摘要
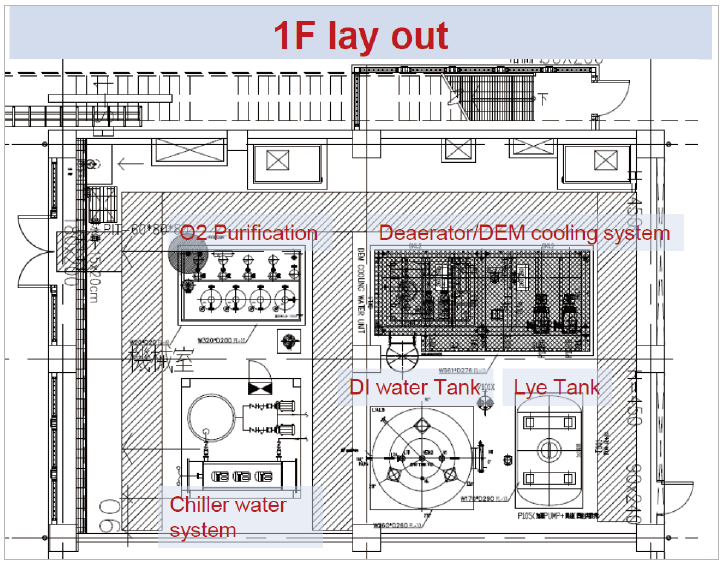
水電解產氫技術應用與系統穩定運轉管理
Keywords / Stream Methane Reformer,MeOH Cracker,Electrolysis2
氫氣為晶圓製造上會使用到的大宗氣體(Bulk Gas),N5製程以下EUV機台更讓用量突增(18廠滿載狀況下,估計氫氣每天需求達48台槽車),先前台積工廠用的氫氣主要由蒸氣甲烷(天然氣)重整或甲醇裂解方式生產,生產過程中會造成二氧化碳副產物排至大氣中,而水電解產氫方式副產物僅有氧氣及水,運用此技術可達到低碳排目標。本文除了探討目前氣體廠主流製氫方法流程外,更詳細說明在台積廠內建置第一套氫氣製造系統(水電解,最大產能為1000CMH)的心路歷程,包含安全設計符合國際氫氣安全設計標準(41項),氫氣/氧氣vent管路位置也透過模擬排放濃度軟體進行配置,最後藉由氣體廠經驗複製學習(共完成BKM 21項、PRS 11項、LSL 7項)、同時要求氣體廠需有常駐值班人員並對其進行相關應變操作訓練,確保此套系統能安全導入且產品品質亦能符合標準。
Hydrogen is one kind of bulk gas used in semiconductor fabrication plant. Below N5 node process, EUV tools import will cause a sudden increase in consumption(Depend on F18 factory full loading, it is estimated that the daily demand for hydrogen will reach 48 H2 trailers). TSMC factories use Hydrogen that is produced by Stream Methane Reformer or MeOH Cracker process, but these production process would cause carbon dioxide by-products to be discharged into the atmosphere. By-products of water electrolysis hydrogen process are only oxygen and water, and using this technology can achieve the goal of low carbon emission. In addition to discussing the hydrogen production methods in gas plants, this paper also describe in detail the mental journey of building the first hydrogen production system(water electrolysis, with a maximum production