之環保標竿企業」,因此,除完全遵守政府之環保法規外,更領先業界採取諸多環保措施,善盡企業之社會及環境責任。
廠務以此為理念檢視空污處理系統,由分析數據顯示處理後排放氣體以VOCs佔最大宗,以十二廠一期為例,2014年VOCs佔總排量54.8%,因此,如何降低排氣中VOCs總量乃成為落實環保政策之首要目標。
文獻回顧
為找出降低VOCs排放總量之有效對策,必須先針對廠內現況,沸石濃縮轉輪+直燃式燃燒爐現有設計及各項操作參數進行探討。
依上游排氣需求,本公司空氣污染處理設備運轉風量約介於40,000~ 10,0000 CMH (m3/h)之間,處理設備入口濃度介於50~180ppm之間,考量高處理效率及低經濟成本(USEPA, 1999 )[1],如 圖1所示,各廠設計時皆選用沸石濃縮轉輪+直燃式燃燒爐當作VOCs處理設備。其原理主要分為以下幾步驟,如 圖2所示,VOCs從上游製程經排氣管道進入此系統,第一步驟為先通過含疏水性沸石之轉輪,疏水性沸石於常溫下可吸附氣體中之VOCs,剩餘空氣則從煙道排出;第二步驟利用從入口導入之一部分排氣,先經過沸石轉輪中的冷卻區進行轉輪降溫以提升吸附能力,再進入熱交換器與後端焚化系統熱交換而預熱至180~230℃,並進入轉輪內利用高溫將有機物脫附,此時氣體中污染物濃度大約可控制為入口處廢氣之5至20倍左右,而脫附下來之有機物則可於第三階段進行高溫焚化,在超過700℃以上的溫度下,可有項達到濃度VOCs去除之效用。
圖1、製程排氣中VOCs 濃度及流量關係圖
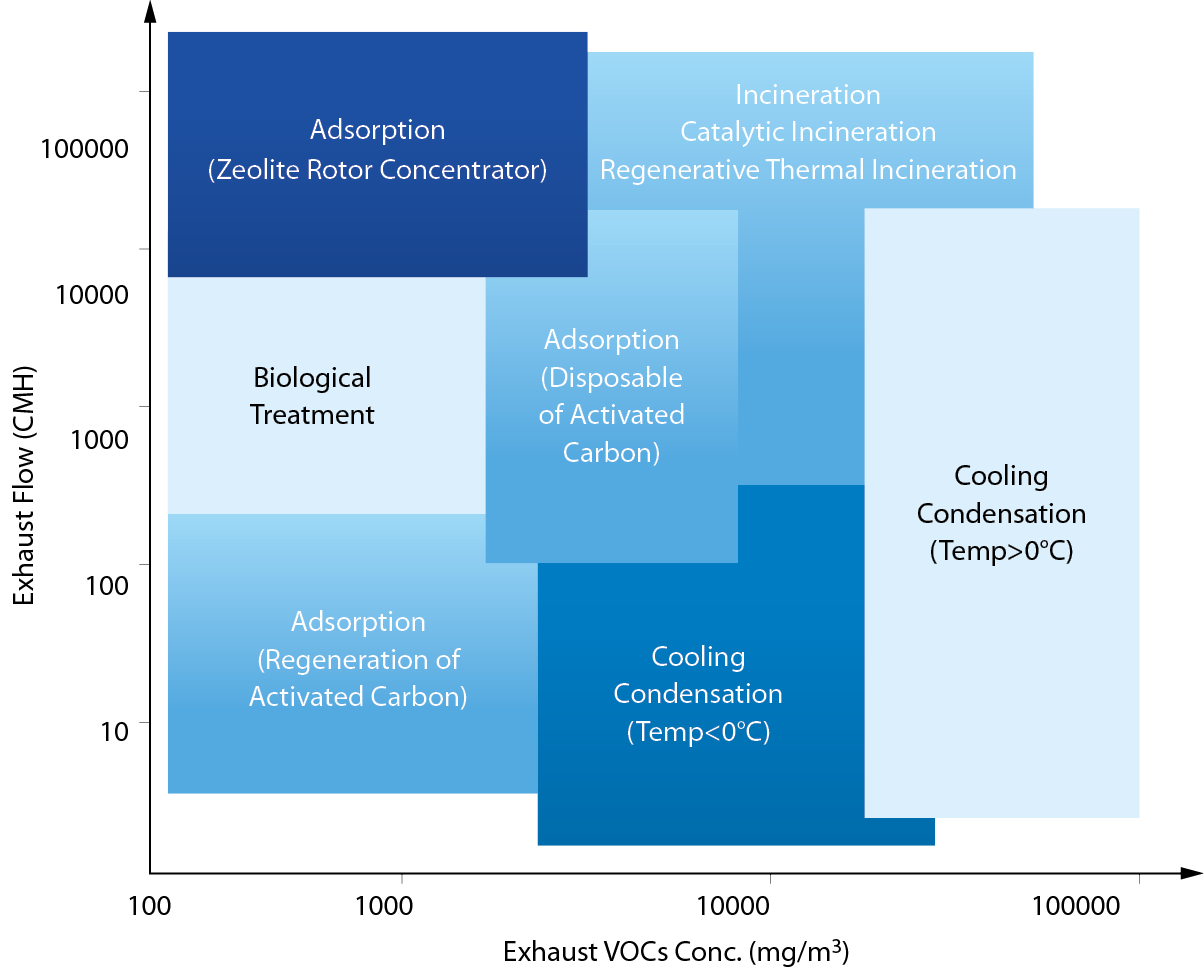