capacity of 1000CMH) in the TSMC plant, including safety design in compliance with international hydrogen safety design standards, the position of the hydrogen/oxygen vent pipeline is also configured by simulating the emission concentration software, and finally learned by copying the experience of the gas plant. At the same time, request supplier have dedicated on duty in TSMC plant and provide them with relevant emergency operation training to ensure that the system can be safely introduced and the product quality can also meet the standards.
1. 前言
現今產氫氣來源(圖1)超過95%以化石燃料為基礎[1],48%來自天然氣重整、30%來自醇類重整,18%來自焦爐煤氣,但生產過程中無法避免副產物(二氧化碳)排至大氣中造成溫室效應,而低碳排的電解產氫方式僅占約4%。亞東氣體為台積三大Bulk Gas供應商之一,目前主要供應F18P4/5/6氫氣原物料,其安南廠區於2021年3月18日正式啟用水電解製程產氫設備,其成品氫氣純度達99.9995%,且經過純化後可滿足半導體產業需求,滿載產能情況下,每年將減少超過3萬5000噸的二氧化碳直接排放,相當於超過100萬棵樹的年固碳量,對於節能減碳與效率都有顯著提升。台積F18P4/5/6工廠在Module/IMQR/NMC/FAC共同配合下,經過四次Pi-Run驗證,也於2022年1月14日轉為亞東安南水電解廠所生產的氫氣做使用。本文的重點將說明台積廠內(F18P4)設置的第一套水電解設備產氫後直接供應至FAB,除了低碳排優點外亦可減少人員更換氫氣槽車的Loading及槽車運輸上風險。
圖1、氫氣原料來源佔比
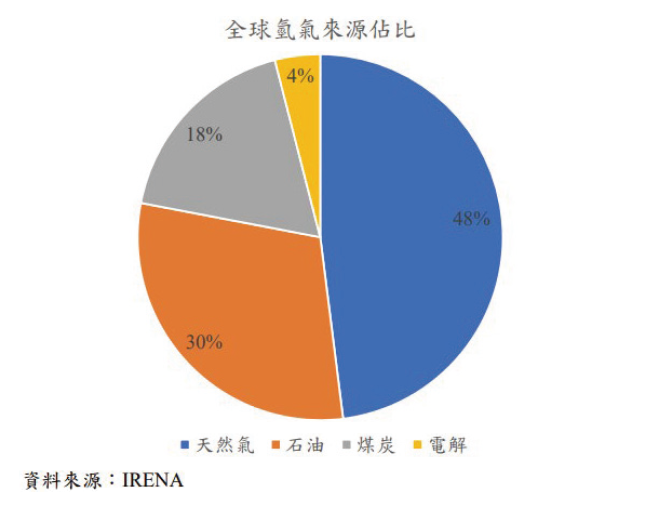
2. 文獻探討
2.1 台積現況使用氫氣製造方法探討
台積各廠目前使用氫氣的製造方法主要有三種 : 蒸汽甲烷(天然氣)重整、甲醇裂解、水電解,詳細可參見(表1)。
蒸汽甲烷(天然氣)重整方法主要在高溫(攝氏700~1100度)和金屬基催化劑催化的條件下,水蒸汽與甲烷反應產生一氧化碳和氫氣,重整反應中一氧化碳和水蒸氣會發生水煤氣變換,可以得到更多的氫氣,反應方程式如下。
CH4+H2O ⇌ CO+3H2
CO+H2O ⇌ CO2+H2
甲醇裂解方法為甲醇與超純水混合並在一定的溫度與壓力條件下通過催化劑,在催化劑的作用下,發生甲醇裂解反應和一氧化碳的變換反應,生成氫和二氧化碳,這是一個多組分、多反應的氣固催化反應系統,重整反應生成的氫氣和二氧化碳,再經過變壓吸附法(PSA)將其分離,最終得到高純度氫氣,反應方程式如下。
CH3OH → CO+2H2
H2O+CO → CO2+H2
CH3OH+H2O → CO2+3H2 (Total Reaction)
水電解製氫(鹼性電解法)由電解液(氫氧化鉀, KOH)及純水經電解槽電解後轉送至氣液分離器,液體經由泵浦回流電解槽,氫氣及氧氣分離並經脫氫/氧器(鈀觸媒催化)反應後送至分子篩吸附器進行游離水吸附最終出口產出製程用氣體,反應方程式如下。
4H2O+4e → 2H2↑+4OH- (Cathode)
4OH- → 2H2O+O2↑+4e (Anode)
2H2O → 2H2↑+O2↑(Total Reaction)
由製氫方式比較表(表2)來看,電力來源皆為綠電狀況下,水電解製程不僅為碳足跡最好(0.9kg CO2/kg H2),另在原物料取得、佔地空間、交期、Impurity、操作溫度、操作壓力、開機(復機)時間都優於其他兩項。
2.2 水電解產氫技術發展
目前常見水電解技術共有三種(圖2)[2]: ①鹼性電解法(Alkaline electrolysis, AEL)使用具有腐蝕性的氫氧化鉀(KOH)做為電解液,通直流電作用於電解液中的氫氧根離子(OH-)經多孔傳導膜遷移至陽極進行氧化反應釋出電子產生水與氧氣;水在陰極電解成氫離子(H+)與氫氧根離子(OH-)並接受電子而析出氫氣。此技術成熟且成本低,為大型電解產氫系統主要採用也是本案選用的方法;②質子交換膜電解法(Polymer electrolyte membrane electrolysis, PEMEL)使用固態的酸性聚合膜做為電解質,水在陽極電解成氫離子與氧氣並放出電子;氫離子經質子交換膜遷移至陰極與外部迴路傳導而來的電子結合產生氧氣。此技術因具有高電流密度特性而有較高的電解效率;③固態氧化物電解法(Solid oxide electrolysis, HTEL)使用具傳導氧離子(O2-)之陶瓷材料電解質,水以蒸氣的形式進入電解槽,在陰極電解成氫離子與氧離子,氫離子接受外部迴路傳導而來的電子生成氫氣,氧離子經陶瓷電解質遷移至陽極生成氧氣與放出電子。此方法需操作在高溫環境(攝氏700-1000度),目前仍處於未實用階段。
H2氣體廠 | 產線 | 製程 | 產能(NM3/h) | 產能利用率 | 品質[Ar] in H2 | 主要供應廠區 |
---|---|---|---|---|---|---|
三福台中廠 | Line1 | 天然氣重組 | 2500 | 53% | 6~12ppb | F15P7使用中 |
聯亞觀音廠 | SMR1 | 天然氣重組 | 700 | 100% | 1~20ppb | F15P34/F12P1245 使用中 F18P123有license |
SMR2 | 天然氣重組 | 1400 | 57% | F12P6使用中 F18P123/F12P7有license |
||
SMR3 | 天然氣重組 | 1400 | 99% | F15P56/ F12P7 使用中 F18P123有license |