圖2、沸石濃縮轉輪系統示意圖
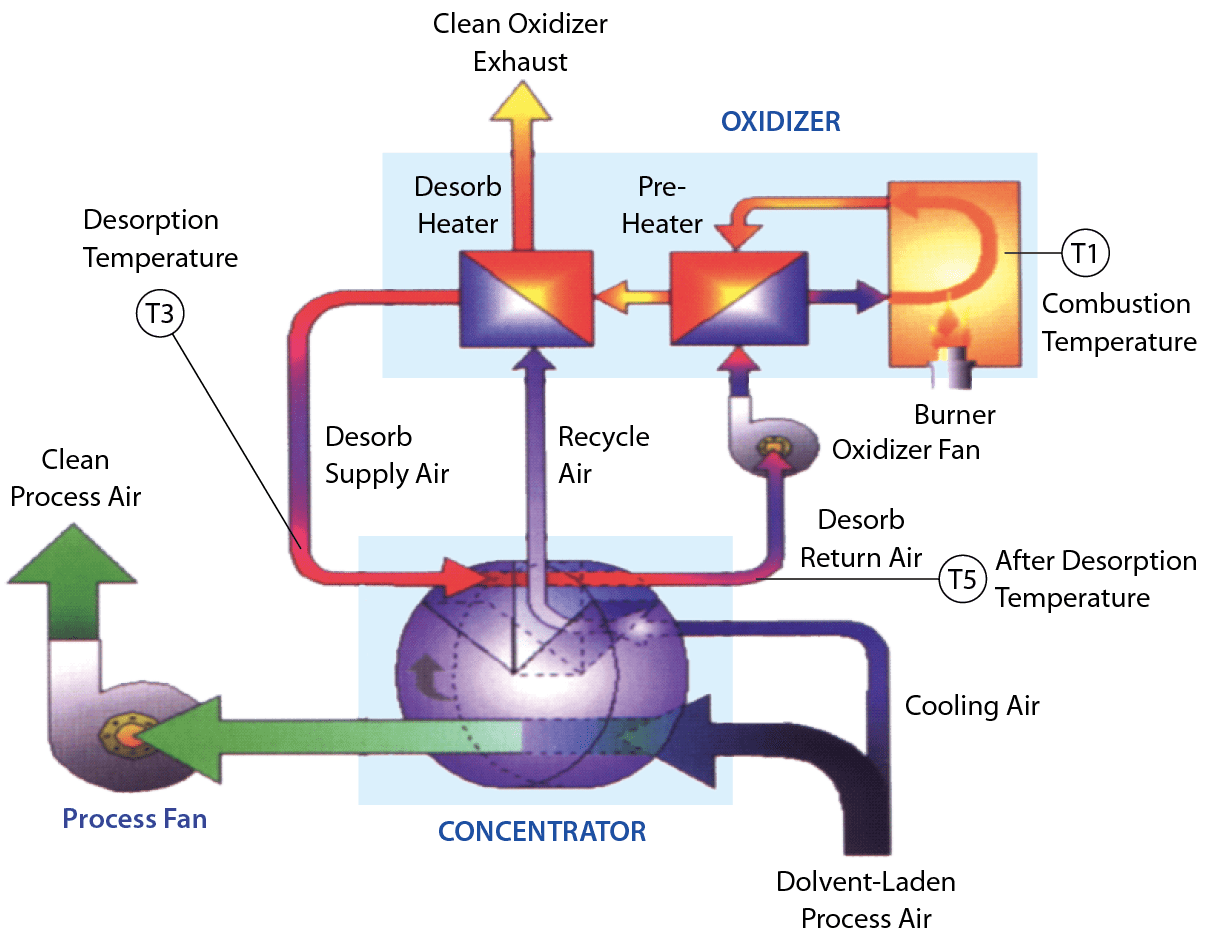
運轉參數測試上找尋最佳效能已經普遍被研究,文獻指出[2],利用實驗室建置小型沸石濃縮轉輪系統進行進流溫度、濕度、轉輪轉速、濃縮倍率對VOCs排放削減率之影響,測試結果顯示處理的廢氣若溫度高於35℃時,去除效率明顯下降,理論上溫度越低VOCs越易吸附於沸石上,但實際溫度低導致相對濕度變高,水氣堵塞沸石影響其效能;而轉輪轉速若太快,將導致脫附區未有充足時間進行脫附,而太慢則會造成吸附區已飽和卻尚未運行至脫附區,兩者皆會使排放削減率下降。
計畫方法
本計畫主要針對沸石濃縮轉輪系統之設計進行改善,第一步為解析本廠VOCs之組成成份,以瞭解其特性當作後續改善之基礎。研究方法以適合實廠採樣之傅里葉轉換紅外光譜儀(FTIR)架設於沸石濃縮轉輪入口、轉輪出口及與燃燒爐排氣合併之煙囪出口(如 圖3),並選擇入口VOCs成份分析之主要物種PGME (佔整體廢氣63.1%)、PGMEA、HMDS等(如 表1)。T3操作許可介於180~220℃之間,各廠實際操作參數介於200~220℃之間,但從監測發現沸石轉輪脫附區出口載流氣體溫度T5皆小於80℃,以Fab12A P1為例,調整脫附風車風量改變濃縮比,脫附風車全載時風量3420CMH時(濃縮比12.7倍)脫附區出口載流氣體溫度只能達到70℃,而為節省天然氣而減小脫附風量,調整濃縮比至20倍時,T5溫度更只能達40℃,此時轉輪脫附區剖面如 圖4所示。