||
聯亞樹谷廠 | SMR1 | 天然氣重組 | 1400 | 88%→100%(M209) | 4~20ppb | F14P3456 /F18P123 使用中
F18P78 / F14P8 預計M209使用 |
SMR2 | 天然氣重組 | 1400 | 88%→100%(M209) | F14P3456 /F18P123 使用中
F18P78 / F14P8 預計M209使用 |
||
亞東觀音廠 | Line1 | 甲醇裂解 | 2000 | 75% | 10ppb | F15P12使用中 |
亞東安南廠 | Line1 | 甲醇裂解 | 1000 | 80% | 10ppb | F18P456/F12P8 使用中 |
Line1 | 水電解 | 1000 | 80% | 1~10ppb | F18P46使用中 |
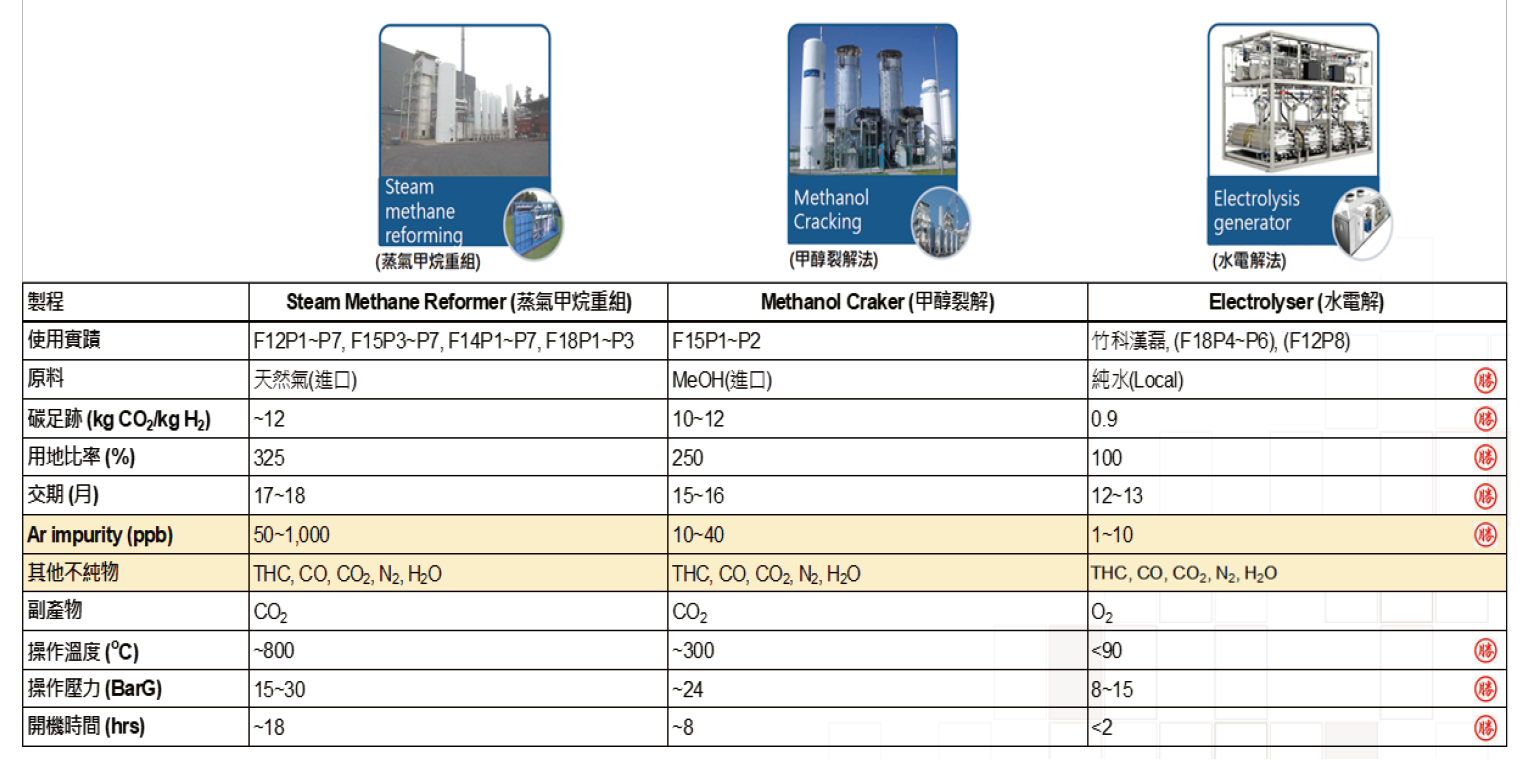
圖2、水電解技術介紹
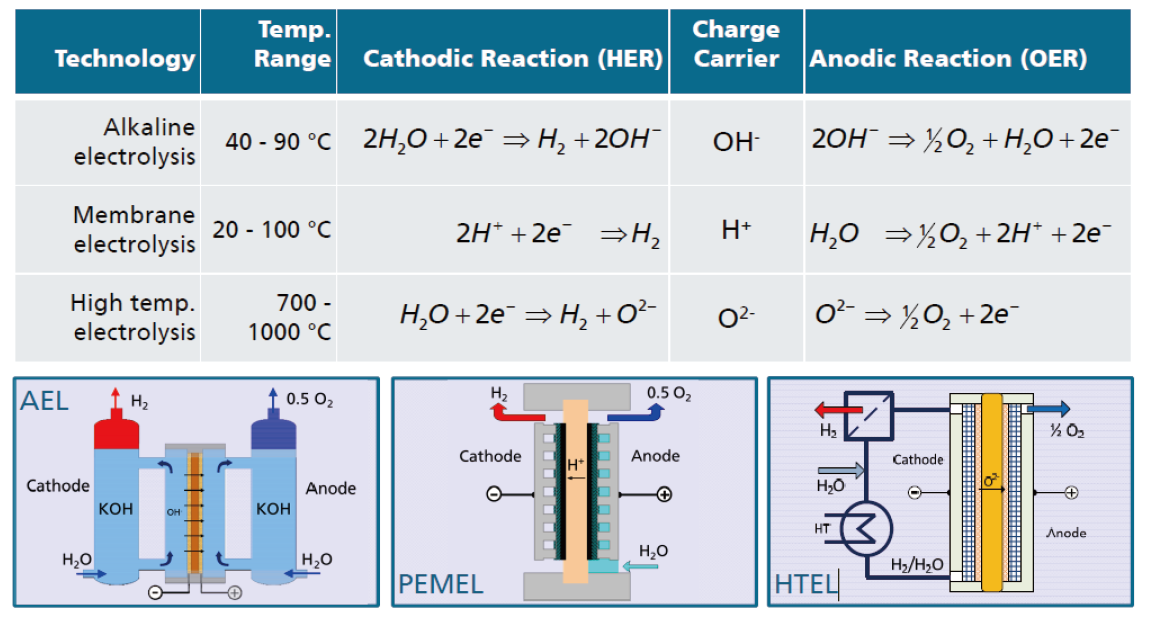
3. On-site氫氣水電解系統設計規劃
3.1 安全評估標準及設置
水電解氫氣設備於18P4新建廠時就納入評估規劃並需符合國際氫氣水電解安全設計標準 : 共6大類、41項(表3),系統建置於BSGS區域,採1F、2F房間配置才能涵蓋所有主設備及附屬設備。1F設置氧純化器、冰水機系統、純水桶槽、KOH桶槽、脫氧處理系統(圖3);2F共有兩間房間,除了電器室(圖4)外另1間房間為防爆規劃(圖5),設置電解槽、製氫框架(氫/氧分離器)、氫純化器。
分類(6) | 安全設計標準(41) | |
---|---|---|
1.生產設施安全 | 取得第三方符合認證(5) | 1.ISO 22734-2019使用水電解產氫製程安規 2. NFPA 2-2020 Chapter 2 Hydrogen Generation System 3. ASME for Piping & Vessel 4. SEMI S2 ESH Guideline 5.PHA(製程危害安全評估) |
2.本質安全設計 | 管控壓力(2) | 1.最大操作壓力 <15kg/cm2 2.無加壓設施 |
管控火載量(3) | 1.無儲存設施 2.製造含氫設施、管線.加總內部體積<30m3 3.採用乾式(無油式)變壓器 |
|
使用不燃、耐燃材(3) | 1.樑、柱、隔間牆、樓地板、天花板不燃材構造 2.設備、設施、管線不燃材構造 3.保溫棉不燃材、保險公司FM認可耐燃材 |
|
預防蓄積.火災爆炸(4) |
1.設置室外空間(3面不得有牆) 2.設置緊急排氣設備,當環境偵測25%LEL自動啟動緊急排器 3.氫氣排放管線,需符合『CGA G-5.5 H2 Vent system』安全標準 4.屋頂以輕質金屬板或不燃材料覆蓋,並保持斜度 |
|
保持安全距離(4) |
1.>15m:生產設施與臨近建築物或廠務重要供應設施(Fab/CUP/桶槽) 2.>15m:氫氣排放口與臨近臨近空氣入口、引火源、CDA compressor 3.>5m:與廠區週界線,臨近空氣入口、引火源、開口、行人動線、停車區 4.>4m:臨近危險性氣體管線、設施 |
|
3.防火、防爆 | 防火構造2小時(1) | 樑、柱、牆、樓地板 |
防爆構造(1) | 防爆牆、樓地板:氫氣製造場所 | |
設置消防安全設備(3) |
1.製造區:Deluge 一齊開放消防撒水設備+火焰偵測器 2.製造區:消防撒水設備+室內外消防栓 3.電氣房:惰性氣體滅火設備+空氣採樣火警+偵煙火警 |
|
4.供電安全 | 防爆電器(2) | 1.氫氣製造區 2.氫氣排放口<5m |
供電穩定(2) | 1.N+1設計 (廠務供電、氫氣電解槽供電) 2.緊急電+UPS |
|
5.耐震設計 | 安全重要係數(2) | 1. 1.25(建築物); 1.5(設施、設備) 2.管架、設施、設備耐震斜撐、角座固定 |
緊急關斷製造(4) | 1.地表加速度>120gal; 2.GMS-環境H2(氫氣生產區)/O2(氧氣生產區)或火焰偵測器作動 3.過流量偵測器或開關; 4.Local/Remote EMO連動ESOV |
|
6.監控、緊急應變 | 避難逃生(1) | 任一點兩方向逃生出口 |
災後搶救(4) |
1.四週門禁、CCTV 監控 2.風險評估,不同情境提供相對應變演練計畫 3.半年緊急應變演練 4.氫氣槽車Backup |
圖3、氫氣水電解房1F Layout
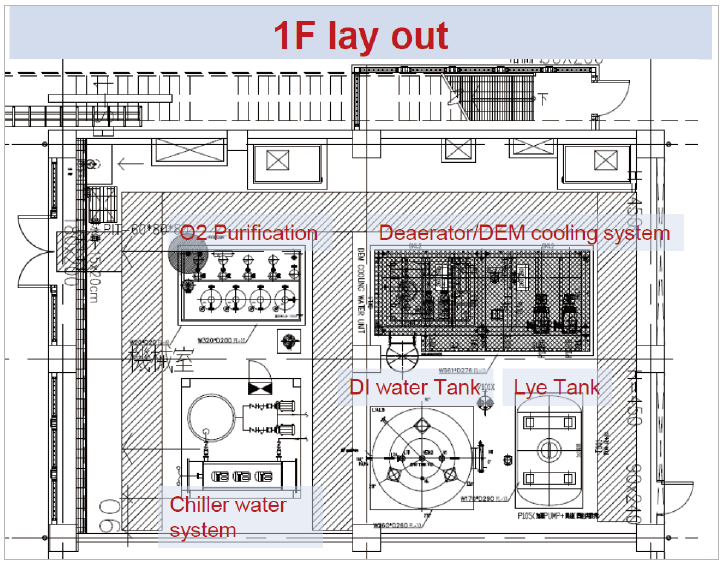
圖4、氫氣水電解房2F Layout(電器室)
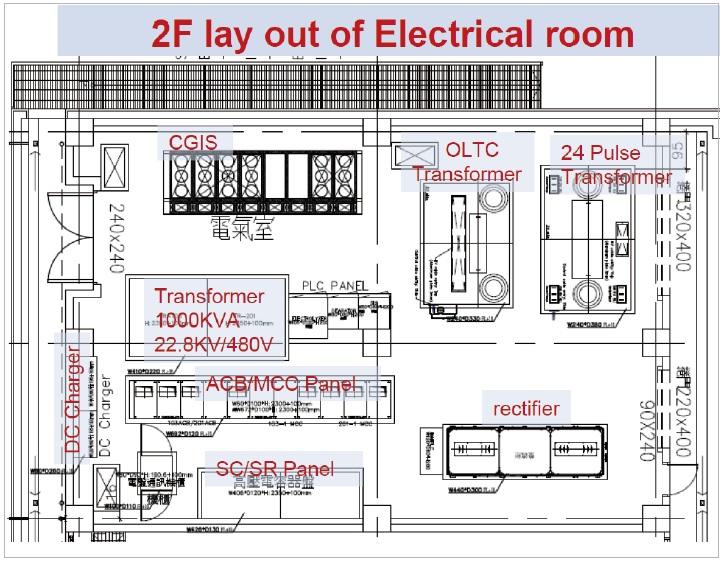
圖5、氫氣水電解房2F Layout(電解房)
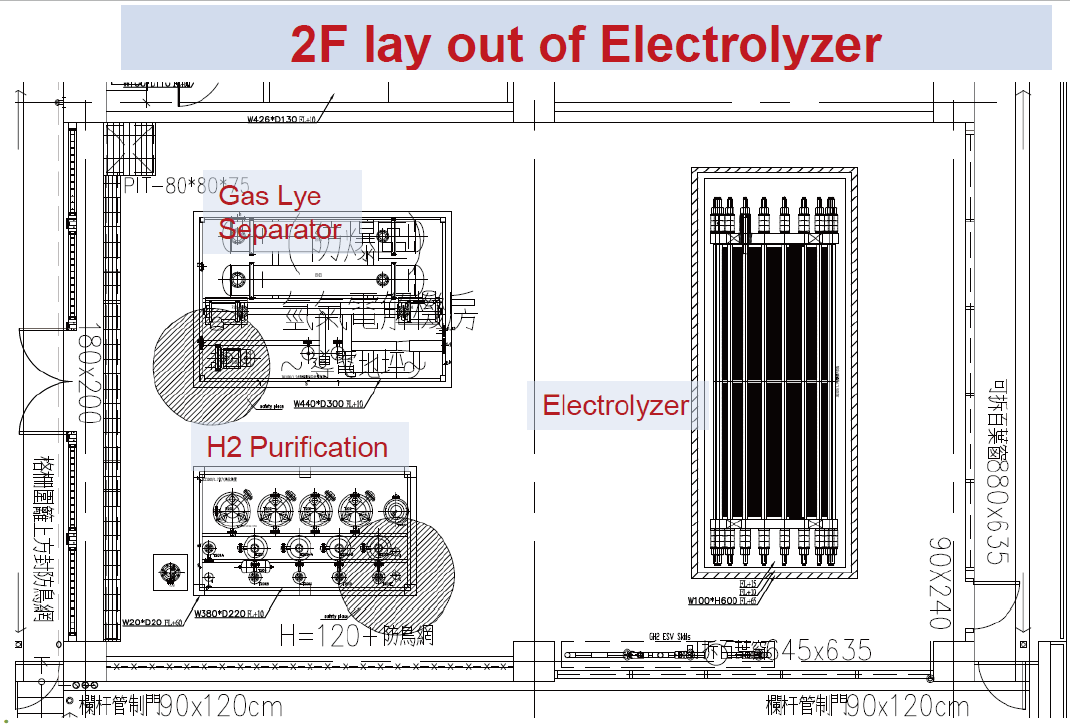
3.2 水電解理論及系統製程架構
水電解理論基礎依據法拉第第一定率,電解時在電極上析出物質的數量與通過溶液的電流強度和通電時間成正比,也就是與通過溶液的電量成正比,即G(生成量)=Ke(電化當量)I(電流)t(通電時間)。法拉第第二定律定義,用相同的電量通過不同的電解質溶液時,各種溶液在兩極上析出物質的量與它的電化當量成正比,而析出一克當量的任何物質都需要96500庫倫(C)的電量,以法拉第(F)表示。(1法拉第=96500庫倫=26.8A*小時) ; 電化當量的數值應等於化學當量e被法拉第常數除所得的商 : Ke=e/F ; 故G=KeIt=(e/F)It。氫離子是一價的,所以需要2mole的電子才能產生1mole的氫,因此要產生1mole的氫氣需要2法拉第的電量。1Nm3的氫氣是(22.4*2)=44.8mole,所以產生所需的電量是(44.8*2)=89.6法拉第,等於所需電量為 : 89.6*26.8=2401A*h。