圖3、廠內製程排氣VOCs 成份濃度監測示意圖
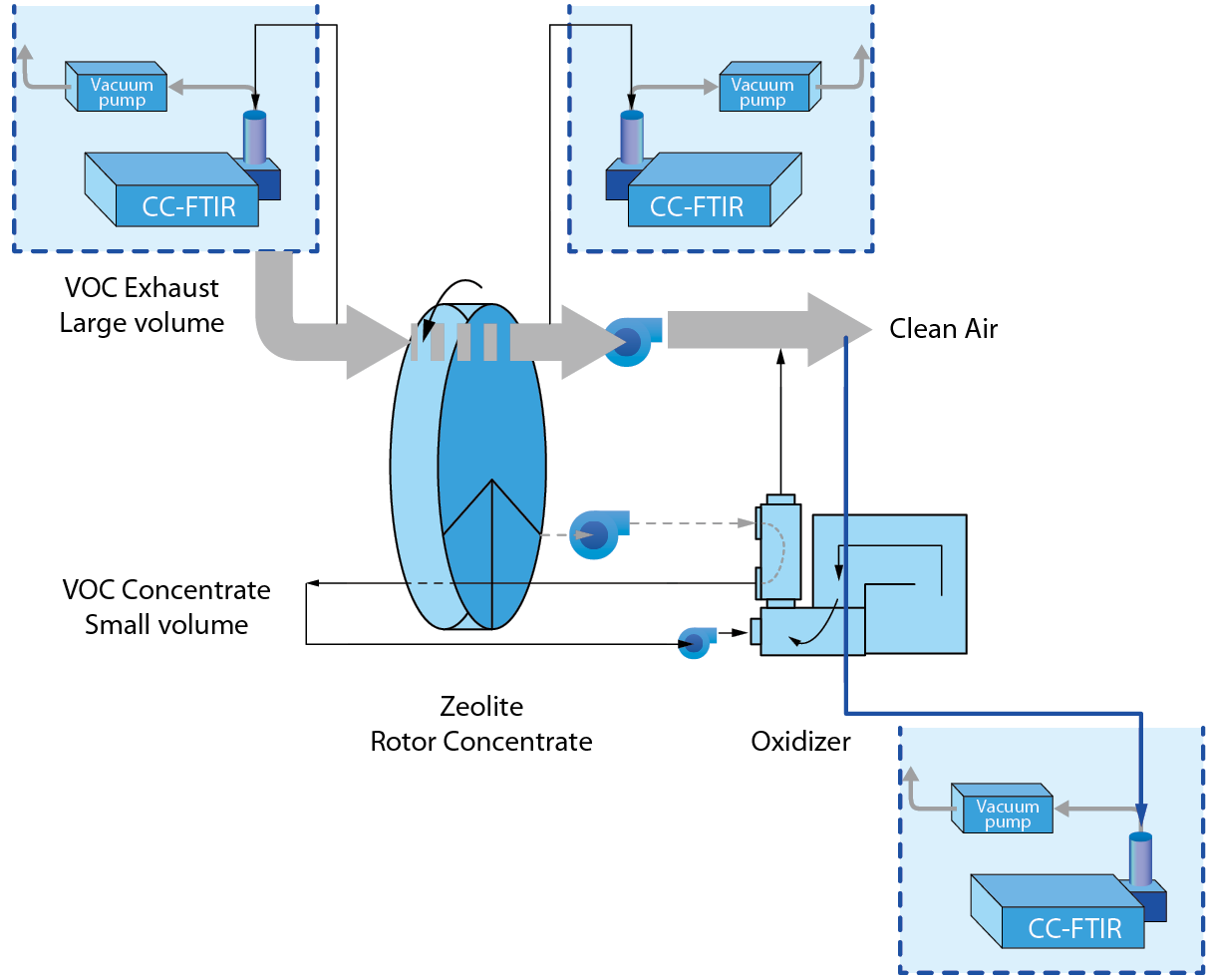
Chemical Compounds |
Concentration (ppmv) |
|||||||
---|---|---|---|---|---|---|---|---|
Max |
Average |
|||||||
Rotor In |
Rotor Out |
Rotor In |
Rotor Out |
|||||
PGMEA |
17.37 |
12.2% |
0.29 |
22.0% |
12.57 |
12.5% |
0.19 |
23.5% |
Isopropanol |
35.05 |
24.5% |
ND |
- |
23.38 |
23.3% |
ND |
- |
HMDS |
0.33 |
0.2% |
ND |
- |
0.18 |
0.2% |
ND |
- |
PGME |
90.11 |
63.1% |
1.03 |
78.0% |
64.11 |
64.0% |
0.62 |
76.5% |
圖4、轉輪脫附區剖面溫度變化示意圖
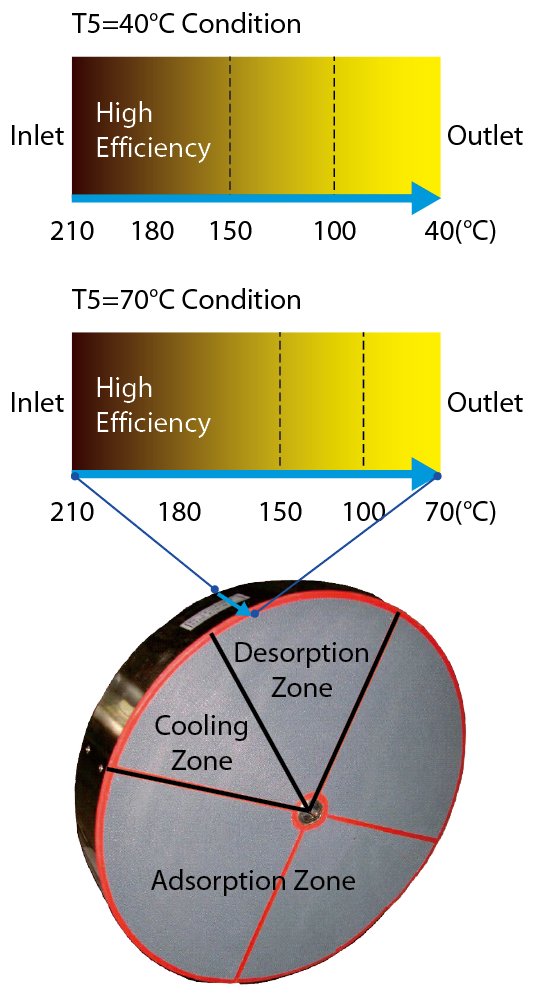
脫附為吸熱反應,反應物沸點越高代表脫附所需熱值越高,脫附區溫度決定是否可將沸石中VOCs脫附乾淨,而VOCs成份分析之主要物種PGMEA沸點高達146℃、PGME、HMDS沸點皆大於120℃ (詳見 表2),分子量較小之Iso-propanol亦超過80℃,顯示若只靠熱脫附,沸石濃縮轉輪中後段將無法脫附乾淨,高沸點物質於沸石內殘存影響排放削減率。