本案採鹼性電解法系統設置,製程流程示意如(圖6),設備卡通圖及F18P4現場設備照片分別為(圖7、圖8) ; 製程原料來源為台積電廠務水課提供的純水(UPW)補充進純水槽,在純水槽加入氧氣曝氣純水,降低水中的含氮量 ; 曝氣過後的純水再到除氣器處理,利用電加熱器加熱純水至約100℃,氣化後經過蒸餾塔去除水中的雜質(N2, Ar) ; 電解質為KOH與除氣後的純水維持30%比例後就開始做電解槽循環,於電解槽陽極出口產出氧氣/KOH液,陰極產出氫氣/KOH液 ; 並各自到氫氣/氧氣的氣液分離器,利用重力將氣體與液體初級分離出,氣體往上繼續到純化器,液體則回流到電解槽繼續循環製程 ; 純化器內會先經過除氫(氧)器,其利用金屬鈀觸媒催化劑將氫/氧氣中的微量氧/氫合成為水,最後再經過分子篩,吸附氫/氧氣中的水分,常溫吸附,高溫脫附,去除的水由冷卻器除水排出,並得到最終成品的氫/氧氣。
圖6、水電解製程流程
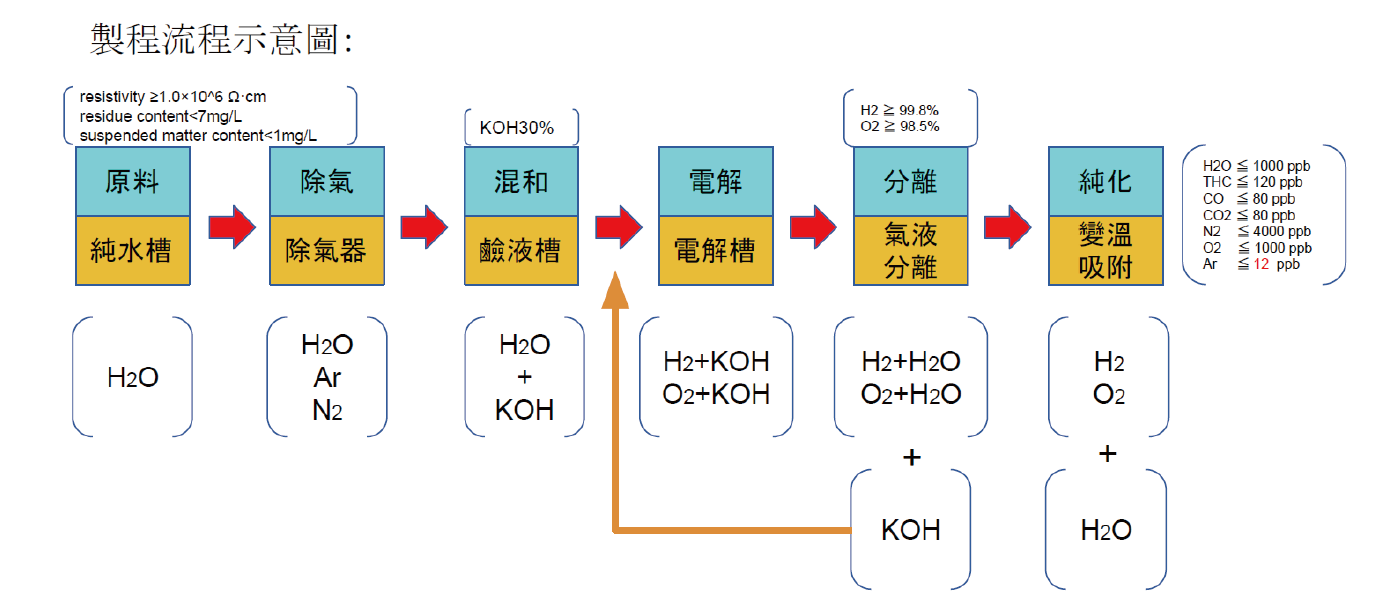
圖7、水電解製程卡通圖
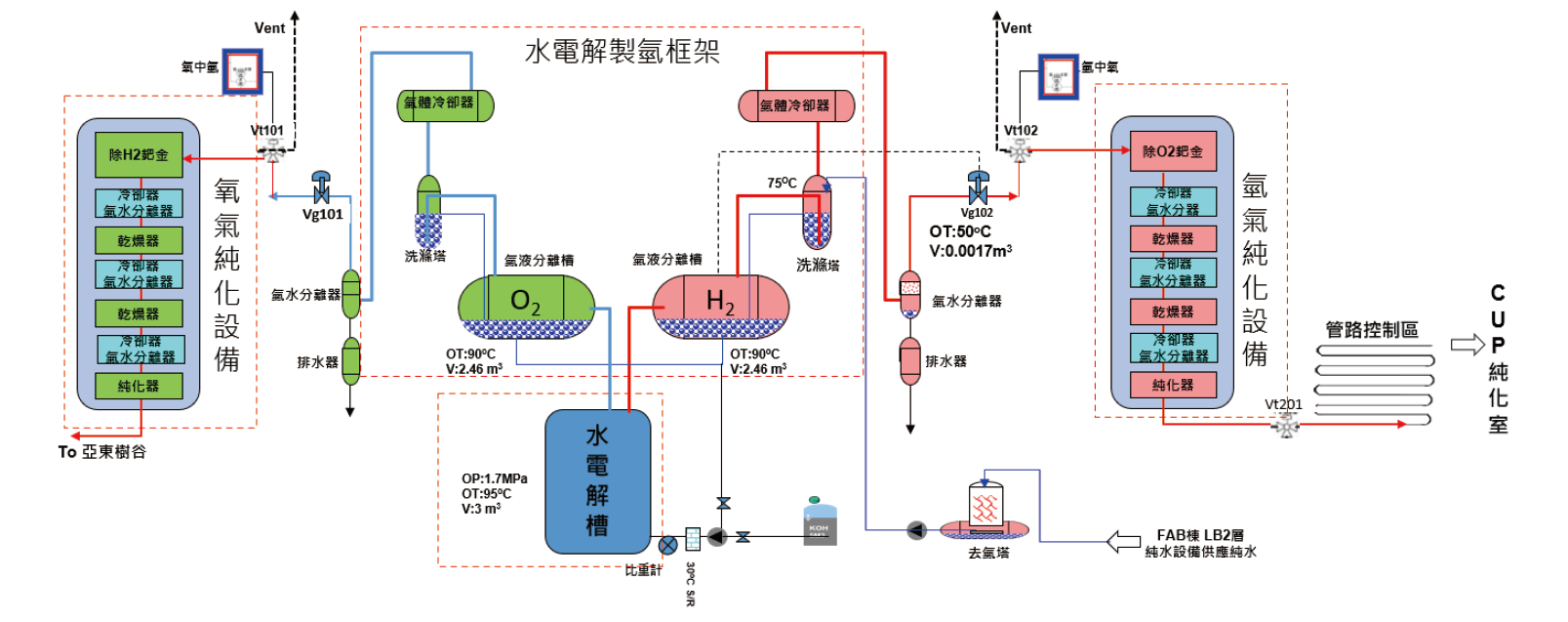
圖8、F18P4現場設備照片

3.3 KOH管路設計工法規範
純水幾乎不導電,所以在電解時必須加入其他的強電解質來增加導電能力,強酸(H2SO4)、強鹼(NaOH、KOH)都可以選用,考量鹼液的電導率較好且對鍍鎳電極穩定性好,故目前工業上都採用鹼性電解液 ; 而KOH在導電性能比NaOH好,又可以節約電能,但缺點是有較容易腐蝕的風險。在亞東安南廠也有發生管路腐蝕洩漏案例,特此委外專家進行分析及改善。
研究洩漏管路分析主因有兩項(管路材料及銲接手法)[3],在本廠針對其改善手法如(表4)。選用高鎳成分管材有助於提升抗應力腐蝕破裂(stress corrosion cracking, SCC) ; 此外銲接一定會造成成份偏析,材料微觀組織也會改變,導致有縫管材銲縫的耐蝕力會較差。除非要求管材在銲接成型後,得經至少35%斷面縮率的冷加工處理後,才進行完全退火水淬處理,否則難以確保材料退火後的耐蝕度均勻一致 ; 故分析後需在材料規格上選用無縫管且是日本JIS 316L規格(因美規含鎳量低),另外也不能做額外噴砂處理(噴砂後也會有殘留應力,易造成鏽蝕)。銲接施工上為避免KOH管路產生「熱裂、應力腐蝕與均勻腐蝕」等問題,都需著重「降低銲道殘留應力」與「避免因析出而影響材料耐蝕力」兩項大原則 ; 故規定試銲必須確認全滲透銲及寬度要求,另額外新增銲道退火熱處理程序 : 工法為焊道加熱約至1100度後保持兩小時然後自然降溫(圖9),最後再做PT銲道探傷檢測(圖10)。
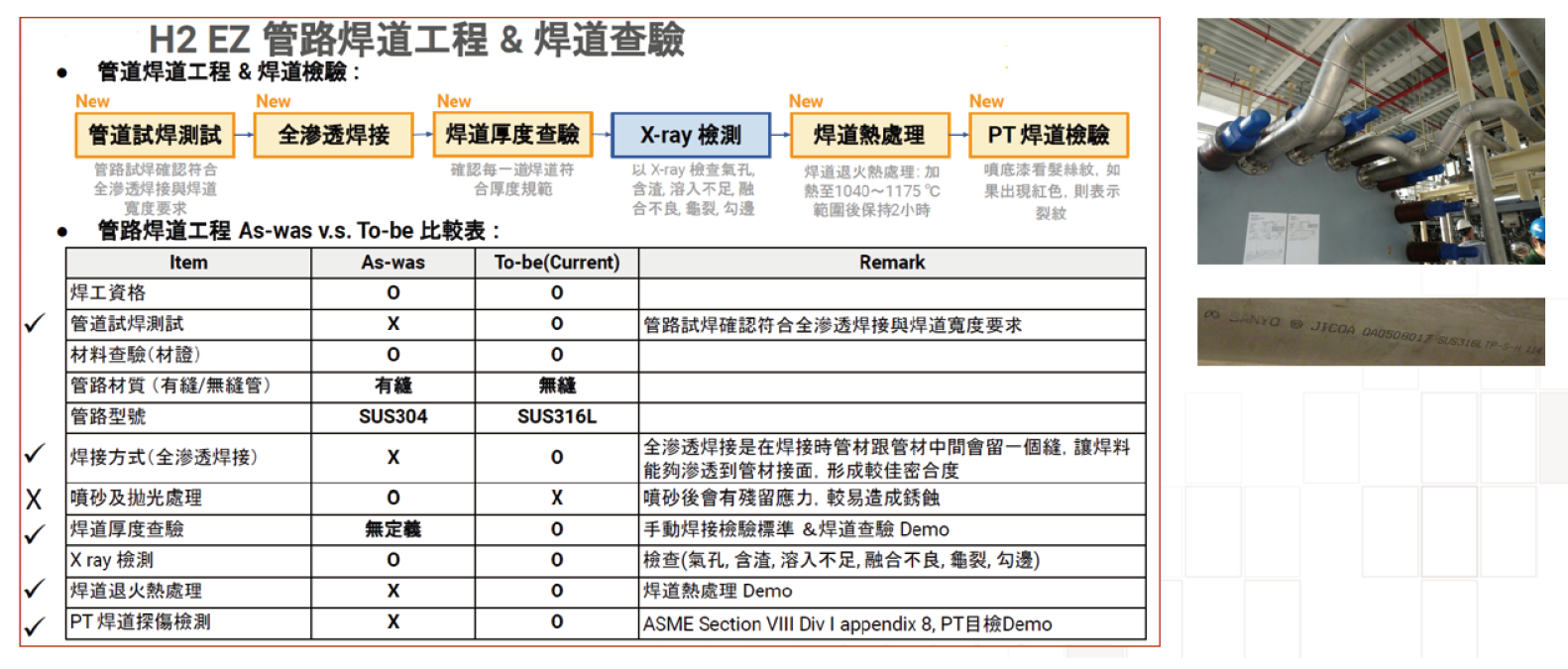
圖9、焊道退火熱處理
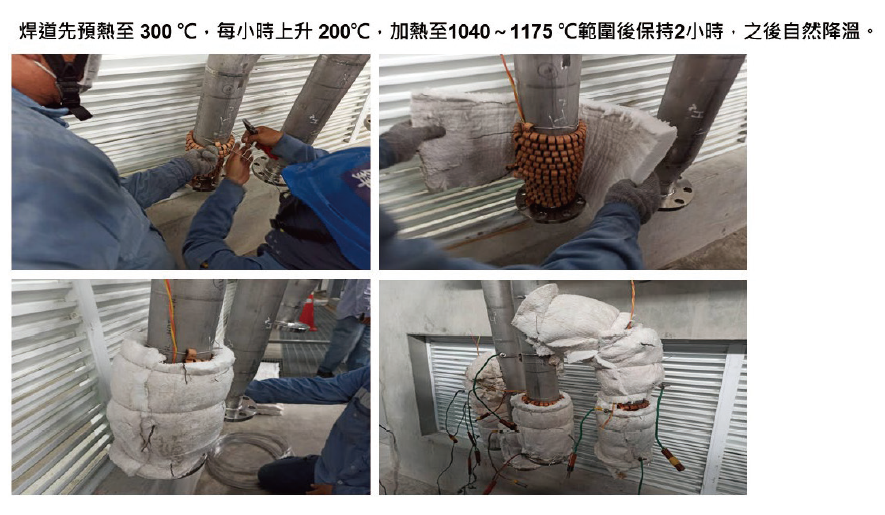
圖10、PT焊道探傷檢測
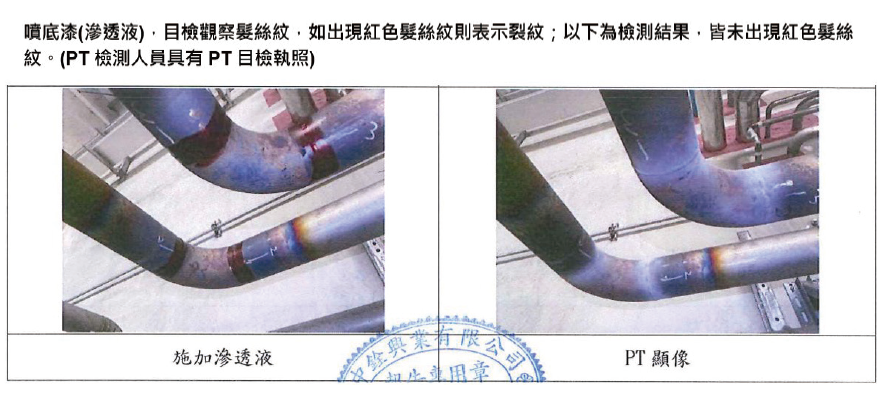
3.4 氫氣/氧氣排放管路濃度模擬與設計
系統於試車或復歸啟停機時會有持續排放氣體需求,最大排放量可達1000CMH(氫氣)/490CMH(氧氣),排放管區域除了安全性考量外亦要避免干擾到GMS偵測點。
氫氣排放管設計準則 : ①大氣擴散濃度在25%LEL (10000ppm)範圍內無電器設備;②避雷針傘覆可涵蓋排放管周界25%LEL之範圍;③排放管周界濃度1000ppm以上無吸氣口;④依據NFPA2 & CGA-5.5可燃性氣體排放管線應設置阻火器(Fire Arrester)避免爆轟(detonation),詳細構造圖面如 圖11。起初規劃3點位置選擇(圖12),A點 : BSGS L20屋頂 ; B點 : BSGS L10綠地 ; C點 : CUP RF,藉由濃度擴散模擬(圖13)最後選定C點(CUP RF)位置可符合上述規範。