此時若採增加脫附區入口溫度(T3)可提升脫附區整體溫度,但文獻顯示將增加系統當機頻率[3]及超過氣密膠條材質耐溫極限,故本研究跳脫調整各項操作參數之桎梏,嘗試新思維,從檢討系統設計著手。
Compounds |
Boiling point(°C) |
---|---|
PGMEA |
146 |
Isopropanol |
83 |
HMDS |
126 |
PGME |
120 |
沸石轉輪吸脫附方程式較常使用Freundlich Isotherm Equation,如下列等式:
qe = KCf1/n
qe = 吸附劑的平衡吸附容量,mg(吸附質)/g(吸附劑)
Cf = 平衡時吸附質在氣相中的分壓或濃度,atm或ppm
K, n =經驗常數,吸附劑性質、溫度相關
從吸附容量qe與平衡時氣相濃度Cf呈正相關可知,脫附用載流氣體初始濃度越低,則與沸石上吸附濃度差距越大,殘留於沸石上之VOCs越少,脫附較乾淨之沸石濃縮轉輪轉至吸附區後VOCs排放削減率更佳。目前各廠沸石濃縮轉輪使用之脫附用載流氣體,皆來自轉輪入口尚未處理之高濃度廢氣,如圖5,VOCs濃度高達180ppm,本計畫修改原始設計,利用吸附後之乾淨氣體抽回脫附區當作載流氣體(如 圖6),其濃度低至4ppm,與原始設計使用入口高濃度廢氣相比差距達45倍之多。
圖5、改善前沸石濃縮轉輪系統設計圖
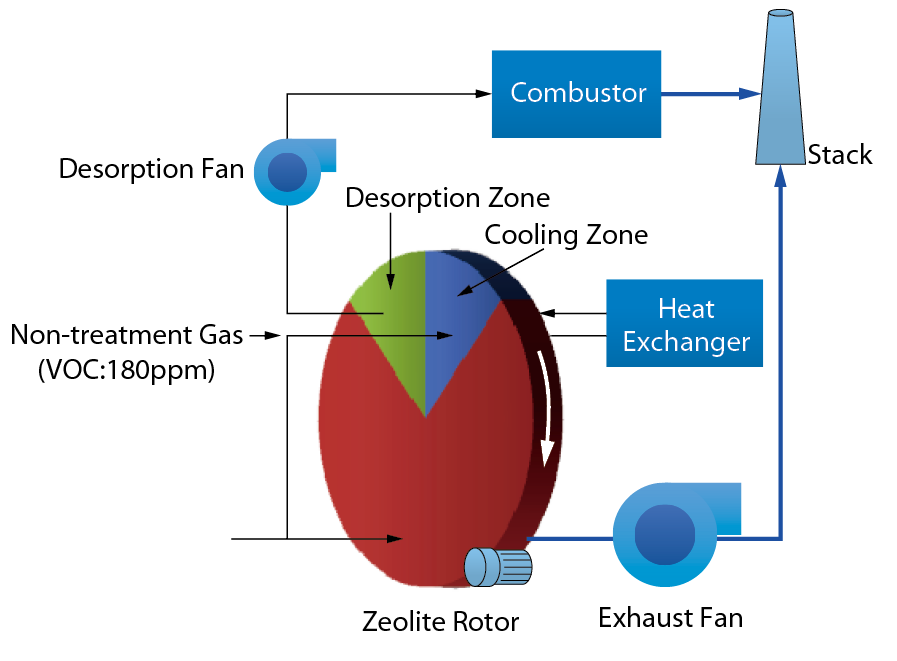
圖6、改善後沸石濃縮轉輪系統設計圖
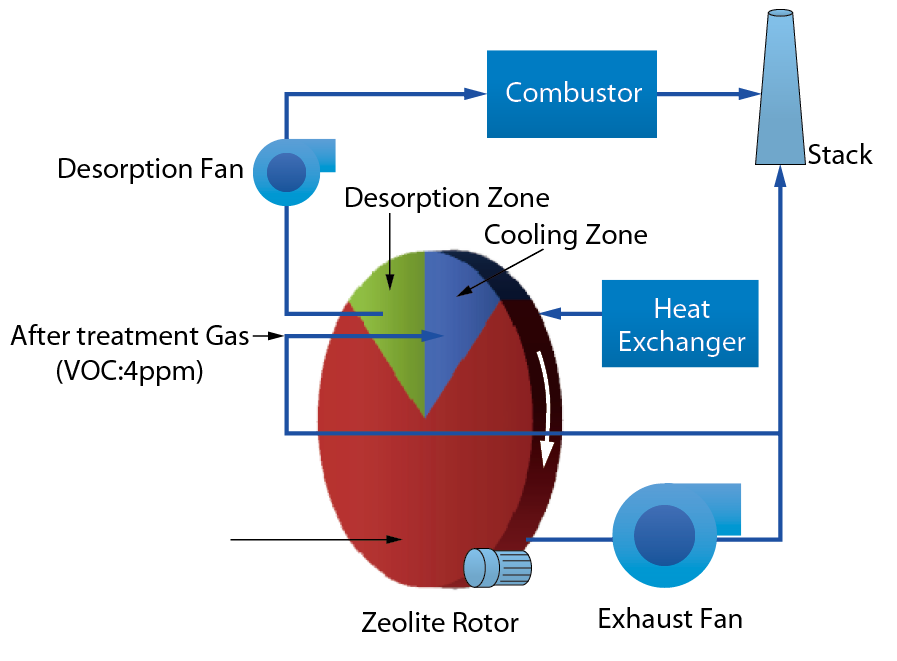
結果與分析
本研究首先於十二廠一期VOCs處理設備進行改善,並以變頻器控制脫附風車以調整脫附風量,因脫附區總熱值與脫附風量成正比關係,脫附風車增加變頻器更可精確增減脫附風車風量以達到改變熱值之實驗目的,而熱值增加之顯著監測因子即為脫附區出口載流氣體溫度(T5)上升。
脫附區出口載流氣體溫度(T5) vs排放削減率實驗結果顯示(詳見 圖7),脫附區出口載流氣體溫度越高,沸石濃縮轉輪排放削減率越佳,當脫附區出口載流氣體溫度由40℃上升至55℃時,排放削減率增加0.30%,排放總量下降10%;當溫度進一步調升至70℃(此時脫附風車60Hz滿載),排放削減率增加至0.62%,排放總量下降達20%,證實轉輪後確實殘留高沸點VOCs。
圖7、VOCs 排放削減率與脫附區出口載流氣體溫度(T5) 關係圖
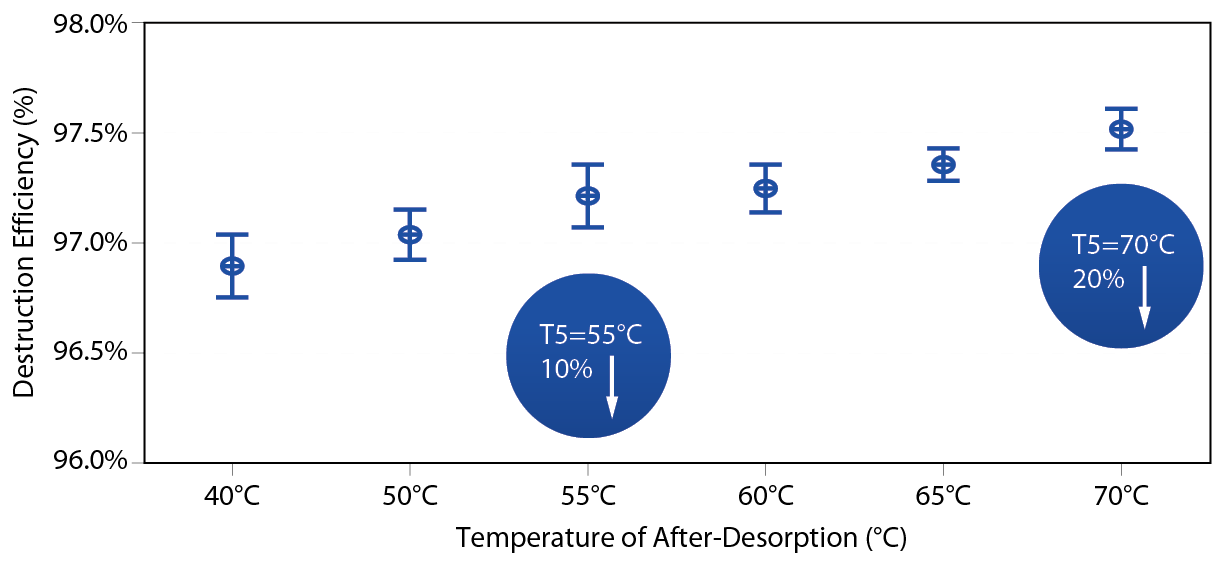
為進一步驗證沸石濃縮轉輪脫附用載流氣體初始濃度越低,則與沸石上吸附濃度差距越大,殘留於沸石上之VOCs越少,脫附較乾淨,使沸石濃縮轉輪轉至吸附區後VOCs排放削減率更佳之假設,十二廠一期選擇兩台沸石濃縮轉輪當作實驗組與對照組(如 圖8)。實驗組為本團隊改善後之沸石濃縮轉輪,脫附用載流氣體來自吸附後之乾淨氣體,對照組則使用原廠設計,脫附用載流氣體來自轉輪入口尚未處理之高濃度廢氣,兩組背景條件比較如下:
圖8、脫附用載流氣體變更改善前後入出口濃度變化趨勢圖