氧氣排放管設計依據EIGA Table(圖14)及管路plan view濃度示意(圖15),選定於BSGS L20屋頂,距離地面高度17m,管路設計為80A其富氧區域(含氧濃度>23.5%)為水平距離13米、垂直距離4米,(含氧濃度>25%)為水平距離9米、垂直距離3米,此範圍內會標示嚴禁動火,並且施工需提出Level-1申請。
圖11、阻火器構造及現場安裝照片
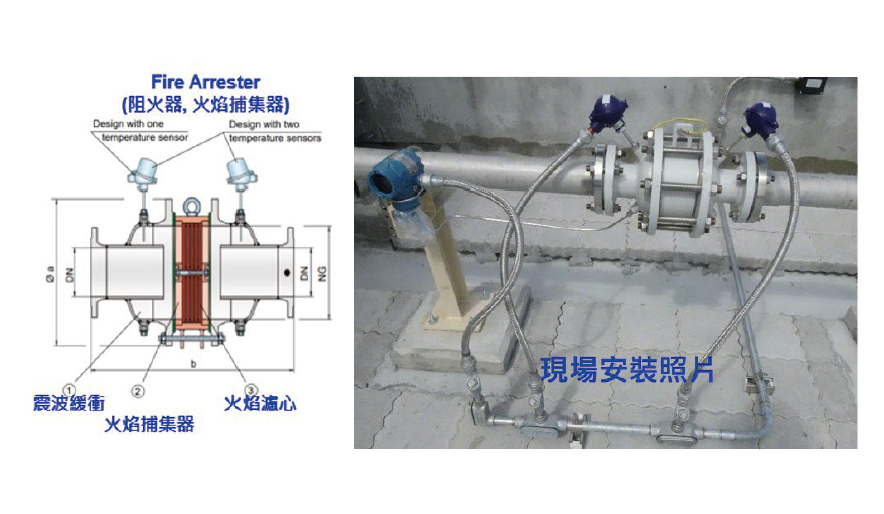
圖12、氫氣排放管位置規劃
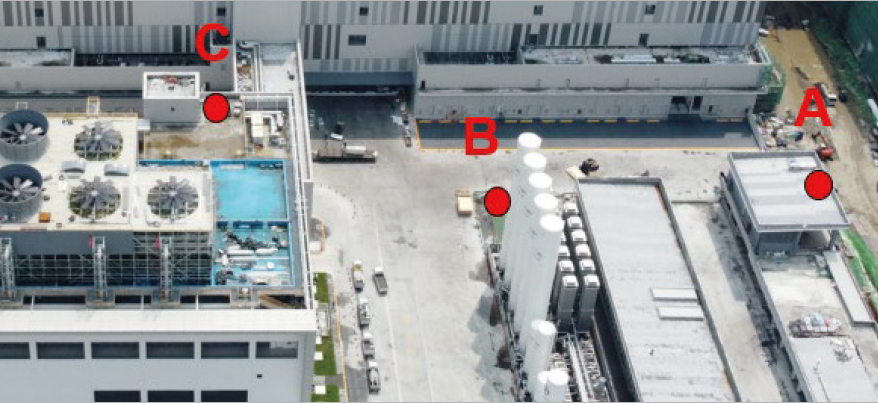
圖13、氫氣排放模擬濃度範圍
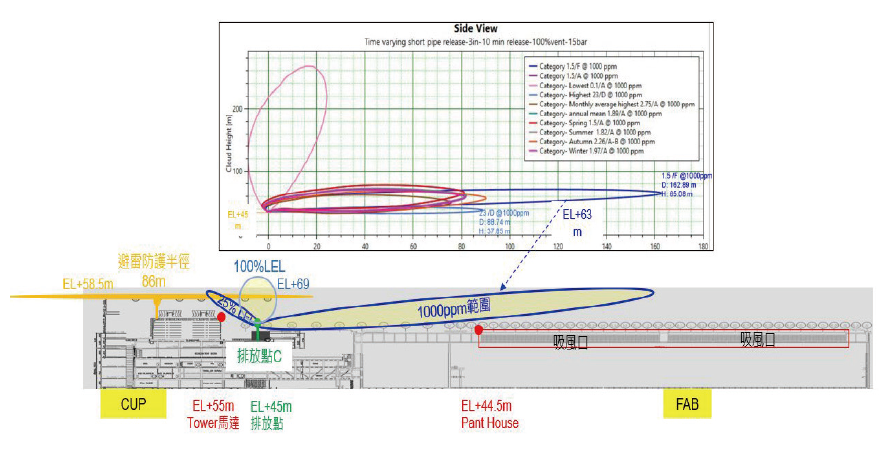
圖14、EGIA Code Table A-1
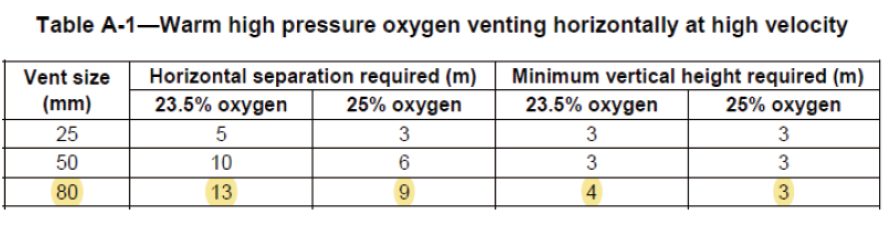
圖15、氧氣排放模擬濃度範圍
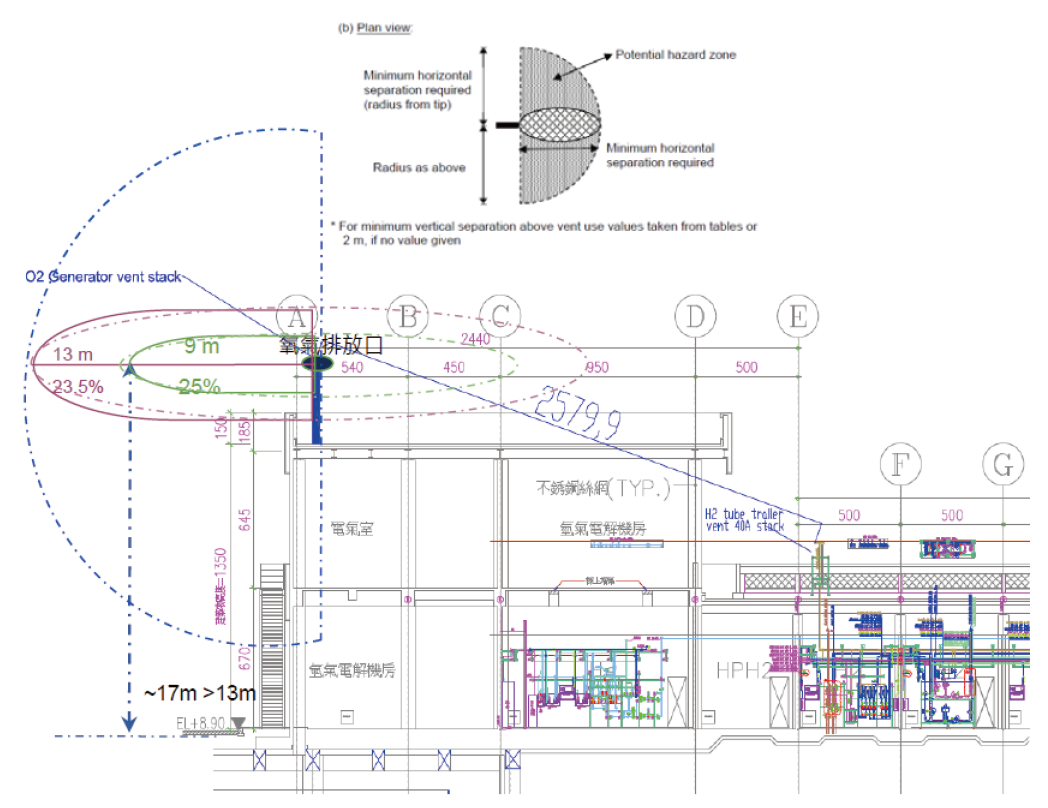
4. 系統穩定運轉管理
4.1 氣體廠經驗傳承
本案為台積廠內所設置的第一座氫氣製造設備,考慮缺乏相關運轉及維護經驗,從去年8月開始就有派相關同仁陸續到亞東安南廠參訪學習,針對軟硬體BKM導入共21項(表5),已完成14項,剩餘7項正在試車調適中 ; PRS比較共11項(表6),與安南廠主要不同3項 : ①純水桶大小(廠內空間問題->確認size可符合capacity);②供應方式(安南 : 槽車 ; 台積 : 地管);③H2緩衝槽/氧液化塔On-site無配置是只有灌充槽車出貨才需要 ; 運轉LsL共計7項(表7),皆全數完成。藉由上述的經驗複製傳承來確保生產過程安全性及品質正確性的導入。
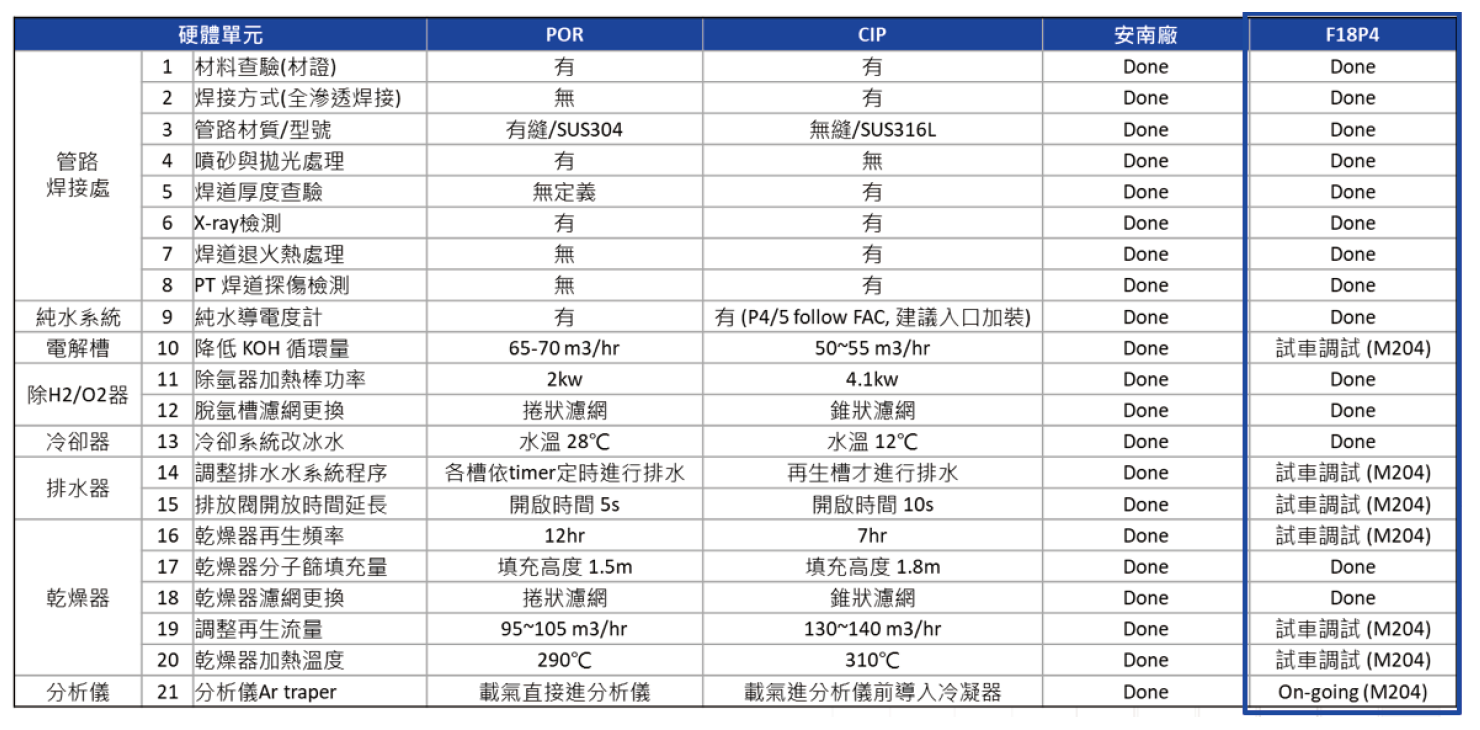
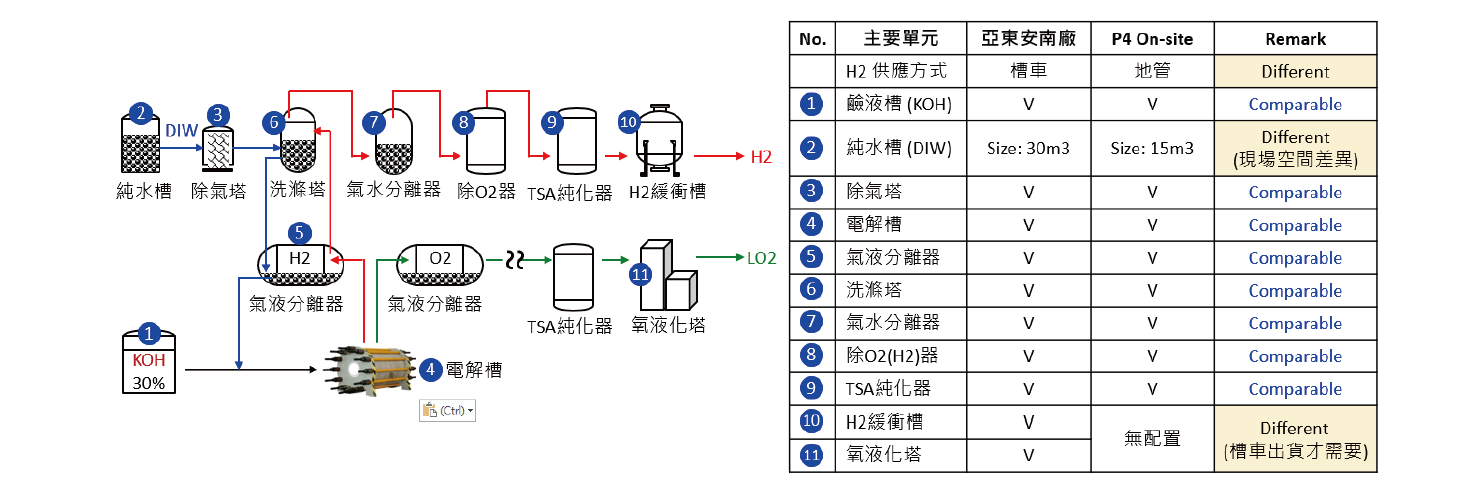
Item | Issue | Root Cause | F18P4 Improve Action | Status |
---|---|---|---|---|
LSL | 整流器髙溫Trip |
|
|
Done |
LSL | 整流器突波保護器燒壞 | 啟動瞬間突波電流過大超過當初設計值(100W) | 專家評估:突波保護器改600W | Done |
LSL | 純水脫氣塔板式熱交換器無N + 1 | 板式熱交渙器效能不佳造成無N+1設計(設計2組),目前使用率會達110% |
|
Done |
LSL | 純水脫氣塔安裝工期長 | 純水脫氣塔分成許多單元安裝及配管,施工時間拉長 | 純水脫氣塔己於原廠銜接模組化,大幅縮短施工時間 | Done |
LSL | 氧純化氣壓差較大造成流量不足 | 濾網設計造成壓差過大 | 濾網更換錐形Type | Done |