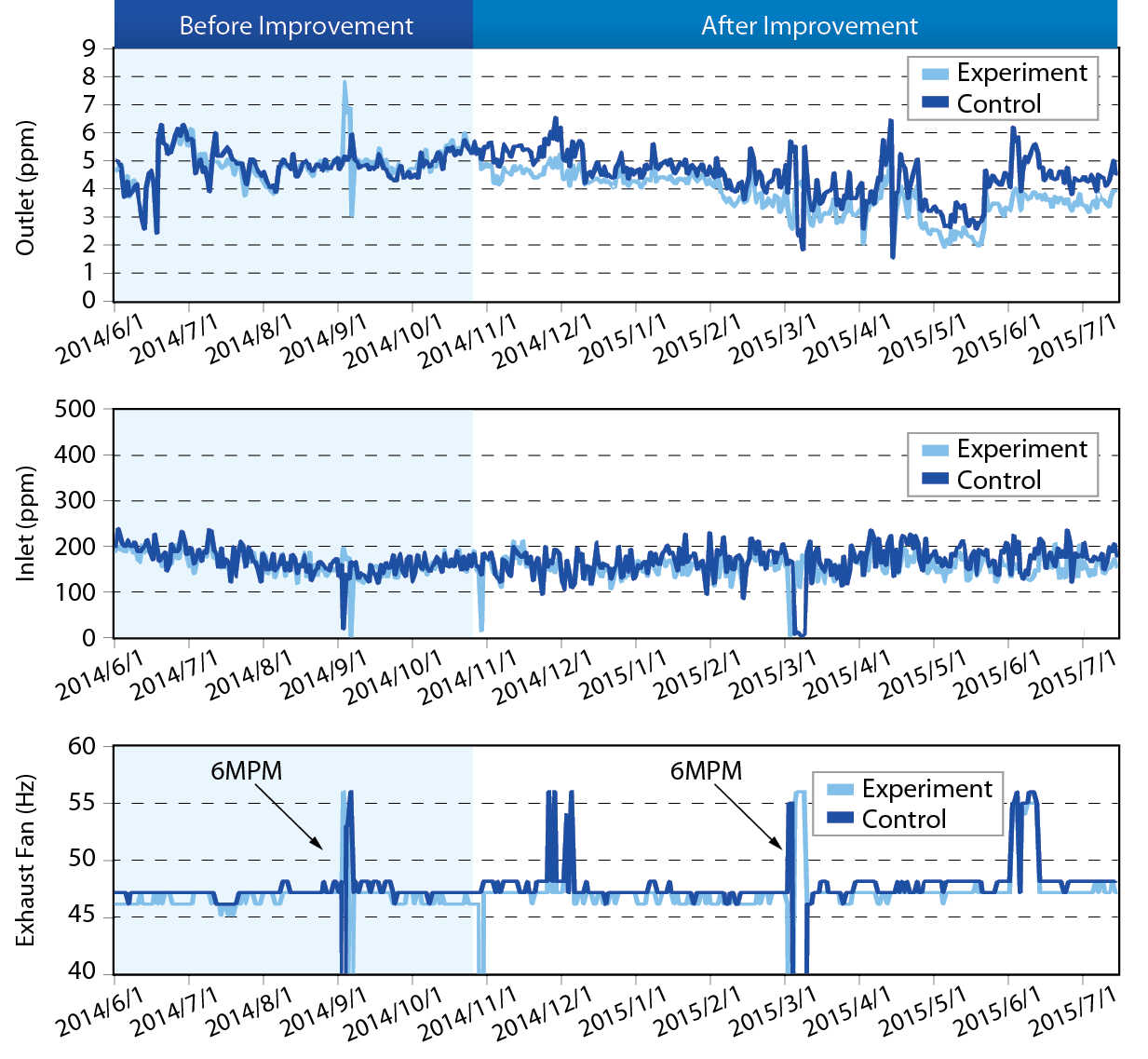
- 入口來源相同:F12P1 VOC05/ 06兩台VOC來源皆為P2 Litho,共管至VOC轉輪入口處才分流至兩台處理,入口濃度平均約160ppm,入出口VOCs濃度相差<3%。
- 測量儀器相同:VOC05/06兩台為同一支煙道排放(P014) ,入出口皆採用同一台THC監測儀進行切點監測。
分析結果顯示(詳見 表3),實驗組相較對照組出口濃度降低0.6ppm,去除率提升0.36%,總VOCs排放量降低12% [0.36%÷(100%-97.04%)= 12%]。
Before Improve- ment (1) |
Inlet Conc. (ppm) |
Outlet Conc. (ppm) |
Defect Removal Efficiency (DRE; %) |
|||||
---|---|---|---|---|---|---|---|---|
Experiment Group (A) |
Control Group (B) |
Experiment Group (A) |
Control Group (B) |
Experiment -Control (A-B) |
Experiment Group (A) |
Control Group (B) |
Experiment -Control (A-B) |
|
162.22 |
167.07 |
4.8 |
4.88 |
-0.08 |
97.04% |
97.08% |
-0.04% |
|
After Improve- ment (2) |
Inlet Conc. (ppm) |
Outlet Conc. (ppm) |
Defect Removal Efficiency (DRE; %) |
|||||
Experiment Group (A) |
Control Group (B) |
Experiment Group (A) |
Control Group (B) |
Experiment -Control (A-B) |
Experiment Group (A) |
Control Group (B) |
Experiment -Control (A-B) |
|
160.9 |
167.3 |
3.77 |
4.46 |
-0.69 |
97.66% |
97.34% |
0.32% |
|
Before- After (1-2) |
Inlet Conc. (ppm) |
Outlet Conc. (ppm) |
Defect Removal Efficiency (DRE; %) |
|||||
Experiment Group (A) |
Control Group (B) |
Experiment Group (A) |
Control Group (B) |
Experiment -Control (A-B) |
Experiment Group (A) |
Control Group (B) |
Experiment -Control (A-B) |
|
1.32 |
-0.22 |
1.03 |
0.43 |
Improvement Benefit: 0.6ppm |
0.62% |
0.26% |
Improvement Benefit: 0.36% |
結論
半導體廠生產晶圓的流程中因使用大量VOCs,佔廠務端空污排放量的大宗,其排放量佔總量高達50%左右,故投入資源針對其進行改善可達到較佳效益。本研究結論顯示改變沸石濃縮轉輪之原始設計,將脫附用載流氣體從入口高濃度廢氣變更為脫附後乾淨空氣,確實幫助提升排放削減率,降低廠內VOCs之排放量,達到空污排放減量的目標。本研究主要成果如下:
- 利用吸附後之乾淨氣體抽回脫附區當作載流氣體,其濃度與原始設計使用入口高濃度廢氣相比差距達45倍之多 (180ppm4ppm)。
- 由實驗組與對照組進行比對,VOCs處理設備出口濃度降低0.6ppm,去除率提升0.36%,總VOCs排放量降低12%。
- 由實驗結果顯示,脫附區出口載流氣體溫度越高,沸石濃縮轉輪排放削減率越佳,當脫附區出口載流氣體溫度由40℃上升至55℃時,排放削減率增加0.30%,排放總量下降10%;當溫度進一步調升至70℃,排放削減率增加至0.62%,排放總量下降達20%。
參考文獻
- Technical Bulletin:Choosing an Adsorption System for VOC: Carbon, Zeolite, or Polymers (USEPA, 1999)
- 白曛綾,沸石濃縮轉輪焚化系統操作績效自我評估管理制度參考手冊(2003)
- 張豐堂,沸石轉輪焚化技術常見問題與解決方法(2003)
留言(0)