LSL | 電解槽出口管路洩漏 | 管路材質選用,焊接手法不良(焊道leak) |
|
Done |
LSL | O2純化後H2 Impurity過高 25ppm |
去氫觸煤的加熱糸統功率不足(~2.1Kw),無法加熱至高溫 | 更換加熱系統功率高(~4.1Kw)Type,可加熱至180度,O2純化後H2不純物降到5~10ppb | Done |
4.2 值班應變訓練及備援規劃
On-site水電解設備為連續生產並直接供應,因此規劃亞東氣體人員需在台積駐廠值班。值班除了監控系統是否正常外,緊急應變處理是非常重要的,所以在系統上線前,台積廠務與亞東值班共完成了三次現場緊急應變演練(圖16為第1次演練紀錄),也安排在每季都會進行演練。另系統安全連鎖機制導致跳俥總共設置34項,也在安檢時與ISEP確認測試正常,其相關處理程序及OCAP如(圖17) ; 品質異常跳俥亦有其對應程序及OCAP如(圖18)。跳俥後氫氣供應會自動轉槽車備援供應(壓差供應,槽車供應壓力設定小於水電解供應壓力),後續槽車運補計畫也有納入事先考量(表8)。
圖16、水電解氫氣洩漏演練紀錄

圖17、水電解設備安全跳車連鎖機制與OCAP
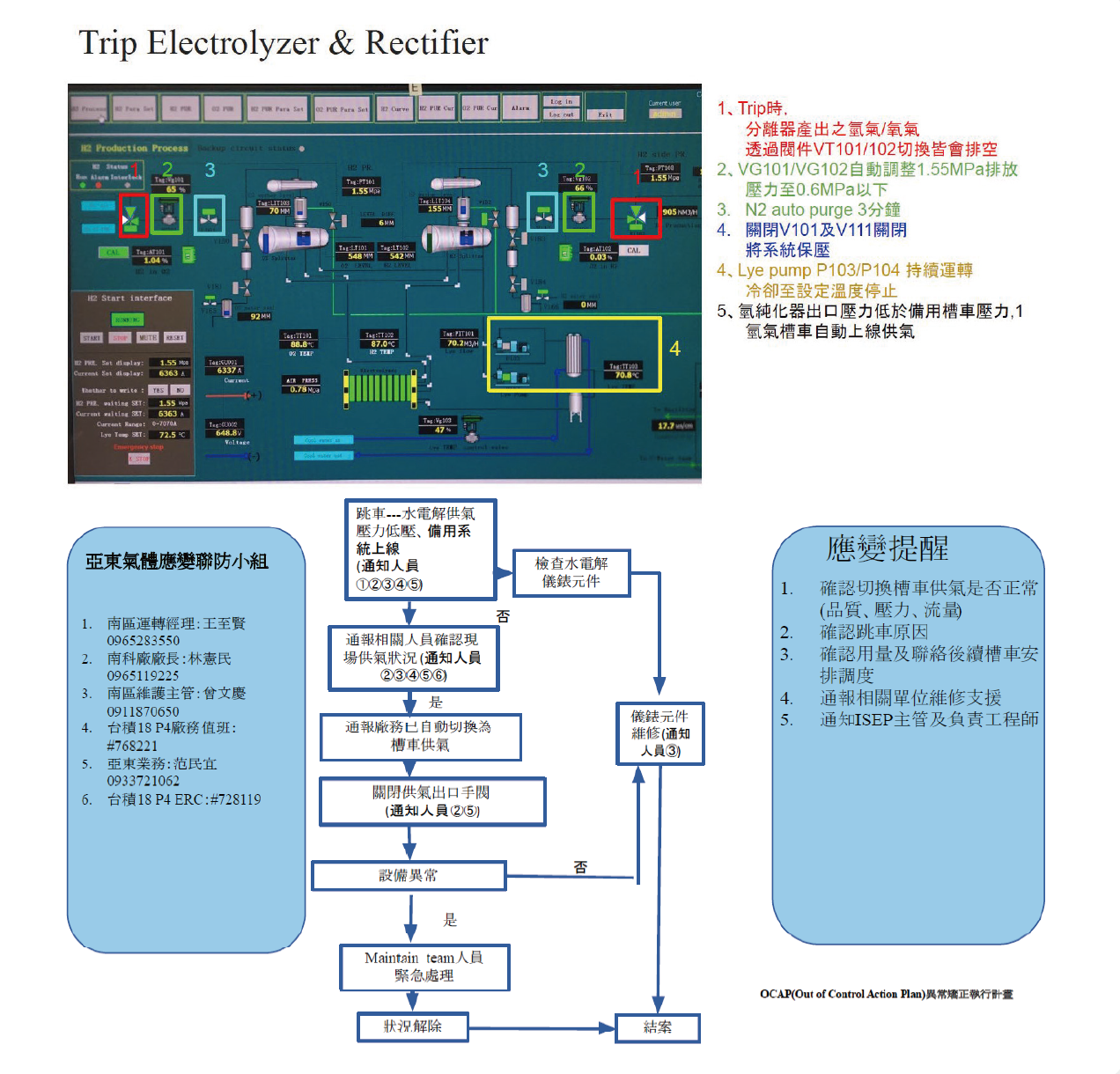
圖18、水電解製程品質異常連鎖機制與OCAP
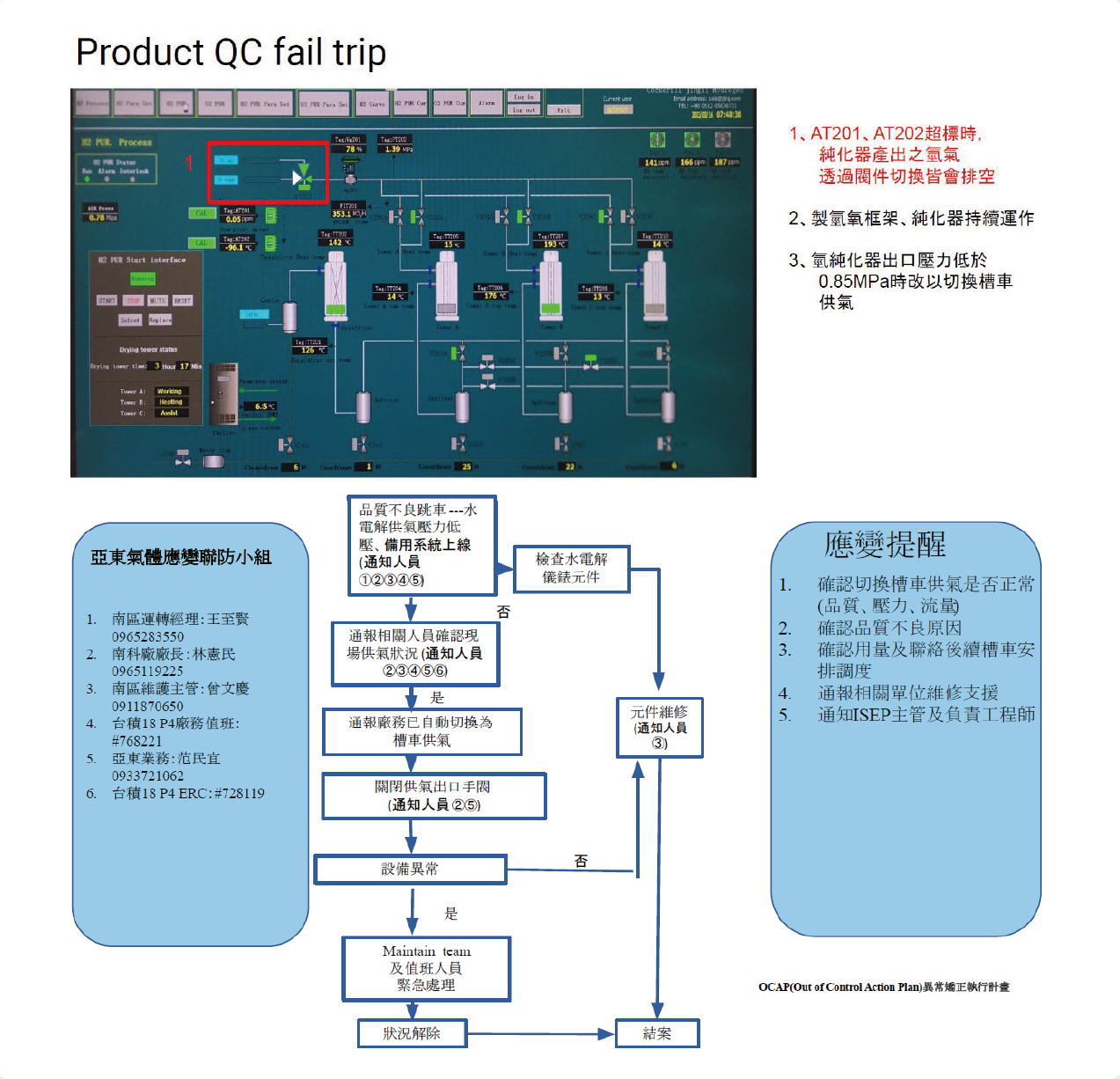
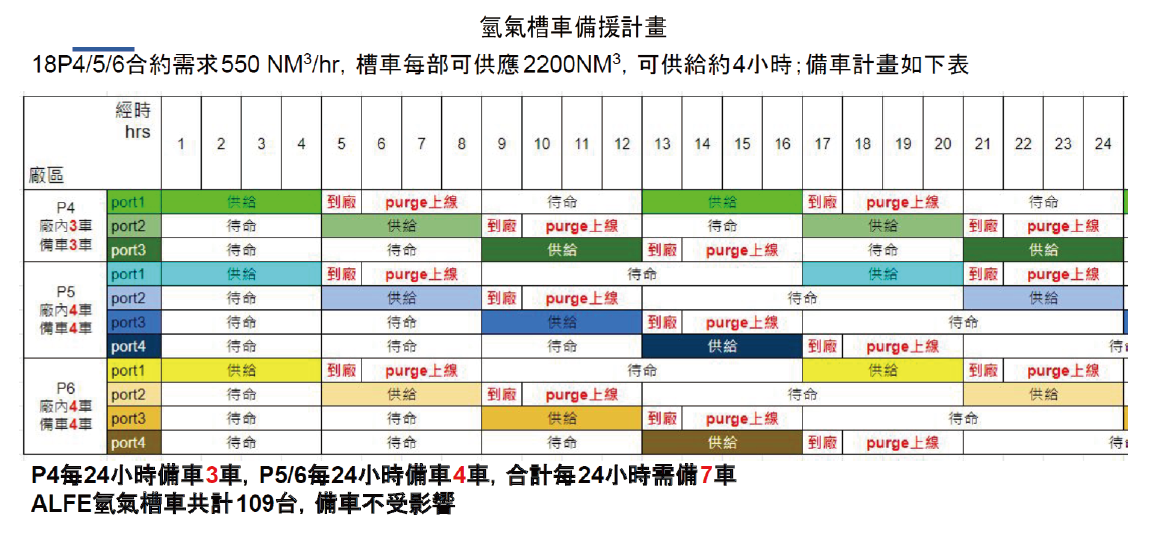
5. 結論與未來展望
5.1 結論
本案(F18P4氫氣水電解)建置工程共花了約3個多月 (2021/9/1~12/23),2022年2月25日取得系統所有設備的高特證照(共41張),在3月29日進行丙危現勘審查,於4月25日收到南科管理局核發丙危合格函。期間感謝廠務新工處、RM、Site ISEP、亞東同仁及其他各相關單位共同努力,現在已進入試俥階段,期間有發現試俥排放的氫氣會干擾到FAB有微量讀值狀況,經分析氣候條件歸納風向、降雨、風速為關鍵因子,試俥與否會卡控這三項條件(圖19),另外新工也針對氫氣尾氣處理提出燃燒塔的方案,預計會在2023年Q1達成,未來會持續收集試俥遇到的問題給之後的廠參考改善(F12P8、F18P5建置中),待品質穩定且符合標準後將安排廠內的pi-run驗證。
圖19、初期試俥停機vs.氣候分析
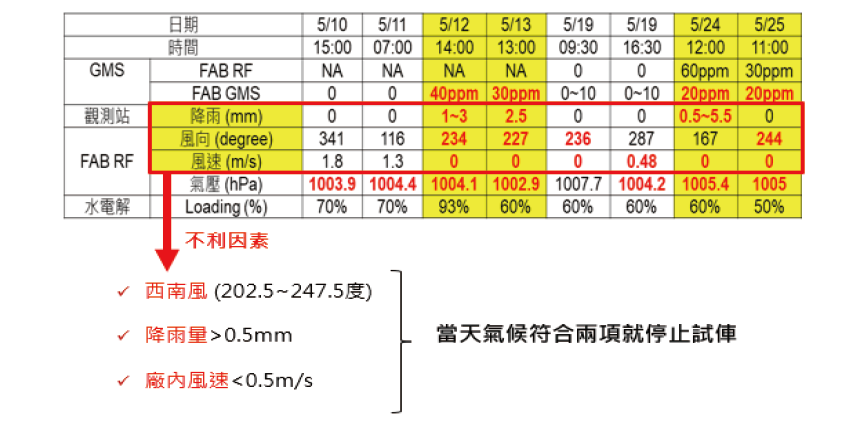
5.2 未來展望
耗電量仍是目前氫氣水電解最大缺點,每生產1m3的氫氣必須消耗電力達4.5~5.5kwh左右,電費佔生產總成本約80%。若未來電力來源為綠電狀況下,水電解製氫設備就可完全達到零碳排放成效。另外現況EUV用到大量氫氣後就直接排放,已在設計將氫氣做回收利用進而轉為能源儲存的氫氣回收系統,相信不久後也會導入台積廠內建置測試,為台積在零碳排里程碑上又更進一步。
參考文獻
- 電解氫技術發展概況分析,台灣經濟研究院陳婕莉。
- 太原麗子(2018),電解產氫技術簡介及日本發展現況研析。
- 設備配管查驗報告,楊山毅博士。
留言(2)
test......